RH精炼技术的发展资料
RH精炼技术的发展
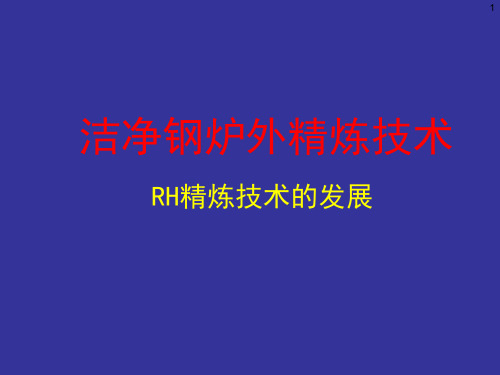
脱
磷
7
将RH吹氧工艺与喷粉工艺相结合可以实现RH脱磷。在RH吹氧脱碳期同时喷 吹石灰粉可以达到理想的脱磷效果。如日本新日铁名古屋厂230tRH采用OB/PB工 艺,可生产[P]≤20×10-6的超低磷钢。 粉剂中(%CaO)≈20%时,炉渣脱磷能力最强。提高真空度使炉渣脱磷能力略 有提高。根据RH-PB处理中取出的粉剂颗粒,经X光衍射分析的结果绘出右图。 由于RH喷粉避免了顶渣的影响,延长了粉剂与钢水直接反应的时间,使脱磷效 率提高。如图所示,上浮粉剂颗粒中P2O5含量接近3CaO· 2O5或4CaO· 2O5的理 P P 论极限。远高于铁水预处理或转炉脱磷效率。
杂的排出速度可以表示为: d[O]T ko [O]T dt out
渣中FeO+MnO含量和脱氧速度 常数k间的关系
夹杂物尺寸对去除的影响
钢中夹杂物的上浮决定于夹杂物的尺寸:大颗粒夹杂上浮去除,而小颗粒夹杂 通过碰撞聚合后才能上浮去除。因此,精炼过程中钢水夹杂物的数量可采用浅野等 人提出的表达式描述: N = N0· exp(-· D) 式中:D为夹杂物的半径;N为夹杂物的数量(l/kg);N=、为常数。 钢水氧含量的变化表达式如下:
9
3M 0 T [O] 10 P D 3 N o exp( D)dD M Al2O3 6 0
6
0.50
RH精炼过程中T[O]的行为
ko和搅拌能量的关系
NK-PERM法
10
为了提高RH的脱氧效率,日本 NKK公司开发了一种通过钢包脱气 处理去除夹杂物的新方法,称为NKPERM法。该工艺的技术原理是:首 先将可熔气体(如N2、H2)强行熔解 到钢水中,然后进行真空精炼,再降 NK-PERM处理后夹杂物分布的变化情况 压过程中过饱和气体在悬浮的微细夹杂物表面形成气泡,气泡 与夹杂物上浮到液面迅速与钢水分离。通过250t RH工业试验, 该工艺获得良好的冶金效果,细小夹杂物的去除效率明显提高。 采用RH喷粉工艺,使链状Al2O3夹杂与CaO粉剂形成低熔 点CaO· 2O3夹杂,利于上浮排除。采用RH喷粉工艺后, Al Al2O3夹杂含量明显降低。
RH精炼炉工艺

RH精炼炉工艺摘要:介绍了RH的发展历史,对RH中最关键的真空系统原理进行了说明,介绍了莱钢RH的功能、设备及工艺,针对莱钢情况,对莱钢品种开发进行了探讨。
关键词: RH 原理工艺品种1 RH的历史与发展RH精炼全称为RH真空循环脱气精炼法。
于1959年由德国人发明,其中RH为当时德国采用RH精炼技术的两个厂家的第一个字母。
真空技术在炼钢上开始应用起始于1952年,当时人们在生产含硅量在2%左右的硅钢时在浇注过程中经常出现冒渣现象,经过各种试验,终于发现钢水中的氢和氮是产生冒渣无法浇注或轧制后产生废品的主要原因,随之各种真空精炼技术开始出现,如真空铸锭法、钢包滴流脱气法、钢包脱气法等,从而开创了工业规模的钢水真空处理方法,特别是蒸汽喷射泵的出现,更是加速了真空炼钢技术的发展。
随着真空炼钢技术的开发与发展,最终RH和VD因为处理时间短、成本低、可以大量处理钢水等优点而成为真空炼钢技术的主流,70年代开始随着全连铸车间的出现,RH因为采用钢水在真空槽环流的技术从而达到处理时间短、效率高、能够与转炉连铸匹配的优点而被转炉工序大量采用。
RH从开始出现到现在40多年来,有多项关键性技术的出现,从而加速了RH精炼技术的发展。
表1为40多年来RH技术的发展情况。
表1 RH技术发展情况2 RH系统概述RH系统设备是一种用于生产优质钢的钢水二次精炼工艺装备。
整个钢水冶金反应是在砌有耐火衬的真空槽内进行的。
真空槽的下部是两个带耐火衬的浸渍管,上部装有热弯管。
被抽气体由热弯管经气体冷却器至真空泵系统排到厂房外。
钢水处理前,先将浸渍管浸入待处理的钢包钢水中。
当真空槽抽真空时,钢水表面的大气压力迫使钢水从浸渍管流入真空槽内(真空槽内大约0.67mbar时可使钢水上升1.48m高度)。
与真空槽连通的两个浸渍管,一个为上升管,一个为下降管。
由于上升管不断向钢液吹入氩气,相对没有吹氩的下降管产生了一个较高的静压差,使钢水从上升管进入并通过真空槽下部流向下降管,如此不断循环反复。
RH(真空循环脱气法)

RH 的发展状况
RH工艺发展过程中装置变化图 工艺发展过程中装置变化图
RH工艺 工艺
RH 的发展状况
• 1. RH——O(RH顶吹法) 1969年德国蒂森钢铁公司恒尼西钢厂开发 成就:首次用铜质水冷氧枪从真空室顶部向循 环着的钢水表面吹氧,强制脱碳升温。
RH-O产品 产品—Made in china 产品
• 1.RH的起源 • 2.RH的应用成效 • 3.RH的发展状况 • 4.RH在世界的开发与应用
RH 的起源
1. RH真空精炼技术起源于50年代,1957阿尔 贝德公司申请了钢水真空精炼脱气法的技术 专利,这是真空脱气法发展的开端 。
RH 的起源
2.1958年德国Rheinstahl(莱茵钢公司)和 Heratus (赫拉乌斯)真空泵厂合作成功地进行了工业性生 产实验,取得了可喜的处理效果,在1959年德国冶 金工作者协会上引起了同行的极大关注.定名—— RH
1963年日本引进rh真空精炼技术后在脱氢的基础上又开发了脱碳脱氧吹氧升温喷粉脱硫和成分控制等功能使改进后的rh法能进行多种冶金操作更好地满足了扩大处理钢种范围提高钢材质量的要求11995年攀钢130trhmfb项目引进技术的消化吸收21998年宝钢250trhmfb项目引进技术的消化吸收32000年梅钢150trhmfb项目基本立足国内设计制造42002年宝钢2号130trh项目的建设52003年攀钢2号rh投产开辟了我国用rh精炼超纯净合金钢的先河宝钢二炼钢厂rhktb设备主要规格参数1000kg05乇以下35分钟内达到1乇类型双槽体处理周期3651min真空系统2boosters2ejectors排气能力浸渍管内径750mm环流量max
工艺装置图
RH 的起源
3. 最初RH装置主要是对钢水脱氢,后来增加了真空 脱碳、真空脱氧、改善钢水纯净度及合金化等功 能。采用RH工艺后,可以缩短转炉生产周期,提 高收得率,节约脱氧剂及合金元素,改善钢质量 ,而且脱气处理后一般可缩短热处理时间,获得 较好的经济效果。
1RH真空循环脱气炉发展概论及相关设备
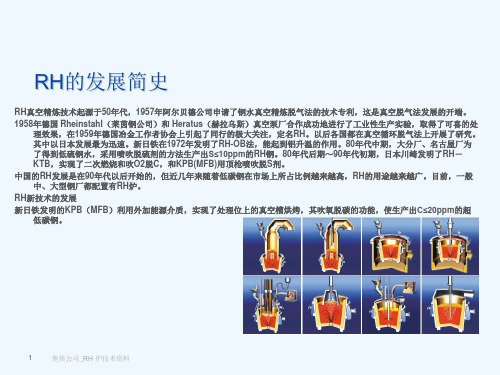
为解决这个难题,目前部分工厂将真空槽设计成整体式,即用焊接 代替法兰连接,避免了水冷法兰造成的耐材损坏。目前浸渍管 与下部槽之间已基本取消了水冷法兰连接,改为电焊连接,上、 下部槽之间有的已经取消水冷法兰,有的仍在运用。本厂RH上、 下真空槽仍采用水冷法兰连接。
1
奥镁公司_RH 炉技术资料
Degassing processes – RH 炉发展简史
DH
=
DH-OB =
RH
=
RH-OB
=
RH-OTB = RH-KTB =
RH-MFB =
Dortmund Hörde,1956 at the Dortmund-Hörder-Hüttenunion.. Dortmund Hörde with Oxygen Blowing Ruhrstahl Heraeus,RH精练法是德国钢铁公司Ruhrstahl和Heraens 联合于1958年成功开发的真空循环脱气法 Ruhrstahl Heraeus with Oxygen Blowing. 1972年新日铁室兰厂根据VOD 生产不锈钢的原理,开发了RH-OB真空吹氧技术。 Ruhrstahl Heraeus with Oxygen Top Blowing (same as RH-KTB) Ruhrstahl Heraeus Kawasaki Top Blowing. 1986年日本原川崎钢铁公司( 现已和NKK重组为JEE公司)在传统的RH基础上,成功地开发了RH顶 吹氧(RH KTB)技术,将RH技术的发展推向一个新阶段。 Ruhrstahl Heraeus Multifunctional. 1992年日本新日铁 公司广畑厂在日本 原川崎公司开发RH-KTB精炼技术之后,为降低初炼炉的出钢温度以及脱 碳的需要,开发了多功能喷嘴的RH顶吹氧技术
新版近十年来国内RH真空精炼技术的发展

邱勤
宝钢工程技术集团有限公司
1.
近十年来国内RH真空精炼技术发展现状
2.
RH真空精炼技术的完善和发展
1 近十年来国内RH真空精炼技术发展现状
2009年在太钢召开 全国精炼年会。
2011年………
2007年在宝钢召开了 第一届RH年会。
中国RH真空装置增长趋势图
宝钢股份炼钢厂转炉分厂钢水RH真空精炼比
阀站照片
监控画面
监控画面
(2) 布置的多样化
布置工位 多样化
、双台车单工位、大包回转台 式 双工位:两车三位、两车四位、 三车五位、四车六位。
(3) 设备的适应性更强
整体槽、分体槽
单路、多路 小合金料仓的设计 不同真空料斗的设计 环流的控制
真空泵形式多样化
(4)研发的核心技术装备 大型真空泵 真空主阀 大吨位钢包 顶升技术 钢包提升装置 顶枪预热枪技术
“多功能 化”的充 分应用
进一步实 现高效化
如何在生产中不断优化RH工艺和设备将是今后重点工作
2 RH真空精炼技术的完善和发展
RH喷粉工艺、设备、控制技术完善 RH氮控制技术完善 耐火材料合理选择和开发
开发适应电炉厂的RH真空精炼设备
开发新的RH钢水热补偿升温技术
如何在生产中不断优化RH工艺和设备将是今后重点工作
1.1
RH真空精炼生产工艺技术的发展和应用推广
产品品种的变化, 质量的不断提高
RH真空精炼生产 工艺技术的发展 RH真空精炼生产 工艺技术的推广
1.2
RH真空精炼工艺和设备技术的开发和应用
1.2.1 RH真空精炼工艺设备设计的创新和发展 (1)功能的多样化 去除有害气体 脱碳 成分微调 脱硫 降低非金属夹杂物含量 钢水升温 协调转炉、连铸生产
RH机械设备介绍
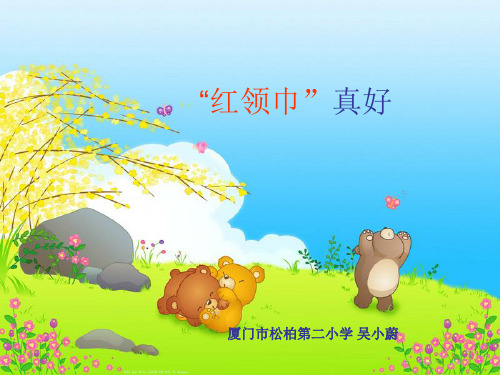
╳
24,000 =>6,670
28000
450
(180=> 50)
〇〇〇
╳〇 〇
╳
6.670=> 930
25600
1700 450
(50=> 7)
〇〇 〇
╳ ╳〇 〇
930=>270
26700
1700 450
(7=> 2)
〇 〇〇mit
28000
1700 450
(2=>Limit) 〇 〇 〇 〇
六级泵(原1RH)
抽气
1
2
排气
3
水封池
系统中共有6个蒸汽喷射泵,4个冷凝器,系统所选 用的蒸汽压力一般为0.8MPa,排出压力为大气压 760Torr,而各级泵的真空度如下表如示:
1B 2B 3B 4E 5E 6E 泵
真空度
0.5 1.5 6
(Torr)
55
120 320
排气能力(换算为常温空气): 在200乇 时 7000kg/h 在10乇 时 3000kg/h 在0.5乇 时 950kg/h 在0.15乇 时 250kg/h
- 根据所判定的钢水液面高度,钢包被液压缸顶升,使真空槽的浸渍管浸 入钢水到预定的深度。同时,上升浸渍管以一定的流速喷吹氩气。随着 浸渍管完全浸入钢液,真空泵启动。
- 各级真空泵根据预定的抽气曲线进行工作。
- 进行测温、取样、定氧操作。
- 真空脱氢处理,将在规定时间及规定低压条件下持续进行循环脱气操作 以达到氢含量的目标值。
去冷钢
1988年鹿岛制铁所开发了用烧嘴去冷钢方法 解决真空槽结冷钢问题
真空槽
九十年代德国MEVAC把真空槽改成整体式及 焊接的浸渍管
RH培训资料
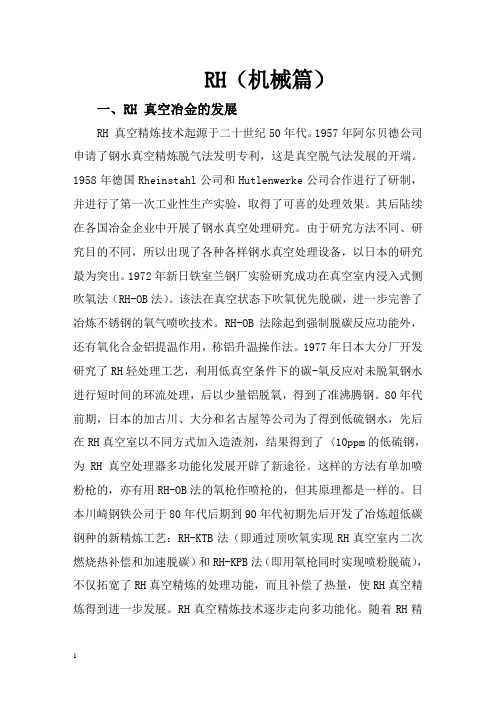
RH(机械篇)一、RH 真空冶金的发展RH 真空精炼技术起源于二十世纪50年代。
1957年阿尔贝德公司申请了钢水真空精炼脱气法发明专利,这是真空脱气法发展的开端。
1958年德国Rheinstahl公司和Hutlenwerke公司合作进行了研制,并进行了第一次工业性生产实验,取得了可喜的处理效果。
其后陆续在各国冶金企业中开展了钢水真空处理研究。
由于研究方法不同、研究目的不同,所以出现了各种各样钢水真空处理设备,以日本的研究最为突出。
1972年新日铁室兰钢厂实验研究成功在真空室内浸入式侧吹氧法(RH-OB法)。
该法在真空状态下吹氧优先脱碳,进一步完善了冶炼不锈钢的氧气喷吹技术。
RH-OB法除起到强制脱碳反应功能外,还有氧化合金铝提温作用,称铝升温操作法。
1977年日本大分厂开发研究了RH轻处理工艺,利用低真空条件下的碳-氧反应对未脱氧钢水进行短时间的环流处理,后以少量铝脱氧,得到了准沸腾钢。
80年代前期,日本的加古川、大分和名古屋等公司为了得到低硫钢水,先后在RH真空室以不同方式加入造渣剂,结果得到了〈10ppm的低硫钢,为RH真空处理器多功能化发展开辟了新途径。
这样的方法有单加喷粉枪的,亦有用RH-OB法的氧枪作喷枪的,但其原理都是一样的。
日本川崎钢铁公司于80年代后期到90年代初期先后开发了冶炼超低碳钢种的新精炼工艺:RH-KTB法(即通过顶吹氧实现RH真空室内二次燃烧热补偿和加速脱碳)和RH-KPB法(即用氧枪同时实现喷粉脱硫),不仅拓宽了RH真空精炼的处理功能,而且补偿了热量,使RH真空精炼得到进一步发展。
RH真空精炼技术逐步走向多功能化。
随着RH精炼技术研究的深入,可处理的钢种范围逐渐扩大,处理钢的质量不断提高,使得人们对RH精炼技术更加重视,逐步形成了一系列冶炼优质品种钢的工艺规程。
二、RH工作原理:它是由吸入和排出钢水的浸渍管和真空槽以及真空排气装置所组成。
处理钢水时,先将两个浸渍管浸入到钢包,使钢包和真空室形成密闭系统。
RH培训
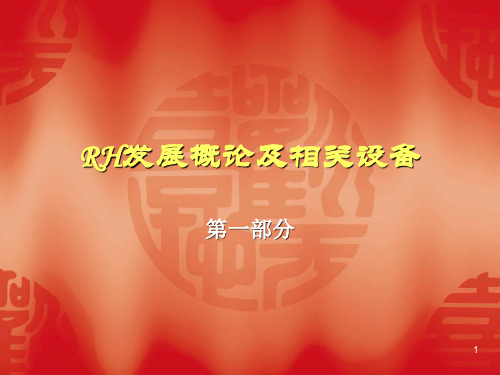
第一部分
1
RH的发展简史
RH真空精炼技术起源于50年代,1957年阿尔贝德公司申请了钢水真空
精炼脱气法的技术专利,这是真空脱气法发展的开端。 1958年德国 Rheinstahl(莱茵钢公司)和 Heratus(赫拉乌斯)真空 泵厂合作成功地进行了工业性生产实验,取得了可喜的处理效果,在 1959年德国冶金工作者协会上引起了同行的极大关注,定名RH。以后 各国都在真空循环脱气法上开展了研究。其中以日本发展最为迅速。新 日铁在1972年发明了RH-OB法,能起到铝升温的作用。80年代中期, 大分厂、名古屋厂为了得到低硫钢水,采用喷吹脱硫剂的方法生产出 S≤10ppm的RH钢。80年代后期~90年代初期,日本川崎发明了RH- KTB,实现了二次燃烧和吹O2脱C,和KPB(MFB)用顶枪喷吹脱S剂。 中国的RH发展是在90年代以后开始的,但近几年来随着低碳钢在市场 上所占比例越来越高,RH的用途越来越广。目前,一般中、大型钢厂 都配置有RH炉。 RH新技术的发展 新日铁发明的KPB(MFB)利用外加能源介质,实现了处理位上的真空 槽烘烤,其吹氧脱碳的功能,使生产出C≤20ppm的超低碳钢。
22
二、RH脱气原理
2、RH脱氮原理及影响因素
A:氮主要以化合物形态存在于钢中; B:氮可作为提高钢的硬度、耐磨性、抗蚀性的合金元素; C:对低碳钢Fe4N的析出将造成时效和蓝脆,达到一定程度时形成气泡
和疏松,使钢的塑性下降,对超低碳钢影响更大; D:氮在α-Fe、δ-Fe中的溶解度随温度升高而增加,在γ-Fe中相反; E:就氮在钢中的溶解度而言,遵循以下规律:[%N]=K [N] *(PN2)1/2, 在1600℃、1mbar下K [N] =0.045%,所以[%N]= 0.045%(PN2)1/2; F:V、Cr、Nb、Mn将提高N在钢中的溶解度,Si、C、Ni将降低其溶 解度; G:影响因素:原始氮含量、RH处理时间、真空度、钢中[O]、[S]的含 量、真空系统的泄漏率、环流量等。
武钢RH多功能真空精炼技术开发
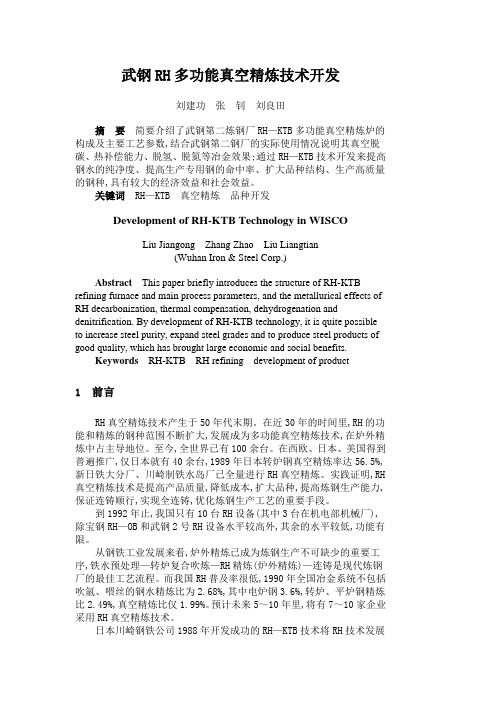
武钢RH多功能真空精炼技术开发刘建功张钊刘良田摘要简要介绍了武钢第二炼钢厂RH—KTB多功能真空精炼炉的构成及主要工艺参数,结合武钢第二钢厂的实际使用情况说明其真空脱碳、热补偿能力、脱氢、脱氮等冶金效果;通过RH—KTB技术开发来提高钢水的纯净度、提高生产专用钢的命中率、扩大品种结构、生产高质量的钢种,具有较大的经济效益和社会效益。
关键词RH—KTB 真空精炼品种开发Development of RH-KTB Technology in WISCOLiu Jiangong Zhang Zhao Liu Liangtian(Wuhan Iron & Steel Corp.)Abstract This paper briefly introduces the structure of RH-KTB refining furnace and main process parameters, and the metallurical effects of RH decarbonization, thermal compensation, dehydrogenation and denitrification. By development of RH-KTB technology, it is quite possible to increase steel purity, expand steel grades and to produce steel products of good quality, which has brought large economic and social benefits.Keywords RH-KTB RH refining development of product1 前言RH真空精炼技术产生于50年代末期。
在近30年的时间里,RH的功能和精炼的钢种范围不断扩大,发展成为多功能真空精炼技术,在炉外精炼中占主导地位。
RH生产工艺及脱硫技术的控制
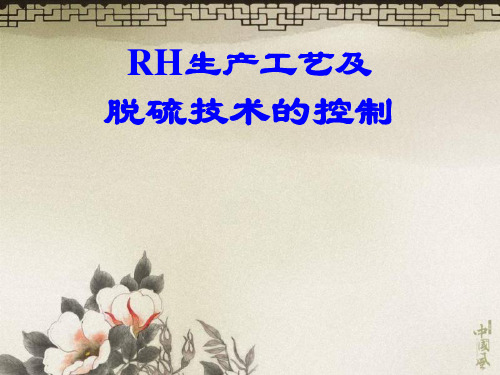
脱硫技术的控制
主要内容
1 RH生产工艺简介
1.1 RH的发展概况 1.2 RH精炼技术的种类及特点 1.3 RH喷粉技术及其发展
2 RH脱硫技术
2.1 脱硫的热力学与动力学 2.2 RH脱硫剂的种类、使用方法与脱硫效果 2.3 提高脱硫率的措施
2
1.1 RH精炼技术的发展概况 RH生产工艺简介
17
RH-PB(IJ)
RH-PB(IJ)法是日本新日铁大分厂于 1985年开发的,该法是将粉剂通过置于上 升管下方的喷枪喷入钢液中,带脱硫粉剂 的钢液经上升管进入RH上部真空室,在 钢液循环过程实现脱硫。该方法既可将氩 气与粉剂呈气粉两相流同时吹入,又可单 独吹氩(如下图)。
18
RH-PB(IJ)
22
RH-PTB
为冶炼超低硫深冲钢,日本住友 工业公司和歌山厂于1994年开发 了RH顶喷粉法,即RH-PTB喷粉 法。该法通过水冷顶枪进行喷粉 操作,粉剂输送较流畅,喷嘴不 易堵塞;不使用耐火材质的浸入 式喷枪操作操作成本较低;无钢 液阻力,载气耗量小。
RH-PTB装置原理图
1994年日本住友公司和歌山厂开发
高
33
序列 1 2 3 4 5 6
7
类型 RH RH-OB RH-PB RH-KTB RHPB(OB) RH-MFB
RH-PTB
RH及多功能RH精炼技术的概况汇总表
开发厂家
主要功能
适用钢种
处理效果
1957年前西 德鲁尔钢铁 公司和赫拉 欧斯公司
真空脱气(H2), 减少杂质,均匀
成分、温度
特别用于对含氢量要 求严格钢种,主要是 低碳钢、超低碳深冲 钢等
13(平均),15(max)
最新RH真空精炼技术
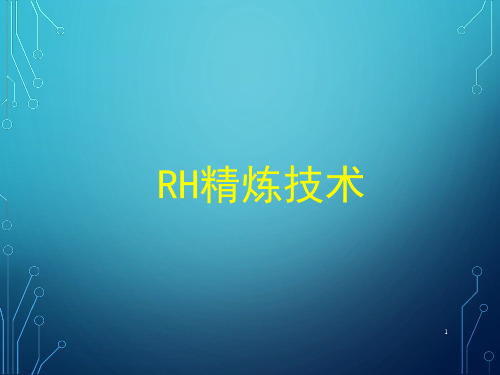
产品 热轧钢板 冷轧深冲钢板 镀层板,涂层板 锅炉板、桥梁板 造船板
产品 IF 钢 电工用钢 石油管线钢 低温用钢 超 深 冲4钢
5
特殊钢厂冶炼工艺路线
废钢
UHP
生铁
电炉
D R I/H B I
VD
轴轴承承钢钢
精炼
齿齿轮轮钢钢
优优质质弹弹簧簧钢钢
LF
大方
硬硬线线钢钢
精炼
坯连
帘帘线线钢钢
RH
铸
精炼
石石油油套套管管
RH精炼技术
__________________________________________________
1
现代纯净钢生产工艺流程
在纯净钢生产中,RH是最重要的真空精炼装置之一,
应用越来越广泛,新建钢厂多数选择RH精炼。 __________________________________________________
• 对钢水进行该钢种所必须进行的处理,(如脱氢处理,深
脱碳处理,轻处理,深脱氧处理等)。处理过程中真空度 和环流气体流量按各处理模式自动进行变换。
• 处理结束前再次测温取样,确认处理目的是否已达到。 • 合金微调及最终脱氧。 • 测温取样后关闭主真空阀,破真空。 • 钢包下降,座落到钢包台车,同时将环流气体切换成氮气。 • 钢包台车运行到喂丝工(加保温剂)位,按钢种要求喂丝,
2
钢
铁
冶
炼工艺Fra bibliotek路线 __________________________________________________
3
大型联合企业冶炼工艺流程
CAS-OB
板坯连铸
铁水脱硫 转炉复吹
RH-OB精炼技术综述
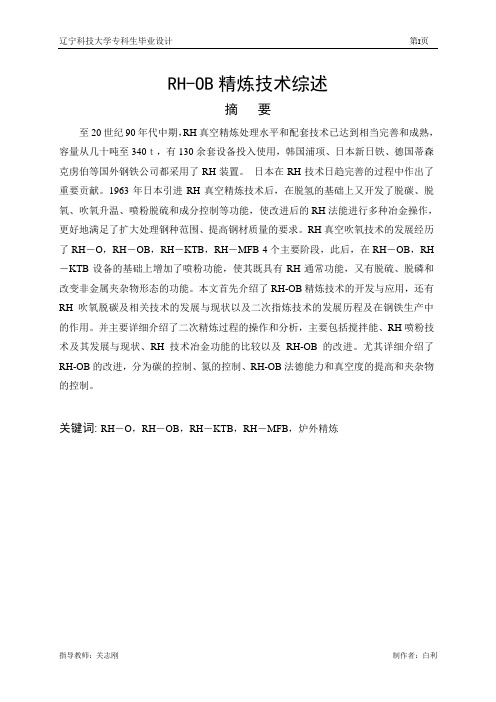
RH-OB精炼技术综述摘要至20世纪90年代中期,RH真空精炼处理水平和配套技术已达到相当完善和成熟,容量从几十吨至340t,有130余套设备投入使用,韩国浦项、日本新日铁、德国蒂森克虏伯等国外钢铁公司都采用了RH装置。
日本在RH技术日趋完善的过程中作出了重要贡献。
1963年日本引进RH真空精炼技术后,在脱氢的基础上又开发了脱碳、脱氧、吹氧升温、喷粉脱硫和成分控制等功能,使改进后的RH法能进行多种冶金操作,更好地满足了扩大处理钢种范围、提高钢材质量的要求。
RH真空吹氧技术的发展经历了RH-O,RH-OB,RH-KTB,RH-MFB 4个主要阶段,此后,在RH-OB,RH -KTB设备的基础上增加了喷粉功能,使其既具有RH通常功能,又有脱硫、脱磷和改变非金属夹杂物形态的功能。
本文首先介绍了RH-OB精炼技术的开发与应用,还有RH吹氧脱碳及相关技术的发展与现状以及二次指炼技术的发展历程及在钢铁生产中的作用。
并主要详细介绍了二次精炼过程的操作和分析,主要包括搅拌能、RH喷粉技术及其发展与现状、RH技术冶金功能的比较以及RH-OB的改进。
尤其详细介绍了RH-OB的改进,分为碳的控制、氮的控制、RH-OB法德能力和真空度的提高和夹杂物的控制。
关键词: RH-O,RH-OB,RH-KTB,RH-MFB,炉外精炼目录摘要 (I)1 前言 (1)1.1RH-OB精炼技术的开发与应用 (2)1.2RH吹氧脱碳及相关技术的发展与现状 (3)1.2.1 RH-O真空吹氧技术 (4)1.2.2 RH-OB真空吹氧技术 (4)1.2.3 RH-KTB真空吹氧技术 (4)1.2.4 RH-MFB多功能喷嘴技术 (5)1.3二次指炼技术的发展历程及在钢铁生产中的作用 (5)2 二次精炼过程的操作和分析 (9)2.1搅拌能 (9)2.1.1低吹气的搅拌能 (9)2.1.2顶吹气的搅拌能 (9)2.1.3行波电磁场的搅拌能 (10)2.2淹没吹A R时气泡的行为及去[H]作用 (11)2.3渣系选择 (12)3 RH喷粉技术及其发展与现状 (14)3.1RH-PB法 (14)3.2RH-PTB喷粉法 (14)3.3MESID技术 (14)4 RH技术冶金功能的比较 (15)5 RH-OB改进 (17)5.1碳的控制 (17)5.1.1吹氧强化脱碳 (17)5.1.2控制凝钢壳 (17)5.1.3 自然脱碳 (17)5.2氮的控制 (19)5.2.1 浸入管法兰盘设计改进 (19)5.2.2 Ti合金中N的影响 (19)5.3RH-OB法德能力和真空度的提高 (19)5.4夹杂物控制 (19)5.4.1 终点温度控制 (19)5.4.2 夹杂物的减少 (20)5.5缩短处理时间 (20)结论 (21)致谢 (22)参考文献 (23)1 前言RH法是一种重要的炉外精炼方法,具有处理周期短、生产能力大、精炼效果好、容易操作等一系列优点,在炼钢生产中获得了广泛应用。
RH炉工作原理,主要功能
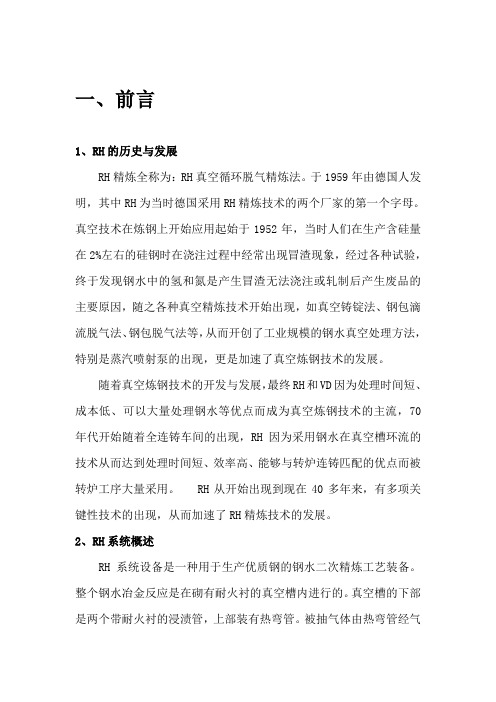
一、前言1、RH的历史与发展RH精炼全称为:RH真空循环脱气精炼法。
于1959年由德国人发明,其中RH为当时德国采用RH精炼技术的两个厂家的第一个字母。
真空技术在炼钢上开始应用起始于1952年,当时人们在生产含硅量在2%左右的硅钢时在浇注过程中经常出现冒渣现象,经过各种试验,终于发现钢水中的氢和氮是产生冒渣无法浇注或轧制后产生废品的主要原因,随之各种真空精炼技术开始出现,如真空铸锭法、钢包滴流脱气法、钢包脱气法等,从而开创了工业规模的钢水真空处理方法,特别是蒸汽喷射泵的出现,更是加速了真空炼钢技术的发展。
随着真空炼钢技术的开发与发展,最终RH和VD因为处理时间短、成本低、可以大量处理钢水等优点而成为真空炼钢技术的主流,70年代开始随着全连铸车间的出现,RH因为采用钢水在真空槽环流的技术从而达到处理时间短、效率高、能够与转炉连铸匹配的优点而被转炉工序大量采用。
RH从开始出现到现在40多年来,有多项关键性技术的出现,从而加速了RH精炼技术的发展。
2、RH系统概述RH系统设备是一种用于生产优质钢的钢水二次精炼工艺装备。
整个钢水冶金反应是在砌有耐火衬的真空槽内进行的。
真空槽的下部是两个带耐火衬的浸渍管,上部装有热弯管。
被抽气体由热弯管经气体冷却器至真空泵系统排到厂房外。
钢水处理前,先将浸渍管浸入待处理的钢包钢水中。
当真空槽抽真空时,钢水表面的大气压力迫使钢水从浸渍管流入真空槽内。
与真空槽连通的两个浸渍管,一个为上升管,一个为下降管。
由于上升管不断向钢液吹入氩气,相对没有吹氩的下降管产生了一个较高的静压差,使钢水从上升管进入并通过真空槽下部流向下降管,如此不断循环反复。
在真空状态下,流经真空槽钢水中的氩气、氢气、一氧化碳等气体在钢液循环过程中被抽走。
同时,进入真空槽内的钢水还进行一系列的冶金反应,比如碳氧反应等;如此循环脱气精炼使钢液得到净化。
经RH处理的钢水优点明显:合金基本不与炉渣反应,合金直接加入钢水之中,收得率高;钢水能快速均匀混合;合金成分可控制在狭窄的范围之内;气体含量低,夹杂物少,钢水纯净度高;还可以用顶枪进行化学升温的温度调整,为连铸机提供流动性好、纯净度高、符合浇铸温度的钢水,以利于连铸生产的多炉连浇。
RH精炼技术的应用与发展
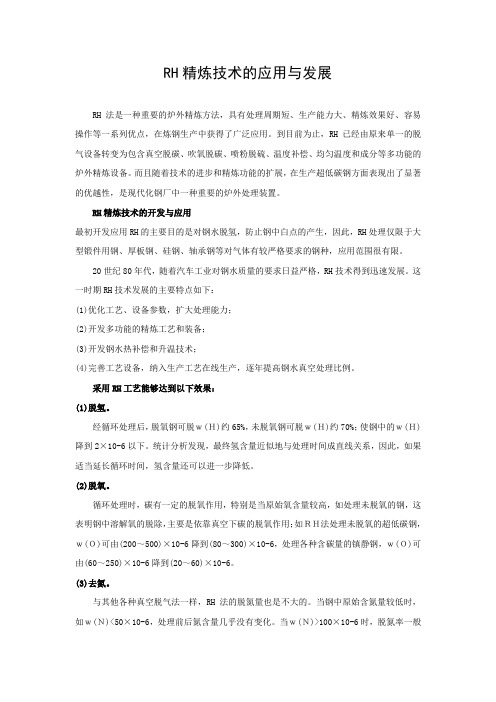
RH精炼技术的应用与发展RH法是一种重要的炉外精炼方法,具有处理周期短、生产能力大、精炼效果好、容易操作等一系列优点,在炼钢生产中获得了广泛应用。
到目前为止,RH已经由原来单一的脱气设备转变为包含真空脱碳、吹氧脱碳、喷粉脱硫、温度补偿、均匀温度和成分等多功能的炉外精炼设备。
而且随着技术的进步和精炼功能的扩展,在生产超低碳钢方面表现出了显著的优越性,是现代化钢厂中一种重要的炉外处理装置。
RH精炼技术的开发与应用最初开发应用RH的主要目的是对钢水脱氢,防止钢中白点的产生,因此,RH处理仅限于大型锻件用钢、厚板钢、硅钢、轴承钢等对气体有较严格要求的钢种,应用范围很有限。
20世纪80年代,随着汽车工业对钢水质量的要求日益严格,RH技术得到迅速发展。
这一时期RH技术发展的主要特点如下:(1)优化工艺、设备参数,扩大处理能力;(2)开发多功能的精炼工艺和装备;(3)开发钢水热补偿和升温技术;(4)完善工艺设备,纳入生产工艺在线生产,逐年提高钢水真空处理比例。
采用RH工艺能够达到以下效果:(1)脱氢。
经循环处理后,脱氧钢可脱w(H)约65%,未脱氧钢可脱w(H)约70%;使钢中的w(H)降到2×10-6以下。
统计分析发现,最终氢含量近似地与处理时间成直线关系,因此,如果适当延长循环时间,氢含量还可以进一步降低。
(2)脱氧。
循环处理时,碳有一定的脱氧作用,特别是当原始氧含量较高,如处理未脱氧的钢,这表明钢中溶解氧的脱除,主要是依靠真空下碳的脱氧作用;如RH法处理未脱氧的超低碳钢,w(O)可由(200~500)×10-6降到(80~300)×10-6,处理各种含碳量的镇静钢,w(O)可由(60~250)×10-6降到(20~60)×10-6。
(3)去氮。
与其他各种真空脱气法一样,RH法的脱氮量也是不大的。
当钢中原始含氮量较低时,如w(N)<50×10-6,处理前后氮含量几乎没有变化。
冶金工业RH炼技术的发展

RH精炼技术的发展
2
现代纯净钢生产工艺流程
在纯净钢生产中,RH是最重要的真空精炼装置之一, 应用越来越广泛,新建钢厂多数选择RH精炼。
3
钢 铁 冶 炼 工 艺 路 线
4
大型联合企业冶炼工艺流程
5
特殊钢厂冶炼工艺路线
脱硫
6
短流程钢厂冶炼工艺路线
7
RH的发展历史
RH精炼技术是1959年德国Rheinstahl和Hutlenwerke公司联合开发成
RH装置示意图
9
RH处理钢水过程
• 钢水处理前,先将浸渍管浸入待处理的钢包钢水中。当 真空槽抽真空时,钢水表面的大气压力迫使钢水从浸渍 管流入真空槽内。(真空槽内大约0.67 mbar时可使钢水 上升1.48m高度)。与真空槽连通的两个浸渍管,一个为 上升管,一个为下降管。由于上升管不断向钢液吹入氩 气,形成气泡泵,使钢水从上升管进入并通过真空槽下 部流向下降管,如此不断循环反复。在真空状态下,流 经真空槽钢水中的氩气、氢气、一氧化碳等气体在钢液 循环过程中被抽走。同时,进入真空槽内的钢水还进行 一系列的冶金反应,比如碳氧反应等如此循环脱气精炼 使钢液得到净化。
1
提高循环流量和体积传质系数。如图,千叶厂RH最初的工况,脱碳速度
常数K = 0.1min-1。扩大上升管直径增加环流后,达到K= 0.15min-1。进一步改进
吹Ar方式使传质系数 k值增大,K= 0.2min-1。
2 提高抽气速率。定义RH真空系统的抽气速度常数R:R=-ln( / 0)/t (min-1)。 3 吹氧。采用KTB顶吹氧工艺,提高了RH前期脱碳速度,使表观脱碳速度常
数Kc从0.21min-1提高到0.35min-1。
RH精炼
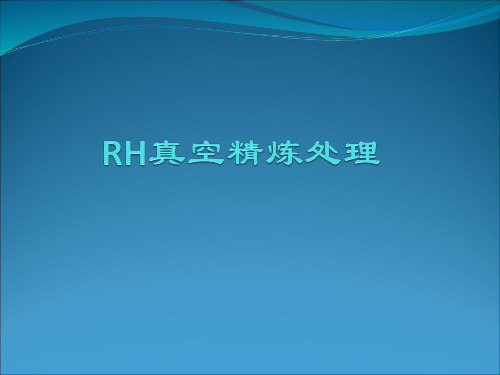
4.RH真空精炼的冶金功能
在短时间就可达到较低的碳、氢、氧含量;不用采 取专门的渣对策;可准确调整化学成分,Al,Si等合金收 得率在90~97%。汽车钢板以及电工钢等是RH钢生产的典 型产品。最初RH装置主要是对钢水脱氢,随着RH真空精炼 实践和精炼技术的发展,其冶金功能得到了充分的发展。
1)脱氢 可生产[H]≤0.00015%,延长钢水精炼时间,可使 [H]≤0.00010%。 2)脱碳 在20min处理周期内可生产出[C]≤0.002%的超低碳钢水。在脱碳过程 中,钢水中的碳和氧反应形成一氧化碳并通过真空泵排出。如钢中氧含量不够, 可通过顶枪吹氧提供氧气。脱碳结束时,钢水通过加铝进行脱氧。 3)脱氧 RH真空精炼后T[O]量可≤0.0020%,如和 LF法配合,钢水T[O]可降到 0.0010%以下。
近年来,我国钢铁企业普遍对钢水炉外精炼技术的应 用较为重视,投入大量资金上马先进的炉外精炼技术装备, 炉外精炼已经不再是特大型钢铁企业或特钢企业的专利品。 炉外精炼在提高钢材产品质量、扩大品种、提高炼钢生产 能力、保障连铸顺行、降低成本、优化炼钢生产工艺等方 面发挥着极其重要的作用,甚至成为限制环节。而RH真空 处理又是炉外精炼领域的一个突出典型。铁水预处理-转炉 复合吹炼(或电弧炉冶炼)-炉外精炼(LF、VD、VOD、RH)-连 铸,已成为越来越多的钢铁企业炼钢厂的典型流程模式。
3.在真空条件进行精炼,脱碳、脱氧、脱硫、合金化、净化钢质,减少 钢中非金属夹杂物,提高合金收得率,减小成分波动范围。冶炼出一 般平炉电炉转炉中作不能冶炼的钢种,为冶炼很多新钢种提供了一个 新的工艺。 4.RH真空精炼可以实现计算机自动控制,从而使其精炼工艺过程实现高 度的自动化。 5.由于双真空室设备和计算机自动控制的应用,使得RH真空精炼设备的 作业率大幅度提高,从而达到了LD—RH—CC三者配合连续作业。
RH炉工操作
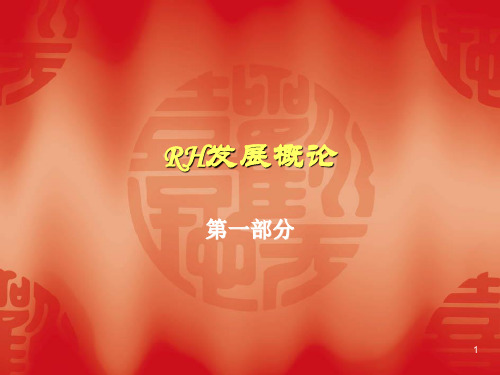
二、RH脱气原理
1、RH脱氢原理及影响因素
A:氢在钢液中的溶解度取决于于温度和压力,在常压常温下
氢在钢中的溶解度≤1.5ppm,超过将析出形成白点; B:白点在钢坯冷却至200℃时形成,将使其内部产生无数 小裂纹,塑性急剧下降; C:在冶炼过程中影响氢含量的因素:加入石灰的数量和状 态;加入合金的品种和数量;冶炼方法; D:脱氢:[%H]=K [H] *(PH2)1/2,,式中K [H] 为温度的涵 数,Lg K [H] =--167/T—1.68,在1600℃时K [H] =0.00268, 则[%H]= 0.00268(PH2)1/2。从左式可以看出氢含量与温度 和压力的关系; E:Cr、Mn、Ti、Nb将提高氢在钢中的溶解度,C、Si、Al 将降低氢在钢中的溶解度; F:影响RH脱氢的因素:原始氢含量,原材料品种、状态、 数量,气候,耐火材料,钢水的脱氧程度,真空度和处理时 间。 21
22
二、RH脱气原理
2、RH脱氮原理及影响因素
A:氮主要以化合物形态存在于钢中; B:氮可作为提高钢的硬度、耐磨性、抗蚀性的合金元素; C:对低碳钢Fe4N的析出将造成时效和蓝脆,达到一定程度时形成气泡
和疏松,使钢的塑性下降,对超低碳钢影响更大; D:氮在α-Fe、δ-Fe中的溶解度随温度升高而增加,在γ-Fe中相反; E:就氮在钢中的溶解度而言,遵循以下规律:[%N]=K [N] *(PN2)1/2, 在1600℃、1mbar下K [N] =0.045%,所以[%N]= 0.045%(PN2)1/2; F:V、Cr、Nb、Mn将提高N在钢中的溶解度,Si、C、Ni将降低其溶 解度; G:影响因素:原始氮含量、RH处理时间、真空度、钢中[O]、[S]的含 量、真空系统的泄漏率、环流量等。
RH精炼技术
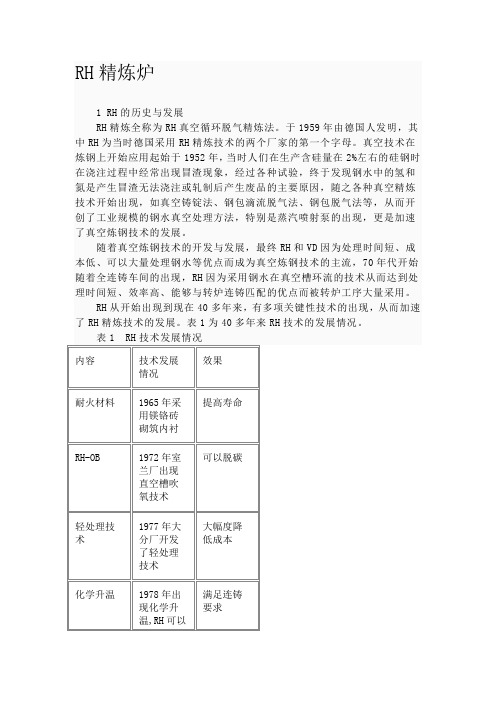
空槽内的钢水还进行一系列的冶金反应,比如碳氧反应等;如此循环脱气精炼使钢液得到净化。
经RH处理的钢水优点明显:合金基本不与炉渣反应,合金直接加入钢水之中,收得率高;钢水能快速均匀混合;合金成分可控制在狭窄的范围之内;气体含量低,夹杂物少,钢水纯净度高;还可以用顶枪进行化学升温的温度调整,为连铸机提供流动性好、纯净度高、符合浇铸温度的钢水,以利于连铸生产的多炉连浇。
3真空泵工作原理在工业炼钢生产中,现经常采用的抽真空设备主要有罗茨泵、水环泵和蒸汽喷射泵,其中以水环泵和蒸汽喷射泵最为常见。
1)水环泵工作原理水环泵中带有叶片的转了被偏心的与泵的壳体相配合,在泵体中装有适量的水作为工作液。
当叶轮顺时针方向旋转时,水被叶轮抛向四周,由于离心力的作用,水形成了一个决定于泵腔形状的近似于等厚度的封闭圆环。
水环的下部分内表面恰好与叶轮轮毂相切,水环的上部内表面刚好与叶片顶端接触(实际上叶片在水环内有一定的插入深度)。
此时叶轮轮毂与水环之间形成一个月牙形空间,而这一空间又被叶轮分成和叶片数目相等的若干个小腔。
如果以叶轮的下部0°为起点,那么叶轮在旋转前180°时小腔的容积由小变大,且与端面上的吸气口相通,此时气体被吸入,当吸气终了时小腔则与吸气口隔绝;当叶轮继续旋转时,小腔由大变小,使气体被压缩;当小腔与排气口相通时,气体便被排出泵外。
2)蒸汽喷射泵工作原理喷射泵是由工作喷嘴和扩压器及混合室相联而组成。
工作喷嘴和扩压器这两个部件组成了一条断面变化的特殊气流管道。
气流通过喷嘴可将压力能转变为动能。
工作蒸汽压强和泵的出口压强之间的压力差,使工作蒸汽在管道中流动。
在这个特殊的管道中,蒸汽经过喷嘴的出口到扩压器入口之间的这个区域(混合室),由于蒸汽流处于高速而出现一个负压区。
此处的负压要比工作蒸汽压强和反压强低得多。
此时,被抽气体吸进混合室,工作蒸汽和被抽气体相互混合并进行能量交换,把工作蒸汽由压力能转变来的动能传给被抽气体。
炼钢rh炉技术资料(第二期)
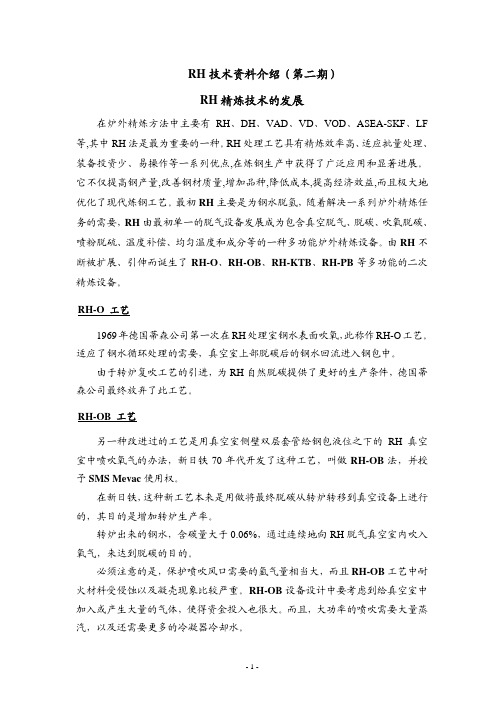
[H]<2ppm [N]<40ppm [O]<20~40ppm
原为钢水 脱氢开 发,短时 间内可使 [H] 降 到 远低于白 点敏感极 限以下
1972 年 新 日铁公司 名古屋厂
同 1,还可 同 1,并能 生 产 不 锈 吹氧脱碳、 钢,多用于 加热钢水 超 低 碳 钢
的生产
同 RH,并可使 终 点 [C] ≤ 35ppm
RH-O 工艺
1969 年德国蒂森公司第一次在 RH 处理室钢水表面吹氧,此称作 RH-O 工艺。 适应了钢水循环处理的需要,真空室上部脱碳后的钢水回流进入钢包中。
由于转炉复吹工艺的引进,为 RH 自然脱碳提供了更好的生产条件,德国蒂 森公司最终放弃了此工艺。
RH-OB 工艺
另一种改进过的工艺是用真空室侧壁双层套管给钢包液位之下的 RH 真空 室中喷吹氧气的办法,新日铁 70 年代开发了这种工艺,叫做 RH-OB 法,并授 予 SMS Mevac 使用权。
并申请专利。此顶枪系统使用脉冲气流,能对气体和固体的混合物进行喷吹;再
者,顶枪烧嘴可实现真空室耐材的加热与保温。
表 1 为几种 RH 真空精炼方法的持点比较。
表 1 RH 及多功能 RH 技术的特点
序 类型
号
1
RH
2 RH-OB 3 RH-PB(IJ)
代号意义
开发厂家 主要功能 适用钢种 处理效果
备注
开发了高级多功能顶枪系统。这些创新包括在高位置喷吹(称之为短枪),从而
减小了 RH 处理设施的高度。最近的创新表现在用同一套顶喷枪系统,结合现有
的技术开发其它工艺应用。
1995 年 1 月份比利时根特的 SIDMAR 公司,在其 RH 设施上使用了顶枪
- 1、下载文档前请自行甄别文档内容的完整性,平台不提供额外的编辑、内容补充、找答案等附加服务。
- 2、"仅部分预览"的文档,不可在线预览部分如存在完整性等问题,可反馈申请退款(可完整预览的文档不适用该条件!)。
- 3、如文档侵犯您的权益,请联系客服反馈,我们会尽快为您处理(人工客服工作时间:9:00-18:30)。
2
工艺指标 技术水平
C≤20SFra bibliotekT.O
P
≤20
N
≤20
H
≤1.0
≤10 ≤15
(3)极低碳钢的冶炼技术(2000年~ ):为了解决极低碳钢 ([C]≤10×10-6)精炼的技术难题,需要进一步克服钢水的静压力,以 提高熔池脱碳速度。
RH喷粉 钢包喷粉
脱
磷
7
将RH吹氧工艺与喷粉工艺相结合可以实现RH脱磷。在RH吹氧脱碳期同时喷 吹石灰粉可以达到理想的脱磷效果。如日本新日铁名古屋厂230tRH采用OB/PB工 艺,可生产[P]≤20×10-6的超低磷钢。 粉剂中(%CaO)≈20%时,炉渣脱磷能力最强。提高真空度使炉渣脱磷能力略 有提高。根据RH-PB处理中取出的粉剂颗粒,经X光衍射分析的结果绘出右图。 由于RH喷粉避免了顶渣的影响,延长了粉剂与钢水直接反应的时间,使脱磷效 率提高。如图所示,上浮粉剂颗粒中P2O5含量接近3CaO· P2O5或4CaO· P2O5的理 论极限。远高于铁水预处理或转炉脱磷效率。
5
RH钢水循环流量Q和体积传 质系数k对脱碳速度的影响
RH抽气速度R和吹Ar流量 对脱碳速度的影响
KTB法与普通RH脱碳速度的比较
脱
对铝脱氧钢水,脱硫反应为:
硫
6
3(CaO) + 2[Al] + 3[S] = (Al2O3) + 3(CaS)
钢水脱硫效率主要决定于钢中铝含量和炉渣指数(S· P):
粉剂配比和真空度对炉渣脱磷 能力的影响
RH-PB工艺中粉剂颗粒的脱磷 效果比较
脱氧与夹杂物上浮
RH精炼通常采用铝脱氧工艺,生成的脱氧夹杂物大多为细小的Al2O3夹 杂,RH精炼过程中钢水氧含量的变化
8
可以表示为:
d[O]T d[O]T d [O]T dt dt dt in out
d [% S ] A k s {[% S ] [% S ]e } dt V
粉剂消耗量与脱硫效率的关系
,根据高桥等人的测定:ks = 0.27m/min。 采用RH喷粉脱硫的主要优点是: (1)脱硫效率高。 (2)顶渣影响小,与钢水间的传质速度大幅度 降低。
渣中FeO+MnO含量对渣—钢间硫的分配比的影响
/3 (S P) a1 Al2O3 /(%S ) sat aCaO
当(S· P)= 0.1时,渣—钢间硫的分配比最大
(400~600)。因此,脱硫渣的最佳组成是:60%(CaO)+ 25%(Al2O3)+10%(SiO2)。RH喷粉通常采用CaO+CaF2系脱 硫剂,该种粉剂的脱硫分配比可按下式计算: La = (%S)/[%S] = 1260-25(%Al2O3) – 75(%SiO2)±250 钢水脱硫速度为:
1
洁净钢炉外精炼技术
RH精炼技术的发展
RH的发展历史
RH精炼技术是1959年德国Rheinstahl和Hutlenwerke公司联合开发成 功的。RH将真空精炼与钢水循环流动结合起来,具有处理周期短,生产能 力大,精炼效果好等优点,适合冶炼周期短,生产能力大的转炉工厂采用。 RH发展到今天,大体分为三个发展阶段: (1)发展阶段(1968年~1980年):RH装备技术在全世界广泛采用。 (2)多功能RH精炼技术的确立(1980年~2000年):RH技术几乎达到 尽善尽美的地步。 表1 RH工艺技术的进步
0.32 1.48 k AV Q1.17 CV
钢水含碳量和吹Ar方式对RH脱碳 过程的体积传质系数k的影响
提高RH脱碳速度的工艺措施
(1)提高循环流量和体积传质系数。如图,千叶厂RH最初的工况,kc = 0.1min-1。扩大上升管直径增加环流后,达到kc = 0.15min-1。进一步改进吹Ar方 式使 k值增大,kc = 0.2min-1。 (2)提高抽气速率。定义RH真空系统的抽气速度常数R:R=-ln(/0)/t (min-1)。 (3)吹氧。采用KTB顶吹氧工艺,提高了RH前期脱碳速度,使表观脱碳速度常 数kc从0.21min-1提高到0.35min-1。 (4)改变吹Ar方式。实验证明,在RH真空室的下部吹入大约1/4的氩气,可使 RH的脱碳速度提高大约2倍。
真
速度的限制性环节:
dC L kc CL dt
空
脱
kc
碳
60 w(1 / Q 1 / kc ) (min1 )
3
RH内的脱碳速度主要决定于钢液中碳的扩散。低碳区碳的传质是反应
CL CL exp(kc t )
RH钢水循环流量Q = 钢水循环流速×上升管截面积,根据前人对RH钢 水循环流量的测定结果表明: • 增加吹氩流量Qg使RH的循环流量增大; • 扩大上升管直径使循环流量Q增大; • 增加浸入管的插入深度也会使循环流量变 大。 总结以上研究,RH内钢水的循环流量可以表 示为:
1/ 3 4/3 Q K QG Du H 1/ 3
循环流量Q的计算值与实测 值的比较
真
空
脱
碳
4
RH精炼中发生的各种化学反应的反应速度决定于金属侧各元素的传质
系数,根据Shigeru的研究证明,在整个RH精炼过程中各元素的传质系数
基本保持不变,但反应界面积随时间发生明显变化。为了方便描述各种反 应速度,常采用体积传质系数k(=传质系数×反应界面积)。 RH的体积传质系数与以下因素有关: • k和钢水碳含量成正比; •增加钢水的循环流量Q使k值提高; •改变吹氩方式利于提高k值:如在 300tRH的真空室底部增设8支2mm吹Ar 管吹氩(QA=800Nl/min),使k值提 高。 Koji YMAMGUCHI总结100t~260tRH的实 际生产数据提出以下关联式:
RH处理钢水中夹杂物的形貌和成份
RH精炼中,炉渣传氧决定于渣中(%FeO)+
(%MnO)含量。由于RH有效地避免了卷渣,顶渣 对钢水的氧化大为减弱。RH的表观脱氧速度常
[O] 数 k ln(
o t T i t
[O]
/ t)
比钢包吹氩(GI)工艺大约提高1倍。