Formation of DNA nanoparticles in the presence
制备液相法 英文

制备液相法英文Liquid-Phase SynthesisLiquid-phase synthesis, also known as liquid-phase method, is a versatile technique used in the preparation of a wide range of materials with specific properties. This method involves the formation of materials in a liquid medium, allowing for precise control over the reaction conditions and the resulting product. Liquid-phase synthesis is commonly used in the synthesis of nanoparticles, thin films, and nanocomposites.One of the key advantages of liquid-phase synthesis is the ability to achieve high purity and homogeneity in the final product. By carefully controlling the reaction parameters such as temperature, pressure, and reaction time, researchers can produce materials with the desired size, shape, and composition. This level of control is essential for applications in fields such as catalysis, sensor technology, and nanomedicine.In liquid-phase synthesis, the starting materials are typically dissolved or suspended in a solvent, which acts as a reaction medium. The solvent not only provides a medium for the reaction to take place, but it also helps to control the rate of the reaction and the distribution of the reactants. Common solvents used in liquid-phase synthesis include water, ethanol, and organic solvents such as toluene and hexane.The choice of solvent is crucial in liquid-phase synthesis, as it can significantly impact the properties of the resulting material. For example, water is often used as a solvent for the synthesis of metal nanoparticles, as it can stabilize the particles and prevent agglomeration. Organic solvents, on the other hand, are commonly used in the synthesis of polymers and organic compounds, as they can dissolve a wide range of organic materials.In addition to the solvent, the choice of reagents and reaction conditions also play a critical role in the success of a liquid-phase synthesis. The concentration of the reactants, the temperature, the pH, and the presence of catalysts or surfactants can all influence theoutcome of the reaction. By carefully optimizing these parameters, researchers can tailor the properties of the final material to meet specific requirements.Liquid-phase synthesis is a versatile and powerful technique that has been widely used in the preparation of a diverse range of materials. From metal nanoparticles to organic polymers, this method offers a high degree of control over the properties of the final product, making it an essential tool for researchers in fields such as materials science, chemistry, and nanotechnology. By understanding the principles of liquid-phase synthesis and optimizing the reaction conditions, scientists can create materials with tailored properties and functionalities for a variety of applications.。
Plasmonics and Nanophotonics
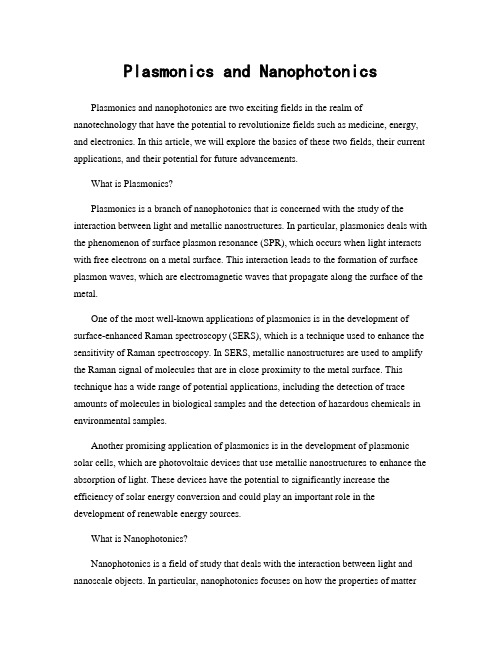
Plasmonics and NanophotonicsPlasmonics and nanophotonics are two exciting fields in the realm of nanotechnology that have the potential to revolutionize fields such as medicine, energy, and electronics. In this article, we will explore the basics of these two fields, their current applications, and their potential for future advancements.What is Plasmonics?Plasmonics is a branch of nanophotonics that is concerned with the study of the interaction between light and metallic nanostructures. In particular, plasmonics deals with the phenomenon of surface plasmon resonance (SPR), which occurs when light interacts with free electrons on a metal surface. This interaction leads to the formation of surface plasmon waves, which are electromagnetic waves that propagate along the surface of the metal.One of the most well-known applications of plasmonics is in the development of surface-enhanced Raman spectroscopy (SERS), which is a technique used to enhance the sensitivity of Raman spectroscopy. In SERS, metallic nanostructures are used to amplify the Raman signal of molecules that are in close proximity to the metal surface. This technique has a wide range of potential applications, including the detection of trace amounts of molecules in biological samples and the detection of hazardous chemicals in environmental samples.Another promising application of plasmonics is in the development of plasmonic solar cells, which are photovoltaic devices that use metallic nanostructures to enhance the absorption of light. These devices have the potential to significantly increase the efficiency of solar energy conversion and could play an important role in the development of renewable energy sources.What is Nanophotonics?Nanophotonics is a field of study that deals with the interaction between light and nanoscale objects. In particular, nanophotonics focuses on how the properties of matterchange when it is confined to small length scales. This includes the study of both artificial nanostructures, such as photonic crystals and plasmonic nanoparticles, and natural systems, such as biological cells and tissues.One of the most exciting applications of nanophotonics is in the development of optoelectronic devices that use light to control the flow of electrons. These devices, known as nanophotonic circuits, have the potential to be faster, smaller, and more energy-efficient than traditional electronic circuits. This could lead to the development of new technologies such as ultrafast computers, high-speed data communication networks, and advanced sensors.Another area where nanophotonics shows promise is in the development of new cancer therapies. Researchers are exploring the use of nanoscale devices that can deliver therapeutic agents directly to cancer cells, using light to trigger the release of the drugs. This approach could potentially lead to more targeted and effective cancer treatments that have fewer side effects than conventional chemotherapy.The Future of As plasmonics and nanophotonics continue to develop, researchers are exploring new and exciting applications in a wide range of fields. In addition to the applications described above, these fields have the potential to revolutionize areas such as data storage, environmental monitoring, and quantum computing.One of the challenges facing these fields is the development of materials with the appropriate properties to achieve the desired performance in specific applications. For example, the development of plasmonic materials that can withstand high temperatures and harsh environments is critical for their use in catalysis and other industrial applications.Another challenge is the development of reliable methods for manufacturing and scaling up these materials. Advances in nanofabrication techniques, such as electron beam lithography and nanoimprint lithography, have led to significant progress in this area. However, there is still a need for more cost-effective and scalable methods that can produce large quantities of high-quality materials.Despite these challenges, the potential benefits of plasmonics and nanophotonics are too significant to ignore. With continued research and development, these fields have the potential to revolutionize our world and address some of the biggest challenges that we face as a society.。
沉淀聚合诱导自组装
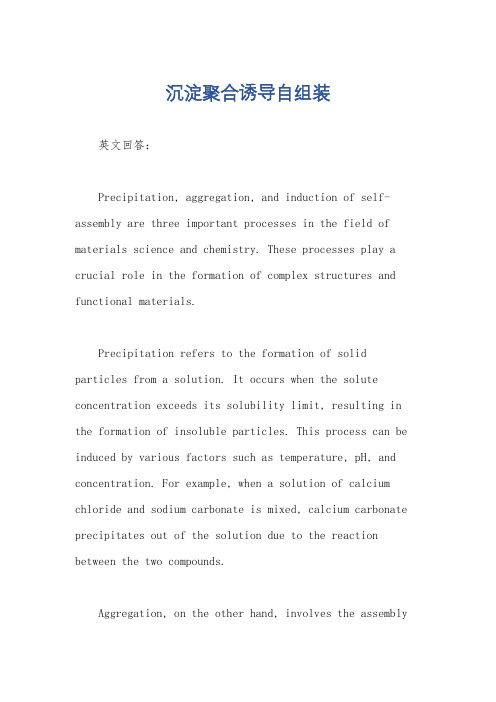
沉淀聚合诱导自组装英文回答:Precipitation, aggregation, and induction of self-assembly are three important processes in the field of materials science and chemistry. These processes play a crucial role in the formation of complex structures and functional materials.Precipitation refers to the formation of solid particles from a solution. It occurs when the solute concentration exceeds its solubility limit, resulting in the formation of insoluble particles. This process can be induced by various factors such as temperature, pH, and concentration. For example, when a solution of calcium chloride and sodium carbonate is mixed, calcium carbonate precipitates out of the solution due to the reaction between the two compounds.Aggregation, on the other hand, involves the assemblyof particles or molecules to form larger structures. This process can occur through various mechanisms, such as van der Waals forces, electrostatic interactions, orhydrophobic interactions. An example of aggregation is the formation of micelles in a solution of surfactant molecules. These micelles are formed when the hydrophobic tails of the surfactant molecules aggregate together, while the hydrophilic heads remain in contact with the solvent.Induction of self-assembly refers to the process of guiding the formation of ordered structures throughexternal stimuli or templates. This can be achieved byusing molecules or nanoparticles as templates, or by applying external fields such as magnetic or electric fields. For instance, in the field of nanotechnology, researchers have developed methods to induce the self-assembly of nanoparticles into specific patterns by using DNA strands as templates.Overall, precipitation, aggregation, and induction of self-assembly are important processes in the formation of complex structures and functional materials. Theseprocesses can be controlled and manipulated to create materials with desired properties and functionalities.中文回答:沉淀、聚合和诱导自组装是材料科学和化学领域中三个重要的过程。
材料制备英语

材料制备英语Material PreparationThe preparation of materials is a crucial step in various fields such as chemistry, engineering, and manufacturing. Different materials require different methods of preparation, and the choice of preparation method can significantly impact the properties and performance of the final product.In the field of chemistry, materials can be prepared through various techniques such as precipitation, sol-gel synthesis, and hydrothermal synthesis. For example, in the synthesis of nanoparticles, the sol-gel method is commonly used to produce homogeneous and pure materials with controlled particle size and shape. This method involves the formation of a colloidal suspension (sol) that is then transformed into a gel and subsequently dried to form the desired material.In engineering and manufacturing, materials are often prepared through processes such as casting, forging, and sintering. For instance, in the production of metalcomponents, casting is a widely used method where molten metal is poured into a mold and allowed to solidify, resulting in the desired shape. On the other hand,sintering is a process commonly used in the preparation of ceramics and powder metallurgy components, where powdered materials are heated to form a solid mass without melting.In addition to these traditional methods, advanced techniques such as 3D printing and chemical vapor deposition are being increasingly used for material preparation. 3D printing, also known as additive manufacturing, allows for the layer-by-layer construction of complex geometries, providing new opportunities for the fabrication of customized materials and components. Chemical vapor deposition, on the other hand, is a process used to produce high-quality thin films and coatings by enabling the deposition of materials from a gas phase onto a substrate.Materials can also be prepared through biological methods, such as the use of microorganisms and enzymes to produce biomaterials and biofuels. For example, microorganisms can be engineered to produce bioplastics andbio-based chemicals through fermentation processes,offering sustainable alternatives to conventionalpetroleum-based materials.Overall, the choice of material preparation method depends on the desired properties, application, and scaleof production. It is essential to carefully consider the advantages and limitations of each method to ensure the successful preparation of materials with the desired characteristics.材料制备材料的制备是化学、工程和制造等领域的关键步骤。
从纳米晶到三维超晶格结构

[综合评述]03-0429-08收稿日期:2010-10-12.基金项目:国家重大科学研究计划项目(批准号:2011CB932401)和国家自然科学基金创新研究群体项目(批准号:20921001)资助.联系人简介:李亚栋,男,博士,教授,博士生导师,主要从事纳米材料的合成及应用研究.E-mail :ydli@mail.tsinghua.edu.cn 彭卿,男,博士,副教授,主要从事无机半导体纳米材料的制备及性能研究.E-mail :pengqing@mail.tsinghua.edu.cn在过去的20年间,晶态胶体粒子的制备技术有了长足的发展[1 9].人们在不断获得各类新型纳米晶的同时,也一直致力于探寻它们的功能性质,特别是希望在一定尺度上实现其规模化应用.将纳米晶作为构建单元,组装成三维有序的高级结构(组装体),并发挥整体的集合性能,被认为是由微观材料向介观甚至宏观器件模块迈进的一条可能的途径.胶体纳米晶三维有序组装体是纳米晶按照一定的规则立体堆积而形成的周期结构.这种结构往往与晶体中原子的长程有序阵列有很多相似性,也被人们称为纳米晶的“超结构”或者“超晶格”.其中规模较大的(尺寸不小于微米量级)、块状的纳米晶超晶格又被称为“超晶体”或“胶体晶体”.超晶格的构筑主要依靠纳米晶本身或者其表面修饰分子之间存在的范德华力、电性力、磁作用力、分子表面作用和熵驱动作用等,Grzybowski 等[10]已经就此作出了较为全面的论述(表1).Table 1Interaction potentials for nanocrystals (spherical models )[10]Interaction type FormulaRange1纳米晶三维有序组装体的研究价值目前,许多具有晶体学周期堆垛方式的纳米晶组装体已经被成功构建.研究表明,这些组装体在一定程度上具有“晶化”和“生长”行为,同样也有位错[11]和孪晶[12]等典型的晶体学特征.甚至准晶结构也可以由纳米晶组装而成[13].既然纳米晶三维有序组装体的构造模式与原子晶格结构非常接近,就不妨将这种人造的超晶格作为研究晶体构成、演化和表现的直观模型.从比较研究的角度讲,大家一面力求依据现有的晶体学理论来指导制备超晶格,预测其性质;另外也致力于借助纳米晶超结构来更好地认识晶体.纳米晶超结构受到学界的广泛关注,不仅因为它们有作为晶体学模型的研究价值,还因为它们会体现出孤立纳米晶所不具备的集合性能,即纳米晶的个体属性并未改变,但在整体上却产生了新的应用性能.集合性能主要来自3个方面:(1)有序排列的相邻纳米晶在电、磁等作用下彼此互相影响,使自身原本的性质发生变化[14,15].例如,Bawend 和Murray 等[16]很早就发现,由于粒子间的耦合效应,半导体量子点的光致发光谱会出现红移现象.(2)由于组装体的周期性有序结构而产生的新性质,比如形成某种特定尺寸的有序孔道(介孔特性)[17]以及构造出光子带隙(光子晶体特性)[18].(3)不同功能的纳米晶通过二元或二元以上组装形成复合材料,使其整体表现出各独立组元的综合特性.2纳米晶三维有序组装体的几类制备方法2.1胶体溶液蒸发法通常,单分散胶体纳米晶的形貌和尺寸控制是借助于活性剂分子在晶体粒子表面的吸附包裹行为来实现的.活性剂分子之间存在着相互作用场(以范德华力为最普遍形式),故而在一定条件下纳米晶粒子会受到热力学驱动而自发地进行有序组装.作为一种形成有序纳米晶组装结构的传统方法,胶体溶液蒸发法遵循了上述的原理.该方法和晒Fig.1Schematic illustration of the solvent evaporation method [19]Nanocrystal superlattices are deposited on a solid substrate bycontrolling evaporation of the solvent of colloidal solution.制无机盐的过程类似,即将预先制得的由长链有机分子包裹的纳米晶粒子分散于适当溶剂中形成胶体溶液,随着溶剂的蒸发,胶体溶液的浓度逐渐增大,导致纳米晶粒子从液相中“结晶”析出至容器壁或者预置衬底上(如图1所示).这种方法应用的重要前提是作为组装基元的纳米晶要具有高度均匀的尺寸,此外胶体溶液的浓度和溶剂挥发速率等因素也会影响组装产物的有序度和规模[11,19 21].Fig.2Ag nanocrystal superlattice [22]近年来,有若干研究小组采用胶体溶液蒸发法在纳米晶的立体组装方面做出了有价值的工作.比如,Yang 等[22]将Ag 纳米晶组装成“等离子体晶体”(图2),在可见光波段实现了频率选择性响应;Wang和Chen 等[23]用几种均一而不同形貌的Au 纳米晶在硅衬底上构建了单构和双构的三维有序结构,并发现有序堆积使得Au 纳米棒的双光子激发性能有所增强;Korgel 等[24]则将衬底斜置于Fe 2O 3纳米晶(A )和Au 纳米晶(B )共混的胶体溶液中,得到了AB 2型的二元类晶体结构,并034高等学校化学学报Vol.32对产物的结构缺陷加以探讨.不过总的来说,由于沉积物对基底的平面依附效应,直接蒸发溶剂的方法就制备块状超晶体而言并无优势,多被用于获得连续的层状组装结构[25,26].2.2不良溶剂扩散法如果一种溶剂能有效地分散纳米晶并形成胶体溶液,那么我们就将其称为纳米晶的良溶剂,反之则称为不良溶剂.例如,对于长链有机分子包裹的纳米晶,弱极性溶剂通常为良溶剂,而极性溶剂通常为不良溶剂.事实上,在早期人们以挥发溶剂的方法组装纳米粒子时,已经尝试过在弱极性体系中加入少量极性溶剂,收到了很好的效果.1995年,Bawendi 和Murray 等[16]将CdSe 量子点分散于含90%辛烷和10%辛醇的混配溶剂中,在一定条件下低沸点的辛烷优先挥发,使胶体溶液的浓度不断增大,同时极性溶剂辛醇的百分含量也逐渐上升,从而得到了CdSe 胶体晶体.2001年,Rogach 和Talapin 等[27]进一步发展出了一种不良溶剂扩散法(图3),其原理是将纳米晶分散在其良溶剂中,然后向体系中加入不良溶剂,随着不良溶剂向良溶剂中缓慢地扩散,在原分散相和非溶剂层的接合部,纳米晶的“溶解度”会比加入不良溶剂前大大降低,这样就形成了局部过饱和的胶体溶液环境,于是纳米晶组装体便得以析出.如果引入适当的第三溶剂,在不良溶剂层和良溶剂层之间设置一个缓冲层,降低不良溶剂扩散的速度,则会使纳米晶组装得更为缓慢,形成的有序结构的质量也会更高.这类方法已经被成功地用于制备CdSe[27,28],FePt [29],CoPt 3[28],PbS [12,28],Ni [21]和Au [30]等多种纳米晶超结构,但操作起来耗时较长,往往少则一周,多则数月.Fig.3Scheme of the non-solvent diffusion method [27](A )and microscopy images of PbS nanocrystals and their 3Dassemblies [28][(B )—(E )](B )TEM image of PbS nanocrystals ;(C )optical microscopy ;(D )SEM images of a supercrystal ;(E )high-resolution SEM imageof tightly packed surface of PbS supercrystal.2.3胶束引导法胶体溶液蒸发法和不良溶剂扩散法都是依赖于有机液相来完成纳米晶组装的.为了在含水介质中实现类似的过程,人们不断探索,形成了一种胶束引导有序集聚的策略.采用该方法时,首先把有机相分散的粒子体系移入表面活性剂(如长链烷基磺酸钠或长链烷基三甲基溴化铵)的水溶液中,而后挥发掉有机溶剂,使粒子包裹于形成的胶束之中,再利用胶束的引导作用通过后续不同的处理工艺得到超晶格组装体.Fig.4Formation of water-soluble gold nanocrystal-micelles through surfactant /lipid encapsulationand their self-assembly [31](A )and a representative transmission electron micrograph of3D gold nanocrystal-micelle superlattice (B )Fan 等[31,32]将前驱体胶束溶液直接脱水沉积于衬底表面,制备了Au 等纳米晶的立方结构三维有序阵列(图4).本课题组[17,33]利用胶束微乳液中的油相液滴为模板,获得了一系列单质和化合物的有134No.3孟令镕等:从纳米晶到三维超晶格结构Fig.5Scheme of the emulsion-based bottom-up self-assembly method[33]Fig.6Typical TEM images of the colloidal spheres[33]of BaCrO4(A,B)and Ag2Se(C,D)序“胶体球”结构(图5和图6),并对双组元纳米晶复合功能材料的组装进行了初步的尝试[34].Cao 等[35 37]则将Fe3O4和CdSe/CdS纳米晶胶束注入乙二醇体系中,靠改变溶剂环境的极性使纳米晶聚集成球团,再经液相退火使球团状聚集体最终“晶化”成有序结构.2.4一些其它方法2.4.1氢键连接法氢键连接法是又一种制备亲水性纳米晶三维超结构的方法,操作流程是先在晶体粒子表面修饰上含大电负性元素的分子,然后利用水分子中的H和修饰分子上的大电负性原子形成氢键,从而将纳米粒子连接组装在一起.Kimura课题组[38 42]在这方面做了许多工作,他们制备了Au、Ag纳米晶的超晶体,并就其功能化展开了一些有益的研究(图7).值得注意的是,目前氢键连接法主要适用于强酸性体系,这就要求被组装的纳米粒子必须耐酸.Fig.7Water molecule connect with carbonyl groups from different gold particles that passivated by mercaptosuccin-ic acid(MSA),resulting in aggregation of gold particles in a humid condition[40](A)and microscope imagesof gold particle supercrystals(B)(Inset:low-angle electron diffraction from one superlattice)2.4.2静电聚集法这种方法的思路是先通过表面修饰使纳米晶粒子带上电荷,然后将电性相反的234高等学校化学学报Vol.32粒子在液相中混合,使它们凭借彼此间的静电作用力有序地结合在一起,形成自组装体.静电聚集法应用的前提是对纳米晶粒子尺寸和所带电荷的精确调控.Grzybowski 等[43]用等尺寸的受HS (CH 2)10·COO -包裹的Au 粒子(带负电)和受HS (CH 2)11NMe +3包裹的Ag 粒子(带正电)组装出了闪锌矿结构的超晶体(图8),被认为是一宗经典案例[44].Fig.8Au-Ag binary supercrystals [43](A —C )SEM images ;(D )scheme of an AB unit cell and the projections of supercrystal planes.2.4.3DNA 导向法众所周知,DNA 上的碱基具有固定的互补配对规律,于是,一些研究小组考虑将适当的DNA 修饰到纳米粒子表面,然后通过其配对行为引导粒子有序组装[如图9(A )所示].这种方法先是用于构建纳米晶的二维阵列,但被认为难于实现三维组装[44,45].2008年,Gang 等和Mirkin 等[45 47]在同一期的Nature 杂志上分别报道了利用该方法制备金纳米粒子三维立方超结构的工作,虽然产物的“结晶度”有待提高,但还是带给人们以新的希望[图9(B )].Fig.9Scheme of DNA linkages between nanoparticles (A )and representative SEM image ofnanoparticles after DNA-guided assembly at room temperature (B )[47]Fig.10Ag 2S tetrahedral superlattice and a schematic illustration of the plausible formation mechanism [48]2.4.4“水-油”界面辅助机制2007年,我们课题组[48,49]构思了一种利用“水-油(有机相)”界面辅助制备半导体硫化物纳米晶并实现其原位自组装的途径(图10):首先,金属离子水溶液(如银氨溶液或铜盐溶液)与硫醇(或含有硫醇的有机相)在“水-油”界面处反应,生成硫醇金属离子配合物前驱体;而后,硫醇金属离子配合物热分解,源源不断地产生金属硫化物(如Ag 2S 、Cu 2S )纳米晶;最终,纳米晶在极性-弱极性两相邻接区部分自组装成有序结构.2.4.5外场辅助法一些文献也报道了外场引导组装纳米晶的方法.如Alivisatos 等[50]在直流电场下334No.3孟令镕等:从纳米晶到三维超晶格结构蒸发CdS 纳米棒胶体溶液,制备了轴向垂直于衬底的三维纳米棒阵列;Cheon 等[51]以钴纳米粒子为基元,在磁场引导下制备了具有取向性的面心立方堆积超结构(图11);Song 和Clays 等[18]则在椭球形Fe 2O 3/SiO 2核壳粒子的对流自组装过程中施加磁场,得到了粒子长轴平行于衬底的三斜型超结构光子晶体.外场辅助法的优势是可以通过场的作用来调控纳米晶组装体的向性生长,但该法只能应用于对外场有特定响应的材料.Fig.11Schematic of Co supercrystal formation via magnetic field induced assembly (A );unit cell struc-ture (B );low (C )and high (D )magnification TEM images ;[001]SL (E )and [111]SL (F )pro-jections of fcc-structured supercrystals [51]SL :Superlattice.Fig.12Fe 3O 4octahedral supercrystals [52]Low (A )and high (B )magnification SEM images ;TEM images of the superlattice structure (C ,D );3D schematic model of the supercrystals (E ).2.4.6表面活性剂浓度控制的一步法溶剂热自组装最近,我们[52]设计了一种一步法实现纳米晶制备及原位组装的工艺,即在封闭的溶剂热体系中,通过改变脂肪酸活性剂的浓度,来调节新生成纳米晶的表面修饰分子偶极作用强度,以达到促使粒子聚集“晶化”的目的.实验取得了初步进展,在几小时内制备出了具有规则八面体外形且无衬底依赖的微米级Fe 3O 4超晶体(图12).434高等学校化学学报Vol.323结论在公元前2500 2600年间,古埃及人就用巨石建造出了雄伟的金字塔[53].几千年之中,形形色色的人工建筑物让世界的面貌和人类的生活都为之巨变,然而在微观世界里,我们的建筑工作才刚刚起步.虽然人们在纳米晶超结构组装方面已取得了上述的进展,但是在这一领域内还存在着无法回避的挑战.首先,对于目前的人工纳米晶三维组装体,材料物质的种类还很有限,多为几类金属(如Ag ,Au )或半导体(如硫化物,硒化物).而且,在工艺上,纳米晶的制备和组装往往是两步完成的,整个流程所需步骤较多,耗时较长,有时还要消耗大量的有机试剂,不利于大规模生产.不仅如此,迄今为止纳米晶组装体超结构的规模还较为有限,形态也多不规则,结构稳定性亦有待提高,同时也没有完全解除对衬底的依赖.今后,科研工作者必将拓宽研究对象的范围,在改进和创新的基础上,寻找环境友好、简便经济、普便适用的组装方法,力争能早日按照实用需求“量体裁衣”,可按地制备出具有较大尺寸与统一规格的组装产品.参考文献[1]Cushing B.L.,Kolesnichenko V.L.,O ’Connor C.J..Chem.Rev.[J ],2004,104(9):3893—3946[2]Wang X.,Zhuang J.,Peng Q.,Li Y.D..Nature [J ],2005,437(7055):121—124[3]Wang X.,Peng Q.,Li Y.D..Acc.Chem.Res.[J ],2007,40(8):635—643[4]Wang X.,Li Y.D..Chem.Commun.[J ],2007,(28):2901—2910[5]Kwon S.G.,Hyeon T..Acc.Chem.Res.[J ],2008,41(12):1696—1709[6]Wang D.S.,Xie T.,Li Y.D..Nano Res.[J ],2009,2(1):30—46[7]ZHANG Hao (张皓),YANG Bai (杨柏).Chem.J.Chinese Universities (高等学校化学学报)[J ],2008,29(2):217—229[8]WANG Ding-Sheng (王定胜),PENG Qing (彭卿),LI Ya-Dong (李亚栋).Sci.China Ser.G ,Phys.Mech.Astron.(中国科学G 辑:理学,力学,天文学)[J ],2008,38(11):1434—1454[9]PENG Qing (彭卿),LI Ya-Dong (李亚栋).Sci.China Ser.B ,Chem (中国科学B 辑:化学)[J ],2009,39(10):1028—1052[10]Bishop K.J.M.,Wilmer C.E.,Soh S.,Grzybowski B.A..Small [J ],2009,5(14):1600—1630[11]Wang Z.L..Adv.Mater.[J ],1998,10(1):13—30[12]Rupich S.M.,Shevchenko E.V.,Bodnarchuk M.I.,Lee B.,Talapin D.V..J.Am.Chem.Soc.[J ],2010,132(1):289—296[13]Talapin D.V.,Shevchenko E.V.,Bodnarchuk M.I.,Ye X.C.,Chen J.,Murray C.B..Nature [J ],2009,461(7266):964—967[14]Murray C.B.,Kagan C.R.,Bawendi M.G..Annu.Rev.Mater.Sci.[J ],2000,30:545—610[15]Talapin D.V.,Lee J.S.,Kovalenko M.V.,Shevchenko E.V..Chem.Rev.[J ],2010,110(1):389—458[16]Murray C.B.,Kagan C.R.,Bawendi M.G..Science [J ],1995,270(5240):1335—1338[17]Wang D.,Xie T.,Peng Q.,Li Y..J.Am.Chem.Soc.[J ],2008,130(12):4016—4022[18]Ding T.,Song K.,Clays K.,Tung C.H..Adv.Mater.[J ],2009,21(19):1936—1940[19]Shevchenko E.V.,Talapin D.V.,Murray C.B.,O'Brien S..J.Am.Chem.Soc.[J ],2006,128(11):3620—3637[20]Pileni M.P..Acc Chem.Res.[J ],2007,40(8):685—693[21]Park J.,Kang E.,Son S.U.,Park H.M.,Lee M.K.,Kim J.,Kim K.W.,Noh H.J.,Park J.H.,Bae C.J.,Park J.G.,Hyeon T..Adv.Mater.[J ],2005,17(4):429—434[22]Tao A.R.,Ceperley D.P.,Sinsermsuksakul P.,Neureuther A.R.,Yang P..Nano Lett.[J ],2008,8(11):4033—4038[23]Ming T.,Kou X.S.,Chen H.J.,Wang T.,Tam H.L.,Cheah K.W.,Chen J.Y.,Wang J.F..Angew.Chem.Int.Ed.[J ],2008,47(50):9685—9690[24]Smith D.K.,Goodfellow B.,Smilgies D.M.,Korgel B.A..J.Am.Chem.Soc.[J ],2009,131(9):3281—3290[25]Shevchenko E.V.,Talapin D.V.,Kotov N.A.,O'B rien S.,Murray C.B..Nature [J ],2006,439(7072):55—59[26]Urban J.J.,Talapin D.V.,Shevchenko E.V.,Kagan C.R.,Murray C.B..Nature Mater.[J ],2007,6(2):115—121[27]Talapin D.V.,Shevchenko E.V.,Kornowski A.,Gaponik N.,Haase M.,Rogach A.L.,Weller H..Adv.Mater.[J ],2001,13(24):1868—1871[28]Podsiadlo P.,Krylova G.,Lee B.,Critchley K.,Gosztola D.J.,Talapin D.V.,Ashby P.D.,Shevchenko E.V..J.Am.Chem.Soc.[J ],2010,132(26):8953—8960[29]Shevchenko E.,Talapin D.,Kornowski A.,Wiekhorst F.,Kotzler J.,Haase M.,Rogach A.,Weller H..Adv.Mater.[J ],2002,14(4):287—290534No.3孟令镕等:从纳米晶到三维超晶格结构634高等学校化学学报Vol.32[30]Zheng N.,Fan J.,Stucky G.D..J.Am.Chem.Soc.[J],2006,128(20):6550—6551[31]Fan H.Y.,Leve E.,Gabaldon J.,Wright A.,Haddad R.E.,Brinker C.J..Adv.Mater.[J],2005,17(21):2587—2590[32]Fan H.Y..Chem.Commun.[J],2008,(12):1383—1394[33]Bai F.,Wang D.S.,Huo Z.Y.,Chen W.,Liu L.P.,Liang X.,Chen C.,Wang X.,Peng Q.,Li Y.D..Angew.Chem.Int.Ed.[J],2007,46(35):6650—6653[34]Li P.,Peng Q.,Li Y.D..Adv.Mater.[J],2009,21(19):1945—1948[35]Zhuang J.,Wu H.,Yang Y.,Cao Y.C..J.Am.Chem.Soc.[J],2007,129(46):14166—14167[36]Zhuang J.Q.,Wu H.M.,Yang Y.G.,Cao Y.C..Angew.Chem.Int.Ed.[J],2008,47(12):2208—2212[37]Zhuang J.Q.,Shaller A.D.,Lynch J.,Wu H.M.,Chen O.,Li A.,Cao Y.C..J.Am.Chem.Soc.[J],2009,131(17):6084—6085[38]Kimura K.,Sato S.,Yao H..Chem.Lett.[J],2001,(4):372—373[39]Wang S.H.,Sato S.,Kimura K..Chem.Mat.[J],2003,15(12):2445—2448[40]Wang S.H.,Yao H.,Sato S.,Kimura K..J.Am.Chem.Soc.[J],2004,126(24):7438—7439[41]Nishida N.,Shibu E.S.,Yao H.,Oonishi T.,Kimura K.,Pradeep T..Adv.Mater.[J],2008,20(24):4719—4723[42]Shibu E.S.,Muhammed M.A.H.,Kimura K.,Pradeep T..Nano Res.[J],2009,2(3):220—234[43]Kalsin A.M.,Fialkowski M.,Paszewski M.,Smoukov S.K.,Bishop K.,Grzybowski B.A..Science[J],2006,312(5772):420—424[44]Velev O.D..Science[J],2006,312(5772):376—377[45]Richert C.,Meng M.,Muller K.,Heimann K..Small[J],2008,4(8):1040—1042[46]Park S.Y.,Lytton-Jean A.,Lee B.,Weigand S.,Schatz G.C.,Mirkin C.A..Nature[J],2008,451(7178):553—556[47]Nykypanchuk D.,Maye M.M.,van der Lelie D.,Gang O..Nature[J],2008,451(7178):549—552[48]Zhuang Z.B.,Peng Q.,Wang X.,Li Y.D..Angew.Chem.Int.Ed.[J],2007,46(43):8174—8177[49]Zhuang Z.B.,Peng Q.,Zhang B.,Li Y.D..J.Am.Chem.Soc.[J],2008,130(32):10482—10483[50]Ryan K.M.,Mastroianni A.,Stancil K.A.,Liu H.T.,Alivisatos A.P..Nano Lett.[J],2006,6(7):1479—1482[51]Park J.I.,Jun Y.W.,Choi J.S.,Cheon J..Chem.Commun.[J],2007,(47):5001—5003[52]Meng L.,Chen W.,Tan Y.,Zou L.,Chen C.,Zhou H.,Peng Q.,Li Y..Nano Res.[J],DOI10.1007/s12274-010-0091-8[53]Spence K..Nature[J],2000,408:320—324Self-assembly of3D Nanocrystal-superlatticesMENG Ling-Rong1,PENG Qing1,2*,ZHOU He-Ping1,LI Ya-Dong1,2*(1.State Key Laboratory of New Ceramics and Fine Processing,2.Department of Chemistry,Tsinghua University,Beijing100084,China)Abstract The assembly of nanocrystals into various ordered structures is key to their future applications.In this article,we describe the recent progresses in the assembly routes and mechanisms of the three-dimensional superlattices of nanocrystals.This review focuses on the techniques of nanocrystal assembly based on solvent evaporation of colloidal solutions,non-solvent diffusion,micelle-induced aggregation,hydrogen bonding linkage,electrostatic interactions,DNA base-pairing,external field-assistance,and oil-water interface templating.The existing challenges and future development of nanocrystals assembly are also discussed.Keywords Nanocrystal;Self-assembly;3D superlattice;Supercrystal;Collective property(Ed.:M,G)。
纳米金属颗粒物原位催化 英文
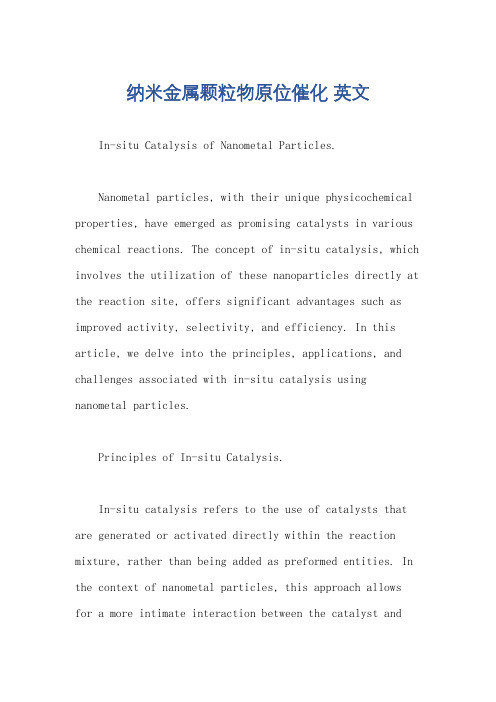
纳米金属颗粒物原位催化英文In-situ Catalysis of Nanometal Particles.Nanometal particles, with their unique physicochemical properties, have emerged as promising catalysts in various chemical reactions. The concept of in-situ catalysis, which involves the utilization of these nanoparticles directly at the reaction site, offers significant advantages such as improved activity, selectivity, and efficiency. In this article, we delve into the principles, applications, and challenges associated with in-situ catalysis using nanometal particles.Principles of In-situ Catalysis.In-situ catalysis refers to the use of catalysts that are generated or activated directly within the reaction mixture, rather than being added as preformed entities. In the context of nanometal particles, this approach allowsfor a more intimate interaction between the catalyst andthe reactants, leading to enhanced catalytic activity. The small size of these nanoparticles ensures a high surface-to-volume ratio, which in turn results in a greater numberof active sites available for catalysis.The catalytic activity of nanometal particles isfurther enhanced by their unique electronic and structural properties. The quantum size effects observed in nanoparticles lead to changes in their electronic structure, which can significantly alter their catalytic behavior. Additionally, the high surface energy of nanoparticles promotes their stability and prevents sintering, even at elevated temperatures, maintaining their catalytic activity over extended periods.Applications of In-situ Catalysis.The applications of in-situ catalysis using nanometal particles are diverse and span across various fields of chemistry and engineering. Some of the key applications include:1. Organic Synthesis: Nanometal particles, especially those of platinum, palladium, and gold, have found widespread use in organic synthesis reactions such as hydrogenation, carbon-carbon bond formation, and oxidation reactions. Their use in in-situ catalysis allows for more efficient and selective transformations.2. Fuel Cells: Nanometal particles, particularly those of platinum and palladium, are key components in the electrodes of fuel cells. Their in-situ catalysis promotes the efficient oxidation of fuels such as hydrogen, leading to improved fuel cell performance.3. Photocatalysis: The combination of nanometal particles with photocatalysts such as titanium dioxide offers a powerful tool for solar-driven reactions. The in-situ generation of reactive species at the interface of these materials enhances photocatalytic activity and selectivity.Challenges and Future Directions.While the potential of in-situ catalysis using nanometal particles is immense, there are several challenges that need to be addressed. One of the key challenges is the stability of these nanoparticles under reaction conditions. The aggregation and sintering of nanoparticles can lead to a decrease in their catalytic activity. To address this, strategies such as stabilization by ligands or supports, and the use of bimetallic or core-shell structures have been explored.Another challenge lies in the scale-up of these processes for industrial applications. While laboratory-scale experiments often demonstrate promising results, translating these findings to large-scale operations can be challenging due to factors such as mass transport limitations and heat management.Future research in in-situ catalysis with nanometal particles could focus on developing more robust and stable catalyst systems. The exploration of new nanomaterials with enhanced catalytic properties, as well as the optimization of reaction conditions and reactor designs, are likely tobe key areas of interest. Additionally, the integration ofin-situ catalysis with other technologies such as microfluidics and nanoreactors could lead to more efficient and sustainable catalytic processes.In conclusion, the field of in-situ catalysis using nanometal particles offers significant potential for enhancing the efficiency and selectivity of chemical reactions. While there are still challenges to be addressed, the ongoing research in this area is likely to lead to transformative advancements in catalysis and beyond.。
碳酸氢钙与过量氢氧化钙溶液反应的离子方程式

碳酸氢钙与过量氢氧化钙溶液反应的离子方程式碳酸氢钙与过量氢氧化钙溶液反应的离子方程式主题:碳酸氢钙与过量氢氧化钙溶液反应的离子方程式概念:碳酸氢钙(化学式:Ca(HCO3)2)是一种常见的无机化合物,可溶于水中。
氢氧化钙(化学式:Ca(OH)2)也是一种常见的无机化合物,也可溶于水中。
碳酸氢钙与过量氢氧化钙溶液反应时,生成的产物是什么?反应方程式是怎样的?本文将从简单到复杂、由浅入深的方式,逐步探讨碳酸氢钙与过量氢氧化钙溶液反应的离子方程式,并探讨相关的化学原理。
1. 碳酸氢钙的结构和性质(提及主题文字:碳酸氢钙)碳酸氢钙是由钙离子(Ca2+)和碳酸根离子(HCO3-)组成的盐类。
它的化学名称显示了它的结构:一个钙离子与两个碳酸根离子结合。
2. 过量氢氧化钙溶液的性质(提及主题文字:过量氢氧化钙溶液)氢氧化钙是由钙离子(Ca2+)和氢氧根离子(OH-)组成的盐类。
过量氢氧化钙溶液指的是溶解了较多氢氧化钙的水溶液。
3. 反应方程式的推导在碳酸氢钙和过量氢氧化钙溶液反应中,发生了酸碱反应。
碳酸氢钙可以被看作是一个酸性物质,而氢氧化钙溶液可以被看作是一种碱性物质。
酸碱中和反应会使酸和碱中的氢离子(H+)和氢氧根离子(OH-)结合形成水(H2O)。
由此可知,碳酸氢钙中的碳酸根离子(HCO3-)与过量氢氧化钙溶液中的氢氧根离子(OH-)会反应生成水。
反应方程式可以写作:Ca(HCO3)2 + Ca(OH)2 → 2 CaCO3 + 2 H2O4. 反应产物的解释反应方程式表明,碳酸氢钙和过量氢氧化钙溶液反应后,生成了两个产物:碳酸钙(CaCO3)和水(H2O)。
碳酸钙是一种常见的无机盐类,常见于贝壳、珊瑚、石灰石等自然界中。
5. 反应过程中的离子在反应中,离子在溶液中起着至关重要的作用。
当溶液中的碳酸氢钙和氢氧化钙溶解时,它们会分解成离子。
主要的离子包括:Ca2+、HCO3-、OH-。
这些离子在反应中重新组合形成了碳酸钙和水。
04级(1)无机化学期末考试试卷
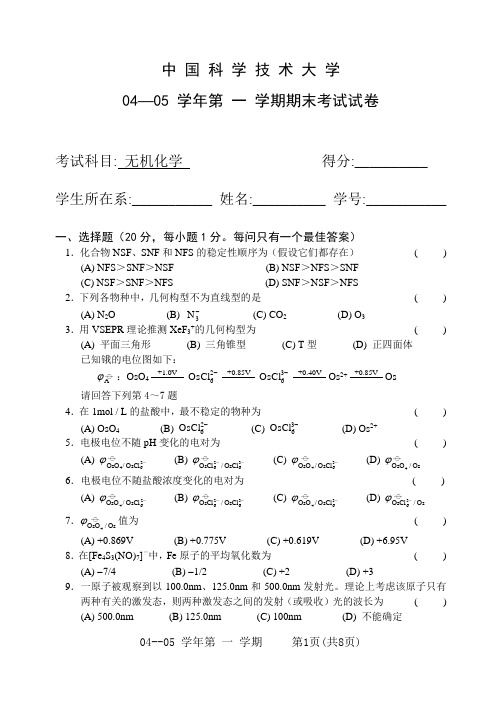
04--05 学年第 一 学期 第1页(共8页)中 国 科 学 技 术 大 学 04—05 学年第 一 学期期末考试试卷考试科目: 无机化学 得分:__________ 学生所在系:___________ 姓名:__________ 学号:___________一、选择题(20分,每小题1分。
每问只有一个最佳答案)1.化合物NSF 、SNF 和NFS 的稳定性顺序为(假设它们都存在) ( ) (A) NFS >SNF >NSF (B) NSF >NFS >SNF (C) NSF >SNF >NFS (D) SNF >NSF >NFS2.下列各物种中,几何构型不为直线型的是 ( )(A) N 2O (B) -3N (C) CO 2 (D) O 33.用VSEPR 理论推测XeF 3+的几何构型为 ( ) (A) 平面三角形 (B) 三角锥型 (C) T 型 (D) 正四面体 已知锇的电位图如下:A ϕ :OsO 4+1.0V-26OsCl+0.85V-36OsCl+0.40VOs 2++0.85VOs请回答下列第4~7题4.在1mol / L 的盐酸中,最不稳定的物种为 ( )(A) OsO 4 (B) -26OsCl (C) -36OsCl (D) Os2+ 5.电极电位不随pH 变化的电对为 ( )(A) -264OsCl/sO O ϕ (B) --3626OsCl/OsCl ϕ (C) -364OsCl/sO O ϕ (D) Os/OsO 4ϕ6.电极电位不随盐酸浓度变化的电对为 ( )(A) -264OsCl/sO O ϕ (B) --3626OsCl/OsClϕ (C) -364OsCl/sOO ϕ (D) Os/OsCl36-ϕ7.Os/OsO4ϕ值为 ( )(A) +0.869V (B) +0.775V (C) +0.619V (D) +6.95V8.在[Fe 4S 3(NO)7]-中,Fe 原子的平均氧化数为 ( ) (A) -7/4 (B) -1/2 (C) +2 (D) +39.一原子被观察到以100.0nm 、125.0nm 和500.0nm 发射光。
量子点合成方法总结(2018)
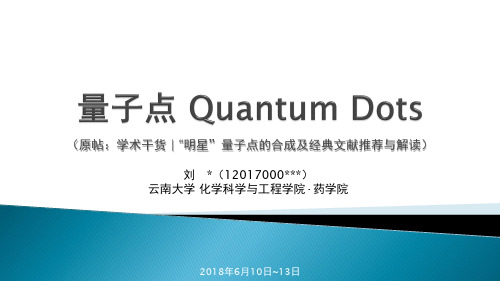
(LaMer机理)
Murray, C. B., et al. J. Am. Chem. Soc., 1993, 115 (19): 8706-8715.
10
2.2.非注射法
热注射法是合成高质量单分散量子点 的有效方法,然而可用的前驱体有限、剧 毒,暴露了热注射法的缺点。后来研究人 员不断努力,发展出不需要剧毒前驱体的 非热注射法。以李亚栋老师课题组2009 的JACS为例,简单介绍一下该方法。
12
LSS法机理:
13
参考文献(1/2):
1.Kwon, S. G.; Hyeon, T., Formation Mechanisms of Uniform Nanocrystals via Hot-Injection and Heat-Up Methods. Small 2011, 7 (19), 2685-2702.
6.Murray, C. B.; Norris, D. J.; Bawendi, M. G., Synthesis and characterization of nearly monodisperse CdE (E = sulfur, selenium, tellurium) semiconductor nanocrystallites. Journal of the American Chemical Society 1993, 115 (19), 8706-8715. (热注射法合成CdSe量子点)
Synthesis of ZnO nanoparticles from microemulsions in a flow type microreactor
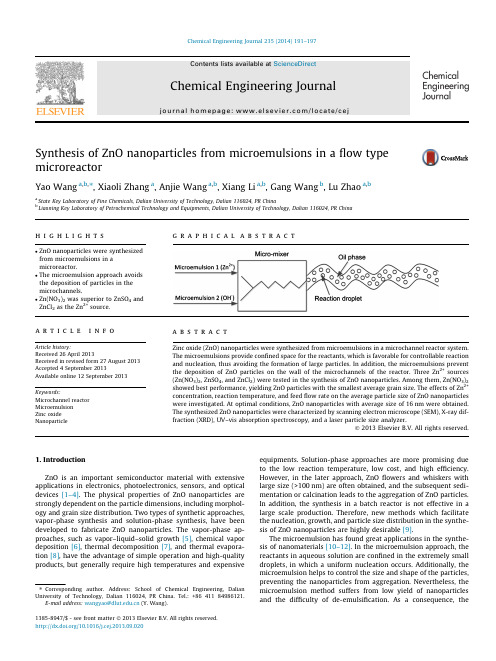
Synthesis of ZnO nanoparticles from microemulsions in a flow typemicroreactorYao Wang a ,b a State Key Laboratory bLiaoning Key Laboratory a r t i c l e i n f o Article history:Received 26April 2013Received in revised form 27August 2013Accepted 4September 2013Available online 12September 2013Keywords:Microchannel reactor Microemulsion Zinc oxide Nanoparticlea b s t r a c tZinc oxide (ZnO)nanoparticles were synthesized from microemulsions in a microchannel reactor system.The microemulsions provide confined space for the reactants,which is favorable for controllable reaction and nucleation,thus avoiding the formation of large particles.In addition,the microemulsions prevent the deposition of ZnO particles on the wall of the microchannels of the reactor.Three Zn 2+sources (Zn(NO 3)2,ZnSO 4,and ZnCl 2)were tested in the synthesis of ZnO nanoparticles.Among them,Zn(NO 3)2showed best performance,yielding ZnO particles with the smallest average grain size.The effects of Zn 2+concentration,reaction temperature,and feed flow rate on the average particle size of ZnO nanoparticles were investigated.At optimal conditions,ZnO nanoparticles with average size of 16nm were obtained.The synthesized ZnO nanoparticles were characterized by scanning electron microscope (SEM),X-ray dif-fraction (XRD),UV–vis absorption spectroscopy,and a laser particle size analyzer.Ó2013Elsevier B.V.All rights reserved.1.IntroductionZnO is an important semiconductor material with extensive applications in electronics,photoelectronics,sensors,and optical devices [1–4].The physical properties of ZnO nanoparticles are strongly dependent on the particle dimensions,including morphol-ogy and grain size distribution.Two types of synthetic approaches,vapor-phase synthesis and solution-phase synthesis,have been developed to fabricate ZnO nanoparticles.The vapor-phase ap-proaches,such as vapor–liquid–solid growth [5],chemical vapor deposition [6],thermal decomposition [7],and thermal evapora-tion [8],have the advantage of simple operation and high-quality products,but generally require high temperatures and expensive equipments.Solution-phase approaches are more promising due to the low reaction temperature,low cost,and high efficiency.However,in the later approach,ZnO flowers and whiskers with large size (>100nm)are often obtained,and the subsequent sedi-mentation or calcination leads to the aggregation of ZnO particles.In addition,the synthesis in a batch reactor is not effective in a large scale production.Therefore,new methods which facilitate the nucleation,growth,and particle size distributionin the synthe-sis of ZnO nanoparticles are highly desirable [9].The microemulsion has found great applications in the synthe-sis of nanomaterials [10–12].In the microemulsion approach,the reactants in aqueous solution are confined in the extremely small droplets,in which a uniform nucleation occurs.Additionally,the microemulsion helps to control the size and shape of the particles,preventing the nanoparticles from aggregation.Nevertheless,the microemulsion method suffers from low yield of nanoparticles and the difficulty of de-emulsification.As a consequence,the1385-8947/$-see front matter Ó2013Elsevier B.V.All rights reserved./10.1016/j.cej.2013.09.020⇑Corresponding author.Address:School of Chemical Engineering,DalianUniversity of Technology,Dalian 116024,PR China.Tel.:+8641184986121.E-mail address:wangyao@ (Y.Wang).reactor performance is generally low when the synthesis takes place in a batch reactor.Recently,microchannel reactors have been utilized for produc-ing nano-sized particles,including metals and alloys [13–18],me-tal salts [19,20],metal oxides [21],polymers [22],mesoporous materials [23],and zeolites [24].The flow type microchannel reac-tors are able to intensify the mass and heat transfers as well as the mixing.The high surface-to-volume ratio in the microchannel reactors is favorable to enhance the response time and maintain isothermal conditions.Because the concentrations of reactants and temperature are homogeneous in the reaction zone,the ob-tained particles are uniform and reproducible.When a single phase is involved,the velocity distribution in a microchannel is substantially broadened along the flow direction.Gunther et al.[25]compared the well mixing efficiency chaotic mixer with a liquid–liquid two phase mixer,and found that,when the fluid was mixed completely (P 95%),the length of the channel required for the two-phase flow was 2–3times shorter than for the single-phase flow.The computational fluid dynamics (CFD)simula-tions indicate that the enhancement of mass transfer can be inter-preted in terms of an internal circulation flow within the plugs.As a consequence,narrow particle size distribution could be obtained in the synthesis of nanoparticles due to the enhanced mixing and the narrow residence time distribution in the segmented liquid–li-quid flow [26].Another important issue in the synthesis of solid materials in a microchannel is that the formed particles may nucle-ate and deposit on the microchannel walls,leading to runawayIn the present paper,ZnO nanoparticles were synthesized by mixing the Zn 2+-containing water-in-oil microemulsion with the NaOH-containing one in a micromixer followed by subsequent reaction in the relay tube (Fig.1).The synthesis conditions were optimized,and the obtained ZnO nanoparticles were characterized.2.Experimental 2.1.SynthesisAll of the chemicals were of analytical grade,and used without further purification (Tianjin Kermel Chemical Reagent Co.Ltd.).De-ionized water was obtained from a water purification system.The microemulsions were prepared in the following way.N-butanol,cetyltrimethyl ammonium bromide (CTAB),and n-octane were mixed at a mass ratio of 1.0:1.2:4.4to form an organic phase.CTAB served as the surfactant,whereas n-butanol as the co-surfac-tant.An aqueous solution of Zn 2+(Zn(NO 3)2,ZnSO 4,and ZnCl 2)were prepared by dissolving the salt in water under stirring.The solution of NaOH was prepared in a similar way.The microemul-sion of Zn 2+(denoted as M(Zn 2+))were obtained by adding the aqueous solution of Zn 2+into the above organic phase under vigor-ous stirring with an aqueous mass fraction of 15%,and the mixture was stirred until it became transparent.The microemulsion of NaOH (denoted as M(NaOH))was prepared by the same procedure with the same aqueous mass fraction.Fig.1.Schematic diagram for the synthesis of nanoparticles by microemulsion in a microreactor.Fig.2.The experimental setup for the flow type synthesis of ZnO nanoparticles.were obtained by drying the solid prod-followed by calcination at550°C for3h.nanoparticles were synthesized in aflaskM(Zn2+)and M(NaOH).M(Zn2+)wasthen M(NaOH)was added under vigorouswhite precipitates were separated,dried,way.the synthesized ZnO nanoparticles wereemission scanning electron microscope(NovaCompany,USA,acceleration voltage of3.0kV).were measured by a laser particle sizeParticles Instruments Co.).The powderwere recorded on a Rigaku RAD-2Xradiation at40kV.The photos of dropletstaken on an optical microscope(EC300,fined space.Therefore,the synthesis reaction will terminate when no Zn2+source is available,thus making the fast reaction controlla-ble and preventing the formation of substantially larger particles. Another favorable advantage of this approach is that the resultant precipitates are entrapped in the droplet,which is dispersed in the organic phase,thus avoiding the deposition of solid product on the microchannel walls.3.1.Effect of Zn2+sourceThree Zn2+sources were used in the investigation and the syn-thesis was conducted under the following conditions:50°C, 2.0MPa,feedflow rate 2.0mL/min,respectively,NaOHFig.3.Synthesis of ZnO precursor by microemulsions dispersed in an oil phase.Fig.4.Photos of the aqueous droplets in M(NaOH)(a)and M(Zn(NO3)2)(b).concentration1.0mol/L,Zn2+concentration0.5mol/L.Fig.5shows the XRD patterns of the ZnO nanoparticles synthesized from ZnSO4, Zn(NO3)2,and ZnCl2,respectively.Only the diffraction peaks char-acteristic of hexagonal ZnO structure were observed,indicating that pure ZnO crystals were obtained from the different Zn2+ sources.The particle diameter(D)was calculated according to the Debye–Scherrer equation(D=0.89k/b cos h).It is found that the crystallite sizes were13.0,27.0,and10.4nm for ZnCl2,ZnSO4, and Zn(NO3)2,respectively.It suggests that the Zn2+source mark-edly affects the formation and crystallization of Zn(OH)2in the microreactor system.Among them,Zn(NO3)2was the most suitable2+source in the synthesis of ZnO nanoparticles.Srikanth and Jeevanandam investigated the effect of anionsÀ,SO2À4,NOÀ3,and CH3COOÀ)on the size and morphology of syn-thesized ZnO particles in urea-induced homogeneous precipitation [28].They also found that the anion affected the morphology and size of the synthesized ZnO particles.They proposed that the an-ions serve as the surface modifiers,influencing the nucleation and the growth of the crystallites.3.2.Effect of Zn2+concentrationIn the precipitation of Zn(OH)2,the reaction rate depends onboth the Zn2+concentration and reaction temperature from the viewpoint of reaction kinetics.The effects of Zn2+concentration were investigated in the synthesis of ZnO nanoparticles from ZnSO4and Zn(NO3)2.The reaction conditions were as follows:feed flow rates of M(Zn2+)and M(NaOH),2.0mL/min,respectively;tem-perature,50°C;NaOH/Zn2+molar ratio,2.0;pressure,2.0MPa.The Zn2+concentration was varied in the range of0.3–0.8mol/L.Fig.6 illustrates the XRD patterns of ZnO nanoparticles synthesized at various concentrations of ZnSO4and Zn(NO3)2.Only hexagonal crystalline phase was detectable in each sample,regardless of the Zn2+sources and their concentrations.The dependence of the aver-age particle size on the Zn2+source and concentration is illustrated in Fig.7.As shown in Fig.5,the Zn2+source significantly affected the particle size of the obtained ZnO nanoparticles.The average sizes of ZnO nanoparticles synthesized from ZnSO4were1.2–1.3 times those of the nanoparticles from Zn(NO3)2at the same Zn2+ concentrations.The difference may relate to the different rate con-stants of ZnSO4and Zn(NO3)2with NaOH.Because the anion va-lence of SO2À4is higher than that of NOÀ3,the ionic strength ofSO2À4is larger,resulting in a decline in Zn2+activity of ZnSO4.It is indicated that the average size of ZnO nanoparticles also depended on the Zn2+concentration,decreasing with increasing the Zn2+con-centration for both ZnSO4and Zn(NO3)2.According to the crystalli-zation kinetics[29],the crystal average size(D)and nucleation rate (B)are determined by:D¼4E s V mm RT ln Sð1ÞB¼Z c expÀ16p E3s V2m N a"#ð2ÞFig.5.XRD patterns of ZnO nanparticles synthesized from different Zn2+sources.Fig.6.XRD patterns of ZnO nanoparticles synthesized with different Zn2+source and various concentrations.(a)C NaOH=1.2M,C ZnSO4=0.6M;(b)C NaOH=1.0ZnSO4=0.5M;(c)C NaOH=0.8M,C ZnSO4=0.4M;(d)C NaOH=0.6M,C ZnSO4=0.3C NaOH=1.2M,C ZnðNO3Þ2¼0:6M;(f)C NaOH=1.0M,C ZnðNO3Þ2¼0:5M;NaOH =0.8M,C ZnðNO3Þ2¼0:4M;(h)C NaOH=0.6M,C ZnðNO3Þ2¼0:3M.Fig.7.Dependence of the average size of ZnO particles on the Zn2+source andconcentration.(d)ZnSO4,(j)Zn(NO3)2.Journal235(2014)191–1978.XRD patterns of ZnO nanoparticles synthesized at different temperatures. Fig.9.The average size of ZnO particles synthesized at different temperatures.Fig.10.The average size of ZnO particles as a function of feedflow rate in synthesis from Zn(NO3)2at50°C.11.SEM images of ZnO particles synthesized in the microreactor(a)andreactor(b).3.4.Effect of feedflow rateZn(NO3)2was used as the Zn2+source,and the concentrations of Zn(NO3)2and NaOH were0.5and1.0mol/L,respectively.The syn-thesis reaction was conducted at50°C and2.0MPa,and the feed flow rate was varied from2.0to6.0mL/min.The variation of the average size of ZnO nanoparticles with the feedflow rate is shown in Fig.10.The average particle size of ZnO did not change markedly with feedflow rate.At lowflow rates(2.0–4.0mL/min),the aver-age particle size was reduced slightly with the feedflow rate.At lowflow rates,the increased residence time allowed for the com-pletion of both synthesis reaction and crystallization in the reac-tion system.At highflow rates,the residence time was probably long enough for the completion of synthesis reaction,because the synthesis reaction is substantially fast.However,the reduced residence time at highflow rate might be not long enough for the completion of the precipitate crystallization.The crystalliza-tion might continue to take place in the collection container the outlet of the reaction system,leading to the formation of larger particles.parison of the microreactor with a batch reactorFor comparison,a batch reactor was used to synthesize ZnO nanoparticles from the two emulsions.The synthesis reaction con-ditions were as follows:temperature50°C;Zn(NO3)2concentra-tion0.5mol/L;NaOH concentration1.0mol/L,pressure0.1MPa, and time3h.The synthesis was conducted in aflask under stirring. The post-treatment was the same as that in the microreactor.The obtained ZnO nanoparticles synthesized from different reactors were characterized by means of scanning electron microscopy (SEM)observation,measurement of particle size distribution and UV–visible absorption spectroscopy.Both the SEM images Fig.11)and particle size distribution curves(Fig.12a and b)indi-cated that the ZnO nanoparticles synthesized in the microreactor were smaller and more narrowly distributed in size than those synthesized in the batch reactor.The UV–visible absorption spectra Fig.13)indicated that the absorption edge for the ZnO nanoparti-cles synthesized in the microreactor was slightly blue-shifted, compared with those synthesized in a batch reactor,probably due to the size effects[30].the obtained ZnO nanoparticles was compared with those of the particles synthesized in the microreator and in the batch reactor (Fig.12).It is apparent that the micromixer significantly reduced the particle size and improved the size distribution of ZnO nanoparticles.4.ConclusionsZnO nanoparticles synthesized from microemulsions in a con-tinuous microreactor were smaller in grain size and more narrowly distributed than those in a batch reactor.The microemulsions pro-vide confined space for the reactants,which is favorable for con-trollable reaction and nucleation,avoiding the formation of large particles.In addition,the microemulsions prevent the deposition of ZnO particles on the wall of the microchannels of the reactor,Fig.12.Size distributions of ZnO nanoparticles synthesized in different reactors.(a)Microreactor.(b)Batch reactor.(c)Mixing by T-joint.Fig.13.UV–visible absorption spectra of ZnO synthesized in different reactors.and no clogging of the microchannels occurred in the investigation. Three Zn2+sources(Zn(NO3)2,ZnSO4,and ZnCl2)were tested in the synthesis of ZnO nanoparticles.It is found that Zn(NO3)2showed best performance in the synthesis.Both Zn2+concentration and reaction temperature significantly affected the average particle sizes of the synthesized ZnO nanoparticles,probably due to their effects on the kinetics of the synthesis reaction and nucleation. The average particle size was reduced with increasing the Zn2+ concentration,whereas a minimum average particle size was ob-served50°C when the reaction temperature was increased from 40to70°C.The feedflow rate did not affect considerably the aver-age particle size of ZnO nanoparticles.However,at highflow rates, larger particles were obtained,probably because the crystallization might continue after the droplets had left the reaction system.This may imply that the crystallization step was slower that the synthe-sis reaction.AcknowledgmentsThis work wasfinancially supported by NSFC(20773020, 20973030,21173033,U1162203),the‘‘863’’Project (2008AA030803),NCET(04-0275),The Ph.D.Programs Foundation (MOE,20100041110016),and the‘‘111’’Project.References[1]Y.N.Xia,P.D.Yang,Y.G.Sun,Y.Y.Wu,B.Mayers,B.Gates,Y.D.Yin,F.Kim,H.Q.Yan,One-dimensional nanostructures:synthesis,characterization,and applications,Adv.Mater.15(2003)353–389.[2]P.X.Gao,Z.L.Wang,Mesoporous polyhedral cages and shells formed bytextured self-assembly of ZnO nanocrystals,J.Am.Chem.Soc.125(2003) 11299–11305.[3]X.D.Wang,C.J.Summers,Z.L.Wang,Large-scale hexagonal-patterned growthof aligned ZnO nanorods for nano-optoelectronics and nanosensor arrays, Nano Lett.4(2004)423–426.[4]A.Moezzi, A.M.McDonagh,M.B.Cortie,Zinc oxide particles:synthesis,properties and applications,Chem.Eng.J.185–186(2012)1–22.[5]P.Yang,H.Yan,S.Mao,R.Russo,J.Johnson,R.Saykally,N.Morris,H.J.Choi,Controlled growth of ZnO nanowires and their optical properties,Adv.Funct.Mater.12(2002)323–331.[6]W.I.Park,D.H.Kim,Metalorganic vapor-phase epitaxial growth of verticallywell-aligned ZnO nanorods,Appl.Phys.Lett.80(2002)4232–4234.[7]C.K.Xu,G.D.Xu,Y.K.Liu,G.H.Wang,A simple and novel route for thepreparation of ZnO nanorods,Solid State Commun.122(2002)175–179. [8]B.D.Yao,Y.F.Chan,N.Wang,Formation of ZnO nanostructures by a simple wayof thermal evaporation,Appl.Phys.Lett.81(2002)757–759.[9]P.G.McCormick,T.Tsuzuki,Recent developments in mechanochemicalnanoparticle synthesis,Mater.Sci.Forum.386-388(2002)377–386.[10]M.Boutonnet,J.Kizling,P.Stenius,G.Maire,The preparation of monodispersecolloidal metal particles from microemulsions,Colloids Surf.5(1982)209–225.[11]J.Eastoe,M.J.Hollamby,L.Hudson,Recent advances in nanoparticles synthesiswith reversed micelles,Adv.Colloid Interface Sci.128(2006)5–15.[12]C.M.Bender,J.M.Burlitch,D.Barber,C.Pollock,Synthesis andfluorescence ofneodymium-doped bariumfluoride nanoparticles,Chem.Mater.12(2000) 1969–1976.[13]D.V.Ravi Kumar,B.L.V.Prasad,A.A.Kulkarni,Segmentedflow synthesis of Agnanoparticles in spiral microreactor:role of continuous and dispersed phase, Chem.Eng.J.192(2012)357–368.[14]C.Zeng,C.Wang,F.Wang,Y.Zhang,L.Zhang,A novel vapor–liquid segmentedflow based on solvent partial vaporization in microstructured reactor for continuous synthesis of nickel nanoparticles,Chem.Eng.J.204–206(2012) 48–53.[15]J.Baumgard,A.-M.Vogt,U.Kragl,K.Jähnisch,N.Steinfeldt,Application ofmicrostructured devices for continuous synthesis of tailored platinum nanoparticles,Chem.Eng.J.227(2013)137–144.[16]J.Wagner,T.Kirner,G.Mayer,J.Albert,J.M.Köhler,Generation of metalnanoparticles in a microchannel reactor,Chem.Eng.J.101(2004)251–260.[17]L.Sun,W.Luan,Y.Shan,S.Tu,One-step synthesis of monodisperse Au–Agalloy nanoparticles in a microreaction system,Chem.Eng.J.189–190(2012) 451–455.[18]A.Knauer,A.Thete,S.Li,H.Romanus,A.Csáki,W.Fritzsche,J.M.Köhler,Au/Ag/Au double shell nanoparticles with narrow size distribution obtained by continuous micro segmentedflow synthesis,Chem.Eng.J.166(2011)1164–1169.[19]D.Jeevarathinam,A.K.Gupta,B.Pitchumani,R.Mohan,Effect of gas and liquidflowrates on the size distribution of barium sulfate nanoparticles precipitated in a two phaseflow capillary microreactor,Chem.Eng.J.173(2011)607–611.[20]L.Du,Y.J.Wang,Y.C.Lu,G.S.Luo,Preparation of highly purified b-tricalciumphosphate ceramics with a microdispersion process,Chem.Eng.J.221(2013) 55–61.[21]S.Li,S.Meierott,J.M.Köhler,Effect of water content on growth and opticalproperties of ZnO nanoparticles generated in binary solvent mixtures by micro-continuousflow synthesis,Chem.Eng.J.165(2010)958–965.[22]A.K.Yadav,M.J.Barandiaran,J.C.de la Cal,Synthesis of water-borne polymernanoparticles in a continuous microreactor,Chem.Eng.J.198–199(2012) 191–200.[23]X.Chen,M.Arruebo,K.L.Yeung,Flow-synthesis of mesoporous silicas andtheir use in the preparation of magnetic catalysts for Knoevenagel condensation reactions,Catal.Today204(2013)140–147.[24]L.Yu,Y.Pan, C.Wang,L.Zhang,A two-phase segmented microfluidictechnique for one-step continuous versatile preparation of zeolites,Chem.Eng.J.219(2013)78–85.[25]A.Günther,M.Jhunjhunwala,M.Thalmann,Martin A.Schmidt,Klavs F.Jensen,Micromixing of miscible liquids in segmented gas-liquidflow,Langmuir21 (2005)1547–1555.[26]N.Harries,J.R.Burns, D.A.Barrow, C.Ramshaw,A numerical model forsegmentedflow in a microreactor,Int.J.Heat Mass Transfer46(2003)3313–3322.[27]N.Jongen,J.Lemairte,P.Bowen,H.Hofmann,Oxalate precipitation using anew tubular plug-flow reactor,in:The proceedings of the5th world congress of,chemical engineering,1996,pp.31–36.[28]C.K.Srikanth,P.Jeevanandam,Effect of anion on the homogeneousprecipitation of precursors and their decomposition to zinc oxide,J.Alloys Compd.486(2009)677–684.[29]Y.T.Qian,Introduction to Crystal Chemistry,University of Science andTechnology of China Press,Hefei,2005.[30]X.M.Hou,F.Zhou,W.M.Liu,A facile low-cost synthesis of ZnO nanorods via asolid-state reaction at low temperature,Mater.Lett.60(2006)3786–3788.Y.Wang et al./Chemical Engineering Journal235(2014)191–197197。
PEI纳米颗粒基因转染技术方法.
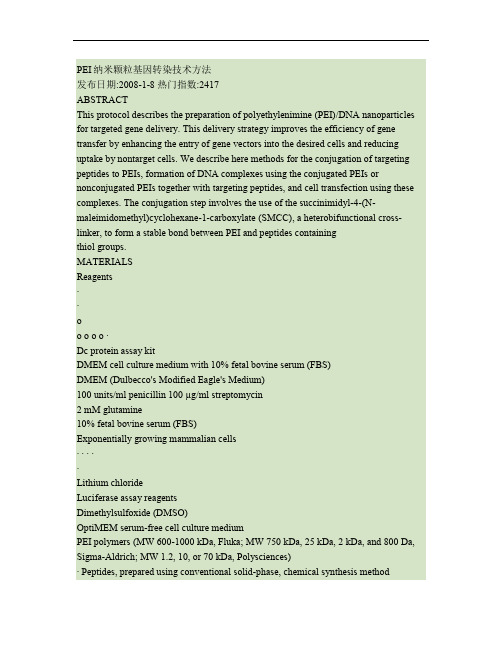
PEI纳米颗粒基因转染技术方法发布日期:2008-1-8 热门指数:2417ABSTRACTThis protocol describes the preparation of polyethylenimine (PEI)/DNA nanoparticles for targeted gene delivery. This delivery strategy improves the efficiency of gene transfer by enhancing the entry of gene vectors into the desired cells and reducing uptake by nontarget cells. We describe here methods for the conjugation of targeting peptides to PEIs, formation of DNA complexes using the conjugated PEIs or nonconjugated PEIs together with targeting peptides, and cell transfection using these complexes. The conjugation step involves the use of the succinimidyl-4-(N-maleimidomethyl)cyclohexane-1-carboxylate (SMCC), a heterobifunctional cross-linker, to form a stable bond between PEI and peptides containingthiol groups.MATERIALSReagents∙∙oo o o o ∙Dc protein assay kitDMEM cell culture medium with 10% fetal bovine serum (FBS)DMEM (Dulbecco's Modified Eagle's Medium)100 units/ml penicillin 100 µg/ml streptomycin2 mM glutamine10% fetal bovine serum (FBS)Exponentially growing mammalian cells∙∙∙∙∙Lithium chlorideLuciferase assay reagentsDimethylsulfoxide (DMSO)OptiMEM serum-free cell culture mediumPEI polymers (MW 600-1000 kDa, Fluka; MW 750 kDa, 25 kDa, 2 kDa, and 800 Da, Sigma-Aldrich; MW 1.2, 10, or 70 kDa, Polysciences)∙ Peptides, prepared using conventional solid-phase, chemical synthesis method∙oPhosphate buffered saline (PBS)137 mM NaClo o o2.7 mM KCl 10 mM Na2HPO4 2 mM KH2PO4To prepare 1 liter of PBS(Phosphate-buffered Saline), dissolve 8 g of NaCl, 0.2 g of KCl, 1.44 g of Na2HPO4, and 0.24 g of KH2PO4 in 800 ml of distilled H2O. Adjust the pH to 7.4 (or 7.2 if required) with HCl. Add H2O to 1 liter. Dispense the solution into aliquots and sterilize them by autoclaving for 20 minutes at 15 psi (1.05 kg/cm) on liquid cycle or by filter sterilization. Store the buffer at room temperature. If necessary, PBS may be supplemented with 1 mM CaCl2 and 0.5 mM MgCl2. Can bemade as a 10x stock.∙∙∙Plasmid DNA encoding the luciferase reporter geneReporter Lysis Buffer, 5X (Promega), dilute to 1X in PBSSuccinimidyl-4-(N-maleimidomethyl)cyclohexane-1-carboxylate (SMCC)∙ Water, ultrapure sterilized Equipment∙ Dialysis membranes (molecular weight size exclusion specification for purification of sidereaction and excess products)∙∙∙∙∙Freeze dryerLuminometerMagnetic stirrer and magnetic rodReaction vesselTissue culture vesselsMETHODActivation of PEI with a cross-linker1.Prepare a SMCC stock solution of 50 mM in DMSO. SMCC is moisture sensitive. The stocksolution should be prepared using high-quality anhydrous DMSO in a dry nitrogen atmosphere. When stored at 4°C, the SMCC solution remains stable for ~3 months. Steps 1-10 should be performed in achemical fume hood following chemical safe handling procedures.2.Prepare a 10 mg/ml stock solution of PEI in DMSO. Add 2-5 mg of lithium chloride to increasethe solubility of PEI.3. Using a syringe, slowly add the SMCC solution into the PEI solution. Incubate the reaction for2 hours at room temperature. The amount of SMCC solution added should be based on the desiredmolar ratio between SMCC to PEI.4. Purify the modified PEI by dialysis against ultrapure water for 2 days, changing the water atleast five times a day.5. Collect the solution in a dialysis tube and freeze dry the sample.Conjugation of peptide to activated PEI6.7.8. Prepare a peptide stock solution of 20-50 mM in PBS. Prepare a 10 mg/ml stock solution of the activated PEI (Step 5) in PBS. Slowly add the peptide solution to the activated PEI solution. Incubate the conjugationreaction for 24 hours at room temperature.The amount of the peptide added to the reaction should be based on the desired molar ratio in the finalconjugate.9. Purify the peptide-conjugated PEI by dialysis against ultrapure water for 2 days, changing thewater at least five times a day.10. Collect the solution into a dialysis tube and freeze dry the sample.Preparation of PEI/DNA complexes11.i.ii.iii. Prepare the stock solutions. Prepare a 1 mg/ml plasmid DNA stock solution in ultrapure water. Prepare a stock solution of PEI (Step 5) or peptide-conjugated PEI (Step 10) to contain 10 nmol amino nitrogen per microliter in ultrapure water (pH 7.2). For ternary complexes, prepare a 5-mg/ml stock solution of a targeting peptidelinked with a DNA-binding sequence in ultrapure water.Steps 11-22 should be performed under aseptic conditions using sterile reagents. Manipulation of thecomplexes should be performed at room temperature in a horizontal flow hood.12.i.. Prepare the working solutions. Dilute 1 µg of plasmid DNA (for transfection of cells seeded in a well of a 24-well plate) in 50 µl of OptiMEM serum-free cell culture medium. Dilute the appropriate quantity of PEI or peptide-conjugated PEI in 50 µl of OptiMEMserum-free cell culture medium.ii. For ternary complexes, dilute the appropriate quantity of the targeting peptide in 50 µl of OptiMEM serum-free cell culture medium.13. Add the peptide-conjugated PEI solution dropwise into the DNA solution while vortexing. Or,for ternary complexes, add the targeting peptide dropwise into the DNA solution while vortexing.14. Incubate the mixture for 30 minutes at room temperature. The peptide-conjugated PEI/DNAcomplexes may now be used directly for transfection (Step 16)15. To form ternary complexes, add the PEI solution dropwise into the targeting peptide/DNAcomplexes while vortexing. Incubate the ternary complexes for 30 minutes at room temperature.The ternary complexes may now be used directly for transfection (Step 16) Transfection assay16. One day before transfection, harvest mammalian cells, grown in DMEM complete cell culturemedium with 10% FBS by trypsinization, and replate them into 24-well plates at a density of 50,000cells/well. Incubate the cultures for 24 hours at 37°C in a humidified incubator with 5% CO2.17.18. Remove the medium from the wells and wash the cells twice with PBS (prewarmed to 37°C). Add the following to the cells, and incubate them for 4 hours at 37°C in a humidified incubatorwith 5% CO2. 100-150 µl/well of OptiMEM serum-free cell culture medium 100-150 µl/well of the genetransfection complex containing 1 µg of plasmid DNA (Step 14 or Step 15)19. Remove the transfection solution, wash the cells twice with PBS (prewarmed to 37°C) andadd 1 ml/well of DMEM complete cell culture medium with 10% FBS. Incubate the cells for 24-48hours.20. To assay for luciferase expression, lyse the cells by adding 100 µl/well of 1X Reporter LysisBuffer (dilute 5X stock solution with PBS).21. To detect luciferase activity, add 20 µl of cell lysate to 100 µl of luciferase assay reagent.Measure luciferase activity with a luminometer.22. To normalize the luciferase activity, determine the protein concentrations of the cell lysatesusing the Dc protein assay kit.ACKNOWLEDGMENTSThe work was funded by the Institute of Bioengineering and Nanotechnology, the Agency for Science,Technology and Research (A* STAR) in Singapore.Anyone using the procedures in this protocol does so at their own risk. Cold Spring Harbor Laboratory makes norepresentations or warranties with respect to the material set forth in this protocol and has no liability in connection with the use of these materials. Materials used in this protocol may be considered hazardous and should be used with caution. For a full listing of cautions regarding these material, please consult:Gene Transfer: Delivery and Expression of DNA and RNA, A Laboratory Manual, edited by Theodore Friedmann and JohnRossi, © 2007 by Cold Spring Harbor Laboratory Press, Cold Spring Harbor, New York, p. 473-478。
构建下转换荧光-适配体的免疫层析试纸条用于快速检测黄曲霉毒素B_(1)
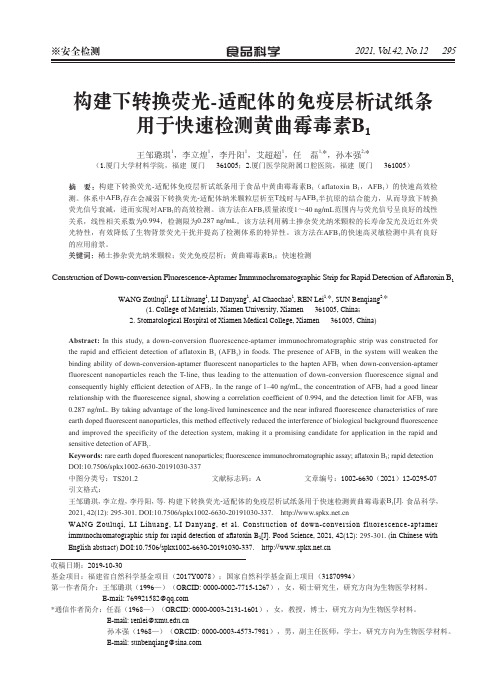
构建下转换荧光-适配体的免疫层析试纸条用于快速检测黄曲霉毒素B1王邹璐琪1,李立煌1,李丹阳1,艾超超1,任磊1,*,孙本强2,*(1.厦门大学材料学院,福建厦门361005;2.厦门医学院附属口腔医院,福建厦门361005)摘 要:构建下转换荧光-适配体免疫层析试纸条用于食品中黄曲霉毒素B1(aflatoxin B1,AFB1)的快速高效检测。
体系中AFB1存在会减弱下转换荧光-适配体纳米颗粒层析至T线时与AFB1半抗原的结合能力,从而导致下转换荧光信号衰减,进而实现对AFB1的高效检测。
该方法在AFB1质量浓度1~40 ng/mL范围内与荧光信号呈良好的线性关系,线性相关系数为0.994,检测限为0.287 ng/mL。
该方法利用稀土掺杂荧光纳米颗粒的长寿命发光及近红外荧光特性,有效降低了生物背景荧光干扰并提高了检测体系的特异性。
该方法在AFB1的快速高灵敏检测中具有良好的应用前景。
关键词:稀土掺杂荧光纳米颗粒;荧光免疫层析;黄曲霉毒素B1;快速检测Construction of Down-conversion Fluorescence-Aptamer Immunochromatographic Strip for Rapid Detection of Aflatoxin B1 WANG Zouluqi1, LI Lihuang1, LI Danyang1, AI Chaochao1, REN Lei1,*, SUN Benqiang2,*(1. College of Materials, Xiamen University, Xiamen361005, China;2. Stomatological Hospital of Xiamen Medical College, Xiamen361005, China)Abstract: In this study, a down-conversion fluorescence-aptamer immunochromatographic strip was constructed for the rapid and efficient detection of aflatoxin B1 (AFB1) in foods. The presence of AFB1 in the system will weaken the binding ability of down-conversion-aptamer fluorescent nanoparticles to the hapten AFB1 when down-conversion-aptamer fluorescent nanoparticles reach the T-line, thus leading to the attenuation of down-conversion fluorescence signal and consequently highly efficient detection of AFB1. In the range of 1–40 ng/mL, the concentration of AFB1 had a good linear relationship with the fluorescence signal, showing a correlation coefficient of 0.994, and the detection limit for AFB1 was0.287 ng/mL. By taking advantage of the long-lived luminescence and the near infrared fluorescence characteristics of rareearth doped fluorescent nanoparticles, this method effectively reduced the interference of biological background fluorescence and improved the specificity of the detection system, making it a promising candidate for application in the rapid and sensitive detection of AFB1.Keywords: rare earth doped fluorescent nanoparticles; fluorescence immunochromatographic assay; aflatoxin B1; rapid detection DOI:10.7506/spkx1002-6630-20191030-337中图分类号:TS201.2 文献标志码:A 文章编号:1002-6630(2021)12-0295-07引文格式:王邹璐琪, 李立煌, 李丹阳, 等. 构建下转换荧光-适配体的免疫层析试纸条用于快速检测黄曲霉毒素B1[J]. 食品科学, 2021, 42(12): 295-301. DOI:10.7506/spkx1002-6630-20191030-337. WANG Zouluqi, LI Lihuang, LI Danyang, et al. Construction of down-conversion fluorescence-aptamer immunochromatographic strip for rapid detection of aflatoxin B1[J]. Food Science, 2021, 42(12): 295-301. (in Chinese with English abstract) DOI:10.7506/spkx1002-6630-20191030-337. 收稿日期:2019-10-30基金项目:福建省自然科学基金项目(2017Y0078);国家自然科学基金面上项目(31870994)第一作者简介:王邹璐琪(1996—)(ORCID: 0000-0002-7715-1267),女,硕士研究生,研究方向为生物医学材料。
植物介导金属纳米颗粒合成的研究进展
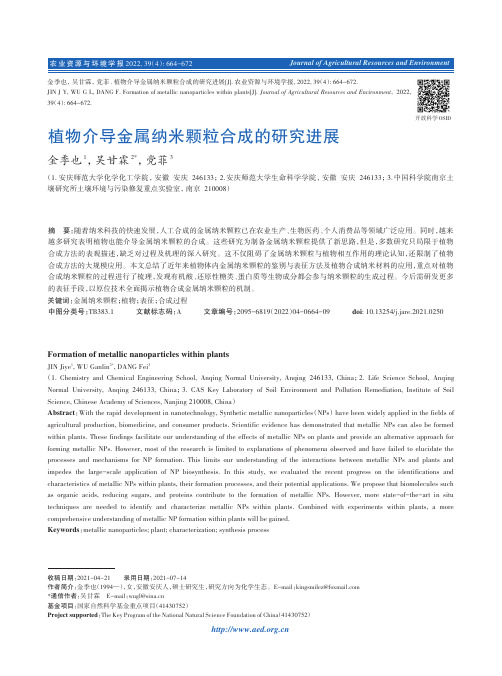
Formation of metallic nanoparticles within plantsJIN Jiye 1,WU Ganlin 2*,DANG Fei 3(1.Chemistry and Chemical Engineering School,Anqing Normal University,Anqing 246133,China ;2.Life Science School,Anqing Normal University,Anqing 246133,China ;3.CAS Key Laboratory of Soil Environment and Pollution Remediation,Institute of Soil Science,Chinese Academy of Sciences,Nanjing 210008,China )Abstract :With the rapid development in nanotechnology,Synthetic metallic nanoparticles (NPs )have been widely applied in the fields of agricultural production,biomedicine,and consumer products.Scientific evidence has demonstrated that metallic NPs can also be formed within plants.These findings facilitate our understanding of the effects of metallic NPs on plants and provide an alternative approach for forming metallic NPs.However,most of the research is limited to explanations of phenomena observed and have failed to elucidate the processes and mechanisms for NP formation.This limits our understanding of the interactions between metallic NPs and plants and impedes the large-scale application of NP biosynthesis.In this study,we evaluated the recent progress on the identifications and characteristics of metallic NPs within plants,their formation processes,and their potential applications.We propose that biomolecules such as organic acids,reducing sugars,and proteins contribute to the formation of metallic NPs.However,more state-of-the-art in situ techniques are needed to identify and characterize metallic NPs within bined with experiments within plants,a morecomprehensive understanding of metallic NP formation within plants will be gained.Keywords :metallic nanoparticles;plant;characterization;synthesis process植物介导金属纳米颗粒合成的研究进展金季也1,吴甘霖2*,党菲3(1.安庆师范大学化学化工学院,安徽安庆246133;2.安庆师范大学生命科学学院,安徽安庆246133;3.中国科学院南京土壤研究所土壤环境与污染修复重点实验室,南京210008)收稿日期:2021-04-21录用日期:2021-07-14作者简介:金季也(1994—),女,安徽安庆人,硕士研究生,研究方向为化学生态。
Nanoparticle Microreactor Application to Synthesis Of Titania by Thermal Decomposition
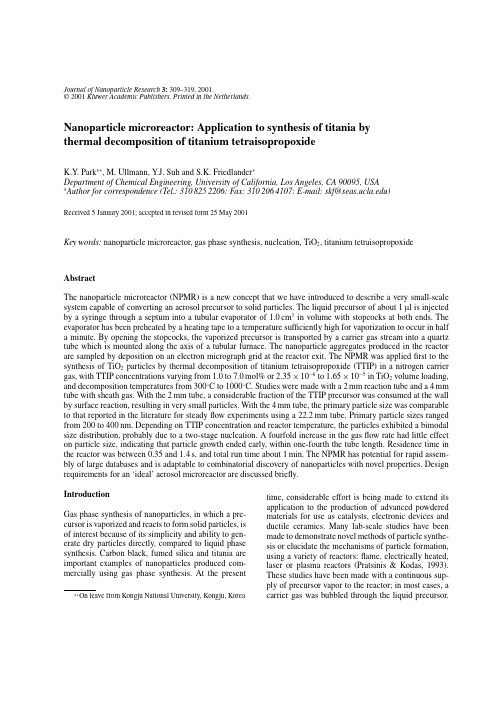
Journal of Nanoparticle Research3:309–319,2001.©2001Kluwer Academic Publishers.Printed in the Netherlands.Nanoparticle microreactor:Application to synthesis of titania bythermal decomposition of titanium tetraisopropoxideK.Y.Park∗∗,M.Ullmann,Y.J.Suh and S.K.Friedlander∗Department of Chemical Engineering,University of California,Los Angeles,CA90095,USA∗Author for correspondence(Tel.:3108252206;Fax:3102064107;E-mail:skf@)Received5January2001;accepted in revised form25May2001Key words:nanoparticle microreactor,gas phase synthesis,nucleation,TiO2,titanium tetraisopropoxide AbstractThe nanoparticle microreactor(NPMR)is a new concept that we have introduced to describe a very small-scale system capable of converting an aerosol precursor to solid particles.The liquid precursor of about1µl is injected by a syringe through a septum into a tubular evaporator of1.0cm3in volume with stopcocks at both ends.The evaporator has been preheated by a heating tape to a temperature sufficiently high for vaporization to occur in half a minute.By opening the stopcocks,the vaporized precursor is transported by a carrier gas stream into a quartz tube which is mounted along the axis of a tubular furnace.The nanoparticle aggregates produced in the reactor are sampled by deposition on an electron micrograph grid at the reactor exit.The NPMR was appliedfirst to the synthesis of TiO2particles by thermal decomposition of titanium tetraisopropoxide(TTIP)in a nitrogen carrier gas,with TTIP concentrations varying from1.0to7.0mol%or2.35×10−6to1.65×10−5in TiO2volume loading, and decomposition temperatures from300◦C to1000◦C.Studies were made with a2mm reaction tube and a4mm tube with sheath gas.With the2mm tube,a considerable fraction of the TTIP precursor was consumed at the wall by surface reaction,resulting in very small particles.With the4mm tube,the primary particle size was comparable to that reported in the literature for steadyflow experiments using a22.2mm tube.Primary particle sizes ranged from200to400nm.Depending on TTIP concentration and reactor temperature,the particles exhibited a bimodal size distribution,probably due to a two-stage nucleation.A fourfold increase in the gasflow rate had little effect on particle size,indicating that particle growth ended early,within one-fourth the tube length.Residence time in the reactor was between0.35and1.4s,and total run time about1min.The NPMR has potential for rapid assem-bly of large databases and is adaptable to combinatorial discovery of nanoparticles with novel properties.Design requirements for an‘ideal’aerosol microreactor are discussed briefly.IntroductionGas phase synthesis of nanoparticles,in which a pre-cursor is vaporized and reacts to form solid particles,is of interest because of its simplicity and ability to gen-erate dry particles directly,compared to liquid phase synthesis.Carbon black,fumed silica and titania are important examples of nanoparticles produced com-mercially using gas phase synthesis.At the present ∗∗On leave from Kongju National University,Kongju,Korea time,considerable effort is being made to extend its application to the production of advanced powdered materials for use as catalysts,electronic devices and ductile ceramics.Many lab-scale studies have been made to demonstrate novel methods of particle synthe-sis or elucidate the mechanisms of particle formation, using a variety of reactors:flame,electrically heated, laser or plasma reactors(Pratsinis&Kodas,1993). These studies have been made with a continuous sup-ply of precursor vapor to the reactor;in most cases,a carrier gas was bubbled through the liquid precursor.310Figure 1.Concept of nanoparticle microreactor (precursor vapor is indicated in gray).This method provides reliable data in steady state oper-ation.However,it is less satisfactory for very small volumes of precursor and may be too time-consuming for rapid searching of product properties for new mate-rials and varying process conditions.The search can be made more efficient by using small-scale reactors with short run time.An idea is to have a small volume of precursor vapor converted to particles,ideally under conditions of uniform temperature,concentration and residence time.In the present work,a nanoparticle microreactor (NPMR)was developed which can accept a micro-liter of precursor and complete a run within a minute.Figure 1shows the concept of the microreactor.The liquid precursor is injected into an evaporator,1cm 3in volume and vaporized.Then,the precursor vapor is transported by a carrier gas to the reactor as a bolus,similar to a pulse injection.The reaction volume of the vapor is as small as 1cm 3and the reaction time is only a few seconds.Because of the small system size,NPMR operating conditions can easily and quickly be varied to produce large databases relating product prop-erties (for example,particle size and crystal structure),to precursor properties and process conditions.These databases should be useful for discovery of nanopar-ticles with novel properties.This is an application of the combinatorial approach,which the pharmaceuti-cal industry uses for the rapid synthesis and screen-ing of new drug candidates (Dagani,1999).Another advantage of the NPMR is that chemical consumption is smaller,producing fewer pollutants.The NPMR was tested on the synthesis of TiO 2par-ticles from titanium tetraisopropoxide (TTIP)over the reaction temperature from 300◦C to 1000◦C,using two reaction tubes:a simple 2mm tube and a 4mm tubewith sheath gas entry.Earlier studies of TiO 2from TTIP using tubular reactors have been made by Kirkbir and Komiyama (1987),Okuyama et al.(1986)and Jang and Friedlander (1998).In these studies,however,the reaction tubes were an order of magnitude larger,13–22.2mm in diameter,and the precursor was trans-ported to the reactor continuously by a carrier gas bub-bled through a bottle containing liquid TTIP.Another difference is in the concentration of TTIP;in the present study concentration ranged from 1.0to 7.0mol%,much higher than those of previous studies ranging from 0.00136to 1.34mol%.A concentration of 7.0mol%is in the range typical of silica flame synthesis in indus-trial reactors (Ulrich,1971);data in commercial reac-tors for TiO 2were not available to us.The production of TiO 2by thermal decomposition of TTIP was exper-imentally validated earlier at a temperature higher than 250◦C (Komiyama et al.,1984).We assume that the solid decomposition product of the present study made at 300–1000◦C is TiO 2.In the present paper,the particle size was chosen for discussion,out of various product properties.The effects of tube size,TTIP concentration,reactor temperature and residence time on the primary particle size were investigated.The particle sizes were compared with those of Kirkbir and Komiyama (1987),who bubbled helium through the liquid precursor and passed the mixed vapors through a 22.2mm reaction tube.Our goal was to study the effect of scale and batch vs.continuous operation on product properties.Experimental sectionNanoparticle microreactor systemFigure 2shows a schematic diagram of the microreac-tor system which consists of an oxygen trap (Hewlett-Packard,Model HP3150-0528),a drying column (Hammond,Model 27066)a carrier gas preheater,an evaporator,a tubular furnace (Thermolyne,Model 21100)and a particle collector.The preheater is a pyrex cylinder wrapped with a heating coil,with a volume of 100cm 3selected to give a residence time of 3min at the carrier gas rate of 34cm 3/min.The carrier gas is heated by the preheater to a temperature higher by about 20◦C than the evaporation temperature to protect the vapor generated in the evaporator from being condensed by the incoming carrier gas.The evaporator is a pyrex tube with stopcocks at both ends,measuring 0.5cm I.D.and 5cm long.A septum is placed in the center for injection of liquid precursor by a syringe.The evaporator was311Figure 2.Schematic drawing of nanoparticle microreactorsystem.Figure 3.Two types of reaction tube used in the present study.wrapped with a heating coil,and the temperature mon-itored by a thermocouple inserted through the septum.The evaporator was heated to a predetermined temper-ature before evaporation began.To start the evapora-tion,the two stopcocks were closed and the precursor injected by a syringe.By opening the stopcocks simul-taneously,a bolus of the precursor vapor is transported to the reactor by the carrier gas.During evaporation,the carrier gas bypasses the evaporator through the three-way stopcock on the right hand side.The reactor is a quartz tube 45cm long,mounted along the axis of an electric furnace.Figure 3shows the two reaction tubes used in our study.In the case of the 2mm tube,one end is connected to the evaporator and the other end to the particle collector by O-ring ball joints.The distance from the evaporator outlet to the furnace inlet is about 10cm.For the 4mm tube withsheath gas,a 1/4-inch stainless steel union cross was added for the introduction of sheath gas,between the evaporator and the furnace (Figure 4).The sheath gas preheated in a heating pipe comes from the bottom of the union cross,turns to the right and passes through a 80mesh screen,and enters the 4mm tube to form a sheath layer outside the TTIP stream leaving the 2mm inner tube.The union cross is wrapped with a heating tape and a thermocouple is installed to measure the sheath gas temperature.At the reactor exit,a transmission electron microscopy (TEM)grid about 3mm in diameter was mounted on a stainless steel tube and inserted into the center of the aerosol stream.Particle deposition took place probably by diffusion to the surface of the grid from the gas flowing along the axis of the reactor tube.After completion of a run (about 1min)the grid holding tube was removed through an O-ring.Experimental procedureNitrogen (99.99%)was passed through the oxygen trap and dryer in series and split into two streams:one to the carrier gas preheater and the other to the sheath gas preheater.The flow rate of each stream was mea-sured by a rotameter before the preheater.The sheath gas flow rate was three times the carrier gas flow rate to keep the linear velocity of each stream the same at the entrance to the reaction tube.The carrier gas was preheated to 170◦C in the preheater and passed through the evaporator with the stopcocks open for about312Figure 4.Illustration of sheath gas entry section.Inside the union cross,a 2mm stainless steel tube,64mm in length and 0.2mm in thickness,is installed extending into the 4mm reaction tube by 25mm.30min until the evaporator was purged and heated to 152◦C,10◦C higher than the saturation temperature at the maximum TTIP concentration of 7mol%.Then,the stopcocks were closed and a predetermined vol-ume of TTIP was injected into the evaporator by a 1µl syringe (SGE,Model SG-000500).The TTIP was of ultra high purity (99.999%,Sigma-Aldrich).The vol-ume of TTIP required for a concentration of 7mol%in the reactor gas flow was 0.7µl.The concentration was controlled by the injection volume of TTIP.The time to vaporize the TTIP was estimated to be 53s,assuming that the 1mm TTIP droplet remaining suspended from the tip of the syringe during the entire period of evaporation.In reality,the drop may fall to the evaporator wall during heating,due to the decrease of surface tension.Based on the estimate,the residence time in the evaporator was varied from 5to 30and 60s,with the reactor temperature at 700◦C.Particle size was smaller with a residence time of 5s indicating the time is too short for complete vaporization.There was no difference in particle size for residence times between 30and 60s;therefore,the evaporation time was kept at 30s.The stopcocks were opened immediately after evap-oration to transport the TTIP vapor to the reactor which had already been heated to a predetermined temperature.The power to the heating tape wrap-ping the transport line was controlled to maintain the vapor temperature at about 170◦C,well above theTable 1.Operating conditions Operating parameterFor 2mm For 4mm tube tube with sheath gas TTIP conc.(mol%)7.0 1.0–7.0N 2carrier flow rate 34.017.0–68.0(cm 3/min)N 2sheath flow rate0.51.0–204.0(cm 3/min)Space time at STP (s) 2.21.1–4.4Reactor temp.(◦C)500–1000300–700Evaporator volume:1.0cm 3Evaporator temperature:152◦C Evaporation time:30sOperating pressure:101.3kPasaturation temperature.The operating conditions for the experiments are shown in Table 1.At the exit from the reactor,the particles were col-lected on the carbon film coating a 200mesh nickel grid (Electron Microscopy Science,Model CF200-Ni),and examined by transmission electron microscopy (JEOL,Model JEM 100CX).The particles were present both as individual primary particles and aggregates.From an image obtained by scanning the TEM micrograph,70–200primary particles were selected and their sizes were determined to calculate the number average and Sauter mean diameters using a computer program in which the number of pixels occupied by a particle is counted and converted into a diameter.The Sauter mean313diameter,D 32is defined asN i d 3i / N i d 2i ,where N i is the number of particles of diameter d i .It was used earlier by Kirkbir and Komiyama (1987)and employed for comparison purposes.Results and discussion Two millimeter reaction tubeFigure 5shows the change in primary particle size for the 2mm reaction tube,as the reactor tempera-ture was increased from 500◦C to 700◦C and 1000◦C.A constant temperature zone about 30cm long was maintained in the reaction tube.The SautermeanFigure 5.TEM images of TiO 2particles with 2mm reaction tube (N 2flow:34cm 3/min;TTIP concentration:7mol%).D 32is the Sauter mean primary particle diameter.Most of the TTIP conver-sion took place on the reactor wall.diameter of the primary particles increased with reactor temperature from 9.0nm at 500◦C to 20.6nm at 700◦C and 31.7nm at 1000◦pared to those of Kirkbir and Komiyama (1987),120nm at 500◦C and 65nm at 700◦C,our primary particle size is much smaller even though our TTIP concentration was 10times higher,and the effect of the temperature on particle size is in the opposite direction.We set out to determine the cause of the discrepancy.The TTIP concentration,initially 7mol%in the evaporator,decreases due to dispersion as the bolus moves from the evaporator to the reactor.By a rough calculation,the dispersion must have affected the parti-cle size to some extent,but was probably not the critical factor causing the discrepancy.After the run,inspec-tion of the wall of the 2mm tube showed a zone coated with what was probably TiO 2.At a reactor tempera-ture of 500◦C,a coated zone 2.2cm in length formed starting at 1.2cm from the furnace inlet (Figure 6).The length of coated zone was decreased to 0.7cm by an increase of the reactor temperature to 700◦C.A considerable portion of the TTIP vapor admitted to the reaction tube probably reacted at the wall,reduc-ing the amount of TTIP available for particle forma-tion.This may be the main reason why our primary particle sizes with the 2mm reaction tube were much smaller than those of the earlier studies.As the tem-perature increased,the rate of homogeneous reaction in the gas phase increased,and the TTIP loss to the wall decreased,leading to an increase in particlesize.Figure 6.Temperature profile and location of coated zones with 2mm reaction tube.314The coalescence of colliding particles may also have played a role in the particle size increase with the tem-perature increase to 1000◦C;the collision-coalescence mechanism described earlier by our group (Windeler et al.,1997)predicts significant coalescence at this tem-perature.At a reaction temperature of 1000◦C,another zone coated with black carbonaceous materials formed,probably by decomposition of propylene,a byproduct of TTIP decomposition.The leaf-like features seen in the TEM micrograph at 1000◦C (Figure 5c)may be the carbonaceous materials.Four millimeter reaction tube with sheath gas To reduce the surface-reaction effect,the 2mm reac-tion tube was replaced by a 4mm tube with sheath gas entry.As shown in Figure 3,sheath nitrogenwasFigure 7.Effect of reactor temperature on particle morphology for 4mm reaction tube with sheath gas (N 2carrier gas:34cm 3/min;TTIP concentration:7mol%).introduced to protect the wall from being coated by surface reaction.The carrier gas flow rate was kept the same as with the 2mm tube.The sheath gas rate was controlled such that its average linear velocity was the same as that of the TTIP stream leaving the inner 2mm tube.After a run,no coated zone was seen.After a few more runs,a coated zone became visible indicating that the surface reaction at the wall was not eliminated completely.Kirkbir and Komiyama (1987)reported earlier that a coated zone formed even with a much larger tube,22mm in diameter,in the absence of sheath gas.The precursor loss to some extent by surface reaction seems to be unavoidable in laboratory-scale reactors.In the present study,it was difficult to measure the loss because of the small volume of precursor admitted to the reactor.Figure 7shows the TEM micrographs of parti-cles produced with reactor temperatures varying from315400◦C to 1000◦C,holding the TTIP concentration at 7mol%and the carrier gas rate at 34cm 3/min.At tem-peratures higher than 500◦C,the particle size showed a bimodal distribution:one group of larger spheri-cal particles,250–650nm in diameter and the other group of chain-like aggregates composed of 15–20nm particles.At 400◦C,however,those chain aggregates disappeared,indicating that the aggregates were gen-erated between 400◦C and 500◦C.The cracks seen around the particles at 400◦C (Figure 7a)formed in a few seconds after the TEM grid was placed under an illumination of electron beam for exam-ination.Some unconsolidated materials may have deposited around the particles and undergone a struc-tural change under the beam to develop a stress result-ing in the formation of the cracks.Figure 8shows the effect of TTIP concentration on particle mor-phology.The concentration was varied from 7to 3.5and 1.0mol%,keeping the reactortemperatureFigure 8.Effect of TTIP concentration on particle morphology for 4mm reaction tube with sheath gas (N 2carrier gas:34cm 3/min;Reactor temperature:700◦C).constant at 700◦C and the carrier gas flow rate at 34cm 3/min.As the concentration was reduced from 7to 3.5mol%,the length and the number of the aggre-gates decreased markedly.The chain aggregates finally disappeared as the concentration was further reduced to 1mol%.The bimodal size distribution has not been reported in previous studies,which were performed at TTIP concentrations much lower than in the present study and with larger reaction tubes.To elucidate the cause of the bimodal distribution,it may be necessary to understand the mechanism by which the decompo-sition occurs.The overall reaction can be repre-sented by Ti (OC 3H 7)4=TiO 2+4C 3H 6+2H 2O.However,the reaction mechanism is not well known yet.By analogy to the mechanism of tetraethoxysi-lane (TEOS)decomposition (Satake et al.,1996),we assume that the decomposition of TTIP proceeds as follows by (1)β-hydride elimination of propene and316(2)polymerization:(CH 3CHCH 3O )3Ti (OCH 3CHCH 3)→(CH 3CHCH 3O )3Ti (OH )+CH 2CHCH 3(1)(CH 3CHCH 3O )3Ti (OH )+(CH 3CHCH 3O )Ti (OCH 3CHCH 3)3→(CH 3CHCH 3O )3Ti–O–Ti (OCH 3CHCH 3)3+CH 3CH (OH )CH 3(2)By successive β-hydride elimination and polymeriza-tion,the dimeric species in Eq.(2)continues to growwith its vapor pressure decreasing,and eventually leads to a stable particle or a nucleus when the vapor pressure drops below a certain level.The nucleus may not be pure TiO 2,but contain carbon and hydrogen to some extent.Once nuclei are formed,they grow by surface reaction of TTIP vapor and scavenging of the clus-ters and by coagulation as well.During the growth,residual carbon and hydrogen are removed by further decomposition to make TiO 2.The isopropyl alcohol in Eq.(2)is dehydrated to produce propene and water.TiO 2is known to catalyze the dehydration (Carrizosa &Munuera,1977).TTIP vapor decomposes at temperatures above 250◦C (Fictorie et al.,1994).Komiyama et al.(1984)reported a similar decomposition temperature.Figure 9shows the temperature profile measured at a reactor set point of 500◦C,over the transient zone where the tem-perature is on the increase.The approximate concentra-tion profile shown in the figure illustrates the discussion that follows.The TTIP vapor admitted at 200◦C to the 4mm tube starts to be heated and decomposition begins.Nucleation occurs when the gas is heated to a sufficiently high temperature.This temperatureisFigure 9.Two-stage nucleation in furnace.not known,but may be between 250◦C and 400◦C.The nuclei,then,grow as described above.When the vapor temperature reaches 400◦C,further nucleation occurs provided that a sufficient amount of TTIP vapor remains unconsumed.The larger particles in Figures 7and 8may have originated from the first nucleation and the smaller particles composing the chain aggregates from the second nucleation.The second nucleation rate may be faster than the first because of the higher temperature generating more nuclei resulting in smaller primary particles.At the TTIP concentration of 1mol%and the reactor temperature of 700◦C (Figure 8a),the second nucle-ation did not occur because the amount of TTIP left after the first nucleation and subsequent growth was not enough to generate new particles.At the reac-tor temperature of 400◦C and the TTIP concentration of 7mol%(Figure 7a),the second nucleation did not take place either because the temperature was too low,even though the TTIP concentration was high enough.In the synthesis of silicon from silane (SiH 4),Alam and Flagan (1986)reported that undesired nucleation could be avoided by controlling the temperature pro-file in the reactor.Experimental evidence that the heat-ing rate in the early stages affected particle size can also be found in the work of Park et al.(1991)on the generation of iron particles by hydrogen reduc-tion of FeCl 2vapor.Thus,the temperature profile in the transient zone must be a factor in controlling the particlesize.Figure 10.Axial temperature profiles with varying carrier gas flow rates at 700◦C for 4mm reaction tube with sheath gas.317 Figure11.Effect of carrier gasflow rate on particle size for4mm reaction tube with sheath gas(reactor temperature:700◦C;TTIP concentration:1mol%).The residence time,τ(reactor volume/volumetricflow rate at700◦C),varied from0.35to1.4s.There was no effect of residence time on primary particle size.Holding the reactor temperature at700◦C and the TTIP concentration at1mol%,the carrier gasflow rate was varied from17to68cm3/min,while main-taining the ratio of sheath to carrier gas rates at3.0. The temperature profiles with varying gasflow rates are shown in Figure10.There exist some temper-ature differences in the transient zone,between the three gasflow rates,but nearly no difference in the isothermal zone.Figure11shows that the particle size is insensitive to the variation of the gas rate or the increase of the residence time by a factor of four. This implies that the particle growth was completed within one-fourth of the tube length.A similar result was reported by Kirkbir and Komiyama(1987)who found that the variation of the residence time in the range3.8–10.2s had no effect on the particle diame-ter of TiO2produced from TTIP at300◦C.In contrast, Akhtar et al.(1991)reported that for TiO2particles generated by oxidation of TiCl4in a tubular reactor, particle size increased with increasing residence time at a reactor temperature of1123◦C.They attributed the size increase to an increase in time for coagulation. The reactor temperature of the present study may be too low for coalescence to occur;once the primary par-ticles formed,the residence time had little effect on their size.Comparison with results from a steadyflowlarger scale systemA principal goal of our study was to compare the microreactor data with results for larger scale systems. For this purpose,the primary particle sizes were com-pared with results of Kirkbir and Komiyama(1987) whose tube size was larger,22.2mm in diameter,with the precursor vapor supplied steadily to the reactor by bubbling helium through a precursor reservoir. Figure12shows the comparison for TTIP concentra-tions near1.0mol%with reactor temperatures ranging from300◦C to700◦C.The concentration indicated318parison of primary particle size for the NPMR and a larger scale system.for our data is the one at the evaporator.The actual concentration of TTIP in the reaction zone must be lower because the TTIP vapor disperses during trans-port from the evaporator to the reactor and diffuses to the sheath gas layer,on entering the reactor.At present,no quantitative information is available on the concentration decay.Figure12shows that our particle sizes were com-parable to theflow reactor data and the dependence of particle size on the temperature was similar,the parti-cle size decreasing with increasing temperature.In the gas-phase synthesis of TiO2from TTIP or TiCl4,some investigators(Suyama&Kato,1976;Jang&Jeong, 1995)reported a similar decrease in particle diame-ter with increasing temperature,while other studies (Formenti et al.,1972;Akhtar et al.,1991)showed an increase.By examining the operating temperatures at which those data were obtained,the transition temper-ature was near1100◦C.At temperatures below1100◦C, the particle size seems to be controlled by the nucle-ation rate because the temperature is probably too low for significant coalescence of aggregates.Above 1100◦C,coalescence becomes dominant,and the par-ticle size increases with increasing temperature.Sum-marizing,an important factor in the scaling of these systems is the time–temperature history as well as the concentration of the precursor vapor;if these features are similar for different aerosol reactors,the particle size of the product should be similar.Summary and conclusionsIn aerosol reactor design,the main goal is to produce particles with desired properties–primary particle size,aggregate size,crystalline state and primary par-ticle bond energies.It is generally not possible to predict particle properties fromfirst principles alone, and pilot scale studies and modeling are important in scale-up.We have introduced the concept of a small-scale‘microreactor’capable of generating particle samples on TEM grids which are easily examined for particle properties.To test this concept,we designed a miniaturized reac-tor capable of producing TiO2nanoparticles from about 1µl of TTIP in a1min run time.With a2mm reac-tion tube,a considerable fraction of the TTIP was con-sumed at the wall by surface reaction,resulting in very small particles.For a4mm tube with sheath gas,the surface reaction was reduced and the particle size was comparable to that reported earlier by other investiga-tors for steadyflow experiments with a22.2mm tube. Increasing the gasflow rate by four times had little effect on particle size,implying that particle growth had been completed within one-fourth of the tube length, also in agreement with previous work using a larger reactor.Depending on TTIP concentration and reactor temperature,particles showed a bimodal size distribu-tion probably due to a two-stage nucleation.The microreactor has potential for the rapid assem-bly of large databases and is adaptable to combinato-rial discovery of nanoparticles with novel properties. Results compare well over some ranges with a larger scale reactor.Still much work remains to be done to make the microreactor a reliable tool for predicting par-ticle properties of larger scale systems.Accounting for axial dispersion requires further study.Rapid analysis of TEM grid particle deposits is another challenge. AcknowledgementsThis research was supported by the Korea Research Foundation Program for Support for Faculty Research Abroad and by NSF Grant#CTS9911133. S.K.Friedlander is Parsons Professor of Chemical Engineering.ReferencesAkhtar K.M.,Y.Xiong&S.E.Pratsinis,1991.Vapor synthesis of titania powder by titanium tetrachloride oxidation.AIChE J. 37,1561–1570.。
Synthesis of Nanoparticles in High Temperature Ceramic Microreactors

Synthesis of Nanoparticles in High Temperature CeramicMicroreactors:Design,Fabrication and TestingKartavya Jain,Carl Wu,Sundar V.Atre,*Goran Jovanovic,Vinod Narayanan,andShoichi KimuraOregon Nanoscience and Microtechnologies Institute,Oregon State University,Corvallis,OregonVincent Sprenkle and Nathan CanfieldPacific Northwest National Laboratory,Richland,WashingtonSukumar RoyBharat Heavy Electricals Ltd.,Bangalore,IndiaMicroreactors as a novel concept in chemical technology enable the introduction of new reaction procedures in chemistry, pharmaceutical industry,and molecular biology.These miniaturized reaction systems offer many exceptional technical advantages for a large number of applications.One major application is in the bulk synthesis of nanoparticles.Despite the availability of a plethora of nanoparticle synthesis processes,there exist many difficulties in controlling the shape,size,and purity of nanoparticles in large quantities in a safe and cost-effective manner.These difficulties have been the principal factors adversely limiting the applications of ceramic nanoparticles.Recent experiments have shown that to study the process of growth and formation of nanoparticles,a reactor having much smaller dimensions,namely a microreactor is more appropriate. These studies have also shown that a microchannel reactor provides control over the mean residence time and hence over the nanoparticle size and shape.This paper deals with the design,fabrication,and testing issues related to a high temperature, ceramic microreactor by investigating the use of reactive gas streams in arrays of microchannel reactors.These innovations offerthe potential to overcome the barriers associated with synthesis of ceramic nanoparticles in large quantities.IntroductionMicroscale process engineering is the science of con-ducting chemical or physical processes(unit operations) inside small volume.These processes are usually carried out in continuousflow mode,as opposed to batch pro-duction,allowing a throughput high enough to make microscale process engineering a tool for chemical pro-duction.It involves the use of microsystems that are now available in many devices for commercial applica-tions including micromixers and microreactors as alter-native to batch production in pharmaceutical andfine chemical industry,lab-on-chip devices,microsensors, advanced rapid throughput chemical and catalyst screen-ing tools,distributed or portable power and chemical Int.J.Appl.Ceram.Technol.,6[3]410–419(2009)DOI:10.1111/j.1744-7402.2008.02285.x Ceramic Product Development and Commercialization*Sundar.Atre@r2008The American Ceramic Societyproduction,distributed heating and cooling,and even space applications.1The subfield of microscale process engineering that deals with chemical reactions,carried out in microstruc-tured reactors or microreactors,is also known as micro-reaction technology.Microreaction technology,with its unprecedented heat and mass transfer advantages as well as uniform residence time andflow pattern,is one of the few technologies with the potential to develop efficient, environmentally benign,and compact processes.It is a highly interdisciplinary research area,where chemistry, physics,and engineering merge together.It involves the use of microreactors that allow reactions to be performed at the micrometer scale.Microreactors offer many advantages for the performance of heat and mass-transfer-limited rge gradients in concentra-tion and temperature can be achieved by shrinking the characteristic dimensions of a microreactor down to the microscale.This is especially advantageous in the case of highly exothermal reactions as well as in the case of mass-transport-limited processes.The use of micro-reactors for in situ and on-demand production is gaining increasing importance as thefield of microreaction tech-nology emerges from the stage of being regarded as a theoretical concept to a technology with significant industrial applications.2While the dimensions of the individual channels are small,a microreactor can contain many thousands of such channels,and its overall size can be on the scale of meters.However,the objective of microreaction technology is not primarily to miniaturize production plants,but to increase yields and selectivities of reactions,thus reducing the cost of production.An important application of microreactors is for the synthesis of nanoparticles.3For example,nanoscale ceramic powders can significantly help in the miniatur-ization of current products and can be used for various high performance applications due to their excellent mechanical,thermal,dielectric and corrosion proper-ties.4The performance of these nanoscale ceramic pow-ders is strongly affected by particle properties,such as the particle size,the distributions of the size,and the shape.Conventionally large-scale batch reactors have been used for the synthesis of ceramic nanoparticles.5 However,the particle size distribution of nanoparticles synthesized in batch reactors often does not satisfy the requirements for many applications.Prior work has shown that the shape,size,and yield of nanoparticles are strongly influenced by the mean residence time and temperature required to produce the nanoparticles.6A microreactor provides control over the mean residence time,mixing and reaction temperature and hence over the nanoparticle size and shape.The most important advantages of a microreactor are rapid reaction times and scalable throughput of highly pure ceramic nano-particles,which is due to several microreactor features such as,high temperature gradient,short and control-lable residence time,small reactor size,and high heat transfer rates.The focus of this paper is to design and fabricate a microreactor with multiple microchannel arrays and investigate the use of reactive gas streams of silicon oxide (SiO)and ammonia(NH3)to synthesize silicon nitride (Si3N4)nanoparticles.This work also demonstrates the feasibility and effectiveness of multiple microchan-nel reactors in synthesis of nanoparticles as compared with single microchannel reactors and the use of porous alumina as a prospective ceramic material for fabricating the microreactor.It is anticipated that the principles demonstrated in this study can help overcome the bar-riers associated with the production and safe handling of nanoparticles in large quantities.Microscale Reactor vs.Macroscale Reactor It will be possible to construct a plant consisting of microreactors that is small enough to be moved from place to place in less time with low capital cost.7These portable plants can be used for on-site production of hazardous chemicals,which currently incur considerable risk to human beings and the environment.The hazard potential of strongly exothermic or explosive reactions can also be drastically reduced and higher safety can also be achieved with very less toxic substances at higher operating pressures.8Another advantage of microreac-tors is the high surface area to volume ratio due to the microchannel dimensions.The small size of these microchannels makes it easier to control the reaction parameters such as pressure,temperature,residence time,andflow rate,as compared with the large batch reactor,thus influencing reaction rate and selectivity.9 The difference between the macroscale or batch reactor and the microreactor is not just the diameter of channels but also the length of reaction zone.The mean residence time of the reactants in the reaction zone of the microreactor can be at least two orders of magnitude smaller as compared with the macroscale reactor.Addi-tionally,scale-up only involves adding more microchan-/ACT Synthesis of Nanoparticles in High Temperature Ceramic Microreactors411nels in the reactor.Owing to all of these advantages,a microreactor is a useful tool that allows for a safe and fast transfer from a microscale to pilot or production scale. Material Selection for the MicroreactorMicroreactors represent a scaled-down method to perform chemical reactions in a just-in-time fashion. Theyfind applications in a variety of sectors such as au-tomotive,aerospace,electrical,mechanical,and chemical industries.Therefore,microreactors can be generally made out of ceramics(silicon carbide,silicon nitride,alumina, titania),glass,quartz,silicon,and metals(stainless steel), as well as polymers(polydimethylsiloxane,parylene, polyimide,PMMA).1Each material has its own advanta-ges and disadvantages;however ceramics have the potential to add beneficial properties to microreactors for applica-tions involving high temperature reactions thanks to their key properties such as high chemical resistance,10hightemperature structural stability,and wear resistance.11 Based on the design and fabrication considerations and the material requirements for the microreactor,the microreactor was manufactured using ceramic alumina.Alumina is one of the most cost effective and widely used materials in the family of engineering ceramics.It possesses strong ionic inter-atomic bonding giving rise to its desirable material properties such as high hardness (11–14GPa),good thermal conductivity(27W/m1C), high temperature stability(17501C),low thermal expan-sion coefficient(8.4Â10À6/1C),and excellent dielectric thus making it the material of choice for a wide range of high temperature applications like microreactors. Basis of the WorkIn this work,the microreactor will be used to synthesize silicon nitride nanoparticles.Silicon nitride is chosen as the basis of this work because of its significance in high-temperature structural applications.It exhibits unique combination of thermal,mechanical,dielectric, and corrosion properties such as high temperature capability(10001C),high hardness(14–16GPa),good thermal conductivity(29–30W/m.K),low thermal ex-pansion coefficient(3.3Â10À6/1C),good oxidation,and wear resistance,under severe environment.12Prior work in a macroscale tubularflow reactor has identified that nanoscale particle formation is limited by diffusion between reactant and gas streams.6 The effects of mean residence time as well as the reac-tion temperature on the growth of nanosized particles were investigated.Figure1shows that the average mean particle size of Si3N4nanoparticles increases with an increase in the res-idence time of reactants in the reaction zone.The growth process may be divided into two stages:an induction stage,and a cluster growth stage.During the induction stage,the homogenous vapor-phase nucleation takes place as sequence of additions of single molecules for developing an embryo.This process leads to the forma-tion of nucleus with a radius equal to the critical nucleus radius,above which it becomes stable.Based on the ther-modynamic conditions,the critical radius for a silicon nitride nucleus to be stable and grow is0.3–0.6nm.The minimum residence time to produce particles of critical size turned out to be about6ms(refer Fig.1).This is an indication that the mean residence time achieved in the tubularflow reactor6was much larger than the residence time needed for the formation of stable clusters.So,to study the process of nanoparticle formation and growth, a reactor having smaller dimensions is more appropriate, namely,as small as those of microchannel reactors.When a microreactor is used,the mean residence time can be easily controlled upwards of0.1ms,and the average particle size can be reduced to those close to critical size.The yield of nano-sized silicon nitride powder in the tubular reactor was found to be at most 43%because of the formation of whiskers and crystals. However,the use of microreactor is expected to increase and control the residence times and yieldscalable Fig.1.Growth of average Si3N4particle size with residence time of reactant gas mixture.412International Journal of Applied Ceramic Technology—Jain,et al.Vol.6,No.3,2009throughputs of high purity nanoparticles.In addition to requiring small quantities of reagent,the microreactor having sub-millimeter reaction channels will allow for the precise control of reaction variables,such as reagent mixing,flow rates,reaction time,and heat and mass transfer which is ideal for integration with a post pro-cessing system.DesignA computer model of the microreactor and its parts was generated using commercially available 3-D CAD software package,SolidWorks.This computer drawing is at least a two-dimensional drawing and more typically a three-dimensional drawing of the different parts and fully assembled micro-reactor.Figure 2shows the 3D model of a microreactor.As seen in the Fig.2,the microreactor consists of three parts:the top plate,the bottom plate,and the extruded body.The circular array of holes in all these parts acts as microchannels through which the reactants are carried into the hot reaction zone of the microreactor,where they react to obtain the final product.These computer-generated parts of the micro-reactor were then patterned and bonded together using different microfabrication tech-niques to obtain the final microreactor.Table I shows the dimensions of all these three parts of the ceramic microreactor.This microreactor design is expected to produce silicon nitride nanoparticles with a small mean diameter and narrow size distribution as compared with the batch reactor,because it provides a uniform reaction field in which the reaction conditions can be precisely controlled.Owing to its portability and compactness,this microreactor allows for in-situ synthesis of silicon nitride nanoparticles,thus avoiding severalsafety and health concern issues related with handling of these nanoparticles.Another advantage is the low patterning cost involved,because the number of parts to pattern is reduced to just three as compared with nor-mally used 10–100parts or shims in previously reported microreactor designs and fabrication methods.13FabricationFabrication,through its role in microelectronics and optoelectronics,is an indispensable contributor to microsystems technology.It is ubiquitous in the fabri-cation of sensors,microreactors,combinatorial arrays,14microelectromechanical systems (MEMS),microanalyt-ical systems,15and micro-optical systems.Fabrication of microreactors involves different patterning and bonding techniques.The fabrication of functional models of a microreactor is very important.Processing effects that play a minor role in the macroscale cannot be neglected at the microscale regime as they may have a much larger impact due to the increased surface-to volume ratio.Ceramic microreactors like almost all ceramic compo-nents are formed in the green,unfired state by consol-idating the ceramic powder with the help of binder additives into the desired shape.Following are the steps involved in fabrication of the ceramic microreactor used in this study.PatterningConventionally,ceramic microreactors have not been used due to the costs associated with their design and development and because methods for the produc-tion of larger series have not yet been fully established.10During product development,high costs can be incurred for the fabrication of models and prototypes for design optimization.However,to speed up this process and to reduce the costs involved,different patterningtechniquesFig.2.3D model and sectional view of the microreactor created using SolidWorks.Table I.Dimensions of the Top Plate,the Bottom Plate,and the Extruded Body of the MicroreactorTop plate (mm)Bottom plate (mm)Extruded body (mm)Diameter 172727Length0.50.520Diameter of truth holes133/ACT Synthesis of Nanoparticles in High Temperature Ceramic Microreactors 413such as laser machining,micropunching,micropowder injection molding,extrusion,etching,photolithography,electro discharge machining (EDM),are nowadays available for fabricating ceramic microreactors.16,17In the microreactor used in this study,the top plate and the bottom plate were fabricated by laser machining green tape alumina at PNNL,Richland,WA.The green tape alumina used for these plates was Alcoa A-16Super Grind (Alcoa,Leetsdale,PA)with Rohm &Haas Dura-max B-1000aqueous binder (Rohm &Haas,Philadel-phia,PA).The laser used for fabricating the top and bottom plates was a CO 2laser with 35W beam power.Figure 3shows the experimental set-up of the laser ma-chining process.One repetition cut along with 28%beam power and 20%speed were used as the cutting parameters.Both these plates were then sintered with the following schedule:0.51C/min ramp to 4001C with a 1h hold followed by 3.01C/min ramp to 16001C and a 1h hold.Figures 4and 5show the top and bottom plates fabricated using this procedure.The extruded body of the microreactor was fabri-cated using alumina at BHEL,New Delhi,India.Figure 6shows the schematic representation of the extrusion process and the porous extruded body (with 50–60%porosity)obtained using this process.The reason behind using highly porous alumina is to allow the ammonia gas to diffuse into the microchannels through the pores of extruded body and react with the silicon oxide stream.All these parts were characterized using scanning electron microscopy (SEM).The SEM image of ex-truded body at Â5000magnification (refer Fig.7)confirms the presence of pores in the extruded body.Bonding and Post BondingFollowing patterning,the next step in fabricating the ceramic microreactor was the bonding of different parts together to obtain the final microreactor assembly.Many difficulties have been previously observed in bonding or joining of the ceramics due to their high melting temperature.Further,traditional methods,such as riveting,bolting,and threading,are not suitable to be applied in the joining of ceramic materials for that the stress concentration is an inevitable problem.At present,the main techniques used for bonding ceramics are diffusion bonding,metal brazing,diffusion and friction welding,adhesive bonding,and solvent welding.18TheFig.3.Experimental set-up for lasermachining.Fig.4.Top plate fabricated using lasermachining.Fig.5.Bottom plate fabricated using laser machining.414International Journal of Applied Ceramic Technology—Jain,et al.Vol.6,No.3,2009post-bonding process may be required for some designs which involve machining of excess material from the microreactor assembly.All the three parts of the microreactor,namely,the top plate,the bottom plate,and the extruded body were sinter-bonded by using an alumina paste.TestingRecently,considerable efforts have been made to obtain ceramic nanoparticles.A number of methods have been proposed to produce nanoparticles,including low-pressure chemical vapor deposition (CVD),laser-induced CVD,and thermal plasma.All of these processes result in high cost and lower quality of product.10In principle,gas phase reactions give high purity silicon nitride nanoparticles and are recognized as simple,fast,efficient,and economical method for mass-producing nanoparticles.These processes involve an evapora-tion phase,where the reactants are vaporized to react,followed by rapid cooling which leads to nucleation and growth of particles.In the present study,the ammonoly-sis process has been used to produce Si 3N 4.There are two major sources of Si to produce Si 3N 4:chlorinated silicon (SiCl 4,SiH 2Cl 4,etc.)and SiO:3SiCl 4þ16NH 3!Si 3N 4þ12NH 4Cl at T >1000 C3SiH 2Cl 2þ10NH 3!Si 3N 4þ6NH 4Cl þ6H 2;at T >600 CAs evidenced by the above reactions,when chlorinated silicon reacts with ammonia,the byproduct is ammo-nium chloride (NH 4Cl)which is in solid form and can get mixed with the silicon nitride nanoparticles.Therefore,the present work focused on the ammo-nolysis of silicon monoxide in microchannel arrays of the reactor to synthesize silicon nitride nanoparticles at elevated temperatures ranging from 13001C to 14001C.Figure 8shows the sketch of the microreactor in a hor-izontal tube furnace used to synthesize silicon nitride nanoparticles.SiO particles (produced from a mixture of silica and silicon powders)were carried in the hot reaction zone of the reactor by argon gas from the top plate of the microreactor through the inner alumina tubing.The ammonia gas was diffused through the pores and the circular array of holes on the extruded body of the reactor using the outer alumina tubing.The reaction between SiO and NH 3takes place in the hot reaction zone of the heating furnace at high temperatures (1300–14001C)to produce silicon nitride nanoparticles.These particles were collected through the outlet in a 0.5m m pore size filter paper.3SiO ðg Þþ4NH 3ðg Þ!Si 3N 4ðs Þþ3H 2O ðg Þþ3H 2ðg ÞThe silicon nitride nanoparticles (refer Fig.9)were characterized by X-ray diffraction (XRD)to confirm the chemistry.The control of key variables such as contact pattern of reactant gas,feed concentration ofammoniaFig.6.Schematic representation of the extrusion process and the extruded body fabricated using highly porousalumina.Fig.7.Scanning electron microscopy image of the extruded body at Â5000magnification./ACT Synthesis of Nanoparticles in High Temperature Ceramic Microreactors 415and SiO,residence time of reactant gas mixture in the uniform temperature zone,reaction temperature,and length of the reaction zone will provide great flexibility over the size and shape of the product.Initial studies on process effects indicate that the mean particle size increased with residence time,as measure by change in the flow rate of NH 3.In initial experiments,an increase in ammonia flow rate from 1000to 4000cm 3/min at 13501C reduced the average particle size from B 100to B 20nm.Rough estimates of the particle size distribu-tion by TEM indicate a 715%spread in any given process setting.On-going studies are focused on eluci-dating further details.An additional benefit of the present reaction chem-istry is that no solid and toxic by-products are formed when SiO reacts with ammonia,resulting in highly pure Si 3N 4nanoparticles.However,due to the high surface area,there is a tendency for the materials to oxidize,placing importance on the issue of storage and handling.It is anticipated that integrating the microreactor syn-thesis with downstream processing can help address this issue,as discussed later.Design Evaluation and Flow ModelingTable II gives a summary of the time scales relevant to the flow.Based on various parameters and time scales important conclusions can be drawn related to the potential of using this microreactor for synthesis of nanoparticles.19The residence time of SiO and NH 3reactants in the microreactor can be controlled by vary-ing the reactor length.The upper limit for the length can be set by particle agglomeration and the lower limit can be controlled by the need to form stable particle nucleus.This microreactor will provide a laminar flow environment in the mixing of the reactant streams of SiO and NH 3,resulting in a reaction zone where particle nucleation can be controlled more effectively as compared with the large-scale batch reactors.Based on the principles of kinetics and transport phenomena,CFD simulations will be used in future work to opti-mize the reactor arrangement and conditions and to better understand the performance of microreactor in synthesis of Si 3N 4nanoparticles.Initially,acommer-Fig.8.Schematic diagram of microreactor in a horizontal tube furnace for ammonolysis of SiOvapor.Fig.9.Silicon nitride nanoparticles.416International Journal of Applied Ceramic Technology—Jain,et al.Vol.6,No.3,2009cially available CFD software package such as Star/ Kinetics will be used for modeling and simulating the particle nucleation and growth and theflow of reactant streams.A more realistic2D,compressible,laminar, multicomponent,gas-particle transport simulation will be performed as the next step.Based on the value of K n in Table II it is clear that although continuumflow conditions will be valid,but the local slipflow could also alter the particle-wall interactions.The simulation offlow will allow analyzing of theflow characteristics in realistic geometries,and make it easier to improve process and reactor design.DiscussionOwing to its portability and compactness,the microreactor presented in the previous section will pro-vide a tremendous potential for process integration of the shape-forming stage.It will allow reducing the number of steps between synthesis of nanoparticles and nanoparticle shape forming,thus resolving several issues related to environmental and health safety.Fur-thermore,the amorphous silicon nitride nanoparticles are prone to oxidation when exposed to the atmosphere and have to be stored and handled in inert conditions.Table II.Summary of the Time Scales with Estimated Values for the Present Work Time scale(orratio)Typical estimates CommentsReactor residence time t res¼L= U B0.03/1505200m s; U5meanfluid velocity in reactor;L5reactor lengthAverage basis for comparingfluid,particle,andthermal time scalesLocal characteristic time t f¼l=U B0.1m s;l5local mixing layerthickness(B10m m);U5localfluid velocityLocal basis for comparingfluid,particle,andthermal time scalesSi3N4reaction time t R;Si3N4¼1=k SiO;reaction modeled aspseudo-first order,with rate coefficient(k SiO)dependence only on SiONo data available,will be determined as a part ofthe project;typically smaller than diffusion timescales in a macroreactorReactant species (gas phase) diffusion time t D;SiO=NH3¼l2=D SiO=NH3$1m s;D SiO=NH3¼binary diffusion coefficientScales as l2,the transverse length scale of thelaminar mixing layerReaction-to-diffusion scale ratio t R;Si3N4=t D;SiO=NH3Indicator of chemical to physical time—can beused to determine k SiOParticle collision time t c;p¼1=ðn p p d2p v rÞB50m s;n p5particlenumber density(1017particles/m3);v r5random relative particle velocity(100m/s);d p5particle diameter(25nm)t c;p=t res¼0:25-particle growth by collisions isminimalMomentum Stokes number, St v St v;l¼t v=t f$1;St v;L¼t v=t res<<1;t v5momentum response time(B0.1m s),relative Stokesflow assumedMomentum response time of particle iscomparable to local mixing time but muchsmaller than t resThermal Stokes number,St t St t;l¼t t=t f$1;St t;L¼t t=t res<<1;t t B0.3m s,relative Stokesflow assumedParticle attains thermal equilibrium rapidly withrespect to reactorDilute versusdenseflowst v=t c;p¼10À7=ð5Â10À5Þ¼0:002o1-diluteflow assumption is goodKnudsen number based on L and l Kn L¼l=D h¼m g=ðc r g D hÞB0.001;Kn l¼l=l¼m g=c r g l B0.03;c5speed ofsound in the gas;m g5gas viscosity;r g5gasdensityContinuumflow based D h,but slipflow based onl20Knudsen number, based on particle diameter Kn p¼l=d p¼m g=ðc r g d pÞ$13Free molecularflow around the particles-needcorrections for continuum-based models forsource/coupling terms/ACT Synthesis of Nanoparticles in High Temperature Ceramic Microreactors417Therefore,the compact size of the microreactor will allow for synthesis to be located at the point of use.Figure 10shows an example of the integration of nanoparticle synthesis with nanoparticle consolidation.The reaction product from the microreactor will be directed into a compaction press for fabricating com-ponents for further sintering.Integrating the microre-actor to a compaction press using a sliding feed shoe will allow for creating net-shaped components from nano-particles directly after synthesis.ConclusionsMicroreactors offer tremendous promise as a gen-eralized platform for portable and distributive systems for energy generation,chemical and pharmaceutical production,and environmental remediation.Despite the availability of a plethora of synthesis schemes the difficulties in controlling the reaction parameters and particle morphology have been the factors adversely limiting the applications and economics of ceramic nanoparticles.This work investigated the use of reac-tive gas streams in arrays of the microreactor as a means to overcome the barriers associated with the prior ap-proaches in the synthesis of silicon nitride nanoparticles with controlled size and shape attributes.The microreactor presented in this work has made some contributions to the field of microreaction tech-nology.In terms of design,because this microreactor is made of alumina,it is capable of working at high tem-peratures.The design also lowered the fabrication cost as the number of plates to pattern was reduced to just three as compared with normally used 10–100plates or shims in other microreactors.In terms of fabrication,the microreactor involves the use of different manufac-turing processes such as laser machining and extrusion.This work examined the use of porous alumina as a feasible material for fabricating the microreactor and also demonstrates the effectiveness of using multiple channel arrays in synthesizing ceramic nanoparticles.Finally,this work will help us to identify,understand,and remove several key barriers in materials,manufac-turing and economics of nanoparticles.Further work can be done by modifying the reactor design (e.g.,diameter of the plates,length of the reac-tion zone,and diameter of the holes),using a different heating furnace,and also by varying the key reaction parameters such as temperature,flow rate,and residence time.This work can also be further extended to produce different non-oxide ceramic nanoparticles such as,titanium nitride (TiN),silicon carbide (SiC)and aluminum nitride (AlN)by varying the reactants.AcknowledgmentThis material is based on research sponsored by Air Force Research Laboratory under agreement number FA8650-05-1-5041.The views and conclusions con-tained herein are those of the authors and should not be interpreted as necessarily representing the official poli-cies or endorsements,either expressed or implied,of Air Force Research Laboratory or the ernment.References1.H.Lowe,V.Hessel,and A.Mueller,‘‘Microreactors –Prospects Already Achieved and Possible Misuse,’’Pure Appl.Chem.,74[12]2271–2276(2002).Fig.10.Integration of bulk synthesis with nanoparticle consolidation.418International Journal of Applied Ceramic Technology—Jain,et al.Vol.6,No.3,2009。
高考总复习优化设计二轮用书英语(新高考)阅读理解 文体分类练4 说明文之发明创新类
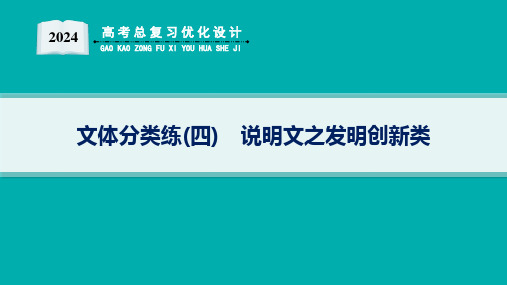
3.How does Steager feel about the future of the device?
A.Uncertain. √B.Confident.
C.Concerned. D.Surprised. 解析 推理判断题。根据最后一段可知,Steager认为这个清洁牙齿的设备从 概念到产品,还需要很多工程,但是不失为一个好的想法,故Steager对这款 产品很自信。
Passage 1 Passage 2 Passage 3
The new device is just a proof of concept.The researchers still need to turn it into a product that people will want to use.“There’s a lot of engineering to get from here to there,but every good idea needs to have a start,” says Steager.
Passage 1 Passage 2 Passage 3
4.Which of the following would be the best title? A.A Tooth-Cleaner Fighting Bacteria B.A Breakthrough in Medicine
√C.A Shape-Shifting Robotic Tooth-Cleaner
D.A New Concept for a New Start 解析 主旨大意题。通读全文,尤其是第一段以及第二段最后一句“But these bristles shape-shift to fit whatever surface they encounter.”可知,文章主 要介绍了一款纳米材料的洁牙器,在口腔中会根据具体状况变化形状。C 项“A Shape-Shifting Robotic Tooth-Cleaner (一种可以变形的机器人洁牙 器)”作标题比较贴切。
自组装丝素蛋白纳米颗粒的制备
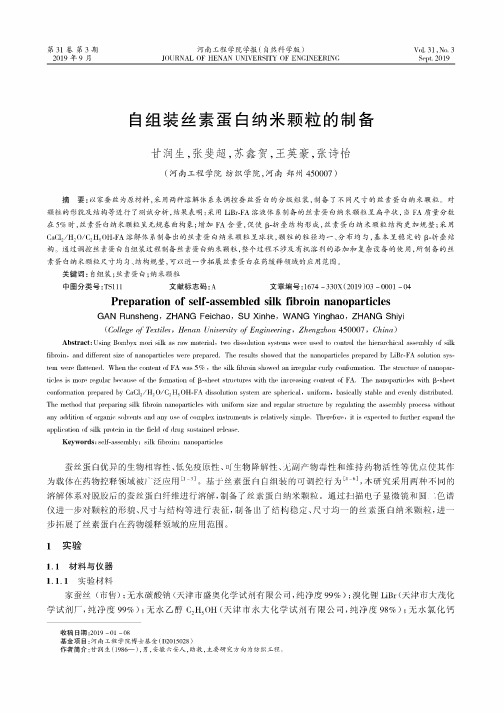
Vol. 31, No. 3Sept. 2019第31卷第3期2019年9月河南工程学院学报(自然科学版)JOURNAL OF HENAN UNIVERSITY OF ENGINEERING 自组装丝素蛋白纳米颗粒的制备甘润生,张斐超,苏鑫贺,王英豪,张诗怡(河南工程学院纺织学院,河南郑州450007)摘 要:以家蚕丝为原材料,采用两种溶解体系来调控蚕丝蛋白的分级组装,制备了不同尺寸的丝素蛋白纳米颗粒。
对 颗粒的形貌及结构等进行了测试分析,结果表明:采用LiBr-FA 溶液体系制备的丝素蛋白纳米颗粒呈扁平狀,当FA 质量分数 在5%时,丝素蛋白纳米颗粒呈无规卷曲构象;增加FA 含量,促使p-折叠结构形成,丝素蛋白纳米颗粒结构更加规整;采用 CaCl 2/H 2O/C 2H 5OH-FA 溶解体系制备出的丝素蛋白纳米颗粒呈球状,颗粒的粒径均一、分布均匀,基本呈稳定的0-折叠结 构。
通过调控丝素蛋白自组装过程制备丝素蛋白纳米颗粒,整个过程不涉及有机溶剂的添加和复杂设备的使用,所制备的丝 素蛋白纳米颗粒尺寸均匀、结构规整,可以进一步拓展丝素蛋白在药缓释领域的应用范围。
关键词:自组装;丝素蛋白;纳米颗粒中图分类号:TS111 文献标志码:A 文章编号:1674 -330X (2019)03 -0001 -04Preparation of self-assembled silk fibroin nanoparticlesGAN Runsheng, ZHANG Feichao, SU Xinhe, WANG Yinghao, ZHANG Shiyi(College of Textiles f Henan University of Engineering T Zhengzhou, 450007 ? China )Abstract : Using Bombyx moii silk as raw material, two dissolution systems were used to control the hierarchical assembly of silk fibroin, and different size of nanoparticles were prepared. Tlie results showed that tlie nanoparticles prepared by LiBr-FA solution sys tem were flattened. When the content of FA was 5% , the silk fibroin showed an irregular curly conf (>iTnation. The structure of nanopai- ticles is more regular because of the formation of p-sheet structures with the increasing content of FA. The nanoparticles with p-sheet conformation prepared by CaCl 2/H 2 0/C 2 H 5 OH-FA dissolution system are spliericaL unifonn , basically stable and evenly distributed. The metliod that preparing silk fibroin nanoparticles with uniform size and regular stiucture by regulating the assembly process without any addition of oiganic solvents and any use of complex instruments is relatively simple. Therefore, it is expected to further expand the application of silk protein in the field of drug sustained release.Keywords : self-assembly ; silk fibroin ; nanoparticles蚕丝蛋白优异的生物相容性、低免疫原性、可生物降解性、尤副产物毒性和维持约物活性等优点使其作 为载体在药物控释领域被广泛应用基于丝素蛋白自组装的可调控行为木研究采用两种不同的 溶解体系对脱胶后的蚕丝蛋白纤维进行溶解,制备了丝素蛋白纳米颗粒。
抗感染药物的研发和应用前景
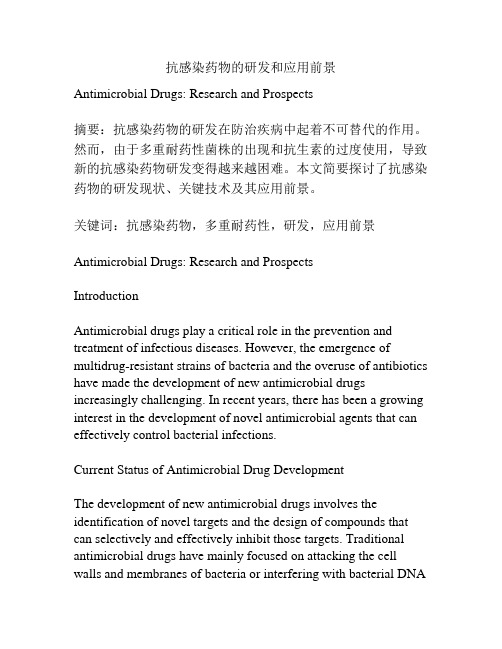
抗感染药物的研发和应用前景Antimicrobial Drugs: Research and Prospects摘要:抗感染药物的研发在防治疾病中起着不可替代的作用。
然而,由于多重耐药性菌株的出现和抗生素的过度使用,导致新的抗感染药物研发变得越来越困难。
本文简要探讨了抗感染药物的研发现状、关键技术及其应用前景。
关键词:抗感染药物,多重耐药性,研发,应用前景Antimicrobial Drugs: Research and ProspectsIntroductionAntimicrobial drugs play a critical role in the prevention and treatment of infectious diseases. However, the emergence of multidrug-resistant strains of bacteria and the overuse of antibiotics have made the development of new antimicrobial drugs increasingly challenging. In recent years, there has been a growing interest in the development of novel antimicrobial agents that can effectively control bacterial infections.Current Status of Antimicrobial Drug DevelopmentThe development of new antimicrobial drugs involves the identification of novel targets and the design of compounds that can selectively and effectively inhibit those targets. Traditional antimicrobial drugs have mainly focused on attacking the cell walls and membranes of bacteria or interfering with bacterial DNAreplication and protein synthesis. However, these approaches have become less effective due to the emergence of resistance mechanisms used by bacteria to circumvent these mechanisms.In recent years, researchers have explored new targets and developed new approaches to treat bacterial infections. These include targeting bacterial virulence factors to weaken bacterial infection and manipulating host factors to stimulate the host immune response against bacterial infections.Key Technologies in Antimicrobial Drug DevelopmentThe development of new antimicrobial drugs requires a range of technologies, including high-throughput screening, molecular docking, structure-based drug design, and combinatorial chemistry. High-throughput screening is used to identify new compounds with antimicrobial activity from large libraries of molecules. Molecular docking is used to predict the interactions between the potential compound and target protein. Structure-based drug design is used to design compounds that can selectively inhibit the target protein with minimal side effects. Combinatorial chemistry is used to generate large libraries of compounds with diverse structures and properties.Application Prospects of Antimicrobial DrugsThe application prospects of antimicrobial drugs are promising, as there is an urgent need for new antimicrobial agents that can overcome resistance mechanisms and effectively treat infectious diseases. New approaches, such as targeting bacterial virulencefactors and host factors, have shown promise in preclinical studies. Moreover, advances in technologies such as high-throughput screening and molecular docking have enabled the rapid identification of new antimicrobial compounds.ConclusionThe development of new antimicrobial drugs is critical for the prevention and treatment of infectious diseases. With the emergence of multidrug-resistant bacteria, innovative approaches and technologies are needed to develop novel antimicrobial drugs. The application prospects of antimicrobial drugs are promising, and research in this field will continue to advance and provide new tools for combating infectious diseases.Keywords: antimicrobial drugs, multidrug-resistant, development, application prospectsIn recent years, the increasing prevalence of multidrug-resistant strains of bacteria has become a major public health concern worldwide. The overuse of antibiotics has contributed to the emergence of these resistant strains. As a result, the development of new antimicrobial drugs has become increasingly important in the fight against infectious diseases. New approaches to antimicrobial drug development are emerging. For example, researchers are now exploring the use of phage therapy as a potential alternative to antibiotics. Bacteriophages, or viruses that target bacteria, have been used in some countries to treat bacterial infections. While this approach is still in its early stages, it shows promise as a potential solution to the growing problem of antibiotic resistance.Another emerging area of research is into the use of nanoparticles as antimicrobial agents. Nanoparticles have been shown to have antimicrobial properties that can be used to combat infections. Research is ongoing into the development of nanoparticles that can be targeted at specific bacterial strains, and this may pave the way for the future use of nanoparticles in the treatment of infectious diseases.As the development of new antimicrobial drugs continue to progress, researchers are also looking at ways to slow down the emergence of antibiotic resistance. One approach is to use combination therapies that involve the use of multiple drugs to target different aspects of bacterial infections. Another approach is to use antibiotic stewardship programs to promote the responsible use of antibiotics in order to slow down the development of resistance.In addition to the development of new drugs and approaches, there is also a need for increased surveillance of infectious diseases. This can help to identify outbreaks of drug-resistant infections and to track the emergence of new resistant strains of bacteria. This information can help to guide public health policies and inform the development of new drugs and approaches.In conclusion, the development of new antimicrobial drugs is critical in the fight against infectious diseases. While the challenges of antibiotic resistance are significant, the emergence of new approaches and technologies provides hope for the future. Through continued research, innovation, and responsible use ofantibiotics, we can work towards a future where infectious diseases can be controlled and treated effectively.The development of new antimicrobial drugs is important for several reasons. First, infections caused by drug-resistant bacteria are becoming increasingly difficult to treat, leading to increased illness and in severe cases, death. Second, the evolution of bacteria means that existing antibiotics will become less effective over time, creating a need for new drugs to replace them. Third, some types of bacteria are becoming resistant to multiple types of antibiotics, which makes treating infections even more challenging.One of the main challenges in developing new drugs is finding compounds that are effective against drug-resistant bacteria. Researchers are looking for new compounds that work differently than existing antibiotics, such as compounds that target bacterial virulence factors rather than their ability to multiply. They are also studying the molecular mechanisms of antibiotics to identify ways to modify them to make them more effective or to create new compounds with similar properties.Another approach is to use combinations of existing compounds to treat infections caused by resistant bacteria. Researchers have found that certain combinations of antibiotics can be more effective than using a single drug. This approach involves using drugs that target different aspects of bacterial function, such as cell wall synthesis and protein synthesis. This approach can slow the development of antibiotic resistance because it is less likely for bacteria to become resistant to multiple drugs at once.In addition to developing new drugs, researchers are studyingalternative therapies for treating infections. Phage therapy is one such alternative that is being studied. This involves using bacteriophages, which are viruses that infect and kill bacteria. Phages can be used to target specific types of bacteria, making them a promising approach for treating drug-resistant infections. However, there are still many questions to answer about the effectiveness and safety of phage therapy.Nanoparticles are also being investigated as a potential antimicrobial therapy. Nanoparticles are tiny particles that can be engineered to have antimicrobial properties. They can be designed to target specific types of bacteria, making them a potential alternative to antibiotics. However, research is still in the early stages, and more research is needed to determine their effectiveness and safety.Finally, it is important to promote responsible use of antibiotics to slow the development of antibiotic resistance. This includes using antibiotics only when necessary, not prescribing antibiotics for viral infections, and completing the full course of antibiotics prescribed by a healthcare provider. By reducing the use of antibiotics, we may be able to slow the development of antibiotic resistance and preserve the effectiveness of existing antibiotics.In conclusion, the development of new antimicrobial drugs and alternative therapies is critical to combat drug-resistant infections. While the challenges are significant, research is ongoing, and new approaches are being explored. In addition to developing new drugs, it is important to promote responsible use of antibiotics to slow the development of antibiotic resistance. Through continuedresearch and responsible use of antibiotics, we can work towards a future where infectious diseases can be controlled and treated effectively.。
LncRNA
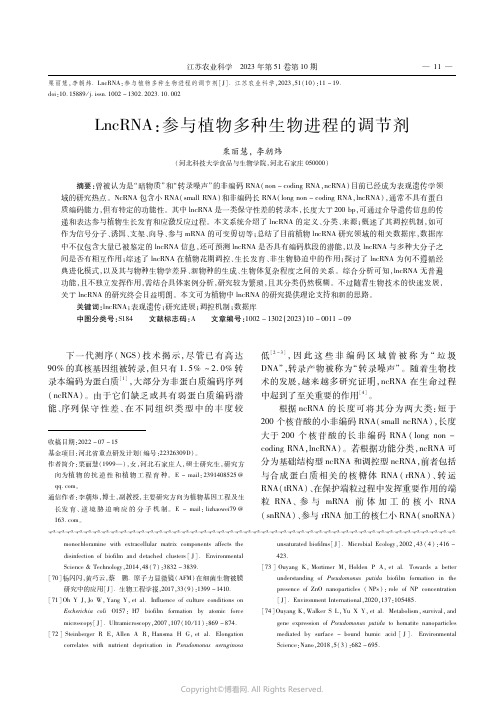
櫄櫄櫄櫄櫄櫄櫄櫄櫄櫄櫄櫄櫄櫄櫄櫄櫄櫄櫄櫄櫄櫄櫄櫄櫄櫄櫄櫄櫄櫄櫄櫄櫄櫄櫄櫄櫄櫄櫄櫄櫄櫄櫄櫄櫄櫄 monochloraminewithextracellularmatrixcomponentsaffectsthedisinfectionofbiofilmanddetachedclusters[J].EnvironmentalScience&Technology,2014,48(7):3832-3839.[70]杨闪闪,黄巧云,蔡 鹏.原子力显微镜(AFM)在细菌生物被膜研究中的应用[J].生物工程学报,2017,33(9):1399-1410.[71]OhYJ,JoW,YangY,etal.InfluenceofcultureconditionsonEscherichiacoliO157:H7biofilmformationbyatomicforcemicroscopy[J].Ultramicroscopy,2007,107(10/11):869-874.[72]SteinbergerRE,AllenAR,HansmaHG,etal.ElongationcorrelateswithnutrientdeprivationinPseudomonasaeruginosaunsaturatedbiofilms[J].MicrobialEcology,2002,43(4):416-423. [73]OuyangK,MortimerM,HoldenPA,etal.TowardsabetterunderstandingofPseudomonasputidabiofilmformationinthepresenceofZnOnanoparticles(NPs):roleofNPconcentration[J].EnvironmentInternational,2020,137:105485.[74]OuyangK,WalkerSL,YuXY,etal.Metabolism,survival,andgeneexpressionofPseudomonasputidatohematitenanoparticlesmediatedbysurface-boundhumicacid[J].EnvironmentalScience:Nano,2018,5(3):682-695.栗丽慧,李朝炜.LncRNA:参与植物多种生物进程的调节剂[J].江苏农业科学,2023,51(10):11-19.doi:10.15889/j.issn.1002-1302.2023.10.002LncRNA:参与植物多种生物进程的调节剂栗丽慧,李朝炜(河北科技大学食品与生物学院,河北石家庄050000) 摘要:曾被认为是“暗物质”和“转录噪声”的非编码RNA(non-codingRNA,ncRNA)目前已经成为表观遗传学领域的研究热点。
Applications of Nanoparticles in Medicine
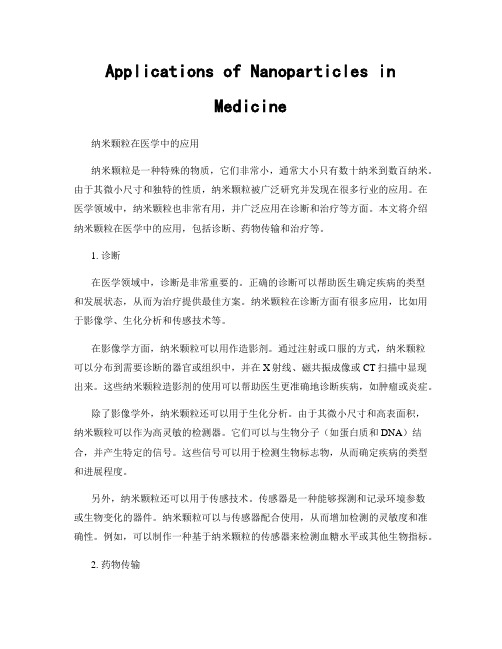
Applications of Nanoparticles inMedicine纳米颗粒在医学中的应用纳米颗粒是一种特殊的物质,它们非常小,通常大小只有数十纳米到数百纳米。
由于其微小尺寸和独特的性质,纳米颗粒被广泛研究并发现在很多行业的应用。
在医学领域中,纳米颗粒也非常有用,并广泛应用在诊断和治疗等方面。
本文将介绍纳米颗粒在医学中的应用,包括诊断、药物传输和治疗等。
1. 诊断在医学领域中,诊断是非常重要的。
正确的诊断可以帮助医生确定疾病的类型和发展状态,从而为治疗提供最佳方案。
纳米颗粒在诊断方面有很多应用,比如用于影像学、生化分析和传感技术等。
在影像学方面,纳米颗粒可以用作造影剂。
通过注射或口服的方式,纳米颗粒可以分布到需要诊断的器官或组织中,并在X射线、磁共振成像或CT扫描中显现出来。
这些纳米颗粒造影剂的使用可以帮助医生更准确地诊断疾病,如肿瘤或炎症。
除了影像学外,纳米颗粒还可以用于生化分析。
由于其微小尺寸和高表面积,纳米颗粒可以作为高灵敏的检测器。
它们可以与生物分子(如蛋白质和DNA)结合,并产生特定的信号。
这些信号可以用于检测生物标志物,从而确定疾病的类型和进展程度。
另外,纳米颗粒还可以用于传感技术。
传感器是一种能够探测和记录环境参数或生物变化的器件。
纳米颗粒可以与传感器配合使用,从而增加检测的灵敏度和准确性。
例如,可以制作一种基于纳米颗粒的传感器来检测血糖水平或其他生物指标。
2. 药物传输药物传输是治疗中的一个重要环节。
药物需要通过血液或淋巴系统迅速到达目标部位,并保持一定浓度以发挥治疗作用。
但是,传统的药物传输方式往往存在一些问题,如药物不能准确地达到目标位置,或者过早地被代谢或排泄,从而导致药效不佳或产生副作用。
纳米颗粒在药物传输方面也有广泛的应用。
由于纳米颗粒的纳米尺度和高比表面积,它们可以更容易地进入细胞内部,并在体内保持稳定。
同时,纳米颗粒可以通过表面修饰来实现定向输送,从而减少药物在体内的分布。
- 1、下载文档前请自行甄别文档内容的完整性,平台不提供额外的编辑、内容补充、找答案等附加服务。
- 2、"仅部分预览"的文档,不可在线预览部分如存在完整性等问题,可反馈申请退款(可完整预览的文档不适用该条件!)。
- 3、如文档侵犯您的权益,请联系客服反馈,我们会尽快为您处理(人工客服工作时间:9:00-18:30)。
Formation of DNA nanoparticles in the presence of novel polyamine analogues:a laser light scattering and atomic force microscopic studyVeena Vijayanathan 1,Thresia Thomas 2,3,4,Thomas Antony 5,Akira Shirahata 6and T.J.Thomas 1,3,*Departments of 1Medicine,and 2Environmental and Community Medicine,University of Medicine and Dentistry of New Jersey,Robert Wood Johnson Medical School,125Paterson Street,CAB 7090,New Brunswick,NJ 08903,3The Cancer Institute of New Jersey,New Brunswick,NJ 08903,4Environmental and Occupational Health Sciences Institute,Piscataway,NJ 08854,USA,5Department of Molecular Biology,Max Planck Institute forBiophysical Chemistry,Am Fassberg 11,D-37077,GoÈttingen,Germany and 6Department of Biochemistry and Cellular Physiology,Josai University,Saitama,JapanReceived October 5,2003;Revised and Accepted October 27,2003ABSTRACTWe synthesized a pentamine (3-3-3-3)and two hex-amine (3-3-3-3-3and 3-4-3-4-3)analogues of the natural polyamine,spermine (3-4-3)and studied their effectiveness in condensing pGL3plasmid DNA,using light scattering and atomic force micro-scopic (AFM)techniques.The midpoint concentra-tion of the polyamines on pGL3condensation (EC 50)was 11.3,10.6,1.5,0.49and 0.52m M,respectively,for 3-4-3,norspermine (3-3-3),3-3-3-3,3-3-3-3-3and 3-4-3-4-3in 10mM Na cacodylate buffer.Dynamic laser light scattering study showed a decrease in hydrodynamic radii of plasmid DNA particles as the number of positive charges on the polyamines increased.AFM data showed the presence of toroids with outer diameter of 117±191nm for differ-ent polyamines,and a mean height of 2.61T 0.77nm.AFM results also revealed the presence of intermediate structures,including those showing circumferential winding of DNA to toroids.The dependence of the EC 50on Na +concentration sug-gests different modes of binding of spermine and its higher valent analogues with DNA.Our results show a 20-fold increase in the ef®cacy of hexamines for DNA condensation compared to spermine,and pro-vide new insights into the mechanism(s)of DNA nanoparticle formation.These studies might help to develop novel nonviral gene delivery vehicles.INTRODUCTIONThe compaction of DNA to nanoparticles is a biologically important phenomenon involved in the packaging of DNA in virus heads and the cell nucleus,as well as in the development of nonviral gene delivery vehicles (1±5).A large number of cationic molecules,including cationic lipids,polyaminolipids,dendrimers and polyethylenimine,are currently under development as nonviral gene delivery vehicles (1,6±10).The ®rst step in the mechanism of action of these molecules is the condensation of DNA to nanoparticles,which can be transported through the cell membrane by endocytosis and/or by other mechanisms that are not well de®ned at present (1,8,10±13).Detailed studies of DNA condensation were ®rst conducted with the natural polyamines,spermidine and spermine using electron microscopy (EM)and light scattering techniques (14±18).Polyamines are ubiquitous cellular components and are believed to play important roles in cellular functions,includ-ing the packaging of DNA in virus heads (19,20).Polyamine±DNA interactions have been modeled on the basis of electrostatic interactions between the positively charged amino and imino groups of polyamines and the negatively charged phosphate groups of DNA (21).Liquid crystalline textures,including ®ngerprint textures of the cholesteric phase and columnar hexagonal phase,have been identi®ed in DNA±polyamine complexes formed at high (>1mg/ml)concentra-tions of DNA (2,22±24).At very low (~1m g/ml)DNA concentrations,nanometric DNA particles are formed in the presence of spermidine,and these particles appear as toroids,spheroids and rods when visualized by EM (14±17,25).Dynamic light scattering (DLS)studies showed a hydro-dynamic radius of 40±60nm for these particles in solution (1,16,18,26).EM and atomic force microscopy (AFM)revealed the presence of intermediates,including ¯ower-like and spaghetti-like structures during the formation of toroids and spheroids as end products of DNA condensation (1,27±31).A recent investigation using freeze-fracture EM showed a hexagonal packaging arrangement of DNA in toroids (32).However,this study was done with Co(NH 3)63+as the condensing agent.Although investigations with Co(NH 3)63+have provided valuable information on the physical chemical aspects of DNA condensation (1,18,32),cationic molecules used in developing gene delivery vehicles are organic cations,*To whom correspondence should be addressed.Tel:+17322358460;Fax:+17322358473;Email:thomastj@Nucleic Acids Research,2004,Vol.32,No.1127±134DOI:10.1093/nar/gkg936Nucleic Acids Research,Vol.32No.1ãOxford University Press 2004;all rights reservedPublished online January 2, 2004at Jinan University on December 24, 2010 Downloaded fromsuch as polyamine-derivatized lipids,polyethylenimine,and dendrimers (1).In addition,most of the reported EM and AFM studies were performed on dried DNA samples that could introduce artifacts on drying as well as by uranyl acetate staining of DNA for EM.Investigations into the ionic and structural effects of oligoamines (polyamine analogues with a higher positive charge than that of spermine)on the condensation of DNA are lacking at present.In addition,long chain polyamines,such as polyethylenimine are being studied for their ability to promote DNA condensation and gene delivery,although oligoamines of intermediate charge density have received little attention (1).Such molecules might ®nd application in gene delivery vehicles,including the transport of therapeutic oligonucle-otides in cancer cells (33).In this study,we synthesized a pentamine and two hexamine analogues of spermine and examined their ef®cacy in provoking the condensation of a plasmid DNA,pGL-3,using light scattering and AFM techniques.Our results show that the higher valent polyamine analogues are more ef®cient than spermine in the induction and stabilization of DNA nanoparticles.AFM studies demon-strate the presence of toroidal condensates in the presence of polyamine analogues.MATERIALS AND METHODS Plasmid DNA and polyaminesPGL-3luciferase control vector (5256bp),which contains the SV40promoter and enhancer sequences,was purchased from Promega (Madison,WI).The integrity of the plasmid DNA was checked with 1%agarose gel electrophoresis followed by ethidium bromide staining.The results indicated that the plasmid was >90%supercoiled.The plasmid DNA was dissolved in 10mM Na cacodylate buffer (pH 7.2)containing 0.5mM EDTA (Na cacodylate buffer),dialyzed from the same buffer,and stored at 4°C.The concentration of the plasmid DNA was determined by measuring the absorbance at 260nm.Molar DNA phosphate concentration was calculated using a molar extinction coef®cient of 6900M ±1cm ±1.Buffer solutions were ®ltered through 0.22m m Millipore ®lters.Spermidine.3HCl and spermine.4HCl were purchased from Sigma Chemical Co.(St Louis,MO).Polyamine analogues,1,11-diamino-4,8-diazaundecane (3-3-3),1,15-diamino-4,8,12-triazapentadecane (3-3-3-3),1,19-diamino-4,8,12,16-tetra-azanonadecane (3-3-3-3-3),and 1,21-diamino-4,9,13,18-tetra-azaheneicosane (3-4-3-4-3)were synthesized by us,as described previously (33).Elemental analysis,NMR,HPLC and mass spectrometry con®rmed the chemical structure and purity of polyamine analogues.The protonated chemical structures of the polyamines used in this study are shown in Figure 1.Stock solutions of these polyamine analogues were prepared in double distilled water and appropriate dilutions made in 10mM Na cacodylate buffer,pH 7.2.Total intensity light scatteringDNA condensation experiments were performed in 10mM Na cacodylate buffer,as described previously (26).The mono-valent salt concentrations of the buffer were adjusted using 1M NaCl stock solutions.Polyamine stock (1±10mM)solutions were added to DNA solution (1.5m M)to obtain thedesired polyamine concentration in a total volume of 2ml.The samples were mixed with a vortex mixer for several seconds,and kept undisturbed for a period of 1h at 22°C to attain equilibrium.The solution was then centrifuged at 500g for 30min at 22°C to avoid variations due to aggregates or dust particles.The centrifugation step had no effect on the DNA concentration,as con®rmed by measuring the absorbance of DNA at 260nm before and after centrifugation.Light scattering experiments were performed using a Fluoromax-2spectro¯uorometer.Light from a 150W Xenon lamp was ®ltered through double monochromators.The excitation and emission monochromators were set to the same wavelength of 305nm with a 5nm bandpass,the integration time set to 5s,and the scattered light collected at a 90°angle with respect to the incident beam.Dynamic laser light scatteringWe used DynaPro dynamic laser light scattering equipment (Protein Solutions,Lakewood,NJ)with a temperature controlled micro sampler for determining the diffusion coef®cients of DNA nanoparticles formed in the presence of different polyamines.DNA solutions were prepared,mixed with polyamine solutions,and 50m l of the mixture was transferred to the standard quartz cuvette,and scattered light measured at a 90°angle to the incident beam.For monodisperse particles much smaller than the incident beam,the autocorrelation function is given by the equation:g (1)(t )=exp[±Dq 2(t )]where g (1)(t )is the autocorrelation function,(t )is the decay time and q is the scattering vector [=(4p n /l 0)sin q /2],which is a function of solvent refractive index n ,the wavelength of the incident beam l 0,the scattering angle q ,and the diffusion coef®cient D .The hydrodynamic radius (R h )is calculated from the diffusion coef®cient using the Stokes-Einstein equation:R h =kT /6ph Dwhere k is the Boltzmann constant and T is the absolute temperature in Kelvin.Variability of the data was controlled by programing the software to reject runs with standard deviations higher than 5%.Atomic force microscopyThe AFM images were acquired on a Nanoscope III micro-scope (Digital Instruments,Santa Barbara,CA).PlasmidFigure 1.Chemical structures of polyamines used in this study.The proton-ated structures are shown here because these molecules are positively charged under the ionic and pH conditions used in this study.3-4-3is spermine and 3-3-3is norspermine.128Nucleic Acids Research,2004,Vol.32,No.1at Jinan University on December 24, 2010 Downloaded fromDNA was incubated with the appropriate concentrations of polyamine analogues in 10mM Na cacodylate buffer for 1h and deposited onto a freshly cleaved mica surface.The AFM head,equipped with a ¯uid cell,was placed on top of the scanner (J-scanner,Digital Instruments)and more samples added through the ¯uid cell.Imaging was done in tapping mode in liquid.Cantilevers (NP-S,Digital Instruments)with a nominal spring constant of 0.32N/m were used at an oscillation frequency of ~9kHz.Image analysis was performed using Nanoscope software after removing the background slope by ¯attening images.Height and outer diameter of the toroids were measured using the Nanoscope software.Data are given as mean T standard error of the mean (S.E.M.).RESULTSStatic light scatteringWe ®rst determined the ef®cacy of different polyamines to condense DNA by total intensity light scattering using a Fluoromax-2spectro¯uorometer.Figure 2shows typical plots of the scattered light intensity of the DNA solution in the presence of different concentrations of polyamines.The scattered light intensity was low in the absence of polyamines;however,a marked increase in the intensity of the scattered light occurred at a critical concentration of each polyamine,due to the formation of condensed DNA particles (26).The increase in the scattered light intensity was concentration-dependent up to a certain concentration of the polyamine,and then leveled off at higher concentrations.Similar scattering pro®les were obtained when samples were analyzed after 1±2h of equilibration.The ef®cacy of different polyamines on DNA condensation was quanti®ed by determining the EC 50value,the concentration of a polyamine at the midpoint of DNA condensation.In the presence of 10mM Na +concentration,the EC 50values were 11.3T 0.3,10.6T 1.3,1.5T 0.27,0.49T 0.05and 0.52T 0.1,respectively,for 3-4-3,3-3-3,3-3-3-3,3-3-3-3-3and 3-4-3-4-3(Table 1).This result indicates that the pentamine and hexamine analogues are more ef®ca-cious than spermine in condensing the plasmid pGL3.However,there was no signi®cant difference in the EC 50values (Table 1)between the two tetramines (3-4-3and 3-3-3)or between the hexamines (3-3-3-3-3and 3-4-3-4-3)used in our study,indicating that chemical structural differences of isovalent polyamines may have no signi®cant effect on EC 50values when the charge separation differed by one methylene group.Hydrodynamic radii of DNA condensatesWe next determined the diffusion coef®cient of DNA condensates with dynamic laser light scattering equipment and calculated the hydrodynamic radius using the Stokes-Einstein equation.The results are summarized in Table 2.Dynamic light scattering measurements indicated the presence of compact particles with hydrodynamic radii in the range of 50±95nm.The diffusion coef®cient of these particles varied from 2.4to 4.5Q 10±8cm 2/s.There was a 2-fold decrease in the hydrodynamic radius of the particles as the condensing agent was changed from tetramine (3-4-3)to hexamine (3-4-3-4-3).The nanometric particles produced in the presence of 3-4-3-4-3were smaller than those produced with 3-3-3-3-3(67T 6.4versus 51T 1.6nm).We also tested the effects of increasing DNA concentration on the hydrodynamic radii of the condensed particles.A 4-fold increase (from 1.5to 6m M)in DNA concentration resulted in condensed particles with hydrodynamic radii of 75±105nm,when spermine was used as the condensing agent.Inter-molecular association becomes dominant at higher DNA concentrations,yielding larger condensates.Hence,theFigure 2.Typical plots of the relative intensity of scattered light at 90°plotted against the concentrations of spermine and its analogues.The pGL-3luciferase plasmid DNA solution had a concentration of 1.5m M DNA phosphate,dissolved in 10mM Na cacodylate buffer,pH 7.2.The symbols are as follows:(A )3-3-3,®lled circle;3-4-3,open circle;(B )3-3-3-3,open square;3-3-3-3-3,open triangle;and 3-4-3-4-3,®lled triangle.Table 1.The relative ef®cacy of spermine and its analogues to condense plasmid DNA PolyaminePolyamine concentration at midpoint of plasmid DNA condensation (EC 50,m M)a 3-4-3(Spermine)11.3T 0.33-3-3(Norspermine)10.6T 1.33-3-3-3 1.5T 0.273-3-3-3-30.49T 0.053-4-3-4-30.52T 0.1a Allmeasurements were made in 10mM Na cacodylate buffer.EC 50values were determined by plotting the total intensity of scattered light against polyamine concentration (Fig.1).Data given are mean T S.E.M.of 3±5separate measurements.Nucleic Acids Research,2004,Vol.32,No.1129at Jinan University on December 24, 2010 Downloaded frommajority of our experiments were performed at a low DNA concentration (1.5m M),to minimize the formation of intermolecular aggregates.Under these conditions,there were no signi®cant differences in the diffusion coef®cients of the condensates when measurements were done within 1±2h of mixing,indicating that the system is equilibrated within this time period.Structural morphology of DNA condensates by AFM In order to determine the morphology of the DNA condensates formed in the presence of polyamines,we used an atomic force microscope with tapping mode in solution.Figure 3shows an image of the plasmid DNA condensates formed with 2m M of 3-3-3-3-3.AFM revealed the presence of individual toroids,circular DNA and a network of toroids.Figure 3also shows the presence of linear strands and loop-like structures,which are intermediates in the condensation of the DNA.The inset in Figure 3shows an individual toroid staying on its side,indicating that surface attachment is not a requirement for toroid formation.Similar structures were formed with other polyamines used in this study.Representative toroids,inter-mediates and toroidal aggregates formed in the presence ofspermine (panel A),3-3-3-3(panel B)and 3-4-3-4-3(panel C)are presented in Figure 4.Panel D provides evidence for toroid formation by spooling in the case of 3-4-3-4-3(marked by arrows).The dimensions of well-developed toroids were measured using the Nanoscope software.The outer diameter varied from 117to 191nm (Table 3).There was a decrease in outer diameter of the toroids as the size and charge of the polyamine increased.This result suggests that altering the nature of the polyamine used in condensation can control the size of the DNA nanoparticle.Multimolecular toroids with much larger structures were also found along with the individual toroids (data not shown).The average height of all toroids,including those formed with spermine to hexamines,was 2.61T 0.77nm (28toroids were measured).Individual heights varied from 1.5to 4.2nm.It is important to note here that the heights of these toroids are signi®cantly lower than that expected from a theoretical calculation,based on the 2nm theoretical diameter of DNA.This is a limitation of AFM measurements in tapping mode [(34),please see Discussion].Effect of salt concentrationPrevious studies by others (16)and us (26)have shown that the EC 50values of tri-and tetravalent polyamines increased with the concentration of monovalent ions,such as Na +,in the medium.We therefore determined the salt dependence of the EC 50using the following concentrations of Na +in the buffer:10,25,50,75and 100mM.Plots of scattered light intensity versus polyamine concentrations were generated for each polyamine at each of the NaCl concentrations to determine the EC 50values.We then plotted the log[EC 50]values against log[Na +](Fig.5).Within experimental error,these plots were linear over the entire range of Na +concentration in the case of spermine and 3-3-3,with slopes of 0.89and 1.02,respectively.Figure 3.Atomic force microscopy images of pGL3plasmid DNA com-plexed with 2m M 3-3-3-3-3.pGL3plasmid DNA solution (1.5m M)was incubated with the polyamine solution for 1h before making the measure-ments.The imaging was done in tapping mode and in solution.Scale bar is 200nm.The color bar represents the height of the condensed DNA.The inset shows a single toroid on its side.Scale bar for the inset is 45nm.Figure 4.Scanning force microscopy images showing the toroid structures of pGL3plasmid DNA formed by incubation with 25m M spermine (A ),5m M 3-3-3-3(B ),2m M 3-4-3-4-3(C ),and the partly formed toroids,observed in the presence of 2m M 3-4-3-4-3(D ).Scale bar is 200nm.Table 2.Hydrodynamic parameters of DNA nanoparticles formed in the presence of different polyamines PolyaminePolyamine concentration used for nanoparticle formation (m M)Diffusion coef®cient (cm 2/s)Hydrodynamic radius (nm)a 3-4-3(Spermine)25 2.4Q 10±894.6T 1.63-3-325 2.5Q 10±891.8T 5.33-3-3-35 2.8Q 10±880T 10.43-3-3-3-32 3.4Q 10±867T 6.43-4-3-4-324.5Q 10±851T 1.6a Allmeasurements were made in 10mM Na cacodylate buffer with the indicated concentrations of polyamines.Data given are mean T S.E.M.of 3±5separate measurements.130Nucleic Acids Research,2004,Vol.32,No.1at Jinan University on December 24, 2010 Downloaded fromHowever,two linear regions were observed for the pentamine and hexamines,the slope of the plot at 10±50mM Na +concentration was 0.52for 3-3-3-3and ~0.23for the hexamines.At higher Na +concentrations,the slope values were 2,2.5and 3.2for 3-3-3-3-3,3-4-3-4-3and 3-3-3-3,respectively (Table 4).These slope values,dlog[EC 50]/dlog[Na +]are a quantitative measure of the concentration dependence between multivalent and monovalent cations in condensing the plasmid DNA (16,26).In addition,these values provide a measure of the binding af®nity of the polyamines with DNA:a lower value of dlog[EC 50]/dlog[Na +]indicates a higher binding af®nity,according to the equations of the counterion condensation theory [(26),a theoretical description is given in this reference].DISCUSSIONResults presented in this report demonstrate formation of nanoparticles from a plasmid DNA in the presence of spermine and three higher valent spermine analogues.Previous studies using light scattering,electron microscopic,calorimetric and AFM techniques demonstrated thecondensation of closed and linear DNAs in the presence of spermidine and spermine (18,24±28,35±39).Electron micro-scopic studies have shown the presence of toroids,spheroids and rod-like structures of DNA in the presence of these naturally occurring polyamines.In comparison to distinct toroidal structures of DNA provoked by spermidine and cobalt hexamine [Co(NH 3)63+],aggregated structures were formed with spermine (35,40±44),and hence investigations with this tetramine remain limited.In the present study,we examined DNA condensation by novel polyamine analogues by laser light scattering and AFM techniques.Our results show that hexamines are about 20-fold more effective than spermine in compacting the plasmid DNA.Data obtained from dynamic laser light scattering and AFM studies are in excellent agreement.As can be seen from Table 1,the higher valent polyamines,3-3-3-3,3-3-3-3-3and 3-4-3-4-3are very ef®cient in compacting plasmid DNA to nanoparticles.The charge of the condensing agent has a profound in¯uence on the size of the particles formed.The hexamines provoked the formation of more toroidal structures than that by the pentamine,which in turn was better than spermine.The size of the particles decreased with an increase in the charge of the condensing agent.The hexamine analogues condensed DNA to an average hydrodynamic diameter of 118nm,compared to that of 191nm for spermine-condensed DNA.In general,the hydrodynamic diameter determined by dynamic laser light scattering and the outer diameter of the toroids measured by the Nanoscope software of the AFM are comparable (Tables 2and 3),and the data show a consistent decrease in size of the particles as the charge of the polyamine molecule increased.Our results using AFM are comparable to those reported by other investigators using this method,although different DNA samples and condensing agents were used.For example,Golan et al.(29)measured the dimensions of toroids prepared from pCMV luciferase DNA and poly-L -lysine (PLL)or PLL-asialoorosomucoid (AsOR)conjugate,and reported the height and outer diameter of the toroids as 3.7T 0.1and 142T 3.1nm,respectively.The height of toroids measured in our study is 2.61T 0.77nm.This value is averaged from measurements for all toroids,provoked by spermine to hexamines.The outer diameter of the toroids measured by us varied from 118to 191nm,depending on the charge of theTable 3.AFM measurement of the outer diameter and height of toroids Polyamine Outer diameter (nm)Mean height (nm)3-4-3(Spermine)191T 12a2.61T0.77b3-3-3-3168T 5.43-3-3-3-3117T 8.83-4-3-4-3118T 10.8a Mean T S.E.M.of 5±7toroids measured in each case.b Thetoroid height given here is the average value for 28toroids,formed in the presence of polyamines shown in column 1of thistable.Figure 5.Effect of Na +in the buffer on the midpoint concentration of poly-amines (EC 50)to induce DNA condensation.The EC 50values were deter-mined at Na +concentrations of 10,25,50,75and 100mM,as described in Figure 1.The plots of log[Na +]against log[EC 50]are in accordance with the equations of the counterion condensation theory (16).A theoretical descrip-tion of the implications of the slopes of these plots to determine the binding af®nity of the cations to DNA is given in a previous publication from this laboratory (26).The symbols represent EC 50values for 3-3-3(®lled square),3-4-3(open circle),3-3-3-3(®lled triangle),3-3-3-3-3(inverted open tri-angle),and 3-4-3-4-3(®lled circle).Error bars indicate standard deviation from three separate experiments.Absence of an error bar indicates that the standard deviation was within the size of the symbol.Table 4.Dependence of EC 50of polyamines on monovalent ion concentration Polyamined[log(EC 50)]/d[log(Na +)]a 10±100mM Na +10±50mM Na +50±100Na +3-4-3(Spermine)0.89±b ±b 3-3-3(Norspermine) 1.02±b ±b 3-3-3-3±0.52 3.23-3-3-3-3±0.24 2.033-4-3-4-3±0.222.5a d[log(EC 50)]/d[log(Na +)]values were determined from the slopes of the lines shown in Figure 5.In the case of spermine and norspermine,a straight line could be constructed over the entire range of Na +concentrations used.However,in the case of higher polyamine analogues,two straight lines were drawn (Fig.5),and two slopes calculated.b No separate slopes were determined,as a straight line was obtained over the entire range of Na +concentrations.Nucleic Acids Research,2004,Vol.32,No.1131at Jinan University on December 24, 2010 Downloaded frompolyamine used in our study.Lin et al.(24)found an average outer diameter of 120T 15nm for toroidal structures formed from l -DNA (48kb)and spermidine.Golan et al.(29)also found several rods under the conditions of their experiment;the height and widths of these rods were 3.9T 0.2and 50.7T 1.7nm,respectively.These authors proposed an arrangement of DNA in parallel rows in toroids,a mechanism consistent with a folding model for DNA condensation.They also proposed that the folding of rods into toroids could have formed some of the toroids.Such a mechanism has also been proposed by Dunlap et al.(31),who studied the formation of toroids from plasmid DNAs in the presence of didodecyl-amidoglycylspermine (DOGS)in ethanol or polyethylen-imine.The binding af®nity and cross-linking tendency of the condensing agent might affect the ¯exibility of DNA strands and packing density of toroids.Other factors,such as local concentration of condensing agent,temperature,pH and the presence and concentration of monovalent ions may also play important roles for the development of toroids.It is interesting to note here that the height of toroids measured in this study and that reported by other investigators is lower than that expected on the assumption that toroid formation does not require a surface to initiate the process.For a 6832bp plasmid DNA,Golan et al.(29)found a toroid height of 3.7T 0.1nm,compared to a height of 0.3T 0.1nm for the uncondensed molecule.Lin et al.(24)found discon-tinuity in the height distribution of toroids formed from l -DNA,with heights of 11T 4,20T 5,30T 6and 40T 3nm,measured in multiple Gaussian simulations at the four highest points of the toroids.In a recent study,Sitko et al.(45)reported the width of dense bundles of poly(dG-dC).poly(dG-dC)(~800bp)as 22T 6nm,with maximum heights of ~4±8nm.They also estimated ~6±8parallel molecules of the polynucleotide at the thinner regions of the bundle and 15±20molecules at the thicker regions of the bundle.These height values are much lower than that expected from condensates composed of several DNA molecules.In fact,the AFM measured height values of single DNA molecules are almost always lower than the theoretical DNA diameter of 2nm,and the problem associated with this discrepancy has been the topic of a recent publication (34).From a detailed study using non-contact tapping mode in air and jumping mode in aqueous solution,Moreno-Herrero et al.(34)concluded that a major factor contributing to the low height values of DNA is the presence of a salt layer around DNA on the mica surface.In addition,the elastic deformation induced by tip-sample interaction and the compression of the molecule caused by the attractive forces between DNA and the substrate contribute to the reduction in measured height of DNA.The toroid height (2.61T 0.77)measured in our study is lower than the theoretical value because of the above mentioned limitations in using AFM for height measurements of biological macromolecules.Polyamine±DNA interaction has been previously modeled on the basis of the counterion condensation theory developed by Manning (46)and Record et al.(47).This theory predicts a direct relationship between DNA charge neutralization and the concentrations of the monovalent and multivalent ions (16,26,48,49).Assuming a ®xed fraction of charge on the DNA is neutralized,Manning's theory predicted a power law relationship between the concentration of free polyamines insolution and monovalent ion concentration,independent of the nature of the DNA.The salt dependence of the EC 50values of spermine and norspermine (3-3-3)followed a straight line relationship,within experimental error,when log[EC 50]was plotted against log[Na +],with slope values of ~1(Table 4)over the range of Na +concentrations studied.In contrast,two linear regions were observed for the pentamine and hex-amines.At ionic strengths between 50and 100mM Na +,the experimental relationship between polyamine concentration and Na +concentration obeys the power law with a slope value of 2.5±3.2,which falls between the predicted range of 1and 6for the hexamines.But at lower Na +concentrations,it deviates from the power law.At low salt concentrations,the bound fraction of polyamines is comparable or even larger than free polyamines in solution.Since the relationship holds true only for the concentration of free polyamines in solution,the plots deviate from Manning's simpli®ed one variable treatment.The deviation was more prominent for the higher valent polyamine analogues than that for the lower valent cations,like spermidine and spermine,probably due to the higher binding af®nity of the hexamine and pentamine analogues to DNA.Several models of polyamine binding to DNA were based on the direct electrostatic interactions between the positive charges of polyamine and the negative charges of DNA (50,51).The binding may depend on the distance between the positive charges on the polyamine relative to the distance between the negative charges of the DNA phosphates.Our previous study (26)on DNA compaction by a series of tetraamine homologues of spermine,differing in the number of methylene groups between the secondary amino groups,demonstrated the structural effects of polyamines on the size of the condensates.Studies on the effect of spermidine on DNA compaction by Baase et al.(52)indicated that cross-linking by polyamine is required for DNA compaction.Polyamine homologues exhibited signi®cant differences in their ability to aggregate and condense genomic DNA and oligonucleotides (53).X-Ray diffraction studies of DNA condensates indicated that the Bragg spacing and interhelical spacing depend on the nature of the counterion (54).The Bragg spacing was in accordance with the model in which the amine groups make contact with the phosphate groups of different helices with fully extended aliphatic chains.Suwalsky et al.(55)proposed a cross-linked model,which assumed that the trimethylene spacing of 0.49nm is suitable to interact with the adjacent phosphate groups while the tetramethylene spacing of 0.614nm is suitable to bridge between different duplex strands.Molecular mechanics cal-culations (56)further predicted folding of DNA strands over the polyamines,while a recent molecular dynamics simulation study predicted differences in the nature of interaction between natural and synthetic polyamines with DNA (57).AFM of DNA complexes with dendronized polymers indicate that DNA wraps around dendronized polymers and the calculated pitch decreased with increase in the linear charge density of the polymer (58).Increasing the number of methylene groups of the polyamine may also enable them to wrap around the DNA molecule instead of being localized in the DNA major groove.Among the polyamine analogues with the same charges,smaller ions produce more tightly packed condensates (26).132Nucleic Acids Research,2004,Vol.32,No.1at Jinan University on December 24, 2010 Downloaded from。