硫酸烧渣提金新工艺和新设备
贵金属提炼黄金提炼加工工艺流程大全
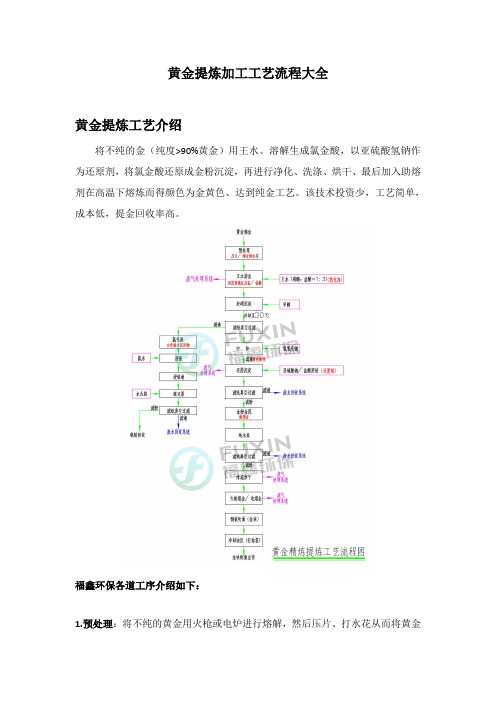
黄金提炼加工工艺流程大全黄金提炼工艺介绍将不纯的金(纯度>90%黄金)用王水。
溶解生成氯金酸,以亚硫酸氢钠作为还原剂,将氯金酸还原成金粉沉淀,再进行净化、洗涤、烘干、最后加入助熔剂在高温下熔炼而得颜色为金黄色、达到纯金工艺。
该技术投资少,工艺简单,成本低,提金回收率高。
福鑫环保各道工序介绍如下:1.预处理:将不纯的黄金用火枪或电炉进行熔解,然后压片、打水花从而将黄金分解成为小颗粒,为后续工艺做预处理,此工艺产生一定的高温热气及熔金废气。
2.溶解:将打散后小颗粒黄金或片金放入耐酸反应器(钛、玻璃器皿)中,在通风条件下加入金属重量3倍的王水,待剧烈反应过后,加热蒸发到原体积的1/5左右,使金完全溶解,再加浓盐酸驱赶游离的硝酸至无红棕色气体发生为止,取下冷却,用盐酸酸化,过滤除去不溶的杂物,余下的含氯金酸溶液用蒸馏水稀释,调节PH值,此工艺产生的废气包括NOX、HCL、HNO3等酸雾废气。
3.还原:将氯金酸溶液加热,一边搅拌一边迅速加入亚硫酸氢钠溶液,直至金全部还原成金粉沉淀,然后静置溶液为无色透明再进行过滤,此工艺产生的废气包括NOX、HCL、硫化物等废气。
4.净化:过滤所得的金粉沉淀中可能还吸附有一些铁化合物等杂质,必须除掉以提高金粉的纯度。
用盐酸加入金粉中,加热搅拌煮沸,然后小心倾出酸液,如此反复几次,直至不呈现黄色为止,此工艺产生的废气包括少量HCL雾。
5.洗涤、烘干:将经净化的金粉用蒸馏水反复洗涤多次直至溶液呈中性PH值为7为止,然后静置、过滤、烘干而得纯金粉,此工艺产生一定的高温热气及烘烤废气。
6.熔炼:将纯金粉和适量的纯碱、硼砂等化学纯级溶剂一起放入坩埚中,在1200度高温下熔炼2--3次,即得颜色为金黄色、纯度达99.9%以上的纯金。
7.后处理:后处理包括倒板料、吹面、用水冷却及打标签(油压/千斤顶/镭射等等),最后至收发出货。
说明:提纯后的海绵金经烘干后即可铸锭,铸锭要根据你的黄金重量大小选择不适合的坩埚和模具。
黄金选矿
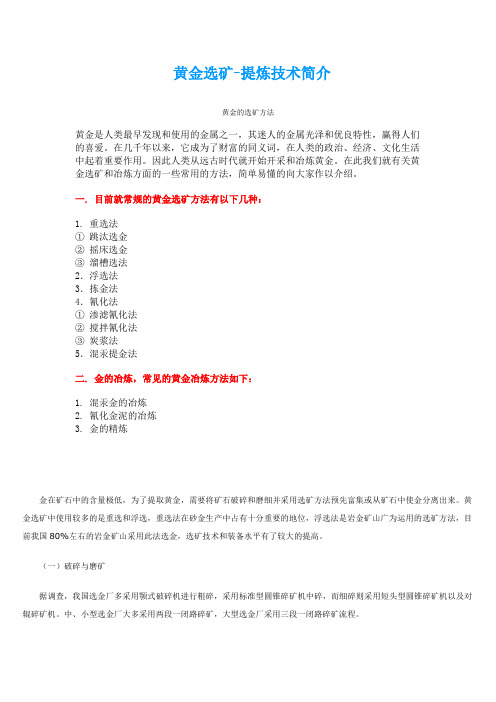
黄金选矿-提炼技术简介黄金的选矿方法黄金是人类最早发现和使用的金属之一,其迷人的金属光泽和优良特性,赢得人们的喜爱。
在几千年以来,它成为了财富的同义词,在人类的政治、经济、文化生活中起着重要作用。
因此人类从远古时代就开始开采和冶炼黄金。
在此我们就有关黄金选矿和冶炼方面的一些常用的方法,简单易懂的向大家作以介绍。
一. 目前就常规的黄金选矿方法有以下几种:1. 重选法① 跳汰选金② 摇床选金③ 溜槽选法2.浮选法3.拣金法4.氰化法① 渗滤氰化法② 搅拌氰化法③ 炭浆法5.混汞提金法二. 金的冶炼,常见的黄金冶炼方法如下:1. 混汞金的冶炼2. 氰化金泥的冶炼3. 金的精炼金在矿石中的含量极低,为了提取黄金,需要将矿石破碎和磨细并采用选矿方法预先富集或从矿石中使金分离出来。
黄金选矿中使用较多的是重选和浮选,重选法在砂金生产中占有十分重要的地位,浮选法是岩金矿山广为运用的选矿方法,目前我国80%左右的岩金矿山采用此法选金,选矿技术和装备水平有了较大的提高。
(一)破碎与磨矿据调查,我国选金厂多采用颚式破碎机进行粗碎,采用标准型圆锥碎矿机中碎,而细碎则采用短头型圆锥碎矿机以及对辊碎矿机。
中、小型选金厂大多采用两段一闭路碎矿,大型选金厂采用三段一闭路碎矿流程。
为了提高选矿生产能力,挖掘设备潜力,对碎矿流程进行了改造,使磨矿机的利用系数提高,采取的主要措施是实行多碎少磨,降低入磨矿石粒度。
(二)重选重选在岩金矿山应用比较广泛,多作为辅助工艺,在磨矿回路中回收粗粒金,为浮选和氰化工艺创造有利条件,改善选矿指标,提高金的总回收率,对增加产量和降低成本发挥了积极的作用。
山东省约有10多个选金厂采用了重选这一工艺,平均总回收率可提高2%~3%,企业经济效益好,据不完全统计,每年可得数百万元的利润。
河南、湖南、内蒙古等省(区)亦取得好的效果,采用的主要设备有溜槽、摇床、跳汰机和短锥旋流器等。
从我国多数黄金矿山来看,浮—重联合流程(浮选尾矿用重选)适于采用,今后应大力推广阶段磨矿阶段选别流程,提倡能收、早收的选矿原则。
硫酸烧渣提金新工艺和新设备(二)

书山有路勤为径,学海无涯苦作舟硫酸烧渣提金新工艺和新设备(二)三.新工艺和设备的优点浸出方法的优点: 1.本浸出方法使用工业上广泛使用的氯气(开始使用少量食盐)做浸出药剂及少量助剂,避免了氰化物的污染,使用的助剂降低氯气的消耗,使其药剂成本低于氰化法. 2.本方法浸出时间仅3 分钟,因此浸出设备有效容积仅为氰化法的0.2%~0.4%,以处理能力100t/d 的工厂为例,浸出设备有效容积仅0.3 立米.不但投资可减少20%,浸出的电耗也可降低4~5kwh/t. 新式浸出设备的优点: 采用新式反应器,适应大颗粒物料的浸出.常规浸出设备只适用于处理200 目以下的矿浆,否则就会出现”沉槽”、压搅拌浆等故障.本设备容积很小,采用其它方法解决反应器问题,避免搅拌不均. 新式固液分离设备具有投资少、生产成本低、易防腐等特点.现有的过滤设备不能解防腐问题,而且价格很高,大约需要投资100 万元,新式固液分离设备投资仅30 万元. 新工艺的优点: 1.省去了磨矿及相应的分级、浓密设备,减少投资40%左右;节省占地400 平米;减少材料消耗10 元/t;减少电费5 元/t;减少操作工3--6 人. 2.不磨的烧渣本身粒度较大,一般在-80 目占70%以上,40-80 目占25%左右,其余5%在20-40 目之间,沉降速度快.特别适合用新式固液分离设备进行液固分离.这种设备易于操作.与氰化工艺相比,省去了浓密机和压滤机,易于控制浸出液物量平衡. 3. 选用活性炭吸附法回收浸出液中的金,考虑到在吸附过程中可能产生沉淀物,采用我单位已获专利的吸附槽.吸附装置投资仅2 万元. 4.由于在酸性含氯溶液中吸附金氯络合物,并使金离子最终转变为单质金.因此载金炭上金品位至少可富集到10kg/t,采用焚烧—王水溶解—还原的联合工艺即可生产出纯金.冶炼工艺设备简单,仅使用常规药剂,与氰化法比,冶炼工段节约设备投资30 万元,冶炼成本也低于常规工艺. 5.贫液中杂质主要是铁、锌和铜,可用石灰沉淀,分离掉杂质的溶液可循环使用;由于不断加氯,浸出液的酸度将不断增加,加石灰除杂的过程还。
硫酸渣工艺技术

硫酸渣工艺技术
硫酸渣是由硫酸制造过程中产生的一种废弃物,含有一定的硫酸盐和残留的硫酸。
对于硫酸渣的处理,通常会采用渣处理工艺技术,以将其转化为有用的产品或实现资源化利用。
硫酸渣处理工艺技术最常用的方法是酸浸法。
该方法将硫酸渣与稀硫酸进行反应,将其溶解,生成硫酸溶液和沉淀物。
硫酸溶液可以进一步回收,用于制造硫酸,而沉淀物则可以通过固液分离进行分类和处理。
固液分离是硫酸渣处理中非常重要的一步。
通过重力沉淀、过滤、离心等方法,将沉淀物与溶液分离开来。
分离后的沉淀物主要是硫酸盐和其他杂质,可以进行进一步处理。
其中一种处理方法是进行热处理。
将沉淀物加热至高温,使其中的有机物和水分蒸发,生成无机固体物质。
这些无机固体物质可以用于建筑材料、陶瓷和玻璃工业等领域。
另一种处理方法是进行化学处理。
通过与其他化学物质反应,改变沉淀物的性质,使其具有一定的应用价值。
例如,可以将硫酸盐转化为硫酸盐肥料,用于农业生产。
为了提高硫酸渣的资源化利用率,还可以采取一些先进的技术。
例如,可以利用化学和生物技术手段,将硫酸渣中的重金属和有害物质进行提取和分离,以减少对环境的影响。
此外,还可以通过研发新的工艺技术,实现硫酸渣的高效利用。
总之,硫酸渣处理工艺技术是将硫酸渣转化为有用产品或实现资源化利用的重要手段。
通过酸浸法、固液分离、热处理、化学处理以及先进技术的应用,可以将硫酸渣转化为硫酸溶液、建筑材料、肥料等有用的产品,同时减少对环境的影响,实现资源的循环利用,提高资源利用效率。
黄金科技档案的科学管理

黄
金
GOLD
黄金 科 技 档 案 的科 学 管 理
米春 华
( 长春 黄 金 研 究 院 )
摘 要 : 了充分 发挥 黄金 科技 档 案在 黄金科 研 、 为 生产 中的作 用 , 做好 档 案 管理 的科 学化 、 息 应 信 化 、 度化 建设 。介 绍 了长春 黄金 研 究 院黄金科 技 档 案 管理 制 度 、 制 管理措 施 , 以及 黄 金 科技 档 案 在
科 学 技术 档 案 ( 称科 技 档 案 ) 指 在 自然科 学 简 是 研 究 、 产技 术 、 本 建 设 ( 生 基 以下 简 称 科 研 、 生产 、 基
供 了权威 的技 术 支 持 。在 黄 金 行 业 历 次重 大技 术 升 级 中 , 春黄 金研 究 院都 提供 了 强有 力 的技 术 支 撑 。 长 如 喷锚 支护 、 水砂 充 填 技术 的 开发 , 矿脉 机械 化 开 薄 采技 术 的研究 与应 用 ; 全泥 氰化 炭浆 工 艺 的引进 及推
题 1 5 多项 , 中, 0 7 其 国家和地 方重点攻关项 目 5 1 4 项。取得各项科研成果 4 3 , 0 项 获得 国家和省部级以 上 的科 技进 步 奖 8 8项 。 目前 拥 有 专 利技 术 16项 。 1
科技档案管理办法》 对黄金科技档案资料的收集 、 立 档、 管理 、 使用 、 安全保密等方面都作 了明确的规定 , 使 黄金 科技 档 案 从 形 成 时起 就 对 它 的真 实 性 、 整 完
大 。现 今 , 春 黄 金 研 究 院 已形 成 科 研 机 构 配 置 齐 长 全 、 术手 段先 进 的综 合 研 发 体 系 。该 院 拥 有 地 质 、 技 采矿 、 冶金 、 环保 、 岩矿 、 分析 、 械制 造 、 机 电气 自动 化 、 计 算机 应 用等专 业 技 术 , 盖 了黄 金 生 产 的 全 过程 ; 涵 拥 有一 支具 备科 学 研究 、 品开发 、 艺设 计 、 目管 产 工 项 理 、 产经 营 等 综 合 性 高 素 质 、 水 准 的 技 术 队伍 生 高 目前 , 院 已发 展成 为一 家技 术转 让 、 该 技术 服务 、 术 技 咨 询为 主体 经 营 , 以新 工 艺 、 新技 术 、 产 品 、 材 料 新 新 的研发 为创 新经 营 , 以科 技 成 果 的工 程 化 、 业 化 为 产 目标经 营 的新 型高科 技企 业 。 5 年来 , 春 黄 金 研 究 院 共 完 成 各 类 科 研 课 0多 长
硫铁矿渣处理技术

硫铁矿渣处理技术摘要本文简述了硫铁矿渣对环境带来的危害,在建筑材料、提取有价贵金属、制备铁系产品等方面的综合利用与实践,并且总结了近十年内国内外对硫铁矿渣二次利用的研究进展。
关键词硫铁矿烧渣综合利用1、引言我国硫酸生产过程中生产的硫铁矿烧渣(又称硫酸渣、黄铁矿烧渣),是化学工业产生的主要固体废物之一。
每生产1吨硫酸会排放烧渣0.8~1.5吨的硫铁矿烧渣,全国每年将会排放约7x106吨,占化工废渣的1/3。
由于硫铁矿烧渣大多采用堆填处理,从而出现“晴日红尘飞,雨天红水流”的现象,不仅对环境造成了严重污染,而且堆填挤占土地,减少了耕地,对资源也是一种严重的浪费。
我国是资源相对不足的国家,在45种重要矿产资源中,有10多种不能满足需求。
目前,我国铁矿生产能力将比上世纪末减少10%以上[1],如能把硫铁矿烧渣加以利用,可大大缓解铁矿石的供应不足。
而且这两年铁价上涨,综合利用硫铁矿烧渣,不仅可以保护环境,也避免了资源的浪费,并且也可为企业赢得利润。
硫铁矿烧渣是一种非常有价值的二次资源。
国外对硫铁矿烧渣的利用非常重视,在综合利用方面取得了很好的成果。
日本硫铁矿烧渣的利用率为70%~80%,美国为80%~85%,德国和西班牙几乎为100%。
我国硫铁矿烧渣的利用率较低,还不到50%。
造成这一现象的一个重要原因是硫铁矿烧渣的质量不高。
比如铁品位低,硫和二氧化硅的含量高等。
而烧渣质量不高是由于焙烧原料硫铁矿质量不高造成的。
产品质量标准反应了国家的生产现状和生产水平。
我国将硫铁矿的标矿含硫量定为含硫35%,烧渣的铁品位在45%左右。
而国外对硫铁矿的要求为含硫量45%以上,如前苏联将硫铁矿的标矿含硫量定为48%,日本为49%~50%,美国为52%,西班牙要求48%以上,砷、氟含量一般均不大于0.05%。
2、国内外利用现状如何对硫铁矿烧渣综合利用,已引起国内外广泛的重视。
目前国内外对硫铁矿烧渣的综合利用已经进行了一些研究,下面具体罗列出了国内外对于硫铁矿烧渣的一些利用现状。
《国家鼓励发展的资源节约综合利用和环境保护技术》(国发改委科技部环保部2005第65号)

国家鼓励发展的资源节约综合利用和环境保护技术
2005年 第65号
为进一步推进资源节约综合利用和环境保护技术进步,加快新技术的推广应用, 引导投资方向,促进经济社会可持续发展,经各地方、国务院有关部门、有关行 业协会推荐,专家评审、评估和广泛征求意见,现将《国家鼓励发展的资源节约 综合利用和环境保护技术》260项技术予以公布。
国家鼓励发展的资源节约综合利用和环境保护技术(综合利用部分)
国家发展改革委
科技部 二0(五年十月二十八
国家环保总局
拥有炼铁废渣资源的企业,钢铁行业,实现从钢铁行业向非钢产业的转化,完成炼铁废弃物资源的综合利用。
国家鼓励发展的资源节约综合利用和环境保护技术(资源节约部分)
国家鼓励发展的资源节约综合利用和环境保护技术(环境保护部分)。
黄金提取和回收技术

D0101、黄金提取和回收技术1、从氰化含金废水中回收金的吸附装置2、氰化贵液碳纤维电积提金槽3、渗滤氰化提金的快速浸出附加装置4、黄金难选原生矿直接焙烧提金工艺5、一种从难浸金、银精矿中提出金、银的方法6、一种从含金银物料中分析金、银量的方法7、一种粗金提纯的方法8、一种难选冶金精矿的生物提金方法及专用设备9、提高含硫铜铅金银矿中银回收率的方法10、从贫金液、废金液中提取金的液膜及工艺11、一种粗金或合金快速溶解及提纯方法12、含砷等难处理金精矿的预处理方法13、碱硫氧压浸出提取金银方法14、两段细菌氧化提金方法15、一种以氰化提金废渣再提金的工艺方法16、由电解含金萃取有机相制备高纯金的方法17、从浮选金精矿焙砂废矿浆中回收金的方法18、从含金物中无氰浸提金的方法19、从铁矿中综合回收金的方法20、含金氯化液还原制取金的方法21、一种复用氰化浸金贫液的提金工艺22、一种从金银矿物中氰化提取金银的方法23、提高焙烧-氰化浸金工艺中银的回收率的技术方法24、加盐培烧一氰化法从含铜金精矿中综合回收金,银,铜25、从载金炭上解吸电解金的工艺方法26、含砷含硫难浸金矿的强化碱浸提金工艺27、控温掺氧式燃气热解炉分解原生金矿——氰化法提金工艺28、从难处理金精矿中提取金的方法29、混合助浸剂氰化浸金技术30、用于含金铜锌矿石氰化提金的制剂31、含金矿粉氰化提金添加剂32、用于提纯金的配方及其快速湿法金提纯方法33、一种湿法精炼高纯金的新工艺34、湿法协同氧化氰化浸出提金工艺新型助剂35、从铅阳极泥提取金、银及回收锑、铋、铜、铅的方法36、使用带胍官能物的萃取剂回收金的方法37、从金铜矿中提取铜铁金银硫的方法38、氨氧化炉废料回收铂金的方法39、从碱性氰化液中萃取金的方法40、氰化浸出中用混合氧化剂提取金的方法41、一种无氰解吸提金方法42、从难浸硫化物矿石、碳质矿石中提金的预处理方法及其专用设备43、从难浸矿石中提取金的方法44、难浸独立银矿浮选银精矿提取银和金的方法45、一种水氯法硫酸烧渣提金新工艺46、一种浸出液提金工艺47、无汞炼金方法及设备48、一种从废料中回收金的简易方法49、从铅阳极泥中回收银、金、锑、铜、铅的方法50、一种从含金的氰碴中提取金精矿的生产工艺51、从废炭中回收金的新工艺52、尾矿浆中金的回收53、无氰电铸K金制品的电铸液54、用溴酸盐和加合溴提取金的方法55、无氰电铸K金制品的方法56、高压釜内快速氰化提金方法57、金泥全湿法金、银分离新工艺58、首饰用金提纯方法59、从硫化物铜矿中浸提回收铜、银、金、铅、铁、硫的方法及设备60、用巯基乙酸(盐)和硫脲联合浸提金、银的方法61、一种从含金尾矿砂中提取金精矿砂的选矿工艺62、回收低浓度金的方法63、边磨边浸-液膜萃取提金工艺方法64、一种乳化液膜法提金及回收氰化钠工艺65、从废催化剂回收金和钯的方法及液体输送阀66、用石硫合剂提取金、银的方法67、低压热酸浸聚氨酯泡沫提金法68、萃取分离金和钯的萃取剂及其应用69、从金矿尾矿库溢流水中回收金的方法70、从铜阳极泥中回收金铂钯和碲71、一种无毒提金工艺方法72、氰化贵液用钢棉直接电解提金工艺73、一种焊锡阳极泥硝酸渣提取银和金的方法74、一种从重砂中回收细粒金的方法75、金选择吸附树脂合成及提取金的方法76、金、银分离方法77、一种提炼金属金的方法78、从难处理金矿中回收金、银79、载氯体氯化法浸提金和银80、氨法分离金泥中的金银81、从低品位金矿中回收金的工艺方法82、用复合萃取剂生产高纯金的方法83、金的回收方法84、催化氧化酸法预处理难冶炼金精矿85、一种从银阳极泥提金的新工艺86、硫脲铁浸法提金工业生产新工艺87、锑、金冶炼工艺方法88、酸浸聚氨酯泡沫提金法及装置89、从含金贫液中萃取金的方法90、一种从含金王水中提取金的方法91、低温硫化焙烧—选矿法回收铜、金、银92、从难熔含金含铁硫化物精矿中回收黄金的工艺93、氰化金泥的全湿法精炼工艺94、从难熔含金含铁的硫化物矿石中回收黄金95、吸附、浮选回收金的方法96、从含金含铁硫化物矿当中回收黄金的工艺97、高含量黄金样品中金含量的快速测定法98、从金矿中综合提取金、银、铜的工艺过程99、用巯基胺型螯合树脂回收电镀废液中的金和钯100、从铜电解阳极泥中提取金、银的萃取工艺101.用巯基胺型螯合树脂回收电镀废液中的金和钯102.从铜电解阳极泥中提取金、银的萃取工艺103.[ 200510020503 ]- 一种预处理金矿石和提取黄金的方法104.[ 03109562 ]- 在含砷金精矿中提取黄金的方法105.[ 03204697 ]- 贵金属提取用的保温电解槽106.[ 03240144 ]- 贵金属提取用的电解槽107.[ 02244217 ]- 难浸黄金矿石深度热压氧化处理设备108.[ 01134738 ]- 一种以氰化提金废渣再提金的工艺方法109.[ 200410006992 ]- 黄金分离方法及黄金分离装置110.[ 98814359 ]- 分离黄金微粒的方法和设备111.[ 93110180 ]- 首饰用金提纯方法112.[ 02139401 ]- 黄金难选原生矿直接焙烧提金工艺113.[ 200510033706 ]- 贵金属的无毒低成本提炼方法114.黄金冶炼方法综述115.哈国苏兹达尔金矿利用生物氧化技术提炼黄金116.从镀金废料中回收黄金的扩大试验研究117.萃取法精炼黄金的研究和工业实践118.改进工艺操作条件提高金冶炼回收率及产品纯度119.萃取法精炼黄金技术在矿山生产中的应用120.细菌湿法浸矿技术在黄金冶炼中的应用121.黄金冶炼厂含氰废水中氰化物的分析方法研究122.黄金冶炼厂酸浸系统结晶物形成机理研究123.黄金精炼工艺特点分析及选择124.黄金冶炼厂污染源治理技术125.国内黄金矿山炼金炉综述126.浅谈我国黄金精炼技术与工艺127.烟台市黄金冶炼厂金精矿生物氧化—氰化提金工艺128.黄金湿法冶炼新型无毒浸出剂试验研究129.黄金冶炼厂污染源治理技术130.松衬钛制容器在黄金生产中的应用131.18K金镀液的研制及黄金回收与精炼132.钛设备在黄金矿山湿法提金工艺中的应用实践与研究133.以焙烧-湿法工艺从含金废料中回收金134.黄金选冶技术的现状与发展135.黄金精炼提纯工艺研究与生产实践136.降低黄金冶炼厂氰渣金品位的研究137.湿法黄金精炼提纯工艺试验研究138.黄金色铜粒子制取技术的试验研究139.黄金冶炼设备的现场管理140.含铜金精矿金铜分离浮选试验研究141.斑岩铜-金矿和难处理含金硫化矿中金的浮选研究142.斑岩铜金矿和难选含金硫化矿中金的浮选性能研究(一) 143.黄金浸出剂的分子设计研究(Ⅰ)144.黄金提炼新工艺145.中原黄金冶炼厂技术改进评述及流程改进意见146.黄金矿山合质金锭熔炼技术与实践147.黄金精炼148.从金银多金属硫化物矿中提取黄金的初步试验149.含金烧渣采用炭浆法提金工艺的研究150.采用TPG冶炼技术提高冶炼回收率的生产实践151.黄金冶炼炉述评152.山渣核活性炭在提炼黄金中的应用研究153.有色冶炼中的黄金回收154.中频炉冶炼金泥新工艺及其在黄金生产中的应用155.黄金冶金技术的研究进展与前景156.国外黄金选冶生产技术发展趋势157.美国黄金选冶最新技术与工艺158.招远黄金冶炼厂工艺技术及特点159.湿法从氰化金泥中提取金、银、铜、铅工艺试验研究160.从含金含铁硫化物矿当中回收黄金的工艺161.用活性碳纤维回收、提取黄金162.从砂砾中提取氯金酸(氯化金)的工艺163.金选择吸附树脂合成及提取金的方法164.黄金分选机165.控温掺氧式燃气热解炉分解原生金矿——氰化法提金工艺166.氯浸法从硫酸烧渣中提取黄金新工艺167.采用液膜法从氰化浸出矿浆中提金的可行性研究探讨168.从砂砾中提取氯金酸(氯化金)的工艺169.用活性碳纤维回收、提取黄金170.用含偕胺肟基材料还原提取黄金171.磁性炭及以其为吸附剂的黄金提取方法172.从氰化贵液中直接电解提取黄金的技术173.一种回收提取黄金的方法174.黄金提取方法的环境负荷效用指数及定量评估探讨175.黄金提取新工艺问世176.金矿尾砂提取黄金177.堆浸法从剥离贫矿石中提取黄金的工业试验178.新型黄金浮选剂的合成及浮选性能研究179.黄金提取与环境保护180.黄金提取技术研究进展181.从含铜铅金精矿中提取金提的工艺方法182.生物氧化提取黄金技术的发展现状及其应用183.黄金提取工艺综述184.从油箱中提取黄金185.国内外堆浸提金技术的发展与实践186.从废液中提取黄金:HJ-1型黄金提取机回收报告187.从金银多金属硫化物矿中提取黄金的初步试验188.提金废渣的综合利用189.v黄金开发技术的现状,趋势和建议190.难浸金矿石的预处理:Ⅱ.焙烧-氰化法提取金的研究191.用磁选和磁流体分选法从重选精矿中提取黄金192.细菌提取黄金193.国外黄金氰化浸出的发展状况194.v黄金提取冶金的过去,现在和将来195.黄金提取技术的发展和展望196.黄金提取技术的现状和趋势197.黄金提取工艺的进展198.从不同矿物中提取黄金的技术199.状态图在黄金提取中的应用200.HW树脂-TMB络合吸附-从氰化液和氰化矿浆中提取黄金的新方法201.黄金选冶技术综述202.从含金废料中回收金与金的提纯203.氯氨净化法黄金提纯工艺204.萃取法精炼黄金技术在矿山生产中的应用205.一种湿法提纯黄金工艺206.黄金提纯的酸溶设备207.黄金提纯的过滤与装置简介208.氯氨净化法黄金提纯技术209.从含金废料中回收金与金的提纯210.化学提纯法生产1^#金研究211.氯化提金方法与工艺的研究和应用212.黄金难选原生矿直接焙烧提金工艺213.某含砷金矿石提高回收率研究214.从难熔含金含铁的硫化物矿石中回收黄金115.萃取并回收黄金的方法216.提金尾渣的再利用214.氨法分离金泥中的金银218.废旧手机中金钯银的回收219.黄金电镀废液中的黄金萃取方法220.电子垃圾简单的产业链221.废旧手机暗藏黄金222.黄金矿山尾矿的综合利用223.从含金含铁硫化物矿中回收黄金的工艺224.从难熔含金含铁硫化物精矿中回收黄金的工艺225.黄金回收工艺过程226.青海省滩间山金矿堆浸尾矿提金工艺试验研究227.尾矿浆中金的回收228.氰化提金--锌丝置换过程中铅盐应用改进229.贵州省丹寨县四相厂难选汞金矿回收黄金工艺流程研究230.提高尾矿黄金回收的新技术231.黄金回收技术232.湿法提金中的离子交换工艺233.便于迁移的黄金回收厂234.多金属矿石精矿中黄金的回收235.黄金回收厂的工艺设备236.黄金回收十法237.从硫精矿烧渣中回收黄金的探讨238.我国有色金属及黄金的综合回收技术239.均质阴离子交换膜在电解提纯金中的应用240.黄金堆浸工艺的设计与应用241.提高某选厂黄金选矿回收率的生产实践242.应用高效捕收剂Y89提高黄金回收率的研究243.从首饰垃圾回收金的研究244.炭浆法提金工艺理论回收率计算245.高效捕收剂Y-89--黄药家族的新成员246.从废液中提取黄金:HJ-1型黄金提取机回收报告247.用重选方法回收微细粒金248.从矿石中萃取金的综述249.提高黄金回收率技术的新进展250.金精矿无氰提金新工艺的研究251.尾矿中流失黄金的回收252.黄金回收技术253.提高龙水选厂黄金选矿回收率的生产实践254.镀金件退除与回收255.改变现行生产流程提高张全庄金矿黄金生产回收率256.试论油团聚法回收黄金工艺257.从黄金尾矿筛析看提高黄金回收率的方向258.硫脲法从电镀污泥中提金工艺研究259.ICP-AES测定电镀污泥中的金和钯260.铜镍电镀污泥的湿法冶金试验261.电镀重金属污泥的水泥固化处理试验研究262.电镀重金属污泥的处理及综合利用现状263.电镀重金属污泥的水泥固化/稳定化处理264.电镀重金属污泥的处理及其铁氧体化综合利用265.南京沿江冶金废渣利用厂266.利用冶金工业废渣作水泥高活性混合材和混凝土高活性掺合料是冶金渣高价值利用最有效的途径267.招远洪伟变金矿废渣为宝268.工业废渣在难处理金矿固化焙烧中的应用269.一种以氰化提金废渣再提金的工艺方法270.利用南钢冶金废渣生产多彩砖271.冶金废渣的综合利用技术272.太钢冶金废渣治理之我见273.冶金废渣在地基处理工程中的应用274.上杭紫金山金矿废水废渣的处理及生态环境影响275.有色金属冶炼废渣综合治理276.冶金废渣地砖277.大板金矿尾矿堆浸废渣治理278.利用冶金工业废渣制备建材玻璃279.金矿废水和尾矿中氰化物的处理研究进展280.硫代硫酸盐法回收某金矿废水池污泥中金的研究281.金矿堆浸中废水治理的工艺研究282.水淬渣-累托石混合吸附剂处理含Cu^2+冶金废水的研究283.冶金废水悬浮物分析中需要注意的几个问题284.氰化浸金废水零排放工艺的实践及其改进的探讨285.锌冶金废水综合治理实践286.稀土湿法冶金废水处理287.稀土湿法冶金废水处理288.混凝法处理铝合金废水所得污泥的再利用研究289.新型反渗透工艺零排放处理冶金废水290.ICP-AES法同时测定冶金废水中多种无机元素291.环保及三废处理:金矿氰化提金废水处理技术292.镍冶金废水处理工艺研究293.水芹菜对黄金废水的净化与富集作用研究294.多花黑麦草对黄金废水净化与富集的研究295.紫金山金矿矿渣边坡治理与植被恢复技术296.用木屑粉末从含金矿渣(炉渣)中回收金297.掺加矿渣的土壤聚合物对重金属的固化298.冶金矿渣提升机专用轴承设计299.利用金尾矿渣生产烧结空心砖的试验300.金矿尾矿渣及其污染土壤中氰化物的分布及自然降解301.张家口金矿治理废弃矿渣山实践302.金矿渣场废水对地面水环境的影响评价303.张家口金矿走出一条开发性综合治理废弃矿渣的新路子304.难浸金矿废矿渣中金的分析与提取305.电镀污泥焚烧后的灰渣分析306.清查电镀污泥307.电镀污泥综合利用技术308.从金属废料中回收金,银,铂的二步法309.氯化法处理氰化金泥310.镍铬合金表面金泥涂层耐磨性的实验研究311.氰化金泥低温焙烧预处理冶炼工艺的研究312.氰化金泥的全湿法精炼工艺313.氨法分离金泥中的金银314.从氰化金泥中提取金银新工艺的试验研究315.粉末冶金泥浆泵缸套材料的研究316.氰化金泥综合回收新工艺317.含铜铅金泥的冶炼实践318.火法氯化替代硝酸分银精炼金泥319.氰化金泥低温焙烧预处理--全温法多金属冶炼工艺研究与应用320.氰化金泥全控电湿法直接精炼新工艺321.金泥冶炼新方法322.酸处理金泥产生硫化氢及氰化氢污染浅析323.直接灰吹法测定金泥中的金和银324.全泥氰化低品位金泥的冶炼实践325.金泥(金矿石)中金的测试研究326.从电积金泥中提金的生产实践327.完善工艺操作,提高金泥品位,增加经济效益328.金泥控电氯化除铜铅富集贵金属329.掘金:电子垃圾提炼黄金330.[ 200610034682 ]- 一种从黄金尾矿中提取黄金的方法331.[ 200510021755 ]- 一种提取黄金的方法332.[ 200610017035 ]- 树脂法提纯黄金工艺333.[ 200510018000 ]- 一种黄金湿法提纯工艺334.[ 200610013172 ]- 镁合金泥板及其生产方法335.[ 00254265 ]- 含金贵液的电解设备336.[ 99115343 ]- 含金氯化液还原制取金的方法337.[ 96116082 ]- 一种从金泥中提取有价金属的工艺方法338.[ 93105978 ]- 金泥全湿法金、银分离新工艺339.[ 88108466 ]- 氨法分离金泥中的金银340.[ 85100106 ]- 氰化金泥的全湿法精炼工艺341.[ 200610050002 ]- 从电镀污泥中回收有价金属的方法342.微区X射线荧光黄金首饰分析装置343.X射线荧光光谱分析互标法无损检测黄金饰品344.低能γ源X荧光光谱分析法测定黄金饰品中的含金量345.黄金饰品中金含量的X-荧光能谱分析346.黄金制品中Au含量的测定方法347.实心黄金饰品中金含量的密度法测定348.高含量黄金样品中金含量的快速测定法349.高含量黄金样品中金含量的快速测定法350.一种测定固体密度和黄金成色的方法及黄金秤351.黄金饰品质量的X射线荧光光谱无损测定352.无损测定黄金饰品中的金353.用流体静力学称量法测定黄金饰品中金的含量354.电子探针X射线能谱法测定黄金饰品的成色355.密度法无损测定黄金饰品中金量的原理及影响因素讨论356.波长色散X射线荧光光谱法测定黄金饰品含金量357.火焰原子吸收光谱法测定黄金中铜,铁,镍,镉358.比重法测定黄金首饰中金的含量详细内容请到天农高科网查看。
难处理金矿强化氰化提金的发展
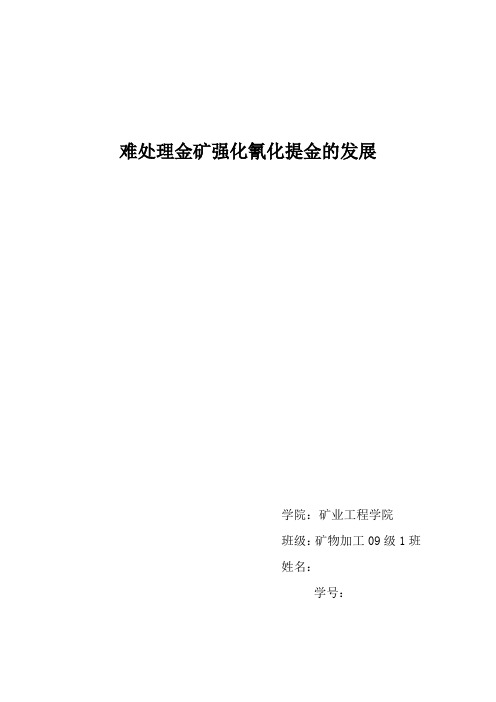
难处理金矿强化氰化提金的发展学院:矿业工程学院班级:矿物加工09级1班姓名:学号:难处理金矿强化氰化提金的发展氰化法仍是目前普遍采用的提金方法, 但对于难处理金矿, 如何提高浸出率, 缩短浸出时间,降低氰化物消耗依然是各国研究者不断研究探索的问题。
从难处理金矿中提取金, 事先都需要进行预处理, 相应的预处理方法有焙烧法、加压氧化法、细菌预氧化法与化学药剂氧化法等。
近几年这些预处理方法都得到了发展, 有些并得到了工业应用。
焙烧预处理法尽管存在成本高、会污染环境的可能性, 但只要条件控制得好, 还是可以取得较好的技术经济指标的。
王云针对我国西部某含砷含碳含锑微细粒浸染型难选金矿, 采用原矿直接焙烧预氧化- 焙砂再磨- 氰化工艺进行小型试验, 在小型试验的基础上进行了500t/d 规模的焙烧预氧化装置设计和生产试运行, 1年多的试生产指标表明金的浸出率平均达到了70%以上,较该矿石直接氰化金浸出率12.65%相比有了较大的提高;同时, 在无任何化学添加剂的状况下,矿石焙烧固砷率83%, 固硫率67% , 基本上实现了自洁焙烧。
罗德生采用焙烧- 氰化工艺技术处理, 使微粒浸染型难选冶金矿石得到充分利用, 当粒度为2~ 0mm, 焙烧温度为650~ 750 e ,焙烧时间为3-4小时时, 其浸出率可达85%以上。
吴海国在控制焙烧条件, 使金精矿中As、Sb、S、C有效脱除, 其中的金表露。
焙烧矿磨细至0.041mm以下86%以上,采用常规氰化浸出,金浸出率达92.13%,砷以As2O3形式回收。
袁朝新等对镇沅含砷、锑、碳难处理金精矿直接氰化金浸出率小于10% , 采用常规焙烧-焙砂氰化提金工艺金浸出率仅达到73.2% , 而采用先行除锑, 再焙烧脱除硫、碳、砷的提金工艺方案, 金氰化浸出率达到90. 4%。
邱美珍等通过对广西六梅金矿、明山金矿、金牙金矿含高砷高硫难浸金矿石进行固化焙烧- 氰化提金的试验研究, 获得了砷、硫固定率分别为99.03%、97.04%、97.04%,金浸出率92.35% 的较好指标。
硫铁矿烧渣提取贵重金属金、银
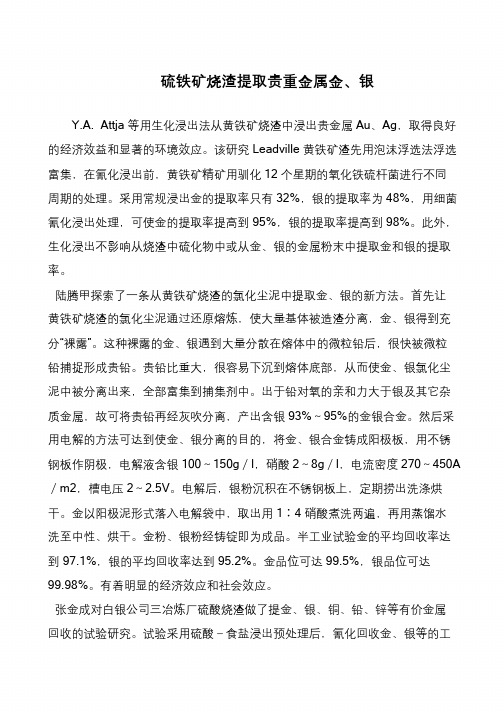
书山有路勤为径,学海无涯苦作舟硫铁矿烧渣提取贵重金属金、银Y.A. Attja 等用生化浸出法从黄铁矿烧渣中浸出贵金属Au、Ag,取得良好的经济效益和显著的环境效应。
该研究Leadville 黄铁矿渣先用泡沫浮选法浮选富集,在氰化浸出前,黄铁矿精矿用驯化12 个星期的氧化铁硫杆菌进行不同周期的处理。
采用常规浸出金的提取率只有32%,银的提取率为48%,用细菌氰化浸出处理,可使金的提取率提高到95%,银的提取率提高到98%。
此外,生化浸出不影响从烧渣中硫化物中或从金、银的金属粉末中提取金和银的提取率。
陆腾甲探索了一条从黄铁矿烧渣的氯化尘泥中提取金、银的新方法。
首先让黄铁矿烧渣的氯化尘泥通过还原熔炼,使大量基体被造渣分离,金、银得到充分“裸露”。
这种裸露的金、银遇到大量分散在熔体中的微粒铅后,很快被微粒铅捕捉形成贵铅。
贵铅比重大,很容易下沉到熔体底部,从而使金、银氯化尘泥中被分离出来,全部富集到捕集剂中。
出于铅对氧的亲和力大于银及其它杂质金属,故可将贵铅再经灰吹分离,产出含银93%~95%的金银合金。
然后采用电解的方法可达到使金、银分离的目的,将金、银合金铸成阳极板,用不锈钢板作阴极,电解液含银100~150g/l,硝酸2~8g/l,电流密度270~450A /m2,槽电压2~2.5V。
电解后,银粉沉积在不锈钢板上,定期捞出洗涤烘干。
金以阳极泥形式落入电解袋中,取出用1∶4 硝酸煮洗两遍,再用蒸馏水洗至中性、烘干。
金粉、银粉经铸锭即为成品。
半工业试验金的平均回收率达到97.1%,银的平均回收率达到95.2%。
金品位可达99.5%,银品位可达99.98%。
有着明显的经济效应和社会效应。
张金成对白银公司三冶炼厂硫酸烧渣做了提金、银、铜、铅、锌等有价金属回收的试验研究。
试验采用硫酸-食盐浸出预处理后,氰化回收金、银等的工。
《国家鼓励发展的资源节约综合利用和环境保护技术》(国发改委 科技部 环保部 2005第65号)
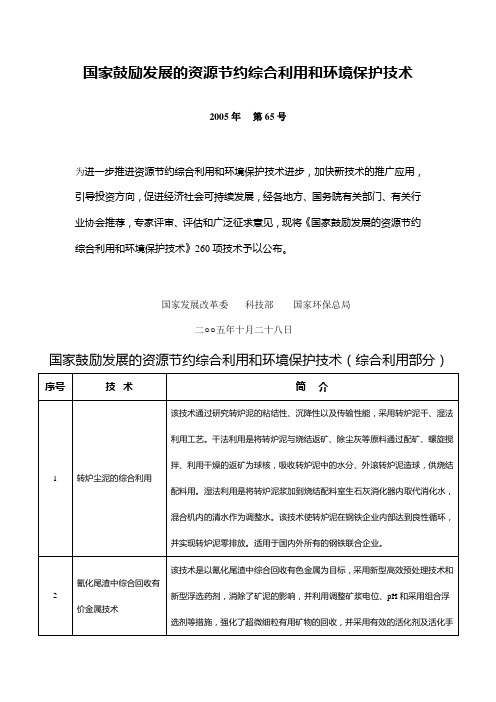
国家鼓励发展的资源节约综合利用和环境保护技术
2005年第65号
为进一步推进资源节约综合利用和环境保护技术进步,加快新技术的推广应用,
引导投资方向,促进经济社会可持续发展,经各地方、国务院有关部门、有关行
业协会推荐,专家评审、评估和广泛征求意见,现将《国家鼓励发展的资源节约
综合利用和环境保护技术》260项技术予以公布。
国家发展改革委科技部国家环保总局
二○○五年十月二十八日
国家鼓励发展的资源节约综合利用和环境保护技术(综合利用部分)
备注:国家鼓励发展的综合利用技术按所属行业排序,技术排名不分先后。
国家鼓励发展的资源节约综合利用和环境保护技术(资源节约部分)
备注:国家鼓励发展的资源节约技术按所属行业排序,技术排名不分先后。
提取黄金方法资料目录集

1、一种从难处理金矿中提金的方法2、一种高盐、氨氮和难处理的黄金冶炼厂废水的处理方法3、一种黄金矿山含氰废水系统处理方法4、黄金矿山氰化废渣淋洗溶液处理方法5、一种黄金矿山含氰废水综合治理方法6、一种黄金矿山氰化废渣淋洗溶液处理方法7、一种环保金矿选矿剂的生产系统8、一种新型环保提金剂及其制备方法9、一种高盐、氨氮和难处理的黄金冶炼厂废水的处理方法10、一种黄金矿山含氰废水系统处理方法11、一种黄金矿山含氰废水综合治理方法12、一种含锑复杂难浸金矿的生物提金工艺及所用微生物13、一种黄金矿山含氰废水综合处理方法14、一种黄金矿山含氰废水治理方法15、一种从含金炼汞尾渣中回收黄金的方法16、一种含铁金矿氰化尾矿同步回收金和铁17、支撑液膜技术回收工业废水或矿产冶炼浸提液中贵重金属1-718、一种从电子废弃物中直接电解回收金属的方法1-719、电子废弃物分级电解回收方法20、氯氨净化法黄金提纯工艺21、一种使用可控~。
脉。
冲~辅~》助~电ji的黄金提纯方法22、超微细浸染型金矿多段式固硫固砷控温焙烧工艺及设备23、一种以氰化提金废渣再提金的工艺方法24、高砷高硫金精矿脱除砷硫元素25、含砷硫等难处理金矿砂的超声预处理方法26、一种难选冶金精矿的生物提金方法及专用设备27、在含砷金精矿中提取黄金的方法及其系统28、一种从难浸金银精矿中提出金银的方法29、一种粗金提纯的方法30、一种非氰化提金方法31、回收金的方法32、用氯化物浸析和萃取回收金属的方法33、难浸金精矿的生物氧化——硫脲树脂矿浆法提金工艺34、黄金分离方法及黄金分离装置35、一种高砷金矿的提金工艺36、从炼锑废渣回收金银铂贵金属的工艺37、一种黄金。
湿。
法提纯工艺38、从含铂族金属矿石中提取铂族金属的工艺39、一种预处理金矿石和提取黄金的方法40、一种提取黄金的方法41、金属萃取提取剂及其方法和用途42、回收金的方法43、包括精细研磨制浆和氧化的用于金属如金和铂的提取方法44、含砷锑难处理金矿石的。
硫铁矿渣处理技术
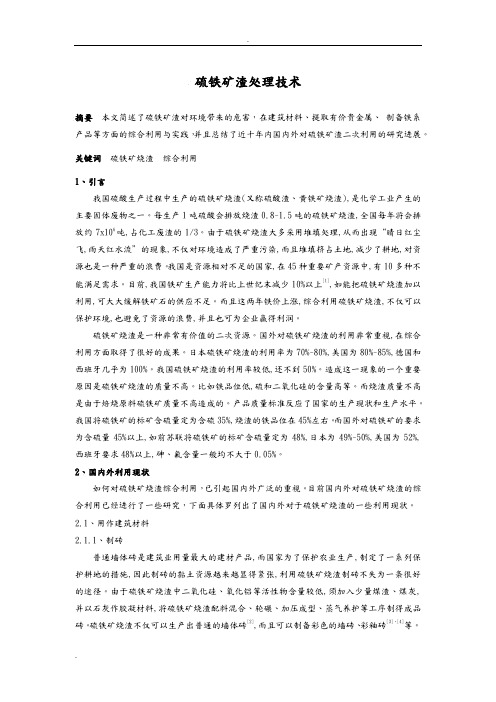
硫铁矿渣处理技术摘要本文简述了硫铁矿渣对环境带来的危害,在建筑材料、提取有价贵金属、制备铁系产品等方面的综合利用与实践,并且总结了近十年内国内外对硫铁矿渣二次利用的研究进展。
关键词硫铁矿烧渣综合利用1、引言我国硫酸生产过程中生产的硫铁矿烧渣(又称硫酸渣、黄铁矿烧渣),是化学工业产生的主要固体废物之一。
每生产1吨硫酸会排放烧渣0.8~1.5吨的硫铁矿烧渣,全国每年将会排放约7x106吨,占化工废渣的1/3。
由于硫铁矿烧渣大多采用堆填处理,从而出现“晴日红尘飞,雨天红水流”的现象,不仅对环境造成了严重污染,而且堆填挤占土地,减少了耕地,对资源也是一种严重的浪费。
我国是资源相对不足的国家,在45种重要矿产资源中,有10多种不能满足需求。
目前,我国铁矿生产能力将比上世纪末减少10%以上[1],如能把硫铁矿烧渣加以利用,可大大缓解铁矿石的供应不足。
而且这两年铁价上涨,综合利用硫铁矿烧渣,不仅可以保护环境,也避免了资源的浪费,并且也可为企业赢得利润。
硫铁矿烧渣是一种非常有价值的二次资源。
国外对硫铁矿烧渣的利用非常重视,在综合利用方面取得了很好的成果。
日本硫铁矿烧渣的利用率为70%~80%,美国为80%~85%,德国和西班牙几乎为100%。
我国硫铁矿烧渣的利用率较低,还不到50%。
造成这一现象的一个重要原因是硫铁矿烧渣的质量不高。
比如铁品位低,硫和二氧化硅的含量高等。
而烧渣质量不高是由于焙烧原料硫铁矿质量不高造成的。
产品质量标准反应了国家的生产现状和生产水平。
我国将硫铁矿的标矿含硫量定为含硫35%,烧渣的铁品位在45%左右。
而国外对硫铁矿的要求为含硫量45%以上,如前苏联将硫铁矿的标矿含硫量定为48%,日本为49%~50%,美国为52%,西班牙要求48%以上,砷、氟含量一般均不大于0.05%。
2、国内外利用现状如何对硫铁矿烧渣综合利用,已引起国内外广泛的重视。
目前国内外对硫铁矿烧渣的综合利用已经进行了一些研究,下面具体罗列出了国内外对于硫铁矿烧渣的一些利用现状。
硫酸工艺和设备选择中的节能问题研究
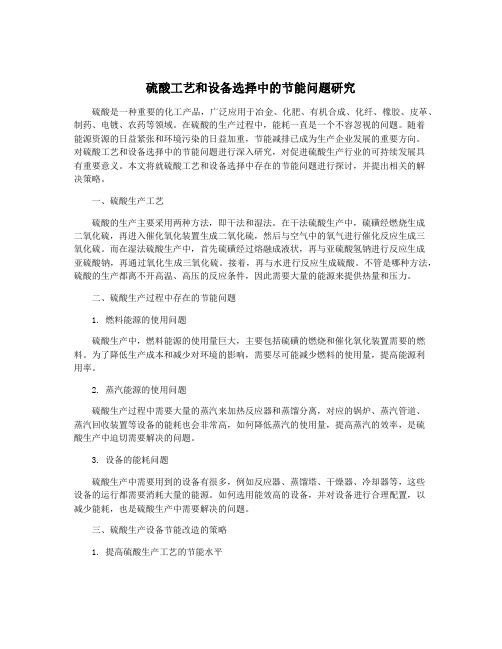
硫酸工艺和设备选择中的节能问题研究硫酸是一种重要的化工产品,广泛应用于冶金、化肥、有机合成、化纤、橡胶、皮革、制药、电镀、农药等领域。
在硫酸的生产过程中,能耗一直是一个不容忽视的问题。
随着能源资源的日益紧张和环境污染的日益加重,节能减排已成为生产企业发展的重要方向。
对硫酸工艺和设备选择中的节能问题进行深入研究,对促进硫酸生产行业的可持续发展具有重要意义。
本文将就硫酸工艺和设备选择中存在的节能问题进行探讨,并提出相关的解决策略。
一、硫酸生产工艺硫酸的生产主要采用两种方法,即干法和湿法。
在干法硫酸生产中,硫磺经燃烧生成二氧化硫,再进入催化氧化装置生成二氧化硫,然后与空气中的氧气进行催化反应生成三氧化硫。
而在湿法硫酸生产中,首先硫磺经过熔融成液状,再与亚硫酸氢钠进行反应生成亚硫酸钠,再通过氧化生成三氧化硫。
接着,再与水进行反应生成硫酸。
不管是哪种方法,硫酸的生产都离不开高温、高压的反应条件,因此需要大量的能源来提供热量和压力。
二、硫酸生产过程中存在的节能问题1. 燃料能源的使用问题硫酸生产中,燃料能源的使用量巨大,主要包括硫磺的燃烧和催化氧化装置需要的燃料。
为了降低生产成本和减少对环境的影响,需要尽可能减少燃料的使用量,提高能源利用率。
2. 蒸汽能源的使用问题硫酸生产过程中需要大量的蒸汽来加热反应器和蒸馏分离,对应的锅炉、蒸汽管道、蒸汽回收装置等设备的能耗也会非常高,如何降低蒸汽的使用量,提高蒸汽的效率,是硫酸生产中迫切需要解决的问题。
3. 设备的能耗问题硫酸生产中需要用到的设备有很多,例如反应器、蒸馏塔、干燥器、冷却器等,这些设备的运行都需要消耗大量的能源。
如何选用能效高的设备,并对设备进行合理配置,以减少能耗,也是硫酸生产中需要解决的问题。
三、硫酸生产设备节能改造的策略1. 提高硫酸生产工艺的节能水平对于干法和湿法硫酸生产工艺,可以采用新型催化剂、反应器的优化设计等方式来提高反应效率,从而减少能源和原料消耗。
黄金 冶炼 方法

黄金冶炼方法黄金冶炼产品为成品金。
冶炼有粗炼和精炼之分。
精粗炼产品为合金(俗称合质金),我国黄金矿山就地产金多为合质金,直接交售给银行。
黄金富矿块和各种金精矿运往有色冶炼厂加工提炼成品金(俗称含量金)。
建国40年来,黄金冶炼和综合回收发展较快,冶炼技术和工艺装备水平不断提高,冶炼成本日益降低,促进了黄金生产的发展。
1.黄金矿山金的就地冶炼70年代以前,黄金生产处于初步发展阶段,除少数矿山开始采用氰化法提金工艺外,矿山就地产金主要是从砂矿重选所得的自然金和精矿的冶炼,以及混汞法提金工艺产出的汞膏为原料就地冶炼,就地产金量仅占总产量的30%,70%的金依靠有色冶炼厂回收。
1970年以后,黄金生产逐步发展,氰化法提金工艺日益广泛地应用,矿山就地产金量日渐增多,1985年矿山成品金的产量已占全国黄金产量的70%,选厂产出的精矿产品大部分就地氰化冶炼产出成品金。
矿山就地冶炼多数采用传统的坩埚法熔炼,因生产工艺和处理物料性质不同,所产合质金的含金量也不一样,直接交售银行因含金量不高或含银不计价等原因,有的矿山为提高质量和经济效益采取了化学法除杂再次熔炼或电解法进行金银分离精炼。
焦家金矿曾于1984年试验采用水冶新工艺,将氰化金泥经电氯化除去贱金属(用水溶液氯化法提金和氨浸法提银)获得含金品位99.9%成品金和含银99.9%的银锭,金泥中的铜、铅也同时回收(用湿法处理金泥有被推广的趋势)。
招远金矿成功地研制出一种Φ1.5×1.8m的转炉熔炼金泥,取代了过去的坩埚熔炼,降低了成本,改善了劳动条件。
这一方法在山东新城金矿等矿山普遍推广应用,效果较好。
招远冶炼厂是我国自行研究、设计和建设的第一家黄金冶炼厂,专门处理多金属硫化物金精矿,以提取黄金为主,同时回收银、铜、铅、硫等,是综合冶炼、化工为一体的新型企业。
招远冶炼厂的建成投产,为我国黄金生产冶炼工艺填补了一项技术空白,采用焙烧-酸浸-(盐浸)-氰化浸出联合工艺,解决了长期以来采、选、冶之间的生产矛盾,解决了金精矿长途外运损失(年损失率2%~3%),运输压力大和综合利用问题。
硫酸生产工艺及通用机械设备[1]
![硫酸生产工艺及通用机械设备[1]](https://img.taocdn.com/s3/m/ba03ac59804d2b160b4ec037.png)
硫酸生产工艺及通用机械设备[1].txt﹃根网线''尽赚了多少人的青春い有时候感动的就是身边微不足道的小事。
﹎破碎不是最残酷的最残酷的是踩着这些碎片却假装不疼痛固执的寻找﹎将来就算我遇见再怎么完美的人,都有一个缺点,他不是你,_____下辈子要做男生,娶一个像我这样的女生。
本文由qhdxlyq贡献pdf文档可能在WAP端浏览体验不佳。
建议您优先选择TXT,或下载源文件到本机查看。
产业与市场GM论坛 GM Forum硫酸生产工艺及通用机械设备东华工程科技股份有限公司副总工程师王颖一、前言硫酸是一种重要的基本化工原料,广泛使用于各工业部门,硫酸的产量常常被用作衡量一个国家工业发展水平的标志。
硫酸主要用于生产磷肥。
合成纤维、涂料、洗涤剂、制冷剂、饲料添加剂、石油精炼、有色金属冶炼,钢铁、医药和化学工业等,也都离不开硫酸。
随着我国高浓度磷复肥和有色金属工业的发展,我国的硫酸工业也得到了迅速发展。
2003年达到创记录的3 371万t,产量超过美国位居世界第一。
2006年我国硫酸产量5 044万t,同比增长9.0%,其中硫磺制酸产量2 233万t,同比增长13.1%;冶炼烟气制酸产量1 163万t,同比增长18.6%;硫铁矿制酸产量1 593万t,同比减产 1.2%;其他原料制酸产量55万t,同比减少6.9%。
截止到2007年9月,全国硫酸累计产量3 957万t,同比增长 10.2%。
蒸汽。
2)S O 2的第二个来源是焙烧硫化物矿石产生的烟气(硫铁矿制酸或冶炼烟气制酸)2F e S 2+5O2+1/3O2→ 2/3F e3O4+4S O2+Q 或2F e S2+5O2+1/2O2→F e2O3+4S O2+Q ,反应放出的高温位热能同样用于生产中高压蒸汽。
3)磷石膏(石膏)焦炭还原煅烧反应:2C a S O4+C →2CaO+2SO2+CO2。
4 )硫化氢与空气燃烧反应: H 2S + O 2+ 1 / 2 O 2→ H2O+SO2+Q 。
- 1、下载文档前请自行甄别文档内容的完整性,平台不提供额外的编辑、内容补充、找答案等附加服务。
- 2、"仅部分预览"的文档,不可在线预览部分如存在完整性等问题,可反馈申请退款(可完整预览的文档不适用该条件!)。
- 3、如文档侵犯您的权益,请联系客服反馈,我们会尽快为您处理(人工客服工作时间:9:00-18:30)。
硫酸烧渣提金新工艺和新设备
一.硫酸烧渣提金技术现状与研究方向
目前我国黄金资源的利用明显出现勘探跟不上生产要求的局面,制约着我国黄金产量的提高,与此同时,从含金废料中和难选矿石中回收金的技术和扶持政策却不够理想,这部分金资源尚未得到充分的利用.含金硫酸烧渣回收金技术急待开发.
我国每年产生含金硫酸烧渣几十万吨,目前仅大于3克/吨的烧渣得以利用.每年仅有7.5万吨的处理能力,其余烧渣或废崐弃或以十几元/吨的价格出售给水泥厂做原料,•所含黄金白白流失,十分可惜.
从国内外的技术文献看,从烧渣中回收金的技术也只限于氰化工艺,重选、浮选、磁选、硫脲工艺等均处于研究阶段.
现时的氰化工艺仅适合处理金品位高于2.5克/•吨的硫酸烧渣,品位再低则利润太低,投资难以在短期内收回,因此尽管具有较好的社会效益,但经济效益不明显而无建提金厂的积极性;堆浸法虽然能使生产成本降低,•但不能连续生产而且冬季无法生产,因此这种工艺也难以推广;重选、•磁选和浮选均能崐回收烧渣中的一部分金,但回收率不如氰化法高而且从产生的精矿中再回收金时回收率不理想,也难以推广.•硫脲法药剂成本高且浸出条件不易控制,溶液中金的回收尚满意的方法,•还处在探索阶段,距工业应用尚远.
我们认为,影响从烧渣中提金的主要因素有两个,•一是投资过大、二是生产成本过高.如果能解决这两个问题,•低品位硫酸烧渣提金技术将被顺利推广.
通过对我国推广使用的氰化法工艺进行研究,发现该工艺存在如下问题:
1.长春黄金研究院的多年研究证明,硫酸烧渣不须再磨氰化浸出率就能保证,采用磨矿工段的目的仅仅是为了保证氰化反应时矿浆被搅拌均匀,不沉槽.磨矿工段投资达40余万元,生产成本高达15元/吨,如果能通过其它办法砍掉该工段,氰化法的崐投资和生产成本会大幅度下降.
2.由于靠排放磨矿后浓密机溢流进行洗矿--•除去烧渣中溶出的铁铜
等杂质,在磨矿过程中就不能加氰化物,•因此贫液也不能全部循环使用,贫
液处理后排放不但使生产成本提高,•还产生环境污染问题,在一些环境质量要求高的地区,•环保部门就不会批准建氰化厂.
3.不少硫酸厂建在城市内•,无足够的场地建较大的尾矿库.采用现在的氰化工艺时,无论用锌粉置换还是用炭浆法,•都必须过滤氰尾分离出废渣,
用机动车把渣运到它处.•过滤工段增加了投资,又因磨矿使渣粒度变细增加了过滤难度、增加了生产成本.
4.采用锌粉置换将使贫液中锌浓度不断增加,恶化浸出条件,造成金回收率降低;由于烧渣硬度大,用炭浆法炭磨损大,金流失多,生产成本增高.
5.氰化法的最大不足不在于反应时间太长,一般至少要16小时,这就要求建很大体积的浸出槽,投资增大、电耗增加,厂房面积增加.
综上所述,从低品位硫酸烧渣中提金必须开发新的浸出技术或新的工艺,降低投资和成本.•其具体研究内容包括以下几个途径:
1.使用新的浸出设备,不磨矿即可保证浸出反应顺利进行.•而且浸出电耗不增加或增加较少.
2.使用浸出速度快的浸出方法,浸出时间仅几小时或更短.•可增加搅拌
强度来保证浸出效果,由于反应时间短,•单位电耗也不会增加很多.
3.采用贫液全循环工艺,不外排废水,节约废水处理费用,节约浸出药剂.
4.用固定床吸附法从贵液中回收金,不设洗涤工段或炭浆工段,浸后直接过滤,提高贵液金浓度以使吸附剂上金品位提高,•减少设备投资和生产成本.
通过大量的研究和试验,选择了水氯法工艺.•小试结果表明,浸出率比氰化法高,•其原因是氰化过程中烧渣颗粒上金表面产生阻碍金浸出和扩散的膜.均由烧渣的性质决定--氰尾渣制酸时的焙烧温度致关重要.
二.新工艺和新设备的技术经济指标
1.技术工艺指标
金回收率: 55%
浸出时间: 3min •石灰耗量: 3kg/t
电耗: 15kwh/t
水耗: 0.15m3•/t 液氯耗量: 3kg/t
投资: 80万元
生产成本: 38.6元•/t 生产人员: 35人
2.黄金产量和产值、利润
按每年生产300天,处理能力为•100m3•/d,烧渣金品位1.5g/t,回收率55%计,产金量如下:
每吨烧产金量: 1×1.5×55%=0.825g
日产黄金: 100×0.825=82.5g
年产金量: 300×82.5=24750g
每吨烧渣产值: 0.825×96=79.2元
日产值: 100×79.2=0.792万元
年产值: 300×0.792=237.6万元
年利润: 300×100×(79.2-38.6)=120万元
按100万元投资计算,返还期为10个月.
用本工艺提金的最低经济品位为0.75g/t.
3.新工艺与常规氰化工艺比较
新工艺:
4.新式固液分离设备的特点
常规固液分离设备有板框压滤机、带式过滤机、浓密机,板框压滤机的配套高压泵易损不易防腐,而且在压滤前要设搅拌槽平衡流量,设备投资达150万元,电耗大;带式真空过滤机过滤带易损,不易防止氯的腐蚀,投资达200
万元;浓密机不易处理大颗粒物料.而且防腐也不易,占地大,投资达150万元.
新式固液分离设备类似池浸用的浸出池,多池串联,上部设溢液口,下部设分布板,矿浆进入后,大颗粒物料很快沉降到池下部,水颗粒物料将通过溢液口向后面的池中流去,经过较长时间的沉降,较清的贵液从固液分离设备中流出,进入吸附工段.待前面的池中充满浸渣后,打开分布板下面的排液阀并从池上部加水洗涤,从分布板下液出的贵液也进入吸附工段.新设备用混凝土制成,涂以防腐材料即可.投资仅30万元.
三.新工艺和设备的优点
浸出方法的优点:
1.本浸出方法使用工业上广泛使用的氯气(开始使用少量食盐)做浸出药剂及少量助剂,避免了氰化物的污染,使用的助剂降低氯气的消耗,使其药剂成本低于氰化法.
2.本方法浸出时间仅3分钟,因此浸出设备有效容积仅为氰化法的0.2%~0.4%,以处理能力100t/d的工厂为例,浸出设备有效容积仅0.3立米.不但投资可减少20%,浸出的电耗也可降低4~5kwh/t.
新式浸出设备的优点:
采用新式反应器,适应大颗粒物料的浸出.常规浸出设备只适用于处理200目以下的矿浆,否则就会出现"沉槽"、压搅拌浆等故障.本设备容积很小,采用其它方法解决反应器问题,避免搅拌不均.
新式固液分离设备具有投资少、生产成本低、易防腐等特点.现有的过滤设备不能解防腐问题,而且价格很高,大约需要投资100万元,新式固液分离设备投资仅30万元.
新工艺的优点:
1.省去了磨矿及相应的分级、浓密设备,减少投资40%左右;节省占地400平米;减少材料消耗10元/t;减少电费5元/t;减少操作工3--6人.
2.不磨的烧渣本身粒度较大,一般在-80目占70%以上,40-80目占25%左右,其余5%在20-40目之间,沉降速度快.特别适合用新式固液分离设备进行液固分离.这种设备易于操作.与氰化工艺相比,省去了浓密机和压滤机,易于控制浸出液物量平衡.
3.选用活性炭吸附法回收浸出液中的金,考虑到在吸附过程中可能产生沉淀物,采用我单位已获专利的吸附槽.吸附装置投资仅2万元.
4.由于在酸性含氯溶液中吸附金氯络合物,并使金离子最终转变为单质金.因此载金炭上金品位至少可富集到10kg/t,采用焚烧—王水溶解—还原的联合工艺即可生产出纯金.冶炼工艺设备简单,仅使用常规药剂,与氰化法比,冶炼工段节约设备投资30万元,冶炼成本也低于常规工艺.
5.贫液中杂质主要是铁、锌和铜,可用石灰沉淀,分离掉杂质的溶液可循环使用;由于不断加氯,浸出液的酸度将不断增加,加石灰除杂的过程还会起到调节酸度的作用.
6.与常规氰化工艺相比,采用本工艺建设100t/d处理能力的提金厂,可节约设备投资80万元,降低生产成本30元/t.使那些用氰化法处理没有利润的低品位烧渣提金成为可能,换句话说,使烧渣的提金经济品位大幅度降低.
以处理能力100t/d的工厂为例,投资60~80万元,供电不超过50kw,处理成本约40元/t,即使烧渣品位低至1.5g/t,浸出率为55%,年利润也可达到100万元.
我国有这类烧渣的工厂至少10座,金品位都在2g/t以下,如果推广本工艺,每年至少回收金250kg.利润1000万元以上.
硫酸烧渣提金工艺设计
一.工艺数据
1.处理能力: 100t/d
2.浸出液浓度: 氯气1.5kg/M3 PH=1.5-2.5 Cl-4kg/M3
3.液固比: 2~5:1
4.反应时间: 3 分钟
5.反应类型: 全返混
6.液固分离方法:新式固液分离设备
7.贵液中金回收方法:活性炭固定床吸附法
8.贫液循环措施:石灰中和沉淀杂质后再循环
9.金浸出率:55%
10.废气处理方法: 烧碱液吸附再利用
二.原料
1.烧渣金品位:1.67克/t
2.液氯
3.石灰
4.活性炭:木质炭或果核炭
5.自来水
6.烧碱
三.物料流量
1.硫酸烧渣: 4.17t/h
2.浸出液流量: 8.34~20M3/h
3.活性炭吸附剂用量: 1t
4.废气处理排气量: >500M3/h
收液流量: 2-4M3/h 四.工艺流程。