PCB制造流程简要说明(doc 14页)
pcb制作的基本流程
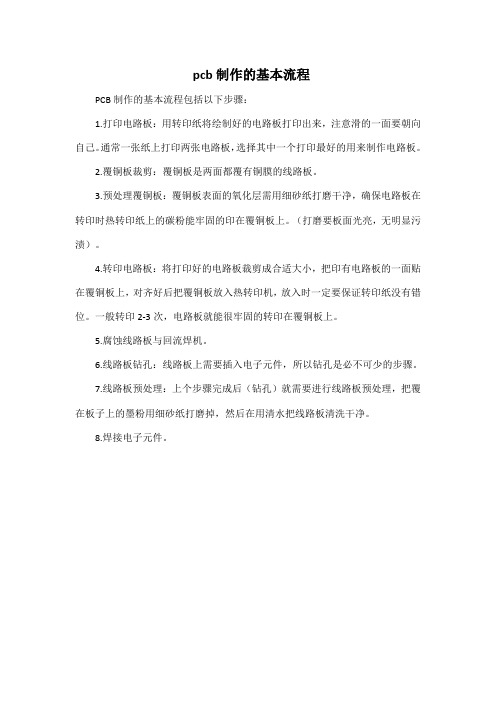
pcb制作的基本流程
PCB制作的基本流程包括以下步骤:
1.打印电路板:用转印纸将绘制好的电路板打印出来,注意滑的一面要朝向自己。
通常一张纸上打印两张电路板,选择其中一个打印最好的用来制作电路板。
2.覆铜板裁剪:覆铜板是两面都覆有铜膜的线路板。
3.预处理覆铜板:覆铜板表面的氧化层需用细砂纸打磨干净,确保电路板在转印时热转印纸上的碳粉能牢固的印在覆铜板上。
(打磨要板面光亮,无明显污渍)。
4.转印电路板:将打印好的电路板裁剪成合适大小,把印有电路板的一面贴在覆铜板上,对齐好后把覆铜板放入热转印机,放入时一定要保证转印纸没有错位。
一般转印2-3次,电路板就能很牢固的转印在覆铜板上。
5.腐蚀线路板与回流焊机。
6.线路板钻孔:线路板上需要插入电子元件,所以钻孔是必不可少的步骤。
7.线路板预处理:上个步骤完成后(钻孔)就需要进行线路板预处理,把覆在板子上的墨粉用细砂纸打磨掉,然后在用清水把线路板清洗干净。
8.焊接电子元件。
PCB板的生产流程介绍
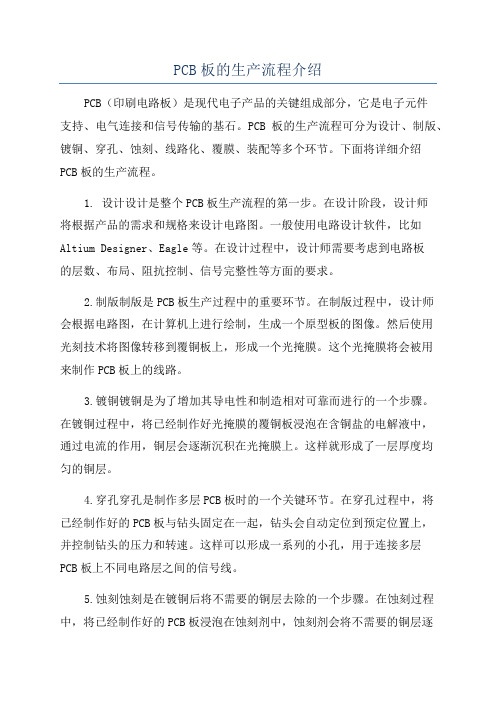
PCB板的生产流程介绍PCB(印刷电路板)是现代电子产品的关键组成部分,它是电子元件支持、电气连接和信号传输的基石。
PCB板的生产流程可分为设计、制版、镀铜、穿孔、蚀刻、线路化、覆膜、装配等多个环节。
下面将详细介绍PCB板的生产流程。
1. 设计设计是整个PCB板生产流程的第一步。
在设计阶段,设计师将根据产品的需求和规格来设计电路图。
一般使用电路设计软件,比如Altium Designer、Eagle等。
在设计过程中,设计师需要考虑到电路板的层数、布局、阻抗控制、信号完整性等方面的要求。
2.制版制版是PCB板生产过程中的重要环节。
在制版过程中,设计师会根据电路图,在计算机上进行绘制,生成一个原型板的图像。
然后使用光刻技术将图像转移到覆铜板上,形成一个光掩膜。
这个光掩膜将会被用来制作PCB板上的线路。
3.镀铜镀铜是为了增加其导电性和制造相对可靠而进行的一个步骤。
在镀铜过程中,将已经制作好光掩膜的覆铜板浸泡在含铜盐的电解液中,通过电流的作用,铜层会逐渐沉积在光掩膜上。
这样就形成了一层厚度均匀的铜层。
4.穿孔穿孔是制作多层PCB板时的一个关键环节。
在穿孔过程中,将已经制作好的PCB板与钻头固定在一起,钻头会自动定位到预定位置上,并控制钻头的压力和转速。
这样可以形成一系列的小孔,用于连接多层PCB板上不同电路层之间的信号线。
5.蚀刻蚀刻是在镀铜后将不需要的铜层去除的一个步骤。
在蚀刻过程中,将已经制作好的PCB板浸泡在蚀刻剂中,蚀刻剂会将不需要的铜层逐渐去除,留下需要的线路。
蚀刻过程需要控制时间和温度,以确保蚀刻剂的作用恰到好处。
6.线路化线路化是将PCB板上的线路连接起来的一个步骤。
在线路化过程中,使用导电胶或者导电油笔将电路板上的线路连接起来。
线路化可以适当增加电路板的可靠性和连接性。
7.覆膜覆膜是为了保护已制作好的PCB板免受损坏和腐蚀的一个步骤。
在覆膜过程中,将特殊覆膜料湿敷在PCB板的表面,并通过加热和压力固化为一层薄膜。
PCB生产制造全流程介绍

全板镀铜(主要是为加厚保护那层薄薄的化学铜以防其在空气
中氧化,形成孔内无铜或破洞)
pcb的生产流程
磨板(采用去毛刺、清洁、刷光和研磨等手段来调整金属表面
状态)
pcb的生产流程
贴膜(加热加压的条件下将干膜抗蚀剂粘贴在覆铜箔板上
)
pcb的生产流程
图形转移(将照相底版上的电路图像转移到覆铜箔层压板上,
HPGL 及 Post Script. HPGL 及 Post Script.
HPGL 及 Post Script. Gerber (RS-274) Text file文字檔 Excellon Format Text file文字檔 IPC-356 or 其它從CAD輸出之各種 格式 Text file文字檔
钻孔刀径=成品孔径+6mil(在满
足最小刀径和板厚孔径比情况下,又 无特殊需求,via孔不必遵循此条件)
阻焊焊盘直径=焊盘直径+4mil
9 最小成品孔径板厚比 10 最小内层隔离环宽(mil) 11 最小焊环宽(mil) 12 最小芯材板厚 13 最大成品板厚范围(mm) 14 最小焊盘直径(mil) 15 最大成品板尺寸(inch) 16 压板厚度公差(mil) 17 成品层间对位精度(mil) 18 成品孔径精度(mil) 19 最小网格间距(mil) 20 最小绿油桥间距(mil) 21 机械加工精度(mil) 22 最小外型铣刀(mm) 23 最大V-CUT板尺寸(inch) 24 最小金属化槽钻咀(mm) 25 层数
PCB厂典型组织结构图
PCB全流程介绍
1.销售(接单---工程审核单-报价规则 ---报价) 2.工程(出菲林,层压叠板) 3.计划 (Bom) 4.生产(品
(PCB印制电路板]PCB制造流程及说明
![(PCB印制电路板]PCB制造流程及说明](https://img.taocdn.com/s3/m/0ae02bbda45177232e60a29a.png)
(PCB印制电路板)PCB 制造流程及说明PCB制造流程及说明一. PCB演变1.1 PCB扮演的角色PCB的功能为提供完成第一层级构装的组件与其它必须的电子电路零件接合的基地,以组成一个具特定功能的模块或成品。
所以PCB在整个电子产品中,扮演了整合连结总其成所有功能的角色,也因此时常电子产品功能故障时,最先被质疑往往就是PCB。
图1.1是电子构装层级区分示意。
1.2 PCB的演变1.早于1903年Mr. Albert Hanson首创利用"线路"(Circuit)观念应用于电话交换机系统。
它是用金属箔予以切割成线路导体,将之黏着于石蜡纸上,上面同样贴上一层石蜡纸,成了现今PCB的机构雏型。
见图1.22. 至1936年,Dr Paul Eisner真正发明了PCB的制作技术,也发表多项专利。
而今日之print-etch (photo image transfer)的技术,就是沿袭其发明而来的。
1.3 PCB种类及制法在材料、层次、制程上的多样化以适合不同的电子产品及其特殊需求。
以下就归纳一些通用的区别办法,来简单介绍PCB的分类以及它的制造方法。
1.3.1 PCB种类A. 以材质分a. 有机材质酚醛树脂、玻璃纤维/环氧树脂、Polyamide、BT/Epoxy等皆属之。
b. 无机材质铝、Copper Inver-copper、ceramic等皆属之。
主要取其散热功能B. 以成品软硬区分a. 硬板Rigid PCBb.软板Flexible PCB 见图1.3c.软硬板Rigid-Flex PCB 见图1.4C. 以结构分a.单面板见图1.5b.双面板见图1.6c.多层板见图1.7D. 依用途分:通信/耗用性电子/军用/计算机/半导体/电测板…,见图1.8 BGA.另有一种射出成型的立体PCB,因使用少,不在此介绍。
1.3.2制造方法介绍A. 减除法,其流程见图1.9B. 加成法,又可分半加成与全加成法,见图1.10 1.11C. 尚有其它因应IC封装的变革延伸而出的一些先进制程,本光盘仅提及但不详加介绍,因有许多尚属机密也不易取得,或者成熟度尚不够。
PCB印制电路板-PCB生产流程介绍精品

PCB印制电路板-PCB生产流程介绍精品PCB(Printed Circuit Board)印制电路板是电子产品中不可或缺的一部分,它提供了电子元件之间的电气连接,并且提供了电气和机械支持。
PCB的制造过程是一个复杂而精细的过程,本文将详细介绍PCB的生产流程。
PCB的生产流程通常包括以下几个主要步骤:设计,制作光掩膜,制作基板,材料选择,印制,设备组装,测试和质量控制。
1.设计:2.制作光掩膜:光掩膜是制造PCB的关键工具,用于将电路图图案转移到基板上。
制作光掩膜通常采用光刻技术。
首先,根据设计文件制作金属板,然后使用光刻机将设计的图案转移到光刻胶上,形成光掩膜。
3.制作基板:制作基板是PCB生产的核心步骤之一、在制作基板之前,需要选择合适的基板材料(如FR-4、铝基板、FR-1等)。
基板制作过程包括以下步骤:切割基板,抛光基板表面,形成铜箔,制作过孔和盲孔,以及涂覆焊盘。
4.材料选择:根据设计要求和功能需求,选择合适的材料用于制造PCB。
除了基板材料,还需要选择适合的电阻、电容、晶体管和其他电子元件。
这些材料的选择将直接影响PCB的性能和可靠性。
5.印制:印制是将电路图的图案转移到基板上的过程。
在印制过程中,使用印制设备将光刻胶覆盖在基板表面上,然后通过光敏化、曝光和腐蚀等步骤,将图案转移到基板上。
在印制过程中,还可以添加阻焊和丝印等附加层。
6.设备组装:设备组装是将PCB上的电子元件焊接到其应对的位置上的过程。
这个过程通常分为手工焊接和自动化焊接。
手工焊接通常适用于小批量生产,而自动化焊接适用于大规模生产。
焊接方法包括表面贴装技术(SMT)和插针式焊接。
7.测试:在设备组装之后,需要对PCB进行测试来确保其功能和可靠性。
测试过程可以包括电气测试、AOI(Automated Optical Inspection)检查和功能测试等。
这些测试将帮助发现可能存在的缺陷和问题。
8.质量控制:质量控制是整个PCB生产流程中至关重要的一环。
PCB制程工艺简要介绍
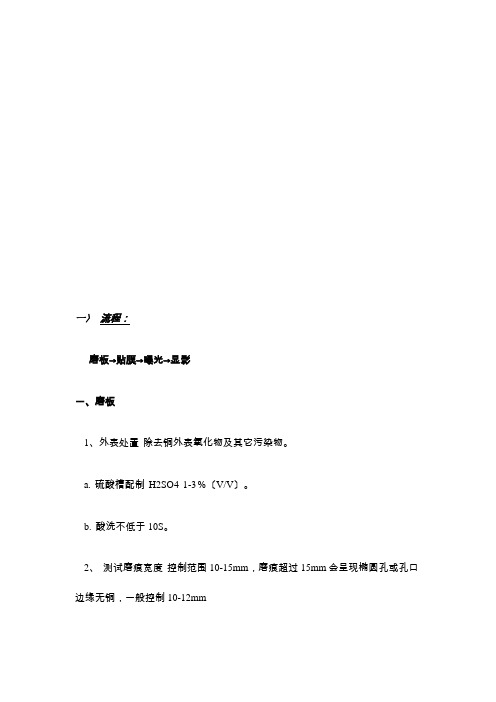
一〉流程:磨板→贴膜→曝光→显影一、磨板1、外表处置除去铜外表氧化物及其它污染物。
a. 硫酸槽配制H2SO4 1-3%〔V/V〕。
b. 酸洗不低于10S。
2、测试磨痕宽度控制范围10-15mm,磨痕超过15mm会呈现椭圆孔或孔口边缘无铜,一般控制10-12mm为宜。
3、水磨试验每日测试水膜破裂时间≥15s,试验说明,在不异条件下磨痕宽度与水膜破裂时间成正比。
4、磨板控制传送速度,间隔1",水压,枯燥温度70-90℃。
二、干膜房1、干膜房洁净度10000级以上。
2、温度控制20-24°C,超出此温度范围容易引起菲林变形。
3、湿度控制60-70%,超出此温度范围也容易引起菲林变形。
4、工作者每次进入干膜房必需穿戴防尘服及防尘靴风淋15-20s。
三、贴膜1、贴膜参数控制a. 温度100-120°C,精细线路控制115-120°C,一般线路控制105-110°C,粗线路控制100-105°C。
b. 速度<3M/min。
c. 压力30-60Psi,一般控制40Psi摆布。
2、本卷须知a. 贴膜时注意板面温度应保持38-40°C,冷板贴膜会影响干膜与板面的粘接性。
b. 贴装前须查抄板面是否有杂物、板边是否光滑等,假设板边毛刺过大会划伤贴膜胶辊,影响使用寿命。
c. 在气压不变情况下,温度较高时可适当加快传送速度,较低时可适当减慢传送速度,否那么会呈现皱膜或贴膜不牢,图形电镀时易发生渗镀。
d. 切削干膜〔手动贴膜机〕时用力均匀,保持切边整齐,否那么显影后呈现菲林碎等缺陷。
e. 贴膜后须冷却至室温前方可进行曝光。
四、曝光1、光能量a.光能量〔曝光灯管5000W〕上、下灯控制40-100毫焦/平方厘米,用下晒架测试上灯,上晒架测试下灯。
b.曝光级数7-9级覆铜〔Stoffer 21级曝光尺〕,一般控制8级摆布,但此级数须显影后才能反映出来,因此对显影控制要求较严。
PCB制作工艺流程

PCB制作工艺流程一、开料目的:以制造流程单之规格,将大面积的敷铜泊基板依制前设计所规化的工作尺寸裁切尺寸及厚度发料并裁板。
1、裁板作业流程:仓库→裁板室→调整尺寸→裁板→检查测量2、磨边作业流程:设置长、宽→磨边→水洗一→水洗二→水洗三→挤干→吹干→烘干二、内层1、内层前处理目的:将除去板面氧化物及油污,再加磨刷粗化铜面增加感光材料于铜面的附著力。
作业流程:上板→化学清洗(H2SO4:3%~5%,压力:1.5±0.5㎏/C㎡)→溢流水洗(压力:1.5±0.5㎏/C㎡)→磨刷→中压水洗(压力:3.0±0.5㎏/C㎡)→微蚀刻(SPS:100~120g/1, H2SO4:1%~3%,压力:1.5±0.5㎏/C㎡)→溢流水洗(压力:1.5±0.5㎏/C㎡)→酸洗(H2SO4:1%~3%)→溢流水洗(压力:1.5±0.5㎏/C㎡)→烘干→检查注意事项:1、做板之前要做刷痕实验、水纹实验,刷痕宽度:1.0±0.2㎝,水纹:15秒以上;2、内层板厚分为两种:47mil的为普通基板,其他为特殊基板,特殊基板要做标记,还要测板厚;3、检查压力表;2、涂布目的:以抗蚀性材料附著力在铜面上,制作内层线路GND、VCC作业流程:进料→粘尘→下降→入料→涂布→烘烤(第一阶段:145℃;第二阶段:125℃;第三阶段:115℃;第四阶段:55℃;第五阶段:35℃) →出料→检查注意实项:1、粘尘纸200片后换一次;2、油墨刮刀压力调整(压力:1.0~3.0㎏/C㎡);3、检测膜厚(8.0±1.5mil),检查脏点等3、曝光(半自动曝光)目的:曝光灯发出紫外光投射在已贴有干膜的板面上,将曝光菲林上线路图形转移到感光干膜上,未吸紫外光的干膜显影时会溶解于显影液中作业流程:检查底片→架底片→调整对准度→放板→吸真空→曝光→检查注意事项:1、每天清洁机台,做能量测试;2、室内温度:22.0±2℃,湿度:55±5%;3、黑色底片每曝光2000次后报废,每曝光500次后底片检查;4、每曝光前用手动滚轮清洁一次底片,底片每曝光10片清洁一次,每50片上机检查一次;5、底片L2朝上,L3朝下;6、灯管亮到熄灭:12秒;7、抽真空度至少600~700MMHG;8、抽真空后用刮刀赶气;9、放板时,把底片翻开看到压条后,沿着压条放板,避免刮伤底片4、显影目的:显影是把尚未发生聚合反应的区域用显影液将之冲洗掉,已感光部分则因已发生聚合反应而洗不掉乃留在铜面上成为蚀刻之阻剂膜5、蚀刻目的:以蚀刻液将铜表面去除,留有抗蚀油墨之线路,制作内层线路GND、VCC 6、去墨剥膜目的:将线路上之抗蚀材料去掉,露出铜线路完成制作内层线路ND、VCC(4,5,6)工作流程:显影(温度:31.0±2℃;浓度:碳酸钠:1.0±0.2wt%,传送速度:4.0±0.5m/min;压力:1.75±0.25㎏/C㎡)→水洗(压力:1.5±0.3㎏/C㎡)→蚀刻(温度:40~45℃;传动速度:4.0±0.5m/min;喷压:上压3.0±0.5㎏/C㎡,下压2.8±0.5㎏/C㎡;铜含量:105~115g/l) →水洗(压力:1.5±0.3㎏/C㎡)→检查→软化去墨(温度:45~50℃;传动速度:4.5±0.5m/min;浓度:NaOH1.0~0.2%;去墨第一段0.1~0.2㎏/C㎡;去墨第二段0.5~0.2㎏/C㎡;去墨第三段1.5~0.2㎏/C㎡)→水洗→酸洗(温度:RT;压力:1.5±0.3㎏/C㎡,H2SO4浓度:1~3%)→水洗→烘干(温度:90.0±10℃)→检查→收板注意事项:1、每天退槽一次;2、有线路的板含有线路的板面朝上,没有线路的板不作要求;3、每天用报废板做显影、蚀刻实验,检查参数是否合格;4、检查压力表;5、每班换水一次;6、滤网每天清洗一次;7、检查喷嘴7、黑化处理工作流程:上料→碱性清洁(16″)→水洗(6″)→水洗(11″)→微蚀(8″)→水洗(1″)→水洗(5″)→预侵(6″)→黑化(15″)→热纯水洗(8″)→水洗(5″)→水洗(16″)→后侵(16″)→纯水洗(3″)→纯水洗(8″)→热纯水洗(16″)→滴干→烘干(35″)注意事项:1、开机前须检查各槽液位是否正常;2、插板时须一片一片的插;3、黑化好的板做首件、自主检查时需垂直向上取板且手指不能拿入单元内;4、黑化OK板预叠前所停放的时间不能超过一小时;5、生产的合格黑化板必须在24小时之内压合完毕,否则超过时间需要新烘烤或重工;6、卸板时需两手平行从飞靶上取出,轻放板上,防止动作不规范造成板面刮伤;7、检查黑化颜色均匀不均匀、漏不漏铜、刮伤、有没有烘干;8、HTG170以上只能在白班做;9、检查压力表;10、参数:微蚀35±2℃,室温32.8℃,黑化75±5℃,热水洗50±3℃,后侵28±5℃,热纯水洗50±3℃,烘干一:120±10℃,烘干二:120±10℃,烘干三:120±10℃,共用35分,清洁:50分8、棕化处理(TG150℃以上的不做棕化)作业流程:上料→酸洗(温度:30±5℃,浓度: 5±2%H2SO4,压力:上压1.5±0.2㎏/C㎡,下压1.5±0.2㎏/C㎡)→水洗(压力:上压1.0±0.2㎏/C㎡,下压1.0±0.2㎏/C㎡)→清洁(温度:50±2℃,压力:上压1.5~2.5㎏/C㎡,下压1.5~2.5㎏/C㎡,碱度:0.96±0.1N)→纯水洗(压力:上压1.0±0.2㎏/C㎡,下压1.0±0.2㎏/C㎡)→预侵(温度:30±3℃,强度:70~100%,酸度:0.06~0.12N,速度:3.6±0.2m/min)→棕化(温度:38~45℃,酸度:1.8~2.3N,CB2218A强度:90~120%,CB2218B强度:150±30%,H2O2:11.5±2g/l,CU2+<50g/l,微蚀量:40~80u″,速度:3.6±0.2m/min)→纯水洗(压力:上压1.0±0.2㎏/C㎡,下压1.0±0.2㎏/C㎡)→干燥1(温度:90±5℃)→干燥2(温度:90±5℃)→收板→检查注意事项:1、每天须做首件,检查各个参数是否合格;2、生产的合格棕化板必须在小时之内压合完毕;3、做完后,检查颜色均匀度、是否漏铜、是否刮伤;4、检查压力表;9、压合①、PP裁切工作流程:安装PP→调整刀具(上下间隙为0.08mm)→开机→长度设定(控制单位inch换mm,裁板尺寸依OP单规定)→速度设定→张数设定→加工作业(在更换裁切不同的TG材料前必须把机台上的粉尘清理干净后方可裁切)→手动部分→收料注意事项:1、温度:22±5℃,湿度:50±10℃;2、PP的经向、纬向一定要根据OP来裁切:3、裁切OK的PP可以静至一个月,超过时间不能用;4、裁切好的TG180℃PP用红色大字报表示,TG140℃的PP用白色大字报表示,TG150℃的PP用黄色大字报表示;5、裁好HTG的PP不能超过6小时;6、裁切首片,测量尺寸是否与OP单要求的尺寸相符;②、预叠(温度:20~18℃,湿度:55±5%)⑴、熔合(六层板或六层板以上)工作流程:开机(检查三点组合)→机台调整(检查定位pin位置是否于板的对位孔相重合)→参数设定→加工作业→关机⑵、铆合(六层板或六层板以上)工作流程:开机→机台调整→调整铆钉→加工作业→关机注意事项:1、预叠前,先看板是否有刮伤、颜色是否均匀等,方可叠合;2、熔合、铆合必须做首件,检查是否合格;3、熔合、铆合要求L2、L5朝外,L3、L4向里;4、隔2小时测量一次铆钉高度,铆钉高度的范围:1.27±0.2mm;5、熔合的温度不做限制,但是就好在340~360℃,时间:加光板的是30~33秒,其他的是22秒③、叠合(温度:22±2℃,湿度:60±5℃)工作流程:准备工作(铜箔、无尘纸、粘尘布、钢板)→清洁机台→检查铜箔→选择排版数→参数设定→叠板注意事项:1、读取工单叠合图所用铜箔规格、产商等,检查机台铜箔是否一致,否则更换;2、根据生产胺尺寸计算在钢板上的排版面积,排版所在钢板上的利用率尽可最大,在排版台上调整红外线固定排版位置或方向;3、根据SOP规定,生产板层数设定排版层数,排版总高度必须高于防滑块高度;4、把板放在红外线固定位置上,叠板时不能在叠台上齐板或抖动PP,叠板动作要轻快;5、六层板要求11叠,四层板12叠④、压合作业流程:开机→设立压合参数→上机→热压→冷压→下机注意事项:1、热板温度测试:180℃恒温10分钟状态,每个热盘取9点,使用感温探针直接测试;2、每6个月测试一次热板,正常热板温差为3.0℃±1.5℃;3、热盘平行度测试:①取直径3.0mm铅条,各热盘放置5根铅条并注意避开盘面滚珠依左右平均放置;②放置后以100psi压力压合10分钟;③取该热盘每一点值与该热盘所有点的平均值对比其差异值小于±0.03mm,否则进行维修,每年测试一次;4、热压真空度:700mmHg以上,热盘温度及压力:依附件之温度及压力设定;5、冷压系统压力设定:100~125㎏/C㎡(板面压力为85~105psi),时间:50min,冷压的降温速率为5℃/min下,冷压后板面的实际温度设定为53℃以下压合程式一览表:阶段T(℃)(±5℃)t(min)(±0.1min)P(psi)(±3psi)t(psi)(±0.1min)1 150 13 100 132 150 12 300 123 195 25 400 254 195 65 400 655 185 5 300 56 180 3 150 37 170 2 50 2 Total 125 125阶段T(℃)(±5℃)t(min)(±0.1min)P(psi)(±3psi)t(psi)(±0.1min)1 150 13 100 152 150 12 300 133 195 25 400 274 195 65 400 605 185 5 300 56 180 3 150 37 170 2 50 2Total 125 125压合程式执行完毕;②超出5分钟外来电时,将压合板取出,把表面PP及铜箔撕掉,再做一次黑化制程,后续正常作业(注:1、黑化制程不能做微蚀处理;2、只能适用于无阻抗控制板子)压合扳子取出→PP及铜箔撕掉→黑化→后续正常作业2、在压合程式第二阶段时停电停机因此时PP的树脂开始融化流动,有大量气泡存在不能重工3、在压合程式第三阶段(高压段)时停电停机①在压合程式第三阶段(高压段上压1~50分钟)时停电停机,因此时PP的树脂开始融化流程,有大量气泡存在不能重工②在压合程式第三阶段(高压段上压50分钟以上)时停电停机,此时树脂已固化,保证足够固化时间即可来电后接着该压合程式执行,下压后须测TG值、热冲击爆实验、介质厚度测试,判定是否合格10、裁切→捞边→铣靶→钻靶→磨边①磨边作业流程:开机→送板→磨边(根据不同板厚调整刀具的位置每次更换刀具后应做一次对应位置检测,进给量每边磨掉0.5mm左右即可)→洗板(传输速度:5.5±0.5m/min,水洗压力:第一段1.0±0.5㎏/C㎡,第二段1.5±0.5㎏/C㎡,第三段1.0±0.5㎏/C㎡)→烘干→收板11、钻孔多层板作业流程:钻孔工具准备→程式输入→裁定位PIN→上料→钻孔作业→下机台检验→刷磨去毛头双面板作业流程:磨板边→上PIN→钻孔工具准备→程式输入→上料→钻孔作业→下PIN→下机台检验→刷磨去毛头注意事项:1、核对OP,所取钻头是否合乎OP上之尺寸;2、检查钻头条件:进刀速、转速、孔限数设定,这些参数根据钻针大小、材质来设定的;3、打PIN (PIN直径:0.123″,深度12.5mm);4、铝垫板必须能涵盖所有的孔,以免断针;5、孔径15.7mil以下(﹤1.5mil),钻孔片数双面板2片,4-10层板2片;孔径15.7mil以上(≧15.7mil),钻孔片数双面板3片,4-6层板3片,8-10层板2片;6、钻孔前要空跑孔数,确认无误;7、胶带距离板边小于0.8cm;8、冰水机温度:19±2℃;9、喷锡板使用手推磨机600﹟,化金板、化银板、OSP 板、金手指板使用800﹟~1000﹟;10、检查备针是否备错,测量大小;11、钻孔、刷磨完后,用X-RAY孔位检查机检查是否钻偏;12、温度:22~25℃,湿度:45~50%;13、检查铝片上的压痕,确认压力角是否水平重工流程:检查并输入钻孔程式→上料→找孔→下料→检查①因停电、停气、断针等造成的漏孔、孔未钻透的板子检查后按照重工流程重工②因用错针造成孔小的板须重工12、去胶渣与化学铜目的:钻孔中造成高温产生胶渣黏于内层铜箔上,此胶渣会造成内层OPEN,所以要去胶渣工作流程:上板→酸洗(压力:1.0±0.2㎏/C㎡,H2SO4:3~5%)→水洗(压力:1.7±0.3㎏/C㎡)→刷磨(刷痕:1.0±0.2cm,电流:2.8±0.5A)→水洗(压力:1.7±0.3㎏/C㎡)→高压水洗(38±2㎏/C㎡)→超音波水洗(温度:40±5℃,电流:2.5±0.2A)→水洗(压力:1.7±0.3㎏/C㎡)→烘干(温度:75±5℃)→收板注:传动速度:3.5±0.5m/min;刷磨完成后的板子,须于12小时内完成一铜电镀作业13、一铜线工作流程:上架(抽样方式检视板子是否有严重凹陷及刮伤)→膨胀剂(Normal FR-4 材料:温度67~73℃,强度:10~16%;HTG材料:温度72~80℃,强度:13~16%,NaOH浓度:0.75~1.1N)→高锰酸钾(Normal FR-4 材料:温度72~78℃;HTG材料:温度76~80℃,NaOH浓度:1.0~1.4N,KmnO4浓度:45~65g/L,Mn6+:须保持在25g/L以下)→预中和(H2SO4浓度:2~4%,H2O2浓度:1.0~2%)→中和(温度:42~46℃)→碱性清洁(温度:47~51℃,碱当量:0.012~0.018N)→微蚀(温度:25~30℃,H2O2浓度:2~5%,SPS浓度:40~70g/L,CU﹥25g/L更槽)→预侵(温度:28~32℃,比重:1.100~1.1600,CU:少于1500PPM)→活化(温度:42~46℃,强度:70~100%,氯化亚钾﹥3g/L,比重:1.140~1.1820,CU:少于2000PPM,铁:少于100PPM)→化学铜(温度:30~36℃,CU2+:1.7~2.3g/L,NaOH:9.0~13g/L,甲醛浓度:3~5g/L,EDTA浓度:25~30g/L)→酸侵(H2O2浓度:100~120ml/L)→镀铜(温度:20~30℃,电流密度:14±2ASF,CuSO4.5H2O浓度:60~80g/L,H2SO4浓度:100~120ml/L,HCL浓度:40~80PPM,EP1100B-2:0.7~3.0ml/L,EP1100C-2:2.8~17ml/L)→烘烤(温度控制:95±5℃,速度:4.5±0.5m/min)→下架注意事项:1、每班分析膨胀剂后在添加,每周更换滤芯,每生产84万平方尺换槽;2、高锰酸钾槽,电流控制在1500±50A,不生产时控制在1000±50A,每生产100万平方尺后换槽;3、中和槽每生产15万平方尺后换槽;4、碱性清洁槽每生产6.7万平方尺后换槽;5、预侵槽每生产30万平方尺换槽;6、活化槽每日槽液浓度分析后添加,滤芯2周换一次,每一年换槽一次或CU﹥2000PPM换槽;7、化学铜槽每天依分析后添加,控制在14 ~26 ,每天二次试验控制在8-10级;8、镀铜槽:阳极铜块每星期检视、添加一次一年更换一次,每周做一次Hull Cell试验,每周分析一次槽液,每次分析后添加。
PCB制造流程简介

PCB制造流程简介一.A/W 底片制作这是一个在单张胶片上用激光或绘图或是接触印制形成电路图的过程。
根据应用需要将底片母片或是生产母片,生产母片用来在涂覆了感光材料或贴了感光干膜的Laminate上印制电路。
二.原材料采购/IQC检查Incoming Inspection of Laminates覆铜板的来料检验检验从Vendor处采购的符合采购规范的半固化片,使得只有合格的覆铜板被用于生产。
(覆铜板由半固化片和铜箔经热压而成,laminate必须是FR4级的,四功能环氧树脂或高功能环氧树脂,laminate的玻璃转移温度范围是130~140℃)Incoming Inspection of Prepreg半固化片的来料检验检验从合格的Vendor处采购的符合采购规范的半固化片,使得只有合格的半固化片用于生产。
(Prepreg由玻璃布和涂抹在上面的半固化环氧树脂组成。
)三.Warehouse Shearing切板货仓作为一个辅助性功能的部门,担负着产品需要之物料的收发工作包括(收料&发货)。
平时,货仓需要帮助生产部门,将较大尺寸的板裁剪成所需尺寸,材料准备。
四.Inner Layer内层Pre-clean预清洗预清洗:清洗内层板表面及改进铜面与湿膜的黏附性。
Coating涂膜涂膜:在内层表面涂湿膜(湿膜被用印刷线路或导电图形)。
Stricky Roller粘性滚轮粘性滚轮:在印图前通过滚轮除去已涂膜内层上的灰尘颗粒。
Imaging印刷线路印刷线路:在已涂有光阻剂的内层上使用底边印刷图形并使用紫外光确定图形。
Developing显影此过程是除去或溶解掉软的未曝光的光阻剂,露出不想要的铜并为蚀刻做好准备。
显影后硬化的光阻剂将留在内层表面。
Etching蚀刻蚀刻:从内层表面除去不想要的铜。
Strip去膜去膜:在光阻剂下的铜线路将被去膜,露出所要的铜线路。
AOI自动光学检测自动光学检测:扫描出任何能造成板面故障的缺陷。
PCB制造流程简要说明

PCB制造流程简要说明PCB (Printed Circuit Board) 制造流程简要说明PCB 是现今电子产品中必不可少的组件之一。
随着电子产品的不断发展,PCB 的制造也越来越复杂。
其制造流程分为以下几个步骤:1. 原材料准备首先,需要准备好PCB 制作所需的原材料,包括基板、铜箔、化学品和光敏胶等。
2. 图纸设计设计师根据产品的需求确定PCB 的电路结构和布局。
在图纸中,需要绘制电路图,并确定每个元件的引脚位置和走线路径。
3. 制作底图和膜图根据图纸设计制作底图和膜图,底图用于制作电路板的基板,而膜图则用于制作PCB 的打印层。
4. 制作基板基板是PCB 制作的核心部件,需要通过化学蚀刻的方式制作。
首先,需要将基板中没有电路的区域涂上光敏胶,并在其上面覆盖上膜图。
然后,将基板暴露在紫外线下,使光敏胶形成图案。
接着,将基板放入腐蚀液中,使带有铜箔的区域腐蚀,最终形成PCB 电路。
5. 制作打印层制作打印层,需要先将底纸覆盖在PCB 上,然后使用暴光机将膜图的图案转移到底纸上,形成电路走线。
接下来,进行酸洗等处理,将不需要的铜箔完全去除。
6. 焊接焊接是将元件与PCB 进行连接的过程。
该过程分为手工焊接和波峰焊接两种方式。
手工焊接需要使用焊锡将元件与PCB 进行焊接,而波峰焊接则是将PCB 放到焊接机上,通过波峰将焊料均匀涂在PCB 上,实现焊接。
7. 检测和包装最后一步是对制作好的PCB 进行检测和包装。
检测可以保障PCB 的性能符合产品要求,而包装则可以使PCB 在运输和装配过程中不受到损坏。
以上就是PCB 制造流程的简要说明。
需要注意的是,该流程对不同的PCB 类型有不同的要求,因此在实际制作时需要根据需要进行调整。
同时,制作PCB 需要有专业的技术和设备,因此切勿尝试DIY 制作,以免引起不必要的麻烦。
PCB线路板生产流程

PCB线路板生产流程PCB线路板生产流程(单/双面板)一、单面松香板(不用钻孔,用模具冲孔)开料——丝印线路(黑油)——蚀刻——蚀刻QC ——手钻管位孔——丝印UV 绿油——丝印字符——冲板—— V-CUT (连片)——过松香—— FQC ——FQA ——真空包装出货二、单板松香板(钻孔锣板)开料——钻孔——丝印线路(黑油)——蚀刻——蚀刻QC——丝印UV绿油——丝印字符——CNC锣板——V-CUT(需连片)——过松香——FQC——FQA——包装出货三、单面喷锡板(不用钻孔,用模具冲)开料——丝印线路(黑油)——蚀刻——蚀刻QC——手钻管位孔——丝印热固绿油——丝印字符——喷锡——冲板——V-CUT——成品测试——FQC——FQA——包装出货四、单面镀金板(不用钻孔,用模具冲孔)开料——丝印线路(黑油)——镀镍、金——蚀刻——蚀刻QC——手钻管位孔——丝印UV绿油——丝印字符——锣板——UV -V-CUT——(连片)——成品测试——FQC——FQA——包装出货五、单面镀金板(钻孔、锣板)开料——钻孔——丝印线路(黑油)——镀镍、金——蚀刻——蚀刻QC——丝印UV 绿油——丝印字符——锣板——UV-CUT (连片)——成品测试——FQC——FQA——包装出货六、双面镀金板开料——焗板——钻孔——沉铜——感光线路——电铜、镍、金——蚀刻——测试——蚀刻QC——感光绿油——丝印字符——冲板或锣板——V-CUT——成品测试——FQC——FQA——包装出货七、双面喷锡板开料——焗板——钻孔——沉铜——图形转移——电铜、锡——蚀刻——退锡——光板测试——蚀刻QC——感光绿油——丝印字符——喷锡——冲板或锣板——V-CUT——成品测试——FQC——FQA——包装出货八、双面喷锡金手指板开料——焗板——钻孔——沉铜——线路——电铜、锡——蚀刻——退锡——蚀刻QC——感光绿油——丝印字符——电金手指——喷锡——冲板或锣板——V-CUT——金手指斜边——成品测试——FQC——FQA——包装出货九、双面沉金(化金)板开料——焗板——钻孔——沉铜——一全板电镀——感光线路——电铜、锡——蚀刻——退锡——光板测试——蚀刻QC——感光绿油——丝印字符——沉金(化金)——冲板或锣板——V-CUT——成品测试——FQC——FQA——包装出货十、双面沉银和沉锡板开料——焗板——钻孔——沉铜——感光线路——电铜、锡——蚀刻——退锡——光板测试——蚀刻QC——感光绿油——丝印字符——冲板或锣板——V-CUT——成品测试——沉银(沉锡)——FQC——FQA——包装出货。
PCB的生产流程简介

PCB的生产流程简介PCB板(Printed Circuit Board,印刷电路板)是一种用于支持和连接电子元件的基础材料。
它起着支撑和传导作用,是电子设备中不可或缺的组成部分。
本文将简要介绍PCB的生产流程。
一、PCB设计在PCB制造的过程中,首先需要进行电路板的设计。
设计人员根据电子设备的需求和功能要求,使用专业的电路设计软件,进行电路板的布局和布线设计。
通过设计软件,我们可以确定电路板的尺寸、层数和线路连接方式。
二、电路板原材料准备在PCB制造过程中,需要准备各种原材料,包括基材、铜箔、耐火材料和覆盖层。
其中,基材是支持电路板结构的主要材料,可以选择有机基材(如FR-4)或无机基材(如陶瓷);铜箔是用于导电的材料,可根据设计需求进行选择;耐火材料用于板材层之间的隔热和阻燃,通常是一种玻璃纤维材料;覆盖层用于保护电路板上的电子元件。
三、电路板层压电路板层压是将多层电路板结合在一起的过程。
首先,将准备好的基材和覆铜箔放在一起,形成厚度适当的层,在层与层之间放置耐火材料。
然后,将堆叠好的板材放入预热机中进行预热,使板材中的树脂熔化。
最后,将板材放入层压机中进行高温高压处理,使树脂熔化并与铜箔粘合在一起。
四、电路板图形化在电路板层压之后,需要通过图形化的过程来形成电路板的形状和尺寸。
这个过程通常被称为电路板的切割和切割。
首先,将层压好的电路板放入机器中,通过数控机床或激光切割机来切割和切割板材。
完成后,通过机器来修整和打磨电路板的边缘。
五、电路板开孔电路板开孔是为了在板上安装电子元件和连接器。
通过机器或激光,将电路板上需要开孔的位置进行加工。
开孔过程可以分为铣削孔和钻孔两种方式。
铣削孔适用于较大直径的孔,而钻孔则适用于较小孔径。
六、电路板表面处理电路板的表面处理是为了提高电路板的焊接能力和抗氧化能力。
目前常用的表面处理方法有热浸金和喷锡。
热浸金是将电路板浸入一种金属液体中,使金属与电路板表面发生化学反应,形成一层金属保护层。
PCB制作流程简单介绍

PCB制作流程简单介绍1. 概述Printed Circuit Board〔PCB〕,即印刷电路板,是现代电子器件的重要组成局部。
PCB制作是将电路设计图印刷在电路板上的过程。
本文将简要介绍PCB制作的根本流程及相关本卷须知。
2. PCB制作流程2.1 设计电路图PCB制作的第一步是设计电路图。
设计师使用电子设计自动化〔EDA〕软件,如Altium Designer或Eagle,绘制电路图。
电路图包括电器元件〔如电阻、电容、晶体管等〕和它们之间的连接线。
在设计电路图时,还要考虑电路板的尺寸、布局和层数。
2.2 PCB布局设计在设计电路图完成后,需要进行PCB布局设计。
布局设计是将电路图上的零件布置在电路板上的过程。
在布局设计中,需要考虑到电器元件之间的连接、引脚位置的对应、电源线和地线的布置等方面。
良好的布局设计可以降低电路板的噪声、提高信号完整性。
2.3 编写PCB制造文件完成布局设计后,需要编写PCB制造文件。
PCB制造文件包括Gerber文件、钻孔文件和掩膜文件等。
Gerber文件包含了电路板的丝网层、焊盘层和符号层等信息,用于制造厂商生产电路板。
钻孔文件包含了电路板上需要钻孔的位置和尺寸。
掩膜文件那么是用于印刷电路板的焊盘位置和元件标记。
2.4 PCB制造完成PCB制造文件后,将其发送给PCB制造厂商进行制造。
在制造过程中,制造商将根据Gerber文件制作电路板,包括将电路图上的图案印刷到电路板上、蚀刻、钻孔、贴装等工艺步骤。
最终会得到一个成品的PCB。
2.5 测试和调试制作完成的PCB需要进行测试和调试。
测试是为了验证PCB是否符合设计要求,包括电气连通性测试、元件放置正确性测试等。
调试阶段那么是通过连接电源和其他外部设备来验证PCB的工作性能。
3. 本卷须知3.1 自检与验收在提交PCB制造文件之前,设计师需要进行自检。
自检包括检查电路图是否符合需求、电路板布局是否合理、PCB制造文件是否完整等。
PCB制造工艺流程
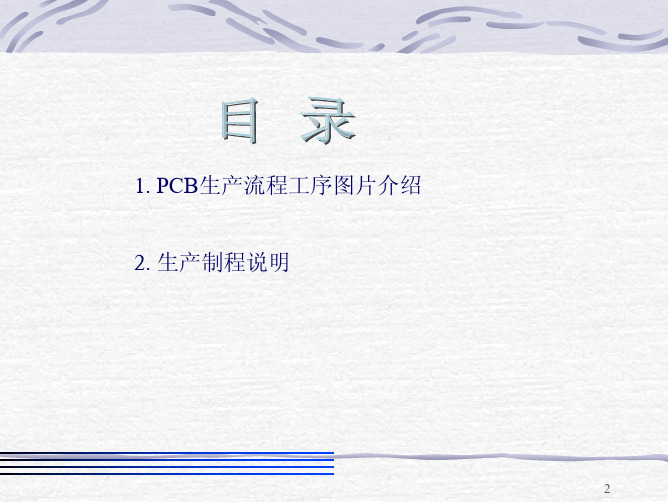
已钻孔 (Been Drilled)
QA检查 (QA Inspection )
下工序 (Next Process)
2
2.5钻孔
2.5.1流程说明
利用钻咀的高速旋转和落速,在PCB 板面加工出客户所需要的孔;线路板中孔主要用于 线路中元件面与焊接面及层与层之间的导通、IC引脚的插装;
1 1和2层之间导通
线路开短/路、线路缺口、干膜碎、偏位、线幼
8
1.6、图形电镀 &蚀刻 (Pattern Plating&Etching)
干膜板 (Finished Dry-film )
图形电镀 (Pattern Plating )
待蚀刻 (Finished Plating )
退膜 (Peeling Dry-film )
因此在蚀刻过程中,随着铜的溶解,应不断补充氨水和氯化铵。
2.3.2 控制要点 A、蚀刻:速度、温度(48-52℃)压力(1.2-2.5kg/cm2)
B、退膜:44-54℃ 8-12% NaOH溶液
2.3.3常见问题
蚀刻不净、蚀刻过度
7
1.2、压合 (Lamination)
开半固化片 (Pre-preg Cutting)
体。
盖板
压合叠板方式(如图)
牛皮纸
2.4.2控制要点
铜箔
A、棕化:各药水槽浓度、温度,
传送速度
B、压合:叠层结构、热压机参数 PP
钢板
2.4.3常见问题 棕化不良、压合白点、 滑板、板面凹痕
芯板
牛皮纸 底盘
1
1.3、钻孔 (Drilling)
待钻孔 (Waiting Drilling)
钻孔 (Drilling)
PCB制造流程简要说明(doc14页)

PCB制造流程简要说明(doc 14页)PCB制造流程及说明一.PCB演变1.1PCB扮演的角色PCB的功能为提供完成第一层级构装的组件与其它必须的电子电路零件接合的基地,以组成一个具特定功能的模块或成品•所以PCB在整个电子产品中,扮演了整合连结总其成所有功能的角色,也因此时常电子产品功能故障时,最先彼质疑往往就是PCB■图是电子构装层级区分示意。
1.2PCB的演变1 •早于1903年Mr. Albert Hanson首创利用•’线路'(Circuit)观念应用于电话交换机系统。
它是用金属箔予以切割成线路导体,将之黏着于石蜡纸上,上面同样贴上一层石蜡纸,成了现今PCB的机构雏型.见图1・22•至1936年,Dr Paul Eisner真正发明了PCB的制作技术,也发表多项专利.而今日之printetch (photo image transfer)的技术,就是沿袭其发明而来的。
1.3PCB种类及制法在材料、层次、制程上的多样化以适合不同的电子产品及其特殊希求。
以下就归纳一些通用的区別办法,来简单介绍PCB的分类以及它的制造方法.1.3.1PCB 种类A・以材质分a •有机材质酚醛树脂、玻璃纤维/环氧树脂.Polyamide. BT/Epoxy等皆属之铝、Copper Inver-copper, ceramic等皆属之。
主要取其散热功能B・以成品软硬区分a■歿板Rigid PCBb•软板Flexible PCB 见图1.3c •软便板Rigid-Flex PCB 见图1.4C・以结构分a •单面板见图1.5b •双面板见图1.6C •多层板见图1.7D•依用途分:通信/耗用性电子/军用/计算机/半导体/电测板…,见图1.8 BGA.另有一种射出成型的立体PCB,因使用少,不在此介绍。
1.3.2制造方法介绍A・减除法,其流程见图1.9B・加成法,又可分半加成与全加成法,见图1.10 1.11C・尚有其它因应IC封装的变革延伸而出的一些先进制程,本光盘仅提及但不详加介绍,因有许多尚属机密也不易取得,或者成熟度尚不够。
PCB制造流程及工艺说明

更新日期:20作者: 来源:PCB制造流程及说明(外观检查,防焊,金手指喷锡,表面处理等)464411.1前言一般pcb制作会在两个步骤完成后做全检的作业:一是线路完成(内层与外层)后二是成品,本章针对线路完成后的检查来介绍.11.2检查方式11.2.1电测11.2.2目检以放大镜附圆形灯管来检视线路品质以及对位准确度,若是外层尚须检视孔及镀层品质,通常会在备有10倍目镜做进一步确认,这是很传统的作业模式,所以人力的须求相当大.但目前高密度设计的板子儿乎无法在用肉眼检查,所以下面所介绍的A0I会被大量的使用.11. 2. 3 A0I — Automated optical Inspection 自动光学检验因线路密度逐渐的提高,要求规格也愈趋严苛,因此目视加上放大灯镜已不足以过滤所有的缺点,因而有A0I的应用。
11.2.3. 1应用范围A.板子型态一信号层,电源层,钻孔后(即内外层皆可)・一底片,干膜,铜层.(工作片,干膜显像后,线路完成后)B.目前AOI的应用大部分还集中在内层线路完成后的检测,但更大的一个取代人力的制程是绿漆后已作焊垫表面加工(surface finish)的板子.尤其如BGA,板尺寸小,线又细,数量大,单人力的须求就非常惊人•可是应用于这领域者仍有待技术上的突破.11.2. 3.2 原理一般业界所使用的〃自动光学检验CCD及Laser两种;前者主要是利用卤素灯通光线,针对板面未黑化的铜面,利用其反光效果,进行断、短路或碟陷的判读。
应用于黑化前的内层或线漆前的外层。
后者Laser AOI 主要是针对板面的基材部份,利用对基材(成铜面)反射后产荧光(Fluorescences)在强弱上的不同,而加以判读。
早期的Laser AOI对〃双功能〃所产生的荧光不很强,常需加入少许"荧光剂"以增强其效果,减少错误警讯当基板薄于6mil时,雷射光常会穿透板材到达板子对另一面的铜线带来误判。
完整的pcb制作流程

完整的pcb制作流程完整的pcb制作流程2007-10-05 20:31:23分类:今天进行了一个完整的pcb设计.对pcb流程有了初步的了解.现在将步骤概括如下:一.1. 原理图元件设计如果PROTEL元件库中有所需要的元件,则直接找出放在原理图中即可.若没有所需要的元件,则需要建立一个新的原理元件库(Sch.lib).过程:在原有的元件库中找出跟所需元件管脚数目相同(或差不多)的元件1,先将元件1放置到原理图编辑区(即Schdoc文件),单击该元件,执行菜单命令Edit|Copy,此时光标变成十字光标,将光标移到元件上,单击鼠标确定一个基准点.然后切换到所需编辑的Sch.lib文件,在该文件中新创建一个器件(快捷键creat component)并修改名字.在该环境右下角点击SCH Lib,将鼠标光标移动到空元件名上,单击鼠标右键,在弹出额快捷菜单中执行Paste命令,将该元件1粘贴到新建的元件库中.而后修改引脚属性.然后执行菜单命令Report|Component Rule Check,进行规测检查.2. 原理图设计新建原理图文件-->加载元件库(包括加载自己创建的元件库)-->放置元件-->原理图布线||输出器件报表<--纠正错误--comile all projects<-先设置编译错误报告选项(Reports/Bills of Materials)||输出网络报(若没有层次原理图则可只生成单个文档的网络报表Design/Netlist For Document/Protel 若有层次模块图则需生成项目的网络报表Design/Netlist For Project/Protel)在原理图设计中,若电路图比较复杂,可以采用从上到下(或从下到上)的层次化原理图设计.3.元件PCB封装设计可以利用利用一个相同(或相似)封装的元件,对其进行简单的属性修改得到所需要的元件封装.具体操作过程也就是元件封装从.pcbdoc 到.PCBlib复制然后修改的过程.在此不再赘述.元件封装修改完毕后,要执行Edit/Set Preference/pin 1设置封装参考点在第一引脚.然后还要执行Report/Component Rule check 设置齐全要检查的规则,并OK.至此,封装建立完毕.4.pcb设计首先新建一个PCB文件,在封装lib都已经加载的情况下,导入网络表.元件自动布局.在进行该步之前,要先设定PCB的大小,你得给他规划一下大小和形状。
- 1、下载文档前请自行甄别文档内容的完整性,平台不提供额外的编辑、内容补充、找答案等附加服务。
- 2、"仅部分预览"的文档,不可在线预览部分如存在完整性等问题,可反馈申请退款(可完整预览的文档不适用该条件!)。
- 3、如文档侵犯您的权益,请联系客服反馈,我们会尽快为您处理(人工客服工作时间:9:00-18:30)。
PCB制造流程简要说明(doc 14页)PCB制造流程及说明一. PCB演变1.1 PCB扮演的角色PCB的功能为提供完成第一层级构装的组件与其它必须的电子电路零件接合的基地,以组成一个具特定功能的模块或成品。
所以PCB在整个电子产品中,扮演了整合连结总其成所有功能的角色,也因此时常电子产品功能故障时,最先被质疑往往就是PCB。
图1.1是电子构装层级区分示意。
1.2 PCB的演变1.早于1903年Mr. Albert Hanson首创利用"线路"(Circuit)观念应用于电话交换机系统。
它是用金属箔予以切割成线路导体,将之黏着于石蜡纸上,上面同样贴上一层石蜡纸,成了现今PCB的机构雏型。
见图1.22. 至1936年,Dr Paul Eisner真正发明了PCB的制作技术,也发表多项专利。
而今日之print-etch (photo image transfer)的技术,就是沿袭其发明而来的。
1.3 PCB种类及制法在材料、层次、制程上的多样化以适合不同的电子产品及其特殊需求。
以下就归纳一些通用的区别办法,来简单介绍PCB的分类以及它的制造方法。
1.3.1 PCB种类A. 以材质分a. 有机材质酚醛树脂、玻璃纤维/环氧树脂、Polyamide、BT/Epoxy等皆属之。
b. 无机材质Industries Association)主要两大组成:1.Function Code:如G codes, D codes, M codes 等。
2.Coordinate data:定义图像(imaging)C. RS-274X是RS-274D的延伸版本,除RS-274D之Code 以外,包括RS-274X Parameters,或称整个extended Gerber format它以两个字母为组合,定义了绘图过程的一些特性。
D. IPC-350IPC-350是IPC发展出来的一套neutral format,可以很容易由PCB CAD/CAM产生,然后依此系统,PCB SHOP 再产生NC Drill Program,Netlist,并可直接输入Laser Plotter绘制底片.E. Laser Plotter见图2.1,输入Gerber format或IPC 350 format以绘制ArtworkF. Aperture List and D-Codes见表 2.1 及图2.2,举一简单实例来说明两者关系, Aperture的定义亦见图2.12.3.制前设计流程:2.3.1客户必须提供的数据:电子厂或装配工厂,委托PCB SHOP生产空板(Bare Board)时,必须提供下列数据以供制作。
见表料号数据表-供制前设计使用.上表数据是必备项目,有时客户会提供一片样品, 一份零件图,一份保证书(保证制程中使用之原物料、耗料等不含某些有毒物质)等。
这些额外数据,厂商须自行判断其重要性,以免误了商机。
2.3.2 .资料审查面对这么多的数据,制前设计工程师接下来所要进行的工作程序与重点,如下所述。
A. 审查客户的产品规格,是否厂内制程能力可及,审查项目见承接料号制程能力检查表.B.原物料需求(BOM-Bill of Material)根据上述资料审查分析后,由BOM的展开,来决定原物料的厂牌、种类及规格。
主要的原物料包括了:基板(Laminate)、胶片(Prepreg)、铜箔(Copper foil)、防焊油墨(Solder Mask)、文字油墨(Legend)等。
另外客户对于Finish的规定,将影响流程的选择,当然会有不同的物料需求与规格,例如:软、硬金、喷钖、OSP等。
表归纳客户规范中,可能影响原物料选择的因素。
C. 上述乃属新数据的审查, 审查完毕进行样品的制作.若是旧资料,则须Check有无户ECO(Engineering Change Order) .再进行审查.D.排版排版的尺寸选择将影响该料号的获利率。
因为基板是主要原料成本(排版最佳化,可减少板材浪费);而适当排版可提高生产力并降低不良率。
有些工厂认为固定某些工作尺寸可以符合最大生产力,但原物料成本增加很多.下列是一些考虑的方向:一般制作成本,直、间接原物料约占总成本30~60%,包含了基板、胶片、铜箔、防焊、干膜、钻头、重金属(铜、钖、铅),化学耗品等。
而这些原物料的耗用,直接和排版尺寸恰当与否有关系。
大部份电子厂做线路Layout时,会做连片设计,以使装配时能有最高的生产力。
因此,PCB工厂之制前设计人员,应和客户密切沟通,以使连片Layout的尺寸能在排版成工作PANEL时可有最佳的利用率。
要计算最恰当的排版,须考虑以下几个因素。
a.基材裁切最少刀数与最大使用率(裁切方式与磨边处理须考虑进去)。
b.铜箔、胶片与干膜的使用尺寸与工作PANEL的尺寸须搭配良好,以免浪费。
c.连片时,piece间最小尺寸,以及板边留做工具或对位系统的最小尺寸。
d.各制程可能的最大尺寸限制或有效工作区尺寸.e.不同产品结构有不同制作流程,及不同的排版限制,例如,金手指板,其排版间距须较大且有方向的考量,其测试治具或测试次序规定也不一样。
较大工作尺寸,可以符合较大生产力,但原物料成本增加很多,而且设备制程能力亦需提升,如何取得一个平衡点,设计的准则与工程师的经验是相当重要的。
2.3.3 着手设计所有数据检核齐全后,开始分工设计:A. 流程的决定(Flow Chart) 由数据审查的分析确认后,设计工程师就要决定最适切的流程步骤。
传统多层板的制作流程可分作两个部分:内层制作和外层制作.以下图标几种代表性流程供参考.见图 2.3 与图2.4B. CAD/CAM作业a. 将Gerber Data 输入所使用的CAM系统,此时须将apertures和shapes定义好。
目前,己有很多PCB CAM系统可接受IPC-350的格式。
部份CAM系统可产生外型NC Routing 档,不过一般PCB Layout设计软件并不会产生此文件。
有部份专业软件或独立或配合NC Router,可设定参数直接输出程序.Shapes 种类有圆、正方、长方,亦有较复杂形状,如内层之thermal pad等。
着手设计时,Aperture code和shapes的关连要先定义清楚,否则无法进行后面一系列的设计。
b. 设计时的Check list依据check list审查后,当可知道该制作料号可能的良率以及成本的预估。
c. Working Panel排版注意事项:-PCB Layout工程师在设计时,为协助提醒或注意某些事项,会做一些辅助的记号做参考,所以必须在进入排版前,将之去除。
下表列举数个项目,及其影响。
-排版的尺寸选择将影响该料号的获利率。
因为基板是主要原料成本(排版最佳化,可减少板材浪费);而适当排版可提高生产力并降低不良率。
有些工厂认为固定某些工作尺寸可以符合最大生产力,但原物料成本增加很多.下列是一些考虑的方向:一般制作成本,直、间接原物料约占总成本30~60%,包含了基板、胶片、铜箔、防焊、干膜、钻头、重金属(铜、钖、铅、金),化学耗品等。
而这些原物料的耗用,直接和排版尺寸恰当与否有关系。
大部份电子厂做线路Layout时,会做连片设计,以使装配时能有最高的生产力。
因此,PCB工厂之制前设计人员,应和客户密切沟通,以使连片Layout的尺寸能在排版成工作PANEL时可有最佳的利用率。
要计算最恰当的排版,须考虑以下几个因素。
1.基材裁切最少刀数与最大使用率(裁切方式与磨边处理须考虑进去)。
2.铜箔、胶片与干膜的使用尺寸与工作PANEL的尺寸须搭配良好,以免浪费。
3.连片时,piece间最小尺寸,以及板边留做工具或对位系统的最小尺寸。
4.各制程可能的最大尺寸限制或有效工作区尺寸.5不同产品结构有不同制作流程,及不同的排版限制,例如,金手指板,其排版间距须较大且有方向的考量,其测试治具或测试次序规定也不一样。
较大工作尺寸,可以符合较大生产力,但原物料成本增加很多,而且设备制程能力亦需提升,如何取得一个平衡点,设计的准则与工程师的经验是相当重要的。
-进行working Panel的排版过程中,尚须考虑下列事项,以使制程顺畅,表排版注意事项。
d. 底片与程序:-底片Artwork 在CAM系统编辑排版完成后,配合D-Code档案,而由雷射绘图机(Laser Plotter)绘出底片。
所须绘制的底片有内外层之线路,外层之防焊,以及文字底片。
由于线路密度愈来愈高,容差要求越来越严谨,因此底片尺寸控制,是目前很多PCB厂的一大课题。
表是传统底片与玻璃底片的比较表。
玻璃底片使用比例已有提高趋势。
而底片制造商亦积极研究替代材料,以使尺寸之安定性更好。
例如干式做法的铋金属底片.一般在保存以及使用传统底片应注意事项如下:1.环境的温度与相对温度的控制2.全新底片取出使用的前置适应时间3.取用、传递以及保存方式4.置放或操作区域的清洁度-程序含一,二次孔钻孔程序,以及外形Routing程序其中NC Routing程序一般须另行处理e. DFM-Design for manufacturing .PCB layout 工程师大半不太了解,PCB制作流程以及各制程需要注意的事项,所以在Lay-out线路时,仅考虑电性、逻辑、尺寸等,而甚少顾及其它。
PCB 制前设计工程师因此必须从生产力,良率等考量而修正一些线路特性,如圆形接线PAD修正成泪滴状,见图2.5,为的是制程中PAD一孔对位不准时,尚能维持最小的垫环宽度。
但是制前工程师的修正,有时却会影响客户产品的特性甚或性能,所以不得不谨慎。
PCB厂必须有一套针对厂内制程上的特性而编辑的规范除了改善产品良率以及提升生产力外,也可做为和PCB线路Lay-out人员的沟通语言,见图2.6 .C. Tooling指AOI与电测Netlist檔..AOI由CAD reference文件产生AOI系统可接受的数据、且含容差,而电测Net list档则用来制作电测治具Fixture。
2.4 结语颇多公司对于制前设计的工作重视的程度不若制程,这个观念一定要改,因为随着电子产品的演变,PCB制作的技术层次愈困难,也愈须要和上游客户做最密切的沟通,现在已不是任何一方把工作做好就表示组装好的产品没有问题,产品的使用环境, 材料的物,化性, 线路Lay-out的电性, PCB的信赖性等,都会影响产品的功能发挥.所以不管软件,硬件,功能设计上都有很好的进展,人的观念也要有所突破才行.三. 基板印刷电路板是以铜箔基板(Copper-clad Laminate 简称CCL )做为原料而制造的电器或电子的重要机构组件,故从事电路板之上下游业者必须对基板有所了解:有那些种类的基板,它们是如何制造出来的,使用于何种产品, 它们各有那些优劣点,如此才能选择适当的基板.表 3.1简单列出不同基板的适用场合.基板工业是一种材料的基础工业,是由介电层(树脂Resin ,玻璃纤维Glass fiber ),及高纯度的导体(铜箔Copper foil )二者所构成的复合材料(Composite material),其所牵涉的理论及实务不输于电路板本身的制作。