数控车床编程与操作课件
数控车床编程与操作加工PPT课件

G00 Z104.0 X29.3 ap1=0.35 G32 Z56.0 F1.5 G00 X40.0 Z104.0 X28.9 ap2=0.2 G32 Z56.0 F1.5 G00 X40.0 Z104.0 X28.5 ap2=0.2 …….
1.绝对编程与增量编程
(1)绝对编程
绝对值编程是根据预先设定的编程原点计算出绝对值坐标尺寸进行编程的一种方法。即采用绝对值编程时,首先要指出编程原点的位置,并用地址X,Z进行编程(X为直径值)。
增量值编程是根据与前一个位置的坐标值增量来表示位置的一种编程方法。即程序中的终点坐标是相对于起点坐标而言的。
根据试切后工件的尺寸确定刀尖的位置。
O
(a) 确定刀尖在Z向的位置
L
图3-3 数控车床的对刀
O
(a) 确定刀尖在Z向的位置
L
图3-3 数控车床的对刀
O
(b) 确定刀尖在X向的位置
d
O
(b) 确定刀尖在X向的位置
d
三、有关编程代码说明
(一)G功能
准备功能也称为G功能(或称G代码),它是用来指令机床动作方式的功能。准备功能是用地址G及其后面的数字来指令机床动作的。如用G00来指令运动坐标快速定位。表3-2为FANUC-0TD系统的准备功能G代码表。
10.刀具偏置功能 (G40/G41/G42)
1. 格式 G41 X_ Z_;G42 X_ Z_;
在刀具刃是尖利时,切削进程按照程序指定的形状执行不会发生问题。不过,真实的刀具刃是由圆弧构成的 (刀尖半径) 就像上图所示,在圆弧插补和攻螺纹的情况下刀尖半径会带来误差。
2. 偏置功能
1、非直线切削形式的定位 我们的定义是:采用独立的快速移动速率来决定每一个轴的位置。刀具路径不是直线,根据到达的顺序,机器轴依次停止在命令指定的位置。
2024版数控车床ppt课件完整版

根据故障诊断结果,采取相应的维修措施,如更 换损坏部件、调整参数等。
预防性保养措施建议
保持机床清洁
定期清理切屑、擦拭机床,避免 灰尘、油污等对机床造成损害。
定期检查
定期对机床各部位进行检查,及 时发现并处理潜在问题。
加强润滑
根据机床润滑要求,定期加注润 滑油或润滑脂,确保机床各部件 得到充分润滑。
数控车床网络化技术
介绍数控车床网络化技术的实现方式及在智 能制造中的应用前景。
数控车床自动化技术
分析数控车床自动化技术的现状与发展方向, 如自动上下料、自动换刀等。
数控车床绿色制造技术
探讨数控车床绿色制造技术的意义及实现途 径,如节能减排、环保型切削液等。
07 总结与展望
课程重点内容回顾
数控车床基本概念、分类及 应用领域
数控编程步骤
包括分析零件图样、确定加工工艺过程、 数学处理、编写零件加工程序、程序校 验与首件试切等。
常用编程指令介绍
准备功能指令
如G00(快速定位)、G01(直 线插补)、G02/G03(圆弧插补) 等,用于控制刀具的运动轨迹。
辅助功能指令
如M03(主轴正转)、M05(主 轴停止)、M08(冷却液开)等,
参数调整方法 根据加工过程监控结果,可以适时调整进给速度、主轴转 速等参数,以提高加工效率和保证加工质量。
异常处理措施 在加工过程中如遇到异常情况,如刀具磨损、工件变形等, 需要及时采取相应措施进行处理,避免影响加工质量和机 床安全。
加工后质量检测与评估
1 2 3
质量检测方法 加工完成后需要对工件进行质量检测,常用的检 测方法包括尺寸测量、表面粗糙度检测、形位公 差检测等。
复杂曲面零件加工编程
数控车床编程与操作PPT课件

加工完成后,对工件进行检测,确保满足设计要 求和加工精度。
05 常见问题与解决方案
G代码编程常见问题与解决方案
G代码编程错误
检查G代码编程的语法和逻辑,确保指令正确无误。
刀具路径问题
检查刀具路径是否合理,避免出现干涉和碰撞。
加工参数设置不当
根据材料和加工要求,合理设置主轴转速、进给速度等加工参数。
数控车床操作常见问题与解决方案
1 2
操作界面不熟悉
熟悉数控车床的操作界面,了解各功能键的作用。
刀具安装不正确
按照规定正确安装刀具,确保刀具夹紧牢固。
3
加工区域安全问题
确保加工区域的安全防护措施到位,避免发生意 外事故。
加工过程常见问题与解决方案
加工精度不足
01
检查刀具磨损情况,及时更换刀片,确保加工精度。
遵守安全操作规程
在操作数控车床时,必须遵守安全操作规程, 确保人身安全和设备安全。
注意刀具状态
在加工过程中,应时刻关注刀具的状态,如 刀具是否松动、破损等。
禁止带手套操作
数控车床在高速旋转时,带手套操作容易发 生危险。
避免超负荷运转
在加工过程中,应避免因切削力过大而引起 的机床超负荷运转。
04 实际操作案例
表面质量不佳
02
调整切削参数和刀具角度,改善表面质量。
加工效率低下
03
优化加工参数和刀具路径,提高加工效率。
THANKS FOR WATCHING
感谢您的观看
并进行必要的编辑和修改。
加工参数设置
根据工件材料、刀具类型和加工要 求,设置合理的加工参数,如主轴 转速、进给速度、切削深度等。
自动加工
数控车床编程与操作培训课件

3 T功能
刀具功能,表示选刀或换刀。 用地址T和后面的四位数字来指定刀具号和刀具补偿号,其中前两位 为刀具号,后两位为既是刀具长度补偿号,又是刀尖圆弧半径补偿号。
T ×× ××
刀补号 刀具号
T0101表示1号刀具及1号刀具长度补偿和半径补偿。至于刀具的长度 和刀尖圆弧半径补偿的具体值,应到1号刀具补偿位去查找和修改。如果后 面两位数为零,如T0300; 表示取消刀具补偿状态,调用第三号刀具。
分别按下 、 、 、 键,控制刀架的移动方向。按进 给方向按钮开始连续移动,松开则停止。按下快速按钮 ,进 入手动快速移动状态。
(3)手动脉冲方式
旋转控制面板上的模式选择旋钮指向“手轮/单步”,机床进
入手动脉冲模式。
旋转旋钮 ,选择坐标轴。
旋转“手轮进给速度”旋钮
,选择合适的脉冲当量。
摇动手轮,精确控制机床的移动。
数控车床FANUC-0i Mate TC操作面板
1 数控系统操作面板
以大连机床厂FANUC-0i Mate TC数控系统为例,介 绍数控车床FANUC-0i Mate TC操作面板。
操作面板由数控系统操作面板(也称CRT/MDI面板) 和机床操作面板组成。
图3-8 FANUC-0i Mate数控系统操作面板
①换2号切槽刀。 转到MDI模式,按小键盘上的[PROG]键,转 到编辑模式,输入“T0202;”,按[INSERT]键 插入,光标移至程序号处。
按“循环启动”按钮,换上2号刀。
图3-30 换2号刀MDI输入操作
②操作让主轴正转,转到JOG或手轮模式,设 置2号刀具刀尖位于加工坐标系原点在Z方向相对于 机床原点偏置值。
图3-25 编辑程序
④接着按键盘的[OFFSET
数控车床编程和操作[1].pptx
![数控车床编程和操作[1].pptx](https://img.taocdn.com/s3/m/1e28b0a20b4e767f5bcfce1f.png)
2020年10月13日
图4—2 六轴控制的数控车床加工示意图
2020年10月13日
现代数控车床,必须具备良好的便于操作的优 点。
数控车床加工具有如下特点: 1.节省调整时间 ▪(1)快速夹紧卡盘减少了调整时间。 ▪(2)快速夹紧刀具减少了刀具调整时间。 ▪(3)刀具补偿功能节省了刀具补偿的调整时间。 ▪(4)工件自动测量系统节省了测量时间并提高 加 工质量。 ▪(5)由程序指令或操作盘的指令控制顶尖架的 移动也节省了时间。
(2)全功能型数控车床
▪较高档次的数控车床,具有刀尖圆弧半径自动 补偿、恒线速、倒角、固定循环、螺纹切削、图 形显示、用户宏程序等功能,加工能力强,适宜 于加工精度高、形状复杂、循环周期长、品种多 变的单件或中小批量零件的加工。
2020年10月13日
(3)精密型数控车床 ▪采用闭环控制,不但具有全功能型数 控车床的全部功能,而且机械系统的动 态响应较快,在数控车床基础上增加其 他附加坐标轴。适用于精密和超精密加 工。
2020年10月13日
(3)淬硬工件的加工
▪在大型模具加工中,有不少尺寸大且形状 复杂的零件。
▪这些零件热处理后的变形量较大,磨削加 工有困难,而在数控车床上可以用陶瓷车 刀对淬硬后的零件进行车削加工,以车代 磨,提高加工效率。
2020年10月13日
(4)高效率加工 ▪为了进一步提高车削加工的效率, 通过增加车床的控制坐标轴,就能 在一台数控车床上同时加工出两个 多工序的相同或不同的零件。
2020年10月13日
二、数控车床的主要类型
1.数控车床的组成及其作用
(1)主体
▪机床主体主要包括床身、主轴箱、床鞍、 尾座、进给机构等机械部件。
(2)数控装置(CNC装置)
数控车床编程ppt课件

1)G 准备功能(车床)
G代码 G00 G01 G02 G03 G54-G59 G70-G73 G99
功能
快速定位
G0O
直线插补
G01
顺圆插补
G02
逆圆插补
G03
选择工作坐标系 G92
复合型固定循环
进给速度mm/r
格式 XZ
XZ
XZR X_ Z_R_ X_Z_I_F_
15 15
(1)、工件坐标系选择G54~G59
29 29
N22 X29.00 N23 G01 Z- 14.85 F50. N24 G03 X30.40 Z- 15.80 F50.I28.40 K- 15.80 N25 G01 Z-25,80 F50. N26 Z-34.80 F50. N27 Z-43.80 F50. N28 G02 X33.20 Z-45.71 F50.I34.40 K-43.80 N29 G01 X36.03 Z-44.29 F50. N30 G00 Z2.70 N31 X25.20 N32 G01 Z- 14.80 F50. N33 X28.40 F50. N34 G03 X29.40 Z- 14.93 F50.I28.40 K- 15.80 N35 G01 X32.23 Z- 13.52 F50. N36 G00 Z2.70 N37 X21.40 N38 G01 Z- 14.80 F50. N39 X25.60 F50. N40 X28.43 Z- 13.39 F50. N41 G00 Z2.70 N42 X17.60 N43 G01 Z-5.43 F50. N44 G03 X20.40 Z- 10.80 F50.I-1.60 K- 10.80
N53 G00 Z2.70
数控车编程与操作(课件)
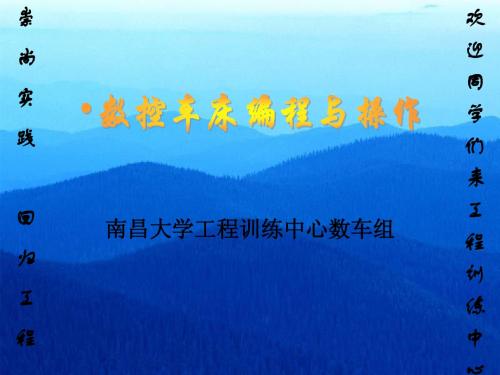
南昌大学工程训练中心数车组迎同学们来工程训练中崇尚实践回归工程习内容数控车床编程与操作认知数控车床数控车床安全操作规程数控车床的编程编程例题及作业数控车床之一(SINMENS 802C系统)数控车床之二(FANUC 0i Mate TB系统)数控车床之三(FANUC 0i TB系统)1、数控车床只能单人操作2、零件加工时须将防护门关上3、车床总电源开关不许乱动4、启动“循环启动”按钮前须报告指导老师5、长头发须戴工作帽,以防头发卷入机床6、遵守其他《安全教育》内容返回数控车床的编程编程的基础知识程序的结构编程的内容和步骤编程注意事项返回1、坐标轴及运动方向的规定笛卡儿坐标系(右手坐标系)坐标正向规定:一般取远离工件的方向(即工件尺寸增大的方向)为正。
2、坐标轴的确定:先确定Z轴(为提供切削功率的轴,一般与主轴平行),再确定X轴,然后根据笛卡尔坐标系(右手坐标系)确定Y轴。
车床坐标系Z X 0的分类1、机床坐标系:机床本身固有的坐标系,一般不能改动。
在机床坐标系中,坐标值是刀架中心点相对机床原点的距离。
2、参考坐标系:以参考点为原点,坐标方向与机床坐标方向相同建立的坐标系。
通常以参考坐标系计算坐标值。
3、工件坐标系:编程员为了简化编程,在工件上指定的坐标系。
在工件坐标系中,坐标值是刀尖相对工件原点的距离。
工件坐标系原点设置原则:a、尽可能与设计、工艺和检验基准重合b、便于数学计算、简化程序编制c、便于对刀d、便于观察数控车床几个坐标系的区别返回参考点机床坐标系参考坐标系工件坐标系车床卡盘工 件刀补Z值刀补X值=2L车刀1、程序号:Oxxxx (四位数字)2、程序段格式:N—G—X—Z—F—S—T—M—EOB顺序号准备功能尺寸功能进给速度主轴转速刀具指令辅助功能结束符返回F:进给速度指令用于指定加工时刀具的进给速度。
单位:mm/min(程序用G98指令时)或mm/r(程序用G99指令时)。
F: 外圆:0.1~0.2 (mm/r)切断:0.02~0.05 (mm/r)园弧:0.05~0.1 (mm/r)F指令为模态指令,实际进给率可通过CNC面板上的进给倍率旋钮,在0-120%之间控制。
- 1、下载文档前请自行甄别文档内容的完整性,平台不提供额外的编辑、内容补充、找答案等附加服务。
- 2、"仅部分预览"的文档,不可在线预览部分如存在完整性等问题,可反馈申请退款(可完整预览的文档不适用该条件!)。
- 3、如文档侵犯您的权益,请联系客服反馈,我们会尽快为您处理(人工客服工作时间:9:00-18:30)。
二、培养目标
1.方法能力目标 培养学生自学的能力;培养学生勤于思考、做事认真 的态度;培养学生良好的职业道德;培养学生收集信息、 正确评价信息的能力;培养学生展示自己的技能的能力。 2.社会能力目标 培养学生的沟通能力及团队协作精神;培养学生分析 问题、解决问题的能力;培养学生的社会适应能力;培养 学生质量、成本、安全意识;培养学生接受新事物的能力。 3.专业能力目标 熟练掌握数控车床对刀技术;熟悉不同系统的数控车 床之间代码的区别;熟悉车床编程的原则和维修保养方法。
数控车床编程与操作
适用专业: 数控技术 开设时间: 第二学年第一期 课 时 数: 64 制 定 人: 刘祥 审 核 人: 金江
内容介绍:
一、课程概述
二、培养目标
三、与前后课程的联系 四、教学内容与学时分配 五、学习资源的选用 六、教师要求
七、学习场地、设施要求
八、考核方式与标准 九、学习情境设计
一、课程概述
项目编号 考核点及占项目分值比
9 10 11 12 13 14 15 16 17 18 组织协调能力(5%) 工件坐标系的设定(5%) 详细设计方案(5%) 操作实施(5%) 项目总结报告(10%) 制订加工方案(5%) 实施(5%) 检查与产品上交(谈话方式)(5%) 根据引导文通过资讯制定总体设计方案 (5%) 项目总结报告(10%)
九、学习情境设计
学习情境是学习领域进行知识与技能传授的纽 带,本学习领域课程安排台阶轴的数控车削工艺分 析及程序编制等8个学习情境,每个学习情境从项 目目标、项目任务、教师知识与能力要求、学生知 识与能力准备、教学材料、使用工具、实施步骤等 多个方面提出了要求。
例 1:
学习情境 1.台阶轴的数控车削工艺分析及程序编制 项目目 标 学时:8
《数控车床编程与操作》课程是数控技术专业的一门专 业课。它系统的介绍了数控车床编程与操作的知识。数控 车床作为当今使用最广泛的数控机床之一,主要用于加工 轴类、盘套类等回转体零件,能够通过程序控制自动完成 各工序的切削加工,而数控车削中心和数控车铣中心的使 用,不仅可以一次装夹中可以完成多种工序,还提高了加 工质量和生产效率。 本课程有助于培养具有较高动手能力的技术人员,让他 们熟知常见的几种数控车床的操作技巧。
四、教学内容与学时分配
项目编号 项目名称
1 2 台阶轴的数控车削工艺分析及程序编制 锥度小轴的数控车削加工工艺分析及程序编制
3
4 5
螺零件的数控加工工艺及编程与实施
内孔零件的数控加工艺编程与实施 工艺花瓶的数控加工工艺与实施
6
7 8
工艺酒杯的数控加工工艺与实施 工艺葫芦的数控加工工艺与实施 工艺子弹头的数控加工工艺与实施
为保证学生项目、任务的实施与完成,本课程在具备 安装宇龙仿真软件的多媒体教室及数控实训车间完成教学 过程。
八、考核方式与标准
项目编号 考核点及占项目分值比
1 2 3 4 5 6 7 8 了解数控车床的发展及分类(5%) 常用的数车系统(5%) 刀具及常用量具的认识及制图的相关知识(5%) 项目总结报告(5%) 工作与职业操守(5%) 学习态度(5%) 团队合作精神(5%) 交流及表达能力(5%)
教学方法 建议 讲授法 讨论法 演示法 自学法 小组讨论 法 小组工作 法 交互检查 法 讨论法
学 时 1
0.5 6
0.5
步骤 1.认 知、 资讯 2.计 划与 决策 3.实 施 4.检 查与 评估
教学过程 学生根据任务书,分析任务要求。确定台阶轴 的加工方案。 1.各小组考虑安全问题,讨论台阶轴的加工工 艺方案以及刀具的选择。 2.教师引导小组确定方案。 小组成员依照方案,分工合作完成台阶轴的加 工。 1.学生加工的产品是否满足精度要求,并对整 个过程进行评估。 2.教师对学生的操作过程及小组的产品质量进 行评估。
六、教师要求
1.具有数控车床编程与操作的理论知识与实践操 作能力; 2.具备宇龙仿真软件的使用能力; 3.课内实践部分主讲教师必须具备2年以上现场实 际工作经验或3年以上实践指导教学经历; 4.具备设计基于行动导向的教学法的设计应用能 力; 5.拥有相关考评员资格证或中、高级资格证。
七、学习场地、设施要求
1.掌握数控车床的种类及组成; 2.掌握数控车床面板功能; 3.掌握数控车床手动操作与试切削; 4.掌握数控车床MDI操作及对刀。 1.完成数控车床回参考点操作; 2.完成数控车床刀具装拆和工件装夹; 3.完成数控车床手动操作及试切加工; 4..完成数控车床程序输入; 5.完成数控车床程序复制、删除等编辑操作 6.完成程序内容的编辑处理; 7.完成数控车床简单报警处理 8.形成项目报告。
五、学习资源的选用
1.教材选取的原则 强调理论与实践的结合、教材与实际的结合、操作与 管理的结合,教学内容符合现场生产管理要求。 2.推荐教材 数控编程与操作技术(实训版).北京.冶金工业出版 社,2008. 3.参考的教学资料 学习情景授课计划、引导文、参考资料、工艺文件、 项目检查单、项目评价表、教学课件、练习题、企业生产 视频。
三、与前后课程的联系
1.前续课程 《机械制造基础》 本课程使学生初步掌握各种成形方法、 零件加工工艺知识,具有选择毛坯、零件加工方法及进行 工艺分析的能力;了解现代机械制造有关的新材料、新工 艺、新技术及其发展趋势。 《公差配合与测量技术》 本课程通过介绍几何量公差的 有关标准、选用方法和误差检测的基本知识,使学生学到 有关精度设计和几何量检测的基础理论知识和基本技能。 2. 后续课程 为《数控机床诊断与维护》、《数控车(铣)床编程与操 作工》等后续课程打下基础。
项目任 务
教师 知识 与能 力准 备 学时 知识 与能 力准 备 教学 材料 使用 工具
熟悉数控机床操作技能,熟悉数控加工的工艺与流程,熟练掌 握数控加工工艺,熟悉机械产品的相关生产管理知识,具有娴 熟的教学组织与管理能力。
具备机械加工工艺基础、识图能力,了解数控车床的基本编程 方法。
工艺文件、教学资料、引导文、任务书、评价表。 多媒体、数控车床、常用车刀、量具、毛坯、绘图工具、绘图 软件、仿真软件、电脑。