重油催化裂化装置加工加氢精制蜡油的技术分析
蜡油的加氢裂化反应
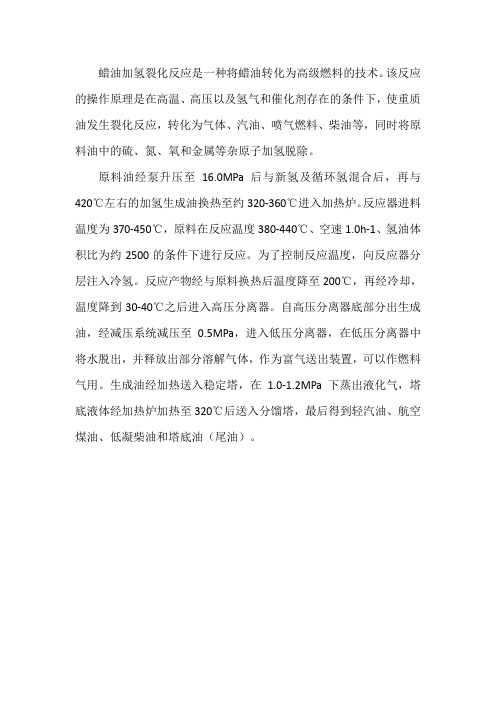
蜡油加氢裂化反应是一种将蜡油转化为高级燃料的技术。
该反应的操作原理是在高温、高压以及氢气和催化剂存在的条件下,使重质油发生裂化反应,转化为气体、汽油、喷气燃料、柴油等,同时将原料油中的硫、氮、氧和金属等杂原子加氢脱除。
原料油经泵升压至16.0MPa后与新氢及循环氢混合后,再与420℃左右的加氢生成油换热至约320-360℃进入加热炉。
反应器进料温度为370-450℃,原料在反应温度380-440℃、空速1.0h-1、氢油体积比为约2500的条件下进行反应。
为了控制反应温度,向反应器分层注入冷氢。
反应产物经与原料换热后温度降至200℃,再经冷却,温度降到30-40℃之后进入高压分离器。
自高压分离器底部分出生成油,经减压系统减压至0.5MPa,进入低压分离器,在低压分离器中将水脱出,并释放出部分溶解气体,作为富气送出装置,可以作燃料气用。
生成油经加热送入稳定塔,在1.0-1.2MPa下蒸出液化气,塔底液体经加热炉加热至320℃后送入分馏塔,最后得到轻汽油、航空煤油、低凝柴油和塔底油(尾油)。
4.0Mta蜡油加氢裂化装置的运行优化
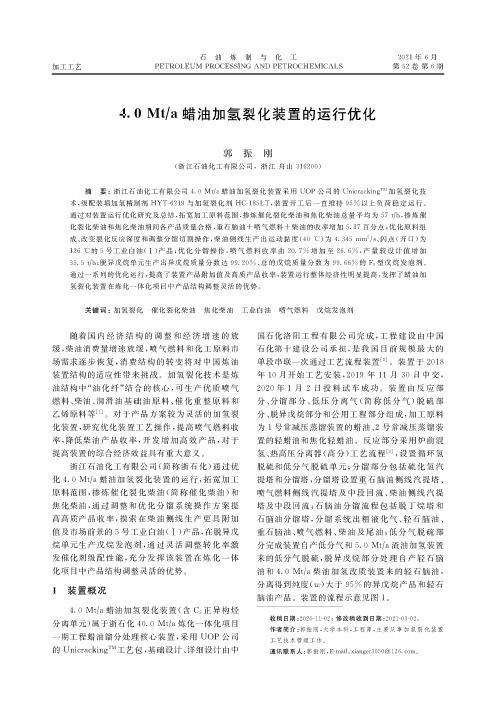
石油炼制与化工PETROLEUM PROCESSING AND PETROCHEMICALS2021年6月第52卷第6期加工工艺40Mt/a蜡油加氢裂化装置的运行优化郭振刚(浙江石油化工有限公司,浙江舟山316200/摘要:浙江石油化工有限公司4.0Mt/a蜡油加氢裂化装置采用UOP公司的Unicracking TM加氢裂化技术,级配装填加氢精制剂HYT6219与加氢裂化剂HC-185LT,装置开工后一直维持95%以上负荷稳定运行。
通过对装置运行优化研究及总结,拓宽加工原料范围,掺炼催化裂化柴油和焦化柴油总量平均为57t/h,掺炼催化裂化柴油和焦化柴油期间各产品质量合格,重石脑油+喷气燃料+柴油的收率增加5.17百分点;优化原料组成、改变裂化反应深度和调整分馏切割操作,柴油侧线生产出运动黏度(0O为4.345mm2/s、闪点(开口)为126c的5号工业白油(I)产品;优化分馏操作,喷气燃料收率由20.7%增加至26.6%,产量较设计值增加35.5t/h;脱异戊烷单元生产出异戊烷质量分数达99.20%、总的戊烷质量分数为99.66%的F。
型戊烷发泡剂。
通过一系列的优化运行,提高了装置产品附加值及高质产品收率,装置运行整体经济性明显提高,发挥了蜡油加氢裂化装置在炼化一体化项目中产品结构调整灵活的优势。
关键词:加氢裂化催化裂化柴油焦化柴油工业白油喷气燃料戊烷发泡剂随着国内经济结构的调整和经济增速的放缓,柴油消费量增速放缓,喷气燃料和化工原料市场需求逐步恢复,消费结构的转变将对中国炼油装置结构的适应性带来挑战。
加氢裂化技术是炼油结构中“油化纤”结合的核心,可生产优质喷气燃料、柴油、润滑油基础油原料、催化重整原料和乙烯原料等[1]。
对于产品方案较为灵活的加氢裂化装置,研究优化装置工艺操作,提高喷气燃料收率,降低柴油产品收率,开发增加高效产品,对于提高装置的综合经济效益具有重大意义。
浙江石油化工有限公司(简称浙石化)通过优化4.0Mt/a蜡油加氢裂化装置的运行,拓宽加工原料范围,掺炼催化裂化柴油(简称催化柴油)和焦化柴油,通过调整和优化分馏系统操作方案提高高质产品收率,摸索在柴油侧线生产更具附加值及市场前景的5号工业白油(I)产品,在脱异戊烷单元生产戊烷发泡剂,通过灵活调整转化率激发催化剂级配性能,充分发挥该装置在炼化一体化项目中产品结构调整灵活的优势。
浅析重油加氢技术

运动 , 形成气 、液、同三相床层 , 从而使原料油 、氢气以及催化剂充分 接触而完成加氢裂化反应 。此工艺能够处理残炭值 与金属含量较高 的原
料, 并能深度转化重油。但是此工艺 的操作温度较高,一般在 4 0 0 ~ 4 5 0
合反应 ,避免产生大量焦炭 和低价值产物 ,加氢裂化产物 中不含烯烃 ,
( 1 )固定床一段加氢裂化工艺
一
段加氢裂化一般来说用于 由粗汽油生产液化气 ,由脱沥青油与减
硫 、氮的含量也非常少 ,因此产品的胶质 、色泽与安定性都很好 , 产品
j 蜡油生产柴油 与航空煤油 等。一段加氢裂 的化反应器只有一个 ,原料
℃。
就是组合工艺。 最常见的是重油加氢一 催化裂化组合工艺 , 其液收率与轻 油收率高 , 投资省 ,回报大 。此外 , 依照原料的性质还能够发展重油加
二段加氢裂化 ;另一种是第一段不但进行精制,还进行部分裂化 ,第二 段进行加氢裂化 。 两段加氢裂化工艺对原料的适应性大 , 操作 比 较灵活 。 ( 3 ) 沸腾床加氢裂化 沸腾床加氢裂化工艺是借助于流体流速带动一定颗粒粒度 的催化剂
硫 、氮、金属的脱 除率 ,提高加 工能力 ,在降低装置投资和操作费用方
【 关键 词 】 重 油 加 氢技 术 中图分类号 :T E 6 2 4文献标识码:B 文章编号:1 0 0 9 _ 4 O 6 7 ( 2 0 1 4 ) 2 1 — 7 2 O 1
一
、
概 述
三、重油加氢 裂化技术 的特点
重油加氢裂化技术使用的催化剂具有加氢和裂化两种作用 ,所以该 技术具有原料适应性强 、 转化率商、操作灵活性大、 产 品质量好等特点。 l 、原料适应陛强 :高压加氢裂化的原料可以是焦化馏分油 、催化裂 化循环油 、 常减压渣油 、 脱沥青油等 。同时还能有效 的处理含硫 、 金属 、 残炭 、 氮等杂质含量高的劣质原料油。
催化裂化装置优化技术分析-收率与能耗

一、催化裂化装置能耗分析
影响的催化裂化装置能耗的第二大因素是装置 蒸汽输出量。由于重油催化裂化装置原料较重,生 焦率高,焦炭在再生器中燃烧释放出的热量除提供 裂化反应热外,还有大量的剩余,如何合理利用装 置的高温位余热发生蒸汽,以蒸汽为介质回收热量、 提高装置利用热能的能力是降低装置能耗的有效手 段。
中国石油大庆石化公司炼油厂
二、催化裂化装置节能措施
2.7催化与气分装置进行热联合 因此,催化装置低温热能的综合利用,对装置能耗有
很大的影响。锦西石化公司1.0Mt/a重油催化裂化装置分 馏系统与气分装置进行热联合,其中,催化顶循环油引 至气分脱丙烷塔底作源;两外把高温热水由P311A/B抽 出后去催化,分别和分馏塔顶油气、轻柴油、一中循环 油、产品油浆换热,把油品冷却到合适温度,把高温热 水加热到105℃左右送到了气分装置,作为气分装置的热 源。
中国石油大庆石化公司炼油厂
一、催化裂化装置能耗分析
项目 焦炭 新鲜水 循环水 除盐水 电耗 3.6MPa 蒸汽 1.0MPa 蒸汽 3.6+1.0 蒸汽 0.3MPa 蒸汽 低温输出热 总加工原料量 合计能耗
表-1 某催化裂化装置近四年能耗构成
能耗系数 950 0.18 0.1 2.3
0.2338 88 76
题目:催化裂化装置优化技术分析 ——收率与能耗
王文清
中国石油大庆石化公司炼油厂
目录
催化裂化装置能耗分析 催化裂化装置节能措施 优化工艺提高催化装置产品收率 其他提高产品收率及降低能耗的措施 炼油厂能耗计算与评价方法
中国石油大庆石化公司炼油厂
一、催化裂化装置能耗分析
催化裂化装置是我国炼油行业的主要二次加工装 置,也是占炼油厂能耗比例最大的装置之一,催化装 置能耗一般占炼油厂全厂能耗的30%~50%。随着原 油价格的不断攀升以及催化裂化原料的日益重质化, 催化裂化节能降耗问题成为了提高催化裂化装置经济 效益的关键问题,装置节能降耗的重要性尤为突出。 表-1为某催化裂化装置近四年来的能耗分析数据。
石油化工重油催化裂化工艺技术

石油化工重油催化裂化工艺技术石油化工重油催化裂化工艺技术是一种将重油转化为轻质油和化学品的过程。
该过程主要利用催化剂的作用,在高温高压条件下,使重油的大分子裂解成小分子,同时发生异构化、芳构化和氢转移等反应,以获得更多的轻质油和化学品。
催化剂的选择:催化剂是该技术的核心,其选择对产品的质量和产量有着至关重要的影响。
目前,常用的催化剂包括酸性催化剂、金属催化剂和金属氧化物催化剂等。
工艺条件的控制:工艺条件包括反应温度、压力、空速等,这些因素对产品的质量和产量都有着极大的影响。
因此,精确控制这些工艺条件是重油催化裂化工艺技术成功应用的关键。
产品的质量和性能:重油催化裂化工艺技术生产的产品具有高辛烷值、低硫含量等特点,被广泛应用于汽油、柴油、航空煤油等领域。
在应用方面,石油化工重油催化裂化工艺技术适用于不同类型重油,如减压渣油、催化裂化残渣油、脱沥青油等。
对于不同工业应用,可根据实际需求选择合适的工艺技术。
例如,对于生产高质量汽油和柴油的需求,可以选择更为精细的催化剂和严格的工艺条件;对于生产高附加值化学品的需求,则可以通过调整工艺流程和催化剂类型来增加化学品产量。
虽然石油化工重油催化裂化工艺技术在提高石油利用率、生产高质量石油化工产品方面具有重要作用,但也面临着一些挑战。
催化剂的活性、选择性和稳定性是该技术的关键,而目前催化剂的研究与开发尚存在诸多困难。
重油催化裂化过程中产生的固体废物和废气等对环境造成了严重影响,亟需解决。
由于重油资源的有限性,需要进一步探索和研发更为高效、环保的石油化工技术,以适应未来可持续发展的需要。
石油化工重油催化裂化工艺技术在石油化工产业中具有重要地位。
随着经济的发展和科技的进步,该技术将不断完善和优化,提高石油利用率和生产效率,同时注重环保和可持续发展。
未来,需要加强催化剂的研发与优化,减少环境污染,提高技术的绿色性和可持续性。
应积极探索新的石油化工技术,以应对全球能源危机和环境问题的挑战。
催化裂化操作要素及案例分析
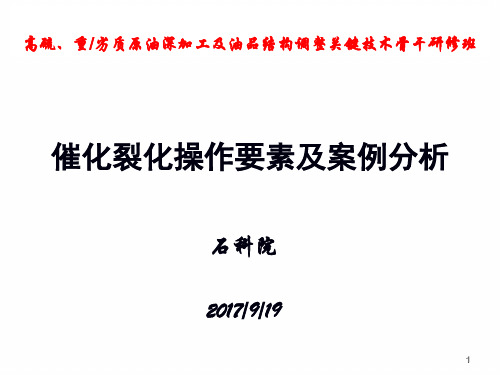
243 298
331
291 333 367 358
367 397 426 406
409 436 470 453
450 477 521 500
507 534
562
0.35 0.51 3.28 1.4
1812 1043 1105 1558
0.9408 0.9117 0.9238 0.9372
3
二次加工—催化裂化技术
以重油为原料,通常为大于350℃的重质油,包 括 VGO、CGO、DAO、AR、VR和经过加氢处理的 相应馏分
采用酸性催化剂和流化反应器 通过催化裂化反应 生产汽油、柴油和液化气等产物的工艺过程 装置主要包括反应再生、分馏、吸收稳定及能
量回收系统
4
石脑油、催汽与汽油标准的差异
0.4 0.2 2.6
1.2
0.6 0.4 5.5
1.8
2.6 1.36 1.92 2.1
UOP EMII R2R UOP
3.0
0.928 9.0 9.0
0.82 UOP
344
轻收 82.10 81.92 81.80 82.71 83.89 83.76 83.95 83.70 83.42 转化率 67.53 67.84 68.94 70.32 71.41 71.65 72.45 72.89 73.57
14
催化汽油
催化汽油
催化汽油为目的产物,产率相对较高, 通常在40%以上,约占汽油池的60%
38 49 63 79 113 161 184
19.9 28.2 51.8
汽油 2 0.7276
30.5 44.9 59.6 84.7 126.3 167.4 199.1
催化裂化
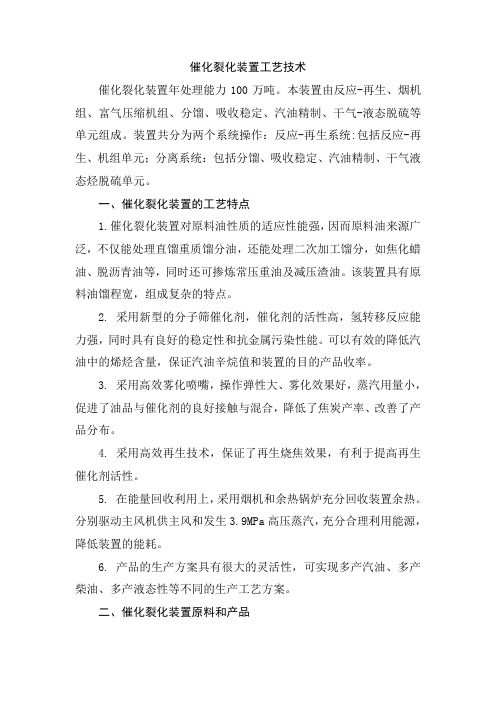
催化裂化装置工艺技术催化裂化装置年处理能力100万吨。
本装置由反应-再生、烟机组、富气压缩机组、分馏、吸收稳定、汽油精制、干气-液态脱硫等单元组成。
装置共分为两个系统操作:反应-再生系统:包括反应-再生、机组单元;分离系统:包括分馏、吸收稳定、汽油精制、干气液态烃脱硫单元。
一、催化裂化装置的工艺特点1.催化裂化装置对原料油性质的适应性能强,因而原料油来源广泛,不仅能处理直馏重质馏分油,还能处理二次加工馏分,如焦化蜡油、脱沥青油等,同时还可掺炼常压重油及减压渣油。
该装置具有原料油馏程宽,组成复杂的特点。
2. 采用新型的分子筛催化剂,催化剂的活性高,氢转移反应能力强,同时具有良好的稳定性和抗金属污染性能。
可以有效的降低汽油中的烯烃含量,保证汽油辛烷值和装置的目的产品收率。
3. 采用高效雾化喷嘴,操作弹性大、雾化效果好,蒸汽用量小,促进了油品与催化剂的良好接触与混合,降低了焦炭产率、改善了产品分布。
4. 采用高效再生技术,保证了再生烧焦效果,有利于提高再生催化剂活性。
5. 在能量回收利用上,采用烟机和余热锅炉充分回收装置余热。
分别驱动主风机供主风和发生3.9MPa高压蒸汽,充分合理利用能源,降低装置的能耗。
6. 产品的生产方案具有很大的灵活性,可实现多产汽油、多产柴油、多产液态性等不同的生产工艺方案。
二、催化裂化装置原料和产品(一)原料催化裂化装置原料主要是减三线、减四线蜡油和加氢蜡油HGO,一般来讲,衡量原料油性质指标有:馏份组成、烃类族组成、残碳、重金属、硫氮含量等五个方面。
(l) 馏份组成:馏份组成可以辨别原料的轻重和沸点范围的宽窄,在组成类型相近时,馏份越轻,越不易裂化,馏份越重,越容易裂化,因为轻组分多,不但裂化条件苛刻,而且减少了装置处理能力,同时降低汽油的辛烷值。
重组分多,使重金属含量增加及焦炭产率增加,轻质油收率下降,还会使催化剂中毒。
(2) 烃类族组成:原料油的烃类族组成说明了原料油被催化剂吸附反应的快慢。
石油化工催化裂化技术的工艺优化分析

石油化工催化裂化技术的工艺优化分析发布时间:2023-03-03T08:56:47.868Z 来源:《科技新时代》2022年第20期作者:王中亮杨立志[导读] “三油并轨”政策的实施和车用柴油标准的升级将进一步减少污染物的排放王中亮杨立志中国石油哈尔滨石化公司第二联合车间 150056摘要:“三油并轨”政策的实施和车用柴油标准的升级将进一步减少污染物的排放,保护环境,并推动发动机企业技术进步和炼油企业转型升级。
例如,车用柴油国Ⅵ质量标准要求大幅降低柴油的硫含量和多环芳烃含量,这将使催化裂化柴油(LCO)占比较高的炼油企业面临巨大技术经济挑战。
这是因为LCO的总芳烃质量分数为50%~70%,且双环芳烃占比很大,为总芳烃的40%~60%;同时LCO的硫、氮等杂质含量高、十六烷值低,难以直接作为柴油馏分,必须进一步深入加工才能满足国Ⅵ柴油质量标准的要求。
LCO深加工技术主要有加氢精制、加氢改质等技术。
通过加氢,可以脱除LCO中的硫和氮元素,但LCO加氢过程需要高苛刻度的工况条件,氢耗高、操作成本高、经济效益差。
同时,随着消费柴汽比的不断下降,炼油企业间的竞争不断加剧,为LCO加工路线的选择带来巨大挑战。
因此,探寻最优LCO加工路径,实现低成本提升LCO经济价值成为研究热点。
关键词:催化裂化;低辛烷值汽油;辛烷值引言我国FCC汽油为商品汽油的主要组分,其在商品汽油中的比例达70%以上,无论目前还是可预见的未来,FCC汽油在炼油厂中的重要地位不容置疑。
FCC汽油性质明显优于热裂化汽油,而且,稳定性要比热裂化汽油高得多,各种烃类在FCC汽油中大致分为正构烷烃约5%,异构烷烃在25%~33%之间,环烷烃在6%~12%之间,烯烃在33%~46之间,芳烃在16%~22%之间。
高辛烷值汽油能够提高发动机的功率和热效率,提高汽油辛烷值已经成为各汽油生产单位的主要努力方向。
粗汽油作为终止剂在催化裂化装置上进行工业应用已经取得了不错的效果,能够抑制氢转移二次反应和减少热裂化反应,提高重油催化裂化的轻质油和液化气收率,降低干气和焦炭产率。
重油催化裂化柴油吸附脱氮-加氢精制组合工艺的开发
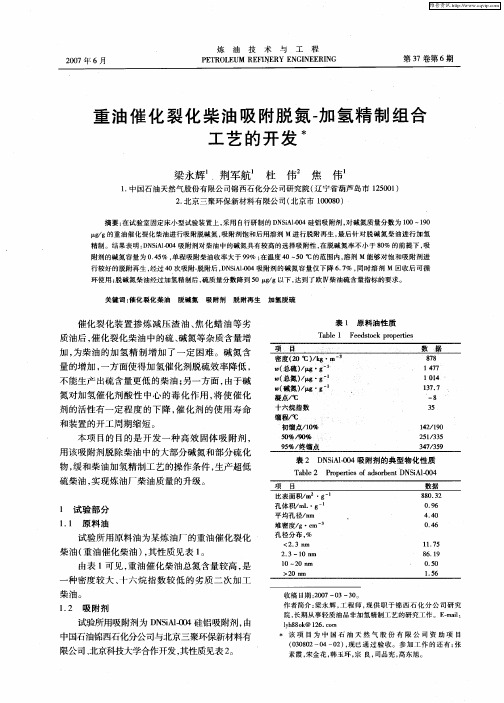
1 中国石油 天然气股份有 限公 司锦西石化分公 司研究 院( . 辽宁省葫芦岛市 150 ) 20 1 2 北京三 聚环保新材料有 限公 司( 京市 10 8 ) . 北 0 0 0
摘要 : 在试验室固定床小 型试验装置上 , 采用 自行研制 的 D SA - 4硅铝吸附剂, N i1 0 0 对碱 氮质量分数为 10~10 0 9
gg的重油催化裂化柴油进行吸附脱碱氮 , / 吸附剂饱和后用溶剂 M进行脱 附再生 , 最后针 对脱碱氮柴 油进行加氢
精制。结果表明 : N i1 0 D SA- 4吸附剂对柴油 中的碱氮具有较高 的选择吸附性 , 0 在脱碱氮率不小于 8 % 的前提下 , 0 吸 附剂的碱氮容量为 04 % , .5 单程吸附柴 油收率大于 9 % ; 9 在温度 4 5 0~ 0℃ 的范 围内, 溶剂 M能够对饱 和吸附剂进 行较好的脱附再 生 , 经过 4 0次吸附一 附后 , N i1 0 脱 D SA - 4吸附剂的碱氮容量仅 下降 6 7 , 0 . % 同时溶 剂 M 回收后可循
由表 1 见 , 油催 化柴油 总氮 含量 较高 , 可 重 是
一
种 密度 较大 、 十六 烷 指 数较 低 的劣 质 二 次加 工
收 稿 日期 :0 7—0 20 3—3 0。
柴油。
1 2 吸 附 剂 .
ห้องสมุดไป่ตู้
作者简介 : 梁永辉 , 工程 师 , 供职 于锦西 石化 分公 司研 究 现 院, 长期从事轻质油品非加氢精 制工艺 的研究工作。Ema : — i l
l h 8 k 1 6. o y 8 o @ 2 c m
试验所 用吸附剂为 D S ID N i - 4硅铝 吸附剂 , A( 由 中国石油锦西石化分公司与北京三聚环保新材料有
1#催化裂化装置加工蜡油适应性改造效果分析
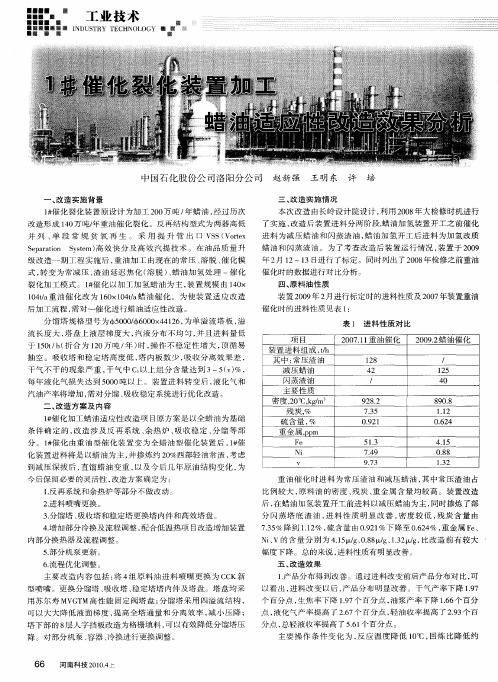
1 再系统和余热炉等部分不做改动 。 . 反 2进 料 喷 嘴 更 换 。 . 3分 馏 塔 、 . 吸收 塔 和 稳 定 塔 更 换 塔 内件 和高 效 塔 盘 。 4增 加部 分 冷换 及 流程 调整 , 合 低 温 热 项 目改 造 增 加 装 置 . 配 内部 分 换 热 器 及 流 程 调 整 。
工业 技术
一 圈 黼 曩 瓣 ■ ■ 糕 ■ ■ 糕 ■ ■ 囊 器 藤 麟 瀑
瓣
I NDUS RY T T ECHNOLOGY 爨
中 国石化 股份 公 司洛 阳分 公 司
一
赵 新 强 王 明 东
三 、 造 实 施 情 况 改
许
培
、
改 造 实 施 背 景
l 催 化 裂 化 装 置 原 设 计 为 加 工 2 0 吨 / 蜡 油 , 过 历 次 # 0万 年 经
流 长度 大 , 盘 上 液 层 梯 度 大 , 液 分 布 不 均 匀 , 且 进 料 量 低 塔 汽 并
装 置 2 0 年 2 进 行 标 定 时 的 进 料 性 质 及 2 0 年 装 置 重 油 09 月 07 催 化 时 的进 料 性 质 见 表 1 :
表 1 进 料 性 质 对 比
98 2. 2 73 - 5 0 2 . 1 9
5l_ 3
7. 49
9 73 .
2 0 .蜡 油 催 化 09 2 |
l5 2 4 0 8 08 9. 11 . 2 064 . 2
催化裂化、催化裂解、热裂解技术对比

催化裂化、催化裂解、催化重整、加氢精制与裂解、芳烃抽提技术总结
MGG是以减压渣油、掺渣油和常压渣油等为原料的最大量生产富含烯烃的液态烃,同时最大生产高辛烷值汽油的工艺技术,与其他同类工艺的差别在于它在多产液态烃下还能有较高的汽油产率,并且可以用重油作原料(包括常压渣油)。
反应温度在510~540℃时,液化气产率可达25%~35%(摩尔比),汽油产率40%~55%(摩尔比)。
液化气加汽油产率为70%~80%。
汽油RON 一般为91~94,诱导期为500~900 min。
这一技术是以液化气富含烯烃、汽油辛烷值高和安定性好为特点的,现已有多套装置应用。
MIO技术是以掺渣油为原料,较大量地生产异构烯烃和汽油为目的产物的工艺技术。
1995年3-6月在中国兰州炼化总厂实现了工业化。
以石蜡基为原料时,缩短反应时间和采取新的反应系统,异构烯烃的产率高达15%(摩尔比)。
重油催化裂化装置主要工艺流程说明
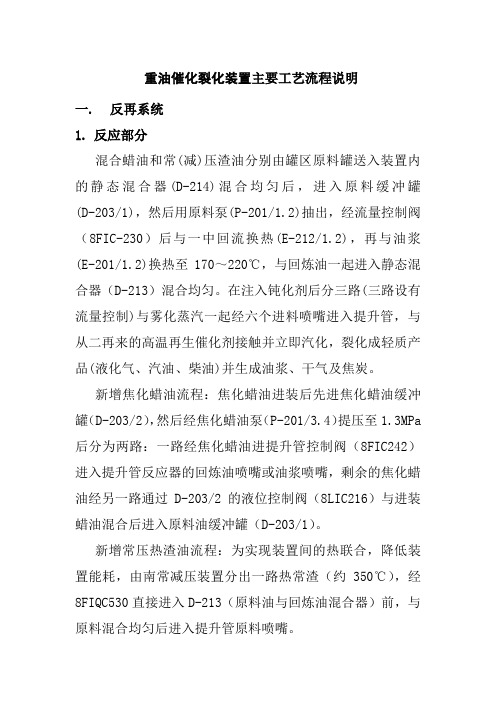
重油催化裂化装置主要工艺流程说明一. 反再系统1.反应部分混合蜡油和常(减)压渣油分别由罐区原料罐送入装置内的静态混合器(D-214)混合均匀后,进入原料缓冲罐(D-203/1),然后用原料泵(P-201/1.2)抽出,经流量控制阀(8FIC-230)后与一中回流换热(E-212/1.2),再与油浆(E-201/1.2)换热至170~220℃,与回炼油一起进入静态混合器(D-213)混合均匀。
在注入钝化剂后分三路(三路设有流量控制)与雾化蒸汽一起经六个进料喷嘴进入提升管,与从二再来的高温再生催化剂接触并立即汽化,裂化成轻质产品(液化气、汽油、柴油)并生成油浆、干气及焦炭。
新增焦化蜡油流程:焦化蜡油进装后先进焦化蜡油缓冲罐(D-203/2),然后经焦化蜡油泵(P-201/3.4)提压至1.3MPa 后分为两路:一路经焦化蜡油进提升管控制阀(8FIC242)进入提升管反应器的回炼油喷嘴或油浆喷嘴,剩余的焦化蜡油经另一路通过D-203/2的液位控制阀(8LIC216)与进装蜡油混合后进入原料油缓冲罐(D-203/1)。
新增常压热渣油流程:为实现装置间的热联合,降低装置能耗,由南常减压装置分出一路热常渣(约350℃),经8FIQC530直接进入D-213(原料油与回炼油混合器)前,与原料混合均匀后进入提升管原料喷嘴。
反应油气、水蒸汽、催化剂经提升管出口快分器分离出大部分催化剂,反应油气经过沉降器稀相沉降,再经沉降器(C-101)内四组单级旋风分离器分离出绝大部分催化剂,反应油气、蒸汽、连同微量的催化剂细粉经大油气管线至分馏塔人档下部。
分馏塔底油浆固体含量控制<6g/L。
旋分器分出的催化剂通过料腿返回到汽提段,料腿装有翼阀并浸没在汽提段床层中,保证具有正压密封,防止气体短路,汽提蒸汽经环形分布器进入汽提段的上中下三个部位使催化剂不仅处于流化状态,并汽提掉催化剂夹带的烃油气,汽提后的催化剂通过待生滑阀进入一再催化剂分布器。
重油催化裂化装置掺炼焦蜡总结
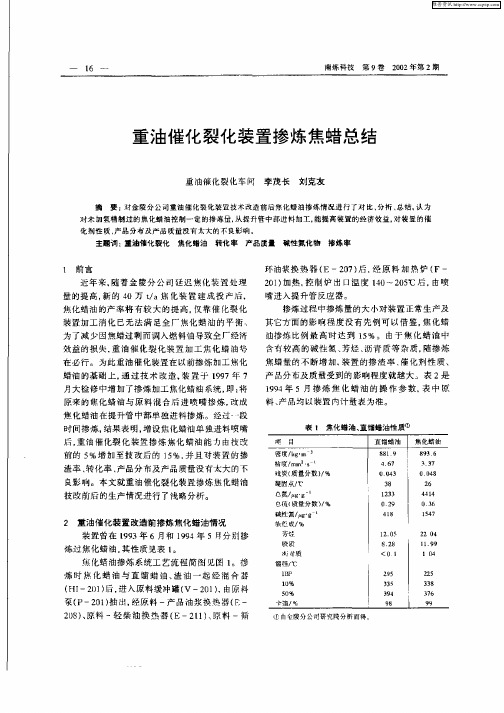
l O% 5 0%
35 3 34 9
33 8 36 7
蒲/ %
9 8
9 9
① 巾 采睦 丹 公 司 研 究 院 丹折 而 得
维普资讯
重油催化裂化装置掺炼焦蜡总结——李茂 长 刘克友
一
1 7
m ㈣
图 1 改造前焦化蜡油掺炼 系统工艺流程筒图 表 2 19 年 5月掺炼焦 化蜡油的操作参数 94
1 前 言
环油浆换 热 器 ( E一27 后 . 原 料加 热 炉 ( 0) 经 F一
2 1 加 热, 制 炉 出 口温 度 10 0 ℃ 后 , 0) 控 4 ~2 5 由喷 嘴进 入提 升管反应器 。 掺炼过 程中掺炼 量 的大小 对装置 正常 生产 及 萁它方 面 的影响 程 度 没有 先 例 可 以借 鉴 , 化 蜡 焦 油掺 炼 比例 最 高 时达 到 1 %。 由于 焦 化 蜡 油 中 5
近年 来 , 随着金 陵分 公 司 延迟 焦 化 装置 处 理 量 的提 高 , 的 4 新 0万 ta焦 化 装置 建 成 投 产 后, / 焦 化蜡油 的产率 将 有较 大 的提高 , 靠 催 化 裂化 仅 装置加 工 消化 已无 法 满 足全 厂 焦 化蜡 油 的平 衡 。 为 了减少 固焦蜡过 剩 而调 入燃料油 导致全 厂经济 效益 的损 失, 油 催化 裂 化 装置 加 工 焦化 蜡 油 势 重 在必行 。 为此重 油催化 装置 在 以前 掺炼加 工焦 化 蜡油 的基础 上, 过 技 术 改造 , 置于 19 通 装 9 7年 7 月大检 修 中增 加 了掺 炼加 工焦 化蜡油 系统 , : 即 将 原来 的焦 化蜡 油与 原 料混 合后 进 喷 嘴 掺炼 , 成 改
维普资讯
1 一 6
催化裂化装置流程模拟与优化案例分析[1]
![催化裂化装置流程模拟与优化案例分析[1]](https://img.taocdn.com/s3/m/75cdd7b38bd63186bcebbc7a.png)
裂化热因子
裂化热因子 =
表观裂化热 理论裂化热
第16/45页
8
3、数据输入及模型校正
焦中氢
第17/45页
4、预测研究及模型微调
预测模式
主体预测 全部预测
第18/45页
9
4、预测研究及模型微调
典型独立变量
新鲜进料流率 提升管出口温度 原料预热温度 主风量 烟气O2含量 再生剂定碳 新鲜剂补充量 平衡剂活性
5
10
15
柴油(W%)与操作条件关系
6.00 5.95 5.90 5.85 5.80 5.75
0
5
10
15
生焦量(W%)与操作条件关系
92.0
91.8
91.6
91.4
91.2
91.0
0
2
4
6
8
10
12
14
装置液收(C3+液体,W%)与操作条件关系
从以上产品收率变化趋势 可以出工况5为预测工况中最 好操作条件。
序号 1 2 3 4 5
解吸塔塔底温度 122℃ 123℃ 124℃ 125℃ 126℃
干气中丙烯(wt%) ? ? ? ? ?
第28/45页
14
例:操作参数目标值筛选
序号 1 2 3 4 5
解吸塔塔底温度 122℃ 123℃ 124℃ 125℃ 126℃
干气中丙烯 1.69wt% 1.73wt% 1.80wt% 1.89wt% 2.47wt%
原料重量 — 产品重量 误差 =
× 100
原料重量
误差大于 +/- 2.0% 数据需要重新核查
第11/45页
2、物料平衡校验
合理的产品收率
加氢裂化装置加工焦化蜡油的难点分析与对策

加氢裂化装置加工焦化蜡油的难点分析与对策吴瑕;赵秀文;孙嫚;董佳鑫;王国旗【摘要】Through a case study of a 1.0 MM TPY hydrocracking Unit (HCU)in an overseas refinery,the physical and chemical properties of coker gasoil are compared with those of straight-run VGO.The difficulties in processing coker gas oil (CGO) in HCU are the high contents ofsulfur,nitrogen,unsaturated hydrocarbons,aromatics and coke powders as well as higher end boiling point of feedstock and higher impurities.The following countermeasures are proposed,such as:the end point of coker gas oil is controlled to be no higher than 520 ℃,the nitrogen sealing is provided for feedstock tank and water injection drum,50 ~ 100 mg/kg fouling inhibitor is injected,water injection is strictly controlled and the water from hydrocracker stripper,overhead condensate of hydrocracker tower and deaerated water are optimally selected,equipment design and material selections are optimized and filters are installed for CGO.All these are favorable for the long-term stable operation of the hydrocracking unit and provide good guidelines for the engineering design of HCU with CGO feedstocks.%以国外某炼油厂1.0 Mt/a加氢裂化装置为例,对焦化蜡油与直馏蜡油的理化性质进行了对比,分析出加氢裂化装置加工焦化蜡油的难点为硫、氮、不饱和烃、芳烃及焦粉含量高,原料干点偏高且重杂质多.针对焦化蜡油加工难点提出了以下对策:尽量控制焦化蜡油干点不高于520℃;原料油和注水罐设置氮气气封;适当注入质量分数为50~100 μg/g的阻垢剂;加强注水管理,优先选用加氢类汽提水、加氢裂化塔顶凝结水、除氧水等优质水源;优化设备设计与选材;设置焦化蜡油预过滤器等一系列针对性措施,有利于加氢裂化装置的长周期稳定运行.对进料中含有焦化蜡油的加氢裂化装置的设计具有一定的指导意义.【期刊名称】《炼油技术与工程》【年(卷),期】2017(047)006【总页数】4页(P19-22)【关键词】加氢裂化;焦化蜡油;难点分析【作者】吴瑕;赵秀文;孙嫚;董佳鑫;王国旗【作者单位】中国石油工程建设有限公司华东设计分公司,山东省青岛市266071;中国石油工程建设有限公司华东设计分公司,山东省青岛市266071;中国石油工程建设有限公司华东设计分公司,山东省青岛市266071;中国石油工程建设有限公司华东设计分公司,山东省青岛市266071;中国石油工程建设有限公司华东设计分公司,山东省青岛市266071【正文语种】中文加氢裂化技术是加工焦化蜡油的有效途径。
重油催化裂化装置主要技术方案

重油催化裂化装置主要技术方案1.1 工艺技术路线①采用多产丙烯技术采用多产丙烯技术,在降低汽油中的烯烃含量的同时,增加液化石油气特别是丙烯的产率。
②采用增产丙烯专用催化剂为满足本装置生产低烯烃汽油的要求,设计考虑采用增产丙烯专用催化剂。
③重油原料雾化采用CS型高效喷嘴CS型喷嘴具有雾化效果好、焦炭产率低、轻质油收率高、操作平稳等特点,可以充分满足工艺过程的要求,且在一定程度上可降低蒸汽消耗。
④反应再生系统采用PLY型高效旋风分离器从维持反-再系统平稳操作,减少催化剂自然跑损的角度出发,反应再生系统中旋风分离器均采用分离效率高的PLY型旋风分离器。
⑤采用高效汽提技术提高汽提效果对降低再生器烧焦负荷有很大好处。
本设计重油沉降器及汽油沉降器采用了高效汽提技术并对汽提段进行特殊设计,以改善汽提蒸汽与待生催化剂的接触,提高汽提效果。
1.2 工艺技术特点1.2.1采用同轴式两器型式本设计重油沉降器与再生器采用同轴式两器布置。
该两器型式具有技术先进、操作简单、抗事故能力强、能耗低及占地少等特点。
1.2.2再生工艺方案再生方案的选择以满足降低再生催化剂的定碳、使催化剂性能得以充分恢复,同时避免采用过于苛刻的再生条件,有利于保护催化剂活性为前提。
本装置采用单段逆流再生,催化剂定碳<0.1%。
该技术由以下几种单项技术组成:⑴采取加CO助燃剂的完全再生方案采用该方案后,平均氧浓度的提高可使再生剂含碳明显降低,特别对于单段再生其效果更加明显。
⑵采用较低的再生温度较低的再生温度有利于提高剂油比并保护催化剂活性,为反应原料提供更多的活性中心。
⑶采用逆流再生通过加高待生套筒使待生催化剂进入密相床上部,并良好分配,然后向下流动与主风形成气固逆流接触,有利于提高总的烧焦强度并减轻催化剂的水热失活。
⑷采用待生催化剂分配技术在待生套筒出口配置特殊设计的待生催化剂分配器,使待生剂均匀分布于再生密相床上部,为单段逆流高效再生提供基本的保证。
蜡油加氢和催化裂化组合工艺的应用

广州化工
2009年 37 卷第 4 期
生产技术
蜡油加氢和催化裂化组合工艺的应用
周应谦
(中石化广州分公司,广东 广州 510726)
摘 要:广州石化 210×104t/a 蜡油加氢装置是广石化加工中东含硫原油及生产清洁燃料配套改造工程之一,该装置采用劣质
蜡油加氢处理部分转化技术,对 VGO、CGO、DAO 进行加氢处理,从而为催化裂化装置提供优质蜡油原料。蜡油加氢和催化裂化组合工 艺,为广州分公司提高含硫原油的综合加工能力,改善产品分布,降低运行成本,提高经济效益起到了重要的作用。本文着重对加氢处 理装置的投产和组合工艺的运行效果进行分析。
2 蜡油组合工艺的应用
广州石化现有一套 200 万吨 / 年的催化裂化装置、一套 100 万吨 / 年的重油催化装置。加氢处理投产前催化裂化主要原料为 VGO、CGO,重油催化的主要原料为 VGO、常渣、DAO。加氢处理 投产后,加氢处理和催化裂化装置组成蜡油组合工艺,两套焦化 装置的 CGO、溶剂脱沥青装置的 DAO 等二次加工的劣质蜡油和 蒸馏 (二)B 高硫的 VGO 进加氢处理加工后作催化裂化混合进 料,而重催主要加工蒸馏(一)相对低硫的常渣和 VGO。蜡油组 合工艺自 2006 年 7 月 21 日加氢处理装置投产后开始运行。
广州石化在千万吨炼油改扩建中建设了多套加工中东含硫 原油及生产清洁燃料配套改造工程,其中 210×104t/a 加氢处理 装置就是采用劣质蜡油加氢处理部分转化技术,对 VGO、CGO、 DAO 进行加氢处理,从而为催化裂化提供优质蜡油原料。
该加氢工艺采用 FRIPP 的 FF- 14 催化剂 (保护剂采用 FZC 系 列)。 采 用 带 部 分 转 化 的 加 氢 处 理 工 艺 , 柴 油 收 率 控 制 在 15~20%(w)、精制蜡油硫含量要求不大于 0.2%(w)[2]。
蜡油加氢装置掺炼催化裂化柴油的工业应用
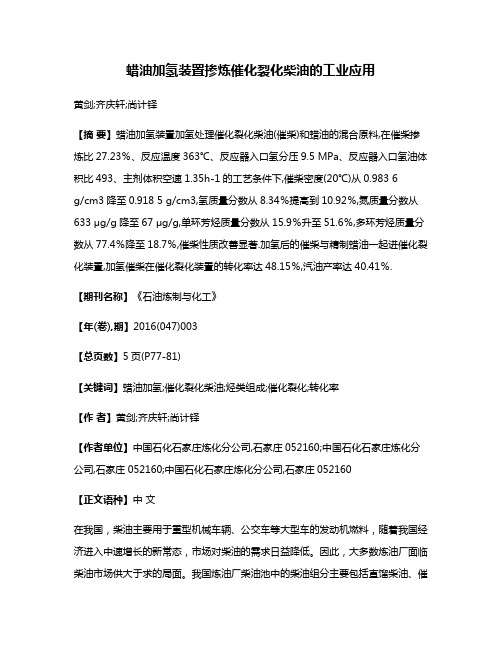
蜡油加氢装置掺炼催化裂化柴油的工业应用黄剑;齐庆轩;尚计铎【摘要】蜡油加氢装置加氢处理催化裂化柴油(催柴)和蜡油的混合原料,在催柴掺炼比27.23%、反应温度363℃、反应器入口氢分压9.5 MPa、反应器入口氢油体积比493、主剂体积空速1.35h-1的工艺条件下,催柴密度(20℃)从0.983 6g/cm3降至0.918 5 g/cm3,氢质量分数从8.34%提高到10.92%,氮质量分数从633 μg/g降至67 μg/g,单环芳烃质量分数从15.9%升至51.6%,多环芳烃质量分数从77.4%降至18.7%,催柴性质改善显著.加氢后的催柴与精制蜡油一起进催化裂化装置,加氢催柴在催化裂化装置的转化率达48.15%,汽油产率达40.41%.【期刊名称】《石油炼制与化工》【年(卷),期】2016(047)003【总页数】5页(P77-81)【关键词】蜡油加氢;催化裂化柴油;烃类组成;催化裂化;转化率【作者】黄剑;齐庆轩;尚计铎【作者单位】中国石化石家庄炼化分公司,石家庄052160;中国石化石家庄炼化分公司,石家庄052160;中国石化石家庄炼化分公司,石家庄052160【正文语种】中文在我国,柴油主要用于重型机械车辆、公交车等大型车的发动机燃料,随着我国经济进入中速增长的新常态,市场对柴油的需求日益降低。
因此,大多数炼油厂面临柴油市场供大于求的局面。
我国炼油厂柴油池中的柴油组分主要包括直馏柴油、催化裂化柴油(简称催柴)、加氢裂化柴油及少量焦化柴油和其它加氢单元副产的少量柴油,其中催柴性质差,严重影响出厂柴油产品质量。
目前,催柴加工工艺技术主要有加氢精制工艺、加氢改质工艺[1]、加氢裂化工艺、加氢处理-催化裂化联合工艺[2-3]。
催柴通过加氢精制和加氢改质工艺,性质得到改善,但柴油十六烷值提高幅度有限,且不能降低柴油总产量;通过加氢裂化工艺,能够将部分催柴转化成高辛烷值汽油,但该工艺存在工艺条件苛刻,催化剂使用寿命短、氢耗高的问题;通过加氢处理-催化裂化联合工艺,能够将部分催柴转化成高辛烷值汽油,且加氢单元操作条件相对缓和,常规的加氢装置即可满足要求。