现场改善(2)(1)
5S现场改善方案:提高效率、优化环境、提升质量

5S现场改善方案:提高效率、优化环境、提升质量5S现场改善方案为了提升工作效率、优化生产环境、提高产品质量,我们对生产现场进行了全面的5S改善。
以下是我们的具体实施方案:1.整理实施2.我们首先对生产现场进行了全面的物品整理,将不必要的物品清除出工作区域,并对必需的物品进行分类放置。
同时,我们对生产流程进行了优化,减少了生产线的冗余环节,提高了生产效率。
此外,我们还制定了定期整理的时间表,确保了整理工作的持续进行。
3.整顿提高4.我们对生产现场的布局进行了调整,使设备、物品的摆放更加整齐、有序。
同时,我们对生产流程进行了整顿,减少了生产线的瓶颈环节,提高了生产效率。
此外,我们还推广了先进的生产管理方法和技术,加强了员工技能培训,提高了员工的专业素养。
5.清扫清洁6.我们制定了严格的清洁卫生制度,对生产现场的卫生、设备保养、废弃物处理等方面进行了明确规定。
同时,我们加强了对现场的日常清洁和保养,使生产现场始终保持整洁状态。
此外,我们还推广了清扫清洁的方法和技巧,提高了员工的清洁意识和技能。
7.素养提升8.我们通过开展各类培训、宣传活动,加强了员工的职业素养、道德品质等方面的教育。
同时,我们还推广了团队合作、积极沟通等方面的技巧和方法,提高了员工的团队协作能力。
此外,我们还鼓励员工参与现场改善活动,激发了员工的工作积极性和创造力。
9.审查坚持10.我们对现场改善工作进行了定期审查,针对存在的问题及时进行调整和改进。
同时,我们还建立了持续改进机制,鼓励员工提出改善意见和建议,不断完善和优化现场管理。
11.环境改善12.我们充分考虑了生产环境的特点和问题,采取了相应的改善措施。
例如,我们优化了生产线布局,减少了物料搬运距离,降低了能源消耗和碳排放。
同时,我们还引入了环保设备和工艺,降低了生产过程中的环境污染风险。
此外,我们还加强了对供应商的环境管理,要求供应商符合我们的环保标准和要求。
13.习惯养成14.我们强调了养成良好工作习惯的重要性,通过制定相应的规章制度和操作规程,引导员工养成良好的工作习惯。
现场管理培训系列之现场改善篇
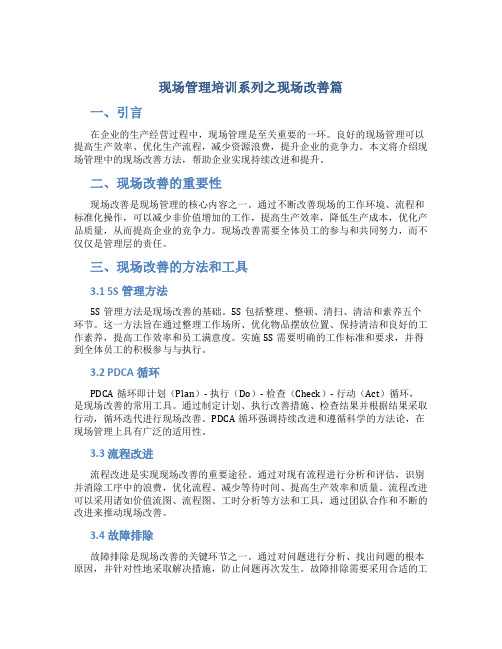
现场管理培训系列之现场改善篇一、引言在企业的生产经营过程中,现场管理是至关重要的一环。
良好的现场管理可以提高生产效率、优化生产流程,减少资源浪费,提升企业的竞争力。
本文将介绍现场管理中的现场改善方法,帮助企业实现持续改进和提升。
二、现场改善的重要性现场改善是现场管理的核心内容之一。
通过不断改善现场的工作环境、流程和标准化操作,可以减少非价值增加的工作,提高生产效率,降低生产成本,优化产品质量,从而提高企业的竞争力。
现场改善需要全体员工的参与和共同努力,而不仅仅是管理层的责任。
三、现场改善的方法和工具3.1 5S管理方法5S管理方法是现场改善的基础。
5S包括整理、整顿、清扫、清洁和素养五个环节。
这一方法旨在通过整理工作场所、优化物品摆放位置、保持清洁和良好的工作素养,提高工作效率和员工满意度。
实施5S需要明确的工作标准和要求,并得到全体员工的积极参与与执行。
3.2 PDCA循环PDCA循环即计划(Plan)- 执行(Do)- 检查(Check)- 行动(Act)循环,是现场改善的常用工具。
通过制定计划、执行改善措施、检查结果并根据结果采取行动,循环迭代进行现场改善。
PDCA循环强调持续改进和遵循科学的方法论,在现场管理上具有广泛的适用性。
3.3 流程改进流程改进是实现现场改善的重要途径。
通过对现有流程进行分析和评估,识别并消除工序中的浪费,优化流程、减少等待时间、提高生产效率和质量。
流程改进可以采用诸如价值流图、流程图、工时分析等方法和工具,通过团队合作和不断的改进来推动现场改善。
3.4 故障排除故障排除是现场改善的关键环节之一。
通过对问题进行分析、找出问题的根本原因,并针对性地采取解决措施,防止问题再次发生。
故障排除需要采用合适的工具和方法,如5W1H(What、When、Where、Who、Why、How)分析、鱼骨图(Ishikawa Diagram)等,帮助确定问题的全貌并解决问题。
四、现场改善的关键要素实施现场改善需要关注以下关键要素:4.1 领导力和员工参与现场改善需要企业领导的关键决策和支持,并鼓励员工积极参与。
现场改善的技巧

现场改善的技巧
现场改善是指在实际工作场景中进行的改善工作,旨在提高工作效率、降低成本、提升质量等方面的综合改进。
以下是一些现场改善的技巧:
1. 制定明确的目标:在开始改善之前,需要明确所要解决的问题、目标和预期结果。
这可以帮助团队在改善过程中保持聚焦,并衡量改善的成效。
2. 进行现场观察:在改善之前,对现有的工作场景进行现场观察和调研。
这样可以帮助发现问题、瓶颈和潜在的改进机会。
3. 采用持续改进的方法:现场改善需要持续不断地进行,而不是一次性的改进活动。
可以采用Kaizen(改善)方法,通过持续小步改进来不断优化工作流程。
4. 制定改进计划:根据观察结果和团队的共识,制定具体的改进计划。
计划应该包括具体的行动步骤、责任人和时间表。
5. 培养改进文化:现场改善需要全员参与和支持。
可以通过培训和认识活动来激发员工对改进的热情,并建立一个积极的改进文化。
6. 使用适当的工具和方法:在改进过程中,可以使用一些常见的工具和方法,如5S整理、流程图、因果图、统计分析等,以帮助团队更好地分析问题、找出根本原因和制定解决方案。
7. 进行试点和持续监控:在进行一项改进之前,可以选择一个小范围的试点项目来验证改进效果。
同时,要持续监控改进措施的实施情况和效果,并及时调整。
8. 推广和分享成果:在成功实施改进之后,要及时向整个团队推广和分享改进成果。
通过分享案例和经验,可以激励其他团队成员进行类似的改进工作。
9. 持续学习和改进:现场改善是一个不断学习和改进的过程。
团队成员应该时刻保持学习的心态,并定期进行回顾和反思,以寻找进一步的改进机会。
现场改善方案

现场改善方案第1篇现场改善方案一、背景分析随着经济社会的快速发展,企业现场管理的重要性日益凸显。
有效的现场管理不仅能提升生产效率,降低成本,还能增强企业核心竞争力。
针对目前我国企业现场管理中存在的问题,本方案旨在提出一套合法合规的现场改善方案,以实现企业现场管理的优化与提升。
二、现状分析1. 现场环境存在安全隐患,可能导致安全事故的发生。
2. 现场物料管理混乱,影响生产效率。
3. 现场人员操作不规范,导致产品质量不稳定。
4. 现场设备维护不及时,影响生产进度。
三、改善目标1. 消除现场安全隐患,降低安全事故发生率。
2. 优化现场物料管理,提高生产效率。
3. 规范现场人员操作,提升产品质量。
4. 加强设备维护,保障生产进度。
四、具体措施1. 安全管理(1)加强安全培训,提高员工安全意识。
(2)设立安全警示标志,提醒员工注意安全。
(3)定期开展安全检查,及时发现并整改安全隐患。
(4)建立健全应急预案,提高应对突发事件的能力。
2. 物料管理(1)建立物料管理制度,明确物料分类、标识、存储、领用等要求。
(2)实行物料先进先出原则,减少库存积压。
(3)定期盘点物料,确保账物相符。
(4)优化物料摆放布局,提高物料取用效率。
3. 人员操作(1)制定操作规程,明确各岗位操作要求。
(2)加强操作培训,提高员工操作技能。
(3)实施标准化作业,降低操作失误率。
(4)建立激励机制,鼓励员工提高工作效率。
4. 设备管理(1)制定设备维护保养计划,确保设备正常运行。
(2)加强设备点检,及时发现并排除设备故障。
(3)提高设备操作人员技能,降低设备故障率。
(4)引进先进设备,提升生产效率。
五、实施与监督1. 成立现场改善小组,负责方案的实施与监督。
2. 制定详细实施计划,明确时间节点、责任人和完成标准。
3. 定期召开现场改善会议,汇报进展情况,协调解决问题。
4. 对实施效果进行评估,对优秀个人或团队给予奖励。
六、总结与展望(全文完)第2篇现场改善方案一、引言现场管理是企业运营的重要组成部分,直接关系到生产效率、产品质量和员工安全。
现场改善(今井正明)
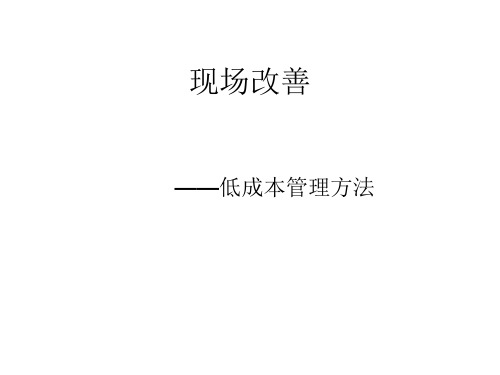
A
C
S D
A
C
P D
维持
改善
一、改善概论
把质量放在第一位
要实践“质量第一”的理念,需要管理层的承诺。
用数据说话
“改善”是一种解决问题的过程。为了能正确地了解及解决问题,必 须收集及分析相关的资料,以确定问题的真相。
下一个流程就是顾客
所有的产品与工作,都是经历一连串的加工流程来完成,而每一道流 程都有其供应商及顾客。 一个真正良好的质量保证体系,就是指在组织内的每一个人,都能认 同及实践“下一个流程就是顾客”的理念。在此理念中顾客包含内部 顾客与外部顾客两种形态。
高层管理 中层管理 督导人员 作业人员
改 进 维 持
一、改善概论
过程与结果
• 要改进“结果”,必须先改进“过程”。因此改善重在“过程为导向” 的思考模式。
以“过程为导向”的思想,应运用到各种改善活动中:
计划→执行→检查→行动(PDCA)的循环; 标准化→执行→检查→行动(SDCA)的循环; 质量→成本→交货期(QCD)的活动; 全面质量管理(TQM); 全员生产保全(TPM); 准时制(JIT)…
一、改善概论
主要的改善活动
• 全面质量控制TQC/全面质量管理TQM
强调总体管理绩效及质量改进。
• 准时制JIT(丰田生产方式)
重在消除各种无附加值的动作,同时达到一个去芜存菁的生产体系。
• 全员生产保全TPM
重在设备质量的改进,追求设备效率最大化。
• 方针展开
改善是在每个人都能为达成目标而工作时,才能产生最大的效果;管理部门 的职责是要设定这个改善目标。 没有目标的改善,如同没有终点的旅途。
• 提案建议制度(改善提案)
“个人导向”的改善活动,重在激励员工参与以提高士气。
工作现场改善后总结范文

一、前言随着企业不断发展壮大,工作现场作为企业生产经营的重要场所,其环境、设施、管理等方面的重要性日益凸显。
为了提高工作效率,降低生产成本,提升员工满意度,我单位于近期对工作现场进行了全面改善。
现将改善后的情况总结如下:二、改善内容1. 环境改善(1)清理工作现场,清除杂物,确保现场整洁有序。
(2)增设绿化带,改善现场空气,营造舒适的工作环境。
(3)合理布局设备,提高现场空间利用率。
2. 设施改善(1)更新老旧设备,提高生产效率。
(2)增设防护设施,确保员工安全。
(3)优化生产线布局,提高物流效率。
3. 管理改善(1)制定现场管理制度,明确各岗位职责。
(2)加强现场巡查,及时发现问题并整改。
(3)开展员工培训,提高员工素质。
三、改善效果1. 提高工作效率通过改善工作现场,设备更新和优化生产线布局,使得生产效率得到显著提高。
据统计,改善后生产周期缩短了15%,生产效率提高了20%。
2. 降低生产成本改善后的工作现场,设备故障率降低了30%,能源消耗减少了20%,有效降低了生产成本。
3. 提升员工满意度舒适的工作环境、合理的设施配置和严格的管理制度,使得员工满意度得到了显著提升。
员工满意度调查结果显示,改善后的工作现场员工满意度提高了25%。
4. 增强企业竞争力改善后的工作现场,使得企业整体形象得到了提升,增强了企业在市场上的竞争力。
四、总结通过对工作现场的全面改善,我单位取得了显著成效。
在今后的工作中,我们将继续关注工作现场,不断优化管理,提高员工素质,为企业的发展奠定坚实基础。
以下是具体总结:1. 强化现场管理,确保现场整洁有序。
2. 优化设备配置,提高生产效率。
3. 增强员工培训,提升员工素质。
4. 营造良好的工作氛围,提高员工满意度。
5. 关注市场动态,提高企业竞争力。
总之,工作现场改善是一项长期、系统的工程,我们将继续努力,为企业的持续发展贡献力量。
生产现场改善
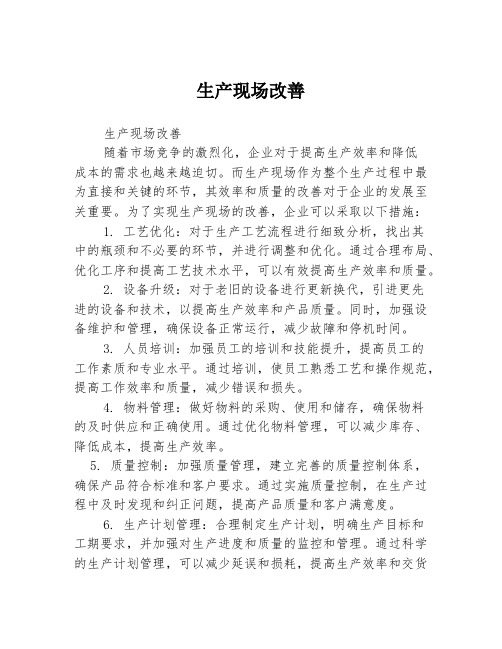
生产现场改善生产现场改善随着市场竞争的激烈化,企业对于提高生产效率和降低成本的需求也越来越迫切。
而生产现场作为整个生产过程中最为直接和关键的环节,其效率和质量的改善对于企业的发展至关重要。
为了实现生产现场的改善,企业可以采取以下措施:1. 工艺优化:对于生产工艺流程进行细致分析,找出其中的瓶颈和不必要的环节,并进行调整和优化。
通过合理布局、优化工序和提高工艺技术水平,可以有效提高生产效率和质量。
2. 设备升级:对于老旧的设备进行更新换代,引进更先进的设备和技术,以提高生产效率和产品质量。
同时,加强设备维护和管理,确保设备正常运行,减少故障和停机时间。
3. 人员培训:加强员工的培训和技能提升,提高员工的工作素质和专业水平。
通过培训,使员工熟悉工艺和操作规范,提高工作效率和质量,减少错误和损失。
4. 物料管理:做好物料的采购、使用和储存,确保物料的及时供应和正确使用。
通过优化物料管理,可以减少库存、降低成本,提高生产效率。
5. 质量控制:加强质量管理,建立完善的质量控制体系,确保产品符合标准和客户要求。
通过实施质量控制,在生产过程中及时发现和纠正问题,提高产品质量和客户满意度。
6. 生产计划管理:合理制定生产计划,明确生产目标和工期要求,并加强对生产进度和质量的监控和管理。
通过科学的生产计划管理,可以减少延误和损耗,提高生产效率和交货能力。
7. 现场标准化:建立现场管理的标准化制度,明确责任分工和工作要求。
通过规范化现场管理,可以减少混乱和错误,提高生产效率和安全性。
8. 持续改进:建立改进机制,鼓励员工提出改进意见和建议,并及时实施和跟踪改进措施的效果。
通过持续改进,不断提高生产现场的效率和质量,逐步实现精益生产。
生产现场改善涉及到多个方面的工作,需要企业全面考虑和积极推动。
通过加强管理和技术创新,完善生产现场的各个环节,企业可以提高生产效率和产品质量,增强竞争力,实现可持续发展。
现场管理改善点怎么写

现场管理改善点现场管理是企业管理中非常重要的一环,它涉及到生产、质量、成本、交期等多个方面。
为了提高现场管理的效率和效果,需要进行不断的改善和优化。
以下是一些常见的现场管理改善点:1. 工艺流程优化工艺流程是生产过程中的核心环节,对工艺流程进行优化可以显著提高生产效率和产品质量。
在优化工艺流程时,需要考虑生产设备的布局、生产过程的稳定性、操作顺序、物流等方面。
通过对工艺流程进行详细分析,可以找到瓶颈和影响效率的环节,进而采取措施进行改进。
2. 设备布局调整设备布局是影响生产效率和产品质量的重要因素之一。
通过对设备布局进行调整,可以使设备之间的距离更加合理,减少物流和人力成本,提高生产效率和质量。
同时,合理的设备布局还可以提高设备的利用率和减少维修成本。
3. 物料管理强化物料管理是现场管理中的重要环节之一,它直接影响到生产效率和产品质量。
通过对物料进行分类管理和规划,可以更好地保证物料的供应和质量,减少物料浪费和成本支出。
同时,合理的物料管理还可以提高库存周转率和降低库存成本。
4. 人员培训加强人员是现场管理中最具活力和创造力的因素,对人员进行培训可以不断提高他们的技能和能力水平,提高工作效率和质量。
同时,培训还可以增强员工的归属感和责任感,降低人员流失率。
5. 生产计划优化生产计划是现场管理中的重要环节之一,它直接影响到交期和成本。
通过对生产计划进行优化,可以更好地平衡人力、物力和财力资源,保证生产计划的顺利执行。
同时,合理的生产计划还可以减少库存积压和浪费现象。
6. 环境卫生改善环境卫生是影响产品质量和员工健康的重要因素之一。
通过加强环境卫生管理,可以营造一个更加整洁、安全的工作环境,提高产品质量和员工满意度。
同时,环境卫生改善还可以提高企业形象和品牌价值。
7. 安全隐患排查安全生产是现场管理中不可忽视的环节之一。
通过对现场进行定期的安全隐患排查,可以及时发现和处理潜在的安全风险和事故隐患,保障员工的人身安全和企业的正常运转。
精益现场改善提案表范文

精益现场改善提案表范文
内容:
尊敬的领导:
我代表部门,就现场改善提出以下提案。
一、存在问题
1. 物料堆放无序,查找不便
我们部门的物料堆放没有固定位置,员工需要花费时间去不同地方找料,降低了工作效率。
2. 器具使用无序,不易查找
部门共用器具放置混乱,使用后没有放回原位,导致频繁搜索器具的时间。
3. 作业区划分不清晰,容易发生混乱
作业区没有明确的标示与划分,不同作业区域混杂,导致人员频繁走动和工具搜索。
二、改善措施
1. 设立物料固定堆放区,贴标示,定期清点。
在部门空地处划定物料专区,分类堆放物料,并贴上标示,定期核查物料。
2. 设置公共器具存放处,使用后放回原位。
在显眼位置设置公共器具架,要求使用后放回原位。
3. 对作业区进行标示划分,人员就地作业。
用标示标出不同作业区域,人员就近当前区域作业,减少走动。
三、预期效果
1. 查找物料效率提高30%
2. 查找器具效率提高20%
3. 每人无效走动减少50%
改善这些问题,可以提高部门作业效率,创建更好的工作环境。
感谢领导的支持!
此致
礼!
部门全体员工
年月日。
生产现场改善方案

生产现场改善方案生产现场改善是指通过不断优化和改进生产现场的各种因素,以提高生产效率、降低生产成本、提升产品质量和保障员工安全等目标的一系列措施。
在生产现场改善中,我们可以采取以下方案来提升生产效率和质量。
一、标准化工作流程标准化工作流程是生产现场改善的基础,它可以确保每一项工作都按照固定的程序进行,并且能够无差错地完成。
通过标准化工作流程,可以减少工作中的浪费和瑕疵,提高生产效率和质量。
标准化工作流程的实施需要进行详细的工作流程分析和标准操作程序的制定,包括设备设置、原材料准备、工艺操作、质量检验等各个环节。
同时,还需要进行相关员工培训,确保每一位员工都能够准确地遵循标准操作程序进行工作,并且能够熟练地应对各种工作场景。
二、自动化设备的应用在现代生产中,自动化设备的应用可以大大提高生产效率和质量。
自动化设备能够取代人工操作,减少人为的误差和疲劳,提高生产效率,减少生产时间。
同时,自动化设备能够提供更高的精确度和稳定性,减少产品瑕疵率,提高产品质量。
在引入自动化设备时,需要评估投资回报率,并进行详细的设备选型和安装调试。
同时,还需要进行相关员工培训,让员工熟练掌握自动化设备的操作和维护,确保设备的正常运转。
三、现场布局的优化现场布局是生产现场改善的重要内容之一,它能够影响到生产效率和安全性。
通过优化现场布局,可以减少物料和人员的移动距离,缩短物料和信息的传递时间,提高生产效率。
同时,优化现场布局还能够提高生产现场的安全性,减少事故发生的概率。
在优化现场布局时,需要进行详细的现场调研和分析,了解现场的工作流程和各个设备之间的关系。
同时,还需要考虑人员的工作条件和安全要求,合理分配工作空间和通道。
最后,需要进行现场布局的调整和改进,确保布局的合理性和可行性。
四、供应链管理的优化供应链管理是生产现场改善的重要组成部分,它关系到物料的准时供应、库存的控制和质量的保障。
通过优化供应链管理,可以提高物料的及时性和准确性,减少物料的浪费和停工现象。
现场改善报告范文
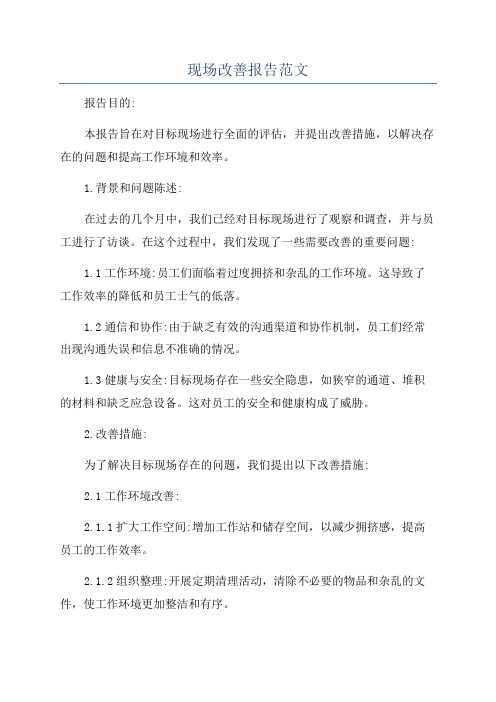
现场改善报告范文报告目的:本报告旨在对目标现场进行全面的评估,并提出改善措施,以解决存在的问题和提高工作环境和效率。
1.背景和问题陈述:在过去的几个月中,我们已经对目标现场进行了观察和调查,并与员工进行了访谈。
在这个过程中,我们发现了一些需要改善的重要问题:1.1工作环境:员工们面临着过度拥挤和杂乱的工作环境。
这导致了工作效率的降低和员工士气的低落。
1.2通信和协作:由于缺乏有效的沟通渠道和协作机制,员工们经常出现沟通失误和信息不准确的情况。
1.3健康与安全:目标现场存在一些安全隐患,如狭窄的通道、堆积的材料和缺乏应急设备。
这对员工的安全和健康构成了威胁。
2.改善措施:为了解决目标现场存在的问题,我们提出以下改善措施:2.1工作环境改善:2.1.1扩大工作空间:增加工作站和储存空间,以减少拥挤感,提高员工的工作效率。
2.1.2组织整理:开展定期清理活动,清除不必要的物品和杂乱的文件,使工作环境更加整洁和有序。
2.1.3提供舒适的工作设施:安装符合人体工程学的办公家具,提供足够的光照和空气流通,以提高员工的工作舒适度。
2.2通信和协作改善:2.2.1沟通渠道:建立有效的沟通渠道,如电子邮件、团队聊天工具和例会,以提高信息传递的准确性和速度。
2.2.2团队培训:开展沟通和协作技巧培训,提高员工处理冲突和有效合作的能力。
2.2.3建立团队合作文化:鼓励员工共享知识和经验、开展团队合作项目,并设立奖励机制,以改善团队间协作和合作的意愿。
2.3健康与安全改善:2.3.1安全设施更新:完善火灾报警器、消防设备等应急设备,并定期检查和维护。
2.3.2提供安全培训:为员工提供必要的安全培训,包括应急疏散演练和使用紧急救护设备的指导。
2.3.3定期巡检:定期对工作场所进行全面巡检,及时发现和解决存在的安全隐患。
3.实施计划:为了确保改善措施的顺利实施,我们建议以下实施计划:3.1资源调配:分配必要的人力、物力和财力资源,以支持改善计划的实施。
现场改善 管理方法
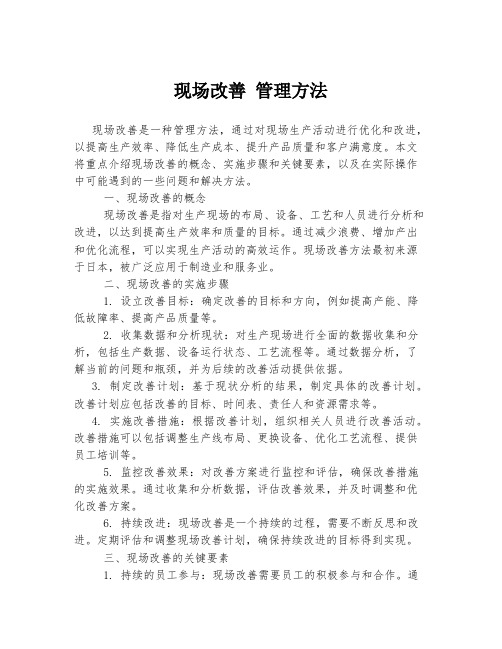
现场改善管理方法现场改善是一种管理方法,通过对现场生产活动进行优化和改进,以提高生产效率、降低生产成本、提升产品质量和客户满意度。
本文将重点介绍现场改善的概念、实施步骤和关键要素,以及在实际操作中可能遇到的一些问题和解决方法。
一、现场改善的概念现场改善是指对生产现场的布局、设备、工艺和人员进行分析和改进,以达到提高生产效率和质量的目标。
通过减少浪费、增加产出和优化流程,可以实现生产活动的高效运作。
现场改善方法最初来源于日本,被广泛应用于制造业和服务业。
二、现场改善的实施步骤1. 设立改善目标:确定改善的目标和方向,例如提高产能、降低故障率、提高产品质量等。
2. 收集数据和分析现状:对生产现场进行全面的数据收集和分析,包括生产数据、设备运行状态、工艺流程等。
通过数据分析,了解当前的问题和瓶颈,并为后续的改善活动提供依据。
3. 制定改善计划:基于现状分析的结果,制定具体的改善计划。
改善计划应包括改善的目标、时间表、责任人和资源需求等。
4. 实施改善措施:根据改善计划,组织相关人员进行改善活动。
改善措施可以包括调整生产线布局、更换设备、优化工艺流程、提供员工培训等。
5. 监控改善效果:对改善方案进行监控和评估,确保改善措施的实施效果。
通过收集和分析数据,评估改善效果,并及时调整和优化改善方案。
6. 持续改进:现场改善是一个持续的过程,需要不断反思和改进。
定期评估和调整现场改善计划,确保持续改进的目标得到实现。
三、现场改善的关键要素1. 持续的员工参与:现场改善需要员工的积极参与和合作。
通过鼓励员工提出改善建议,创建改善氛围,可以激发员工的创新和潜力,推动现场改善的实施和持续改进。
2. 效率和质量的平衡:现场改善的目标是提高生产效率的同时保证产品质量。
在制定改善方案时,需要充分考虑效率和质量的平衡,避免只追求效率而忽略产品的质量。
3. 流程优化和标准化:通过优化工艺流程和建立标准化操作程序,可以提高生产效率、降低变动性和减少错误。
学习《现场改善》一书体会(2篇)

学习《现场改善》一书体会《现场改善》一书是一本关于企业管理与运营的书籍,作者通过详细的案例和实战经验,分享了现场改善的方法和技巧。
阅读这本书,我对如何有效地进行现场改善有了更深入的理解和体会。
首先,现场改善是指通过对工作现场的细致观察和分析,找出问题的根源,并采取相应的措施进行改进的过程。
这种方法强调的是现场问题的解决,而不仅仅是依赖于上层的指示和规定。
现场改善要求管理者和员工紧密合作,共同努力解决问题,并最终实现企业的效益提升。
书中的案例描述了具体的现场改善过程和方法。
作者通过实地走访和观察,发现了一些问题和瓶颈,然后通过团队的努力和创新,找到了解决问题的方法。
例如,有一个案例是关于某家企业的生产线问题。
作者发现生产线存在着效率低下、错误频繁等问题。
经过团队的观察和分析,他们发现问题的根源是工人缺乏培训并且工作流程不严谨。
他们通过培训工人、优化工作流程等方法,最终提高了生产线的效率和质量。
在阅读过程中,我深深地感受到了现场改善的重要性。
现场改善可以帮助企业提高运营效率,提高产品质量,降低成本,提升竞争力。
通过对工作现场的细致观察和分析,可以及时发现问题,并采取相应的措施进行改善。
这种方法可以避免问题被放大,降低解决问题的成本。
另外,现场改善还可以增加员工参与的积极性,提高员工的工作满意度和绩效。
与此同时,现场改善也是一项具有挑战性的任务。
找到问题的根源并不容易,需要对现场进行深入的观察和分析。
并且,在实施改善措施的过程中,可能会遇到各种各样的阻力和困难。
例如,员工可能会对改变表示抵触,管理者可能会担心改变会造成工作停滞等。
因此,在进行现场改善时,需要有足够的耐心和决心,同时也需要善于倾听和沟通,以便更好地解决问题。
通过阅读《现场改善》,我对现场改善的方法和技巧有了更深入的了解。
首先,在进行现场观察时,要善于发现问题的根源。
这意味着要对整个工作流程进行细致的观察和分析,了解每一个环节的运作情况。
现场改善工作总结
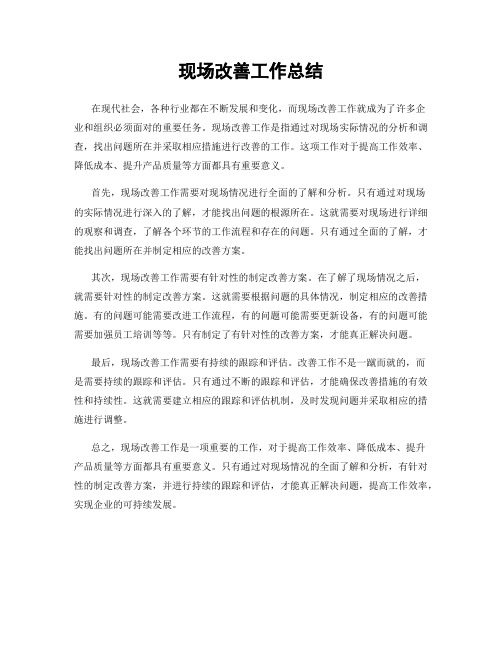
现场改善工作总结
在现代社会,各种行业都在不断发展和变化,而现场改善工作就成为了许多企
业和组织必须面对的重要任务。
现场改善工作是指通过对现场实际情况的分析和调查,找出问题所在并采取相应措施进行改善的工作。
这项工作对于提高工作效率、降低成本、提升产品质量等方面都具有重要意义。
首先,现场改善工作需要对现场情况进行全面的了解和分析。
只有通过对现场
的实际情况进行深入的了解,才能找出问题的根源所在。
这就需要对现场进行详细的观察和调查,了解各个环节的工作流程和存在的问题。
只有通过全面的了解,才能找出问题所在并制定相应的改善方案。
其次,现场改善工作需要有针对性的制定改善方案。
在了解了现场情况之后,
就需要针对性的制定改善方案。
这就需要根据问题的具体情况,制定相应的改善措施。
有的问题可能需要改进工作流程,有的问题可能需要更新设备,有的问题可能需要加强员工培训等等。
只有制定了有针对性的改善方案,才能真正解决问题。
最后,现场改善工作需要有持续的跟踪和评估。
改善工作不是一蹴而就的,而
是需要持续的跟踪和评估。
只有通过不断的跟踪和评估,才能确保改善措施的有效性和持续性。
这就需要建立相应的跟踪和评估机制,及时发现问题并采取相应的措施进行调整。
总之,现场改善工作是一项重要的工作,对于提高工作效率、降低成本、提升
产品质量等方面都具有重要意义。
只有通过对现场情况的全面了解和分析,有针对性的制定改善方案,并进行持续的跟踪和评估,才能真正解决问题,提高工作效率,实现企业的可持续发展。
关于现场改善总结
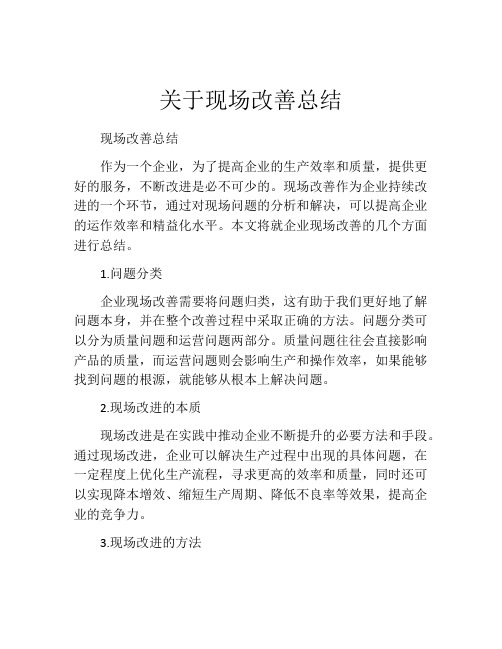
关于现场改善总结现场改善总结作为一个企业,为了提高企业的生产效率和质量,提供更好的服务,不断改进是必不可少的。
现场改善作为企业持续改进的一个环节,通过对现场问题的分析和解决,可以提高企业的运作效率和精益化水平。
本文将就企业现场改善的几个方面进行总结。
1.问题分类企业现场改善需要将问题归类,这有助于我们更好地了解问题本身,并在整个改善过程中采取正确的方法。
问题分类可以分为质量问题和运营问题两部分。
质量问题往往会直接影响产品的质量,而运营问题则会影响生产和操作效率,如果能够找到问题的根源,就能够从根本上解决问题。
2.现场改进的本质现场改进是在实践中推动企业不断提升的必要方法和手段。
通过现场改进,企业可以解决生产过程中出现的具体问题,在一定程度上优化生产流程,寻求更高的效率和质量,同时还可以实现降本增效、缩短生产周期、降低不良率等效果,提高企业的竞争力。
3.现场改进的方法①标准化工作:通过建立标准化工作流程,规定操作步骤和流程,从而达到提高生产效率和保证质量的目的。
②6S活动:通过定期整理、排序、清洁、标准化、养护和培育企业良好的习惯等方式,改善生产环境,提高生产效率。
③Kaizen活动:通过开展小改进活动,不断提高生产工艺和技术,以达到更高的生产效率。
4.现场改进管理现场改进是一项持续性的工作,它需要良好的管理和组织。
改进管理需要充分调动员工的积极性,提高员工的工作经验和技能,通过正确的管理手段,达到不断优化现场工作流程和效率,不断满足顾客的需求。
总之,现场改进是企业效率提高、成本减少、品质提升和企业文化建设等方面都需要重视的一个重要环节。
企业需要有足够的准备和资源,紧密团结在一起,合理分析问题的来源,集思广益,共同制定改进计划,进行有效的改进和优化工作,从而不断提高企业竞争力和产品质量,创造更为优良的经济效益。
现场改善主要要点

现场改善主要要点现场改善主要要点工作关键字:现场改善主要要点工作一、现场改善考虑下手的几个方面:1、工艺流程查一查即向工艺流程要效益。
分析现有生产、工作的全过程,哪些工艺流程不合理,哪些地方出现了倒流,哪些地方出现了停放,包括储藏保管、停放状态、保管手段(如储存容器配备、货架配备、设施条件)、有无积压状态?哪些工艺路线和环节可以取消、合并、简化?寻找最佳停放条件,确定经济合理的工艺路线。
2、平面图上找一找即向平面布置要效益。
仔细检查和分析工厂平面布置图、车间平面布置图和设备平面布置图,分析作业方式和设备、设施的配置,按生产流程的流动方向,有无重复路线和倒流情况,找出不合理的部分,调整和设计一种新的布局,使生产流程在新的布置图上路线最短,配置最合理。
3、人机工程挤一挤即向人机联合作业要效益。
人和设备构成了人机工程,在分析时要分析作业者和机器在同一时间内的工作情况,有无窝工、等待、无效时间,通过调整工作顺序改进人机配合,寻求合理的方法,使人的操作和机器的运转协调配合,将等待时间减少到最大限度,充分发挥人和机器的效率。
4、关键路线缩一缩即向网络技术要效益。
将现有的工序和作业流程绘制成网络图。
从中找出关键路线,然后从非关键路线上抽调人财物,加强关键路线,或采用平行作业。
交差作业等等形式,实现时间和费用的优化。
5、流水线上算一算即向流水线要效益。
研究流水线的节拍、每个工序的作业时间是否平衡,如果发现不平衡,就要通过裁并、简化、分解等等手法,平衡流水线。
消除因个别工序缓慢而导致的窝工和堆积。
6、动作分析测一测即向动作分析要效益。
研究工作者的动作,分析人与物的结合状态,消除多余的动作、无效动作或缓慢动作,如弯腰作业、站在凳子上作业、蹲着作业、作业场所不畅、没有适合的工位器具、人与物处于寻找状态等,通过对人的动作和环境状态的分析和测定,确定合理的操作或工作方法;探讨减少人的无效劳动,消除浪费,解决现场杂乱,实现人和物紧密结合,提高作业效率。
现场改善方案(二)

现场改善方案(二)
现场改善方案
方案背景
•描述目标群体和机构
•说明现场存在的问题和挑战
方案目标
•描述方案的主要目标和预期成果
方案步骤
1.问题分析
–对现场问题进行全面调研和分析
–列出问题的具体细节和影响因素
2.制定改善策略
–根据问题分析结果确定改善方向
–考虑改善策略的可行性和可持续性
3.设计改善方案
–制定具体的改善方案,包括行动计划和时间安排
–确定相关资源、人员和预算等方面的需求4.实施改善方案
–按照行动计划逐步推进改善方案的实施
–监测改善效果,及时调整或改进方案
5.评估和总结
–对改善方案的效果进行评估和总结
–提取经验教训,为未来的改善工作提供参考方案推进
•列出项目推进的关键要点和措施
•提及关键人员的角色和职责分工
预期成果
•描述方案实施后预期达到的具体成果
•强调成果对目标群体和机构的积极影响
风险和应对措施
•列出可能的风险和问题
•提供相应的风险应对措施
结束语
•强调方案的重要性和必要性•表达对实施方案的信心和期待。
- 1、下载文档前请自行甄别文档内容的完整性,平台不提供额外的编辑、内容补充、找答案等附加服务。
- 2、"仅部分预览"的文档,不可在线预览部分如存在完整性等问题,可反馈申请退款(可完整预览的文档不适用该条件!)。
- 3、如文档侵犯您的权益,请联系客服反馈,我们会尽快为您处理(人工客服工作时间:9:00-18:30)。
8.要精益求精,永無止境的改善。
9.不是要等待沒問題後才能改善。
10.發揮團隊精神,不要單打现獨场改鬥善(2。)(1)
UMAX
解決問題的兩種方法
一﹒創新:應用最新、最好的科技及設備
但須投資大筆的金錢。
二﹒改善:利用常識性的觀念與方法
不須花費多少金錢。
现场改善(2)(1)
UMAX
現場改善三項基礎原則
豐田工機公司
豐田工機公司的董事島吉男說:「在一九八0年代,公司導入TQM以
追求戴明獎為目的時,其為品質保證而建立的制度和標準,終於使
公司在一九八五年獲頒戴明獎。
早期所建立的各式標準,反映出它不僅是品質保證的重要步驟,而
且也反映出管理當局的願望、思想與他們對理想程序的願景。
為了保持運作,必須定期檢討及提升,因此整個公司品質改進的歷
管理階 層的支 援
现场改善(2)(1)
UMAX
現場中心主義成功的條件
現場管理人員必須承擔達成QCD的責任
現場應給予充分的自由空間以便改善
管理階層應該對現場提出欲達成的改善目標,但應對其結果負責
現場的需求,較容易被在現場工作的同仁所認同
在線上,有些人總會去思考各式各樣的問題及其解答
抗拒改變的阻力最小化
˙不斷提昇現有水準
现场改善(2)(1)
UMAX
維持與改善
高層管理 中階管理 督導人員 作業人員
改進
維持
日本觀的工作機能
高層管理 中階管理 督導人員 作業人員
創新
改善 維持
改進分為創新和现场改改善善(2)(1)
UMAX
PDCA 循環 與 SDCA 循環
改進
處置
計劃
AP
維持
處置
標準化
AS
C
查核
D
C
執行 查核
必要的。
現場改善應當成為申請國際認證不可或缺的一部份,而且在取
得認證之後,現場改善應當做為持續提升水準的方法。
现场改善(2)(1)
UMAX
现场改善(2)(1)
UMAX
3rew
演讲完毕,谢谢听讲!
再见,see you again
2020/11/23
现场改善(2)(1)
现场改善(2)(1)
UMAX
主要的改善觀念
一﹒改善與管理
二﹒過程與結果
三﹒遵循 PDCA 循環 / SDCA 循環
四﹒品質第一
五﹒用數據說話
六﹒下一製程就是顧客
现场改善(2)(1)
UMAX
管理的主要兩項功能
一﹒維持:˙按計劃、按標準行事
˙確實執行新標準 ˙使正常狀態能持續出現
二﹒改善:˙將異常迅速改善至正常(消極)
一﹒環境維持﹝Housekeeping﹞:落實5S活動
※5S:整理(Seiri)、整頓(Seiton)、清掃(Seiso)、 清潔(Seiketsu)、教養(Shitsuke)
二﹒消除「無駄」﹝Muda﹞=「浪費」
※任何不會產生附加價值的活動就是無駄
三﹒標準化﹝Standardization﹞
※標準:做事的最佳方法
D
執行
PDCA 循環 計劃-執行-查核-處置
SDCA 循環 標準化-執现场行改善-(2)查(1) 核-處置 UM
主要的改善活動
一﹒全面品質管理 ( TQM ) 二﹒及時生產方式 ( JIT ) 三﹒全員生產保全 ( TPM ) 四﹒方針展開 五﹒提案建議制度 六﹒小集團活動 ( QCC )
现场改善(2)(1)
现场改善(2)(1)
UMAX
現場改善~今井正明三大理念
一﹒重視現場:任何問題都要到現場去了解,當場用最簡
單、最不花錢的方式來尋求「改善」,而
非以投入資金,從外界購買最新的科技設
備來提升工廠的水準。
二﹒最簡單的「改善」方式:日本式的 TQM、TPM、JIT、
5S、QCC及提案建議...等。
三﹒高階層的承諾﹝Commitment﹞
所謂承諾不是指應允某一件事,而是說從事這些改善
活動必需要長久、持續地做下去,這不是一年、二年
之事,而是一輩子的事。
现场改善(2)(1)
UMAX
日本式改善活動 ~ 「五心」
一﹒信心:相信這些改善活動會帶給你好處。 二﹒決心:下定決心趕快去做,不要猶豫不決。 三﹒耐心:要永遠持續做下去,成果自然呈現。 四﹒關心:對員工表示出你的關懷及重視之意。 五﹒愛心:多用鼓勵的方式來鼓舞員工士氣。
「作業標準」為員工實踐達成QCD所應執行的工作方式,並滿
足顧客之外部需求。
日本公司對所建立的標準,是熱衷採納與信奉,而歐美公司則
將標準視為某種程度的輕蔑之事。
「標準」一詞,意為應用製程使作業人員更安全,更容易地工
作,以及公司為確保顧客品質及生產力的最有效工作方式。
现场改善(2)(1)
UMAX
標準的主要特徵
现场改善(2)(1)
UMAX
現場改善 第三章
如何管理現場的品質﹑成本和交 期
主講人
彭文彬
现场改善(2)(1)
UMAX
品質~不僅是指[結果面的品質]而已
廣義而言是指產品與服務的工作和過程的 品質
前者為[結果面]的品質,後者為[過程面] 的品質
品質涉及到公司內每一個過程內之活動
涵蓋了產品或服務之開發﹑設計﹑生產﹑ 銷售和服務
1.改進品質 2.改進生產力 3.降低庫存 4.縮短生產線 5.減少機器停機時間 6.減少空間 7.降低生產交期 這些消除無駄的努力,將可降低營運现场的改善總(2)(1成) 本 UMAX
降低生產交期
交期: 是從公司支付購進材料及耗材開始,到公司收到 售出貨物的貨款時間為止 較短的交期其意表較佳的資金週轉率,更有彈性 的符合顧客的需求,以及花較低的營運成本 是衡量管理能的真實力 隱藏在交期領域的無駄,是改善的黃金時機
现场改善(2)(1)
2020/11/23
现场改善(2)(1)
現場改善
日本競爭力成功之鑰
今井正明 著
許文治 譯 品管部 製
现场改善(2)(1)
UMAX
學習型組織的五項核心修練
一﹒自我超越﹝Personal Mastery﹞ 二﹒心智模式﹝Mental Models﹞ 三﹒共享願景﹝Shared Vision﹞ 四﹒團隊學習﹝Team Learning﹞ 五﹒系統思考﹝Systems Thinking﹞
主題選定。
現況掌握及目標設定。
分析蒐集到的資料,以確定真正的原因。
依據資料分析,立定改善對策。
實施改善對策。
對改善對策做效果確認。
建立或修正標準,防止再發。
檢視上述步驟以及進行下一步驟。 现场改善(2)(1)
UMAX
改善/ISO 9000/QS 9000
認證活動計劃,絕大部份強調在對主要的製程的標準化,及持
代表最好、最容易與最安全的工作方法。 提供了一個保持技巧和專業技術的最佳方法。 提供了一個衡量績效的方法。 表現出因果之間的關係。 提供維持及改善的基礎。 做為目標及訓練目的。 做為訓練的基礎。 建立成為稽查或診斷的基礎。 防止錯誤再發生及變異最小化的方法现。场改善(2)(1)
UMAX
UMAX
現場改善 第二章
現場改善
主講人
侯建平
现场改善(2)(1)
UMAX
現場之定義
廣義:開發,生產,銷售之場所 狹義:製造產品或服務的地方
现场改善(2)(1)
UMAX
現場與管理之關係
現場:藉由提供產品或服務來滿足顧客 管理:藉著策略的設定和方針展開,以達成在現場的目標
管理階 層的控 制
現場
現場
工人的 作業
情報
設備
產品及 材料
標準化
5S(良好的廠房環境維持)
銷除無駄
團隊合作 目視管理
士氣強化 品管圈
自律 现提场案改善建(2議)(1)
UMAX
現場管理的金科玉律
1.當問題(異常)發生時,要先去現場 2.檢查現物(有關的物件) 3.當場採取暫行處置措施 4.發掘真因並將之排除 5.標準化以防止再發生
二.然後開始採取行動:
推行現場的五項金科玉律
訓練員工,承諾不將不良品送至下一製程
鼓勵團隊活動及提案建議制度以解決問題
蒐集資料,以獲取對問題性質有更多的了解並解決
製作簡單的治工具使工作更容易做,結果更可靠
现场改善(2)(1)
UMAX
現場的成本降低
成本管理:
是指管理開發,生產及銷售良好品質之過程時,又能致力 於降低成本或維持在目標成本之水準上 降低成本必須實施下列活動:
六﹒全員現場改善﹝Gemba Kaizen﹞
(彼得聖吉)
现场改善(2)(1)
UMAX
改善十大格言
1.先顧大局,例外狀況例外處理。
2.不要先下結論,要嘗試做做看。
3.用頭腦改善,不是用金錢改善。
4.不在會議室討論,直接到現場改善。
5.不要解釋理由,去想出改善方法。
6.問五次為什麼,找出問題真相。
7.不要等到百分之百把握才做。
續地改善活動上。
在「改善」的術語裡,標準即意指最好的工作方法,而且現場
改善:諸如消除無馱及廠房環境維持(特別是5S),應當要寫成標
準。
現在的現場有太多的無馱及變異,而將它寫下來做為標準是沒
有用處的。
一旦建立了標準,緊接著就是要改進這些標準。在申請認證之
前,現場改善絕對必須先做好,獲得認證之後的水準提升也是
现场改善(2)(1)
UMAX
源流管理
一.作業方式:
在現場生產之前之有關活動
是從管理階層的方針開始展開
依序確認改善上游之需求