紧密纺纱成纱机理的分析
紧密纺纱的原理性能特点及产品开发
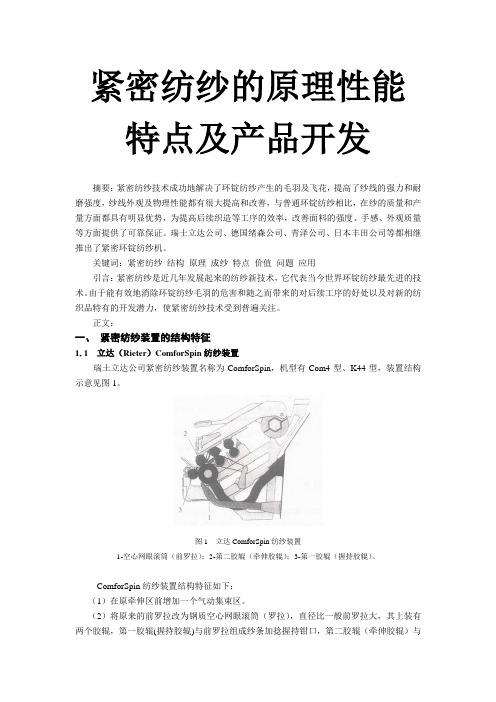
紧密纺纱的原理性能特点及产品开发摘要:紧密纺纱技术成功地解决了环锭纺纱产生的毛羽及飞花,提高了纱线的强力和耐磨强度,纱线外观及物理性能都有很大提高和改善,与普通环锭纺纱相比,在纱的质量和产量方面都具有明显优势,为提高后续织造等工序的效率,改善面料的强度、手感、外观质量等方面提供了可靠保证。
瑞士立达公司、德国绪森公司、青泽公司、日本丰田公司等都相继推出了紧密环锭纺纱机。
关键词:紧密纺纱结构原理成纱特点价值问题应用引言:紧密纺纱是近几年发展起来的纺纱新技术,它代表当今世界环锭纺纱最先进的技术。
由于能有效地消除环锭纺纱毛羽的危害和随之而带来的对后续工序的好处以及对新的纺织品特有的开发潜力,使紧密纺纱技术受到普遍关注。
正文:一、紧密纺纱装置的结构特征1.1 立达(Rieter)ComforSpin纺纱装置瑞土立达公司紧密纺纱装置名称为ComforSpin,机型有Com4型、K44型,装置结构示意见图1。
图1 立达ComforSpin纺纱装置1-空心网眼滚筒(前罗拉);2-第二胶辊(牵伸胶辊);3-第一胶辊(握持胶辊)。
ComforSpin纺纱装置结构特征如下:(1)在原牵伸区前增加一个气动集束区。
(2)将原来的前罗拉改为钢质空心网眼滚筒(罗拉),直径比一般前罗拉大,其上装有两个胶辊,第一胶辊(握持胶辊)与前罗拉组成纱条加捻握持钳口,第二胶辊(牵伸胶辊)与前罗拉组成牵伸区的前牵伸钳口。
第一胶辊与第二胶辊间为须条的集聚区。
(3)前罗拉为钢质网眼滚筒,形似一个小尘笼,内有圆形截面吸聚管(负压)与吸风风机等组成吸聚罗拉,即有负压的前罗拉。
圆形截面吸聚管上装有一块开了一个由后向前逐渐变窄的V形狭槽的工程塑料部件组成的吸气槽,V形槽长度跟须条与前罗拉接触长度相适应,并与输出方向有一定偏斜度,当在主牵伸区须条离开牵伸钳口时,因负压的吸附作用,须条由V形槽控制在网眼前罗拉上,并向前输送到第一胶辊处,即握持钳口处。
1.2 绪森(Suessen)Elite纺纱装置德国绪森公司紧密纺纱装置名称为Elite,机型有Fiomax E1型、Fiomax E2型,装置结构示意见图2。
(完整版)不同纺纱方法的成纱结构和特性

不同纺纱方法的成纱结构和特性当前棉纺领域有5种实用的、倍受关注的纺纱方法,即传统环锭纺、转杯纺、喷气纺、涡流纺和改进环锭纺——紧密纺。
环锭纺纱方法已有逾一个半世纪的历史,而后四者是在近几十年甚至是近几年发展起来的,统称为新型纺纱方法。
不同的纺纱方法无论在产量、质量方面,还是在成纱结构和特性方面,都有各自非常独特之处。
1 成纱机理1.1 传统环锭纺环锭纺纱是将牵伸、加捻和卷绕同时进行的一种纺纱方法,粗纱在牵伸系统中被牵伸至所要求纱支的须条,再经钢领、钢丝圈的加捻和卷绕形成一根纱线。
由于牵伸作用,主牵伸区中的须条宽度是所纺纱线直径的数倍,此时各根纤维抵达前钳口线时呈自由状态。
当这些纤维离开前钳口线后即被捻合在一起,这样就形成了一个纺纱加捻三角区。
此纺纱加捻三角区阻止了边缘纤维完全进入纱体,部分边缘纤维脱离主体形成飞花,较多的边缘纤维则是一端被捻入纱体,而另一端形成毛羽。
这些纤维不但对纱线的均匀度、弹性等性能起消极作用,且对纱线的强力极其不利。
另外,在加捻时处于三角区外侧的纤维受到的张力最大,而在中心的纤维受到的张力最小,故成纱时这些纤维的初始张力不等,从而影响成纱的强力。
这些都是传统环锭纺纺纱三角区造成的缺陷。
1.2 转杯纺转杯纺又称气流纺,属于自由端纺纱方法。
直接喂入纺纱器的棉条经分梳辊分梳成了单纤维状,纤维靠分梳辊的离心力和纺杯内负压气流的作用脱离分梳辊表面经输棉管道而进入纺杯,并在凝聚槽中形成一个完整的纤维环,纤维环随着纺杯高速旋转,在接头纱的作用下,随着捻度不断的传递和连续剥离纤维束而成纱。
1.3 喷气纺喷气纺纱以日本村田公司制造的MJS(Murata Jet Spinner)机型为代表。
棉条直接喂入牵伸装置,经牵伸后的须条进入喷嘴,两个方向相反的高速旋转气流对纱条进行假捻并包缠成纱,纱条引出后经电子清纱器去除疵点后被卷绕在筒子上。
1.4 涡流纺涡流纺纱是继MJS之后,村田公司推出的新一代的喷气纺纱技术MVS(Murata Vortex Spinning)。
紧密纺的纺纱原理

紧密纺的纺纱原理主要是通过改变纺纱工艺,增加纤维束之间的摩擦力和相互间的吸附力,使纤维束更加紧密。
具体来说,它是在环锭细纱机上经过改造实现的,核心技术是在前罗拉输出端加装一个集聚装置。
这个装置使须条经过集聚后再输出加捻,实现了牵伸和集聚的分离。
这样能避免牵伸区中由于集合作用的存在而影响摩擦力分布,牵伸后的须条经集合后宽度减少,使加捻三角区减少甚至消除。
从而消除了因加捻三角区的存在而产生的不利影响,改善了纱线质量。
此外,紧密纺纱的原理还包括纤维束的并列排列和摩擦力、吸附力的增加。
通过采用细纱和合纱工艺,使纤维束并列排列,减小纤维束之间的间隙。
同时,调整纺纱过程中的拉伸力和摩擦系数,增加纤维束之间的摩擦力,使其更加紧密。
此外,通过改变纺纱液的粘度、温度和纺纱机械结构等因素,增加纤维束的吸附力。
以上信息仅供参考,如需了解更多信息,建议查阅紧密纺相关论文或咨询纺织专家。
紧密纺纱技术

紧密纺纱技术紧密纺纱技术是一种现代纺织工艺,它通过将纺织纤维紧密排列在一起,使纱线更加均匀、强度更高,从而提高纺织品的质量和性能。
它在纺织行业中得到广泛应用,并对纺织品的质量和市场竞争力产生了积极影响。
紧密纺纱技术的核心是纺纱机。
它通过一系列的工艺操作,将纺织纤维在纺纱机的作用下进行拉伸、捻合和强力拉伸,使其纤维间的间隙减小,纤维之间的结合更紧密。
这种技术可以使纱线的结构更加均匀,纤维之间的摩擦力增大,从而提高纱线的强度和耐磨性。
同时,紧密纺纱技术还可以改善纱线的外观,使其更加光滑、柔软,提高纺织品的手感和舒适度。
紧密纺纱技术在纺织品的制造中具有重要的意义。
首先,它可以提高纺织品的质量和耐久性。
由于纱线的结构更加紧密,纤维之间的摩擦力增大,使得纺织品更加坚固耐用,不易磨损和变形。
其次,紧密纺纱技术可以提高纺织品的色牢度和抗褪色性能。
由于纱线的结构更加均匀,纤维之间的结合更紧密,使得染料更容易渗透纤维内部,从而提高了染色的均匀度和牢固度。
再次,紧密纺纱技术可以提高纺织品的舒适性和透气性。
由于纱线的结构更加紧密,纤维之间的间隙减小,使得纺织品更加柔软、透气,提高了穿着的舒适度和透气性。
紧密纺纱技术在纺织行业中的应用非常广泛。
首先,在高档服装制造中,紧密纺纱技术可以提高服装的品质和档次,增加其附加值。
其次,在工业纺织品的制造中,紧密纺纱技术可以提高纺织品的强度和耐久性,延长其使用寿命。
再次,在家居纺织品的制造中,紧密纺纱技术可以提高床上用品、窗帘等纺织品的舒适性和美观度,增加其市场竞争力。
此外,紧密纺纱技术还可以应用于汽车内饰、航空航天等领域,提高产品的性能和质量。
随着科学技术的不断发展,紧密纺纱技术也在不断创新和改进。
目前,一些新型的纺纱机已经应用到紧密纺纱技术中,使得纺织品的质量和性能得到进一步提升。
例如,无捻纺纱技术、双向拉伸纺纱技术等都是紧密纺纱技术的创新应用,它们可以使纺织品的强度、耐磨性、柔软度等方面得到进一步提高。
紧密纺纱技术及紧密纺纱特性分析

第3期2005年9月化纤与纺织技术ChemicalFiber&TextileTechnology文章编号:1672—500X(2005)03—001l一03紧密纺纱技术及紧密纺纱特性分析陶珏(淮安东方清棉纺织有限公司,江苏淮安223002)摘要:介绍紧密纺纱技术如何消除纺纱三角区来提高成纱质量,介绍紧密纺纱技术的纺纱机理及其特性。
关键词:紧密纺纱纺纱三角区毛羽环锭纺条干中图分类号:TS103.27+7文献标识码:B1引言一种在普通环锭纺纱机纺纱原理的基础上发展而成的紧密纺纱技术已被成功地研制和推广。
紧密纺作为一种新型纺纱方法,以其独特的纺纱原理,改善了环锭纺成纱的结构,其优越的纱线性能,显著的经济效益,引起了国内外纺织行业的密切关注。
据统计国内引进紧密纺纱设备已有几十万纱锭,国内各纺机厂也相继开发研制紧密纺纱机。
除个别厂大都有以网眼(格)胶圈加吸风槽为基本形式。
现就国产紧密纺纱机进行研究和分析。
2传统纺纱机的缺陷和紧密纺纱技术的纺纱机理传统环锭纺细纱机就是在牵伸区对粗纱施加一定的牵伸比,以获得所需要的纱线支数。
为了使纱线获得所要的强度必须加上捻度,束纤维在细纱前罗拉输出处到加捻成细纱加捻点之间形成纺纱加捻三角区。
当纤维进入三角区时几乎失去控制,完全处于松散状态,边缘纤维在加捻前脱离主体成为飞花,据统计细纱车间约有80%以上的飞花由此处造成,也有的可能成为毛羽,是因为纤维一端被捻入纱体,另一端就造成毛羽,另外在纺纱三角区中,’三角形两边的纤维比三角形中间的纤维所受的张力大,纺出的纱在受力时纤维不能平均负担,两边的纤维先断,成纱断裂强度达不到应有的水平,造成强力或高或低不稳定,因此普通环锭纺加工过程还得进一步改善。
紧密纺是在环锭纺纱细纱机上进行重大革新和创造的纺纱技术,在环锭纺纱机上的牵伸与加捻之间加上一种特殊的新型纺纱装置——集聚装置,来彻底消除环锭纺中存在的加捻三角区。
即扁平的须条从前罗拉输出时,纤维束受空气负压气流的压缩与控制,在负压气流与一定角度的吸风口复合作用下,很快地把一定宽度的纤维束横向收缩,使纤维束的宽度柔和地转化为成纱的宽度,边缘纤维向中间集聚,须条在纤维排列平顺、紧密、受力均匀的情况下被加捻,纤维之间的抱合力大大增加,成纱的结构和机械物理性能及纤维的强力利用情况都将得到明显的改善。
紧密纺技术在麻纺细纱领域的成功运用

紧密纺技术在麻纺细纱领域的成功运用传统麻纺细纱机纺纱过程中因纺纱三角区的存在,苎麻纱毛羽多且长,影响织物质量。
紧密纺技术适用于苎麻及苎麻混纺产品的生产,应用紧密纺技术改造麻的纺细纱机,能够提高苎麻纱的质量,改善传统苎麻纱毛羽多、表面发毛、疵点明显等缺点,使得苎麻纤维的优良特性得到展现,苎麻织物表面光洁、手感滑爽并具有较好的透气性,面料品质得到提高。
为了对麻纺细纱机进行紧密纺技术改造,安徽省铜陵华源麻业纺织有限公司于2004年后半年开始与铜陵松宝机械有限公司合作进行研究、设计,取得了一定的成效,下面对紧密纺技术在麻纺细纱机上的应用情况作一简单介绍。
1、麻纺细纱机紧密纺纱原理分析麻纺细纱机紧密纺技术改造应主要依据麻纺细纱机的结构及苎麻纤维的特性来进行。
苎麻纤维长度长、无卷曲、纤维细度粗,通常在6.7 dtex左右,刚性大,弹性低,纤维之间抱合力较小,苎麻纤维在传统的环锭纺生产中,麻粗纱进入后牵伸区经较小张力牵伸,同时粗纱捻度尽量转移。
在前牵伸区须条被牵伸至所要求的纱号,与此同时,须条内苎麻纤维之间的抱合力很小,所以,各根纤维到达前钳口线呈自由状态,当苎麻纤维脱离前钳口线后即被捻合在一起形成苎麻纱,这时的纱线形成区就是所谓的纺纱三角区。
纺纱三角区对苎麻纱的外观,如毛羽、麻粒、强力、弹性、断头以及飞花起着决定性的影响。
边缘纤维或短纤维常常不能捻人纱内而变成飞花损失掉,或者大部分边缘纤维和短纤维不能包进纱内而伸出纱外形成毛羽。
在加捻时苎麻纤维纵向受到张力,在纺纱三角的外侧张力最大,而在中心处张力最小,因此成纱中这些苎麻纤维的初始张力是不等的。
当苎麻纱线在后加工过程中承受拉伸载荷时,具有最大初始张力的一些苎麻单纤维就最先断裂。
因此,苎麻纱的强力就会低于纱断面上各根苎麻纤维强力的总和。
为了提高苎麻纱的强力,减少苎麻纱的毛羽和飞花,并且提高工作元件的耐用性、可*性及维修操作方便性,设计改造方案时决定取消纺纱三角。
叙述紧密纺包芯纱的加工原理和特点

叙述紧密纺包芯纱的加工原理和特点紧密纺包芯纱是一种特殊的纱线类型,它由两种不同纤维构成,其中一种纤维包裹在另一种纤维的周围。
这种纱线的加工原理和特点使其在纺织业中具有广泛的应用。
加工原理:紧密纺包芯纱的加工原理主要涉及两种不同纤维的组合。
一种纤维通常被称为芯纤维,另一种纤维称为包纤维。
在纺纱过程中,芯纤维首先通过纺纱机的芯纺纱头被纺成纱线。
然后,包纤维被加入到芯纱线周围,并通过外包纺纱头进行纺织。
这样,芯纤维就被完全包裹在包纤维的周围,形成了紧密纺包芯纱。
特点:1. 强度和耐磨性强:由于芯纤维的存在,紧密纺包芯纱具有较高的强度和耐磨性。
芯纤维通常是一种强度较高的材料,如聚酯纤维或尼龙纤维,而包纤维可以是柔软的天然纤维或其他化学纤维。
这种结构使纱线既柔软又耐用。
2. 织物具有良好的光泽和手感:由于包纤维可以是具有良好光泽的纤维,如丝绸或人造丝绸,紧密纺包芯纱制成的织物通常具有较好的光泽。
同时,芯纤维的加入还可以使织物具有柔软的手感。
3. 收缩性低:由于芯纤维的存在,紧密纺包芯纱相对于普通纱线来说,具有较低的收缩性。
这意味着在织造过程中,织物的尺寸变化较小,保持形状和尺寸的稳定性。
4. 多样化的应用:紧密纺包芯纱由于其独特的结构和特点,广泛应用于纺织工业中。
它可以制成各种不同类型的织物,包括服装、家居纺织品、工业用纺织品等。
同时,紧密纺包芯纱还可以制成缝纫线、绣线和其他纺织品相关的产品。
总之,紧密纺包芯纱通过将不同纤维组合在一起,形成了具有高强度、良好光泽和手感,低收缩性等特点的纱线。
这种纱线在纺织业中得到广泛应用,满足了各种不同织物的需求。
新纺紧密纺及名词解释

紧密纺纱(Compact Spinning)紧密纺又称:集聚纺,卡摩纺、依丽纺二、紧密纺纱设计原理(一) 环锭纺纱强力高的原因环锭纱中纤维形态转杯纱中纤维形态环锭纱形成圆锥形螺旋线的原因:加捻三角区F1=Fsinα使纱线向中间转移F2=Fcosα使纱线沿纱轴运动(二) 加捻三角区引起的问题1.毛羽的形成头端毛羽形成尾端毛羽形成2.飞花的形成细纱车间85%的飞花是加捻三角区产生的。
3.纤维张力不匀边缘纤维形成纱线表面纤维,预张力大,拉伸时先断裂飞花形成中间纤维形成纱芯校外,预张力小,拉伸时后断裂纤维不同时断裂,纱线强力低(三) 紧密纺纱的设计理念紧密纺设计理念:缩小甚至去掉加捻三角区三、紧密纺纱的机构及原理(一)瑞士立达Comforspin1. 瑞士立达Comforspin 纺纱装置示意图2. 瑞士立达Comforspin 纺纱装置照片3. 瑞士立达Comforspin 纺纱装置吸风内胆4. 瑞士立达Comforspin 纺纱装置成纱过程5. 瑞士立达Comforspin 纺纱装置纺纱效果6. 瑞士立达Comforspin 纺纱装置纺纱效果环锭纺纱线紧密纺纱线(二)德国Sussen Elite 纺纱装置1.机构示意图2.德国Sussen Elite 纺纱装置照片3.德国Sussen Elite 纺纱装置纺纱效果(三)德国青泽Zinser 纺纱装置1.机构示意图2.德国青泽Zinser 纺纱装置照片3.德国青泽Zinser 纺纱装置纺纱效果(四)德国Rocos 纺纱装置德国Rocos 纺纱装置纺纱效果四、德国青泽Zinser 纺纱装置录像五、紧密纺纱的优点1.纱线毛羽少:3mm以上毛羽减少70%-80%。
2.纤维平行取向度好,纤维整体结构好,取向规则,纤维利用率高,纤维张力均匀,拉伸时同时断裂纤维多,纱线强力高,伸长率大,耐磨性大。
强力提高10%-20%,伸长率提高20%。
3.减少了络筒、整经、织布、针织等工序的断头,提高了经济效益。
紧密纺纱的原理、性能特点及产品开发
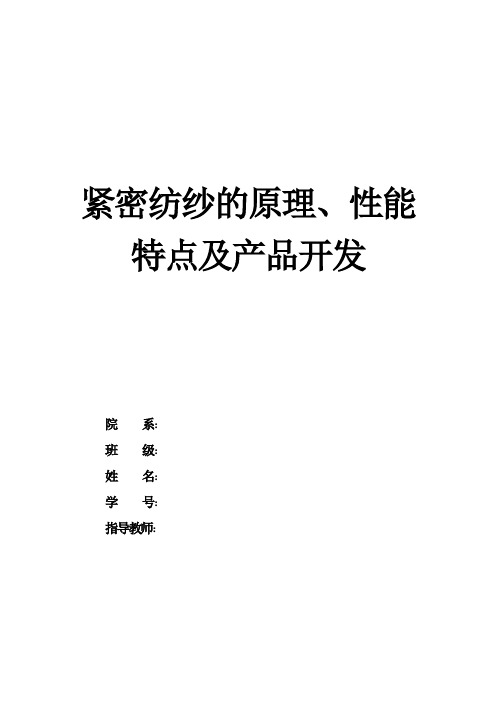
紧密纺纱的原理、性能特点及产品开发院系:班级:姓名:学号:指导教师:紧密纺纱的原理、性能特点及产品开发【摘要】:紧密纺纱技术成功地解决了环锭纺纱产生的毛羽及飞花,提高了纱线的强力和耐磨强度,纱线外观及物理性能都有很大提高和改善,与普通环锭纺纱相比,在纱的质量和产量方面都具有明显优势,为提高后续织造等工序的效率,改善面料的强度、手感、外观质量等方面提供了可靠保证。
瑞士立达公司、德国绪森公司、青泽公司、日本丰田公司等都相继推出了紧密环锭纺纱机。
文章对紧密环锭纺纱技术和紧密纺纱在色织、针织方面的使用情况作了介绍。
【关键词】:紧密纺纱、成纱机理、性能特点、产品开发1 导言紧密纺纱是近几年发展起来的利用多种形式的纱线凝聚区使加捻三角区减小或消除的纺纱技术。
是优化纱线结构的重要有效的纺纱装置。
这些装置利用钳口位置的改变,并辅以各种凝聚作用,使纱线在形成过程中的加捻三角区尽量减小或消失。
另外还可以减少纱线形成时由于位置不同而形成的张力差异,从而提高纱线强力、均匀度和减少毛羽。
这种纱线完全可以进行单纱织造,有利于轻薄均匀的高档织物的开发。
目前所生产的紧密纺纱系统有Rieter公司生产的Comforspin纺纱设备,现已从COMl发展到COM4型。
Suessen公司生产的Fiomax 特色Elite纺纱设备,有分别适合长短纤维的El型和E2型。
还有MAL公司生产的Oifil纺纱设备以及Zinser公司生产的air-com-tex 700纺纱设备。
其中在Comforspin纺纱设备和Elite纺纱设备中,是由多孔滚筒或网格胶圈表面由于负压造成的凝聚区对纤维进行凝聚,从而减小加捻三角区。
而Oifil纺纱设备以及air-com-tex 700纺纱设备则采用胶圈在受负压作用的中空体上转动,形成凝聚区使纤维凝聚。
以下就针对Comforspin和Elite两种紧密纺纱设备的机理作初步探讨。
2 紧密纺纱成纱机理卡摩纺纱是英文Compact yarn的简译音,意思是紧密纺纱。
紧密纺纱的原理
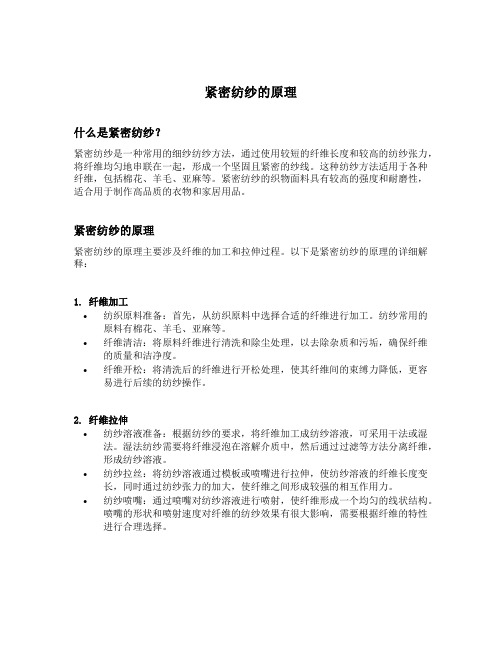
紧密纺纱的原理什么是紧密纺纱?紧密纺纱是一种常用的细纱纺纱方法,通过使用较短的纤维长度和较高的纺纱张力,将纤维均匀地串联在一起,形成一个坚固且紧密的纱线。
这种纺纱方法适用于各种纤维,包括棉花、羊毛、亚麻等。
紧密纺纱的织物面料具有较高的强度和耐磨性,适合用于制作高品质的衣物和家居用品。
紧密纺纱的原理紧密纺纱的原理主要涉及纤维的加工和拉伸过程。
以下是紧密纺纱的原理的详细解释:1. 纤维加工•纺织原料准备:首先,从纺织原料中选择合适的纤维进行加工。
纺纱常用的原料有棉花、羊毛、亚麻等。
•纤维清洁:将原料纤维进行清洗和除尘处理,以去除杂质和污垢,确保纤维的质量和洁净度。
•纤维开松:将清洗后的纤维进行开松处理,使其纤维间的束缚力降低,更容易进行后续的纺纱操作。
2. 纤维拉伸•纺纱溶液准备:根据纺纱的要求,将纤维加工成纺纱溶液,可采用干法或湿法。
湿法纺纱需要将纤维浸泡在溶解介质中,然后通过过滤等方法分离纤维,形成纺纱溶液。
•纺纱拉丝:将纺纱溶液通过模板或喷嘴进行拉伸,使纺纱溶液的纤维长度变长,同时通过纺纱张力的加大,使纤维之间形成较强的相互作用力。
•纺纱喷嘴:通过喷嘴对纺纱溶液进行喷射,使纤维形成一个均匀的线状结构。
喷嘴的形状和喷射速度对纤维的纺纱效果有很大影响,需要根据纤维的特性进行合理选择。
3. 纤维串联•过滤和整理:将喷嘴喷射出的纤维进行过滤和整理,去除杂质和不规则的纤维。
•纤维融合:纤维经过过滤和整理后,温度逐渐升高,使纤维表面的粘性增加,纤维之间开始相互融合。
通过这种融合作用,纤维之间形成牢固的连接。
•纺纱张力:通过调节纺纱设备的张力,使纤维之间产生更强的相互作用力,确保纤维能够紧密地串联在一起。
•喷射速度和温度:控制喷嘴的喷射速度和温度,调整纺纱过程中纤维的拉伸程度和相互之间的融合程度。
这些因素在一定范围内的调整,可以获得理想的纺纱效果。
紧密纺纱的应用紧密纺纱的纱线适用于各种织物的制作,包括衣物、家居用品和工业用品。
紧密赛络纺成纱机理及关键部件的研究的开题报告
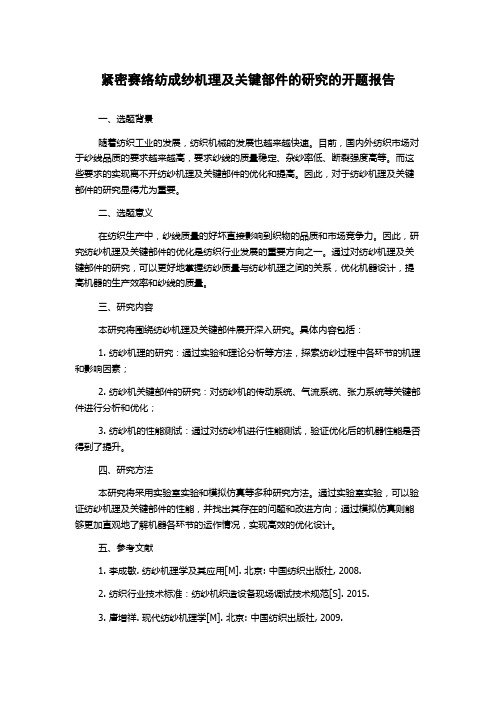
紧密赛络纺成纱机理及关键部件的研究的开题报告一、选题背景随着纺织工业的发展,纺织机械的发展也越来越快速。
目前,国内外纺织市场对于纱线品质的要求越来越高,要求纱线的质量稳定、杂纱率低、断裂强度高等。
而这些要求的实现离不开纺纱机理及关键部件的优化和提高。
因此,对于纺纱机理及关键部件的研究显得尤为重要。
二、选题意义在纺织生产中,纱线质量的好坏直接影响到织物的品质和市场竞争力。
因此,研究纺纱机理及关键部件的优化是纺织行业发展的重要方向之一。
通过对纺纱机理及关键部件的研究,可以更好地掌握纺纱质量与纺纱机理之间的关系,优化机器设计,提高机器的生产效率和纱线的质量。
三、研究内容本研究将围绕纺纱机理及关键部件展开深入研究。
具体内容包括:1. 纺纱机理的研究:通过实验和理论分析等方法,探索纺纱过程中各环节的机理和影响因素;2. 纺纱机关键部件的研究:对纺纱机的传动系统、气流系统、张力系统等关键部件进行分析和优化;3. 纺纱机的性能测试:通过对纺纱机进行性能测试,验证优化后的机器性能是否得到了提升。
四、研究方法本研究将采用实验室实验和模拟仿真等多种研究方法。
通过实验室实验,可以验证纺纱机理及关键部件的性能,并找出其存在的问题和改进方向;通过模拟仿真则能够更加直观地了解机器各环节的运作情况,实现高效的优化设计。
五、参考文献1. 李成敏. 纺纱机理学及其应用[M]. 北京: 中国纺织出版社, 2008.2. 纺织行业技术标准:纺纱机织造设备现场调试技术规范[S]. 2015.3. 唐增祥. 现代纺纱机理学[M]. 北京: 中国纺织出版社, 2009.4. 纺织行业标准:纺纱机机械安全技术规范[S]. 2019.六、预期成果通过本研究,我们将得到如下预期成果:1. 探究纺纱机理及关键部件的原理和实现方式,提出一些优化方案;2. 优化机器设计,提升机器的纺纱效率和纱线质量;3. 验证所提出方案的有效性和性能,为生产实践提供参考和借鉴。
紧密纺的纺纱机理及五大优点
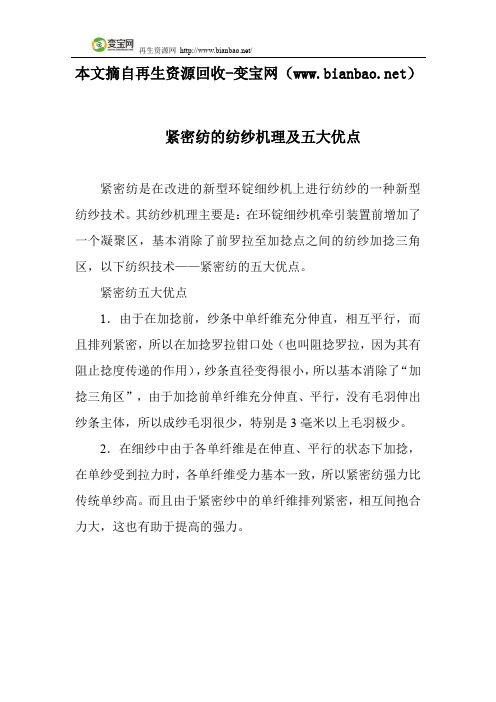
本文摘自再生资源回收-变宝网()
紧密纺的纺纱机理及五大优点
紧密纺是在改进的新型环锭细纱机上进行纺纱的一种新型纺纱技术。
其纺纱机理主要是:在环锭细纱机牵引装置前增加了一个凝聚区,基本消除了前罗拉至加捻点之间的纺纱加捻三角区,以下纺织技术——紧密纺的五大优点。
紧密纺五大优点
1.由于在加捻前,纱条中单纤维充分伸直,相互平行,而且排列紧密,所以在加捻罗拉钳口处(也叫阻捻罗拉,因为其有阻止捻度传递的作用),纱条直径变得很小,所以基本消除了“加捻三角区”,由于加捻前单纤维充分伸直、平行,没有毛羽伸出纱条主体,所以成纱毛羽很少,特别是3毫米以上毛羽极少。
2.在细纱中由于各单纤维是在伸直、平行的状态下加捻,在单纱受到拉力时,各单纤维受力基本一致,所以紧密纺强力比传统单纱高。
而且由于紧密纱中的单纤维排列紧密,相互间抱合力大,这也有助于提高的强力。
3.在紧密纺工艺中,纱条是在完成了工艺规定的牵伸之后再进行聚集,所以其条干不匀的指标没有大的改善,但在其聚集区有对纱条的整理作用,且在加捻罗拉钳口处加捻时纤维的内、外层转移没有传统工艺强烈,所以紧密纱的条干不匀,粗、细节指标比传统纱要好。
4.由于紧密纱的上述特点,为下道工序提供了非常好的条件,紧密纱毛羽少,所以减轻了上浆、烧毛等工序的压力,在无梭织机的纬纱使用紧密纱时大大减少了引纬的阻力,提高了织机效率。
5.由于紧密纱纤维排列紧密,和相同号数的传统纱线相比直径小,所以用相同经、纬密织成的布透气性好,布面平整、光滑,是高档的理想用纱。
本文摘自变宝网-废金属_废塑料_废纸_废品回收_再生资源B2B交易平台网站;变宝网官网:/?cj
买卖废品废料,再生料就上变宝网,什么废料都有!。
紧密纺纱的原理
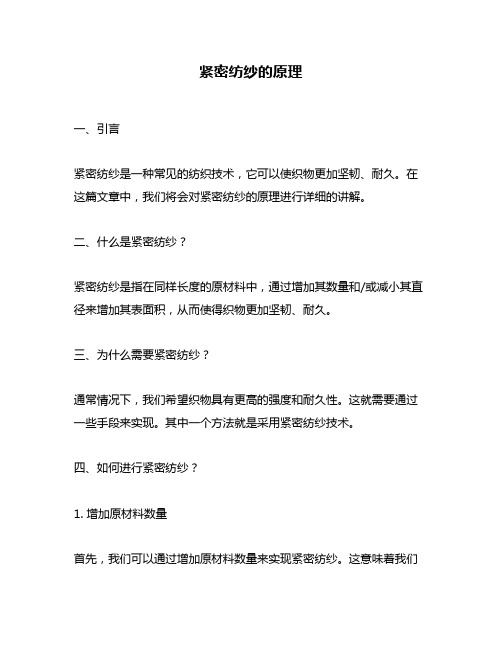
紧密纺纱的原理一、引言紧密纺纱是一种常见的纺织技术,它可以使织物更加坚韧、耐久。
在这篇文章中,我们将会对紧密纺纱的原理进行详细的讲解。
二、什么是紧密纺纱?紧密纺纱是指在同样长度的原材料中,通过增加其数量和/或减小其直径来增加其表面积,从而使得织物更加坚韧、耐久。
三、为什么需要紧密纺纱?通常情况下,我们希望织物具有更高的强度和耐久性。
这就需要通过一些手段来实现。
其中一个方法就是采用紧密纺纱技术。
四、如何进行紧密纺纱?1. 增加原材料数量首先,我们可以通过增加原材料数量来实现紧密纺纱。
这意味着我们需要使用更多的原材料来制造同样长度的线。
这样做会导致线变得更加厚实,表面积也会相应地增大。
2. 减小原材料直径另外一个方法是减小原材料直径。
这意味着我们需要使用更细的线来制造同样长度的织物。
这样做会导致线变得更加细长,表面积也会相应地增大。
3. 组合方法最后,我们可以结合上述两种方法来实现紧密纺纱。
这意味着我们需要同时增加原材料数量和减小原材料直径。
这样做会使得线变得更加厚实和细长,表面积也会相应地增大。
五、如何选择紧密纺纱的方法?通常情况下,我们需要根据具体的需求来选择不同的紧密纺纱方法。
如果需要制造更坚韧、耐久的织物,那么可以选择组合方法;如果只是需要提高织物的强度或耐久性,那么可以选择其中一种方法即可。
六、结论通过本文的讲解,我们了解了紧密纺纱的原理以及如何进行紧密纺纱。
在实际生产中,我们可以根据具体需求来选择不同的紧密纺纱方法,以达到最佳效果。
紧密牵伸压力抱合纺纱技术的机理分析(二)

o igpo p ry ti o rra hn infc c n fl asn hn s an po u t ai . pn rs i .I s f a-e c gsg i a ei l riig C eey r rd c l e t f i i n uy i u q y t
2 紧密 牵伸压 力抱合纺纱技术 的应 用实践
2 1 紧密牵 伸压 力抱 合 纺纱 的概 念 .
维普资讯
兰 兰垒 : 堂 : 塑 旦 蔓 蔓里
V 1 5N . 20 o . o6。 0 7 3
兰苎鱼
兰竺 堕 垦 鱼 设 备 与 工 艺
紧密牵伸压力 抱合纺纱技术 的机理 分析 ( ) 二
刘 国卫 键词 : 纺纱 ; 环锭纺纱 ; 牵伸 ;压力棒 ;条干 ; 毛羽 ;比较 ;紧密纺纱 中图分类号 : S 0 .1 T 14 3 文献标识码 : B 文章编 号 : 0 12 4 (0 7 0 ・0 5 0 10 ・0 4 2 0 )6 0 2 -2
Meh ns a a s fcmp c r f p es r o ee c pn igtc n lg Ⅱ) ca i m n l i o o a t at rsu ec h rn esinn eh oo y( ys d
Ab t a t sr c :Ba e n t e c mp rs n w t e d atn e i e fc mp c p n i g fa r d c b o d,t c n c li n v t n o o s d o h o a io i t r f g d vc s o o a ts i n n r me p o u e a r a hh i d e h ia n o a o fd - i
(. 1中国棉纺织行业 协会 专家委员会 。 北京 104 ; . 072 2 浙江余 姚市精伟纺织机械厂 , 浙江 余姚 357 ;) 145
紧密纺的原理
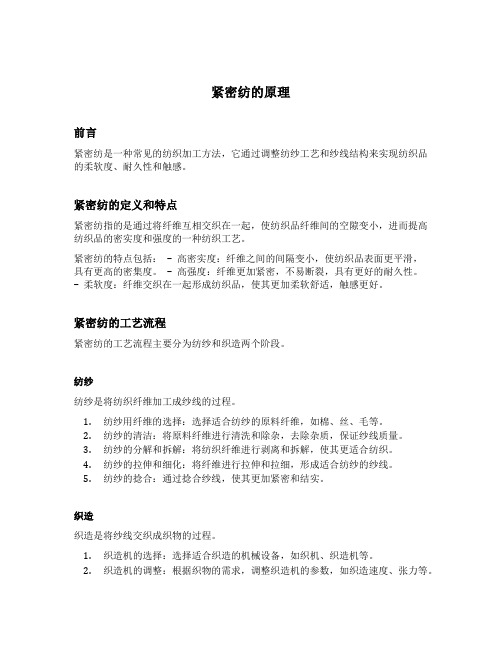
紧密纺的原理前言紧密纺是一种常见的纺织加工方法,它通过调整纺纱工艺和纱线结构来实现纺织品的柔软度、耐久性和触感。
紧密纺的定义和特点紧密纺指的是通过将纤维互相交织在一起,使纺织品纤维间的空隙变小,进而提高纺织品的密实度和强度的一种纺织工艺。
紧密纺的特点包括: - 高密实度:纤维之间的间隔变小,使纺织品表面更平滑,具有更高的密集度。
- 高强度:纤维更加紧密,不易断裂,具有更好的耐久性。
- 柔软度:纤维交织在一起形成纺织品,使其更加柔软舒适,触感更好。
紧密纺的工艺流程紧密纺的工艺流程主要分为纺纱和织造两个阶段。
纺纱纺纱是将纺织纤维加工成纱线的过程。
1.纺纱用纤维的选择:选择适合纺纱的原料纤维,如棉、丝、毛等。
2.纺纱的清洁:将原料纤维进行清洗和除杂,去除杂质,保证纱线质量。
3.纺纱的分解和拆解:将纺织纤维进行剥离和拆解,使其更适合纺织。
4.纺纱的拉伸和细化:将纤维进行拉伸和拉细,形成适合纺纱的纱线。
5.纺纱的捻合:通过捻合纱线,使其更加紧密和结实。
织造织造是将纱线交织成织物的过程。
1.织造机的选择:选择适合织造的机械设备,如织机、织造机等。
2.织造机的调整:根据织物的需求,调整织造机的参数,如织造速度、张力等。
3.织造机的操作:将纱线经过织造机进行交织,形成织物。
4.织物的处理:对织成的织物进行整理、熨烫、检验等,使其更加平整和完美。
紧密纺的应用领域紧密纺广泛应用于各个行业和领域,包括服装、家居纺织品、工业纺织品等。
1.服装:紧密纺的纺织品具有柔软度和耐久性,适合用于制作高级定制服装、高档面料等。
2.家居纺织品:床上用品、沙发套等需求具有柔软度和耐久性的纺织品,紧密纺能够满足这些需求。
3.工业纺织品:紧密纺的纺织品具有较高的强度和耐磨性,适用于工业领域的防护服、工装等。
紧密纺的优缺点紧密纺作为一种纺织工艺,有其优点和缺点。
优点•增加纺织品的耐磨性和耐用性。
•提高纺织品的柔软度和舒适度。
•改善纺织品的外观和触感。
紧密赛络纺成纱机理及.

(二)纱线对比研究
加捻纱线的纵向结构分析(350倍)
紧密塞络纺棉纱
紧密纺棉纱
赛络纺棉纱
普通环锭纺棉纱
退捻后纱线的纵向结构(100倍)
紧密赛 络纱 赛络纱 紧密纱 传统环 锭纱
紧密赛 络纱 赛络纱 紧密纱 传统环 锭纱
小结
自制紧密赛络纺纱装置结合了集聚与合股的 双重作用,可有效减小加捻三角区,成纱毛 羽明显减少,尤其是长毛羽可基本消除;纱 线的同向同步加捻,使其结构更加清晰紧密, 表面纤维排列整齐顺直,截面形状也更圆, 退捻后有明显的双股结构;成纱强伸性能和 条干得到了较好的改进。与普通环锭纺单纱、 赛络纱、紧密纱相比,紧密赛络纱突显其优 越性。
10 310 335 360 385 410 捻系数
粗细节和棉结/个
30 25 20 15 10
5 0
310 335 360 385 410 捻系数
断裂强力/cN
吸风负压对纱线性能的影
440 430 420 410 400 390 380
1500
2100 2700 吸风负压/Pa
断裂伸长率/%
5.4 5.2
14.5×2/29
80 70 60 50 40 30 20 10 0
14.5×2/29
9.7×2/19.4 纱线细度/tex
9.7×2/19.4 纱线细度/tex
7.3×2/14.6 7.3×2/14.6
紧密赛 络纱 赛络纱
紧密纱
传统环 锭纱
9.7×2/19.4 纱线细度/tex
紧密纺的原理
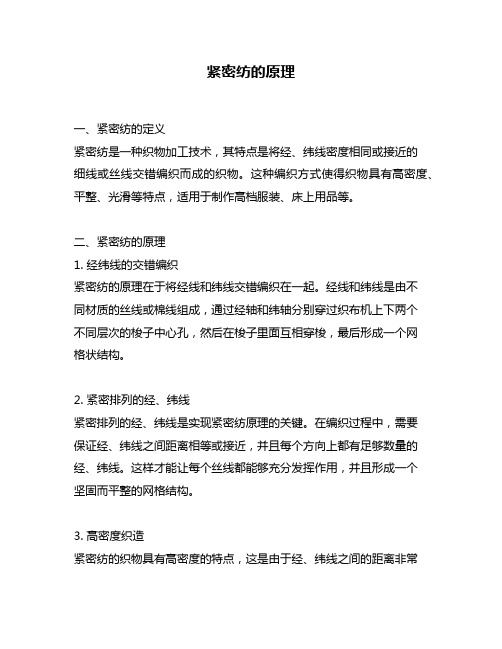
紧密纺的原理一、紧密纺的定义紧密纺是一种织物加工技术,其特点是将经、纬线密度相同或接近的细线或丝线交错编织而成的织物。
这种编织方式使得织物具有高密度、平整、光滑等特点,适用于制作高档服装、床上用品等。
二、紧密纺的原理1. 经纬线的交错编织紧密纺的原理在于将经线和纬线交错编织在一起。
经线和纬线是由不同材质的丝线或棉线组成,通过经轴和纬轴分别穿过织布机上下两个不同层次的梭子中心孔,然后在梭子里面互相穿梭,最后形成一个网格状结构。
2. 紧密排列的经、纬线紧密排列的经、纬线是实现紧密纺原理的关键。
在编织过程中,需要保证经、纬线之间距离相等或接近,并且每个方向上都有足够数量的经、纬线。
这样才能让每个丝线都能够充分发挥作用,并且形成一个坚固而平整的网格结构。
3. 高密度织造紧密纺的织物具有高密度的特点,这是由于经、纬线之间的距离非常短,每个方向上都有足够数量的经、纬线。
这种高密度织造使得织物更加平整、光滑,并且可以有效地防止织物表面出现毛刺、起球等现象。
4. 特殊的织造方式紧密纺的原理还包括一些特殊的织造方式,例如采用双层或多层编织技术、采用不同材质丝线交错编织等。
这些特殊的技术可以进一步增强织物的强度、耐久性和美观性。
三、紧密纺与其他编织方式的比较1. 与平纹比较平纹是最基本的编织方式之一,其原理是将经线和纬线交错编织在一起,但是经、纬线之间距离较大。
相比之下,紧密纺更加致密,可以形成更加坚固和平整的网格结构。
2. 与斜纹比较斜纹是一种斜向交错编织方式,其原理是将经线和斜向交错的纬线编织在一起。
相比之下,斜纹的织物更加柔软、透气,但是强度和耐久性较差,不适合制作高档服装等。
3. 与针织比较针织是一种由单根或多根丝线按照特定方式交织而成的编织方式。
相比之下,针织的织物更加柔软、弹性好,但是密度较低,容易出现毛刺和变形等问题。
四、紧密纺的应用紧密纺可以用于制作各种高档服装、床上用品、鞋帽等产品。
其优点在于具有高密度、平整、光滑等特点,可以有效地提升产品的品质和价值。
新型纺纱技术之紧密纺

新型纺纱技术之紧密纺一、简介紧密纺首次出现在巴黎ITMA’99(中国国际纺织机械展览会暨ITMA亚洲展览会)上,目前国际上有5种不同结构的紧密纺纱系统,分别是Rieter,Sussen,Mal,Zinser和TOYT公司的产品,它们在集聚方式上有所不同,但集聚原理均相同。
A)瑞士Rieter公司的Com4集聚纺纱系统:其核心技术是将前罗拉改为尘笼式实现抽风,并内置不回转的斜管使空气具有缩合作用以达到集聚纱条的目的。
B)其他几种均是在原来的细纱牵伸系统中加了一个气动集束区,负压形式均是采用网格圈或带孔皮圈来实现凝聚。
由于专利权的因素,各公司通过不同的主、被动传动形式和凝聚纱条的上、下形式来避免雷同,但由于凝聚槽的长度、角度、方式不同,以致最终效果也有所不同。
综合分析,认为Sussen的Eliter集聚方式、凝聚时间、凝聚长度及进入加捻握持点最近,又同原纺纱形式差异最小,特别对设备改造较为理想。
二、原理2.1原理紧密纺纱系统多数采用空气动力学原理,在纺纱三角区位置,通过一组集聚元件,使牵伸后的松散纤维须条经过负压吸聚管表面时,利用空气导向作用使纤维紧密地抱合在一起,经导向胶辊输出加捻成纱,纺纱过程中加捻三角区变得很小,基本消失,大大减少浮游外露纤维(即毛羽)的数量。
2.2环锭纱与紧密纱形成机理的异同在传统的环锭纺生产中,粗纱在牵伸系统的主牵伸区须条被牵伸至所要求的纱支,主牵仲区中的须条宽度是所纺纱线直径的数倍。
此时各根纤维抵达前针口线时呈自由状态,当这些纤维离开前钳几线后,即被捻合在一起形成根纱线,这样就形成了一个纺纱三角区。
在这个三角区中,纤维几乎完全失控,边缘纤维在加捻之前脱离主体形成飞花,或者纤维一段被捻入纱体,而另一端形成毛羽。
因此此,加捻三角区对纱线表面毛羽的形成及飞花的产生有着重要影响。
另外,纤维在加捻时,处于三角区外删的纤维受到的张力最大,而在中心的纤维受到的张力最小,故成纱时这些纤维的初始张力不等,使后续工序及最终产品受到拉伸时,预张力大的纤维会首先断裂,从而影响到纱线及成品的强力(见图一)。
紧密纺纱的原理和应用有哪些

紧密纺纱的原理和应用1. 紧密纺纱的原理紧密纺纱是一种纺纱技术,它通过改变纺纱过程中纱线的结构和密度,使纱线更加紧密和均匀。
这种纺纱技术在纺织工业中得到广泛应用,可以改善纺织品的手感、强度、耐磨性和色彩牢度等性能。
紧密纺纱的原理主要包括以下几个方面:1.1 选择纱线适当的纤维材料不同的纤维材料具有不同的强度、延伸性和弹性等特性,选择适当的纤维对于紧密纺纱至关重要。
一般来说,纤维的柔韧性和延伸性越高,纱线的紧密度就越高。
1.2 改变纺纱机的工艺参数在纺纱过程中,通过调整纺纱机的参数,如纱锭的转速、卷绕张力和加湿度等,可以控制纱线的细度、强度和紧密度。
例如,提高纱锭的转速和卷绕张力,可以使纱线更加紧密。
1.3 使用机械和化学方法处理纱线通过机械和化学方法处理纱线,可以改变纱线的结构和纤维间的相互作用力,从而增加纱线的紧密度。
常见的处理方法包括拉伸、压缩、浸渍和涂覆等。
2. 紧密纺纱的应用紧密纺纱技术广泛应用于纺织工业,对于提高纺织品的质量和性能有着重要的作用。
以下是紧密纺纱的几个主要应用领域:2.1 纺织品生产紧密纺纱技术在纺织品生产过程中被广泛应用,可以改善纺织品的手感、强度和耐磨性。
通过紧密纺纱技术生产的纱线更加均匀和紧密,可以制造出更加柔软、舒适和耐用的纺织品。
2.2 纺织品印染紧密纺纱技术可以增加纺织品纱线的染色区域,使得颜料更好地渗透进纱线中,从而提高纺织品印染的效果和色彩牢度。
此外,紧密纺纱还可以增加纺织品的吸水性和透气性。
2.3 纺织品防缩处理通过紧密纺纱技术可以改变纱线中纤维的排列方式,减少纤维之间的移动和变形,从而降低纺织品在使用和清洗过程中的收缩程度。
这对于需要保持稳定尺寸的纺织品非常重要,如衣物、床上用品和家具套等。
2.4 纺织品增强纺织品经过紧密纺纱处理后,其强度和耐磨性得到大幅提升。
这对于需要承受较大拉力和摩擦的纺织品非常重要,如运动装备、工业绳索和车辆安全带等。
结论紧密纺纱是一种通过改变纱线结构和密度的纺纱技术,可以改善纺织品的手感、强度、耐磨性和色彩牢度等性能。
- 1、下载文档前请自行甄别文档内容的完整性,平台不提供额外的编辑、内容补充、找答案等附加服务。
- 2、"仅部分预览"的文档,不可在线预览部分如存在完整性等问题,可反馈申请退款(可完整预览的文档不适用该条件!)。
- 3、如文档侵犯您的权益,请联系客服反馈,我们会尽快为您处理(人工客服工作时间:9:00-18:30)。
紧密纺纱成纱机理的分析
陈国华,曲丽君,隋淑英,王金泉
(青岛大学)
摘要:对Rieter公司生产的Comforspin纺纱设备以及Suessen公司生产的Fiomax特色Elite纺纱设备为代表的紧密纺纱设备的成纱机理做了初步研究,并与传统环锭纺纱的成纱机理做了比较,得到了紧密纺纱设备能够使纱线毛羽降低、纱线强力提高、细纱断头降低的机理。
首先紧密纺纱能使边缘纤维向中央收拢捻入纱中;其次紧密纺纱装置的凝聚作用使横向加捻三角区减小,增加成纱强力;最后紧密纺纱装置的输出钳口配置能使纵向加捻三角区减小,使细纱断头降低。
关键词:紧密纺纱;环锭纺纱;成纱机理
1 导言
紧密纺纱是近几年发展起来的利用多种形式的纱线凝聚区使加捻三角区减小或消除的纺纱技术。
是优化纱线结构的重要有效的纺纱装置。
这些装置利用钳口位置的改变,并辅以各种凝聚作用,使纱线在形成过程中的加捻三角区尽量减小或消失。
另外还可以减少纱线形成时由于位置不同而形成的张力差异,从而提高纱线强力、均匀度和减少毛羽。
这种纱线完全可以进行单纱织造,有利于轻薄均匀的高档织物的开发。
目前所生产的紧密纺纱系统有Rieter公司生产的Comforspin纺纱设备,现已从COMl 发展到COM4型。
Suessen公司生产的Fiomax特色Elite纺纱设备,有分别适合长短纤维的El型和E2型。
还有MAL公司生产的Oifil纺纱设备以及Zinser公司生产的air-com-tex 700纺纱设备。
其中在Comforspin纺纱设备和Elite纺纱设备中,是由多孔滚筒或网格胶圈表面由于负压造成的凝聚区对纤维进行凝聚,从而减小加捻三角区。
而Oifil纺纱设备以及air-com-tex 700纺纱设备则采用胶圈在受负压作用的中空体上转动,形成凝聚区使纤维凝聚。
以下就针对Comforspin和Elite两种紧密纺纱设备的机理作初步探讨。
2 传统环锭纺纱成纱机理
从图l a的传统环锭细纱机工艺过程可见,在传统环锭纺纱成纱过程中,由于罗拉座倾角与出纱方向不同,加捻三角区存在且长度较长(a+A),(图l b)传统环锭纺纱由于加捻三角区较大,而加捻三角区强力最低(无捻),纺纱段的纺纱张力又波动最大,因此大部分的细纱断头发生在加捻三角区内,造成细纱断头居高不下。
而纺纱张力的大小与波动范围又与细纱机车速有关,因此这也限制了车速的提高。
由图1 c可见,传统环锭纺纱输出的须条非常松散,横向宽度较宽,一些边缘纤维头端先伸出牵伸区,形成漂浮纤维头端。
这些纤维在成纱过程中由于纱线回转的离心力而不容易向纱条中心靠拢,从而形成纱线毛羽。
车速越高,离心力越大,因此也限制了车速的提高。
图1 传统环锭纺纱的成纱机理
3 Comforspin纺纱系统的成纱机理
Rieter公司生产的Comforspin纺纱系统是将传统环锭细纱机的牵伸机构稍加改装而成的。
如图2 a所示,它的前下罗拉被一个直径较大的孔眼滚筒所代替。
滚筒内安装有固定斜管抽吸系统,使滚筒内产生一定负压用来使纤维凝聚。
孔眼滚筒与第一上皮辊组成了牵伸区的前罗拉。
纤维从孔眼滚筒与第一上皮辊组成的前钳口输出后,被稳定地吸附在孔眼滚筒表面,并随孔眼滚筒向外移动到第二上皮辊与孔眼滚筒组成的输出钳口。
在输出钳口和前钳口之间由于孔眼滚筒中的斜管的作用,使气流产生缩合作用,须条中的纤维在此缩合吸力的作用下向中间收拢,这种收拢使纤维被有效地约束,须条的宽度逐渐变窄,到达输出钳口时,纤维一离开钳口即形成纱线,输出纱线方向与第二上皮辊及孔眼滚筒的圆周均相切,因此加捻三角区变得很小。
边缘纤维也由于负压作用很容易捻合到纱条中。
图2 Comforspin纺纱系统的成纱机理
从图2 b可见,由于第二上罗拉作为输出罗拉,须条被输出钳口后立即捻合,须条对输出罗拉的包围角α=o,相应加捻三角区长度比相同宽度须条的三角区长度减小了a,这种输出方法即使没有凝聚作用,纱线各项性能也会提高,特别是由于纵向加捻三角区长度变短,此处须条强力提高,断头率自会降低。
其效果相当于改变了罗拉座的倾斜角度。
二个上罗拉之间由于凝聚作用已由宽度B收拢到B′(图2 c),使加捻三角区横向宽度减小,三角区宽度的减小使边缘纤维与中央纤维之间的张力差异减小(θi差异减小),因此纤维几乎没有内外转移,纤维之间的应力差异很小,这样成纱中的纤维强力利用率则大的多,成纱强力也就大的多。
在吸管吸力的作用下使边缘纤维向中间收拢,而成纱回转的离心力也不会传递到凝聚区,边缘纤维被有效地捻入须条中,成纱毛羽显著降低。
4 Elite纺纱系统的成纱机理
Sussen公司生产的Elite细纱机是在该公司传统环锭Fiomax细纱机的前罗拉出口处加装一组合件(图3a)。
包括输出罗拉l、网眼胶圈2和异型斜槽吸管3。
输出罗拉由前罗拉4通过小齿轮5传动,网眼胶圈则由输出罗拉靠摩擦传动。
异型截面吸管内部处于负压状态,吸管上部每个纺纱位置上开一个狭槽,狭槽长度与凝聚区长度相适应,并在横向倾斜一定角度。
而凝聚区长度等于前钳口与输出罗拉和网眼胶圈钳口之间的须条长度。
当须条离开前钳口时,须条受真空作用吸附在孔眼胶圈表面,并凝聚在吸管狭槽部位,向输出钳口前进。
与Comforspin相同,须条在输出前钳口后立即成纱,加捻三角区非常小。
图3 Elite纺纱系统的成纱机理
由于须条先经凝聚区的凝聚作用,且输出后立即成纱(图3 b),所以与Comforspin的成纱原理相同,纱线毛羽减少及纱线强力提高。
但Elite纺纱与Comforspin还是有区别的。
例如Elite纺纱在凝聚区内,由于吸管斜槽与须条行进方向呈一定夹角,使须条在前进过程中产生横向运动(图3c),在摩擦力的作用下,须条产生滚动,从而把边缘纤维卷进须条内部,到达输出钳口时,已不存在边缘纤维,因此成纱时就不会产生毛羽。
由于须条在凝聚过程中还有滚动,使凝聚效果更好,输出须条的宽度更小,因此与Elite 与Comforspin相比其毛羽降低程度更大,纱线强力更高。
图4为传统环锭纺纱与Elite纺纱的输出须条加捻三角区处的图片,可以清楚的看到紧密纺纱的效果。
Elite纺纱机中的紧密纺纱装置是单独设置的,不用改变原先的纺纱机结构,只需在原来机台上将紧密纺纱装置安装上即可,因此适用于任何机型。
而Comforspin则需要重新改造前下罗拉,因此设计与安装难度较大。
5 结语
紧密型纺纱机虽然机构各不相同,但其原理基本相同。
要实现紧密纺纱其机构必须有以下几个方面的作用:
(1)使边缘纤维向中央收拢,以减少毛羽。
目前的紧密纺纱装置均为空气动力集束法,Comforspin利用网眼滚筒内的吸管制造负压,而Elite则采用网眼胶圈内的异型截面吸管来实现。
(2)使横向加捻三角区减小。
加捻三角区的减小有横向和纵向两种。
横向加捻三角区的减小靠须条宽度的减小来实现,一方面加捻三角区减小使须条宽度变小,边缘纤维减少;另一方面加捻三角区减小使成纱内纤维受力均匀,提高纤维强力利用率,使纱线强力增加。
(3)使纵向加捻三角区减小。
纵向加捻三角区的减小靠减小输出纱线与输出下罗拉的包围角α来实现。
以上两种紧密纺纱装置均能使此包围角为零,增加了加捻三角区的强力,从而减少了细纱断头。
有了以上几个基本的作用即可进行紧密纺纱。
因此,紧密纺纱的研究方向应该是在保证实现以上基本作用的基础上使结构尽可能简单化,成本低,易安装。
参考文献:
[1] 于修业.纺纱原理[M].北京:中国纺织出版社.1995.
[2] Textile Progress,2000,1/2,5-8.。