聚晶金刚石涂层的元素含量
金刚石聚晶的堆积密度

金刚石聚晶的堆积密度1.引言1.1 概述金刚石聚晶的堆积密度是指在固定容器或结构中,金刚石颗粒的紧密程度。
金刚石作为一种重要的宝石和工业材料,其堆积密度对于其性能和应用具有重要的影响。
金刚石是一种由碳元素组成的矿物,拥有优异的物理和化学性质。
它具有极高的硬度和强度,是目前已知的最坚硬的物质之一。
由于其硬度和耐磨性,金刚石被广泛应用于宝石加工、石油钻探、切割工具等领域。
金刚石聚晶是指将金刚石颗粒通过特定的工艺方法进行堆积和固结而形成的一种材料。
聚晶的过程中,金刚石颗粒之间通过化学键或物理键相互吸附和结合,形成了一个坚固的结构。
聚晶可以增加金刚石的密度和坚固性,使其更具实用性。
金刚石聚晶的堆积密度受多种因素的影响。
其中,金刚石颗粒的形状和大小、颗粒间的间隙大小以及聚晶工艺等因素都会对堆积密度产生影响。
较为紧密的堆积密度可以提高金刚石材料的坚固性和耐磨性,使其在工业领域中的应用更加广泛。
金刚石聚晶的堆积密度在各个领域都具有重要的应用价值。
在宝石加工中,通过增加金刚石的堆积密度,可以提高宝石的光泽和折射率,使其更具观赏价值。
而在工业领域,金刚石聚晶的堆积密度可以增加切削工具的锋利度和使用寿命,提高生产效率。
总之,金刚石聚晶的堆积密度是金刚石材料重要的性质之一,对于其性能和应用具有重要意义。
进一步研究金刚石聚晶堆积密度的影响因素和应用价值,将有助于推动金刚石材料的发展和应用。
1.2 文章结构文章结构部分的内容可以写成:本文主要分为三个部分:引言、正文和结论。
在引言部分,我们将概述金刚石聚晶的堆积密度的重要性以及研究的目的。
首先,我们将介绍金刚石的特性,特别是与其堆积密度相关的特性。
然后,我们将解释聚晶的概念,并概述其在金刚石领域中的应用。
通过这些介绍,读者将对金刚石聚晶的堆积密度有一个初步的了解。
在正文部分,我们将更详细地介绍金刚石的特性,包括其物理和化学特性。
我们将讨论金刚石晶体的结构和形成过程,并探讨它们在堆积过程中的堆积方式和影响因素。
pcd是什么材料

pcd是什么材料PCD是多晶金刚石(Polycrystalline Diamond)的缩写,是一种由金刚石微粉和金属结合剂通过高温高压烧结而成的超硬材料。
PCD具有极高的硬度、耐磨性和热导性,因而被广泛应用于刀具、磨具、车削刀具、铣刀、钻头等领域。
PCD材料是由金刚石微粉和金属结合剂混合而成的,经过高温高压烧结而成的一种超硬材料。
金刚石微粉作为主要成分,赋予了PCD极高的硬度和耐磨性,而金属结合剂则起到了固化和连接金刚石微粉的作用。
PCD的硬度仅次于天然金刚石,但相对于单晶金刚石而言,PCD更具有韧性和耐磨性,因此在实际应用中更加耐用和稳定。
PCD材料的硬度主要来源于其中的金刚石微粉,金刚石是自然界中最坚硬的物质之一,其摩氏硬度高达10级,是其他材料无法比拟的。
而PCD材料中的金刚石微粉经过高温高压烧结后,其硬度更是得到了进一步的提升,使得PCD具有了出色的耐磨性和切削性能。
因此,PCD被广泛应用于刀具、磨具等领域,用于加工各类硬质材料。
除了硬度和耐磨性之外,PCD材料还具有优异的热导性能。
金刚石是一种优良的热导体,因此PCD材料具有良好的散热性能,可以有效减少加工过程中的热量积聚,提高刀具的使用寿命和加工质量。
这使得PCD材料在高速切削和高效加工领域有着广泛的应用前景。
在实际应用中,PCD材料已经成为了现代制造业中不可或缺的材料之一。
其在航空航天、汽车制造、机械加工等领域都有着重要的应用价值。
例如,PCD刀具可以用于加工铝合金、铜合金、纤维增强复合材料等难加工材料,具有较高的切削效率和表面质量。
此外,PCD磨具也被广泛应用于精密磨削、超精密加工等领域,为工件加工提供了高效、精确的加工解决方案。
总的来说,PCD是一种具有极高硬度、耐磨性和热导性的超硬材料,其在现代制造业中有着广泛的应用前景。
随着制造技术的不断进步和创新,PCD材料在未来将会有更加广阔的发展空间,为工业制造领域带来更多的创新和突破。
聚晶金刚石

聚晶金刚石(PCD)刀具的开发与应用1 引言高速切削已成为现代制造技术的一个主要发展方向。
由于高速切削刀具的开发与应用直接影响高速切削的加工效率和加工质量,因此具有非常重要的意义。
刀具技术的革新,除了刀具本身的几何形状、切削角度等的革新和改进外,刀具切削刃材质的开发和革新也是提高切削效率、降低切削成本的一个关键因素。
20世纪70年代中期以来,美国、德国、日本等工业发达国家先后开发聚晶金刚石(PCD)刀具并将其用于非金属材料和有色金属材料的高速切削加工,使生产效率获得大幅度提高,切削费用成倍下降,因此被广泛应用于汽车、航空、航天以建材等工业领域。
2 PCD复合片的开发聚晶金刚石(PCD)复合片是由粒度为微米级的金刚石颗粒与Co、Ni 等金属粉末均匀混合后,在高压高温下,在碳化钨(WC)基材上烧结而成的一种刀坯新材料。
PCD 复合片不仅具有金刚石高硬度、高耐磨性、高导热性、低摩擦系数、低热膨胀系数等优越性能,同时还具有硬质合金良好的强度和韧性。
PCD 复合片还具有导电性,因此可用线切割机切割成所需刀头,将刀头焊接在刀体上,经过刃表1公司名称国别牌号金刚石平均粒径(%26micro;m)GE 美国Compax-1600Compax-1300Compax-1500Compax-17005102540Element six (原De Beers) 英国Syndite-CTC002Syndite-CTB002Synd ite-CTB010Syndite-CTB025Syndite-CTH02522102525住友电工日本DA-200DA-150DA-100DA-900.5520+0.550日本韩国CFCMCC21025东名日本TDC-FMTDC-98F2MTDC-GMTDC-SMTDC-HMTDC-SATDC-EpMTDC-EM113710162036+16磨制成PCD 刀具。
目前国内外已有不少PCD 复合片的生产企业,主要生产厂商及产品牌号见表1。
PCD﹑PCBN刀具材料及刀具涂层
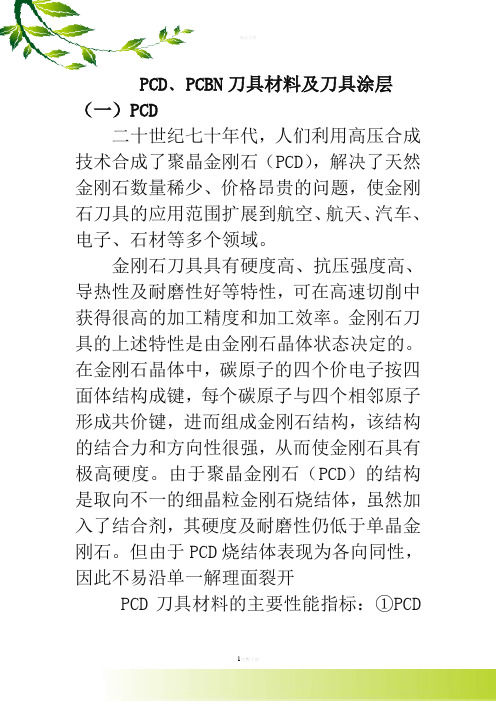
PCD﹑PCBN刀具材料及刀具涂层(一)PCD二十世纪七十年代,人们利用高压合成技术合成了聚晶金刚石(PCD),解决了天然金刚石数量稀少、价格昂贵的问题,使金刚石刀具的应用范围扩展到航空、航天、汽车、电子、石材等多个领域。
金刚石刀具具有硬度高、抗压强度高、导热性及耐磨性好等特性,可在高速切削中获得很高的加工精度和加工效率。
金刚石刀具的上述特性是由金刚石晶体状态决定的。
在金刚石晶体中,碳原子的四个价电子按四面体结构成键,每个碳原子与四个相邻原子形成共价键,进而组成金刚石结构,该结构的结合力和方向性很强,从而使金刚石具有极高硬度。
由于聚晶金刚石(PCD)的结构是取向不一的细晶粒金刚石烧结体,虽然加入了结合剂,其硬度及耐磨性仍低于单晶金刚石。
但由于PCD烧结体表现为各向同性,因此不易沿单一解理面裂开PCD刀具材料的主要性能指标:①PCD的硬度可达8000HV,为硬质合金的80~120倍;②PCD的导热系数为700W/mK,为硬质合金的1.5~9倍,甚至高于PCBN和铜,因此PCD刀具热量传递迅速;③PCD的摩擦系数一般仅为0.1~0.3(硬质合金的摩擦系数为0.4~1),因此PCD刀具可显著减小切削力;④PCD的热膨胀系数仅为0.9×10 -6~1.18×10 -6,仅相当于硬质合金的1/5,因此PCD刀具热变形小,加工精度高;⑤PCD 刀具与有色金属和非金属材料间的亲和力很小,在加工过程中切屑不易粘结在刀尖上形成积屑瘤。
PCD刀具的应用: 工业发达国家对PCD刀具的研究开展较早,其应用已比较成熟。
自1953年在瑞典首次合成人造金刚石以来,对PCD刀具切削性能的研究获得了大量成果,PCD刀具的应用范围及使用量迅速扩大。
目前,国际上著名的人造金刚石复合片生产商主要有英国De Beers公司、美国GE公司、日本住友电工株式会社等。
据报道,1995年一季度仅日本的PCD刀具产量即达10.7万把。
图层金刚石

三、涂层金刚石的发展研究现状
(2)硬质合金基体中的Co具有催石墨化的作用;
(3)金刚石与WC-Co硬质合金热膨胀系数不匹配导致 涂层内存在较大的残余应力。
选择合适的厚度是金刚石涂层刀具合理性价比的关键。
CVD金刚石薄膜太薄,磨损快,刀具使用寿命不高; CVD金刚石薄膜太厚,与硬质合金基体的粘附性变差 且制造成本增加。
但材料添加了硬质耐磨 颗粒作为强化剂,这无 疑增加了这些材料加工 难度,这些硬质颗粒会 造成刀具过早磨损产生 大量切削热。
一、涂层金刚石刀具出现的历史背景
因此,多数刀具用户认为, 普通刀具已经不能满足需 求,而迫切需要一种耐磨 性更高、能稳定实现高精、 高效、寿命更长的超硬刀 具。
金刚石涂层刀具因其具有 十分接近天然金刚石的硬 度和耐磨性、高的弹性模 量、极高的热导率、良好 的自润滑性和化学稳定性 等优异性能,成为加工难 加工材料的理想刀具。
三、涂层金刚石的发展研究现状
典型的硬质合金表面预处理方法主要有:
(1)除去或钝化刀具表面层的粘结相Co; (2)施加过渡层; (3)机械处理等。 在实际应用中,为了更好地提高金刚石薄膜与硬质合 金基体的结合强度,往往同时综合采用多种表面预处 理方法。
广东工业大学匡同春等人发表了《CVD金刚石涂层硬质
石的热膨胀系数最为接近,因此一直被认为是CVD金 刚石涂层较为理想的基体材料。 缺点:由于Si3N4陶瓷本身脆性大,抗冲击性能差,一
二、涂层金刚石刀具的含义及其组成
般认为,Si3N4基金
刚石涂层刀具仅宜 用于精加工,而不 宜进行冲击切削加工。
(2) WC系硬质合金
二、涂层金刚石刀具的含义及其组成
四、涂层金刚石刀具的发展前景展望
聚晶金刚石

主要用于研磨,一般配制成研磨液来使用。
也有可能制作刀具,切割时不容易产生崩裂。
谢谢观看
微粉粒度图
聚晶金刚石微粉粒度图D50值也就是中值粒径(Median)
优点
优异的磨削性能:高去除率和韧性,具有自锐性; 与单晶金刚石比较起来,更不容易产生表面划伤; 更适合用来研磨表面由不同硬度材料构成的工件。
应用领域
作为精密磨料,用于蓝宝石、磁头、硬盘、硬质玻璃和晶体、陶瓷以及硬质合金的超精密研磨和抛光,如用 于LED蓝宝石的减薄。
聚晶金刚石
利用独特的定向爆破法由石墨制得的金刚石
01 基本介绍
04 应用领域
聚晶金刚石(PCD)(微粉)是利用独特的定向爆破法由石墨制得,高爆速炸药定向爆破的冲击波使金属飞片 加速飞行,撞击石墨片从而导致石墨转化为聚晶金刚石。
基本介绍
其结构与天然的金刚石极为相似,通过不饱和键结合而成,具有很好的韧性。 制作工艺 聚晶金刚石
金刚石的成分
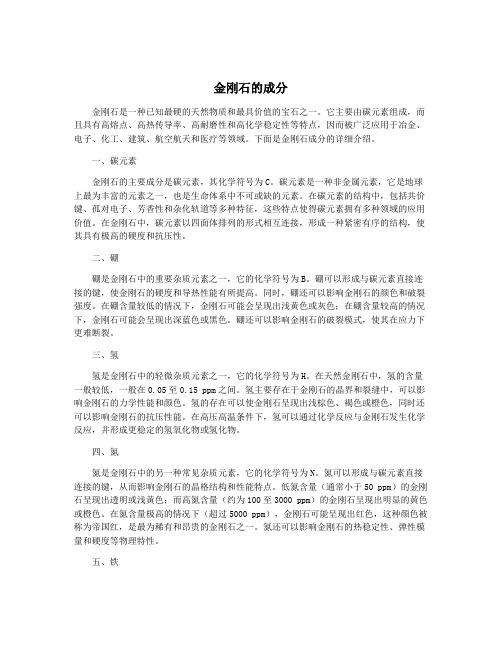
金刚石的成分金刚石是一种已知最硬的天然物质和最具价值的宝石之一。
它主要由碳元素组成,而且具有高熔点、高热传导率、高耐磨性和高化学稳定性等特点,因而被广泛应用于冶金、电子、化工、建筑、航空航天和医疗等领域。
下面是金刚石成分的详细介绍。
一、碳元素金刚石的主要成分是碳元素,其化学符号为C。
碳元素是一种非金属元素,它是地球上最为丰富的元素之一,也是生命体系中不可或缺的元素。
在碳元素的结构中,包括共价键、孤对电子、芳香性和杂化轨道等多种特征,这些特点使得碳元素拥有多种领域的应用价值。
在金刚石中,碳元素以四面体排列的形式相互连接,形成一种紧密有序的结构,使其具有极高的硬度和抗压性。
二、硼硼是金刚石中的重要杂质元素之一,它的化学符号为B。
硼可以形成与碳元素直接连接的键,使金刚石的硬度和导热性能有所提高。
同时,硼还可以影响金刚石的颜色和破裂强度。
在硼含量较低的情况下,金刚石可能会呈现出浅黄色或灰色;在硼含量较高的情况下,金刚石可能会呈现出深蓝色或黑色。
硼还可以影响金刚石的破裂模式,使其在应力下更难断裂。
三、氢氢是金刚石中的轻微杂质元素之一,它的化学符号为H。
在天然金刚石中,氢的含量一般较低,一般在0.05至0.15 ppm之间。
氢主要存在于金刚石的晶界和裂缝中,可以影响金刚石的力学性能和颜色。
氢的存在可以使金刚石呈现出浅棕色、褐色或橙色,同时还可以影响金刚石的抗压性能。
在高压高温条件下,氢可以通过化学反应与金刚石发生化学反应,并形成更稳定的氢氧化物或氢化物。
四、氮氮是金刚石中的另一种常见杂质元素,它的化学符号为N。
氮可以形成与碳元素直接连接的键,从而影响金刚石的晶格结构和性能特点。
低氮含量(通常小于50 ppm)的金刚石呈现出透明或浅黄色;而高氮含量(约为100至3000 ppm)的金刚石呈现出明显的黄色或橙色。
在氮含量极高的情况下(超过5000 ppm),金刚石可能呈现出红色,这种颜色被称为帝国红,是最为稀有和昂贵的金刚石之一。
拉丝模具的几种常见材质概述

拉丝模具的几种常见材质概述经历了几十年的发展,已出现了很多新型拉丝模材质。
按照材料种类,可将拉丝模分为合金钢模、硬质合金模、天然金刚石模、聚晶金刚石模、CVD金刚石模和陶瓷模等多种。
近年来新型材料的开发极大的丰富了拉丝模具的应用范围并提高了拉丝模的使用寿命。
(1)合金钢模是早期的拉丝模制造材料。
用来制造合金钢模的材料主要是碳素工具钢和合金工具钢。
但是由于合金钢模的硬度和耐磨性差、寿命短,不能适应现代生产的需要,所以合金钢模很快被淘汰,在目前的生产加工中已几乎看不到合金钢模。
(2)硬质合金模由硬质合金制成。
硬质合金属于钨钴类合金,其主要成分是碳化钨和钴。
碳化钨是合金的“骨架”,主要起坚硬耐磨作用;钴是粘结金属,是合金韧性的来源。
因此,硬质合金模与合金钢模相比具有以下特性:耐磨性高、抛光性好、粘附性小、摩擦系数小、能量消耗低、抗蚀性能高,这些特性使得硬质合金拉丝模具有广泛的加工适应性,成为当今应用最多的拉丝模模具。
(3)天然金刚石是碳的同素异性体,用它制作的模具具有硬度高、耐磨性好等特点。
但天然金刚石的脆性较大,较难加工,一般用于制造直径1.2mm以下的拉丝模。
此外,天然金刚石价格昂贵,货源紧缺,因此天然金刚石模并不是人们最终所寻求的即经济又实用的拉丝工具。
(4)聚晶金刚石是用经过认真挑选的质量优良的人造金刚石单晶体加上少量硅、钛等结合剂,在高温高压的条件下聚合而成。
聚晶金刚石的硬度很高,并有很好的耐磨性,与其它材料相比它具有自己独特的优点:由于天然金刚石的各向异性,在拉丝过程中,当整个孔的周围都处在工作状态下时,天然金刚石在孔的某一位置将发生择优磨损;而聚晶金刚石属于多晶体、具有各向同性的特点,从而避免了模孔磨损不均匀和模孔不圆的现象发生。
与硬质合金相比,聚晶金刚石的抗拉强度仅为常用硬质合金的70%,但比硬质合金硬250%,这样,使得聚晶金刚石模比硬质合金模有更多的优点。
用聚晶金刚石制成的拉丝模耐磨性能好,内孔磨损均匀,抗冲击能力强,拉丝效率高,而且价格比天然金刚石便宜许多。
金刚石刀具的优点和缺点

金刚石刀具的优缺点
天然金刚石(ND)刀具 聚晶金刚石(PCD)刀具
金刚石刀具
ห้องสมุดไป่ตู้
人造聚晶金刚石复合片(PDC)刀具
CVD金刚石厚膜(TDF)焊接刀具 金刚石涂层刀具
天然金刚石(ND)刀具:天然金刚石是目前已知矿物中最硬的物质,主要用 于制备刀具车刀。天然金刚石刀具精细研磨后刃口半径可达0.01~ 0.002μm。其中天然单晶金刚石(Single Crystalline Diamond,SCD)刀具切削 刃部位经高倍放大1500倍仍然观察到刀刃光滑。SCD车削铝制活塞时Ra可 达到4μm,而在同样切削条件下用PCD刀具加工时的表面粗糙时的Ra 为 15~50μm 。采用SCD刀具配合精密车床迚行精密和超精密加工,可获得 镜面表面。 聚晶金刚石(PCD)刀具:PCD是高温超高压条件下通过钴等金属结合剂将金 刚石微粉聚集烧结合成的多晶体材料,又称烧结金刚石。聚晶金刚石刀具 整体烧结成铣刀,用于铣削加工,PCD晶粒呈无序排列状态,属各向同性, 硬度均匀,石墨化温度为550℃。刀具具有高硬度、高导热性、低热胀系数、 高弹性模量和低摩擦系数。刀刃非常锋利等特点。 人造聚晶金刚石复合片(PDC)刀具:为提高PCD刀片的韧性和可焊性,常将 PCD与硬质合金刀体做成人造聚晶金刚石复合刀片(PDC)。即在硬质合金基 底其表面压制一层0.5~1mm厚的PCD烧结而成。复合刀片的抗弯强度与硬 质合金基本一致,硬度接近PCD,故可以替代PCD使用。
CVD金刚石厚膜(TDF)焊接刀具:金刚石厚膜焊接刀具是把激光切割好CVD金 刚石厚膜一次焊接至基体(通常为K类硬质合金)上,形成复合片,然后抛光复 合片,二次焊接至刀体上,刃磨成需要的形状和刃口。如图3(a)所示,为CVD 金刚石厚膜(金刚石膜厚度达30μm),具有硬度高、耐磨损、摩擦系数小等特 点,是制造切削有色金属和非金属材料刀具的理想材料。 金刚石涂层刀具:金刚石涂层刀具是用CVD法直接在硬质合金(K类硬质合金) 或陶瓷等基体上沉积一层1~25μm金刚石薄膜,无解理面各向同性。薄膜涂 层刀具硬度达9800~10000HV。热导率高,室温下导热系数高达2000W/m·K, 而硬质合金刀具导热系数仅为80~100W/m·K。CVD方法金刚石可以涂层到 任何复杂形状的刀具上,这是聚晶金刚石无法拥有的最显著的优势。
聚晶金刚石的特点、应用、分类及聚结机理

聚晶金刚石的特点、应用、分类及聚结机理超 /硬 /天 /地文/邹芹,王明智,李艳国,赵玉成摘要:本文主要介绍了聚晶金刚石的特点及应用、烧结型聚晶金刚石的分类、烧结型聚晶金刚石的聚结机理。
聚晶金刚石除了具有金刚石的一些性能外,还具有一些其它的优异性能,如:可以直接合成或加工成特定规整形状;可以设计或预测新产品的性能,赋予产品必要的特点等。
PCD目前主要用于切削工具、石油钻探工具、拉丝模、矿山开采和耐磨元件等领域。
根据PCD中晶粒结合情况可把PCD分为自身烧结和中介结合烧结两种。
烧结型PCD可分为无添加剂和有添加剂两种。
0 引言单晶金刚石由于存在各向异性,导致其在加工、使用过程中会存在方向性的问题,且大块单晶金刚石的制备在目前的合成条件下很难实现,由此人们想到了用聚晶金刚石(PCD)来代替单晶金刚石。
在自然界中存在的天然PCD有卡布那多(Carbonado)和巴拉斯(Ballas)两种。
卡布那多是一种由许多细粒金刚石与其它物质聚结成的块状PCD,很早人们称其为黑金刚石。
巴拉斯其外形似球,坚硬的外壳由辐射状金刚石构成。
它们除具有高硬度外,还具有高韧性、无方向性、无解理面等特点。
但自然界中储量甚少。
自从人造金刚石问世以来,50年代起人们就试图在超高压高温条件下能合成出其性能及结构与卡布那多及巴拉斯相似的PCD,其国家先后有美国、前苏联、南非、中国等。
70年代初期已有产品开始用于工业领域,如美国通用电气公司(GE)在1972年推出的Compax商品,是一种带硬质合金衬底的多晶金刚石复合体;英国De Beers公司在1976年推出的Syndite也属同类型商品;中国在1972年推出的JRS产品是一种整体式的柱状PCD。
人工合成的PCD是一种以许多细金刚石为原料,在有或无添加剂参与和超高压高温条件下聚结而成的金刚石聚集体。
1 聚晶金刚石的特点及应用与单晶金刚石相比PCD具有以下特点:①可以直接合成或加工成特定规整形状;②可以设计或预测新产品的性能,赋予产品必要的特点,从而适应特定用途。
不同硅基聚晶金刚石微观组织结构的对比分析

不同硅基聚晶金刚石微观组织结构的对比分析一、引言介绍研究目的和意义,简述硅基聚晶金刚石的研究现状和应用前景。
二、硅基聚晶金刚石的制备及微观组织结构表征1.硅基聚晶金刚石的制备方法2.常见的硅基聚晶金刚石的微观组织结构表征技术,如SEM、TEM等3.各制备方法及表征技术的优缺点及适用范围三、不同制备方法对硅基聚晶金刚石的微观组织结构的影响1.高温高压方法制备的硅基聚晶金刚石的微观组织结构2.气相沉积法制备的硅基聚晶金刚石的微观组织结构3.化学气相沉积法制备的硅基聚晶金刚石的微观组织结构4.离子束沉积法制备的硅基聚晶金刚石的微观组织结构5.不同制备方法对硅基聚晶金刚石微观组织结构的不同影响分析四、硅基聚晶金刚石的微观性能及其与微观组织结构的关系1.硬度、韧度、弹性模量等宏观性能对微观组织结构的依赖2.晶体缺陷、晶界、孪晶等微观结构对性质的影响3.不同制备方法造成的微观结构变化对性质的影响五、总结与展望综合各种硅基聚晶金刚石制备方法和微观组织结构的研究成果,探讨了微观组织结构对硅基聚晶金刚石性能的影响,分析了不同制备方法对微观结构的影响,对今后硅基聚晶金刚石的研究方向与发展方向进行分析和展望。
一、引言硅基聚晶金刚石是一种新型的材料,具有极高的硬度和热稳定性,被广泛用于工业和科技领域中。
近年来,随着技术的发展和人们对其性能需求的不断提高,硅基聚晶金刚石的微观组织结构研究成为材料科学领域的热点研究领域。
微观组织结构是材料性质的基础,不同制备方法和工艺条件对硅基聚晶金刚石的微观组织结构产生的影响是研究硅基聚晶金刚石性能和应用的关键。
本章将介绍硅基聚晶金刚石的制备方法和常见的微观组织结构表征技术。
二、硅基聚晶金刚石的制备及微观组织结构表征1.硅基聚晶金刚石的制备方法硅基聚晶金刚石的制备方法有多种,其中较为常见的制备方法包括高温高压法、气相沉积法、化学气相沉积法和离子束沉积法等。
(1)高温高压法:通过在高温高压条件下将钻石芯片和硅粉等原料混合加热,利用钻石的超硬度和抵抗高温高压的性质,使硅原子在钻石芯片表面晶化成聚晶金刚石,从而得到硅基聚晶金刚石。
金刚石表面镀覆纳米Ti涂层
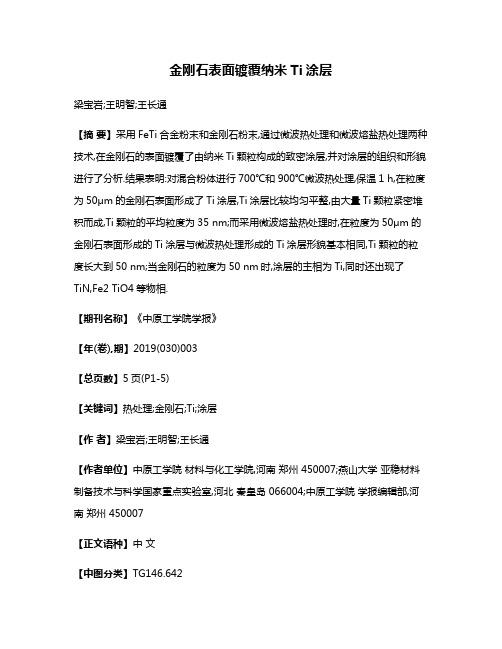
金刚石表面镀覆纳米Ti涂层梁宝岩;王明智;王长通【摘要】采用FeTi合金粉末和金刚石粉末,通过微波热处理和微波熔盐热处理两种技术,在金刚石的表面镀覆了由纳米Ti颗粒构成的致密涂层,并对涂层的组织和形貌进行了分析.结果表明:对混合粉体进行700℃和900℃微波热处理,保温1 h,在粒度为50μm的金刚石表面形成了Ti涂层,Ti涂层比较均匀平整,由大量Ti颗粒紧密堆积而成,Ti颗粒的平均粒度为35 nm;而采用微波熔盐热处理时,在粒度为50μm的金刚石表面形成的Ti涂层与微波热处理形成的Ti涂层形貌基本相同,Ti颗粒的粒度长大到50 nm;当金刚石的粒度为50 nm时,涂层的主相为Ti,同时还出现了TiN,Fe2 TiO4等物相.【期刊名称】《中原工学院学报》【年(卷),期】2019(030)003【总页数】5页(P1-5)【关键词】热处理;金刚石;Ti;涂层【作者】梁宝岩;王明智;王长通【作者单位】中原工学院材料与化工学院,河南郑州 450007;燕山大学亚稳材料制备技术与科学国家重点实验室,河北秦皇岛 066004;中原工学院学报编辑部,河南郑州 450007【正文语种】中文【中图分类】TG146.642金刚石是一种非常重要的材料,具有极高的硬度和良好的耐磨性,同时具有高导热性、抗腐蚀性和电绝缘性等优良性能,在国民经济的多个领域得到了广泛的应用。
但是金刚石具有较高的化学惰性,导致其与结合剂之间粘结性较差。
因此,金刚石工具在工作中,金刚石容易和胎体分离,从而极大地降低工具的使用性能及寿命。
如何改善胎体和金刚石的结合状态,是提高金刚石工具的工作效率以及延长其使用寿命的关键。
采用多种镀覆技术,比如电镀和化学镀[1]、气相沉积[2-3]、真空微蒸发镀[4]、熔盐热处理镀覆[5-9]等技术,可实现在金刚石表面镀覆金属。
通过这些技术在金刚石表面镀覆金属涂层组织,可有效地增强胎体对金刚石的把持力,从而显著改善金刚石工具的使用性能。
金刚石刀具材料的品种分类

金刚石刀具材料的品种分类金刚石刀具材料分为单晶金刚石(有天然和人造两种,天然单晶金刚石价格昂贵,被人造单晶金刚石替代)、人造聚晶金刚石(PCD)和人造聚晶金刚石与硬质合金复合刀片(PCD/CC)以及CVD金刚石。
单晶金刚石单晶金刚石用作切削刀具必需是大颗粒的(质量大於0.1g,最小径长不得小於3mm),重要用于表面粗糙度、几何形状精度和尺寸精度有较高要求的精密和超精密加工应用领域。
天然单晶金刚石是金刚石中最耐磨的材料。
它本身质地细密,经过精细研磨,切削刃的刃口钝圆半径可小到0.008~0.005m。
但天然单晶金刚石较脆,其结晶各向异性,不同晶面或同一晶面不同方向的晶体硬度均有差异,在进行刃磨和使用时必需选择合适的方向。
由於使用条件苛刻,加上天然单晶金刚石资源有限,价格非常昂贵,所以生产上大多采纳PCD、PCD/CC和CVD金刚石刀具。
天然单晶金刚石重要用於某些有色金属的超精紧密削加工或黄金首饰的生产中。
人工合成单晶金刚石的尺寸、形状和性能都具有良好的一致性,目前由于高温高压技术日趋成熟,能够制备肯定尺寸的人工合成单晶金刚石,尤其在加工高耐磨的层状木板时,其性能要优于PCD金刚石,不会引起刃口过早钝化。
人造聚晶金刚石(PCD)和人造聚晶金刚石与硬质合金复合刀片(PCD/CC)PCD是在高温(约1800℃)、高压(5~6MPa)下,利用钴等金属结合剂将很多金刚石单晶粉聚晶成多晶体材料,其硬度虽稍低于单晶金刚石,但它是随机取向的金刚石晶粒的聚合,属各向同性,用作切削刀具时可以任意取向刃磨,无需像天然金刚石那样必需选用最佳的解理面作为前刀面。
在切削时,切削刃对意外损坏很不敏感,抗磨损本领也较强,可长时间保持锋利的切削刃,加工时可采纳很高的切削速度和较大的背吃刀量(吃深),使用寿命一般高于WC基硬质合金刀具10~500倍,而且由於PCD中金属结合剂具有导电性,使得PCD便于切割成形,且原材料来源丰富,其价格只有天然金刚石的几非常之一至十几分之一,已成为传统WC基硬质合金刀具的高性能替代品。
超硬涂层知识图文并茂详解(6种)
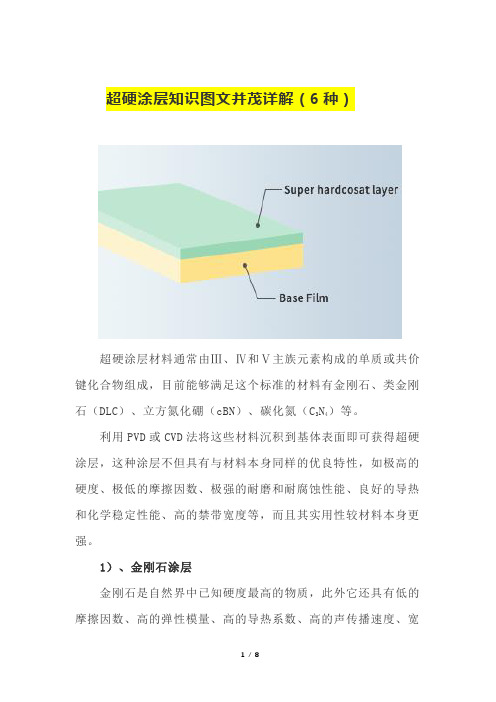
超硬涂层知识图文并茂详解(6种)超硬涂层材料通常由Ⅲ、Ⅳ和Ⅴ主族元素构成的单质或共价键化合物组成,目前能够满足这个标准的材料有金刚石、类金刚石(DLC)、立方氮化硼(cBN)、碳化氮(C3N4)等。
利用PVD或CVD法将这些材料沉积到基体表面即可获得超硬涂层,这种涂层不但具有与材料本身同样的优良特性,如极高的硬度、极低的摩擦因数、极强的耐磨和耐腐蚀性能、良好的导热和化学稳定性能、高的禁带宽度等,而且其实用性较材料本身更强。
1)、金刚石涂层金刚石是自然界中已知硬度最高的物质,此外它还具有低的摩擦因数、高的弹性模量、高的导热系数、高的声传播速度、宽的能带隙以及良好的化学稳定性等,然而天然金刚石的存量及价格限制了它的大规模商业化应用。
目前一般会采用CVD法制备金刚石涂层,它具有与天然金刚石非常相近的物理和化学性能,根据金刚石的晶粒尺寸,可以将CVD金刚石涂层分为微米晶金刚石(MCD)涂层和纳米晶金刚石(NCD)涂层,其中,晶粒尺寸小于10nm时,被称作超纳米金刚石(UNCD)涂层。
CVD金刚石涂层制备技术已取得了非常大的进展,部分产品已进入产业化推广阶段,并形成了一定的市场规模,应用领域非常多,如下图所示:2)、类金刚石(DLC)涂层利用离子束沉积技术制备了一种化学组成、光学透过率、硬度以及耐磨损等性能与金刚石相近的非晶碳涂层。
这种碳涂层具有以sp3键碳共价结合为主体,混合有sp2键碳的亚稳态长程无序立体网状结构,被称为类金刚石(DLC)涂层。
由于DLC涂层中既有类似于金刚石的sp3键合形式,又有类似于石墨的sp2键合形式,因而其结构和性能介于金刚石和石墨之间。
DLC涂层具有与金刚石涂层非常相近的性能,即极高的硬度、电阻率、导热系数、电绝缘强度、高红外透射性以及光学折射率,同时具有良好的化学稳定性和生物相容性等,在机械、电子、光学、声学、计算机以及生物医学等领域有着广阔的应用前景。
不过受沉积方式和环境的影响,DLC涂层中还可能含有氢等杂质,含各种C-H键,因此不同的制备方法和工艺条件对涂层的性能,尤其是硬度的影响很大。
加工铝合金用的类金刚石(DLC)碳涂层

加工铝合金用的类金刚石(DLC)碳涂层类金刚石碳(DLC)涂层的重要成分为碳,是一种兼有高硬度和优异摩擦性能的非晶体硬质薄膜。
由于其优异的摩擦性能,在工业上得到广泛应用。
特别在无润滑剂情况下,摩擦系数也很低(=0.005~0.2),因此被广泛应用于冷热水混合旋塞用单手柄等滑动部件。
DLC涂层不仅摩擦系数小,而且抗粘附性好,硬度高,耐磨性优良,对其在切削刀具中的应用也进行过不少试验。
但是,由于切削刀具的使用环境特别,DLC涂层在切削初始阶段便发生剥离,其性能不能得到充分发挥。
日本住友电工公司近来活着界上首先开发出可用于干式加工铝合金的DLC涂层硬质合金刀具,各种性能均得到很大提高。
1.DLC涂层的性能1.1DLC涂层的机械性能试验所用基体为WC—Co硬质合金,其表面粗糙度为Ra0.01m以下。
DLC涂层特别平滑,其表面粗糙度与涂覆前的基体表面粗糙度均为Ra0.01m,最大高度Ry为0.27m。
为了与加工铝合金用CVD金刚石涂层比较,对涂层表面进行了SEM观测。
观测结果表明:CVD金刚石涂层有金刚石结晶形态引进的突起,表面粗糙度Ra为0.53m,Ry为5.74m,而DLC涂层则重非晶质结构表面特别光滑。
DLC涂层的克氏硬度为30GPa。
1.2DLC涂层的滑动特性为了评价DLC涂层对铝合金的摩擦特性,在DLC涂层试片表面上,以铝合金销(JISA5052、直径6mm)为对偶,在常温、大气中(20℃、相对湿度RH65%)进行20分钟销片滑动试验。
为了比较,还准备了铝合金、硬质合金、各种陶瓷等试片。
滑动试验采纳CSEM公司生产的TRIBOMETER(PINONDISK)。
滑动试验条件为:滑动半径1mm,负荷1N,滑动速度52m/s(500rpm),滑动次数10000次(滑动时间20分钟)。
由滑动试验测定的摩擦系数(为试验即将结束之前的数值)和试片侧粘附铝合金量(用表面粗糙度仪对滑动痕迹横截面进行测定)测定结果可以看出,非DLC涂层试片均显现了销材质铝合金的粘附、咬合,摩擦系数达0.8以上,而DLC涂层试片摩擦系数却只有0.1,其表面也未发觉铝合金粘附。
金刚石聚晶制造原理
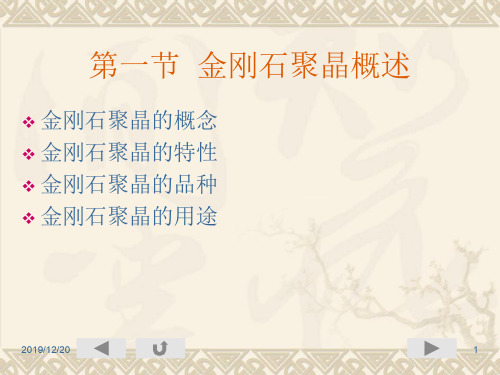
18
第二节 金刚石聚结过程分析
金刚石聚晶烧结过程中的基本物理化学变化 烧结体的显微结构 粘结剂用量及加入方式 烧结压力温度临界曲线 烧结工艺参数对烧结过程及聚晶质量的影响
2019/12/20
19
一、金刚石聚晶烧结过程中的
基本物理化学变化
熔融 浸润 生成过渡相
粘结剂与C原子化合,生成过渡相的碳化物,间隙相。 生成的间隙相比金属熔点高,硬度也高。同时,空间利用率 的提高,使结构更致密,也起了一定作用。 粘结剂不同成分之间发生反应
随着P↑,当ΔV>0时,K↓;ΔV=0时,对K无影响; ΔV<0,K↑。但P对K影响不很大。时间适当延长, 可使反应充分,但值得注意的是时间过长,金刚石 会发生严重石墨化。
2019/12/20
28
第三节 金刚石聚晶烧结机理
粉体烧结过程基础知识 金刚石聚晶粘结机理
2019/12/20
29
无衬底的金刚石聚晶:圆形、三角形、方形、 山墙形等
有衬底的金刚石复合片:圆形、方形、扇形、 半圆形、长条形
种类:刀具头、拉丝模、修整块等
2019/12/20
14
K I
d t
W
I
t
2019/12/20
I tT
d
Compax刀具头
d
Compax拉丝模
Compax修整块
Compax金刚石聚晶
一、粉体烧结过程基础知识
1.一般粉体烧结过程
烧结的一般过程可分为4个阶段。
阶段A:烧结前固体颗粒为自由堆积,颗粒间有的 彼此以点接触,有的则相互分开,保留着较多的空 隙。
阶段B:随着烧结温度的提高和时间的延长,开始 产生颗粒间的键合和重排过程。这时粒子因重排而 相互靠拢,大孔隙逐渐消失,气孔的总体积迅速减 小,但颗粒之间仍以点接触为主,总表面积并没有 缩小。
DLC涂层
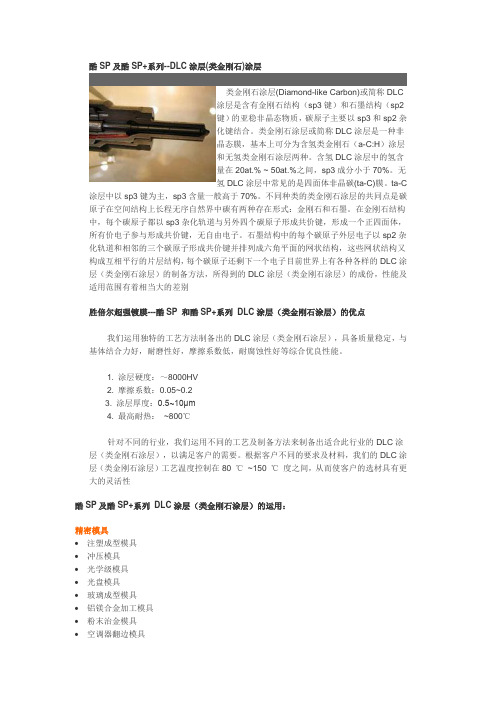
酷SP及酷SP+系列--DLC涂层(类金刚石)涂层类金刚石涂层(Diamond-like Carbon)或简称DLC涂层是含有金刚石结构(sp3键)和石墨结构(sp2键)的亚稳非晶态物质,碳原子主要以sp3和sp2杂化键结合。
类金刚石涂层或简称DLC涂层是一种非晶态膜,基本上可分为含氢类金刚石(a-C:H)涂层和无氢类金刚石涂层两种。
含氢DLC涂层中的氢含量在20at.% ~ 50at.%之间,sp3成分小于70%。
无氢DLC涂层中常见的是四面体非晶碳(ta-C)膜。
ta-C 涂层中以sp3键为主,sp3含量一般高于70%。
不同种类的类金刚石涂层的共同点是碳原子在空间结构上长程无序自然界中碳有两种存在形式:金刚石和石墨。
在金刚石结构中,每个碳原子都以sp3杂化轨道与另外四个碳原子形成共价键,形成一个正四面体,所有价电子参与形成共价键,无自由电子。
石墨结构中的每个碳原子外层电子以sp2杂化轨道和相邻的三个碳原子形成共价键并排列成六角平面的网状结构,这些网状结构又构成互相平行的片层结构,每个碳原子还剩下一个电子目前世界上有各种各样的DLC涂层(类金刚石涂层)的制备方法,所得到的DLC涂层(类金刚石涂层)的成份,性能及适用范围有着相当大的差别胜倍尔超强镀膜---酷SP 和酷SP+系列DLC涂层(类金刚石涂层)的优点我们运用独特的工艺方法制备出的DLC涂层(类金刚石涂层),具备质量稳定,与基体结合力好,耐磨性好,摩擦系数低,耐腐蚀性好等综合优良性能。
1. 涂层硬度:~8000HV2. 摩擦系数:0.05~0.23. 涂层厚度:0.5~10μm4. 最高耐热:~800℃针对不同的行业,我们运用不同的工艺及制备方法来制备出适合此行业的DLC涂层(类金刚石涂层),以满足客户的需要。
根据客户不同的要求及材料,我们的DLC涂层(类金刚石涂层)工艺温度控制在80 ℃~150 ℃度之间,从而使客户的选材具有更大的灵活性酷SP及酷SP+系列DLC涂层(类金刚石涂层)的运用:精密模具•注塑成型模具•冲压模具•光学级模具•光盘模具•玻璃成型模具•铝镁合金加工模具•粉末治金模具•空调器翻边模具•半导体封装模具•吹塑成型模具•铍铜材料模具及产品精密机械•精密轴承•纺织设备及零部件•压缩机螺杆,滑片•泵密封圈,叶片•缝制设备及零部件•弹簧片•精密传动机构切削刀具•加工有色金属的刀具•加工PCB材料的刀具工量具•卡尺•卡规•塞规•治具医疗设备和器具•手术刀片•手术剪•心脏瓣膜•人工关节•血管支架内燃机工业•燃料喷射系统(气门挺杆,柱塞,喷油嘴) •动力传动系统(齿轮,轴承,凸轮轴)•活塞部件(活塞环,活塞销)•门扣锁,内饰娱乐健身•扬声器振膜•移动硬盘•光盘•高尔夫球具•自行车部件•剃须刀片光学•红外增透膜•减反射膜•玻璃镀膜•镜片镀膜•亚克力镀膜•保护膜装饰镀膜•手机外壳•高档手表•室内外五金卫浴产品•饰品航空航天•飞机,导弹整流罩镀膜•卫星,太阳能电池镀膜。
金刚石的表面镀覆
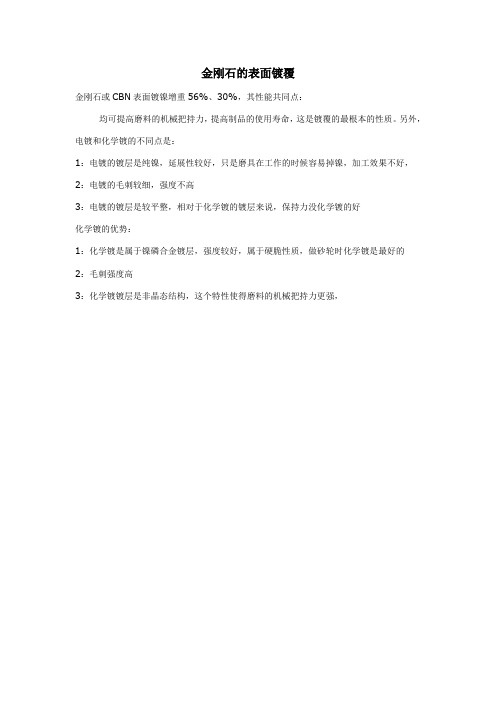
金刚石的表面镀覆
金刚石或CBN表面镀镍增重56%、30%,其性能共同点:
均可提高磨料的机械把持力,提高制品的使用寿命,这是镀覆的最根本的性质。
另外,电镀和化学镀的不同点是:
1:电镀的镀层是纯镍,延展性较好,只是磨具在工作的时候容易掉镍,加工效果不好,2:电镀的毛刺较细,强度不高
3:电镀的镀层是较平整,相对于化学镀的镀层来说,保持力没化学镀的好
化学镀的优势:
1:化学镀是属于镍磷合金镀层,强度较好,属于硬脆性质,做砂轮时化学镀是最好的
2:毛刺强度高
3:化学镀镀层是非晶态结构,这个特性使得磨料的机械把持力更强,。
- 1、下载文档前请自行甄别文档内容的完整性,平台不提供额外的编辑、内容补充、找答案等附加服务。
- 2、"仅部分预览"的文档,不可在线预览部分如存在完整性等问题,可反馈申请退款(可完整预览的文档不适用该条件!)。
- 3、如文档侵犯您的权益,请联系客服反馈,我们会尽快为您处理(人工客服工作时间:9:00-18:30)。
聚晶金刚石涂层的元素含量
聚晶金刚石涂层是一种具有高硬度、高耐磨性和高耐腐蚀性的表面涂层材料,广泛应用于刀具、模具、机械零件等领域。
其优异的性能主要归功于其特殊的元素含量。
本文将从聚晶金刚石涂层的元素含量入手,探讨其特点和应用。
一、碳元素
聚晶金刚石涂层主要由碳元素构成。
碳元素是构成金刚石晶格的主要元素,具有极高的硬度和热稳定性。
在涂层制备过程中,通过热解石墨等方法,将碳元素沉积在基体表面,形成金刚石晶体。
这些金刚石晶体之间通过共价键相互连接,使得涂层具有极高的硬度和耐磨性。
二、金属元素
聚晶金刚石涂层中通常还含有金属元素。
金属元素的添加可以改善涂层的性能,并调节涂层的组织结构和性能。
常见的金属元素包括钛、铬、铝、钼等。
这些金属元素可以与碳元素形成合金化合物,增强涂层的硬度和耐磨性。
此外,金属元素还可以提高涂层的抗腐蚀性能和热稳定性,使其能够在恶劣环境下长时间工作。
三、氮元素
氮元素是聚晶金刚石涂层中的重要添加元素之一。
氮元素可以与碳元素形成碳氮键,增加涂层的硬度和耐磨性。
此外,氮元素还可以
提高涂层的热稳定性和抗氧化性能,使其能够在高温环境下长时间使用。
另外,氮元素还可以调节涂层的晶格结构,使其具有更好的机械性能和导热性能。
四、硅元素
硅元素是聚晶金刚石涂层中的重要添加元素之一。
硅元素可以与碳元素形成硅碳键,增加涂层的硬度和耐磨性。
此外,硅元素还可以提高涂层的抗腐蚀性能和热稳定性,使其能够在恶劣环境下长时间工作。
另外,硅元素还可以调节涂层的晶格结构,使其具有更好的机械性能和导热性能。
五、其他元素
除了上述几种主要元素外,聚晶金刚石涂层中还可能含有其他元素,如氧、氢、氩等。
这些元素的添加可以改善涂层的性能和结构,使其具有更好的机械性能、导热性能和抗腐蚀性能。
总结:
聚晶金刚石涂层的元素含量对其性能具有重要影响。
碳元素是构成金刚石晶格的主要元素,金属元素的添加可以改善涂层的性能,氮元素和硅元素可以增加涂层的硬度和耐磨性。
此外,其他元素的添加也可以改善涂层的性能和结构。
在实际应用中,根据不同的需求可以调节聚晶金刚石涂层的元素含量,以获得最佳的性能和效果。
聚晶金刚石涂层的元素含量研究仍在不断深入,相信将来会有更多
的元素被应用于聚晶金刚石涂层中,为各个领域的应用提供更好的解决方案。