真空压铸实例(日本文献)
真空压铸工艺参数对AZ91D合金抗拉强度的影响

orthogonal experiment showed that the vacuum p ressure and the casting p ressure were the most effective p rocess
parameters on the UTS of the vacuum die castings. Systematicexperim ents were carried out w ith a m echanical
真空压铸工艺参数对 AZ91D 合金抗拉强度的影响 胡 泊等
2 试验结果与分析
正交试验的单一因素影响结果见图 6、图 7、图 8。 图 6显示了随着型腔真空压力的下降 ,不同壁厚的铸件 抗拉强度均表现出上升趋势 。并且随着壁厚的增加 ,进 一步降低型腔真空压力 (从 60 kPa到 5 kPa)的作用越 明显 。这是由于厚大部位铸件卷气现象更为容易发生 , 并且局部型腔中保有的气体总量也更多所造成的 。图 7显示了随着铸造压力的增大 ,不同壁厚的铸件抗拉强 度均表现出上升趋势 。并且较薄壁厚的铸件对于进一 步增大铸造压力 (从 44. 7M Pa到 66. 7M Pa)的作用更为 明显 。产生这一现象的原因是较薄的部位凝固较快 ,压 力传达相对更为困难 。
真空压铸是在压铸过程中抽除型腔内气体 ,以消除 或减少压铸件内的气孔和溶解气体 ,提高压铸件的力学 性能和表面质量的一种压铸工艺 。其原理是在压射过
图 1 真空压铸原理示意图
本课题以压铸生产中广泛应用的 AZ91D 镁合金为
收稿日期 : 2007206208 基金项目 :国家自然科学基金资助项目 (50475016) ,新世纪人才支持计划项目 第一作者简介 :胡泊 ,男 , 1981年出生 ,博士研究生 ,清华大学机械工程系 ,教育部先进成形制造重点实验室 ,北京 (100084) ,电话 : 010 - 62789448, E mail: smxiong@ tsinghua. . edu. . cn
真空压铸资料

一、前言压铸作为有色金属铸造业的一种革命,大大的提高了铸件生产的生产率,成型率,降低了生产成本,也为铸件在各行各业的应用奠定广泛的基础。
现在,即使那些对压铸一无所知的人们也无时无刻不在日常生活中得益于压铸技术的应用。
然而,压铸工艺从它的诞生起就带有严重的先天不足---型腔内的气体影响。
与传统的砂型或金属固定模重力铸造相比,压铸在浇口的高速喷射比重力自然流入的高温液态金属有着更好的充型效果,但也正是由于高温高压高速的金属喷射,使金属与型腔内的空气和热金属与型腔内残留润滑剂所产生的烟气有更大可能的结合。
因此,传统压铸件的金属结构远远不如砂型或固定金属模的铸造件是一个不争的事实。
为改善压铸的这种致命缺陷,业内人士早在大半个世纪前开始就对其工艺进行了不断的改进,诸如在模具上开排气槽,尽量采用小压室的压射,低速压射,以及现代压铸机采用的多段多速压射技术。
但真正堪称革命性的改革是1956年瑞士方达瑞第一次将真空技术引用到压铸生产工艺中。
成立于1942年的瑞士方达瑞起先也是一个压铸工厂,随着成功的将真空应用到压铸工艺中,方达瑞逐渐将研究和发展方向完全转移到压铸真空应用当中来,历经60余年的不断发展和完善,使方达瑞的真空技术和应用日臻完善。
作为这个行业的先驱和领航者,方达瑞始终走在压铸真空技术和应用的最前端。
二、为什么要在压铸工艺中使用真空技术在压铸时存在于行腔中的气体由空气和压射时产生的烟气组成。
我们来看看无排气传统压铸和采用方达瑞真空系统的型腔内气体压力图。
在传统压铸中,由於在注流口处的喷射效应,50%到90%的金属熔液将与型腔内的空气和烟气充分接触,气压在最后充型点将达到3000毫巴以上至4000毫巴;在真空压铸中,最后的气压只有几百至100毫巴以下,只有极少的空气和烟气与金属接触。
滞留在型腔内的空气和烟气越多,就越难形成无缺陷的金属结构铸件。
所以排气就成为决定压铸件质量的重要因素。
这就不难理解真空排气对压铸工艺的重要之处了。
汽车安全件的真空充氧压铸

真 空充氧压铸 与普通 压铸相 比
Th 嚣 in e c n pt m e
具 有以下特 点。 点,完全能满足汽车安全件的要求。 国外该方法 已广泛 用于铝车 轮的生 产 ,日本轻金属株式会社于 18 年开 93 始用此方法大批量生产轿车铝合金车
3充氧 .
抽真空 以后 ,通过 气阀7 与供氧站 8H 的氧 气嘴6 k连 被打开 ,氧气便进 入
压铸室内部 ,并 由此进入模具型腔 ,当氧气进入预 抽真空的模具 型腔 时 ,能
以较快的速度进入型腔中的那些狭窄部位 ,以便绝大部 分原 始的水 蒸气能 被 氧气冲走 ( 图4 见 )。充氧时间应保持3 4 ,直到位于 模具 的两个凹 、凸模 ~s
强度能提高3 %以上 ,伸长率增D 8 %~10 0 no 0 %,屈服极限及冲击韧性也有显 著提高 ( 见表2 )。
Tn 谦in e c n p m e
能爆炸 ,但是 ,当金属液进 入吹氧 的型腔时 ,氧和流进的金属液前端快速反 应 ,实际上减 少了型腔 压力而形成局部真空 。这也有助于金属液流 向型腔 凹 部和狭窄 区域 。由于这个机 理,充氧压铸也能用于压铸薄 壁件 。 问的型腔 中的气体和氧 气都能通过 排 气槽排 出为止。
1 . 模具预热
为 防 止热 冲 击 和提 高 生 产率 ,生 产前 ,压 铸 模具 应 先预 热 到 1 0~ 5
2 0C 。 0
图5 注液过程
注液 口打开以 后 ,金属 液充 向
2}真空 _ 由
模具型腔通过真空管3 与真 空泵4 连接 ,在对模具型腔进 行抽真空 时,真
压铸室 。充型过程 中 ,氧 气继 续从 注液 口溢 出 ,因此 ,在注液 时也能
V法铸造

பைடு நூலகம்
V法造型工艺起源于日本,最早是1971年日本 长野县工业试验场开发的,之后在世界范围内得 到迅速的发展。中国是在20世纪80年代初引进这 项技术,其后在中国得到广泛的发展。
近年来该铸造方法对生产厚大灰铸铁件成为了 一项重要的铸造工艺。并且因其所需投资少,效 率高,铸件表面质量好而迅速取代了部分粘土砂 造型工艺。同时由于其在经济效益方面的优越性 在一定范围内取代了树脂砂、水玻璃砂的生产。 随着科技工作者对该方法的深入研究,已开发 出利用V法造型生产铸钢件、球墨铸铁件、铝合 金制品等铸造产品。
• 山西北绿树铸造有限公司采用V法技术生产叉车及工程机械配重 铸件,具有尺寸精度高,表面光洁等特点,单重可达10吨。
• 山东泰山前田锅炉有限公司是中国第一家生产燃油燃气铸铁锅炉 的厂家,采用V法生产铸铁锅炉铸铁锅片,铸件的形状虽然简单, 但是带有砂芯,工艺上比较复杂,是V法生产复杂件的一个典型。
• 其V法造型生产线是根据日本前田铁工所V法铸造(真空铸造) 生产线及工艺设备设计、制造而成。该生产线包括四工位造型机、 8个下芯合箱工位、3个浇注工位、一次缓冷工位、开箱落砂机、 二次缓冷工位等设备,全部液压推动。该V法造型生产线工艺先 进、装备精良、自动化程度高,可实现手动、联动等功能,在国 内具有领先水平。生产出的锅片、铸件具有尺寸精度高,表面光 洁度好等特点。砂箱内尺寸:2300×1500×320/320mm,生产 率10整形/小时、可年产各类铸件6000吨。
铸铝和铸钢的应用
• 用V法铸造铝合金的工艺美术型的门框、栏杆也得到了发展。这 在V法开发初期就研制过,1991年已交付11条这种生产线,最大 砂箱尺寸为:4900mm×2200mm×200/300mm。当然由于铝合 金的浇注温度较低,塑料薄膜燃烧后的残余物与砂子粘在一起, 会影响填充干砂的密度,影响铸件的质量,仍是一个待研究解决 的问题。
真空压铸
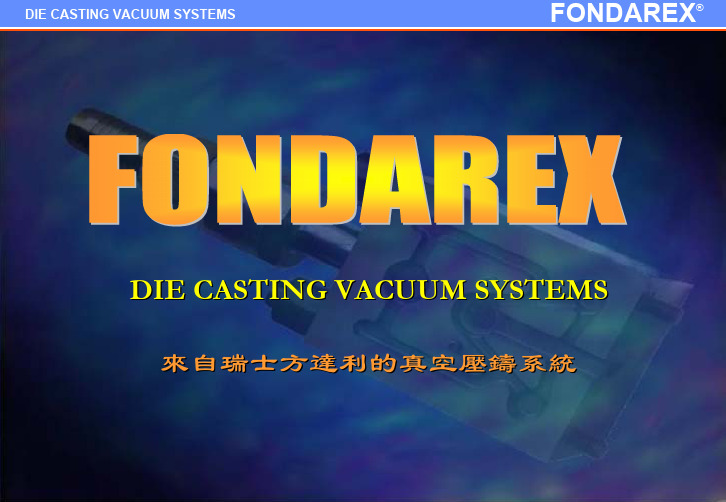
FONDAREX®
- 铸件名称: 转向盘 - 铸件重: 0,304 kg - 真空阀型号:MEDIO-P - 合金原料: Mg - 铸腔数量: 1 - 铸件特点: 注入时间短
流动距离长 - 期望质量: 无气孔率,低延展
率和可弯曲性
DIE CASTING VACUUM SYSTEMS
卫生水龙头
压缩空气
1000
在海平面的大气压力1.019 kg/cm2
500
真空
工业真空 0
DIE CASTING VACUUM SYSTEMS
带有溢流和排气通道的标准模排气
FONDAREX®
- 由於在注流口处的喷射效应, 50%到90%的合金熔液将与铸腔内 的空气和其他气体接触。
- 滞留在铸腔内的空气和其他气体 越多,就越难形成无缺陷的合金 结构铸件。
DIE CASTING VACUUM SYSTEMS
FONDAREX®
Eingangssignale
2 Signals are required:
VAKUSTART
FORM OFFEN Following 7 Signals are on option:
VAKUSPERRE VAKUSTOP EINRICHTEN SPRÜHEN PULVER VAKUUM PULVER LUFT ZENTRALVAKUUMFEHLER
FONDAREX®
- 铸件重: - 真空阀型号: - 合金原料: - 模腔数量: - 期望质量:
2x0,280kg Mini Zinc 2个 高表面质量 适于镀铬
DIE CASTING VACUUM SYSTEMS
FONDAREX®
VACUPAC MEDIO
压铸资料(日本)

空气、水与压铸 1. 铝液与空气相比,前者的密度(比重)大,所以填充的时候,必然流向 外部;空气就被封闭在内部。(当然,如果铝凝固的话,孔气就不能进去了) 2. 空气压缩就会升温 【例】柴油车35atm(大气压)的压缩空气可以升温到60℃ 3. 水在压力低的情况下,即使是常温也会沸腾;若是压力高,即使是100℃ 也不会沸腾 4. 水的饱和蒸汽压: 100℃——1atm 200℃——15.34atm 300℃——84.78atm 5. 体积的检查定律 压力一定的情况下,一定质量的气体的体积每升1℃压力就增加到0℃时 体积的1/273 V=V0· (1+1/273· ℃或k) ▽t ▽t=绝对温度-273或者是摄氏温度值 273℃时的体积是0℃是体积的2倍
铝压铸的必备常识
内容
合金特性
相关知识
金属材料 非铁材料 材料试验 物理性能 流体力学 机械工作性能 工业机器人 焊接 精加工 热处理 划线 制图 测定 铸造 管理
铝合金
材料分析(规格) 熔化 操作(运转)
设备
结构(动作) 工艺 设计
模具
制造 保全 产品用途 找正(划线)
其它
异常处理 不良对策
故障处理
缺陷的处理方法进展情况
谈到毛坯的缺陷,其中有很多是QC等手段也不能解决的。对于压铸,QC手段能解决的 缺陷只占10%,其余的90%是靠技术解决的,没有技术的人,不会知道问题出于何处。实际 上,复杂的湿度分布、流体理论是不容易测量统计的,所以掌握不住实际数值的情况是常 情。因此经验感觉有时是行之有效的,而变一变时间,换一换产品,老经验老感觉就不行 了,在填充到凝固的这个过程中,合理的理论要靠我们重新寻找,并制定出相应的对策。 ——进展方法 1) 调查缺陷现象 【例】气孔——调查内容:大小、内表面形状粗糙度、位置、数量、周围的粗粒层,与 壁厚的关系,与排气的关系(用解脱图来说明) 2) 调查条件以及作业状况 A) 设备——调查内容:低速、高速、高速切换、氮气N2的压力、合模、料柄厚度、工 作油量以及温度、高速、增压开关、异常声音、压射杆与冲头磨损(最佳铸造条件判断确 认) B) 模具——调查内容:模具温度、冷却水泄漏、排气堵塞、铝液泼溅、浇口附着、模 具的油缸工作油和脱模剂有无泄漏等(确认没有异常) C) 其它——调查内容:铝液温度、成型周期、冷却水循环方式、脱模剂喷涂量及喷涂 方式(调查确认凝固与压射是否协调) 3)尽量使用仪器进行测量 ●温度、压力测量 ●毛坯用水泡法观察气孔 ●气孔用显微镜或放大镜观察 4) 照气孔程度划分重点 气孔现象——调查中异常项目考察——记录气孔程度(大、中、小) 5) 着手重点的 ● 明确异常处理方法 ● 是条件造成的更改条件 ● 是作业造成的变更程序 6) 理解掌握调查结果 ● 用切断、加工、水泡法等来确认 ● 确认连续生产不良品数量 7) 标准化 ● 修下作业条件表 ● 修正作业要领书 ● 做成问题点教育或受控文件,并监督指导 压铸不良处理对策最重要的是要针对不同现象做出不同的判断、详细的调查:必须尽快 确认结果、判断举措正确性,此间,事故经过的调查是最重要的。相比之下,经验的用处 很大培养看问题的目光是正确决策的第一步决策过程需要相关部门的协助,所以要积极地 推进小组活动。
浅议高真空压铸技术及其应用

浅议高真空压铸技术及其应用作者:杨春红钱红来源:《中国科技纵横》2017年第07期摘要:高真空压铸技术是指在金属填充压铸模型腔的过程中,利用真空源排出压铸模型腔内部的空气使之真空度达到90kPa以上(绝对压力10kpa以下)的一种压铸成形技术。
高真空压铸的优点是能减少铸件内部气孔,提高材料的力学性能,适合于高强度高韧性、复杂薄壁零件的生产,特别是在汽车受力件的制造上具有很强的技术和效率优势。
关键词:高真空压铸;汽车轻量化;真空度中图分类号:TG249 文献标识码:A 文章编号:1671-2064(2017)07-0052-011 高真空压铸工艺概述压铸工业史上,真空压铸的首次尝试出现在1872年,由于条件不成熟,实际应用效果不大,没有几年就停止了。
1932年,L.Fromer归纳了两种基本方案,一个是直接从模具排气道抽气,另一种是将模具直接置于真空箱内部,但最终都因真空系统难于实现而放弃。
50年代,真空压铸出现复苏迹象。
各国竞相研发,取得一些技术的突破,但是因一些技术难题以及高昂的成本又步入低潮。
高真空压铸是指压铸模型腔内的真空度达到90kPa以上的压铸方法,其实现方法有三种:一是Vacural法,由德国Muller-Weingarten公司和Vaw公司联合研发;二是MFT法,由德国的Alcan-BDW公司推出,还有一种Vacuum Golve Box法,由日本雅马哈公司开发。
Vacural法是通过升液管将压室和熔化炉直接连通,金属铝液通过抽真空的方式被吸入到压室内,当真空度达到预定值时再压射成形。
Vacural法缺点是需要专用压铸机,且价格昂贵,加上受专利技术的保护,应用受到限制。
MFT(Minimum Fill Time)法只需要采用普通的压铸机,其工作原理首先抽取压铸模型腔中的空气,使型腔内真空度到90kPa以上,然后利用多浇道以及大面积的内浇口迅速将金属铝液充填型腔。
Vacuum Golve Box法是将整个模具放置在一个密封罩里面,并设置几个抽气回路来抽取密封罩内模具中的空气,确保压铸模型腔中的高真空度。
GPR JAPAN引进英国公司的真空挤压成型法技术
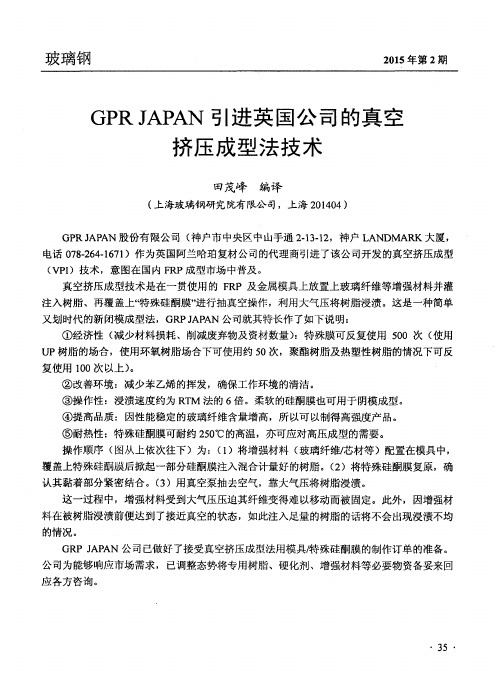
2 0 1 5 年 第2 期
GP R J AP A N 引进 英 国公 司 的真 空
挤压成型法技术
田茂峰 编译
( 上海玻璃钢研究院有 限公司,上海 2 0 1 4 0 4 )
GP R J AP AN 股份有 限公司 ( 神 户市 中央区 中 山手通 2 . 1 3 . 1 2 ,神 户 L A NDMAR K大厦, 电话 0 7 8 . 2 6 4 . 1 6 7 1 )作 为英 国阿兰 哈珀 复材 公司 的代 理 商引进 了该 公司开 发 的真 空挤压成 型
( v P I )技 术 ,意 图在 国 内 F R P成 型市场 中普及 。
真空挤压成型技术是在一贯使用 的 F R P 及金属模具上放置上玻璃纤维等增强材料并灌
注 入树 脂 、再覆 盖上 “ 特 殊硅 酮 膜” 进行 抽真 空操作 ,利 用大气 压将 树脂 浸 渍 。这 是 一种简 单
又划 时代 的新 闭模成 型法 ,GR P J A P A N 公 司就其特 长作 了如 下说 明 :
③ 操 作性 :浸渍 速度 约为 R T M 法 的 6倍 。柔 软的硅 酮膜也 可用 于 阴模 成 型 。
④提高品质 :因性能稳定的玻璃纤维含量增高,所以可以制得高强度产品。
⑤耐热性:特殊硅酮膜可耐约 2 5 0 ℃的高温,亦可应对高压成型的需要。
操作顺序 ( 从上依次往一 F )为:( 1 )将增强材料 ( 玻璃纤维/ 芯材等 )配置在模具中,
覆 盖上特殊 硅酮 膜后 掀起 一部 分硅酮 膜注 入混合 计量 好 的树 脂 。( 2 )将特 殊硅 酮膜 复原 ,确 认其 黏着部 分 紧密结 合 。( 3 )用真 空泵抽 去空气 ,靠大 气压 将树 脂浸 渍 。 这 一过 程 中 ,增 强材料 受 到大气 压压 迫其 纤维变得 难 以移动 而被 固定 。此 外 ,因增强 材 料 在 被树脂 浸渍 前便 达到 了接 近真 空的状 态 ,如此注 入足量 的树 脂 的话将 不会 出现浸 渍不 均 的情 况 。
真空压铸中型腔真空压力的理论计算及试验研究

铸
・
造
R Y
Ma . 0 7 r2 0
V I5 N0 3 o .6 .
28・ 5
F O
真空压铸 中型腔真空压力的理论计算
及 试 验 研 究
胡 泊 ,熊守 关 ,村 上 正幸2 本悦 豪 ,松 ,池 田伸 吾
(. 1 教育部先进 成形制造重点实验 室 ,清华大学机械 工程 系,北京 10 8 ;2 日本 东洋机械金 属株 式会社) 004 .
su id b h o e i Ic lua in a d e p r e t lme s r m e tb n t ln a u m r s u e t de y te r t ac lt n x e i na a c o m a ue n y is al g a v c u p e s r i s n o n ie a x e i n a i.Th ac lt n wa r v d c icd n t h x e i e t l e s risd n e p r me t Ide e c luai s p o e on ie twi t e e p r o h m na
c sig p o e st e pt ec vt a u m r s u eo n a p o r t v 1 a t r c s k e a i v c u p e s r n a p r p i e l e. n o h y a e
K ywo d : a u m i sig p o e sp r me e ; a u m rs u e p o s p i ia in e r s v c u de c t ; rc s a a t r v c u p e s r ; r c so t z t a n e m o
『工艺的秘密6』真空铸造(VacuumCasting)

『工艺的秘密6』真空铸造(VacuumCasting)本期要说的工艺是:真空铸造,一个专门用于手板模型制作等小批量复制的制造工艺工艺成本:加工费用(低),单件费用(中)典型产品:手板模型,电子消费品,体育设备,玩具等产量适合:适合单件定做和小批量生产质量:精确成型的产品表面,非常适合表现产品的表面细节和3D 纹理速度:根据零件尺寸决定(45分钟- 4小时/ 件)真空铸造(Vacuum Casting):专门用于制作精致手板模型和小批量复制的工艺,广泛用于注塑产品的打样预览。
真空铸造常用的塑料材料有PP和PA,成型零件的色彩选择和强度大小灵活性很高,非常适合产品设计师做产品手板定做。
设计建议1.设计过程中应考虑产品的体积(建议单片零件重量在2.5kg之内),因为在用真空铸造做产品手板时,体量越大的产品冷却收缩的比例也越大,耗时也越久2.应尽量避免尖锐的产品造型工艺过程详解前期准备:用单件成品翻制两片硅胶模(详见视频)步骤1:将事先准备好的两片硅胶模合并,放置在65°-70°的环境下,两片硅胶模接缝处开始融化直至无缝衔接步骤2:抽空硅胶模内空气,引流管倒入液体PUR,直至充满模内腔体。
冷却(45分钟-4小时)步骤3:割开两片硅胶模,取出成品,等待修边和打磨实例:用真空铸造制作显示器外壳手板模型步骤1:割开事先准备好的硅胶模步骤2:取出用于翻制硅胶模的单件成品步骤3:将两片硅胶模用胶布捆绑固定,插入引流管,抽出膜内空气,加热至少45分钟,做到两片硅胶模无缝衔接步骤4:通过引流管倒入液体PUR步骤5:等待冷却后,向橡胶模内注入空气,便于后期分离硅胶模步骤6:割开分离两片硅胶模,取出成品,等待修边和打磨相关产品。
真空压铸中型腔真空压力的理论计算及试验研究
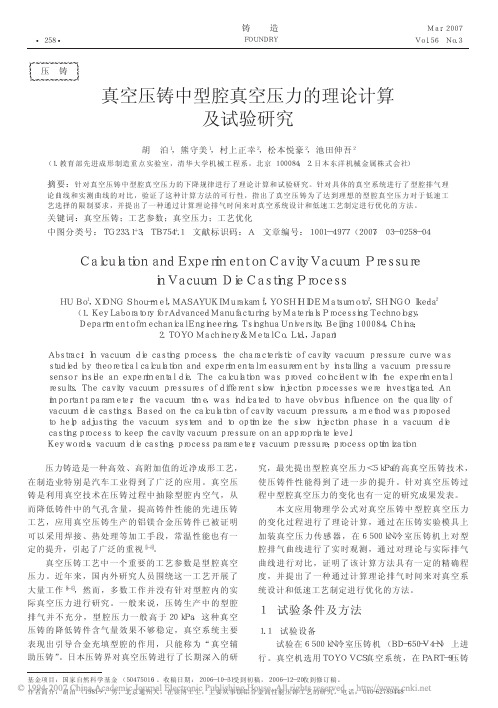
80
275
1
66.7
图4 低速射出工艺0.1 ̄0.02 m/s Fig. 4 Slow injection speed 0.1 ̄0.02 m/s
2 试验结果与分析
2.1 型腔排气过程分析 图5所示为一般真空压铸工艺所采用的排气结构。
当 冲 头 前 进 至 图 中 虚 线 所 示 位 置 时 , 压 室 — ——型 腔— ——排气通道形成一个封 闭 系 统, 如 图 中 空 白 区 域 所示。真空压铸的主要目的就是在金属液充满型腔之 前将这一封闭系统中的气体尽可能多的抽除。
1 试验条件及方法
1.1 试验设备 试验在6 500 kN冷室压铸机 ( BD-650-V4-N) 上进
行。真空机选用TOYO VCS真空系统, 在PART-9压铸
基金项目: 国家自然科学基金 ( 50475016) 。收稿日期: 2006- 10- 31受到初稿, 2006- 12- 20收到修订稿。 作者简介: 胡泊 ( 1981-) , 男, 北京通州人, 在读博士生, 主要从事镁铝合金高性能压铸工艺的研究。电话: 010-62789448
压力铸造是一种高效、高附加值的近净成形工艺, 在制造业特别是汽车工业得到了广泛的应用。真空压 铸是利用真空技术在压铸过程中抽除型腔内空气, 从 而降低铸件中的气孔含量, 提高铸件性能的先进压铸 工艺, 应用真空压铸生产的铝镁合金压铸件已被证明 可以采用焊接、热处理等加工手段, 常温性能也有一 定的提升, 引起了广泛的重视[1-3]。
压 铸 的 型 腔 压 力 处 在 101 ( 1个 大 气 压)  ̄1 kPa 区 间 ,
在真空区域的划分中属于低真空, 在本试验中真空泵
的抽速S为0.013 8 m3/s, 入口压强P为0.67 Pa, 管 道 直
日本的压铸机械
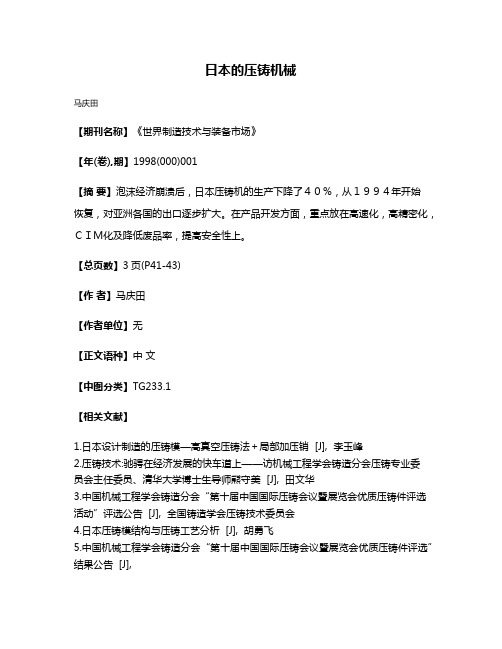
日本的压铸机械
马庆田
【期刊名称】《世界制造技术与装备市场》
【年(卷),期】1998(000)001
【摘要】泡沫经济崩溃后,日本压铸机的生产下降了40%,从1994年开始
恢复,对亚洲各国的出口逐步扩大。
在产品开发方面,重点放在高速化,高精密化,CIM化及降低废品率,提高安全性上。
【总页数】3页(P41-43)
【作者】马庆田
【作者单位】无
【正文语种】中文
【中图分类】TG233.1
【相关文献】
1.日本设计制造的压铸模—高真空压铸法+局部加压销 [J], 李玉峰
2.压铸技术:驰骋在经济发展的快车道上——访机械工程学会铸造分会压铸专业委
员会主任委员、清华大学博士生导师熊守美 [J], 田文华
3.中国机械工程学会铸造分会“第十届中国国际压铸会议暨展览会优质压铸件评选活动”评选公告 [J], 全国铸造学会压铸技术委员会
4.日本压铸模结构与压铸工艺分析 [J], 胡勇飞
5.中国机械工程学会铸造分会“第十届中国国际压铸会议暨展览会优质压铸件评选”结果公告 [J],
因版权原因,仅展示原文概要,查看原文内容请购买。
高真空铸造技术在发动机缸体生产中的运用

高真空铸造技术在发动机缸体生产中的运用摘要:高真空铸造技术由高真空设备与高真空模具组合而成,高真空模具用于形成密闭型腔,高真空设备用于将密闭型腔内的气体抽出,使型腔内达到较高的真空度。
采用高真空铸造技术生产缸体,可有效的减少型腔内的气体,从而减少铸造过程中卷气的发生,进一步降低工件内部的有害气孔,提高工件品质。
关键词:高真空铸造;发动机缸体;高真空模具;真空压铸发动机缸体属于汽车动力总成中关键核心零件,具有结构形状复杂、壁厚不均且精度要求高的特点,其材质一般为铸铁或者铝合金,因铝合金具有强度高、重量低、易加工等优点,本田直列系列发动机缸体材料大多为铝合金材质。
铝合金材质缸体通常采用压铸工艺进行生产,随着发动机的不断进化,其形状越来越复杂,壁厚越来越薄,生产难度加大,显然现有生产工艺难以满足日益苛刻的品质、效率以及成本的要求。
自2018年以来,东风本田汽车有限公司动力总成新工厂建设为了实现从“制”造到“质”造的飞跃,决定引进日本本田的高真空压铸生产技术。
从调研考察,再结合自身实际情况,制定出新技术的导入方案,整个过程严格按照本田的评价流程进行,确保各个阶段的目标均有效的达成,最终确保新技术导入后稳定生产。
1高真空设备1.1 高真空设备功能可以根据压射曲线或压射装置位移来精准控制真空通道的开启与关闭,能实时监测压力、并进行数据存储、追溯查询以及可根据不同的压铸工艺进行参数设置调整。
1.2 高真空设备组成真空泵采用罗茨真空泵,其极限真空度可达0.02kPa_abs,真空罐容积为1000L,抽真空结束后60s内真空罐内的真空度值可回到0.5kPa_abs以下,满足一个压铸循环时间。
真空阀组用于控制抽真空、型腔与大气相连以及吹气动作,其功能通过电磁阀动作来进行切换,其响应时间在70ms以内。
①抽真空时,真空阀组切换至与真空罐相连,对型腔进行抽真空;②抽真空完成后,为了使工件能正常脱模,型腔内压力需恢复至大气压,此时真空阀组切换至与大气相连;③为防止异物夹杂使真空阀密闭不严,从而导致铝液进入真空管道,下次铸造循环开始前真空阀组切换至与压缩空气相连,可对附着在真空阀上的毛刺等异物进行反向吹气。
- 1、下载文档前请自行甄别文档内容的完整性,平台不提供额外的编辑、内容补充、找答案等附加服务。
- 2、"仅部分预览"的文档,不可在线预览部分如存在完整性等问题,可反馈申请退款(可完整预览的文档不适用该条件!)。
- 3、如文档侵犯您的权益,请联系客服反馈,我们会尽快为您处理(人工客服工作时间:9:00-18:30)。
真空压铸产品的高品质化技术
株式会社ダイエンジニアリング○逢坂裕義
森川巖
王黎
Technology for qualitative improvement of vacuum die casting manufactures
Die Engineering Corporation○Hiroyoshi Osaka
Iwao Morikawa
Li Wang
Abstract:
By utilizing vacuum die casting, our corporation had taken measures against a lot of defects. Through their measures, we have thought that adiabatic compression of gas on the eve of filling finish has a major effect on quality: in case of the adiabatic compression on the product’s surface and inside the product, the soldering defects and the porosity defects occur respectively. We have thought that the quality can improve provided three sorts of gases are reduced: there is the gas within die, occurred by die lubricant and occurred by plunger lubricant.
摘要
本公司利用真空压铸技术,进行了多种应对不良的对策试验。
在众多的对策中,我们发现产品品质受充填结束前的气体断热压缩影响非常大,例如,产品表面发生断热压缩将导致粘模的产生;产品内部发生断热压缩将导致气孔的产生。
我们将气体的种类分为三种,分别为模具内部产生的气体,润滑剂产生的气体和冲头部润滑剂所产生的气体。
如果减少这三种气体含量,将会有效地改善产品品质。
为了分析这三种气体,我们进行了下列试制。
1)制造了数据测定用的模具,并进行了试制。
2)制造一型六件的模具,使用热室锌合金压铸机进行试制。
3)制造了超薄产品的模具,使用冷室铝合金压铸机进行试制。
试制报告:
1.数据测定用模具的试制报告
1-1模具规格
1)在模具上部安装吸引用,排气槽断面积为0.38c㎡的真空阀。
2)在模具反方向操作底部安装真空度测定用,排气槽断面积为0.2c㎡的真空阀。
铸造方案规格图
附铸造方案图片
3)铸造方案有效的提高了材料的使用率。
1-2真空度的测定-1
合模后,使冲头冲向分流子端面的同时,测定各部位的真空度。
1)在各部位的真空吸引结束后,用线图将同一真空度描绘出来。
2)真空泵的过滤器部与吸引用真空阀的垂直顶部的真空吸引时间发生0.01~0.02秒的延迟。
3)真空泵的过滤器部与模腔部的真空吸引时间发生0.03~0.04秒的延迟。
4)在真空吸引开始0.4秒后,模腔部的真空度进入定状态。
1-3真空度测定-2
测定连续铸造时的各部位的真空度。
1)真空吸引开始前,各部位的真空度缓慢上升。
2)真空泵的过滤器处与真空阀的垂直顶部的真空吸引时间发生0.02~0.03秒的延迟。
3)真空泵的过滤器部与模腔部的真空吸引时间发生0.04~0.5秒的延迟。
1-4产品的气体含量测定数据-1
通过变换真空度,测定产品的气体含量。
1)A-1为真空吸引度在-50kpa时的产品的气体含量。
气体含量少。
2)A-2为真空吸引度在-70kpa时的产品的气体含量。
气体含量少。
3)A-3为真空吸引度在-90kpa时的产品的气体含量。
气体含量少。
(润滑剂为压射用润滑剂)
1-5 产品的气体含量测定数据-2
采用清洁式真空压铸,通过改变真空度,测定产品的气体含量。
1)B-1为真空吸引度在-50kpa时的产品的气
体含量。
气体含量非常少。
2)B-2为真空吸引度在-70kpa时的产品的气
体含量。
气体含量非常少。
3)B-3为真空吸引度在-90kpa时的产品的气
体含量。
气体含量非常少。
(润滑剂为压射用润滑剂)
1-6 产品的气体含量测定数据-3
向套筒内滴入 1.8g的水溶性润滑剂,通过改变真空度,测定产品的气体含量。
1)C-1为真空吸引度在
-50kpa时的产品的气
体含量。
气体含量非常多。
2)C-2为真空吸引度在-70kpa时的产品的气
体含量。
气体含量非常多。
3)C-3为真空吸引度在-90kpa时的产品的气
体含量。
气体含量非常多。
(润滑剂为水溶性润滑剂)
1-7 产品的气体含量测定数据—4 通过改变模具温度,测量产品的气体含量。
1)D-1与D-2是真空吸引度在-90kpa时的产品的气体含量,气体含量都很少。
模具温度较高的D-1的气体含量较D-2少。
(润滑剂为压射用润滑剂)
D-1模具温度
D-2模具温度
辅助说明
1)冲头处使用的润滑剂为東垣産業株式会社生产的压射用润滑剂。
这是一种气体含量非常少的润滑剂。
2)清洁式真空铸造方法的说明。
1-8 归纳总结
1)提高真空泵的真空度将降低产品的气体含量。
2)采用清洁式真空铸造可以减少产品的气体含量。
3)向套筒内滴入润滑剂后,产品的气体含量增多。
在CH4及CO2的含量增多的同时产生了CO,C2H4及C2H6等气体。
4)提升模具温度后,产品的气体含量减少。
2.热室锌合金压铸机的试制报告。
铸造厂商 株式会社シンコーテック
地址 新潟県糸魚川市大字能生1408 技术支援 YS企画
地址 新潟県三条市北入蔵2-29-10
试制报告
A
2-1 模具规格
1)因为是一型六件,因此产品之间的间距设计地较窄。
2)使用六个滑块控制冷却水,将合模前的模具温度设置在120~140度之间。
3)调整动模的温度。
铸造方案规格图
附铸造方案照片
4)铸造方案有效的提高了材料的使用率。
5)真空吸引时间与冷室压铸机不同。
2-2归纳总结
1)由于套筒及冲头处无润滑剂,因此利用真空压铸技术可以做到产品高质量化。
2)虽然定模温度没有问题,但是动模温度偏低,因此调整了模温。
由于套筒及冲头处无润滑剂,因此利用真空压铸技术可以做到产品高品质化。
3)六个滑块的冷却水水压为4.5kg/c㎡、通水时间需保持在0.1~0.2秒之间。
4)S 型喷嘴处有间隙会导致产品品质低下,真空阀堵塞发生。
3.冷室铝合金压铸机的试制报告。
铸造厂商 NIIGATA DIECAST 地址 新潟県燕市輿野8-11 技术支援 YS-PLAN
地址 新潟県三条市北入蔵2-29-10
试制报告A
3-1 模具规格
1)为了生产厚度为1.2mm的超薄产品,调节了模温。
2)在侧浇口处,控制金属液的流动。
3) 产品中央部的六个肋条与外部的形状相连接,是非常难生产的产品。
铸造方案规格图
附铸造方案图
2)铸件投影面积为大模具面积。
3)除特别需将铸造压力设低之外,一般使用常用压铸条件。
3-2归纳总结
1)将模具温度调至140度以上。
2)最小化涂抹润滑剂的量。
3)一般的真空压铸无法对外观品质进行改善,因此采用了清洁式真空压铸。
这是一种通过使用压缩空气改善产品品质的方法,我们期待通过使用气体氮可以更好的改善产品的品质。
4.试制总结
1)由于模具内部气体受到断热压缩的影响,导致产品的内部外部品质低下。
2)由润滑剂产生的气体在金属液热量的作用下在其凝结点凝结,导致产品表面品质低下。
产生的气体含量多,会导致产品内部的品质也变得较为低下。
3)冲头部润滑剂产生的气体在金属液热量的作用下在其凝结点凝结,导致产品内部产生破断的激冷层。
5.成果
通过此次试制,我公司成功申报了三个专利。
1与真空压铸相关的2件
2与模具冷却装置相关的1件
6.致谢本次试制得到了SHINCOTEC、NIIGATA DIECAST、YS-PLAN、MARUMO ELECTRIC CO., LTD及TOKOH SANAGYO., LTD等公司的大力协助。
在此,对各公司的协助表示深深地谢意。
-所有试制品均在我公司展台展出-。