切割过程建模及刀具磨损仿真
在切削过程中建模与仿真刀具的磨损
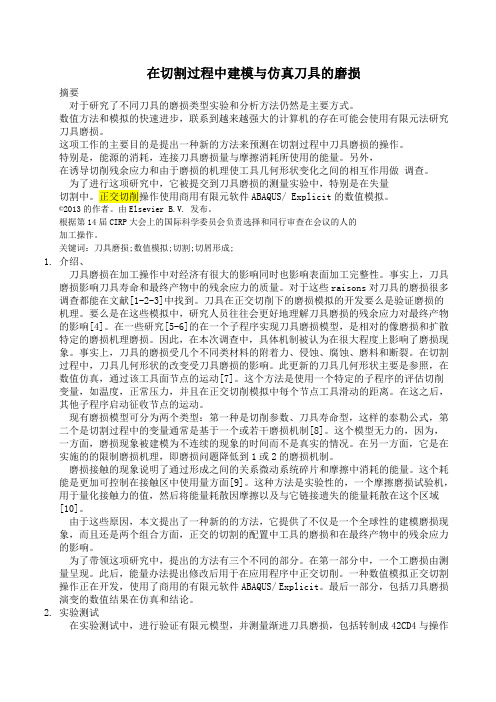
在切割过程中建模与仿真刀具的磨损摘要对于研究了不同刀具的磨损类型实验和分析方法仍然是主要方式。
数值方法和模拟的快速进步,联系到越来越强大的计算机的存在可能会使用有限元法研究刀具磨损。
这项工作的主要目的是提出一种新的方法来预测在切割过程中刀具磨损的操作。
特别是,能源的消耗,连接刀具磨损量与摩擦消耗所使用的能量。
另外,在诱导切削残余应力和由于磨损的机理使工具几何形状变化之间的相互作用做调查。
为了进行这项研究中,它被提交到刀具磨损的测量实验中,特别是在失量切割中。
正交切削操作使用商用有限元软件ABAQUS/ Explicit的数值模拟。
©2013的作者。
由Elsevier B.V. 发布。
根据第14届CIRP大会上的国际科学委员会负责选择和同行审查在会议的人的加工操作。
关键词:刀具磨损;数值模拟;切割;切屑形成;1.介绍、刀具磨损在加工操作中对经济有很大的影响同时也影响表面加工完整性。
事实上,刀具磨损影响刀具寿命和最终产物中的残余应力的质量。
对于这些raisons对刀具的磨损很多调查都能在文献[1-2-3]中找到。
刀具在正交切削下的磨损模拟的开发要么是验证磨损的机理。
要么是在这些模拟中,研究人员往往会更好地理解刀具磨损的残余应力对最终产物的影响[4]。
在一些研究[5-6]的在一个子程序实现刀具磨损模型,是相对的像磨损和扩散特定的磨损机理磨损。
因此,在本次调查中,具体机制被认为在很大程度上影响了磨损现象。
事实上,刀具的磨损受几个不同类材料的附着力、侵蚀、腐蚀、磨料和断裂。
在切割过程中,刀具几何形状的改变受刀具磨损的影响。
此更新的刀具几何形状主要是参照,在数值仿真,通过该工具面节点的运动[7]。
这个方法是使用一个特定的子程序的评估切削变量,如温度,正常压力,并且在正交切削模拟中每个节点工具滑动的距离。
在这之后,其他子程序启动征收节点的运动。
现有磨损模型可分为两个类型:第一种是切削参数、刀具寿命型,这样的泰勒公式,第二个是切割过程中的变量通常是基于一个或若干磨损机制[8]。
钛合金TC4高速切削刀具磨损的有限元仿真_陈燕

式中:G为材料常数;V为相对滑移速度。
1.2 粘结磨损
切削钛合金时,由于钛合金的亲和力大而使
摩擦表面的接触点容易相互粘结,在相对运动
下,带走刀具材料从而造成粘结磨损,而且刀-屑
接 触 长 度 小 , 导 致 接 触 面 间 的 压 应 力 达 到 GPa
级,超过了工件材料的屈服极限,因此,切削钛
合金时其粘结磨损非常严重。针对粘结磨损,国
引用格式:Chen Y, Yang S B, Fu Y C, et al. FEM estimation of tool wear in high speed cutting of Ti6Al4V alloy. Acta Aeronautica et Astronautica Sinica, 2013, 34(x): xxx-xxx. 陈燕,杨树宝,傅玉灿,等.钛合金 TC4 高速切削刀具磨损的有限元仿真.航空学报, 2013, 34(x): xxx-xxx.
A
exp
⎛ ⎜⎝
−B T
⎞ ⎟⎠
(3)
式中: dWa 为滑移 dL 距离后的磨损量;而 σt 为刀 屑接触面上的正应力;A及B均为材料常数。方程
两边同除以磨损时间 dt ,则方程变为:
陈燕等:钛合金 TC4 高速切削刀具磨损的有限元仿真
3
dWa dt
=
Aσ
t
V
exp
⎛ ⎜⎝
−B T
⎞ ⎟⎠
(4)
由公式(4)可以看出,单位时间内的磨损量与
敛的特点,计算中使用网格重画的功能解决工件
变 形 严 重 的 问 题 。 钛 合 金 TC4 工 件 尺 寸 为
16×8mm,刀具与工件均设定为弹塑性体。工件
切削过程刀具磨损状态决策模型构建

切削过程刀具磨损状态决策模型构建下载提示:该文档是本店铺精心编制而成的,希望大家下载后,能够帮助大家解决实际问题。
文档下载后可定制修改,请根据实际需要进行调整和使用,谢谢!本店铺为大家提供各种类型的实用资料,如教育随笔、日记赏析、句子摘抄、古诗大全、经典美文、话题作文、工作总结、词语解析、文案摘录、其他资料等等,想了解不同资料格式和写法,敬请关注!Download tips: This document is carefully compiled by this editor. I hope that after you download it, it can help you solve practical problems. The document can be customized and modified after downloading, please adjust and use it according to actual needs, thank you! In addition, this shop provides you with various types of practical materials, such as educational essays, diary appreciation, sentence excerpts, ancient poems, classic articles, topic composition, work summary, word parsing, copy excerpts, other materials and so on, want to know different data formats and writing methods, please pay attention!随着传统制造业的发展,切削加工技术在各个领域得到了广泛的应用。
三维金属切削过程刀具磨损的有限元模拟仿真
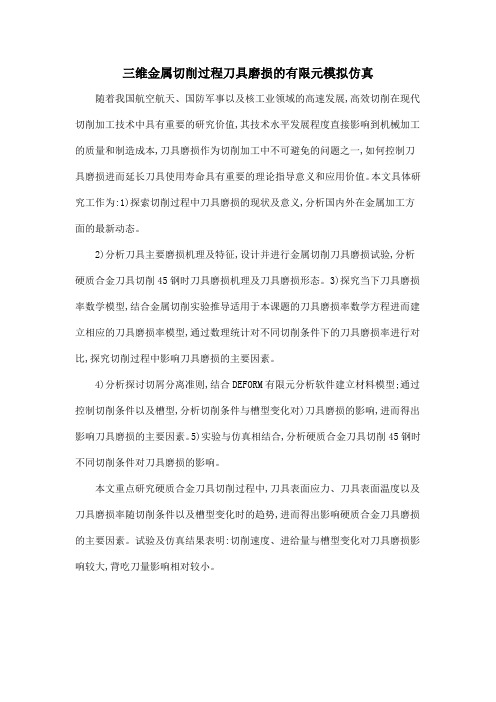
三维金属切削过程刀具磨损的有限元模拟仿真随着我国航空航天、国防军事以及核工业领域的高速发展,高效切削在现代切削加工技术中具有重要的研究价值,其技术水平发展程度直接影响到机械加工的质量和制造成本,刀具磨损作为切削加工中不可避免的问题之一,如何控制刀具磨损进而延长刀具使用寿命具有重要的理论指导意义和应用价值。
本文具体研究工作为:1)探索切削过程中刀具磨损的现状及意义,分析国内外在金属加工方面的最新动态。
2)分析刀具主要磨损机理及特征,设计并进行金属切削刀具磨损试验,分析硬质合金刀具切削45钢时刀具磨损机理及刀具磨损形态。
3)探究当下刀具磨损率数学模型,结合金属切削实验推导适用于本课题的刀具磨损率数学方程进而建立相应的刀具磨损率模型,通过数理统计对不同切削条件下的刀具磨损率进行对比,探究切削过程中影响刀具磨损的主要因素。
4)分析探讨切屑分离准则,结合DEFORM有限元分析软件建立材料模型;通过控制切削条件以及槽型,分析切削条件与槽型变化对)刀具磨损的影响,进而得出影响刀具磨损的主要因素。
5)实验与仿真相结合,分析硬质合金刀具切削45钢时不同切削条件对刀具磨损的影响。
本文重点研究硬质合金刀具切削过程中,刀具表面应力、刀具表面温度以及刀具磨损率随切削条件以及槽型变化时的趋势,进而得出影响硬质合金刀具磨损的主要因素。
试验及仿真结果表明:切削速度、进给量与槽型变化对刀具磨损影响较大,背吃刀量影响相对较小。
金属难加工材料切削及刀具磨损虚拟仿真报告(一)
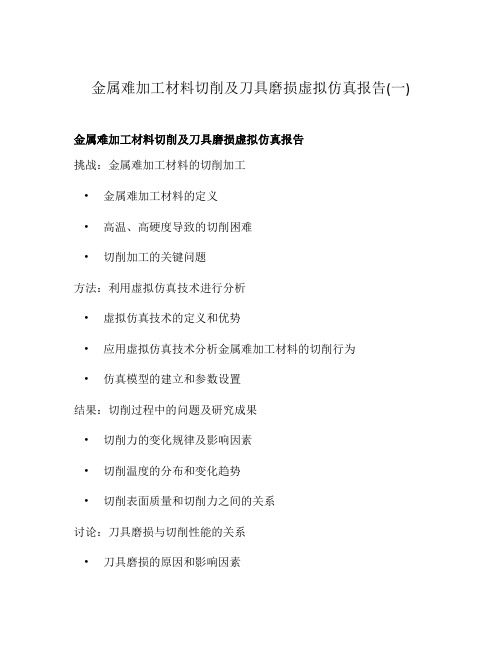
金属难加工材料切削及刀具磨损虚拟仿真报告(一)金属难加工材料切削及刀具磨损虚拟仿真报告挑战:金属难加工材料的切削加工•金属难加工材料的定义•高温、高硬度导致的切削困难•切削加工的关键问题方法:利用虚拟仿真技术进行分析•虚拟仿真技术的定义和优势•应用虚拟仿真技术分析金属难加工材料的切削行为•仿真模型的建立和参数设置结果:切削过程中的问题及研究成果•切削力的变化规律及影响因素•切削温度的分布和变化趋势•切削表面质量和切削力之间的关系讨论:刀具磨损与切削性能的关系•刀具磨损的原因和影响因素•切削力和刀具磨损的关系•如何通过优化切削参数延缓刀具磨损总结:虚拟仿真技术在切削加工中的应用前景•虚拟仿真技术的优势和局限性•未来发展方向和研究重点•为实际切削加工提供参考和决策依据金属难加工材料切削及刀具磨损虚拟仿真报告挑战:金属难加工材料的切削加工•金属难加工材料的定义–金属难加工材料是指具有高硬度、高强度和高耐磨性的金属材料,如钛合金、高速钢等。
•高温、高硬度导致的切削困难–由于金属难加工材料的硬度较高,切削时需要更大的切削力。
–高温会导致材料软化和脆性增加,使刀具损耗加剧。
•切削加工的关键问题–如何降低切削力和温度,提高切削效率和加工质量。
方法:利用虚拟仿真技术进行分析•虚拟仿真技术的定义和优势–虚拟仿真技术利用计算机模拟真实物理过程,可以减少实验成本、提高研究效率。
–通过虚拟仿真可以提前预测切削加工过程中的各种参数和结果。
•应用虚拟仿真技术分析金属难加工材料的切削行为–通过建立切削仿真模型,可以模拟金属难加工材料在切削过程中的变形、热力分布等行为。
–利用仿真结果可以分析切削力、切削温度和切削表面质量等参数的变化趋势。
•仿真模型的建立和参数设置–建立金属难加工材料的切削仿真模型。
–设置切削参数,如切削速度、进给速度和切削用量。
–调整模型和参数以获得准确的仿真结果。
结果:切削过程中的问题及研究成果•切削力的变化规律及影响因素–切削力随着切削速度的增加而增加,随着进给速度的增加先增加后减小。
磨损问题的仿真求解研究
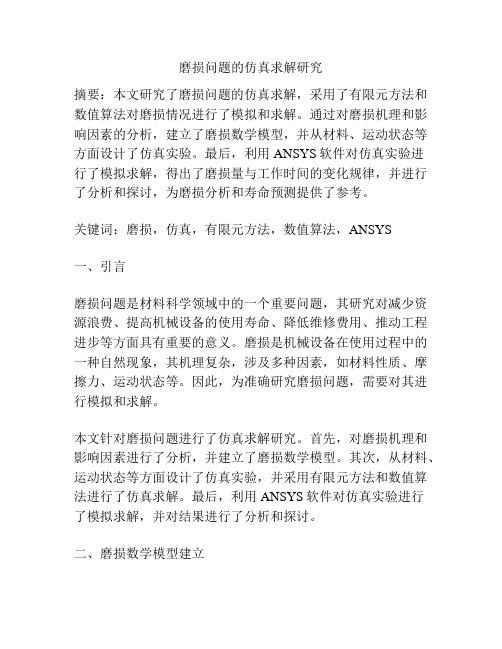
磨损问题的仿真求解研究摘要:本文研究了磨损问题的仿真求解,采用了有限元方法和数值算法对磨损情况进行了模拟和求解。
通过对磨损机理和影响因素的分析,建立了磨损数学模型,并从材料、运动状态等方面设计了仿真实验。
最后,利用ANSYS软件对仿真实验进行了模拟求解,得出了磨损量与工作时间的变化规律,并进行了分析和探讨,为磨损分析和寿命预测提供了参考。
关键词:磨损,仿真,有限元方法,数值算法,ANSYS一、引言磨损问题是材料科学领域中的一个重要问题,其研究对减少资源浪费、提高机械设备的使用寿命、降低维修费用、推动工程进步等方面具有重要的意义。
磨损是机械设备在使用过程中的一种自然现象,其机理复杂,涉及多种因素,如材料性质、摩擦力、运动状态等。
因此,为准确研究磨损问题,需要对其进行模拟和求解。
本文针对磨损问题进行了仿真求解研究。
首先,对磨损机理和影响因素进行了分析,并建立了磨损数学模型。
其次,从材料、运动状态等方面设计了仿真实验,并采用有限元方法和数值算法进行了仿真求解。
最后,利用ANSYS软件对仿真实验进行了模拟求解,并对结果进行了分析和探讨。
二、磨损数学模型建立磨损数学模型是研究磨损问题的重要基础。
在建立磨损数学模型时,需要考虑材料性质、运动状态、受力情况等多种因素。
本文基于磨损机理和影响因素的分析,建立了如下的磨损数学模型:$$W = kHd$$其中,$W$表示磨损量,$H$表示受力情况,$d$表示工作时间,$k$为比例系数。
该数学模型考虑了磨损与受力情况、工作时间、材料性质等因素的关系。
其中,受力情况是决定磨损量的重要因素,其受力情况的大小和方向都会对磨损量产生影响。
三、仿真实验设计为了验证磨损数学模型的有效性,本文利用有限元方法和数值算法对磨损情况进行了模拟和求解。
具体的仿真实验设计如下:1. 材料选择:本文选择了工程塑料作为材料,其具有良好的韧性和抗磨损性能。
2. 运动状态:本文采用了滑动摩擦运动状态,其运动状态为水平滑动,速度恒定,摩擦力为定值。
磨齿机的刀具加工与磨齿过程的仿真模拟
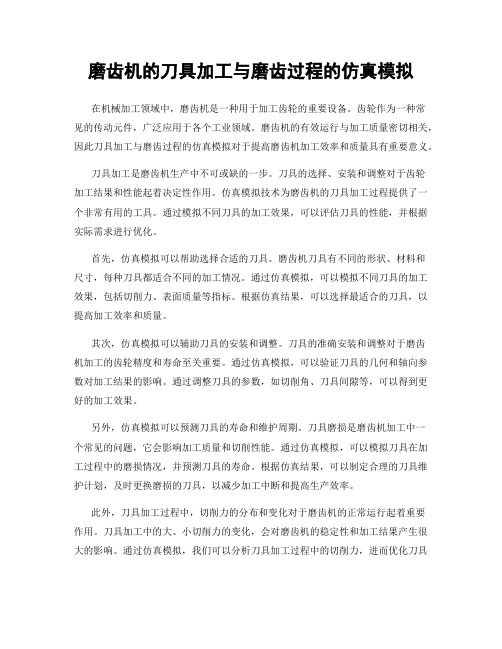
磨齿机的刀具加工与磨齿过程的仿真模拟在机械加工领域中,磨齿机是一种用于加工齿轮的重要设备。
齿轮作为一种常见的传动元件,广泛应用于各个工业领域。
磨齿机的有效运行与加工质量密切相关,因此刀具加工与磨齿过程的仿真模拟对于提高磨齿机加工效率和质量具有重要意义。
刀具加工是磨齿机生产中不可或缺的一步。
刀具的选择、安装和调整对于齿轮加工结果和性能起着决定性作用。
仿真模拟技术为磨齿机的刀具加工过程提供了一个非常有用的工具。
通过模拟不同刀具的加工效果,可以评估刀具的性能,并根据实际需求进行优化。
首先,仿真模拟可以帮助选择合适的刀具。
磨齿机刀具有不同的形状、材料和尺寸,每种刀具都适合不同的加工情况。
通过仿真模拟,可以模拟不同刀具的加工效果,包括切削力、表面质量等指标。
根据仿真结果,可以选择最适合的刀具,以提高加工效率和质量。
其次,仿真模拟可以辅助刀具的安装和调整。
刀具的准确安装和调整对于磨齿机加工的齿轮精度和寿命至关重要。
通过仿真模拟,可以验证刀具的几何和轴向参数对加工结果的影响。
通过调整刀具的参数,如切削角、刀具间隙等,可以得到更好的加工效果。
另外,仿真模拟可以预测刀具的寿命和维护周期。
刀具磨损是磨齿机加工中一个常见的问题,它会影响加工质量和切削性能。
通过仿真模拟,可以模拟刀具在加工过程中的磨损情况,并预测刀具的寿命。
根据仿真结果,可以制定合理的刀具维护计划,及时更换磨损的刀具,以减少加工中断和提高生产效率。
此外,刀具加工过程中,切削力的分布和变化对于磨齿机的正常运行起着重要作用。
刀具加工中的大、小切削力的变化,会对磨齿机的稳定性和加工结果产生很大的影响。
通过仿真模拟,我们可以分析刀具加工过程中的切削力,进而优化刀具的设计和加工参数。
通过减小切削力的变化范围,可以提高磨齿机的稳定性和加工质量。
最后,仿真模拟可以预测磨齿过程中的加工精度。
齿轮加工的质量要求通常很高,例如齿形误差、齿距误差等。
通过仿真模拟,可以预测磨齿过程中的加工精度,并找到影响加工精度的关键因素。
金属难加工材料切削及刀具磨损虚拟仿真报告

金属难加工材料切削及刀具磨损虚拟仿真报告金属难加工材料切削及刀具磨损虚拟仿真报告1. 简介•金属难加工材料指那些具有高硬度、高强度和高耐磨性等特征的金属材料,如高速钢、硬质合金、陶瓷等。
•金属材料的难加工性严重影响了加工效率和质量,而切削及刀具磨损虚拟仿真技术可用于解决这一问题。
2. 金属难加工材料的特点•高硬度:金属难加工材料具有极高的硬度,使得切削时刀具与工件之间的摩擦和剪切力增大。
•高强度:金属难加工材料具有较高的抗拉强度和屈服强度,增加了切削时材料的塑性变形阻力。
•高耐磨性:金属难加工材料的表面具有较高的硬度和耐磨性,导致切削加工时刀具易受磨损。
3. 切削及刀具磨损虚拟仿真技术•切削仿真:通过建立切削过程的数值模型,仿真分析切削力、温度分布、变形等参数,为切削参数的选定提供指导。
•刀具磨损仿真:基于刀具磨损的机理,模拟切削过程中刀具表面的磨损情况,预测刀具寿命并优化刀具设计。
4. 仿真结果与应用•通过切削仿真,可以优化切削参数,减小切削力和温度,提高切削效率和加工质量。
•通过刀具磨损仿真,可以预测刀具寿命,合理安排刀具更换周期,降低生产成本。
•仿真结果可应用于金属难加工材料的切削加工过程优化和刀具寿命管理等领域。
5. 总结•切削及刀具磨损虚拟仿真技术为金属难加工材料的切削加工提供了新的解决方案。
•仿真结果可为制造企业提供更科学、高效的切削方案和刀具磨损管理策略。
•进一步研究和应用虚拟仿真技术可以不断优化金属难加工材料的切削加工过程,提高生产效率和质量。
6. 下一步研究方向•开发更精准的金属难加工材料的切削仿真模型,提高仿真结果的准确性。
•结合材料力学和热力学等理论,深入研究金属难加工材料的切削机理。
•发展更高效的刀具磨损仿真算法,准确预测刀具寿命。
•研究切削仿真与实际切削加工过程的关联,进一步验证仿真结果的可靠性。
7. 实际应用与展望•虚拟仿真技术在金属难加工材料的切削加工领域具有广泛的应用前景。
刀具磨损与寿命预测的建模与仿真研究

刀具磨损与寿命预测的建模与仿真研究刀具在机械加工过程中起着至关重要的作用,而刀具的磨损与寿命预测则成为提高加工质量和效率的关键。
本文将探讨刀具磨损与寿命预测的建模与仿真研究。
1. 引言随着制造业的高速发展,对于刀具的精度和耐久性的要求越来越高。
刀具的磨损与寿命预测对于优化加工过程、提高生产效率具有重要意义。
通过建模与仿真,我们可以预测刀具的磨损程度和失效时间,进而实现及时更换和维护,提高加工效率和质量。
2. 刀具磨损建模刀具磨损是刀具与工件接触摩擦过程中的渐进性损伤。
磨损过程可以通过建模来描述。
传统的刀具磨损建模通常基于试验数据,如冲击试验、磨损试验等。
然而,试验方法受到成本、时间和实验条件的限制。
因此,基于仿真的刀具磨损建模成为一种有效的研究手段。
3. 刀具寿命预测建模刀具寿命预测是指根据刀具使用过程中的工艺参数和刀具状态信息来估计刀具的寿命。
刀具寿命预测的主要挑战是准确地识别刀具寿命的衰减规律。
传统方法中常采用统计学模型和经验公式进行刀具寿命预测,但这些方法受限于数据样本的局限性和通用性。
因此,建立基于仿真的刀具寿命预测模型成为一种可行的方法。
4. 基于仿真的刀具磨损与寿命预测基于仿真的刀具磨损与寿命预测是利用计算机模拟技术,模拟刀具在工件上的接触与磨损过程。
该方法可以基于刀具材料的损伤力学性质、工件材料的硬度和加工参数等因素进行建模。
通过仿真模拟,可以得到刀具磨损程度和寿命衰减的数据,进而预测刀具的失效时间。
5. 仿真参数的选择与优化在进行刀具磨损和寿命预测的仿真中,选择合适的参数和优化模型是关键。
参数的选择包括切削速度、进给速度、切削深度等,而优化模型则可以采用遗传算法、粒子群优化等方法。
通过合理选择参数和优化模型,可以更准确地模拟刀具磨损和寿命预测过程。
6. 刀具磨损与寿命预测的实例研究为了验证基于仿真的刀具磨损与寿命预测方法的有效性,我们进行了一些实例研究。
通过采集实际加工数据,并运用建模与仿真技术,我们成功预测了不同刀具在不同加工条件下的磨损程度和寿命。
在切削过程中建模与仿真刀具的磨损
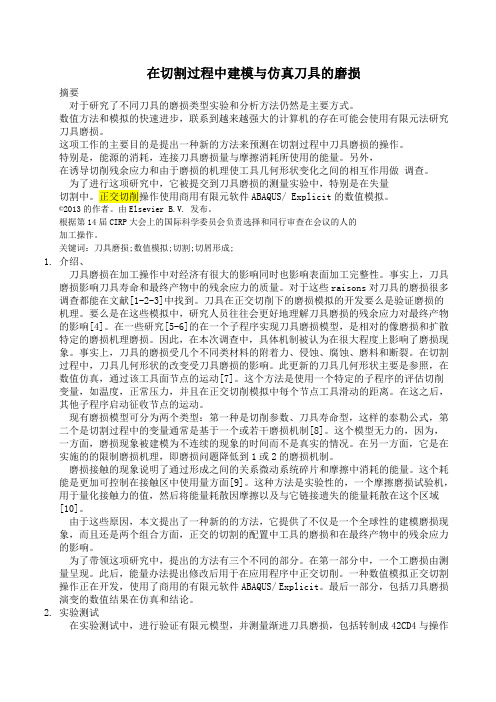
在切割过程中建模与仿真刀具的磨损摘要对于研究了不同刀具的磨损类型实验和分析方法仍然是主要方式。
数值方法和模拟的快速进步,联系到越来越强大的计算机的存在可能会使用有限元法研究刀具磨损。
这项工作的主要目的是提出一种新的方法来预测在切割过程中刀具磨损的操作。
特别是,能源的消耗,连接刀具磨损量与摩擦消耗所使用的能量。
另外,在诱导切削残余应力和由于磨损的机理使工具几何形状变化之间的相互作用做调查。
为了进行这项研究中,它被提交到刀具磨损的测量实验中,特别是在失量切割中。
正交切削操作使用商用有限元软件ABAQUS/ Explicit的数值模拟。
©2013的作者。
由Elsevier B.V. 发布。
根据第14届CIRP大会上的国际科学委员会负责选择和同行审查在会议的人的加工操作。
关键词:刀具磨损;数值模拟;切割;切屑形成;1.介绍、刀具磨损在加工操作中对经济有很大的影响同时也影响表面加工完整性。
事实上,刀具磨损影响刀具寿命和最终产物中的残余应力的质量。
对于这些raisons对刀具的磨损很多调查都能在文献[1-2-3]中找到。
刀具在正交切削下的磨损模拟的开发要么是验证磨损的机理。
要么是在这些模拟中,研究人员往往会更好地理解刀具磨损的残余应力对最终产物的影响[4]。
在一些研究[5-6]的在一个子程序实现刀具磨损模型,是相对的像磨损和扩散特定的磨损机理磨损。
因此,在本次调查中,具体机制被认为在很大程度上影响了磨损现象。
事实上,刀具的磨损受几个不同类材料的附着力、侵蚀、腐蚀、磨料和断裂。
在切割过程中,刀具几何形状的改变受刀具磨损的影响。
此更新的刀具几何形状主要是参照,在数值仿真,通过该工具面节点的运动[7]。
这个方法是使用一个特定的子程序的评估切削变量,如温度,正常压力,并且在正交切削模拟中每个节点工具滑动的距离。
在这之后,其他子程序启动征收节点的运动。
现有磨损模型可分为两个类型:第一种是切削参数、刀具寿命型,这样的泰勒公式,第二个是切割过程中的变量通常是基于一个或若干磨损机制[8]。
ABAQUS切削仿真步骤
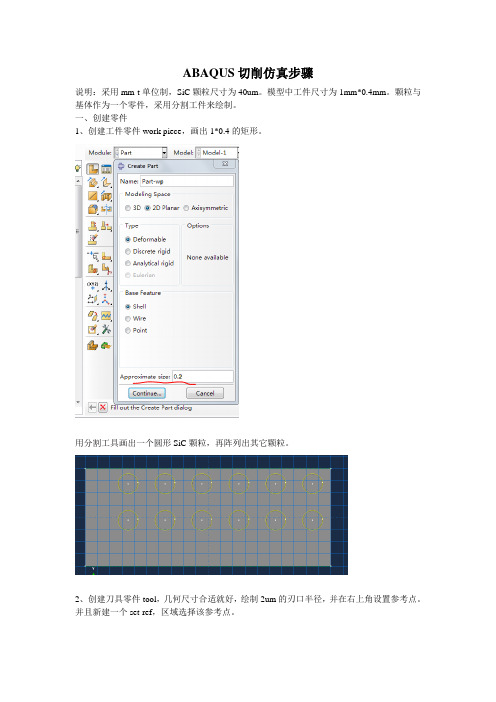
ABAQUS切削仿真步骤说明:采用mm-t单位制,SiC颗粒尺寸为40um。
模型中工件尺寸为1mm*0.4mm。
颗粒与基体作为一个零件,采用分割工件来绘制。
一、创建零件1、创建工件零件work piece,画出1*0.4的矩形。
用分割工具画出一个圆形SiC颗粒,再阵列出其它颗粒。
2、创建刀具零件tool,几何尺寸合适就好,绘制2um的刃口半径,并在右上角设置参考点。
并且新建一个set-ref,区域选择该参考点。
二、材料参数设置及赋值Al采用shear damage,断裂应变1.2,损伤演化中的displacement at failure填4*10-6。
三、装配依次调入刀具和工件零件,为避免干涉,将刀具向右下方移动一定的距离,其中向下移动的距离为切削深度。
四、定义分析步和输出1、新建分析步,选择分析步类型为“Dynamic, Temp-disp, Explicit”,时间长度为工件长度除以切削速度。
本模型刀具速度为125mm/s,工件长度为1mm,故时间长度为0.008s。
2、修改场输出变量。
时间间隔改为80,并勾选status3、新建历程输出变量,区域选择为刀具零件中的set-ref,并且勾选RT、RF、RM,该点即作为刀具切削力的输出点。
五、定义接触属性和接触1、新建接触属性,接受Contact为默认选择。
切向属性选择罚函数,摩擦系数选0.25。
法向属性接受默认选项。
2、定义接触对。
接触类型选择surface-to-surface Contact(Explicit),主面选择刀具的前刀面、后刀面和刀尖的圆弧,从面类型选择node region,把整个工件全部选中。
力学约束公式选Penalty contact method,划移公式选择Finite sliding,接触属性选择上步定义的属性,其它保持默认。
3、定义刀具零件刚性约束。
(定义刀具为刚体就是说刀具的在切削过程中变形很小,所以认为是刚体,在刚体的参考点上可以看刀具在切削过程的反力)。
开题报告-基于ABAQUS的切削过程刀具磨损仿真
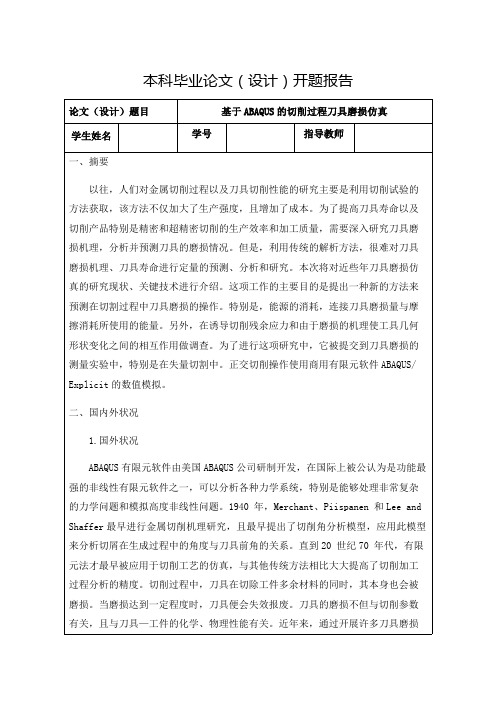
的预测工作,使用 Deform2D 有限元软件,模拟了切削 AISI1045 钢时硬质合金刀 具的磨损情况,结果表明:以粘结磨损为机理建立的 Usui 模型能够较好地预测刀 具的磨损,但是刀具寿命预测值(后刀面磨损 VB)较试验值要低。分析认为,其 仿真模型中工件被设定为刚塑性体,这就忽略了材料回弹对后刀面磨损的影响, 导致后刀面与工件几乎没有接触,从而造成后刀面磨损计算值与试验值的差别较 大。如果后角稍大则后刀面几乎不存在磨损,这与实际刀具磨损规律不符。
①调研,查阅有关文献资料,清楚切削过程,并学习 ABAQUS 软件; ②根据切削过程和特点,分析切削过程有限元仿真模型的难点; ③在 ABAQUS 仿真软件中建立切削过程模型; ④进行切削过程仿真; ⑤对切削过程中刀具受力情况进行分析; ⑥根据主要任务详细安排论文进度。 五、论文提纲 第 1 章 摘要 第 2 章 金属切削理论和刀具磨损理论
2.国内状况
现有磨损模型可分为两个类型:第一种是切削参数、刀具寿命型,这样的泰 勒公式,第二个是切割过程中的变量通常是基于一个或若干磨损机制。这个模型 无力的,因为,一方面,磨损现象被建模为不连续的现象的时间而不是真实的情 况。在另一方面,它是在实施的的限制磨损机理,即磨损问题降低到 1 或 2 的磨 损机制。 磨损接触的现象说明了通过形成之间的关系微动系统碎片和摩擦中消 耗的能量。这个耗能是更加可控制在接触区中使用量方面。这种方法是实验性 的,一个摩擦磨损试验机,用于量化接触力的值,然后将能量耗散因摩擦以及与 它链接遗失的能量耗散在这个区域。随着计算机技术的迅速发展,有限元在工程 分析中的作用已从分析、校核扩展到优化设计并和计算机辅助设计技术相结合 正在逐步达到其性能的最佳化状态。21 世纪以来,随着计算机等技术的进一步发
支持向量机刀具磨损预测模型及MATLAB仿真

基金项目:国家支撑计划项目(2006BAF01A27)收稿日期:2009年1月支持向量机刀具磨损预测模型及MAT LAB 仿真叶蔚,王时龙,雷松重庆大学摘要:针对刀具使用时加工参数多变的实际情况,提出使用最小二乘支持向量机(LS -S VM )建立模型并对刀具磨损进行预测:首先引入最小二乘支持向量机建立刀具磨损模型,然后针对具体实验数据,采用交叉验证的办法,选取优化的核参数。
实验和仿真结果表明:该模型可以有效地学习刀具磨损中的非线性关系,刀具磨损的预测精度较高。
因此该模型可以用作对实际加工中的刀具磨损进行有效预测,并为切削参数的实际选择提供依据。
关键词:刀具磨损;向量机模型;M AT LAB 仿真中图分类号:TG 701 文献标志码:APredicting Model of Cutting Tool Wear B ased on Least Squares SupportV ector Machine and MAT LAB SimulationY e Wei ,Wang Shilong ,Lei S ongAbstract :With the variable parameter appearing in the using of tool ,the m odel built by least squares support vector ma 2chines (LS -S VM )method is provided to predicting tool wear.Firstly ,LS -S VM was introduced to m odel the wearing of tool.Aiming at the specific sam ple ,the method of cross validation is used to choose the proper kernel function parameters.Results of simulations and experiments showed that the LS -S VM m odel based on radial basis function kernel (R BF )could effectively learn the non 2linear relationship in tool wear.This method could obtain higher prediction accuracy.As a result ,the m odel could effec 2tively predict tool wear and provide theoretical basis for the selection of machining parameters in the actual processing.K eyw ords :cutting tool wear ;S VM m odel ;M AT LAB simulation 1 引言在切削加工中,刀具寿命是一个重要的参数,它直接影响到刀具需求计划制定、刀具成本核算、生产效率和加工成本。
超高强度钢切削仿真和刀具磨损率建模研究
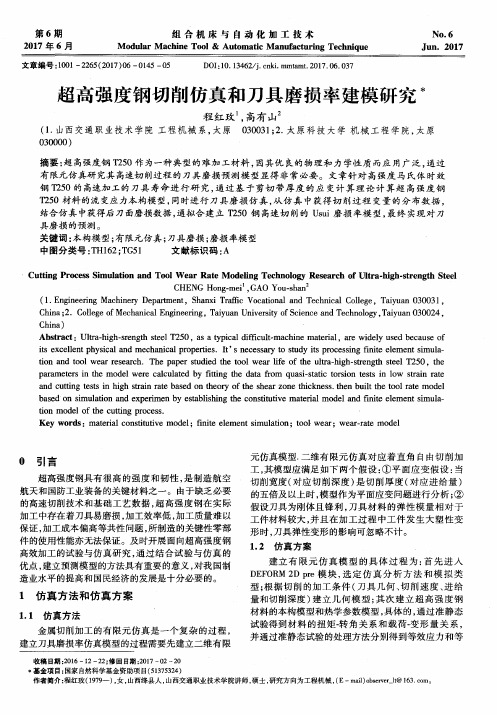
第 6期
2 0 1 7年 6月
组 合 机 床 与 自 动 化 加 工 技 术
Mo du l a r M ac h i ne To o l& A u t o ma t i c Ma n u f a c t ur i ng Te c h ni q u e
NO. 6
J u n .2 0 1 7
文章编号 : 1 0 0 1 — 2 2 6 5 ( 2 0 1 7 ) 0 6—0 1 4 5— 0 5
D O I : 1 0 . 1 3 4 6 2 / j . c n k i . mm t a mt . 2 0 1 7 . 0 6 . 0 3 7
超高强度钢切 削仿真和 刀具磨损率建模研究 术
C h i n a )
Ab s t r a c t :Ul t r a - h i g h - s r e n g t h s t e e l T 2 5 0,a s a t y p i c a l d i f ic f u l t — ma c h i n e ma t e r i a l ,a r e wi d e l y u s e d b e c a u s e o f i t s e x c e l l e nt p h y s i c a l a n d me c h ni a c a l p r o p e r t i e s .I t ’ S n e c e s s a r y t o s t u d y i t s p r o c e s s i n g in f i t e e l e me n t s i mu l a — t i o n nd a t o o l we r a r e s e rc a h . Th e p a p e r s t u d i e d t he t o o l we a r l i f e o f he t ul t r a — h i g h- s re t n g h t s t e e l T2 5 0,t he p ra a me t e r s i n he t mo d e l we r e c a l c u l a t e d b y it f i t n g he t d a t a f r o m q u a s i — s t a i t c t o r s i o n t e s t s i n l o w s ra t i n r a t e nd a c u t in t g t e s t s i n h i g h s t r a i n r a t e b a s e d o n he t o r y o f t h e s h e a r z o n e hi t c k ne s s . he t n b u i l t he t t o o l r a t e mo de l b a s e d o n s i mu l a io t n a n d e x p e im e f n b y e s t a b l i s in h g he t c o ns i t ut t iv e ma t e r i a l mo d e l nd a in f it e e l e me n t s i mu l a — t i o n mo d e l o f t h e c u t i t n g p r o c e s s . Ke y wo r d s:m a t e r i a 1 c o n s i t ut t i v e mo d e 1 ;f in i t e e l e me n t s i mu l a i t o n;t o o l  ̄ we r ;we a r. a r a t e mo d e l
旋转刀具切削过程的数值模拟与分析

旋转刀具切削过程的数值模拟与分析数值模拟与分析在加工制造领域中扮演着重要的角色。
通过使用数值模拟方法,我们可以更好地理解切削过程中刀具与工件之间的相互作用,以及材料的去除行为。
本文将针对旋转刀具切削过程进行数值模拟与分析,并探讨其在加工制造领域中的应用。
首先,为了对旋转切削过程进行数值模拟,我们需要选择合适的数值模拟软件。
常用的数值模拟软件包括ANSYS、COMSOL、ABAQUS等。
这些软件通常基于有限元理论,能够对复杂的切削过程进行模拟,并提供详细的结果分析。
在进行数值模拟之前,我们需要收集切削过程所需的输入信息。
这些信息包括刀具的几何参数、材料特性、切削力、切削速度等。
其中,刀具几何参数是非常重要的,它们是定义切削过程中切削区域的形状和尺寸的关键因素。
切削力和切削速度则直接影响到切削过程的效果和质量。
接下来,利用数值模拟软件,我们可以建立旋转刀具切削过程的有限元模型。
有限元模型的精度和合理性对于模拟结果的准确性起着至关重要的作用。
我们需要将刀具几何形状、切削区域、工件和切削力等因素考虑进去,以便获得更真实的模拟结果。
在建立有限元模型后,我们可以通过运行数值模拟软件来模拟旋转刀具切削过程。
模拟过程中,软件会根据输入的参数和初始条件,计算切削区域的应力、变形、剩余应力以及材料去除量等重要数据。
通过这些数据,我们能够了解切削过程中刀具的受力状况,工件的破坏机制,以及切削过程中产生的热效应。
一旦数值模拟完成,我们可以通过结果分析来深入了解切削过程。
结果分析包括对切削力、切削温度、刀具磨损等因素的评估。
这些结果对于优化切削过程、改进刀具设计以及预测切削寿命等方面具有重要意义。
除了数值模拟和结果分析外,还有一些其他的方法可以用于旋转刀具切削过程的分析。
例如,实验测试可以通过刀具磨损、切削力和表面质量等指标来对切削过程进行评估。
机器学习方法可以利用已有数据来建立预测模型,帮助提高切削过程的效率和精度。
总结来说,旋转刀具切削过程的数值模拟与分析对于加工制造领域具有重要意义。
仿真模拟方法在金属切削刀具性能评估中的应用研究

仿真模拟方法在金属切削刀具性能评估中的应用研究随着工业化进程的加速和现代制造技术的不断发展,金属切削加工作为一种高效且广泛应用的制造方法,对刀具的性能要求也越来越高。
为了提高刀具的使用寿命、减少生产成本和改善加工质量,金属切削刀具性能的评估成为了制造业中的重要课题。
传统的试验方法需要投入大量的时间和金钱,并且无法实时获取数据,因此,仿真模拟方法应运而生,为金属切削刀具性能评估提供了新的途径。
仿真模拟方法是指使用计算机模型和数值算法来模拟真实系统的行为,并通过解算方程组得到系统的性能指标。
在金属切削刀具性能评估中的应用,主要通过建立刀具与工件的相互作用模型,进行切削过程的模拟,从而得到刀具的磨损、温度分布、工件表面质量等关键性能指标。
首先,仿真模拟方法在金属切削刀具磨损评估中起到重要作用。
磨损是刀具寿命的关键因素之一。
传统试验方法需要大量的时间和成本,而且无法对刀具的不同工况进行评估。
而仿真模拟方法可以基于有效的切削力和切削温度模型,快速准确地预测刀具的磨损情况。
通过对刀具不同使用寿命下磨损的模拟计算,可以得到刀具的寿命曲线,为刀具的选择和更换提供了科学依据。
其次,仿真模拟方法可以用于预测刀具与工件之间的接触表面温度分布。
在金属切削加工中,切削区温度的分布非常重要,直接影响切削过程中刀具的热膨胀、热应力和热变形等。
传统试验难以实时测量和监测切削过程中的温度变化。
而仿真模拟方法通过建立热传导模型和流体力学模型,可以准确地预测切削区的温度分布。
这将有助于优化切削参数,提高加工质量和刀具的使用寿命。
最后,仿真模拟方法还可以用于评估金属切削加工过程中工件表面的质量。
工件表面的质量是加工过程中的重要指标之一,直接影响到工件的使用性能。
传统试验方法需要等到加工完成后才能进行表面质量的测试,而且测试结果难以快速获取和应用于下一步的工艺优化。
而仿真模拟方法可以通过建立表面形貌模型,预测加工过程中的表面质量。
这将有助于实时监控和调整加工过程,提高加工效率和产品质量。
CNC机床加工中的刀具磨损监测与模型
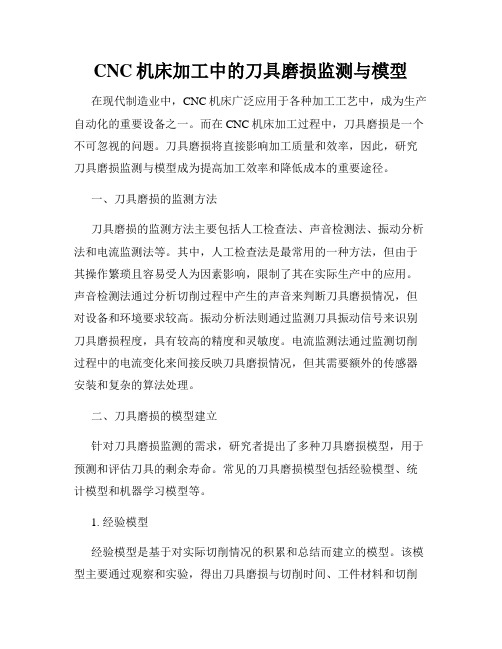
CNC机床加工中的刀具磨损监测与模型在现代制造业中,CNC机床广泛应用于各种加工工艺中,成为生产自动化的重要设备之一。
而在CNC机床加工过程中,刀具磨损是一个不可忽视的问题。
刀具磨损将直接影响加工质量和效率,因此,研究刀具磨损监测与模型成为提高加工效率和降低成本的重要途径。
一、刀具磨损的监测方法刀具磨损的监测方法主要包括人工检查法、声音检测法、振动分析法和电流监测法等。
其中,人工检查法是最常用的一种方法,但由于其操作繁琐且容易受人为因素影响,限制了其在实际生产中的应用。
声音检测法通过分析切削过程中产生的声音来判断刀具磨损情况,但对设备和环境要求较高。
振动分析法则通过监测刀具振动信号来识别刀具磨损程度,具有较高的精度和灵敏度。
电流监测法通过监测切削过程中的电流变化来间接反映刀具磨损情况,但其需要额外的传感器安装和复杂的算法处理。
二、刀具磨损的模型建立针对刀具磨损监测的需求,研究者提出了多种刀具磨损模型,用于预测和评估刀具的剩余寿命。
常见的刀具磨损模型包括经验模型、统计模型和机器学习模型等。
1. 经验模型经验模型是基于对实际切削情况的积累和总结而建立的模型。
该模型主要通过观察和实验,得出刀具磨损与切削时间、工件材料和切削参数等因素之间的经验关系。
尽管经验模型具有一定的实用性,但其局限性在于无法适应不同材料、切削情况和工艺变化等复杂情况。
2. 统计模型统计模型主要通过对大量切削数据的统计分析,建立刀具磨损与各因素之间的统计关系。
通过建立统计模型,我们可以对刀具的寿命进行统计预测,提前进行刀具更换和维护,从而避免生产过程中的突发故障和停机损失。
3. 机器学习模型机器学习模型是近年来发展较快的一种方法。
它基于大量的数据样本和算法模型,通过自动学习和优化来建立刀具磨损与各种因素之间的复杂关系。
机器学习模型具有较高的预测准确性和泛化能力,能够适应不同类型的切削过程和磨损情况。
三、刀具磨损监测与模型的应用刀具磨损监测与模型已经在实际生产中得到了广泛应用。
- 1、下载文档前请自行甄别文档内容的完整性,平台不提供额外的编辑、内容补充、找答案等附加服务。
- 2、"仅部分预览"的文档,不可在线预览部分如存在完整性等问题,可反馈申请退款(可完整预览的文档不适用该条件!)。
- 3、如文档侵犯您的权益,请联系客服反馈,我们会尽快为您处理(人工客服工作时间:9:00-18:30)。
2 0 1 6年 1 2月
长 春 工 业 大 学 学 报
J o u r n a l o f Ch a n g c h u n Un i v e r s i t y o f Te c h n o l o g y
V 01 . 37 No . 6
统碎 片 和摩 擦 中消耗 的 能量 _ 6 ] 。这 个 耗 能 可 控 制在 接触 区 中使用 量 方 面[ 8 ] 。因 此 , 文 中通 过 对
工 工 件 的质 量 , 同时提 高 了加 工效 率 。
加 工 系统 刀具进 给 轨迹决 定 了刀具 和 工件 之
收 稿 日期 : 2 0 1 6 — 0 5 2 5 基金项 目: 福 建 省 自然 科 学 基 金 项 目资 助 ( 2 0 1 5 J 0 1 2 1 5 ) ;福 建 省 中青 年 教 师 教 育 科 研 项 目( J AT1 6 0 6 9 2 ) ;集 美 大 学 诚 毅 学 院 青 年 科研基金科技类项 目( C 1 6 0 0 1 ) 作 者 简 介 :李 红 ( 1 9 8 1 一) , 女, 汉族 , 辽 宁 沈 阳人 , 集美大学诚毅学院讲师 , 硕 士, 主要从事先 进制造技术 ( 精 密 和 特 种 加 工 理 论 与 技术 ) 方 向研 究 , E — ma i l : ws wh q k @1 6 3 . c o n. r
2 . Sc h o o l o f Me c h a n i c a l En g i n e e r i n g,J i me i Un i v e r s i t y ,Xi a me n 3 6 1 0 2 1,Ch i n a )
Ab s t r ac t :I n c u t t i ng t o o l s y s t e m c o o r di na t i on d ur i n g t he c ut t i ng pr o c e s s, bo t h t h e t o ol ge ome t r y mo de l a nd c o nt a c t mod e l a r e bu i l t .Nume r i c a l s i mu l a t i o n f or t h e c u t t i n g p r o c e s s a n d t o ol we a r i s g i v e n
LI Ho n g , W ANG Da z he n , YE Xi a n z h e n
( 1 . De p a r t me n t o f Me c h a n i c a l En g i n e e r i n g,Ch e n g y i Un i v e r s i t y Co l l e g e,J i me i Un i v e r s i t y,Xi a me n 3 61 0 2 1,Ch i n a
1 刀具 加 工 系 统
在 传统 孔加 工 技 术 的基 础 上 , 让 刀 具 和 工件 相 对位 置 之 间 存 在 固 定 方 向上 的 规 律 性 高 频 振 动, 目的是 使孔 加 工 过 程 中速 度 和 深 度 以及进 给 量 都 能够有 规 律地 控 制 , 能够 在 很 大 程 度 上 减少
文 章编 号 :1 6 7 4 — 1 3 7 4 ( 2 0 1 6 ) 0 6 — 0 5 4 0 — 0 4
Cu t t i n g p r o c e s s mo d el i n g a n d t o o l we ar s i mu l a t i o n
切 削力 和加 工 中产 生 的温 度 , 更 为 有 效 地 控 制加
人员 更好 地理 解 刀具磨 损 的残余 应力 对最 终产 物
的影 响[ 4 - 5 ] 。
加工 过程 时 , 刀 具 和 工 件 接 触 的过 程 以及 磨
损接 触 的现象 说 明 了通 过形 成之 间 的关 系微动 系
De c .2 O1 6
DOI : 1 0 . 1 5 9 2 3 / j . c n k i . c n 2 2 — 1 3 8 2 / t . 2 0 1 6 . 6 . 0 5
切 割 过 程 建 模 及 刀 具 磨 损 仿 真
李 红 , 王 大镇 , 叶衔 真
( 1 . 集 美 大 学 诚 毅 学 院 机 械 工 程 系 ,福 建 厦 f - 1 3 6 1 0 2 1 ;2 . 集 美 大 学 机 械 工 程 学 院 ,福 建 厦 门 3 6 1 0 2 1 )
摘 要 :在 切 割过程 中的刀具 加工 系 统 坐标 系建 立 了工件 几 何模 型 和 接 触模 型 , 进 行 了切 割 过 程 以及 刀具 磨损 的仿真研 究 。 关键 词 :刀具磨 损 ;数值 模 拟 ;切 割 ;切屑 形成
中 图分类 号 :TH 1 6 4
文献 标 志码 : A
切 割过 程 中刀具和工 件 的摩 擦 作用 问题 进行 建模
仿 真研究 , 分 析 了刀具 在切 割 时 的磨 损 变化情 况 。
切割 作用 下 实 验 零 件 的 加 工 成 型 】 _ 3 _ 。对 于 这 些
刀具 的磨 损 已经 开 展 了很 多 调 查 , 这 有 助 于 研 究
he r e .
Key wo r d s:t o ol we a r ;n um e r i c a l s i mul a t i on;c u t t i ng;c h i p f o r ma t i o n .
0 引 言
机械 加工 过 程 离 不 开切 削 加 工 , 即在 刀 具 的