配料车控制系统程序设计
配料称重自动控制系统怎么调

配料称重自动控制系统怎么调1. 简介配料称重自动控制系统是一种通过电子秤和控制器实现对配料称重的自动化控制系统。
它可以广泛应用于食品、化工、医药等行业,提高生产效率和产品质量。
在使用配料称重自动控制系统之前,需要对系统进行调试和调整,以确保系统能够正常工作并提供准确的称重结果。
本文将介绍如何对配料称重自动控制系统进行调整。
2. 系统调整前的准备工作在进行系统调整之前,需要进行以下准备工作:•确保所有设备和传感器的连接正确并稳定,包括电子秤和控制器之间的连接。
•检查系统的电源供应是否正常,确保电源电压和频率符合要求。
•确保控制器的参数已经正确设置,包括称重范围、精度要求等。
3. 系统调整步骤步骤一:调整零点和秤量补偿1.连接电子秤和控制器,并打开系统电源。
2.设置称重范围,确保称重范围适合当前的称重任务。
3.将电子秤置为空载状态,即没有物料放置在上面。
4.进入控制器的零点和秤量补偿调整模式。
5.按照控制器的操作指南,根据实际情况进行调整。
6.调整零点时,确保电子秤显示为零。
7.调整秤量补偿时,将已知质量的物料放置在电子秤上,并确保电子秤的显示与实际质量相符。
步骤二:校准称重精度1.取一定数量的已知质量物料,如标准砝码。
2.将已知质量物料放置在电子秤上,并记录下称重结果。
3.比较电子秤的称重结果与已知质量物料的真实质量,计算出误差。
4.根据误差结果,进入控制器的校准模式,根据实际情况进行调整。
5.调整校准参数时,根据误差结果逐步调整,直到达到所要求的精度。
步骤三:调整称重速度1.根据生产工艺要求,确认所需的称重速度。
2.进入控制器的速度调整模式。
3.根据实际情况调整控制器的参数,包括传输速度和称重响应速度。
4.通过实际测试和调整,确保控制器能够在要求的时间范围内完成称重任务。
步骤四:系统稳定性测试1.将一定数量的实际物料进行称重测试。
2.运行测试过程中,观察系统的稳定性和准确性。
3.根据实际情况,进行必要的调整和优化。
PLD800混凝土配料机设计说明书

摘要随着当今世界经济快速发展,人们对建筑行业提出了更高的要求。
以前仅靠工作人员的实践经验,对混凝泥土进行配料,从效率、质量、节约等方面已经无法满足建筑行业的发展。
建筑行业向机械化、自动化、智能化发展是二十一世纪的一大目标。
决定混凝土质量与效率的关键在于制造混泥土初期的配料精度,由此我们可知建筑行业拥有机械化、自动化的混凝土配料机尤为重要。
我设计的课题是PLD系列混凝土配料机。
凝土配料机是一种与搅拌机配套使用的前台自动配料装置。
它可以根据用户设计的混凝土配比自动完成砂、石、水泥等3~6种物料的配料程序。
混凝土配料机是由给料系统、称量系统以及电气系统组成。
在本设计中详细的设计了给料系统及其各部件,并对现存的各种称料系统进行了论述和比较。
给料系统是配料机的重要组成部分,它能够把各种骨料输送至称料料斗中,以备称量,进行配料。
称量系统是配料机中主要组成部分,它决定着各种骨料配料的精度。
建筑机械的自动化大大解放了劳动生产力,减轻了工人的体力劳动,也为高速发展的房地产业,公路建设等等做出了贡献。
本设计首先配料机进行了总体设计,再而详细的设计了料斗、给料机及电动机的选择,比较了不同称量方式的称量系统,还有机架的设计。
关键词:PLD系列配料机;给料机;称量系统;配料。
ABSTRACTWith economic development rapidly of the world, people have put a higher requirements forwart construction industry. Concerning about batching efficiency, quality and conservation, it has been unable to meet the development of the construction by staffs`experience only. What is a major goal of the Construction industry is that to be mechannization, automation, intelligent in twenty-first century. The mixed initial accuracy determine concrete quality and efficiency of manufacturing,.So we know that the construction industry become to mechanization, automation, the concrete batching machine is especially important.This design issue is the PLD series concrete batching machine. Concrete batching machine is a front for use as sand, automatic dosing device. It can be designed according to the user automatically match the concrete sand, stone, cement and other materials from 3 to 6 ingredients procedures. Concrete batching machine is component with feeding system, weighing system and electrical system components. It detailed design the feeding system and its components, and all the existing material systems that are discussed and compared In this design. Feeding system is an important part of batching machine, it can bring a variety of aggregate delivered to said feed hopper, ready for weighing, for ingredients. Weigh batching machine system is the main component, which determines the precision of the various aggregate ingredients. Construction machinery automation greatly liberated the labor productivity, reduce worker's manual, also contribute to the rapid development of real estate, road construction.The design of batching machine include the overall design firstly, then detailed design of the hopper, feeder and motor selection, and further compare different weighing system, and also the rough frame design.Keywords: PLD series batching machine; feeding system ; weighing system; batching.前言当今世界已经入智能化时代,现代建设机械是智能化的产物。
自动配料控制系统的设计
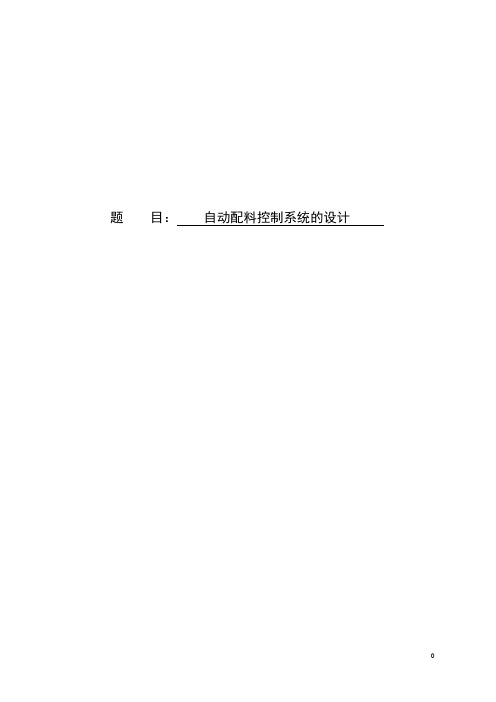
题目:自动配料控制系统的设计内容摘要自动配料系统是一种在线测量动态计量系统,集输送、计量、配料、定量等功能于一体,在冶金、建材、化工、饲料加工等行业中得到广泛应用。
设计开发自动配料优化控制系统,对于改善劳动条件、提高产品质量和生产效率具有十分重要的现实意义。
本文首先对自动配料系统的应用背景、发展趋势进行了综述,针对当前配料生产企业工艺水平相对落后、自动化水平低、生产效率低等不足,设计了一个自动配料优化控制系统,系统能够工作在全自动、远程手动以及本地手动三种模式下。
在硬件设计上,采用工控机与PLC相结合的总体控制结构,由工控制机实现系统的管理和远程监控,PLC完成设备级的动作控制及相关信号的处理,通过以太网及RS-485总线实现系统的联接与通信;改进了配料车定位系统,利用设计的定位盒实现位置编码方案,提高了定位精度。
在软件设计上,设计开发了画面实时监控和数据库管理(SCADA)等上位机应用软件,能够保存产品配方、料仓数据、实时数据等,并能够实现历史数据查询、报表打印、实时数据及状态显示、远程控制等功能,两台上位机数掘库能够有效地保持同步。
设计了下位机PLC主控程序以及通信、配料精度控制和配料车行走子程序。
针对配料系统普遍存在的配料落差控制问题,采用了一种基于模糊自适应结合PID的复合型预测控制算法,算法将模糊自适应控制宽范围快速调节和PID精确调节的特点有机结合起来,当系统的偏差大于某一设定值时,采用结合了人的经验的模糊自适应规则控制,当系统偏差小于设定值时采用PID控制,模糊控制器的两个输入分别为系统期望值和偏差,通过不同的期望值,预测不同的空中落差,并通过仿真实验证明了该方法的有效性;针对批量生产时的工作效率问题,通过对两台配料车工作时序的认真分析,建立了系统的数学模型,并利用遗传算法进行寻优,精心设计了遗传算子,求解出了最大工作效率所需的两台配料车的最佳行走路径,解决了配料车行走路径的优化问题。
基于PLC控制的自动配料系统的研究与应用
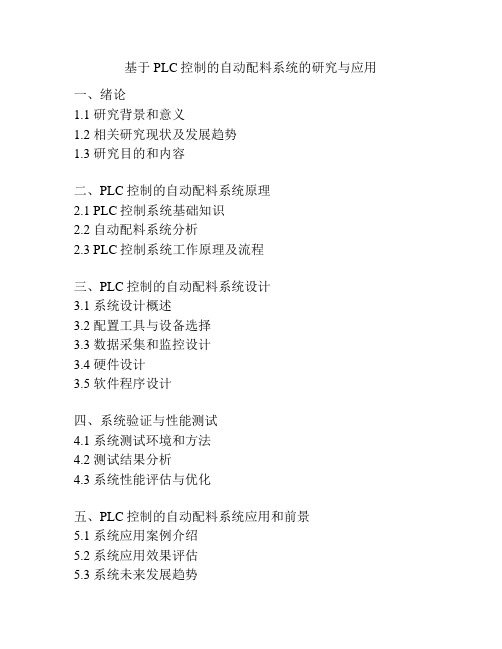
基于PLC控制的自动配料系统的研究与应用一、绪论1.1 研究背景和意义1.2 相关研究现状及发展趋势1.3 研究目的和内容二、PLC控制的自动配料系统原理2.1 PLC控制系统基础知识2.2 自动配料系统分析2.3 PLC控制系统工作原理及流程三、PLC控制的自动配料系统设计3.1 系统设计概述3.2 配置工具与设备选择3.3 数据采集和监控设计3.4 硬件设计3.5 软件程序设计四、系统验证与性能测试4.1 系统测试环境和方法4.2 测试结果分析4.3 系统性能评估与优化五、PLC控制的自动配料系统应用和前景5.1 系统应用案例介绍5.2 系统应用效果评估5.3 系统未来发展趋势六、结论6.1 研究成果总结6.2 存在问题和改进措施6.3 研究展望和意义 elucidate.一、绪论1.1 研究背景和意义随着人工智能和自动化技术的快速发展,PLC(可编程逻辑控制器)在工业自动化控制领域中的应用越来越广泛。
在生产加工过程中,配料是不可或缺的一个环节,传统的人工配料方式已经不能满足现代工业化生产的需求,最佳方式是实施自动配料系统。
PLC控制的自动配料系统可以使生产过程更加高效、准确、节约能源。
PLC是一种可编程控制器,具有高度的可编程性和灵活性。
PLC控制的自动配料系统采用传感器实时采集物料配比情况,通过PLC实时控制阀门的开关,实现自动的配料过程。
相比人工配料,PLC控制的自动配料系统具有较高的精度和效率。
1.2 相关研究现状及发展趋势自动化生产已成为智能制造的重要组成部分,PLC控制的自动配料系统也因其高效、准确、可靠等特点,广泛应用于化工、医药、食品、工业制造等领域。
自动配料系统的研究在过去几十年内得到了很大的发展,但还存在一些问题需要进一步研究。
目前,国内外很多学者和工程师致力于研究和开发PLC控制的自动配料系统。
国外现有的自动配料控制系统包括基于PLC的控制系统和SCADA(监控、控制与数据采集)系统。
PLC配料车控制系统程序设计

PLC配料车控制系统程序设计1. 简介PLC配料车控制系统程序设计是为了实现配料车在工业生产中的自动化控制而开辟的一种程序设计方案。
该方案基于PLC(可编程逻辑控制器)技术,旨在提高配料车的生产效率、减少人工操作、降低生产成本,并确保配料车的安全运行。
2. 系统架构PLC配料车控制系统由以下几个主要组件组成:- PLC控制器:负责接收输入信号、执行程序逻辑、控制输出信号。
- 传感器:用于感知配料车的位置、速度、负载等状态信息,并将其转换为电信号输入给PLC控制器。
- 执行器:包括机电、液压缸等,用于控制配料车的运动、住手、升降等动作。
- 人机界面:提供给操作员与PLC控制器进行交互的界面,如触摸屏、按钮等。
3. 功能需求PLC配料车控制系统的主要功能需求如下:- 自动运行:根据预设的配料车行进路径和速度,实现配料车的自动运行。
- 负载检测:通过传感器实时监测配料车的负载情况,确保负载在安全范围内。
- 安全住手:当配料车超出预设的运行范围或者发生异常情况时,及时住手配料车的运行,确保安全。
- 升降控制:控制液压缸实现配料车的升降功能,以适应不同高度的料仓。
- 故障诊断:通过PLC控制器对系统进行故障诊断和报警,提供故障信息和解决方案。
- 远程监控:通过网络连接,实现对配料车控制系统的远程监控和操作。
4. 程序设计流程PLC配料车控制系统程序设计的基本流程如下:- 系统需求分析:根据实际需求,明确系统的功能需求和性能要求。
- 硬件选型:选择合适的PLC控制器、传感器、执行器和人机界面设备,确保系统的稳定性和可靠性。
- 输入输出定义:根据系统需求,定义PLC控制器的输入输出点位,将传感器和执行器与PLC控制器进行连接。
- 程序逻辑设计:根据功能需求,设计PLC控制器的程序逻辑,包括运动控制、负载检测、安全住手、升降控制等功能。
- 程序编写:使用PLC编程软件,编写程序代码,实现程序逻辑的功能。
- 调试测试:将程序下载到PLC控制器中,进行系统的调试和测试,确保系统能够正常运行。
基于S7-1200的运料小车控制系统设计

本文系宜宾职业技术学院“四川省优质院校建设项目”成果基于S7-1200的运料小车控制系统设计张强(宜宾职业技术学院,四川宜宾644003)摘要:重点阐述了运料小车控制系统控制方案设计、硬件设计、程序设计及HMI 设计,采用TIA 博途全集成自动化软件平台和S7-1200控制器,实现运料小车控制系统的精确、安全和有效控制,提高了生产效率。
关键词:运料小车;S7-1200;TIA Portal ;KTP700;V200引言随着我国工业自动化水平的不断发展和提高,现代的企业工业生产分工越来越细化,流水线生产已成为企业生产环节一种重要的生产模式,运料小车在这种环境下应运而生,已成为企业生产工业运料的主要设备。
“中国制造2025”提出,现代企业生产需不断引入新技术、新工艺,突出先进制造和高端装备,工业自动化水平向着智能化、网络化和集成化方向不断升级。
本文介绍了运料小车控制系统的设计方案,采用了模块化和紧凑型设计,实现了高效性和应用性。
1控制方案设计1.1基本结构运料小车系统结构示意图如图1所示,它主要由甲料斗、乙料斗、卸料斗、清洗设备、传感器和限位开关等部分组成。
1.2控制方案1.2.1控制要求(1)实现运料小车的装料、卸料及清洗的准确控制;(2)实现运料小车多种配料方式;(3)具有手动、单周期、单步、连续、回原点等多种控制方式;(4)具有急停按钮,便于对设备进行调整、检修及紧急情况的事故处理;(5)实现对运料小车的变频调速控制;(6)利用人机界面实现对运料小车的有效监控;(7)系统软件及设备自动化集成,实现高效性和应用性;(8)系统通过PROFINET 实现高速、实时通信。
1.2.2控制系统框图控制系统框图如图2所示。
2控制系统硬件设计2.1控制器选型本系统选用CPU1214C DC /DC /DC 作为控制器。
SIMATIC S7-1200是西门子新推出的基于TIA Portal 的小型PLC ,实现了模块化和紧凑型设计,功能强大、投资安全并且完全适合各种应用;可扩展性强、灵活度高的设计,可实现最高标准工业通信的通信接口以及一整套强大的集成技术功能,已成为完整、全面的自动化解决方案的重要组成部分,是目前工业化自动控制产品PLC 的典型代表。
基于PLC的自动配料系统毕业设计(可编辑修改word版)
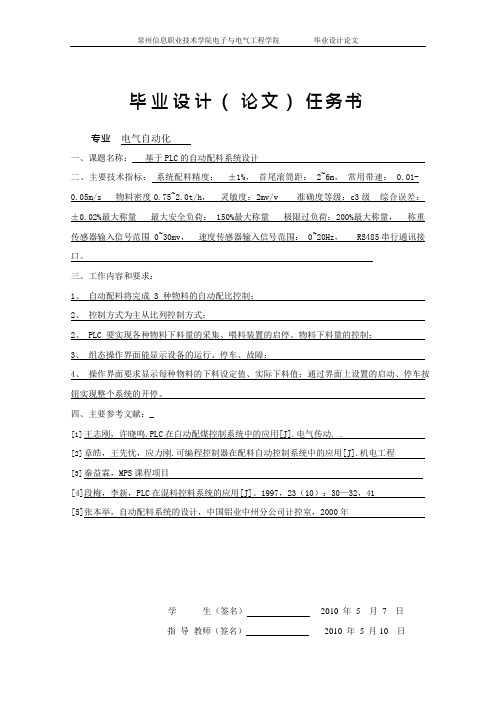
毕业设计(论文)任务书专业电气自动化一、课题名称:基于PLC 的自动配料系统设计二、主要技术指标:系统配料精度:±1%,首尾滚筒距: 2~6m,常用带速: 0.01-0.05m/s 物料密度0.75~2.0t/h,灵敏度:2mv/v 准确度等级:c3 级综合误差:±0.02%最大称量最大安全负荷: 150%最大称量极限过负荷:200%最大称量,称重传感器输入信号范围 0~30mv,速度传感器输入信号范围: 0~20Hz,RS485 串行通讯接口。
三、工作内容和要求:1、自动配料将完成 3 种物料的自动配比控制;2、控制方式为主从比列控制方式;2、 PLC 要实现各种物料下料量的采集、喂料装置的启停、物料下料量的控制;3、组态操作界面能显示设备的运行、停车、故障;4、操作界面要求显示每种物料的下料设定值、实际下料值;通过界面上设置的启动、停车按钮实现整个系统的开停。
四、主要参考文献:_[1]王志刚,许晓鸣.PLC 在白动配煤控制系统中的应用[J].电气传动. .[2]章皓,王先忧,应力刚.可编程控制器在配料自动控制系统中的应用[J].机电工程[3]秦益霖,MPS 课程项目[4]段梅,李新,PLC 在混料控料系统的应用[J]。
1997,23(10):30—32,41[5]张本举,自动配料系统的设计,中国铝业中州分公司计控室,2000 年学生(签名)2010 年 5 月7 日指导教师(签名)2010 年 5 月10 日教研室主任(签名)2010 年 5 月10 日系主任(签名)2010 年 5 月12 日毕业设计(论文)开题报告基于 PLC 的自动配料系统设计目录摘要Abstract第1 章课题来源背景 (1)1.1.1 课题来源……………………………………………………………………1.1.2 研究的目的和意义…………………………………………………………1.2 设计任务与总体方案的确定……………………………………………….1.2.1 设计任务………………………………………………………………………1.2.2 总体设计方案的确定...............................................................第2 章PLC 概述 (1)2.1PLC 的发展历史 (3)2.2PLC 的硬件和软件 (4)2.3 PLC 的通讯联网……………………………………………………………2.4 PLC 的注意事项.....................................................................第3 章配料系统简介 .. (5)3.1自动配料系统的特点及优点 (6)3.2自动配料系统的组成 (8)3.3配料技术的最新进展 (11)第4 章自动配料系统设计 (14)4.1称重方式选择 (14)4.2给料方式选择 ................................................................................................. 15.4.3生产线结构 (16)4.4 配料系统的组成……………….………………………..…………………... 4.5 输送装置的设计………………………………..……………………………..4.6 计量系统的设计........................................................................第5 章控制系统的硬件设计 (19)5.1 PLC 的选配 (19)5.2 S7—200 的特征 (20)5.3 S7—200 的主要组成部件 (23)第6 章系统的软硬件设计 (30)第7 章系统的监控组态 (43)第8 章结束语 (58)参考文献摘要本课题为自动配料自动控制系统的研制。
PLC课程设计配料车控制系统程序设计
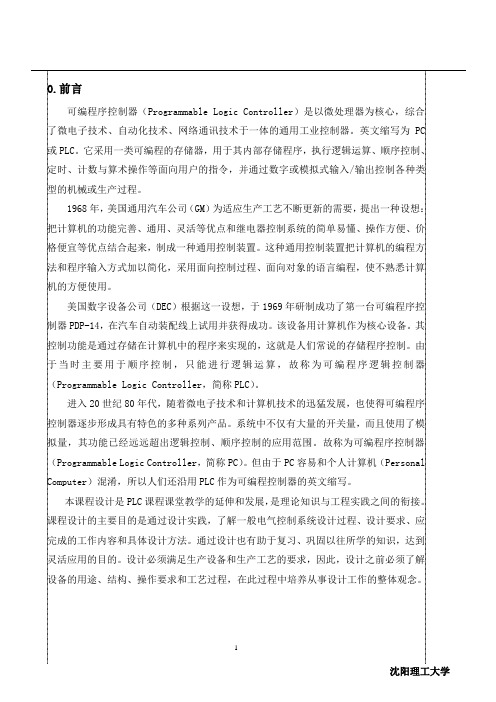
0.前言可编程序控制器(Programmable Logic Controller)是以微处理器为核心,综合了微电子技术、自动化技术、网络通讯技术于一体的通用工业控制器。
英文缩写为PC 或PLC。
它采用一类可编程的存储器,用于其内部存储程序,执行逻辑运算、顺序控制、定时、计数与算术操作等面向用户的指令,并通过数字或模拟式输入/输出控制各种类型的机械或生产过程。
1968年,美国通用汽车公司(GM)为适应生产工艺不断更新的需要,提出一种设想:把计算机的功能完善、通用、灵活等优点和继电器控制系统的简单易懂、操作方便、价格便宜等优点结合起来,制成一种通用控制装置。
这种通用控制装置把计算机的编程方法和程序输入方式加以简化,采用面向控制过程、面向对象的语言编程,使不熟悉计算机的方便使用。
美国数字设备公司(DEC)根据这一设想,于1969年研制成功了第一台可编程序控制器PDP-14,在汽车自动装配线上试用并获得成功。
该设备用计算机作为核心设备。
其控制功能是通过存储在计算机中的程序来实现的,这就是人们常说的存储程序控制。
由于当时主要用于顺序控制,只能进行逻辑运算,故称为可编程序逻辑控制器(Programmable Logic Controller,简称PLC)。
进入20世纪80年代,随着微电子技术和计算机技术的迅猛发展,也使得可编程序控制器逐步形成具有特色的多种系列产品。
系统中不仅有大量的开关量,而且使用了模拟量,其功能已经远远超出逻辑控制、顺序控制的应用范围。
故称为可编程序控制器(Programmable Logic Controller,简称PC)。
但由于PC容易和个人计算机(Personal Computer)混淆,所以人们还沿用PLC作为可编程控制器的英文缩写。
本课程设计是PLC课程课堂教学的延伸和发展,是理论知识与工程实践之间的衔接。
课程设计的主要目的是通过设计实践,了解一般电气控制系统设计过程、设计要求、应完成的工作内容和具体设计方法。
- 1、下载文档前请自行甄别文档内容的完整性,平台不提供额外的编辑、内容补充、找答案等附加服务。
- 2、"仅部分预览"的文档,不可在线预览部分如存在完整性等问题,可反馈申请退款(可完整预览的文档不适用该条件!)。
- 3、如文档侵犯您的权益,请联系客服反馈,我们会尽快为您处理(人工客服工作时间:9:00-18:30)。
《PLC原理及应用》
实训报告
题目:配料车控制系统程序设计
组号:12组
班级学号:11601109
学生姓名:李富民
指导教师:张慧玲
成绩:
沈阳工学院
目录
0、前言 (2)
1、实训的任务和要求 (3)
1.1、实训的任务 (3)
1.2、设计内容 (3)
1.3、设计要求 (4)
1.4、进度安排 (4)
2、总体设计 (4)
2.1、PLC选型 (4)
2.2、PLC端子分配 (4)
3、PLC总体设计 (6)
3.1、设计思想 (6)
3.2、PLC顺序功能图设计 (6)
3.3、PLC梯形图设计 (8)
3.4、PLC指令 (10)
4、结束语 (16)
5、参考文献 (17)
0、前言
近年来,随着科学技术尤其是微电子技术的迅猛发展,可编程序控制器(简称PLC)技术已广泛应用于自动化控制领域。
它以微处理器为核心,
有机地将微型计算机技术、自动化控制技术及通信技术融为一体。
PLC具有控制能力强、可靠性高、配置灵活、编程简单、使用方便、易于扩展等优点,使用PLC进行控制已经形成了一种工业控制趋势。
目前,PLC在国内外已广泛应用于钢铁、石油、化工、电力、建材、机械制造、汽车、轻纺、交通运输、环保及文化娱乐等各行各业。
随着社会的不断发展,科学的不断进步,人们已经对越来越多的事物不是进行手动的操作,而是进行人工智能控制。
本次实训题目配料车控制系统程序设计也正是在这样的背景下应运而生的,本次实训的目的是掌握机电传动控制系统的基本原理,PLC控制电路的设计方法以及继电器—接触器控制电路的PLC改造方法。
掌握机电传动控制系统中继电器—接触器和PLC控制的基本原理,设计方法及两者的关系。
掌握常用电器元件的选择方法。
具备一定的控制电路的分析能力与设计能力。
运用所学的可编程控制器的相关知识在实验电路板上实现小车取料的控制。
改变以往人工取料时间长,难度大,效率低的缺点。
提高工作效率,节省人力资源。
1、实训的任务和要求
1.1 实训的任务
第十二组题目:配料车控制系统程序设计
1.1.1 控制要求:
配料车完成“从配料罐出发,到A处取m车料,再到B处取n车料,送回配料罐进行配料混合”的工作循环。
配料车由三相交流异步电机驱动。
工艺流程图:
配料车工作示意图
1.2 设计内容:
1.2.1 完成要求的控制循环。
1.2.2 按停止按钮,完成当前循环后再停。
1.2.3 按复位按钮,立即返回原位停止。
1.2.4 要求可以实现连续控制。
1.3 设计要求:
1.3.1 设计端子分配图和顺序功能图
1.3.2 设计并调试PLC控制梯形图
1.3.3 撰写实训报告
1.4 进度安排:
1.4.1 理解题目要求,查阅资料,确定设计方案 1天
1.4.2 PLC控制设计与调试
2.5天
1.4.3 实训报告撰写 1天
1.4.4 答辩 0.5天
2、总体设计
2.1 PLC选型
根据我们已学的知识决定我们应该选择ORMON公司的CPM1A系列PLC
主机。
根据题目要求的需要,我们选择CPM1A系列的40点CPM1A-40CDR-A型PLC主机。
该系列主机有24个输入点,16个输出点。
8个输入点
3个SB开关:启动开关、停止开关、复位开关
3个SQ开关:左限位开关、中限位开关、右限位开关
2个SA开关:单周期开关、连续开关
6个输出点
4个YV开关:装A料、装B料、卸料、混料
2个线圈开关:正转、反转
2.2 PLC端子分配
启动按钮SB1 00000 装A料YV1 01001
停止按钮SB2 00001 装B料YV2 01002
单周期开关SA1 00002 卸料YV3 01003
连续开关SA2 00003 右行KM1 01004
左限位开关SQ1 00004 左行KM2 01005
中限位开关SQ2 00005 混料YV6 01006
右限位开关SQ3 00006
复位按钮SB3 00007
3、PLC程序设计
3.1 设计思想
3.1.1 a、小车停靠在最左侧,开启启动按钮,小车右行至A料处,停留
10秒,装A料;
b、小车装完A料,自动左行至罐车旁,停留10秒,自动卸料;
c、如此自动往返5次;
d、往返5次结束后,小车从罐车自动右行至B料处,停留10秒,装B料;
e、小车装完B料,自动左行至罐车旁,停留10秒,自动卸料;
f、如此自动往返5次后结束;
g、如遇输入00007,小车立即回到原位
3.2 PLC顺序功能图设计
3.3 PLC梯形图设计
3.4 PLC指令LD 200.05 AND TIM004 AND 0.05 ANDNOT CNT001 OR 200.00
OR 200.01 ANDNOT 200.02 OUT 200.01
LD 200.05 ANDNOT CNT001 OR 200.00
OR 200.01 ANDNOT 200.02 OUT 200.01
LD 200.01
OR 200.02 ANDNOT 200.03 OUT 200.02 LD 200.02 AND TIM000 OR 200.03 ANDNOT 200.04 OUT 200.03 LD 200.03 AND 0.04
OR 200.04 ANDNOT 200.05 OUT 200.04 LD 200.04 AND TIM001 OR 200.05 ANDNOT 200.01 ANDNOT 200.06 OUT 200.05 LD 200.05 AND CNT001
ANDNOT CNT002 ORLD
OR 200.06 ANDNOT 200.07 OUT 200.06 LD 200.06 AND 0.06
OR 200.07 ANDNOT 200.08 OUT 200.07 LD 200.07 AND TIM002 OR 200.08 ANDNOT 200.09 OUT 200.08 LD 200.08 AND 0.05
OR 200.09 ANDNOT 200.10 OUT 200.09 LD 200.09
OR 200.10 ANDNOT 200.11 ANDNOT 200.06 OUT 200.10 LD 200.10 AND CNT002 OR 200.11 ANDNOT 200.00 OUT 200.11 LD 200.11 AND TIM004 AND 0.03
AND 0.01
OR 200.12 OUT 200.12 LD 200.01 OUT 10.04
LD 200.02 OUT 10.01 OUTNOT 10.04 TIM 000 #100
OUT 10.05 OUTNOT 10.01
LD 200.04
OUT 10.03 OUTNOT 10.05 TIM 001 #100
LD 200.05 OUTNOT 10.03
LD P_First_Cycle CNT 001 #5
LD 200.06
OUT 10.04
LD 200.07
OUT 10.02 OUTNOT 10.04 TIM 002 #100
LD 200.08
OUT 10.05 OUTNOT 10.02
LD 200.09
OUT 10.03
OUTNOT 10.05 TIM 003 #100
LD 200.10
OUT 10.03
LD P_First_Cycle CNT 002 #5
LD 200.11
OUT 10.06
TIM 004 #150
LD 0.01
OR 201.00 ANDNOT 0.00
OUT 201.00
LD 0.07 ANDNOT 0.04
OUT 201.01
LD 201.01
OR 10.05 ANDNOT 0.04
OUT 10.05
4、结束语
通过为期一周的实训,使得我对PLC这门课程又有了进一步的认识。
我学会了PLC基本编程方法,并且掌握了PLC的工作原理和熟悉了PLC的的操作方法。
一周的时间,看似充裕,但是实际操作起来却显得有点窘迫,感觉到一周内完成有点力不从心。
但是,我和王婷婷同学还是在张老师和其他同学的帮助下完成了这次PLC实训。
这一次,我们选择了第十二题“配料车控制系统程序设计”。
这道题并
不像很多同学看到在纸面上呈现的那几行文字和一个简单图像那样简单,可以说是“麻雀虽小,五脏俱全”。
这道题涉及了计时器,计数器、循环的使用等多方面内容,可以说是这次PLC实训的一个典型代表。
由于我们使用的主机是欧姆龙公司生产的,这和网上可以找到的都是使用西门子公司的主机有很多大不同,并且对于我们这些只学过欧姆龙公司编写程序的人来说有很大难度,那么这些资料的借鉴意义就很小。
这次实训,使我对于PLC的I/O口分布及端子线图有了更进一步的认识和了解。
同时,学会了如何由顺序图来编辑梯形图并且学会了如何从CX-P 软件已绘梯形图导出语句表等一系列知识。
再次感谢在这次实训中给予帮助的同学和老师。
5、参考文献
1、夏田、陈婵娟、祁广利《PLC电气控制技术》化学工业出版社
2、刘康康《课程设计说明书》沈阳理工大学应用技术学院。