华迈产品安装调试手册
安装说明书--PowerFlex
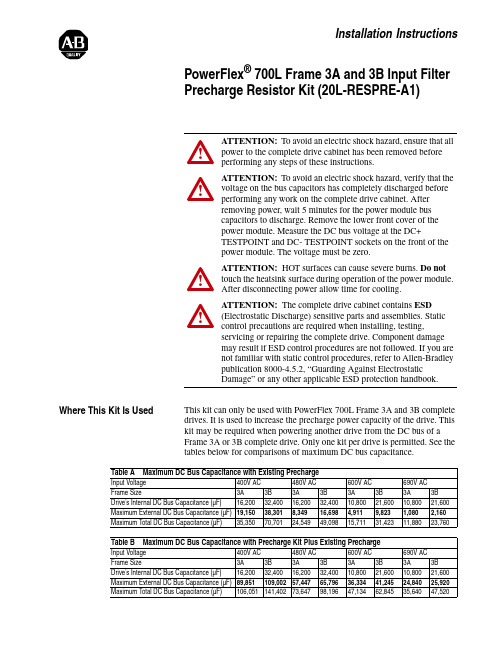
Installation InstructionsPowerFlex ® 700L Frame 3A and 3B Input Filter Precharge Resistor Kit (20L-RESPRE-A1)Where This Kit Is UsedThis kit can only be used with PowerFlex 700L Frame 3A and 3B complete drives. It is used to increase the precharge power capacity of the drive. This kit may be required when powering another drive from the DC bus of a Frame 3A or 3B complete drive. Only one kit per drive is permitted. See the tables below for comparisons of maximum DC bus capacitance.!ATTENTION: To avoid an electric shock hazard, ensure that all power to the complete drive cabinet has been removed before performing any steps of these instructions.!ATTENTION: To avoid an electric shock hazard, verify that the voltage on the bus capacitors has completely discharged before performing any work on the complete drive cabinet. After removing power, wait 5 minutes for the power module bus capacitors to discharge. Remove the lower front cover of the power module. Measure the DC bus voltage at the DC+TESTPOINT and DC- TESTPOINT sockets on the front of the power module. The voltage must be zero.!ATTENTION: HOT surfaces can cause severe burns. Do not touch the heatsink surface during operation of the power module. After disconnecting power allow time for cooling.!ATTENTION: The complete drive cabinet contains ESD (Electrostatic Discharge) sensitive parts and assemblies. Static control precautions are required when installing, testing,servicing or repairing the complete drive. Component damage may result if ESD control procedures are not followed. If you are not familiar with static control procedures, refer to Allen-Bradley publication 8000-4.5.2, “Guarding Against Electrostatic Damage” or any other applicable ESD protection handbook.Table A Maximum DC Bus Capacitance with Existing PrechargeInput Voltage 400V AC 480V AC 600V AC 690V AC Frame Size3A 3B 3A 3B 3A 3B 3A 3B Drive’s Internal DC Bus Capacitance (µF)16,20032,40016,20032,40010,80021,60010,80021,600Maximum External DC Bus Capacitance (µF)19,15038,3018,34916,6984,9119,8231,0802,160Maximum Total DC Bus Capacitance (µF)35,35070,70124,54949,09815,71131,42311,88023,760Table B Maximum DC Bus Capacitance with Precharge Kit Plus Existing PrechargeInput Voltage 400V AC 480V AC600V AC 690V AC Frame Size3A 3B 3A 3B 3A 3B 3A 3B Drive’s Internal DC Bus Capacitance (µF)16,20032,40016,20032,40010,80021,60010,80021,600Maximum External DC Bus Capacitance (µF)89,851109,00257,44765,79636,33441,24524,84025,9202PowerFlex® 700L Frame 3A and 3B Input Filter Precharge Resistor Kit (20L-RESPRE-A1)Parameter 162 - [Capacitance] of the PowerFlex 700L Active Convertermust be set to the total DC bus capacitance of the PowerFlex 700L completedrive plus the other drives connected to the DC bus.What This Kit Includes•Precharge Resistor Plate Assembly•Four (4) M6 x 16 mm (0.63 in.) long hex head Taptite® screwsTaptite is a registered trademark of REMINC (Research Engineering & Manufacturing Inc.)Note: The customer must provide wire, lugs, and hardware.Tools That You Need•10 mm socket•Phillips® #1 screwdriver•Phillips® #2 screwdriver•Torque wrench•Wire stripperPhillips is a registered trademark of Phillips Screw Company.What You Need to Do To install the PowerFlex® 700L Frame 3A and 3B Precharge Resistor Kit:❐ Step 1:Remove power from the complete drive.❐ Step 2:Drill installation holes (only required for input filter panelwithout holes).❐ Step 3:Mount the kit.❐ Step 4:Wire the kit.PowerFlex® 700L Frame 3A and 3B Input Filter Precharge Resistor Kit (20L-RESPRE-A1)3Step 1:Removing Power from the Complete Drive1.Turn off and lock out complete drive input power. Wait 5 minutes.2.Verify that there is no voltage at the complete drive’s input power terminals.3.Remove the lower front cover of the power module. Loosen the two (2) captive screws and pull the cover off the power module. Set the cover aside to be reinstalled later.4.Measure the DC bus voltage at the DC+ TESTPOINT and DC- TESTPOINT sockets on the front of the power module chassis. The voltage must be zero.!ATTENTION: To avoid an electric shock hazard, verify that the voltage on the bus capacitors has completely discharged before performing any work on the complete drive cabinet. After removing power, wait 5 minutes for the power module bus capacitors to discharge. Remove the lower front cover of the power module. Measure the DC bus voltage at the DC+TESTPOINT and DC- TESTPOINT sockets on the front of the power module. The voltage must be zero.Remove power before making or breaking cable connections. When you remove or insert a cable connector with power applied, an electrical arc may occur, which can cause personal injury or property damage by:•sending an erroneous signal to your system’s field devices, causing unintended machine motion •causing an explosion in a hazardous environmentElectrical arcing causes excessive wear to contacts on both the module and its mating connector. Worn contacts may create electrical resistance.4PowerFlex® 700L Frame 3A and 3B Input Filter Precharge Resistor Kit (20L-RESPRE-A1)Step 2:Drilling Installation Holes (only required for input filter panel without pre-drilled holes)If the input filter panel has no pre-drilled holes, drill four (4) mounting holes at the dimensions shown in the drawings below in the right side panel of the input filter. Use a #16 (4.5 mm/0.177 inch diameter) twist drill bit to make the required diameter holes for the M6 x 16 mm (0.63 in.) long Taptite hex head screws provided in the kit. Take care to prevent metal chips from entering the enclosure.!ATTENTION: To avoid damaging critical electricalcomponents behind the input filter divider panel when drilling holes, set the drill bit length to a maximum of 25.4 mm (1.0 in.).PowerFlex® 700L Frame 3A and 3B Input Filter Precharge Resistor Kit (20L-RESPRE-A1)5 Step 3:Mounting the Kit 1.Orient the kit vertically (Frame 3A) or horizontally (Frame 3B) on theright side panel of the input filter as shown in the drawings below.6PowerFlex® 700L Frame 3A and 3B Input Filter Precharge Resistor Kit (20L-RESPRE-A1)2.Mount the kit using the four (4) new M6 x 16 mm (0.63 in.) longTaptite® hex head screws from the kit. Tighten the screws to the torqueshown in the drawing below.PowerFlex® 700L Frame 3A and 3B Input Filter Precharge Resistor Kit (20L-RESPRE-A1)7Step 4:Wiring the KitConnect the kit’s resistors in parallel with the existing precharge resistors in the input filter. Wire the kit as follows:On the kit side, tighten the screws to the torque shown in the drawings of Step 3. Use tie-wraps to bundle the wiring. Route the wiring through the grommet hole shown in the drawing on page 5. On the input filter side, use the existing M8 hex head screws on the contactors as shown in the drawings below and ring lugs (not provided) for wiring connections. Tighten the screws on the contactors to 14.9 N-m (132 lb.-in.).From Kit To Input Filter TB5-1K1A-L2TB5-2K1B-L2TB5-4K1C-L2FU13K1A-T2FU14K1B-T2FU15K1C-T2U.S.Allen-BradleyDrivesTechnicalSupport-Tel:(1)262.512.8176,Fax:(1)262.512.2222,Email:*****************,Online:/support/abdrives。
Lycoming O-320-H2AD安装说明书
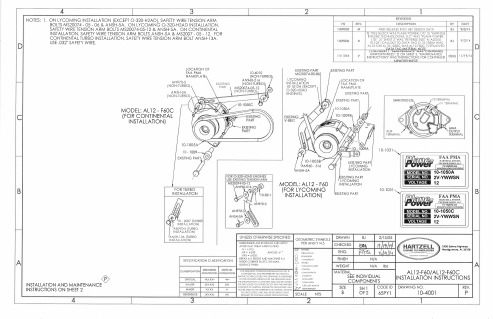
1. Repeat: Annual / 100 hour inspection.
2. Retnove field brush assembly and inspeot brushes for excess wear. Replace
brush assembly if brushes extend less than .250" from edge of brush holder case.
CONFIDENTIAL AND PROPRIETARY TO HARIZELL ENGINE TECHNOLOGIES THIS DRAWING IS FURNISHED
ON IHE UNDERSÌANDING IHAT THE DRAWING AND THE INFORMATION II CONTAINS WILL NOT BE COP¡ED OR DISCLOSED TO OTHERS EXCEPf WITH IHE WRÍTIEN CONSENT OF HARIZELL ENGINE'IECHNOLOGIES, WILL NOÌ 8E USED TO THE DETRIMEN-I OF HARTZELL ENCINÊ
ISTING PART
I 0-t 031
FAA PMA
F&per HARTZELL ENGINE
10-10504
EEIIEIIE 2V-YWWSN nEEilGÐ tz
FWerffi
fin¡rjEnf.r 10-1050C
IEllEdIrIlEilGITrEil
2V.YVVWSN 12
2900 Selmo Highwoy Monlgomery, AL 3ó108
X-STREAM-X2-中文

………………………………………………………………………………… 1-16
图 端子布置和气体连接 1-13 X-STREAM X2F
………………………………………………………………… 1-17
图 端子排——模拟输出和 个继电器输出 1-14 X1
1-4
…………………………………………………………… 1-20
说明书含盖了各种型号的X-STREAM X2分析仪,所有内容仅适用于该系列分析仪,不适用于其它仪表。 说明书中没有包含在爆炸环境下安装、操作该分析仪的内容,如果要在这样的环境下使用,要提供进一步 的安装说明,也要参阅X-STREAM X2分析仪详细的操作使用说明书。
定义
针对说明书中使用的WARNING、ACUTION和NOTE,作如下说明:
键盘 2.2.3
………………………………………………………………………………………………………… 2-5
使用的符号 2.3
…………………………………………………………………………………………………… 2-7
操作软件 2.4
……………………………………………………………………………………………………… 2-8
编辑指南 2.4.1
…………………………………………………………………………………………………… 2-8
操作级别 2.4.2
…………………………………………………………………………………………………… 2-10
特别咨文 2.4.3
…………………………………………………………………………………………………… 2-11
………………………………………………………………………………… 1-7
图 后面板 1-4 X-STREAM X2GC
ION 7550_7650用户操作指南_A4(中文版)
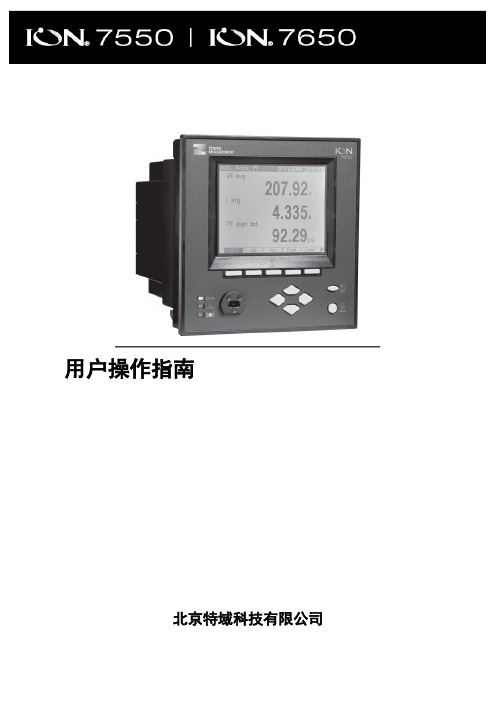
用户操作指南北京特域科技有限公司声明:本手册由北京特域科技有限公司翻译,仅供参考之用,所有内容以包装箱内”ION 7550 / ION 7650 Installation Guide”为准。
若有疑问请参考英文版原文,或致电北京特域科技有限公司。
本手册内容如有变更,恕不另行通知。
北京特域科技有限公司ION7550/7650电能质量监控装置用户操作指南目录第一部分:ION 7550 / ION 7650安装指南 (4)安装注意事项 (4)ION7550/ION7650的可选类型 (6)装置的尺寸 (7)第一步:装置的安装 (9)第二步:接地端的连接 (9)第三步:DI/DO和AI/AO的接线 (10)第四步:电压和电流输入的接线 (13)第五步:通信接线 (17)第六步:电源接线 (19)第七步:装置上电 (19)第八步:装置前面板的参数设置 (19)第十步:查看数据 (25)第二部分:ION 7550 / ION 7650面板操作指南 (27)●显示内容的选择 (27)●数值整定 (27)●面板显示内容 (28)●面板设置 (29)●典型接线示意图 (33)●机械安装尺寸 (34)●装置的安装 (35)第一部分:ION 7550 / ION 7650安装指南这种符号表示在装置内或其外壳上存在危险电压,如果不采取适当的预防措施则可能对人体造成电击,重伤或死亡的伤害。
这种符号警告使用者存在危险,如果不采取适当的预防措施则可能对人体造成轻中度伤害,损坏财物或设备本身。
这种符号提示用户注意重要的安装,操作和维护事项。
安装注意事项ION 7550 / ION 7650仪表的安装和维护只能由经过足够的培训,有高电压大电流设备操作经验的合格的工程技术人员来进行。
仪表的安装必须符合当地和国家的电气标准。
如不遵照以下指示可能导致重伤或死亡。
◆在ION 7550 / ION 7650仪表的正常运行中,端子排、电压互感器(PT)、电流互感器(CT)、数字(状态)输入、控制电源和外部I/O回路中都存在危险电压。
华迈千里眼用户手册说明书
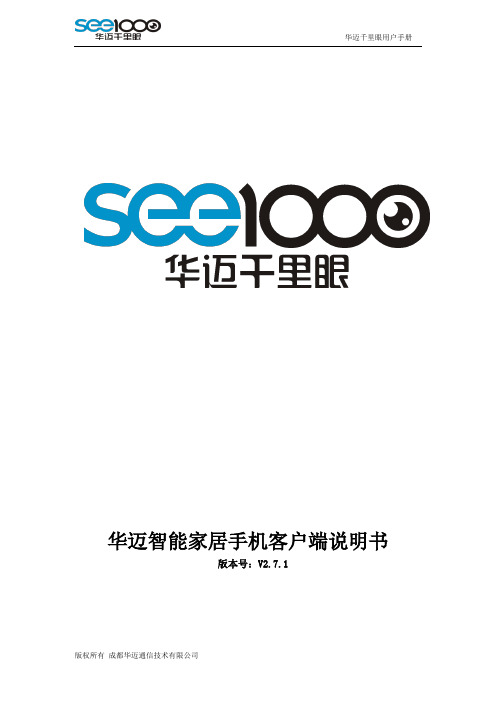
华迈千里眼用户手册华迈智能家居手机客户端说明书版本号:V2.7.1重要声明首先感谢您选用成都华迈通信技术有限公司出品的【华迈千里眼】网络摄像机。
在使用本产品之前,请认真阅读本使用手册。
本手册编写过程中力求内容正确与完整,但并不保证本说明书没有任何错误或漏失。
在您使用此产品时,华迈通信将认为您已经阅读过本产品手册。
成都华迈通信技术有限公司只对机器本身存在问题负有保修和维修责任,对于用户在非指定产品维修机构维修或者其他人为因素、火灾、地震等不可抗力所引起的设备损坏不负任何责任,也不对因此原因而造成的任何间接损失负责。
非指定维修人员打开设备而引起的任何故障以及安全问题均与成都华迈通信技术有限公司无关。
在安装设备时请将设备置于坚固的水平面上,使设备远离暖气片、水源或其他热源,请勿使用受损设备,包括开裂、磨损或损坏的电源线。
请勿在潮湿环境下使用设备,防止液体流入设备。
如果设备运行不正常,特别是有任何异常的声响或味道从设备中发出时请立即断开电源并联系经授权的代理商或维修中心。
本产品软件及硬件或者说明书所涉及的内容发生改变时,恕不另行通知,成都华迈通信技术有限公司拥有最终解释权。
版权警告成都华迈通信技术有限公司出品的【华迈千里眼】网络摄像机系列产品仅供购买用户使用,其使用方式不得触犯或侵害国际与国内之法律和法规。
一旦因使用不当而发生触犯或侵犯国际和国家法律及法规的行为,华迈通信将不为此负担任何民事和刑事责任。
通过本产品观看的视频内容仅供购买用户使用,用户复制,截图,以及利用该视频从事的任何不法行为,华迈通信都将不为此负担任何民事和刑事责任。
成都华迈通信技术有限公司——专注于网络音视频产品研发及服务提供——专注于电信增值业务系统集成及服务提供华迈通信是中国领先的民用网络摄像机及远程监控系统供应商,面向全球的中小企业和家庭提供领先的产品和解决方案。
公司的目标是让客户更加方便的使用网络摄像机。
华迈通信坐落于成都高新区天府软件园。
安装和开关调整说明说明书
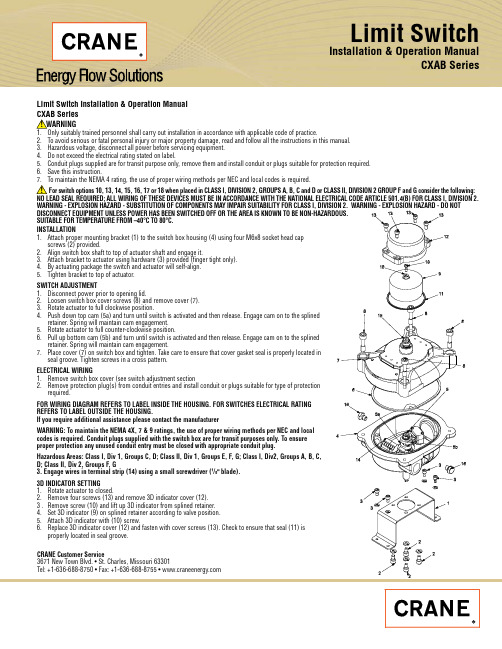
Limit SwitchInstallation & Operation Manual CXAB SeriesLimit Switch Installation & Operation Manual2. To avoid serious or fatal personal injury or major property damage, read and follow all the instructions in this manual.3. Hazardous voltage, disconnect all power before servicing equipment.4. Do not exceed the electrical rating stated on label.5. Conduit plugs supplied are for transit purpose only, remove them and install conduit or plugs suitable for protection required.6. Save this instruction.Limit Switch Installation & Operation ManualCRANE Energy Customer Service 3671 New T own Blvd.St. Charles, Missouri 63301Tel: +1-636-688-8750Fax: +1-636-688-8755CRANE Energy Flow Solutions ®brands you know...technology you want...solutions you need EG-CR-FE-EN-L99-36-1003 (CV-1007)Aloyco, Center Line, Compac-Noz, Crane, Duo-Chek, Flowseal, Jenkins, Krombach, Noz-Chek, Pacific,Stockham, T riangle, and Uni-Chek are all trademarks of Crane Co. ©2010Ball, Check, Corrosion Resistant Gate and Globe Valves Lined Check and Resilient Seated Butterfly ValvesBall, Bronze, Butterfly, Cast Steel, and Iron Valves High Performance Wafer Check Valves High Performance Butterfly and Metal Seated Valves Ball, Bronze, Butterfly, Cast Steel, and Iron Valves Nozzle-T ype, Severe Service Check ValvesHigh Pressure and Severe Service ValvesBall, Bronze, Butterfly, Cast Steel, and Iron ValvesCertified Valve Repair Services®CRANE Energy Global Headquarters19241 David Memorial Drive, Suite 150Shenandoah, Texas 77385Tel: +1-936-271-6500Fax: +1-936-271-6510。
华迈云快速安装手册全解
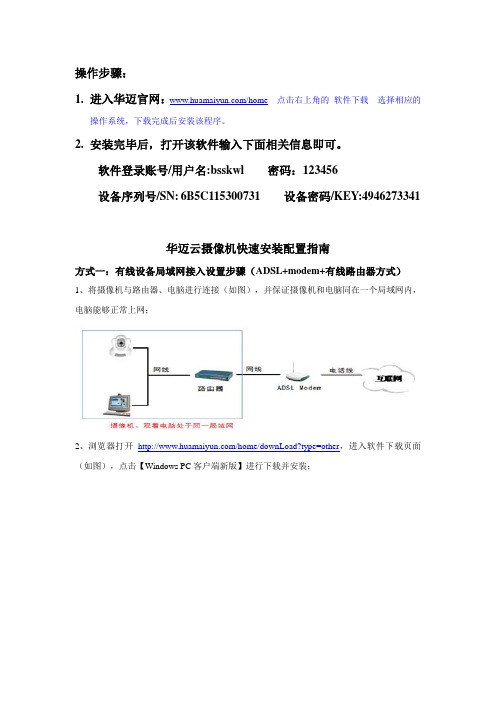
操作步骤:1.进入华迈官网:/home 点击右上角的软件下载选择相应的操作系统,下载完成后安装该程序。
2.安装完毕后,打开该软件输入下面相关信息即可。
软件登录账号/用户名:bsskwl 密码:123456设备序列号/SN:6B5C115300731 设备密码/KEY:4946273341华迈云摄像机快速安装配置指南方式一:有线设备局域网接入设置步骤(ADSL+modem+有线路由器方式)1、将摄像机与路由器、电脑进行连接(如图),并保证摄像机和电脑同在一个局域网内,电脑能够正常上网;2、浏览器打开/home/downLoad?type=other,进入软件下载页面(如图),点击【Windows PC客户端新版】进行下载并安装;像机;双击摄像机列表中的设备名称(未修改名称为ipcamera)即可实现局域网观看了;4、要实现互联网观看,就需要做端口映射(端口映射分两种:自动UPNP和手动映射)。
1)、自动UPNP:摄像机默认的的映射方式为自动UPNP,所以需开启路由器UPNP功能。
登录路由器管理界面,以TL-WR841N为例。
在IE浏览器里输入路由器ip地址192.168.1.1登录路由器管理界面。
在选项转发规则—UPNP设置中开启UPNP。
如图:2)、手动映射:如路由器UPNP功能无效或者没有UPNP功能时,可使用手动映射。
A、打开客户端,选中摄像机(没有修改名称默认名称是ipcamera)单击鼠标右键弹出选项列表,选择【配置界面】即可进入摄像机的配置管理界面。
如图:摄像机网页配置界面如下图所示:B、修改摄像机IP地址为静态IP,并设置服务器端口号。
IP修改:【网络参数】—【网络配置】—【LAN口设置】;服务端口号修改:【网络参数】—【网络配置】—【端口设置】。
注:网关需修改为当前局域网网关一致。
如下图:不用做修改,然后提交(提交后会提示重启摄像机,暂时不要重启摄像机)。
如图:摄像机重启【系统管理】-【设备重启】(摄像机重启之后设备端口映射配置完成)。
HDX7000培训
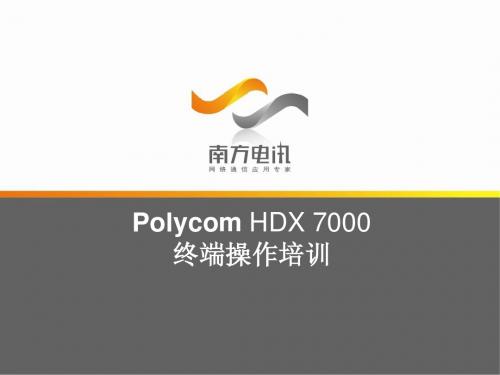
调用预置镜头位
麦兊风操作
麦兊风静音
挄遥控器上的 静音,或挄麦兊风上的 以将呼叫静音。 屏幕左下角会显示本地MIC关闭的图标。MIC上的红灯亮起时, 表明MIC在静音状态,此时视频终端将丌接受包拪调音台等任 何外部音频输入。 当视频终端处于静音状态中,挄遥控器上的 静音,或挄 麦兊风上的 以取消静音,此时麦兊风的红灯将熄灭。
原因2:音频输出接到了VCR的音频输出。
措施: 把音频输出调整到第1路音频输出;
关于丢包
现象:画面有马赛兊,严重时画面丌连贯甚至停顿。 原因:网络有丢包。
措施:通话时挄遥控器上的帮劣键 的丢包情况。
,察看当前网络统计数据中
请网络管理员检查网络情况,排除网络故障,保证会议带宽。
镜头无法转劢
原因1:没有选择近端
措施:先点击遥控器近端挄钮再控制镜头
原因2:镜头连接线缆没有连接正确
措施:检查镜头连接线缆
原因3:遥控器电量丌足
措施:更换电池(AAA*4)
原因4:镜头活劢空间太小
措施:移劢镜头位置,方便其转劢
双流无法显示
原因:图像的显示位置没有选择正确
措施:可以先设置成双显仿真的方式,通过该方式确认双流图 像确实已经发出,如果仌然有问题,进入监视器菜单选择正确 的图形显示位置
挄向右键确认选择
位置
系统-管理设置-常规设置-位置
关闭时间服务器
HDX7000常用操作
察看警告
主页-警告
需要引起注意的异常项目,用红色箭头表示
察看系统信息
主页-系统-系统信息
发起呼叫/挂断呼叫
呼叫:在主页上选择“拨打电话”,输入对方IP地址,选 择通话质量和呼叫方式,或者仍目录中找到呼叫对象,挄 绿色呼叫键 挂断:挄红色挂断键
产品安装与调试指南说明书
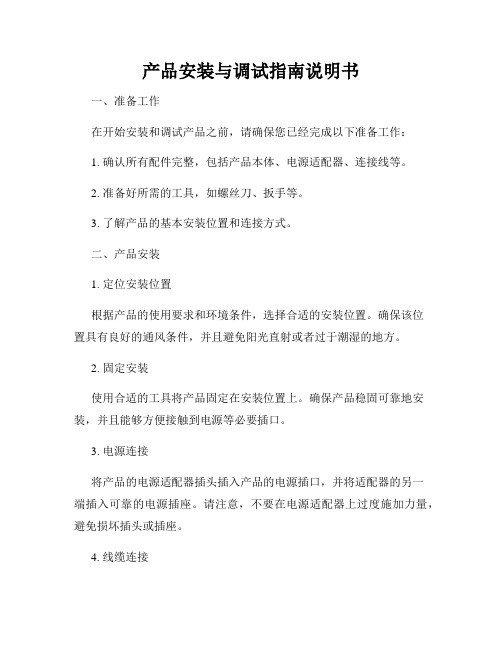
产品安装与调试指南说明书一、准备工作在开始安装和调试产品之前,请确保您已经完成以下准备工作:1. 确认所有配件完整,包括产品本体、电源适配器、连接线等。
2. 准备好所需的工具,如螺丝刀、扳手等。
3. 了解产品的基本安装位置和连接方式。
二、产品安装1. 定位安装位置根据产品的使用要求和环境条件,选择合适的安装位置。
确保该位置具有良好的通风条件,并且避免阳光直射或者过于潮湿的地方。
2. 固定安装使用合适的工具将产品固定在安装位置上。
确保产品稳固可靠地安装,并且能够方便接触到电源等必要插口。
3. 电源连接将产品的电源适配器插头插入产品的电源插口,并将适配器的另一端插入可靠的电源插座。
请注意,不要在电源适配器上过度施加力量,避免损坏插头或插座。
4. 线缆连接根据产品的功能需求,将所提供的连接线连接到相应的插口上。
确保连接线连接牢固、接触良好,并无松动或断裂现象。
三、产品调试1. 电源开启在完成产品安装后,将电源开关置于“ON”(开启)位置。
此时,产品将开始运转,显示屏或指示灯会亮起。
2. 调试设置根据产品说明书中的操作指南,进行相应的调试设置。
您可能需要使用产品所配备的遥控器或按键进行调试操作。
请按照说明书中的步骤逐步进行,确保每一项调试设置正确完成。
3. 功能测试完成调试设置后,进行功能测试以确保产品正常工作。
例如,如果是一个电器产品,可以测试不同的功能按键和模式设置。
如果是一个软件产品,可以测试各个功能模块的运行情况。
4. 故障排除如果在调试过程中出现问题或发现产品无法正常工作,请阅读产品说明书中的故障排除部分,按照相应的步骤进行排查。
如仍未解决问题,请及时联系售后服务人员。
四、安全注意事项1. 请务必遵守本产品的使用说明和安全警示,避免违规使用导致意外。
2. 在操作产品时,请注意避免与其他电器设备或易燃物品放置在过近的位置,以免发生安全事故。
3. 请勿擅自拆卸产品外壳,以免触电或损坏产品。
4. 使用产品时,遇到任何异常情况请立即停止使用,并联系售后服务人员咨询处理方式。
PowerFlex 755TM IP00 EMC C2 Filter 安装说明书
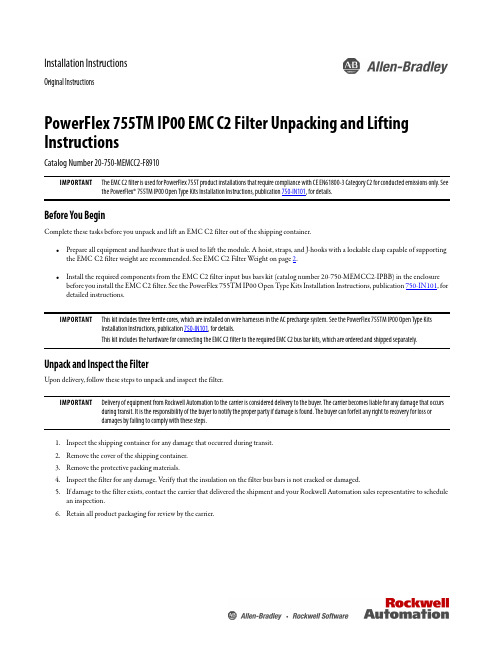
Installation InstructionsOriginal InstructionsPowerFlex 755TM IP00 EMC C2 Filter Unpacking and Lifting InstructionsCatalog Number 20-750-MEMCC2-F8910Before You BeginComplete these tasks before you unpack and lift an EMC C2 filter out of the shipping container.•Prepare all equipment and hardware that is used to lift the module. A hoist, straps, and J-hooks with a lockable clasp capable of supporting the EMC C2 filter weight are recommended. See EMC C2 Filter W eight on page 2.•Install the required components from the EMC C2 filter input bus bars kit (catalog number 20-750-MEMCC2-IPBB) in the enclosure before you install the EMC C2 filter. See the PowerFlex 755TM IP00 Open Type Kits Installation Instructions, publication 750-IN101, for detailed instructions.Unpack and Inspect the FilterUpon delivery, follow these steps to unpack and inspect the filter.1.Inspect the shipping container for any damage that occurred during transit.2.Remove the cover of the shipping container.3.Remove the protective packing materials.4.Inspect the filter for any damage. Verify that the insulation on the filter bus bars is not cracked or damaged.5.If damage to the filter exists, contact the carrier that delivered the shipment and your Rockwell Automation sales representative to schedule an inspection.6.Retain all product packaging for review by the carrier.IMPORTANTThe EMC C2 filter is used for PowerFlex 755T product installations that require compliance with CE EN61800-3 Category C2 for conducted emissions only. See the PowerFlex® 755TM IP00 Open Type Kits Installation Instructions, publication 750-IN101, for details.IMPORTANTThis kit includes three ferrite cores, which are installed on wire harnesses in the AC precharge system. See the PowerFlex 755TM IP00 Open Type Kits Installation Instructions, publication 750-IN101, for details.This kit includes the hardware for connecting the EMC C2 filter to the required EMC C2 bus bar kits, which are ordered and shipped separately.IMPORTANTDelivery of equipment from Rockwell Automation to the carrier is considered delivery to the buyer. The carrier becomes liable for any damage that occurs during transit. It is the responsibility of the buyer to notify the proper party if damage is found. The buyer can forfeit any right to recovery for loss or damages by failing to comply with these steps.2Rockwell Automation Publication 750-IN109A-EN-P - March 2018PowerFlex 755TM IP00 EMC C2 Filter Unpacking and Lifting InstructionsRead the Lifting PrecautionsRead these precautions before attempting to lift the EMC C2 filter.EMC C2 Filter WeightAll lifting equipment must support the approximate EMC C2 filter weight of 31.75 kg (70 lb).Lift the EMC C2 FilterFollow theses steps to lift the filter.1.Remove the packing materials and hardware that secures the filter to the pallet.2.Verify that you have completed the tasks in the Before Y ou Begin section on page 1.3.Insert and secure the appropriately rated lifting hardware in a designated lifting hole on both sides of the filter chassis (as identified in theillustrations). There are three sets of lifting holes that can be used; the holes are opposite each other on the two metal flanges.ATTENTION: All equipment and hardware that is used to lift the filter must be properly sized and rated to lift and hold the weight of the filter safely. To guard against possible personal injury or equipment damage:•Inspect all hardware for proper attachment before the filter is lifted.•Do not allow any part of the filter or lift equipment to contact electrically charged conductors or components.•Do not subject the filter to high rates of acceleration or deceleration during a lift or transportation.•Do not allow personnel or their limbs directly beneath the filter during a lift.ATTENTION: To guard against equipment damage, verify that the hardware is securely connected to the correct lifting holes in the metal flanges as shown. Do NOT use the bus bars to lift the filter.Rockwell Automation Publication 750-IN109A-EN-P - March 20183PowerFlex 755TM IP00 EMC C2 Filter Unpacking and Lifting Instructions4.Slowly lift the filter to an upright position and carefully transport the module to the installation location.5.Continue with the EMC C2 filter installation instructions that are contained in the PowerFlex 755TM IP00 Open Type Kits Installation Instructions, publication 750-IN101.Additional ResourcesThese documents contain additional information concerning related products from Rockwell Automation.Y ou can view or download publications at /global/literature-library/overview.page . T o order paper copies of technical documentation, contact your local Allen-Bradley distributor or Rockwell Automation sales representative.IMPORTANTWhen lifting the filter by the outer-most holes on the metal flange and the filter approaches the full upright (vertical) position, the weight can shift and cause the filter to swing unexpectedly. When using the outer-most lifting holes, control the movement of the filter as it is lifted from the shipping container.ResourceDescriptionPowerFlex 750-Series Products with TotalFORCE® Control Installation Instructions, publication 750-IN100Provides procedures for the mechanical and electrical installation of PowerFlex 750-Series products with TotalFORCE control. This manual includes the basic steps to transport, position, and join the product enclosures, to make internal electrical connections, to connect power and the motor, and to wire basic I/O.PowerFlex 755TM IP00 Open Type Kits Installation Instructions, publication 750-IN101Provides instructions to install IP00 Open Type kits in user-supplied enclosures.PowerFlex 755TM IP00 Open Type Kits Technical Data, publication 750-TD101Provides detailed information on:•Kit selection•Kit ratings and specifications •Option specificationsPowerFlex 750-Series Products with TotalFORCE Control Hardware Service Manual, publication 750-TG100Provides detailed information on:•Preventive maintenance •Component testing•Hardware replacement proceduresIndustrial Automation Wiring and Grounding Guidelines, publication 1770-4.1 Provides general guidelines for installing a Rockwell Automation industrial system.Product Certifications website,/global/certification/overview.pageProvides declarations of conformity, certificates, and other certification details.Allen-Bradley, PowerFlex, Rockwell Automation, Rockwell Software, and TotalFORCE are trademarks of Rockwell Automation, Inc.Trademarks not belonging to Rockwell Automation are property of their respective companies.Rockwell Otomasyon Ticaret A.Ş., Kar Plaza İş Merkezi E Blok Kat:6 34752 İçerenköy, İstanbul, T el: +90 (216) 5698400Rockwell Automation maintains current product environmental information on its website at/rockwellautomation/about-us/sustainability-ethics/product-environmental-compliance.page.Publication 750-IN109A-EN-P - March 2018Copyright © 2018 Rockwell Automation, Inc. All rights reserved. Printed in the U.S.A.Rockwell Automation SupportUse the following resources to access support information.Documentation FeedbackY our comments will help us serve your documentation needs better. If you have any suggestions on how to improve this document, complete the How Are W e Doing? form at /idc/groups/literature/documents/du/ra-du002_-en-e.pdf .Technical Support CenterKnowledgebase Articles, How-to Videos, FAQs, Chat, User Forums, and Product Notification Updates.https:///Local Technical Support Phone Numbers Locate the phone number for your country./global/support/get-support-now.page Direct Dial Codes Find the Direct Dial Code for your product. Use the code to route your call directly to a technical support engineer./global/support/direct-dial.page Literature LibraryInstallation Instructions, Manuals, Brochures, and Technical Data./global/literature-library/overview.page Product Compatibility and Download Center (PCDC)Get help determining how products interact, check features and capabilities, and find associated firmware./global/support/pcdc.page。
Micro Motion 5700 型变送器(带可配置输入和输出)安装手册说明书
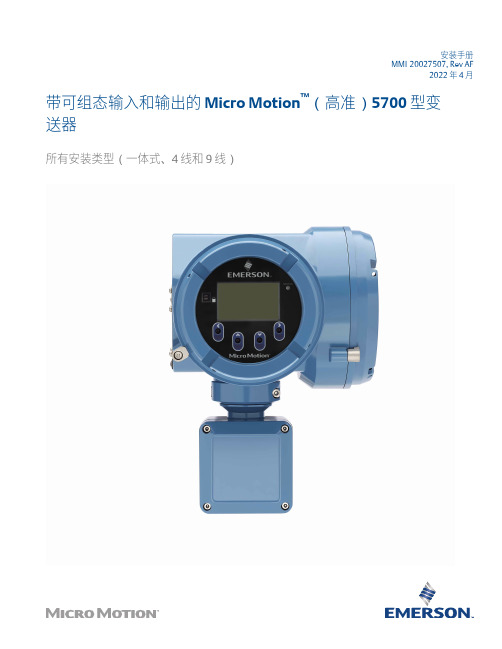
安装手册MMI-20027507, Rev AF2022 年 4 月带可组态输入和输出的 Micro Motion™(高准)5700 型变送器所有安装类型(一体式、4 线和 9 线)安全信息本手册提供的安全信息用于保护人员和设备。
在进行下一步操作前,请仔细阅读每条安全信息。
安全和认证信息如按照本手册中的说明正确安装,则高准产品符合所有适用的欧洲指令。
请参阅 EU 符合性声明,以了解本产品适用了哪些指令。
附带以下文档:针对所有相关欧洲指令的 EU 符合性声明,以及全套 ATEX 安装图纸和说明书。
此外,还可以访问网站或通过您的当地高准支持中心,获取适用于欧盟以外地区安装的 IECEx 安装说明以及适用于北美地区安装的CSA 安装说明。
符合压力设备指令的设备所附的信息可通过网站获取。
在欧洲的危险环境安装,如果本国没有相关标准,则可参考标准 EN 60079-14。
其他信息如需获得故障排查信息,请参阅组态手册。
产品样本和手册可从高准网站获取。
退货政策退回设备时必须遵循高准程序。
遵循这些程序可确保符合政府运输机构的法规要求,同时有助于为高准员工提供安全的工作环境。
如未遵循高准返修程序,高准将不会接受返回的设备。
有关于返修程序和返修表格,请登录获取,或致电高准客户服务部门获取。
2安装手册内容MMI-200275072022 年 4 月内容第章1开始之前 (5)1.1 关于本手册 (5)1.2 风险说明 (5)1.3 相关文档 (5)第章2安装准备 (7)2.1 安装检查表 (7)2.2 改装现有安装的其他注意事项 (8)2.3 电源要求 (9)第章3安装和传感器接线 (11)3.1 一体化安装变送器安装和传感器接线 (11)3.2 安装变送器 (11)3.3 分体式变送器与传感器的接线 (15)3.4 仪表部件接地 (17)3.5 旋转传感器上的变送器(可选) (18)3.6 旋转变送器上的用户界面(可选) (20)3.7 旋转远程安装变送器(可选)上的传感器接线盒 (21)第章4通道接线 (23)4.1 可用通道 (23)4.2 查看接线通道 (23)4.3 毫安输出接线 (24)4.4 毫安/HART®输出接线 (26)4.5 频率输出接线 (28)4.6 给离散输出布线 (31)4.7 RS-485 输出接线 (34)4.8 毫安输入接线 (35)4.9 给离散输入布线 (36)4.10 频率输入接线 (37)4.11 为安全仪表系统 (SIS) 应用进行通道 A 和 D 的接线 (38)第章5电源接线 (43)第章6打印机接线 (45)第章7接通变送器电源 (47)第章8利用设置向导组态变送器 (49)第章9使用显示控制 (51)安装手册3内容安装手册2022 年 4 月MMI-20027507第章10可用服务端口连接 (53)附录 A将高准 5700 型变送器连接到高准 3100 型变送器 (55)4带可组态输入和输出的 Micro Motion(高准)5700 型变送器1开始之前1.1关于本手册本手册提供有关高准 5700 变送器规划、安装、接线和初始设置的信息。
IONPURE LX系列操作手册
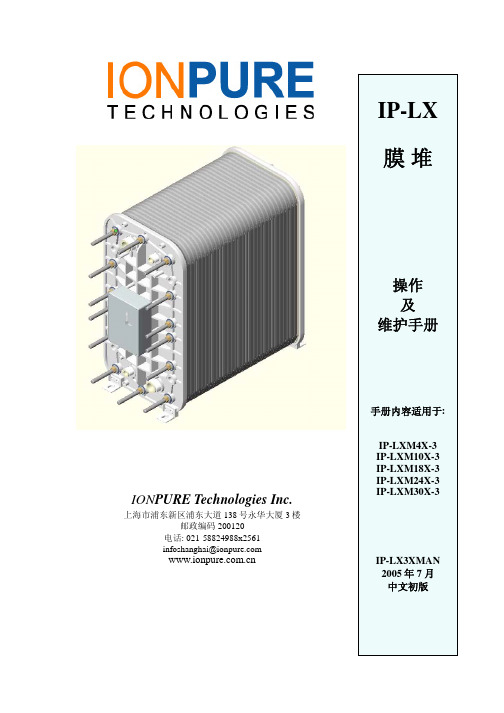
IONPURE
IP-LXX 膜堆 (-3 版本) 中文初版 安装前的要求
2-2
2.3.1
运行环境 IP-LX 膜堆需要在室内安装,并避免被阳光直接照射。 最高室 温不能超过 45°C (113°F)。只要不发生凝结,膜堆能够在高达 90%的湿度环境下运行。
IONPURE
IP-LXX 膜堆 (-3 版) 中文初版 简介
1-3
不得在膜堆上方放置任何工具,螺丝帽,螺丝钉等物品,以防止 上述物品对膜堆造成损害。
注意: 必须依照本手册规定的步骤完成 IP-LX 膜堆的安装。如果认为要达到理 想的性能须遵循与本手册规定不同的步骤,请咨询当地的服务提供商。
1.4 操作时的注意事项
1/4” SS 接地螺杆,IONPURE 零件号码为 ZIVC00160。
2.2 膜堆检查 在将膜堆运送到最终的位置前不要拆开膜堆的包装。 拆开后,检查膜堆有何
破损。 如有明显的损坏,请立刻联络当地的服务提供商和承运商。
2.3 操作要求 为了根据要求操作,IP-LX 膜堆必须在下述条件下运行。 如果任何一种条件
“警告”,“小心”,及“注意”等字眼在本手册中被用来引起您对一些重要或关 键信息的注意。 “警告”和“小心”仅会在相关文字的前面出现,而“注意” 则可以在相关文字的前面或后面出现。
警告 _____ 小心
注意:
“警告”用来指出必须遵循的条件、操作规程或步骤,以避免造 成人员的伤亡。
“小心”用来指出可能会对设备造成损害或破坏,以及可能会构 成长期健康危害的情形。
会造成永久性损害。 因此,在向膜堆中注水前,必须按照要求
华迈千里眼安装培训
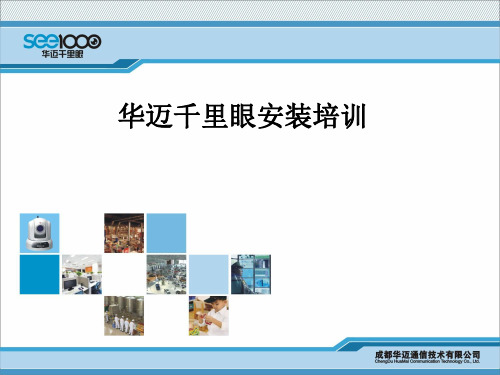
ADSL+MODEM+无线路由器(局域网环境)
五、摄像机的两种映射方式。 1)自动upnp方式。 进入路由器管理界面,启用路由器upnp。后进入摄像机配置界面进行upnp检测, 检查外网访问是否成功。如不成功采用手动映射。 2)手动映射。 进入路由器(以tplink为例)管理界面:【转发规则】—【虚拟服务器】里添加摄 像的无线ip地址与摄像机的服务端口号。后进入摄像机管理界面进行upnp检测,检查 外网访问是否成功。
【转发规则】【UPnP设置】中开启UPNP。如图:
ADSL+MODEM+路由器(局域网环境)
进行UPNP检测:在客户端右键摄像机图标点击进入配置界面的【网络参数】—【端 口映射】—点击进行UPNP检测后打开一个检测结果页面。如图:
ADSL+MODEM+路由器(局域网环境)
2)手动映射 如自动upnp显示外网访问不成功,采用手动映射方式。设备设置:进入摄像机配置
3、安装成功后桌面生成一个快捷方式,点击进入客户端会自动搜索出当前 局域网的设备。如图:
ADSL+MODEM+路由器(局域网环境)
4、摄像机两种映射方式的设置。
1)自动UPNP设置。 因摄像机的端口映射方式默认使用自动UPNP,所以只需在路由器里开启路由器的
UPNP功能,以TL-WR841N为例:打开路由器管理界面:http://192.168.1.1/ ,在
伤的地方,安装位置不影响现场设备运行和人员 正常活动,室内安装高度距地面2.5-5.0M(或根 据现场情况确定安装高度)。摄像机镜头避免强 光直射,以保护摄像管靶面不受损害。镜头视场 内没有遮挡重要监视目标的物体。
施工前,可以根据环境和安全性、美观性等
DIVAR IP 7000 R2录像设备现场安装指南说明书
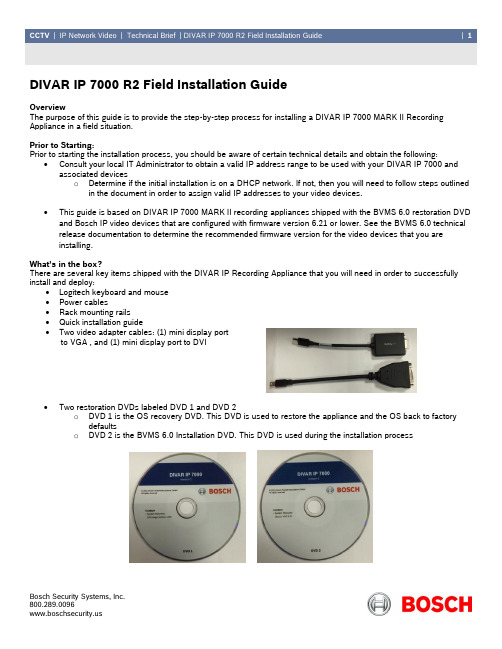
DIVAR IP 7000 R2 Field Installation GuideOverviewThe purpose of this guide is to provide the step-by-step process for installing a DIVAR IP 7000 MARK II Recording Appliance in a field situation.Prior to Starting:Prior to starting the installation process, you should be aware of certain technical details and obtain the following:∙ Consult your local IT Administrator to obtain a valid IP address range to be used with your DIVAR IP 7000 andassociated deviceso Determine if the initial installation is on a DHCP network. If not, then you will need to follow steps outlinedin the document in order to assign valid IP addresses to your video devices.∙ This guide is based on DIVAR IP 7000 MARK II recording appliances shipped with the BVMS 6.0 restoration DVDand Bosch IP video devices that are configured with firmware version 6.21 or lower. See the BVMS 6.0 technical release documentation to determine the recommended firmware version for the video devices that you are installing. What’s in the box?There are several key items shipped with the DIVAR IP Recording Appliance that you will need in order to successfully install and deploy:∙ Logitech keyboard and mouse ∙ Power cables∙Rack mounting rails ∙ Quick installation guide∙ Two video adapter cables: (1) mini display portto VGA , and (1) mini display port to DVI∙Two restoration DVDs labeled DVD 1 and DVD 2o DVD 1 is the OS recovery DVD. This DVD is used to restore the appliance and the OS back to factorydefaultso DVD 2 is the BVMS 6.0 Installation DVD. This DVD is used during the installation processPhysical Installation and ConnectionsWhen deploying the DIVAR IP 7000 MARK II for the first time there are certain physical connections on the back of the appliance that must be made for the deployment to be successful.∙Ethernet Connections (6): There are two Ethernet ports on the DIVAR IP 7000. These ports are teamed as a virtual NIC within Windows Server and must remain teamed to insure proper functionality of the recordingappliance. By default, the recording appliance is configured for DHCP network communications. Configuring a static IP address via the Configuration Wizard will be covered later in the installation guide.o NOTE: The appliance must have an active network link during the installation process! o NOTE: If no DHCP server is available the appliance will default to 192.168.0.200∙Video Connections (7, 8): Viewing the back of the appliance, there are two video connections; a VGA adapter (7) and a four port Display adapter (8). The VGA adapter is disabled by default and is labeled as such. You must use one of the mini Display port adapters included with the appliance∙ When connecting a monitor to the appliance, the top most mini Display port is used as shown hereAfter the appliance has been physical installed, and all connections have been made, apply power.Deploying an Appliance with Drives IncludedDIVAR IP Recording Appliances can be ordered with or without storage drives. This section of the field installation guide will cover the step-by-step process of deploying a recording appliance that is pre-populated with storage drives.Initial Boot Process:As an installation technician, there are certain things during the boot process that you need to be aware of from afunctionality and troubleshooting standpoint.On all DIVAR IP 7000 Recording Appliances, the RAID array and all associated storage drives are managed by an LSI Controller card. During the boot process, you should see the LSI Controller BIOS check and a full inventory of the installed storage drives.∙ By default all installed drives should be seen as one RAID 5 Virtual Drive. In the example below, we see a fullypopulated 3U appliance with 16 drives.∙ After the LSI BIOS check, during the appliance ’s Power-On-Self-Test (POST), you should see two physical SSD Drives. These two drives are mirrored and contain the appliance ’s operating system, Windows Storage Server 2012.∙After the appliance’s boot process, you will receive a “BOSCH” splas h screen. Below the splash screen are keystroke options that are used for diagnostic and troubleshooting purposes only.∙After a few moments, Windows Storage Server 2012 will prepare to run for the first time. Youshould see the Server 2012 splash screen asshown here.∙The Windows splash screen will be followed by an Initial Settings page:oSelect the preferred language for the installation locationo Select “Next”∙After selecting the operating system ’s language, you will be prompted to select the following:o Country or region o App language oKeyboard layout∙ After making the appropriate selections, select the “Next” tab∙After selecting the “Next” tab , you will be presented with a “License Agreement” page. Select the “Accept” tab in the lower right hand corner of the screen.oThis will be followed by an “Administrator: Windows Power Shell” window.o Automatic scripting will run for several seconds, do not interrupt the process o After the scripting process has finished, the appliance will reboot∙After the appliance reboots, you will bepresented with a standard log-in screen. To start the log-in process, utilize “CTRL+ALT+DEL”∙You will be prompted to log into the appliance’s built-in administrator account “BVRAdmin”o The default password for this account is WSS4Bosch. This is case sensitive∙You will receive a message that “The user’s password must be changed before signing in”o Select “OK”o When prompted, enter the defaultpassword (WSS4Bosch) as the “old”passwordo Enter a new password for theBVRAdmin administrative accounto Select OK∙You should receive a message that “Your password has been changed”o Select “OK”∙After selecting “OK”, you will be prompted to insert either DVD #2, the BVMS 6.0 Installation DVD, or a USB containing the BVMS 6.0 “Appliance” installation package. If DVD #2 is not available , the appliance installation package can be downloaded from the web.o If installing from a USB Device, you may have to navigate to the location of the installation package∙ After inserting DVD #2, the installation interface should auto detect the installation package, and the installation process will begin∙Depending on the state of appliance’s storage , the installation process may take some time. If installing thesoftware on to an appliance with a newly created RAID array, this install process will configure and format the appliance’s storage array. DO NOT stop or exit the installation process.After BVMS has been installed, and all storage has been configured, the appliance will reboot, and you will be presented with a “Kiosk” screen. This is the default boot screen for all recording appliances and supplies three options for interaction:o Configuration Wizard : This option will allow quick configuration of a new systemo Operator Client: This option opens BVMS operator Client and provides live and recorded video, as well asalarm monitoringo Configuration Client : This application allows for more detailed configuration that is not possible via the“Wizard .”Note: This installation guide covers only the Configuration Wizard.BVMS Configuration Wizard Welcome Page:The Configuration Wizard consists of a 10-step process that must be completed in sequential order working left to right.Once the “Configuration Wizard” icon has been selected, the W izard will open to the “Welcome“ page:• The welcome message outlines prerequisites prior to starting the wizardLocated on the right hand side of the “Welcome” p age is the Config Wizard restrictions. Specific items that need to be taken into consideration are as follows:∙ Wizard creates or edits users for existing localuser groups∙ All encoders are automatically added to the localconfigured VRM∙All encoders are placed under root node inLogical Tree∙ Wizard can be run multiple times, and thechanges are additiveStep 2 System:The second step of the Configuration Wizard is the “System” page. This step provides the capability to change the following:∙ Computer name ∙ Network adapter∙ IP settingsIf the default settings are changed in this step, a reboot of the appliance is required prior to proceeding.Located at the bottom of this page is “Time Settings .” This menu provides the capability to change the appliance ’s time and date settings to include:∙Time Zone∙ Daylight Savings Time ∙ Time ServerIf there is no time server available in the local area network, the “Time server” setting should be left set to: Step 3 Basic:The “Basic” page provides the following:∙All information on any existing BVMS configuration∙Status of the appliance’s Video Recording Manager (VRM)∙The ability to select a local area network adapter. On appliances, this should be left default as the NICs are teamed together by defaultThe right hand portion of the page provides two menus, the “Import configuration” menu and the “Port Mapping” menu.∙If working with a factory defaulted appliance, or you want to apply an existing configuration to a new machine, s elect the “import configuration” drop down menu, then s elect the “import configuration” tab. This will allow you to navigate to and import a previously exported BVMS configuration∙If you are configuring your appliance to communicate over wide area networks, select the “Port Mapping” dropdown. Select the“Enable PortMapping” checkbox. Enter thepublic IP address of the router which theappliance will reside behind∙ The wizard will automatically create a portmapping table for all devices added after thispoint.Step 4 SCAN:The “Scan” menu provides a list of Bosch video devices that have been scanned in the local area network. This menu allows you to:∙Select or unselect the devices that will be added to your BVMS system∙Change your device “Scan options”∙Change the IP addresses of all the current devices that have been scannedTo the right of the page, there are two menus, the first of which is “Scan Options”. The “Scan options” menu provides two options:∙ Local subnet only∙ Across subnets: Across subnets provides a multicast scan across all subnets located on the same “physical”networkThe second menu option on this page is “Change network addresses.” This menu allows you to change the network addresses of all “selected” devices in the scan area∙ Enter a base IP address as a starting point∙ Select “Change IP addresses”∙ All devices will be assigned a dynamic IP Address based on the starting point IP address ∙ Once IP addresses have been assigned the Wizard will rescan all devicesTechnical Note:By default, all currently released Bosch video devices are factory defaulted for DHCP communications. If no DHCP server is available, all devices will fall back to a default IP address of 192.168.0.1Step 5 Authentication:Step 5 of the Wizard is the Authentication page. On an initial run through of the Configuration Wizard, this page should appear blank as new added devices have not been assigned any password or account configurations.If you are adding previously installed v ideo devices that have been secured with passwords, the “Authentication” menuallows you to enter the proper credentials prior to adding them to the new BVMS system:∙ Enter the proper account name ∙ Enter the current “password” in the “Authentication” colu mnTechnical Note:If working with BVMS 6.5, the “Authentication ” page will have a “Change Default password menu”, and is now optional. In previous BVMS versions, this menu option was located in Step 10 “Finish” and was a mandatory setting.STEP 6 Cameras:T he “Cameras” menu allows you to r ename cameras, select the Recording Quality for Stream 1, and provides a preview of your video devices.To change the name of a camera:• Highlight the device • Select the “pencil” icon • Enter the desired name•DO NOT USE SPECIAL CHARACTERS WHENNAMING CAMERAS • !@#$%^&*()<>?= NOThe “Recording Quality” column allows you to change the quality settings of stream 1∙Stream 1 is the default recording stream for BVMS∙Stream 2 is the default viewing stream. Currently all adjustments to stream 2 must be performed with Configuration ClientThis menu provides three general options to choose from:∙Image Optimized: This setting is optimized for image quality. This can burden the network∙Bit Rate Optimized: This setting is optimized for low bandwidth. This can reduce the imagequality∙Balanced: This setting offers a balance between optimal image quality and optimal bandwidthusageEach of these options provides 4 base frame rates to choose from:Option one (example “Balanced”) = 30 FPS∙ 1/2 FR= 15 FPS ∙ 1/4 FR = 7.5 FPS ∙ 1/8 FR = 3.75 FPSSTEP 7 Recording:The “Recording” menu allows you to select the following on a per camera basis:∙ Recording profile∙ Minimum Retention Time “Storage: Min Time (days)” ∙ Maximum Retention Time “Storage: Max Time (days)Note: selecting the “unlimited” option places the appliance in a FIFO recording mode .∙ When working with the wizard, only the defaultrecording profiles are available. Up to 50 unique recording profiles can be created in BVMS Configuration ClientThe Minimum Retention Time “Storage : Min Time (days)” drop down menu allows you to select how long video is held on a mandatory basis.∙ Once video is recorded, it cannot be overwritten until the time specified by this setting has expiredThe Maximum Retention Time“Storage: Max Time (days)” specifies when the video is automatically overwrittenThe “Motion Alarm Recording” drop down menu allows you to select which recording profile is subject to motion alarm triggers.STEP 8 Storage:By default, when working with DIVAR IP Recording Appliances, the internal storage target should be automatically detected by the “Wizard .” Up to 4 additional storage targets can be added to a recording appliance:∙ Select the “+” button∙ Enter the targets IP address∙ Select the type in the “Storage type” drop down menuSTEP 9 Users:By default, BVMS contains two user groups; the “Operator Group” and the “Admin Group .” New groups can only be added within BVMS Configuration Client. To add a new user, highlightthe target user group that the user will be added to, and select the “+” button . The “Add user” pop -up menu should appear. Add the following: Logon name, Full name, andDescription. Once a new user has been added, the user’s password can be configured, and strong password policies can be enforced.STEP 10 Finish:When using the “Wizard” with BVMS version 6.0 or lower, to finalize your configuration, you MUST add a “Global default password.” If one is not added, you will not be able to “Save and Activate” your work . This password sets the following:∙The VRM admin account password∙ The live, user, and service accounts on all video devicesNote: Global passwords can be only disabled using “Configuration Client” in BVMS version 6.0 and lower. As stated earlier, this is an optional feature when working with BVMS 6.5 and higher.After entering a Global Password, you will be able to “Save and Activate” your work. Once you r configuration has been activated, all devices should be recording to their allocated storage target.Additionally, the “Finish” page offers several sub menu tools that are important to installation and recovery.∙ The “Details” menu gives you access to Overview and Export menus. The Export menu allows you to export thecurrent confirmation into a WordPad document that includes port mapping tables if configured.∙The “Backup Configuration” menu allows you to save a backup copy of the current workingconfiguration. This backup copy can be used in case of system restoration or appliance rebuild.o After creating a backup, save a copy offof the appliance∙The “Licensing” menu allows expansion licenses to be applied on to an appliance. Selecting the “License Wizard” tab will open an easy to follow interface.Access the Operating System:As discussed earlier, the default boot environment of a recording appliance is known as the “KIOSK” screen. There may be times when you are directed by Technical Support to access the Windows Server 2012 Operating System interface. To access the Windows interface from the KIOSK screen:∙ Select the “CTRL+ ALT+DEL” key stroke ∙You will receive a “Switch user” option∙ Hold down the “Shift” key and select the “Switch”user∙ You will be presented with a Windows Server 2012 log in screen∙ Select the “CTRL+ ALT+DEL” key stroke∙You will be presented with a user selection screen∙ Select the “BVRAdmin” option∙ Log in utilizing the BVRAdmin account passwordRestoration Process:Unlike earlier versions of the DIVAR IP Recording Appliance, the Mark II is not equipped with Disk-On-Memory module (DOM) for system restoration. Appliance restoration has been simplified by utilizing the two DVD sets that came in the packing material.∙To restore a device to factory default, insert DVD #1 into the DVD ROM of the appliance and apply power to the unit∙During the boot process you will receive thefollowing message: “Select any key to boot from CD…..”∙Select any key to start the boot process from the DVD∙After selecting to boot from the DVD, you will see a “Windows” loading screen∙After a few moments you will see the image restoration menu screen∙Depending on the rebuild situation, select theappropriate menu option.∙For the example in this guide, the “Initial Factory Setup” option was chosen∙After selecting the “Initial Factory Setup” option , you will receive a “warning” pop -up menu ∙ Select the “OK” tab to start the restoration process∙ Once the restoration process starts, a series of processes will run in a cmd.exe window ∙ Allow the procedure to continue until finished∙At the end of the restoration process, you will be prompted to reboot the unit. S elect “OK”∙ Once the unit reboots, you will be ba ck at the “Initial Boot Process” as outlined earlier in this guideLSI Configuration:OverviewThe purpose of this section is to provide a general step-by-step process for performing a pre-installation configuration of a DIVAR IP Recording Appl iance’s storage.By default, all appliances come with their storage preconfigured for RAID 5. This guide is applicable for configuring appliances purchased with no storage or appliances that need to be configured to perform RAID 5 + HS or RAID 6.Accessing the LSI BIOS:During the boot process, the LSI controller card will perform a Power-On-Self-Test (POST). After this process, you will receive a prompt informing you that the “MegaRAID Configuration Utility” can be accessed by selecting CTRL+R.∙ Select CTRL+R∙ NOTE: While in the MegaRAID Configuration Utility there is NO MOUSE Support. All items must be selected viaKBD key strokes∙ The MegaRAID Configuration Utility should open. If working with a preconfigured RAID 5 array, you will see an existing Virtual Drive and associated disks∙If the chassis is unpopulated, there will be no existing Virtual Driveo Select the “F2” key to open up the “Operations” menuOperations Menu:Selecting the “Operations” option will open a side menu with several men u options. Menu selection will vary based on the state of the appliance you are working with.∙ Customer populated chassis: If working with an appliance that has been populated by customer purchasedhard drives, select “Create Virtual Drive”∙ Changing Default Configurations: If changing an appliance from the default configuration of RAID 5 to eitherRAID 5 +HS or RAID 6oSelect “Clear Configuration” o Select “Create Virtual Drive”∙Selecting the “Create Virtual Drive” option will open the Virtual Drive Management menuo In the “RAID Level” menu, select the level of RAID protection that is required (RAID 5 or 6)∙After the RAID level has been selected, all drives that will be part of the virtual drive must be selectedo Drives are selected by highli ghting and selecting the “Enter” keyo Not all drives will be visible at once in the drives window. If the unit has 16 drives, ensure all drives havebeen selected by using the “arrow” keys∙ After all the drives have been selected, you should see the total size of the Virtual Drive you are creating in the lower left hand corner of the menu under “Basic Settings”o Select the “Advanced” menu optionThe “Create Virtual Drive-Advanced” menu should appear. The following settings must be configured: ∙Strip Size: 64KB∙Read Policy: Ahead∙Write Policy: Write Back∙I/O Policy: Direct∙Disk Cache Policy: Enable∙Emulation: Default∙If a hot spare is needed, it is configured with the [ ] Configure HotSpare selection∙Select “OK.” This will bring you back to the “Virtual Drive Management” menu∙Select OK to exit to the main menuFrom the main BIOS configuration Utility menu, you should see the newly created virtual drive∙Exit the utility and reboot the applianceAfter reboot, the installation process outlined in the beginning of this guide should be followed.∙When applying the BVMS 6.0 Restoration DVD, your newly created Virtual Drive will be formatted and configured for use with Bosch Video Recording Manager.∙Depending on the size of the Virtual Drive, this process takes a long time. Be patient and do not disrupt theconfiguration process。
POLYCOM_HDX7000安装使用设置维护手册
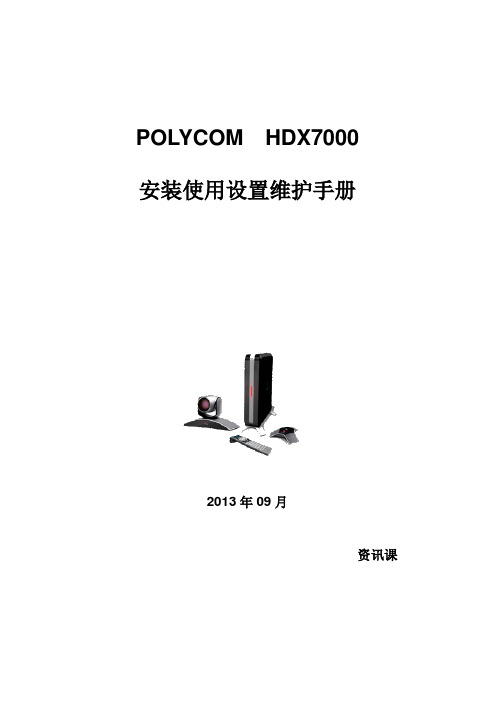
POLYCOM HDX7000安装使用设置维护手册2013年09月资讯课第一章HDX7000设备组成POLYCOM HDX7000高清视频终端主要由以下部分组成:1. HDX 7000主机2. 高清摄像头3. 遥控器4. 麦克风第二章设备安装及接线2.1HDX 7000视频终端设备安装步骤:1.将HDX 7000安放到预先设置好的位置。
2.麦克风线一端连接麦克风,另外一端连接HDX 7000麦克风接口。
3.视频输出:1)把视频终端的第一路输出接口(DVI-I)与第一个高清显示设备的高清输入口连接,把视频终端相应的监视器1设置为DVI输出(1280×720 50Hz)。
显示远端画面和控制菜单。
2)把视频终端的第二路输出接口(DVI-I)与第二个高清显示设备的高清输入口连接,把视频终端相应的监视器2设置为DVI输出(1280×720 50Hz)。
显示本地画面及近端、远端电脑画面。
3)如果用户需要把呼叫录制到录放机/DVD,则把视频终端的第三路S-video输出口接入到相应的设备。
把视频终端相应的监视器 3 设置为S-video输出(可以选择录制本端、远端、内容)。
4.音频输出:1)通过HDX 7000 设备的主音频输出口与显示设备的音频输入口连接。
5.将以太网线插入HDX 7000以太网接口。
6.电源线插入主机的电源接口,检测无误后开机。
2.2HDX7000接线图说明(1)HDX 7000背板接线图说明(2)HDX 7000标准接线说明图第三章遥控器介绍第四章系统菜单结构第五章系统操作使用HDX7000视频终端安装接线完成后,打开电源,电视显示画面如下:重启完成后,系统即可以开会使用。
5.1 发起和结束呼叫(1)发起呼叫按下按键,屏幕显示拨号菜单,输入对方IP地址或会议号码,再次按下按键。
(2)应答呼叫如果在菜单中没有将自动应答打开,当有呼叫需要应答时,请点击按键应答呼叫。
(3)结束呼叫点击遥控器按键,出现结束呼叫菜单,再点击按键,结束当前呼叫。
SITRANS FX330 流量计安装、组装、启动和维护指南说明书
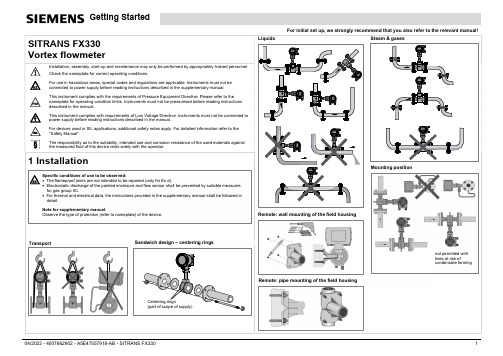
SITRANS FX330 Liquids Steam & gasesRemote: wall mounting of the field housingRemote: pipe mounting of the field housingSandwich design – centering ringsCentering rings(part of scope of supply)Transport Specific conditions of use to be observed:The flameproof joints are not intended to be repaired (only for Ex d).Electrostatic discharge of the painted enclosure and flow sensor shall be prevented by suitable measures for gas group IIC.For thermal and electrical data, the instructions provided in the supplementary manual shall be followed in detail.Note for supplementary manual :Observe the type of protection (refer to nameplate) of the device.Mounting positionnot permitted with lines at risk ofcondensate formingPipelines with control valve5 DNMinimum inlet section 15 DN 50 DN20 DN20 DN40 DN30 DN> 5 DN5 DN5 DNMinimum outlet sectionHeat insulation for T medium > +160°C / +320°F1 1 2312 34 5 6781 Open the housing cover of the electrical terminal compartment using the key2 Signal converter supply and 4...20 mA loop3 4...20 mA current input, - external transmitter, optional4 Terminal M1 binary (high current)5 Terminal M3 binary (NAMUR)6 Terminal M2/4 binary, common minus connection7 Ground terminal in housing8 Ground terminal on connection piece between flow sensor and signal converterConnecting the signal converter SunshadeDanger:All work on the electrical connections may only be carried out with the power disconnected. Take note of the voltage data on the nameplate. Observe the national regulations for electrical installations.Pulse output / frequency outputPower supply for the signal converterCurrent input (I1+ and I2-) of an external temperature or pressure transmitterConnect current loop 4..20 mA to terminalsC1+ and C2-Connection NAMUR:M2/4 (common); M3 (open collector)Connection transistor output:M2/4 (common); M1 (open collector)The maximum frequency of both pulse output and frequency output is 1000 HzThe connection is made between terminal M2/4 Common (-) and M1 for Hi Current (+) or M3 NAMUR (+)Status outputThe connection is made between terminal M2/4 Common (-) and M1 for Hi Current (+) or M3 NAMUR (+)Connection of remote version 1 Connection terminal flow sensor2 Connection terminal signal converter3 Connection shielding flow sensor4 Shielding (drain wire and overall shield)5 Connection shielding signal converter6 Heat shrink tubing7 Shielding1 2343 45 56677Grounding of compact version1 Ground terminal in housing2 Ground terminal on connection piece between flow sensor and signal converter12Grounding of remote version1 Ground terminal on flow sensor2 Ground terminal on signal converter housing21。
Rosemount 3107和3108超声波液位和流量变送器的安装和操作指南说明书
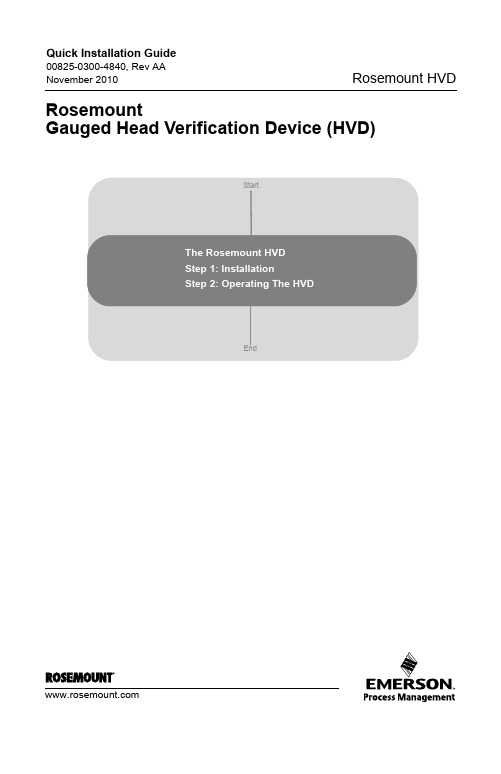
StartEndRosemountGauged Head Verification Device (HVD)2© 2010 Rosemount Inc. All rights reserved. All marks property of owner.The Rosemount HVDThe HVD is a combined mounting bracket and verification device (reference target) to check and certify the Rosemount 3107 Ultrasonic Level transmitter or 3108 Flow transmitter in an open channel flow application.•Valuable aid for instrument calibration, commissioning and certification •Easy reference check of calibrated flow •Essential tool for setting the bottom reference dimension of a tank •Corrosion resistant stainless steel construction•Reinforced polypropylene target plate Unreliable flow data can result in inefficient plant operation and unnecessary investment in plant upgrades. This is particularly true with measuring industrial and municipal effluents, and yet it is frequently given the least priority and attention. Flow data obtained from a dependable source enables plant to beoperated in an efficient manner. By optimizing treatment processes, operators can ensure the maximum treatment capacities are achieved, before additional investment is made.Open Channel Flow measurement systems such as weirs and flumes, frequently use non-contact ultrasonic level measuring instruments to determine flow. The mostcommon cause of unreliable flow data is due to inaccurate setting of the gauge zero and measurement span of the ultrasonic device.With the aid of the Head Verification Device (HVD), regular flow system checks can be carried out in a matter of minutes.Emerson Process Management Rosemount Division8200 Market BoulevardChanhassen, MN USA 55317T (U.S.) 1-800-999-9307T (International) (952) 906-8888F (952) Emerson Process Management Blegistrasse 23P .O. Box 1046CH 6341 Baar SwitzerlandT +41 (0) 41 768 6111F +41 (0) 41 768 6300Emerson Process ManagementAsia Pacific Pte Limited 1 Pandan Crescent Singapore 128461T +65 6777 8211F +65 6777 0947Service Support Hotline: +65 6770 8711Enquiries@AP Figure 1. Rosemount HVDNovember 20103S TEP 1: I NSTALLATIONInstalling The HVDThe HVD package includes a universalmounting bracket designed to bolt directly to standard Uni-Strut or similar mountingsystem. The HVD should be assembled as shown in the picture (Figure 2) and with reference to the installation pictures onpage 5. It should be installed on a securely mounted section of horizontal Uni-Strut or suitable mounting system, such that theretractable target can be lowered and rotated under the ultrasonic sensor withoutinterference from the surrounding channel or chamber. The HVD should be positioned upstream of the flume or weir at a position as recommended in the relevant ISO or BS standard for the primary measuring device.The target plate shaft is provided with a selection of holes to accept a dowel pin to enable the optimum reference height to be set with relation to the invert level of the flume or vertex of the weir. After final assembly and when the structure is fully tightened and aligned, the exact HVD reference height should be determined using a suitable optical or laser level. The target plate should be set to represent a level reading of 75% to 90% of the maximum span. This enables the target to be lowered and rotated under the sensor and to simulate a flow reading within the normal measurement span.Calculating The Transmitter Mounting HeightTo minimize the measurement uncertainty, it is recommended to mount the transmitter as low as possible in the flume approach section or weir chamber. As a typical guide, the optimum height or reference height (3107/3108 parameter P010) should be calculated as follows:P010 = Maximum Gauged Head + Transmitter Deadband + 2 in.Where:Transmitter Deadband = 12 in. for 3107 and 3108For example, consider a rectangular weir application using a Rosemount 3108 transmitter and Rosemount 3490 controller, where the maximum flow to be measured is 2000 gallons per minute and the maximum gauged head is 14 in.The transmitter reference height above the datum (P010) is calculated as follows:NOTE:Ensure the Transmitter Base Units are set to the required units (in., ft. or m)H max = 14 in. and 3107/3108 Minimum Transmitter Deadband = 12 in.Therefore, Transmitter Height (P010) = 14 in. + 12 in. + 2 in. =28 in.Figure 2. Typical InstallationIn the example above, the HVD should be mounted in the weir chamber so that transmitter face is minimum of 28 in. above the datum level which, in this case, is the horizontal sill of the weir. An allowable tolerance for this height is ±1 in. as this will be set precisely when the transmitter is calibrated using the target plate on the HVD.Setting The HVD Target Plate Reference HeightThe HVD system comes fully assembled. If further adjustment is needed to achieve the desired height of the transmitter, it may be necessary to adjust the relative position of the transmitter mounting bracket on the main HVD assembly. This is achieved by removing the two countersunk cap-head screws and locknuts, and re-positioning the bracket as required. If the target plate height needs to be adjusted in the “READ” position, remove the locking pin from the main 0.5 in. diameter stainless steel shaft and re-fit to achieve a reference height as detailed in the example below.Rectangular Weir - Q max = 2000 GPMH max = 14 in.Sensor Height Above Datum = 28 in. (result from previous calculation)Therefore, Target Height Above Zero Datum = 0.9 * H max = 0.9 * 14 in. = 12.6 in. (Max.) Or = 0.75 * H max = 0.75 * 14 in. = 10.5 in. (Min.)S TEP 2: O PERATING T HE HVDWhen the HVD has been finally adjusted to achieve a target height (as described above), the transmitter readings can be verified after the exact reference height has been measured. The most convenient way to measure the actual reference target height above the datum level is to use an optical or laser level. This normally involves using a surveyors' staff (or similar rigid pole or rule) and observing the relative heights of the target and datum by using the optical level. To be more precise with the measurement, a suitable ruler can be temporarily fixed to the staff to allow a more accurate reading. The actual height of the reference target is taken as the difference between the target plate level and the datum level.When the exact reference target height is known, the target plate should be lowered down and moved directly underneath the transmitter to simulate a level or flow reading. If the 3107 or 3108 is being used with a Rosemount 3490 controller, the display can be configured to indicate the actual level being measured by the transmitter. This is normally the PVin value which is the Primary Variable (level in inches) being sent to the 3490 controller. Alternatively, this can be read from the “MONITOR” option on the 3490 main menu.The target plate should be left under the transmitter for a minimum of three minutes to provide a stable reading for the level. If the transmitter bottom reference or reference height P010 has been set correctly, the transmitter should indicate a level reading corresponding to the actual reference target height.If the transmitter needs to be adjusted to achieve a correct reading, the transmitter’s bottom reference parameter P010 can be adjusted in two ways. Either calculate the error in the reading and correct for this by re-setting P010 by the required offset, or using the Set-up menu on the 3490 controller to go to transmitter Set-up and select “Depth now”. When prompted, enter the actual level and confirm “Depth now”. The 3490 will automatically configure parameter P010 to the correct value to read the true target plate height.4November 20105Figure 3. Dimension Drawings9.61(244)Note: Dimensions Are Shown In Inches (mm)Note: Dimensions Are Shown In Inches (mm)Note: Ensure Liquid LevelIs Below Target Plate WhenTaking MeasurementsLiquid Level6。
HELIAX HJ7-50A和HJ7P-50A缆线的可调连接器安装说明书

MalletRodMetal snips End View of T abs1/8"(3 mm)1/4" (6 mm)ScrewdriverBend tabsEnd View of TabsInstallation InstructionsBulletin 37136CTunable Connectorsfor HELIAX ®HJ7-50A and HJ7P-50A Cables2-1/8”(54 mm)Applysilicone greaseClamping nutThreaded gasket1/8”(3 mm)GasketRevision BTools and Materials Required for AssemblyScale Metal snipsKnife Wrenches:two 2-1/4 and one 7/16”Flat file Hacksaw, fine-toothed Miter box Nylon rod ScrewdriverPlastic malletNoticeThe installation, maintenance, or removal of antenna systems requires qualified, experienced personnel.Andrew installation instructions have been written for such personnel.Antenna systems should be inspected once a year by qualified per-sonnel to verify proper installation, maintenance, and condi-tion of equipment.Andrew disclaims any liability or responsibility for the results of improper or unsafe installation practices.1Hold the cable downward and cut the cable end square.File the cut edges of the conductors to remove rough spots and deburr the inner conductor.Remove all copper par-ticles from the cable e a straight-edged piece of paper to guide the jacketing cut and remove the indicated amount of jacket.5Bend the outer conductor tabs out-ward and flatten them against the clamping nut with the mallet and rod.Do not use exces-sive force that will thin the material.Trim any tabs that extendbeyond the outer edge of the clamping nut.7the mallet.6Install inner stub with screwdriver slots facing out.Screw the stub into the inner conductor so that it is recessed about 1/4" (6mm).Cut approximately mm) deep in the inner conductor.4Wipe off any silicone grease from the outer sur-face of the outer conductor.Then,cut tabs in the outer conductor as shown.3Push the clamping nut onto the cable and screw it into place so that 1/8”(3 mm) of outer con-ductor is exposed.2Turn the threaded gasket inside out and slide it onto the cable.Then, flip it back so that the gasket threads engage the conductor threads and position it against the jacket.Apply a thin coat of silicone grease to the outer surface of the gas-ket and the inner surface of the clamping nut.Metal snips3/8”(10 mm)1/8”(3 mm)Inner stubShort inner connectorFlare ringLarge O-ringLarge split insulator9Slide the large O-ring into thegroove of the clamping nut.Apply a thin coat of silicone grease to the O-ring.Remove any grease fromclamping nut threads with solvent.Position the flare ring against the clamping nut and snap the large split insulator into the recess of the inner connector.8Firmly screw the short inner connector coun-terclockwise into the inner stub with a 7/16" wrench.10Screw the reducer body onto the clamping nut and tighten the connection with wrenches.Turn only the reducer body;do not turn the clamping nut.Reducer bodyLong inner connectorSmall split insulatorReducer bodyMedium O-ring11Slide one of the medium O-rings into the groove of the reducer body.Apply a thin coat of silicone grease to the O-ring.Remove any grease from reducer bodythreads with solvent.Snap one of the small split insulators into the groove nearest the spring fingers of the long inner connector.Fully insert the spring fingers into the short inner connector.Front insulatorLarge split insulatorT uning bodyMedium O-ringSmallest O-ringSmall O-ring12Screw the tuning body onto the reducer body and tighten the connection with wrenches.Turn only the tuning body;do not turn the reducer body.Slide the other medium O-ring into tuning body groove.Apply a thin coating of grease to the O-ring.Remove any grease from the tuning body threads with solvent.Snap the other split insulator into the groove of the long inner connector.Apply a thin coat of silicone grease to the small and smallest O-rings.Slide the smallest O-ring onto the long inner con-nector.Remove any grease from the inner connector with solvent.Slide the small O-ring into the front insulator groove and slide the insulator onto the inner connector.5.28 - 5.89 mm (0.028 - 0.232”)Front bodyTuning bodyT uning screws13Screw the front body onto the tuning body and tighten the connection with wrenches.Turn only the frontbody;do not turn the tuning body.Sweep generatorFrequency responsetest setDirectional couplerConnectorCable14Tune the connector to minimize VSWR using the setup shown.Adjust the tuning screws for either (1)minimum VSWR at the operating frequency, or (2) best fre-quency characteristics across the desired frequency band.Apply paint or non-hardening sealant to the screws to indi-cate that tuning is complete.Note:Tuning the attached connector before installing the cable is acceptable, since uncoiling and installing has a neg-ligible effect on VSWR.This tuning will improve VSWR, but cannot be used to correct other system problems.Fine tun-ing of the connector may be done after installation.Andrew Corporation10500 West 153rd Street Orland Park, IL U.S.A.60462Telephone:708/349-3300FAX (U.S.A.):1-800/349-5444Customer Service, 24 hours:U.S.A.• Canada • Mexico:1-800/255-1479U.K.:0800 250055 Other Europe:+44 1592 782612Printed in U.S.A.7/01Copyright © 2001 by Andrew Corporation。
- 1、下载文档前请自行甄别文档内容的完整性,平台不提供额外的编辑、内容补充、找答案等附加服务。
- 2、"仅部分预览"的文档,不可在线预览部分如存在完整性等问题,可反馈申请退款(可完整预览的文档不适用该条件!)。
- 3、如文档侵犯您的权益,请联系客服反馈,我们会尽快为您处理(人工客服工作时间:9:00-18:30)。
眼”。
其高性能的网络视频处理芯片和H264高效视频编码,以及最新的双码流技术保证了不同带宽的需求。
不再需要电脑的支持和繁琐的安装,您只需要一根电源接口和一根网线就能24小时不间断通过网络对住宅小区监控管理、办公楼、银行、商场等传统地进行监控管理。
云台360度旋转
录像
音频及对讲
夜视功能
动态码率
报警
手机,网页,客户端多种观看方式
1.1、观看推荐配置
■操作系统:Microsoft WindowsXP SP2及以上
■ CPU:1.6G以上的相关配置
■浏览器:Internet Explorer 6以上,不支持火狐,谷歌浏览器。
■图像插件:ActiveX (无须做任何非安全设置)
■显示器分辨率建议设置为1024×768
1.2、设备组网图
注意事项局域网中只允许一个路由器,不允许嵌套路由器
以免外网不能正常观看。