浅析大型合成氨生产装置节能降耗途径
浅析合成氨工艺节能措施
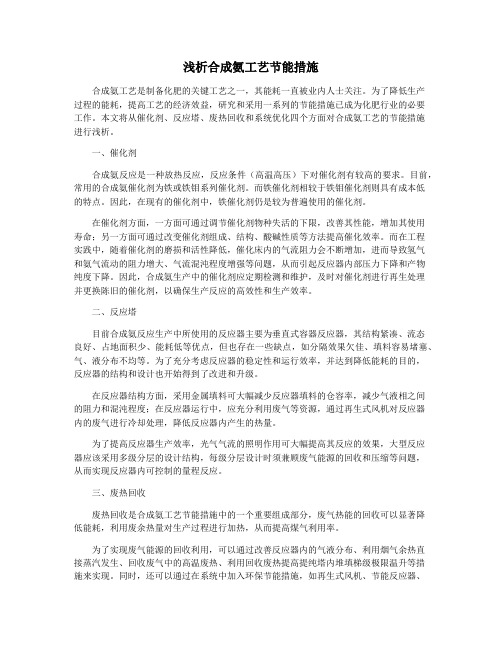
浅析合成氨工艺节能措施合成氨工艺是制备化肥的关键工艺之一,其能耗一直被业内人士关注。
为了降低生产过程的能耗,提高工艺的经济效益,研究和采用一系列的节能措施已成为化肥行业的必要工作。
本文将从催化剂、反应塔、废热回收和系统优化四个方面对合成氨工艺的节能措施进行浅析。
一、催化剂合成氨反应是一种放热反应,反应条件(高温高压)下对催化剂有较高的要求。
目前,常用的合成氨催化剂为铁或铁钼系列催化剂。
而铁催化剂相较于铁钼催化剂则具有成本低的特点。
因此,在现有的催化剂中,铁催化剂仍是较为普遍使用的催化剂。
在催化剂方面,一方面可通过调节催化剂物种失活的下限,改善其性能,增加其使用寿命;另一方面可通过改变催化剂组成、结构、酸碱性质等方法提高催化效率。
而在工程实践中,随着催化剂的磨损和活性降低,催化床内的气流阻力会不断增加,进而导致氢气和氨气流动的阻力增大、气流混沌程度增强等问题,从而引起反应器内部压力下降和产物纯度下降。
因此,合成氨生产中的催化剂应定期检测和维护,及时对催化剂进行再生处理并更换陈旧的催化剂,以确保生产反应的高效性和生产效率。
二、反应塔目前合成氨反应生产中所使用的反应器主要为垂直式容器反应器,其结构紧凑、流态良好、占地面积少、能耗低等优点,但也存在一些缺点,如分隔效果欠佳、填料容易堵塞、气、液分布不均等。
为了充分考虑反应器的稳定性和运行效率,并达到降低能耗的目的,反应器的结构和设计也开始得到了改进和升级。
在反应器结构方面,采用金属填料可大幅减少反应器填料的仓容率,减少气液相之间的阻力和混沌程度;在反应器运行中,应充分利用废气等资源,通过再生式风机对反应器内的废气进行冷却处理,降低反应器内产生的热量。
为了提高反应器生产效率,光气气流的照明作用可大幅提高其反应的效果,大型反应器应该采用多级分层的设计结构,每级分层设计时须兼顾废气能源的回收和压缩等问题,从而实现反应器内可控制的量程反应。
三、废热回收废热回收是合成氨工艺节能措施中的一个重要组成部分,废气热能的回收可以显著降低能耗,利用废余热量对生产过程进行加热,从而提高煤气利用率。
浅析合成氨工艺节能措施

浅析合成氨工艺节能措施合成氨是一种重要的化工原料,广泛用于制造化肥、塑料、合成纤维等产品。
目前,合成氨的生产过程中存在能耗高、资源浪费等问题,因此需要采取一系列的节能措施来提高生产效率,降低生产成本。
本文将就合成氨工艺的节能措施进行浅析。
一、提高合成氨转化率合成氨的转化率是指在合成氨反应中氮气和氢气的利用率,转化率越高,氨气的产量就越高,单位能耗就越低。
提高合成氨的转化率是节能减排的重要途径之一。
为了提高合成氨的转化率,可以采取以下措施:1. 优化催化剂催化剂是合成氨反应的关键,优化催化剂能够提高反应速率,降低反应温度,从而提高转化率。
可以采用高活性的催化剂,增加催化剂的使用寿命,减少更换频率,降低生产成本。
2. 控制反应条件在合成氨反应中,温度、压力等反应条件对转化率有着重要影响。
通过调节反应条件,可以提高反应效率,降低单位能耗。
3. 净化原料气原料气中的杂质会影响催化剂的活性,降低转化率。
在合成氨生产中,需要对原料气进行净化,去除氮气和氢气中的杂质,保持催化剂的活性,提高转化率。
二、优化能源利用在合成氨生产过程中,燃料消耗是比较大的一部分能源消耗,因此需要优化能源利用,降低燃料消耗,提高能源利用率。
可以采取以下措施:1. 余热利用合成氨生产过程中会产生大量的余热,可以通过余热回收系统将余热用于蒸汽生产、发电等用途,减少对外部能源的依赖,降低生产成本。
2. 高效燃料选择高效、清洁的燃料,如天然气、甲烷等,降低燃料的消耗,减少对能源资源的依赖,降低环境污染。
3. 节能设备引进节能设备,如高效的换热器、蒸汽轮机等,提高能源利用率,降低能源消耗。
三、提高生产装置的运行稳定性和可靠性合成氨生产过程中,生产装置的运行稳定性和可靠性对节能减排至关重要。
只有保证生产装置的稳定运行,才能够提高生产效率,降低能耗。
可以采取以下措施:1. 定期检修对生产装置进行定期检修,维护设备的完好性,减少设备故障,提高设备的可靠性。
浅析合成氨工艺节能措施

浅析合成氨工艺节能措施1. 引言1.1 研究背景合成氨是一种重要的化工产品,广泛应用于农业和工业领域。
随着社会经济的发展和人们对资源利用效率的要求越来越高,合成氨工艺节能措施成为研究的热点之一。
在合成氨生产过程中,能源消耗大、设备复杂、工艺流程繁琐,因此如何有效减少能源消耗,提高生产效率,已成为工程技术人员急需解决的问题之一。
当前,我国合成氨工业正处于转型升级的关键时期,节能减排已成为企业的必修课。
研究合成氨工艺的节能措施具有重要的现实意义。
本文旨在通过对合成氨生产工艺的概述,以及对节能措施的分析和探讨,探讨如何在合成氨生产中实施节能措施,提高工艺设备的能源利用效率,降低生产成本,促进我国合成氨工业的可持续发展。
1.2 研究目的本文旨在探讨合成氨工艺节能措施的相关问题,通过对合成氨生产工艺的概述和各种节能措施的分析,旨在为工程技术人员提供一些有益的启示和参考。
具体来说,本研究旨在通过优化催化剂配方、改进循环系统、提高装置热效率和优化工艺操作等方式,探讨如何在合成氨生产过程中降低能耗,提高生产效率,减少资源浪费,实现可持续发展。
通过本研究的展开,希望可以为合成氨工艺的节能改造提供一些实用的技术和经验,促进我国化工行业节能减排工作的开展,为环保和可持续发展贡献一份力量。
1.3 研究意义合成氨是一种重要的化工产品,广泛应用于农业、医药、化肥等领域。
在当前能源紧缺和环境污染日益严重的情况下,合成氨工艺的节能措施显得尤为重要。
通过对合成氨工艺的节能研究,可以有效降低生产成本,减少能源消耗,减少排放物,提高工艺效率,从而实现可持续发展的目标。
合成氨工艺的节能研究对于推动我国化工产业的可持续发展具有重要意义。
随着我国经济的不断发展,合成氨工业正处于快速发展阶段,然而高能耗、高排放的问题亟待解决。
通过对节能措施的研究,可以有效提升合成氨工业的生产效率,降低生产成本,减少对环境的影响,提高企业的竞争力,从而实现可持续发展。
合成氨工业节能减排的分析

合成氨工业节能减排的分析合成氨是一种用途广泛的化学品,在肥料、塑料、药品等多个领域都有重要的应用。
然而,合成氨的生产过程却会带来大量的能耗和碳排放。
因此,进行合成氨工业的节能减排是非常必要和重要的。
首先,我们需要分析合成氨工业节能减排的现状和挑战。
目前,合成氨的主要生产方法是哈柏-博仑过程(Haber-Bosch Process),该过程通过将氢气和氮气在高温高压条件下反应得到合成氨。
然而,这个过程的主要能耗是氢气的制备,而氢气的制备则依赖于化石燃料的消耗,导致大量的碳排放。
此外,合成氨工业还有其他能耗,例如电力消耗、冷却水消耗等。
为了节能减排,我们可以采取以下措施。
首先,改进哈柏-博仑过程本身。
通过改进反应器和催化剂,提高合成氨的产率,从而减少氢气的消耗。
其次,优化氢气的制备过程。
可以采用新型的氢气制备技术,如水电解、生物制氢等,减少对化石燃料的依赖,从而减少碳排放。
此外,还可以通过烟气余热回收、蒸馏废热回收等措施来提高能量利用效率,减少能耗。
除了上述技术措施,还可以采取管理措施来节能减排。
例如,优化生产计划和调度,合理利用产能,减少闲置和能耗;通过培训和教育,提高员工的环保意识和操作技能,减少不必要的能耗和浪费;加强能源管理和监测,及时发现和解决能源浪费问题等。
此外,政府的政策支持也是促进合成氨工业节能减排的重要因素。
政府可以提供财政补贴和税收优惠,鼓励企业采用节能减排措施;出台相关的法规和标准,限制能耗和碳排放;建立监测和监管体系,加强对合成氨工业的能耗和排放的监管等。
然而,合成氨工业节能减排面临一些挑战。
首先,新技术的应用和推广需要投入大量的资金和时间,企业可能面临负担压力;其次,由于合成氨工业涉及多个环节和多个企业,要实现全行业的节能减排需要协调和合作,可能存在协调成本和困难。
综上所述,合成氨工业节能减排是一项重要而复杂的任务,需要从技术、管理和政策等多个方面综合考虑。
通过改进生产工艺、提高能源利用效率、管理能耗和监管等措施,可以有效减少合成氨工业的能耗和碳排放,实现可持续发展。
浅析合成氨工艺节能措施

浅析合成氨工艺节能措施合成氨工艺是工业领域中非常重要的一种化工过程,它是制造化肥和其他化学品的关键步骤。
在合成氨工艺中,大量的能源和原材料被消耗,因此如何降低能耗和提高节能效果是非常重要的。
本文将对合成氨工艺中的节能措施进行浅析,探讨在工业生产中如何更加科学、有效地利用能源资源。
合成氨工艺的节能措施可以从多个方面入手,包括原料利用率的提高、设备单位能耗的降低、新技术的应用等方面。
优化原料利用率是节能降耗的重中之重。
通过减少原料的损耗和提高原料的利用率,可以有效地减少生产过程中的能源消耗和资源浪费。
降低设备单位能耗是节能措施中的另一个重要方面。
通过改进设备结构、提高设备运行效率、优化工艺流程等措施,可以有效地降低设备的能耗水平,从而实现节能降耗的目标。
还可以通过应用新技术,如膜分离技术、催化剂技术等,来改善合成氨工艺的能耗状况,提高生产效率,降低生产成本。
对于合成氨工艺的原料利用率提高,可以采取的措施包括:一是加强原料的预处理工作,通过精选原料、改进原料的储存和运输方式,减少原料的损耗和浪费。
二是完善反应条件,通过优化反应条件、提高反应的选择性和效率,实现原料的充分利用。
三是推广循环利用技术,通过回收利用反应产物或废气废热,实现能源的再利用,减少资源的浪费。
通过以上措施的综合应用,可以有效地提高原料的利用率,降低生产过程中的能耗消耗和资源浪费。
在降低设备单位能耗方面,可以采取的措施包括:一是优化设备结构,通过改进设备设计和制造工艺,提高设备的密封性、传热效率和运行稳定性,减少设备的能耗消耗。
二是提高设备运行效率,通过改善设备的运行条件、加强设备的维护管理,保持设备的良好状态,提高设备的运行效率,降低设备的能耗水平。
三是优化工艺流程,采用先进的控制技术和优化的操作策略,实现设备的合理调度和运行,降低设备的能耗消耗。
合成氨工业节能减排的分析
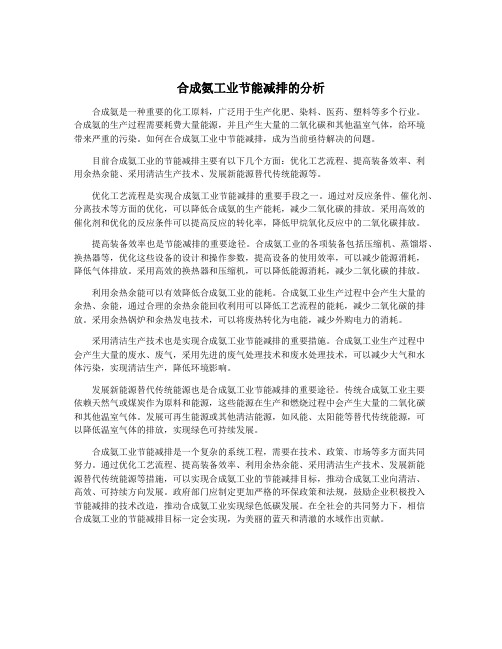
合成氨工业节能减排的分析合成氨是一种重要的化工原料,广泛用于生产化肥、染料、医药、塑料等多个行业。
合成氨的生产过程需要耗费大量能源,并且产生大量的二氧化碳和其他温室气体,给环境带来严重的污染。
如何在合成氨工业中节能减排,成为当前亟待解决的问题。
目前合成氨工业的节能减排主要有以下几个方面:优化工艺流程、提高装备效率、利用余热余能、采用清洁生产技术、发展新能源替代传统能源等。
优化工艺流程是实现合成氨工业节能减排的重要手段之一。
通过对反应条件、催化剂、分离技术等方面的优化,可以降低合成氨的生产能耗,减少二氧化碳的排放。
采用高效的催化剂和优化的反应条件可以提高反应的转化率,降低甲烷氧化反应中的二氧化碳排放。
提高装备效率也是节能减排的重要途径。
合成氨工业的各项装备包括压缩机、蒸馏塔、换热器等,优化这些设备的设计和操作参数,提高设备的使用效率,可以减少能源消耗,降低气体排放。
采用高效的换热器和压缩机,可以降低能源消耗,减少二氧化碳的排放。
利用余热余能可以有效降低合成氨工业的能耗。
合成氨工业生产过程中会产生大量的余热、余能,通过合理的余热余能回收利用可以降低工艺流程的能耗,减少二氧化碳的排放。
采用余热锅炉和余热发电技术,可以将废热转化为电能,减少外购电力的消耗。
采用清洁生产技术也是实现合成氨工业节能减排的重要措施。
合成氨工业生产过程中会产生大量的废水、废气,采用先进的废气处理技术和废水处理技术,可以减少大气和水体污染,实现清洁生产,降低环境影响。
发展新能源替代传统能源也是合成氨工业节能减排的重要途径。
传统合成氨工业主要依赖天然气或煤炭作为原料和能源,这些能源在生产和燃烧过程中会产生大量的二氧化碳和其他温室气体。
发展可再生能源或其他清洁能源,如风能、太阳能等替代传统能源,可以降低温室气体的排放,实现绿色可持续发展。
合成氨工业节能减排是一个复杂的系统工程,需要在技术、政策、市场等多方面共同努力。
通过优化工艺流程、提高装备效率、利用余热余能、采用清洁生产技术、发展新能源替代传统能源等措施,可以实现合成氨工业的节能减排目标,推动合成氨工业向清洁、高效、可持续方向发展。
合成氨行业能耗现状与主要节能途径

合成氨行业能耗现状与主要节能途径摘要:合成氨工业是基础化学工业的重要组成部分,在国民经济中占有重要地位。
氨是化学工业的重要原料之一,具有非常广泛的用途。
我国合成氨技术发展迅速,在工艺技术和节能降耗能方面都有重大进步,我国氨产量排名世界第一。
文章重点就合成氨行业能耗现状与主要节能途径进行研究分析,以供参考和借鉴。
关键字:合成氨;能耗现状;节能途径;分析引言现阶段国内较早引进的一批大型合成氨生产装置大多经过一次或几次扩能技改,与当今先进的装置相比,能耗偏高主要受限于主线工艺流程的差别,再进行大规模的技改技革来实现节能降耗已极不经济,只有在现有装置基础上实施小的革新及开停车过程、正常运行中进行优化操作来实现节能降耗。
1合成氨的意义合成氨工业是基本无机化工之一,氨是化肥工业和基本有机化工的主要原料。
合成氨工业在二十世纪初期形成,开始用氨作火炸药工业的原料,为战争服务;第一次世界大战结束后,转向为农业、工业服务,农业对化肥的需求是合成氨工业发展的持久推动力。
世界人口不断增长给粮食供应带来压力,而施用化学肥料是农业增产的有效途径。
氨水(即氨的水溶液)和液氨体本身就是一种氮肥;农业上广泛采用的尿素、硝酸铵、硫酸铵等固体氮肥和磷酸铵、硝酸磷肥等复合肥料,都是以合成氨加工生产为主。
用于生产各种氮肥的氨占氨总产量的80%-90%,氨和这些含氮化合物是生产燃料、炸药、医药、合成纤维、塑料的重要原料。
硝酸、各种含氮的无机盐及有机中间体、磺胺药、聚氨酯、聚酰胺纤维和丁腈橡胶等都需直接以氨为原料,经历了发明阶段、技术推广阶段、原料结构变迁阶段、单系列大型化自动化阶段和节能降耗阶段。
历时近一个世纪,目前合成氨技术正处于节能降耗阶段。
2合成氨的工艺流程2.1原料气的制取合成氨的原料是煤、天然气、重油、石脑油和焦碳等,无论何种原料均可用来表示,这些原料在高温下与水蒸气作用生成以氢和一氧化碳为主体的合成氨原料气,煤气化法是我国合成氨的主要制气方法。
合成氨装置节能降耗控制措施
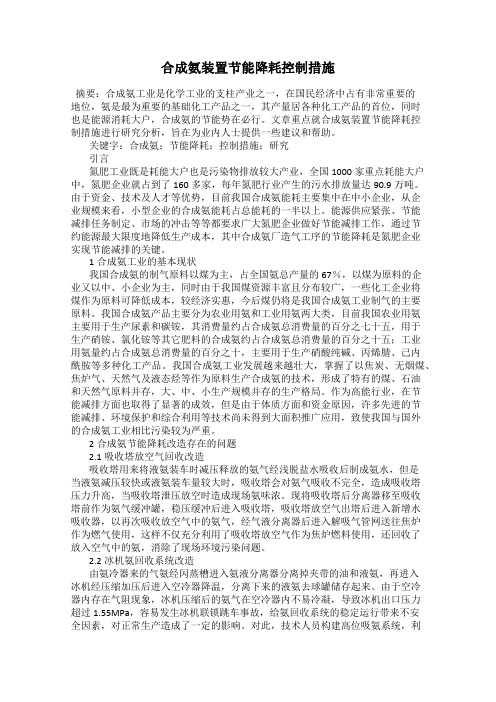
合成氨装置节能降耗控制措施摘要:合成氨工业是化学工业的支柱产业之一,在国民经济中占有非常重要的地位,氨是最为重要的基础化工产品之一,其产量居各种化工产品的首位,同时也是能源消耗大户,合成氨的节能势在必行。
文章重点就合成氨装置节能降耗控制措施进行研究分析,旨在为业内人士提供一些建议和帮助。
关键字:合成氨;节能降耗;控制措施;研究引言氮肥工业既是耗能大户也是污染物排放较大产业,全国1000家重点耗能大户中,氮肥企业就占到了160多家,每年氮肥行业产生的污水排放量达90.9万吨。
由于资金、技术及人才等优势,目前我国合成氨能耗主要集中在中小企业,从企业规模来看,小型企业的合成氨能耗占总能耗的一半以上。
能源供应紧张、节能减排任务制定、市场的冲击等等都要求广大氮肥企业做好节能减排工作,通过节约能源最大限度地降低生产成本,其中合成氨厂造气工序的节能降耗是氮肥企业实现节能减排的关键。
1合成氨工业的基本现状我国合成氨的制气原料以煤为主,占全国氨总产量的67%,以煤为原料的企业又以中、小企业为主,同时由于我国煤资源丰富且分布较广,一些化工企业将煤作为原料可降低成本,较经济实惠,今后煤仍将是我国合成氨工业制气的主要原料。
我国合成氨产品主要分为农业用氨和工业用氨两大类,目前我国农业用氨主要用于生产尿素和碳铵,其消费量约占合成氨总消费量的百分之七十五,用于生产硝铵、氯化铵等其它肥料的合成氨约占合成氨总消费量的百分之十五;工业用氨量约占合成氨总消费量的百分之十,主要用于生产硝酸纯碱、丙烯腈、己内酰胺等多种化工产品。
我国合成氨工业发展越来越壮大,掌握了以焦炭、无烟煤、焦炉气、天然气及液态烃等作为原料生产合成氨的技术,形成了特有的煤、石油和天然气原料并存,大、中、小生产规模并存的生产格局。
作为高能行业,在节能减排方面也取得了显著的成效,但是由于体质方面和资金原因,许多先进的节能减排、环境保护和综合利用等技术尚未得到大面积推广应用,致使我国与国外的合成氨工业相比污染较为严重。
浅析合成氨工艺节能措施

浅析合成氨工艺节能措施1. 引言1.1 合成氨工艺的重要性合成氨是一种重要的化工原料,被广泛用于制造化肥、农药、燃料等产品。
合成氨工艺的重要性在于其在现代社会中的广泛应用,为农业生产、工业生产以及能源生产提供了必要的原料。
合成氨不仅可以提高农作物的产量,还可以满足工业生产对氮肥的需求,同时也可以用作燃料和化工原料。
合成氨的生产工艺一直是工业界关注的焦点之一,因为其生产过程中会消耗大量的能源。
采取节能措施对于合成氨工艺的持续发展至关重要。
通过提高能源利用效率,优化设备设计,改进余热回收系统以及应用先进的控制技术,可以有效降低合成氨生产过程中的能源消耗,实现更加高效、环保的生产过程。
合成氨工艺的重要性体现在其在各个领域的广泛应用以及对现代生产体系的贡献。
为了实现可持续发展,节能减排已经成为全球工业界的共同目标,合成氨工艺的节能措施也需要不断完善和深化。
1.2 能源消耗与节能意义合成氨工艺是工业生产中非常重要的一项工艺,其生产过程需要消耗大量的能源。
能源消耗不仅会增加生产成本,还会对环境造成负面影响。
节能对于合成氨工艺来说至关重要。
合成氨工艺的能源消耗主要来自于压缩、制冷和反应等环节。
压缩机是能源消耗的重要组成部分,压缩机效率的提高可以有效降低能源消耗。
反应器设计的优化和余热回收系统的改进也能有效减少能源消耗。
采用先进的控制技术可以使工艺运行更加稳定高效,也可以进一步减少能源消耗。
节能在合成氨工艺中具有重要的意义,不仅可以降低生产成本、提高生产效率,还可以减少能源消耗对环境的负面影响。
未来的发展方向应当是在不断提高工艺效率的进一步优化能源利用,实现合成氨工艺的可持续发展。
通过不断探索创新,合成氨工艺节能措施将有更广阔的发展前景。
2. 正文2.1 合成氨工艺中的能源消耗主要来源合成氨工艺中最主要的能源消耗来源是氮气的制备。
在合成氨的过程中,氮气与氢气通过催化剂反应生成氨气,而氮气的制备通常涉及空分设备和氧氮分离设备,这些设备消耗大量能源。
合成氨工业节能减排的分析

合成氨工业节能减排的分析合成氨工业是一项重要的工业生产过程,它主要用于生产氮、磷、钾等肥料。
然而,合成氨工业的生产过程会消耗大量的能源,同时会产生大量的二氧化碳排放和废水废气。
如何实现合成氨工业的节能减排,是当前合成氨生产企业必须面对和解决的重要问题。
合成氨工业的节能减排主要可以从以下几个方面进行分析和实施:第一,优化反应过程。
合成氨生产的主要反应是通过加热高压氢气和氮气,在催化剂的作用下生成氨气。
当前,可以在反应过程中采用节能催化剂,比如氯化铯、氯化铷等物质,以提高反应速率,缩短反应时间,并减少能源消耗。
此外,在优化催化剂的同时,需注意控制反应的温度和压力,以确保反应效率和质量。
第二,改进热力学循环。
在合成氨工业中,氨气在反应过程中会产生大量的热能,而当前大多数企业采用的是中间循环冷却系统来回收这种能量,如果能够引入更成熟的热力学循环联合发电技术,不仅可以实现能源的高效利用,还可以减少二氧化碳排放量。
第三,加强废水、废气治理。
合成氨工业的生产过程中,会产生大量的废水和废气,这些废水和废气中的有害物质会对环境造成严重的污染。
因此,企业需采取授权的治理措施,对废水废气进行收集、处理和排放。
比如,可以使用膜分离技术和化学吸收等方法对废水进行处理,以达到要求的排放标准。
第四,推广可再生能源。
建立可再生能源发电站,将可再生能源与合成氨工业的过程相结合,实现电力和热力的供应,降低污染以及减少能源消耗。
综上所述,合成氨工业的节能减排需要企业采取措施,采用新技术和方法,实现生产过程中的高效利用能源,减少二氧化碳排放,加强废水、废气等污染物的治理等方面开展工作。
这些措施不仅有助于企业实现可持续发展,还有利于环保和资源保护,促进经济与环境的协调发展。
浅析合成氨工艺节能措施

浅析合成氨工艺节能措施合成氨是一种重要的化工原料,广泛应用于农业、化肥、医药、合成纤维等领域。
合成氨的生产过程是一种耗能较大的化工工艺,因此节能减排一直是合成氨生产过程中关注的问题之一。
本文将从合成氨工艺的节能方面进行分析和讨论。
一、合成氨工艺的原理和流程简介合成氨是由氮气和氢气在催化剂的作用下经过一系列反应而成,其生产过程一般包括氢气制备、氮气净化、氮气和氢气混合、合成氨反应和提取等步骤。
氢气制备是合成氨生产中最耗能的步骤之一,而氮气的净化和氢气的制备都需要大量的能源和资源投入。
节能减排在合成氨工艺中显得尤为重要。
二、合成氨工艺的节能措施1. 提高氢气制备的能源利用率氢气是合成氨的重要原料之一,其制备过程需要大量的能源投入。
为了提高氢气制备的能源利用率,可以采用先进的氢气制备技术,例如采用高效的蒸汽重整工艺、改进煤气化工艺、提高蒸汽催化重整的热效率等方法。
还可以利用余热和余压进行能量回收,将废热废气转化为加热和蒸汽产生等能量,从而降低能源消耗。
2. 氮气净化和氢气制备过程中的催化剂优化在氮气净化和氢气制备过程中,催化剂的选择和使用对能源消耗和生产效率有着重要的影响。
通过优化催化剂的制备工艺、配方和结构设计,可以提高催化剂的活性和稳定性,降低反应温度和压力,减少能源消耗。
还可以通过催化剂再生和循环利用,延长催化剂的使用寿命,减少对资源和能源的消耗。
3. 合成氨反应过程的优化合成氨反应是合成氨工艺中能耗较大的环节之一,为了降低合成氨反应的能耗,可以采用先进的反应器设计和控制技术,提高反应器的稳定性和效率。
还可以优化反应条件,如提高催化剂的活性和选择性、减少反应温度和压力、优化气体流动和混合方式等,从而降低合成氨反应的能耗。
4. 提高合成氨提取的能源利用率合成氨提取是合成氨工艺中的最后一个环节,其能源消耗主要集中在脱气和脱硫过程中。
为了提高合成氨提取的能源利用率,可以采用先进的脱气和脱硫技术,如采用低温吸附脱附、多级脱气和脱硫、利用膜分离和超临界流体萃取等技术,降低能源消耗,提高提取效率。
合成氨装置节能降耗措施分析
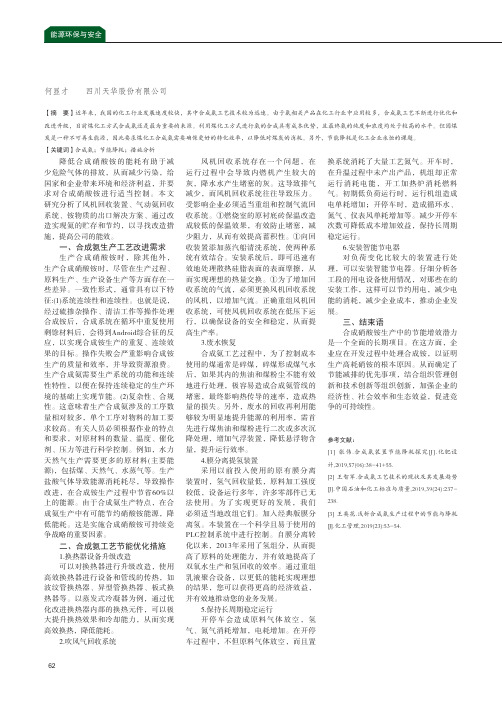
降低合成硝酸铵的能耗有助于减少危险气体的排放,从而减少污染,给国家和企业带来环境和经济利益,并要求对合成硝酸铵进行适当控制。
本文研究分析了风机回收装置、气动氨回收系统、铵物质的出口解决方案、通过改造实现氦的贮存和节约,以寻找改造措施,提高公司的能效。
一、合成氨生产工艺改进需求生产合成硝酸铵时,除其他外,生产合成硝酸铵时,尽管在生产过程、原料生产、生产设备生产等方面存在一些差异。
一致性形式,通常具有以下特征:(1)系统连续性和连续性。
也就是说,经过硫掺杂操作、清洁工作等操作处理合成铵后,合成系统在循环中重复使用剩馀材料后,会得到Android综合征的反应,以实现合成铵生产的重复、连续效果的目标。
操作失败会严重影响合成铵生产的质量和效率,并导致资源浪费。
生产合成氨需要生产系统的功能和连续性特性,以便在保持连续稳定的生产环境的基础上实现节能。
(2)复杂性、合规性。
这意味着生产合成氨涉及的工序数量相对较多,单个工序对物料的加工要求较高。
有关人员必须根据作业的特点和要求,对原材料的数量、温度、催化剂、压力等进行科学控制。
例如,水力天然气生产需要更多的原材料(主要能源),包括煤、天然气、水蒸气等。
生产盐酸气体导致能源消耗耗尽,导致操作改进,在合成铵生产过程中节省60%以上的能源。
由于合成氨生产特点,在合成氨生产中有可能节约硝酸铵能源,降低能耗。
这是实施合成硝酸铵可持续竞争战略的重要因素。
二、合成氨工艺节能优化措施1.换热器设备升级改造可以对换热器进行升级改造,使用高效换热器进行设备和管线的传热,如波纹管换热器、异型管换热器、板式换热器等。
以蒸发式冷凝器为例,通过优化改进换热器内部的换热元件,可以极大提升换热效果和冷却能力,从而实现高效换热,降低能耗。
2.吹风气回收系统风机回收系统存在一个问题,在运行过程中会导致内燃机产生较大的灰,降水水产生堵塞的灰。
这导致排气减少,而风机回收系统往往导致压力。
受影响企业必须适当重组和控制气流回收系统。
合成氨生产过程的节能降耗分析
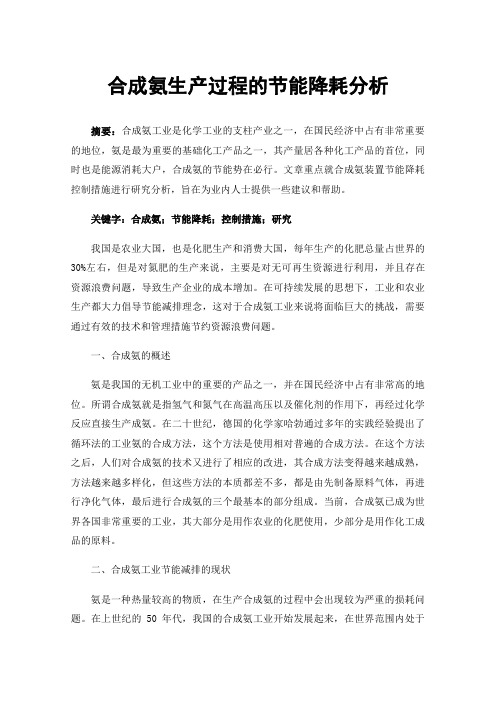
合成氨生产过程的节能降耗分析摘要:合成氨工业是化学工业的支柱产业之一,在国民经济中占有非常重要的地位,氨是最为重要的基础化工产品之一,其产量居各种化工产品的首位,同时也是能源消耗大户,合成氨的节能势在必行。
文章重点就合成氨装置节能降耗控制措施进行研究分析,旨在为业内人士提供一些建议和帮助。
关键字:合成氨;节能降耗;控制措施;研究我国是农业大国,也是化肥生产和消费大国,每年生产的化肥总量占世界的30%左右,但是对氮肥的生产来说,主要是对无可再生资源进行利用,并且存在资源浪费问题,导致生产企业的成本增加。
在可持续发展的思想下,工业和农业生产都大力倡导节能减排理念,这对于合成氨工业来说将面临巨大的挑战,需要通过有效的技术和管理措施节约资源浪费问题。
一、合成氨的概述氨是我国的无机工业中的重要的产品之一,并在国民经济中占有非常高的地位。
所谓合成氨就是指氢气和氮气在高温高压以及催化剂的作用下,再经过化学反应直接生产成氨。
在二十世纪,德国的化学家哈勃通过多年的实践经验提出了循环法的工业氨的合成方法,这个方法是使用相对普遍的合成方法。
在这个方法之后,人们对合成氨的技术又进行了相应的改进,其合成方法变得越来越成熟,方法越来越多样化,但这些方法的本质都差不多,都是由先制备原料气体,再进行净化气体,最后进行合成氨的三个最基本的部分组成。
当前,合成氨已成为世界各国非常重要的工业,其大部分是用作农业的化肥使用,少部分是用作化工成品的原料。
二、合成氨工业节能减排的现状氨是一种热量较高的物质,在生产合成氨的过程中会出现较为严重的损耗问题。
在上世纪的50年代,我国的合成氨工业开始发展起来,在世界范围内处于生产总量第一的位置,但是我国的很多小型合成氨企业受到生产消耗较大的困扰,基本在44-67GJ/t之间,相较于国外的平均28GJ/t这个水平存在很大的差距。
为此,我国诸多学者开始加强研究,发现在合成氨工业生产中可以通过诸多的手段实现节能减排的目标,目前主要是受到技术因素的影响,导致节能减排工作在合成氨生产中没有得到普及,需要国家在制度和技术上作出更多努力,让企业取得良好效益的同时,减少污染物的排放。
浅析合成氨生产过程中的节能与降耗

2019年08月续工序的原料气增加,提高LNG 产量,降低生产成本。
3.3缺点(1)富氢尾气与焦炉煤气相比,氢气含量高,热值低,在其他用户使用过程中须及时进行用量大调整,否则会导致加热量不足,继而引发一系列问题。
(2)富氢尾气中氮气含量较焦炉煤气高,在燃烧温度较高时,易产生NOx 等污染气体,需要合理控制富氢尾气使用量。
(3)富氢尾气对TSA 吸附塔再生完毕后,塔内残留的富氢尾气会随原料煤气进入后续工序,在后续工序中,这一部分富氢尾气会起到稀释原料起的作用,甲烷化反应热减少,导致系统温度降低。
(4)塔内残留的富氢尾气进入离心压缩机,由于氢气含量高,分子质量小,容易引起离心压缩机防喘振点的波动,导致后续精脱硫、甲烷化工段原料其波动,不利于生产稳定。
4富氢尾气制氢气4.1工艺介绍富氢尾气首先进入PSA 工序吸附塔,自下而上经过吸附床层,气体中的烷烃、氮气、等被塔内吸附剂吸附,氢气等组分从吸附塔顶部连续排出至产品氢气缓冲罐,压力≥1.75MPa 送氢气净化工序。
先进入粗氢加热器,将粗氢气的温度提高至60~80℃,再进入脱氧塔。
在脱氧塔中装填的新型钯催化剂的催化下,氧和氢反应生成水,然后经冷却器冷却至常温,此时反应生成的部分水分微量饱和析出,,再进入等压TSA 干燥系统。
经干燥后的产品氢即可达到纯度99.999%、氧含量小于2ppm 、露点低于-65℃的氢气。
4.2优点富氢尾气相对于焦炉煤气,更加洁净,无苯、萘、焦油、H 2S 等杂质。
同时富氢尾气中氢气体积含量可达到90%左右,需脱除的杂质含量少,尤其是富氢尾气中基本没有氧,可为氢气提纯降低能耗,使制氢催化剂和设备的寿命大幅度延长,降低生产成本。
4.3缺点气源同样受焦炉煤气制LNG 生产制约,在前道工序工况调整或异常时,一方面富氢尾气的组成或发生变化,甲烷含量波动较大;另一方面气体压力也会出现波动。
此时如果制氢工况调整不及时,会导致氢气纯度受影响。
5结语焦炉煤气制LNG 工艺中深冷液化分离出的富氢尾气,虽然是一种洁净能源和原料,但若在使用过程中控制不好,会影响到各系统的热稳定性和吸附、反应效果,只有对其严加管控,才能保证整个系统的稳定运行。
合成氨装置节能降耗探究

有效措施.
作者简介:张伟(
1982 年—),男,宁夏 银 川 人,
2005 年 毕 业 于 宁 夏 大
学应用化学专业,工程师,现主要从事合成氨生产技术工作.
第6期
39
张 伟 合成氨装置节能降耗探究
图 1 合成氨装置工艺流程
注:
1—氨合成塔;
2—开工加热炉;
3— 合成汽包;
4—蒸汽过热器;
5—合成气余热回收器;
6—锅炉给水预热器;
7—热交换 器;
8—水
冷器;
9—冷交 换 器;
10—一 级 氨 冷 器;
11—二 级 氨 冷 器;
12—氨 分 离 器;
13—氨 闪 蒸 罐;
14—氨 产 品 泵;
15—第 二 氨 压 缩 机;
l
ue
ynga
ge
gys
ywo
do
i:
10.
3969/
i
s
sn.
1004-8901.
2019.
06.
011
j.
企业的生存发 展 离 不 开 经 济 效 益 提 高,降 低 生
产成本、节能降耗 是 提 高 经 济 效 益 的 有 效 手 段. 企
业在 生 产 阶 段,优 化 工 艺 指 标、生 产 管 理 精 细 化 是
l
z
ed,andme
a
sur
e
ssucha
sr
educ
i
ngt
henumbe
ro
fope
r
a
t
i
ngs
sc
omp
r
e
s
s
o
合成氨生产造气工段能耗分析与节能途径探究

合成氨生产造气工段能耗分析与节能途径探究针对合成氨生产造气工段能耗分析与节能途径,结合理论实践,在分析合成氨生产造气工段主要能耗的基础上,分析了实现节能的主要途径。
得出采用蒸汽驱动空气鼓风机、应用自动加煤技术和自动出渣技术、应用专用高效炉箅、应用过热蒸汽入炉制气技术降低合成氨生产造气工段能耗,提高经济效益关键的结论,希望对相关单位有一定帮助。
标签:合成氨;生产造气工段;能耗分析;节能途径1 合成氨生产造气工段能耗分析目前我国绝大多数企业在合成氨操作中,以煤为主要原料。
合成氨的能耗普遍在58.62GJ/t以上,大约是理论能耗21.27GJ/t的2.8倍左右,和美国的24.36GJ/t,德国18.97GJ/t相比具有非常大的节能潜力。
而合成氨厂能耗最大的物料为原料煤,仅仅原料煤一项,就占据合成氨总能耗的60%以上,原料煤的采购成本占合成氨总成本的45.6%左右。
因此,如果可以通过一系列科学先进措施和技术来降低原料煤的损耗量,既能有效减低能耗,还能大幅度降低合成氨的成本。
2 合成氨生产造气工段节能途径分析(1)采用蒸汽驱动空气鼓风机。
通过蒸汽透平的方法来取代传统电机来推动造气用空气鼓风机运行,和传统电机驱动相比,蒸汽驱动具有投资小,升级改造方便,且节能效益明显的优点。
比如:在合成氨生产造气工段可利用吹风气余热来回收可副产中压过热蒸汽,最常见的中压过热蒸汽有两种,一种是2.47MPa,最高气温可达350℃,另一种是3.84MPa,最高溫度可达400℃[1]。
通过中压过热蒸汽来驱动气化系统来驱动鼓风机,被压出来的低压过热蒸汽,可直接应用在造气炉制气上,从而达到一举两得的目的,既能有效节约电能的消耗,而且得到的低压过热蒸汽还能带来节能降耗的效果。
具体应用流程如图1所示:(2)充分应用自动加煤技术。
自动加煤技术是在原来造气炉加料口增设机电一体化控制系统,来取代传统人工加煤,应用实例表明,通过应用此项技术,可为气化生产和操作带来便利条件。
合成氨装置节能降耗探究

合成氨装置节能降耗探究摘要:2017年国家对企业环保提出更高要求,我公司也相应的制定更高的排污指标要求。
合成氨工艺主要含氨废水排出设备为排放系统的S6,为使废水达到规定的氨氮值再进行排放,需要定期进行蒸汽煮洗,合格后排放至中水污水池,这样可以减轻中水事故水池的工作压力。
且采取了在半负荷运行情况下,降低合成气压缩机和氨冷冻机运行台数、减少循环水用量等措施,所以,本文就合成氨装置节能降耗探究进行了研究。
关键词:合成氨;储存;危险特性;岗位安全;培训一、合成氨工艺技术概述合成氨工艺技术是一门很复杂的技术,包含很多门综合技术,其中有物理、化学、化工等等,是典型的无机化工专业的一部分。
2.1半水煤气的制取(以煤合成氨为例):向造气炉内加入煤,通入空气,让其燃烧升温,再间断通入蒸汽和空气,使蒸汽与炙热的碳发生反应生成H2和CO,空气中的O2被消耗掉,剩下N2,与此同时产生其它一些杂质性气体和粉尘,去除粉尘,回收余热,就得到半水煤气。
2.2原料气体的净化:主要是将半水煤气的硫脱去,然后经过变换,再将气体中少量的一氧化碳和二氧化碳脱去。
二、节能降耗1.燃料气系统优化在合成新系统合成氨生产中,燃料气是由本系统高压天然气、回收系统驰放气、合成老系统低压天然气和驰放气组成;燃料气的消耗主要是一段转化加热用的顶烧、烟烧燃料气为转化反应提供热量;其次是辅锅产汽所需要的天然气和为提高高压蒸汽过热度所需要天然气,所以节约燃料气也要从这几方面着手。
1.1合理控制水碳比,减少转化反应燃料气消耗减少一段炉蒸汽转化的热负荷就要降低转化反应的水碳比,降低水碳比不但降低了工艺蒸汽消耗量而且可有效地降低一段炉转化的热负荷,但是水碳比不是越低越好,因为过量的水蒸汽还是防止转化炉管析炭的重要手段。
所以要从实际情况出发,根据一段炉催化的效率,将水碳比控制在3.38—3.41左右,在全面评价经济效益的基础上确定转化反应的最优水碳比。
2.2依据一段炉出口残余在线监测参数,优化调整一段炉和压缩机参数在生产中,气矿输送的天然气组分经常发生变化,根据一段炉出口残余甲烷量参数AI-1A和原料气压缩机的负荷参数,及时调整天然气压缩机转速和一段炉出口温度参数,将一段炉的残余甲烷调控在<13.28%,以控制燃料气的消耗,减少转化燃料气的消耗量。
浅析合成氨节能减排

浅析合成氨节能减排摘要:近年来,由于企业生产成本增加,生产原材料的价格上涨,为了进一步提高企业经营利润,扩大企业生存空间,降低合成氨的成本和耗能迫在眉睫。
本文首先对合成氨的内涵和意义进行论述,然后通过对节能新系统的燃料气系统和蒸汽系统方面的节能改造分析,旨在降低合成氨在实际应用过程中消耗的能量,为企业提高经济效益,降低运行成本提供参考。
关键词:合成氨;新型系统;节能减排;优化操作1 合成氨节能减排的内涵和意义合成氨指在化工生产中,通过人工将氮和氢在高温度、高压力和相应催化行为的共同作用下,合成氨气的过程。
合成氨为广泛应用在现代化学工业中,是农业企业、化肥企业和有机化工企业中重要的生产原料。
合成氨节能减排意义重大。
首先受各种因素影响,近年来一些化工企业生产成本急剧增加,生产产品的利润不断缩小。
传统的合成氨智能达到国家相关规定的最低标准,不能为化工企业更新生产系统、优化生产结构提供较多帮助。
其次,合成氨的节能减排是顺应环境保护、节约生态能源的环境发展理念的需要。
环保事业一直是我国关注的重点,根据建设社会主义现代化建设的需要,生态环境建设是重要的建设部分。
目前我国合成氨的生产过程中,对蒸汽、燃料物和其他能源消耗非常巨大,同时对周围生活环境和空气质量造成了不同程度的污染。
最后,目前我国化工企业发展迅猛,在国际市场中的地位不可忽视,但我国对合成氨技术的研究却落后于部分发达国家。
这种现象的出现具有多种原因,比如我国对合成氨专业化技术人才的培养不足、对未来合成氨应用的广泛性认识不足等。
2 燃料气系统优化根据新系统合成氨的合成过程,其中系统根据高压转化系统、回收系统等对燃料气进行放气、回收气的操作。
一般在热能转化、能量提供、天然气提供和帮助锅炉产生汽化过程中消耗大量的燃料气。
为了减少在过程中对燃料气的使用,可以从以下几点方面进行节能:2.1合理控制水碳比率合理控制水碳比就是控制过程中的平均碳分子数量。
一般情况下,水碳比例具有严格的控制范围,常见范围在3.38-3.41左右。
合成氨生产过程的节能降耗分析
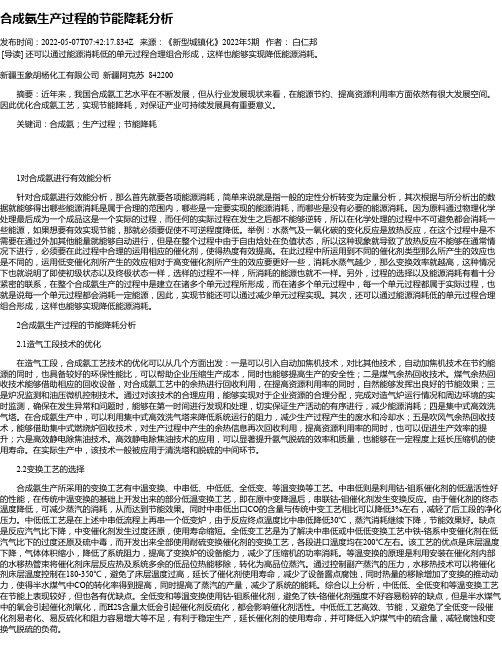
合成氨生产过程的节能降耗分析发布时间:2022-05-07T07:42:17.834Z 来源:《新型城镇化》2022年5期作者:白仁邦[导读] 还可以通过能源消耗低的单元过程合理组合形成,这样也能够实现降低能源消耗。
新疆玉象胡杨化工有限公司新疆阿克苏 842200摘要:近年来,我国合成氨工艺水平在不断发展,但从行业发展现状来看,在能源节约、提高资源利用率方面依然有很大发展空间。
因此优化合成氨工艺,实现节能降耗,对保证产业可持续发展具有重要意义。
关键词:合成氨;生产过程;节能降耗1对合成氨进行有效能分析针对合成氨进行效能分析,那么首先就要各项能源消耗,简单来说就是指一般的定性分析转变为定量分析,其次根据与所分析出的数据就能够得出哪些能源消耗是属于合理的范围内,哪些是一定要实现的能源消耗,而哪些是没有必要的能源消耗。
因为原料通过物理化学处理最后成为一个成品这是一个实际的过程,而任何的实际过程在发生之后都不能够逆转,所以在化学处理的过程中不可避免都会消耗一些能源,如果想要有效实现节能,那就必须要促使不可逆程度降低。
举例:水蒸气及一氧化碳的变化反应是放热反应,在这个过程中是不需要在通过外加其他能量就能够自动进行,但是在整个过程中由于自由焓处在负值状态,所以这种现象就导致了放热反应不能够在通常情况下进行,必须要在此过程中合理的运用相应的催化剂,使得热度有效提高。
在此过程中所运用到不同的催化剂类型那么所产生的效应也是不同的,运用低变催化剂所产生的效应相对于高变催化剂所产生的效应要更好一些,消耗水蒸气越少,那么变换效率就越高,这种情况下也就说明了即使初级状态以及终极状态一样,选样的过程不一样,所消耗的能源也就不一样。
另外,过程的选择以及能源消耗有着十分紧密的联系,在整个合成氨生产的过程中是建立在诸多个单元过程所形成,而在诸多个单元过程中,每一个单元过程都属于实际过程,也就是说每一个单元过程都会消耗一定能源,因此,实现节能还可以通过减少单元过程实现。
- 1、下载文档前请自行甄别文档内容的完整性,平台不提供额外的编辑、内容补充、找答案等附加服务。
- 2、"仅部分预览"的文档,不可在线预览部分如存在完整性等问题,可反馈申请退款(可完整预览的文档不适用该条件!)。
- 3、如文档侵犯您的权益,请联系客服反馈,我们会尽快为您处理(人工客服工作时间:9:00-18:30)。
浅析大型合成氨生产装置节能降耗途径
作者:龚志强张晓如陈波
来源:《科技探索》2013年第04期
摘要:针对国内现有大型合成氨生产装置,在不经过大的技改项目和无需大量资金投入的情况下,通过在开停车及装置运行维护过程中的一系统列优化操作、介质回收、无接缝衔接,深挖装置潜能,最大限度地实现现有装置节能降耗。
关键词:节能降耗优化控制
现阶段国内较早引进的一批大型合成氨生产装置大多经过一次或几次扩能技改,与当今先进的装置相比,能耗偏高主要受限于主线工艺流程的差别,再进行大规模的技改技革来实现节能降耗已极不经济,只有在现有装置基础上实施小的革新及开停车过程、正常运行中进行优化操作来实现节能降耗。
以某公司生产装置为例:某合成氨装置是凯洛格工艺天然气连续加压转化日产1000吨氨装置,经过两次技改产量达到1500T/D,能耗也由开始的9.37 Gcal/TNH3降低到7.85Gcal/TNH3,但离国际先进能耗水平6.5Gcal/TNH3仍有一定的差距。
现以该装置为引导,对各节能降耗具体途径及效果情况进行总结与说明。
1、装置正常生产运行中采取的节能降耗措施
1.1、原料气压缩机低压缸进口采取提压操作:装置原设计中低压缸进口压力为0.47MPa,根据压缩机性能曲线我们将低压缸进口压力提至最高达到0.57MPa,由于低压缸进口压力的提高,低压缸出口压力也较大的提高,与未提压运行时的100%负荷相比,转速下降了
400RPM,一级后压力降低了0.05MPa,对应透平蒸汽耗量减少了0.9T/H,吨氨消耗减少
0.012Gcal。
需要注意的是,由于压力的提高其导致出口分离器117-F的运行压力接近安全阀整定值,需对117-F作强度试验并根据强度试验结果提高其安全阀的整定值,以实现提压后运行的安全稳定。
1.2、循环(冷却)水温度对压缩机组透平蒸汽用量的影响
根据装置运行参数得出,在高负荷情况下若凉水塔的出水温度在26~28℃以上,通过增开凉水塔一台冷却风扇可使出水温度将下降2℃左右。
从能耗的角度考虑吨氨电耗增加了
0.007Gcal,吨氨汽耗是降低了0.025Gcal,综合能耗降低0.018 Gcal。
高温季节不得不全开风机的时间和低负荷下返回阀有开度的时间,全年需要多开风机的时间约200天以上,预计全年可节约总费用约116万元。
风机运行台数调整的同时现场各岗位应对各机泵油温作相应调整,并根据工艺参数的化对各水冷器水量作调整,以达到最优化。
1.3、空压机运行方式优化
101-J、JA并联同时向系统送工艺空气,101-J为蒸汽透平驱动,而101-JA动力来源于电机,两台空压机负荷变化对系统能耗有较大的影响,以生产中采集的两组数据进行对比列表如下(压缩机机出口压力、循环水温度、气温基本一致)
从表中对比可看出,101-J一级后压力由1.078MPa上涨至1.173MPa,机组多送出空气3.1T/H,透平蒸汽用量增加2.3T/H,多送出1吨空气增加0.74吨,耗能约为0.518 Gcal,从费用来多送出1吨空气花费113元(按每吨蒸汽153元计);101-JA电流由472A增加至494A,机组多送出空气1.9T/H,计算出多耗电194KW.H,折算出多送一吨空气多耗0.089 Gcal
(1KW.H的热值按860 kcal来计算),从费用来多送出1吨空气花费41元(1度电按0.4元计)。
通过以上的比较得出将透平负荷将电机转移可将吨氨能耗降低0.518-0.089=0.429 Gcal。
所以在系统负荷满足两个机组的防喘振阀均关完的情况下,应先加101-JA的负荷,直至机组额定负荷后再增加101-J的负荷,以实现装置节能降耗及两台机组的优化运行。
2、开停车过程中对可燃介质的回收
2.1、对钴钼加氢和氧化锌升温放空天然气的回收:通过配置管线将其中一部分作为一段炉燃料气,一部分返回进入天然气压缩机102-JLP进口循环利用,每次开车的回收量达7万标方,停车降温时可同样进行回收,流量在2万标方左右。
2.2、对停车后合成系统卸压气体的回收:合成系统停车后可对驰放气回收作一段炉燃料气用,直至合成系统压力降至3Mpa,可回收驰放气量约5万方。
2.3、对低变还原载气的回收:新更换低变催化剂在开车过程中需进行还原操作,还原载气一般为天然气,平均流量约为16000Nm3/H,在满足还原质量和系统稳定的情况下,通过新配专用回收管线,可实现载气的全部回收。
3、无接缝开车及开车过程中负荷控制
3.1、无接缝开车首先是建立在检修质量过关、调节阀联动完好、机泵有条件的试车及有条件的查漏情况下才能实现,关键在于开车过程中各阶段的衔接配合,各工段做好充分开车准备工作,保证整个开车流程才能畅通,不至于出现要投用时还不具备条件的情况,力争做到等待、拖延时间为零,实现无节缝开车就等于减少排放及节能降耗。
3.2、开车过程中不同阶段负荷的控制
3.2.1、系统在开车时加天然气时要求的负荷为18%,加空气时负荷为30%,直至串甲烷化时负荷要求均为30%,但在串甲烷化就进入103-J的开车准备中,为提供103-JAT所用的高压蒸汽要求负荷要加至50%,但实际操作中可在103-J开始慢转时才将负荷在1小时内由30%加至40%,负荷加至40%时刚好进入103-J升速大量用蒸汽的时间。
3.2.2 在合成塔催化剂升温过程中负荷保持在40%,同时放空氢氮气也可进行回收。
相比开103-J前就将负荷加至50%,40%的负荷到合成系统开车正常可减少天然气耗量6万标方。
4、结束语:
装置的节能降耗需要我们从开停车、正常运行中的点滴中做起,在能源价格上涨并且短缺的今天,装置节能降耗就显得尤为重要,这就需要我们在工作进一步去思考装置节能降耗途径,也需要操作人员在运行中作精细化操作及优化操作。