油井管公司套管生产工艺
石油套管N80的生产工艺设定

石油套管N80的生产工艺设定N80级石油管是我国目前油井管中使用量最大的品种, 占各类油井管总产量的40% 以上。
针对N80级非调质钢的使用要求及性能特点, 对36Mn2V调质钢的生产工艺过程进行了研究和制定。
(1)表1为36Mn2V调质钢的工艺参数(2)N80 油管表面出现的典型缺陷有鱼鳞外折、夹渣性大外折和渣坑。
有必要进行生产工艺优化以提高产品质量。
(3) N80 油管采用Φ89 mm 半浮芯棒连轧管机组轧制,管坯使用36Mn2V 水平连铸圆管坯。
(4)N80石油套管是高强度高韧性无缝钢管, 国际上通常采用的方法有: 调质处理(含轧后直接淬火+回火处理)、常化、常化+ 回火以及轧制后回火。
36Mn2V 是生产N80 级石油套管的专用钢种,属微合金化非调质钢。
该钢适宜于采用控温、控冷和控制变形量等方法加工,钢管勿需调质即可达到要求的性能,由此简化了生产工艺,降低了钢管制造成本。
冶炼—连铸—轧制过程控制1 配料要求由于36Mn2V 油井管对非金属夹杂物、气体含量等要求较严格,同时从化学成分要求看,S、P 含量要求较低;因此要求入炉原材物料和浇注系统干燥、洁净、烘烤良好,入炉钢铁料要求含S、P量低。
根据上述要求,制定配料结构为:45%~60%铁水+生铁、40%~55%优质废钢(含磷较低)、渣料(石灰)150 kg/炉。
2 电炉工艺控制电炉控制的重点是氧化前期做好去P 操作。
造好泡沫渣,氧化终点碳>0.10%,出钢时用硅锰合金进行预脱氧,在出钢至1/3 时随钢流一次加足Al块。
应该选用低磷合金、中锰合金进行合金化操作。
3 精炼工艺控制由于电炉过程控制较好,精炼炉到位炉渣流动性良好,精炼过程深脱氧变渣较快,通过含量调整炉渣状况,炉渣碱度平均为3.5,Σ(FeO)≤0.5%,白渣保持时间在30 min 以上,脱氧充分,熔炼成分控制理想,见表2。
其他残余元素Zn、Pb、Sb、Cu、As、Sn、Bi 等的含量均≤0.006%。
石油地质专用管基本知识

10.36
11.51 8.94
外径(mm)
101.6 114.3
壁厚(mm)
7.8 7.37
244.5
244.5 244.5
10.03
11.99 13.84
114.3
127 139.7 139.7
8.56
9.19 7.72 9.17
273.1
339.7 339.7 508
8.89
9.65 10.92 12.7
油套管的规格、钢级和扣型
油套管特殊钢级(宝钢):
2014-12-1
11
油套管的规格、钢级和扣型
2014-12-1
12
API油套管钢级的色环表示(库房常见):
系列
钢级 J55
颜色标识、 接箍 管体
接箍 全涂绿色+一条白 色环 全涂红色
管 体 一条绿色环
API 系 列 套 管
N80 1 类
一条红色环
2 3/8 2 7/8 3 1/2 4 4 1/2 5 60 73 88.9 101.6 114.3 127 in 5 1/2 7 7 5/8 9 5/8 10 3/4 13 3/8 20 mm 139.7 177.8 193.7 244.48 273.05 339.7 508
-3
油套管的规格、钢级和扣型
系列 钢级 TP90H TP 系 列 热 采 井 用 套 管 颜色标识、 接箍 管体 接箍 全涂棕色 管体 一条棕色环 +一 条蓝色环 二条白色环 +一 条蓝色环 一条白色环 +一 条蓝色环 TP120H(T) 、 TP125H 全涂橙色 一条橙色环 +一 条蓝色环
TP100H
全涂白色
TP110H
石油工程技术 井下作业 悬挂小套管修套技术

悬挂小套管修套技术1工艺简介悬挂小套管修套技术就是在原损坏套管内通过一定手段悬挂一段小套管,然后在其环空固上水泥的一种工艺方法。
其适用范围有大段套管破漏的修复;原生产层位因射孔,常规方法已无法调层,采用悬挂小套管固井后重新射孔调层生产。
1.1具体方法按小套管悬挂位置不同分为:1.1.1顶管法。
由井口开始向下悬挂,悬挂器可坐于原井口大四通内或另行制作套管头。
1.1.2中间悬挂法。
采用小套管悬挂装置,将一段套管悬挂于井的某段,然后固井。
1.1.3尾管法。
采用悬挂装置将小套管悬挂到井底。
1.2常用的悬挂丢手装置有液压尾管悬挂器、机械尾管悬挂器、正反扣接头3种。
1.3施工主要工序:起出原井内生产管柱;通洗井,保证井壁干净,防止伤害地层;找出确切的套管破漏段;打底水泥塞;悬挂小套管、固井;钻开小套管内残余水泥;对小套管进行试压;钻通底水泥塞(尾管法不钻);验证生产层位是否堵塞,必要时进行补孔;投产。
2技术关键2.1储层保护储层井段要替入储层保护液,必要时可填砂保护,防止施工中工作液或水泥浆对储层的伤害。
2.2井筒清洁为了保证固井时水泥浆与原套管的胶结强度,破漏井段及上下各50m以上必须用热水清洁原套管上的油蜡,必要时进行低浓度酸洗。
2.3套管通径、试压原套管必须严格通径,确保小套管能够顺利下入。
对完好的套管试压应根据生产压差情况提高试压标准,防止因破漏段堵住后生产动液面下降引起原完好套管承受外压增大而发生新的破漏。
2.4打悬空水泥塞为保证固井时水泥浆不会向下沉,必须在悬挂小套管的底界打一悬空水泥塞。
若套管破漏处存在漏失,打底塞顶替时,油套往往不平衡而使施工失败。
解决办法是:当水泥浆顶替到管鞋时,边替边上提管柱。
大修机通常可提20m,这样可保证有近20m的水泥塞。
为防止水泥塞在固井时因胶结强度不够下滑,实探水泥塞面时加压负荷可按下式计算:N=7.7x10-6(ρ2—ρ1)(H—h)d2+K式中N—探水泥塞面应加的负荷,KN;ρ2—ρ1—水泥浆与顶替液的密度差,Kg/cm3;H—h—顶替时小套管内外水泥浆最大高度差,m;d—水泥塞处套管直径,mm;K—附加负荷,20~30KN。
石油钻井用套管头详解
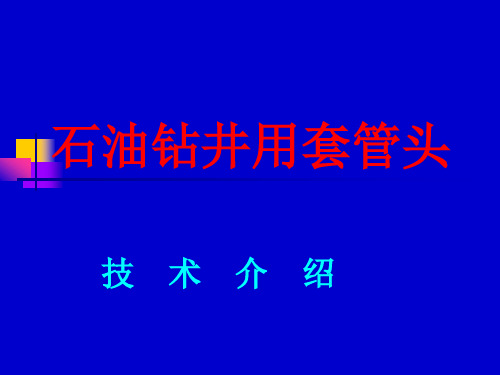
一、底部卡瓦式连接
采用WD型卡瓦连接表 层套管 采用BT型二次密封结构 不需精确计算套管下入 深度 不受环境、气候等条件 影响 安装方便、迅速、安全、 可靠 适用于各种规格套管: 30” 20” 13-3/8 ” 121/4” 9-5/8 ” 7 ” 5-1/2 ” 等
2001.8.15
JMP
底部卡瓦连接
侧阀
BT密封
压力表 截止阀
WD卡瓦
2001.8.15
JMP
“WD”型套管悬挂器
采用 整 体开 合 式 结构安 装 非常方便,安装时,只要 将套管头套入表层套管到 位后,上紧底部螺钉即可 在 WD 型 卡 瓦 悬 挂 器 上 部 带 有两道“ BT” 密封圈,用 于密封表层套管,防止套 管环空串压。
20”,13-3/8”,9-5/8”
2001.8.15
JMP
二、底部螺纹连接
底部可采用各种规 格螺纹与表套连接, 如:CSG、LCSG、 BCSG 、TM等 适用于各种规格套 管:20 、133/8、 9-5/8 7、 5-1/2 等
底部螺纹
WE卡瓦
2001.8.15
JMP
三、底部焊接连接
检验合格,符合标准要求
日期 93.10.4 93.12.16 93.12.16 94.1.20 94.7.26
载荷试验(375T)
检验合格,符合标准要求
载荷试验(265T)
检验合格,符合标准要求
载荷试验(265T)
检验合格,符合标准要求
载荷试验(438T)
检验合格,Hale Waihona Puke 合标准要求载荷试验(375T)
检验合格,符合标准要求
L80-13Cr油套管的制造工艺

[ 2] 张启富. 现代钢带连续热镀锌 [M ]. 北京: 冶金工业出版社,
2007: 871 - 875.
(收稿日期: 2009- 11- 19 )
专利信息
双辊薄带连铸开浇方法
专 利 号: ZL200510027432. 2 专利权人: 宝山钢铁股份有限公司 发 明 人: 方 园 崔 健 叶长宏 本发明涉及双 辊薄带连铸工 艺中的开 浇技 术。一种双辊 薄带连铸开浇方 法, 其 特征是: 首 先, 设置初始辊缝 (S0 )、初始浇铸速度 ( V0 ), 初始 浇铸速度 /初始辊缝的比例配合使初始的铸轧力 (F )小于设定值 ( F ); target 接着, 监控结晶 辊的表 面温度 (T ), 当结晶辊表面温度 (T )达到 目标值 (Ttarget )后, 控制结晶辊开始变辊缝, 辊缝从初始 (S0 )变到目标值 S ; targe t 在这过程中, 监控铸轧力 (F ), 当铸轧力 (F )大于设定值 (F target )时, 启动速 度调节器来抵消由于辊缝变化所引起的铸轧力的 变化。本发明 控制容易, 操作方便, 装置结 构简 单, 能实现开浇的稳定性。
L80- 13Cr油套管的制造工艺
专 利 号: ZL200510030294. 3 专利权人: 宝山钢铁股份有限公司 发 明 人: 唐豪清 黄子阳 张忠铧 万化忠 L80- 13C r油套管的制造工艺, 其步骤如下: ! 管坯加热、热轧钢管。 冷床。 # 空淬调质热 处理, 空淬调质热理是在带氮气保护的光亮退火 炉上进行, 淬火温度: 90 ~ 1 020 ; 保温时间: 20 ~ 30 m in; 淬 火 介 质: 空 气; 回 火 温 度: 608 ~ 740 ; 保温 时间: 40 ~ 60 m in; 空 冷。 管子 矫 直、切头尾、分段、其他后续工序; 其中, 加热采用 辐射管进行加热; 热处理加热炉内用氮气压力保 持正压。本发明保证 L80- 13C r油套管经空淬调 质热处理后, 机械性能和硬度满足 AP I 5CT 标准 规定, 管子内外表面氧化轻微, 内表面不必再进行 酸洗或抛丸处理, 生产工艺简化, 产品成本下降。
石油钻井下套管操作规程
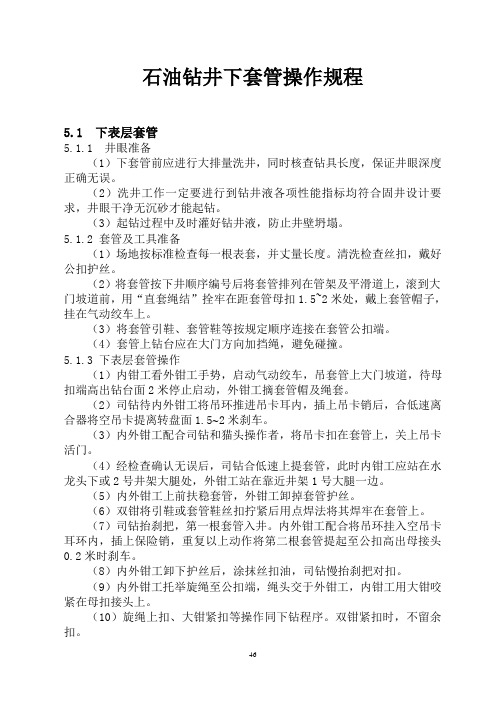
石油钻井下套管操作规程5.1 下表层套管5.1.1 井眼准备(1)下套管前应进行大排量洗井,同时核查钻具长度,保证井眼深度正确无误。
(2)洗井工作一定要进行到钻井液各项性能指标均符合固井设计要求,井眼干净无沉砂才能起钻。
(3)起钻过程中及时灌好钻井液,防止井壁坍塌。
5.1.2 套管及工具准备(1)场地按标准检查每一根表套,并丈量长度。
清洗检查丝扣,戴好公扣护丝。
(2)将套管按下井顺序编号后将套管排列在管架及平滑道上,滚到大门坡道前,用“直套绳结”拴牢在距套管母扣1.5~2米处,戴上套管帽子,挂在气动绞车上。
(3)将套管引鞋、套管鞋等按规定顺序连接在套管公扣端。
(4)套管上钻台应在大门方向加挡绳,避免碰撞。
5.1.3 下表层套管操作(1)内钳工看外钳工手势,启动气动绞车,吊套管上大门坡道,待母扣端高出钻台面2米停止启动,外钳工摘套管帽及绳套。
(2)司钻待内外钳工将吊环推进吊卡耳内,插上吊卡销后,合低速离合器将空吊卡提离转盘面1.5 2米刹车。
(3)内外钳工配合司钻和猫头操作者,将吊卡扣在套管上,关上吊卡活门。
(4)经检查确认无误后,司钻合低速上提套管,此时内钳工应站在水龙头下或2号井架大腿处,外钳工站在靠近井架1号大腿一边。
(5)内外钳工上前扶稳套管,外钳工卸掉套管护丝。
(6)双钳将引鞋或套管鞋丝扣拧紧后用点焊法将其焊牢在套管上。
(7)司钻抬刹把,第一根套管入井。
内外钳工配合将吊环挂入空吊卡耳环内,插上保险销,重复以上动作将第二根套管提起至公扣高出母接头0.2米时刹车。
(8)内外钳工卸下护丝后,涂抹丝扣油,司钻慢抬刹把对扣。
(9)内外钳工托举旋绳至公扣端,绳头交于外钳工,内钳工用大钳咬紧在母扣接头上。
(10)旋绳上扣、大钳紧扣等操作同下钻程序。
双钳紧扣时,不留余扣。
(11)表层套管的沉砂口袋不得大于2m。
(12)下完套管,确保套管居中,套管中心和井口中心偏差不得大于10毫米。
(13)将大小头连接在套管与方钻杆之间,顶通钻井液循环两周,作好固表层准备。
下套管方案

下套管方案1. 简介下套管是指在油气井中的一种钻井工艺,它是为了保证井筒的完整性、加强固井质量和确保油气井的安全生产而进行的。
下套管旨在保护油气井的井壁,防止井筒塌陷、漏失等问题的发生。
本文将介绍下套管方案的基本原理、流程以及相关注意事项。
2. 下套管方案的基本原理下套管方案的基本原理是通过将金属套管下入井内,与井壁形成密封,并通过水泥浆灌注套管和井壁之间的空隙,形成固定的井筒结构。
下套管方案能够增强井壁的承载力,并提供有效的隔离层,从而确保油气井的安全生产。
3. 下套管方案的流程下套管方案的实施流程包括以下几个步骤:3.1 套管设计在制定下套管方案之前,需要进行套管设计。
套管设计包括确定套管的尺寸、壁厚以及套管钢级等参数。
套管设计需要根据井眼的地质情况、井深、井压等因素进行综合考虑。
3.2 套管下入套管下入是指将设计好的套管逐节下入井内,直至套管达到预定位置。
套管下入需要使用特殊的套管下入工具,通过逐节将套管下入井内。
在下套管过程中,需要确保套管与井壁之间的间隙尽量小,并避免套管发生扭转和卡住的情况。
3.3 套管固井套管下入到预定位置后,需要进行套管固井操作。
套管固井是通过注入水泥浆的方式,将水泥浆灌注到套管与井壁之间的空隙中,形成坚固的固定结构。
套管固井操作需要注意固井质量和注入水泥浆的流动性,以确保固井效果。
3.4 套管上移套管上移是指在套管固井完成后,将钻头从套管内抬出,并进行上移操作。
套管上移有助于确保套管固井的质量和效果,并为后续工作创造条件。
4. 注意事项在实施下套管方案时,需要注意以下几个事项:•套管设计要符合井筒的地质条件和井口管理要求,避免出现套管选型不当的情况。
•套管下入过程中,需要注意控制下套速度,避免套管发生扭转和卡住的情况。
•套管固井操作要严格控制注入水泥浆的流量和质量,确保固井效果和固井质量。
•套管上移过程中,要注意保护套管和井的完整性,避免损坏套管。
•在下套管过程中,需要根据井筒的情况进行监测和记录,及时处理井筒异常情况。
石油天然气-油井套管和油管用钢管内控
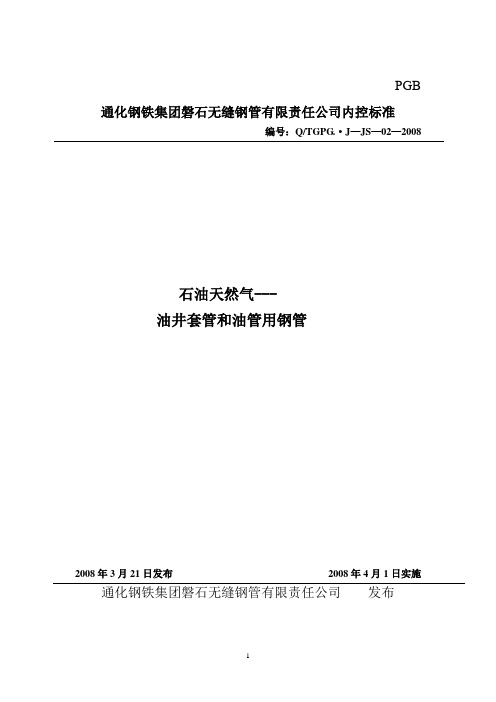
PGB 通化钢铁集团磐石无缝钢管有限责任公司内控标准编号:Q/TGPG.·J—JS—02—2008石油天然气---油井套管和油管用钢管2008年3月21日发布2008年4月1日实施通化钢铁集团磐石无缝钢管有限责任公司发布油、套管及接箍坯料的生产检测规范1范围本规范适用于J55、K55、N801外径为φ73.02—φ177.8的油、套管及接箍料的生产检测。
2引用标准API SPEC 5CT —套管和油管规范3尺寸、外形3.1外径和壁厚的允许偏差应符合表1的规定。
表 1 外径和壁厚的允许偏差注:如需方有协议要求按协议要求的尺寸生产及检验3.2长度具体长度要求见合同,范围定尺按上限控制,切头后长度不足合同要求的不准回切3.3弯曲全长弯曲度不超过0.2%,管端1.5m范围内不超过1.5mm;0.5m范围内不超过0.5mm。
3.4端头外形钢管的两端端面应与钢管的轴线垂直,切口毛刺彻底清除。
3.5不圆度不圆度不超过外径公差的80%4技术要求4.1化学成分磷含量不超过0.03%;硫含量不超过0.025%。
4.2 制造方法油、套管及接箍料采用热轧或冷拔制造。
4.3交货状态钢管以热轧状态交货。
5力学性能5.1拉伸5.1.1 试验方法钢管的拉伸性能应在纵向试样上测定。
5.1.2试验温度拉伸试验在室温下进行。
5.1.3拉伸试样的尺寸要求条形试样,对于外径小于φ101.6的管子试样的宽度为19mm,对于外径为φ101.6—φ177.8的管子试样宽度为25mm。
5.1.4强度数值应符合表2的规定表2 钢管的强度数值5.1.5伸长率应符合表3的规定(50.8mm标距内)表3 伸长率表5.2冲击功试验要求5.2.1 冲击功的试验方法一个冲击功实验应由三个试样组成,该三个试样从同一根钢管的同一个位置截取,三个试样的平均值应不小于规定冲击功的要求。
允许其中一个试样的冲击功小于规定冲击功要求,但其值不得小于规定冲击功的三分之二。
油管、套管用途和分类
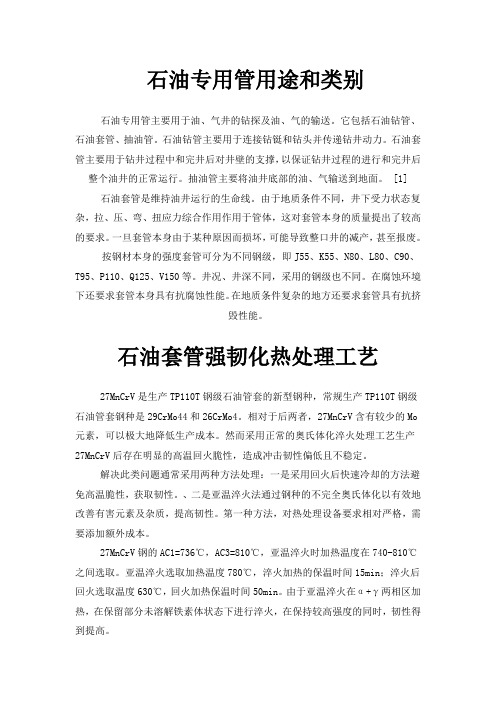
石油专用管用途和类别石油专用管主要用于油、气井的钻探及油、气的输送。
它包括石油钻管、石油套管、抽油管。
石油钻管主要用于连接钻铤和钻头并传递钻井动力。
石油套管主要用于钻井过程中和完井后对井壁的支撑,以保证钻井过程的进行和完井后整个油井的正常运行。
抽油管主要将油井底部的油、气输送到地面。
[1] 石油套管是维持油井运行的生命线。
由于地质条件不同,井下受力状态复杂,拉、压、弯、扭应力综合作用作用于管体,这对套管本身的质量提出了较高的要求。
一旦套管本身由于某种原因而损坏,可能导致整口井的减产,甚至报废。
按钢材本身的强度套管可分为不同钢级,即J55、K55、N80、L80、C90、T95、P110、Q125、V150等。
井况、井深不同,采用的钢级也不同。
在腐蚀环境下还要求套管本身具有抗腐蚀性能。
在地质条件复杂的地方还要求套管具有抗挤毁性能。
石油套管强韧化热处理工艺27MnCrV是生产TP110T钢级石油管套的新型钢种,常规生产TP110T钢级石油管套钢种是29CrMo44和26CrMo4。
相对于后两者,27MnCrV含有较少的Mo 元素,可以极大地降低生产成本。
然而采用正常的奥氏体化淬火处理工艺生产27MnCrV后存在明显的高温回火脆性,造成冲击韧性偏低且不稳定。
解决此类问题通常采用两种方法处理:一是采用回火后快速冷却的方法避免高温脆性,获取韧性。
、二是亚温淬火法通过钢种的不完全奥氏体化以有效地改善有害元素及杂质,提高韧性。
第一种方法,对热处理设备要求相对严格,需要添加额外成本。
27MnCrV钢的AC1=736℃,AC3=810℃,亚温淬火时加热温度在740-810℃之间选取。
亚温淬火选取加热温度780℃,淬火加热的保温时间15min;淬火后回火选取温度630℃,回火加热保温时间50min。
由于亚温淬火在α+γ两相区加热,在保留部分未溶解铁素体状态下进行淬火,在保持较高强度的同时,韧性得到提高。
同时低温淬火较常规温度低,减小了淬火的应力,从而减小了淬火的变形,这样保证了热处理的生产的顺利操作,而且为后续的车丝加工等提供了很好的原料。
油井管生产制造工艺

报告人:赵鹏
宝山钢铁股份有限公司 Baoshan Iron&Steel Co., Ltd.
目录
油井管概述 油井管生产制造工艺 油井管新产品开发
油套管概述
套管下入钻成井眼,用于防止地层 流体流动及地层挤毁。油管下入生 产套管内,构成井下油气层与地面 的通道,控制原油和天然气的流动。
油管和套管 Tubing & Casing
环形炉加热 Heating in rotary hearth
furnace
穿孔 Piercing
空心坯减径 Reducing of hollow billet
连轧 Rolling in mandrel mill
冷锯分段 Cutting with saws
冷却 Cooling on
适
宝钢油套管水压工艺
德国SMS MEER、西重所 按标准对油套管进行水压试验,检测
管体强度。 采用预压带径向密封环槽密封圈进行
密封,提高了密封圈的使用寿命。
宝钢钻杆摩擦焊工艺
惯性摩擦焊 德国SMS MEER
连续摩擦焊 英国Thompson
宝钢钻杆摩擦焊工艺
连续摩擦焊 在焊接过程中,钻杆工具接头 被主轴电机连续驱动,以恒定 的转速旋转焊接,直至达到规 定的摩擦时间或摩擦变形量, 工具接头才停止旋转并顶锻完 成焊接。
缺陷 采用通交流电的芯棒法实现周向磁
化,检测内外表面的纵向缺陷 采用输入三相全波整流电的线圈法实
现纵向磁化,检测内外表面存在的横 向缺陷 芯棒法磁化的内外接触块采用锑合 金,避免电弧烧伤
宝钢油套管管体螺纹车削工艺
德国SMS MEER 、法美PMC Colinet 、 德国EMAG
套管知识培训

套管的发展方向
5、ERW套管 ERW(Electric Resistant Weld)管,是指通过高频电阻焊接工艺制造而成的直缝焊管。ERW焊管的原料钢板(卷板)系低碳微合金钢经TMCP(Thermo-Mechanical Control Process)轧制而成,具有很好的强韧性。 从20世纪50年代开始,欧美及日本等发达国家已经在油井管领域大量使用了直缝焊管。美国在1992年焊接油井管的比例达到了58.5%,2005年达到了62.1%,2006年达到了66%以上;目前日本的焊接油井管比例已高达75%以上;英国、德国等国家焊接油井管的比例也在50%左右。从世界范围来讲,ERW油井管已经占到油井管总量的50%以上,而且这种趋势在不断上升。 国内以前很少使用焊管油井管,但从2003年以后受国外影响,焊管油井管已经越来越多被国内用户采用,2006年焊管油井管已占油井管总量的8%,2008年可达到12%左右。
套管的分类、用途、特点
套管型号示意
API套管型号英制表示方法: 规格代号+重量代号+钢级代号+螺纹形式 其中: 规格代号为套管的外径,单位为英寸。 重量代号为套管单位长度的重量,单位为磅/英尺。 例:7 23.00 J STC表示外径为7英寸,每英尺重量为23.00磅,钢级为J55的短圆螺纹套管。
套管的发展方向
3、连续管(柔性套管) 连续管过去主要用于修井和完井作业。连续管钻井技术是 近年来的一个研究热点。连续管是一种强度和韧性良好的钢管,卷在滚筒上。主要采用ERW焊管,已成功试制无缝钢管连续管。其材料也由碳钢发展到低合金钢 (包括淬火回火钢)及钛合金。目前正在研制复合材料连续管。连续管的屈服强度一般为492MPa或562MPa,现已发展到703MPa。连续管用钢必须 有良好的强韧性匹配,以保证较高的低周疲劳寿命。安东石油公司与BJ公司合作,正在开展连续油管修井作业,连续油管打捞,连续油管拖动酸化压裂,连续油管钻井、侧钻井等业务。
Q125钢级高强度石油套管的试制生产

技术交漁35Q125钢级高强度石油套管的试制生产张然(天津钢管集团股份有限公司,天津300301)摘要:介绍了按API Spec5CT-2011标准PSL-2类要求生产的Q125钢级高强度石油套管的试制过程:以Mn-Cr-Mo中碳钢为基础,通过合理的成分设计,使合金元素总含量W2.5%;采用电炉-精炼-真空脱气-连铸工艺生产连铸圆管坯;在斜轧穿孔、PQF连轧工序,保证产品在奥氏体区实现高温大变形;采用(920±10)T:淬火、保温时间17min,(620±10)1C回火、保温时间35min热处理制度。
检验结果表明:试生产的¢127mmx9.19mm规格Q125钢级高强度石油套管的屈服强度、抗拉强度、伸长率、冲击功(包括统计冲击功)均符合API Spec5CT-2011标准对PSL-2类Q125钢级的要求。
关键词:石油套管;Q125钢级;高强度;研制;淬火;回火中图分类号:TG335.71;TE931+.2文献标志码:B文章编号:1001-2311(2019)02-0035-05Trial Production of Q125High-strength Oil CasingZHANG Ran(Tianjin Pipe(Group)Corporation,Tianjin300301,China)Abstract:Elaborated is the trial production process of the QI25high-strength oil casing as per API Spec5CT—2011,PSL-2.On the basis of the medium carbon Mn-Cr-Mo steel,the chemical composition is reasonably designed to make sure that the total alloy element content is W2.5%.For steel making,the process flow as used is EF—refining―►vacuum degassing—>CC round casting.During the processes of rotary-piercing and PQF rolling,it must be guaranteed that the work-piece undergoes hi-temperature big deformation in the austenite zone.And after rolling,the①127mmx9.19mm high-strength oil casing has to be quenched at(920±10)^C and with a soaking time of17min.,and tempered at (620±10)弋and with a soaking time of35min.The testing and inspection results show that the said oil casing has been fully up to the requirements for yield strength,tensile strength,elongation,and impact energyC including statistic impact energy)as specified under API Spec5CT—2011for QI25steel grade of PSL-2.Key words:oil casing;St.G Q125;high-strength;manufacture;quenching;tempering石油套管是用于支撑油、气井井壁的钢管,以保证钻井过程进行和完井后整个油井的正常运行。
P110(30Mn5V)油井套管焊接工艺试验

P110(30Mn5V)油井套管焊接工艺试验吐哈油田的油井套管有很大一部分使用的是P110(30Mn5V)材质,这种材质采用美国API (美国石油工程协会)标准,强度级别较高,难以实现焊接,而油田根据工作需要,在更换井口时必须要对这种材质进行切割、焊接作业,这在油田焊接领域提出了新的焊接工艺要求,吐哈油田目前还没有该类钢的焊接工艺技术,在国内咨询其它油田也没有相应的焊接工艺。
因此对P110(30Mn5V)高强钢焊接工艺的研究是很有必要的,以便今后能安全、平稳、有效的完成维抢修井口工作任务。
第二章主要研究内容该项目主要研究焊接材料选用、焊接方法选用、焊后热处理工艺、焊接电压、电流、焊接线能量等参数的试验与确定,并进行拉伸、弯曲等一系列的力学试验。
通过试验获得P110(30Mn5V)高强钢的焊接工艺,实现P110(30Mn5V)高强钢在现场的焊接。
第三章关键技术(难点)及研究试验第一节关键技术和试验思路1.关键技术1.1 P110(30Mn5V)高强钢焊接应如何选择焊接材料。
1.2 如何确立P110(30Mn5V)高强钢在调制处理(淬火+高温回火)状态下的焊接工艺。
1.3 如何保证此类材料焊后的机械性能(抗拉强度、塑性)。
2.试验思路2.1 首先进行材料的复验,以确定材料的可靠性。
按照对新型材料的工艺要求,我们进行了材质复验,复验结果能够满足要求。
2.2 依据强度、合金成分、热处理状态分别选择相应的焊接材料并分别进行实验。
首先,分析材料的特性,将材料进行归类,在按照相应类别的材料进行焊接性分析;其次,对于强度、合金成分进行分析,确定焊接材料及热处理工艺的选择;然后,进行焊接试验并选择一组焊接试件进行焊后热处理。
2.3 与焊材生产厂家进行联系,确保所选择的焊材能及时生产。
2.4 鉴于施工现场实际情况,尽量在不进行焊后热处理(或后热处理)的条件下如何保证其可操作性。
选焊接材料时在保证强度的条件下重点考虑其塑性,制定焊接工艺上也尽量采用不进行焊后热处理(或后热处理)的条件,使其更具有实用性、推广性。
套管滑套压裂工艺技术

套管滑套压裂工艺技术套管滑套压裂工艺技术是一种利用高压泵将压裂液体注入井壁中,以增强地层渗透性和提高油井产能的技术。
在油田勘探和开发中广泛应用,具有操作简单、效果明显等优点。
套管滑套压裂工艺技术主要步骤如下:首先,进行作业前的准备工作。
包括选址、井眼设计、井身清洗、套管下入等。
选好钻井地点后,进行井眼设计,确定井径、设计套管等。
然后进行井身清洗,将井壁中的杂质清除干净。
最后将套管下入井。
其次,进行套管固井。
套管下入后,进行固井操作。
通过注入水泥浆,将井壁固定住,避免井壁塌陷。
然后,进行套管滑套压裂。
将套管滑入井内,与套管固井间留一定的间隙,形成套管滑套。
然后,利用高压泵将压裂液体注入套管滑套中,产生高压,使压裂液体进入地层裂缝中,扩大油井产能。
接下来,进行压裂液体回收与处理。
在压裂过程中,压裂液体会携带地层中的油气等物质一起流出井口。
对于这部分流出的压裂液体,需要进行回收和处理,以防止对环境造成污染。
最后,进行产能测试和评估。
压裂完毕后,需要对油井进行产能测试和评估,确定压裂的效果。
通过测试和评估,可以了解到底裂缝扩展情况如何,油井产能有没有提高等信息。
总的来说,套管滑套压裂工艺技术是一种有效增强地层渗透性和提高油井产能的方法。
通过高压泵将压裂液体注入井壁中,形成裂缝,扩大油井的产能。
在实际应用中,需要注意操作规范,确保施工质量。
此外,也要重视压裂液体的回收和处理,以保护环境。
通过不断优化和改进该工艺技术,可以更好地应对油田开发的需求,提高油井产能,实现经济效益。
浅谈套管固井滑套压裂工艺及其在红河油田的展望

浅谈套管固井滑套压裂工艺及其在红河油田的展望套管固井滑套压裂工艺是一种在油田开发中常用的采油工艺,通过在油井套管中注入压裂液,使岩石产生裂缝,从而增加油井产能。
本文将从套管固井滑套压裂工艺的基本原理、在红河油田的应用及展望等方面进行讨论。
一、套管固井滑套压裂工艺的基本原理套管固井滑套压裂是一种通过在井筒内部设置滑套,在滑套上关闭注水或注压器具,实现在固定井深和对应的地层段上的封闭作业,然后钻杠压裂消化封隔器具并形成压裂缝,最终实现井筒的经济有效输出。
在油井开发中,套管固井滑套压裂工艺可以有效地增加油井的产能,提高油田的采油效率,是一种重要的采油工艺。
红河油田地处于中国云南省的东南部,地处滇西北山脉边缘。
该地区盆地内多是沉积岩相,含油气矿产条件非常优越。
套管固井滑套压裂工艺在红河油田首次应用于2005年,自此之后,逐渐成为红河油田常规的采油工艺之一。
在红河油田,套管固井滑套压裂工艺成功地应用于多口油井,通过压裂液的注入,有效地增加了油井的产能,提高了油田的开发效率。
套管固井滑套压裂工艺还可以减少水驱油层中的水量,提高采油率,对于红河油田的油气资源开发起到了积极的作用。
随着新型油田开发技术的不断推广和应用,套管固井滑套压裂工艺在红河油田将有更广泛的应用前景。
随着油井的深水化和大规模开采,套管固井滑套压裂工艺可以提高油井的产能,同时减少油井的堵塞情况,保障油田的稳定产能。
套管固井滑套压裂工艺可以减少油井的维护成本,降低开采成本,提高油田的经济效益。
相比传统的采油工艺,套管固井滑套压裂工艺可以更加精准地控制油井产量,避免了因为井筒堵塞导致的维修和清洗成本,降低了油田的开采成本。
套管固井滑套压裂工艺在红河油田的应用和发展都取得了一定的成绩,未来,随着油田开发技术的不断进步,套管固井滑套压裂工艺将在红河油田得到更广泛的应用,并对油田的持续发展起到重要的作用。
同时需要不断加强对新技术的研发和应用,提高工艺的稳定性和可靠性,从而更好地为油田的开发和生产提供技术支持。
套管施工工艺

套管施工工艺套管施工工艺一、简介套管施工是一种在油井或井下开采工程中常用的技术。
通过将套管安装在井筒中,实现对井壁的加固和井底流体的控制。
本文档将详细介绍套管施工的各个阶段和相关工艺。
二、套管施工前的准备工作1.取得探测数据:在进行套管施工之前,需要先取得探测数据,包括地质数据、井深数据等。
这些数据将作为决策的依据。
2.设计套管程序:根据探测数据,制定套管程序。
考虑到井壁稳定性、井底流体控制等因素,确定套管的位置和型号。
3.选择套管材料:根据井内的环境条件和工程需求,选择适合的套管材料,如碳钢套管、合金套管等。
三、套管施工工艺1.套管下施工套管下施工是指将套管从井口向下逐节安装到井底的过程。
具体步骤如下:1)将套管的第一节放入井内,并通过旋转和推力的方式逐渐推入。
2)当第一节套管安装到位后,继续安装下一节套管。
在安装过程中,要注意控制套管的下行速度,避免造成井筒塌陷。
3)重复以上步骤,直到完成所有套管的安装。
在施工过程中,需要不断监测套管的下行情况,确保施工的顺利进行。
2.套管固井套管固井是指在套管下施工完成后,通过注入水泥浆来加固井壁的过程。
具体步骤如下:1)准水泥浆:根据工程需求,准备适量的水泥和水以及其他混合材料,制水泥浆。
2)进行固井配套工作:在注水泥浆之前,需进行套管环空的处理,如清洗、防漏处理等。
3)注入水泥浆:通过注水泥泥浆泵,将预先制备好的水泥浆注入套管环空,填充井筒空间。
4)固化并测量:水泥浆注入后,需要等待一定时间让水泥固化。
固化完成后,需要进行水泥固井质量的检验。
四、本文档所涉及附件如下:1、套管施工工艺示意图2、套管设计方案示例3、水泥固井质量检验标准五、相关法律名词及注释:1、《矿产资源法》:中华人民共和国矿产资源管理的基本法律,用于规范和管理矿产资源的开发和利用。
2、《石油天然气法》:中华人民共和国石油和天然气资源开采管理的法律,在石油和天然气开采领域具有法律约束力。
- 1、下载文档前请自行甄别文档内容的完整性,平台不提供额外的编辑、内容补充、找答案等附加服务。
- 2、"仅部分预览"的文档,不可在线预览部分如存在完整性等问题,可反馈申请退款(可完整预览的文档不适用该条件!)。
- 3、如文档侵犯您的权益,请联系客服反馈,我们会尽快为您处理(人工客服工作时间:9:00-18:30)。
油井管公司套管生产工艺
钢管先进行钢级鉴别,合格的钢管由辊道输送,依次经过涡流、漏磁,在线探伤仪器对管体的纵、横向缺陷进行检查。
合格的钢管经输送辊道送到1号车丝工位,在此共有多台专用数控车床进行钢管一端的丝扣加工,包括铣端面、倒内外棱、扒皮和车丝。
然后经辊道运送到2号车丝工位同1号工位一样有相同数量的专用数控车丝机进行钢管另一端的丝扣加工。
车丝以后的钢管由输送辊道送到螺纹检查台架进行丝扣检查,在此共包括三个工位。
在第一个检查工位上,人工检查丝扣,用单项仪检查丝扣的螺距、齿高和尾扣。
在第二个检查工位上检查丝扣的锥度。
在第三个位上用工作环规检查紧密距。
丝扣不合格的钢管被收集,返回切除废丝扣后重新加工和检查。
检查合格的钢管运送到接箍拧紧机前,给丝扣上涂上螺纹油脂,并由手工预拧接箍。
接着钢管被送到接箍拧紧机上将接箍拧到规定的程度。
拧接时的力矩和圈数必须同时符合要求。
拧接接箍后钢管进行全长通径试验。
通径后的钢管进行水压试验。
在此按照API规定的压力进行试压,并保持一定时间。
试压后钢管被拔出,在一个倾斜的装置使管内的水迅速流出。
水压试验的废品也被收集在废料箱中。
试压合格的钢管被运送到拧保护环的台架上。
在此处首先要给两端裸露的丝扣上涂上螺纹脂,同时在管端喷上色环。
然后分别将内、外保护环拧到钢管的两端。
钢管继续经辊道输送到测长、称重和打印设备前,依次进行测长、称重和打钢印。
接下来进行喷印,把测长、称重的数据连同钢管尺寸、钢级、标准号、厂标等喷印在钢管表面上。
钢管沿辊道通过连续涂漆机喷涂防锈油,为了加快防锈油的干燥,在涂油以后钢管通过一座干燥炉的下方用热风将油层吹干。
经过称重测长、打标、涂油并干燥以后的钢管就可以收集和打捆,然后进行成品检验最后运送到成品库存放或发货。
套管生产工艺流程简图如下:。