CVD工艺卡.
cvd工艺技术

cvd工艺技术CVD(化学气相沉积)工艺技术是一种在半导体和材料科学领域中应用广泛的制备薄膜的技术。
CVD技术通过在气氛中加热化学物质,使其分解并产生反应,最终形成固体薄膜。
在以下的文章中,我将介绍一下CVD工艺技术的原理、应用以及它对于半导体和材料领域的重要性。
首先,我们来了解一下CVD工艺的原理。
CVD工艺是基于化学反应的原理。
在CVD过程中,化学物质被加热并分解为原子或分子,然后在衬底上重新组合形成固体薄膜。
这些化学物质通常是易挥发的有机化合物或无机化合物。
加热源可以是电阻加热、光照或者激光。
通过控制温度、压力和反应气氛的成分,可以调节薄膜的成分、晶格结构以及厚度。
其次,CVD工艺技术在半导体和材料科学领域中有着广泛的应用。
例如,CVD可以用于制备硅薄膜,用于太阳能电池、显示屏和集成电路的制造。
此外,CVD还可以用于制备金属薄膜,用于硬盘驱动器和光学薄膜。
此外,CVD还可以用于制备氮化硅等无机薄膜,用于涂层和保护层。
总的来说,CVD工艺技术提供了一种非常灵活和精确的薄膜制备方法,能够满足不同材料和器件的需求。
最后,CVD工艺技术在半导体和材料科学领域的重要性不可忽视。
制备高质量薄膜是半导体和材料领域中的一个关键步骤。
CVD工艺技术提供了一种控制制备过程的方法,可以实现高度纯净、高度均匀以及良好结晶的薄膜。
这对于提高材料的性能和器件的效率至关重要。
此外,CVD工艺技术还可以实现高度控制的厚度和界面,对于设计和制造复杂的器件非常重要。
总之,CVD工艺技术是一种在半导体和材料领域中应用广泛的制备薄膜的技术。
它基于化学反应的原理,通过控制温度、压力和反应气氛的成分,实现高质量的薄膜制备。
CVD工艺技术在半导体和材料科学领域有着广泛的应用,能够满足不同材料和器件的需求。
它对于提高材料的性能和器件的效率具有重要作用。
因此,CVD工艺技术在半导体和材料科学中扮演着不可忽视的角色。
CVD工艺介绍

-----CVD入门介绍
CISEMI 周华强 2012/07/25
目录
1: CVD概念和特点 2:几种CVD类型、原理及特性 3:薄膜CVD膜和扩散CVD膜的区别 4: 薄膜区其它工艺介绍 5:薄膜各种膜及各膜在IC的作用 6:薄膜常见异常
1: CVD的概念、特点
1.1 CVD的概念:
一般而言,淀积的二氧化硅同热生长二氧化硅相比,密度较低,硅与氧数量之比与热生 长SiO2也存在轻微的差别,因而薄膜的力学和电学特性也就有所不同.高温淀积或者在淀积 之后进行高温退火,都可以使CVD二氧化硅薄膜的特性接近于热生长SiO2的特性.
3.2 LPCVD和PECVD SiO2膜的区别
(1)APCVD(400℃,P=760Torr):SiH4+O2 a. dep rate<2000A/min b. coverage:50-60%
段。
2.4 低压化学气相淀积系统
晶圆装载 门
压力计
晶圆
加热线圈
制程气体入口 温度
晶舟 中心区
均温区
至真空pump 石英管 距离
2.5 等离子增强型化学气相淀积(PECVD)
PECVD的特性:
• 相对低温,有高的淀积速率. • 较低的压力下离子有较长的平均自由路径,会提高淀积速
率
• Plasma的离子轰击能够去除表面杂质,增强黏附性 • 射频RF可以控制淀积薄膜的应力 • 反应室可用Plasma清洗.
上面讲了 PECVD和LPCVD的区别;
Any Questions
下面我进入薄膜区,来介绍 薄膜区其它工艺介绍
1:SACVD 2: SOG 3: CMP 4: WCVD
Any Questions
cvd化学气相沉积工艺

CVD(化学气相沉积)是一种重要的薄膜生长工艺,广泛应用于半导体、光电子、纳米材料和涂层工业中。
以下是CVD工艺的基本概述:1. 概念:CVD是一种通过将气体前体化合物沉积在固体表面上来生长薄膜或涂层的工艺。
这些前体气体通过加热可升华或分解,然后在基底表面反应并形成所需的材料。
2. 基本步骤:CVD工艺包括以下基本步骤:a. 前体气体引入:气体前体化合物以气体或液体形式引入反应室。
b. 基底准备:基底通常是硅片、玻璃、金属等,必须事先准备,例如清洗和加热,以确保薄膜附着良好。
c. 气体分解或反应:前体气体在高温下分解或反应,生成反应产物。
d. 反应产物沉积:反应产物沉积在基底表面,形成所需的薄膜或涂层。
e. 废气排放:废气将未反应的气体和副产物排出反应室。
3. 温度和压力控制:控制CVD工艺的温度和压力非常重要。
温度通常高于反应气体的沸点,以确保气体前体可以蒸发或分解。
压力可以调整以控制气体的浓度和反应速率。
4. 类型:CVD工艺有多种类型,包括:a. 热CVD:在高温下进行,常用于硅片生产等。
b. 低压CVD(LPCVD):在较低的压力下进行,适用于高质量薄膜的生长。
c. PECVD(等离子体增强化学气相沉积):使用等离子体激活气体前体,通常用于生长氢化非晶硅薄膜等。
d. MOCVD(金属有机化学气相沉积):用于生长半导体材料,如GaAs、InP等。
5. 应用:CVD工艺在半导体制造、光电子器件、太阳能电池、涂层技术、纳米材料制备等领域具有广泛应用。
它用于生长晶体薄膜、导电涂层、光学涂层、硅片的外延生长等。
6. 控制和监测:CVD工艺需要精确的温度、压力和气体流量控制,以及监测反应产物和废气的化学成分。
总之,CVD是一种重要的化学气相沉积工艺,可用于生长各种薄膜和涂层,广泛应用于多个工业领域,是现代微电子和纳米技术的基础之一。
cvd五大工艺参数

cvd五大工艺参数CVD五大工艺参数化学气相沉积(Chemical Vapor Deposition,CVD)是一种广泛应用于材料制备和薄膜涂覆的工艺方法。
在CVD过程中,通过控制五大工艺参数,可以实现对薄膜的形貌、结构和性能的调控。
本文将分别介绍CVD工艺中的五大参数:温度、压力、气体流量、沉积时间和底物表面状态。
一、温度温度是CVD过程中最关键的参数之一。
通过调节温度,可以控制反应的速率和产物的结构。
温度过高会导致反应速率过快,产物结构不稳定,甚至引发副反应和膜层破裂。
温度过低则反应速率过慢,薄膜质量较差。
因此,在CVD过程中需要根据所需薄膜的性质和反应的特点选择合适的温度。
二、压力压力是CVD过程中另一个重要的参数。
通过调节反应室的压力可以控制气体的浓度和反应的速率。
较低的压力可以提高气体分子的自由程度,加快气体分子与底物表面的反应速率。
然而,过低的压力可能导致反应过程中气体流动不稳定,难以实现均匀的薄膜沉积。
因此,在CVD过程中需要综合考虑反应速率和薄膜质量,选择合适的压力条件。
三、气体流量气体流量是CVD过程中决定反应物质供应的重要参数。
不同的材料和反应需要不同的气体组分和流量。
过高或过低的气体流量都会影响薄膜的沉积速率和质量。
过高的气体流量容易导致气体分子的稀释,降低反应速率。
过低的气体流量则会限制反应物质的供应,导致薄膜质量不佳。
因此,在CVD过程中需要准确控制气体流量,以满足反应的要求。
四、沉积时间沉积时间是CVD过程中影响薄膜厚度和形貌的参数之一。
通过调节沉积时间可以实现对薄膜厚度的控制。
较短的沉积时间会得到较薄的薄膜,而较长的沉积时间则会得到较厚的薄膜。
同时,沉积时间还会对薄膜的形貌产生影响。
过短的沉积时间可能导致薄膜不充分生长,表面不平整。
过长的沉积时间则容易导致薄膜结构松散、颗粒较大。
因此,在CVD过程中需要根据所需薄膜的厚度和形貌选择合适的沉积时间。
五、底物表面状态底物表面状态是CVD过程中容易被忽视但十分重要的参数之一。
CVD的原理与工艺

CVD的原理与工艺CVD(化学气相沉积)是一种常用的薄膜制备技术,通过在高温条件下将气体衍生物在固体表面沉积形成薄膜。
它在半导体、光电子、材料科学等领域有着广泛的应用。
本文将介绍CVD的基本原理和常见的工艺流程。
CVD的基本原理是利用气体在固体表面发生化学反应产生固体沉积。
其过程可以简单概括为三个步骤:传输扩散、化学反应和沉积。
首先,在高温下,气体分子从气相传输到固相表面,这个过程称为传输扩散。
然后,在固体表面发生化学反应,气体分子与表面原子或分子发生物理或化学相互作用。
最后,与固体表面反应的产物发生聚集并沉积到固相表面上,形成薄膜。
CVD工艺可以分为四个主要组成部分:反应室、基底、前驱物和载气。
反应室是进行反应的容器,通常由高温和高真空环境下的材料制成。
基底是待沉积薄膜的衬底,可以是玻璃、硅等多种材料。
前驱物是产生沉积薄膜的化学物质,通常是气态或液态的。
载气是用来稀释前驱物的气体,使其在反应室中更均匀地传输。
CVD的工艺流程是在反应室中将前驱物供应和载气送入,通过传输扩散和化学反应后,形成薄膜并覆盖在基底上。
根据前驱物供应的方式和反应室的特点,CVD可以分为几个常见的工艺类型。
最常见的是热CVD,也称为低压CVD(LPCVD)。
在低压下,前驱物和气体通过加热传输到反应室中,沉积在基底上。
这种方法适用于高温下的材料制备,例如多晶硅、氮化硅等。
另一种常见的是PECVD(等离子体增晶体化学气相沉积)。
在PECVD 中,通过产生等离子体来激活前驱物的化学反应。
在等离子体的作用下,前驱物转化为离子和活性物种,进一步在基底上反应形成薄膜。
这种方法适用于制备非晶硅、氮化硅等。
还有一种CVD工艺称为MOCVD(金属有机化学气相沉积)。
在MOCVD 中,金属有机化合物作为前驱物供应,经氢气或氨气稀释。
通过热解和化学反应,金属有机前驱物转化为金属原子和活性物种,在基底上形成薄膜。
这种方法适用于制备复杂的金属氧化物、尖晶石等。
CVD的原理与工艺

CVD的原理与工艺CVD是化学气相沉积的缩写,是一种重要的薄膜制备工艺。
其原理是通过化学反应在基板表面沉积出所需的薄膜。
CVD工艺具有高温、通用性、高产率等优点,被广泛应用于半导体、光电子、材料科学等领域。
CVD工艺的原理主要涉及三个基本过程:传输过程、反应过程和沉积过程。
传输过程是指气相中物质在反应室中的输送和混合过程。
反应过程是指气相中物质发生化学反应的过程。
沉积过程是指反应生成物在基板表面的吸附和成膜过程。
CVD工艺的实施基础是高温条件下反应气体中的化学反应。
通常,CVD工艺需要在几百摄氏度到几千摄氏度的高温下进行。
高温条件下,反应气体中的分子活性增加,促使反应发生。
此外,高温条件下也有利于沉积物的生长和晶格匹配。
CVD工艺中常用的气体有两种类型:反应物气体和载体气体。
反应物气体是指与基板表面发生化学反应的气体,可以是纯净气体或有机金属(如金属有机化合物)。
载体气体是指将反应物气体输送到反应室中,并稀释以便控制反应速率和成膜均匀性的气体。
常用的载体气体有氢气、氮气、氩气等。
具体而言,CVD工艺的实施过程可以分为以下几个步骤:1.反应物气体输送:反应物气体通常通过质量流控制器控制流量,并由气体输送系统输送到反应室中。
2.传输与混合:反应物气体进入反应室后,通过传输与混合过程,与载体气体充分混合,形成气相反应体系。
3.化学反应:在高温条件下,混合的反应气体在反应器中发生化学反应。
这些化学反应通常是复杂的多步骤反应,生成物在气相中。
4.吸附与扩散:生成物与基板表面发生吸附和扩散,使得沉积物开始形成。
5.成膜和生长:沉积物在基板表面不断生长,并形成所需的薄膜。
CVD工艺的成功实施需要考虑许多因素。
其中,关键的因素包括:反应温度、反应气体浓度、反应压力、基板表面状态等。
这些因素直接影响了沉积物的结构、性能和均匀性。
为了实现理想的薄膜沉积,CVD工艺还需要进行流程优化和参数调控。
通过控制反应条件、改变反应气体浓度和流量,以及调整基板表面状态,可以实现不同结构和性能的沉积物。
cvd涂层工艺流程

cvd涂层工艺流程
CVD(化学气相沉积)涂层工艺流程如下:
1. 清洗:首先需要将金属基材表面进行清洗,以去除任何杂质和氧化物。
2. 预处理:提高金属表面的粗糙度,通常采用切削、抛光、喷砂等方法。
3. 材料预处理:将所需的陶瓷材料制成粉末或使用气相前驱体,通过加热或其它方式将其转化为可用于CVD的气态物质。
这一步骤可以在一个独立的设备中完成。
4. 反应室装载:将经过预处理的材料输送到CVD反应室中。
反应室通常是一个密封的高温容器,内部具有特殊的反应条件,如高温、低压等。
5. 反应条件控制:在反应室中,通过控制温度、压力和气体流动等参数,创造出适宜的反应条件。
这些条件可以根据不同的材料和涂层要求进行调整。
6. 气相反应:在适宜的反应条件下,气态前驱体与基材表面发生化学反应,生成陶瓷涂层。
这个过程中可能会产生一些副产物,需要通过排气系统进
行处理。
7. 涂层生长:通过控制反应时间和材料供应速率等参数,使涂层在基材表面逐渐生长。
涂层的厚度可以通过调整反应时间来控制。
8. 冷却和除气:涂层生长完成后,将反应室冷却至室温,并进行适当的气体排放和清洗,以准备下一次涂层。
9. 鉴定和测试:通过使用显微镜和其他表征技术,对涂层进行质量检查和测试,以确保其满足预期的技术参数。
以上是CVD涂层工艺流程的简要介绍,如需了解更多信息,建议咨询专业人士。
CVD工艺介绍

4.6 CMP 的作用效果
Pre-CMP
During CMP
Post-CMP
The pressure of high step area is much bigger , so the remove rate is much higher , that makes surface global planarity when CMP a long time .
化学气相淀积(Chemical Vapor Deposition)
化学气体或蒸气在晶圆表面产生反应,在表面上以薄膜形式产生固态的产品,其它 的副产品是挥发性的,会从表面离开.
1.2 CVD工艺的特点:
(1)CVD成膜温度远低于体材料的熔点,减轻衬底的热形变,减少玷污,抑制缺陷生成 ,减轻杂质再分布,适于浅结工艺。设备简单、重复性好。 (2)CVD膜的成分可精确控制,配比范围较大。 (3)淀积速率快,产能强。 (4)CVD膜结构致密、完整,与衬底黏附性好,台阶覆盖性能好。
P5000 BPTEOS 淀积: TEOS、O2、
TMB、TMP、NH3 清洗:C2F6 O2
辅助气体:He
APCVD 淀积: SiH4、O2、
BH3、PH3
清洗:HF (清洗皮带) 辅助气体:N2
TR6132 涂布:SOG 21F或 SOG 211 清洗:IPA(异丙醇)
辅助气体:He
P5000 PESIN 淀积: SiH4、NH3 清洗:CF4或者NF3
Step Height: IMD1 CMP Pre - Center SEM Bar
10000 9000 8000 7000 6000 5000 4000 3000 2000 1000 0 1
196 391 586 781 976 1171 1366 1561 1756 1951 2146
cvd纳米金刚石涂层工艺流程

CVD纳米金刚石涂层工艺流程一、概述CVD (化学气相沉积)纳米金刚石涂层工艺是一种先进的表面涂层技术,通过在基材表面沉积纳米级厚度的金刚石薄膜,可以显著提高材料的硬度、耐磨性和耐腐蚀性。
本文将详细介绍CVD纳米金刚石涂层的工艺流程,包括材料选择、表面处理、沉积工艺、质量控制等环节。
二、材料选择1. 基材材料:金属、陶瓷、塑料等材料均可用于CVD纳米金刚石涂层。
常用的基材包括硬质合金、不锈钢、钛合金等。
2. 基材形状:CVD纳米金刚石涂层工艺适用于各种形状的基材,包括平板、管材、复杂形状零件等。
3. 表面粗糙度:基材表面粗糙度对涂层的质量有重要影响,一般要求基材表面粗糙度在Ra<0.4um。
三、表面处理1. 清洗:将基材进行去油、除尘、去氧化处理,以保证涂层与基材之间的良好结合。
2. 粗糙化处理:对于一些表面平整的基材,可以采用砂喷或喷丸处理,增加表面粗糙度,有利于涂层附着。
3. 防粘接处理:在表面处理之后,可以在基材表面进行一些特殊的处理,以增强涂层与基材之间的黏附力。
四、CVD纳米金刚石涂层工艺1. 基材预热:将基材置于CVD反应室中进行预热,通常温度在800-1000摄氏度之间。
2. 气氛控制:在反应室中控制好气氛,通常使用氢气和甲烷混合气体,通过精确控制气氛比例和流量来控制沉积速率和涂层质量。
3. 沉积过程:在预热后的基材表面开始沉积金刚石薄膜,通过化学气相反应在基材表面沉积碳原子,形成金刚石晶粒,不断沉积形成厚度可控的金刚石薄膜。
4. 控制工艺参数:沉积过程中需要严格控制温度、压力、气氛比例、沉积时间等工艺参数,以确保获得高质量的纳米金刚石涂层。
五、质量控制1. 涂层厚度检测:使用X射线衍射仪、激光剥蚀仪等设备对涂层厚度进行检测。
2. 显微结构分析:通过光学显微镜、扫描电子显微镜等设备对涂层显微结构进行分析。
3. 涂层性能测试:对涂层的硬度、耐磨性、耐腐蚀性等性能进行测试,确保涂层符合要求。
第四章 CVD工艺
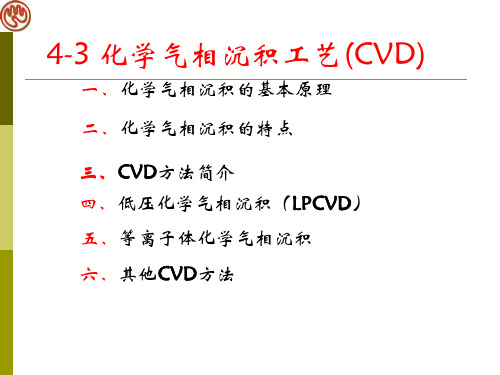
热分解反应(吸热反应)
(2)金属有机化合物
M-C键能小于C-C键,广泛用于沉积金属和氧化物薄膜。
金属有机化合物的分解温度非常低,扩大了基片选
择范围以及避免了基片变形问题。
(3)氢化物和金属有机化合物系统
广泛用于制备化合
物半导体薄膜。
一、化学气相沉积的基本原理
☞化学气相沉积的基本原理
因素对其影响的科学。
CVD反应动力学分析的基本任务是:通过实验研究
薄膜的生长速率,确定过程速率的控制机制,以便进一
步调整工艺参数,获得高质量、厚度均匀的薄膜。
反应速率r是指在反应系统的单位体积中,物质(反应
物或产物)随时间的变化率。
一、化学气相沉积的基本原理
☞化学气相沉积的基本原理
➢ CVD的(化学反应)动力学
热力学分析可作为确定CVD工艺参数的参考。
一、化学气相沉积的基本原理
☞化学气相沉积的基本原理
➢ CVD的化学反应热力学
∆ G r与反应系统的化学平衡常数有关 K P
例:热分解反应
一、化学气相沉积的基本原理
☞化学气相沉积的基本原理
➢ CVD的化学反应热力学
反应方向判据:
可以确定反应温度
一、化学气相沉积的基本原理
光CVD
一、化学气相沉积的基本原理
☞化学气相沉积的基本原理
➢化学气相沉积的定义
化学气相沉积是利用气态物质通过化学反应在基片
表面形成固态薄膜的一种成膜技术。
化学气相沉积(CVD)
——Chemical Vapor Deposition
CVD反应是指反应物为气体而生成物之一为固体的
化学反应。
CVD完全不同于物理气相沉积(PVD)
CVD制程工艺及设备介绍课件

CVD优缺点
1 优点
制备的化学气相沉积薄膜均匀,成膜速度快,沉积时间短;能沉积较复杂的组成均匀和 纯度高的薄膜。
2 缺点
设备复杂,维护麻烦;原料的寿命和成本较高;薄膜厚度难以控制。
总结与展望
总结
本课程介绍了CVD的定义、工艺、设备、应用领 域、优缺点等。我相信,通过本次课程,大家 对CVD会有更深入的了解。
CVD制程工艺及设备介绍 ppt课件
本课程介绍了化学气相沉积(CVD)的基本原理、工艺流程、设备、应用领域, 以及其优缺点。
背景介绍
历史
CVD始于20世纪初,在半导体工业中得到广泛应用。如今,CVD已经被广泛应用于化学、光 电、生物制药等领域。
概念
CVD是一种将外源性固体沉积在基体表面上(化学反应),形成薄膜、涂层或材料的技术。 在气相状态下,通过将气体或蒸汽引入反应室,加热并分解,在基体表面上沉积出新的固体 材料。
采用管式炉结构。在高温情况下, 反应气体由管外注入,通过炉管 加热反应产物,反应产物通过炉 管被输出。
电子感应耦合等离子体 CVD设备
主要由等离子体炉室、渗透源、 泵及阀门、感应线圈等部件组成。 可实现高质量、大面积薄膜和复 杂结构薄膜的制备。
滚筒式CVD设备
可实现大面积、一次性CVD,并 且是一种快速的制备方法,被广 泛应用于批量制备。
展望
CVD技术作为一种新兴技术,未来还有很大的发 展空间和潜力。希望能够有更多的技术革新, 为推动相关产业的发展做出更大的贡献。
发展情况
随着材料科学、微电子技术等领域的迅速发展,CVD技术也得到了迅速发展。目前,CVD已 经成为材料表面修饰以及化学分析中不可或缺的手段之一。
CVD的定义和原理
CVD制程工艺及设备介绍ppt课件
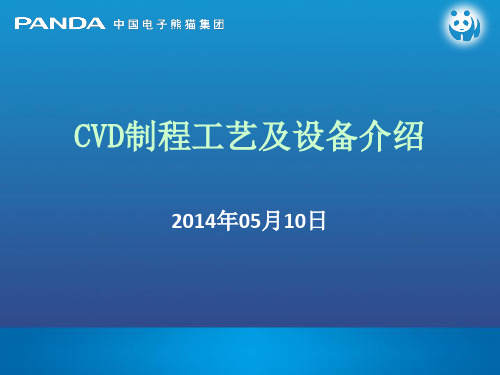
D(漏电极)
Drain
CVD工程在TFT流程中的作用
Pas-SiNx层
a-Si层
G-SiNx 层
N+ a-Si层
TFT断面图
CVD各层膜的用途及特性要求
作用
G-SiNx(栅极绝缘层) a-Si(通道层)
N+ a-Si(欧姆接触层) Pas-SiNx(绝缘保护层)
绝缘保护 电子沟道 信号线性传输 绝缘保护
PECVD反应示意图
气体 原料
与电子碰
撞 离子
等离子体
激发 分解
化学反应
吸着 表面反应
析出 堆积
脱离
PECVD反应过程
基板加热
二次生成物
未反应 气体
排气
再吸着
(1)电子和反应气体发生碰撞,产生大量的活性基; (2)活性基被吸附在基板上,进行表面反应; (3)被吸附的原子在自身动能和基板温度的作用下,在基板表面迁移,选择能量最低的点堆 积下来; (4)同时,基板上的原子不断脱离周围原子的束缚,进入等离子体气氛中参与化学反应,达 到动态的平衡; (5)不断地补充原料气体,使原子沉积速率大于原子逃逸速率,薄膜持续生长; (6)二次生成物和未反应的气体会经排气口排出。
①Trouble时 ②趋势监控
项目 ①Mura ②成膜区域 ③基板破损,划伤 ④异常放电
Particle ① Mura ② Particle
目的 ①特性特性异常 ②成膜区域 ③防止后工程基板裂纹 ④特性异常 点缺陷和线缺陷 ①特性异常 ②点缺陷,线缺陷
① Particle ①特性异常
项目 ①Mura ②成膜区域 ③基板破损,划伤 ④异常放电 ① Mura ② Particle
Gas panel Mainframe control
第四章CVD工艺优质获奖课件

CVD反应是指反应物为气体而生成物之一为固体旳
化学反应。
CVD完全不同于物理气相沉积(PVD)
一、化学气相沉积旳基本原理
☞化学气相沉积旳基本原理
➢ CVD
CVD法实际上很早就有应用,用于材料精制、装
饰涂层、耐氧化涂层、耐腐蚀涂层等。
在电子学方面PVD法用于制作半导体电极等。
CVD法一开始用于硅、锗精制上,随即用于适合
➢ CVD法制备薄膜过程描述
(1)反应气体向基片表面扩散;
(2)反应气体吸附于基片表面;
(3)在基片表面发生化学反应;
(4)在基片表面产生旳气相副产物脱离表面,向空间扩
散或被抽气系统抽走;
(5)基片表面留下不挥发旳固相反应产物——薄膜。
CVD基本原理涉及:反应化学、热力学、动力学、输
运过程、薄膜成核与生长、反应器工程等学科领域。
化学气相沉积工艺(CVD)
一、化学气相沉积旳基本原理
二、化学气相沉积旳特点
三、CVD措施简介
一、化学气相沉积旳基本原理
☞化学气相沉积旳基本原理
➢化学气相沉积旳定义
化学气相沉积是利用气态物质经过化学反应在基片
表面形成固态薄膜旳一种成膜技术。
化学气相沉积(CVD)
——Chemical Vapor Deposition
外延生长法制作旳材料上。
表面保护膜一开始只限于氧化膜、氮化膜等,之
后添加了由Ⅲ、Ⅴ族元素构成旳新旳氧化膜,近来还
开发了金属膜、硅化物膜等。
以上这些薄膜旳CVD制备法为人们所注意。CVD
法制备旳多晶硅膜在器件上得到广泛应用,这是CVD
法最有效旳应用场合。
一、化学气相沉积旳基本原理
☞化学气相沉积旳基本原理
CVD的原理与工艺PPT演示文稿

集成电路制造过程中,常需要在衬底上生长固体材料层; 若固体膜三维尺寸中,某一维尺寸(通常指厚度)远远小于另外 两维上的尺寸,称为薄膜,通常描述薄膜厚度的单位是埃。 薄膜淀积:任何在硅片衬底上物理沉淀聚积一层薄膜的工艺。
•1
薄膜特性
硅片加工中可接受的膜必须具备一定特性:台阶 覆盖能力、深宽比间隙填充能力、厚度均匀性、可 控化学剂量、膜纯度与密度、膜应力、电学特性与 粘附性等。
化学气相淀积
CVD:在反应室内,气态反应物经化学反应生成固态物 质并淀积在硅片表面的薄膜淀积技术; PVD:通过蒸发、电离或溅射等过程,产生固态粒子沉 积在硅片表面或继续与气体反应得到所需薄膜。
CVD的基本特征: 1、产生化学变化(化学反应或热分解); 2、膜中所有材料都来源于外部的源; 3、CVD工艺中反应物必须以气相形式参与反应;
膜纯度和密度:纯度和密度决定影响膜质量的化学元素或原 子的多少和膜层中针孔或空洞多少;
膜应力往往会导致硅片变形,造成膜的开裂与分层等;膜的 电特性和粘附性对器件可靠性和膜层质量有重要影响。
•4
薄膜生长步骤
膜淀积过程有三个不同阶段: 第一步,晶核的形成:成束的稳定小晶核; 第二步,聚集成束—岛生长:岛束沿随机方向生长; 第三步,形成连续的膜:岛束汇集并延伸铺展;
•8
CVD化学原理与步骤
原理:气相反应物中生长晶体的复相物理-化学过程 第一步:气体传输至淀积区域 第二步:膜先驱物的形成与输运 第三步:膜先驱物粘附与扩散 第四步:表面反应,导致膜淀积和副产物的形成
第五步:副产物的移除(表面和反应腔)
•9
CVD传输和反应步骤
•10
CVD反应控制要点
温度与反应速率的限制:温度升高,表面反应速度增加, 过程速率最慢环节决定整个淀积过程的速度。
PVDCVD工艺参数

PVDCVD工艺参数PVD(Physical Vapor Deposition)和CVD(Chemical Vapor Deposition)是两种常用的表面涂层工艺,用于为材料表面添加附着性、耐磨性、耐腐蚀性等功能薄膜。
下面将详细介绍PVD和CVD的工艺参数,以及它们各自的特点和应用。
PVD工艺参数:1.作用气体:PVD过程通常使用惰性气体,如氩气,用于提供等离子体和清除反应生成物。
2.工作压力:标准PVD系统通常在0.1-1Pa的真空范围内工作,以减少气体碰撞和增加薄膜的纯度。
3.沉积速率:沉积速率取决于多个因素,包括材料的性质、沉积温度、工艺参数等。
一般来说,PVD的沉积速率较低,通常在几纳米到几十纳米每分钟。
4.沉积温度:PVD可以在较低的温度下进行,通常在室温到几百摄氏度之间。
较低的沉积温度使得PVD可以用于对温度敏感的基底材料。
5.靶材料:PVD将以所需物质构成的靶材放置在真空腔室中,并使用极性放电和磁控制来释放蒸汽,并形成薄膜。
PVD的特点和应用:1.高纯度薄膜:PVD薄膜具有高纯度和致密性,能够提供优异的耐磨、耐腐蚀和美观性能。
2.可控薄膜厚度:通过调整沉积时间和速率,可以精确控制薄膜的厚度和均匀性,以满足不同的应用需求。
3.易于制备复杂形状薄膜:PVD可以在复杂形状的基底表面上均匀沉积,适用于制备微细结构、凹凸不平的薄膜表面。
4.应用广泛:PVD在很多领域得到应用,如太阳能电池板、LED光源、汽车零部件、钟表、饰品等。
CVD工艺参数:1.反应气体:CVD过程通常使用易于分解的反应气体,如氨、硅烷、四氯化钛等。
反应气体的选择和纯度对薄膜的品质和成分有重要影响。
2.工作压力:CVD系统通常需要较高的工作压力,以保持反应气体在腔体中的适当浓度,并促进分解和沉积。
3.沉积温度:CVD需要较高的沉积温度,通常在数百到上千摄氏度之间。
高温可以促进气体分解和反应的进行,形成致密的薄膜。
4.沉积速率:CVD的沉积速率通常较高,可以达到几微米到几十微米每小时,因此适用于快速生长较厚的薄膜。
cvd工艺步骤

cvd工艺步骤
CVD(化学气相沉积)工艺是一种在高温下使用化学反应使气体产生化学反应生成固体薄膜的方法。
以下是一般CVD工艺的步骤:
1. 准备基片:选择合适的基片材料,并清洗表面以去除杂质和污垢。
2. 预处理基片:在基片表面涂覆一层稳定的催化剂或反应层,以帮助调控化学反应。
3. 封闭反应室:将基片放入反应室中,并确保反应室密封。
4. 加热反应室:将反应室加热至适当的温度,通常在几百至一千摄氏度之间,以促使化学反应发生。
5. 提供反应气体:将需要的反应气体通过适当的通道引入反应室中。
6. 化学反应:在高温下进行的化学反应将反应气体分解,生成粒子或分子,然后在基片表面沉积形成薄膜。
7. 控制沉积速率:根据需要,可以通过调节反应气体浓度、温度和靶材的选择来控制薄膜的沉积速率。
8. 结束反应:在达到所需的薄膜厚度后,停止供应反应气体,并保持温度以保持反应室内的环境稳定。
9. 冷却处理:缓慢降低反应室温度至室温,以避免薄膜受到应力破裂。
10. 取出基片:打开反应室并取出薄膜沉积完毕的基片。
需要注意的是,具体的CVD工艺步骤可能会因所使用的气体和材料而有所不同。
此外,CVD工艺还有其他特殊的变体,如PECVD(辅助等离子体化学气相沉积)和MOCVD(金属有机化学气相沉积),其步骤也有所不同。
CVD工艺简介

.1 LPCVD(低压CVD)一、 LPCVD 工艺简介LPCVD(Low Pressure Chemical Vapor Deposition ):低压气相淀积,是在27-270Pa的反应压力下进行的化学气相淀积。
它的特点是:膜的质量和均匀性好,产量高,成本低,易于实现自动化。
一般工艺流程:装片——进舟——对反应室抽真空——检查设备是否正常——充N2吹扫并升温——再抽真空——保持压力稳定后开始淀积——关闭所有工艺气体,重新抽真空——回冲N2到常压——出炉。
二、低压化学气相淀积Si3N4LP Si3N4在工艺中主要作为局部氧化的掩蔽膜,电容的介质膜等。
CMOS工艺最常用的隔离技术就是LOCOS(硅的选择氧化),它以氮化硅为掩膜实现了硅的选择氧化,在这种工艺中除了形成有源晶体管的区域外,其他所有重掺杂硅区上均生长一层厚的氧化层,该厚氧化层通常称为场氧。
在工艺中我们通常使用的气体是:NH3+ DCS(SiH2Cl2)。
这两种气体的反应生成的Si3N4质量高,副产物少,膜厚均匀性极佳,而且是气体源便于精确控制流量,是目前国内外普遍采用的方法。
反应式: 3SiH2Cl2 + 4NH3 = Si3N4 + 6HCl + 6H2NH3在过量的情况下,HCl与NH3继续反应: HCl+ NH3 = NH4Cl合并为: 10NH3+ 3SiH2Cl2 = Si3N4 + 6H2 + 6NH4Cl目前我们生产使用的温度是780℃,压力为375mt。
在VLSL工艺中,由于沿器件有源区方向上的场氧侵蚀和场注入杂质的横向扩散,使得LOCOS工艺受到很大的限制,场氧的横向侵蚀使LOCOS氧化层和栅氧的交界面形成类似鸟嘴的结构,随着工艺条宽的不断减少,鸟嘴的大小必须加以控制,而SI3N4与硅之间的应力很大,为了避免对硅表面的应力损伤,在硅表面与SI3N4膜之间插入一层薄的SIO2作为应力缓冲层。
因此我们常用的方法是通过改变SIN与二氧的厚度比来减少鸟嘴大小,其中鸟头的高度和鸟嘴的宽度与SI3N4的厚度成反比,与应力缓冲层SIO2的厚度成正比。
PVD、CVD工艺参数

一,化学气相沉积硅薄膜背底真空1.33x10-2Pa热丝电流6 (A)工作气压100Pa气体比例(CH4:SiH4:H2) 3:3:50沉积时间110min二,PECVD沉积氮化硅薄膜1,温度:450o CNH3/SiH4 =8:1总气体流量:4320sccm压力:170pa沉积时间:720s2,:NH3/SiH4流量比的范围为3.5—4.5衬底温度范围为2850C—3150C反应压力90Pa—130Pa淀积时间90s—105s为较理想的沉积工艺条件。
三,PECVD淀积二氧化硅薄膜衬底温度:150-300o CSiH4/CO2=1:3-1:6沉积时间:10-20分钟沉积压力:1.5-2.0托真空度:2x10-2托四,射频磁控溅射制备ZNO薄膜Ar 流量固定为 26 标况毫升每分(sccm)功率:200W压强:1PA五,磁控溅射PbTe 纳米颗粒膜背景真空: 2.0×10-4Pa工作气体:高纯Ar工作压力:0.15 Pa溅射功率:30W退火温度:400℃退火时间:15 min六,磁控溅射CUO薄膜真空度:2.0xlO-4Pa溅射气体:99.999%的高纯氩气沉积室的气压:0.5Pa射频功率:35W衬底温度为200o C溅射时间:1h。
七,磁控溅射硅基薄膜射频频率: 13.56MHz溅射气体:Ar,纯度 99.999%溅射靶材:多晶硅,纯度 99.999%,直径 60mm靶材与基片间的距离:8cm本底真空:1.4X10-4Pa八,磁控溅射制备ZNO-SNS复合膜衬底温度为 400K,真空度为 4 . 0X10-4Pa衬度与蒸发源的距离为 10cm蒸发源温度为 1000o C沉积时间:40min工作气压:0.2pa溅射功率:150W九,三步共蒸法制备CIGS薄膜真空度:10-3以下预蒸镀:5min正式蒸镀:2min预置层退火温度:350-400o CCuln0.7Gao0.3Se2的化学计量比称量原料(Cu:0.18929,ln:0.23939,Ga:0.10269,Se:0.47029)抽真空至3.gx1o一:‘Pa,分三步蒸发Cu、In、Ga、Se材料,而后始终保持真空度为 3.9x10-3Pa 以下,快速加热至所需温度进行原位真空退火.第一步:常温下共蒸发工n、Ga、Se约1.smin,退火30min。
CVD 工艺

2015/10/25
23
比值J/D:当气相射入到衬底表面上的硅原
子流J和硅原子在衬底表面上的扩散系数 D的比值,J/D,小时,在硅单晶衬底上 的淀积物将具有长程有序,得到单晶薄 膜;反之,当J/D比值大时,则淀积膜将 短程有序,从多晶硅向无定形硅转化。
2015/10/25
24
生长方法
A.常压CVD: I)区:单晶;ii)区多晶;无定形硅。 B.低压CVD : J/D 增加 550℃生长, 再经过900℃退火处理 600℃~650℃生长的多晶硅,以(100)为 优选晶向。
2015/10/25
27
(式三)表示吸附,(式四)表示分解。其
中g,s分别表示气态和固态。在充分吸附 的情况下,(式二)和(式三)处于平衡状 态下,而(式四)即(Si-H*)的热分解过 程将决定淀积率。当衬底温度一定时, 即分解率一定时,淀积率将直接与吸附 反应剂分子的多少有关.
2015/10/25 28
2015/10/25
29
三簇元素,如硼,掺杂使将增加空穴,
它的表面吸附有助于表面呈现正电性, 因而将促进多晶硅的淀积。 而五簇元素,如磷、砷的掺杂,将有助 于表面的电子积累,从而减少分子的吸 附,减少浓度,因而将降低多晶硅的淀 积率。
2015/10/25
30
B、掺杂对多晶硅形貌和晶粒大小的影响: 晶粒生长机构是扩散控制机构。晶粒长 大的过程是由一系列原子通过晶粒间界 的扩散运动所形成的,晶粒生长速率是 由硅原子通过晶粒间界的自扩散速率所 决定。 具体地则于两个因素有关:促使原子运 动的外界驱动力和硅的自扩散系数。
A、等离子淀积优点及方程式:等离子增 强CVD的突出优点是淀积温度低,最常 用的温度是300-3500C。等离子体增强 化学气相淀积氮化硅,常由SiH4与氨在 氩等离子气氛下或SiH4在氮等离子气氛 下反应生成,其反应式如下:
- 1、下载文档前请自行甄别文档内容的完整性,平台不提供额外的编辑、内容补充、找答案等附加服务。
- 2、"仅部分预览"的文档,不可在线预览部分如存在完整性等问题,可反馈申请退款(可完整预览的文档不适用该条件!)。
- 3、如文档侵犯您的权益,请联系客服反馈,我们会尽快为您处理(人工客服工作时间:9:00-18:30)。
第21页共23页
拟 制PI审 核
设备名称
适用产品Recipe No
NPCVP02
PH232001.5120075033607850
PH26
注意事项:1. 异常时请及时通知值班工程师; 2. 请注意工艺卡的版本日期及更新状况;
生效日期
2014.08.20
Temperature (Inner /℃)285±10Temperature (Outer /℃)
295
±10
PL
PH Time (s)
8
58±10%N2(sccm)
13100
7850
±7%
二级管控参数
制程站点设备工艺参数名称设备工艺参数指标允许变化范围
SiH4(sccm)220750±5%NH3(sccm)22403360±5%Pressure(Torr) 1.2 1.5±5%Space(mils)800900±50PL
PH R/F Power(W)22703200±5%N2
空气化工
NA
>99.9997%
一级管控参数
制程站点
设备工艺参数名称
设备工艺参数指标
允许变化范围
SiH4液化空气NA >99.9999%NH3昭和化学、联华林德
NA >99.9995%CVD200
PSIN:2000A的所有产品
Recipe Name
主要材料
材料名称
材料生产厂家材料型号材料规格文件编号: C-WI01007 附件3 版号:1.1Passivation Depo 工艺卡
李金万
审 核
批 准。