CPC1824N;中文规格书,Datasheet资料
744230181;中文规格书,Datasheet资料

2.1 2.0 1.02012-07-172012-07-172010-09-30SStSStSBaSStSBaWürth Elektronik eiSos GmbH & Co. KGEMC & Inductive SolutionsMax-Eyth-Str. 174638 WaldenburgGermanyTel. +49 (0) 79 42 945 - 0A Dimensions: [mm]F Typical Impedance Characteristics:H1: Classification Reflow Profile for SMT components:H2: Classification Reflow ProfilesProfile FeaturePreheat- Temperature Min (T smin ) - Temperature Max (T smax ) - Time (t s ) from (T smin to T smax )Ramp-up rate (T L to T P )Liquidous temperature (T L )Time (t L ) maintained above T L Peak package body temperature (T p )Time within 5°C of actual peak temperature (t p )Ramp-down rate (T P to T L )Time 25°C to peak temperature Pb-Free Assembly 150°C 200°C60-180 seconds 3°C/ second max.217°C60-150 seconds See Table H320-30 seconds 6°C/ second max.8 minutes max.refer to IPC/JEDEC J-STD-020DH3: Package Classification Reflow TemperaturePB-Free Assembly PB-Free Assembly PB-Free Assembly Package Thickness< 1.6 mm 1.6 - 2.5 mm ≥ 2.5 mmVolume mm³<350260°C 260°C 250°CVolume mm³350 - 2000260°C 250°C 245°CVolume mm³>2000260°C 245°C 245°Crefer to IPC/JEDEC J-STD-020DH Soldering Specifications:I Cautions and Warnings:The following conditions apply to all goods within the product series of WE-CNSWof Würth Elektronik eiSos GmbH & Co. KG:General:All recommendations according to the general technical specifications of the data sheet have to be complied with.The disposal and operation of the product within ambient conditions which probably alloy or harm the wire isolation has to be avoided.If the product is potted in customer applications, the potting material might shrink during and after hardening. Accordingly to this the product is exposed to the pressure of the potting material with the effect that the core, wire and termination is possibly damaged by this pressure and so the electrical as well as the mechanical characteristics are endanger to be affected. After the potting material is cured, the core, wire and termination of the product have to be checked if any reduced electrical or mechanical functions or destructions have occurred.The responsibility for the applicability of customer specific products and use in a particular customer design is always within the authority of the customer. All technical specifications for standard products do also apply for customer specific products.Cleaning solvents which are used to clean the application might damage or change the characteristics of the component.Direct mechanical impact to the product shall be prevented as the ferrite material of the core could flake or in the worst case it could break. Product specific:Follow all instructions mentioned in the datasheet, especially:•The soldering profile has to be complied with according to the technical reflow soldering specification, otherwise no warranty will be su-stained.•All products are supposed to be used before the end of the period of 12 months based on the transfer of title, if not a 100% solderability can´t be warranted.•Violation of the technical product specifications such as exceeding the nominal rated current will result in the loss of warranty.1. General Customer ResponsibilitySome goods within the product range of Würth Elektronik eiSos GmbH & Co. KG contain statements regarding general suitability for certain application areas. These statements about suitability are based on our knowledge and experience of typical requirements concerning the are-as, serve as general guidance and cannot be estimated as binding statements about the suitability for a customer application. The responsibi-lity for the applicability and use in a particular customer design is always solely within the authority of the customer. Due to this fact it is up to the customer to evaluate, where appropriate to investigate and decide whether the device with the specific product characteristics described in the product specification is valid and suitable for the respective customer application or not.2. Customer Responsibility related to Specific, in particular Safety-Relevant ApplicationsIt has to be clearly pointed out that the possibility of a malfunction of electronic components or failure before the end of the usual lifetime can-not be completely eliminated in the current state of the art, even if the products are operated within the range of the specifications.In certain customer applications requiring a very high level of safety and especially in customer applications in which the malfunction or failure of an electronic component could endanger human life or health it must be ensured by most advanced technological aid of suitable design of the customer application that no injury or damage is caused to third parties in the event of malfunction or failure of an electronic component.3. Best Care and AttentionAny product-specific notes, warnings and cautions must be strictly observed.4. Customer Support for Product SpecificationsSome products within the product range may contain substances which are subject to restrictions in certain jurisdictions in order to serve spe-cific technical requirements. Necessary information is available on request. In this case the field sales engineer or the internal sales person in charge should be contacted who will be happy to support in this matter.5. Product R&DDue to constant product improvement product specifications may change from time to time. As a standard reporting procedure of the Product Change Notification (PCN) according to the JEDEC-Standard inform about minor and major changes. In case of further queries regarding the PCN, the field sales engineer or the internal sales person in charge should be contacted. The basic responsibility of the customer as per Secti-on 1 and 2 remains unaffected.6. Product Life CycleDue to technical progress and economical evaluation we also reserve the right to discontinue production and delivery of products. As a stan-dard reporting procedure of the Product Termination Notification (PTN) according to the JEDEC-Standard we will inform at an early stage about inevitable product discontinuance. According to this we cannot guarantee that all products within our product range will always be available. Therefore it needs to be verified with the field sales engineer or the internal sales person in charge about the current product availability ex-pectancy before or when the product for application design-in disposal is considered.The approach named above does not apply in the case of individual agreements deviating from the foregoing for customer-specific products.7. Property RightsAll the rights for contractual products produced by Würth Elektronik eiSos GmbH & Co. KG on the basis of ideas, development contracts as well as models or templates that are subject to copyright, patent or commercial protection supplied to the customer will remain with Würth Elektronik eiSos GmbH & Co. KG.8. General Terms and ConditionsUnless otherwise agreed in individual contracts, all orders are subject to the current version of the “General Terms and Conditions of Würth Elektronik eiSos Group”, last version available at .J Important Notes:The following conditions apply to all goods within the product range of Würth Elektronik eiSos GmbH & Co. KG:分销商库存信息: WURTH-ELECTRONICS 744230181。
nRF24L01P产品说明书V1.0资料
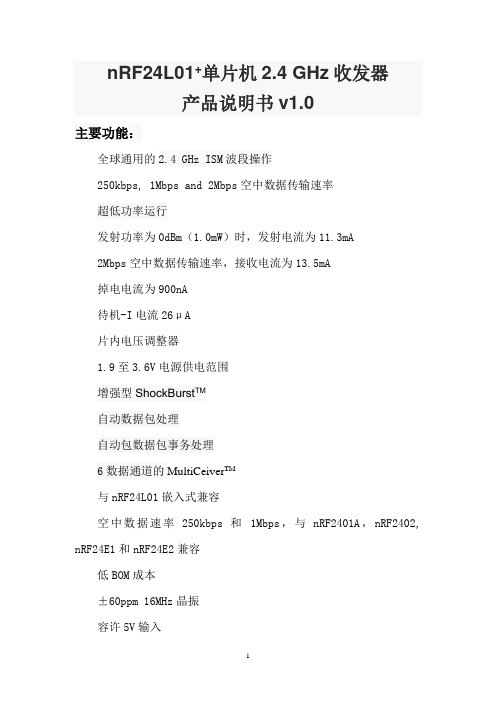
nRF24L01+单片机2.4 GHz收发器产品说明书v1.0主要功能:全球通用的2.4 GHz ISM波段操作250kbps, 1Mbps and 2Mbps空中数据传输速率超低功率运行发射功率为0dBm(1.0mW)时,发射电流为11.3mA2Mbps空中数据传输速率,接收电流为13.5mA掉电电流为900nA待机-I电流26μA片内电压调整器1.9至3.6V电源供电范围增强型ShockBurst TM自动数据包处理自动包数据包事务处理6数据通道的MultiCeiver TM与nRF24L01嵌入式兼容空中数据速率250kbps 和1Mbps,与nRF2401A,nRF2402, nRF24E1和nRF24E2兼容低BOM成本±60ppm 16MHz晶振容许5V输入紧凑的20引脚4x4mm QFN封装应用无线 PC外围设备鼠标,键盘和遥控器三和一桌面捆绑先进的媒体中心遥控器网络电话耳机游戏控制器蓝牙模块运动手表和传感器消费电子产品射频遥控器家庭和商业自动化超低功率无线传感器网络RFID 射频识别资产跟踪系统玩具免责条款北欧半导体ASA有权做出随时更改,提高产品可靠性、功能或设计,不另行通知。
北欧半导体ASA不承担由于应用程序或使用任何所述产品或电路引起的责任。
所有应用程序的信息咨询,不构成说明书的组成部分。
极限值超过一个或多个限制的应力可能会造成设备永久性损坏。
这些应力等级只有在这样或那样的操作环境中提出,在规范中没有给出。
长时间暴露在限制值附近可能会影响设备的可靠性。
生命支持应用这些产品并非为因故障会引起人身伤害的维生装备,设备或系统设计的。
北欧半导体ASA客户使用或出售这些产品,他们将自担风险并同意完全赔偿北欧半导体ASA因使用不当或销售行为造成任何损害。
详细联系方式访问www.nordicsemi.no进入北欧半导体销售办事处和全世界的分销商网站总办公室:Otto Nielsens vei 127004 Trondheim电话: +47 72 89 89 00传真: +47 72 89 89 89www.nordicsemi.no写作惯例本产品规范遵循一套排版规则,文档一致,容易阅读。
NSW1824说明书
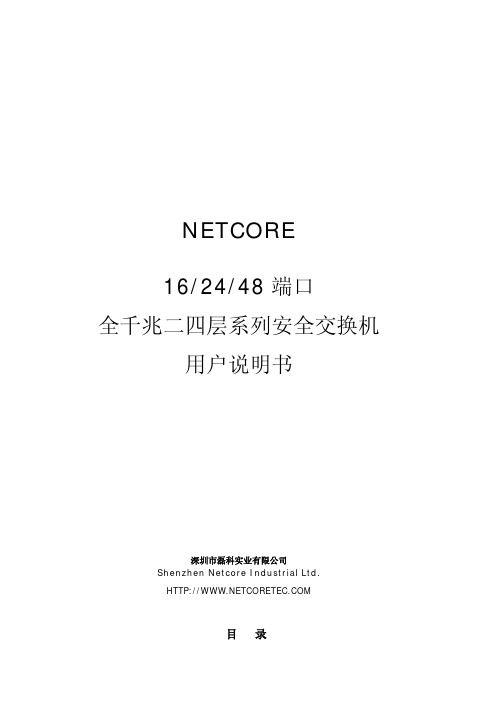
NETCORE16/24/48端口全千兆二四层系列安全交换机用户说明书深圳市磊科实业有限公司Shenzhen Netcore Industrial Ltd.目录第一章 前 言 (5)1.1公司简介 (5)1.2约定 (5)1.3说明 (5)1.4版权、商标声明 (6)第二章 认识NETCORE二四层安全交换机 (7)2.1产品特性 (7)2.1.1硬件特性 (7)2.1.2网络协议 (7)2.1.3网络应用 (7)2.1.4支持强大QoS能力 (8)2.1.5管理方式 (8)2.1.6系统升级、参数备份和恢复 (8)2.2面板布置 (8)2.2.1前面板 (8)2.2.2后面板 (9)2.2.3侧面板 (9)2.2.4 LED指示灯 (9)2.2.5 技术指标 (10)第三章 安装方法 (11)3.1安置方法 (11)3.2安装在桌面上的方法 (12)3.3安装在机架中的方法 (12)3.4加电 (12)第四章 交换机的连接方法 (12)4.1交换机的连接 (12)4.2与网络最终节点的连接方法 (13)4.3与其它HUB或交换机的连接方法 (13)第五章 配置您的交换机 (14)5.1概述 (14)5.2管理方式 (14)5.2.1 Web管理方式(HTTP) (14)5.2.2 控制台方式(CONSOLE) (16)第六章 交换机的功能配置指南 (17)6.1系统管理 (17)6.1.1 IP地址 (17)6.1.2 修改密码 (17)6.1.3 MAC地址 (18)6.1.4 CONSOLE信息 (18)6.1.5 管理VLAN (18)6.1.6 系统升级 (19)6.1.7 参数保存 (19)6.1.8 参数备份与恢复 (19)6.1.9 恢复缺省参数 (20)6.1.10 重新启动 (20)6.2端口管理 (21)6.2.1 端口配置 (21)6.2.2 端口带宽限制 (22)6.3冗余与备份 (24)6.3.1 链路聚合原理 (24)6.3.2 Netcore 二、四层安全交换机的链路聚合方式 (24)6.3.3 Netcore 二、四层安全交换机的链路聚合配置 (25)6.4安全 (26)6.4.1 安全防御 (26)6.4.2 VLAN配置 (26)6.4.3 MAC地址绑定 (39)6.4.4 MAC地址过滤 (40)6.4.5 MAC地址老化 (41)6.4.6 MAC地址老化 (42)6.5Q O S (43)6.5.1 QoS 简介 (43)6.5.2 QoS 配置 (45)6.7网络分析 (50)6.7.1 端口镜像 (50)6.8网络分析 (51)6.8.1 主机安全保护 (51)6.8.2 应用程序优先级 (57)第七章常见问题和处理方法 (59)7.1开机故障 (59)7.1.1 电源故障 (59)7.1.2 交换机启动故障 (59)7.2以太链路故障 (59)7.2.1 概述 (59)7.2.2 链路状态指示灯显示不正常(Link-Error) (59)7.2.3 链路状态指示灯显示正常但无法通讯 (60)7.3无法远程登陆管理交换机 (60)7.3.1概述 (60)7.3.2 检查IP地址设置 (60)7.3.3 检查远程登录帐号 (60)附录 (62)附录A配件清单 (62)附录B FCC认证 (62)第一章 前 言1.1公司简介衷心感谢您选用NETCORE产品!您将得到长期、全面和高质量的服务!NETCORE公司1988年正式成立于台湾,是新竹工业园早期创业者之一,作为国际知名的网络通信专业厂商,主要从事于局域网络、无线网络、SOHO网络以及通讯产品研发、生产和销售。
0458021211;中文规格书,Datasheet资料

This document was generated on 08/14/2012PLEASE CHECK FOR LATEST PART INFORMATIONPart Number:45802-1211Status:ActiveOverview:HD Mezz™Description:1.20mm by2.00mm Pitch HD Mezz™ Receptacle, 143 Circuits, 18.00mm Unmated Height, 11 Rows, Lead-FreeDocuments:3D ModelProduct Specification PS-45802-001 (PDF)Drawing (PDF)RoHS Certificate of Compliance (PDF)Agency CertificationCSA LR19980ULE29179GeneralProduct Family PCB Receptacles Series45802Application Board-to-Board, SignalComments 1.20mm Pitch Pin-to-Pin and 2.00mm Pitch Row-to-Row OverviewHD Mezz™Product Name Mezzanine UPC822350629713PhysicalCircuits (Loaded)143Circuits (maximum)143Color - ResinBlack Durability (mating cycles max)100Flammability94V-0Glow-Wire Compliant No Guide to Mating Part No Keying to Mating Part None Lock to Mating Part YesMaterial - MetalHigh Performance Alloy (HPA)Material - Plating MatingGold Material - Plating Termination TinMaterial - Resin High Temperature Thermoplastic Net Weight15.463/g Number of Rows 11Orientation Vertical PCB Locator Yes PCB RetentionYes PCB Thickness - Recommended 1.60mm Packaging TypeTray Pitch - Mating Interface2.00mm Pitch - Termination Interface 2.00mm Plating min - Mating0.762µm Plating min - Termination 2.540µm Polarized to Mating Part Yes Polarized to PCB YesRobotic Placement Vacuum Pick-Up Tape StackableNo Surface Mount Compatible (SMC)YesTemperature Range - Operating -55°C to +105°C Termination Interface: Style Surface Mount Unmated Height18.00mmSeriesimage - Reference onlyEU RoHSChina RoHSELV and RoHS Compliant REACH SVHCContains SVHC: No Low-Halogen Status Not ReviewedNeed more information on product environmental compliance?Email productcompliance@For a multiple part number RoHS Certificate of Compliance, click herePlease visit the Contact Us section for any non-product compliance questions.Search Parts in this Series 45802SeriesMates With45830 HD Mezz™ PlugElectricalCurrent - Maximum per Contact2AGrounding to PCB NoVoltage - Maximum250V ACSolder Process DataDuration at Max. Process Temperature (seconds)20Lead-free Process Capability Reflow Capable (SMT only)Max. Cycles at Max. Process Temperature2Process Temperature max. C260Material InfoReference - Drawing NumbersProduct Specification PS-45802-001Sales Drawing SD-45802-0001, SD-45802-0002This document was generated on 08/14/2012PLEASE CHECK FOR LATEST PART INFORMATION分销商库存信息: MOLEX 0458021211。
H1102NLT;HX1188NLT;HX1198NL;H1100NL;H1102NL;中文规格书,Datasheet资料
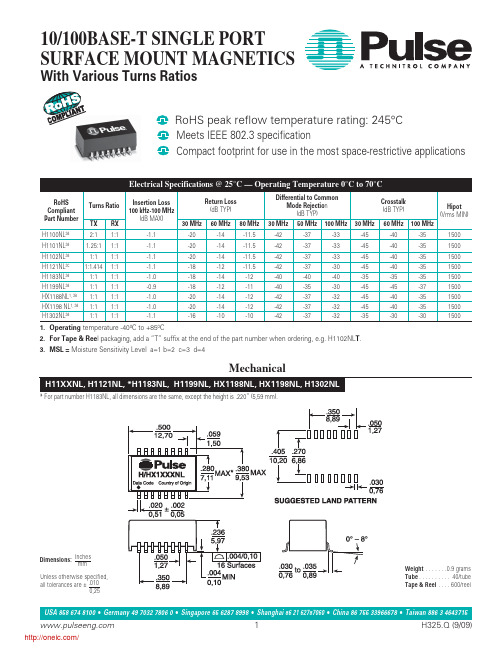
-30
-45
-40
-35
1500
-18
-14
-12
-40
-40
-40
-35
-35
-35
1500
-18
-12
-11
-40
-35
-30
-45
-45
-37
1500
-20
-14
-12
-42
-37
-32
-45
-40
-35
1500
-20
-14
-12
-42
-37
-32
-45
-40
-35
1500
-16
-10
-10
-42
1
16
2
15
3
14
RECEIVE
6
11
7
10
8
9
TRANSMIT
1
16
3
ቤተ መጻሕፍቲ ባይዱ14
2
1:1
15
RECEIVE
7
10
6
11
8
1:1
9
HX1198NL, H1183NL
H1302NL
1
16
TRANSMIT
1
2 16
15
2
15
3 1:1
14
3
14
4
1:1
13
5
12
RECEIVE
6
11
6
11
7
10
7
10
8
1:1
9
Pulse North China Room 2704/2705 Super Ocean Finance Ctr. 2067 Yan An Rd. West Shanghai 200336 China
CPC1008N;CPC1008NTR;中文规格书,Datasheet资料

3
/
CPC1008N
0 4.4 4.6 4.8 5.0 5.2 On-Resistance (:) 5.4 5.6
0 106 109 112 115 118 121 Blocking Voltage (VP) 124
Typical LED Forward Voltage Drop vs. Temperature
1.6 LED Forward Voltage (V) Turn-On Time (ms) 1.5 1.4 1.3 1.2 1.1 IF=50mA IF=20mA IF=10mA IF=5mA IF=2mA -20 0 20 40 60 Temperature (ºC) 80 100 2.5 2.0 1.5 1.0 0.5 0.0 0
1
Absolute Maximum Ratings are stress ratings. Stresses in excess of these ratings can cause permanent damage to the device. Functional operation of the device at conditions beyond those indicated in the operational sections of this data sheet is not implied.
25 20 15 10 5 0
20
20
Device Count (N)
Device Count (N)
Device Count (N)
15
15
10
10
5
5
0 1.250 1.255 1.260 1.265 1.270 LED Forward Voltage (V) 1.275 0.85 0.90 0.95 1.00 1.05 1.10 Turn-On Time (ms) 1.15
LMD18245TNOPB;中文规格书,Datasheet资料

LMD18245LMD18245 3A, 55V DMOS Full-Bridge Motor DriverLiterature Number: SNVS110DLMD182453A,55V DMOS Full-Bridge Motor DriverGeneral DescriptionThe LMD18245full-bridge power amplifier incorporates all the circuit blocks required to drive and control current in a brushed type DC motor or one phase of a bipolar stepper motor.The multi-technology process used to build the device combines bipolar and CMOS control and protection circuitry with DMOS power switches on the same monolithic struc-ture.The LMD18245controls the motor current via a fixed off-time chopper technique.An all DMOS H-bridge power stage delivers continuous out-put currents up to 3A (6A peak)at supply voltages up to 55V.The DMOS power switches feature low R DS(ON)for high efficiency,and a diode intrinsic to the DMOS body structure eliminates the discrete diodes typically required to clamp bipolar power stages.An innovative current sensing method eliminates the power loss associated with a sense resistor in series with the motor.A four-bit digital-to-analog converter (DAC)provides a digital path for controlling the motor current,and,by extension,simplifies implementation of full,half and microstep stepper motor drives.For higher resolution applications,an external DAC can be used.Featuresn DMOS power stage rated at 55V and 3A continuous n Low R DS(ON)of typically 0.3Ωper power switch n Internal clamp diodesn Low-loss current sensing methodn Digital or analog control of motor current n TTL and CMOS compatible inputsn Thermal shutdown (outputs off)at T J =155˚C n Overcurrent protection n No shoot-through currentsn15-lead TO-220molded power packageApplicationsn Full,half and microstep stepper motor drivesn Stepper motor and brushed DC motor servo drives n Automated factory,medical and office equipmentFunctional Block and Connection Diagram(15-Lead TO-220Molded Power Package (T))01187801Order Number LMD18245T See NS Package Number TA15A©2006National Semiconductor Corporation 01187802Top View15-Lead TO-220Molded Power PackageOrder Number LMD18245TSee NS Package Number TA15APinout Descriptions(See Functional Block and Connection Diagrams)Pin1,OUT1:Output node of the first half H-bridge.Pin2,COMP OUT:Output of the comparator.If the voltage at CS OUT exceeds that provided by the DAC,the compara-tor triggers the monostable.Pin3,RC:Monostable timing node.A parallel resistorca-pacitor network connected between this node and ground sets the monostable timing pulse at about1.1RC seconds. Pin5,PGND:Ground return node of the power bridge.Bond wires(internaI)connect PGND to the tab of the TO-220 package.Pins4and6through8,M4through M1:Digital inputs of the DAC.These inputs make up a four-bit binary number with M4as the most significant bit or MSB.The DAC pro-vides an analog voltage directly proportional to the binary number applied at M4through M1.Pin9,V CC:Power supply node.Pin10,BRAKE:Brake logic input.Pulling the BRAKE input logic-high activates both sourcing switches of the power bridge—effectively shorting the load.See Table1.Shorting the load in this manner forces the load current to recirculate and decay to zero.Pin11,DIRECTION:Direction logic input.The logic level at this input dictates the direction of current flow in the load. See Table1.Pin12,SGND:Ground return node of all signal level c Pin13,CS OUT:Output of the current sense amplifie current sense amplifier sources250µA(typical)per a of total forward current conducted by the upper two sw of the power bridge.Pin14,DAC REF:Voltage reference input of the DA DAC provides an analog voltage equal to V DAC REF x where D is the decimal equivalent(0–15)of the number applied at M4through M1.Pin15,OUT2:Output node of the second half H-brTABLE1.Switch Control Logic Truth Table BRAKE DIRECTION MONO Active SwitchH X X Source1,SourceL H L Source2L H H Source2,Sink1L L L Source1L L H Source1,Sink2 X=don’t careMONO is the output of the monostable.L2please contact the National Semiconductor Sales Office/ Distributors for availability and specifications.DC Voltage at:OUT1,V CC,and OUT2+60V COMP OUT,RC,M4,M3,M2,M1,BRAKE,+12VDIRECTION,CS OUT,and DAC REFDC Voltage PGND to SGND±400mV Continuous Load Current3A Peak Load Current(Note2)6A Junction Temperature(T J(max))+150˚C Power Dissipation(Note3):ESD Susceptibility(Note4)1500V Storage Temperature Range(T S)−40˚C to+150˚C Lead Temperature(Soldering,10seconds)300˚COperating Conditions(Note1) Temperature Range(T J)(Note3)−40˚C to+125˚C Supply Voltage Range(V CC)+12V to+55V CS OUT Voltage Range0V to+5V DAC REF Voltage Range0V to+5V MONOSTABLE Pulse Range10µs to100msElectrical Characteristics(Note2)The following specifications apply for V CC=+42V,unless otherwise stated.Boldface limits apply over the operating tem-perature range,−40˚C≤T J≤+125˚C.All other limits apply for T A=T J=25˚C.Symbol Parameter Conditions Typical Limit Units(Note5)(Note5)(Limits)I CC Quiescent Supply Current DAC REF=0V,V CC=+20V8mA15mA(max) POWER OUTPUT STAGER DS(ON)Switch ON Resistance I LOAD=3A0.30.4Ω(max)0.6Ω(max)I LOAD=6A0.30.4Ω(max)0.6Ω(max)V DIODE Body Diode Forward Voltage I DIODE=3A 1.0V1.5V(max)T rr Diode Reverse Recovery Time I DIODE=1A80nsQ rr Diode Reverse Recovery Charge I DIODE=1A40nCt D(ON)Output Turn ON Delay TimeSourcing Outputs I LOAD=3A5µsSinking Outputs I LOAD=3A900nst D(OFF)Output Turn OFF Delay TimeSourcing Outputs I LOAD=3A600nsSinking Outputs I LOAD=3A400nst ON Output Turn ON Switching TimeSourcing Outputs I LOAD=3A40µsSinking Outputs I LOAD=3A1µst OFF Output Turn OFF Switching TimeSourcing Outputs I LOAD=3A200nsSinking Outputs I LOAD=3A80nst pw Minimum Input Pulse Width Pins10and112µst DB Minimum Dead Band(Note6)40ns CURRENT SENSE AMPLIFIERCurrent Sense Output I LOAD=1A(Note7)200µA(min)250175µA(min)300µA(max)325µA(max) Current Sense Linearity Error0.5A≤I LOAD≤3A(Note7)±6%±9%(max)3perature range,−40˚C≤T J≤+125˚C.All other limits apply for T A=T J=25˚C.LSymbol Parameter Conditions Typical Limit U(Note5)(Note5)(L CURRENT SENSE AMPLIFIERCurrent Sense Offset I LOAD=0A520µA DIGITAL-TO-ANALOG CONVERTER(DAC)Resolution4BitMonotonicity4BitTotal Unadjusted Error0.1250.25LSB0.5LSBPropagation Delay50I REF DAC REF Input Current DAC REF=+5V−0.5±10µA COMPARATOR AND MONOSTABLEComparator High Output Level 6.27Comparator Low Output Level88Comparator Output CurrentSource0.2Sink 3.2t DELAY Monostable Turn OFF Delay(Note8) 1.22.0µsPROTECTION AND PACKAGE THERMAL RESISTANCESUndervoltage Lockout,V CC5V8V T JSD Shutdown Temperature,T J155Package Thermal ResistancesθJC Junction-to-Case,TO-220 1.5˚θJA Junction-to-Ambient,TO-22035˚LOGIC INPUTSV IL Low Level Input Voltage−0.1V0.8VV IH High Level Input Voltage2V12VI IN Input Current V IN=0V or12V±10µANote1:Absolute Maximum Ratings indicate limits beyond which damage to the device may occur.Electrical specifications do not apply when operating th outside the rated Operating Conditions.Note2:Unless otherwise stated,load currents are pulses with widths less than2ms and duty cycles less than5%.Note3:The maximum allowable power dissipation at any ambient temperature is P Max=(125−T A)/θJA,where125˚C is the maximum junction temper operation,T A is the ambient temperature in˚C,andθJA is the junction-to-ambient thermal resistance in˚C/W.Exceeding P max voids the Electrical Specifica forcing T J above125˚C.If the junction temperature exceeds155˚C,internal circuitry disables the power bridge.When a heatsink is used,θJA is the su junction-to-case thermal resistance of the package,θJC,and the case-to-ambient thermal resistance of the heatsink.Note4:ESD rating is based on the human body model of100pF discharged through a1.5kΩresistor.M1,M2,M3and M4,pins8,7,6and4are pro 800V.Note5:All limits are100%production tested at25˚C.Temperature extreme limits are guaranteed via correlation using accepted SQC(Statistical Quality methods.All limits are used to calculate AOQL(Average Outgoing Quality Level).Typicals are at T J=25˚C and represent the most likely parametric nor Note6:Asymmetric turn OFF and ON delay times and switching times ensure a switch turns OFF before the other switch in the same half H-bridge begin ON(preventing momentary short circuits between the power supply and ground).The transitional period during which both switches are OFF is commonly to as the dead band.Note7:(I LOAD,I SENSE)data points are taken for load currents of0.5A,1A,2A and3A.The current sense gain is specified as I SENSE/I LOAD for the1A da The current sense linearity is specified as the slope of the line between the0.5A and1A data points minus the slope of the line between the2A and3A da all divided by the slope of the line between the0.5A and1A data points.Note8:Turn OFF delay,t DELAY,is defined as the time from the voltage at the output of the current sense amplifier reaching the DAC output voltage to t DMOS switch beginning to turn OFF.With V CC=32V,DIRECTION high,and200Ωconnected between OUT1and V CC,the voltage at RC is increased fro 5V at1.2V/µs,and t DELAY is measured as the time from the voltage at RC reaching2V to the time the voltage at OUT1reaches3V.4RDS(ON)vs Temperature RDS(ON)vs Load Current0118782901187830RDS(ON)vs Supply Voltage Current Sense Output vs Load Current0118783101187832Supply Current vs Supply Voltage Supply Current vs Temperature01187833011878345TYPICAL OPERATION OF A CHOPPER AMPLIFIER Chopper amplifiers employ feedback driven switching of a power bridge to control and limit current in the winding of a motor(Figure1).The bridge consists of four solid state power switches and four diodes connected in an H configu-ration.Control circuitry(not shown)monitors the winding current and compares it to a threshold.While the winding current remains less than the threshold,a source switch and a sink switch in opposite halves of the bridge force the supply voltage across the winding,and the winding current increases rapidly towards V CC/R(Figure1a and Figure1d). As the winding current surpasses the threshold,the control circuitry turns OFF the sink switch for a fixed period or rent recirculates and decays slowly towards zero(Fig and Figure1e).At the end of the off-time,the cont cuitry turns back ON the sink switch,and the winding c again increases rapidly towards V CC/R(Figure1a an ure1d again).The above sequence repeats to pro current chopping action that limits the winding curren threshold(Figure1g).Chopping only occurs if the w current reaches the threshold.During a change in the tion of the winding current,the diodes provide a deca for the initial winding current(Figure1c and Figur Since the bridge shorts the winding for a fixed perio type of chopper amplifier is commonly referred to as off-time chopper.L6(a)01187803(b)01187804(c)01187805(d)01187806(e)01187807(f)01187808(g)01187809FIGURE 1.Chopper Amplifier Chopping States:Full V CC Applied Across the Winding (a)and (d),Shorted Winding (b)and (e),Winding Current Decays During a Change in the Direction of the Winding Current (c)and (f),and theChopped Winding Current (g)7The LMD18245incorporates all the circuit blocks needed to implement a fixed off-time chopper amplifier.These blocks include:an all DMOS,full H-bridge with clamp diodes,an amplifier for sensing the load current,a comparator,a monostable,and a DAC for digital control of the chopping threshold.Also incorporated are logic,level shifting and drive blocks for digital control of the direction of the load current and braking.THE H-BRIDGEThe power stage consists of four DMOS power switches and associated body diodes connected in an H-bridge configura-tion(Figure2).The time constant to charge or discharge any inductor,in this case the motor windings,is defined as:τ=L/Rwhere L is the winding inductance,and R is the sum of the series resistance in the current path including the winding resistance.Turning ON a source switch and a sink switch in opposite halves of the bridge forces the full supply voltage less the creases exponentially towards a limit dictated by the voltage,the switch drops(I x R DS(ON)),and the w resistance.However,the winding current exponential increase will end when the current chopping circui comes active.Subsequently turning OFF the sink switch causes a v transient that forward biases the body diode of the source switch.The diode clamps the transient at one drop above the supply voltage and provides an alte current path.While the bridge remains in this state,it tially shorts the winding,the winding current recirculat decays exponentially towards zero at a rate that is d by the L/R time constant.During a change in the direction of the winding curren the switches and the body diodes provide a decay p the initial winding current(Figure3).During actual motor operation there are many variabl can effect the motor winding magnetic behavior and mance.Resonance,eddy currents,friction,motor lo damping,temperature coefficients of the windings,are few.These are all issues that are beyond the scope this data sheet.L80118781001187811FIGURE2.The DMOS H-Bridge9分销商库存信息: NATIONAL-SEMICONDUCTOR LMD18245T/NOPB。
414;中文规格书,Datasheet资料
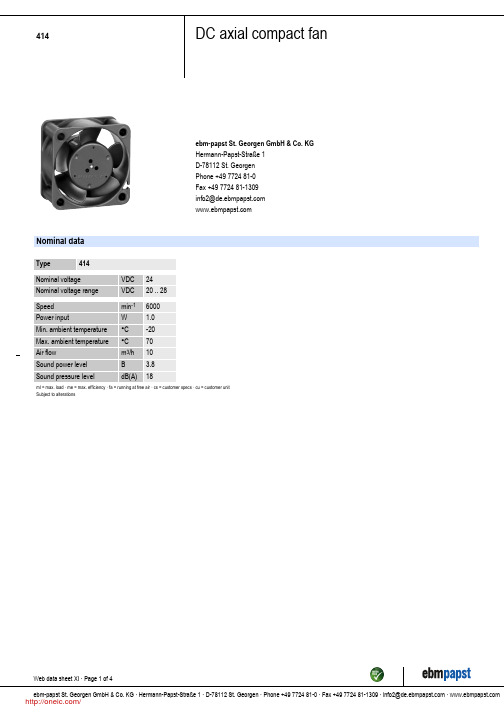
/
414
DC axial compact fan
Product drawing
Web data sheet XI · Page 3 of 4 ebm-papst St. Georgen GmbH & Co. KG · Hermann-Papst-Straße 1 · D-78112 St. Georgen · Phone +49 7724 81-0 · Fax +49 7724 81-1309 · info2@ ·
Mass Dimensions Material of impeller Housing material Direction of air flow Direction of rotation Bearing Lifetime L10 at 20 °C Lifetime L10 at 60 °C Connection line Motor protection Approval
/
分销商库存信息:
EBM-PAPST 414
/
414
DC axial compact fan
Technical features
General description Particular design features: Compact fan with low power consumption. Some models suitable for use at high ambient temperatures. General features: Material: fibreglass-reinforced plastic. Impeller PA, housing PBT. Electronic commutation completely integrated. Protected against reverse polarity and locking. Connection via single strands AWG 28, TR 64, bared and tin-plated. Air exhaust over bars. Direction of rotation counter-clockwise seen on rotor. Masse: 17 g. 0.027 kg 40 x 40 x 20 mm Fiberglass-reinforced PA plastic Fiberglass-reinforced PBT plastic Air exhaust over bars Left, looking at rotor Sintec sleeve bearing 50000 h 20000 h Single strands AWG 28, TR 64, bared and tin-plated. Protected against reverse polarity and locking. VDE, CSA, UL
美军标 18240
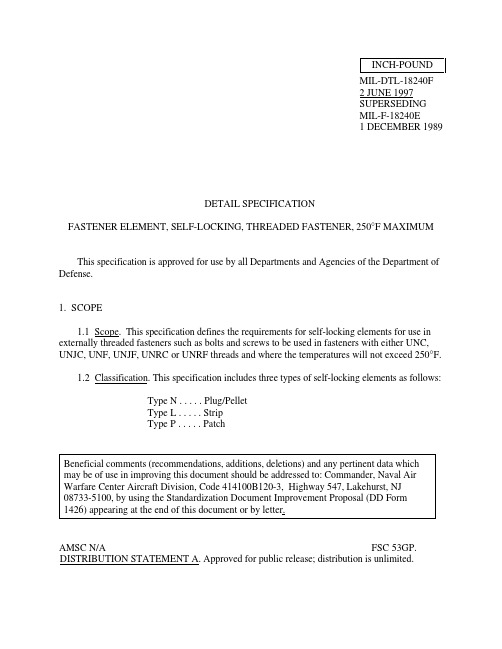
MIL-DTL-18240F2 JUNE 1997SUPERSEDINGMIL-F-18240E1 DECEMBER 1989DETAIL SPECIFICATIONFASTENER ELEMENT, SELF-LOCKING, THREADED FASTENER, 250°F MAXIMUM This specification is approved for use by all Departments and Agencies of the Department of Defense.1. SCOPE1.1 Scope. This specification defines the requirements for self-locking elements for use inexternally threaded fasteners such as bolts and screws to be used in fasteners with either UNC, UNJC, UNF, UNJF, UNRC or UNRF threads and where the temperatures will not exceed 250°F.1.2 Classification. This specification includes three types of self-locking elements as follows:Type N . . . . . Plug/PelletType L . . . . . StripType P . . . . . PatchAMSC N/A FSC 53GP.DISTRIBUTION STATEMENT A. Approved for public release; distribution is unlimited.2. APPLICABLE DOCUMENTS2.1 General. The documents listed in this section are specified in sections 3 and 4 of this specification. This section does not include documents cited in other sections of this specification or recommended for additional information or as examples. While every effort has been made to ensure the completeness of this list, document users are cautioned that they must meet all specified requirements documents cited in sections 3 and 4 of this specification, whether or not they are listed. .2.2 Government document.2.2.1 Specifications Standards and handbooks. The following specifications, standards, andhandbooks form a part of this document to the extent specified herein. Unless otherwisespecified, the issues of these documents are those listed in the issue of the Department of Defense Index of Specification and Standards (DODISS) and supplement thereto, cited in the solicitation (see 6.2).SPECIFICATIONSFEDERALQQ-P-416-Plating, Cadmium (Electrodeposited).GGG-W-686-Wrench, Torque, Unidirectional.DEPARTMENT OF DEFENSEMIL-S-7742-Screw Threads, Standard, Optimum Selected Series: GeneralSpecification forMIL-S-8879-Screw Threads, Controlled Radius Root with Increased MinorDiameter, General Specification for.STANDARDSFEDERALFED-STD-H28/2-Screw Threads Standards for Federal Services Section 2Unified inch Screw Threads UN and UNR Thread Forms DEPARTMENT OF DEFENSEMIL-STD-1312-7- Fastener, Test Methods, Method 7, VibrationMS15981 - Fasteners, Externally Threaded, Self-locking, Design andUsage Limitations ForAIR FORCE - NAVY AERONAUTICALAN 3 THRU AN 20- Bolt, Machine, Aircraft.(Unless otherwise indicated, copies of the above specifications, standards, and handbooks are available from the Standardization Document Order Desk, 700 Robbins Avenue, Building 4D, Philadelphia, PA 19111-5094.)2.2.2 Non-Government publications. The following documents form a part of this document to the extent specified herein. Unless otherwise specified, the issues of the documents which are DoD adopted shall be those listed in the issue of the DoDISS cited in the solicitation. Unless otherwise specified, the issues of documents not listed in the DODISS are the issue of the documents cited in the solicitation (see 6.2).AMERICAN SOCIETY FOR QUALITY CONTROL (ASQC)ASQC Z1.4- Sampling Procedures and Tables for Inspection by Attributes (Application for copies should be addressed to AMERICAN SOCIETY FOR QUALITY CONTROL, P.O. Box 3005, 611 E Wisconsin Ave, Milwaukee, WI 53201-4606)AMERICAN SOCIETY OF MECHANICAL ENGINEERSASME B1.1- Unified Inch Screw Threads (UN and UNR Thread Form) (DoD adopted) (Application for copies should be addressed to American Society of Mechanical Engineers (ASME), 22 Law Drive, P.O. Box 2900, Fairfield NJ 07007-2900)NATIONAL AEROSPACE STANDARDS (NAS)NAS 600 THRU NAS 606- Screw, Machine, Aircraft, Pan Head, Cruciform Recess,Full Threaded, Alloy Steel. (DoD adopted) (Application for copies should be addressed to the Aerospace Industries Association ofAmerica, Inc., 1250 Eye Street, N.W., Washington, DC 20005.)AMERICAN SOCIETY FOR TESTING AND MATERIALSASTM D1535-Standard Practice for Specifying Color By The MunsellSystem(Application for copies should be addressed to the American Society for Testing andMaterials, 100 Barr Harbor Drive, W. Conshohocken, PA (19428-2959).2.3 Order of precedence. In the event of a conflict between the text of this document and the references cited herein (except for related associated specifications or specification sheets), the text of this document shall take precedence. Nothing in this document, however, supersedes applicable laws and regulations unless a specific exemption has been obtained.3. REQUIREMENTS3.1 Qualification. The self-locking elements furnished under this specification shall be products which are authorized by the qualifying activity for listing on the applicable qualified products list (QPL) before contract award (see4.2 and 6.3).3.1.1 Extent of qualification. Qualification approval of external self-locking element in UNF or UNJC external thread constitutes approval of external self-locking element in UNC, UNJC, UNF, UNJF, UNRC, or UNRF external thread of the same diameter.3.2 Design. The self-locking element design shall conform to the types illustrated onfigure 1 and MS15981.3.2.1 Dimensions. The self-locking element dimensions shall be as specified in table I,table IA, and figure 1. In cases of dimensional conflict, the dimensions of table I, table IA and figure 1 shall take precedence over those identified in MS15981.3.3 Performance characteristics.3.3.1 Torque. The self-locking fastener shall conform to the torque test as specified in4.4.2.3.3.2 High temperature torque. The self-locking fastener shall conform to the high temperature torque test in4.4.3.3.3.3 Off prevailing torque at maximum temperature. The self-locking fastener shall meet the off minimum prevailing torque values specified in table II at maximum temperature when tested in accordance with4.4.4.3.3.4 Vibration. The self-locking fastener shall be subjected to and pass the vibration testfor 30,000 cycles as specified in 4.4.5. For qualification purposes, the activity responsible for qualification may waive the vibration requirement for thread sizes greater than .500inch provided the .500inch thread size having the same type locking element has passed the vibration test. The vibration test is not required for thread sizes below .190.3.4 Reusability. The self- locking fastener shall be capable of 5 seated cycles without damage to either the nut or bolt threads (see4.4.2d through f and 4.4.6).3.5 Identification.3.5.1 Self-locking element. The self-locking element shall be identified by color code as identified in ASTM D1535 and in table VIII.3.5.2 Color. Each manufacturer of the products specified herein shall color code theirself-locking elements produced per this specification in accordance with their designated colors identified per QPL-18240.3.6 Workmanship. Workmanship shall be consistent with high-grade commercial practice. Parts are required to be free of burrs and slivers except slight burrs are permissible in the area of the self-locking element provided maximum locking torque values specified in table II are not exceeded.4. VERIFICATION4.1 Classification of inspections. The inspection requirements specified herein are classified as follows:a. Qualification inspection (see 4.2).b. Quality conformance inspection (see 4.3).4.1.1 Responsibility of the self-locking element supplier. The self-locking element supplier shall be responsible for compliance with all the requirements of sections 3 and 4. The seller of the completed fastener shall be responsible for proving that the fastener product has met all the quality conformance inspections of the completed fastener.4.2 Qualification inspection. Qualification inspection shall be performed at a laboratory acceptable to the Government on sample units produced with equipment and procedures normally used in production. Qualification inspections shall be as specified in table VII. Qualification inspection shall be limited to the fasteners shown in tables IV and shall be authorized only upon presentation of certified test reports to the activity responsible for qualification. The test reports shall include actual results of all the tests and a drawing which shows the location, size, material, method of attachment and protrusion of the self-locking element for each diameter upon which qualification is desired. A manufacturer's designation shall be submitted for the locking element to be used in each diameter of fastener. For qualification of sizes up to and including .500" (government designation 80), the manufacturer must submit samples for full testing to be conducted by the qualifying test facility for each individual desired size. For qualification of sizes above .500" nominal diameter size, the manufacturer must submit actual torque test data and samples of the specific size to the qualifying testing facility and must be qualified to the .500" nominal diameter size.4.2.1 Retention of qualification. Certification shall be requested by Naval Air Warfare Center from each manufacturer and forwarded to the preparing activity for those specifications which do not contain a requirement for retention of qualification by testing. Certification shall be at the time of the two year review and shall be signed by a responsible official or management,attesting that the listed product(s) is still available from the listed plant, and is produced under the same conditions as originally qualified; i.e., same process, materials, construction, design, manufacturer's part number, or designation, and meets the requirements of the current issue of the specification. Failure to provide the certification will be cause for removal from the QPL.4.2.2 Sampling instructions. The qualification inspection samples shall consist of 60 fasteners with the self-locking elements conforming to table IV for each diameter for which qualification is desired. All test nuts necessary for the inspections shall conform to tables VA and VB and shall be furnished by the manufacturer. Samples shall be identified as required and forwarded to the activity designated in the letter of authorization from the activity responsible for qualification (see 6.3).4.3 Quality conformance inspection. Prior to installation of the self-locking element, the quality conformance inspections of the applicable fastener specification shall be met. In addition, after installation of the self-locking element on to the applicable fastener, the quality conformance inspections specified in table VI shall be met. Also, the self-locking fastener shall meet any other tests which are considered necessary by the procuring activity to determine conformance with the requirements of this specification. Any rework of the fastener as defined by the Fastener Quality Act shall require retesting.4.3.1 Sampling. For the quality conformance inspections specified herein, the sample self-locking fasteners shall be selected at random from each finished lot as specified in 4.3.1.1. Group A quality conformance inspection sampling shall be in accordance with ANSI/ASQZ 1.4-1993, single sampling inspection, Level II, of zero acceptance level.Group B torque inspection sampling shall be in accordance with the sampling plan in table IX orX at the supplier’s option.4.3.1.1 Lot. A lot shall consist of finished fasteners with the self-locking element incorporated which are of the same diameter and length, fabricated by the same process, heat treated in the same manner, and produced as one continuous run or order or part thereof, whichever is of the smaller quantity.4.4 Methods of inspection.4.4.1 Examination of product. The self-locking fastener shall be examined for the following items before any other tests are conducted..a. Presence of self-locking element.b. Location of self-locking element.c. Dimensions of self-locking element.d. Presence of burrs and slivers (see 3.6).e. Identification of product.4.4.2 Torque test. For qualification testing 10 sample fasteners with self-locking elements installed as specified in table IV shall be tested with the test nuts specified in tables VA and VB. For quality conformance purposes, the bolts shall be as specified in the applicable document which requires a self-locking element per MIL-DTL-18240 and the test nut shall be as specified in table VA and VB for the correct thread type. The following test shall be performed:NOTE: Parts that can not be seated shall be tested unseated.a. Prior to the actual testing of self-locking screws and bolts, a test nut asspecified in table VA and table VB with the same thread form, class and pitch,shall be gauged with a go and no go threaded plug gage. The test nut shall notaccept the no go gage for more than 1.5 turns and shall freely accept the go gagefor the entire length of the nut. The minor thread diameter shall also be checkedfor conformance with table VA and VB.b. A light lubricating oil shall be applied directly to the locking element prior totorque testing, unless otherwise specified. ( see 6.4.1)c. The torque shall be measured using a calibrated torque wrench in accordancewith GGG-W-686 or a digital torque sensor capable of measuring the torquevalues encountered during the test. (see 6.4.2)d. A self-locking fastener shall be assembled with hardened spacers, or washers asnecessary, and a test nut. The total thickness of the spacers and washers for thetest assembly shall be selected so that the locking element of the self-lockingfastener is fully engaged in the test nut. Set screws shall be tested in a blind hole.If the self-locking fastener is turned, the restraining mechanism shall be such that itimparts no radial load to the nut.For testing of self-locking fastener withoutsufficient thread length for a locking element in accordance with table I or forthread sizes not covered in table II only a positive indication of off prevailingtorque is required for five cycles. Sufficient thread length is eight threads (onecomplete thread pitch, plus five complete thread pitches for the locking element,plus two run-out pitches for ease of starting, for a total of eight threads minimum.)Sufficient thread length may be calculated as follows:Sufficient Thread Length = 18 PXWhere P = Thread Pitch EXAMPLE: .250-28 ThreadSufficient Thread Length = 1288286X in=.e. First cycle test: During the first tightening of the assembly, the 1st cycle ONPREVAILING TORQUE (see 6.5) shall be measured and recorded.. Tighteningshall be continued until the required SEATING TORQUE (see 6.5) as specified intable II for the applicable thread size and pitch is developed. The axial clamp loadshall be reduced to zero by backing the self-locking fastener or test nut off, untilthe spacers are free to rotate. Following the removal of the axial clamp load, the1st cycle OFF PREVAILING TORQUE (see 6.5) shall be measured during thenext 360 degrees of rotation and recorded. The self-locking fastener and test nutshall be disassembled until the locking element is disengaged. The driving speedshall not exceed 30 RPM.f. Second through fifth cycle tests: The self-locking fastener and test nut shall bereassembled, seated, and disassembled four more times following the sameprocedure as the 1st cycle test. The ON and OFF PREVAILING TORQUE shallbe measured and recorded for each cycle. Sufficient time shall elapse betweentorquing cycles to prevent overheating of the test assembly. During the torque testthe temperature shall not be grater than 75°F above the starting temperature.g. For qualification testing any torque value determined to be in excess of thelimitations of table II constitutes failure of this test. For quality conformancetesting determine whether the lot passes or fails in accordance with table IXor table X.4.4.3 High temperature torque.a. Assemble ten new fasteners as tested in 4.4.2, steps a through d and the on cycle ofstep e.b. Bake the assemblies to 250°F ±10° for 3 hours.c. Air cool the assemblies to room temperature for a minimum of 1 hour.d. Test the torque values as indicated in 4.4.2, steps e through f, starting with the firstOFF PREVAILING TORQUE. Any torque determined in this test to be in excessof 150 percent of the maximum prevailing torque values in table II or not meetingthe minimum prevailing torque in table II constitutes failure of this test.4.4.4 OFF PREVAILING TORQUE at maximum temperature.a. Assemble the same ten fasteners used in paragraph 4.4.3.b. Bake the assemblies for one hour to 250°F ±10°.c. While the fastener is still at 250°F, determine that the OFF PREVAILING TORQUEvalue shall not be less than the minimum prevailing torque value listed in table II.4.4.5 Vibration. Sample nuts and bolts of the size and quantities specified in table III shall be subjected to the vibration test specified in MIL-STD-1312-7, Vibration. The sample nuts and bolts shall be assembled to the specified torque in table III and disassembled 4 times, then reassembled and tested. The fastener assembly shall traverse the entire length of the slots in the test fixture during the test.4.4.5.1 Vibration failure conditions. The self-locking element shall have failed the vibration test for any of the following conditions:a. When any structural failure occurs in the fastener in the region of the self-lockingelement during the vibration test such as a crack intersecting the region of thethreads containing the self-locking element.b. When any nut rotates greater than 360° during 30,000 cycles.c. When any nut can be turned completely on or off the bolt or screw, with the fingers,during or after completion of 30,000 cycles.4.4.6 Reusability. At the conclusion of the tests specified in 4.4.2 (and 4.4.3 and 4.4.4 for qualification testing), the test nuts and self-locking fasteners used in this test shall be examined for damage to the threads. Noticeable distortion or scratches deep enough to reduce the efficiency of the threads shall be considered a failure of the self-locking element. The threads shall remain in serviceable condition and permit the installation of a new self-locking fastener or test nut (as applicable) freely with the fingers up to the self-locking element.4.4.7 Noncompliance. If a sample fails to pass Group B inspection of table VI, the manufacturer shall notify the qualifying activity and the cognizant inspection activity of such failure and take corrective action on the materials or processes, or both, as warranted, and on all units of products which can be corrected and which are manufactured under essentially the samematerials and processes, and which are considered subject to the same failure. Acceptance and shipment of the product shall be discontinued until corrective action, acceptable to the inspection activity has been taken. After corrective action has been taken, Group B inspection shall be repeated on additional sample units (all tests and examinations, or the test which the original sample failed, at the option of the qualifying activity). Groups A and B inspections may be reinstituted; however, final acceptance and shipment shall be withheld until the Group B inspection has shown that the corrective action was successful. In the event of failure after reinspection, information concerning the failure shall be furnished to the cognizant inspection activity and the qualifying activity.5. PACKAGING5.1 Packaging. For acquisition purposes, the packaging requirements shall be as specified in the contract or order (see6.2). When actual packaging of material is to be performed by DoD personnel, these personnel need to contact the responsible packaging activity to ascertain requisite packaging requirements. Packaging requirements are maintained by the Inventory Control Point’s packaging activity within the Military Department or Defense Agency, or within the Military Department’s System Command. Packaging data retrieval is available from the managing Military Department’s or Defense Agency’s automated packaging files, CD-ROM products or by contacting the responsible packaging activity.6. NOTES.(This section contains information of a general or explanatory nature that may be helpful, but is not mandatory).6.1 Intended use. The self-locking elements covered by this specification are intended to be incorporated in external screw threads to be used in applications where maximum temperature does not exceed 250°F. When these self-locking elements are incorporated in external threads and are used in compliance with MS15981, all the configurations of figure 1 are interchangeable Type N element, plug/pellet configuration is intended to be installed via a hole drilled into the fastener. Type L element, strip configuration is intended to be installed via a strip cut through the threads parallel to the length of the fastener. Type P element, patch configuration is intended to be installed without removal of any material of the fastener.A specific type should be specified only when required by design or application requirements. The prevailing-torque values given in this specification are conformance requirements for self-locking elements and apply only to the combination of test conditions described in the locking torque test procedure. If the conditions of the actual service application differs from those of 4.4.2 (e.g. internally threaded hole in a different material, length of thread engagement, class of internal thread tolerance, speed of driving, different plating or coating on screw or mating part) the prevailing-torque values may vary. Such values can only be determined through testing the locking element in its application. The plug/pellet is not recommended for sizes below .190.6.1.1 Cross reference.From Configurations listed in Revision D dated 25 February 1972Configuration A plug /pellet type superceeded by Type NConfiguration B strip type superceeded by Type LConfiguration B patch type superceeded by Type P6.2. Acquisition requirements. Acquisition documents must specify the following:a. Title, number, and date of this specification.b. Issue of DODISS to be cited in the solicitation.c. Type (see 1.2, table I and figure 1).d. Part number in accordance with the applicable standard.e. Packaging requirements (see 5.1).6.3 Qualification. With respect to products requiring qualification, awards will be made only for products which are, at the time of award of contract, qualified for inclusion in qualified products list QPL-18240, whether or not such products have actually been so listed by that date. The attention of the contractors is called to these requirements, and manufacturers are urged to arrange to have the products that they propose to offer to the Federal Government tested for qualification in order that they may be eligible to be awarded contracts or purchase orders for the products covered by this specification. Information pertaining to qualification of products may be obtained from the Naval Air Warfare Center Air Craft Division, Code 435200A, Bldg 2187, 48110 Shaw Rd., Unit 5, Patuxent River MD, 20670-1906.6.3.1 Qualification evaluation. Qualification inspection and evaluation of type N (see figure 1) locking element designs were based on the protrusion of the element being in accordance with figure 1, dimension "B". Type N designs with protrusion of "B + 0.007 inch and design that are otherwise the same as listed, also have qualification approval. To identify the element design with greater protrusion of the dimension "B + 0.007inch, figure 1 of this specification, the additional +0.007 inch protrusion must be specified on the standard or drawing for the part, for nonstandard parts that require a specific configuration, add a "P" to the government designation.6.4 Torque test notes6.4.1 A light oil such as Rainkote 400 or equivalent is used in the test (4.4.2) of fasteners to reduce wear, prevent galling or seizure, prevent fretting, and aid in the installation and removal of fasteners. A minimum amount may be used. This will give more consistent torque test results.6.4.2 Some torque measuring devices, such as beam wrenches, could be 20-40% off on the lower 20 percent of the scale and should not be used.6.5 Definitions.6.5.1 Self-locking externally or internally threaded fastener(s). In this specification a"self-locking externally threaded fastener" refers to bolts, or screws, that incorporate self-locking elements conforming to this specification.6.5.2 ON PREVAILING TORQUE. The maximum torque occurring while the fastener is being installed and prior to development of any axial clamp load.6.5.3 SEATING TORQUE. The torque required to overcome the self-locking feature and produce an axial clamp load to the test assembly.6.5.4 OFF PREVAILING TORQUE. The maximum torque occurring while the fastener is in motion during the first 360 degrees of rotation in the untighting direction after the test assembly has been unseated.6.6 Subject term (keyword) listing..Plug/PelletStripPatch6.7 Changes from previous issue. Marginal notations are not used in this revision to identify changes with respect to the previous issue due to the extent of the changes.6.8 Previously manufactured product. Product manufactured prior to the date of this specification may be used until the supply is exhausted.TABLE I Self-locking element dimensions. (see figure 1)1/ Plug/Pellet is not recommended for sizes below .190.2/ Screws .500 inch and larger may have two self-locking elements. They shall not be more than 120 degrees of thread diameter apart.Table IA Screw and bolt slot and hole depths for self-locking strips and pellets.TABLE II Torque. 1/ 3/1/ These values apply to MIL-S-8879, MIL-S-7742, ASME B1.1, and FED-STD-H28/2 threads. They do not apply to Class 1A threads.2/ These values are for testing only, and are NOT recommended installation torque values. 3/ Values for coarse and fine threads are the same.TABLE III. Vibration requirements.TABLE IV. Length and diameter of self-locking fasteners requiredfor qualification inspection.TABLE VA. Dimensions of nuts required for qualification and conformance tests (inches) 1/ 2/ 3/ 4/ 5/UNF, UNJF, UNC, UNJC THREAD FORMSNotes: 1/ Material: 300 series stainless steel.2/ The nut minor diameter finish shall be 63 MI or better.3/ Nut thread dimensions not listed in table VA shall conform to MIL-S-8879 for class 3B threads Threads shall be cut not formed.4/ For thread sizes above .437 diameter see table VB.5/ Test nuts manufactured to MIL-F-18240 Revision E may be used until 1 year from the date of this specification. The test nuts specified in Revision E must be used in accordance with therequirements of Revision E.TABLE VB. Dimensions of nuts required for qualification and conformance tests (inches) 1/ 2/ 3/ 4/ 5/Notes: 1/ Material: 300 series stainless steel.2/ The nut minor diameter finish shall be 63 MI or better.3/ Nut thread dimensions not listed in table VB shall conform to MIL-S-8879 for class 3Bthreads. Threads shall be cut not formed.4/ For thread sizes less than .500 diameter see table VA.6/Test nuts manufactured to MIL-F-18240 Revision E may be used until 1 year from the date of this specification. The test nuts specified in Revision E must be used in accordance with therequirements of Revision E。
4580N;中文规格书,Datasheet资料

/
分销商库存信息:
EBM-PAPST 4580N
/
4580 N
AC axial compact fan
Product drawing
Web data sheet XI · Page 3 of 4 ebm-papst St. Georgen GmbH & Co. KG · Hermann-Papst-Straße 1 · D-78112 St. Georgen · Phone +49 7724 81-0 · Fax +49 7724 81-1309 · info2@ ·
/
4580 N
AC axial compact fan
Charts: Air flow
(in H ² O) 0,05 0,10 0,15
∆ pf ä
Pa
40
30
20
10
0
15
30
45
60
CFM50
75
100
Web data sheet XI · Page 4 of 4 ebm-papst St. Georgen GmbH & Co. KG · Hermann-Papst-Straße 1 · D-78112 St. Georgen · Phone +49 7724 81-0 · Fax +49 7724 81-1309 · info2@ ·
Nominal data
Type Phase Nominal voltage Frequency Speed Power input Min. ambient temperature Max. ambient temperature Air flow Sound power level Sound pressure level VAC Hz min-1 W °C °C m3/h B dB(A) 4580 N 1~ 230 50 2350 18.0 -10 55 123 5.2 41
E2SCA18-7.999M中文资料(ECLIPTEK)中文数据手册「EasyDatasheet - 矽搜」

(5 DigitsMaximum + Decimal)
HC-49/UP
规格如有更改,恕不另行通知.
CR44
.
08/08
包装选择
空白=散装,TR =卷带式
频率
负载电容
S =串联谐振 XX = XXpF并联谐振
动作模式 /水晶切割 A =基本/ AT, B =三次泛音/ AT D =基本/ BT
外形尺寸 ALL DIMENSIONS IN MILLIMETERS
建议焊盘布局 ALL DIMENSIONS IN MILLIMETERS
电气特性
频率范围频率ຫໍສະໝຸດ 差 /稳定性在工作温 度范围
工作温度范围
老化( 25°C)
存储温度范围
并联电容
绝缘电阻
驱动电平
负载电容(C
)
3.579545MHz为50.000MHz
为±50ppm /±100ppm(标准),±30ppm/为±50ppm(AT切割只),±15ppm/±30ppm(AT切割只),
环境/机械特性
PARAMETER
ESD敏感性
精细泄漏测试 可燃性 总泄漏测试 机械冲击 耐湿性 湿度敏感度 耐焊接热 抗溶剂 可焊性 温度循环 振荡
SPECIFICATION
MIL-STD-883,方法3015,1级,HBM:1500V MIL-STD-883,方法1014,条件A UL94-V0 MIL-STD-883,方法1014,条件C MIL-STD-202,方法213,条件C MIL-STD-883,法1004 J-STD-020, MSL1 MIL-STD-202,方法210,满足条件K MIL-STD-202,方法215 MIL-STD-883,方法2003 MIL-STD-883,方法1010,条件B MIL-STD-883,方法2007条件A
74435561100;中文规格书,Datasheet资料

74435561100
DATUM / DATE : 2009-11-02 Gurtspezifikation / Tape specification:
G H
SPEICHERDROSSEL WE-HCI POWER-CHOKE WE-HCI
I Rollenspezifikation / tape and reel specification:
74435561100
DATUM / DATE : 2009-11-02
SPEICHERDROSSEL WE-HCI POWER-CHOKE WE-HCI
H Induktivitätskurve / Inductance curve:
Induktivität vs Strom (typ.) Inductance vs Current (typ.)
08-09-29
Geprüft / checked
Kontrolliert / approved
Datum / date
D-74638 Waldenburg · Max-Eyth-Strasse 1 - 3 · Germany · Telefon (+49) (0) 7942 - 945 - 0 · Telefax (+49) (0) 7942 - 945 - 400 http://www.we-online.de
12,00
10,00
8,00
L (µH)
6,00
4,00
2,00
0,00 0 5 10 15 Current (A) 20 25 30 35
Freigabe erteilt / general release:
..................................................................................
CPC1018N;CPC1018NTR;中文规格书,Datasheet资料

Features
• Designed for Use in Security Systems Complying with EN50130-4 • Only 1mA of LED Current Required to Operate • 1500Vrms Input/Output Isolation • Small 4-Lead SOP Package • TTL/CMOS Compatible Input • No Moving Parts • High Reliability • Arc-Free With No Snubbing Circuits • No EMI/RFI Generation • Immune to Radiated EM Fields • SMD Pick & Place, Wave Solderable • Tape & Reel Version Available
Switching Characteristics of Normally Open Devices
Form-A IF
90%
ILOAD
ton
10% toff
Pb
/
RoHS
2002/95/EC
e3
1
DS-CPC1018N-R09
CPC1018N
Typical On-Resistance Distribution (N=50, IF=1mA, IL=0.6A, TA=25ºC)
25 20 15 10 5 0
Device Count (N)
Device Count (N) 0.16 0.18 0.20 0.22 0.24 LED Current (mA) 0.26
Typical Turn-Off Time (N=50, IF=5mA, IL=100mA, TA=25ºC)
1824340中文资料

Extract from the onlinecatalogMSTBU 2,5/24-STD-5,08Order No.: 1824340The figure shows a 10-position version of the producthttp://eshop.phoenixcontact.de/phoenix/treeViewClick.do?UID=1824340Plug component, nominal current: 12 A, rated voltage: 320 V, pitch: 5.08 mm, no. of positions: 24, type of connection: Screw connectionhttp://Please note that the data givenhere has been taken from theonline catalog. For comprehensiveinformation and data, please referto the user documentation. TheGeneral Terms and Conditions ofUse apply to Internet downloads. Technical dataDimensions / positionsPitch 5.08 mmDimension a116.84 mmNumber of positions24Screw thread M 3Tightening torque, min0.5 NmTechnical dataInsulating material group IRated surge voltage (III/3) 4 kV Rated surge voltage (III/2) 4 kV Rated surge voltage (II/2) 4 kV Rated voltage (III/2)320 V Rated voltage (II/2)630 V Connection in acc. with standard EN-VDE Nominal current I N12 A Nominal voltage U N320 V Nominal cross section 2.5 mm2 Insulating material PA Inflammability class acc. to UL 94V0 Internal cylindrical gage A3 Stripping length7 mmConnection dataConductor cross section solid min.0.2 mm2 Conductor cross section solid max. 2.5 mm2 Conductor cross section stranded min.0.2 mm2 Conductor cross section stranded max. 2.5 mm2 Conductor cross section stranded, with ferrule0.25 mm2 without plastic sleeve min.Conductor cross section stranded, with ferrule2.5 mm2 without plastic sleeve max.Conductor cross section stranded, with ferrule0.25 mm2 with plastic sleeve min.Conductor cross section stranded, with ferrule2.5 mm2 with plastic sleeve max.2 conductors with same cross section, solid min.0.2 mm2 2 conductors with same cross section, solid max. 1 mm22 conductors with same cross section, stranded0.2 mm2 min.2 conductors with same cross section, stranded1.5 mm2 max.2 conductors with same cross section, stranded,0.25 mm2 ferrules without plastic sleeve, min.2 conductors with same cross section, stranded,1 mm2ferrules without plastic sleeve, max.2 conductors with same cross section, stranded,0.5 mm2TWIN ferrules with plastic sleeve, min.2 conductors with same cross section, stranded,1 mm2TWIN ferrules with plastic sleeve, max.Conductor cross section AWG/kcmil min.24Conductor cross section AWG/kcmil max12Certificates / ApprovalsApproval logoCSANominal voltage U N300 VNominal current I N10 AAWG/kcmil28-12CULNominal voltage U N300 VNominal current I N10 AAWG/kcmil30-12ULNominal voltage U N300 VNominal current I N10 AAWG/kcmil30-12Certification CB, CSA, CUL, GOST, UL, VDE-PZIAccessoriesItem Designation DescriptionGeneral1733169EBP 2- 5Insertion bridge, fully insulated, for plug connectors with 5.0 or5.08 mm pitch, no. of positions: 2Marking0804293SK 5,08/3,8:FORTL.ZAHLEN Marker card, printed horizontally, self-adhesive, 12 identicaldecades marked 1-10, 11-20 etc. up to 91-(99)100, sufficient for120 terminal blocksPlug/Adapter1734634CP-MSTB Coding profile, is inserted into the slot on the plug or invertedheader, red insulating materialTools1205053SZS 0,6X3,5Screwdriver, bladed, matches all screw terminal blocks up to 4.0mm² connection cross section, blade: 0.6 x 3.5 mm, without VDEapprovalAdditional productsItem Designation DescriptionGeneral1786394IC 2,5/24-ST-5,08Plug component, nominal current: 12 A, rated voltage: 250 V,pitch: 5.08 mm, no. of positions: 24, type of connection: Screwconnection1824065ICC 2,5/24-STZ-5,08Plug component, nominal current: 12 A, rated voltage: 250 V,pitch: 5.08 mm, no. of positions: 24, type of connection: Crimpconnection1759237MSTB 2,5/24-G-5,08Header, nominal current: 12 A, rated voltage: 250 V, pitch: 5.08mm, no. of positions: 24, mounting: Soldering1757462MSTBA 2,5/24-G-5,08Header, nominal current: 12 A, rated voltage: 250 V, pitch: 5.08mm, no. of positions: 24, mounting: Soldering1758238MSTBV 2,5/24-G-5,08Header, nominal current: 12 A, rated voltage: 250 V, pitch: 5.08mm, no. of positions: 24, mounting: Soldering1755956MSTBVA 2,5/24-G-5,08Header, nominal current: 12 A, rated voltage: 250 V, pitch: 5.08mm, no. of positions: 24, mounting: SolderingDrawingsDrilling diagramDimensioned drawingAddressPHOENIX CONTACT GmbH & Co. KGFlachsmarktstr. 832825 Blomberg,GermanyPhone +49 5235 3 00Fax +49 5235 3 41200http://www.phoenixcontact.de© 2008 Phoenix ContactTechnical modifications reserved;。
LA1824资料
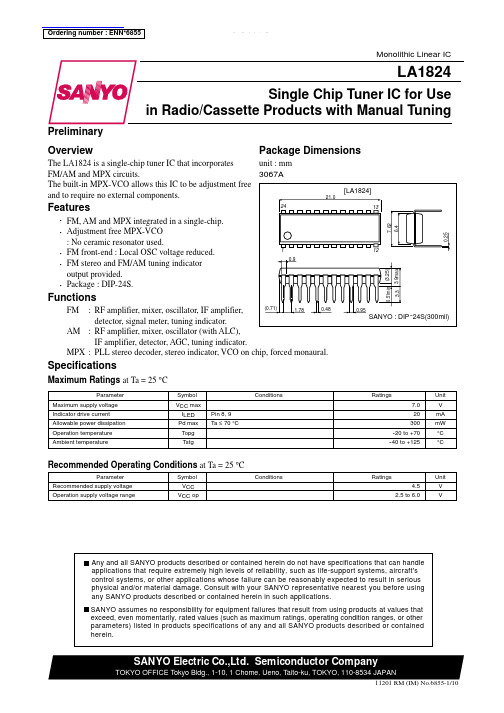
Block Diagram
FM Ant B.P.F
24
23
22
21
20
GND2 FM
RF
VCC2
FM OSC
FM MIX
+
19
18
TRIG
ST SW
+
+
R-OUT
L-OUT
AM FM
MN ST
17
16
DECODER
VCO
FF
15
14
PHASE COMP
FF
FF
PILOT DET
13 DET
LA1824
Overview
PackageБайду номын сангаасDimensions
The LA1824 is a single-chip tuner IC that incorporates FM/AM and MPX circuits. The built-in MPX-VCO allows this IC to be adjustment free and to require no external components.
AM MIX
AM
RF
AM
REG
OSC
VCC1
GND1
S-METER
DET
AGC
TUN
ST
LED
LED
FM IF
AM-IF
1
2
3
4
5
6
7
8
9
10
11
12
AM Ant +
AM / FM TUN
FM ST
10.7MHz +
CPC1014N;CPC1014NTR;中文规格书,Datasheet资料
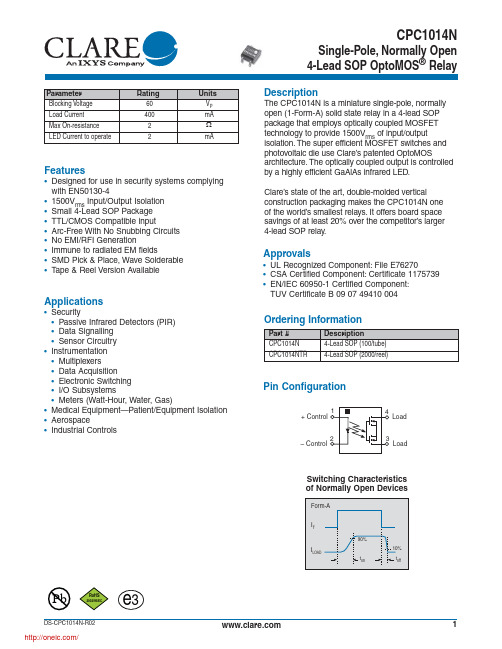
0.15
0.10 -40 -20 0
IF=10mA 20 40 60 80 100
Temperature (ºC)
Device Count (N)
(IL=80mA)
0.6
0.5
0.4
0.3
0.2
0.1
0 0 5 10 15 20 25 30 35 40 45 50
LED Forward Current (mA)
Typical LED Forward Voltage Drop
vs. Temperature
1.6
1.5
IF=50mA
I =20mA
25
20
15
10
5
0 0.16 0.18 0.20 0.22 0.24 0.26 0.28 LED Current (mA)
Device Count (N)
Typical IF for Switch Dropout
(N=50, T =25ºC, I =400mA)
A
L
25
20
15
10
5
0 0.16 0.18 0.20 0.22 0.24 0.26
Typical On-Resistance Distribution (N=50, TA=25ºC, IL=400mA, IF=1mA)
25
20
15
10
5
0 0.505 0.510 0.515 0.520 0.525 0.530 0.535 On-Resistance (Ω)
Typical IF for Switch Operation (N=50, TA=25ºC, IL=400mA)
Parameter Blocking Voltage Load Current Max On-resistance LED Current to operate
CPC1230N中文资料

CPC1230NThe CPC1230N is a miniature 1-Form-A solid state relay in a 4 pin SOP package that employs optically coupled MOSFET technology to provide 1500V of input to output isolation and is BSI certified for supplemental insulation in accordance with EN60950. The efficient MOSFET switch-es and photovoltaic die use Clare’s patented OptoMOS ®architecture. The optically coupled input is controlled by a highly efficient GaAIAs infrared LED. The CPC1230N uses Clare’s state of the art double molded vertical con-struction packaging to produce the world’s smallest 4 pin relay. The CPC1230N offers board space savings of at least 20% over the competitor’s larger 4 pin SOP relay.•Telecommunications •Telecom Switching •Tip/Ring Circuits•Modem Switching (Laptop, Notebook, Pocket Size)•Hookswitch •Dial Pulsing •Ground Start •Ringer Injection •Instrumentation •Multiplexers •Data Acquisition •Electronic Switching •I/O Subsystems•Meters (Watt-Hour, Water, Gas)•Medical Equipment—Patient/Equipment Isolation •Security •Aerospace•Industrial Controls•UL/C-UL Recognized Component File #: E76270•BSI Certified - Certificate #: 8416(Supplementary Isolation Requirement of EN60950)•Small 4 Pin SOP Package•Low Drive Power Requirements (TTL/CMOS Compatible)•No Moving Parts •High Reliability•Arc-Free With No Snubbing Circuits •Supplemental Isolation •FCC Compatible•1500VRMS Input/Output Isolation •0.4mm Distance Through Insulation •FCC Compatible•No EMI/RFI Generation•Machine Insertable, Wave Solderable •Tape & Reel Version AvailableApplicationsFeaturesDescriptionApprovals4 Pin SOP OptoMOS ®RelayOrdering InformationPin Configuration+ÐControlLoadLoadSwitching Characteristics of Normally Open (Form A) DevicesCPC1030N PinoutCPC1230NElectrical CharacteristicsAbsolute Maximum Ratings are stress ratings. Stressesin excess of these ratings can cause permanent damage to the device. Functional operation of the device at these or any other conditions beyond those indicated in the operational sections of this data sheet is not implied.Exposure of the device to the absolute maximum ratings for an extended period may degrade the device and effect its reliability.Absolute Maximum Ratings (@ 25˚ C)2Measurement taken within 1 second of on time.3For applications requiring high temperature operation (greater than 60o C) an LED drive current of 10mA is recomended.2Derate Linearly 6.67 mw / o CCPC1230NPERFORMANCE DATA*The Performance data shown in the graphs above is typical of device performance. For guaranteed parameters not indicated in the written specifications, please contact our application department.CPC1230NTypical LED Forward Voltage Drop(Ambient Temperature = 25 C)35302520151050LED Forward Voltage Drop (V)D e v i c e C o u n t (N )oCPC1230NTypical On-Resistance Distribution(Ambient Temperature = 25 C)(Load Current = 120mA)35302520151050On-Resistance (Ω)D e v i c e C o u n t (N )oCPC1230NTypical Blocking Voltage Distribution(Ambient Temperature = 25 C)35302520151050Blocking Voltage (V)D e v i c e C o u n t (N )oCPC1230NTypical I F for Switch Operation (Ambient Temperature = 25 C)(Load Current = 120mA)LED Current (mA)D e v i c e C o u n t (N )2520151050o CPC1230NTypical I F for Switch Dropout(Ambient Temperature = 25 C)(Load Current = 120mA)2520151050LED Current (mA)D e v i c e C o u n t (N )oCPC1230NTypical Turn-On Time(Ambient Temperature = 25 C)(Load Current = 120mA; I= 5mA)Turn-On (ms)D e v i c e C o u n t (N )2520151050oCPC1230NTypical Turn-Off Time(Ambient Temperature = 25 C)(Load Current = 120mA; I= 5mA)Turn-Off (ms)D e v i c e C o u n t (N )252015105oCPC1230NTypical Load Current vs. TemperatureTemperature ( C)L o a d C u r r e n t (m A )oCPC1230NTypical Leakage vs. TemperatureTemperature ( C)L e a k a g e (µA )0.0160.0140.0120.0100.0080.0060.0040.002o CPC1230NTypical Blocking Voltagevs. TemperatureTemperature ( C)B l o c k i n g V o l t a g e (V R M S )365o CPC1230NTypical Turn-On vs. Temperature(Load Current = 80mA)Temperature ( C)T u r n -O n (m s )0oCPC1230NTypical Turn-Off vs. Temperature(Load Current = 80mA)Temperature ( C)T u r n -O f f (m s )0oCPC1230NPERFORMANCE DATA**The Performance data shown in the graphs above is typical of device performance. For guaranteed parameters not indicated in the written specifications, please contact our application department.CPC1230NTypical LED Forward Voltage Dropvs. TemperatureTemperature ( C)L E D F o r w a r d V o l t a g e D r o p (V )1.81.61.41.21.00.8oCPC1230NTypical Turn-On vs. LED Forward Current(Load Current = 120mA)LED Forward Current (mA)T u r n -O n (m s )0CPC1030NTypical Turn-Off vs. LED Forward Current(Load Current = 120mA)LED Forward Current (mA)T u r n -O f f (m s )CPC1230NTypical On-Resistance vs. Temperature (Load Current = 80mA; I F = 10mA)Temperature ( C)O n -R e s i s t an c e (Ω)6050403020100oLoad Voltage (V)L o a d C u r r e n t (m A )-150CPC1230NTypical Load Current vs. Load Voltage(Ambient Temperature = 25 C)I F = 5mAoCPC1230NEnergy Rating CurveTimeL o a d C u r re n t (A )CPC1230NTypical I F for Switch Operationvs. Temperature (Load Current = 80mA)Temperature ( C)L E D C ur r e n t (m A )-403.0002.5002.0001.5001.0000.500-20020406080100oCPC1230NTypical I F for Switch Dropoutvs. Temperature (Load Current = 80mA)Temperature ( C)L E D C ur r e n t (m A )3.0002.5002.0001.5001.0000.500oCPC1230NDimensionsmm (inches)Mechanical DimensionsPC Board Pattern (Top View)2.54 ± 0.1271.448(0.035)(.100TYP.)1.01±.025(.040±.13.38TYP.±0.20±0.008)0.432±(.017±CLARE LOCATIONSClare Headquarters78 Cherry Hill DriveBeverly, MA01915Tel: 1-978-524-6700Fax: 1-978-524-4900Toll Free: 1-800-27-CLARE Clare Micronix Division145 ColumbiaAliso Viejo, CA92656-1490 Tel: 1-949-831-4622Fax: 1-949-831-4628SALES OFFICES AMERICASAmericas HeadquartersClare78 Cherry Hill DriveBeverly, MA01915Tel: 1-978-524-6700Fax: 1-978-524-4900Toll Free: 1-800-27-CLARE Eastern RegionClareP.O. Box 856Mahwah, NJ 07430Tel: 1-201-236-0101Fax: 1-201-236-8685Toll Free: 1-800-27-CLARE Central RegionClare Canada Ltd.3425 Harvester Road, Suite 202 Burlington, Ontario L7N 3N1 Tel: 1-905-333-9066Fax: 1-905-333-1824Western RegionClare1852 West 11th Street, #348 Tracy, CA95376Tel: 1-209-832-4367Fax: 1-209-832-4732Toll Free: 1-800-27-CLARE CanadaClare Canada Ltd.3425 Harvester Road, Suite 202 Burlington, Ontario L7N 3N1 Tel: 1-905-333-9066Fax: 1-905-333-1824EUROPEEuropean HeadquartersCP Clare nvBampslaan 17B-3500 Hasselt (Belgium)Tel: 32-11-300868Fax: 32-11-300890FranceClare France SalesLead Rep99 route de Versailles91160 ChamplanFranceTel: 33 1 69 79 93 50Fax: 33 1 69 79 93 59GermanyClare Germany SalesActiveComp Electronic GmbHMitterstrasse 1285077 ManchingGermanyTel: 49 8459 3214 10Fax: 49 8459 3214 29ItalyC.L.A.R.E.s.a.s.Via C. Colombo 10/AI-20066 Melzo (Milano)Tel: 39-02-95737160Fax: 39-02-95738829SwedenClare SalesComptronic ABBox 167S-16329 SpångaTel: 46-862-10370Fax: 46-862-10371United KingdomClare UK SalesMarco Polo HouseCook WayBindon RoadTauntonUK-Somerset TA2 6BGTel: 44-1-823 352541Fax: 44-1-823 352797ASIA PACIFICAsian HeadquartersClareRoom N1016, Chia-Hsin, Bldg II,10F, No. 96, Sec. 2Chung Shan North RoadTaipei, Taiwan R.O.C.Tel: 886-2-2523-6368Fax: 886-2-2523-6369Worldwide Sales OfficesSpecification: DS-CPC1230N-R2©Copyright 2000, Clare, Inc.OptoMOS®is a registered trademark of Clare, Inc.All rights reserved. Printed in USA.1/12/01Clare cannot assume responsibility for use of any circuitry otherthan circuitry entirely embodied in this Clare product. No circuitpatent licenses nor indemnity are expressed or implied. Clarereserves the right to change the specification and circuitry, with-out notice at any time. The products described in this documentare not intended for use in medical implantation or other direct lifesupport applications where malfunction may result in direct phys-ical harm, injury or death to a person.。
偏光片规格书
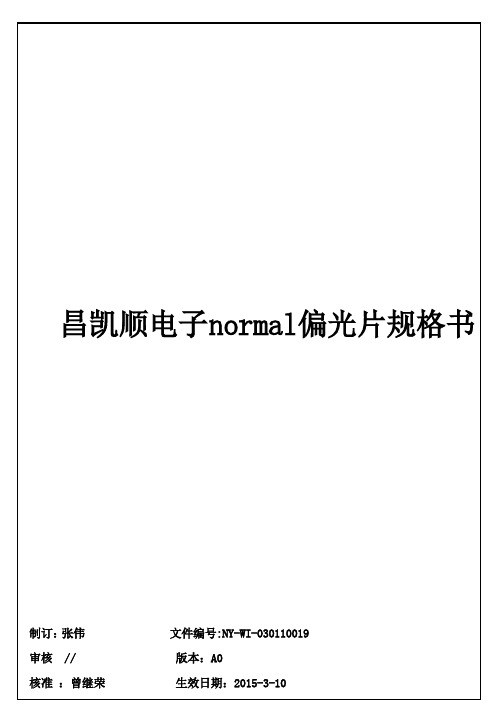
3.6.2 穿透光检查: 穿透灯箱采水平平放,检测时需将保护膜膜面朝上。偏光板检测需不穿透灯箱上的偏光子,呈 直 交(吸收轴角度相差90度)方式检测。
3.7 光学特性:单体透过率,直交透过率,偏光度,色相,雾度及UV-CUT规格值请参照附件1(产品特性) 3.7.1 单体透过率: 依据JISZ8701,使用分光光度计量测偏光板400nm~700nm(取每5nm)波长穿透
3.2.4 尺寸规格: 依照各产品尺寸规格。
3.2.5 尺寸量测方式: 利用光标卡尺量测外型尺寸,量测前先将Polarizer轻放在平台上,将游标尺卡归零,再量测其长 边 不短边长度
3.3 角度特性
3.3.1 定义 直角度:
吸收轴角: θ1 配向轴角: θ2 平均倾斜角: β
长边
90
θ1
θ2
3.3.2 角度规格:
第 10 页
6.质量 6.1 材料 表1
序号
1
2
3
4
偏光板产品规格书
品名 Normal Normal Normal Normal
偏光片型号 RTT00014SAG13S1
RTT00014S1 NTA3N022AG25TB NTA3N022TB
表面处理 AG
Hard Cotting AG
Hard Cotting
1. 制定目的 订定偏光片产品规格书,作为不客户沟通产品规格时使用 2. 适用范围 本 产 品 规 格 书 ,仅 为 初 步 规 格 说 明 , 详 细 内 容 与 遵 行 范 围 ,与客 户 确 认 后 方 可 生 效 。 3. 内容 3.1 基本结构 3.1.1 RTT00014SAG13S1 基本结构
温度 (℃)
80℃ 60℃
MCP1824T-3302EOT系列规格书,Datasheet 资料

ISNS
Cf Rf
Driver w/limit and SHDN
SHDN
VREF
+ EA
–
Sense
Reference
Comp
TDELAY
92% of VREF
© 2007 Microchip Technology Inc.
芯天下--/
DS22070A-page 5
MCP1824/MCP1824S
MCP1824 Adjustable Output Voltage VADJ
SHDN
VIN
1
R1 40 kΩ VOUT
GND
R2 20 kΩ VOUT = 1.2V @ 300 mA
C2 1 µF
© 2007 Microchip Technology Inc.
芯天下--/
4
VOUT
5
PWRGD
6 GND (TAB)
Adjustable
SHDN VIN
GND (TAB) VOUT ADJ
GND (TAB)
SOT-23
Fixed
VIN GND (TAB)
SHDN PWRGD
VOUT —
Adjustable
VIN GND (TAB)
SHDN ADJ VOUT —
MCP1824S
MCP1824/MCP1824S
Functional Block Diagram - Fixed Output (MCP1824S)
PMOS
VIN
VOUT
Undervoltage Lock Out (UVLO)
SHDN
Overtemperature Sensing
- 1、下载文档前请自行甄别文档内容的完整性,平台不提供额外的编辑、内容补充、找答案等附加服务。
- 2、"仅部分预览"的文档,不可在线预览部分如存在完整性等问题,可反馈申请退款(可完整预览的文档不适用该条件!)。
- 3、如文档侵犯您的权益,请联系客服反馈,我们会尽快为您处理(人工客服工作时间:9:00-18:30)。
DS-CPC1824-R021CPC1824e 3Pb* Direct sunlight (Approximately 6000 lux)ApplicationsFeaturesDescriptionOrdering InformationPin Configuration• Portable Electronics • Solar Battery Chargers • Battery O perated Equipment • Consumer Electronics • O ff-Grid Installation• Wireless Sensors and Detection • Flame Detection• Self Powered Sunlight/ Light Detection • Self Powered Products • Remote Installation• 4V Output• T riggers with Natural Sunlight • Provides T rue Wireless Power • No EMI/RFI Generation • Wave Solderable• Replacement of Discrete Components • Solid State ReliabilityThe CPC1824 is a monolithic photovoltaic string of solar cells with switching circuitry. When operating in sunlight or a bright artificial light environment the optical energy will activate the cell array and generate a voltage at the output. The solar cells are capable of generating a floating source voltage and current sufficient to drive and power CMOS ICs, logic gates and/or provide “trickle charge” for battery applications.V-V+/2R02Absolute Maximum Ratings are stress ratings. Stresses in excess of these ratings can cause permanent damage to the device. Functional operation of the device at conditions beyond those indicated in the operational sections of this data sheet is not implied.Absolute Maximum RatingsElectrical CharacteristicsPERFORMANCE DATA**The Performance data shown in the graphs above is typical of device performance. For guaranteed parameters not indicated in the written specifi cations, pleasecontact our application department.Electrical absolute maximum ratings are at 25°CNormalized Open Circuit Output Voltagevs. Light Intensity4.54.03.53.02.52.01.51.00.5002468Light Intensity (lux • 1000)10N o r m a l i z e d O u t p u t V o l t a g e (V )Normalized Short Circuit Output Currentvs. Light Intensity2.502.252.001.751.501.251.000.750.500.250.002468Light Intensity (lux • 1000)N o r m a l i z e d O u t p u tC u r r e n t (μA )10Normalized Open Circuit Output Voltagevs. Incident Angle of Light to Photodiode Surface1.21.00.80.60.40.20.020406080Incident Angle (Degrees)100N o r m a l i z e d O u t p u t V o l t a g e (V )1.21.00.80.60.40.20.020406080Incident Angle (Degrees)N o r m a l i z e d O u tp u t C u r r e n t (μA )100Normalized Short Circuit Output Currentvs. Incident Angle of Light to Photodiode Surface/Clare, Inc. makes no representations or warranties with respect to the accuracy or completeness of the contents of this publication and reserves the right to make changes to specifications and product descriptions at any time without notice. Neither circuit patent licenses nor indemnity are expressed or implied. Except as set forth in Clare’s Standard T erms and Conditions of Sale, Clare, Inc. assumes no liability whatsoever, and disclaims any express or implied warranty, relating to its products including, but not limited to, the implied warranty of merchantability, fitness for a particular purpose, or infringement of any intellectual property right.The products described in this document are not designed, intended, authorized or warranted for use as components in systems intended for surgical implant into the body, or in other applications intended to support or sustain life, or where malfunction of Clare’s product may result in direct physical harm, injury, or death to a person or severe property or environmental damage. Clare, Inc. reserves the right to discontinue or make changes to its products at any time without notice.Specification: DS-CPC1824-R02©Copyright 2009, Clare, Inc.All rights reserved. Printed in USA.2/12/09For additional information please visit our website at: 3Manufacturing InformationMECHANICAL DIMENSIONSPIN 1DIMENSIONSmm(inches)0.60(0.061)e 3PbNOTE: Tape dimensions not shown comply with JEDEC Standard EIA-481-2Tape and Reel Packaging for 16-Pin SOIC PackageDimensionsmm (inches)B 0=10.30± 0.150=2.70±±1=2.30± 0.15± 0.01)Moisture SensitivityClare has characterized the moisture reflow sensitivity of this package, and has determined that this component must be handled in accordance with IPC/JEDEC standard J-STD-033 moisture sensitivity level (MSL), level 3 classification.Soldering Reflow ProfileFor proper assembly, the component must be processed in accordance with the current revision of IPC/JEDEC standard J-STD-020. Failure to follow the recommended guidelines may causepermanent damage to the device resulting in impaired performance and/or a reduced lifetime expectancy.WashingClare does not recommend ultrasonic cleaning or the use of chlorinated solvents./分销商库存信息: IXYSCPC1824N。