氧气底吹熔炼—鼓风炉还原炼铅新技术
氧气底吹熔炼—鼓风炉还原炼铅新技术
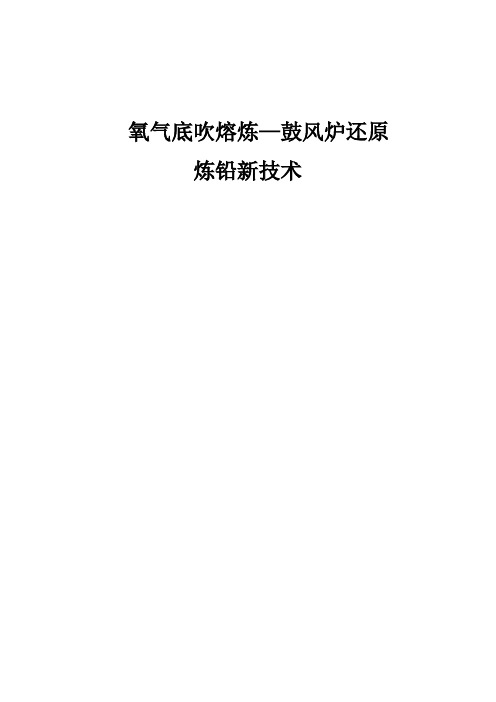
氧气底吹熔炼—鼓风炉还原炼铅新技术氧气底吹熔炼—鼓风炉还原炼铅法一、氧气底吹熔炼—鼓风炉法简介氧气底吹熔炼—鼓风炉还原炼铅法工艺流程为:熔剂、铅精矿或二次铅原料及铅烟尘经配料、制粒或混捏后进行氧气底吹熔炼,产出烟气、一次粗铅和铅氧化渣,烟气经余热锅炉回收余热和电收尘器收尘后采用二转二吸工艺制酸,尾气排放,铅烟尘返回配料。
铅氧化渣经铸块后与焦块、熔剂块混合后入鼓风炉进行还原熔炼,产出炉渣、烟气和粗铅,烟气经收尘后放空,铅烟尘返回配料。
工艺主要设备包括可旋转式氧气底吹熔炼炉,多元套管结构氧枪(多通道水冷高温喷镀耐磨底吹氧枪),特殊耐磨材质的氧枪口保护砖,浅层分格富铅渣速冷铸渣机(铅氧化渣铸渣机),带弧型密封罩和垂直模式壁中压防腐余热锅炉,全封闭铅烟尘输送配料等, 新型结构鼓风炉(双排风口大炉腹角高料柱)等。
工艺的核心设备是氧气底吹熔炼炉。
熔炼炉炉型结构为可回转的卧式圆筒形,在炉顶部设有2~3 个加料口,底侧部设有3~6 个氧气喷入口,炉子两端分别设一个虹吸放铅口和铅氧化渣放出口。
炉端上方设有烟气出口。
铅精矿的氧化熔炼是在一个水平回转式熔炼炉中进行的。
铅精矿、铅烟尘、熔剂及少量粉煤经计量、配料、圆盘制粒后, 由炉子上方的气封加料口加入炉内, 工业纯氧从炉底的氧枪喷入熔池。
氧气进入熔池后, 首先和铅液接触反应, 生成氧化铅(PbO ) , 其中一部分氧化铅在激烈的搅动状态下, 和位于熔池上部的硫化铅(PbS) 进行反应熔炼, 产出一次粗铅并放出SO 2。
反应生成的一次粗铅和铅氧化渣沉淀分离后, 粗铅虹吸或直接放出,铅氧化渣则由铸锭机铸块后, 送往鼓风炉工段还原熔炼, 产出二次粗铅。
出炉SO 2 烟气采用余热锅炉或汽化冷却器回收余热, 经电收尘器收尘, 送硫酸车间处理。
熔炼炉采用微负压操作, 整个烟气排放系统处于密封状态, 从而有效防止了烟气外逸。
同时, 由于混合物料是以润湿、粒状形式输送入炉的, 加上在出铅、出渣口采取有效的集烟通风措施, 从而避免了铅烟尘的飞扬。
氧气底吹熔炼炉
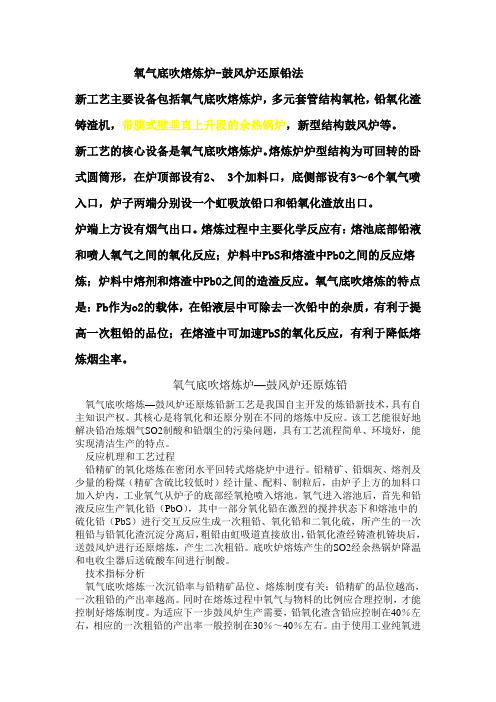
氧气底吹熔炼炉-鼓风炉还原铅法新工艺主要设备包括氧气底吹熔炼炉,多元套管结构氧枪,铅氧化渣铸渣机,带膜式壁垂直上升段的余热锅炉,新型结构鼓风炉等。
新工艺的核心设备是氧气底吹熔炼炉。
熔炼炉炉型结构为可回转的卧式圆筒形,在炉顶部设有2、 3个加料口,底侧部设有3~6个氧气喷入口,炉子两端分别设一个虹吸放铅口和铅氧化渣放出口。
炉端上方设有烟气出口。
熔炼过程中主要化学反应有:熔池底部铅液和喷人氧气之间的氧化反应;炉料中PbS和熔渣中PbO之间的反应熔炼;炉料中熔剂和熔渣中PbO之间的造渣反应。
氧气底吹熔炼的特点是:Pb作为o2的载体,在铅液层中可除去一次铅中的杂质,有利于提高一次粗铅的品位;在熔渣中可加速PbS的氧化反应,有利于降低熔炼烟尘率。
氧气底吹熔炼炉—鼓风炉还原炼铅氧气底吹熔炼—鼓风炉还原炼铅新工艺是我国自主开发的炼铅新技术,具有自主知识产权。
其核心是将氧化和还原分别在不同的熔炼中反应。
该工艺能很好地解决铅冶炼烟气SO2制酸和铅烟尘的污染问题,具有工艺流程简单、环境好,能实现清洁生产的特点。
反应机理和工艺过程铅精矿的氧化熔炼在密闭水平回转式熔烧炉中进行。
铅精矿、铅烟灰、熔剂及少量的粉煤(精矿含硫比较低时)经计量、配料、制粒后,由炉子上方的加料口加入炉内,工业氧气从炉子的底部经氧枪喷入熔池。
氧气进入溶池后,首先和铅液反应生产氧化铅(PbO),其中一部分氧化铅在激烈的搅拌状态下和熔池中的硫化铅(PbS)进行交互反应生成一次粗铅、氧化铅和二氧化硫,所产生的一次粗铅与铅氧化渣沉淀分离后,粗铅由虹吸道直接放出,铅氧化渣经铸渣机铸块后,送鼓风炉进行还原熔炼,产生二次粗铅。
底吹炉熔炼产生的SO2经余热锅炉降温和电收尘器后送硫酸车间进行制酸。
技术指标分析氧气底吹熔炼一次沉铅率与铅精矿品位、熔炼制度有关:铅精矿的品位越高,一次粗铅的产出率越高。
同时在熔炼过程中氧气与物料的比例应合理控制,才能控制好熔炼制度。
为适应下一步鼓风炉生产需要,铅氧化渣含铅应控制在40%左右,相应的一次粗铅的产出率一般控制在30%~40%左右。
氧气底吹熔炼_鼓风炉还原炼铅工艺的开发和应用
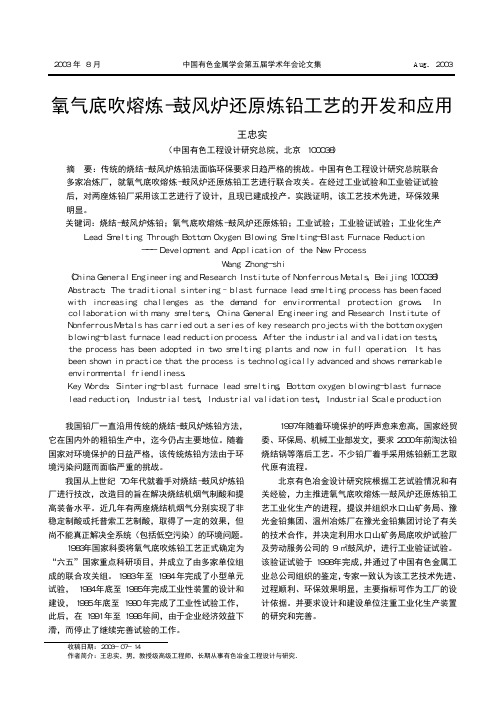
2003 年 8 月 中国有色金属学会第五届学术年会论文集 Aug . 2003 收稿日期:2003-07-14 作者简介:王忠实,男,教授级高级工程师,长期从事有色冶金工程设计与研究.氧气底吹熔炼-鼓风炉还原炼铅工艺的开发和应用 王忠实 (中国有色工程设计研究总院,北京 100038) 摘 要:传统的烧结-鼓风炉炼铅法面临环保要求日趋严格的挑战。
中国有色工程设计研究总院联合多家冶炼厂,就氧气底吹熔炼-鼓风炉还原炼铅工艺进行联合攻关。
在经过工业试验和工业验证试验后,对两座炼铅厂采用该工艺进行了设计,且现已建成投产。
实践证明,该工艺技术先进,环保效果明显。
关键词:烧结-鼓风炉炼铅;氧气底吹熔炼-鼓风炉还原炼铅;工业试验;工业验证试验;工业化生产 Lead Smelting Through Bottom Oxygen Blowing Smelting-Blast Furnace Reduction --- Development and Application of the New Process Wang Zhong-shi (China General Engineering and Research Institute of Nonferrous Metals, Beijing 100038) Abstract: The traditional sintering – blast furnace lead smelting process has been faced with increasing challenges as the demand for environmental protection grows. In collaboration with many smelters, China General Engineering and Research Institute of Nonferrous Metals has carried out a series of key research projects with the bottom oxygen blowing-blast furnace lead reduction process. After the industrial and validation tests, the process has been adopted in two smelting plants and now in full operation. It has been shown in practice that the process is technologically advanced and shows remarkable environmental friendliness. Key Words: Sintering-blast furnace lead smelting, Bottom oxygen blowing-blast furnace lead reduction, Industrial test, Industrial validation test, Industrial Scale production 我国铅厂一直沿用传统的烧结-鼓风炉炼铅方法,它在国内外的粗铅生产中,迄今仍占主要地位。
氧气底吹转炉炼铅法
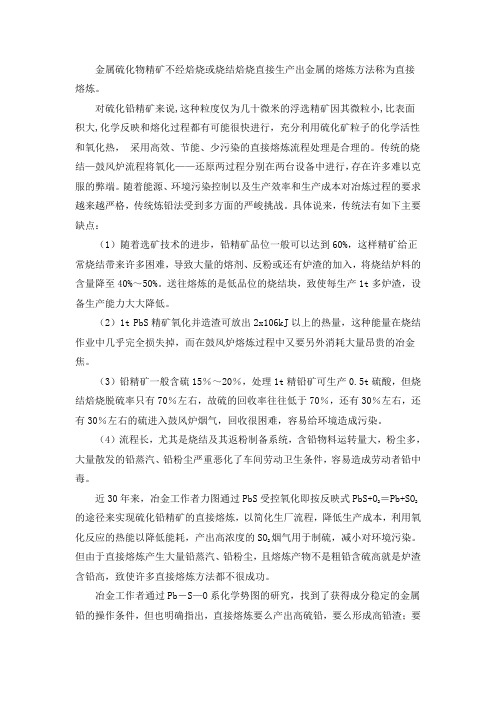
金属硫化物精矿不经焙烧或烧结焙烧直接生产出金属的熔炼方法称为直接熔炼。
对硫化铅精矿来说,这种粒度仅为几十微米的浮选精矿因其微粒小,比表面积大,化学反映和熔化过程都有可能很快进行,充分利用硫化矿粒子的化学活性和氧化热,采用高效、节能、少污染的直接熔炼流程处理是合理的。
传统的烧结—鼓风炉流程将氧化——还原两过程分别在两台设备中进行,存在许多难以克服的弊端。
随着能源、环境污染控制以及生产效率和生产成本对冶炼过程的要求越来越严格,传统炼铅法受到多方面的严峻挑战。
具体说来,传统法有如下主要缺点:(1)随着选矿技术的进步,铅精矿品位一般可以达到60%,这样精矿给正常烧结带来许多困难,导致大量的熔剂、反粉或还有炉渣的加入,将烧结炉料的含量降至40%~50%。
送往熔炼的是低品位的烧结块,致使每生产1t多炉渣,设备生产能力大大降低。
(2)1t PbS精矿氧化并造渣可放出2x106kJ以上的热量,这种能量在烧结作业中几乎完全损失掉,而在鼓风炉熔炼过程中又要另外消耗大量昂贵的冶金焦。
(3)铅精矿一般含硫15%~20%,处理1t精铅矿可生产0.5t硫酸,但烧结焙烧脱硫率只有70%左右,故硫的回收率往往低于70%,还有30%左右,还有30%左右的硫进入鼓风炉烟气,回收很困难,容易给环境造成污染。
(4)流程长,尤其是烧结及其返粉制备系统,含铅物料运转量大,粉尘多,大量散发的铅蒸汽、铅粉尘严重恶化了车间劳动卫生条件,容易造成劳动者铅中毒。
近30年来,冶金工作者力图通过PbS受控氧化即按反映式PbS+O2=Pb+SO2的途径来实现硫化铅精矿的直接熔炼,以简化生厂流程,降低生产成本,利用氧化反应的热能以降低能耗,产出高浓度的SO2烟气用于制硫,减小对环境污染。
但由于直接熔炼产生大量铅蒸汽、铅粉尘,且熔炼产物不是粗铅含硫高就是炉渣含铅高,致使许多直接熔炼方法都不很成功。
冶金工作者通过Pb-S—O系化学势图的研究,找到了获得成分稳定的金属铅的操作条件,但也明确指出,直接熔炼要么产出高硫铅,要么形成高铅渣;要获得含硫低的合格粗铅,就必须还原处理含铅高的直接熔炼炉渣。
氧气底吹法(以此为准)

“吹氧造锍多金属捕集技术”创造中国冶金奇迹人民日报记者部主任张平力,记者王明峰中国冶金史上的一场技术革命正在黄河三角洲滨海城市东营悄然掀起。
由山东方圆有色金属集团公司与中国有色工程设计研究总院共同研制开发的“吹氧造锍多金属捕集技术”点燃了这场革命。
新技术的发明我国不仅是产铜大国,而且是炼铜大国。
传统炼铜工艺在世界上曾一度领先,现代工艺却没有一席之地。
先秦时期就已出现鼓风炉法炼铜,西汉时用铁从硫酸铜(胆铜)溶液中置换铜。
现在我国使用的炼铜技术几乎都来自国外:11种技术中,引进的6种,未经引进而消化吸收开发的有3种。
自己研发的两种炼铜技术中,只有“氧气底吹法”可与国际先进工艺媲美。
之前,国外先进的吹氧炼铜工艺有顶吹和侧吹两种。
中国有色工程设计研究总院(原北京有色冶金设计研究总院)原副院长兼总工程师、全国工程设计大师蒋继穆经过多年潜心研究,改换顶吹、侧吹送氧位置,将氧气用氧枪从熔炼炉底部送入炉内,并攻克了很多工艺和工程难题,发明了氧气底吹炼铜法。
令同行惊奇的是,这一改变竟为有色冶金技术带来了革命性变化,不仅打破了国内铜冶炼技术由国外长期垄断的局面,还为铜铅和金银等稀有贵金属的综合回收提取开辟了一条新路子。
从顶吹、侧吹到底吹,只是吹氧位置的不同,难道别人就想不到吗?“用氧气底吹法炼铜最早是美国和德国的教授于上世纪70年代末80年代初提出来的,并且做过试验。
”蒋继穆坦言,可是他们在做扩大试验时,大量的工程问题解决不了,后来,只好宣布这个“玩意”不行。
“我们最早用氧气底吹技术试验炼铅。
做完5000吨铅冶炼试验后,就想用这个工艺和装置试验炼铜。
”霜染双鬓的蒋继穆娓娓道来,把思绪带回到了1991年的湖南水口山。
“准备半年的试验炉料(相当于3000吨铜的规模),两个月就‘吃’完了。
可是,炉子一点故障都没有,于是接着弄铜精矿连续试验,一试就开了217天。
”通过试验,发现底吹较之顶吹、侧吹不只是位置不同,它还具有噪音低,车间操作环境更好的优点。
浅析SKS法氧气底吹熔炼炉开炉的基础环节

浅析SKS法氧气底吹熔炼炉开炉的基础环节(湘南学院吴建林许尚平曹健)氧气底吹熔炼—鼓风炉还原炼铅新工艺及工业化装置开发,彻底改变了中国铅冶炼污染现状,在环境治理上取得突破性进展,是中国有色金属行业的重大技术进步,对国民经济可持续发展具有深远意义。
该工艺属有色金属行业冶炼技术的重大技术创新,达到国际先进技术水平。
其特点是利用氧气底吹炉氧化,替代烧结工艺,彻底解决了原烧结过程中SO2及铅尘严重污染环境的难题。
底吹产出的高铅渣用创新后的鼓风炉还原,有效抑制了低沸点铅物的挥发,克服了其他炼铅新工艺普遍存在的烟尘率高、返尘量大的缺点,且具有金属回收率高、热能利用好等许多优点。
在我国所采用此法的铅冶炼企业投产连续运行几年多实践表明,该工艺具有投资省(为传统流程的70%,不到引进工艺的50%),综合能耗低(为380-400kg标煤/t 粗铅,与基夫赛特和顶吹浸没熔炼工艺持平),环保好(硫的捕集率>99%,所有排放物均达标),金属回收率高(铅、银达98%-98.5%),生产成本低(为传统工艺的85%,比国外新工艺更低)等特点。
该工艺是先进的熔池熔炼现代技术与创新后的鼓风炉还原工艺的完美结合,具有显著的经济和环保效益,已获得铅冶炼同行的认可,并已扩展到铜冶炼。
该技术在我市宇腾有色、华信集团等企业已成功应用,综合效益显著。
笔者根据目前此法在我市几家铅冶炼企业所应用的基本情况,就该法氧气底吹熔炼炉的开炉环节,畅所欲言:一、开炉前所要做的准备工作开炉前的首要工作是人员配备,这是氧气底吹熔炼炉开炉的先决条件。
开炉及投底铅前应做到人手齐备、确保快速完成投底铅,快速开炉。
因新砌底吹炉体在长期处于冷态,因此,在底吹炉升温过程要求严格按底吹炉升温工艺要求执行,防止因升温不当而导致炉衬及附属设施热应力损伤,给后续生产带来安全隐患;同时也防止升温不够,使底吹炉进入生产位时各熔池反应难以迅速进行,没有很好的熔池挠动的结果会产生氧枪工作不稳定,从而直接导致加料口大量烟气外溢。
铅冶炼工艺流程
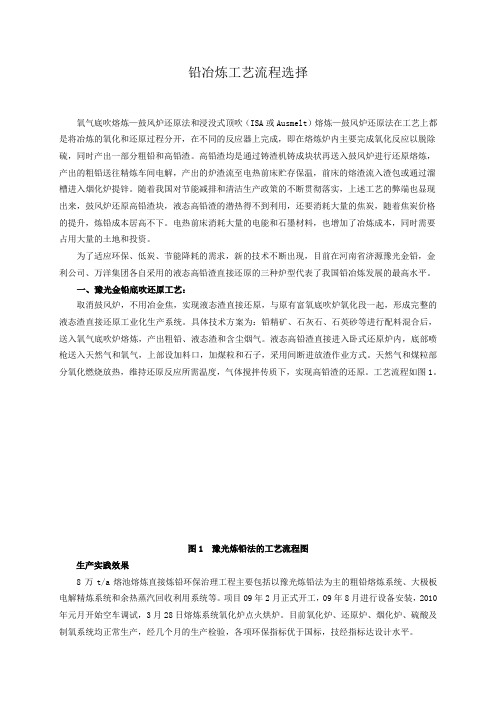
铅冶炼工艺流程选择氧气底吹熔炼—鼓风炉还原法和浸没式顶吹(ISA或Ausmelt)熔炼—鼓风炉还原法在工艺上都是将冶炼的氧化和还原过程分开,在不同的反应器上完成,即在熔炼炉内主要完成氧化反应以脱除硫,同时产出一部分粗铅和高铅渣。
高铅渣均是通过铸渣机铸成块状再送入鼓风炉进行还原熔炼,产出的粗铅送往精炼车间电解,产出的炉渣流至电热前床贮存保温,前床的熔渣流入渣包或通过溜槽进入烟化炉提锌。
随着我国对节能减排和清洁生产政策的不断贯彻落实,上述工艺的弊端也显现出来,鼓风炉还原高铅渣块,液态高铅渣的潜热得不到利用,还要消耗大量的焦炭,随着焦炭价格的提升,炼铅成本居高不下。
电热前床消耗大量的电能和石墨材料,也增加了冶炼成本,同时需要占用大量的土地和投资。
为了适应环保、低炭、节能降耗的需求,新的技术不断出现,目前在河南省济源豫光金铅,金利公司、万洋集团各自采用的液态高铅渣直接还原的三种炉型代表了我国铅冶炼发展的最高水平。
一、豫光金铅底吹还原工艺:取消鼓风炉,不用冶金焦,实现液态渣直接还原,与原有富氧底吹炉氧化段一起,形成完整的液态渣直接还原工业化生产系统。
具体技术方案为:铅精矿、石灰石、石英砂等进行配料混合后,送入氧气底吹炉熔炼,产出粗铅、液态渣和含尘烟气。
液态高铅渣直接进入卧式还原炉内,底部喷枪送入天然气和氧气,上部设加料口,加煤粒和石子,采用间断进放渣作业方式。
天然气和煤粒部分氧化燃烧放热,维持还原反应所需温度,气体搅拌传质下,实现高铅渣的还原。
工艺流程如图1。
图1 豫光炼铅法的工艺流程图生产实践效果8万t/a熔池熔炼直接炼铅环保治理工程主要包括以豫光炼铅法为主的粗铅熔炼系统、大极板电解精炼系统和余热蒸汽回收利用系统等。
项目09年2月正式开工,09年8月进行设备安装,2010年元月开始空车调试,3月28日熔炼系统氧化炉点火烘炉。
目前氧化炉、还原炉、烟化炉、硫酸及制氧系统均正常生产,经几个月的生产检验,各项环保指标优于国标,技经指标达设计水平。
铅冶炼氧气底吹资料
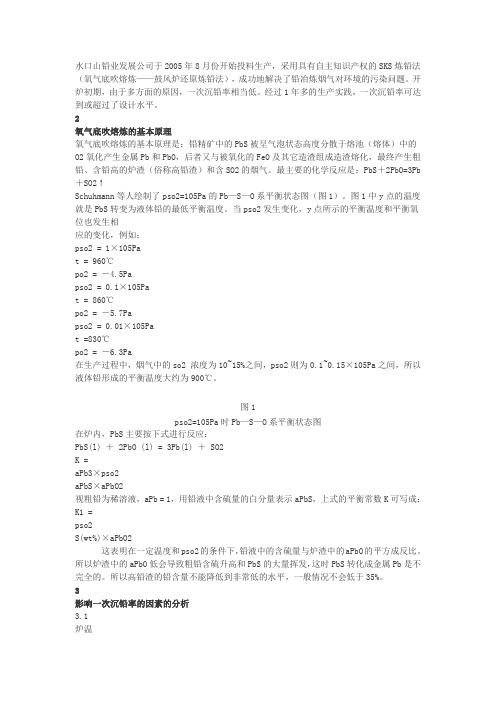
水口山铅业发展公司于2005年8月份开始投料生产,采用具有自主知识产权的SKS炼铅法(氧气底吹熔炼——鼓风炉还原炼铅法),成功地解决了铅冶炼烟气对环境的污染问题。
开炉初期,由于多方面的原因,一次沉铅率相当低。
经过1年多的生产实践,一次沉铅率可达到或超过了设计水平。
2氧气底吹熔炼的基本原理氧气底吹熔炼的基本原理是:铅精矿中的PbS被呈气泡状态高度分散于熔池(熔体)中的O2氧化产生金属Pb和PbO,后者又与被氧化的FeO及其它造渣组成造渣熔化,最终产生粗铅、含铅高的炉渣(俗称高铅渣)和含SO2的烟气。
最主要的化学反应是:PbS+2PbO=3Pb +SO2↑Schuhmann等人绘制了pso2=105Pa的Pb—S—O系平衡状态图(图1)。
图1中y点的温度就是PbS转变为液体铅的最低平衡温度。
当pso2发生变化,y点所示的平衡温度和平衡氧位也发生相应的变化,例如:pso2 = 1×105Pat = 960℃po2 = -4.5Papso2 = 0.1×105Pat = 860℃po2 = -5.7Papso2 = 0.01×105Pat =830℃po2 = -6.3Pa在生产过程中,烟气中的so2 浓度为10~15%之间,pso2则为0.1~0.15×105Pa之间,所以液体铅形成的平衡温度大约为900℃。
图1pso2=105Pa时Pb—S—O系平衡状态图在炉内,PbS主要按下式进行反应:PbS(l) + 2PbO (l) = 3Pb(l) + SO2K =aPb3×pso2aPbS×aPbO2视粗铅为稀溶液,aPb = 1,用铅液中含硫量的白分量表示aPbS,上式的平衡常数K可写成:K1 =pso2S(wt%)×aPbO2这表明在一定温度和pso2的条件下,铅液中的含硫量与炉渣中的aPbO的平方成反比。
所以炉渣中的aPbO低会导致粗铅含硫升高和PbS的大量挥发,这时PbS转化成金属Pb是不完全的。
科技网 --《科技日报》-- 氧气底吹熔炼—底吹熔融电热还原炼铅法
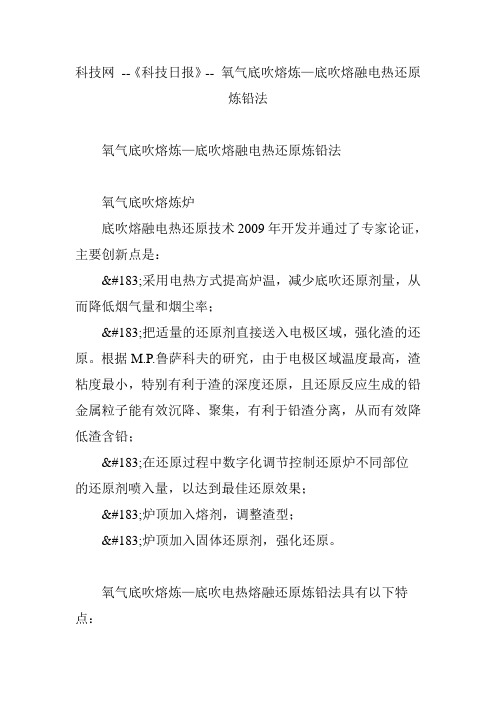
科技网--《科技日报》-- 氧气底吹熔炼—底吹熔融电热还原炼铅法氧气底吹熔炼—底吹熔融电热还原炼铅法氧气底吹熔炼炉底吹熔融电热还原技术2009年开发并通过了专家论证,主要创新点是:·采用电热方式提高炉温,减少底吹还原剂量,从而降低烟气量和烟尘率;·把适量的还原剂直接送入电极区域,强化渣的还原。
根据M.P.鲁萨科夫的研究,由于电极区域温度最高,渣粘度最小,特别有利于渣的深度还原,且还原反应生成的铅金属粒子能有效沉降、聚集,有利于铅渣分离,从而有效降低渣含铅;·在还原过程中数字化调节控制还原炉不同部位的还原剂喷入量,以达到最佳还原效果;·炉顶加入熔剂,调整渣型;·炉顶加入固体还原剂,强化还原。
氧气底吹熔炼—底吹电热熔融还原炼铅法具有以下特点:1. 对原料适应性强——氧气底吹熔炼炉入炉原料(包括熔剂)无需干燥,无需破碎,无需磨矿,湿料、块矿、粒矿、粉矿均可直接送入炉内进行熔炼;——可搭配处理其它各种二次铅原料,如废蓄电池铅膏等,根据氧气底吹熔炼炉的生产实践,在处理硫化铅精矿时,废蓄电池铅膏配入量可达50%,在回收铅的同时,还可以有效回收其中的硫;目前,世界上以废蓄电池铅膏为代表的二次铅原料处理工艺和设施普遍比较落后,氧气底吹熔炼炉的生产实践为二次铅原料的处理开辟了既经济又环保的技术路线;——氧气底吹熔炼炉可处理各种品位的硫化矿,并可搭配处理氧化矿,实际生产中入炉原料Pb的品位波动在30%—75%均能正常作业;——氧气底吹熔炼炉可搭配处理锌系统铅银渣等含铅物料,对铅锌联合企业可实现生产互补,循环利用。
河南安阳一家铅冶炼厂实际生产中,铅银渣配入比例达50%,入炉原料Pb品位降低至30%,氧气底吹熔炼炉运行正常;——氧气底吹熔炼炉可处理含铜高的铅精矿,生产实践中,含Cu 3%的铅精矿也能顺利进行熔炼,产生的铜锍和铅一同从虹吸口放出,然后在铅液中熔析分离;2. 能耗低——氧气底吹熔炼炉和还原炉均采用工业纯氧熔炼,动力消耗少;产出烟气量小,烟气带走热少;——氧气底吹熔炼炉和还原炉均内衬耐火材料,熔池部位没有水套,炉子保温性能好,散热损失小;——低碳还原熔炼,和目前其他炼铅法相比,熔炼相同原料时,能耗相对是低的;——采用余热锅炉有效回收氧气底吹熔炼炉,和还原炉烟气中的余热,产出中压蒸气(4MPa)进行发电;3. 环保好——熔炼过程在密闭的氧气底吹熔炼炉中进行,生产中能稳定控制氧气底吹熔炼炉微负压操作,有效避免了SO2烟气外逸;氧气底吹熔炼厂房生产操作环境用空气采样器检测典型的结果为:Pb含量:0.03mg/m3,SO2含量:0.05mg/m3;——氧枪底吹作业,熔炼车间噪音小;——工艺流程短捷,生产过程中产出的铅烟尘均密封输送并返回配料,有效防止了铅尘的弥散污染;4. 有价元素回收率高——铅回收率高:还原终渣含铅可保证≤3%,与其他炼铅工艺相比是较低的;——贵金属回收率高:氧气底吹熔炼炉和还原炉两段产粗铅,对贵金属实施两次捕集,较一段炼铅法,Au、Ag回收率可提高1—3个百分点,实际Ag,Au进入粗铅率≥99%;——氧气底吹熔炼炉脱硫率高,S回收率>96%;5. 作业率高——氧气底吹熔炼炉和还原炉构造简单,故障率低,维护方便;——氧气底吹熔炼炉炉衬寿命较高,实际生产炉寿高达3年以上;——氧气底吹熔炼炉氧枪寿命长,实际喷枪寿命为30—60d;——还原炉喷枪寿命预计大于90d;——氧气底吹熔炼炉只有在更换喷枪时才停止加料;——作业率>90%,年有效作业时间>7900h;6. 操作控制简单——氧气底吹熔炼炉和还原炉工艺控制容易,操作简单;7. 自动化水平高——整个生产系统采用DCS控制;8. 单机处理能力大——现有氧气底吹炼铅装置单系列产能已达20万t/a,可预期的单系列产能可达50万t/a;9. 投资省——工艺流程简短,设备投资省;——熔炼厂房建筑结构简单,建筑面积小,土建费用低。
氧气底吹熔炼——鼓风炉还原炼铅新技术及应用
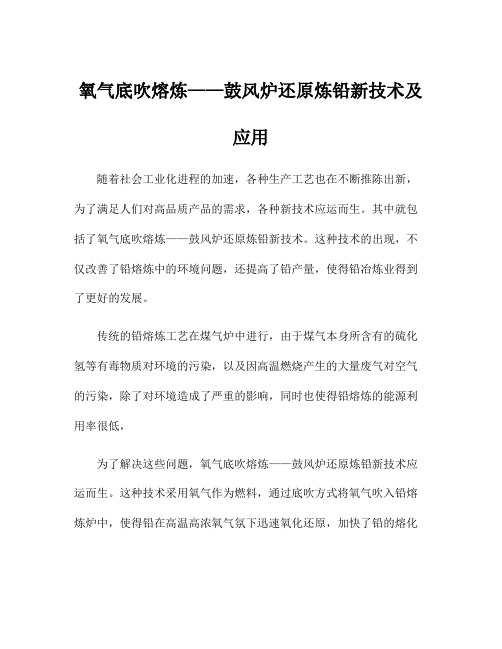
氧气底吹熔炼——鼓风炉还原炼铅新技术及
应用
随着社会工业化进程的加速,各种生产工艺也在不断推陈出新,为了满足人们对高品质产品的需求,各种新技术应运而生。
其中就包括了氧气底吹熔炼——鼓风炉还原炼铅新技术。
这种技术的出现,不仅改善了铅熔炼中的环境问题,还提高了铅产量,使得铅冶炼业得到了更好的发展。
传统的铅熔炼工艺在煤气炉中进行,由于煤气本身所含有的硫化氢等有毒物质对环境的污染,以及因高温燃烧产生的大量废气对空气的污染,除了对环境造成了严重的影响,同时也使得铅熔炼的能源利用率很低,
为了解决这些问题,氧气底吹熔炼——鼓风炉还原炼铅新技术应运而生。
这种技术采用氧气作为燃料,通过底吹方式将氧气吹入铅熔炼炉中,使得铅在高温高浓氧气氛下迅速氧化还原,加快了铅的熔化
和反应速率,同时废气、废渣产生率也得到了大幅度降低,不仅对环
境影响减小,而且对于铅产出质量的提高也有明显作用。
在现如今的铅冶炼业,氧气底吹熔炼——鼓风炉还原炼铅新技术
得到了广泛应用。
采用这种技术可以使得铅炉的能耗比传统炉子降低
约25%~35%不等,同样的情况下也能产生更多的铅产出,同时在生产过程中无污染的废气排放,使得工作环境更加安全,这给企业的生产过
程增加了很多收益和竞争力。
综上所述,氧气底吹熔炼——鼓风炉还原炼铅新技术的广泛应用,不仅对于环保和节能的发展产生了积极的推动作用,而且在提高生产
成本的同时也促进了铅冶炼业的发展。
因此,这种技术的应用前景非
常广阔,也值得我们在实际生产中予以重视。
铅阳极泥富氧底吹还原熔炼--氧化精炼新工艺的生产实践的开题报告

铅阳极泥富氧底吹还原熔炼--氧化精炼新工艺的生产实践的开题报告标题:铅阳极泥富氧底吹还原熔炼--氧化精炼新工艺的生产实践一、研究背景及意义铅阳极泥是电解铅生产中不可避免的废弃物,其主要成分为氧化铅和氧化铅、氧化钠以及少量的碳酸钙、硅酸钙等杂质。
目前,铅阳极泥的处理主要采用高温煅烧工艺,其环境治理压力也日益增大。
因此,对铅阳极泥进行资源化处理已成为发展电解铅工业的重要途径。
富氧底吹还原熔炼--氧化精炼新工艺是一种可行的铅阳极泥资源化处理工艺,该工艺可以将铅阳极泥中的氧化铅还原为金属铅,并将氧化钠转化为碱熔渣,从而实现铅和钠的有效回收,同时降低环境污染和减少生产成本,具有重要的理论和实际意义。
二、研究内容和方法1. 研究铅阳极泥的物化性质,包括其组成、物相、粒度和比表面积等;2. 构建富氧底吹还原熔炼--氧化精炼新工艺的试验装置,并对铅阳极泥进行试验研究,探究其还原和氧化等反应过程的机理;3. 对实验结果进行分析处理,考察铅阳极泥的还原和氧化效果、熔体温度、铅和钠回收率等重要参数的变化规律;4. 对富氧底吹还原熔炼--氧化精炼新工艺的经济效益和环境效益进行评估,为该工艺的规模化应用提供科学依据。
三、研究进展和意义目前,我们已经对铅阳极泥进行了初步的物化性质分析,并针对其还原和氧化等过程进行了实验研究。
研究结果表明,富氧底吹还原熔炼--氧化精炼新工艺是一种可行的铅阳极泥资源化处理工艺,其还原和氧化效果显著,同时可实现铅和钠的有效回收,环境污染和生产成本也得到了有效控制,具有重要的现实应用价值和理论意义。
未来,我们将继续深入开展研究,完善富氧底吹还原熔炼--氧化精炼新工艺的技术和装备,进一步提高其处理能力和产品质量,同时推进其规模化应用,为推动电解铅工业的可持续发展做出贡献。
冶炼工艺流程铅冶炼工艺流程
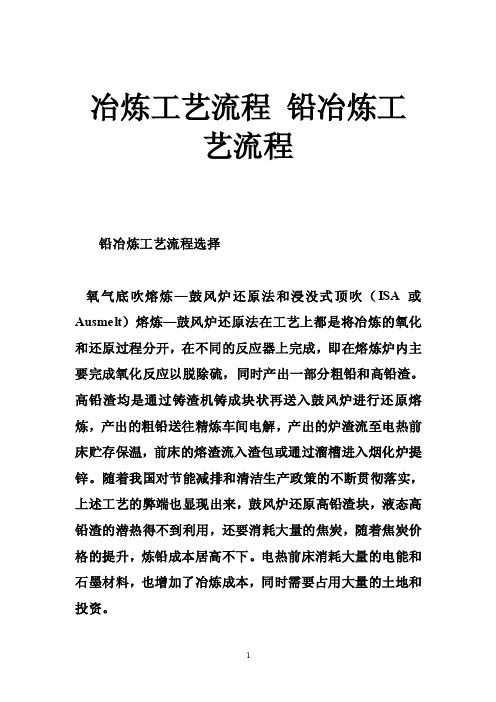
冶炼工艺流程铅冶炼工艺流程铅冶炼工艺流程选择氧气底吹熔炼—鼓风炉还原法和浸没式顶吹(ISA或Ausmelt)熔炼—鼓风炉还原法在工艺上都是将冶炼的氧化和还原过程分开,在不同的反应器上完成,即在熔炼炉内主要完成氧化反应以脱除硫,同时产出一部分粗铅和高铅渣。
高铅渣均是通过铸渣机铸成块状再送入鼓风炉进行还原熔炼,产出的粗铅送往精炼车间电解,产出的炉渣流至电热前床贮存保温,前床的熔渣流入渣包或通过溜槽进入烟化炉提锌。
随着我国对节能减排和清洁生产政策的不断贯彻落实,上述工艺的弊端也显现出来,鼓风炉还原高铅渣块,液态高铅渣的潜热得不到利用,还要消耗大量的焦炭,随着焦炭价格的提升,炼铅成本居高不下。
电热前床消耗大量的电能和石墨材料,也增加了冶炼成本,同时需要占用大量的土地和投资。
为了适应环保、低炭、节能降耗的需求,新的技术不断出现,目前在河南省济源豫光金铅,金利公司、万洋集团各自采用的液态高铅渣直接还原的三种炉型代表了我国铅冶炼发展的最高水平。
一、豫光金铅底吹还原工艺:取消鼓风炉,不用冶金焦,实现液态渣直接还原,与原有富氧底吹炉氧化段一起,形成完整的液态渣直接还原工业化生产系统。
具体技术方案为:铅精矿、石灰石、石英砂等进行配料混合后,送入氧气底吹炉熔炼,产出粗铅、液态渣和含尘烟气。
液态高铅渣直接进入卧式还原炉内,底部喷枪送入天然气和氧气,上部设加料口,加煤粒和石子,采用间断进放渣作业方式。
天然气和煤粒部分氧化燃烧放热,维持还原反应所需温度,气体搅拌传质下,实现高铅渣的还原。
工艺流程如图1。
图1 豫光炼铅法的工艺流程图生产实践效果8万t/a熔池熔炼直接炼铅环保治理工程主要包括以豫光炼铅法为主的粗铅熔炼系统、大极板电解精炼系统和余热蒸汽回收利用系统等。
项目09年2月正式开工,09年8月进行设备安装,2010年元月开始空车调试,3月28日熔炼系统氧化炉点火烘炉。
目前氧化炉、还原炉、烟化炉、硫酸及制氧系统均正常生产,经几个月的生产检验,各项环保指标优于国标,技经指标达设计水平。
科技成果——氧气底吹熔炼技术

科技成果——氧气底吹熔炼技术适用范围有色金属行业铅冶炼企业,规模5-20万t/a均可,亦适用于铜及其它硫化矿物的提取冶金企业行业现状氧气底吹熔炼技术在不断完善与提升,已取得一系列的技术进步。
铅冶炼“氧气底吹熔炼-液态铅渣直接还原”取代“氧气底吹熔炼-鼓风炉还原”,吨粗铅综合能耗由360kgce降至200kgce,吨粗铅减排422.4kgCO2。
液态铅渣直接还原升级改造投资约4000万。
氧气底吹炼铜技术工业化应用以来,吨粗铜综合能耗降至120-140kgce,比2012年全国粗铜平均能耗261.84kgce低很多。
采用氧气底吹炼铜工艺投资比采用其他炼铜工艺投资省至少10%。
目前该技术可实现节能量6万tce/a,减排约16万tCO2/a。
成果简介1、技术原理氧气底吹炼炉为一卧式圆柱体,支撑于设于硐基础的托辊之上,炉体通过齿轮转动,可绕水平轴左右转动。
炉体下部设有氧枪或还原枪,用于氧化硫化矿或还原氧化物。
由于氧气浓度高,烟气量少,炉内衬耐火材料,无冷却水套,热损失少。
铅精矿或铜精矿均可不加任何燃料,实现自然熔炼。
且系统设有烟气余热锅炉生产蒸汽发电,热能利用率高。
故氧气底吹炼铅或炼铜,目前均为世界上所有炼铅炼铜工艺中能耗最低的技术。
2、关键技术氧气底吹熔炼-液态铅渣直接还原炼铅工艺、氧气底吹熔炼-氧气底吹连续吹炼炼铜工艺、熔炼炉、还原炉、底吹连续吹炼炉、氧枪、余热锅炉等与该工艺配套的技术装备。
3、工艺流程铅硫化矿物、二次铅原料(铅膏、含铅玻璃、锌厂铅银渣、钢厂烟灰等)、熔剂及烟尘返料经配料制粒后,直接进入氧气底吹熔炼炉中进行熔炼,产出的高温SO2烟气经余热锅炉回收余热和电收尘器收尘后送两转两吸制酸;产出的一次粗铅送精炼;产出的熔融铅氧化渣直接流入还原炉。
熔融铅氧化渣与配入的熔剂、碎煤在还原炉内进行还原熔炼,也可以配入适量的铅氧化矿,产出的高温烟气经余热锅炉回收余热和收尘器收尘后送尾气脱硫;产出的二次粗铅送精炼;产出的还原炉渣直接流入烟化炉。
氧气底吹熔炼炉

氧气底吹熔炼炉氧气底吹熔炼炉-鼓风炉还原铅法新工艺主要设备包括氧气底吹熔炼炉,多元套管结构氧枪,铅氧化渣铸渣机,带膜式壁垂直上升段的余热锅炉,新型结构鼓风炉等。
新工艺的核心设备是氧气底吹熔炼炉。
熔炼炉炉型结构为可回转的卧式圆筒形,在炉顶部设有2、 3个加料口,底侧部设有3~6个氧气喷入口,炉子两端分别设一个虹吸放铅口和铅氧化渣放出口。
炉端上方设有烟气出口。
熔炼过程中主要化学反应有:熔池底部铅液和喷人氧气之间的氧化反应;炉料中PbS和熔渣中PbO之间的反应熔炼;炉料中熔剂和熔渣中PbO之间的造渣反应。
氧气底吹熔炼的特点是:Pb作为o2的载体,在铅液层中可除去一次铅中的杂质,有利于提高一次粗铅的品位;在熔渣中可加速PbS的氧化反应,有利于降低熔炼烟尘率。
氧气底吹熔炼炉—鼓风炉还原炼铅氧气底吹熔炼—鼓风炉还原炼铅新工艺是我国自主开发的炼铅新技术,具有自主知识产权。
其核心是将氧化和还原分别在不同的熔炼中反应。
该工艺能很好地解决铅冶炼烟气SO2制酸和铅烟尘的污染问题,具有工艺流程简单、环境好,能实现清洁生产的特点。
反应机理和工艺过程铅精矿的氧化熔炼在密闭水平回转式熔烧炉中进行。
铅精矿、铅烟灰、熔剂及少量的粉煤(精矿含硫比较低时)经计量、配料、制粒后,由炉子上方的加料口加入炉内,工业氧气从炉子的底部经氧枪喷入熔池。
氧气进入溶池后,首先和铅液反应生产氧化铅(PbO),其中一部分氧化铅在激烈的搅拌状态下和熔池中的硫化铅(PbS)进行交互反应生成一次粗铅、氧化铅和二氧化硫,所产生的一次粗铅与铅氧化渣沉淀分离后,粗铅由虹吸道直接放出,铅氧化渣经铸渣机铸块后,送鼓风炉进行还原熔炼,产生二次粗铅。
底吹炉熔炼产生的SO2经余热锅炉降温和电收尘器后送硫酸车间进行制酸。
技术指标分析氧气底吹熔炼一次沉铅率与铅精矿品位、熔炼制度有关:铅精矿的品位越高,一次粗铅的产出率越高。
同时在熔炼过程中氧气与物料的比例应合理控制,才能控制好熔炼制度。
氧气底吹炼铅新工艺概况
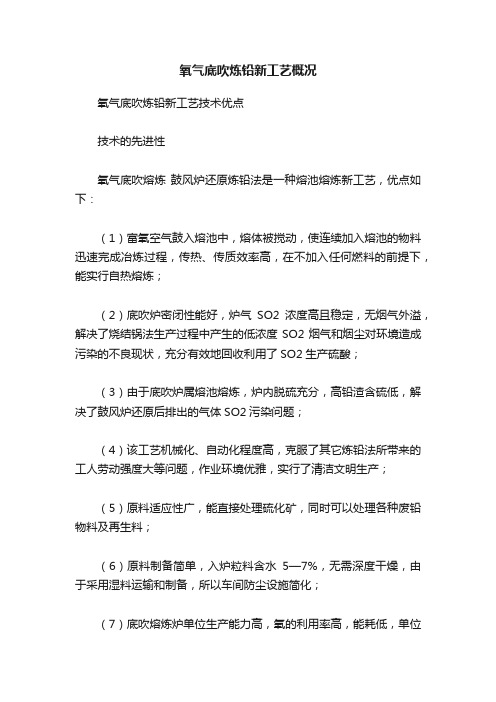
氧气底吹炼铅新工艺概况氧气底吹炼铅新工艺技术优点技术的先进性氧气底吹熔炼鼓风炉还原炼铅法是一种熔池熔炼新工艺,优点如下:(1)富氧空气鼓入熔池中,熔体被搅动,使连续加入熔池的物料迅速完成冶炼过程,传热、传质效率高,在不加入任何燃料的前提下,能实行自热熔炼;(2)底吹炉密闭性能好,炉气SO2浓度高且稳定,无烟气外溢,解决了烧结锅法生产过程中产生的低浓度SO2烟气和烟尘对环境造成污染的不良现状,充分有效地回收利用了SO2生产硫酸;(3)由于底吹炉属熔池熔炼,炉内脱硫充分,高铅渣含硫低,解决了鼓风炉还原后排出的气体SO2污染问题;(4)该工艺机械化、自动化程度高,克服了其它炼铅法所带来的工人劳动强度大等问题,作业环境优雅,实行了清洁文明生产;(5)原料适应性广,能直接处理硫化矿,同时可以处理各种废铅物料及再生料;(6)原料制备简单,入炉粒料含水5—7%,无需深度干燥,由于采用湿料运输和制备,所以车间防尘设施简化;(7)底吹熔炼炉单位生产能力高,氧的利用率高,能耗低,单位成本大大降低。
2、技术的成熟、可靠性本企业新建的氧气底吹炼铅新工艺产业化示范项目一次性投料生产的成果和各项经济技术指标达到并超过了设计指标的事实,证明了该工艺技术是成熟的,产业化生产时可靠的。
(1)作业率经过8个月的试生产,经测算作业率达90%以上。
主要停炉时间是更换氧枪,氧气底吹炉中设有4支氧枪,均由氮气和水保护,喷雾冷却效果好,氧枪平均使用寿命已达50天以上,最长时间57天。
更换氧枪时间较短,一般在2—3小时,炉衬使用至今,仍完好无损。
(2)工艺过程控制通过试生产,操作工已熟练掌握操作技能和工艺条件的控制,主要运用DCS系统对各运转设备及数据监测、观察、分析与处理,同时对氧气底吹炉加料口、放铅口、放渣口及余热锅炉加强管理,熟练掌握了氧枪检查与更换。
目技术内容项“氧气底吹熔炼—鼓风炉还原”炼铅新工艺是由氧气底吹熔炼铅精矿和鼓风炉还原高铅渣,烟气经除尘回收SO2制酸以及制O2、N2系统四大部分组成,其核心技术是氧气底吹熔炼。
三连炉炼铅工艺优势
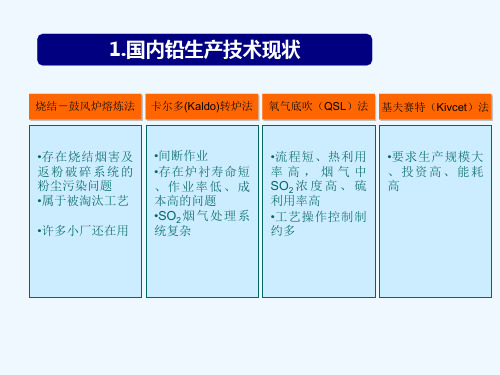
3.“三连炉”炉型结构及工艺特点
❖ (4)高铅渣还原仅用煤作为还原剂,与鼓风炉相比煤比焦炭价格低廉, 与国内其他的还原炉相比不需要天然气或煤气作为还原剂,使不具有 燃气的厂家也可采用此种工艺,对建厂条件的适应性更好,推广前 (5) 还原炉高温炉渣直接流入烟化炉,不需要提温阶段,可直接进入还原 提锌,节省了粉煤,烟化炉增加炉缸设计,氧化锌粉品位在80%以上,品 质很好。
1.国内铅生产技术现状
烧结-鼓风炉熔炼法 卡尔多(Kaldo)转炉法 氧气底吹(QSL)法 基夫赛特(Kivcet)法
•存在烧结烟害及 返粉破碎系统的 粉尘污染问题 •属于被淘汰工艺
•许多小厂还在用
•间断作业 •存在炉衬寿命短 、作业率低、成 本高的问题 •SO2 烟 气 处 理 系 统复杂
•流程短、热利用 率高,烟气中 SO2 浓 度 高 、 硫 利用率高
❖ (6)“三连炉”占地很小,布置紧凑,系统全部集中在一个厂房内,节省了 投资。
❖ (7) “三连炉”生产操作简单,实现DCS集中自动控制,指标易于控制, 工人劳动强度小,生产操作环境好。
4.其它液态渣直接还原炉型及工艺比较
❖ 济源某甲厂:氧化段为氧气底吹炉,还原段为氧气底吹卧式 炉,液态高铅渣直接还原,上部加入煤粒和石子,下部通入 天然气和氧气,间断进放渣作业,一个周期后,实现高铅渣 的还原,还原炉渣进入电热前床保温贮存,流入烟化炉烟化 提锌。
工艺弊端: •高铅渣的潜热得不到利用。 •鼓风炉需要消耗大量的冶金焦。 •鼓风炉与烟化炉之间均设有电热前床,消耗大量的电极材料和电能。
2.“三连炉”工艺流程及研发过程
❖ “三连炉”炼铅新工艺,采用氧化 炉—还原炉—烟化炉三炉相连,布置 紧凑、占地很小,热渣直流,节能降 耗。三台熔池熔炼炉由两道连接溜槽 串接在一起组成一整体;充分利用液 态高铅渣和还原炉渣的潜热,紧凑的 布置使得流程短占地很少,工人劳动 强度小,环保效果好,实现了铅冶炼 生产的低碳模式。
氧气底吹炼铅演示文稿
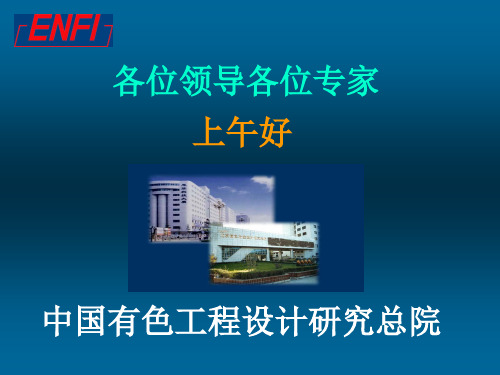
4-7d <0.5t标煤/t粗铅 3.5-4.0亿元 消除了SO2和铅 尘污染,熔炼车 间噪音大
<0.4t标煤/t粗铅 5.5-6.0亿元
<0.4t标煤/t粗铅 4.0-4.5亿元
环境条件
消除了SO2和铅 消除了SO2和铅 消除了SO2和铅 尘污染,熔炼 尘污染,熔炼车 尘污染,熔炼车 中国有色工程设计研究总院 车间环境良好 间环境良好 间环境良好
金属工业科学技术一等奖。
该技术及装置已受到国家知 识产权专利保护。
氧气底吹熔炼区域
中国有色工程设计研究总院
各种炼铅新工艺比较表
项目
经济规模 对原料适应性 备料要求 出炉烟气 S02浓度 终渣含Pb 铅回收率 氧枪Biblioteka 命 综合能耗 投资(按8万t/a)
氧气底吹熔炼鼓风炉还原法
3-10万t/a粗铅 铅精矿及二次 铅原料 简单,只需制 粒或混合 9-13% 2.5-3.5% 较高,97-98% 4-6周 <0.4t标煤/t粗 铅 2.0 -2.5亿元
(6)回收率高
有价元素回收率如下:Pb > 97% S > 95% Au > 98% Ag > 98%
中国有色工程设计研究总院
(7)对原料适应性强 氧气底吹熔炼炉既可直接处理各种品位的硫化铅精矿,
又可同时处理各种二次铅原料。实际生产中,铅原料含铅品
位波动在40 ~65%之间,均能直接入炉进行熔炼。 (8)自动化水平高 氧气底吹熔炼过程采用DCS 控制系统,实现了配料、制粒、
先。
中国有色工程设计研究总院
谢谢大家
中国有色工程设计研究总院
中国有色工程设计研究总院
结处理,现由于经济原因已关闭;云冶曲靖铅厂在建,但只用
- 1、下载文档前请自行甄别文档内容的完整性,平台不提供额外的编辑、内容补充、找答案等附加服务。
- 2、"仅部分预览"的文档,不可在线预览部分如存在完整性等问题,可反馈申请退款(可完整预览的文档不适用该条件!)。
- 3、如文档侵犯您的权益,请联系客服反馈,我们会尽快为您处理(人工客服工作时间:9:00-18:30)。
氧气底吹熔炼—鼓风炉还原炼铅新技术氧气底吹熔炼—鼓风炉还原炼铅法一、氧气底吹熔炼—鼓风炉法简介氧气底吹熔炼—鼓风炉还原炼铅法工艺流程为:熔剂、铅精矿或二次铅原料及铅烟尘经配料、制粒或混捏后进行氧气底吹熔炼,产出烟气、一次粗铅和铅氧化渣,烟气经余热锅炉回收余热和电收尘器收尘后采用二转二吸工艺制酸,尾气排放,铅烟尘返回配料。
铅氧化渣经铸块后与焦块、熔剂块混合后入鼓风炉进行还原熔炼,产出炉渣、烟气和粗铅,烟气经收尘后放空,铅烟尘返回配料。
工艺主要设备包括可旋转式氧气底吹熔炼炉,多元套管结构氧枪(多通道水冷高温喷镀耐磨底吹氧枪),特殊耐磨材质的氧枪口保护砖,浅层分格富铅渣速冷铸渣机(铅氧化渣铸渣机),带弧型密封罩和垂直模式壁中压防腐余热锅炉,全封闭铅烟尘输送配料等, 新型结构鼓风炉(双排风口大炉腹角高料柱)等。
工艺的核心设备是氧气底吹熔炼炉。
熔炼炉炉型结构为可回转的卧式圆筒形,在炉顶部设有2~3 个加料口,底侧部设有3~6 个氧气喷入口,炉子两端分别设一个虹吸放铅口和铅氧化渣放出口。
炉端上方设有烟气出口。
铅精矿的氧化熔炼是在一个水平回转式熔炼炉中进行的。
铅精矿、铅烟尘、熔剂及少量粉煤经计量、配料、圆盘制粒后, 由炉子上方的气封加料口加入炉内, 工业纯氧从炉底的氧枪喷入熔池。
氧气进入熔池后, 首先和铅液接触反应, 生成氧化铅(PbO ) , 其中一部分氧化铅在激烈的搅动状态下, 和位于熔池上部的硫化铅(PbS) 进行反应熔炼, 产出一次粗铅并放出SO 2。
反应生成的一次粗铅和铅氧化渣沉淀分离后, 粗铅虹吸或直接放出,铅氧化渣则由铸锭机铸块后,送往鼓风炉工段还原熔炼, 产出二次粗铅。
出炉SO 2 烟气采用余热锅炉或汽化冷却器回收余热, 经电收尘器收尘, 送硫酸车间处理。
熔炼炉采用微负压操作, 整个烟气排放系统处于密封状态, 从而有效防止了烟气外逸。
同时, 由于混合物料是以润湿、粒状形式输送入炉的, 加上在出铅、出渣口采取有效的集烟通风措施, 从而避免了铅烟尘的飞扬。
经实地检测, 熔炼车间岗位含铅尘低于0. 1m g/Nm 3, 完全达到了国家劳动卫生标准。
由于在熔炼炉内只进行氧化作业, 不进行还原作业, 工艺过程控制大为简单。
氧气底吹熔炼一次成铅率与铅精矿品位有关, 品位越高, 一次粗铅产出率越高。
为适应下一步鼓风炉还原要求, 铅氧化渣含铅应控制在40% 左右, 略低于烧结块含铅率, 相应地,一次粗铅产出率一般为35%~40% , 粗铅含S< 0. 2%。
和烧结块相比, 铅氧化渣孔隙率较低, 同时, 由于是熟料, 其熔化速度较烧结块要快些, 从而增加了鼓风炉还原工艺的难度。
但是, 经过半工业试验证明, 采用鼓风炉处理铅氧化渣在工艺上是可行的, 鼓风炉渣含Pb 可控制在4% 以内。
通过炉型改进, 渣型调整、适当控制单位时间物料处理量等措施, 渣含Pb 可望进一步降低。
另外, 尽管现有指标较传统工艺渣含Pb1. 5%~2% 的指标稍高, 但由于新工艺中鼓风炉渣量仅为传统工艺的50%~60% , 因而,鼓风炉工段铅的损失基本不增加。
在技改过程中, 利用原有的鼓风炉作适当改进即可, 这样, 可以节省大笔投资。
新工艺的一个重要组成部分是氧气站。
目前, 国内工业纯氧的制备技术有两种, 一种为传统的深冷法, 一种为变压吸附法。
前者生产能力大, 氧气纯度高, 但成本高, 氧气单位电耗一般为0. 6~0. 7kw h/Nm 3; 后者投资省, 成本低, 氧气单位电耗低于0. 45kw h/Nm 3。
目前, 国内1500m 3/h 的吸附制氧机组已研制成功, 其氧气纯度达93% 以上。
对于1 万t/a 规模的炼铅厂, 氧气需要量一般为700~800m 3/h。
采用变压吸附法制氧完全能满足中型炼铅厂技改需要, 该技术为首选方案。
氧气底吹熔炼工艺取代传统烧结工艺后, 不仅解决了SO 2 烟气及铅烟尘的污染问题, 还有如下效益:(1) 由于熔炼炉出炉烟气SO 2 浓度在12% 以上, 对制酸非常有利, 元素硫总回收率可达95%。
( 2) 熔炼炉出炉烟气温度高达1000~1100℃, 可利用余热锅炉或汽化冷却器回收余热。
(3) 采用氧气底吹熔炼, 原料中Pb、S 含量的上限不受限制, 不需要添加返料,简化了流程, 且取消了破碎设备, 从而降低了工艺电耗。
(4) 由于减少了工艺环节, 提高了Pb 及其它有价金属的回收率, 氧气底吹熔炼车间Pb 的机械损失< 0. 5%。
经测算, 采用新的工艺改造传统工艺后,粗铅单位产品综合能耗可降至400kgbm/t·粗铅以下, 达到国家规定的一级能耗标准。
熔炼过程中主要化学反应有:熔池底部铅液和喷入氧气之间的氧化反应,炉料中PbS 和熔渣中PbO 之间的反应熔炼;炉料中熔剂和熔渣中PbO 之间的造渣反应。
氧气底吹熔炼的特点是:Pb 作为O2 的载体,在铅液层中可除去一次铅中的杂质,有利于提高一次粗铅的品位;在熔渣中可加速PbS 的氧化反应,有利于降低熔炼烟尘率。
水口山工业试验遗留两个关键问题未能解决。
其一是氧枪寿命较短,其二是鼓风炉渣含铅较高。
工厂设计对氧枪和鼓风炉的工艺参数及设备结构进行了重大革新。
氧枪由工业试验的二元结构改为多元结构,氧枪冷却介质由空气改为氮气+ 软化水,并对氧枪材质、加工工艺和操作参数进行了改进,经生产验证,新型氧枪寿命由工业试验的5d ±提高至20~50d ,保证了熔炼炉的稳定操作,提高了作业率,降低了生产成本。
针对铅氧化渣还原熔炼的特殊性,工厂设计改进了鼓风炉结构,调整了鼓风炉渣型和供风操作制度,经生产验证,鼓风炉渣含铅由工业试验的7 %~9 %降至3 %~4 % ,提高了铅冶炼回收率。
水口山工业试验熔炼烟气处理设施简陋,不能满足工业生产要求。
工厂设计针对铅精矿熔池熔炼过程烟尘率较高等特点,设计了带垂直上升段、膜式壁结构的余热锅炉,有效回收了烟气余热,并解决了铅烟尘的粘结和密闭输送问题。
新工艺在国内外炼铅行业中首次设计并成功采用铅氧化渣直线铸渣机,氧气底吹熔炼炉产出的铅氧化渣连续铸渣后直接送入鼓风炉还原化渣连续铸渣后直接送入鼓风炉还原。
二、新工艺实际生产指标项目指标氧气底吹熔炼炉有效作业率/ % > 95氧气底吹熔炼炉工业氧气消耗量/ (m3·t - 1粗铅) 300~350氧气底吹熔炼燃料率/ % 0~210氧气底吹熔炼炉一次粗铅产出率/ % 45~55一次粗铅品位/ % > 9815铅氧化渣含Pb/ % 40~50铅氧化渣含S/ % < 015氧气底吹熔炼烟尘率/ % 12~15氧气底吹熔炼炉出炉烟气SO2 浓度/ % 12~14制酸后尾气含SO2/ (mg·m- 3) < 300鼓风炉床能力/ (t·m - 2·d - 1) 45~55鼓风炉焦率/ % 13~15Pb 回收率/ % > 97S 回收率/ % > 95Au 回收率/ % > 98Ag 回收率/ % > 98鼓风炉渣含Pb/ % 3~4氧枪寿命/ d 20~50余热锅炉蒸气产出量(410MPa) / (t·t - 1粗铅) 015~018三、工艺主要特点(1)环境保护好由于熔炼过程在密闭的熔炼炉中进行,避免了烟气外逸,SO2 烟气经二转二吸制酸后,尾气排放达到了环保要求。
铅精矿或其他铅原料配合制粒后直接入炉,没有烧结返粉作业,生产过程中产出的铅烟尘均密封输送并返回配料,防止了铅烟尘的弥散;同时在虹吸放铅口设通风装置,防止铅蒸气的扩散。
彻底解决了铅冶炼烟气、烟尘污染问题。
河南豫光经环保部门实测,生产岗位含尘量为7mg/ m3 ,其中铅尘含量0103 mg/ m3 , 硫酸尾气SO2 含量< 100mg/ m3。
均远低于国家排放标准。
实际生产比较证明,氧气底吹熔炼炉前噪音较低,岗位操作环境优于氧气顶吹熔炼( ISA 法和Ausmelt 法) 。
(2) 能耗低与传统流程相比,氧气底吹实现了自热熔炼并回收了高温烟气中的余热;熔炼炉已产出一次粗铅,鼓风炉物料处理量大幅减少,焦炭消耗相应节省了30 %~40 %。
与氧气顶吹熔炼( ISA 法和Ausmelt法) 相比,由于采用工业纯氧熔炼,动力消耗较少。
(3)投资省前述两厂的吨铅基建投资为3 000~3 500 元,与国外较先进的炼铅工艺相比,相同生产规模节省投资40 %~60 % ;由于工艺流程短,相同生产规模较传统烧结机—鼓风炉流程投资亦可节省20 % ;新工艺尤其适合烧结—鼓风炉流程的技改:除烧结设施外,其余设施均可通过适当改造加以利用,从而可进一步节省技改费用。
(4) 生产成本低与国外较先进的炼铅工艺相比,投资省,折旧费用低,生产成本低;和传统流程相比,生产过程简单,动力和焦炭消耗量少,生产效率高,人工费用低,同时有价金属和硫回收率高,生产成本相对亦较低,据实际生产测算,和烧结机—鼓风炉流程相比,每吨粗铅生产成本降低约10 %。
(5) 对原料适应性强氧气底吹熔炼炉既可直接处理各种品位的铅精矿,又可同时处理各种二次铅原料。
实际生产中,上述两厂处理的铅原料含铅品位在45 %~65 % ,均能正常作业。
(6) 自动化水平高氧气底吹熔炼过程采用DCS 控制系统,实现了配料、制粒、供氧、熔炼、余热锅炉、锅炉循环水、电收尘、高温风机等全流程、全部设备的集中控制。
(7) 产品质量好氧气底吹熔炼炉产出的一次粗铅品位高,烟气制酸可产出无色透明的一级酸。
4 新工艺应用中的问题讨论(1) 关于氧枪寿命影响氧枪寿命的因素有氧枪结构、材质、制造工艺、操作参数和冷却介质,控制合理的氧气流速对提高氧枪寿命有显著效果。
(2) 关于熔炼烟尘率由于PbS 在高温下有较大挥发性,铅熔池熔炼过程烟尘率较高。
生产中降低烟尘率的关键因素是控制较低的熔炼温度和较高的PbO 活度。
(3) 关于鼓风炉还原氧气底吹熔炼炉产出的铅氧化渣含硫较低,有效防止了由ZnS 造成的炉结的产生。
生产中基本不需要清理炉结。
针对铅氧化渣熔点较低等特点,为降低渣含铅,除需调整渣型和适当提高焦率外,应严格控制较高的料柱和适当的床能力。
氧气底吹熔炼—鼓风炉还原炼铅新工艺除根治了铅冶炼的环境污染外,还具有投资省、节能、生产成本低和对原料适用性强等优点,工艺技术水平达到国际先进。
该工艺及装置的投产成功,为国内外炼铅行业新建和技改起到良好示范作用,具有广阔的推广前景。
主要工艺过程1.电解铅生产所进矿源主要为浮选后的硫化铅精矿,用抓斗吊车进行预配料,再与辅料混合,混合料由梭式布料机给烧结机布料,烧结采用鼓风返烟烧结,烧结机大烟罩较高浓度的二氧化硫烟气收尘后送非定态制酸系统生产硫酸。