Auditingch5-7
KSZ8795 Evaluation Board 用户指南说明书
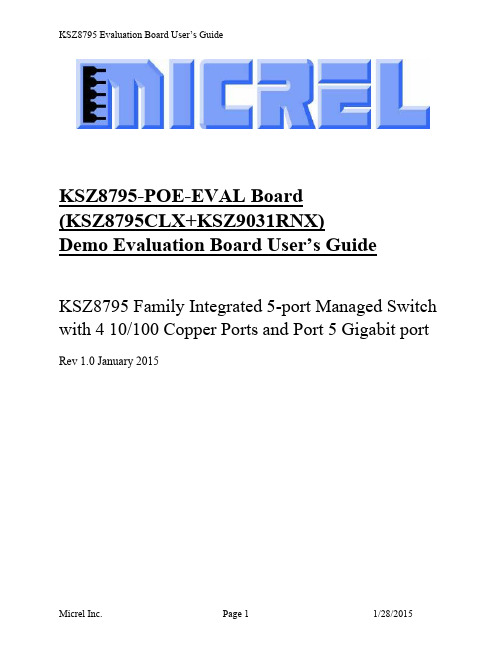
KSZ8795-POE-EVAL Board(KSZ8795CLX+KSZ9031RNX)Demo Evaluation Board User’s GuideKSZ8795 Family Integrated 5-port Managed Switch with 4 10/100 Copper Ports and Port 5 Gigabit port Rev 1.0 January 2015Table of contents1.0 Introduction (4)2.0 Features (4)3.0 Evaluation Kit Contents (4)4.0 Hardware Description (5)4.1 Strap in Mode (6)4.2 Feature Setting Jumpers (7)4.3 SPI Mode (8)4.4 10/100 Ethernet Ports (8)4.4 10/100/1000 Gigabit Ports (8)4.5 LED indicators (9)5.0 Software Tools Description (10)5.1 Introducing Application Software Tools (10)5.2 Window Driver Installation First (10)5.3 Installation Application Software Tools (13)5.4 DOS SPI Tool (15)5.5 Window SPI Software Tool (16)5.6 LinkMD Software Tool (17)6.0 Reference Documents (19)7.0 Bill of Material (19)8.0 Schematics (19)List of Figures and TablesFigure 1 KSZ8795-POE-EVAL Board (5)Figure 2 KSZ8795-POE-EVAL Board Block Diagram (6)Table 1 General Setting Jumpers (7)Table 2 Power Setting Jumpers (7)Table 3 LED Modes (9)Revision History1.0 IntroductionThe KSZ8795 family is Micrel Operations new generation integrated 5-port switch with Gigabit up-link. The KSZ8795CLX is one of KSZ8795 family. KSZ8795CLX contains four MAC/PHYs for four copper ports and one GMAC5 interface with configurable GMII/RGMII/MII/RMII interfaces. The device had been designed with cost sensitive systems in mind but still offers a multitude of new features such as port based security ACL filtering, 802.1az EEE, LinkMD and so on. Also support port and tag based VLAN; QoS priority; SPI and MDC/MDIO interfaces for the registers access. The KSZ8795 family is an excellent choice in broadband gateway applications, integrated broadband router applications, industrial automatic, automotive, etc. fields and as a standalone switch. The KSZ8795-POE-EVAL board is designed to allow the user to experience Gigabit up-link with KSZ9031 Gigabit PHY to Gigabit port of any processor board directly, and can provide PoE PSE power to other four ports. Other rich feature set can be evaluated on this board. The evaluation board is highly configurable and easy to use.2.0 Features∙Micrel KSZ8795 Integrated 5-port 10/100 Managed Ethernet Switch∙ 4 RJ-45 Jacks for 10/100Base-T/TX Ethernet LAN with Corresponding Isolation Magnetics. ∙Auto MDI/MDIX on All Ports.∙Port 5 SW5-RGMII hook-up with a KSZ9031RNX GPHY and provide a Gigabit port.∙Easily set to different VDDIO of 3.3V, 2.5V and 1.8V by jumpers.∙ 1 USB Port Interface Configurable to Emulate an SPI Interface for all registers access by using Window GUI and DOS based software tools.∙ 2 LEDs per Port with 5 LED sets to indicate the Status and Activity for 4 fast Ethernet ports and1 Gigabit port.∙The board powered can be used by a 12V DC power supply.3.0 Evaluation Kit ContentsThe KSZ8795-POE-EVAL Evaluation kit includes the following:∙KSZ8795-POE-EVAL Evaluation Board Rev. 1.x∙KSZ8795-POE-EVAL Ev aluation Board User’s Guide Rev 1.x∙Micrel SPI Configuration Software tools∙KSZ8795-POE-EVAL Evaluation Board Schematics and BOM∙KSZ8795-POE-EVAL PCB file, Gerber file and IBIS model∙The software, reference schematics and other design information will be found in the Design Kit (Design Package) of the KSZ8795 Ethernet switch products on Micrel website.(Contact your Micrel FAE for the latest schematic).∙One 12V DC power supply.∙The USB cable is not included.4.0 Hardware DescriptionThe KSZ8795-POE-EVAL evaluation board is in a compact form factor and can sit on a bench near a computer with USB connector. There are two options for configuration: strap in mode; SPI mode and Strap-in mode that is easily done with on board jumper options. SPI mode is accomplished through a built in USB port interface. You can configure the KSZ8795 device on board by the USB port. Using Micrel SPI software and your PC, you can access the KSZ8795’s full feature set registers by the USB to SPI interface. The board also features RGMII to hook up a KSZ9031RNX as a Gigabit uplink for Gigabit port 5.The KSZ8795-POE-EVAL evaluation board is easy to use. There are programmable LED indicators for link and activity on all ports and a power LED. A manual reset button allows the user to reset the board without removing the power plug. A standard 12VDC power supply can be used by the power jack so that the user can supply power from any 110-240 Volt AC wall or bench socket.Figure 1 KSZ8795-POE-EVAL BoardFigure 2 KSZ8795-POE-EVAL Board Block Diagram4.1 Strap in ModeStrap in configuration mode is the quickest and easiest way to get started. In the default mode, the KSZ8795 acts as a stand-alone 4 port switch and one RGMII up-link. The user has to simply set the board’s configuration jumpers to the desired settings and apply power to the board. The user can also change jumper settings while power is applied to the board and press the convenient manual reset button for the new settings to take effect. Note that even if there is no external strap in values are set, internal pull up and pull down resistors will set the KSZ8795 default configuration. Section 4.1.1 covers each jumper on the board and describes its function.The KSZ8795 will start automatically after power up or reset.4.2 Feature Setting JumpersThe evaluation board provides jumpers to allow the user to easily set strap in configurations for the KSZ8795. Tables below describe the jumpers and their functions in the open or closed state.Table 1 General Setting JumpersTable 2 Power Setting Jumpers4.3 SPI ModeFrom SPI interface to the KSZ8795, use a USB to SPI converter that allows accessing all of the KSZ8795 features and registers. The user can easily access the SPI interface using a computer connected to the evaluation board’s USB port interface. Micrel provides a Windows GUI based program for the user to evaluate the KSZ8795’s full feature set. KSZ8795’s SP I interface will be able to access all static MAC table, the VLAN table, dynamic MAC address table, the MIB counters and all enhanced features.To prepare the KSZ8795CLXD-EVAL board for SPI mode configuration follow these steps:1. Copy the Micrel provided SPI interface software on your computer.2. KSZ8795-POE-EVAL board is fixed at SPI slave mode.3.Connect the computer’s USB port to the KSZ8795CLXD-EVAL board with a USB port cable.4.Connect the 12V DC power supply to J7 of the KSZ8795-POE-EVAL board.5.Open the Windows and navigate to the directory where the Window SPI file is stored. Click itsicon to invoke the software.6.Program the desired settings using the Micrel SPI interface software. See the softwareoperation description section for details.4.4 10/100 Ethernet PortsThere are five 10/100 Ethernet ports on the KSZ8795-POE-EVAL board. The ports J1, J2, J3 and J4 are the standard RJ45 connectors and using CAT-5 cables. Each port can be used as either an uplink or downlink. All ports support Auto-MDI/MDIX, so there is no need for cross over cables. J1 = RJ45 connector for port 1J2 = RJ45 connector for port 2J3 = RJ45 connector for port 3J4 = RJ45 connector for port 4JM1, JM2, JM3, JM4 and JS1, JS2, JS3, JS4 special connectors for Automotive used only.4.4 10/100/1000 Gigabit PortsThere is one KSZ9031RNX with 10/100/1000 Ethernet ports on the KSZ8795-POE-EVAL board. The ports RJ1 is the standard RJ45 connectors for port 5 and can connect to one Gigabit port of a processor platform by using CAT-5 cables. The port supports Auto-MDI/MDIX, so there is no need for the cross over cables.RJ1 = RJ45 connector for port 54.5 LED indicatorsEthernet Port LEDsThere are four columns of LED indicators on the board, one column for each of the four ports. The LED indicators are programmable to two different modes. You can program the LED mode through Register 11 bits [5:4]. The mode definitions are shown in Table below. There are two LEDs per port. The naming convention is “LEDx_y”, where “x” is the port number, and “y” is the number of the LED for that port.Table 3 LED ModesLED1_y are assigned to port 1LED2_y are assigned to port 2LED3_y are assigned to port 3LED4_y are assigned to port 4Gigabit Port LEDThe board also has a Gigabit port LED D3 to indicate the link-up speed for port 5.Green Color: 1G LinkRed Color: 100M LinkOrange Color: 10M LinkPower LEDThe board also has a power LED D7 for the 3.3V power supply. D7 LED indicates Power on and off.5.0 Software Tools Description5.1 Introducing Application Software ToolsThe Design Kit provides some software tools to support SPI access for all registers andMDC/MDIO access for MIIM registers. The installation file is located folders in the software tool directory within subdirectory of Window SPI_MDIO_Tools, this file name is MicrelSwitchPhyTool_x.xx.msi.5.2 Window Driver Installation FirstBefore use the Window based application software tool, the support drivers need to be installed to PC/Laptop first and this installation is just one times only. When connect one standard USB cable with type A and type B connectors between the evaluation board and PC computer first time, the Found New Hardware Wizard window will pop-up and then follow the instructions step by step as below.. Choose ‘No, not this time’ radio button and click the ‘Next’ button.Choose the ‘Install from a list or specific location (Advanced)’ radio button and click the ‘Next’ button.Click the ‘Include this location in the search’ check box, and use ‘Browse’ button to select the‘C:\MicrelEthernetChipConfig\D2XXDriver\CDM 2.02.04 WHQL Certified’ directory and click the ‘Next’ button. The window will install the drivers from this location.Click ‘Finish’ button. The Window will install another driver called ‘USB Serial Converter B’. After the drivers installed, Window Device Manager will show ‘USB Serial Converter A’ and ‘USB Serial Converter B’ as below figure. That means the installation successful.5.3 Installation Application Software ToolsIn the Design Kit, the installation file is located folders in the software tool directory within subdirectory of Window SPI_MDIO_Tools, this file name is MicrelSwitchPhyTool_x.xx.msi. Double click this file name, an installation Window will pop-up and then follow the instructions step by step as below.In this pop-up Window, this application software tools can be assigned to default Micrel directory in above window shown or is assigned to a specified folder what you want. Click ‘Next’ button, next Window will pop-up as below.Click ‘Next’ button to start the installation.Click ‘Close’ button to finish the installation. All application software tools are installed into the default Micrel directory or assigned directory in installation as below.5.4 DOS SPI ToolThis is a simple and powerful tool to access all register. The tool located in the default or assigned folder in the installation. There is an USBSPI.exe file which can be executed directly by clicking its icon. Before run the software tool, the SPI jumper setting should follows Table 5 in 4.3 SPI mode section and USB cable is plugged in both KSZ8795-POE-EVAL board and PC/Laptop. After click its icon, a DOS Window will pop up as follow:T ype a ‘help’ and press Enter, all commands will display as follows,For Read or Write registers, reg is the offset address of the register, value is Hex number.The ‘run file’ command can execute multiple commands by a script file, the script file is a .txt file which can be created by any edit tools.run xxxx.txt //will run the .txt script file.5.5 Window SPI Software ToolThis is a powerful tool to access all register. The tool located in the default or assigned folder in the installation. There is a MicrelSwitchConfigApp.exe file which can be executed directly by clicking its icon.Before run the software tool, the SPI jumper setting should follows Table 5 in 4.3 SPI mode section and USB cable should be plugged in both KSZ8795CLXD-EVAL board and PC/Laptop. After click its icon, a GUI Window will pop up as follow:The default is SPI interface to do switch configuration. From the device selection window to select any devices then press ‘Continue’ button or click ‘Continue’ button directly, the software tool can detect devices automatically. A control Window will be pop up as follow.All register can be read/ written in the window.The control Window includes all application registers, static MAC table, VLAN table, dynamic table and MIB counters that are supported by SPI. The software can save and open the configuration file as a back-up.5.6 LinkMD Software ToolThis is a simple and powerful tool to test Micrel LinkMD feature. The tool is in the installation folder. There is a LinkMDUSB.exe file which can be executed directly by clicking its icon.After click the icon of this executed file, a GUI Window will pop up as follow:Select one part and clik ‘Next’ button, using SPI interface and clik ‘Next’ button again, pop up a test windown as below:An example for CAT-5 cable diagnostic with open on port 1, just clic k ‘TEST’ button, a test result shows as below.The test result shows both MDIX mode for pair 3-6 and MDI mode for 1-2 pair. The detail LinkMD diagnostic testing configuration is described in the datasheet.6.0 Reference DocumentsKSZ8795CLX Data Sheets (Contact Micrel for Latest Datasheet), KSZ8795 Design Package includes all design information as a Design kit. The Design Kit will be found on Micrel website (Contact Micrel for the updates).7.0 Bill of MaterialPlease see the detail BOMs in the BOM folder of the hardware design package for theKSZ8795-POE-EVAL Boards.8.0 SchematicsPlease see the schematics of the evaluation board and reference design in the schematicsfolder of the hardware design package (Design kit) for the KSZ8795-POE-EVAL Board. Magnetics Vendors:See the datasheets for the recommendation.MICREL, INC. 1849 FORTUNE DRIVE SAN JOSE, CA 95131 USA TEL +1 (408) 944-0800 FAX +1 (408) 474-1000 WEB http:/ The information furnished by Micrel in this data sheet is believed to be accurate and reliable. However, no responsibility is assumed by Micrel for its use. Micrel reserves the right to change circuitry and specifications at any time without notification to thecustomer.Micrel Products are not designed or authorized for use as components in life support appliances, devices or systems where malfunction of a product can reasonably be expected to result in personal injury. Life support devices or systems are devices or systems that (a) are intended for surgical implant into the body or (b) support or sustain life, and whose failure to perform can be reasonably expected to result in a signi ficant injury to the user. A Purchaser’s use or sale of Micrel Products for use in life support appliances, devices or systems is a Purchaser’s own risk and Purchaser agrees to fully indemnify Micrel for any damagesresulting from such use or sale.© 2015 Micrel, Incorporated.。
Soundcheck 7.0 操作指南

Soundcheck 7.01.安装原理系统硬件基础系统软件基础测试扬声器,耳机需要的配置:1. 声卡2. 功率放大器3. 标咪(扬声器)或者仿真耳(耳机)4.标咪或者仿真耳前置供电电源5.电脑2. 测试简图:耳机测试简图:扬声器测试简图:阻抗测试简图:3. 电脑配置要求SoundCheck将利用您的电脑来处理所有的计算以及信号处理功能,所以电脑的配置运行速度将影响SoundCheck的运行速度。
处理信号越长运行速度将越慢。
对电脑硬件的基本要求如下:Windows®XP or Windows®2000. (同样可以运行在Microsoft®Windows®98,)Windows 64 Bit OS is currently not supported. 64 bit device drivers are not available forrequired hardware. 暂时不支持Windows Vista.注:脚踏开关不能使用在Windows NT.Pentium®4, 1.6 MHz processor minimum or equivalent (Celeron处理器不建议使用).1 GB of RAM (2 GB or more recommended for large WAV files or high resolutionmeasurements below 50Hz).300MB of free hard-disk space required for complete software installation.4. 软件安装软件重新安装前,请注意备份之前的测试文件,如下。
SequencesStepsLast session.txt(Stores the preference that were last used inSoundCheck.)此时可以使用右图所示Flie/Import Seq Export Seq导入到处qc程序1 声卡3 扬声器2 功放仿真耳5. 注意事项:1.请不要直接将两个输出通道对接2. 外接线材请做好测试,没有短路等不良问题后,方可接入声卡接口3. 电脑开机状态,使用状态中,声卡接口处的插头不要做硬插拔4. 硬件系统的自检功能:只需要在搭建好后自检一次即可,无特殊变动,无需自检;5. 更换外设,如功放,仿真耳等,都需要重新校准功放和仿真耳6. 扬声器测试qc程序简介一个完整的qc 程序包括以下:1.硬件Hardware 设置2. 校准设置3. 信号发生器参数设置4. 信号发生与记录5. 信号的接受处理分析6. 对分析结果的后处理(数据)7. Limits 的编写8.结果显示界面的设置9.对话框弹出设置10. 序列号计数方法的设置11.数据保存设置QC 的编写信道的选择要完全符合以上硬件的连接。
关于MAX6675的说明书
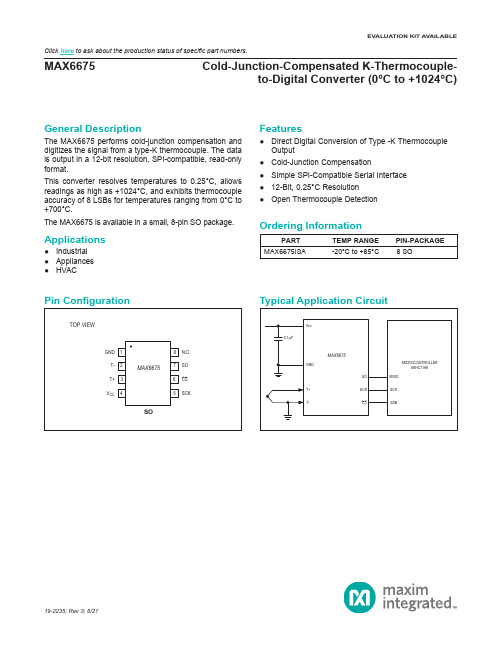
General DescriptionThe MAX6675 performs cold-junction compensation and digitizes the signal from a type-K thermocouple. The data is output in a 12-bit resolution, SPI-compatible, read-only format.This converter resolves temperatures to 0.25°C, allows readings as high as +1024°C, and exhibits thermocouple accuracy of 8 LSBs for temperatures ranging from 0°C to +700°C.The MAX6675 is available in a small, 8-pin SO package.Applications●Industrial ●Appliances ●HVACFeatures●Direct Digital Conversion of Type -K ThermocoupleOutput ●Cold-Junction Compensation●Simple SPI-Compatible Serial Interface ●12-Bit, 0.25°C Resolution ●Open Thermocouple DetectionPART TEMP RANGE PIN-PACKAGE MAX6675ISA-20°C to +85°C8 SOMAX6675Cold-Junction-Compensated K-Thermocouple-to-Digital Converter (0°C to +1024°C)19-2235; Rev 3; 6/21Ordering InformationEVALUATION KIT AVAILABLEClick here to ask about the production status of specific part numbers.Supply Voltage (V CC to GND) ............................... -0.3V to +6V SO, SCK, CS , T-, T+ to GND .....................-0.3V to V CC + 0.3V SO Current ....................................................................... 50mA ESD Protection (Human Body Model) .......................... ±2000V Continuous Power Dissipation (T A = +70°C)8-Pin SO (derate 5.88mW/°C above +70°C) ............. 471mW Operating Temperature Range ..........................-20°C to +85°CStorage Temperature Range ...........................-65°C to +150°C Junction Temperature .................................................... +150°C SO PackageVapor Phase (60s) . .....................................................+215°C Infrared (15s) ..............................................................+220°C Lead Temperature (soldering, 10s) ............................... +300°C(V CC = +3.0V to +5.5V, T A = -20°C to +85°C, unless otherwise noted. Typical values specified at +25°C.) (Note 1)PARAMETERSYMBOLCONDITIONSMINTYP MAX UNITSTemperature ErrorT THERMOCOUPLE = +700°C,T A = +25°C (Note 2)V CC = +3.3V -5+5LSBV CC = +5V -6+6T THERMOCOUPLE = 0°C to +700°C, T A = +25°C (Note 2)V CC = +3.3V -8+8V CC = +5V -9+9T THERMOCOUPLE = +700°Cto +1000°C, T A = +25°C (Note 2)V CC = +3.3V -17+17V CC = +5V-19+19Thermocouple Conversion Constant10.25µV/LSB Cold-JunctionCompensation Error T A = -20°C t o +85°C (Note 2)V CC = +3.3V -3.0+3.0°C V CC= +5V-3.0+3.0Resolution0.25°C Thermocouple Input Impedance 60k W Supply Voltage V CC 3.05.5V Supply CurrentI CC0.7 1.5mA Power-On Reset Threshold V CC rising12 2.5V Power-On Reset Hysteresis 50mV Conversion Time (Note 2)0.170.22sSERIAL INTERFACE Input Low Voltage V IL 0.3 x V CCV Input High Voltage V IH 0.7 x V CCV Input Leakage Current I LEAK V IN = GND or V CC±5µA Input CapacitanceC IN5pFto-Digital Converter (0°C to +1024°C)Electrical CharacteristicsStresses beyond those listed under “Absolute Maximum Ratings” may cause permanent damage to the device. These are stress ratings only, and functional operation of the device at these or any other conditions beyond those indicated in the operational sections of the specifications is not implied. Exposure to absolute maximum rating conditions for extended periods may affect device reliability.Absolute Maximum RatingsNote 1: All specifications are 100% tested at T A = +25°C. Specification limits over temperature (T A = T MIN to T MAX ) are guaranteedby design and characterization, not production tested.Note 2: Guaranteed by design. Not production tested.(V CC = +3.3V, T A = +25°C, unless otherwise noted.)(V CC = +3.0V to +5.5V, T A = -20°C to +85°C, unless otherwise noted. Typical values specified at +25°C.) (Note 1)PARAMETERSYMBOL CONDITIONSMIN TYPMAXUNITS Output High Voltage V OH I SOURCE = 1.6mA V CC - 0.4V Output Low Voltage V OLI SINK = 1.6mA0.4VTIMINGSerial Clock Frequency f SCL 4.3MHz SCK Pulse High Width t CH 100ns SCK Pulse Low Width t C L 100ns CSB Fall to SCK Rise t CSS C L = 10pF 100ns CSB Fall to Output Enable t DV C L = 10pF 100ns CSB Rise to Output Disable t TR C L = 10pF 100ns SCK Fall to Output Data Validt DOC L = 10pF100ns-50510-103050OUTPUT CODE ERROR vs. VOLTAGE DIFFERENTIALM A X 6675 t o c 02VOLTAGE DIFFERENTIAL (mV)O U T P U T C O D E E R R O R (L S B )1020401086420451530607590OUTPUT CODE ERROR vs. AMBIENT TEMPERATUREM A X 6675 t o c 01TEMPERATURE (°C)O U T P U T C O D E E R R O R (L S B )to-Digital Converter (0°C to +1024°C)Typical Operating CharacteristicsElectrical Characteristics (continued)Detailed DescriptionThe MAX6675 is a sophisticated thermocouple-to-digi- tal converter with a built-in 12-bit analog-to-digital con-verter (ADC). The MAX6675 also contains cold-junction compensation sensing and correction, a digital con- troller, an SPI-compatible interface, and associated control logic.The MAX6675 is designed to work in conjunction with an external microcontroller (µC) or other intelligence in ther-mostatic, process-control, or monitoring applications. Temperature ConversionThe MAX6675 includes signal-conditioning hardware to convert the thermocouple’s signal into a voltage compat-ible with the input channels of the ADC. The T+and T- inputs connect to internal circuitry that reduces the intro- duction of noise errors from the thermocouple wires. Before converting the thermoelectric voltages into equivalent temperature values, it is necessary to com-pensate for the difference between the thermocouple cold-junction side (MAX6675 ambient temperature) and a 0°C virtual reference. For a type-K thermocouple, the voltage changes by 41µV/°C, which approximates the thermocouple characteristic with the following linear equation:V OUT = (41µV / °C) x (T R - T AMB)Where:V OUT is the thermocouple output voltage (µV).T R is the temperature of the remote thermocouple junc-tion (°C).T AMB is the ambient temperature (°C).Cold-Junction CompensationThe function of the thermocouple is to sense a differ- ence in temperature between two ends of the thermo- couple wires. The thermocouple’s hot junction can be read from 0°C to +1023.75°C. The cold end (ambi-ent temperature of the board on which the MAX6675 is mounted) can only range from -20°C to +85°C. While the temperature at the cold end fluctuates, the MAX6675 continues to accurately sense the tempera- ture difference at the opposite end.The MAX6675 senses and corrects for the changes in the ambient temperature with cold-junction compen-sation. The device converts the ambient temperature reading into a voltage using a temperature-sensing diode. To make the actual thermocouple temperature measurement, the MAX6675 measures the voltage from the thermocouple’s output and from the sensing diode. The device’s internal circuitry passes the diode’s volt- age (sensing ambient temperature) and thermocouple voltage (sensing remote temperature minus ambient temperature) to the conversion function stored in the ADC to calculate the thermocouple’s hot-junction tem-perature.Optimal performance from the MAX6675 is achieved when the thermocouple cold junction and the MAX6675 are at the same temperature. Avoid placing heat-gen-erating devices or components near the MAX6675 because this may produce cold-junction-related errors. DigitizationThe ADC adds the cold-junction diode measurement with the amplified thermocouple voltage and reads out the 12-bit result onto the SO pin. A sequence of all zeros means the thermocouple reading is 0°C. A sequence of all ones means the thermocouple reading is +1023.75°C.PIN NAME FUNCTION1GND Ground2T-Alumel Lead of Type-K Thermocouple.Should be connected to ground externally. 3T+Chromel Lead of Type-K Thermocouple4V CC Positive Supply. Bypass with a 0.1µFcapacitor to GND.5SCK Serial Clock Input6CS Chip Select. Set CS low to enable the serialinterface.7SO Serial Data Output8N.C.No Connection to-Digital Converter (0°C to +1024°C)Pin DescriptionApplications InformationSerial InterfaceThe T ypical Application Circuit shows the MAX6675 interfaced with a microcontroller. In this example, the MAX6675 processes the reading from the thermocou- ple and transmits the data through a serial interface. Force CS low and apply a clock signal at SCK to read the results at SO. Forcing CS low immediately stops any conversion process. Initiate a new conversion process by forcing CS high.Force CS low to output the first bit on the SO pin. A complete serial interface read requires 16 clock cycles. Read the 16 output bits on the falling edge of the clock. The first bit, D15, is a dummy sign bit and is always zero. Bits D14–D3 contain the converted temperature in the order of MSB to LSB. Bit D2 is normally low and goes high when the thermocouple input is open. D1 is low to provide a device ID for the MAX6675 and bit D0 is three-state.Figure 1a is the serial interface protocol and Figure 1b shows the serial interface timing. Figure 2 is the SO out-put.Open ThermocoupleBit D2 is normally low and goes high if the thermocou- ple input is open. In order to allow the operation of the open thermocouple detector, T- must be grounded. Make the ground connection as close to the GND pin as possible.Noise ConsiderationsThe accuracy of the MAX6675 is susceptible to power- supply coupled noise. The effects of power-supply noise can be minimized by placing a 0.1µF ceramic bypass capacitor close to the supply pin of the device.Thermal ConsiderationsSelf-heating degrades the temperature measurement accuracy of the MAX6675 in some applications. The magnitude of the temperature errors depends on the thermal conductivity of the MAX6675 package, the mounting technique, and the effects of airflow. Use a large ground plane to improve the temperature mea- surement accuracy of the MAX6675.The accuracy of a thermocouple system can also be improved by following these precautions:●Use the largest wire possible that does not shuntheat away from the measurement area.●If small wire is required, use it only in the region ofthe measurement and use extension wire for theregion with no temperature gradient.●Avoid mechanical stress and vibration, which couldstrain the wires.●When using long thermocouple wires, use a twisted-pair extension wire.●Avoid steep temperature gradients.●Try to use the thermocouple wire well within its tem-perature rating.●Use the proper sheathing material in hostile environ-ments to protect the thermocouple wire.●Use extension wire only at low temperatures andonly in regions of small gradients.●Keep an event log and a continuous record of ther-mocouple resistance.Reducing Effects of Pick-Up NoiseThe input amplifier (A1) is a low-noise amplifier designed to enable high-precision input sensing. Keep the thermocouple and connecting wires away from elec-trical noise sources.to-Digital Converter (0°C to +1024°C)Figure 2. SO OutputFigure 1b. Serial Interface TimingFigure 1a. Serial Interface ProtocolBIT DUMMY SIGN BIT12-BITTEMPERATURE READING THERMOCOUPLEINPUTDEVICE IDSTATE Bit15141312111098765432100MSBLSBThree-stateCSSCKSOD15D14D13D12D11D10D9D8D7D6D5D4D3D2D1D0to-Digital Converter (0°C to +1024°C)PACKAGE TYPEPACKAGE CODE OUTLINE ND PATTERN NO.8 SOS8+221-004190-0096to-Digital Converter (0°C to +1024°C)Package InformationFor the latest package outline information and land patterns (footprints), go to /packages . Note that a “+”, “#”, or “-” in the package code indicates RoHS status only. Package drawings may show a different suffix character, but the drawing pertains to the package regardless of RoHS status.Chip InformationTRANSISTOR COUNT: 6720PROCESS: BiCMOSREVISION NUMBERREVISION DATE DESCRIPTIONPAGES CHANGED24/14Removed automotive reference136/21Updated equation in Temperature Compensation section.4Maxim Integrated cannot assume responsibility for use of any circuitry other than circuitry entirely embodied in a Maxim Integrated product. No circuit patent licenses are implied. Maxim Integrated reserves the right to change the circuitry and specifications without notice at any time. The parametric values (min and max limits) shown in the Electrical Characteristics table are guaranteed. Other parametric values quoted in this data sheet are provided for guidance.to-Digital Converter (0°C to +1024°C)Revision HistoryFor pricing, delivery, and ordering information, please visit Maxim Integrated’s online storefront at https:///en/storefront/storefront.html.。
LANTEK 6 7G 配件说明书
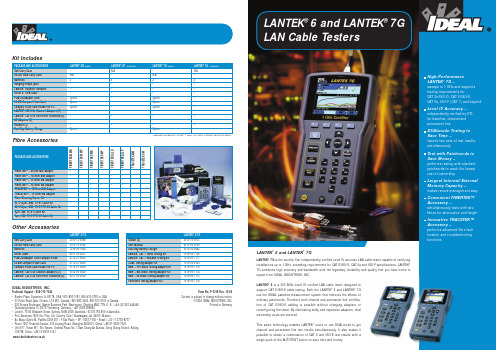
Other AccessoriesFibre AccessoriesKit Includes*Upgrades available for LANTEK 7 users, call IDEAL Customer Service for details.High-Performance LANTEK sweeps to 1 GHz and supports testing requirements for CAT 5e/ISO-D, CAT 6/ISO-E,CAT 6a, ISO-F (CAT 7) and beyond Level IV Accuracy – independently verified by ETL for baseline, channel and permanent linkDUALmode Testing to Save Time –reports two sets of test results simultaneouslyTest with Patchcords to Save Money –performs testing with standard patchcords to reach the lowest cost of ownershipLargest Internal/External Memory Capacity –makes record management easy Convenient FIBERTEK™ Accessory –simultaneously tests with two fibres for attenuation and length Innovative TRACETEK™ Accessory –performs advanced fibre fault location and troubleshooting functionsLANTEK ® 6 and LANTEK ® 7G LAN Cable Testersis a 350 MHz Level III verified LAN cable tester designed to 6 and LANTEK ®7G use the IDEAL patented measurement system that removes the effects of ordinary patchcords. Therefore both channel and permanent link certifica-tion of CAT 6/ISO-E cabling is possible without changing adapters or reconfiguring the tester. By eliminating bulky and expensive adapters, total users to use DUALmode to get channel and permanent link test results simultaneously. It also makes it possible to obtain a combination of CAT 6 and ISO-E test results with a single push of the AUTOTEST button to save time and money.IDEAL INDUSTRIES, INC.Technical Support / 858-715-7044•Becker Place, Sycamore, IL 60178, USA / 815-895-5181, 800-435-0705 in USA•33 Fuller Road, Ajax, Ontario, L1S 2E1, Canada / 905-683-3400, 800-527-9105 in Canada•225 Europa Boulevard, Gemini Business Park, Warrington, Cheshire WA5 7TN, U. K. / +44-(0)1925 444446•Gutenbergstrasse 10, 85737 Ismaning, Germany / +49-(0)89 996860•Level 6, 75-85 Elizabeth Street, Sydney, NSW 2000, Australia / 61300 765 800 in Australia •Prol. Americas 1600 4to. Piso, Col. Country Club / Guadalajara, Jal. 44610, Mexico•Av. Major Sylvio M. Padilha 5200-201 / F São Paulo – SP / 05677-000 – Brazil / +55-11-3759-8777 • Room 1401 Financial Square, 333 Jiujiang Road, Shanghai 2000001, China / +86-21-6360-7045•Unit 911, Tower W1, The Towers, Oriental Plaza, No. 1 East Chang An Avenue, Dong Cheng District, Beijing, 100738, China / +86-10-8518-3141Form No. P-2218 Rev. 10/04Content is subject to change without notice.©2004 IDEAL INDUSTRIES, INC.Printed in GermanyWhether you are just getting into the business or a seasoned veteran, IDEAL has a LAN cable tester for you. LANTEK ®6 and LANTEK®7G are the most advanced testers in the industry.The Only Tester in the World to Support DUALmode Testing to Save Time and Labour Costs.Save time and money by simultaneously conducting a combination of two tests with LANTEK ®6/7G.For example, you can select a combination of channel/permanent link or CAT 5e/6 or CAT 6/ISO-E testing and get both test results in virtually the same amount of time as a single test.Unique Adapter Scheme Reduces Cost of OwnershipSpecificationsLANTEK ®cable testers utilize an advanced link adapter method to reduce cost of ownership. Both testers come with universal link adapters that are used for basic, channel, and permanent link testing. These channel adapters fit into the case of the unit and are locked in place. This creates a stable and repeatable testing platform while eliminating bulky adapters that extend beyond the end of the unit. Simply plug in the appropriate reference patchcord to the channel adapter, to perform permanent link testing.LANTEK ®Reporter SoftwareLANTEK ®Reporter Software allows installers to upload test results and print reports to meet customer reporting requirements. The Reporter can upload stored tests from LANTEK ®’s internal memory or compact flash card.The software is designed to produce three different kinds of reports based on the required level of detail:Single Line Report – one line per testBrief Report –a summary of test results with graphical reportDetailed Report –complete test results with graphs for all tests and cable pairsIn addition to copper cable testing, LANTEK ®’s flexible adapter bay allows a full range of plug-and-test capabilities: FIBERTEK™, TRACETEK™, Coax,110/66/BIX Blocks and Patchcord Testing Kits.FIBERTEK™ Accessory – Attenuation/Length MeasurementFIBERTEK™ supports testing of attenuation and length simultaneously over two fibres. The technician can use the talkset to communicate over the fibre link under test. FIBERTEK™ is available in both multimode (850 nm VCSEL & 1300 nm Fabry Perot Laser) and singlemode (1310 nm and 1550 nm Fabry Perot Laser) to support Gigabit Ethernet testing.TRACETEK™ Accessory – Fibre Distance to Fault TroubleshootingTRACETEK™ is an innovative OTDR-like troubleshooting tool. It is the first fibre accessory to enable a copper tester to trace a fibre run using back reflections to measure the distance to poor quality terminations and cable breaks.TRACETEK™ can save installers money and time by pinpointing the location of the fibre break without an expensive OTDR.Patchcord/Coax/110/66/BIX Block Testing KitsWith the flexible adapter bay design, installers can purchase additional testing kits to support all their testing needs. To support testing of legacy networks,the 110/66/BIX Block adapters are designed to adapt LANTEK ®to test these systems easily. The Coax Testing Kit enables LANTEK ®to test coax runs for security, data backbone, or CATV applications. Finally, installers can use the Patchcord Testing Kit to evaluate the quality of patchcords before deployment.。
NFPA 72和CAN ULC-S524火警报警系统的检测器安装指南说明书

These instructions are written in accordance with the installation guidelines of NFPA 72, National Fire Alarm Code, and CAN/ULC-S524, The Installation of Fire Alarm Systems.DETECTOR PLACEMENTAlthough no specific spacings have been allocated for the detectors used for the 0 to 300 ft/min clean air velocity application, use 30 foot center spacing (900 sq ft) from NFPA Standard 72 Chapter 5 and CAN/ULC-S524, if practical, as a guide or starting point for a detector installation layout. This spacing, however, is based on ideal conditions — smooth ceiling, no air movement, and no physical obstructions. In some applications, therefore, considerably less area is protected adequately by each smoke detector. This is why it is mandatory to closely follow the installation drawings. In all installations (except in special circumstances, such as in computer room underfloors where the velocity may be between 300 and 1200 ft/min) the detector should be located on the ceiling, a minimum of 6 inches from a side wall, or on a wall, 6 inches from the ceiling.Should questions arise regarding detector placement,drawings provided or approved by Siemens Industry, Inc., or by its authorized distributors should be followed. This is extremely important! The detector placements shown on these drawings have been chosen after a careful evaluation P/N 315-081882, Rev. 2ADB-3, or relay RR-3, 40mA max, at 24V (one per detector.) CAUTION: Only one critical function remote should be used in each circuit, since only one alarm per circuit is guaranteed.max steady state. 350μA peak surge uponapplication of power, and 135mA max in alarm.Figure 1SIEMENS Models DI-3, DI-3H, DI-3IS, DI-A3, AND DI-A3H Installation And Wiring Diagram*NOTE : The DI-3IS is FM listed only. Do not use remote function with the DI-3IS.Installation/Wiring InstructionsSmoke and Fire Detector Models DI-3, DI-3H, DI-3IS *, DI-A3, and DI-A3HSiemens Industry, Inc.Building T echnologies DivisionP/N 315-081943-19of all facets of the area being protected. Such factors as air currents, temperature, humidity, pressure, and the nature of the load have been carefully considered. Especially noted have been the room or area configuration and the type of ceiling (sloped or flat, smooth or beamed). Siemens Industry, Inc.'s extensive experience in the design of the system assures the optimum detector placement and is reflected in these drawings.Sound engineering judgment by qualified personnel must prevail.TO AVOID NUISANCE ALARMS:DO NOT locate the DI-3, DI-3H, or DI-3IS detectors where excessive smoke concentrations exist under normal conditions or in areas of prolonged high relative humidity where condensation will occur.DO NOT locate the DI-3, DI-3H, or DI-3IS detectors adjacent to an oil burner, kitchen, or garage where exhaust fumes could trigger an alarm. Other causes of false alarms are dust accumulation, high wind velocity, heavy concentrations of steam, heavy pipe or cigar smoke, and certain aerosol sprays.DO NOT locate the DI-A3 or DI-A3H detectors in an area of prolonged high relative humidity when condensation will occur or adjacent to oil burners or in garages, where exhaust fumes could trigger an alarm.2AIR CURRENTSBefore a detector can sense a fire, the products of combustion or smoke must travel from the fire to the detector. Since their travel is especially influenced by air currents, the movement of air must be considered in the design of the system. While combustion products tend to rise, drafts from hallways, air diffusers, fans, etc., may aid or hinder the travel of combustion products to the detector. When positioning a detector at a particular location, consideration must be given to windows and doors, both open and closed, and to influencing air movement. A detector should never be installed in the air stream of a room air supply diffuser. It may be advantageous to position a detector closer to an air return.The distance that products of combustion or smoke travel from a fire to the detector is not usually the shortest linear route. Combustion products or smoke usually rise to the ceiling, then spread out. With average ceiling height (8 to 10 feet), this will not be an abnormal factor. Height should be taken into account, however, for high ceilings such as in churches, warehouses, auditoriums, etc.SPECIAL CEILING CONSTRUCTION FACTORS Ceiling obstructions can change the natural movement of air and combustion products. Depending on the direction of smoke travel, joists and beams can slow the movement of heated air and smoke, while pockets between them can contain a reduced level of smoke.Take obstructions created by girders, joists, beams, air conditioning ducts, or architectural design into consideration when determining area protection. Refer to the Initiating Devices chapter of NFPA Standard 72 for Location and Spacing requirements for specific types of construction; e.g. beam, suspended, level,sloped and peaked ceilings.TEMPERATURE AND HUMIDITYThe temperature range for Models DI-3, DI-3H, DI-3IS, DI-A3, and DI-A3H is 32o F (0o C) to 100o F (37.8o C). The four models can each be used in environments where the humidity does not exceed 93% (non-condensating).PRESSURENormal changes of atmospheric pressure due to changes in weather have a negligible effect on detector sensitivity.However, the lower air pressure at higher altitudes does have some effect on the sensitivity of ionization type detectors.Refer to the following table.APPLICATIONSl e d o M y t i c o l e V d n a R )n i m /t f (e d u t i t l A e d n a R )t e e f (n o i t a c i l p p A 3-I D 003-00004-0a er a n e p O H 3-I D 003-00008-0003a e r a n e p O S I 3-I D 0003-00004-0a e r a n e p O 3A -I D 0021-00004-0r e t u p m o C /a e r a n e p O s t o p s t c u d r i A /s e i t i l i c a f H3A -I D 0021-0030008-0003yl n o s t o p s t c u d r i A SPECIAL NOTE - HIGH STOCKPILINGIn general, detector placement for high stockpiling requires closer spacing, depending on the nature of the stock, its stored height, and the height of the building. Newer technologies recommend additional detector locations at tiered, lower levels. Detector placement for this type hazard requires a judgment factor that can only be provided by experienced, qualified personnel.DI-3IS ONLY —Use in hazardous atmospheres. The DI-3IS is approved by Factory Mutual to protect areas identified as Class I, Division 1, Groups A, B, C, and D. The intrinsically safe operation requires the use of a diode shunt barrier for System 3 applications or a DC Isolator for MXL CZM-1/-1B6applications. For System 3 applications refer to the Model 515-180238 Installation Instructions, P/N 315-091465. For MXL CZM-1/-1B6 applications, refer to the CZM-1 Installation Instructions, P/N 315-090725 or the CZM-1B6 Installation Instructions, P/N 315-095355, as applicable.DETECTOR WIRINGSiemens Industry, Inc., detectors should be interconnected as shown in Figure 1 and wired to the control panel by following the Wiring Connection drawing installed on the inside face of each control panel cover. Duplicate wiring information is also contained in the Installation, Operation,and Maintenance manual provided with every control panel.Note should be made of any limitations on the number of detectors permitted on each circuit. Quantities may vary,based on the specific type of response designed into the system (fan shutdown, door closing, external relay tie-in,extinguishing system discharge, etc.).DETECTOR MOUNTINGThe detector is provided with a separate base which attaches to a standard 4 inch square, 4 inch octagonal, or single gang outlet electrical box. The depth of the box is determined by the National Electrical Code for the number and size of the conductors used.TO MOUNT:•Route all wires outward from outlet box.•When the alarm LED viewing is critical,position the LED mark in the base in the intended direction. (See Figure 2.)•Mount base to outlet box and route wires through the hole in the center of the base. M ake connections directly to the base terminals.Refer to Figure 1 for details.•After all bases are installed, including the end-of-line device, check loop continuity. (Refer to system operation manual for procedure.) To make the continuity check, a jumper is furnished in every base (between terminals 1a and 1b) to complete the loop (See Figure 2). An open cir-cuit condition exists until the jumper or detector is installed in the base.Figure 23•If loop continuity is acceptable, remove jumper at each detector location and proceed with detector head installation.NOTE:To insure proper installation of the detector head into the base, be sure wires are properly dressed at installation.a.Position all wires flat against the base.b.Take up all slack in the outlet box.c.Route wires away from connector terminals.CAUTIONDetection Device StorageDO NOT install this detection device until all construction is completed.DO NOT store this detection device where it can be contaminated by dirt, dust, or humidity.INSTALLATION OF DETECTOR HEAD 1.Align notch in detector cover to raised surface on outer ring of base (See Figure 3).Figure 32.Push detector head into base and rotate clockwise to engage electrical connections. The detector will automatically stop and lock into place.3.To remove, push detector head up into the base while rotating the detector head counterclockwise. Continue to rotate counterclockwise until stop is reached. Then pull downward to disengage from base.DETECTOR SENSITIVITYThe normal sensitivity range of each Siemens Industry, Inc.,detector can be found on the back of the detector. In general,any condition which causes the detector sensitivity to decrease to a value outside its normal sensitivity range is approaching alarm and indicates that (a) a detector requires cleaning, (b) a change in ambient or environmental conditions has occurred, or (c) the detector is faulty.The DI-3, DI-3H, and DI-3IS sensitivities are field adjustable.Access to the sensitivity adjustment potentiometer is through a hole located on the detector head face. The DI-3, DI-3H,and DI-3IS sensitivity is adjustable ± 0.50 VDC of the nominal factory setting. Adjustment towards “ + ” increases detector sensitivity. Adjustment towards “ – ” decreases detector sensitivity. Refer to Figure 4. The sensitivity of the DI-A3 and DI-A3H detectors is factory set and is not field adjustable.Figure 4TESTINGTesting should be performed by qualified personnel. To ensure that the DI-3, DI-3H, DI-3IS, DI-A3, and DI-A3H are within factory-specified sensitivity limits, a sensitivity jack test is provided to directly measure the sensitivity of the detector in its mounted position while powered by the system. Access to the sensitivity test jack is obtained through five holes located on the front face of the detector (See Figure 4). Use sensitivity tester Model TM-I3 to test. Refer to the sensitivity test OPERATION MANUAL for M odel TM -I3, P/N 315-086641. Test frequency should be in accordance with installation and test guidelines of NFPA Standard 72.NOTE:To test for GO/NO GO operation, use SIEMENS Test Gas, P/N 315-282747, following the instructions on the label.MAINTENANCEDust accumulations may cause a shift in detector sensitivity.For this reason, it is important that each unit be given a periodic check and a light cleaning if necessary. The minimum test schedule may be found in the current edition of NFPA 72, Chapter 7 for installations in the U.S., and CAN/ULC-S537, The Verification of Fire Alarm Systems, for installations in Canada. Cleaning program intervals should be geared to the individual detector environment.Clean a detector by lightly brushing all open slots. You can also clean a detector with the suction of a vacuum cleaner,but the suction may cause the detector to alarm; therefore, it is recommended that power be disconnected during cleaning.The detectors are not designed for thorough cleaning in the field. When the detector sensitivity falls outside the acceptable limits for that detector, and cannot be brought back with sensitivity adjustment (where applicable), replace the detector head with an acceptable head. Send the removed head to the nearest Siemens Industry, Inc. Authorized Service Center for servicing.CAUTION:UNDER NO CIRCUM STANCES IS THE DETECTOR HEAD TO BE DISASSEM BLED. NO FIELD REPAIRS SHOULD BE ATTEMPTED. THE DETECTORS ARE FACTORY REPAIRABLE ONLY.EF A S Y L L A C I S N I R T N I N O N H 3A -I D D N A ,3A -I D ,H 3-I D ,3-I D S L E D O M TN E M P I U Q E L O R T N O C E L B I T A P M O C YT I L I B I T A P M O C T N E M P I U Q E R E I F I T N E D I G N I R I W /N O I T A L L A T S N I SN O I T C U R T S N I R E 2-P C 6-325390-513N /P )3m e t s y S (53-P C 02-209480-513N /P *)m e t s y S Q I -L X M /L X M (1-M Z C 8-527090-513N /P *)m e t s y S Q I -L X M /L X M (6B 1-M Z C 5-553590-513N /P )m e t s y S Q I -L X M /L X M (4-M Z C 8-627090-513N /P L X P 4-131490-513N /P )L X P (D 4-C Z P 2-461490-513N /P )L X P (B 4-E Z P 4-560490-513N /P *L X S 01-914290-513N /P X E -L X S 5-799590-513N /P *)L X S (R 4-E Z S 4-034290-513N /P )X E -L X S (X 4-E Z S 4-810690-513N /P )X E -L X S (X A 8-E Z S 4-220690-513N /P )m e t s y S 3L X (3-X N Z B 265880-513N /P )3m e t s y S (53-U Z 41-222380-513N /P r e i f i t n e d i y t i l i b i t a p m o c e h t s i r e b m u n l e d o m r o t c e t e d e h T .*s e i r o s s e c c a e t o m e r t r o p p u s t o n s e o d t n e m p i u q E l o r t n o C ;.s y a l e r r o s p m a l .g .e )Y L N O D E V O R P P A M F (E F A S Y L L A C I S N I R T N I Y L N O S I -I D L E D O M Y T I L I B I T A P M O C T N E M P I U Q E R E I F I T N E D I GN I R I W /N O I T A L L A T S N I SN O I T C U R T S N I r e i r r a B t n u h S e d o i D h t i w 03-S Z 61-650420-513N /P r o t a l o s I .C .D h t i w 1-M Z C 8-527090-513N /P r o t a l o s I .C .D h t i w 6B 1-M Z C 5-553590-513N /P r e i f i t n e d i y t i l i b i t a p m o c e h t s i r e b m u n l e d o m r o t c e t e d e h T .Siemens Industry, Inc.Building T echnologies Division Florham Park, NJP/N 315-081943-19Siemens Building Technologies, Ltd.Fire Safety & Security Products 2 Kenview BoulevardBrampton, Ontario L6T 5E46 Canada。
翰辰说明书HC500
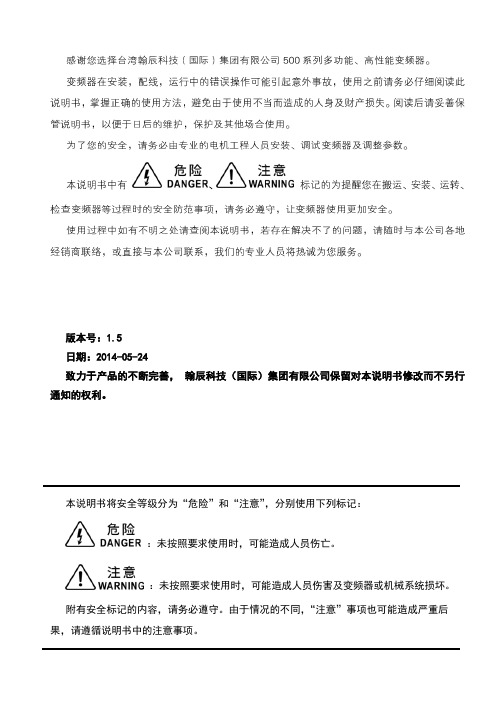
● 请勿对变频器内部的零部件进行耐压测试,这些半导体零件易受高压损毁。 ● 绝不可将变频器输出端子 U.V.W 连接至交流电源。 ● 正在通电或断开电源不久,变频器和制动电阻处于高温状态,请不要接触它们,以免
引起烫伤。 ● 各个端子上所加的电压只能是使用手册上所加的电压,以防止爆裂,损坏等等。 ● 变频器主电路板 CMOS、IC 易受静电影响及破坏,请勿触摸主电路板。 ● 只有合格的专业人员才可以安装、调试及保养变频器。 ● 变频器报废请按工业废物处理,严禁焚烧。 ● 变频器长时间保存后再使用,使用前必须进行检查和试运行。 ● 变频器可以容易地进行高速运行的设定,更改设定之前,检查电机和机械特性是否进
保修及服务................................................................. 88
No.1 安全注意事项
NO.1 安全注意事项
1.1 拆箱检查
图 1-1 变频器铭牌说明
1
NO.1 安全注意事项
1.2 安装
图 1-2 变频器型号说明
1.3 使用
NO.3 配线.................................................................. 6
3.1 主回路端子排列 .......................................................... 6 3.2 控制端子排列 ............................................................ 6 3.3 主回路端子说明 .......................................................... 6 3.4 控制端子说明 ............................................................ 7 3.5 跳线功能说明 ............................................................ 7 3.6 基本配线图 .............................................................. 9
ICP DAS I-7017R 8-ch Voltage and Current Input DAQ

I-7017R - 8-ch Voltage and Current Input DAQ Module - QuickStart (May/2020)ICP DAS USA, Inc. | | 1-310-517-9888 | 24309 Narbonne Ave. Suite 200. Lomita, CA 90717I-7017R8 Channels Voltage & Current InputData Acquisition ModuleQuick Start GuideProduct Website:https:///i_7017_r.html/dcon_utility_pro.htmlIntroductionThe I-7017R is an 8-channel analog input module with an extremely high quality protection mechanism where the overvoltage protection is 240 Vrms. The input type includes both voltage and current. The sampling rate of the I-7017R is adjustable, meaning that either fast mode or normal mode can be selected. The I-7017R also has 4 kV ESD protection as well as 3000 VDC intra-module isolation. The I-7017R-A5 is an 8-channel analog input module that is especially designed for high voltage input, and has an input range of between -50 V ~ +50 V or -150 V ~ +150 V.Packing ListI-7017RPlastic RailCDQuick Start GuideI-7017R - 8-ch Voltage and Current Input DAQ Module - QuickStart (May/2020)ICP DAS USA, Inc. | | 1-310-517-9888 | 24309 Narbonne Ave. Suite 200. Lomita, CA 90717⏹Internal I/O Structure < I-7017R >⏹Pin Assignments < I-7017R, I-7017R >⏹Internal I/O Structure (I-7017R)⏹Modbus Table (M-7017R only)Address Description R/W 10129 ~Over/under range status of channel 0R 10136to 7 for 4 ~ 20mA or 0 ~ 20mA ranges 00129 ~0013630001 ~Analog input value of channel 0 to 7R 3000840001 ~4000840481Firmware version (low word)R 40482Firmware version (high word)R 40483Module name (low word)R 40484Module name (high word)R 40485Module address, valid range: 1 ~ 247R/W 40486Bits 5:0R/WBaud rate, 0x03 ~ 0x0ACode0x030x040x050x06Baud1200240048009600Code0x070x080x090x0ABaud192003840057600115200Bits 7:600: no parity, 1 stop bit01: no parity, 2 stop bit10: even parity, 1 stop bit11: odd parity, 1 stop bit40487Type code R/W Address Description R/W 40488Modbus response delay time in ms,R/W valid range: 0 ~ 3040489Host watchdog timeout value, 0 ~R/W 255, in 0.1s40490Channel enable/disable, 00h ~ FFh R/W 40492Host watchdog timeout count, write 0R/W to clear00257Protocol, 0: DCON, 1: Modbus RTU R/W 00259Filter setting, 0: 60Hz rejection, 1:R/W 50Hz rejection002611: enable, 0: disable host watchdog R/W 00269Modbus data format, 0: hex, 1:R/W engineering00270Host watch dog timeout status, write R/W1 to clear host watch dog timeoutstatus002711: enable, 0: disable fast mode R/W 00273Reset status, 1: first read after R powered on, 0: not the first read afterpowered on⏹DCON ProtocolFunctions Command Response NotesRead module name$AAM!AA(Data)AA: address number Read module firmware version$AAF!AA(Data)Read all analog input data#aa>(data)Read analog input data of each channel (<=16 channel)#aai>(data)i: channel number (Hex) Read analog input data of each channel (>16 channel)#aaii>(data)ii: channel number (Hex) If you want to know the detail DCON protocol, please check it from CD or webCD path: \\napdos\7000\manual\Web: ftp:///pub/cd/8000cd/napdos/7000/manual/I-7017R - 8-ch Voltage and Current Input DAQ Module - QuickStart (May/2020)ICP DAS USA, Inc. | | 1-310-517-9888 | 24309 Narbonne Ave. Suite 200. Lomita, CA 90717I-7017R - 8-ch Voltage and Current Input DAQ Module - QuickStart (May/2020)ICP DAS USA, Inc. | | 1-310-517-9888 | 24309 Narbonne Ave. Suite 200. Lomita, CA 90717⏹Module test and configurationStep 1: INIT switch Operation Step 2: Install & Run DCON Utility 1. Please Install DCON Utility firstYou can find the software in the CD.CD path:<Driver>:\napdos\driver\dcon_utility\Web link:/pub/cd/8000cd/napdos/driver/dcon_utility/ 2. Run DCON utility1. Find out the INIT switch( back of the module),and turn to INIT.2. Reboot the moduleStep 3: Set search configuration & search module Select COM Port Number1. Click “COM Port”2. Assign the communication information and click“OK”Module Default Setting COM Port Refer converter Port Number Baud Rate 9600ProtocolDCON for I-7000Modbus RTU for M-7000Parity Option N,8,13. Click “Search” and select “Start Searching”Software will search the modules from COM Port 4. Click “Search“ and select “stop searching”Manual stop when the modules searchedNote:When no module can be searched, please check the wire and communication informationStep 4: Select Module for testing and configurationDouble click “select module”Step 5: Configuration Settings & Channel SettingsChannel StatusModule SettingsProtocol DCON / ModbusAddress1~255 (0:INIT)Baud rate1200~115200Parity option N,8,1Input range Depends on signalsourcesStep 6: Change to normal mode and keep the settings1.Turn the INIT Switch to Normal.2.Reboot the moduleI-7017R - 8-ch Voltage and Current Input DAQ Module - QuickStart (May/2020)ICP DAS USA, Inc. | | 1-310-517-9888 | 24309 Narbonne Ave. Suite 200. Lomita, CA 90717Trouble ShootingQ1. How to do when forgot module address or baud rate?Please turn to INIT mode, and run DCON Utility to search.The module supports DCON protocol at the INIT mode.And the address is 0. The communication setting is “9600,N,8,1”.Q2. How to configure the I-7000 and M-7000 modules?ICP DAS provide DCON Utility to configure I-7000 and M-7000 modules.Please download the last version from: /pub/cd/8000cd/napdos/driver/dcon_utility/Q3. How to calibrate the analog input module?Usually it is not necessary to calibrate the analog input module.However, in case you need to perform this operation, we provide a function to calibrate the module.Please refer to user manual 1.10.Notice:1.Please update DCON Utility to version 5.2.3 or more.2.Keep the module running more than 30 minutes to warm-up.Q4. How to measure the current?I-7017R and I-7017R require optional external resistance (125Ω) for current measurement.Please refer wired connections diagram.And then select a suitable input range by DCON Utility.Or please use our I-7017RC or I-7017RC modules.Q5. How to programming with I-7000 or M-7000 by C#, VB, VC?ICP DAS I-7000 and M-7000 series both support DCON protocol. And Only M-7000 series supports Modbus protocol.For DCON protocol, please download SDK and Demo from:/pub/cd/8000cd/napdos/driver/dcon_dll_new/For Modbus protocol, please refer this web link:/products/PAC/i-8000/modbus.htmIfthereisanyotherquestion,pleasefeelfreetocontactus.Email:******************Website: /contact_us/contact_us.htmlI-7017R - 8-ch Voltage and Current Input DAQ Module - QuickStart (May/2020)ICP DAS USA, Inc. | | 1-310-517-9888 | 24309 Narbonne Ave. Suite 200. Lomita, CA 90717。
Q-SYS NC Series Cameras 2 Hardware User Manual
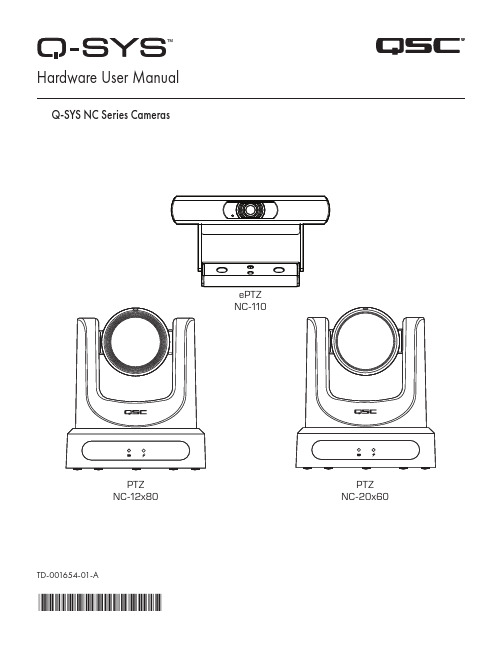
TD-001654-01-A*TD-001654-01*ePTZ NC-110PTZ NC-12x80PTZNC-20x60 Hardware User ManualQ-SYS NC Series CamerasEXPLANATION OF TERMS AND SYMBOLSThe term “WARNING!” indicates instructions regarding personal safety. If the instructions are not followed, the result may be bodily injury or death.The term “CAUTION!” indicates instructions regarding possible damage to physical equipment. If these instructions are not followed, it may result in damage to the equipment that may not be covered under the warranty.The term “IMPORTANT!” indicates instructions or information that are vital to the successful completion of the procedure.The term "NOTE" is used to indicate additional useful information.The intent of the lightning flash with an arrowhead symbol within an equilateral triangle is to alert the user to the presence of un-insulated "dangerous" voltage within the product's enclosure that may be of sufficient magnitude to constitute a risk of electric shock to humans.The intent of the exclamation point within an equilateral triangle is to alert the user to the presence of important safety,operating, and maintenance instructions in this manual.IMPORTANT SAFETY INSTRUCTIONS1. Read these instructions.2. Keep these instructions.3. Heed all warnings.4. Follow all instructions.5. Install in accordance with the manufacturer's instructions.6. Refer all servicing to qualified service personnel.7. Adhere to all applicable local codes.Maintenance and RepairsWARNING!: Advanced technology, e.g., the use of modern materials and powerful electronics, requires specially adapted maintenance and repair methods. To avoid the danger of subsequent damage to the apparatus, injuries to persons, and/or the creation of additional safety hazards, all maintenance or repair work on the apparatus should be performed only by a QSC authorized service station or an authorized QSC International Distributor. QSC is not responsible for any injury, harm, or related damages arising from any failure of the customer, owner, or user of the apparatus to facilitate those repairs. FCC StatementNote: This equipment has been tested and found to comply with the limits for a Class A digital device, pursuant to Part 15 of the FCC Rules.These limits are designed to provide reasonable protection against harmful interference when the equipment is operated in a commercial environment. This equipment generates, uses, and can radiate radio frequency energy and, if not installed and used in accordance with the instruction manual, may cause harmful interference to radio communications. Operation of this equipment in a residential area is likely to cause harmful interference in which case the user will be required to correct the interference at his own expense.Expected Product Life Cycle: 10 years, Storage Temperature range: –-20°C to +60°C, Relative Humidity: range of 5 —85% RH non-condensing.WarrantyFor a copy of the QSC Limited Warranty, visit the QSC, LLC., website at .RoHS StatementThe QSC Q-SYS NC Series: NC-110, NC-12x80, and NC-20x60 are in compliance with European Directive 2015/863/EU – Restriction of Hazardous Substances (RoHS2).What's in the BoxNC-12x80, NC-20x60 PTZ CamerasNC-110 ePTZ CameraIntroductionThe QSC Q-SYS™ NC Series comprises three camera models: NC-12x80, NC-20x60, and NC-110. These cameras send IP streams across a Q-LAN network to certain Q-SYS Core processors and peripherals, which bridge this IP signal to a USB signal for host computers to use in software applications.Connections and Controls (NC-12x80 and NC-20x60 PTZ) Front Panel1. Status LED (Green)• Off indicates the camera is in standby mode; network streams are off.• On indicates the camera is streaming video over the network.• Blinking indicates the ID mode is on.2. Power LED (Blue)• On indicates the camera has power applied.• Off indicates the camera has no power applied.Connections and Controls (NC-12x80 and NC-20x60 PTZ) (continued)Rear Panel56781. Product Label• Identifies product model: NC-12x80 or NC-20x60• Identifies the product serial number • Identifies the product MAC address2. ID Button: Press to identify this product in Q-SYS Designer Software and Q-SYS Configurator. The green STATUS LED on the frontpanel blinks when in ID mode. Press again to turn off.3. Factory Reset pin-hole: Use a paperclip or similarly sized object to insert. Press and hold the reset button for 5 seconds. This resetsall parameters to the factory defaults.4. Kensington™ Lock Slot: for use with a security cable (not supplied).5. DC 12 V: Connect an external power supply (not included). Supply must be rated at 12VDC 1A, EIAJ-04, center pin positive,outside barrel negative. Use only a class 2/LPS power supply.6. LAN/PoE: RJ-45 connector for Q-SYS Gigabit Ethernet and Power over Ethernet. Cat5e cabling or better required.7. 3G-SDI: 3G-SDI output via various video formats. Video formats can be changed via Q-SYS Designer Software or a Q-SYS UserControl Interface (UCI). Maximum video format is 1080p60.8. HDMI: HDMI® 1.4b output via various video formats. Video formats can be changed via Q-SYS Designer Software or a Q-SYSUCI. Maximum video format is 4K30. Note: NC Series PTZ Cameras support the usage of either HDMI or SDI, but not both simultaneously.Installation — NC-12x80 & NC-20x60 PTZInstall the Wall Mount Bracket1. Select a location on the wall or other vertical surface where the camera is tobe mounted. Make sure the surface is strong enough to hold the weight of the camera and bracket.2. Use the short side (1) of the bracket as a template to mark the location of thefour mounting holes (2) onto the wall.3. If the camera cables are installed inside the wall, run the cables through thelarge hole (3) in the short side of the bracket.4. Using appropriate screws (4), as necessary, attach the bracket to the wall.Tighten the attaching hardware. (Screws not supplied.)Bottom plate of Camera Mount the Camera on the Wall Bracket1. Align hole A on the bottom of the camera with the alignment pin A on thewall bracket. Place the camera onto the bracket so the alignment pin isinserted into the alignment hole on the camera and the rubber feet (C) on the bottom of the camera are inserted into the two slots (C).2. Install the larger screw (B) up through the wall bracket into the threaded holeon the bottom of the camera. Use a Phillips screwdriver to loosely tighten the screw.3. Install three smaller screws D, E, and F up through the wall bracket into thebottom of the camera. Tighten the screws using a Phillips screwdriver. 4. Tighten the larger screw installed earlier.5. If the camera cables are not installed in the wall, run the cables up throughthe oval hole (5) in the longer part of the bracket.6. Attach the cables to the appropriate connectors on the back of the cameraper installation requirements.7. Secure the cables to the bracket so that there is no strain placed on theconnectors.Connections and Controls (NC-110 ePTZ)Front Panel1. LED• Blinking Green: ID Mode• Solid Blue: Power On; Not Streaming• Solid Green: Streaming• Off: Camera is in Privacy Mode2. Included Camera Mount: This product can be configured for monitor-mounting or surface-mounting.3. Surface Mounting Screw Holes4. Universal Mounting Adapter: This can be used when connecting the NC-110 to a different mount.Rear Panel1. Factory Reset Pinhole: Use a paperclip or similarly sized object to insert. Press and hold the reset button for 5 seconds. This resetsall parameters to the factory defaults.2. ID Button: Press to identify this product in Q-SYS Designer and Configurator. The STATUS LED on the front panel blinks green whenin ID mode. Press again to turn off.3. LAN/PoE: RJ-45 connector for Q-SYS Gigabit Ethernet and Power over Ethernet. Cat5e cabling or better required.Installation (NC-110 ePTZ)Mounting Above a MonitorBend the bracket at the indicated pivot points shown to allow the optimal fit to the selected monitor. Mounting to a WallUsing the Existing Bracket for a Third-Party Mount1/4-20 UNC ThreadAttach the third-party mount to one of the 1 /4 -20 mounting holes on the included bracket. Removing the Existing Bracket for a Third-Party Mount1. On the bottom side of the camera, remove the two screws on the bracket.Remove 2 x Screws2.Slide the bracket off the camera.3. Mount the camera to the third-party mount.// DO NOT REMOVE \\Screws in block or camera1/4-20 UNC ThreadUse on various camera mounting bracketsInstalling Privacy Cover1. Peel adhesive.2. Center and attach to top of camera.3. Press firmly to affix adhesive.Dimension Drawings NC-12x80 & NC-20x60 PTZPTZ With Lens CapNC-110 ePTZQSC Self Help PortalRead knowledge base articles and discussions, download software and firmware, view product documents and training videos, and create support cases.https:///selfhelpportal/s/Customer SupportRefer to the Contact Us page on the QSC website for Technical Support and Customer Care, including their phone numbers and hours of operation.https:///contact-us/© 2021 QSC, LLC. All rights reserved. QSC, the QSC logo, Q-SYS, and the Q-SYS logo are registered trademarks of QSC, LLC, in the U.S. Patent and Trademark office and other countries. Q-LAN and Q-SYS Designer are trademarks of QSC, LLC. Patents may apply or be pending.All other trademarks are the property of their respective owners.。
动词后加-ing的规则
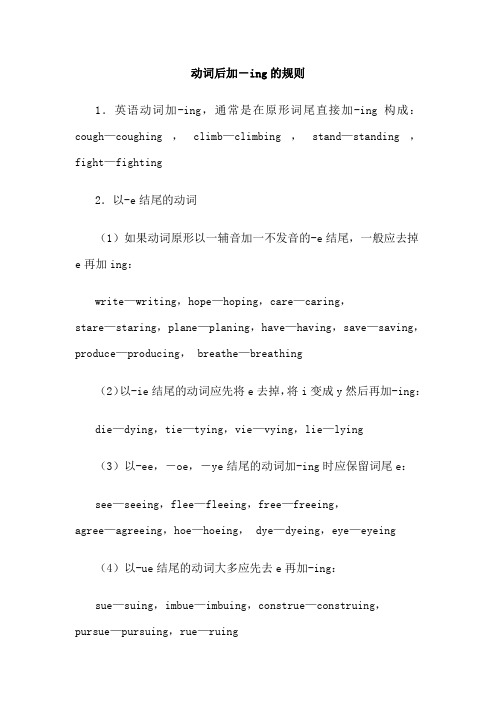
动词后加-ing的规则1.英语动词加-ing,通常是在原形词尾直接加-ing构成:cough—coughing,climb—climbing,stand—standing,fight—fighting2.以-e结尾的动词(1)如果动词原形以一辅音加一不发音的-e结尾,一般应去掉e再加ing:write—writing,hope—hoping,care—caring,stare—staring,plane—planing,have—having,save—saving,produce—producing, breathe—breathing(2)以-ie结尾的动词应先将e去掉,将i变成y然后再加-ing:die—dying,tie—tying,vie—vying,lie—lying(3)以-ee,-oe,-ye结尾的动词加-ing时应保留词尾e:see—seeing,flee—fleeing,free—freeing,agree—agreeing,hoe—hoeing, dye—dyeing,eye—eyeing (4)以-ue结尾的动词大多应先去e再加-ing:sue—suing,imbue—imbuing,construe—construing,pursue—pursuing,rue—ruing有时,词尾e可去掉也可保留:glue—gluing或 glueing,cue—cuing或 cueing,blue—blueing或 bluing,true—truing或trueing,clue—clueing或cluing3.以一元音加一辅音结尾的动词(1)如果动词最后一音节为重读闭音节,最后一个字母需要重复:run—running, stop—stopping, hop—hopping,plan—planning,star—starring, control—controlling但辅音x是个例外,无需重复(x其实起着两个辅音的作用):tax—taxing,relax—relaxing(2)如果动词最后一个音节为次重读音节,最后一个字母有时也重复:kidnap—kidnapping或kidnaping,program—programming或programing(3)如果动词最后一个音节为非重读音节,最后一个字母大多无需重复:open—opening,offer—offering,audit—auditing但在有些动词中,重复或不重复均可:worship—worshiping或 worshipping,focus—focusing或focussing,cancel—canceling或cancelling,travel—traveling 或travelling以非重读的-el结尾的动词加-ing时,英国英语习惯于重复词尾l,而美国英语则习惯于不重复1。
5700A 5720A 系列 II 多功能校准仪 使用说明书

PN 3474006 (Traditional Chinese)May 1996, Rev. 1, 5/09© 2009 Fluke Corporation. All rights reserved. Printed in USA. All product names are trademarks of their respective companies. 5700A/5720A Series II Multi-Function Calibrator使用說明書目錄表標題頁碼本說明書的內容包括什麼? (1)使用安全摘要 (1)W保險絲和電源電壓 (2)基本操作 (2)簡短的校準程序練習 (2)暖機 (3)練習:直流歸零校準 (3)連接電錶 (3)施加直流電壓 (3)檢查校準儀的不準確度 (4)練習:啟動誤差計算模式 (4)檢查電錶的高低檔位 (4)練習:施加交流電壓 (4)前面板組件 (5)輸出顯示器(左邊) (5)控制顯示器(右邊) (5)顯示器保護裝置 (5)前面板按鍵 (5)前面板連接器 (10)後面板組件 (11)後面板連接器 (11)開關及保險絲座 (12)推薦電纜 (13)連接受測機器(Unit Under Test) (14)誤差計算模式的使用 (19)遙控操作 (19)RS-232-C 介面參數 (20)i5700A/5720A使用說明書iiSeries II Multi-Function Calibrator 本說明書的內容包括什麼? 1本說明書的內容包括什麼本說明書內包含如何安全使用本儀器的資料,一節簡單的儀表校準操作程序及本機使用手冊的摘要。
有關本校準儀詳細的特點、功能及操作程序,請參閱使用手冊(Operator Manual)使用安全摘要WX 警告本機各接頭可能產生致命的電壓。
請遵守本說明書的所有安全考量。
為避免觸電,操作者不可接觸到OUTPUT HI 或者SENSE HI 的連接柱。
CG1777_Wire_Crimp_Process_Audit_rev001_2009-10-24

Appendix X-1(CG-1777)Statement of Requirements forSolder-less Crimp ConnectionsRevision: 001Issue Date: 2009-10-24This document contains Component and Manufacturing Description of Requirements for PSDS Vehicle Wiring Systems under sourcing. This document is used in conjunction with the PSDS SOR document package, GMN11012 - Summary Document for All Product Commodities and GMN 11039 - Statement of Requirements for All Electrical and Electronic Systems and Components.Revision Level: 001CHANGE LOG for SOR Appendix "X-1"Beginning with Initial ReleaseRevision Level: 001Table of Contents1Scope of Document (4)2Solder-Less Crimp Requirement Overview (4)2.1Description of Crimp System Applications (4)2.2Overview of Deliverables (4)3Crimp Validation and Process Requirements (4)3.1Crimp Validation (4)3.2Manufacturing Process Control (5)3.3Visual aids and Operator Training (6)3.4Self Process Audits (6)3.5Records Retention (6)4Resolution of Nonconformance of Crimp Validation (6)Revision Level: 0011Scope of DocumentThis appendix provides solder-less crimp requirements for PSDS components which are in addition to those specified in other PSDS sourcing documents or not covered elsewhere in SOR product documents. Included are additional requirements and deviations to GMN-11012 and/or GMN-11039, additional requirements and deviations to Connector SOR Appendix C, and other program specific requirements.Questions regarding this document can be directed to the GM Connection System or PSDS BOM Family Owner (BFO).2Solder-Less Crimp Requirement Overview2.1Description of Crimp System ApplicationsThis specification provides the validation test method and manufacturing process requirements for solder-less crimped connections (crimp) using stranded automotive copper wire. Wire types using compressed, compacted, or solid core construction or other core materials (clad, steel core, etc) or non-mechanical type wire to terminal applications will require additional requirements to be developed and agreed to by the GM PSDS DRE and the wiring harness supplier. Deviations to this document must be approved by the GM PSDS Lead Wiring Engineer.2.2Overview of DeliverablesThe awarded PSDS wiring harness supplier will be responsible for establishing and providing the following:1. Crimp validation for all wire to terminal applications used in wiring harnesses.2. Manufacturing process controls to ensure crimp conformance adherence on a regular basis.3. Various manufacturing plant and operator training.4. Validation and process control record retention.3Crimp Validation and Process Requirements3.1Crimp ValidationAll cable to terminal crimp applications must be validated to SAE/USCAR-21, Performance Specification for Cable to Terminal Electrical Crimps. The SAE/USCAR-21 document is available through SAE at .1. Every terminal to cable type, cable size, cable strand configuration and cable manufacturer(non-SAE cable type only) combination must be validated accordingly.2. To claim conformance to this specification, the tooling and process settings used to crimp aterminal/wire application must be traceable to a passed USCAR-21 test using the samesettings. The tooling and process used to meet USCAR-21 are very likely to be different than what is listed on a terminal drawing or process sheet developed per anotherspecification. Therefore, the settings traceable to USCAR-21 must supersede allRevision Level: 001Revision Level: 001documentation to the contrary (including crimp information on the part drawings) in order to claim compliance.3. All data compiled to validate each crimp shall be documented and stored for production use andaudit retrieval. This data shall include but not be limited to the following:a. Conductor crimp height (CCH)b. Conductor crimp width (CCW)c. Insulation crimp height (ICH)d. Insulation crimp width (ICW)e. Core compaction ratiof. Cross section visual inspection photographg. Cable pull test valuesh. Insulation strip length valuesi. Any and all values established in USCAR-21 documents.Crimp settings and data shall be documented in a form similar to that found in the document “Sample Report and Inspection.xls” shown in Section 3.2.3.2 Manufacturing Process ControlThe PSDS harness and/or lead prep supplier shall institute a manufacturing process control plan that ensures that crimp settings established to meet the validation criteria for each terminal to cable application are maintained throughout the build life cycle of the harness assembly. Each lead prep processing manufacturing plant shall have access to equipment capable of inspecting and logging the crimp performance validation data (a thru i) in Section 3.1. The process control plan must include at a minimum the following:1. Regular monitoring of production crimps. The beginning setup, during regular intervals andat the end of the production run for any cable to terminal configuration, the physical inspection and measurement of the crimp parameters shall be performed and compared against data compiled and documented in the validation process to verify that crimp settings are inconformance. Unless SPC data can prove otherwise, the minimum regular interval shall be set at no more than 40K crimp applications. Crimp monitoring data shall be documented for the purpose of inspection audits. Documentation information shall be similar to that shown in the document “Sample Report and Inspection.xls ”.2. Tool maintenance schedule. The Lead prep manufacturing plant shall perform a SPC studyto establish the maintenance schedule for crimp dies and tool adjustments. Tool maintenance shall be documented for inspection audits.3. Crimp force monitoring. Crimp force monitoring equipment capable of identifying crimpanomalies such as missing core strands, cable insulation under core crimp wings and damaged/worn crimp dies and tooling shall be utilized.4. Post crimp material handling, storage and handling. Processes and procedures shall beestablished for post production storage, protection and identification of terminated leads.Revision Level: 0013.3 Visual aids and Operator TrainingThe lead prep manufacturing plant shall utilize visual aids and provide operator training such that all aspects of the crimp process are clearly defined and that the expected quality of the terminated lead can be confirmed.3.4 Self Process AuditsThe lead prep manufacturing plant shall on a regular basis, perform self audits of the crimp process perthe wire crimp process audit form.3.5 Records RetentionThe supplier shall maintain a central file for the storage of laboratory reports and calibration records. Such record storage must be in accordance with established ISO and AIAG policies and practices.4Resolution of Nonconformance of Crimp ValidationThe GM DRE shall approve root cause and corrective actions (including any re-validation testing) of any Validation Plan failures, functional, mechanical, or failing to meet the requirements. Discrepancies, variations, and deviations shall be resolved by irreversible corrective action and retest to complete first article component design validation requirements. Resolution by waiver may be granted at thediscretion of the platform as a last resort if justified by circumstance but not to the extent of failure to meet performance requirements.In summary, no changes to this SOR and its subsequently developed components will be made without the written consent of the GM Lead Wiring Engineer.End of documentOnce printed, this document is uncontrolled。
DIN6701_audit_questions

ቤተ መጻሕፍቲ ባይዱ18
Assembly
Process observation: prevention of faults, acclimatisation, complying with processing requirements of the adhesive, with other process parameters and waiting times, adjusting of bondline thickness, accordance with work instructions, expert discussions with line operators
7
Processes
List of processes
8
Area of validity of the certificate
Class, main function, surface preparation, assembly processes,testing,degree of machanisation
M903L Bluetooth SiP Module - BT 4.0 LE 初步版本说明书
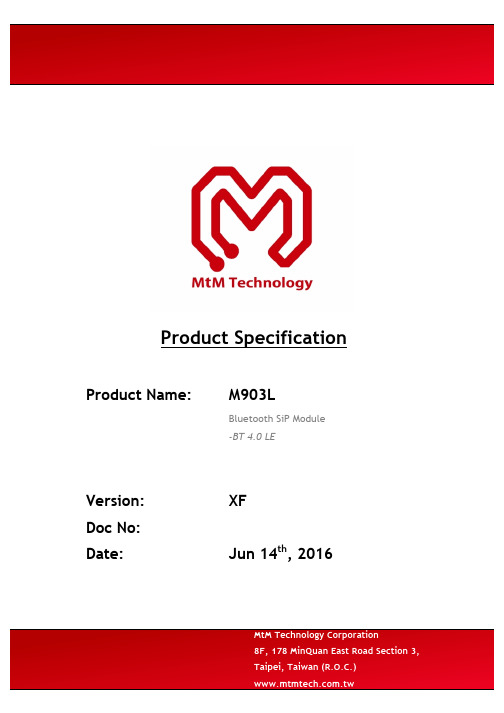
© MtM Technology Corporation. All rights reserved.
Page 3 / 24
MtM Technology Corporation
1 Description
The SiP module: M903L is a small size module that provides full function of Bluetooth 4.0 Low Energy in a tiny module via 32 pins LGA Foot Print. The M903L module provides everything required to create Bluetooth 4.0 Low Energy product with RF, baseband, MCU, qualified Bluetooth v4.0 stack and customer application running on a single IC. M903L enables ultra-low power connectivity and basic data transfer for applications previously limited by the power consumption, size constraints and complexity of other wireless standards. The low power consumption and excellent radio performance make it the best solution for OEM /ODM customers who require embedded Bluetooth 4.0 Low Energy feature, such as, IP camera, car key, sport and fitness watch, mouse, led light bulb etc. The module is based on CSR Bluetooth Low Energy single mode chipset provides Bluetooth Low Energy communication. M903L provides command line interface (CLI) for being easily controlled by a host CPU through UART communication. It also contains a 16 bit MCU to run a variety of applications and for embedded application development. For the software and driver development, we provide extensive technical document and reference software code for the system integration. Hardware evaluation kit and development utilities will be released base on listed OS and processors to OEM customers.
阿伦斯-审计学:一种整合的方法-课后习题答案ch02

阿伦斯-审计学:⼀种整合的⽅法-课后习题答案ch02 Chapter 2The CPA ProfessionReview Questions2-1The four major services that CPAs provide are:1. Assurance services Assurance services are independentprofessional services that improve the quality of information fordecision makers. Assurance services include attestation services,which are any services in which the CPA firm issues a report thatexpresses a conclusion about the reliability of an assertion that isthe responsibility of another party. The four categories of attestationservices are audits of historical financial statements, attestation onthe effectiveness of internal control over financial reporting, reviewsof historical financial statements, and other attestation services.2. Accounting and bookkeeping services Accounting services involvepreparing the client's financial statements from the client's records.Bookkeeping services include the preparation of the client'sjournals and ledgers as well as financial statements.3. Tax services Tax services include preparation of corporate,individual, and estate returns as well as tax planning assistance.4. Management consulting services These services range fromsuggestions to improve the client's accounting system to computerinstallations.2-2The major characteristics of CPA firms that permit them to fulfill their social function competently and independently are: 1. Organizational form A CPA firm exists as a separate entity to avoidan employer-employee relationship with its clients. The CPA firmemploys a professional staff of sufficient size to prevent one clientfrom constituting a significant portion of total income and therebyendangering the firm's independence.2. Conduct A CPA firm employs a professional staff of sufficient sizeto provide a broad range of expertise, continuing education, andpromotion of a professional independent attitude and competence.3. Peer review This practice evaluates the performance of CPA firmsin an attempt to keep competence high.2-3The Public Company Accounting Oversight Board provides oversight for auditors of public companies, includingestablishing auditing and quality control standards for public company audits, and performing inspections of the quality controls at audit firms performing those audits.2-4The purpose of the Securities and Exchange Commission is to assist in providing investors with reliable information upon which to make investment decisions. Since most reasonably large CPA firms have clients that must with the SEC each year (all companies filing registration statements under the securities acts of l933 and l934 must financial statements and other reports with the SEC at least once each year), the profession is highly involved with the SEC requirements.The SEC has considerable influence in setting generally accepted accounting principles and disclosure requirements for financial statements because of its authority for specifying reporting requirements considered necessary for fair disclosure to investors. In addition, the SEC has power to establish rules for any CPA associated with audited financial statements submitted to the Commission.2-5The AICPA is the organization that sets professional requirements for CPAs. The AICPA also conducts research and publishes materials on many different subjects related to accounting, auditing, management advisory services, and taxes. The organization also prepares and grades the CPA examinations, provides continuing education to its members, and develops specialty designations to help market and assure the quality of services in specialized practice areas.2-6Statement on Standards for Attestation Engagements was first issued in 1986 and its purposes were to provide a framework for attest engagements and to develop standards for those engagements. In 2001, the Auditing Standards Board issued SSAE 10 in response to the need for more detailed standards for specific types of attestation services. SSAE 10 supercedes the previously issued standards and its main purpose is to improve the usefulness of the attestation standards and provide greater flexibility to practitioners in providing assurance services.2-7 The PCAOB now has responsibility for establishing auditing standards for public companies, while the Auditing Standards Board (ASB) of the AICPA establishes auditing standards for private companies. The ASB previously had responsibility for establishing auditing standards for both public and private companies. Existing auditing standards were adopted by the PCAOB as interim auditing standards for public company audits.2-8 Generally accepted auditing standards are ten general guidelines to aid auditors in fulfilling their professional responsibilities. These guidelines include three general standards concerned with competence, independence, and due professional care; three standards of field work including planning and supervision, study and evaluation of internal control, and the gathering of competent evidential matter; and four standards of reporting which require a statement as to presentation in accordance with generally accepted accounting principles, inconsistency observed in the current period in relation to the preceding period, adequate disclosure, and the expression of an opinion as to the fairness of the presentation of the financial statements.2-8 (continued)Generally accepted accounting principles are specific rules for accounting for transactions occurring in a business enterprise. Examples may be any of the opinions of the FASB.2-9Auditors can obtain adequate technical training and proficiency through formal education in auditing and accounting, adequate practical experience, and continuing professional education. Auditors can demonstrate their proficiency by becoming licensed to practice as CPAs, which requires successful completion of the Uniform CPA Examination. The specific requirements for licensure vary from state to state.2-10For the most part, generally accepted auditing standards are general rather than specific. Many practitioners along with critics of the profession believe the standards should provide more clearly defined guidelines as an aid in determining the extent of evidence to be accumulated. This would eliminate some of the difficult audit decisions and provide a source of defense if the CPA is charged with conducting an inadequate audit. On the other hand, highly specific requirements could turn auditing into mechanical evidence gathering, void of professional judgment. From the point of view of both the profession and the users of auditing services, there is probably a greater harm from defining authoritative guidelines too specifically than too broadly.2-11International Standards on Auditing (ISAs) are issued by the International Auditing Practices Committee (IAPC) of the International Federation of Accountants (IFAC). ISAs are designed to improve the uniformity of auditing practices and related services throughout the world by issuing pronouncements on a variety of audit and attest functions and promoting their acceptance worldwide. A CPA who conducts an audit in accordance with GAAS may not comply with ISAs because there may be additional ISA requirements that extend beyond GAAS requirements.2-12 Quality controls are the procedures used by a CPA firm that help it meet its professional responsibilities to clients. Quality controls are therefore established for the entire CPA firm as opposed to individual engagements.2-13The element of quality control is personnel management. The purpose of the requirement is to help assure CPA firmsthat all new personnel should be qualified to perform their work competently. A CPA firm must have competent employees conducting the audits if quality audits are to occur.2-14 A peer review is a review, by CPAs, of a CPA firm's compliance with its quality control system. A mandatory peer review means that such a review is required periodically. AICPA member firms are required to have a peer review every three years. Registered firms with the PCAOB are subject to quality inspections. These are different than peer reviews because they are performed by independent inspection teams rather than another CPA firm.2-14 (continued)Peer reviews can be beneficial to the profession and to individual firms. By helping firms meet quality control standards, the profession gains if reviews result in practitioners doing higher quality audits. A firm having a peer review can also gain if it improves the firm's practices and thereby enhances its reputation and effectiveness, and reduces the likelihood of lawsuits. Of course peer reviews are costly. There is always a trade off between cost and benefits. A CPA firm also gives up some independence of activities when it is reviewed by another CPA firm.2-15The two divisions of practice that a CPA firm may belong to are the SEC Practice Section (renamed the Center for Public Company Audit Firms)and the Private Companies Practice Section. A firm may belong to one section, both sections, or neither. Many of the self-regulatory activities of the SECPS have been taken over by the PCAOB.Proponents of this division believe that this will improve the quality of practice by CPA firms and that it will improve self-regulation. Critics state that it establishes two classes of CPAs and implies a lower performance quality for firms that are not members of the SEC Practice Section.Multiple Choice Questions From CPA Examinations2-16 a. (1) b. (2) c. (3) d. (3)2-17 a. (2) b. (2) c. (3)Discussion Questions And Problems2-18a.The comments summarize the beliefs of many practitioners about theSarbanes–Oxley Act and the PCAOB. The arguments against the Act can be summarized as four arguments:1. Costs of complying with the Act are excessively high, especially therequirement to report on internal control over financial reporting,and will discourage companies from becoming public companies.2. Relative cost for local audit firms is excessively high.3. Additional oversight is not needed because sufficient qualitycontrols have already been implemented by most audit firms.4. Three other things already provide assurance of adequate quality:a competitive economic environment, legal liability, and auditingstandards.To support these comments, it can be argued that the profession has generally functioned well with relatively little controversy and criticism.2-18 (continued)The arguments against these comments are primarily as follows:1. Reporting on the effectiveness of internal control over financialreporting will provide benefits in improved controls, resulting inhigher quality financial reporting and reduced losses from fraud.2. The increased confidence in financial reporting will increase accessto capital and lower the cost of capital by reducing information risk.3. Changes in the scope of CPA practices and other threats to auditquality required government regulation.4. Regulation of public company audits will not affect most audit firmsthat do not have public company audit clients.b. There is no correct answer to this question. Different people reachdifferent conclusions, depending on the weights put on the various arguments. Time is needed to effectively assess both the costs and benefits of the Act.2-19 a. Engagement performanceb. Personnel managementc. Engagement performanced. Engagement performancee. Independence, integrity, and objectivityf. Monitoringg. Acceptance and continuation of clients and engagementsh. Personnel managementi. Personnel management2-20 a. Rossi and Montgomery's primary ethical consideration is their professional competence to perform all of the audit work for filingwith the SEC. In addition, if Rossi and Montgomery have performedbookkeeping services or certain consulting services for MobileHome, they will not be independent under PCAOB and SECindependence requirements. The firm must also be a registeredfirm with the PCAOB.b. The filing with the SEC, in addition to normal audited financialstatements, will require completion and registration with the SEC ofForm S-1 which includes an audited summary of operations for thelast five fiscal years as well as many additional schedules anddescriptions of the business. Each quarter subsequent to the filing,Form 10-Q must be filed; and within 90 days of the end of eachfiscal year Form 10-K must be filed with the SEC.In addition, Form 8-K must be filed whenever significant events have occurred which are of interest to public investors. These forms must be filed in conformity with Regulation S-X, whichrequires considerable disclosures in addition to those normallyrequired in audited financial statements.2-212-22 a. CPAs can provide the following information and Web links on their firm Web sites: Office locations or affiliationsLines of service the firm provides (audit, tax, management consulting, etc.)Industry specialization information for the firmOnline software tools and databasesLatest tax law developments applicable to clientsCalculators for retirement account decisionsOnline privacy management softwareb. CPA firms invest their resources to develop sophisticated Web siteslargely because of a desire to maintain a client-service approach.Increased competition motivates CPA firms to improve thetraditional paths of providing information to their clients. A CPA firmcan reach clients more quickly and efficiently with vital informationvia the firm’s Web site than through more traditional forms ofcommunication, such as a monthly or quarterly newsletter. Also, asmore clients become sophisticated in the area of technology, theyexpect their CPA firms to do the same by providing a useful Website that has links to other helpful tools and resources.c. The Internet is a useful tool for a CPA firm’s accounting andauditing practice in many ways. A firm’s Web site can be used tomarket the firm’s accounting and auditing practice. The Internetalso connects the firm’s global professional staff, making it easierfor staff from all over the world to provide client service on a timelybasis without having to be physically present at the client’s location.CPAs also use online resources and databases to remain currenton emerging business and standards-setting issues. Examplesinclude Standard and Poor’s Net Advantage Database andGoldman Sachs Research Database. These two databases provideextensive industry-specific information and coverage of companiesthat CPAs use on a subscription basis to stay current on industrydevelopments and to obtain industry data useful for auditing andconsulting.Internet Problem Solution: CPA Vision Project2-1 The CPA Vision Project [] is all about helping the “CPA profession stay on top of the change curve.”With input from CPAs across the nation, the CPA Vision process created a comprehensive and integrated vision of the profession’s future.1. What characteristics and professional services come to mind whenyou hear the term CPA? What is your impression of the public’sstereotype of CPAs?Answer: Student responses will vary.2. Fill in the missing words in the following Vision Statement:Answer:“CPAs are the trusted professionals who enable people and organizations to shape their future. Combining insight with integrity, CPAs deliver value by …Communicating the total picture with clarity and objectivity,Translating complex information into critical knowledge,Anticipating and creating opportunities, andDesigning pathways that transform vision into reality.3. Briefly describe the eight forces that will impact the profession.Answer: The eight forces are:1. Non-CPA Competitors - The number of new, non-CPA competitors, not bound by the profession's code of standardsand ethics is increasing at an alarming rate.2. Decline of new CPAs - The number of students and young people electing to join the CPA profession has dramatically declined.3. Technology Displacement - Many of the traditional, essential skills of CPAs are being replaced by new technologies thatare increasing in number and being rapidly developed, oftenfrom unexpected sources.4. Borderless World- As the world becomes borderless, the marketplace is demanding more complex, real-time adviceand services, presenting unlimited opportunities for CPAs to expand their skills, competencies, and services.5. Leadership Imperative - Corporations are conductingbusiness in a world of commerce that is global, technological, instantaneous, and increasingly virtual. The leadership they require from both internal and external advisors requires new insights, new skills, and extraordinary agility.6. Technological Advances - Technology will continue to challenge and reshape our lifestyles, work patterns,educational experiences, and communication styles and techniques. Technology will rewrite the "rules of business," leaving those who will not harness it and effectively integrateit far behind.7. Market Value Shifts- The perceived value of some of the profession's cornerstone services-accounting, auditing, andtax preparation-is declining in the marketplace.8. Pressure to Transform Finance from Scorekeeper toBusiness Partner - The CPA in business is being challengedto deliver value to the organization and help create asustainable competitive advantage.4. The CPA Vision Project suggests that “the increasing complexities of the global environment and the commodity characteristics of traditional services mandate that the CPA profession migrate up theeconomic value chain.” What is meant by “moving up the economicvalue chain,”and how are CPAs going to accomplish this? (Hint:See the “Final Report.”)Answer: Moving up the economic value chain means moving fromproviding low value products and services to providing higher valueproducts and services (i.e., services that will permit the professionto thrive in a knowledge-based, global economy). The higher on theeconomic value chain, the higher the revenue. “The more a productor service is refined and defined, the less market value it will have.For example: tax preparation services have been commoditizedand automated to the point that they can largely be preparedelectronically. Tax form preparation is a Platform 1 service - afoundation service. The higher economic value of this informationlies in understanding what the foundation service implies-the“where do we go from here”and the “so whats”of business andfinance. Higher Platform services, such as estate and financialplanning are where higher economic benefits exist for the future ofthe profession. Higher Platform services are, and will increasinglybe, the most valued services and functions, and therefore willcommand higher fees and salaries. Traditional services are thefoundation from which CPAs can leverage to higher valueservices.” The report describes 7 platforms.Obviously to move up the value chain CPAs need to develop expertise for and market higher value services. For some this mayrepresent “thinking out of the box.”(Note: Internet problems address current issues using Internet sources. Because Internet sites are subject to change, Internet problems and solutions are subject to change. Current information on Internet problems is available at ).。
3GPP 5G基站(BS)R16版本一致性测试英文原版(3GPP TS 38.141-1)

4.2.2
BS type 1-H.................................................................................................................................................. 26
4.3
Base station classes............................................................................................................................................27
1 Scope.......................................................................................................................................................13
All rights reserved. UMTS™ is a Trade Mark of ETSI registered for the benefit of its members 3GPP™ is a Trade Mark of ETSI registered for the benefit of its Members and of the 3GPP Organizational Partners LTE™ is a Trade Mark of ETSI registered for the benefit of its Members and of the 3GPP Organizational Partners GSM® and the GSM logo are registered and owned by the GSM Association
FLUCK 725 中文说明书

Fluke公司的保证责任是有限的,Fluke公司可以选择是否将依购买价退款、免费维修或更换在保证期内退回到Fluke公司授权维修中心的有缺 陷产品。
为了获得保证服务,请联系您附近的Fluke公司授权中心取得将产品返还的授权信息,然后寄送附有产品损坏说明、邮资和预付保险金(目的 地交货)到您附近的Fluke公司授权中心。Fluke公司假设在转送中没有损坏危险。在保修之后,产品将送回买方,提前支付运输费(目的地交 货)。假如Fluke公司认定产品故障是由于疏忽、误用、污染、变造、意外、异常操作和运行造成的,包括使用超出产品的指定额定值而导致 过电压故障,或是由于机件日常使用耗损,Fluke公司将估算修理费用,并在获得客户授权之后才开始进行修理。在修理之后,产品将送回已 预付运输费的买方,买方将收到修理和返回运输费用(寄发地交货)的帐单。Fra bibliotek 目录标题
页码
简介 ................................................................................................................................ 1 联系 Fluke ...................................................................................................................... 1 标准设备......................................................................................................................... 3 安全须知......................................................................................................................... 3 危险禁制区 ..................................................................................................................... 3
2700-5500中文用户操作手册

服务
MAHA Maschinenbau Haldenwang GmbH & Co. KG - Service Dept. Hoyen 20 D-87490 Haldenwang/Allgäu Hotline: +49 (0) 8374-585 + extension 260 for brake testers, test lanes 280 for automotive lifts 290 for dynamometers, exhaust and air conditioning service equipment +49 (0) 8374-585-110, -111, -112, -113, -115 +49 (0) 8374-585-491
诊断型底盘测功机
FPS 2700 / 5500
用于乘用车和轻卡,最大轴重 2,700 / 5,500 kg
操作手册
D1 3907BA1-GB01
FPS 2700 / 5500
版本
第一版:2005-05-19 D1 3907BA1-GB01 软件: FPS 版本高于 V1.08.001 ASM H8 版本高于 V2.50
1.1 1.2
概述 ................................................................................................................................................ 1 技术规格 .... ................................................................................................................................ 2 1.2.1 滚筒 ................................................................................................................................. 2 1.2.2 计算机最低配置(到2005年3月) .................................................................................. 2 噪声 ................................................................................................................................................. 2 键盘描述 ......................................................................................................................................... 3 测量程序 ......................................................................................................................................... 5 基本计算公式 .................................................................................................................................. 6 1.6.1 驱动阻力 ......................................................................................................................... 6 1.6.2 扭矩 ................................................................................................................................. 7 1.6.3 标准功率计算公式 ........................................................................................................... 7 1.6.4 汽油发动机功率转换公式 ................................................................................................ 8 1.6.5 柴油发动机功率转换公式................................................................................................. 9 1.6.6 涡轮增压发动机功率转换公式 ....................................................................................... 10 1.6.7 计算发动机因子fm......................................................................................................... 11
MRCP Asterisk Modules Administrator Guide

MRCPAdministrator GuideRevision: 65Distribution: Debian / UbuntuCreated: February 7, 2015Last updated: May 7, 2021Author: Arsen Chaloyan1Overview (3)1.1Applicable Versions (3)1.2Supported Distributions (3)1.3Authentication (3)2Installing Deb Packages Using Apt-Get (4)2.1Repository Configuration (4)2.2GnuPG Key (4)2.3Repository Update (4)2.4Installation of Asterisk (4)2.5Installation of Applications Suite (app-unimrcp) (5)2.6Installation of Speech Resource (res-speech-unimrcp) (5)3Installing Deb Packages Manually (6)3.1Package List (6)3.2Package Dependency Graph (7)3.3Package Installation Order (8)1OverviewThis guide describes how to obtain and install binary packages of Asterisk and UniMRCP modules on Debian-based distributions. The document is intended for system administrators and developers.1.1Applicable VersionsInstructions provided in this guide are applicable to the following versions.UniMRCP 1.6.0 and aboveAsterisk 16 and above1.2Supported DistributionsUniMRCP binary packages are currently available only for x86_64 (64-bit) architecture.Operating System Released End of SupportUbuntu 16.04 LTS (xenial) February 2017 March 2021Ubuntu 18.04 LTS (bionic) May 2019 TBAUbuntu 20.04 LTS (focal)May 2021 TBANote: packages for other distributions can be made available upon request. For more information, contact ********************.1.3AuthenticationUniMRCP binary packages are available to authenticated users only. In order to register a free account with UniMRCP, please visit the following page.https:///profile-registrationNote: a new account needs to be verified and activated prior further proceeding.2Installing Deb Packages Using Apt-GetUsing the APT package handling utility (apt-get) is recommended for installation of UniMRCP binary packages.2.1Repository ConfigurationThe content of a typical configuration file of the APT repository, to be placed in/etc/apt/sources.list.d/unimrcp.list, is provided below.deb[arch=amd64]https://username:********************/repo/apt/distrmainasterisk-16 The username and password fields included in the HTTPS URI must be replaced with the corresponding account credentials.The distr field must be replaced with the corresponding distribution code name such as bionic.The repository provides the following components:•main – packages containing UniMRCP and its dependencies•asterisk-16 – packages containing Asterisk 16 and corresponding UniMRCP modules2.2GnuPG KeyFor verification of binary packages, UniMRCP provides a public GnuPG key, which can be retrieved and installed as follows.wget -O - https:///keys/unimrcp-gpg-key.public | sudo apt-key add -2.3Repository UpdateIn order to check for updates and apply the changes in the APT configuration, use the following command.sudo apt-get update2.4Installation of AsteriskIn order to install Asterisk and related modules, the following commands can be used.sudo apt-get install asteriskAs a result, yum will check for and install all the required components, including the packages for Asterisk.2.5Installation of Applications Suite (app-unimrcp)In order to install the app-unimrcp module, which provides a suite of MRCP applications for Asterisk, the following command can be used.sudo apt-get install asterisk-app-unimrcpAs a result, apt-get will check for and install all the required components, including the packages for Asterisk and UniMRCP client.2.6Installation of Speech Resource (res-speech-unimrcp)In order to install the res-speech-unimrcp module, which provides an MRCP implementation of the Asterisk Speech Recognition Interface, the following command can be used.sudo apt-get install asterisk-res-speech-unimrcpAs a result, apt-get will check for and install all the required components, including the packages for Asterisk and UniMRCP client.3Installing Deb Packages ManuallyUniMRCP deb packages can be installed manually using the dpkg utility. Note, however, that the system administrator should take care of package dependencies and install all the packages in appropriate order. The deb packages have the following naming convention:$packagename_$universion~$astversion-$distr_$arch.debwhere•packagename is the name of a package•universion is the UniMRCP version•astversion is the Asterisk version•distr is the distribution code name (trusty, xenial, …)•arch is the architecture (amd64, i386, all, …)3.1Package ListThe following is a list of deb packages required for installation of UniMRCP modules for Asterisk, including UniMRCP dependencies.Package Name Component Descriptionasterisk-app-unimrcp Asterisk A suite of MRCP applications.asterisk-res-speech-unimrcp Asterisk An MRCP implementation of Generic SpeechRecognition Interface of Asterisk.asterisk Asterisk Compound Asterisk package.asterisk-config Asterisk Configuration files for Asterisk.asterisk-doc Asterisk Source code documentation for Asterisk. asterisk-dev Asterisk Development files for Asterisk.asterisk-dahdi Asterisk DAHDI devices support for Asterisk.asterisk-modules Asterisk Loadable modules for Asterisk.unimrcp-client UniMRCP Shared libraries and sample applications of theclient.unimrcp-client-dev UniMRCP Development kit of the client.unimrcp-common UniMRCP Data common for the client and the server. unimrcp-common-dev UniMRCP Development kit of the common client andserver data.uniapr UniMRCP UniMRCP edition of the Apache PortableRuntime (APR) library.uniapr-dev UniMRCP Development kit of the corresponding APRlibrary.uniapr-util UniMRCP UniMRCP edition of the Apache PortableRuntime Utility (APU) library.uniapr-util-dev UniMRCP Development kit of the corresponding APR-Util library.unisofia-sip UniMRCP UniMRCP edition of the Sofia SIP library. unisofia-sip-dev UniMRCP Development kit of the corresponding SofiaSIP library.The respective packages for each of the components can be obtained from the UniMRCP website by visiting the download area having logged in to your account.https:///project/release-view3.2Package Dependency GraphThe following is a graph of package dependencies.app-unimrcpres-speech-unimrcpunimrcp-clientunimrcp-commonunimrcp-deps-apr unimrcp-deps-apu unimrcp-deps-sofiaPowered by Universal Speech Solutions LLC | Installing Deb Packages Manually 73.3Package Installation OrderPackages for the APR, APR-Util and Sofia-SIP libraries must be installed first.sudo dpkg --install uniapr_$universion-$distr_$arch.debsudo dpkg --install uniapr-util_$universion-$distr_$arch.debsudo dpkg --install unisofia-sip_$universion-$distr_$arch.debThen, packages for the common data and the client library should follow.sudo dpkg --install unimrcp-common_$universion-$distr_$arch.debsudo dpkg --install unimrcp-client_$universion-$distr_$arch.debThen, the Asterisk packages should follow.sudo dpkg --install asterisk-modules_$astversion-$distr_$arch.debsudo dpkg --install asterisk-config_$astversion-$distr_$arch.debsudo dpkg --install asterisk _$astversion-$distr_$arch.debFinally, based on your requirements, either app-unimrcp and/or res-speech-unimrcp packages can be installed.sudo dpkg --install asterisk-app-unimrcp_$universion~$astversion-$distr_$arch.debsudo dpkg --install asterisk-res-speech-unimrcp_$universion~$astversion_$distr.$arch.deb The same order should be considered for the installation of the corresponding development packages.。
ICP DAS I-7045D 16 Ch DO DAQ Module 快速入门指南说明书

I-7045D16 Channel Digital Output Data AcquisitionModuleQuick Start GuideProduct Website:https:///i_7045_d.html/dcon_utility_pro.html1. IntroductionI-7045D is intelligently designed to provide signal conditioning system monitoring and safe value settings. I-7045 is a cost-effective solution for a wide range of valuable industrial control signals and systems. The DCON utility can help users to configure and test I-7045 16-Channel Isolated Digital Output modules. Plenty of library functions and demo programs are provided to let users develop programs easily under Windows, Linux and DOS operating systems. Users may mount the modules on a DIN rail, panel or wall. Modules have a screw-terminal block to connect to the signals.2. Terminal AssignmentI-7045D 16 Ch DO DAQ Module- QuickStart (May/2017)3. Block/ Wiring DiagramI-7045D 16 Ch DO DAQ Module- QuickStart (May/2017)4. Default SettingsDefault settings for the I-7045D DIO modules are as follows:。
Epic PHI Audit User Guide

P HI Audit Us er G uideTable Of ContentsAuditable Actions (1)Navigating the PHI Audit Dashboard (2)Only community users with selected roles can access PHI Audit. For questionsabout PHI Audit access, contact your community administrator.The PHI Audit application enables you to audit:•Access to operations on a selected patient's data• A selected user's access to, and operations on, patient dataThe purpose of the audit tool is to review users’ accesses of Protected Health Information to verify accesses are in line with HIPAA requirements.PHI Audit allows you to:•Audit a specific patient's data to retrieve information about auditable actions that have been performed on the data.•Audit a specific user's actions to determine whose data they have accessed, and which auditable actions they performed on the data.Auditable ActionsPHI Audit retrieves information associated with actions described in the following table. You can select one or more actions when you create an audit.Patient PatientSearchResults Includes the search results from which the patient was selected.Patient PatientConsent Displays the consent selection that was selected for access to patient data.Patient Patient Opt In Indicates if the Opt In setting was changed. Patient Patient OptOutIndicates if the Opt Out setting was changed.Patient Patient PHIAccessDisplays the viewed patient data.User PatientConsent Displays the consent selection the user selected to access patient data.User PatientSearchCriteriaAudits the criteria used to search for a patient.User PatientSearchResults Audits the search results from which the user selected a patient.PHI Audit User GuideUser Patient Opt In Indicates if the user changed the Opt In setting. User Patient OptOutIndicates if the user changed the Opt Out setting.User Patient PHIAccess Indicates which tabs of patient data the user accessed.Navigating the PHI Audit DashboardImportant: As you perform tasks with the PHI Audit Dashboard, use theapplication's buttons to navigate. Do not use your browser's back button. Ifyou use your browser's back button for navigation, you may be returned to yourhealthcare community home page.Examples of application buttons:You can quickly initiate audit tasks from the Audit Dashboard window. To access tasks, scroll up or down the window as required to reach the section that supports the tasks you want to perform.In sections that display information in columns, you can sort the information by clicking column headings. Multiple clicks on a heading toggle the sort order between ascending and descending sequence.PHI Audit OverviewThe Start a new audit section provides access to two wizards used to create patient or user audits. For details, refer to:•Create a Patient Audit•Create a User AuditThe Scheduled audits section allows you to view or cancel audits that have not been submitted for system processing. For details, refer to View or Cancel Scheduled Audits.The Processed audits section allows you to view and delete processed audits. For details, refer to:•View a Processed Audit•Download Audit Data as CSV•Delete Processed AuditsOnly community users with selected roles can access PHI Audit. For questionsabout PHI Audit access, contact your community administrator.The method used to access PHI Audit can vary depending on your system configuration. If you are not sure how to navigate to PHI Audit, contact your community administrator.Perform the following steps to access PHI Audit:1. Access your health care community using the URL provided by your organization. Yourhealthcare community login page displays.2. Enter your User ID and Password, then click Login. Your health care community homepage displays.3. Navigate to the PHI Audit Dashboard screen. For example, click Audit on the communityhome page navigation bar. The PHI Audit Dashboard window displays.This step can vary, depending upon your system configuration. If you are notsure how to navigate to the PHI Audit Dashboard window, contact yourcommunity administrator.Access PHI AuditYou have successfully accessed PHI Audit.Create a Patient audit when you want to audit PHI data actions for a selected patient.This procedure assumes you have logged in to your healthcare community and navigated to the PHI Audit Dashboard window. For details, refer to Access PHI Audit.Perform the following steps to create a patient PHI Audit:1. On the PHI Audit Dashboard window, click Patient audit. Step 1 of the Patient AuditWizard popup displays.Create a Patient Audit2. Enter your search criteria. Your search criteria may vary, depending on your systemconfiguration.If you enter search criteria in an invalid format, the error indicationdisplays. Hold your cursor over the indicator for details.3. When you are Finished entering search criteria, click Search for patients. If your searchreturns no results, or unexpected results, modify your search criteria and try again.Otherwise, the search results display in the Patient Audit Wizard Step 1 popup.4. Select the patient whose PHI data you want to audit.5. Click Select and continue. Step 2 of the Patient Audit Wizard popup displays.PHI Audit User Guide6. Specify a date range for the audit.Note: The date range must be no more than 30 days.•Enter dates in the required format, or• Click the drop down arrow to display a calendar from which you can select a date.7. Select the Audit actions you want to include in the PHI patient data audit. For moreinformation, refer to PHI Audit Overview.8. Click Select and review. Step 3 of the Patient Audit Wizard popup displays.Create a Patient Audit9. Review your audit's date range and Audit actions criteria, and modify as required.10. Optional - modify the Email Me When Processed field.•If you want to use the default email address for notification emails, leave the field as-is.•If you want the notification email to go to a different email address, click Clear, then enter the alternate email address.11. Click Schedule audit. The audit is scheduled, and a success window, similar to thefollowing displays.12. Click close this window. The audit wizard window closes and you are returned to thePHI Audit Dashboard window.You have successfully created and scheduled a PHI patient data audit.Create a User audit when you want to audit PHI data actions performed by a selected user. This procedure assumes you have logged in to your healthcare community and navigated to the PHI Audit Dashboard window. For details, refer to Access PHI Audit.Perform the following steps to create a user PHI Audit:1. On the PHI Audit Dashboard window, click User audit. Step 1 of the User Audit Wizardpopup displays the list of available users within your organization.2. Select the user you want to audit.Create a User Audit 3. Click Select admin and continue. Step 2 of the User Audit Wizard popup displays.4. Specify a date range for the audit. Note: The date range must be no more than 30 days.•Enter dates in the required format, or• Click the drop down arrow to display a calendar from which you can select a date.5. Select the Audit actions you want to include in the PHI user data audit. For moreinformation, refer to PHI Audit Overview.6. Click Select and review. Step 3 of the User Audit Wizard popup displays.7. Review your audit's date range and Audit actions criteria, and modify as required.PHI Audit User Guide8. Optional - modify the Email Me When Processed field.•If you want to use the default email address for notification emails, leave the field as-is.•If you want the notification email to go to a different email address, click Clear, then enter the alternate email address.9. Click Schedule audit. The audit is scheduled, and a success window, similar to thefollowing displays.10. Click close this window. The audit wizard window closes and you are returned to thePHI Audit Dashboard window.You have successfully created and scheduled a PHI user data audit.Audits display in the Scheduled audits section of the Audit Dashboard windowonly until they are processed. Audits are processed as soon as possible.You may not be able to view or cancel scheduled audits, because they havealready been moved into the processing phase.View Scheduled audits when you want to:•Review the list of audits that have not been submitted for system processing.•Cancel scheduled audits so they are not submitted for system processing.This procedure assumes you have logged in to your healthcare community and navigated to the PHI Audit Dashboard window. For details, refer to Access PHI Audit.Perform the following steps to view Scheduled audits:1. On the PHI Audit Dashboard window, scroll down the screen as required to view theScheduled audits section.•The list of scheduled audits displays, or•The "There are no scheduled audits as this time" message displays,2. Review the list of scheduled audits as required. If you want to cancel scheduled audits,continue to the next step.3. Check the Cancel check box of each audit you want to cancel.4. Click Cancel checked. A confirmation dialog displays.PHI Audit User Guide5. Click Cancel requests. The checked audits are cancelled, and will not be submitted forsystem processing.You have successfully cancelled a scheduled PHI Audit.View Processed audits when you want to:•Review the list of audits that have been processed.•View audit details.This procedure assumes you have logged in to your healthcare community and navigated to the PHI Audit Dashboard window. For details, refer to Access PHI Audit.Perform the following steps to view Processed audits:1. On the PHI Audit Dashboard window, scroll down the screen as required to view theProcessed audits section.2. Sort the audit list as required by clicking column headings. For details, refer toNavigating. the PHI Audit Dashboard.3. Click the Audit name link of the audit whose information you want to view. The AuditDetails view displays in the Audit Dashboard window. The fields available in the AuditDetails view are dependent upon the audit type:•Patient audit view•User audit viewAn example Patient Audit excerpt is shown below.4. [Optional] If you want to see more information about an audit action, click its Detailsbutton. The action's details display in a new window.[Optional] Click Create PDF file to save the audit action details as a PDF.PHI Audit User Guide5. When you are finished viewing audit action details, click Back to the audit details page.The list of audit details displays in the Audit Dashboard window.6. When you are finished viewing audit details, click Back to the main audit page. The PHIAudit Dashboard page displays.You have successfully viewed a PHI audit.The Patient Audit Details screen is organized in two sections:1. The patient section displays a summary that includes the patient's name and other keyinformation.2. The auditable actions section displays a row for each included action.•Date on which the action occurred.•The user who performed the action.•The action name.•[Optional] A link to additional details about the action.From the screen, you can:•Download the audit data in CSV (Comma Separated Values) format.•Delete the audit.•View action details by clicking a Details button.•Return to the main audit page by clicking the button.The User Audit Details screen is organized in two sections:1. The user section displays a summary that includes the user's name and other keyinformation.2. The auditable actions section displays a row for each included action. The row includes:•The date on which the action occurred.•The patient on whose data the action was performed.•The action name.•[Optional] A link to additional details about the action.From the screen, you can:•Download the audit data in CSV (Comma Separated Values) format.•Delete the audit.•View action details by clicking a Details button.•Return to the main audit page by clicking the button.You can download an audit in CSV format. CSV format files can be opened using spreadsheet software such as Microsoft Excel. There is more information in the CSV format files than can be viewed from the Audit Dashboard user interface.Perform the following steps to download audit data in *.CSV format:1. In the Processed audits section, click the Audit name link of the audit you want todownload. The patient or user Audit details display. For details, refer to View a Processed Audit.2. Click Download .csv of audit. A File Download dialog displays.3. In the File Download dialog, click Save. A Save As dialog, similar to the followingdisplays.PHI Audit User Guide4. In the Save As dialog:•Navigate to the folder in which you want to save the *.csv file.•Enter a meaningful *.csv file name.•Click Save. The file is saved to the location you selected.5. To view the saved file, open it with a spreadsheet program such as Microsoft Excel.You have successfully downloaded and viewed a PHI audit in *.csv format.Audits are automatically deleted after a configurable amount of time. Perform this procedure when you want to delete audits before they are automatically deleted.This procedure assumes you have logged in to your healthcare community and navigated to the PHI Audit Dashboard window. For details, refer to Access PHI Audit.Perform the following steps to delete audits before they are automatically deleted:1. Scroll down through the Audit Dashboard window to the Processed audits section.Note: The screen shot indicates the example system is configured to delete audits after30 days.2. Check the Delete check box of each audit you want to delete..3. Click Delete checked. A confirmation dialog, similar to the following, displays.4. Click Delete reports. The audits are deleted. The Processed audits section refreshes.RESULTYou have successfully deleted processed audits.CC S V:HComma Separated Values. A plain text format for storing tabular data. Files in CSV format can be opened by spreadsheet software such as Microsoft Excel.HIP AA:PThe Health Insurance Portability and Accountability Act.P HI:Protected Health Information - information that must be secured to meet HIPAA requirements.。
- 1、下载文档前请自行甄别文档内容的完整性,平台不提供额外的编辑、内容补充、找答案等附加服务。
- 2、"仅部分预览"的文档,不可在线预览部分如存在完整性等问题,可反馈申请退款(可完整预览的文档不适用该条件!)。
- 3、如文档侵犯您的权益,请联系客服反馈,我们会尽快为您处理(人工客服工作时间:9:00-18:30)。
5.58 Internal Control Audit Standards (AICPA solution)a. In planning an audit, an auditor's understanding of the internal control componentsshould be used to identify the types of potential misstatements that could occur, toconsider the factors affecting the risk of material misstatement, and to influence thedesign of substantive procedures.b. An auditor obtains an understanding of the design of relevant internal controlprocedures (policies and procedures) and whether they have been implemented.Assessing control risk below the maximum level further involves identifying specificcontrol procedures (policies and procedures) relevant to specific assertions that arelikely to prevent or detect material misstatements in those assertions. It also involvesperforming tests of controls to evaluate the operating design and effectiveness of theclient's control procedures.c. When seeking a further reduction in the assessed level of control risk, an auditorshould consider whether additional audit evidence s ufficient to support a furtherreduction is likely to be available, and whether it would be efficient to perform testsof controls to obtain that audit evidence.d. An auditor should document the understanding of a client's internal control systemcomponents to plan the audit. The auditor also should document the basis for theconclusion about the assessed level of control risk. If control risk is assessed at themaximum level, the auditor should document that conclusion and the reasons for it.However, if the assessed level of control risk is below the maximum level, theauditor should document the basis for the conclusion that the effectiveness of thedesign and operation of internal control procedures supports that assessed level.5.59Audit Simulation: Segregation of duties5.60 Types of audit tests6.53 The Perfect Crime?The ingenious scheme was a perfect crime for a long time. Only the greed of the embezzlerfinally tipped off the managers, who commissioned a special investigation to learn whyexpenses were high, profits low, and cash flow s mall.Ordinary everyday control activities for detection:1. Someone else taking over the embezzler's duties at vacation time might have beenless willing or able to dig out the documentation to support payment of "past due"amounts, thus leading to suspicion and maybe discovery. The embezzler avoided theproblem by clearing all the vendor payments a month before his regular vacation.2. The treasurer might have been more diligent about remembering earlier payments ofamounts later submitted as "past due," but she had other more important assignments.(In fact, the documents were just scanned and the checks were signed with amechanical signature plate.)3. Someone in charge of investigating budget variances (when they occurred) mighthave been more in tune with "thinking like a crook," but several people in severaldepartments were not that careful. The variances were not very large after the firsttwo years (although some larger ones began to show toward the end when theembezzler got greedy.)Extensive detection efforts:The embezzler was caught because he was too greedy--adverse cash flow alerted the business owner, and an investigation started.1. The investigator spent a long time reviewing the expense accounts and studyingdocumentation. He noticed fairly frequent payments of "past due" balances.2. In the course of repeated interviews with the company president, he learned about thecompany's policy of paying bills on time to obtain trade discounts. The president wassurprised to learn of the numerous incidents of past due bills.3. More searching by the investigator led to notice of five "quarterly payments" in anexpense account for the rental of a photocopy machine. This was the first obvioussign of a duplicate payment.4. The investigator asked the bank to send copies of the checks for the five payments.One proved to be payable to the embezzler. This discovery led to requests for accessto all the company's canceled checks, and the investigator then was able to findnumerous checks payable to the embezzler. The physical differences in thecompany's own checks and the embezzler's private stock were small, but they werenoticeable.5. Charges were filed. The district attorney subpoenaed the embezzler's bank accountrecords, and the bogus checks were matched with deposits.6.54 Select E ffective Extended ProceduresThese procedures are offered without explanation of the information that might be discovered.For each one, a confirmation of the suspicion might arise. One definite instance is enough tojustify proceeding with an investigation (real fraud examination), but failure to findconfirming evidence can mean (1) nothing wrong is going on, or (2) the crook is too cleverfor the auditor. All of these procedures should be conducted with care not to impugn falselythe integrity of the people under investigation.a. Count the petty cash fund on Friday morning in the presence of the supervisor andcustodian of the fund. Then, perform a second surprise count Friday afternoon beforethe custodian leaves work for the day.b. Ask the local Better Business Bureau for reports on the eight new vendors. Ask thelocal Chamber of Commerce if they are members. Look them up in the telephonebook. Telephone them, asking about business hours, product availability, and othermatters. but not in a way to arouse suspicion of investigation. Visit the businesslocation (telephone book address) to browse. Go to the local tax assessor-collectoroffice files to look up the owner of the property where the businesses are located. Ifany of the new vendors are professional people, look them up in state licensingagency directories (e.g. CPAs, attorneys, doctors). Go to the state secretary of stateoffice and look up the corporate charter to see if the purchasing agent is shown as anincorporator, officer, or director (if a large company, you can use the Standard &Poor's Register of Corporations, Directors, and Executives) . Look them up in thestate or county "assumed name" files for real names. Write a check to each business,and use the canceled check to identify the businesses' banks; then get one of thepurchasing agent's canceled payroll checks to see whether they all bank at the sameplace. (This is circumstantial evidence that needs more work, but it would be anunlikely coincidence in most cases if all of them had accounts at the same bank.)Avoid approaching the chief purchasing agent with inquiries about the new vendorapproval process because you might alert the person to the investigation.c. Select the people who have quit and determine their termination dates. In the payrollrecords, find the identification of their last paychecks (check number), then find thecanceled checks and examine the endorsement, looking for two endorsements, one ofwhich might be the payroll supervisor. Contact the terminated employees on thepretext of an exit conversation, and inquire whether they received all their paychecks,being sure to identify the last period or severance pay provision for them.d. Add the customers' subsidiary accounts and compare to the general ledger controlaccount. If clerks are giving customers proper credit in their subsidiary accounts butnot depositing the money and enabling the accounting system to credit the controlaccount, they may be out of balance. If you can identify suspicious accounts, ask thecustomers to give you originals or copies of their canceled checks so you canexamine the endorsements to see whether they appear to have been negotiated by acompany employee.e. Use the cash receipts journal date and the deposit date at the bank to see whetherthere is a pattern of delay that could indicate the cashier is holding the deposits. Lastresort is a surprise cash count at the cashier's desk to see whether cash on hand isactually on hand.7.59 RING AROUND THE REV ENUE: Overstated Sales and Accounts ReceivableThis case is a take-off on the Mattel, Inc. financial statements misstatement case.AUDIT APPROACHObjective: Obtain evidence to determine whether sales were recorded in the proper period and whether gross accounts receivable represented the amounts due from customers at year end.Control: Sales terms should be properly documented. Accounting treatment, including billing at agreed-upon prices, should follow the terms of the sale. If the risks and rewards of ownership have not been transferred to the customer, or the price has not been reliably determined, or the collectibility of the amount is seriously in doubt or not estimable, an accrual sale should not be recognized. Recorded sales should be supported by customer orders and agreements. Shipping documents should be sufficient to show actual shipment or a legitimate field warehousing arrangement.7.62 RING AROUND THE REV ENUE: Overstated Sales and Accounts Receivable(Continued)Tests of Controls: Questionnaires and inquiries should be used to determine the company'saccounting policies. If the auditors do not know about "bill and hold" practices, they shouldlearn the details. For detail procedures: Select a sample of recorded sales, and examine themfor any signs of unusual sales terms. Vouch them to customer orders and other salesagreements, if any. Vouch them to shipping documents,and examine the documents for external reliability—recognizing blank spaces (carrier name,date) and company representative's signature (two places, both company and carrier).Compare prices asked in customers' orders to prices charged on invoices. These tests followthe vouching direction—starting with data that represent the final recorded transactions (sales) and going back to find originating supporting source documents. These procedures mightreveal some transactions of the problem types—bill and hold, and overbilling. The last month of the fiscal year (although a typical seasonal low month) could be targeted for greaterattention because the sales are much higher than the previous January and because the auditors want to pay attention to sales cut-off in the last month.Select a sample of shipping documents, trace them to customer orders, and trace them toinvoices and to recording in the accounts receivable with proper amounts on the proper date.These tests follow the tracing direction—starting with data that represent the beginning oftransactions (orders, shipping) and tracing them through the company's accounting process. If extra attention is given in January for cut-off reasons, this sample might reveal some of theproblem transactions.Audit of Balance: Confirm a sample of customer accounts. Follow up exceptions noted bycustomers relating to bill and hold terms, excessive prices, and double billing. Even a fewexceptions raise red flags for the population of receivables.Use analytical comparison on comparative month's sales. Investigate any unusual fluctuations(e.g. January this year much larger than January last year, the reversal month next year withnegative sales). The January comparative increase in sales should cause auditors to extenddetail procedures on some of the month's transactions.DISCOVERY S UMMARYThe auditors performed a detail sales cut-off test on January sales, selecting a sample ofrecorded sales. However, they did not notice the significance of "bill and hold" marked on the invoices, and they did not figure out the meaning of the blank spaces and duplicate companyemployee signatures on the shipping documents.In the following year's audit, they tested sales transactions in a month when the prior year's bill and hold sales were reversed. They noticed the discrepancy but were told that it involved various billing errors. They did not connect it with reversal of the prior year's sales.The auditors confirmed a judgment sample of large accounts receivable balances. Twelve replies were received on 103 confirmations. Six of the replies were from "bill and hold" customers who listed discrepancies. The auditors followed up the six by examining sales invoices and shipping documents. They did not grasp the significance of the "bill and hold" stamps or the features of the shipping documents described earlier. Three confirmation responses indicated the customers did not owe the amounts. The auditors relied on Mattox internal documents to decide that the customers were wrong. They did not examine the sales orders that indicated that these customers had a right of cancellation.The auditors did not perform month-by-month analytical sales comparisons with the prior year. Thus they did not recognize the significant fluctuations in the comparative January sales. In the next year's audit, they did not recognize the significantcomparative decrease in month's sales for the months when the prior year bill andhold sales were reversed.。