demo_ZQB(2)
102种解密工具
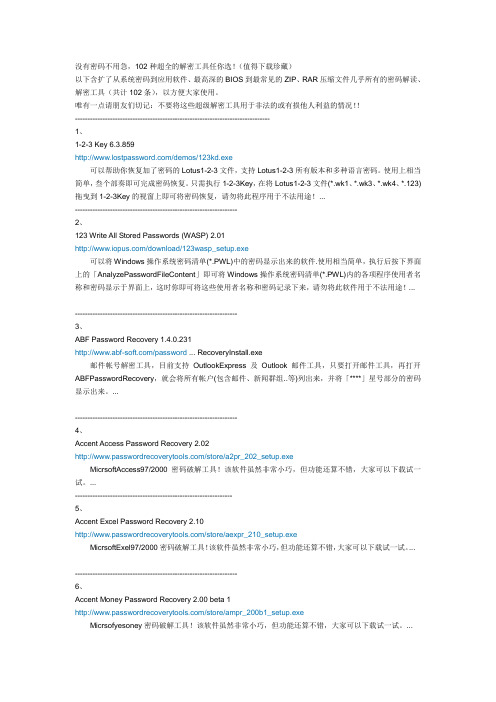
没有密码不用急,102种超全的解密工具任你选!(值得下载珍藏)以下含扩了从系统密码到应用软件、最高深的BIOS到最常见的ZIP、RAR压缩文件几乎所有的密码解读、解密工具(共计102条),以方便大家使用。
唯有一点请朋友们切记:不要将这些超级解密工具用于非法的或有损他人利益的情况!!------------------------------------------------------------------------------1、1-2-3 Key 6.3.859/demos/123kd.exe可以帮助你恢复加了密码的Lotus1-2-3文件,支持Lotus1-2-3所有版本和多种语言密码。
使用上相当简单,叁个部奏即可完成密码恢复。
只需执行1-2-3Key,在将Lotus1-2-3文件(*.wk1、*.wk3、*.wk4、*.123)拖曳到1-2-3Key的视窗上即可将密码恢复,请勿将此程序用于不法用途!...-----------------------------------------------------------------2、123 Write All Stored Passwords (WASP) 2.01/download/123wasp_setup.exe可以将Windows操作系统密码清单(*.PWL)中的密码显示出来的软件.使用相当简单,执行后按下界面上的「AnalyzePasswordFileContent」即可将Windows操作系统密码清单(*.PWL)内的各项程序使用者名称和密码显示于界面上,这时你即可将这些使用者名称和密码记录下来,请勿将此软件用于不法用途!...-----------------------------------------------------------------3、ABF Password Recovery 1.4.0.231/password ... RecoveryInstall.exe邮件帐号解密工具,目前支持OutlookExpress及Outlook邮件工具,只要打开邮件工具,再打开ABFPasswordRecovery,就会将所有帐户(包含邮件、新闻群组..等)列出来,并将「****」星号部分的密码显示出来。
电机控制开发套件motorBench 2.25说明书
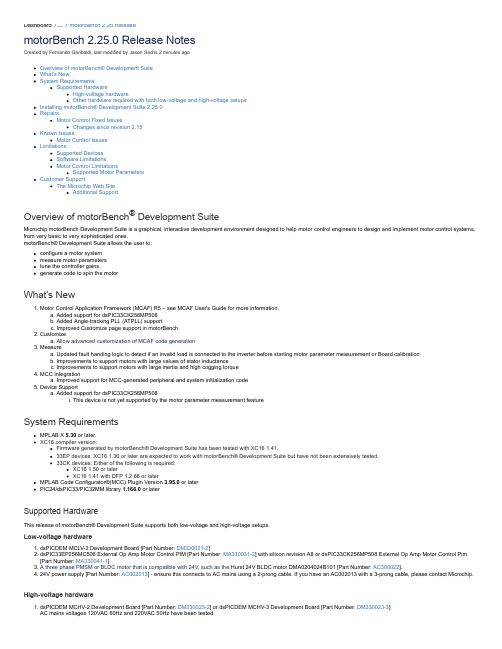
Dashboard/…/motorBench 2.25 ReleasemotorBench 2.25.0 Release NotesCreated by Fernando Garibaldi, last modified by Jason Sachs 2 minutes agoOverview of motorBench® Development SuiteWhat’s NewSystem RequirementsSupported HardwareHigh-voltage hardwareOther hardware required with both low-voltage and high-voltage setupsInstalling motorBench® Development Suite 2.25.0RepairsMotor Control Fixed IssuesChanges since revision 2.15Known IssuesMotor Control IssuesLimitationsSupported DevicesSoftware LimitationsMotor Control LimitationsSupported Motor ParametersCustomer SupportThe Microchip Web SiteAdditional SupportOverview of motorBench® Development SuiteMicrochip motorBench Development Suite is a graphical, interactive development environment designed to help motor control engineers to design and implement motor control systems, from very basic to very sophisticated ones.motorBench® Development Suite allows the user to:configure a motor systemmeasure motor parameterstune the controller gainsgenerate code to spin the motorWhat’s New1. Motor Control Application Framework (MCAF) R5 – see MCAF User's Guide for more information.a. Added support for dsPIC33CK256MP508b. Added Angle-tracking PLL (ATPLL) supportc. Improved Customize page support in motorBench2. Customizea. Allow advanced customization of MCAF code generation3. Measurea. Updated fault handing logic to detect if an invalid load is connected to the inverter before starting motor parameter measurement or Board calibrationb. Improvements to support motors with large values of stator inductancec. Improvements to support motors with large inertia and high cogging torque4. MCC Integrationa. Improved support for MCC-generated peripheral and system initialization code5. Device Supporta. Added support for dsPIC33CK256MP508i. This device is not yet supported by the motor parameter measurement featureSystem RequirementsMPLAB X 5.30 or later.XC16 compiler version:Firmware generated by motorBench® Development Suite has been tested with XC16 1.41.33EP devices: XC16 1.36 or later are expected to work with motorBench®Development Suite but have not been extensively tested.33CK devices: Either of the following is required:XC16 1.50 or laterXC16 1.41 with DFP 1.2.66 or laterMPLAB Code Configurator®(MCC) Plugin Version 3.95.0 or laterPIC24/dsPIC33/PIC32MM library 1.166.0 or laterSupported HardwareThis release of motorBench®Development Suite supports both low-voltage and high-voltage setups.Low-voltage hardware1. dsPICDEM MCLV-2 Development Board [Part Number: DM330021-2]2. dsPIC33EP256MC506 External Op Amp Motor Control PIM [Part Number: MA330031-2] with silicon revision A8 or dsPIC33CK256MP508 External Op Amp Motor Control Pim[Part Number: MA330041-1].3. A three phase PMSM or BLDC motor that is compatible with 24V, such as the Hurst 24V BLDC motor DMA0204024B101 [Part Number: AC300022].4. 24V power supply [Part Number: AC002013] - ensure this connects to AC mains using a 2-prong cable. If you have an AC002013 with a 3-prong cable, please contact Microchip.High-voltage hardware1. dsPICDEM MCHV-2 Development Board [Part Number: DM330023-2] or dsPICDEM MCHV-3 Development Board [Part Number: DM330023-3]AC mains voltages 120VAC 60Hz and 220VAC 50Hz have been tested.2. dsPIC33EP256MC506 External Op Amp Motor Control PIM [Part Number: MA330031-2] with silicon revision A8 or dsPIC33CK256MP508 External Op Amp Motor Control Pim[Part Number: MA330041-1].3. A three phase PMSM or BLDC motor that is compatible with rectified AC mains voltage, such as the Leadshine 400W BLDC motor EL5-M0400-1-24 [Part Number: AC300025].Other hardware required with both low-voltage and high-voltage setups1. A USB-to-logic-level-UART converter from the following list:a. Saelig USB-COM-U or USB-COM-U13b. TRENDnet TU-S9 v2.02. Programming tool - one of the following tools: Real ICE, ICD33. Board calibration load resistors - this is optional, please see motorBench® Development Suite User's Guide document for more detailsInstalling motorBench ® Development Suite 2.25.0To install the MPLAB ® Code Configurator v3.95 Plugin1. In the MPLAB® X IDE, select Plugins from the Tools menu2. Select the Available Plugins tab3. Check the box for the MPLAB® Code Configurator v3, and click on InstallTo install different peripheral library version or motorBench ® Development Suite version when connected to internet1. Create a project with dsPIC33EP256MC506 or dsPIC33CK256MP508, or use the sample project.2. Open MPLAB® Code Configurator3. In the Versions tab under PIC24/dsPIC33/PIC32MM MCUs, find the multiple library versions (loaded version is indicated by the green check mark)4. Right-click on the required version of the library and select Mark for Load5. In the Versions tab under motorBench ® Development Suite find the multiple library versions (loaded version is indicated by the green check mark)6. Right-click on the 2.25.0 version of the library and select Mark for Load7. Click on Load Selected Libraries button to load the marked libraries.To install different peripheral library version or motorBench® Development Suite version when not connected to internet1. In the MPLAB® X IDE, select Options from the Tools menu2. Select Plugins tab3. Click on Install Library4. Add pic24-dspic33-pic32mm_v1.166.mc3lib5. Add motorBench_2.25.0.mc3lib6. Restart MPLAB® X IDERepairsMotor Control Fixed IssuesChanges since revision 2.15The following aspects of motorBench® Development Suite and the Motor Control Application Framework (MCAF) have been updated:MCAF has been updated to R5, includingChanges in R2:Support for DC link compensationSupport for overmodulationSupport for wider range of low-voltage motorsUpdated HAL for future MCHV2 supportUpdated Motor Control LibraryNumerous minor fixesChanges in R3:MCC system module compatibilityMCHV-2 and MCHV-3 supportInverter maximum current now has a 1:1 ratio with the maximum commanded dq-frame current of the drive, operating in FOC (in R2 this incorporated a deratingfactor)Other minor fixesChanges in R4:MCC peripheral supportParameter customizationQuadrature encoder supportAdded new startup method (Weathervane startup)Other minor fixesChanges in R5:Added device support for dsPIC33CK256MP508Added Angle-tracking PLL (ATPLL) sensorless estimatorImproved motorBench Customize page supportOther minor fixesSections in this release notes affected:Other RequirementsLimitationsSupported Motor ParametersKnown IssuesPlease note:We do not recommend using the MCP2200 USB to RS232 Demo Board [Part number: MCP2200EV-VCP ] with this release of motorBench® Development Suite.While testing, we have observed more frequent occurrence of a serial communication timeout issue while running motor parameter measurement using this cable.See Known Issues section of this document for more information (MCGUI-1141)Motor parameter measurement is only supported on dsPIC33EP256MC506 device.Issue Key Summary WorkaroundMBPLAN-673Serial port does not get closed programmatically when MCC exits during motor parametermeasurementIf you exit SC during execution, restart MPLAB X.MBPLAN-932Exception during attempted creation of a runtime properties class No workaround needed, this issue doesn't have an impact on thefunctionality.MBPLAN-984Improve error reporting for SC build errors in the event of a code generation failureMBPLAN-1095Switching projects after loading motorBench erroneously allows motorBench code to generate for new projectMBPLAN-1160"Import Motor" and "Export Motor" buttons can be clicked multiple times, opening multiple dialog boxesMotor Control IssuesIssue Key SummaryDB_MC-411Current calibration happens only once (at part reset) rather than upon entry to MCSM_RESET stateDB_MC-560Speed controller exhibits chattering behavior at voltage saturation hysteresis boundary (MCAF)DB_MC-978"Soft start" gate drive in board_service.c has duty cycle that is too smallDB_MC-1092PLL estimator may not converge into rotor reference frame while using the Classic startup method in MCAFDB_MC-1396PLL calculations in code generation do not allow motor.velocity.nominal to be more than 1250Hz electrical (=20kHz/8/2)DB_MC-1415With some motors and 12V operation, increased velocity margin improves startup but creates unstable estimatorDB_MC-1430Quanum MT4012 unstable in closed-loop operation at 4200 RPM speed and aboveDB_MC-1491With Quanum MT4012, MCAF may not detect stallDB_MC-1492Quanum MT4012 Stalls on pressing 'S3'(reverse) at low speeds and on changes to speed command potentiometerDB_MC-1495Anaheim BLY342D-24V-3000, BLY342D-48V-3200 motors creates hardware over-current during stall-detect testingDB_MC-1521Closed loop speed step response overshoot - MCHV2, Leadshine 400DB_MC-1892Some motors with extreme parameters may produce out-of-range error for stall_detect.group.timerCountsVarianceDetect (detected in Monte Carlo analysis)DB_MC-1920Board service isrCount-based timing is not guaranteedDB_MC-1922LED patterns not displayed when in the TEST_DISABLE or TEST_ENABLE statesDB_MC-2122BLWS232D motor startup in QEI mode causes a false detect for stall-detectionDB_MC-2213Deadtime needs to be changed in both MCC and motorBench to affect codeDB_MC-2275Large current rampup times may not start (STARTUP_TORQUE_RAMPUP_RATE = 0)DB_MC-2309QEI tracking loop Kp and Ki produce out-of-range errors for low-speed motorsDB_MC-2323Weathervane transition state should not have active damping enabledDB_MC-2387DC link voltage measurement may have too much phase delay for MCAF DC link compensation to work effectivelyDB_MC-2606MCC-generated code has incorrect IESO/FNOSC config bits for 33CKDB_MC-2671MCAF_CaptureTimestamp calls incorrect timer function for 33CK devicesDB_MC-2785Current sense signal integrity issue with 33CK during overmodulationLimitationsSupported DevicesmotorBench® Development Suite supports these devices:1. dsPIC33EP256MC5062. dsPIC33CK256MP508Software LimitationsmotorBench® Development Suite is tested for serial communication using Windows 7 and Windows 10 platforms. Other platforms may work with standard baud rates, but this operation has not yet been verified.Motor Control LimitationsFollowing are the known limitations for this release of motorBench® Development Suite:1. One mechanical load - constant load. This represents a mechanical load with constant inertia, viscous damping, and friction. The velocity control loop can generally rejectexternal disturbance torques, within the rated current of the motor and board, and within the bandwidth of the velocity control loop. Mechanical loads with time-varying or angle-varying inertia, viscous damping, and friction, such as a blower, compressor, or pump, are currently not supported.2. One motor type - PMSMMCLV-2:The reference motor is the Nidec Hurst motor DMA0204024B101 (MicrochipDirect part number AC300022). Microchip has also validated motorBench® DevelopmentSuite (including motor parameter measurement) with motors with parameters plotted below. Please also read the following section on Supported Motor Parameters. IfmotorBench® Development Suite is unable to spin a motor successfully, please contact Microchip staff for additional assistance.(Note: Mechanical time constant (2/3)×JR/Ke² represents the time constant of velocity acceleration under an open-loop synchronous-frame voltage step, neglecting the effects of inductance, with J, R, and Ke expressed in canonical metric units. R is expressed as line-neutral resistance = half of line-line resistance, and Ke is expressed as V/(rad/s) line-neutral zero-peak = Vrms/KRPM (line-line) × 0.007796968)MCHV-2/MCHV-3:The reference motor is the Leadshine 400W motor EL5-M0400-1-24 (MicrochipDirect part number: AC300025). Microchip has validated motorBench® DevelopmentSuite (including motor parameter measurement) with motors with parameters plotted below. Please also read the following section on Supported MotorParameters. If motorBench® Development Suite is unable to spin a motor successfully, please contact Microchip staff for additional assistance.3. Boarda. dsPICDEM™ MCLV-2 development board. This release of motorBench® Development Suite is compatible with modifications to the board to alter its rated current orvoltage. Contact your local Microchip office to obtain the document "Using MCLV-2 with motorBench® Development Suite to support alternative current and/or voltageratings", which provides guidance for such modifications. Other modifications may not be compatible.b. dsPICDEM™ MCHV-2 and MCHV-3 development boards. This release of motorBench® Development Suite is compatible with unmodified MCHV-2 and MCHV-3development boards.4. Motors should be well-matched to the board and operating voltage. The nominal DC link voltage of the MCLV-2 board is 24V. This voltage can be changed by cutting jumperJ6 and using an appropriate power supply connected to the appropriate terminals of J7. Use of a mismatched motor (for example, a 12V motor used with a 24V DC link voltage) may cause a hardware over-current fault; in this case motor parameter measurement may fail with the message "Fault Code #10: Undefined Fault". Retry with an appropriate DC link voltage.5. Two PIMs and Two devices - dsPIC33EP256MC506 External OpAmp PIM with silicon revision A8 or dsPIC33CK256MP508 External OpAmp PIM. (Please see the HardwareSetup section of the motorBench User's Guide for important modifications to dsPIC33EP256MC506 External OpAmp PIM for use in MCHV-2 and MCHV-3.)6. One algorithm - FOC7. Estimators - PLL, QEI, ATPLL8. Motor parameter measurement:a. Performance criteria adjustment is not presently supported. This includes adjustment of phase margin and PI phase lag at crossover in the current loop; Microchip hasnot completed validation and documentation of these adjustments.9. Autotuning:a. Performance criteria adjustment of the current loop is not presently supported. This includes adjustment of phase margin and PI phase lag at crossover; Microchiphas not completed validation and documentation of these adjustments.b. Use of performance criteria adjustment of the velocity loop is not fully documented or tested. We recommend not adjusting phase margin or PI phase lag unlessnecessary; cases where this is likely to occur are large inertias where αJ = JR/LK m2 > 10, for which an increase of phase margin is appropriate. Phase margin valuesbetween 70 and 85 degrees are recommended in this case, with larger values providing additional stability at the cost of lower velocity bandwidth.10. Axis management not currently implemented - supports only one axis.11. Code generation:a. PWM switching frequency is fixed at 20kHz and does not reflect the value entered under Board parametersb. Integration with external user-supplied code may involve substantial changes. Some guidelines for this are given in the documentation for the Motor ControlApplication Framework. While it is possible to integrate the code generated from motorBench® Development Suite with external code, it is the responsibility of the end user to validate this combination.12. Required compiler settings:a. Optimization-O1 or greater; -O0 and -Os will both compile without errors but do not execute fast enough to complete within the 50 microsecond ADC ISR. Note: at higheroptimization levels, in-circuit debugging using MPLAB X will behave unreliably with respect to breakpoints and single-stepping through C code.The "Omit frame pointer" and "Unroll loops" settings must be enabled.b. Memory model:Large data model (handles using pointers, not direct addressing, to allow for more than 8K of program variables)Small scalar modelc. Additional options:-Wno-volatile-register-var -finlined. Test harness: In order for the test harness to be enabled, the symbols MCAF_TEST_PROFILING and MCAF_TEST_HARNESS should be defined.13. Recommended compiler settings:a. Additional options:-WundefSupported Motor ParametersSince version 2.15, motorBench®Development Suite supports a wide range of motors, subject to the following notes:Ranges of motor parameters (including rated values and computed metrics) must be within the limits noted in either range-limits-mclv2.html or range-limits-mchv2.html.These ranges were tested to ensure that code generation produced firmware constants that were within bounds.Motor parameter measurement does not need to complete successfully but valid motor parameters are required. Some motors may have too low of an inductance or resistance, and may fail motor parameter measurement.Other particular issues that may cause incompatibility with motorBench®Development Suite includeLarge inertia values – in this case, increasing voltage loop phase margin may prevent stability problems. (See "Autotuning" in the Limitations section of this document.) Rotor magnetic saliency – if there are significant differences between Ld and Lq (>10% difference) then some of the MCAF algorithms may not work optimally. Highermismatch between Ld and Lq is typically found in interior-permanent magnet (IPM) motors, and is an intentional feature of the design. See the MCAF User's Guide for more information.Large back-EMF harmonics – a quasi-sinusoidal back-emf is assumedIssues involving individual motor control algorithms, such as PLL estimator, motor startup, or stall detectionHigh cogging torqueMismatch between motor and drive (namely using a motor with current and/or voltage requirements significantly different from that of the hardware) Microchip cannot guarantee that motorBench®Development Suite will work correctly with all motors. If a particular motor does not work properly, please contact the MCU16 Motor Control Team for further guidance.Customer SupportThe Microchip Web SiteMicrochip provides online support via our web site at . This web site is used as a means to make files and information easily available to customers. Accessible by using your favorite Internet browser, the web site contains the following information:Product Support – Data sheets and errata, application notes and sample programs, design resources, user’s guides and hardware support documents, latest software releases and archived softwareGeneral Technical Support – Frequently Asked Questions (FAQs), technical support requests, online discussion groups/forums (), Microchip consultant program member listingBusiness of Microchip – Product selector and ordering guides, latest Microchip press releases, listing of seminars and events, listings of Microchip sales offices, distributors and factory representativesAdditional SupportUsers of Microchip products can receive assistance through several channels:Distributor or RepresentativeLocal Sales OfficeField Application Engineering (FAE)Technical SupportCustomers should contact their distributor, representative or field application engineer (FAE) for support. Local sales offices are also available to help customers. A listing of sales offices and locations is available on our web site.Technical support is available through the web site at: 。
编程选择题40道:Java开发环境:JDK与JRE的安装与配置.Tex

1.在Java开发环境中,JDK代表什么?o A. Java Development Keyo B. Java Development Kito C. Java Distribution Kernelo D. Java Deployment Knowledge答案: B解析: JDK全称为Java Development Kit,是Java开发工具包,包含了JRE 以及编译、调试、运行Java程序所需的各种工具。
2.JDK安装完成后,哪个环境变量是必须设置的以确保Java程序可以被编译?o A. JAVA_HOMEo B. JRE_HOMEo C. PATHo D. CLASSPATH答案: A解析: JAVA_HOME环境变量用于指向JDK的安装目录,是编译Java程序时需要的。
3.若想在命令行中运行Java程序,PATH环境变量中至少应包含JDK的哪个目录?o A. bino B. libo C. jreo D. demo答案: A解析: JDK的bin目录包含javac和java等工具,它们是编译和运行Java 程序所必需的。
4.JRE的主要组成部分中,哪一项负责解释执行Java字节码?o A. Java虚拟机(JVM)o B. Java类库o C. Java编译器o D. Java文档答案: A解析: JRE的全称是Java Runtime Environment,其中的Java虚拟机(JVM)负责解释执行Java字节码。
5.在安装JDK时,如果只安装JRE,将无法进行以下哪项操作?o A. 运行Java应用程序o B. 编译Java源代码o C. 使用Java类库o D. 调整Java程序的垃圾回收策略答案: B解析: JDK中包含了Java编译器javac,没有安装JDK就无法编译Java源代码。
6.下列选项中,哪个文件用于设置JDK的执行文件所在路径?o A. java.exeo B. javac.exeo C. path.bato D. jdk.conf答案: C解析: 在Windows系统中,通过修改path.bat文件可以设置JDK的执行文件所在的bin目录路径。
Modicon M580处理器模块数据表说明书
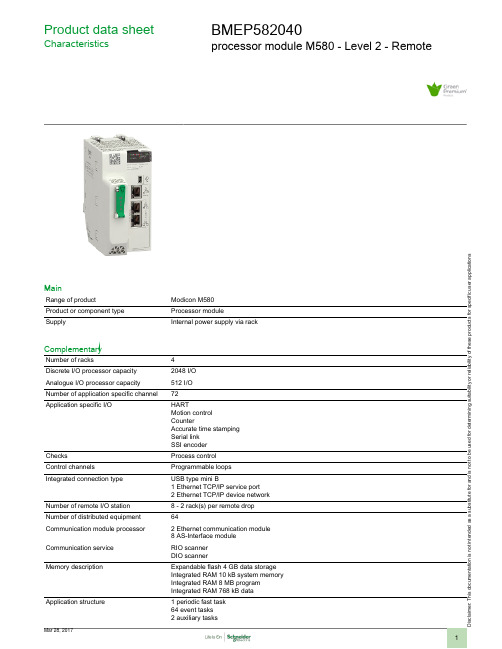
i s c la i me r : T h i s d o c u m e n t a t i o n i s n o t i n t e n d e d a s a s u b s t i t u t ef o r a n d i s n o t t o b e u s e d f o r d e t e r m i n i ng s u i t a b i l i t y o r r e l i a b i l i t y o f th e s e p r o d u c t s f o r s p e ci f i c u s e r a p p l i c a t i o n sProduct data sheetCharacteristicsBMEP582040processor module M580 - Level 2 - RemoteMainRange of productModicon M580Product or component type Processor moduleSupplyInternal power supply via rackComplementaryNumber of racks4Discrete I/O processor capacity 2048 I/O Analogue I/O processor capacity 512 I/O Number of application specific channel 72Application specific I/OHARTMotion control CounterAccurate time stamping Serial link SSI encoder ChecksProcess control Control channelsProgrammable loopsIntegrated connection typeUSB type mini B1 Ethernet TCP/IP service port2 Ethernet TCP/IP device network Number of remote I/O station 8 - 2 rack(s) per remote drop Number of distributed equipment 64Communication module processor 2 Ethernet communication module 8 AS-Interface module Communication service RIO scanner DIO scannerMemory descriptionExpandable flash 4 GB data storage Integrated RAM 10 kB system memory Integrated RAM 8 MB program Integrated RAM 768 kB data Application structure1 periodic fast task 64 event tasks2 auxiliary tasks1 cyclic/periodic master taskNumber of instructions per ms 7.5 Kinst/ms 65 % Boolean + 35 % fixed arithmetic 10 Kinst/ms 100 % Boolean Current consumption 270 mA 24 V DC MTBF reliability 600000 H Marking CEStatus LED1 LED green download in progress (DL)1 LED red memory card or CPU flash fault (BACKUP)1 LED green/red ETH MS (Ethernet port configuration status)1 LED green/red Eth NS (Ethernet network status)1 LED green processor running (RUN)1 LED red I/O module fault (I/O)1 LED red processor or system fault (ERR)Product weight0.849 kgEnvironmentAmbient air temperature for operation 0...60 °C Ambient air temperature for storage -40...85 °C Operating altitude 0...2000 m Relative humidity 5...95 %IP degree of protection IP20StandardsEN/IEC 60079-31CSA C22.2 No 142CSA C22.2 No 213 Class I Division 2EN/IEC 60079-0EN/IEC 60079-15EMC 2004/108/EC EN/IEC 61131-2LWD 2006/95/EC UL 508Product certificationsGOSTREACH directive 1907/2006/EC RCMWEEE directive 2002/96/EC Merchant NavyATEX II 3 Gas & Dust zone 2/22EACRoHS directive 2011/65/EUOffer SustainabilitySustainable offer status Green Premium productRoHS (date code: YYWW)Compliant - since 1623 - Schneider Electric declaration of conformity Schneider Electric declaration of conformity REAChReference not containing SVHC above the threshold Reference not containing SVHC above the threshold Product environmental profileAvailableProduct environmental Product end of life instructionsAvailableEnd of life manualCPU MODULE ONLYModules Mounted on Racksa:additional space below the rack to accommodate the height of the CPU. For an X Bus rack, the value is 30.9 mm (1.217 in.); for an Ethernet rack, the value b:the height of the rack. For an X Bus rack, the height is 103.7 mm (4.083 in.); for an Ethernet rack, the height is 105.11 mm (4.138 in.).c:the height of the main local rack, 134.6 mm (5.299 in.)Modules and Cables Mounted in an Enclosurea:enclosure depth: 135 mm (5.315 in.)b:wiring + module depth: > 146 mm (5.748 in.)c:wiring + module + DIN rail depth: > 156 mm (6.142 in.)d:rack height: for an X Bus rack 103.7 mm (4.083 in.); for an Ethernet rack, 105.11 mm (4.138 in.)e:module height: 134.6 mm (5.299 in.)。
Sennheiser EW-DX MKE2 SET 无线耳麦系统说明书
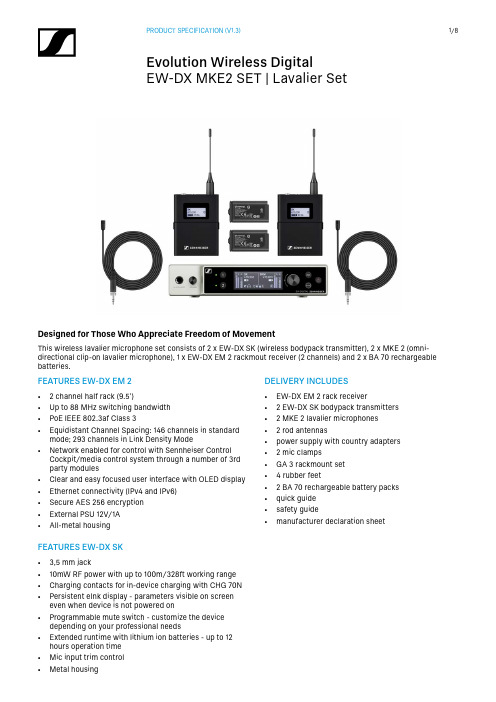
DELIVERY INCLUDES• EW-DX EM 2 rack receiver• 2 EW-DX SK bodypack transmitters • 2 MKE 2 lavalier microphones • 2 rod antennas• power supply with country adapters • 2 mic clamps • GA 3 rackmount set • 4 rubber feet• 2 BA 70 rechargeable battery packs • quick guide • safety guide• manufacturer declaration sheetFEATURES EW-DX EM 2• 2 channel half rack (9.5’)• Up to 88 MHz switching bandwidth • PoE IEEE 802.3af Class 3• Equidistant Channel Spacing: 146 channels in standardmode; 293 channels in Link Density Mode • Network enabled for control with Sennheiser ControlCockpit/media control system through a number of 3rd party modules • Clear and easy focused user interface with OLED display • Ethernet connectivity (IPv4 and IPv6)• Secure AES 256 encryption • External PSU 12V/1A • All-metal housingFEATURES EW-DX SK• 3,5 mm jack• 10mW RF power with up to 100m/328ft working range • Charging contacts for in-device charging with CHG 70N • Persistent eInk display - parameters visible on screeneven when device is not powered on • Programmable mute switch - customize the devicedepending on your professional needs • Extended runtime with lithium ion batteries - up to 12hours operation time • Mic input trim control • Metal housingDesigned for Those Who Appreciate Freedom of MovementThis wireless lavalier microphone set consists of 2 x EW-DX SK (wireless bodypack transmitter), 2 x MKE 2 (omni- directional clip-on lavalier microphone), 1 x EW-DX EM 2 rackmout receiver (2 channels) and 2 x BA 70 rechargeablebatteries.PRODUCT VARIANTSEW-DX MKE2 SET (Q1-9)470.2 - 550 MHz Art. no. 509314 EW-DX MKE2 SET (R1-9)520 - 607.8 MHz Art. no. 509315 EW-DX MKE2 SET (S1-10)606.2 - 693.8 MHz Art. no. 509316 EW-DX MKE2 SET (S2-10)614.2 - 693.8 MHz Art. no. 509319 EW-DX MKE2 SET (S4-10)630 - 693.8 MHz Art. no. 509320 EW-DX MKE2 SET (U1/5)823.2 - 831.8 MHz & 863.2 - 864.8 MHz Art. no. 509321 EW-DX MKE2 SET (V3-4)925.2 - 937.3 MHz Art. no. 509323 EW-DX MKE2 SET (V5-7)941.7 - 951.8 MHz & 953.05 - 956.05 MHz & 956.65 - 959.65 MHz Art. no. 509324 EW-DX MKE2 SET (Y1-3)1785.2 - 1799.8 MHz Art. no. 509327 ACCESSORIESEW-D ASA (Q-R-S)Active Antenna Splitter470 - 694 MHz Art. no. 508879 EW-D ASA (T-U-V-W)Active Antenna Splitter694 - 1075 MHz Art. no. 508880 EW-D ASA (X-Y)Active Antenna Splitter1350 - 1805 MHz Art. no. 508881 EW-D ASA CN/ANZ (Q-R-S)Active Antenna Splitter470 - 694 MHz Art. no. 508998EW-D AB (Q)Antenna Booster470 - 550 MHz Art. no. 508873 EW-D AB (R)Antenna Booster520 - 608 MHz Art. no. 508874 EW-D AB (S)Antenna Booster606 - 694 MHz Art. no. 508875 EW-D AB (U)Antenna Booster823 - 865 MHz Art. no. 508876 EW-D AB (V)Antenna Booster902 - 960 MHz Art. no. 508877 EW-D AB (Y)Antenna Booster1785 - 1805 MHz Art. no. 508878ADP UHF (470 - 1075 MHz)Passive directional antenna470 - 1075 MHz Art. no. 508863BA 70Rechargeable battery pack for SK and SKM-S Art. no. 508860 L 70 USB Charger for BA 70 rechargeable battery pack Art. no. 508861 EW-D CHARGING SET Set of L 70 USB charger and 2 BA 70 rechargeable battery packs Art. no. 508862 CHG 70N Network-enabled charger for SK, SKM and BA 70Art. no. 509455 CHG 70N + PSU KIT CHG 70N charger with NT 12-35 CS power supply unit Art. no. 509456 EW-D COLOR CODING SET Colored labels for wireless link identification for EM, SKM-S, SK Art. no. 508989 EW-D SK COLOR CODING Colored labels for wireless link identification for SK Art. no. 508990 EW-D SKM COLOR CODING Colored labels for wireless link identification for SKM-S Art. no. 508991 EW-D EM COLOR CODING Colored labels for wireless link identification for EM Art. no. 508992MICROPHONE COMPATIBILITYLavalier and headset microphones compatible with the EW-DX SK bodypack transmitterME 2Omni-directional lavalier microphoneModels produced from 2021 onward, featuring a gold-plated connector*ME 4Cardioid lavalier microphoneModels produced from 2021 onward, featuring a gold-plated connector*MKE Essential Omni Omni-directional lavalier microphoneMKE 2 Gold Omni-directional lavalier microphoneModels produced from 2018 onward, featuring a blue serial number plateMKE 1Omni-directional lavalier microphoneME 3Cardioid headset microphoneModels produced from 2021 onward, featuring a gold-plated connector*HSP Essential Omni Omni-directional headset microphoneHSP 2Omni-directional headset microphoneModels produced from March 2020 onward (featuring code 1090 or later)HS 2Omni-directional headset microphoneModels produced from 2021 onward, featuring a gold-plated connector*SL Headmic 1Omni-directional headset microphone* Models produced prior to 2021 will feature a nickel connector. Earlier models may pick up noise when placed close to the transmitter and are not recommended for useMKE 2 (Lavalier Microphone)Transducer principle pre-polarized condensor microphone Pick-up patternomni-directional Sensitivity (free field, no load) (1 kHz) 5 mV/Pa +- 3 dB Max. SPL at 1 kHz 142 dBFrequency response 20 to 20,000 Hz Equivalent noise level A-weighted 26 dB Connector 3.5 mm jack Cable length approx. 1.60 m Supply voltage7.5 VSPECIFICATIONSSystemAudio linkfrequency rangesQ1-9R1-9S1-10S2-10S4-10U1/5V3-4V5-7Y1-3470.2 - 550 MHz 520 - 607.8 MHz 606.2 - 693.8 MHz 614.2 - 693.8 MHz 630 - 693.8 MHz 823.2 - 831.8 MHz & 863.2 - 864.8 MHz 925.2 - 937.3 MHz 941.7 - 951.8 MHz &953.05 - 956.05 MHz &956.65 - 959.65 MHz 1785.2 - 1799.8 MHzBluetooth® Low Energy (BLE) frequency range 2402 - 2480 MHz Audio frequency response 20 Hz - 20 kHz (-3 dB)Audio THD ≤ -60 dB for 1 kHz @ -3 dBfs input level Dynamic range 134 dB System latency 1.9 ms Operating temperature -10 °C - +55 °C (14 °F - 131 °F)Relative humidity5 - 95 % (non-condensing)EW-DX EM 2 (Rack Receiver)Input voltage11 - 13 V ⎓ orPoE IEEE 802.3af Class 0(CAT5e or higher)Input current ≤ 1 ATransmit power (radiated)BLE: max. 10 mW EIRP Audio output power 18 dBu max.Headphone output 2x 70 mW @ 32 ΩEthernetRJ-45 socket, IEEE802.3100Base-TX (half+full duplex) 10Base-T (half+full duplex) (CAT5e or higher)Dimensions 212 x 44 x 189 mm (8.35" x 1.73" x 7.44")Weightapprox. 1000 g (2.2 l bs)(without antennas and power supply)EW-DX SK (Bodypack Transmitter)Input voltage 2.0 - 4.35 V Input current < 300 mAPower supply2 AA batteries 1.5 V(alkali manganese) or BA 70 rechargeable battery pack Occupied bandwidth 200 kHzTransmit power (radiated)Audio link: 10 mW ERP (Range Y1-3: 12 mW ERP)LD mode: 10 mW ERP BLE: max. 10 mW EIRP Dimensions(without antenna)63.5 x 85 x 20 mm (2.5" x 3.35" x 0.79")Weight (without batteries)approx. 115-120 g (0.26-0,27 - l bs)DIMENSIONSEW-DX EM 2DIMENSIONS EW-DX SK5907611785-1800 MHZ 203.8 / 8.02"590758941-960 MHZ 157.8 / 6.21"590757925-938 MHZ157.8 / 6.21"590756823-832 MHZ & 863-865 MHZ166.2 / 6.54"590755630-694 MHZ 195.8 / 7.71"590754614-694 MHZ195.8 / 7.71"590753606-638 MHZ & 650-694 MHZ195.8 / 7.71"590752606-694 MHZ 195.8 / 7.71"590751520-608 MHZ 217.8 / 8.57"470-550 MHZ 231.8 / 9.13"Teile-Nr.Part no.Frequenzbereich Frequency rangeL590750ARCHITECT‘S SPECIFICATIONEW-DX EM 2 rack receiverThe stationary two-channel receiver with switching diver-sity technology shall be for use with up to two companion transmitters as part of a digital wireless RF transmission system.The receiver shall operate within the following UHF fre-quency ranges, with a switching bandwidth of up to 88 MHz: 470.2 – 550 MHz, 520 – 607.8 MHz, 606.2 – 693.8 MHz, 614.2 – 693.8 MHz, 630 – 693.8 MHz, 823.2 – 831.8 MHz, 863.2 – 846.8 MHz, 925.2 – 937.3 MHz, 941.7 – 951.8 MHz, 953.05 – 956.05 MHz, 956.65 – 959.65 MHz, 1785.2 – 1799.8 MHz. Different frequency variants shall be available depending on country-specific regulations.The receiver shall feature Bluetooth® Low Energy (BLE) at a frequency range between 2402 and 2480 MHz for remote controlling the devices via a control App for iOS and And-roid.The receiver shall feature an automatic frequency setup function with spectrum scan functionality in order to es-tablish an equidistant frequency grid with 146 channels in standard mode and 293 channels in Link Density Mode. The audio frequency response shall be between 20 Hz and 20 kHz (-3 dB). Audio total harmonic distortion (THD) shall be≤****************************************** shall be 134 dB. System latency shall be 1.9 ms.The receiver shall be menu-driven with an OLED display showing the current frequency, channel number, metering of RF level, metering of AF level, lock status, muting fun-ction, antenna switching diversity, app connection, gain, audio output level, menu and battery status for each of the two associated transmitters. An auto-lock feature shallbe provided to prevent settings from being accidentally altered.The following settings shall be configurable by function buttons and an encoder for each channel in the menu: frequency, channel name, gain, trim, AF output, low cut, AES 256 encryption, test tone, network settings, integrated antenna booster settings, display brightness, device name, auto setup settings for automatic frequency setup.For each of the two channels the receiver shall feature a balanced XLR-3M audio output with a maximum outputof +18 dBu along with an unbalanced 6.3 mm (¼“) audio output with a maximum output of +12 dBu.For secure transmission the receiver shall feature AES 256 encryption.The receiver shall provide a walktest mode for monitoring the RF and AF signal status in the location over time.Two BNC-type input sockets shall be provided for connec-ting the antennas. The receiver shall be usable with active and passive wide range UHF antennas for the entire sup-ported RF spectrum.A headphone output with headphone volume control shall be provided and shall utilize a 6.3 mm stereo jack socket. The receiver shall have an Ethernet port (RJ-45) for remote network-based monitoring and control using the Sennhei-ser Control Cockpit software or the Sennheiser Wireless Systems Manager software.The receiver shall operate on 12 V DC power supplied from the power supply unit or on Power over Ethernet (PoE IEEE 802.af Class 0). Power consumption shall be ≤ 1 A.The receiver shall have a rugged metal housing; dimensi-ons shall be approximately 212 x 44 x 206 mm (8.35“ x 1.73“ x 8.11“). Weight shall be approximately 1000 grams (2.2 lbs) without antennas and power supply. Operating tempera-ture shall range from −10 °C to +50 °C (+14 °F to +122 °F). The receiver shall be the Sennheiser EW-DX EM 2.EW-DX SK bodypack transmitterThe bodypack transmitter shall be for use with a compa-nion receiver as part of a digital wireless RF transmissionsystem.The bodypack transmitter shall operate within the follo-wing UHF frequency ranges, with a switching bandwidthof up to 88 MHz: 470.2 – 550 MHz, 520 – 607.8 MHz, 606.2– 693.8 MHz, 614.2 – 693.8 MHz, 630 – 693.8 MHz, 823.2– 831.8 MHz, 863.2 – 846.8 MHz, 925.2 – 937.3 MHz, 941.7– 951.8 MHz, 953.05 – 956.05 MHz, 956.65 – 959.65 MHz,1785.2 – 1799.8 MHz. Different frequency variants shall beavailable depending on country-specific regulations.The audio frequency response shall be between 20 Hz and20 kHz (-3 dB). Audio total harmonic distortion (THD) shallbe≤******************************************shall be 134 dB. System latency shall be 1.9 ms.Occupied bandwidth shall be 200 kHz. Transmit power(radiated) shall be 10 mW ERP (1785.2 – 1799.8 MHz Range:12 mW ERP).A programmable mute switch shall be provided for mutingor unmuting either the audio signal or the radio signal. Themute switch can also be deactivated.The bodypack transmitter shall be menu-driven with abacklit eInk display showing the relevant status informati-on such as frequency, battery status or AES 256 encrypti-on status.All transmitter parameters shall be adjustable with functi-on buttons on the device itself or by Bluetooth Low Energy(BLE) synchronization via the associated receiver. The fun-ction buttons shall be lockable against accidental misuse.Power shall be supplied to the bodypack transmitter bytwo 1.5 V AA size batteries or by one Sennheiser BA 70rechargeable battery pack. Operating time shall be typical-ly 12 hours with a battery pack and up to 8 hours with AAbatteries.The bodypack transmitter shall feature charging contactsfor direct charging of the transmitter with inserted BA 70battery pack in a Sennheiser CHG 70N network-enabledcharger.The bodypack transmitter’s microphone/line input shallutilize a lockable 3.5 mm Jack socket.The bodypack transmitter shall be compatible with micro-phones for every application: Sennheiser lavalier micro-phones ME 2, ME 4, MKE 1, MKE 2 Gold and MKE EssentialOmni, Sennheiser headset microphones HS 2, HSP 2, HSPEssential Omni, ME 3 and SL Headmic 1.The bodypack transmitter shall have a rugged metalhousing; dimensions shall be approximately 63.5 x 85 x 20mm (2.5” x 3.35” x 0.79“). Weight without batteries shallbe approximately 115 - 120 grams depending on antennalength. Operating temperature shall range from −10 °C to+50 °C (+14 °F to +122 °F).The handheld transmitter shall be the SennheiserEW-DX SK.Sennheiser electronic GmbH & Co. KG · Am Labor 1 · 30900 Wedemark · Germany · 。
计算机英语常用词汇(整理版)

1常用词汇Hardware[toFBgrUQ]n.[U]金属器件,五金器具计算机辞典hardware硬件硬件Computer[hQmtdsbBfQ]n.[C]电脑,电子计算机计算机辞典computer计算机,计算机作曲计算机,Personal Computer (简称PC)个人计算机Keyboard[th`BeOBg]n.[C](打字机、钢琴等的)键盘vt.2 操作(电脑等的)的键盘;用键盘输入(讯息等)vi.用键盘进行操作计算机辞典keyboard键盘键盘mouse[mAbk]n.[C]鼠vi.捕鼠vt.仔细搜寻,搜索[(+out)]计算机辞典mouse鼠标(器)鼠标Monitor英汉主辞典[tmOn`fQ]n.[C](学校的)班长,级长vt.监控;监听;监测;监视vi.监控;监听;监测;监视计算机辞典monitor监控[督]程序,管程,监视[控]器3 监视器LCD (Liquid Crystal Display) liquid英汉主辞典[tp`hr`g]n.液体[U][C]a.液体的;液态的,流动的crystal英汉主辞典[thq`kfp]n.水晶[U]a.水晶的,水晶制的display英汉主辞典[g`tkdpT`]vt.陈列;展出n.展览,陈列;表演[C][U]计算机辞典display显示,显示器,显示画面液晶显示屏CPU (Center Processor Unit) center英汉主辞典[tkTnfQ]n.中心; 中央, 中心点vt.使集中[(+on)][H]vi.集中; 居中[(+on/upon/around)]4a.(在)中心的计算机辞典center中间对齐,居中processor英汉主辞典[tdqQbkTkQ]n.加工者;制造者计算机辞典processor处理器,处理机,处理程序unit英汉主辞典计算机辞典unit部件,元件,设备,单位中央处理单元Main boardmain英汉主辞典[mT`n]a.[Z][B]主要的,最重要的n.(自来水,煤气等的)总管道[C]main board marketph.主板市场board英汉主辞典[eOBg]n.木板;板[C]vt.用木板覆盖(或封闭)[(+up/over)]vi.搭伙,包饭;膳宿[Q]main board marketph.主板市场计算机辞典board底板,插件板,电路板主板Memory英汉主辞典[tmTmQq`]n.记忆;记忆力[U][S1][(+for)]存储器,内存RAM (Random Access Memory)random英汉主辞典[tq@ngQm]n.(现只用于at random)任意行动;随机过程[U]a.胡乱的;随便的,任意的计算机辞典random随机的access英汉主辞典[t@hkTk]n.接近,进入;接近的机会,进入的权利;使用[U][(+to)]vt.【电脑】取出(资料);使用;接近计算机辞典access存取[访问]方式,存取[访问]过程,存取能力,入口memory英汉主辞典[tmTmQq`]n.记忆;记忆力[U][S1][(+for)]随机存储器(内存) Hard Diskhard英汉主辞典[oFBg]a.硬的,坚固的ad.努力地;艰苦地hard diskph.【电脑】硬盘disk英汉主辞典[g`kh]n.[C]圆盘;盘状物;圆平面hard diskph.【电脑】硬盘计算机辞典disk磁盘hard disk硬(磁)盘硬盘Modem = Modulator-DEModulatormodulator英汉主辞典[tmOgsbpT`fQ]n.调节的人demodulator英汉主辞典[g`BtmOgsbpT`fQ]n.【电信】解调器计算机辞典demodulator解调器调制解调器,将信号由一种形式转换成另一种形式的装置BIOS (Basic – input - Output System) basic英汉主辞典[teT`k`h]a.基础的,基本的;初步的[(+to)]n.[theP]基础计算机辞典BASICBASIC语言input英汉主辞典[t`ndbf]n.投入vt.将(资料等)输入电脑计算机辞典input输入,输入数(据),输入设备output英汉主辞典[tAbfdbf]n.[C][U]出产;生产;使出;用出vt.生产;使出;输出8计算机辞典output输出(数据、过程、设备)system英汉主辞典[tk`kfQm]n.体系;系统[C]计算机辞典system系统基本输入输出系统Printer英汉主辞典[tdq`nfQ]n.[C]印刷工;印花工计算机辞典printer打印机打印机LPT (Line Printer)line1英汉主辞典[pA`n]n.[C]绳,线,索vt.用线标示;划线于vi.排队,排齐[(+up)]计算机辞典line行,线,流线,线路printer英汉主辞典[tdq`nfQ]n.[C]印刷工;印花工计算机辞典printer打印机打印口,并行口Driver英汉主辞典[tgqA`jQ]n.[C]驾驶员,司机;赶车者;马车夫计算机辞典driver驱动器,驱动程序,测试板驱动程序或驱动器AGP (Accelerate Graphics Processor)accelerate英汉主辞典[@htkTpQqT`f]vt.使增速vi.加快;增长;增加graphics英汉主辞典[tvq@i`hk]n.(用作单或复)制图法;坐标算法processor英汉主辞典[tdqQbkTkQ]n.加工者;制造者计算机辞典processor处理器,处理机,处理程序加速图形接口Resolution英汉主辞典[uqTlQtpbBXQn]n.决心;决定[C][+to-v]计算机辞典resolution分辨率,清晰度分辨率Scanner英汉主辞典[tkh@nQ]n.光电子扫描装置;扫描机计算机辞典scanner扫描仪[器],扫描程序,扫描装置扫描仪Adapter英汉主辞典[Qtg@dfQ]n.改编者;改写者计算机辞典adapter适配器,适配卡适配器(卡),俗称“卡”,如声卡、显示卡。
Java程序设计实验指导

附一、实验报告填写方法附1.1 实验开发环境1.硬件:Intel P42.4G/256M/40G PC机一套;2.软件:Windows XP+j2sdk1.5.0+JCreator Pro3.1.0+(MS Access 2000)附1.2实验过程要求1.在上课的同时,将每个实验预习的每个例题直接完成在实验指导书上;2.在实验之前,将实验要求的程序写在草稿本上;3.每次实验之前需要把实验指导书和写有程序的草稿纸带上,以备检查,否则不能进入实验室。
4.实验过程中,不能做与实验无关的事情(如:打游戏、看其他书籍),否则本次实验成绩记0分,在遇到问题的时候举手提问,同学之间交流的声音不可太大。
附1.3实验报告内容填写1.第1页:填写(1)实验目的、(2)实验要求2.第2页~第3页:填写(3)实验程序源代码3.第4页:填写(4)实验运行结果、(5)实验总结实验一:Java基础程序设计Java程序设计语言同大多数程序设计语言一样,具有一些基本特性。
本节实验主要练习Java编程语言的这些基本特性,如Java中的简单数据类型,运算符和表达式,这是学习Java语言必须经过的基础阶段。
掌握了本节实验所讲述的内容后,应该能够对Java程序的构成有一个基本的理解,能够灵活运用Java语言提供的各种数据类型和运算符。
学好Java语言必须具备扎实的语言基础,这对后续学习是很有必要的。
Java程序通过控制语句来执行程序流,完成一定的任务。
程序流是由若干个语句组成的,语句可以是单一的一条语句,也可以是用大括号{}括起来的一个复合语句。
Java中的控制语句主要有分支语句(if-else,switch).循环语句(while,do-while,for)与程序转移有关的跳转语句(break,continue,return)。
本节实验将学习如何控制程序的流程,使程序实现不同功能。
1.1实验目的:1.掌握Java语言的数据类型。
2.掌握Java语言的运算符和表达式。
ZXP Series 7

ZXP Series 7™ Card Printer SpecificationsSpecifications are provided for reference and are based on printer tests using Zebra brand consumables. Results may vary in actual application settings or when using other than recommended Zebra supplies. Zebra recommends always qualifying any application with thorough testing.Standard features• 300 dpi (11.8 dots/mm) print resolution• Image size 1006 x 640 pixels• USB 2.0 and Ethernet 10/100 connectivity• 200 card capacity feeder (30 mil)• 15 card reject hopper (30 mil)• 100 card output hopper (30 mil)• Manual feed capability• 21-character x 6-line LCD with configurable soft keys • Print Touch NFC tag for online printer help access• Kensington® secure lock slotOptional features• Single-sided laminator• FIPS 201 compliant dual-sided laminator*• 802.11 b/g wireless connectivity*• Linear barcode scannerEncoding options and specifications• Magnetic stripe encoder – AAMVA and ISO 7811 (new and pre-encoded, tracks 1, 2, and 3, high and low coercivity)* • Combined MIFARE® ISO 14443 A & B (13.56 MHz) contactless and ISO 7816 Contact Encoder with EMV level 1 certification, and PC/SC compliance*• EPCglobal® Gen 2 v2.0 (ISO/IEC18000-6C) UHF RFID smart card encoder*• ISO 7816 Smart Card Contact Station for third party external contact encoders**Field upgradable optionsSoftware• ZMotif™ SDK support and sample code for application integration in various languages and development environments• Microsoft Windows Certified printer drivers with Toolbox utility features: Windows XP (32 bit), Vista (32 and 64 bit), Server 2003 (32 bit), Windows 7 (32 and 64 bit), Server 2008 (32 and 64 bit), Windows 8 and Win 8 Pro (32 and 64 bit), Server 2012 (64 bit)• CardStudio™ card design and issuance software• Virtual PrintWare™ Printing and laminating specifications•Color dye sublimation or monochrome thermal transfer printing• Single-sided and dual-sided printing• Printing throughput:• Printing and magnetic stripe encoding throughput:NOTE: Printing throughput (cards per hour) based on batch printing with USB connectivity. Times may vary depending on the computer configuration.• Near photographic print quality• Edge-to-edge printing on standard CR-80 media• Image placement specification:Click to Drop (s) Throughput (cards/hr)Ribbon Front Back Printing Printing &LaminatingPrinting Printing &Laminating YMCKO YMCKO N/A 18 28 300 270 YMCKOK YMCKO K 21 35 225 200Mono K N/A 5 22 1375 265Mono K K 10 26 555 260 !Click to Drop (s) Throughput (cards/hr)Ribbon Front Back Printing Printing &LaminatingPrinting Printing &Laminating YMCKO YMCKO N/A 20 32 295 270 YMCKOK YMCKO K 24 38 225 195Mono K N/A 8 20 650 265Mono K K 13 26 435 260 !333 Corporate Woods ParkwayVernon Hills, IL 60061-3109 USAT: +1 847 634 6700F: +1 847 913 8766(877) 232-6799January, 2014SPECS ARE SUBJECT TO CHANGE WITHOUT NOTICE 1Zebra Technologies Corp• Simultaneous printing, encoding, and laminating capability • One-pass single-sided and dual-sided wasteless lamination • Laminate placement specification:Supplies specifications•Zebra’s intelligent technology RFID tags authenticate and automate ix Series™ ribbons and Zebra True Secure™ i Series laminate to assure the best quality possible• Card cleaning rollers are included with each ribbon carton •Specially designed cleaning supplies simplify preventative maintenance•Cleaning Kit: 12 print path and 12 feeder cleaning cards, 60,000 images•Laminator Cleaning Kit: 12 laminator card path cleaning cards, 12 cleaning swabs for media rollers, and3 laminator oven adhesive cleaning cards: 60,000 images • True Colours® ix Series™ ribbons:• YMCKO: 250 or 750 images/roll• YMCKOK: 250 or 750 images/roll• YMCUvK: 750 images/roll• panel YMC, full KO: 1250 images/roll• KdO, KrO: 2000 images/roll• WrKr: 2000 images/roll• Black monochrome: 2500 or 5000 images/roll• Blue, red, gold, silver monochrome: 5000 images/roll• White monochrome: 4000 images/roll• Scratch off gray: 3250 images/roll• True Secure™ i series laminate:•Linerless waste-free 1.0 mil top and bottom laminate: 750 images/roll• Laminate types: clear, magnetic stripe, smart card, and holographic wallpaper designs•Custom laminates with registered or wallpaper holographic images availableNOTE: For optimum print quality and printer performance, use of Zebra genuine supplies is recommended.Card specifications/compatibility• Card Thickness: 10 – 50 mil (0.25 – 1.27mm)• Card Thickness for lamination: 30 mil (0.76 mm) only• Card Size: CR-80, ISO 7810 format, Type ID-1• Card Material: PVC and composite, PET, PET-G, PET-F, and Teslin® composite• Technology cards: contact and contactless smart cards• Specialty cards: adhesive backed, signature panel, transparent cards with IR-blockerArea A: Translucent window allowable only if IRblocker is used. Key-tag holes allowed only if hole isperforated and not punched through.Area B: Translucent window is always allowable.Area C: If Magnetic stripe is present, IR blocker isrequired.Communications interfaces• USB V2.0 supports plug-n-play printer identification• 10/100 Ethernet is standard• 802.11b/g wireless connectivity is optionalElectrical specifications• Auto-switching single-phase AC power• 90V~264V AC and 47–63Hz (50-60Hz nominal)• FCC Class A• Power Consumption• Idle 100 W• Initializing / Warm-up (no Laminator) 120 W• Initializing / Warm-up (with Laminator) 450 W• Printing (no Laminator) 120 W• Printing and Laminating 250 W• Sleep 20 WPhysical characteristics• Height: 306mm (12.0in)• Width (printer only): 699mm (27.5in)• Width (printer with laminator): 964mm (38.0in)• Depth: 277mm (10.9in)• Weight (printer only): 12.2 kg (26.9 lbs)• Weight (printer with laminator): 17.9 kg (39.5 lbs) Environmental• Operating Temperature: 59º F/15ºC to 95º F/35ºC• Storage Temperature: 23º F/-5ºC to 158º F/70ºC• Operating Humidity: 20% to 80% inclusive, non-condensing • Storage Humidity: 10% to 90% inclusive, non-condensing • Media should be stored away from direct sunlight, between +5º and +30ºC, and between 30% to 50% relative humidity(877) 232-67992。
计算机文件格式(Computerfileformat)

计算机文件格式(Computer file format)PBL for PowerBuilder dynamic library to owerBuilder in the development environmentPBM can export bitmapPBR PowerBuilder resourcesPCD Kodak Photo-CD image; P-Code compiler test script, tested by Microsoft and Microsoft Visual testDOS file name of PCE Maps Eudora mailbox namePCL Hewlett-Packard printer control language file (printer standby bitmap)PCM sound file format; OKI MSM6376 synthesis chip PCM formatPCP Symantec Live Update Pro filePCS PICS animation filesPCT Macintosh PICTPCX Zsoft PC brush bitmapPDB 3Com PalmPilot database filePDD can use Paint Shop Pro or other image processing software to open graphics imagesPDF Adobe Acrobat can export document format file (available in Web browser); Microsoft system management server package definition file; NetWare printer definition filePrint Shop Deluxe file of PDP BroderbundPDQ Patton&atton Flowercharting PDQ Lite filePDS photographic image file (the source of the file format is not clear)PF Aladdin system encrypts files for private filesPFA type 1 font (ASC II)PFB type 1 font (binary)PFC PF componentsPFM printer font scalePGD good privacy (Pretty Good Privacy, PGP) virtual disk fileDrawing file of PGL HP plotterPGM can output grayscale (bitmap)PGP encrypts files with good privacy (PGP) algorithmsPH temporary files generated by the Microsoft help file compilerPHP, PHP3 contains PHP scripts with HTML pagesPHTML contains HTML pages with PHP scripts; HTML interpreted by PerlPIC PC drawing bitmap; Lotus picture; Macintosh PICT drawingPICT Macintosh PICT graphics filePIF program information file; IBM PIF drawing fileDark Forces WAD file of PIG LucasArtsPIN Epic Pinball data filePIX built-in system bitmapPJ MKS source integrity filePJX, PJT Microsoft Visual FoxPro engineering filePKG Microsoft Developer Studio application extension (similar to DLL file)Public key ring of PKR PGPPL Perl programPLG file format used by REND386/AVRILPLI Oracle 7 data descriptionPLM Discorder Tracker2 modulePLS Disorder Tracker2 sampling file; MPEG PlayList file (used by WinAmp)PLT HPGL plotter drawing file; AutoCAD plot drawing file; Gerber logo making softwarePM5 Pagemaker 5 filePM6 Pagemaker 6 filePNG portable network graphics bitmap; Paint Shop Pro browser directoryPNT, PNTG MacPaint graphics filePOG Descent2 PIG file extensionPOL Windows NT policy filePOP Visual dBASE top up filePOT Microsoft Powerpoint modulePOV ray video tracker persistencePP4 Picture Publisher 4 bitmapPPA Microsoft Powerpoint interpolatorPinnacle program file of PPF Turtle BeachPPM portable pixel mapped bitmapPPP Parson Power Publisher; Serif PagePlus desktop publishing default outputPPS Microsoft Powerpoint slide showPPT Microsoft Powerpoint presentationPQI PowerQuest driver image filePRC 3COM PalmPiltt resource (text or program) filePRE Lotus Freelance presentationPRF Windows system files, Macromedia director settings fileprg dbase clipper和foxpro程序源文件; wavmaker程序prj 3d studio (dos) 工程文件prn 打印表格 (用空格分隔的文本); datacad windows打印机文件prp oberson的prospero数据转换产品保存的工程文件prs harvard graphics for windows演示文件prt 打印格式化文件; pro / engineer元件文件prv psimail internet提供者模板文件prz lotus freelance graphics 97文件ps postscript格式化文件 (postscript打印机可读文件)the pinnacle sound bankpsd adobe photoshop位图文件a law声音文件 psi psionpsm protracker studio模型格式; epic游戏的源数据文件psp paint shop pro图像文件microsoft outlook个人文件夹文件 pstptd per / engineer表格文件ptm polytracker音乐模块 (mod) 文件pub ventura publisher出版物; microsoft publisher文档microsoft pocket word文档 pwdwindows 95口令列表文件 cpepwp photoworks图像文件 (能被photoworks浏览的一系列文件)pwz microsoft powerpoint向导pxl microsoft pocket excel电子表格py 来自yahoo的电子消息; python脚本文件pyc python脚本文件qad pf quickart文档qbw quickbooks for windows文件qdt 来自quicken uk的quickbooks数据文件, 帐目 / 税 / 货单程序qd3d apple的quickdraw 3d元文件格式qfl family lawyer文档demo version of the oic microsoft备份文件du quicktime相关图像 (mime); quicken导入文件qlb quick库qm quality motion文件microsoft查询文件 qryresults tab文件 spy quakeqt, qtm quicktime电影qti, qtif quicktime相关图像qtp quicktime优先文件qts mac pict图像文件; quicktime相关图像qtx quicktime相关图像qw symantec q & a write程序文件qxd quark xpress文件r pegasus邮件资源文件ra realaudio声音文件ram realaudio元文件rar rar压缩档案 (eugene roshall格式)ras sun光栅图像位图raw raw文件格式 (位图); raw标识的pcm数据rbh 由robohelp维持的rbh文件, 它加入到一个帮助工程文件的信息中rdf 资源描述框架文件 (涉及xml和元数据)rdl descent注册水平文件rec 录音机宏; rapidcomm声音文件reg 注册表文件visual dbase报表文件 repmicrosoft visual c + + 资源文件 resrft 可修订的表单文本 (ibm的dca一部分或文档内容框架结构一部分)rgb, sgi silicon图形rgb文件rle run length编码的位图rl2 descent2注册水平文件rm realaudio视频文件and microsoft regmaid文档rmf rich map格式 (3d游戏编辑器使用它来保存图)rmi m1d1音乐rome 基于盒式磁带的家庭游戏仿真器文件 (来自atari 2600、colecovision、sega、nintendo等盒式磁带里的rom完全拷贝, 在两个仿真器之间不可互修改)rov rescue rover数据文件rpm redhat包管理器包 (用于linux)微软Visual Basic的晶体报表文件RPTRRS王牌游戏保存的文件道路皮疹7报表RSL Borland的悖论RSM万纬履历作家恢复文件富文本格式文档RTK首映使用的用来模拟Windows帮助的搜索功能RTM实际跟踪音乐模块(MOD)文件RTS RealAudio的RTSL文档;首映对复杂操作进行加速规则是使用的扩展名作为微软扫描配置文件(MIME)8多卷档案上的RAR压缩文件(XX = 1~99间的一个数字)的汇编源代码文件s3i尖叫跟踪器V3设备S3M尖叫跟踪器V3的声音模块文件山姆8位抽样数据AMI专业文档;SAV游戏保存文件某人原始带符号字节(8位)数据该创新实验室的音色库1银行文件;(声霸卡)/动车组sonndfont X 银行文件V1。
APX500音频分析仪使用简易图解
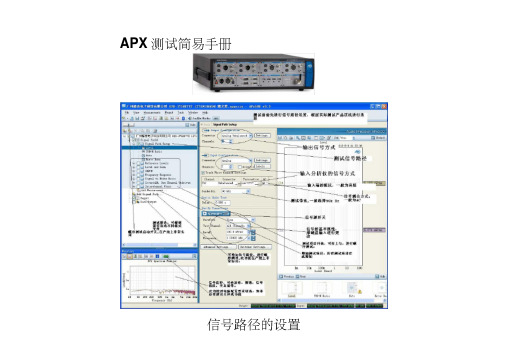
APX测试简易手册蓝牙播放器测试1. 在信号源路径中选择 bluetooth.2. 点击settings 进行配对连接。
3. 选择 A2DP Source HSP4. 点击Scan for devices 搜索被测产品5. 点击pair 进行配对6. 连接A2DP 协议7. 开始测试相关测试项目蓝牙主机 (Audio Gateway)的测试ml •嚼i*F w 口**™.“ Ij lhradn<^.lL r«i irrwT«r™iriUi>L4 血 & JC C DC kv«JE UtzSw 1-iitM-V Q DdQ ■V<rj| jp- 'lit 4*1mi"f二“_仃Tail Chicd Kll r^aravJ a VL*ar*L-R BE j»r 1__F^O-flrHia J-: 1HU*8C111h2 1-雌才播於器匕选择MSP largeL生扫描被测产品,lOOu3.配对也协议1()1005.F 1 TUrl E MXJ a❹ I LIAA 針T” E M 'EA+. □」IHweiiW L™isII |~~],_i l^val ^gfnx. □」TIM• Fr*f*w«fTT r~L 」W LP J t# Ax-34 fcvtne * L ,^J <illh,. CRmUril, I* T . _( In* vr-rlirjal fliiMbsH Fh EjL'lrwshl连接协议]片* 2fcj*:pj*. ' "“E L 「W■■Lu nln£<•:■*■_ | 5" i'Sa* njaz •.単 i© ,■ a2. 点击settings 进行配对连接。
3. 选择 A2DP link ( Hand-free 或者 headset)4. 点击Scan for devices 搜索被测产品5. 点击pair 进行配对6. 连接A2DP 协议7. 开始测试相关测试项目功放测试1. 根据实际接线,设置信号源的输出信号方式1蓝才输入测试/殛 <4閔・出rtHh P QSK I哲"出d 2T1讨2 1上i 妲曲■ *叶■ £} 电讣■!比电■卑"曲 liLF 1Li"丄/jT歼也卜_ L 丄Jf -同二I ■和三匸匹"S LK ^I L J V QJL Tmja I V I LE &Dlt| 0 ETror lai t• It hi mH Lmls • 口7 It Ou TrtlU* LJ ・J h ■电ii ・B 十二 j Sin-Jil t«[_]& gMttlJrr S rrik*i rh«r ・l Fl«4feAdj lifl H.TU MH1A*1 1上4・> ti/Lhr 4 nTf M . “li□ LoiiFh udi Tlw*.wtEIlj| 口 l|.:nnir.li|i i;® nrwchwri.J44VEDD B rJVnr< uQST F -I ^SOFT E hfi Idr-aChi选择协议-20krill p lEUsr*!、口4"財讪吓厂'-vrii rl-arZ XIBU I E打描产品hr-doL^lai rm Rf-'HraMiE M ISKI liliiii L —rl-才口打[=I J祝对AA 亍占■ hUti.JL ”. | | ■承!■'.-LlX…Filr 爭亡円岂已asuiewKn"± Preset Jpuls VflndoM Ne^>萨1 ■匕U 囹十剤J U |口I™? | 4;^Jdtls klqiln [j^a右li. _ 仙fZ P*lh "hjp::SJ :21 」-叵一g口-叵"詡壮Fxtklh叵一乳却心Fi」h他-总L.poj.Andie P-'Rci-;匚a APxB口亡£> nH T(Lat 3 D& Huth ©E TTOF□i__LU □L J—_ [TL J 匚—ELrF>T±TlCTLc^tl an 5 IH:*MFt艸4沁片久山a uCf . E£«ilJC1 *r*l 各I M Eft l4li t□CM C师二al IlwljLVsRii .* sre tiKroiBl tJ-i^i-B_j J i »j«p*4 F F■从弋用ti可□尸□咼L!(r □常□常nr □L□兰口皆□r LI ITLm4G BTBF;tl舐W E LtTel CJ. OOCOi klkDmUi^n g TOO 总-2C OK: k*k.) riiwc.4n»+K m吠轉TJBtlf .tvttl1JA Uni L ri>TO l>*fLD L at-t iu* F L I J H* ? ail ? t?F]DL'ffKitrtL™ Ptr'-dnwt Lrme-1. 理) mun Mi M«uv«Hbl .$8 63 Zh# ' Ji j *■ •Sf5+1. D|DVD、CD的测试1. 信号源设为none2. 分析仪接口设置与实际接线方式一致。
UG370:UG370 AMW007 芯片开发套件用户指南说明书

UG370: Wireless Xpress AMW007 Kit User's GuideThe AMW007 evaluation board is an excellent starting point to get familiar with the AMW007 Wi-Fi module.The evaluation board includes everything a developer needs to exercise the AMW007’s UART interface and demonstrate data transfer over Wi-Fi. The board can operate stand-alone by connecting a PC to the on-board CP2102N USB-to-UART bridge device. Alter-natively, the board can be connected to a Silicon Labs EFM8 or EFM32 starter kit, where a EFM8 or EFM32 microntroller can communicate with the AMW007 over UART.The kit includes the following:KEY FEATURES•The AMW007 can connect to an existing Wi-Fi network or be a Wi-Fi access point.•UART interface and flow control pins use Gecko OS command API to connect and communicate across Wi-Fi•Breakout test points for easy interface with prototype boards•Power sources include USB and EXP Header•AMW007 Evaluation Board • 1 x micro USB cable•Getting Started cardNo tR e co mme nd edf or N e wDe si g n s1. Getting StartedSoftwareTo set up the software for the AMW007 kit, either install Simplicity Studio, available at https:///products/development-tools/software/simplicity-studio to use Xpress Configurator or install a terminal program (e.g. Tera Term).For most userss labeled AMW007, it will not be necessary to install a virtual comm port driver in order to interface with the AMW007 kit using the on-board USB-to-UART bridge. Please see the section below for details.AMW007 evaluation boards labeled AMW007-E04.2 or higher that are connected to Windows and Linux machines should be config-ured to this driver automatically. However, if the board is not automatically recognized by the operating system, please download and install the latest version of the CP210x VCP driver: https:///products/development-tools/software/usb-to-uart-bridge-vcp-drivers HardwareTo set up the hardware for the AMW007 kit:1.Connect the micro USB cable to AMW007 board and the other end to the PC.2.Ensure the two blue LEDs labeled USB and 5V near the USB connector are on.3.Connect to the virtual COM port using the terminal program.•For Windows, use a terminal program (e.g. Tera Term) set to 115200, 8N1.•For a Mac, the terminal can be accessed using [bserial ]. There may be a modifier at the end of this for your computer.Type [bserial_modifier 115200,8n1] to set the connection to the right settings. If using a utility like CoolTerm, make sure the settings are configured to 115200, 8N1.Note that AMW007 kits labeled AMW007-E04.2 and higher that are connected to Windows or Linux machines do not require a driver to be installed in order to communicate with the board. However, if using a Mac or if the driver does not automatically install, please down-load and install the driver from https:///products/development-tools/software/usb-to-uart-bridge-vcp-drivers .No tR e co mme nd edf or N e wDe si g n sCheck the VersionAfter connecting the board to the PC and opening the terminal program, press the [[RESET]] button on the board. You should see a header with the version information for the device. Ensure this version is 2.1.5 or newer. If you find you are using an older version of firmware, perform an over the air update on the board as described on .helpThe [help ] command provides information both for commands and variables on the device.Variables are system-level variables that determine the configuration of the AMW007 mands are actions that can be taken.1.Type [help ] to see the options for the help command.2.Type [help commands ] to see a list of commands supported by this module.Figure 1.1. helpCommands used:•https:///gecko-os/latest/cmd/commands#helpNo tR e co mme nd edf or N e wDe si g n sClaiming Your DeviceThe Zentri Device Management Service (ZentriDMS) tracks GeckoOS devices, their owners, their firmware configuration and many oth-er details. The DMS handles Over-the-Air (OTA) updates, providing a secure way to update devices in the field. You need a free DMS account before using DMS features like OTA.To create an account go to the DMS Signup page. The DMS username (your email address) and password you register are used when you claim your device. To claim your device, in the terminal, issue the dms claim command:Performing an OTAUse OTA to update to the latest version of your device's GeckoOS product, or to load a development GeckoOS device with a specific GeckoOS product or version. You need to claim your device before performing an OTA. See above.To OTA, in the GeckoOS terminal, issue the ota command:For full details of the DMS claim and OTA update process, see .No tR e co mme nwDe s2. Kit Block DiagramAn overview of the AMW007 evaluation board is shown in the figure below.Wi-FiExpansionHeader From PCFigure 2.1. AMW007 Evaluation Board Block DiagramKit Block Diagram NotRecommendedforesigns3. Kit Hardware LayoutThe layout of the AMW007 evaluation board is shown below.CP2102NUSBFigure 3.1. AMW007 Evaluation Board Hardware LayoutKit Hardware LayoutNo tR e co mme nd edf or De si g n s4. Power and Operation4.1 Power SelectionThe AMW007 evaluation board is designed to be powered by two different sources:•External regulator via 5V from USB connector •External regulator via 5V from expansion headerThe figure shows how the different power sources are connected to the AMW007.Figure 4.1. AMW007 Power SupplyWhen the USB is connected, the AMW007 is powered from the external regulator, and the external regulator is powered by the USB cable.The external regulator also be powered externally through the 5V and GND pins of the expansion header when the board is attached to a power supply or an EFM MCU Starter Kit.When power is provided through the USB or an external power supply, the AMW007 module can act as a stand alone device. When it is connected to an EFM MCU Starter Kit through the expansion header, the AMW007 acts as a peripheral to the MCU.4.2 Stand-aloneIn stand-alone mode, the AMW007 on the evaluation board can be communicated with using the USB-to-UART bridge device. Simply connect to the CP2102N’s virtual COM port in a terminal program and send commands to the AMW007.Note: By default, the AMW007 communicates at 115200 baud, though this is a configurable setting.No tR e co mme nd edf or n s4.2.1 AMW007 as an Access PointTo set up the AMW007 as an access point using a terminal program:1.Connect to the AMW007 expansion board's COM port using a terminal program.2.Set/Get commands access variables that configure operation and features in the device. Type [set setup.web.ssid ] to ["GeckoOS #"], where [#] is a unique SSID that will be easy to see on a list of other SSIDs as shown in Figure 1.3. Ensure this SSID does not match any nearby SSIDs. Note that you will need quotes around the network name if it contains spaces.Note: The [Get/Set ] commands access variables that configure operation and features in the device. [Get ] reads a variable from RAM and [Set ] writes a new value to that variable in RAM.3.To read the password on the network, call [get setup.web.passkey ]. The default password is "password". Set the password for the network by calling [set setup.web.passkey ].4.Type [save ] to save the new SSID values.Note: The [save ] command saves the [ssid ] variable to flash.5.Type [setup web ] to enable the module as a Wi-Fi access point.Note: By default, Gecko OS evaluation boards are configured to enter Setup Web mode when you hold down Button 2, press Re-set, and continue to hold down Button 2 for at least three seconds.Figure 4.2. setup web / set setup.web.ssid / save / get setup.web.passkeyNo tR e co mme nd edf or N e wDe si g n s6.Configure GPIO 5 to be an input by executing the command 'gpio_dir 5 in'. Note that this is done to illustrate additional capability in step 9 of this QSG. This command is not typically required to configure your device.ing your computer or phone, connect to the Gecko OS access point [Gecko OS #] using the password.Figure 4.3. Connecting to the Gecko OS Access Pointing a web browser, go to .9.Click the [GPIOs ] area on the left side of the browser.Figure 4.4. Navigating to the Module's index.htmlNo tR e co mme nd edf or N e wDe si g n s10.Press and hold the [BUTTON 2] switch on the AMW007 board to change the GPIO toggle on the webpage. Note that the GPIOstate is able to be read because that GPIO was configured as an input earlier in this tutorial.Figure 4.5. Toggling the GPIO Using the ButtonsPlease see https:/// for a complete description of all commands and variables used in this tutorial.4.2.2 Connecting to an Existing NetworkConnecting to an Existing Network using a Terminal Program To connect to an existing Wi-Fi network using a terminal program:1.Connect to the AMW007 expansion board using a terminal program.2.If the AMW007 was previously configured as an access point, type [reboot ] to disable the AMW007 as an access point.e the [scan ] command to find all the networks in range.Figure 4.6. scanPlease see https:/// for a complete description of all commands and variables used in this tutorial.No tR e co mme nd edf or N e wDe si g n sConnecting to a NetworkThe [wlan.ssid ] and [wlan.passkey ] variables set the Wi-Fi network name and password, respectively.1.Type [set wlan.ssid "Wi-Fi network name"]. The ["Wi-Fi network name"] value is the name of the network you'd like to connect to.Note: Use quotes around the network name if it contains spaces.2.Type [set wlan.passkey password ]. The [password ] value is the password for the network defined by the ssid.3.Type [save ] to save the new values.4.Type [network_up ] to turn on the network.You should now be connected to the network.Figure 4.7. set wlan.ssid / set wlan.passkey / save / network_upNote: To automatically join the network defined by [ssid ] and [passkey ] each time the module is powered on or rebooted, type [set wlan.auto_join.enabled 1].Commands used:•https:///gecko-os/latest/cmd/commands#set •https:///gecko-os/latest/cmd/commands#save•https:///gecko-os/latest/cmd/commands#network-upNo tR e co mme nd edf or N e wDe si g n sGeckoOS includes full operating system commands like [ls -l ]. To test this out:1.Type [ls ] to get a basic file list.2.Type [ls -l ] to view the type, flags, and other information for files in the operating system filesystem.Figure 4.8. ls / ls -lPlease see https:/// for a complete description of all commands and variables used in this tutorial.No tR e co mme nd edf or N e wDe si g n sData sources like files and network sockets are called streams in GeckoOS. To read from one of these files:1.Type [ls ] to get a list of the files, if you don't already have it.e [file_open ] to open the file. Type [file_open webapp/index.html ] to open this file.3.Type [stream_list ] to view all of the open streams. Since we only have one stream open at the moment, it should have the handle of [0].4.Type [stream_read 0 100] to read 100 bytes from stream 0, or unauthorized.html.Figure 4.9. ls / file_open / stream_list / stream_readCommands used:•https:///gecko-os/latest/cmd/commands#ls•https:///gecko-os/latest/cmd/commands#file-open •https:///gecko-os/latest/cmd/commands#stream-list •https:///gecko-os/latest/cmd/commands#stream-readReading from a Website To read data from a website:1.Type [http_get ] to open a stream with the Google homepage. This should now be stream [1].2.Type [stream_read 1 1000] to read the first 1000 bytes from the site (stream 1).Figure 4.10. http_get / stream_readPlease see https:/// for a complete description of all commands and variables used in this tutorial.No tR e co mme nd edf or N e wDe si g n sClosing a Stream To close a stream:1.Type [stream_close 0] to close the open stream to the unauthorized.html file.2.Type [stream_list ] to view the open streams. The open stream to the website should be the only item in the list.Figure 4.11. stream_close / stream_listPlease see https:/// for a complete description of all commands and variables used in this tutorial.No tR e co mme nd edf or N e wDe si g n s5. PeripheralsThe starter kit has a set of peripherals that showcase some of the features of the AMW007 module.Be aware that some I/O routed to peripherals are also routed to the breakout pads. This must be taken into consideration when using the breakout pads for your application.5.1 Push Buttons and LEDsThe board includes 2 active-high LEDs and 2 mechanical buttons to exercise I/O capabilities of the AMW007. The connections are shown in the following table.Table 5.1. LEDs and Buttons Connected to AMW007No tR e co mme nd edf or N i g n s6. Connectors6.1 Test PointsThe test points located to the left and right of the module. Test points are available for the AMW007's power/ground pins, UART pins,all GPIOs, reset pin, wake pin, chip enable pin, boot select pin, and debug TX pin.Test PointsFigure 6.1. Test Points6.2 Expansion HeaderOn the left hand side of the board is a female expansion header to connect to a Silicon Labs EFM8 Starter Kit (STK). The connecter contains a number of output and communication pins that can be used to communicate with the MCU on the STK. Additionally, the 3V3and 5V power rails are also available. The figure below shows the pin assignment of the expansion header.EBID_SDA EBID_SCL See SchematicNC NC NC GPIO_5GPIO_0NC GND3V35V/RESET UART_TX*UART_RX*NC NC NC NC NCAMW007 pin Power GroundReserved (Board Identification)* Only when CP2102N UART-to-USB bridge is unpoweredTop-side view, with connector on left side of the board Figure 6.2. Expansion HeaderNo tR e co mme nd edf or N e wDe si g n s7. Simplicity StudioSimplicity Studio contains tools to configure and evaluate the AMW007.7.1 Xpress ConfiguratorXpress Configurator is a GUI tool used to configure parameters of the AMW007, save those values, and export settings in a number of useful ways.Note: All configuration of the AMW007 executes across the serial interface, and any step taken by Xpress Configurator can be repro-duced by an embedded host connected to the AMW007's UART interface.All communication between the AMW007 expansion board and the Xpress Configurator can be seen in the terminal window embedded in the Xpress Configurator tool.Figure 7.1. Simplicity Studio Xpress ConfiguratorSimplicity StudioNo tR e co mme nd edf or N e wDe si g n s8. Schematics, Assembly Drawings, and BOM8.1 Board FilesThe schematics, assembly drawings and bill of materials (BOM) for the AMW007 evaluation board are available through Simplicity Stu-dio when the kit documentation package has been installed. To access these documents, click the [Kit Documentation ] tile after se-lecting the device in the left pane.Schematics, Assembly Drawings, and BOMNo tR e co mme nd edf or N e wDe si g n sSilicon Laboratories Inc.400 West Cesar Chavez Austin, TX 78701USASimplicity StudioOne-click access to MCU and wireless tools, documentation, software, source code libraries & more. Available for Windows, Mac and Linux!IoT Portfolio /IoTSW/HW/simplicityQuality/qualitySupport and CommunityDisclaimerSilicon Labs intends to provide customers with the latest, accurate, and in-depth documentation of all peripherals and modules available for system and software implementers using or intending to use the Silicon Labs products. Characterization data, available modules and peripherals, memory sizes and memory addresses refer to each specific device, and "Typical" parameters provided can and do vary in different applications. Application examples described herein are for illustrative purposes only. Silicon Labs reserves the right to make changes without further notice and limitation to product information, specifications, and descriptions herein, and does not give warranties as to the accuracy or completeness of the included information. Silicon Labs shall have no liability for the consequences of use of the information supplied herein. This document does not imply or express copyright licenses granted hereunder to design or fabricate any integrated circuits. The products are not designed or authorized to be used within any Life Support System without the specific written consent of Silicon Labs. A "Life Support System" is any product or system intended to support or sustain life and/or health, which, if it fails, can be reasonably expected to result in significant personal injury or death. Silicon Labs products are not designed or authorized for military applications. Silicon Labs products shall under no circumstances be used in weapons of mass destruction including (but not limited to) nuclear, biological or chemical weapons, or missiles capable of delivering such weapons.Trademark InformationSilicon Laboratories Inc.® , Silicon Laboratories®, Silicon Labs®, SiLabs® and the Silicon Labs logo®, Bluegiga®, Bluegiga Logo®, Clockbuilder®, CMEMS®, DSPLL®, EFM®, EFM32®, EFR, Ember®, Energy Micro, Energy Micro logo and combinations thereof, "the world’s most energy friendly microcontrollers", Ember®, EZLink®, EZRadio®, EZRadioPRO®, Gecko®, ISOmodem®, Micrium, Precision32®, ProSLIC®, Simplicity Studio®, SiPHY®, Telegesis, the Telegesis Logo®, USBXpress®, Zentri , Z-Wave, and others are trademarks or registered trademarks of Silicon Labs. ARM, CORTEX, Cortex-M3 and THUMB are trademarks or registered trademarks of ARM Holdings. Keil is a registered trademark of ARM Limited. All other products or brand names mentioned herein are trademarks of their respective holders.No tR e co md edf or N e wDe si g n s。
200多个科研软件下载链接(百度网盘)
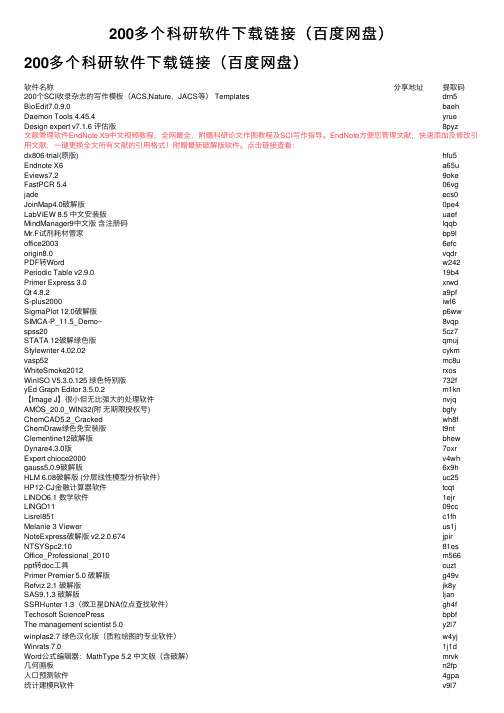
200多个科研软件下载链接(百度⽹盘)200多个科研软件下载链接(百度⽹盘)软件名称分享地址提取码200个SCI收录杂志的写作模板(ACS,Nature,JACS等) Templates drn5 BioEdit7.0.9.0baeh Daemon Tools 4.45.4yrue Design expert v7.1.6 评估版8pyz⽂献管理软件EndNote X9中⽂视频教程,全⽹最全,附赠科研论⽂作图教程及SCI写作指导。
EndNote⽅便您管理⽂献,快速添加及修改引⽤⽂献,⼀键更换全⽂所有⽂献的引⽤格式!附赠最新破解版软件。
点击链接查看:dx806-trial(原版)hfu5 Endnote X6a65u Eviews7.29oke FastPCR 5.406vg jade ecs0 JoinMap4.0破解版0pe4 LabVIEW 8.5 中⽂安装版uaef MindManager9中⽂版含注册码lqqb Mr.F试剂耗材管家bp9l office20036efc origin8.0vqdr PDF转Word w242 Periodic Table v2.9.019b4 Primer Express 3.0xrwdQt 4.8.2a9pfS-plus2000iwl6 SigmaPlot 12.0破解版p6ww SIMCA-P_11.5_Demo~8vqp spss205cz7 STATA 12破解绿⾊版qmuj Stylewriter 4.02.02cykm vasp52mc8u WhiteSmoke2012rxos WinISO V5.3.0.125 绿⾊特别版732fyEd Graph Editor 3.5.0.2m1kn 【Image J】很⼩但⽆⽐强⼤的处理软件nvjq AMOS_20.0_WIN32(附⽆期限授权号)bgfy ChemCAD5.2_Cracked wh8f ChemDraw绿⾊免安装版t9nt Clementine12破解版bhew Dynare4.3.0版7oxr Expert chioce2000v4wh gauss5.0.9破解版6x9h HLM 6.08破解版 (分层线性模型分析软件)uc25HP12-CJ⾦融计算器软件tcqt LINDO6.1 数学软件1ejr LINGO1109cc Lisrel851c1fh Melanie 3 Viewer us1j NoteExpress破解版 v2.2.0.674jpir NTSYSpc2.1081es Office_Professional_2010m566ppt转doc⼯具cuzt Primer Premier 5.0 破解版g49v Refviz 2.1 破解版jk8ySAS9.1.3 破解版ljan SSRHunter 1.3(微卫星DNA位点查找软件)gh4f Techosoft SciencePress bpbfThe management scientist 5.0y2l7 winplas2.7 绿⾊汉化版(质粒绘图的专业软件)w4yj Winrats 7.01j1d Word公式编辑器:MathType 5.2 中⽂版(含破解)mrvk⼏何画板n2fp⼈⼝预测软件4gpa统计建模R软件v9l7统计建模R软件v9l7⽂件完整性md5校验⼯具b8qa 3dBody my7m Answer Tree 绿⾊版me1y ANSYSv12.1-Win32yw31 AutoCAD_20114f09 ChemOffice v8.0.3gl5y chromas(基因测序峰图查看软件)xtqi ClustalX V2.0jo31 CurveExpert 汉化版 V1.40bay diamond 3.2i破解版6x8w Flowjo 7.6.13okn Graphical GenoTypes(图形化基因型表⽰)hmm3 GraphPad Instat V3.0544xz HSC-Chemistry65uiy Image To PDF bsgl KegArray 1.2.3(微阵列数据分析软件)njsk Latex k8ly Mathematica_8.0.4y6w2 MATLAB R2012a xyoi MDL ISISDRAW v2.5ma2h MEGA 4.1yefd TreeView s9a0 WinMDI 2.9e9mb 单位换算器42de 截图⼯具7jle竞聚率计算a48p 麦克明彩⾊⼈体解剖图谱rj9b 欧洲药典EP 7.0zjio批量⽂件改名⼯具otp3学术论⽂防抄袭检测软件qc73医师⽤药参考ecq3 Adobe Photoshop CS6 中⽂破解版ivqr Caesium 1.4.1 简体中⽂便携版ztnk CAJViewer精简绿⾊版8nyw DigitalMicrograph69de DjVuToy转换⼯具4tdr dps7.05 破解版7brd EDraw Max(亿图图⽰专家V5.0)l16c image lab 3.0 (凝胶图形分析软件)4oad Mathematics 简体中⽂版1rg2 minitab 16 破解版jmoi Multisim7绿⾊汉化版yx2h pdf分割与合并5efj (审核失败)protel2006中⽂评估版4mnw Q-Dir yraw SmartDraw6.0 绿⾊破解版pe2g T2000P ⾊谱⼯作站nvuh Tracepro7.03 破解版pur9 uvprobe v2.21 注册版fktq Visual Studio 2010+SP1(专业完美破解版)xk2r WinCVS 1.3 绿化版ps4y WinOFF 5.0.1 简体中⽂版zi2c Wondershare PDF Converter Pro 4cdu6 Zview(交流阻抗普软件)chkt 词博词典4.0 绿⾊免费版zc6p 单词随意背4zybr 鸿飞⽇记本原版5bsf 换热器设计软件9zgt 回收站恢复软件v8tn 尚品桌⾯备忘录软件2012版pu3z 新编全医药学⼤词典【绿⾊版】5m7e (图⽚批量修改器)BatchImageConvert abb2 ACD v11.0汉化绿⾊版b5ck agcain(化合物命名软件)e5y5 CEDA2.23(化⼯设备设计助⼿)ot1i DataFit(数据拟和软件)xfot DouJia ⾖荚加速器9iow engauge digitizer 4.1绿⾊版shy7engauge digitizer 4.1绿⾊版shy7 JMP v9.0.2 破解版ktv2 Latex与word相互转化⼯具gg0p MestRe-C (核磁软件)绿⾊版hc5a Microsoft Visio Premium 2010qrgv MP(分⼦模拟软件)ohah NanotubeModeler1.3.0.3(碳纳⽶管画图软件)79oy Oligo7.37 注册版n3gv PeakFit4.12 注册版copl SpinWoks 3(核磁软件)65av Surfer.v10.3.705 英⽂注册版311y win8 Pro fymi WinRAR4.2免激活版eew6爱问免积分下载器Sealove版v1.5fj7e 标准曲线计算r2r5冰点⽂库下载(百度⽂库下载器) v2.5绿⾊版5erp 定时休息护眼精灵dpjp 给⼒词典vayk 红外光谱处理软件v7em 家庭⽤药查询⼿册1.2 版9ir4结构⼒学求解器 v2.0htk1雷诺数的计算软件oolq 暖通计算软件07bu 期刊杂志全称与缩写互查的软件ejvd 图⽚去字⼯具qob9代理rik4 (BooX Viewer) 绿⾊PDG⽂件阅读器i9uu 3D字制作软件ihia 7math ncmt ASCII对照查询器ucoz ChaosPro 4.0.2491qnf discovery+5000破解版nop4 Gabedit 2.4.5txn1 Image-Pro Plus 6破解版9cm4 KinBoard 1.3mr0g Math-o-mir (数学公式编辑器 )g7qg NirLauncher⼯具箱(汉化增强版)1th8 Notepad2(汉化绿⾊版)65gr PowerPoint 基础⼊门教程o2rs QPeriodicTable6lfe RobotProg kjf1 SQL Server 数据库编程⾃学软件qjbq TC2.0库函数查询软件mka2 TextNext编程黄⾦⼿册a4su vc⼩词典2.0ijtx win7⼯具箱绿⾊版8ooq Word 基础⼊门教程3id1⼤陆⾝份证⽣成器vuxq 电脑菜鸟必备知识宝典2.0rs9f 电脑故障维修⼤全 5.0mbr8汉字内码15ug 绘图助⼿_破解版y0jb ⼏何图霸 V2.3 破解版88jx 马尔⽂粒度分析软件yy93屏幕录像专家2012 (免注册版)yf2d 迅雷⾼速通道破解版ua4i BioXM 2.6fnsg ChemSketch(化学绘图⼯具)o3vr clustalx1.81k9nd CurveSnap_V1.07jlg E-Prime 2.06qpe eNSP gl4k Excel 基础⼊门教程 2.04idc genedoc(多重序列⽐对编辑器)qr6t GIF动画制作软件 V4.23汉化绿⾊版dg71 GraphPad.Prism.v5.0.注册版ik71 LEEDpat 低能电⼦衍射图案模拟软件79iv Nero-12.0 注册版xfzxNero-12.0 注册版xfzx Novoasoft ScienceWord (附激活补丁)vb93 Protel99se zki3 SerialsWorld 3.2.10 (序列号查询器)w3i6 smile view5s6d spss statistics 17.0 中⽂版koci SumatraPDFPortable842x Texmaker 2.2 绿⾊版(LaTeX⽂件编辑软件)ptgz TheUnscrambler9.7 破解版44do Timeline Maker Professional fdrk Transcad 4.5 (绿⾊免安装版)e68h TuneUp Utilities 注册版bpwe Turbo C V2.0sm6k WinEdt.v7.0 破解版(投稿格式编辑软件)xgo1电⼦电路计算程序V1.0绿⾊免费版ca5u 公差带查询软件7flb 君扬定时器绿⾊版vz6q 执业药师(西药)资格考试宝典8.1破解版igxo 执业药师(中药)资格考试宝典9.0绿⾊破解版uq03 ABBYY FineReader 中⽂绿⾊版rw7t Calculator 科学计算器8jr8 CorelDRAW X6.1jtfe EasyRecovery Professional 汉化精简版188y Everything(硬盘搜索⼯具)2hxm FLSolutions2.0(荧光软件数据处理)ggf8 Fragstats 3.3ryzy Kindle阅读软件v1ne Materials Studio 6.0cnby MATLAB⾼阶统计量的⼯具箱xlwc MDI Jade 6.0ywsj mobi⽂件格式阅读器cgg2 office 20138hj4 PDF添加页码⼯具o5cq PDG转pdf⼯具suly voiscript (听⼒练习)m11g (审核失败)XPS格式转换⼯具35pu 草图⼤师中⽂版(SketchUp Pro) 8.0.5fgna 电⼦书转换MP3⼯具1bou 滚动截图⼯具4och 海报制作软件jvne 宏杰⽂件夹加密yi9g 化学⼯具箱V2.025169会声会影(中⽂版)q114 (审核失败)机械⼩软件合集kjaa ⼝语模拟训练软件cluy 论⽂⽂献资料搜索器5bc4拟合软件h493英语国际⾳标gjpf 正交设计助⼿ V3.1 绿⾊版gm8h Windows 8.1官⽅简体中⽂版ISO mgp3 Windows 7 官⽅简体中⽂版ISO ewag。
Silicon Labs CP210x USB-to-UART 驱动程序下载与安装指南说明书
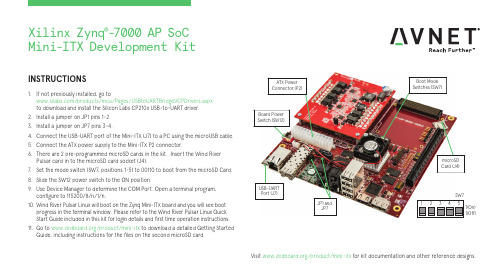
INSTRUCTIONS1. If not previously installed, go to /products/mcu/Pages/USBtoUARTBridgeVCPDrivers.aspx to download and install the Silicon Labs CP210x USB-to-UART driver.2. Install a jumper on JP1 pins 1-2.3. Install a jumper on JP7 pins 3-4.4. Connect the USB-UART port of the Mini-ITX (J7) to a PC using the microUSB cable.5. Connect the ATX power supply to the Mini-ITX P2 connector.6. There are 2 pre-programmed microSD cards in the kit. Insert the Wind River Pulsar card in to the microSD card socket (J4).7. Set the mode switch (SW7, positions 1-5) to 00110 to boot from the microSD Card.8. Slide the SW12 power switch to the ON position.9. Use Device Manager to determine the COM Port. Open a terminal program, configure to 115200/8/n/1/n.10. Wind River Pulsar Linux will boot on the Zynq Mini-ITX board and you will see boot progress in the terminal window. Please refer to the Wind River Pulsar Linux Quick Start Guide included in this kit for login details and first time operation instructions.11. Go to /product/mini-itx to download a detailed Getting Started Guide, including instructions for the files on the second microSD card.Visit /product/mini-itx for kit documentation and other reference designs.1(Off)1(On)JP1 and JP7Xilinx Zynq ®-7000 AP SoCMini-ITX Development KitAVNET DESIGN KIT LICENSE AND PRODUCT WARRANTYTHE AVNET DESIGN KIT (“DESIGN KIT” OR “PRODUCT”) AND ANY SUPPORTING DOCUMENTATION (“DOCUMENTATION” OR “PRODUCT DOCUMENTATION”) IS SUBJECT TO THIS LICENSE AGREEMENT (“LICENSE”). USE OF THE PRODUCT OR DOCUMENTATION SIGNIFIES ACCEPTANCE OF THE TERMS AND CONDITIONS OF THIS LICENSE. THE TERMS OF THIS LICENSE AGREEMENT ARE IN ADDITION TO THE AVNET CUSTOMER TERMS AND CONDITIONS, WHICH CAN BE VIEWED AT. THE TERMS OF THIS LICENSE AGREEMENT WILL CONTROL IN THE EVENT OF A CONFLICT.1. Limited License. Avnet grants You, the Customer, (“You” “Your” or “Customer”) a limited, non-exclusive, non-transferable, license to: (a) use the Product for Your own internal testing, evaluation and design efforts at a single Customer site; (c)make, use and sell the Product in a single production unit. No other rights are granted and Avnet and any other Product licensor reserves all rights not specifically granted in this License Agreement. Except as expressly permitted in this License, neither the Design Kit, Documentation, nor any portion may be reverse engineered, disassembled, decompiled, sold, donated, shared, leased, assigned, sublicensed or otherwise transferred by Customer. The term of this License is in effect until terminated. Customer may terminate this license at any time by destroying the Product and all copies of the Product Documentation.2. Changes. Avnet may make changes to the Product or Product Documentation at any time without notice. Avnet makes no commitment to update or upgrade the Product or Product Documentation and Avnet reserves the right to discontinue theProduct or Product Documentation at any time without notice.3. Product Documentation. Product Documentation is provided by Avnet on an “AS-IS” basis and does not form a part of the properties of the Product. All Product Documentation is subject to change without notice. Avnet makes no representationas to the accuracy or completeness of the Product Documentation, and DISCLAIMS ALL REPRESENTATIONS, WARRANTIES AND LIABILITIES UNDER ANY THEORY WITH RESPECT TO PRODUCT INFORMATION.4. Limited Product Warranty. AVNET WARRANTS THAT AT THE TIME OF DELIVERY, THE PRODUCTS SHALL MEET THE SPECIFICATIONS STATED IN AVNET DOCUMENTATION FOR SIXTY (60) DAYS FROM DELIVERY OF PRODUCTS. IF THE CUSTOMER CANPROVIDE PROOF THAT THE QUALIFIED AVNET PRODUCT WAS PURCHASED FOR THE PURPOSE OF AND DEPLOYED AS A COMPONENT IN THE CUSTOMER’S COMMERCIALLY AVAILABLE PRODUCT THE WARRANTY WILL BE EXTENDED TO TWELVE (12) MONTHS FROM THE DATE OF PURCHASE. TO THE EXTENT PERMITTED BY LAW, AVNET MAKES NO OTHER WARRANTY, EXPRESS OR IMPLIED, SUCH AS WARRANTY OF MERCHANTABILITY, FITNESS FOR PURPOSE OR NON-INFRINGEMENT. YOUR SOLE AND EXCLUSIVE REMEDY FOR BREACH OF AVNET’S WARRANTY IS, AT AVNET’S CHOICE: (I) REPAIR THE PRODUCTS; (ii) REPLACE THE PRODUCTS AT NO COST TO YOU; OR (iii) REFUND YOU THE PURCHASE PRICE OF PRODUCTS.5. LIMITATIONS OF LIABILITY. CUSTOMER SHALL NOT BE ENTITLED TO AND AVNET WILL NOT LIABLE FOR ANY INDIRECT, SPECIAL, INCIDENTAL OR CONSEQUENTIAL DAMAGES OF ANY KIND OR NATURE, INCLUDING, WITHOUT LIMITATION, BUSINESSINTERRUPTION COSTS, LOSS OF PROFIT OR REVENUE, LOSS OF DATA, PROMOTIONAL OR MANUFACTURING EXPENSES, OVERHEAD, COSTS OR EXPENSES ASSOCIATED WITH WARRANTY OR INTELLECTUAL PROPERTY INFRINGEMENT CLAIMS, INJURY TO REPUTATION OR LOSS OF CUSTOMERS, EVEN IF AVNET HAS BEEN ADVISED OF THE POSSIBILITY OF SUCH DAMAGES. THE PRODUCTS AND DOCUMENTATION ARE NOT DESIGNED, AUTHORIZED OR WARRANTED TO BE SUITABLE FOR USE IN MEDICAL, MILITARY, AIR CRAFT, SPACE OR LIFE SUPPORT EQUIPMENT NOR IN APPLICATIONS WHERE FAILURE OR MALFUNCTION OF THE PRODUCTS CAN REASONABLY BE EXPECTED TO RESULT IN A PERSONAL INJURY, DEATH OR SEVERE PROPERTY OR ENVIRONMENTAL DAMAGE. INCLUSION OR USE OF PRODUCTS IN SUCH EQUIPMENT OR APPLICATIONS, WITHOUT PRIOR AUTHORIZATION IN WRITING OF AVNET, IS NOT PERMITTED AND IS AT CUSTOMER’S OWN RISK. CUSTOMER AGREES TO FULLY INDEMNIFY AVNET FOR ANY DAMAGES RESULTING FROM SUCH INCLUSION OR USE.6. LIMITATION OF DAMAGES. CUSTOMER’S RECOVERY FROM AVNET FOR ANY CLAIM SHALL NOT EXCEED CUSTOMER’S PURCHASE PRICE FOR THE PRODUCT GIVING RISE TO SUCH CLAIM IRRESPECTIVE OF THE NATURE OF THE CLAIM, WHETHER INCONTRACT, TORT, WARRANTY, OR OTHERWISE.7. INDEMNIFICATION. AVNET SHALL NOT BE LIABLE FOR AND CUSTOMER SHALL INDEMNIFY, DEFEND AND HOLD AVNET HARMLESS FROM ANY CLAIMS BASED ON AVNET’S COMPLIANCE WITH CUSTOMER’S DESIGNS, SPECIFICATIONS OR IN¬STRUCTIONS,OR MODIFICATION OF ANY PRODUCT BY PARTIES OTHER THAN AVNET, OR USE IN COMBINATION WITH OTHER PRODUCTS.8. U.S. Government Restricted Rights. The Product and Product Documentation are provided with “RESTRICTED RIGHTS.” If the Product and Product Documentation and related technology or documentation are provided to or made available tothe United States Government, any use, duplication, or disclosure by the United States Government is subject to restrictions applicable to proprietary commercial computer software as set forth in FAR 52.227-14 and DFAR 252.227-7013, et seq., its successor and other applicable laws and regulations. Use of the Product by the United States Government constitutes acknowledgment of the proprietary rights of Avnet and any third parties. No other governments are authorized to use the Product without written agreement of Avnet and applicable third parties.9. Ownership. Licensee acknowledges and agrees that Avnet or Avnet’s licensors are the sole and exclusive owner of all Intellectual Property Rights in the Licensed Materials, and Licensee shall acquire no right, title, or interest in the LicensedMaterials, other than any rights expressly granted in this Agreement.10. Intellectual Property. All trademarks, service marks, logos, slogans, domain names and trade names (collectively “Marks”) are the properties of their respective owners. Avnet disclaims any proprietary interest in Marks other than its own. Avnet andAV design logos are registered trademarks and service marks of Avnet, Inc. Avnet’s Marks may be used only with the prior written permission of Avnet, Inc.11. General. The terms and conditions set forth in the License Agreement or at will apply notwithstanding any conflicting, contrary or additional terms and conditions in any purchase order, sales acknowledgement confirmation orother document. If there is any conflict, the terms of this License Agreement will control. This License may not be assigned by Customer, by operation of law, merger or otherwise, without the prior written consent of Avnet and any attempted or purported assignment shall be void. Licensee understands that portions of the Licensed Materials may have been licensed to Avnet from third parties and that such third parties are intended beneficiaries of the provisions of this Agreement. In the event any of the provisions of this Agreement are for any reason determined to be void or unenforceable, the remaining provisions will remain in full effect. This constitutes the entire agreement between the parties with respect to the use of this Product, and supersedes all prior or contemporaneous understandings or agreements, written or oral, regarding such subject matter. No waiver or modification is effective unless agreed to in writing and signed by authorized representatives of both parties. The obligations, rights, terms and conditions shall be binding on the parties and their respective successors and assigns. The License Agreement is governed by and construed in accordance with the laws of the State of Arizona excluding any law or principle, which would apply the law of any other jurisdiction. The United Nations Convention for the International Sale of Goods shall not apply.Copyright © 2017 Avnet, Inc. AVNET, "Reach Further," and the AV logo are registered trademarks of Avnet, Inc. All other brands are the property of their respective owners. LIT# 5117-QSC-AES-MINI-ITX-7Z100-BAS-G-V1。
SPOC+2 User Manual

SPOC™+2 User ManualMultichannel SPI High-Side Power ControllerAbout this documentScope and purposeThis User Manual is intended to enable users to integrate the SPOC TM+2 Software for the SPOC TM+2-Demoboard.Intended audienceThis document is intended for anyone using the SPOC TM+2 Software.Document conventionsConventions for reading the configuration class fieldThe following examples help the integrator to identify the configuration class of the parameter for a given delivery type.Abbreviations and definitionsTable of contentsAbout this document (1)Table of contents (3)Table of figures (4)1General information (5)1.1Required hardware (5)1.2Software Installation (7)1.2.1SPOC TM+2 Application (7)1.2.2µIO-Stick Driver Install (8)1.3Setup Hardware (8)1.3.1Setup details (10)2Using the software (12)2.1Starting the program (12)2.2User Interface (13)2.2.1STD-View (13)2.2.2SPI-View (14)2.3Examples: Command sequences, SPI-View (15)2.3.1Example 1: Switching on 4 lights step by step with 1 Second delay (15)2.3.2Example 2: Let one light blink 10 times (19)Revision history (23)Table of figuresFigure 1 – SPOC TM+2 MB (5)Figure 2 – SPOC TM+2 DB (5)Figure 3 - µIO-Stick (6)Figure 4 - Connection cable (6)Figure 5 - Software installation USB-Stick (7)Figure 6 – SPOC TM+2 - setup.exe (7)Figure 7 - SPOC TM+2 Application - Select Directory (7)Figure 8 – SPOC TM+2 - Application - Start Installation (8)Figure 9 – SPOC TM+2 - Application – Finish (8)Figure 10 - µIO-Updater (for vCOM) (8)Figure 11 – SPOC TM+2 DB plugged onto SPOC TM+2 MB (9)Figure 12 - Connecting µIO-Stick to SPOC TM+2 MB (9)Figure 13 - Finished setup (10)Figure 14 - Device components (11)Figure 15 - SPOC+2 - Application - Finding it (12)Figure 16 – SPOC TM+2 - Application - searching for it (12)Figure 17 - User Interface - STD-View (13)Figure 18 - User Interface - SPI-View (14)Figure 19 - Possible setup (15)Figure 20 - Select register OUT (15)Figure 21 - Write to register OUT (16)Figure 22 - Add command to command list (16)Figure 23 - Write OUT0 (16)Figure 24 - Add to command list (17)Figure 25 - change delay of cammands (17)Figure 26 - repeat until all OUTS (OUT0-OUT3) are selected (17)Figure 27 - switch to STD view (18)Figure 28 - Select channel at IS MUX (18)Figure 29 - Start command sequence (18)Figure 30 - response of SPOC TM+2 to command sequence (19)Figure 31 - Select Register OUT (19)Figure 32 - Select OUT0 and add command (20)Figure 33 - Select no output and add command (20)Figure 34 - change delay of commands (21)Figure 35 - change number of command sequences iterations (21)Figure 36 - Switch to STD view (21)Figure 37 - Select a channel at IS MUX (22)Figure 38 - Switch to SPI and start command sequence (22)Figure 39 - Response od SPOC TM+2 in response list (22)1General information 1.1Required hardwareFirst of all some special hardware is needed: ∙SPOC TM+2 MBo SPOC TM+2 Motherboardo See Figure 1Figure 1 – SPOC TM+2 MB∙SPOC TM+2 DBo Product specific (BTSxxxxx-xxxx)o See Figure 2Figure 2 – SPOC TM+2 DB∙µIO-Sticko Communication between your computer and the Demoboardo Isar Number: SP001215532o See Figure 3Figure 3 - µIO-Stick∙Connection cableo Ribbon cable16 pin female connectoro See figure 4Figure 4 - Connection cableUSB-Sticko For software installationo See Figure 5Figure 5 - Software installation USB-Stick1.2Software Installation1.2.1SPOC TM+2 ApplicationHow to install software for the SPOC TM+2 Evaluation Board:o Plug in the Software-USB-Stick into a USB port of your computero Run setup.exe in the following location:▪USB-Drive:\SPOC+2_Installer\Volume\setup.exe (see Figure 6)Figure 6 – SPOC TM+2 - setup.exe▪Note: You must log in as administrator!o Follow the steps of the Installation Wizard (see Figures below):▪Select installation directory, then click “next”Figure 7 - SPOC TM+2 Application - Select Directory▪Again click “next”Figure 8 – SPOC TM+2 - Application - Start InstallationThe installation will start, after that click …finish“Figure 9 – SPOC TM+2 - Application – Finish1.2.2µIO-Stick Driver InstallAfter installing the SPOC TM+2-Application keep the Software-USB plugged in and plug in the µIO-Stick.In order to use the virtual COM-port (neccesairy for the application) go to https://www.ehitex.de/usb-application-sticks/infineon/2529/uio-stick, scroll to Available Downloads and select Download uIO Updater (zip file) see Figure 10. Extract the zip file and run UpdatePEK afterwards.Figure 10 - µIO-Updater (for vCOM)1.3Setup HardwarePlug the SPOC TM+2 DB onto the SPOC TM+2 MB (see Figure 11)Figure 11 – SPOC TM+2 DB plugged onto SPOC TM+2 MB∙Connect the µIO-Stick to the SPOC TM+2 MB via the connector cable (see Figure 12) o Be careful: Position of Pin 1 is marked with a dot on the SPOC TM+2 MB!Figure 12 - Connecting µIO-Stick to SPOC TM+2 MB∙Connect the µIO-Stick to your computer and run the SPOC TM+2-Application. (see Figure 13)Figure 13 - Finished setup 1.3.1Setup detailsopened.2 If Jumpers J_IN2 and J_IN3 are set to 1-2: SPOC TM Outputs EDD and EDO can control the PROFET. Figure 14 - Device components2Using the software2.1Starting the programInstalled Application can be found in the windows start menu in the section “all programs” →“SPOC+2”→ SPOC+2 (see Figure 15):Figure 15 - SPOC+2 - Application - Finding itor by using the search bar(see Figure 16):Figure 16 – SPOC TM+2 - Application - searching for ito Run the program by clicking on the file (see Figures 15 and 16)2.2User Interface 2.2.1STD-ViewFigure 17 - User Interface - STD-View2.2.2SPI-ViewFigure 18 - User Interface - SPI-View*…menu description not necessairy at the moment Tobias2.3Examples: Command sequences, SPI-ViewFigure 19 below illustrates a possible test setup. The examples in 2.3.1 and 2.3.2 refer to this setup.Figure 19 - Possible setup2.3.1Example 1: Switching on 4 lights step by step with 1 Second delaySwitch to SPI view and select register OUT (See Figure 20)Figure 20 - Select register OUT∙Tick the WRITE?-Box and select no Output (See Figure 21)Figure 21 - Write to register OUT∙Click ADD CMD and your command is added to the command list (See Figure 22)Figure 22 - Add command to command list∙Select OUT0 in the WRITE-Box (See Figure 23)Figure 23 - Write OUT0∙Click ADD CMD (See Figure 24)Figure 24 - Add to command list∙Change the delay of each command to 1000 (delay of 1 second, See Figure 25)Figure 25 - change delay of cammands∙Repeat the last three steps until you reach OUT3 (See Figure 26) Figure 26 - repeat until all OUTS (OUT0-OUT3) are selected∙Switch to STD view (See Figure 27) and select a channel (0 – 3) at IS MUX (See Figure 28) Figure 27 - switch to STD viewFigure 28 - Select channel at IS MUX∙Switch back to SPI view and click the START-button (See Figure 29)Figure 29 - Start command sequence∙The response of the SPOC TM+2 is shown in the response list (See Figure 30)Figure 30 - response of SPOC TM+2 to command sequence2.3.2Example 2: Let one light blink 10 timesDescription t [ms]T_ON Duration light on 500T_OFF Duration light off 500∙Switch to SPI view and select register OUT (See Figure 31)Figure 31 - Select Register OUT∙Tick the WRITE?-Box and select OUT0 and click ADD CMD (See Figure 32)Figure 32 - Select OUT0 and add command∙Select no output in the WRITE-Box and click ADD CMD (See Figure 33)Figure 33 - Select no output and add command∙Also typing in commands directly is possible (See SPOC TM+2 datasheet for command reference) o E.g.:▪The command 80h means Write no output to OUT▪The command 81h would mean Write to OUT and set OUT0 high.▪See Figure 32 above∙Change the delay of command 81 to T_ON, the delay of command 80 to T_OFF (See Figure 34)Figure 34 - change delay of commands∙Change loop all commands x times to 10 (See Figure 35)Figure 35 - change number of command sequences iterations∙Switch to STD view (See Figure 36) and select a channel (0 – 3) at IS MUX (See Figure 37) Figure 36 - Switch to STD viewFigure 37 - Select a channel at IS MUX∙Switch back to SPI view and click the START-button (See Figure 38)Figure 38 - Switch to SPI and start command sequence∙The response of the SPOC TM+2 is shown in the response list (See Figure 39) Figure 39 - Response od SPOC TM+2 in response listRevision historyMajor changes since the last revisionTemplate revision historyNote:The below table is for reference purpose only. Delete this table before circulation. Changes since the last revisionTrademarksAll referenced product or service names and trademarks are the property of their respective owners.Edition <yyyy-mm>Doc_NumberPublished by Infineon Technologies AG 81726 Munich, Germany © 2018 Infineon Technologies AG. All Rights Reserved. Do you have a question about this document? Email: ******************** Document reference IMPORTANT NOTICEThe information given in this document shall in no event be regarded as a guarantee of conditions or characteristics (“Beschaffenheitsgarantie”) .With respect to any examples, hints or any typical values stated herein and/or any information regarding the application of the product, Infineon Technologies hereby disclaims any and all warranties and liabilities of any kind, including without limitation warranties of non-infringement of intellectual property rights of any third party.In addition, any information given in this document is subject to customer’s compliance with its obligations stated in this document and any applicable legal requirements, norms and standards concerning customer’s products and any use of the product of Infine on Technologies in customer’s applications.The data contained in this document is exclusively intended for technically trained staff. It is the responsibility of customer’s technical departments to evaluate the suitability of the product for the intended application and the completeness of theFor further information on the product, technology, delivery terms and conditions and prices please contact your nearest Infineon Technologies office ( ).WARNINGSDue to technical requirements products may contain dangerous substances. For information on the types in question please contact your nearest Infineon Technologies office.Except as otherwise explicitly approved by Infineon Technologies in a written document signed by authorized representatives of Infineon Technologies, Infineon Technologies’ products may not be used in any applications where a failure of the product or any consequences of the use thereof can reasonably be expected to result in personal injury.Mouser ElectronicsAuthorized DistributorClick to View Pricing, Inventory, Delivery & Lifecycle Information:I nfineon:SPOC2DBBTS710404ESETOBO1SPOC2DBBTS712204ESATOBO1SPOC2DBBTS712204ESETOBO1 SPOC2DBBTS722204ESATOBO1SPOC2MOTHERBOARDTOBO1SPOC2DBBTS710404ESATOBO1。
MEC8-EM-02 产品测试报告说明书

Project Number: MEC8-EM-02Tracking Code: TC0311-MEC8-EM-02-0158 Requested by: Jeremy Wooldridge Date: 3/12/2003Product Rev: 2Part #: MEC8-130-02-L-DEM2 Lot #: NONETech: Troy CookEng: John TozierPart description: MEC8-EM-02Qty to test: 50Test Start: 03/21/2003Test Completed: 4/23/2003DVTSummary ReportPART DESCRIPTIONMEC8-130-02-L-DEM2CERTIFICATIONAll instruments and measuring equipment were calibrated to National Institute for Standards and Technology (NIST) traceable standards according to IS0 10012-l and ANSI/NCSL 2540-1, as applicable.All contents contained herein are the property of Samtec. No portion of this report, in part or in full shall be reproduced without prior written approval of Samtec.SCOPETo perform the following tests: DVTAPPLICABLE DOCUMENTSStandards: EIA Publication 364TEST SAMPLES AND PREPARATION1)All materials were manufactured in accordance with the applicable product specification.2)All test samples were identified and encoded to maintain traceability throughout the test sequences.3)After soldering, the parts to be used for LLCR testing were cleaned according to TLWI-0001:a)Sample test boards are to be ultrasonically cleaned after test lead attachment, preparation and/orsoldering using the following process.b)Sample test boards are immersed into Branson 3510 cleaner containing Kyzen Ionox HC1 (orequivalent) with the following conditions:i)Temperature: ---------------55° C+/- 5° Cii)Frequency:-------------------40 KHziii)Immersion Time: ----------5 to 10 Minutesiv)Sample test boards are removed and placed into the Branson 3510 cleaner containing deionized water with the following conditions:v)Temperature:----------------55° C +/- 5° Cvi)Frequency:-------------------40 KHzvii)Immersion Time:-----------5 to 10 Minutesviii)Sample test boards are removed and placed in a beaker positioned on a hot plate with a magnetic stirrer containing deionized water warmed to 55° C +/- 5° C for 1/2 to 1 minutec)Upon removal, the sample test boards are rinsed for 1/2 to 1 minute in room temperature freeflowing deionized water.d)After the final rinse, the sample test boards are dried in an air-circulating oven for 10 to 15minutes at 50° C +/- 5° Ce)Sample test boards are then allowed to set and recover to room ambient condition prior totesting.4)Parts not intended for testing LLCR and DWV/IR are visually inspected and cleaned if necessary.5)Any additional preparation will be noted in the individual test procedures.FLOWCHARTSTEST GROUP 1a GROUP 1b GROUP 1 GROUP 1 STEP 10 Boards 10 Boards 200 test points 1 board min0.068" Card 0.056" Card 0.056" Card 6 Contacts in series,0.056" cardMother/daughter mechanical with thermal/humidity Mother/daughtermechanical withthermal/humidityContact durability withthermal/humidityMother/daughterelectrical01 Mating / Unmating Mating / Unmating LLCR-1 CCC02 Data Review Data Review Data eview03 100 Cycles100 Cycles 100 Cycles04 Mating / Unmating Mating / Unmating LLCR-205 Dataeview06 Thermal Aging07 LLCR-308 Dataeview09 Humidity10 LLCR-4Thermal Aging = EIA-364-17, Test Condition 4, 105 deg C;Time Condition 'B' (250 hours)Humidity =EIA-364-31, Test Condition B (240 Hours)and Method III (+25 ° C to +65 ° C @ 90%RH to 98% RH)delete steps 7a and 7bMating/Un-Mating Forces = EIA-364-13LLCR = EIA-364-23, LLCRuse Keithley 580 in the dry circuit mode, 10 mA MaxTabulate calculated current at RT, 75° C, 80° C and 95° Cafter derating 20% and based on 125 ° CCCC, Temp rise = EIA-364-70ATTRIBUTE DEFINITIONFollowing is a brief, simplified description of attributes.THERMAL AGING:1) EIA-364-17, Temperature Life with or without Electrical Load Test Procedure for ElectricalConnectors.a) Test Condition 4 at 105° C .b) Test Time Condition B for 250 hours. 2) Connectors are mated.CYCLIC HUMIDITY:1) Reference document: EIA-364-31, Humidity Test Procedure for Electrical Connectors.a) Test Condition B, 240 Hours.b) Method III, +25° C to + 65° C, 90% to 98% Relative Humidity excluding sub-cycles 7a and 7b. 2) Connectors are mated.TEMPERATURE RISE (Current Carrying Capacity, CCC):1) EIA-364-70, Temperature Rise versus Current Test Procedure for Electrical Connectors and Sockets .2) When current passes through a contact, the temperature of the contact increases as a result of I 2R(resistive) heating.3) The number of contacts being investigated plays a significant part in power dissipation and thereforetemperature rise.4) The size of the temperature probe can affect the measured temperature. 5) Copper traces on PC boards will contribute to temperature rise:a) Self heating (resistive)b) Reduction in heat sink capacity affecting the heated contacts 6) A de-rating curve, usually 20%, is calculated.7) Calculated de-rated currents at three temperature points are reported:a) Ambientb) 75 оCc) 80 оCd) 95 оC8) Typically, neighboring contacts (in close proximity to maximize heat build up) are energized. 9) The thermocouple (or temperature measuring probe) will be positioned at a location to sense theMAXIMUM temperature in the vicinity of the heat generation area.10) A computer program, TR 803.exe , ensures accurate stability for data acquisition.11) Hook-up wire cross section is larger than the cross section of any connector leads/PC board traces,jumpers, etc.12) Hook-up wire length is longer than the minimum specified in the referencing standard.ATTRIBUTE DEFINITIONS ContinuedMATING/UNMATING:1)Reference document: EIA-364-13, Mating and Unmating Forces Test Procedure for ElectricalConnectors.2)The full insertion position was to within 0.003” to 0.004” of the plug bottoming out in the receptacle toprevent damage to the system under test.3)One of the mating parts is secured to a floating X-Y table to prevent damage during cycling. LLCR:1)EIA-364-23, Low Level Contact Resistance Test Procedure for Electrical Connectors and Sockets.2) A computer program, LLCR 221.exe, ensures repeatability for data acquisition.3)The following guidelines are used to categorize the changes in LLCR as a result from stressinga)<= +5.0 mOhms:---------------------------Stableb)+5.1 to +10.0 mOhms:---------------------Minorc)+10.1 to +15.0 mOhms:-------------------Acceptabled)+15.1 to +50.0 mOhms:-------------------Marginale)+50.1 to +2000 mOhms:------------------Unstablef)>+2000 mOhms:----------------------------Open FailureRESULTSTemperature Rise, CCC, ) tested with the 0.056” Card•At 95°C, relative to 125°C-----------------------------------1.8 A at 20% de-rated with 6 adjacent conductors powered Mating – Unmating Forces, Stressing with 0.056” Card•Initialo MatingMin---------------------------------------4.79 lbsMax---------------------------------------8.78 lbso UnmatingMin---------------------------------------3.04 lbsMax---------------------------------------4.19 lbs•After 100 Cycleso MatingMin---------------------------------------6.05 lbsMax---------------------------------------9.03 lbso UnmatingMin---------------------------------------3.13 lbsMax---------------------------------------4.77 lbsMating – Unmating Forces, Stressing with 0.068” Card•Initialo MatingMin---------------------------------------8.23 lbsMax--------------------------------------10.56 lbso UnmatingMin---------------------------------------5.80 lbsMax---------------------------------------8.96 lbs•After 100 Cycleso MatingMin---------------------------------------9.87 lbsMax--------------------------------------13.30 lbso UnmatingMin---------------------------------------7.75 lbsMax--------------------------------------12.58 lbsLLCR Durability (200 LLCR test points) tested with the 0.056” Card•Initial---------------------------------------------------------------15.8 mOhms Max•Durability, 100 Cycleso<= +5.0 mOhms-----------------------------------200 Points-------------------------Stableo+5.1 to +10.0 mOhms-----------------------------------0 Points-------------------------Minoro+10.1 to +15.0 mOhms---------------------------------0 Points-------------------------Acceptableo+15.1 to +50.0 mOhms---------------------------------0 Points-------------------------Marginalo+50.1 to +2000 mOhms---------------------------------0 Points-------------------------Unstableo>+2000 mOhms------------------------------------------0 Points-------------------------Open Failure •Thermalo<= +5.0 mOhms-----------------------------------200 Points-------------------------Stableo+5.1 to +10.0 mOhms-----------------------------------0 Points-------------------------Minoro+10.1 to +15.0 mOhms---------------------------------0 Points-------------------------Acceptableo+15.1 to +50.0 mOhms---------------------------------0 Points-------------------------Marginalo+50.1 to +2000 mOhms---------------------------------0 Points-------------------------Unstable•Humidityo<= +5.0 mOhms-----------------------------------200 Points-------------------------Stableo+5.1 to +10.0 mOhms-----------------------------------0 Points-------------------------Minoro+10.1 to +15.0 mOhms---------------------------------0 Points-------------------------Acceptableo+15.1 to +50.0 mOhms---------------------------------0 Points-------------------------Marginalo+50.1 to +2000 mOhms---------------------------------0 Points-------------------------Unstableo>+2000 mOhms------------------------------------------0 Points-------------------------Open FailureDATAMATING/UNMATING – Stressing with the 0.056” Card:Test Date: 3/25/2003Operator: Troy CookTemperature (C): 23 Humidity (RH): 34%Equipment ID: TCT-02Load Cell ID: LC-500NPart # MEC8-EMInitial After 100 CyclesMating Unmating Mating UnmatingSample# BoardThickForce(Oz)Force(Lbs)Force(Oz)Force(Lbs)Force(Oz)Force(Lbs)Force(Oz)Force(Lbs)1 0.0595 107.5 6.716 62.1 3.881 135.6 8.478 76.3 4.7672 0.0580 76.7 4.791 48.6 3.036 131.7 8.233 57.8 3.6123 0.0600 108.0 6.748 58.2 3.640 130.2 8.137 59.3 3.7074 0.0580 89.6 5.597 57.6 3.597 133.2 8.328 62.4 3.8995 0.0600 140.5 8.781 67.0 4.185 144.5 9.030 69.5 4.3436 0.0580 87.7 5.482 50.5 3.154 136.4 8.522 54.9 3.4337 0.0585 82.2 5.136 54.2 3.390 96.7 6.045 50.1 3.1348 0.0600 92.8 5.803 54.9 3.433 105.7 6.604 54.8 3.4259 0.0595 96.1 6.004 53.9 3.367 123.9 7.746 55.3 3.45410 0.0580 83.0 5.185 54.4 3.403 126.0 7.872 57.3 3.579MATING/UNMATING – Stressing with the 0.068” Card:Test Date: 3/25/2003Operator: Troy CookTemperature (C): 22 Humidity (RH): 34%Equipment ID: TCT-02Load Cell ID: LC-500NPart # MEC8-EMInitial After 100 Cycles Mating Unmating Mating UnmatingSample# BoardThickForce(Oz)Force(Lbs)Force(Oz)Force(Lbs)Force(Oz)Force(Lbs)Force(Oz)Force(Lbs)1 0.0655 138.8 8.672 125.1 7.821 162.2 10.140 158.8 9.9222 0.0665 169.0 10.560 136.9 8.555 180.5 11.280 139.3 8.7073 0.0665 134.3 8.394 126.5 7.904 172.5 10.780 172.5 10.7804 0.0670 158.1 9.884 143.4 8.964 212.8 13.300 201.3 12.5805 0.0660 146.4 9.149 129.4 8.090 210.9 13.180 190.7 11.9206 0.0660 147.6 9.227 131.9 8.242 190.6 11.910 175.8 10.9907 0.0665 136.8 8.549 103.1 6.442 159.4 9.964 126.4 7.8998 0.0660 134.2 8.388 129.4 8.090 181.9 11.370 177.0 11.0609 0.0655 135.5 8.469 116.8 7.299 158.0 9.872 137.9 8.62110 0.0660 131.6 8.227 92.8 5.797 157.9 9.866 123.9 7.746LLCR:Date Mar. 212003Apr. 072003Apr. 072003Apr. 222003RoomTempC20 20 21 20RH50% 43% 45% 46% Name Troy Cook Troy Cook Troy Cook Troy Cook mOhmvalues Actual Delta Delta DeltaBoard Position Initial100Cycles Thermal Humidity1 P1 17.2 -0.3 0.1 0.9 1 P2 17.1 -0.6 -0.2 0.4 1 P3 17.1 -0.3 0.1 0.5 1 P4 17.2 -0.5 -0.2 1.2 1 P5 17.0 -0.2 0.1 0.4 1 P6 16.8 0.5 1.1 1.0 1 P7 17.3 -0.3 0.1 1.6 1 P8 16.8 0.3 1.0 0.7 1 P9 17.1 -0.7 -0.3 -0.5 1 P10 16.4 0.2 0.6 0.7 1 P11 16.6 0.3 0.4 1.4 1 P12 16.8 0.0 0.7 0.5 1 P13 16.8 -0.1 0.2 0.2 1 P14 16.8 0.1 0.5 3.6 1 P15 16.3 0.5 1.1 3.3 1 P16 16.4 0.5 1.0 2.5 1 P17 16.7 0.4 0.9 3.7 1 P18 16.5 0.8 1.4 2.3 1 P19 17.3 -0.5 0.0 1.5 1 P20 16.6 0.7 1.0 3.3 1 P21 17.1 0.0 0.4 1.1 1 P22 16.9 0.2 0.4 0.2 1 P23 16.9 0.1 0.5 0.2 1 P24 16.8 0.8 1.1 1.21 P25 16.6 1.0 1.6 1.32 P1 17.5 0.2 0.1 2.0 2 P2 17.1 0.2 0.1 0.6 2 P3 17.1 0.4 0.3 0.3 2 P4 16.8 0.5 0.4 0.5 2 P5 16.8 0.5 0.6 0.6 2 P6 17.3 -0.2 -0.2 0.2 2 P7 17.0 0.2 0.2 0.5 2 P8 17.0 0.1 0.1 0.2 2 P9 16.4 0.5 0.6 0.6 2 P10 16.7 0.6 0.9 0.9 2 P11 16.8 0.1 0.3 0.42 P13 16.7 0.5 0.6 1.2 2 P14 16.8 0.2 0.6 0.8 2 P15 16.8 0.0 0.4 0.5 2 P16 17.3 -0.6 -0.1 -0.2 2 P17 16.7 -0.1 0.3 0.4 2 P18 17.1 0.0 0.3 0.5 2 P19 16.9 0.3 0.6 0.8 2 P20 16.9 0.6 0.8 1.0 2 P21 17.9 -1.2 -0.9 -0.8 2 P22 17.7 -1.0 -0.6 -0.4 2 P23 17.7 -0.8 -0.6 -0.6 2 P24 17.4 -0.2 -0.2 0.22 P25 17.9 -0.4 -0.3 1.03 P1 17.3 0.1 0.1 0.5 3 P2 17.2 0.0 0.0 0.4 3 P3 18.0 -1.0 -0.7 -0.7 3 P4 17.9 -0.9 -0.6 -0.5 3 P5 18.3 -0.7 -0.5 -0.5 3 P6 17.3 -0.5 -0.1 -0.2 3 P7 16.8 -0.1 0.3 0.3 3 P8 17.3 -0.4 0.0 -0.1 3 P9 16.8 -0.4 0.2 -0.1 3 P10 17.5 -0.5 0.0 -0.3 3 P11 17.2 -0.2 0.5 0.1 3 P12 17.2 -0.8 -0.3 -0.4 3 P13 17.1 -0.4 0.1 -0.1 3 P14 16.7 0.2 0.6 0.7 3 P15 18.3 -1.7 -1.1 -1.3 3 P16 17.9 -1.7 -1.0 -1.1 3 P17 16.7 -0.2 0.1 0.0 3 P18 17.2 -0.1 0.4 0.2 3 P19 16.9 -0.3 0.2 0.1 3 P20 16.9 0.4 0.7 0.8 3 P21 19.0 -1.5 -1.4 -1.0 3 P22 18.4 -1.1 -0.9 -0.7 3 P23 17.9 -0.8 -0.5 -0.5 3 P24 17.7 -0.8 -0.6 0.33 P25 17.0 0.3 0.5 0.84 P1 18.0 -0.3 0.2 0.1 4 P2 17.5 0.0 0.0 0.6 4 P3 17.6 -0.2 -0.1 0.2 4 P4 17.5 0.2 0.2 1.0 4 P5 17.8 0.1 0.0 1.0 4 P6 17.9 -1.0 -0.6 -0.4 4 P7 17.8 -0.8 0.1 0.1 4 P8 17.6 -0.5 0.0 0.8 4 P9 17.4 -0.5 0.0 0.9 4 P10 17.1 0.1 0.6 1.14 P13 17.5 -0.4 0.4 1.0 4 P14 17.7 -0.2 0.5 1.2 4 P15 17.8 -0.7 0.5 0.0 4 P16 17.9 -0.9 -0.4 -0.6 4 P17 18.0 -0.9 0.0 -0.2 4 P18 18.9 -1.4 -0.7 -1.0 4 P19 17.6 -0.1 0.3 0.3 4 P20 17.3 0.6 0.7 1.4 4 P21 18.4 -0.5 -0.4 -0.1 4 P22 17.9 -0.2 0.2 1.1 4 P23 17.3 0.1 1.1 1.0 4 P24 17.6 0.2 0.9 0.34 P25 17.6 0.8 1.1 1.65 P1 17.0 0.3 0.5 1.0 5 P2 16.7 0.5 1.0 0.8 5 P3 16.7 0.8 1.1 0.9 5 P4 16.5 1.1 1.4 1.1 5 P5 16.5 1.5 1.8 1.3 5 P6 17.1 0.2 0.6 0.2 5 P7 17.3 -0.2 0.1 0.0 5 P8 17.2 0.0 0.4 0.0 5 P9 16.9 0.2 0.6 0.6 5 P10 17.1 0.0 0.6 0.1 5 P11 16.9 0.4 0.8 0.6 5 P12 16.5 0.7 1.3 0.8 5 P13 16.5 0.5 0.9 0.5 5 P14 16.8 -0.1 0.4 0.0 5 P15 16.7 0.7 1.1 0.7 5 P16 16.7 0.9 1.4 0.8 5 P17 16.6 0.8 1.3 1.0 5 P18 16.3 0.8 1.2 1.0 5 P19 16.5 0.9 1.5 1.2 5 P20 16.9 0.8 1.2 0.4 5 P21 16.8 0.0 0.3 0.0 5 P22 16.8 -0.1 0.2 0.1 5 P23 16.9 0.1 0.6 -0.1 5 P24 17.0 -0.2 0.1 -0.15 P25 17.4 0.0 0.3 0.56 P1 17.7 1.0 0.7 1.1 6 P2 17.5 0.1 0.9 1.3 6 P3 17.6 0.2 1.4 1.5 6 P4 17.5 0.1 1.7 1.1 6 P5 17.6 0.4 0.8 1.1 6 P6 17.5 -0.3 -0.2 2.2 6 P7 17.2 0.0 0.4 1.5 6 P8 17.7 -0.6 -0.3 0.3 6 P9 17.0 0.2 0.3 1.7 6 P10 17.3 -0.3 0.1 1.86 P13 17.0 0.1 0.3 0.7 6 P14 17.0 -0.1 0.1 0.9 6 P15 17.5 -0.4 -0.2 0.0 6 P16 17.6 -0.5 -0.3 0.4 6 P17 16.8 0.2 0.3 1.6 6 P18 17.3 0.1 0.3 0.3 6 P19 17.7 -0.5 -0.5 -0.3 6 P20 17.5 -0.2 0.2 0.2 6 P21 17.6 1.1 1.2 1.7 6 P22 17.5 1.0 1.0 2.2 6 P23 17.6 1.1 0.5 0.7 6 P24 18.1 0.3 0.1 1.76 P25 18.4 -0.5 -0.1 1.27 P1 17.2 0.7 0.8 1.2 7 P2 17.3 0.6 0.8 0.9 7 P3 17.1 0.2 0.4 0.4 7 P4 16.5 1.1 1.2 2.0 7 P5 17.0 0.5 0.6 1.7 7 P6 17.0 0.5 1.1 1.4 7 P7 17.3 0.0 0.5 0.4 7 P8 17.0 0.3 1.3 0.7 7 P9 17.1 0.3 1.0 0.7 7 P10 16.5 1.0 1.7 1.2 7 P11 16.5 0.8 1.2 1.3 7 P12 16.6 0.6 1.1 1.1 7 P13 17.0 0.8 1.1 1.0 7 P14 16.5 0.7 1.3 1.0 7 P15 16.7 0.4 1.1 0.6 7 P16 16.8 0.3 0.8 0.8 7 P17 16.7 1.0 1.1 1.2 7 P18 16.9 0.7 1.0 0.9 7 P19 16.7 0.8 0.9 1.0 7 P20 17.1 0.4 0.6 0.8 7 P21 16.9 0.5 0.9 1.4 7 P22 17.1 -0.1 0.5 0.9 7 P23 16.9 0.6 1.0 1.4 7 P24 17.5 0.2 0.6 1.17 P25 17.7 -0.3 0.3 -0.58 P1 16.9 0.0 0.6 1.4 8 P2 16.7 0.1 0.4 0.8 8 P3 16.5 0.1 0.3 1.2 8 P4 16.9 -0.2 0.2 0.7 8 P5 17.4 -0.8 -0.3 0.8 8 P6 16.5 0.1 1.2 0.5 8 P7 16.7 0.1 1.9 1.0 8 P8 16.8 -0.2 0.1 0.4 8 P9 17.0 -0.5 1.2 0.1 8 P10 16.5 0.2 2.1 1.18 P13 18.6 -1.8 -0.7 -0.6 8 P14 16.9 -0.2 1.5 0.3 8 P15 16.8 -0.4 1.1 0.4 8 P16 16.6 -0.2 1.6 0.3 8 P17 16.4 0.3 1.2 0.8 8 P18 16.4 0.5 1.7 1.8 8 P19 16.8 -0.1 0.9 0.7 8 P20 16.5 0.4 1.2 1.0 8 P21 16.6 0.8 1.3 2.9 8 P22 16.4 0.5 1.3 2.4 8 P23 16.5 -0.1 0.7 0.8 8 P24 16.7 0.5 1.5 2.9 8 P25 16.7 0.4 1.7 0.4EQUIPMENT AND CALIBRATION SCHEDULESEquipment #: THL-01Description: Temperature/Humidity Chart RecorderManufacturer: DicksonModel: THDXSerial #: 9316255Accuracy: Temp: +/- 1C; Humidity: +/-2% RH (0 - 60%) +/- 3% RH (61 - 95%).… Last Cal: 7/15/02, Next Cal: 7/15/03Equipment #: TCT-02Description: Dillon Quantrol TC2 Test StandManufacturer: DillonModel: PCMSerial #: 280769Accuracy: Speed Accuracy: +/- 5% of indicated speed; Displacement: +/- 5 micrometers.… Last Cal: 8/15/01, Next Cal: 8/31/03Equipment #: TCT-03Description: Dillon Quantrol TC2 Test StandManufacturer: Dillon QuantrolModel: TC2Serial #: 02-1033-03Accuracy: Speed Accuracy: +/- 5% of indicated speed; Displacement: +/- 5 micrometers.… Last Cal: 8/15/01, Next Cal: 8/31/03Equipment #: LC-25NDescription: 25 N Load CellManufacturer: DillonModel: TC2 Load CellSerial #: 5373Accuracy: See Manual… Last Cal: 8/22/02, Next Cal: 8/22/03Equipment #: LC-2500N(icell)Description: 2500 N Load Cell for Dillon QuantrolManufacturer: Dillon QuantrolModel: icellSerial #: 01-0132-01Accuracy: .10% of capacity… Last Cal: 3/27/03, Next Cal: 3/27/04Equipment #: OV-03Description: Cascade Tek Forced Air OvenManufacturer: Cascade TekModel: TFO-5Serial #: 0500100Accuracy: Temp. Stability: +/-.1C/C change in ambient Temp. Stability: +/-.1C/C change in ambient … Last Cal: 6/25/02, Next Cal: 6/25/03Equipment #: THC-02Description: Temperature/Humidity Chamber Manufacturer: ThermotronModel: SE-1000-6-6Serial #: 31808Accuracy: See Manual… Last Cal: 8/15/02, Next Cal: 8/15/03 Equipment #: MO-01Description: Micro-OhmeterManufacturer: KeithleyModel: 580Serial #: 0772740Accuracy: See Manual… Last Cal: 6/25/02, Next Cal: 6/25/03 Equipment #: MO-03Description: Multimeter /Data Acquisition System Manufacturer: KeithleyModel: 2700Serial #: 0791975Accuracy: See Manual… Last Cal: 6/25/02, Next Cal: 6/25/03 Equipment #: TC090601-103/105 Description: IC Thermocouple-103/105 Manufacturer: SamtecModel:Serial #: 9316255Accuracy: +/- 1 degree CEquipment #: MO-02Description: Multimeter /Data Acquisition System Manufacturer: KeithleyModel: 2700Serial #: 0780546Accuracy: See Manual… Last Cal: 6/25/02, Next Cal: 6/25/03。
摩卡AIRWorks AWK-3121-M12产品简介说明书
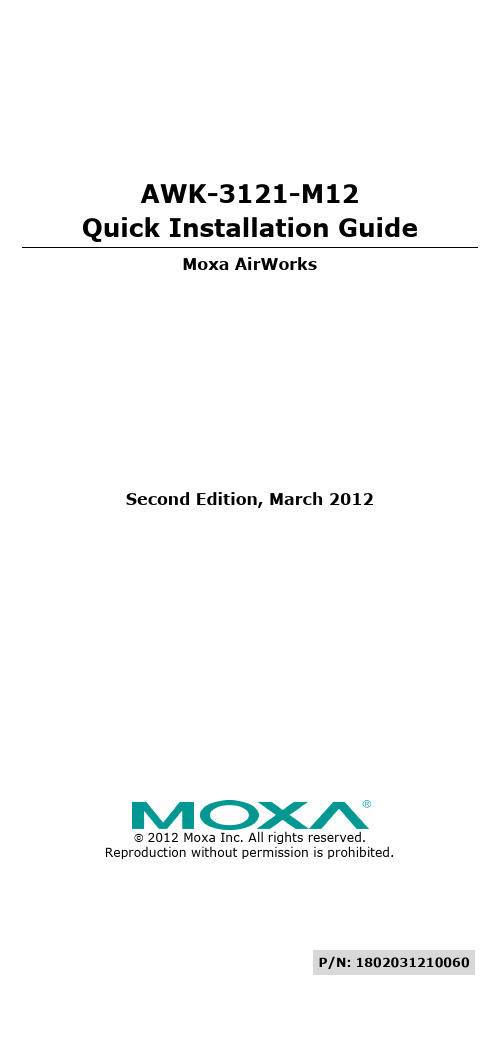
2012 Moxa Inc. All rights reserved.Reproduction without permission is prohibited.P/N: 1802031210060 AWK-3121-M12 Quick Installation GuideMoxa AirWorksSecond Edition, March 2012OverviewMoxa’s AWK-3121-M12 Access Point/Bridge/AP Client is ideal for applications that are hard to wire, too expensive to wire, or use mobile equipment that connects over a TCP/IP network. The AWK-3121-M12 is rated to operate at temperatures ranging from -25 to 60°C for standard models and -40 to 75°C for extended temperature models, and is rugged enough for any harsh industrial environment. Installation is easy, with either DIN-Rail mounting or distribution boxes. The DIN-Rail mounting ability, wide operating temperature range, and IP30 housing with LED indicators make the AWK-3121-M12 a convenient yet reliable solution for any industrial wireless application.Package ChecklistMoxa’s AWK-3121-M12 is shipped with the following items. If any of these items is missing or damaged, please contact your customer service representative for assistance.• 1 AWK-3121-M12• 1 Quick Installation Guide• 1 Software CD• 1 Moxa Product Warranty Booklet• 1 Cable Holder with a Screw• 2 Protective CapsInstallation and ConfigurationBefore installing the AWK-3121-M12, make sure that all items in the Package Checklist are in the box. In addition, you will need access to a notebook computer or PC equipped with an Ethernet port. TheAWK-3121-M12 has a default IP address that you must use when connecting to the device for the first time.Step 1: Select the power sourceThe AWK-3121-M12 can be powered by a DC power input or PoE (Power over Ethernet). The AWK-3121-M12 will use whichever power source you choose.Step 2: Connect the AWK-3121-M12 to a notebook or PC Since the AWK-3121-M12 supports MDI/MDI-X auto-sensing, you can use either a straight-through cable or crossover cable to connect the AWK-3121-M12 to a computer. If the LED indicator on theAWK-3121-M12’s LAN port lights up, it means the connection is established.Step 3: Set up the computer’s IP addressSet an IP address on the same subnet as the AWK-3121-M12. Since the AWK-3121-M12’s default IP address is 192.168.127.253, and the subnet mask is 255.255.255.0, you should set the IP address of the computer to 192.168.127.xxx and subnet mask to 255.255.255.0.Step 4: Use the web-based manager to configureAWK-3121-M12Open your computer’s web browser and then typehttp://192.168.127.253 in the address field to access the homepage of the web-based management. Before the homepage opens, you will need to enter the user name and password. For first-time configuration, enter the default user name and password and then click on the Login button:User name: adminPassword: rootStep 5: Select the operation mode for the AWK-3121-M12 By default, the AWK-3121-M12’s operation mode is set to AP. You can change the setting in Wireless Settings →Basic Wireless Settings if you would like to use the Client mode.NOTE To make the change effective, you must click Save Configuration to save the change or Restart ( Save and Restart button to applyall changes.Step 6: Test communicationsWe will describe two test methods. Use the first method if you are using only one AWK-3121-M12, and use the second method if you are using two or more AWK-3121-M12s.Testing method for one AWK-3121-M12If you are only using one AWK-3121-M12, you will need a second notebook computer (B) equipped with a WLAN card. Configure the WLAN card to connect to the AWK-3121-M12 (the default SSID is MOXA) and change the IP address of notebook B so that it is on the same subnet as the first notebook (A), which is connected to the AWK-3121-M12.After configuring the WLAN card, establish a wireless connection with the AWK-3121-M12 and open a DOS window on notebook B. At the prompt, typeping IP address of notebook Aand then press the Enter key. A “Reply from IP address …” response means the communication was successful. A “Request timed out.” response means the communication failed. In this case, recheck the configuration to make sure the connections are correct.Testing method for two or more AWK-3121-M12s If you have two or more AWK-3121-M12s, you will need a secondnotebook computer (B) equipped with an Ethernet port. Use the default settings for the first AWK-3121-M12 connected to notebook A, andchange the second or third AWK-3121-M12 connected to notebook B to Client mode and then configure the notebooks and AWK-3121-M12s properly.After setting up the testing environment, open a DOS window on notebook B. At the prompt, typeping IP address of notebook Aand then press Enter key. A “Reply from IP address …” response means the communication was successful. A “Request timed out.” response means the communication failed. In this case, recheck the configuration to make sure the connections are correct.Panel Layout of the AWK-3121-M121. Grounding screw2. Terminal block for PWR1, PWR2,relay, DI1, and DI23. Reset button4. Heat dissipation orifices5. System LEDs: PWR1, PWR2,PoE, FAULT, and STATE LEDs6. LEDs for signal strength7. WLAN LEDs: CLIENT BRIDGE,WLAN, and LAN LEDs8. RS-232 console port9. 10/100BaseT(X) RJ45 Port10. MAIN antenna port11. AUX antenna port12. Model name13. Screw hole for wall mounting kit14.DIN-Rail mounting kitMounting Dimensions (unit = mm)DIN-Rail MountingThe aluminum DIN-Rail attachment plate should be fixed to the back panel of the AWK-3121-M12 when you take it out of the box. If you need to reattach the DIN-Rail attachment plate to the AWK-3121-M12, make sure the stiff metal spring is situated towards the top, as shown in the figures below.STEP 1: Insert the top of the DIN-Rail into the slot just below the stiff metal spring.STEP 2:The DIN-Rail attachment unit will snap into place as shown below.To remove the AWK-3121-M12 from the DIN-Rail, simply reverse Steps 1 and 2.Wall Mounting (optional)For some applications, it may be more convenient to mount theAWK-3121-M12 to a wall, as illustrated below.STEP 1:DIN-Rail attachment platefrom the AWK-3121-M12,and then attach the wallmount plates with M3screws, as shown in theadjacent diagrams.STEP 2:Mounting the AWK-3121-M12 to a wall requires 4screws. Use the AWK-3121-M12 device, with wallmount plates attached, as a guide to mark the correctlocations of the 4 screws. The heads of the screwsshould be less than 6.0 mm in diameter, and the shaftsshould be less than 3.5 mm in diameter, as shown inthe figure at the right.Do not screw the screws in all the way—leave a spaceof about 2 mm to allow room for sliding the wall mountpanel between the wall and the screws.NOTE Test the screw head and shank size by inserting the screw into one of the keyhole shaped apertures of the Wall Mounting Platesbefore it is screwed into the wall.STEP 3:Once the screws are fixedinto the wall, insert the fourscrew heads through thelarge opening of thekeyhole-shaped apertures,and then slide theAWK-3121-M12downwards, as indicated tothe right. Tighten the fourscrews for added stability.WARNINGonly be gained by SERVICE PERSONS or by USERS who havebeen instructed about the fact that the metal chassis of theequipment is extremely hot and may cause burns.•Service persons or users have to pay special attention and take special precaution before handling the equipment.•Access is to be controlled through the use of a lock and key ora security identity system, controlled by the authorityresponsible for the location. Only authorized, well-trainedprofessionals are allowed to access the restricted accesslocation.•External metal parts are hot!! Pay special attention or usespecial protection before handling.Wiring RequirementsYou should also pay attention to the following items:•Use separate paths to route wiring for power and devices. If power wiring and device wiring paths must cross, make sure the wires are perpendicular at the intersection point.NOTE: Do not run signal or communications wiring and power wiring in the same wire conduit. To avoid interference, wires with different signal characteristics should be routed separately.•You can use the type of signal transmitted through a wire to determine which wires should be kept separate. The rule of thumb is that wiring with similar electrical characteristics can be bundledtogether.•Keep input wiring and output wiring separate.•It is strongly advised that you label wiring to all devices in the system when necessary.Grounding the Moxa AWK-3121-M12Grounding and wire routing help limit the effects of noise due toelectromagnetic interference (EMI). Run the ground connection from the ground screw to the grounding surface prior to connecting devices.Wiring the Redundant Power InputsThe top two pairs of contacts of the 10-contact terminal block connectoron the AWK-3121-M12’s top panel are used for the AWK-3121-M12’s two DC inputs. Top and front views of the terminal block connector is shown here.STEP 1: Insert the negative/positive DC wiresinto the V-/V+ terminals.STEP 2: To keep the DC wires from pulling loose,use a small flat-blade screwdriver to tighten thewire-clamp screws on the front of the terminalblock connector.STEP 3: Insert the plastic terminal blockconnector prongs into the terminal blockreceptor, which is located on theAWK-3121-M12’s top panel.Wiring the Relay ContactThe AWK-3121-M12 has one relay output, which consists of the twocontacts of the terminal block on the AWK-3121-M12’s top panel. Refer to the previous section for detailed instructions on how to connect the wires to the terminal block connector, and how to attach the terminal block connector to the terminal block receptor. These relay contacts are used to indicate user-configured events. The two wires attached to the Relay contacts form an open circuit when a user-configured event is triggered. If a user-configured event does not occur, the Relay circuit will be closed. Wiring the Digital InputsThe AWK-3121-M12 has two sets of digital input—DI1 and DI2. Each DI comprises two contacts of the 10-pin terminal block connector on the AWK-3121-M12’s top panel. You can refer to the “Wiring the RedundantPower Inputs” section for detailed instructions on how to connect the wires to the terminal block connector, and how to attach the terminalblock connector to the terminal block receptor.Cable Holder Installation (Optional)You can attach the cable holder to the bottom of the AWK-3121-M12. This helps to keep cabling neat and avoid accidents that result from untidy cables.STEP 1: Screw the cable holder onto the bottomof the AWK-3121-M12.STEP 2: After mounting the AWK-3121-M12 and plugging in the LAN cable, tighten the cable along the device and wall.Communication Connections10/100BaseT(X) Ethernet Port ConnectionAll AWK-3121-M12s have a 10/100BaseT(X) Ethernet port (4-pinshielded M12 connector with D coding). The 10/100TX port located on the AWK-3121-M12 front panel is used to connect to Ethernet-enabled devices. Most users configure this port for Auto MDI/MDI-X mode, in which case the port’s pinouts are adjusted automatically depending on the type of Ethernet cable used (straight-through or cross-over), and the type of device (NIC-type or HUB/Switch-type) connected to the port. Pinouts for the 10/100BaseT(X) PortRS-232 ConnectionThe AWK-3121-M12 has one RS-232 (8-pin RJ45) console port located on the front panel. Use either an RJ45-to-DB9 or RJ45-to-DB25 cable to connect the Moxa AWK-3121-M12’s console port to your PC’s COM port. You may then use a console terminal program to access theAWK-3121-M12 for console configuration.Console Pinouts for 10-pin or 8-pin RJ45LED IndicatorsThe front panel of the Moxa AWK-3121-M12 contains several LED indicators. The function of each LED is described in the table below.SpecificationsStandards:IEEE 802.11a/b/g for Wireless LANIEEE 802.11i for Wireless SecurityIEEE 802.3 for 10BaseTIEEE 802.3u for 100BaseTXIEEE 802.3af for Power-over-EthernetIEEE 802.1D for Spanning Tree ProtocolIEEE 802.1w for Rapid STPSpread Spectrum and Modulation (typical):• DSSS with DBPSK, DQPSK, CCK• OFDM wi th BPSK, QPSK, 16QAM, 64QAM• 802.11b: CCK @ 11/5.5 Mbps, DQPSK @ 2 Mbps,DBPSK @ 11 Mbps• 802.11a/g: 64QAM @ 54/48 Mbps, 16QAM @ 36/24 Mbps, QPSK @ 18/12 Mbps, BPSK @ 9/6 MbpsOperating Channels (central frequency):US:2.412 to 2.462 GHz (11 channels)5.18 to 5.24 GHz (4 channels)EU:2.412 to 2.472 GHz (13 channels)5.18 to 5.24 GHz (4 channels)JP:2.412 to 2.472 GHz (13 channels, OFDM)2.412 to 2.484 GHz (14 channels, DSSS)5.18 to 5.24 GHz (4 channels for W52)Security:• SSID broadcast enable/disable• Firewall for MAC/IP/Protocol/Port-based filtering• 64-bit and 128-bit WEP encryption, WPA /WPA2-Personal and Enterprise (IEEE 802.1X/RADIUS, TKIP and AES)Transmission Rates:802.11b: 1, 2, 5.5, 11 Mbps802.11a/g: 6, 9, 12, 18, 24, 36, 48, 54 MbpsTX Transmit Power:802.11b:Typ. 23±1.5 dBm @ 1 to 11 Mbps802.11g:Typ. 20±1.5 dBm @ 6 to 24 Mbps, Typ. 19±1.5 dBm @ 36 Mbps, Typ. 18±1.5 dBm @ 48 Mbps, Typ. 17±1.5 dBm @ 54 Mbps802.11a:Typ. 18±1.5 dBm @ 6 to 24 Mbps, Typ. 16±1.5 dBm @ 36 to 48 Mbps, Typ. 15±1.5 dBm @ 54 MbpsRX Sensitivity:802.11b:-97 dBm @ 1 Mbps, -94 dBm @ 2 Mbps, -*************,-90 dBm @ 11 Mbps802.11g:-93 dBm @ 6 Mbps, -91 dBm @ 9 Mbps, -90 dBm @ 12 Mbps, -88 dBm @ 18 Mbps, -84 dBm @ 24 Mbps, -80 dBm @ 36 Mbps, -76 dBm @ 48 Mbps, -74 dBm @ 54 Mbps802.11a:-90 dBm @ 6 Mbps, -89 dBm @ 9 Mbps, -89 dBm @ 12 Mbps, -85 dBm @ 18 Mbps, -83 dBm @ 24 Mbps, -79 dBm @ 36 Mbps, -75 dBm @ 48 Mbps, -74 dBm @ 54 MbpsProtocol SupportGeneral Protocols: Proxy ARP, DNS, HTTP, HTTPS, IP, ICMP, SNTP, TCP, UDP, RADIUS, SNMP, PPPoE, DHCPInterfaceDefault Antennas*: 2 dual-band omni-directional antennas, 2 dBi,RP-SMA (male)*Only available with the AWK-3121 and AWK-3121-SSC models. Connector for External Antennas:AWK-3121 and AWK-3121-SSC: RP-SMA (female)AWK-3121-M12: QMA (female)RJ45 Ports: 1, 10/100BaseT(X) auto negotiation speed, F/H duplex mode, and auto MDI/MDI-X connection (AWK-3121 only)Fiber Ports: 1, 100BaseFX port (SC connector, AWK-3121 only)M12 Ports: 1, 10/100BaseT(X) auto negotiation speed, F/H duplex mode, and auto MDI/MDI-X connection (AWK-3121-M12 only)Console Port: RS-232 (RJ45-type)LED Indicators: PWR1, PWR2, PoE*, FAULT, STATE, signal strength, CLIENT MODE, BRIDGE MODE, WLAN, 10/100 (TP port), 100M (fiber port), LAN (M12 port)*PoE is only available for the AWK-3121 and AWK-3121-M12 Alarm Contact: 1 relay output with current carrying capacity of 1 A @ 24 VDCDigital Inputs: 2 electrically isolated inputs• +13 to +30 V for state “1”• +3 to -30 V for state “0”• Max. input current: 8 mAPhysical CharacteristicsHousing: Metal, providing IP30 protectionWeight: 850 gDimensions: 53.6 x 135 x 105 mm (2.11 x 5.31 x 4.13 in) Installation: DIN-Rail mounting, wall mounting (with optional kit)Environmental LimitsOperating Temperature:Standard Models: -25 to 60°C (-13 to 140°F)Wide Temp. Models: -40 to 75°C (-40 to 167°F)Storage Temperature: -40 to 85°C (-40 to 185°F)Ambient Relative Humidity: 5% to 95% (non-condensing)Power RequirementsInput Voltage: 12 to 48 VDC, redundant dual DC power inputs or 48 VDC Power-over-Ethernet (IEEE 802.3af compliant)**Compliant with EN 50155 on 24 VDC*PoE is only available for the AWK-3121 and AWK-3121-M12 Connector: 10-pin removable terminal blockPower Consumption: 12 to 48 VDC, 0.121 to 0.494 AReverse Polarity Protection: PresentStandards and CertificationsSafety: UL 60950-1, EN 60950-1Hazardous Location: UL/cUL Class I Division 2, ATEX Zone 2 (for AWK-3121 only)EMC: EN 301 489-1/17; FCC Part 15, Subpart B; EN 55022/55024 Radio: EN 300 328, EN 301 893, DSPR (Japan)Rail Traffic: EN 50155, EN 50121-1/4Note: Please check Moxa’s website for the most up-to-date certification status.ReliabilityMTBF (mean time between failures):AWK-3121: 392,209 hrsAWK-3121-M12: 480,831 hrsAWK-3121-SSC: 445,913 hrsWarrantyWarranty Period: 5 yearsDetails: See /support/warranty.aspxTechnical Support Contact Information /supportMoxa Americas:Toll-free: 1-888-669-2872 Tel: 1-714-528-6777 Fax: 1-714-528-6778 Moxa China (Shanghai office): Toll-free: 800-820-5036 Tel: +86-21-5258-9955 Fax: +86-21-5258-5505Moxa Europe:Tel: +49-89-3 70 03 99-0 Fax: +49-89-3 70 03 99-99 Moxa Asia-Pacific:Tel: +886-2-8919-1230 Fax: +886-2-8919-1231。
评估新产品的过程
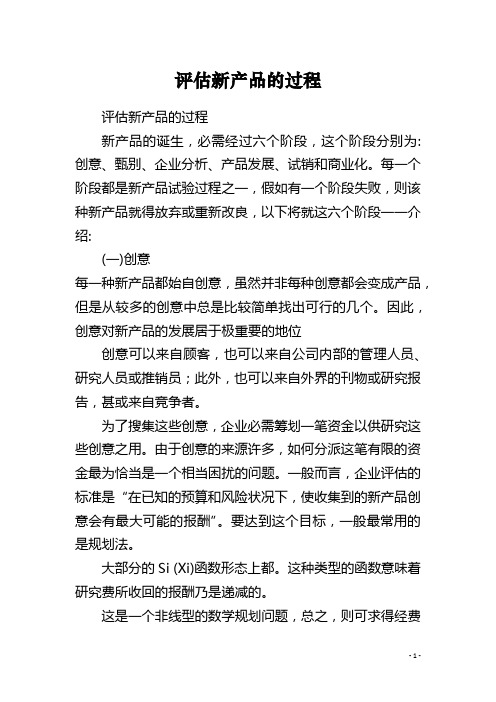
评估新产品的过程评估新产品的过程新产品的诞生,必需经过六个阶段,这个阶段分别为:创意、甄别、企业分析、产品发展、试销和商业化。
每一个阶段都是新产品试验过程之一,假如有一个阶段失败,则该种新产品就得放弃或重新改良,以下将就这六个阶段一一介绍:(一)创意每一种新产品都始自创意,虽然并非每种创意都会变成产品,但是从较多的创意中总是比较简单找出可行的几个。
因此,创意对新产品的发展居于极重要的地位创意可以来自顾客,也可以来自公司内部的管理人员、研究人员或推销员;此外,也可以来自外界的刊物或研究报告,甚或来自竞争者。
为了搜集这些创意,企业必需筹划一笔资金以供研究这些创意之用。
由于创意的来源许多,如何分派这笔有限的资金最为恰当是一个相当困扰的问题。
一般而言,企业评估的标准是“在已知的预算和风险状况下,使收集到的新产品创意会有最大可能的报酬”。
要达到这个目标,一般最常用的是规划法。
大部分的Si (Xi)函数形态上都。
这种类型的函数意味着研究费所收回的报酬乃是递减的。
这是一个非线型的数学规划问题,总之,则可求得经费的最佳派置,也就是说可以从最适合的来源找到期望值最大的创意,不致铺张经费。
(二)甄别取得足够的创意之后,要就这些创意加以研判,研究其可行性,选择出可行性较高的,这就是甄别。
因为并非全部的创意都能付诸实施,也并非全部的创意都符合公司的目标,甄别的目的就是要淘汰那些不可行或可行性低的创意,使公司的有限资源能专注于若干种成功机会较大的创意,加以发展。
图8-3是甄别过程的流程图,一般而言,甄别所要考虑的因素有两个,一个是该种创意是否符合公司的目标;另一个是公司的资源是否足以发展该种创意。
在这两个目标底下,要考虑的项目依企业的状况有所不同。
例如有些企业的目标是为了谋求更多的利润,有些是维持稳定的销货,有些则是创造更佳的商誉;甄别新产品创意时,得就企业所设定的目标来加以评估,以求符合整个公司的政策。
能够通过这个过程中每一甄别阶段的新产品创意,就可以开头下一步骤一一企业分析。
Thumb2指令表(中文)

Rd := SAT(Rm + SAT(Rn * 2))
Q
SUB{S} Rd, Rn, <Operand2>
N Z C V Rd := Rn – Operand2
N
SBC{S} Rd, Rn, <Operand2>
N Z C V Rd := Rn + Operand2 - C的非
N
T2 SUB Rd, Rn, #<imm12>
T
6 <prefix>ADD16 Rd, Rn, Rm
Rd[31:16] := Rn[31:16] + Rm[31:16], Rd[15:0] := Rn[15:0] + Rm[15:0]
G
6 <prefix>SUB16 Rd, Rn, Rm
Rd[31:16] := Rn[31:16] – Rm[31:16], Rd[15:0] := Rn[15:0] – Rm[15:0]
一个由大括号括起来的,用逗号隔开的寄存器列表。如:{ and }。 加载或存储的寄存器列表,不能包含程序计数器PC。 列表须有程序计数器。将SPSR拷贝到CPSR中,用于从异常处理返回。 正或负号。(+号有可能被忽略.) 见表: ARM结构版本 中断标志。一个或多个a,i,f(异常、中断、快速中断). 见表: 处理器模式 由<p_mode>所指定处理器模式的堆栈指针SP 位域的最低有效位 位域的宽度。<width> + <lsb> 必须≤32 如果x置位,RsX为Rs循环移动16位的结果。否则RsX为Rs。 若 ! 存在 (预先定义),则数据传送后更新基址寄存器(Rn)。 若S存在,则更新标志位 若T存在,进用户特权模式 若R存在,则恢复最近的结果,否则丢弃结果。