我国炼铁工艺技术的进步_炼铁_
钢铁行业的技术进展和创新趋势
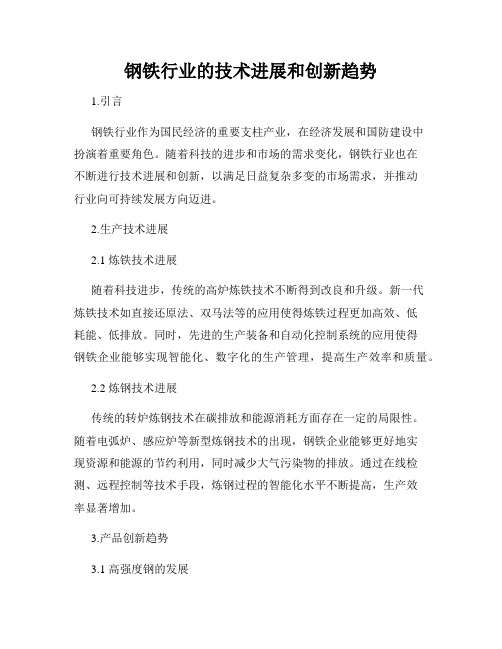
钢铁行业的技术进展和创新趋势1.引言钢铁行业作为国民经济的重要支柱产业,在经济发展和国防建设中扮演着重要角色。
随着科技的进步和市场的需求变化,钢铁行业也在不断进行技术进展和创新,以满足日益复杂多变的市场需求,并推动行业向可持续发展方向迈进。
2.生产技术进展2.1 炼铁技术进展随着科技进步,传统的高炉炼铁技术不断得到改良和升级。
新一代炼铁技术如直接还原法、双马法等的应用使得炼铁过程更加高效、低耗能、低排放。
同时,先进的生产装备和自动化控制系统的应用使得钢铁企业能够实现智能化、数字化的生产管理,提高生产效率和质量。
2.2 炼钢技术进展传统的转炉炼钢技术在碳排放和能源消耗方面存在一定的局限性。
随着电弧炉、感应炉等新型炼钢技术的出现,钢铁企业能够更好地实现资源和能源的节约利用,同时减少大气污染物的排放。
通过在线检测、远程控制等技术手段,炼钢过程的智能化水平不断提高,生产效率显著增加。
3.产品创新趋势3.1 高强度钢的发展随着汽车工业和航空航天工业的迅猛发展,对材料强度和轻量化要求越来越高。
高强度钢材以其强度高、塑性好的特点,成为替代传统材料的首选。
冷轧高强度钢、热轧高强度钢、中锰钢等新型材料得到广泛应用,提供了更多的设计自由度和更优的性能,推动了汽车工业和航空航天工业的发展。
3.2 特种钢的应用特种钢具有耐高温、耐腐蚀、耐磨等特点,在能源、化工、航空、电子等领域得到广泛应用。
高温合金钢、耐磨钢、不锈钢等特种钢制品在现代工业中发挥着重要作用。
随着技术的不断突破,特种钢种类不断增多,性能也不断提升,为各行各业的发展提供了重要支撑。
4.绿色发展趋势4.1 节能减排作为资源消耗和排放较高的行业,钢铁行业积极探索低碳、循环经济发展之路。
通过研发和应用新型节能环保技术,如能源回收利用、煤气发电等手段,有效降低能源消耗,减少污染物排放。
钢铁企业也积极推动资源的循环利用,降低资源浪费,实现可持续发展。
4.2 智能制造智能制造是当前钢铁行业发展的重要方向。
国内外高炉炼铁技术的发展现状和趋势

国内外高炉炼铁技术的发展现状和趋势高炉炼铁技术是金属冶炼工业发展的基础,是保证金属铁质量和产量的关键技术,也是社会经济发展的重要依托。
近年来,随着金属冶炼工业的快速发展,国内外高炉炼铁技术的发展也取得了显著的成就,为保证金属铁质量、提高产量、提高经济效益发挥了重要作用。
首先,国内外高炉炼铁技术取得了重大突破,进一步提高了金属铁质量。
随着科学技术的进步,添加剂和冶炼工艺的改进,使高炉炼铁工艺取得重大进展,不仅能够有效提高铁素体组成,同时也能够改善铁水的流动性,有利于铁块的全面成型。
此外,利用新型炉料和改进的热处理技术,可以有效降低铁水的含氧量,提高铁液的液相容量,从而获得更高品质的铁。
其次,国内外高炉炼铁技术的发展,还大大提高了铁的产量。
传统的高炉炼铁工艺存在着大量的炉料损失,限制了铁的产量。
随着国内外高炉炼铁技术的发展,炉料损失大大减少,产量得到提高。
通过对炼铁工艺及其参数进行优化调整,获得合理的炉料计算和分配,进而有效提高铁的产量。
此外,结合智能技术、自动化技术和智能控制技术,还可以实现远程监控和智能化管理,可以使高炉炼铁效率更高,产量更大。
最后,国内外高炉炼铁技术的发展,对提高经济效益具有重要意义。
国内外高炉炼铁技术的发展,不仅缩短了铁的生产周期,提高了产量,而且可以减少能耗消耗和废气排放,降低了生产成本,有利于提高企业的竞争力,实现更高的经济效益。
此外,国内外高炉炼铁技术的发展还可以改善炼铁终端的工作环境,为炼铁行业的发展创造更加良好的条件。
以上是国内外高炉炼铁技术的发展现状和趋势的概述,未来的发展趋势可以简单地总结为以下几点:继续提高高炉炼铁质量和产量,推广智能技术,进一步优化炼铁工艺,合理设计炉料配比,提高炼铁效率,减少能耗和污染,改善炼铁环境,提高经济效益,实现绿色经济发展。
未来,相信国内外高炉炼铁技术将取得更好的发展,为我们社会的经济发展提供更多的依托。
世界冶铁技术发展史
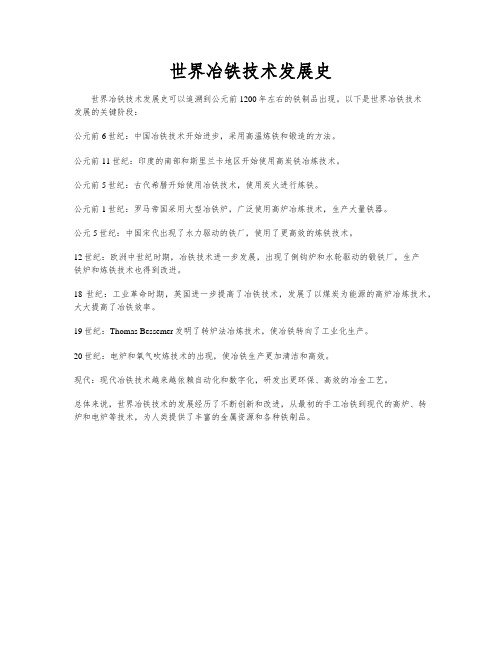
世界冶铁技术发展史
世界冶铁技术发展史可以追溯到公元前1200年左右的铁制品出现。
以下是世界冶铁技术
发展的关键阶段:
公元前6世纪:中国冶铁技术开始进步,采用高温炼铁和锻造的方法。
公元前11世纪:印度的南部和斯里兰卡地区开始使用高炭铁冶炼技术。
公元前5世纪:古代希腊开始使用冶铁技术,使用炭火进行炼铁。
公元前1世纪:罗马帝国采用大型冶铁炉,广泛使用高炉冶炼技术,生产大量铁器。
公元5世纪:中国宋代出现了水力驱动的铁厂,使用了更高效的炼铁技术。
12世纪:欧洲中世纪时期,冶铁技术进一步发展,出现了倒钩炉和水轮驱动的锻铁厂,生产
铁炉和炼铁技术也得到改进。
18世纪:工业革命时期,英国进一步提高了冶铁技术,发展了以煤炭为能源的高炉冶炼技术,大大提高了冶铁效率。
19世纪:Thomas Bessemer发明了转炉法冶炼技术,使冶铁转向了工业化生产。
20世纪:电炉和氧气吹炼技术的出现,使冶铁生产更加清洁和高效。
现代:现代冶铁技术越来越依赖自动化和数字化,研发出更环保、高效的冶金工艺。
总体来说,世界冶铁技术的发展经历了不断创新和改进,从最初的手工冶铁到现代的高炉、转炉和电炉等技术,为人类提供了丰富的金属资源和各种铁制品。
炼铁创新工作总结范文(3篇)

第1篇一、前言近年来,我国炼铁行业在技术创新、设备改进、生产管理等方面取得了显著成果。
作为我国炼铁行业的一份子,我司始终秉持“创新驱动、绿色发展”的理念,积极投身炼铁创新工作,现将我司炼铁创新工作总结如下。
一、创新工作概述1. 技术创新(1)高炉炉顶压力控制技术:通过优化高炉炉顶压力控制策略,提高炉顶压力控制精度,降低能耗,提高高炉产量。
(2)烧结过程控制技术:对烧结过程进行实时监测与控制,优化烧结过程参数,提高烧结矿质量,降低烧结能耗。
(3)炼铁余热回收利用技术:利用炼铁过程中产生的余热,进行发电、供暖等,实现能源的循环利用,降低炼铁生产成本。
2. 设备改进(1)高炉炉体冷却系统改造:通过优化炉体冷却系统设计,提高冷却效率,降低高炉炉体热负荷,延长高炉使用寿命。
(2)烧结机设备升级:采用新型烧结机设备,提高烧结机生产效率,降低烧结能耗。
(3)球团设备改造:优化球团设备结构,提高球团质量,降低生产成本。
3. 生产管理(1)优化生产调度:通过优化生产调度策略,提高生产效率,降低生产成本。
(2)强化设备管理:加强设备维护保养,提高设备运行效率,降低设备故障率。
(3)提高员工素质:加强员工培训,提高员工技能水平,确保生产安全。
二、创新工作成果1. 技术创新方面(1)成功研发高炉炉顶压力控制技术,降低高炉能耗10%。
(2)烧结过程控制技术使烧结矿质量提高10%,烧结能耗降低5%。
(3)炼铁余热回收利用项目实现年发电量1000万千瓦时,供暖面积达20万平方米。
2. 设备改进方面(1)高炉炉体冷却系统改造,延长高炉使用寿命5年。
(2)烧结机设备升级,提高烧结机生产效率20%。
(3)球团设备改造,降低球团生产成本10%。
3. 生产管理方面(1)优化生产调度,提高生产效率15%。
(2)设备管理措施使设备故障率降低20%。
(3)员工培训使员工技能水平提高20%。
三、创新工作展望未来,我司将继续坚持创新驱动发展战略,加大研发投入,深化技术创新、设备改进、生产管理等方面的改革,为实现炼铁行业高质量发展贡献力量。
浅谈我国炼铁技术设备的发展

民营 科技2 0 1 4 年第2 期
浅谈我 国炼铁 技术设 备 的发展
吕遵 勇
( 西林钢铁集 团有限公 司, 黑龙 江 伊春 1 5 3 0 2 5 )
摘 要: 我 国的 炼铁技术在最近的几年 当中得到 了迅猛的发展 , 各 项技 术指标也是不 断的提升 。 在 3前新的工作形势之 - " 下, 还需要 及 时的对以往 的工作进 行总结与归纳 ,找 出炼铁技 术设备发展过程 当中遇 到的阻碍 与难 点,在很好 的分析 了以往 工作经验 的基础 之
以来 , 我 国的热 风温度 已经很好 的克服 了以往工作 当中存 在的阻 炼铁技术 的发展 。 碍, 取 得 了技 术上 的重大突 破与改进 , 尤其是新 建设 的一批 大规 3 今后炼铁技术设备的发展分析 模 的高炉 , 其热 风的平均温度 可 以达到 1 3 0 0摄 氏度以上 , 而使用 我 围烧结机 , 焦炉, 高炉 的装备 容积偏小 , 且数量 太多 , 造成
今后 发展 的方 向进行研究 , 将有助于及 时的归纳以及总结发展的经 以全面的实现增产 以及节能 , 而且还是企业 对 自身结构产 能进 行 不断改 良的重要努力方 向之一 。 验, 进而促进炼铁技术以及设备的稳步前进 。
1 中国高炉炼铁生产技术发展 2 高炉炼铁 操作技术水平发展
且成熟 的发展 阶段 。我 国现今 的高炉炼铁生产技术 已经是位于世 象 , 高炉生产 的技术经济指标仍处于 良好状态。近年来 , 中国高 炉 界 的先进 行列 ,但是在各个 企业之 间存 在有发展 不均 衡的 问题 , 高效化不断取得新进展 。全国重点钢铁企业 的燃料 比、 人炉焦 比、
我国高炉炼铁技术从总体上评述 ,可以说 已达到 国际水 平 , 部分指标 已是先进水平 。近年来 , 中国炼铁生产技 术进入成熟发 也在不断 的扩 大 , 我 国的高炉炼铁生产 技术水准 也是得 到了稳固 的发展 。目前阶段我 国的高炉炼铁生产技术处于全世界 的领先行 展 阶段 。 主要表现是在外界条件不断变化f 特别是原燃 料质量 的波 列之 中 , 并且高 炉的生产操作技术 也是进入 到了一个相对平 稳并 动) 情况下 , 高炉生产 仍能够实现稳定顺 行 , 不出现较 大的失常现
读书笔记1.1高炉炼铁技术的进步近10年来,中国高炉大型化、高效化
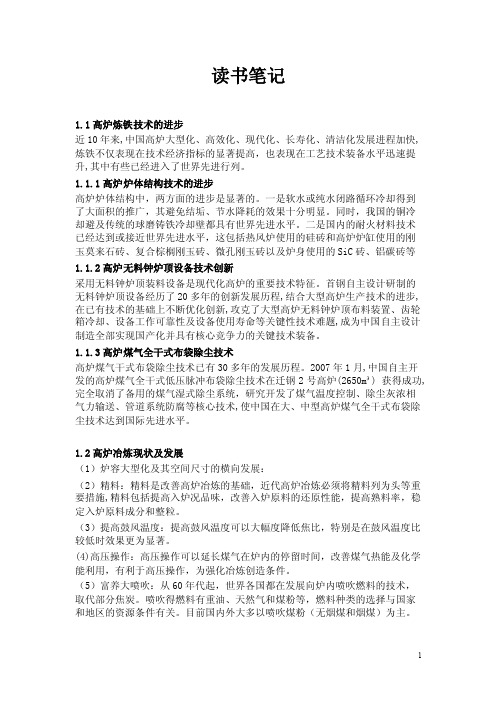
读书笔记1.1高炉炼铁技术的进步近10年来,中国高炉大型化、高效化、现代化、长寿化、清洁化发展进程加快,炼铁不仅表现在技术经济指标的显著提高,也表现在工艺技术装备水平迅速提升,其中有些已经进入了世界先进行列。
1.1.1高炉炉体结构技术的进步高炉炉体结构中,两方面的进步是显著的。
一是软水或纯水闭路循环冷却得到了大面积的推广,其避免结垢、节水降耗的效果十分明显。
同时,我国的铜冷却避及传统的球磨铸铁冷却壁都具有世界先进水平。
二是国内的耐火材料技术已经达到或接近世界先进水平,这包括热风炉使用的硅砖和高炉炉缸使用的刚玉莫来石砖、复合棕榈刚玉砖、微孔刚玉砖以及炉身使用的SiC砖、铝碳砖等1.1.2高炉无料钟炉顶设备技术创新采用无料钟炉顶装料设备是现代化高炉的重要技术特征。
首钢自主设计研制的无料钟炉顶设备经历了20多年的创新发展历程,结合大型高炉生产技术的进步,在已有技术的基础上不断优化创新,攻克了大型高炉无料钟炉顶布料装置、齿轮箱冷却、设备工作可靠性及设备使用寿命等关键性技术难题,成为中国自主设计制造全部实现国产化并具有核心竞争力的关键技术装备。
1.1.3高炉煤气全干式布袋除尘技术高炉煤气干式布袋除尘技术已有30多年的发展历程。
2007年1月,中国自主开发的高炉煤气全干式低压脉冲布袋除尘技术在迁钢2号高炉(2650m³) 获得成功,完全取消了备用的煤气湿式除尘系统,研究开发了煤气温度控制、除尘灰浓相气力输送、管道系统防腐等核心技术,使中国在大、中型高炉煤气全干式布袋除尘技术达到国际先进水平。
1.2高炉冶炼现状及发展(1)炉容大型化及其空间尺寸的横向发展:(2)精料:精料是改善高炉冶炼的基础,近代高炉冶炼必须将精料列为头等重要措施,精料包括提高入炉况品味,改善入炉原料的还原性能,提高熟料率,稳定入炉原料成分和整粒。
(3)提高鼓风温度:提高鼓风温度可以大幅度降低焦比,特别是在鼓风温度比较低时效果更为显著。
钢铁冶炼技术

钢铁冶炼技术钢铁冶炼技术一直以来都是工业生产中的重要环节。
随着科技的发展和工艺的革新,钢铁冶炼技术也在不断进步和改进。
本文将从钢铁冶炼的历史背景、工艺流程、技术创新和展望未来等方面展开探讨。
一、历史背景钢铁作为人类社会发展的重要材料之一,有着悠久的历史。
早在公元前3000年左右,古代中国就开始了一些简单的铸铁和钢铁冶炼活动。
然而,真正的钢铁冶炼技术的突破出现在19世纪,随着工业革命的到来,炼钢技术进入了一个全新的时代。
二、工艺流程钢铁冶炼的过程可以分为炼铁和炼钢两个阶段。
炼铁是从铁矿石中提取出生铁的过程,而炼钢则是通过给生铁加入一定的合金元素,调整其化学成分,以增加硬度和强度。
一般而言,炼铁直接从铁矿石中提取铁,而炼钢则需要将生铁进一步加工。
炼铁的主要工艺是高炉冶炼。
高炉是一种巨大的冶炼设备,将铁矿石、焦炭和石灰石等原料通过一系列的化学反应转化为生铁。
高炉冶炼的核心是利用冶炼炉内高温条件下的还原反应将铁矿石中的氧化铁还原为金属铁。
同时,高炉内还能够将部分含有硫和硅等杂质的铁矿石排除。
炼钢则是在炼铁的基础上进行的。
炼钢的常见工艺有转炉炼钢、电炉炼钢和氧气炼钢等。
转炉炼钢是目前应用最广泛的炼钢工艺,它通过炉料的投入和废气的排出来控制冶炼过程。
电炉炼钢则是利用电能将炉料加热并进行冶炼。
氧气炼钢则是在冶炼过程中通过喷吹氧气来提高炉温和增加氧化反应。
三、技术创新钢铁冶炼技术在长期的发展中取得了诸多重要的创新和突破。
首先,在高炉冶炼领域,高炉煤气的回收利用、炼铁渣的资源化利用等成果取得了重大突破。
其次,在炼钢工艺方面,转炉炼钢技术的改进、电炉炼钢的发展以及氧气炼钢等新技术的应用都为钢铁冶炼行业带来了许多技术创新。
四、展望未来未来的钢铁冶炼技术将面临诸多挑战和机遇。
首先,钢铁冶炼将趋向于更加高效、清洁和环保的方向发展。
煤气的回收利用和废气治理技术将进一步提升。
其次,新型炼钢工艺的研发和应用将逐渐取代传统的转炉和电炉炼钢技术,提高钢铁冶炼的效率和质量。
炼铁行业的技术创新与转型升级

美国阿勒格尼技术公司:利用AI技术优化生产流程,提高生产效率
韩国浦项制铁:采用环保技术,减少污染物排放
技术创新与转型升级的效益分析
提高生产效率:通过技术创新,提高生产效率,降低生产成本
减少环境污染:通过技术创新和转型升级,减少环境污染,实现绿色生产
提高企业效益:通过技术创新和转型升级,提高企业效益,增强企业竞争力
应用:智能控制系统、机器人技术、大数据分析、人工智能等
概念:利用先进的信息技术和自动化技术,实现炼铁过程的智能化、高效化和绿色化
特点:提高生产效率、降低能耗、减少污染、提高产品质量
前景:推动炼铁行业转型升级,提高竞争力,实现可持续发展
新型炉衬材料的应用
添加标题
添加标题
添加标题
添加标题
新型炉衬材料的特点:耐高温、耐腐蚀、耐磨损
炼铁行业技术创新与转型升级的实践与案例
6
国内典型企业实践
宝钢集团:引进先进技术,提高生产效率
首钢集团:推进绿色制造,降低环境污染
鞍钢集团:加强技术创新,开发新产品
沙钢集团:优化生产流程,提高产品质量
国际先进企业案例
德国蒂森克虏伯:采用高效节能技术,降低生产成本
日本新日铁:开发高强度钢,提高产品质量
加强与上下游企业的合作,实现产业链的智能化升级
炼铁行业的技术创新与转型升级的挑战与机遇
5
面临的挑战
环保压力:炼铁行业是高能耗、高污染的行业,需要应对越来越严格的环保法规和标准。
资源紧张:铁矿石等原材料价格波动较大,供应不稳定,需要应对资源紧张的挑战。
技术更新:炼铁行业的技术更新速度较快,需要不断更新技术和设备,以保持竞争力。
市场竞争:炼铁行业竞争激烈,需要应对竞争对手的压力,提高产品质量和降低成本。
高炉炼铁生产管理创新与技术进步

高炉炼铁生产管理创新与技术进步随着现代工业的发展,高炉炼铁作为铁矿石的重要生产方式,承担着重要的任务。
在高炉炼铁生产中,如何创新管理模式,推进技术进步,提高生产效率和产品质量,已成为行业发展的关键问题。
本文将从管理创新和技术进步两方面来探讨高炉炼铁生产的发展趋势。
一、高炉炼铁生产管理创新1.工艺流程优化在高炉炼铁生产中,工艺流程的优化是提高生产效率的重要途径。
通过对生产过程进行分析,不断优化工艺流程,可以提高炉内矿石的还原性能,增加炉渣的碱度,减少燃料消耗和炉缸内压力等,从而提高炉况的稳定性和生产效率。
2.智能化管理随着信息技术的发展,高炉炼铁生产管理也逐渐向智能化方向发展。
采用先进的传感技术和数据分析算法,可以对高炉炼铁生产过程进行在线监测和控制,实现生产过程的自动化和智能化管理,提高生产效率和产品质量。
3.能源节约与环保在高炉炼铁生产中,能源消耗和环境污染一直是困扰行业发展的问题。
通过引进节能环保技术,如余热回收利用、尾气净化技术等,可以有效减少能源消耗和排放污染物,提高生产的可持续发展能力。
4.人力资源管理高炉炼铁生产需要大量的技术工人和管理人员,如何合理配置人力资源,提高员工的技术水平和管理能力,对于保障生产的稳定进行是至关重要的。
建立健全的人力资源管理制度和培训体系,可以提高员工的工作积极性和生产效率。
二、高炉炼铁生产技术进步1.新型高炉技术随着现代冶金技术的发展,一些新型高炉技术逐渐应用于高炉炼铁生产中,如底吹炼铁技术、蓄热式高炉技术等。
这些新型高炉技术能够提高炉内的矿石还原效率,减少冶金副产物的生成,降低燃料的消耗,从而提高生产效率和产品质量。
2.炉料质量控制高炉炼铁生产过程中,炉料的质量直接影响炉内还原和熔融过程,因此炉料的质量控制是提高生产效率的关键。
采用先进的炉料配料技术和原料分析技术,可以确保炉料的合理配比和质量稳定,提高炼铁生产的稳定性和生产效率。
3.炉渣处理技术炼铁生产中生成的炉渣不仅影响了炉内的正常操作,还对环境造成了污染。
炼铁工艺优化提高炼铁生产效率的关键步骤

炼铁工艺优化提高炼铁生产效率的关键步骤炼铁是将铁矿石转化为熔融铁的过程,是钢铁行业的核心环节。
为了提高炼铁生产的效率和质量,不断优化炼铁工艺是关键。
本文将介绍炼铁工艺优化的关键步骤,以实现最佳的炼铁生产效率。
1. 原料质量控制炼铁的原料主要包括铁矿石、焦炭和燃料等,原料的质量直接影响到炉渣的形成和决定炉温。
因此,控制原料的质量是炼铁工艺优化的重要步骤之一。
在原料进入炼铁炉之前,需要对原料进行严格的检测和筛查,确保原料的含铁量、热值和灰分等指标符合要求。
2. 高炉温度的控制高炉的炉温是影响炼铁工艺效率的关键因素之一。
在高炉操作中,通过控制煤气的进气量、风量和出渣的速度等参数,调整高炉的温度。
炉温过低会导致炉内还原反应不充分,炼铁效率低下;炉温过高则容易导致炉渣的过热和炉墙的损坏。
因此,保持适宜的高炉温度是提高炼铁生产效率的关键步骤之一。
3. 合理的炉渣管理炉渣是炼铁过程中产生的一种副产品,它具有决定炼铁工艺效率和钢质质量的重要作用。
合理的炉渣管理包括炉渣的形成、控制和处理等环节。
在炼铁工艺中,通过调整炉渣的成分和比例,可以有效地控制炉温和炼铁反应的速度,提高生产效率。
此外,对产生的炉渣进行合理的处理,可以回收其中的铁和其他有价值的金属,降低资源消耗。
4. 快速而准确的化验分析炼铁过程中,对铁水、炉渣和废气等进行快速而准确的化验分析是确保生产质量和效率的重要步骤之一。
通过化验分析,可以及时了解炼铁过程中各种物质的成分和含量,确定工艺参数的调整范围,并及时采取相应的措施。
因此,建立完善的化验分析体系和设备,提高化验分析的准确性和速度,是优化炼铁工艺的关键之一。
5. 运行和设备的维护管理炼铁工艺的优化离不开设备的高效运行和维护管理。
稳定的设备运行和维护管理可以保证炼铁生产的连续性和稳定性,提高生产效率和质量。
在运行中,需要严格遵守操作规程,及时发现和处理设备故障,确保设备的正常运行。
此外,对设备进行定期的检修和保养,可以有效延长设备的使用寿命,降低维修成本。
钢铁冶炼中的新型炼铁炉技术
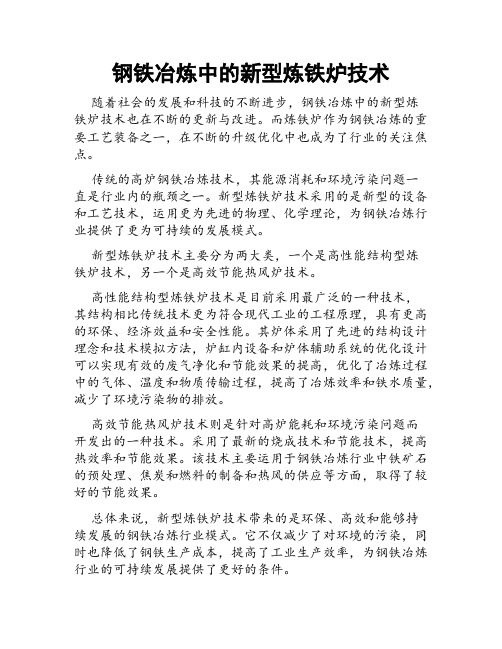
钢铁冶炼中的新型炼铁炉技术随着社会的发展和科技的不断进步,钢铁冶炼中的新型炼铁炉技术也在不断的更新与改进。
而炼铁炉作为钢铁冶炼的重要工艺装备之一,在不断的升级优化中也成为了行业的关注焦点。
传统的高炉钢铁冶炼技术,其能源消耗和环境污染问题一直是行业内的瓶颈之一。
新型炼铁炉技术采用的是新型的设备和工艺技术,运用更为先进的物理、化学理论,为钢铁冶炼行业提供了更为可持续的发展模式。
新型炼铁炉技术主要分为两大类,一个是高性能结构型炼铁炉技术,另一个是高效节能热风炉技术。
高性能结构型炼铁炉技术是目前采用最广泛的一种技术,其结构相比传统技术更为符合现代工业的工程原理,具有更高的环保、经济效益和安全性能。
其炉体采用了先进的结构设计理念和技术模拟方法,炉缸内设备和炉体辅助系统的优化设计可以实现有效的废气净化和节能效果的提高,优化了冶炼过程中的气体、温度和物质传输过程,提高了冶炼效率和铁水质量,减少了环境污染物的排放。
高效节能热风炉技术则是针对高炉能耗和环境污染问题而开发出的一种技术。
采用了最新的烧成技术和节能技术,提高热效率和节能效果。
该技术主要运用于钢铁冶炼行业中铁矿石的预处理、焦炭和燃料的制备和热风的供应等方面,取得了较好的节能效果。
总体来说,新型炼铁炉技术带来的是环保、高效和能够持续发展的钢铁冶炼行业模式。
它不仅减少了对环境的污染,同时也降低了钢铁生产成本,提高了工业生产效率,为钢铁冶炼行业的可持续发展提供了更好的条件。
尽管新型炼铁炉技术在行业内已经确立了一定的地位,其在实际应用中仍然面临很多挑战。
首先,新技术的推广过程需要建立一整套配套的法规、制度和标准,以及相关人员的培训,来降低普及新技术的成本和风险;其次,新技术虽然可以提高生产效率,但前期投资成本相对较高,需要公司在投资决策阶段做好充分的考虑,降低好投资风险。
在新型炼铁炉技术上的发展和应用,不仅可以推动钢铁冶炼行业的技术革新和转型升级,也为国家的可持续发展策略提供了有力的支持和借鉴。
铁的冶炼发展历程
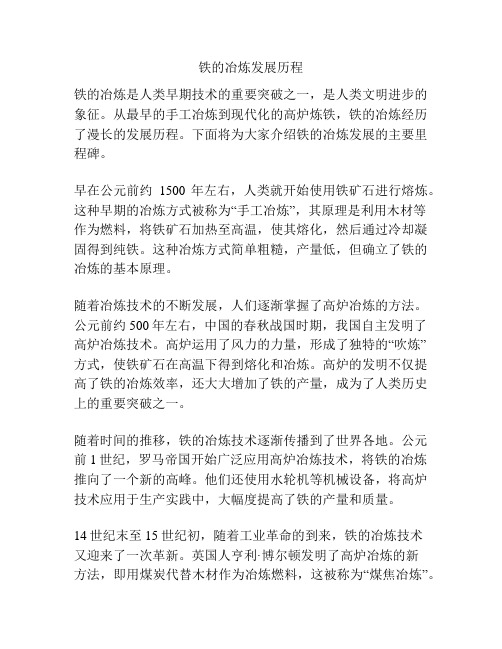
铁的冶炼发展历程铁的冶炼是人类早期技术的重要突破之一,是人类文明进步的象征。
从最早的手工冶炼到现代化的高炉炼铁,铁的冶炼经历了漫长的发展历程。
下面将为大家介绍铁的冶炼发展的主要里程碑。
早在公元前约1500年左右,人类就开始使用铁矿石进行熔炼。
这种早期的冶炼方式被称为“手工冶炼”,其原理是利用木材等作为燃料,将铁矿石加热至高温,使其熔化,然后通过冷却凝固得到纯铁。
这种冶炼方式简单粗糙,产量低,但确立了铁的冶炼的基本原理。
随着冶炼技术的不断发展,人们逐渐掌握了高炉冶炼的方法。
公元前约500年左右,中国的春秋战国时期,我国自主发明了高炉冶炼技术。
高炉运用了风力的力量,形成了独特的“吹炼”方式,使铁矿石在高温下得到熔化和冶炼。
高炉的发明不仅提高了铁的冶炼效率,还大大增加了铁的产量,成为了人类历史上的重要突破之一。
随着时间的推移,铁的冶炼技术逐渐传播到了世界各地。
公元前1世纪,罗马帝国开始广泛应用高炉冶炼技术,将铁的冶炼推向了一个新的高峰。
他们还使用水轮机等机械设备,将高炉技术应用于生产实践中,大幅度提高了铁的产量和质量。
14世纪末至15世纪初,随着工业革命的到来,铁的冶炼技术又迎来了一次革新。
英国人亨利·博尔顿发明了高炉冶炼的新方法,即用煤炭代替木材作为冶炼燃料,这被称为“煤焦冶炼”。
这一新技术极大地丰富了原料来源,推动了铁的冶炼效率的大幅提升,加速了工业革命的进程。
到了18世纪末,人们又取得了对炼钢技术的突破。
英国的亨利·贝塞莫尔发明了气体熔融炼钢法,将工业生产中的铁炼制至钢的水平。
这种炼钢技术使铁产业得以进一步发展,为钢铁产业的崛起奠定了基础。
到了19世纪中叶,铁和钢的冶炼技术逐渐向现代化迈进。
人们利用焦炉、转炉、电炉等新型设备,进一步改良和提高了冶炼工艺。
此外,各国对铁和钢的冶炼技术进行了积极的研究与交流,推动了全球钢铁产业的不断发展。
在现代化工业技术的推动下,铁的冶炼也进一步实现了自动化和集约化。
中国炼铁技术的发展和当前值得探讨的技术问题

国加快 钢 铁 技 术 的发 展 奠 定 了厚 实 的基 础 。3 5
1 改 革 开 放 以来 我 国钢 铁 业发 展
概 况
1 9 7 8年 1 2月 2 3 日是 中 国钢 铁 业 发 展 值 得
年来我 国钢 铁工 业 装 备 、 钢 铁 的 产量 和技 术 经 济
关键 词 : 炼铁 ;焦比 ;燃料 比 中图分类 号 : T F 5 文献标 志码 : B 文章 编号 : 1 0 0 8— 0 7 1 6 ( 2 0 1 4 ) 0 2— 0 0 0 1 —1 7
d o i : 1 0 . 3 9 6 9 / j . i s s n . 1 0 0 8— 0 7 1 6 . 2 0 1 4 . 0 2 . 0 0 1
Th e t e c hn o l o g y d e v e l o pme nt s a n d t h e c u r r e n t t e c hn i c a l i s s u e s wo r t h di s c u s s i ng o f Ch i n e s e i r o n- ma k i ng
L/ W i gu o
( B a o s h a n I r o n& S t e e l C o . , L t d . , S h a n g h a i 2 0 1 9 0 0 , C h i n a )
Abs t r a c t: Th e i r o n — ma k i ng t e c h n o l o g y h a s ma d e c o n s i d e r a b l e p r o g r e s s i n t h e 2 1 s t c e n t u r y, e s pe c i a l l y i n t h e e r a wi t h t h e o v e r s u p p l y o f s t e e l p r o d u c t i o n. I n o r d e r t o e n h a n c e t h e i r ma r k e t c o mp e t i t i v e n e s s a f t e r t h e i r o n a n d s t e e l e n t e r p is r e s e n t e r i n g t h e e r a o f me a g e r p r o it f ,t h e i r o n - ma ki n g t e c h n o l o g i e s,wh i c h l a r g e l y de t e r mi n e t he ma n u f a c t ur i n g c o s t ,a r e f o r c e d t o g o t h e i r wa y o f e n e r y g s a v i n g,e n v i r o n me n t a l p r o t e c t i o n a n d l o w— c o s t .Th i s a r t i c l e l i s t t h e hi g h l i g h t s o f Ch i n e s e i r o n- ma k i n g t e c h n o l o g i e s i n r e c e n t y e a r s . Es p e c i a l l y t he c o n t r o v e r s i a l i s s ue s o f c ur r e n t t e c hn o l o y g s e c t o r a n d t h e d i f f e r e n t p e r s p e c t i v e s o f i r o n - ma k i n g we r e a n a l y s i s e d a n d c a r d e d. Th e d i r e c t i o n f o r t h e f u t u r e d e v e l o p me n t o f Ch i n e s e i r o n — ma k i n g t e c h n o l o y g wa s a l s o d i s c u s s e d. Ke y wo r ds: i r o n- ma k i n g;c o k e r a t e;f u e l r a t i o
中国古代炼铁历史
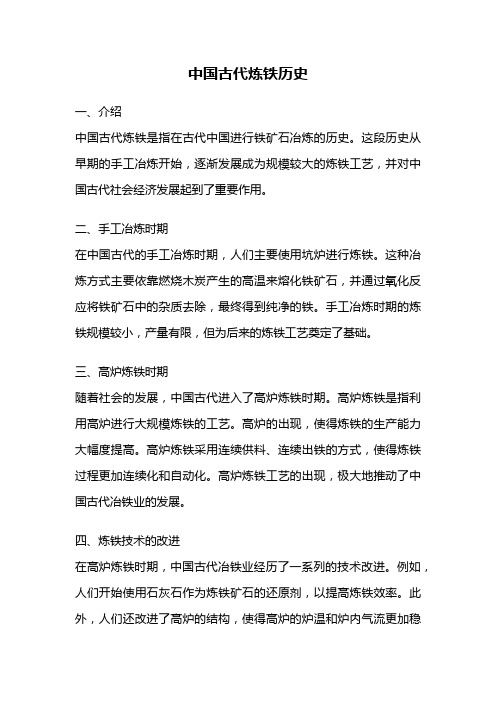
中国古代炼铁历史一、介绍中国古代炼铁是指在古代中国进行铁矿石冶炼的历史。
这段历史从早期的手工冶炼开始,逐渐发展成为规模较大的炼铁工艺,并对中国古代社会经济发展起到了重要作用。
二、手工冶炼时期在中国古代的手工冶炼时期,人们主要使用坑炉进行炼铁。
这种冶炼方式主要依靠燃烧木炭产生的高温来熔化铁矿石,并通过氧化反应将铁矿石中的杂质去除,最终得到纯净的铁。
手工冶炼时期的炼铁规模较小,产量有限,但为后来的炼铁工艺奠定了基础。
三、高炉炼铁时期随着社会的发展,中国古代进入了高炉炼铁时期。
高炉炼铁是指利用高炉进行大规模炼铁的工艺。
高炉的出现,使得炼铁的生产能力大幅度提高。
高炉炼铁采用连续供料、连续出铁的方式,使得炼铁过程更加连续化和自动化。
高炉炼铁工艺的出现,极大地推动了中国古代冶铁业的发展。
四、炼铁技术的改进在高炉炼铁时期,中国古代冶铁业经历了一系列的技术改进。
例如,人们开始使用石灰石作为炼铁矿石的还原剂,以提高炼铁效率。
此外,人们还改进了高炉的结构,使得高炉的炉温和炉内气流更加稳定,有利于炼铁反应的进行。
这些技术改进使得中国古代炼铁工艺更加高效和先进。
五、炼铁的影响中国古代炼铁的发展对中国古代社会经济产生了重要影响。
首先,炼铁工艺的进步提高了铁的产量和质量,满足了农业、军事等领域对铁的需求。
其次,炼铁业的发展也推动了其他相关产业的发展,例如铁矿石的开采、木炭的制造等。
最后,炼铁业的兴盛也带动了城市的发展,形成了一定规模的铁工聚落。
六、炼铁工艺的传承中国古代炼铁工艺的传承主要通过师徒传承的方式进行。
经验丰富的老师傅将自己的技术和经验传授给年轻的学徒,使其掌握炼铁的技术和工艺。
这种传承方式保证了炼铁技术的传承和发展,并且使得中国古代炼铁工艺得以延续。
七、总结中国古代炼铁历史经历了从手工冶炼到高炉炼铁的演变过程,炼铁技术也随着时间的推移得到了不断的改进和发展。
炼铁业的兴盛对中国古代社会经济产生了重要影响,推动了铁器的制造和其他相关产业的发展。
唐代科技的发展与成就

唐代科技的发展与成就唐代是中国历史上最辉煌的时期之一,不仅在文化、艺术等方面取得了重大的成就,而且在科技方面也有许多惊人的发展和创新。
唐代的科技成就对中国的现代化进程和世界的历史进程都产生了深远的影响。
1.农业科技的发展唐代是中国农业科技发展的一个重要时期。
古代农耕技术主要是依靠耕牛、犁等工具对土地进行耕作,而唐代则发明了一种陶制犁,称为犁耙,它分为两部分,一端是犁,另一端是耙,使用时需要反复翻转,既可犁地,又可平整土地。
这种犁的使用,减轻了农民的劳动强度,同时也提高了耕作效率。
唐代还发明了一种灌溉工具——水车。
唐代的水车外形和结构和现代的水车极为相似,但它是由马、牛、人等动力驱动,不同于现代电驱动的水泵。
水车的使用解决了大量的用水问题,使农田得以保持水源充足,增加了产量。
2.炼铁技术的进步唐代,炼铁技术出现了较大的进步。
唐代民间炼铁技术以膜法炼铁为主,它是将生铁放在铁沙中间,在沙内火烧成熟铁,砸开膜后就可以得到铁块。
唐代人还发明了一种新的炼铁工艺——火炉炼铁法。
火炉炼铁法是将生铁放在炉内,加上木炭,加热熔化,通过水流出铜汁而制成铜铁。
这种炼铁方法反应迅速、热量高,可以在更短的时间内完成炼铁过程,炼出的质量也较高。
唐代的炼铁技术进步,也为国家的生产和财政提供了一定的保障。
3.造纸技术的成熟唐代是世界造纸史上的重要时期,这一时期的造纸技术也达到了前所未有的成熟水平。
唐代人采用了二十多种纸品材料,如槐皮、草等。
唐代还发明了用植物残枝可以制纸的方法,是金丝楠材料纸张的重要来源。
唐朝时期,纸张用于会计账目、书籍、官方记录等方面,大大提高了文化和行政管理的效率。
唐代的造纸技术没有逐渐丧失,而是在后代科学家的努力下,不断创新,沿袭至今。
4.船舶科技的进步唐代的航海科技进步也非常显著。
在船舶领域,唐代人发明了舵轮、铸铜传动和拥有可变幅度的帆船,使航行更顺畅、更为安全。
唐代时期传说中的郑和凭着这样的科技,率领的船队曾七下西洋,访问了东南亚、印度、沙特等地,扩大了我国的交往及影响力。
中国古代炼铁技术的发展

中国古代炼铁技术的发展稿子一:嗨,亲爱的小伙伴们!今天咱们来聊聊中国古代炼铁技术的发展,这可太有意思啦!你知道吗,早在春秋时期,咱们老祖宗就开始捣鼓炼铁这事儿啦。
那时候的炼铁技术还比较简单,不过已经迈出了重要的第一步哟。
他们发现了铁矿石能变成有用的铁,就像发现了一个大宝藏。
到了战国时期,炼铁技术可是有了大进步。
人们琢磨出了更多的办法,让炼出来的铁更纯、更好用。
这铁做出来的工具,可比以前的石头、木头厉害多啦,干起活来那叫一个顺手。
秦汉的时候呀,炼铁规模越来越大。
国家也重视起来,专门弄了好多炼铁的地方。
那场面,可热闹啦!炼出来的铁不光能做农具,还能打造兵器,保卫国家呢。
再往后到了唐宋,炼铁技术更是越来越厉害。
新的方法不断出现,铁的质量也越来越好。
而且呀,不光是数量多,品种也丰富起来,什么铁锅、铁锁,生活里到处都能看到铁制品。
明清时期呢,炼铁技术那是炉火纯青啦。
不光自己用,还能出口到别的国家,让外国人也见识见识咱们中国的厉害。
怎么样,中国古代炼铁技术的发展是不是超级牛?咱们的老祖宗可真是聪明又厉害!稿子二:亲爱的朋友们,咱们来聊聊中国古代炼铁技术的神奇发展!一开始的时候啊,炼铁就像小孩子学走路,跌跌撞撞的。
但是古人聪明呀,不断尝试,不断摸索。
春秋那阵子,炼铁刚刚起步。
虽然技术还不太成熟,但大家的热情可高啦。
一点点地积累经验,就盼着能炼出好铁。
等到了汉朝,那可不得了。
炼铁的炉子变大了,技术也改进了不少。
炼出来的铁越来越多,能做的东西也越来越丰富。
唐朝的时候,炼铁就像是开了挂。
各种巧妙的法子都被想出来了,铁的品质那叫一个棒。
老百姓的生活因为有了铁制品,变得更加方便。
宋朝呢,炼铁业更是红红火火。
不光在国内到处都用铁,还传到了周边的国家,让他们都羡慕咱们。
元朝的时候,虽然打仗多,但是炼铁也没落下。
照样能炼出好用的铁来。
到了明朝和清朝,炼铁技术已经非常成熟啦。
不管是大的物件还是小的玩意儿,用铁做起来都不在话下。
高炉炼铁技术装备进步
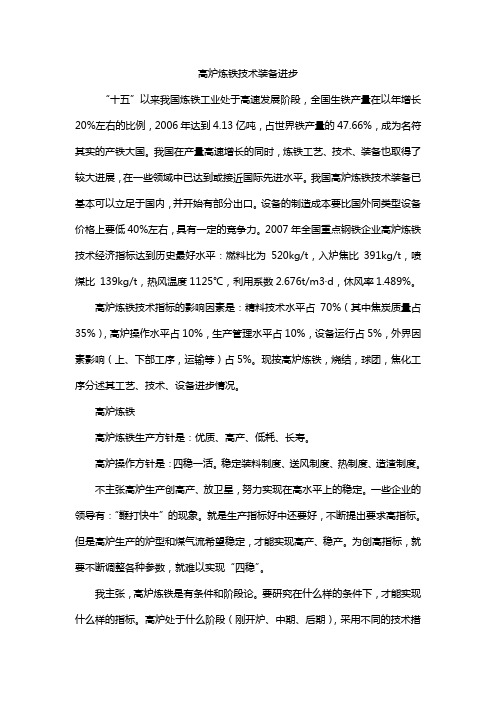
高炉炼铁技术装备进步“十五”以来我国炼铁工业处于高速发展阶段,全国生铁产量在以年增长20%左右的比例,2006年达到4.13亿吨,占世界铁产量的47.66%,成为名符其实的产铁大国。
我国在产量高速增长的同时,炼铁工艺、技术、装备也取得了较大进展,在一些领域中已达到或接近国际先进水平。
我国高炉炼铁技术装备已基本可以立足于国内,并开始有部分出口。
设备的制造成本要比国外同类型设备价格上要低40%左右,具有一定的竞争力。
2007年全国重点钢铁企业高炉炼铁技术经济指标达到历史最好水平:燃料比为520kg/t,入炉焦比 391kg/t,喷煤比139kg/t,热风温度1125℃,利用系数2.676t/m3〃d,休风率1.489%。
高炉炼铁技术指标的影响因素是:精料技术水平占70%(其中焦炭质量占35%),高炉操作水平占10%,生产管理水平占10%,设备运行占5%,外界因素影响(上、下部工序,运输等)占5%。
现按高炉炼铁,烧结,球团,焦化工序分述其工艺、技术、设备进步情况。
高炉炼铁高炉炼铁生产方针是:优质、高产、低耗、长寿。
高炉操作方针是:四稳一活。
稳定装料制度、送风制度、热制度、造渣制度。
不主张高炉生产创高产、放卫星,努力实现在高水平上的稳定。
一些企业的领导有:“鞭打快牛”的现象。
就是生产指标好中还要好,不断提出要求高指标。
但是高炉生产的炉型和煤气流希望稳定,才能实现高产、稳产。
为创高指标,就要不断调整各种参数,就难以实现“四稳”。
我主张,高炉炼铁是有条件和阶段论。
要研究在什么样的条件下,才能实现什么样的指标。
高炉处于什么阶段(刚开炉、中期、后期),采用不同的技术措施,实现什么样的指标。
高炉炼铁要讲科学,减少人为主观因素的影响。
不能不讲条件,只要先进指标,这不是用科学发展观炼铁。
当前,我国高炉炼铁存在的最大技术问题,就是原燃料质量不稳定,造成高炉生产难以稳定。
“一活”是指炉缸活跃。
评价炉缸活跃的指标是:一是高炉鼓风能否吹透中心料柱(要求风速要高,中心煤气CO2含量要高)。
宋朝的冶金与工艺
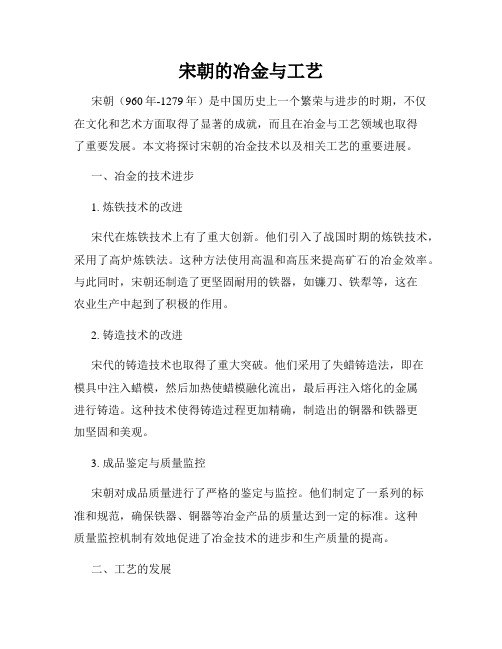
宋朝的冶金与工艺宋朝(960年-1279年)是中国历史上一个繁荣与进步的时期,不仅在文化和艺术方面取得了显著的成就,而且在冶金与工艺领域也取得了重要发展。
本文将探讨宋朝的冶金技术以及相关工艺的重要进展。
一、冶金的技术进步1. 炼铁技术的改进宋代在炼铁技术上有了重大创新。
他们引入了战国时期的炼铁技术,采用了高炉炼铁法。
这种方法使用高温和高压来提高矿石的冶金效率。
与此同时,宋朝还制造了更坚固耐用的铁器,如镰刀、铁犁等,这在农业生产中起到了积极的作用。
2. 铸造技术的改进宋代的铸造技术也取得了重大突破。
他们采用了失蜡铸造法,即在模具中注入蜡模,然后加热使蜡模融化流出,最后再注入熔化的金属进行铸造。
这种技术使得铸造过程更加精确,制造出的铜器和铁器更加坚固和美观。
3. 成品鉴定与质量监控宋朝对成品质量进行了严格的鉴定与监控。
他们制定了一系列的标准和规范,确保铁器、铜器等冶金产品的质量达到一定的标准。
这种质量监控机制有效地促进了冶金技术的进步和生产质量的提高。
二、工艺的发展1. 瓷器工艺的创新宋代以其精美的瓷器而闻名于世。
在宋朝时期,通过改进瓷土的配方、采用更先进的烧制工艺,制造出了细腻而具有独特色彩的汝窑、哥窑、官窑等名瓷。
这些瓷器在装饰技法和釉彩处理上都达到了极高的艺术水平,成为世界陶瓷史上的瑰宝。
2. 织锦工艺的繁荣宋代的织锦工艺在中国历史上也达到了巅峰。
宋代织锦以其精湛的技艺和华丽的纹样而闻名于世。
与此同时,宋代的染色技术也取得了重大突破,使织锦与染色相得益彰。
宋代织锦的流行不仅为传统的服饰和家居装饰增添了华丽的光彩,更在一定程度上推动了中国纺织业的发展。
3. 造纸工艺的提升宋代的造纸工艺逐渐得到改进和提升。
他们通过研究和实践,改良了纸浆的配方和纸张的加工工艺,使得制造的纸张更加均匀、柔韧和耐用。
在宋朝,造纸工艺的进步不仅极大地促进了知识传播和书写文化的繁荣,也为后来的纸张制造工艺提供了宝贵的经验。
炼铁工艺的发展与创新从传统到现代

炼铁工艺的发展与创新从传统到现代炼铁工艺是铁矿石经过一系列工艺流程,将其转化为钢铁的过程。
随着科学技术的不断进步与发展,炼铁工艺也在不断创新和改进。
本文将从传统到现代的角度,探讨炼铁工艺的发展与创新。
一、传统炼铁工艺的演进传统炼铁工艺主要包括高炉法和直接还原法两种。
高炉法是将铁矿石、焦炭和石灰石等原料放入高炉中,在高温下进行还原反应,产生炼铁渣和铁水。
而直接还原法则是将铁矿石与还原剂(如氢气、甲烷等)直接反应,得到铁水。
然而,传统炼铁工艺存在一些问题。
首先,高炉法需要大量使用焦炭作为还原剂,导致能源消耗和环境污染问题。
其次,直接还原法虽然能够节约部分能源,但其还原效率较低,产出的铁水品质也不稳定。
二、基于传统的工艺改进为了解决传统炼铁工艺存在的问题,研究人员开始进行基于传统的工艺改进。
其中一个重要的改进是炼铁炉的结构优化。
通过改变炉膛形状、燃烧方式等,提高炼铁的效率和品质。
此外,还通过添加助熔剂、改变添加时间等方式,进一步优化炼铁工艺。
除了结构改进,工艺改进还包括了炼铁原料的优化选择。
研究人员通过对不同铁矿石的分析和试验,选择更优质的原料,以提高炼铁产品的品质。
同时,也研究了不同焦炭种类和添加量对炼铁过程的影响,为提高炼铁效率和环保性做出了贡献。
三、现代炼铁工艺的创新随着新材料和新技术的不断涌现,现代炼铁工艺得到了进一步的创新。
其中一个重要的创新是氧化还原反应的电磁过程控制技术。
通过在炼铁炉中加入电磁线圈,对炼铁过程中的温度、浓度等参数进行准确控制,提高炼铁效率和产品品质。
另外,为了降低能源消耗和环境污染,现代炼铁工艺还采用了先进的喷射燃烧技术。
该技术通过将高温燃烧产生的废气进行再循环利用,提高炼铁过程中的能量利用率。
同时,还采用了新型炉衬材料和高效能耗炉墙结构,减少了炼铁过程中的热损失。
除了这些技术创新,现代炼铁工艺还注重炼铁过程的数据采集与分析。
通过对炼铁过程中各个参数进行监测和分析,研究人员能够更好地控制和优化炼铁工艺。
- 1、下载文档前请自行甄别文档内容的完整性,平台不提供额外的编辑、内容补充、找答案等附加服务。
- 2、"仅部分预览"的文档,不可在线预览部分如存在完整性等问题,可反馈申请退款(可完整预览的文档不适用该条件!)。
- 3、如文档侵犯您的权益,请联系客服反馈,我们会尽快为您处理(人工客服工作时间:9:00-18:30)。
我国炼铁工艺技术的进步沙永志 滕飞 曹军(钢铁研究总院,北京100081)摘要:本文介绍了近年来我国炼铁生产状况和工艺技术方面的改进。
我国球团生产能力已达到2亿吨,主要归功于链篦机-回转窑工艺的快速应用。
烧结技术进步的特征是烧结机大型化,厚料层烧结,余热回收,以及烟气脱硫。
焦炭质量的改进依赖于焦炉大型化,干熄焦,煤调湿,以及捣固焦技术的应用。
高炉的技术进步体现在高炉大型化,高利用系数,低燃料比,高风温,干法除尘,喷煤工艺改进,新的高炉设备,先进的工艺监控技术,以及污染控制等。
直接还原和熔融还原技术也在开发过程中。
关键词:球团,烧结,焦炭,高炉,炼铁TECHNOLOGICAL IMPROVEMENTS OF IRONMAKING IN CHINASha Yongzhi Teng Fei Cao Jun(Central Iron & Steel Research Institute,Beijing 100081)Abstract: This paper introduces recent ironmaking production status and technological improvements in China. Pellet production capacity has reached up to 180 Mt in 2009, mainly due to quick application of grate-kiln process. Sinter process progress is characterized as sinter machine enlarging, deep bed sintering, heat recovery, and desulphurization application. Coke quality is improved by means of coke oven enlarging, coke dry quenching, coal moisture control and stamp charged technology applications. Progress of BF process consists of BF enlarging, high productivity, low fuel rate, high blast temperature, dry gas cleaning application, PCI technology improvement, new BF facilities, advanced process monitor techniques, and pollution control etc. Direct reduction process and smelting reduction process are under development.Key words: Pellet, sinter, coke, blast furnace, iron making1. 引言近年来,在我国国民经济持续高速增长的动力驱动下,我国的炼铁生产规模发生了巨大变化,产量由1999年的1.24亿吨增加到2010年的5.9亿吨。
产量的增加除了依靠新建和扩建炼铁产能外,整个系统的工艺改进和技术进步也发挥了重要的作用。
我国的炼铁几乎全部是高炉流程,各企业和相关单位围绕高炉流程的降低成本、节能降耗、以及污染控制,开展了大量的富有成效的工艺和技术改进工作。
2. 球团2.1 产量及生产工艺在过去的十年里,我国球团生产的发展速度令人吃惊,从1999年的仅1194万吨猛增到2009年的1.8亿吨(生产能力),而且目前的增长趋势仍在继续。
有力地支撑了炼铁产量的增加。
在各种球团生产工艺中,链篦机-回转窑工艺的贡献最大,竖炉工艺也作出了很好的贡献(见图1)。
2.2 工艺技术进步(1) 工艺优化链篦机-回转窑工艺,由于其生产能力大,球团质量好,能耗低,原料适应能力强,在开发成功后得到快速推广应用。
2000年,首钢开发成功第一套年产1百万吨的链篦机-回转窑球团生产线。
迄今为止,约有近百条该工艺生产线建成投产。
大部分生产能力在60~200万吨/年。
最大的是武钢鄂州的500万吨/年生产线,建成于2005年,且从土建开始到投产仅用13竖炉链篦机-回转窑带式机个月。
竖炉工艺在比例上正在被链篦机-回转窑工艺替代。
但目前仍有200余套装置。
多数是8~10m2规格,单机产量在30~40万吨/年。
从1970年至2009年,带式机工艺一直保持两条生产线。
一个是鞍钢的 321m2 ,另一个是包钢的162 m2。
2010年4月,首钢京唐建成了504 m2带式机生产线,能力为4百万吨/年。
(2) 生产指标的改进伴随着行业节能降耗的大趋势,球团的生产指标也得到显著的改进。
A. 皂土配比降低曾经许多竖炉的皂土配比超过40 kg/t。
现在通过多种改进措施,包括细磨精矿、开发新型复合皂土、增加润磨系统、精粉干燥等,使皂土配比得到显著降低。
目前平均的皂土配比是:竖炉工艺21.2kg/t,链篦机-回转窑和带式机工艺是18.7 kg/t。
但从总的情况看,仍有改进的空间。
B. 球团品位增加由于精矿品位的提高和皂土配比的降低,球团品位提高了2~4个百分点。
通常竖炉球团品位为62%,链篦机-回转窑球团为63.5%。
通过继续改进选矿工艺,该指标还将得到提高。
C. 能耗降低通过全方位的改进,每个工艺的能耗均在不断降低。
目前平均竖炉工艺的能耗是35.6 kgce/t,链篦机-回转窑工艺是27.6 kgce/t。
先进的指标是18.15 kgce/t (首钢球团厂)。
在此方面,先进工艺和生产规模显示其优势。
3. 烧结为了支撑快速增长的铁水产量,我国已大幅度提高其烧结矿的生产能力。
据不完全统计,2009年全国有500余台烧结机,总烧结面积达53800 m2,约生产6亿吨烧结矿。
烧结工艺改进体现在以下几方面:(1) 烧结机尺寸扩大目前,许多钢铁企业都建了大烧结机。
最大的是去年投产的太钢一台 660 m2烧结机。
据2009年统计,≥180m2 烧结机的数量达到125台,总烧结面积为38590 m2 [2].(2) 厚料层烧结为充分利用其蓄热能力和质量均匀等特点,各烧结厂普遍实施了厚料层烧结技术。
许多烧结机的料层厚度达到600 mm 以上。
在京唐550 m2烧结机上实现了 800 mm 厚料层烧结[3]. 其固体燃耗是48.3kg/t,转鼓强度77.65%,FeO含量7.7%。
厚料层烧结需要强化制粒,以保证烧结混合料良好的透气性。
同时还要求偏析布料,使得料层上下的温度分布一致。
许多新建烧结机采取宽皮带(1.2~5.5 m)+多辊(6~11) 布料的方式来替代老式泥辊+反射板的结构,取得良好效果。
(3) 工艺优化固体燃料分加方法已在一些厂的生产实践中采用,其控制烧结气氛和提高烧结速度的效果已得到证明。
生石灰已被用来部分或全部替代石灰石,体现了改进制粒和烧结的良好效果。
一些厂尝试了熔剂分加来改善烧结矿的质量,证明对高褐铁矿比例的混合料是有效的。
随着低品质矿在烧结混合料中比例的增加,为保持烧结产量和烧结矿质量,各厂采取了多种措施,如利用综合料场稳定混合料组成、加强混合料制粒、使用在线水分测量仪精确控制混合料水分、混合料蒸汽预热、增加料层厚度、检测料面平整度、采用烧结专家系统精确控制烧结终点等。
中南大学开发了新的复合造块(CAP)工艺[4]. 该工艺将原料分成两组:一组是球团料,另一组是基料。
将球团料造成8~16 mm 酸性生球,基料制成3~8 mm 高碱度混合料,然后二者混合后布到烧结机上。
CAP 工艺已于2009年6月成功应用到包钢一台 265 m2 烧结机。
在使用35%的本地低品质精矿和1.5碱度的条件下,该生产线生产的烧结矿质量与1.9碱度的烧结矿相同,而且利用系数更高,固体燃耗更低[5]。
(4) 余热回收及节能对众多烧结厂来说,通过热交换器回收冷却烧结矿烟气的余热已是一个普遍的实践。
一些厂将部分热烟气直接用作点火炉的助燃空气(热风点火)和点火炉后的保温段,起到很好的降低点火燃气消耗和改善烧结层表面质量的效果。
在越来越多的新建烧结厂中,安装了余热发电设备来回收烧结环冷机烟气的热量。
2005年,首套为两台300m 2烧结机建的17.5MW 发电设备在马钢建成投产。
从2006年至2009年8月,共发电 2.345 亿 度。
近年来,烧结主抽风机的变频控制(VVVF )得到应用。
它通过改变风机供电的频率而不是阀门的开度来调节抽风负压,达到节电的目的。
它同时避免了短时停烧结机而不停风机所造成的能量浪费。
据报道,一个400m 2烧结机配用变频控制后,节电达30%。
许多烧结厂在布料矿槽采用了蒸汽预热技术。
与在混料筒内蒸汽预热的方法比较,该技术可提高蒸汽利用率高达80%,预热烧结混合料温度超过65℃,并保持了布到烧结机上混合料最小的温降。
在减小烧结机漏风率方面,各厂均开展了卓有成效的工作。
其中,新的机头机尾密封装置能够将烧结机本体的漏风率降低到20%;复合磁性密封技术则可对烧结机两侧进行有效密封,控制漏风率在30%以下。
传统的环冷机有30~45%的漏风率。
而新的液体密封设计能够将该处的漏风率降低到5%以下,节约20%的风机电耗[2] (4) 污染控制近年来,烧结工序的污染控制得到行业的重视。
机头机尾的烟气含尘量要求低于50 mg/Nm 3。
为满足这一要求,需要采取布袋+静电除尘器的方式。
新的除尘设备也在开发过程中。
随着环保制度的加强,越来越多的烧结厂正在安装烟气脱硫装置。
脱硫工艺种类繁多,包括:石灰/石膏法,硫氨法,镁法,CFB ,浓相吸收法(见图2),MEROS, NID, 以及活性碳法等。
SO 2 的脱除率一般可超过90%。
其中,活性碳法已于2010年应用到太钢一台 450m 2 烧结机。
该方法除脱硫外,还可同时脱除NOx 和二噁英。
4. 焦炭质量改进我国是世界最大的焦炭生产国,以支撑其巨大的炼铁生产规模。
2009年焦炭产量达到3.53亿吨。
随着高炉容积加大和喷煤比的提高,焦炭质量越来越成为维持高炉稳定顺行的关键因素。
所采取的改进焦炭质量4个主要措施简述如下。
(1) 焦炉大型化焦炉大型化能显著增加装煤的密度。
与4.3m 炭化室的750kg/m 3密度相比,7.63m 焦炉的密度平均达到821.2 kg/m 3。
大焦炉的焦炭质量更加均匀一致。
从2005年 至 2009年, 所建的 ≥4.3 m 焦炉的总能力达到 144 Mt/a。
其中仅在2009年, 71% 是 ≥5.5 m 的捣鼓焦炉和 ≥6 m 的顶装焦炉。