精密和超精密加工产业研究报告
超精密加工技术研究现状及发展趋势
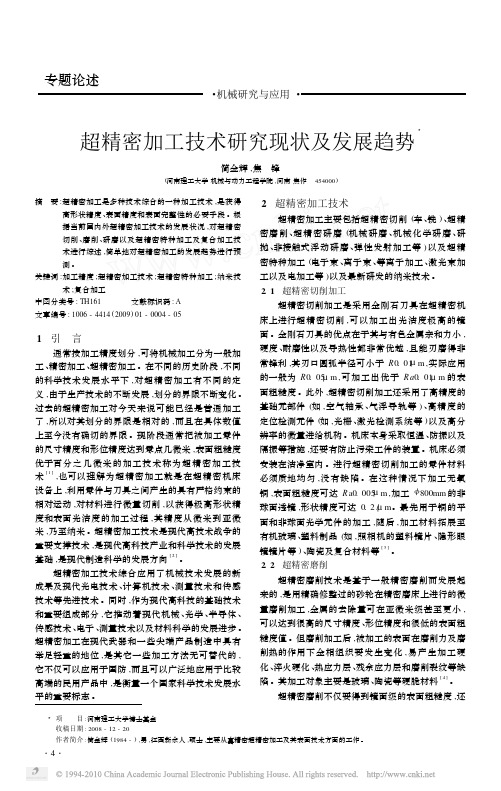
超精密磨削不仅要得到镜面级的表面粗糙度 ,还
3 项 目 :河南理工大学博士基金 收稿日期 : 2008 - 12 - 20 作者简介 :简金辉 (1984 - ) ,男 ,江西新余人 ,硕士 ,主要从事精密超精密加工及其表面技术方面的工作 。
·4·
专题论述
·机械研究与应用 ·
要保证能够获得精确的几何形状和尺寸 。目前超精 密磨削的加工目标是 3~5nm 的平滑表面 ,也就是通 过磨削加工而不需抛光即可达到要求的表面粗糙度 。 砂轮的修整技术相当关键 。尽管磨削比研磨更能有 效地去除物质 ,但在磨削玻璃或陶瓷时很难获得镜 面 ,主要是由于砂轮粒度太细时 ,砂轮表面容易被切 屑堵塞 。日本理化学研究所学者大森整博士发明的 电解在线修整 ( EL ID )铸铁纤维结合剂 ( C IFB )砂轮 技术可以很好地解决这个问题 。主要的修整方法还 有电化学在线控制修整 ( ECD ) [ 5 ] 、干式 ECD[ 6 ] 、电化 学放电加工 ( ECDM ) [ 7 ] 、激光辅助修整 [ 8 ] 、喷射压力 修整 [ 9 ]等 。 2. 3 超精密研磨
精密和超精密加工现状与发展趋势
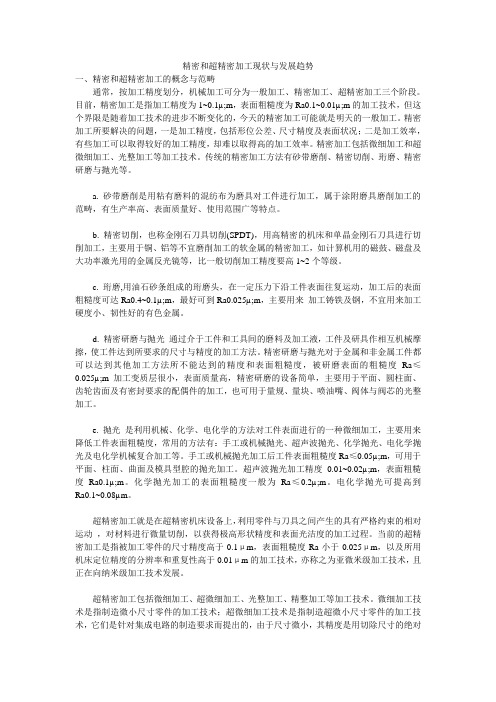
精密和超精密加工现状与发展趋势一、精密和超精密加工的概念与范畴通常,按加工精度划分,机械加工可分为一般加工、精密加工、超精密加工三个阶段。
目前,精密加工是指加工精度为1~0.1µ;m,表面粗糙度为Ra0.1~0.01µ;m的加工技术,但这个界限是随着加工技术的进步不断变化的,今天的精密加工可能就是明天的一般加工。
精密加工所要解决的问题,一是加工精度,包括形位公差、尺寸精度及表面状况;二是加工效率,有些加工可以取得较好的加工精度,却难以取得高的加工效率。
精密加工包括微细加工和超微细加工、光整加工等加工技术。
传统的精密加工方法有砂带磨削、精密切削、珩磨、精密研磨与抛光等。
a. 砂带磨削是用粘有磨料的混纺布为磨具对工件进行加工,属于涂附磨具磨削加工的范畴,有生产率高、表面质量好、使用范围广等特点。
b. 精密切削,也称金刚石刀具切削(SPDT),用高精密的机床和单晶金刚石刀具进行切削加工,主要用于铜、铝等不宜磨削加工的软金属的精密加工,如计算机用的磁鼓、磁盘及大功率激光用的金属反光镜等,比一般切削加工精度要高1~2个等级。
c. 珩磨,用油石砂条组成的珩磨头,在一定压力下沿工件表面往复运动,加工后的表面粗糙度可达Ra0.4~0.1µ;m,最好可到Ra0.025µ;m,主要用来加工铸铁及钢,不宜用来加工硬度小、韧性好的有色金属。
d. 精密研磨与抛光通过介于工件和工具间的磨料及加工液,工件及研具作相互机械摩擦,使工件达到所要求的尺寸与精度的加工方法。
精密研磨与抛光对于金属和非金属工件都可以达到其他加工方法所不能达到的精度和表面粗糙度,被研磨表面的粗糙度Ra≤0.025µ;m加工变质层很小,表面质量高,精密研磨的设备简单,主要用于平面、圆柱面、齿轮齿面及有密封要求的配偶件的加工,也可用于量规、量块、喷油嘴、阀体与阀芯的光整加工。
e. 抛光是利用机械、化学、电化学的方法对工件表面进行的一种微细加工,主要用来降低工件表面粗糙度,常用的方法有:手工或机械抛光、超声波抛光、化学抛光、电化学抛光及电化学机械复合加工等。
超精密加工技术与设备研究

超精密加工技术与设备研究随着科学技术的发展,各种新兴产业的不断涌现,超精密加工技术的应用越来越广泛。
超精密加工技术是指以nm甚至A级为计量单位的高精度加工技术,这种技术可以加工出极为精细的器件、零部件和微型器械等。
近年来,随着光通信、半导体和微机电系统等高新技术的不断发展,超精密加工技术成为了对这些高科技的支撑和发展起到至关重要的作用。
一、超精密加工技术的研究超精密加工技术不仅是现代制造业的一个重要方向,也是当前世界各国争夺高端装备制造市场的关键技术之一。
超精密加工技术具有下列特点:1. 高精度超精密加工技术的加工精度一般在0.1μm以下,甚至可以达到0.01nm。
这种高精度的加工不仅可以满足现代工业的精密加工要求,而且对于微传感器、微机电系统等新兴工业领域的发展也必不可少。
2. 高成本超精密加工需要使用高端的加工设备和高精度的测量仪器,这些设备通常需要耗费巨大的资金才能购买。
此外,加工过程的高要求和长周期也会带来高成本。
3. 高技术门槛超精密加工技术对操作人员的技术要求非常高,需要具备高度的专业知识和操作经验。
因此,这种技术对人员的培训和技术水平的提高也是非常重要的。
二、超精密加工设备的分类超精密加工设备通常可以分为以下几类:1. 雕刻机雕刻机是一种采用非接触方式加工的机床,可以在非接触情况下对工件表面进行加工。
它的加工精度可以达到大约0.1μm,适用于制造光学玻璃、金属模具等精密零件。
2. 电解加工机电解加工机是一种采用电化学反应进行加工的机床,其加工精度可以达到0.1μm以下。
它适用于制造形状复杂的工件和微加工零部件。
3. 雷射加工机雷射加工机是一种采用激光束进行加工的机床,其加工精度可以达到0.1μm以下。
它适用于制造微电子元件、微机械零件和光学器件等。
雷射加工机还可以利用激光束切割薄片材料,以满足高端装备制造的需要。
三、超精密加工技术的应用超精密加工技术的应用非常广泛,主要包括以下几个方面:1. 半导体加工在半导体加工领域,超精密加工是一个非常重要的领域,它可以制造出一些超细的、数量巨大的半导体芯片。
超精密加工技术的发展现状
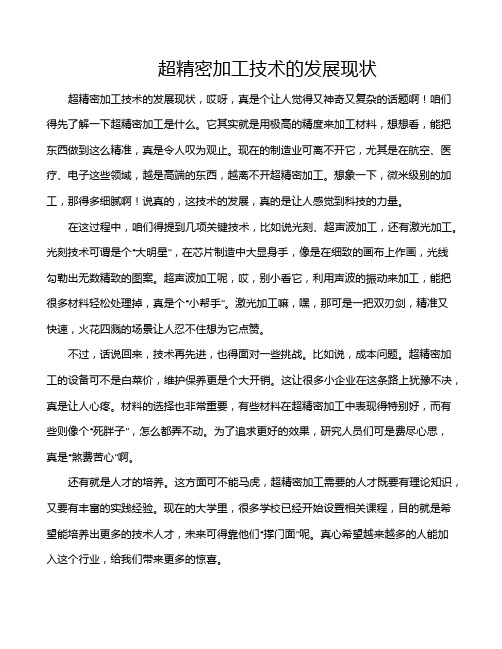
超精密加工技术的发展现状超精密加工技术的发展现状,哎呀,真是个让人觉得又神奇又复杂的话题啊!咱们得先了解一下超精密加工是什么。
它其实就是用极高的精度来加工材料,想想看,能把东西做到这么精准,真是令人叹为观止。
现在的制造业可离不开它,尤其是在航空、医疗、电子这些领域,越是高端的东西,越离不开超精密加工。
想象一下,微米级别的加工,那得多细腻啊!说真的,这技术的发展,真的是让人感觉到科技的力量。
在这过程中,咱们得提到几项关键技术,比如说光刻、超声波加工,还有激光加工。
光刻技术可谓是个“大明星”,在芯片制造中大显身手,像是在细致的画布上作画,光线勾勒出无数精致的图案。
超声波加工呢,哎,别小看它,利用声波的振动来加工,能把很多材料轻松处理掉,真是个“小帮手”。
激光加工嘛,嘿,那可是一把双刃剑,精准又快速,火花四溅的场景让人忍不住想为它点赞。
不过,话说回来,技术再先进,也得面对一些挑战。
比如说,成本问题。
超精密加工的设备可不是白菜价,维护保养更是个大开销。
这让很多小企业在这条路上犹豫不决,真是让人心疼。
材料的选择也非常重要,有些材料在超精密加工中表现得特别好,而有些则像个“死胖子”,怎么都弄不动。
为了追求更好的效果,研究人员们可是费尽心思,真是“煞费苦心”啊。
还有就是人才的培养。
这方面可不能马虎,超精密加工需要的人才既要有理论知识,又要有丰富的实践经验。
现在的大学里,很多学校已经开始设置相关课程,目的就是希望能培养出更多的技术人才,未来可得靠他们“撑门面”呢。
真心希望越来越多的人能加入这个行业,给我们带来更多的惊喜。
说到应用,超精密加工的舞台可大了!像航天器、手术刀、手机的内部零件等等,几乎无处不在。
你看看,航天器上那些复杂的零部件,没有超精密加工,恐怕就飞不起来了!还有手术刀,医生可不能用个普通的刀子,精细的切口直接关系到手术的成功与否,这可是关乎生命的大事啊!而手机的微小零件,哪个能离开超精密加工的加持?所以说,这技术的重要性,不用多说,大家都懂。
精密和超精密加工技术现状和发展趋势

精密和超精密加工技术现状和发展趋势1.引言国际上在超精密加工技术方面处于领先地位的国家有美国、德国和日本发达国家中,美国、日本、德国等在高技术领域(如国防工业、集成电路、信息技术产业等)之所以一直领先,与这些国家高度重视和发展精密、超精密制造技术有极其重要的关系。
由于加工技术水平的发展,精密和超精密加工划分的界限逐渐向前推移,但在具体数值上没有确切的定义。
被加工零件的尺寸精度在 1.0~0.1μm,表面粗糙度Ra在0.1~0.03μm之间的加工方法称为精密加工。
超精密加工当前是指被加工零件的尺寸精度高于0.1μm,表面粗糙度Ra小于0.025μm,以及所用机床定位精度的分辨率和重复性高于0.01μm的加工技术,亦称之为亚微米级加工技术,且正在向纳米级加工技术发展超精密加工技术主要包括:超精密加工的机理,超精密加工的设备制造技术,超精密加工工具及刃磨技术,超精密测量技术和误差补偿技术,超精密加工工作环境条件。
2.发展现状美国是开展研究最早的国家,也是迄今处于世界领先地位的国家。
早在50年代末,由于航天等尖端技术发展的需要,美国首先发展了金刚石刀具的超精密切削技术,并发展了相应的空气轴承主轴的超精密机床,用于加工激光核聚变反射镜、战术导弹及载人飞船用球面、非球面大型零件。
20世纪80年代后期,美国通过能源部“激光核聚变项目”和陆、海、空三军“先进制造技术开发计划”,对超精密金刚石切削机床的开发研究,投入了巨额资金和大量人力,实现了大型零件的微英寸超精密加工。
如美国劳伦斯利弗莫尔国家实验室已经研制出一台大型光学金刚石车床(Large Op tics Diam ond Turn ing Machine, LODTM ), 是一台最大加工直径为1.63m的立式车床,定位精度可达28nm,借助在线误差补偿能力,它已实现了距离超过1m而直线度误差只有±25nm 的加工。
在美国能源部支持下,LLI实验室和Y-12工厂合作,与1983年成功地研制出大型超精密金刚石车床(DTM—3型)。
精密加工和超精密加工的研究与对策

采用液体静压轴承或空气静压轴承的主轴和导轨 , 精 密滚 珠丝 杠传动 , 有微动 工作 台、 配 误差 补偿 装置 , 实
现微 位移 。 ②高 刚度 。除零 、 件本 身 的 刚度 外 , 应 注 意 部 还
接触 刚度 , 同时应 考 虑 由工 件 、 床 、 具 、 具 所 组 机 刀 夹
精密 加工和 超精密 加工是 现代 制造 技术 的前沿 ,
2 精 密 加 工 和 超 精 密 加 工 的 内涵 …
随着 现代工 业 的不断 发展 , 密加 工和超精 密加 精
工 在 机械 、 电子 、 轻工 、 国防等 领域 占有 愈来愈 重要 及
因为许多先 进技术 产 品需要 以高精 度制 造 , 密加工 精
毫 题 论 述
・
机械 研 究 与 应 用 ・
精 密 加 工 和 超 精 密 加 工 的 研 究 与 对 策
程 0 300)
摘
要: 在简述精 密、 超精 密加工 内涵和 重要性的基础上 , 重点分析 了影响精密、 超精 密加 工的 因素及 采取 对策。针对
p o e sn u o t r u o w r . rc s i g o o rc u r a e p t r ad f n y f Ke r s r iin p o e s g l a p e iin p o e sn ;a v n e n ua trn c oo y;a ay i ; y wo d :p e so rc s i ;u t r cso rc si g d a c d ma fcu i g t h lg c n r en n lss
从 先进制 造技术 的技 术实质 性 而论 , 主要有 精密
超精密加工技术的理论和应用研究

超精密加工技术的理论和应用研究超精密加工技术是指在微米和纳米级别下进行的精密加工过程。
随着现代科技的不断发展,超精密加工技术越来越受到重视,并广泛应用于电子、光学、航空航天和生物医疗等领域。
1. 超精密加工技术的发展历程超精密加工技术的发展历程可以追溯到20世纪50年代末期,当时主要应用于金属和陶瓷的球面加工和制造。
随着微电子技术的不断进步,超精密加工技术被广泛运用于微电子制造和微机电系统(MEMS)中,如晶体管、光学元件、压电陶瓷和生物芯片等。
在后来的发展中,超精密加工技术逐渐扩展到玻璃、塑料和石英等非金属材料的加工上。
同时,超精密加工技术还被应用于卫星、航天器和精密仪器的制造和维修中。
2. 超精密加工技术的理论基础超精密加工技术的理论基础主要涉及到两个方面:加工力学和加工控制。
加工力学研究表明,超精密加工过程中的切削作用受到材料本身的特性、切削工具的形状和刃口尺寸、切削速度和切削深度的影响。
因此,了解加工物料的相关特性并选择适当的切削参数,对加工质量和加工效率的提高具有重要意义。
加工控制方面的研究主要涉及到加工路径规划、加工速度和切削深度的控制以及加工设备的精度检测等。
3. 超精密加工技术在电子制造领域中的应用在电子制造领域中,超精密加工技术被广泛应用于半导体器件的制造和加工。
例如,通过超精密加工技术制作的半导体器件可以达到微米甚至纳米级别的精度,从而大大提高了器件的性能和稳定性。
此外,超精密加工技术还可以用于电子元器件的制造,如阻值、电容器和电感器等。
通过超精密加工技术制作的电子元器件具有更好的性能和精度,可以提高电路的稳定性和可靠性。
4. 超精密加工技术在航空航天领域中的应用在航空航天领域中,超精密加工技术主要应用于航空发动机部件的制造和维修。
例如,通过超精密加工技术制造的涡轮叶片具有更好的气动性能和材料特性,可以提高发动机的性能和效率。
同时,超精密加工技术还可以用于航空航天器件的制造和加工,如导航系统和通信设备等。
精密和超精密加工技术的发展
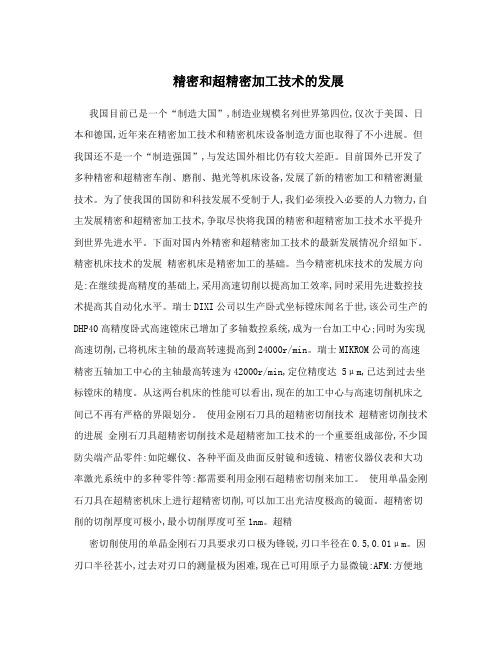
精密和超精密加工技术的发展我国目前已是一个“制造大国”,制造业规模名列世界第四位,仅次于美国、日本和德国,近年来在精密加工技术和精密机床设备制造方面也取得了不小进展。
但我国还不是一个“制造强国”,与发达国外相比仍有较大差距。
目前国外已开发了多种精密和超精密车削、磨削、抛光等机床设备,发展了新的精密加工和精密测量技术。
为了使我国的国防和科技发展不受制于人,我们必须投入必要的人力物力,自主发展精密和超精密加工技术,争取尽快将我国的精密和超精密加工技术水平提升到世界先进水平。
下面对国内外精密和超精密加工技术的最新发展情况介绍如下。
精密机床技术的发展精密机床是精密加工的基础。
当今精密机床技术的发展方向是:在继续提高精度的基础上,采用高速切削以提高加工效率,同时采用先进数控技术提高其自动化水平。
瑞士DIXI公司以生产卧式坐标镗床闻名于世,该公司生产的DHP40高精度卧式高速镗床已增加了多轴数控系统,成为一台加工中心;同时为实现高速切削,已将机床主轴的最高转速提高到24000r/min。
瑞士MIKROM公司的高速精密五轴加工中心的主轴最高转速为42000r/min,定位精度达5μm,已达到过去坐标镗床的精度。
从这两台机床的性能可以看出,现在的加工中心与高速切削机床之间已不再有严格的界限划分。
使用金刚石刀具的超精密切削技术超精密切削技术的进展金刚石刀具超精密切削技术是超精密加工技术的一个重要组成部份,不少国防尖端产品零件:如陀螺仪、各种平面及曲面反射镜和透镜、精密仪器仪表和大功率激光系统中的多种零件等:都需要利用金刚石超精密切削来加工。
使用单晶金刚石刀具在超精密机床上进行超精密切削,可以加工出光洁度极高的镜面。
超精密切削的切削厚度可极小,最小切削厚度可至1nm。
超精密切削使用的单晶金刚石刀具要求刃口极为锋锐,刃口半径在0.5,0.01μm。
因刃口半径甚小,过去对刃口的测量极为困难,现在已可用原子力显微镜:AFM:方便地进行测量。
精密和超精密加工机床的现状及发展对策

工作台尺寸 (宽×长) 800 mm×1 500 mm
最大加工高度
500 mm
最大通过宽度
1 100 mm
工作台进给速度
0.01~30 m/min
砂轮尺寸 (外径×宽) Φ510 mm×100 mm
砂轮转速
1 000~4 000 r/min
砂轮最小进刀量
0.2 μm
在高精度加工的范畴内, 根据精度水平的不 同, 分为 3 个档次:
2
Oct. 2010
第27卷 第10期 Vol.27 No.10
精 度 为 0.3~3 μm, 粗 糙 度 为 0.03~0.3 μm 的 为 精密加工;
精 度 为 0.03~0.3 μm, 粗 糙 度 为 0.005~0.03 μm 的称作超精密加工, 或亚微米加工;
年度 2000 2003 2006 2007
表1 我国机床进出口情况 (亿 美元)
产值 21.97 23.80 64.00 111.9
出口 2.99 3.80 11.90 16.50
进口 18.90 41.60 72.40 70.70
消费 37.88 67.00 131.10 166.10
由于国外对我们封锁禁运一些重要的高精度机 床设备和仪器, 而这些精密设备仪器正是国防和尖 端技术发展所迫切需要的, 因此, 我们必须投入必 要的人力物力, 自主发展精密和超精密加工机床, 使我国的国防和科技发展不会受制于人。
磨头0 mm/min
磨头的横向进给速度 1~4 000 mm/min
砂轮轴驱动电机
11 kW (4P)
机床尺寸 (宽×长×高) 约3 600 mm×5 800 mm×3 700 mm
对精密和超精密加工技术的认识
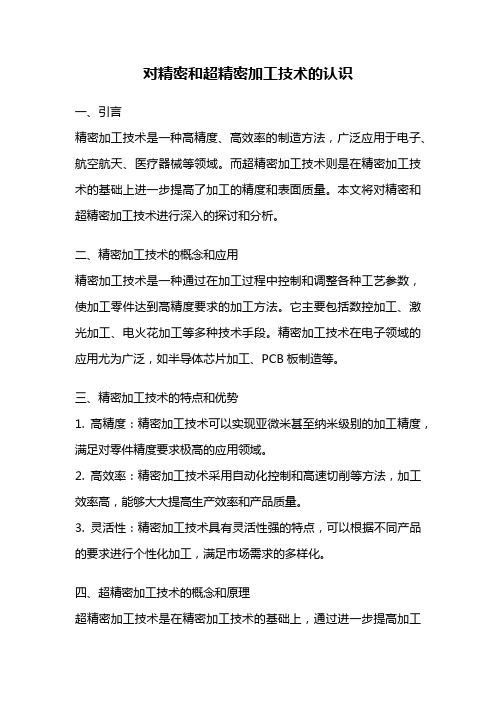
对精密和超精密加工技术的认识一、引言精密加工技术是一种高精度、高效率的制造方法,广泛应用于电子、航空航天、医疗器械等领域。
而超精密加工技术则是在精密加工技术的基础上进一步提高了加工的精度和表面质量。
本文将对精密和超精密加工技术进行深入的探讨和分析。
二、精密加工技术的概念和应用精密加工技术是一种通过在加工过程中控制和调整各种工艺参数,使加工零件达到高精度要求的加工方法。
它主要包括数控加工、激光加工、电火花加工等多种技术手段。
精密加工技术在电子领域的应用尤为广泛,如半导体芯片加工、PCB板制造等。
三、精密加工技术的特点和优势1. 高精度:精密加工技术可以实现亚微米甚至纳米级别的加工精度,满足对零件精度要求极高的应用领域。
2. 高效率:精密加工技术采用自动化控制和高速切削等方法,加工效率高,能够大大提高生产效率和产品质量。
3. 灵活性:精密加工技术具有灵活性强的特点,可以根据不同产品的要求进行个性化加工,满足市场需求的多样化。
四、超精密加工技术的概念和原理超精密加工技术是在精密加工技术的基础上,通过进一步提高加工设备的精度和加工工艺的控制精度,实现更高精度加工的一种技术手段。
超精密加工技术主要包括超精密车削、超精密磨削、超精密拓扑等方法。
五、超精密加工技术的应用领域超精密加工技术在光学仪器、航空航天、精密仪器等领域具有广泛的应用。
例如,在光学仪器领域,超精密加工技术可以用于制造高精度的光学元件,提高光学系统的分辨率和成像质量。
六、精密和超精密加工技术的发展趋势随着科技的进步和工业制造的需求,精密和超精密加工技术也在不断发展和创新。
未来的发展趋势主要包括以下几个方面:1. 加工精度的提高:随着需求的增加,对加工精度的要求也越来越高,未来的精密和超精密加工技术将进一步提高加工的精度和表面质量。
2. 加工效率的提高:随着自动化技术和智能化技术的发展,精密和超精密加工技术将更加高效,加工速度更快,生产效率更高。
精密和超精密加工技术的新进展
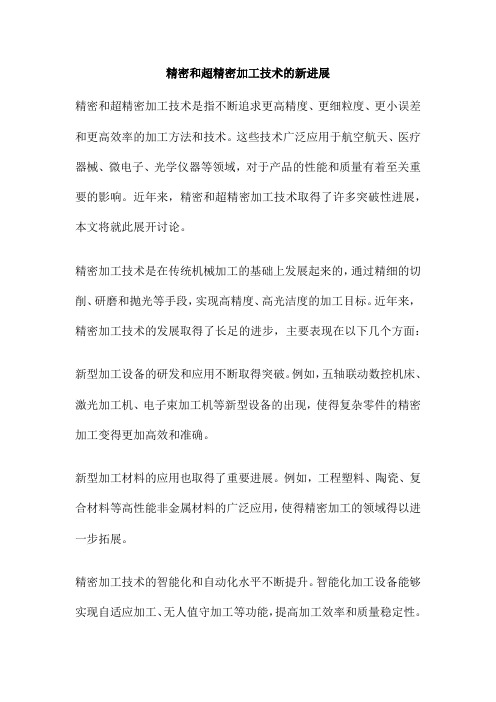
精密和超精密加工技术的新进展精密和超精密加工技术是指不断追求更高精度、更细粒度、更小误差和更高效率的加工方法和技术。
这些技术广泛应用于航空航天、医疗器械、微电子、光学仪器等领域,对于产品的性能和质量有着至关重要的影响。
近年来,精密和超精密加工技术取得了许多突破性进展,本文将就此展开讨论。
精密加工技术是在传统机械加工的基础上发展起来的,通过精细的切削、研磨和抛光等手段,实现高精度、高光洁度的加工目标。
近年来,精密加工技术的发展取得了长足的进步,主要表现在以下几个方面:新型加工设备的研发和应用不断取得突破。
例如,五轴联动数控机床、激光加工机、电子束加工机等新型设备的出现,使得复杂零件的精密加工变得更加高效和准确。
新型加工材料的应用也取得了重要进展。
例如,工程塑料、陶瓷、复合材料等高性能非金属材料的广泛应用,使得精密加工的领域得以进一步拓展。
精密加工技术的智能化和自动化水平不断提升。
智能化加工设备能够实现自适应加工、无人值守加工等功能,提高加工效率和质量稳定性。
超精密加工技术是指比精密加工技术更为精细、精确的加工方法和技术。
随着科技的不断进步,超精密加工技术的应用越来越广泛,主要包括以下几个方面:超精密加工技术广泛应用于微电子领域。
微电子产业对于芯片的精度和光洁度要求极高,超精密加工技术能够实现高精度、高效率的微米级加工,对于提升微电子产业的发展水平和竞争力具有重要意义。
超精密加工技术在光学仪器领域也有着广泛的应用。
光学仪器对于透镜、反射镜等光学元件的精度和表面质量要求极高,超精密加工技术能够实现高精度、高稳定性的光学元件加工,对于提高光学仪器的性能和精度具有重要作用。
再次,超精密加工技术在航空航天领域也有着重要的应用。
航空航天领域对于零件的精度和可靠性要求极为严格,超精密加工技术能够实现高精度、高稳定性的零件加工,对于提升航空航天领域的产品质量和性能具有重要意义。
近年来,精密和超精密加工技术的研究和应用不断取得新的进展,在新型加工设备、新型加工材料和智能化加工等方面都取得了重要突破。
精密和超精密加工技术
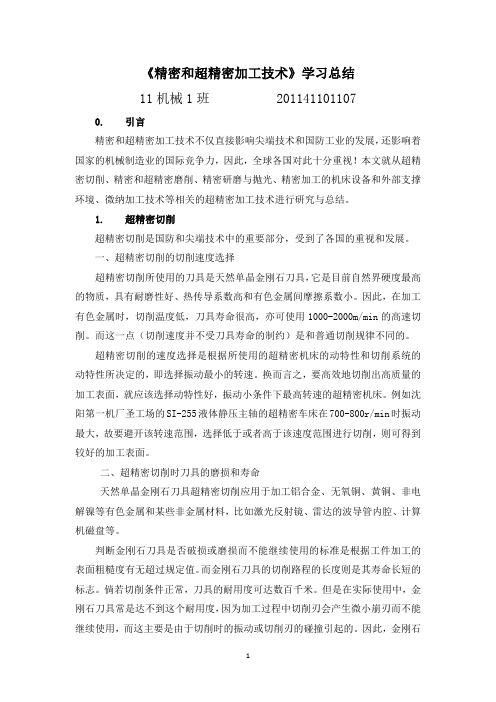
《精密和超精密加工技术》学习总结11机械1班 2011411011070. 引言精密和超精密加工技术不仅直接影响尖端技术和国防工业的发展,还影响着国家的机械制造业的国际竞争力,因此,全球各国对此十分重视!本文就从超精密切削、精密和超精密磨削、精密研磨与抛光、精密加工的机床设备和外部支撑环境、微纳加工技术等相关的超精密加工技术进行研究与总结。
1. 超精密切削超精密切削是国防和尖端技术中的重要部分,受到了各国的重视和发展。
一、超精密切削的切削速度选择超精密切削所使用的刀具是天然单晶金刚石刀具,它是目前自然界硬度最高的物质,具有耐磨性好、热传导系数高和有色金属间摩擦系数小。
因此,在加工有色金属时,切削温度低,刀具寿命很高,亦可使用1000-2000m/min的高速切削。
而这一点(切削速度并不受刀具寿命的制约)是和普通切削规律不同的。
超精密切削的速度选择是根据所使用的超精密机床的动特性和切削系统的动特性所决定的,即选择振动最小的转速。
换而言之,要高效地切削出高质量的加工表面,就应该选择动特性好,振动小条件下最高转速的超精密机床。
例如沈阳第一机厂圣工场的SI-255液体静压主轴的超精密车床在700-800r/min时振动最大,故要避开该转速范围,选择低于或者高于该速度范围进行切削,则可得到较好的加工表面。
二、超精密切削时刀具的磨损和寿命天然单晶金刚石刀具超精密切削应用于加工铝合金、无氧铜、黄铜、非电解镍等有色金属和某些非金属材料,比如激光反射镜、雷达的波导管内腔、计算机磁盘等。
判断金刚石刀具是否破损或磨损而不能继续使用的标准是根据工件加工的表面粗糙度有无超过规定值。
而金刚石刀具的切削路程的长度则是其寿命长短的标志。
倘若切削条件正常,刀具的耐用度可达数百千米。
但是在实际使用中,金刚石刀具常是达不到这个耐用度,因为加工过程中切削刃会产生微小崩刃而不能继续使用,而这主要是由于切削时的振动或切削刃的碰撞引起的。
因此,金刚石刀具只能使用在机床主轴转动非常平稳的高精度机床上,而刀具的维护对机床的要求亦是如此。
超精密机械制造技术研究
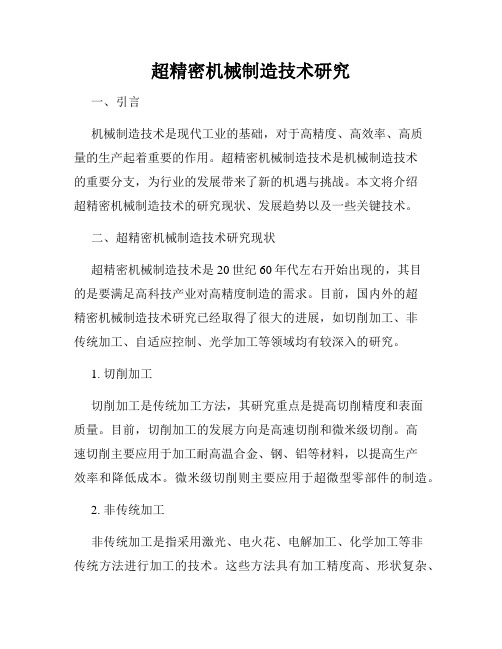
超精密机械制造技术研究一、引言机械制造技术是现代工业的基础,对于高精度、高效率、高质量的生产起着重要的作用。
超精密机械制造技术是机械制造技术的重要分支,为行业的发展带来了新的机遇与挑战。
本文将介绍超精密机械制造技术的研究现状、发展趋势以及一些关键技术。
二、超精密机械制造技术研究现状超精密机械制造技术是20世纪60年代左右开始出现的,其目的是要满足高科技产业对高精度制造的需求。
目前,国内外的超精密机械制造技术研究已经取得了很大的进展,如切削加工、非传统加工、自适应控制、光学加工等领域均有较深入的研究。
1. 切削加工切削加工是传统加工方法,其研究重点是提高切削精度和表面质量。
目前,切削加工的发展方向是高速切削和微米级切削。
高速切削主要应用于加工耐高温合金、钢、铝等材料,以提高生产效率和降低成本。
微米级切削则主要应用于超微型零部件的制造。
2. 非传统加工非传统加工是指采用激光、电火花、电解加工、化学加工等非传统方法进行加工的技术。
这些方法具有加工精度高、形状复杂、工件硬度高等优点,因此被广泛用于微机电系统(MEMS)、光学设备、半导体器件等领域。
3. 自适应控制自适应控制是指在机床加工过程中对加工条件进行自适应调节,以实现高精度、高效率的加工。
自适应控制的关键是实时采集加工过程中的信息,对加工参数进行调整以达到最优化的加工效果。
该技术适用于加工复杂曲面和超硬材料。
4. 光学加工光学加工是利用激光将能量聚焦在工件表面,以实现高精度的加工。
在光学加工中,激光的波长对加工精度有着非常重要的影响。
如在微细加工中,波长越小加工的精度越高。
目前,脉冲激光加工的加工精度已经可以达到亚微米级别。
三、超精密机械制造技术的发展趋势超精密机械制造技术的发展趋势是集成化、自动化、智能化、高速化和柔性化。
集成化技术是利用自动化技术将加工、检测、装备和控制等部分集成在一起,实现一条龙服务。
自动化技术是通过机器人等装备对加工过程进行监控和控制,以提高生产效率和加工精度。
超精密加工技术的发展现状
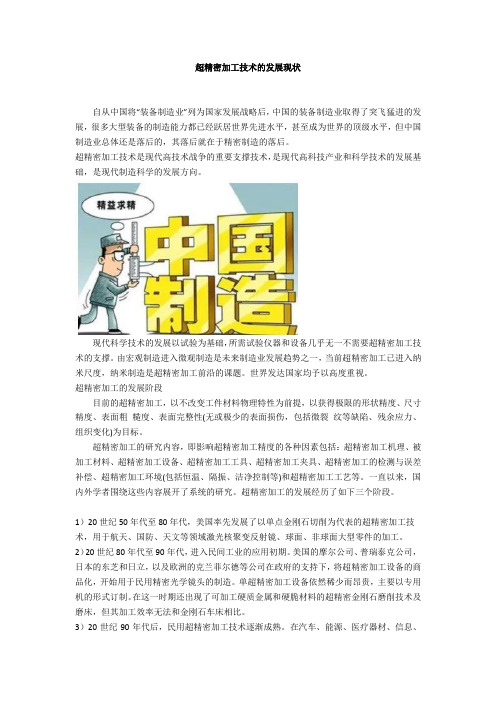
超精密加工技术的发展现状自从中国将“装备制造业”列为国家发展战略后,中国的装备制造业取得了突飞猛进的发展,很多大型装备的制造能力都已经跃居世界先进水平,甚至成为世界的顶级水平,但中国制造业总体还是落后的,其落后就在于精密制造的落后。
超精密加工技术是现代高技术战争的重要支撑技术,是现代高科技产业和科学技术的发展基础,是现代制造科学的发展方向。
现代科学技术的发展以试验为基础,所需试验仪器和设备几乎无一不需要超精密加工技术的支撑。
由宏观制造进入微观制造是未来制造业发展趋势之一,当前超精密加工已进入纳米尺度,纳米制造是超精密加工前沿的课题。
世界发达国家均予以高度重视。
超精密加工的发展阶段目前的超精密加工,以不改变工件材料物理特性为前提,以获得极限的形状精度、尺寸精度、表面粗糙度、表面完整性(无或极少的表面损伤,包括微裂纹等缺陷、残余应力、组织变化)为目标。
超精密加工的研究内容,即影响超精密加工精度的各种因素包括:超精密加工机理、被加工材料、超精密加工设备、超精密加工工具、超精密加工夹具、超精密加工的检测与误差补偿、超精密加工环境(包括恒温、隔振、洁净控制等)和超精密加工工艺等。
一直以来,国内外学者围绕这些内容展开了系统的研究。
超精密加工的发展经历了如下三个阶段。
1)20世纪50年代至80年代,美国率先发展了以单点金刚石切削为代表的超精密加工技术,用于航天、国防、天文等领域激光核聚变反射镜、球面、非球面大型零件的加工。
2)20世纪80年代至90年代,进入民间工业的应用初期。
美国的摩尔公司、普瑞泰克公司,日本的东芝和日立,以及欧洲的克兰菲尔德等公司在政府的支持下,将超精密加工设备的商品化,开始用于民用精密光学镜头的制造。
单超精密加工设备依然稀少而昂贵,主要以专用机的形式订制。
在这一时期还出现了可加工硬质金属和硬脆材料的超精密金刚石磨削技术及磨床,但其加工效率无法和金刚石车床相比。
3)20世纪90年代后,民用超精密加工技术逐渐成熟。
超精密机床加工技术研究与应用

超精密机床加工技术研究与应用随着科技的不断进步与发展,超精密机床加工技术已成为现代制造业中一项不可或缺的关键技术。
它以其高精度、高效率和高稳定性的特点,广泛应用于航空航天、汽车制造、电子设备等行业,对提升产品质量和生产效益发挥了重要作用。
超精密机床加工技术的核心之一是控制系统。
在加工过程中,通过精确的控制手段,能够实现对机床各种参数的调节和控制,从而保证加工过程的准确性和稳定性。
目前,自适应控制、非线性控制和神经网络控制等新兴技术在超精密机床加工中得到了广泛应用。
这些技术不仅在控制精度和稳定性方面有着显著的提高,而且能够有效地降低机床的能耗和生产成本,提高生产效益。
在材料加工方面,超精密机床加工技术也取得了长足的进步。
传统的机床加工方式往往会因切削力大、切削温度高等原因导致材料的残余应力增大,从而影响产品的使用寿命和性能。
而超精密机床加工技术通过采用高速切削、微尺度切削和超精密切削等现代加工手段,能够有效地降低切削力和切削温度,减少残余应力的产生,从而提高产品的质量和性能。
此外,超精密机床加工技术在产品设计和生产方面也发挥了重要作用。
通过引入CAD/CAM和虚拟仿真等先进技术,能够对产品进行准确的建模和参数化设计,实现产品的数字化和可视化管理。
同时,借助先进的模拟和仿真工具,能够对加工过程进行全面的优化和预测,从而降低产品开发周期和成本。
超精密机床加工技术的应用领域广泛,其中最具代表性的是航空航天领域。
在航天器的制造过程中,由于航天器的体积大、质量轻,因此对制造工艺的要求尤为严格。
超精密机床加工技术能够实现对航天器各种复杂零部件的高精度加工和组装,从而保证航天器的整体性能和安全性。
此外,超精密机床加工技术还能够实现对特殊材料的加工,如钛合金、复合材料等,为航空航天领域的发展提供了坚实的技术支撑。
在汽车制造领域,超精密机床加工技术也发挥了重要作用。
随着汽车工业的快速发展,对汽车零部件的加工精度和质量要求越来越高。
精密与超精密加工技术综述

就先进制造技术的技术实质性而论,主要有精密和超精密加工技术和制造自动化两大领域1。
前者包括了精密加工、超精密加工、微细加工,以及广为流传的纳米加工,它追求加工上的精度和表面质量的极限,可统称为精密工程;后者包括了设计、制造和管理的自动化,它不仅是快速响应市场需求、提高生产率、改善劳动条件的重要手段,而且是提高产品质量的有效方式。
两者有密切联系,许多精密和超精密加工要靠自动化技术才能达到预期目标,而不少制造自动化则有赖于精密加工才能达到设计要求。
精密工程和制造自动化具有全局性的、决策性的作用,是先进制造技术的支柱。
精密和超精密加工与国防工业有密切关系。
导弹是现代战争的重要武器,其命中精度由惯性仪表的精度所决定,因而需要高超的精密和超精密加工设备来制造这种仪表。
例如,美国“民兵”型洲际导弹系统的陀螺仪其漂移率为0.03~0.05°/h,加速度计敏感元件不允许有0.05μm的尘粒,它的命中精度的圆概率误差为500m;MX战略导弹(可装载10个核弹头),由于其制导系统陀螺仪精度比“民兵—Ⅲ”型导弹要高出一个数量级,因而其命中精度的圆概率误差仅为50~150m。
对射程4000km的潜射弹道导弹,当潜艇的位置误差对射程偏差的影响为400m、潜艇速度误差对射程偏差的影响为800m、惯性平台的垂直对准精度对射程偏差的影响为400m时,要求惯性导航的陀螺仪的漂移精度为0.001°/h、航向精度在1′以上、10小时运行的定位精度为0.4~0.7海里,因此,陀螺元件的加工精度必须达到亚微米级,表面粗糙度达到Ra0.012~0.008μm。
由此可知,惯性仪表的制造精度十分关键。
如1kg重的陀螺转子,其质量中心偏离其对称轴为0.5nm时,就会造成100m的射程误差和50m的轨道误差;激光陀螺的平面反射镜的平面度为0.03~0.06μm,表面粗糙度要求为Ra0.012μm以上;红外制导的导弹,其红外探测器中接受红外线的反射镜,其表面粗糙度要求达到Ra0.015~0.01μm[2]。
国外超精密加工技术的现状和发展趋势

国外超精密加工技术的现状和发展趋势1. 引言在当今世界,超精密加工技术已经成为了制造业的重要组成部分。
随着科技的不断发展,国外的超精密加工技术也取得了长足的进步。
本文将从多个角度对国外超精密加工技术的现状和发展趋势进行评估和探讨。
2. 现状分析超精密加工技术是指在微米或纳米级别进行加工的技术,其精度和表面质量要求非常高。
当前,国外一些先进制造业发达国家,如日本、德国和美国等,都在超精密加工技术领域具有举足轻重的地位。
这些国家的企业和研究机构不断推动着超精密加工技术的发展,不断推陈出新,取得了许多创新成果。
3. 技术发展趋势未来,国外超精密加工技术将朝着更高精度、更复杂形状、更多材料的加工方向发展。
随着人工智能、大数据和物联网等新一代信息技术的不断涌现,超精密加工技术将更加智能化、数字化和柔性化。
新型材料、纳米技术的应用,也将极大地拓展超精密加工技术的应用范围。
4. 我的观点我认为,国外超精密加工技术的快速发展将为全球制造业带来深远影响。
随着超精密加工技术在航空航天、医疗器械、电子器件等领域的广泛应用,将极大地推动相关产业的发展。
超精密加工技术的不断突破也将为人类社会带来更多便利和可能性。
5. 总结国外超精密加工技术的现状和发展趋势令人振奋。
技术不断创新,应用领域不断拓展,为制造业注入了新的活力。
我对超精密加工技术的未来充满信心,相信它将在全球范围内发挥越来越重要的作用。
通过本文的介绍和分析,相信您已经对国外超精密加工技术的现状和发展趋势有了更深入的了解。
希望本文能够为您带来一些启发和思考,并对您在相关领域的学习和工作有所帮助。
超精密加工技术在国外的发展已经取得了显著的进步,但仍有许多挑战和机遇。
在不断推动超精密加工技术的发展的国外也在积极探索新的技术路径和应用领域,以应对日益复杂的市场需求和竞争压力。
国外超精密加工技术在材料加工和表面处理方面取得了重大突破。
随着新型材料的广泛应用和纳米技术的发展,超精密加工技术已经能够处理更多种类的材料,包括金属、陶瓷、复合材料等。
精密制造业可行性研究报告

精密制造业可行性研究报告1. 引言精密制造业是现代制造业的重要组成部分,在电子、光学、航空航天、医疗设备等领域发挥着重要的作用。
本文主要通过对精密制造业的市场分析、竞争环境分析、技术要求分析以及资源评估,对精密制造业的可行性进行研究,并提出相应的发展建议。
2. 市场分析精密制造业的市场需求主要来自于电子产品、光学仪器、航空航天设备等行业。
近年来,随着科技的快速发展,这些行业对精密制造业的需求不断增加。
根据市场调研数据显示,预计未来几年,精密制造业的市场将保持稳定增长。
3. 竞争环境分析精密制造业的竞争环境主要来自于国内外企业。
国际大型企业在技术和资金上具备明显优势,而国内企业则更加灵活,对市场变化的反应速度较快。
因此,精密制造业的竞争激烈程度较高。
4. 技术要求分析精密制造业对技术要求较高,其中包括制造工艺、设备精度、质量管理等方面。
制造工艺方面,需要采用先进的加工方法和设备,以确保产品的精密度和稳定性。
设备精度方面,要求设备能够达到极高的精度和稳定性,以满足产品加工的要求。
质量管理方面,需要建立严格的质量控制体系,保证产品的质量稳定性。
5. 资源评估精密制造业所需的资源主要包括人力资源、技术资源和资金资源等方面。
人力资源方面,需要拥有一支具备专业知识和经验的技术团队,以保证生产和质量控制的顺利进行。
技术资源方面,需要与研究机构、大学等进行合作,以获取前沿的研究成果和技术支持。
资金资源方面,需要投入大量的资金用于研发、采购设备和市场推广等。
6. 发展建议基于以上分析,为了使精密制造业能够顺利发展,以下是一些建议:•加强技术研发和创新,不断提升产品的精密度和稳定性,以满足市场需求。
•提高质量管理水平,建立完善的质量控制体系,保证产品的质量稳定性。
•加强与研究机构和大学等的合作,共享资源、技术和研究成果,加快技术进步和创新。
•寻求资金支持,通过引入投资者或与金融机构合作,解决资金需求问题。
•加强市场营销和品牌推广,提升企业知名度和市场竞争力。
超精密加工技术的研究与应用
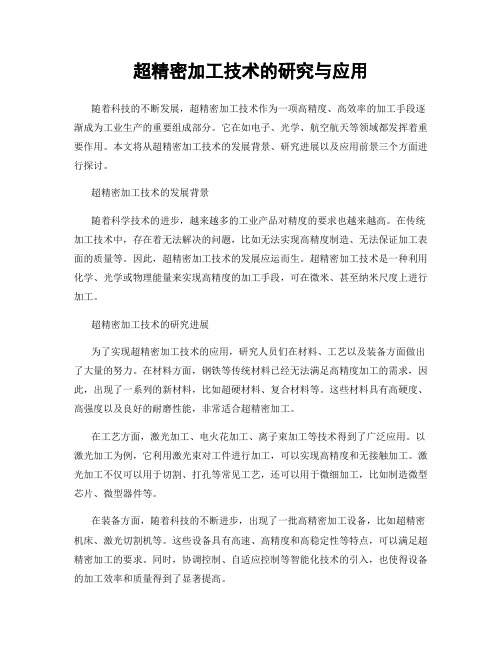
超精密加工技术的研究与应用随着科技的不断发展,超精密加工技术作为一项高精度、高效率的加工手段逐渐成为工业生产的重要组成部分。
它在如电子、光学、航空航天等领域都发挥着重要作用。
本文将从超精密加工技术的发展背景、研究进展以及应用前景三个方面进行探讨。
超精密加工技术的发展背景随着科学技术的进步,越来越多的工业产品对精度的要求也越来越高。
在传统加工技术中,存在着无法解决的问题,比如无法实现高精度制造、无法保证加工表面的质量等。
因此,超精密加工技术的发展应运而生。
超精密加工技术是一种利用化学、光学或物理能量来实现高精度的加工手段,可在微米、甚至纳米尺度上进行加工。
超精密加工技术的研究进展为了实现超精密加工技术的应用,研究人员们在材料、工艺以及装备方面做出了大量的努力。
在材料方面,钢铁等传统材料已经无法满足高精度加工的需求,因此,出现了一系列的新材料,比如超硬材料、复合材料等。
这些材料具有高硬度、高强度以及良好的耐磨性能,非常适合超精密加工。
在工艺方面,激光加工、电火花加工、离子束加工等技术得到了广泛应用。
以激光加工为例,它利用激光束对工件进行加工,可以实现高精度和无接触加工。
激光加工不仅可以用于切割、打孔等常见工艺,还可以用于微细加工,比如制造微型芯片、微型器件等。
在装备方面,随着科技的不断进步,出现了一批高精密加工设备,比如超精密机床、激光切割机等。
这些设备具有高速、高精度和高稳定性等特点,可以满足超精密加工的要求。
同时,协调控制、自适应控制等智能化技术的引入,也使得设备的加工效率和质量得到了显著提高。
超精密加工技术的应用前景超精密加工技术的应用前景非常广阔。
首先,在电子领域,超精密加工技术可以用于制造微型芯片、集成电路等,提高电子产品的性能和可靠性。
其次,在光学领域,超精密加工技术可以用于制造高精度的透镜、棱镜等光学元件,提高光学仪器的分辨率和精度。
此外,在航空航天领域,超精密加工技术可以用于制造高精度的零部件,提高航空器的飞行性能。
精密与超精密加工技术现状和发展展望

精密与超精密加工技术现状和发展展望精密加工技术是一种在当今制造业中非常重要的技术,它的发展与制造业的发展息息相关。
精密加工技术是通过对材料进行高精度的加工来制造出各种精密零部件,这些精密零部件被广泛应用于汽车、航空航天、医疗器械、电子产品等各个领域。
现阶段,精密加工技术已经取得了很大的进步,各种高精度的加工设备和加工工艺层出不穷。
在这些技术发展的基础上,超精密加工技术应运而生。
超精密加工技术是一种相对于精密加工技术更加高端、更加精密的加工技术,它可以实现对材料的超高精度加工,甚至可以达到纳米级的精度。
这种技术对于一些特殊材料的加工非常重要,比如硬质合金、钢、陶瓷等材料。
超精密加工技术的发展展望是非常乐观的。
随着科学技术的不断进步,各种先进的加工设备和工艺将不断涌现。
在这种趋势下,超精密加工技术将会得到更加广泛的应用。
在汽车工业中,超精密加工技术可以用于制造高压油泵的零部件,提高汽车发动机燃油的利用率;在医疗器械领域,超精密加工技术可以用于制造各种医疗器械的零部件,提高医疗器械的精度和安全性。
在未来的发展中,我们还可以看到超精密加工技术将会在航空航天领域得到更广泛的应用。
超精密加工技术可以制造出更加轻巧和高强度的航空零部件,提高航空器的性能和安全性。
超精密加工技术在电子产品领域也有很大的潜力,它可以制造出更小巧、更精密的电子元件,提高电子产品的性能和可靠性。
精密加工技术和超精密加工技术的发展是非常重要的。
它们直接关系到制造业的发展和产品的质量。
相信随着科学技术的不断进步,这些技术将会取得更大的突破,为各个领域带来更多的创新和发展。
精密与超精密加工技术的现状和发展展望精密加工技术是制造业中至关重要的一环,它的发展与制造业的发展密不可分。
精密加工技术通过对材料进行高精度的加工,制造出各种精密零部件,广泛应用于汽车、航空航天、医疗器械、电子产品等各个领域。
当前,精密加工技术已取得了长足的发展,各种高精度加工设备和工艺不断涌现。