模具制造技术 冲压模具装配实例
冲压模具设计和制造实例

冲压模具设计和制造实例冲压模具设计与制造实例例:图1所示冲裁件,材料为A3,厚度为2mm,大批量生产。
试制定工件冲压工艺规程、设计其模具、编制模具零件的加工工艺规程。
零件名称:止动件生产批量:大批材料:A3材料厚度:t=2mm一、冲压工艺与模具设计1.冲压件工艺分析①材料:该冲裁件的材料A3钢是普通碳素钢,具有较好的可冲压性能。
②零件结构:该冲裁件结构简单,并在转角有四处R2圆角,比较适合冲裁。
③尺寸精度:零件图上所有未注公差的尺寸,属自由尺寸,-0.74 0-0.52-0.52-0.52-0.52可按IT14级确定工件尺寸的公差。
孔边距12mm 的公差为-0.11,属11级精度。
查公差表可得各尺寸公差为:零件外形:65 mm 24 mm 30 mm R30 mm R2 mm零件内形:10 mm孔心距:37±0.31mm 结论:适合冲裁。
2.工艺方案及模具结构类型该零件包括落料、冲孔两个工序,可以采用以下三种工艺方案:①先落料,再冲孔,采用单工序模生产。
②落料-冲孔复合冲压,采用复合模生产。
③冲孔-落料连续冲压,采用级进模生产。
方案①模具结构简单,但需要两道工序、两套模具才能完成零件的加工,生产效率较低,难以满足零件大批量生产的需求。
由于零件结构简单,为提高生产效率,主要应采用复合冲裁或级进冲裁方式。
由于孔边距尺寸12 mm 有公差要求,为了更好地保证此尺寸精度,最后确定用复合冲裁方式进行生产。
+0.36 0-0.11工件尺寸可知,凸凹模壁厚大于最小壁厚,为便于操作,所以复合模结构采用倒装复合模及弹性卸料和定位钉定位方式。
3.排样设计查《冲压模具设计与制造》表2.5.2,确定搭边值:两工件间的搭边:a=2.2mm工件边缘搭边:a1=2.5mm步距为:32.2mm条料宽度B=D+2a1=65+2*2.5=70确定后排样图如2所示一个步距内的材料利用率η为:η=A/BS×100%=1550÷(70×32.2)×100%=68.8%查板材标准,宜选900mm×1000mm的钢板,每张钢板可剪裁为14张条料(70mm×1000mm),每张条料可冲378个工件,则η为:η=nA1/LB×100%=378×1550/900×1000×100%=65.1%即每张板材的材料利用率为65.1%4.冲压力与压力中心计算⑴冲压力落料力F总=1.3Ltτ=1.3×215.96×2×450=252.67(KN)其中τ按非退火A3钢板计算。
冲压模具设计实例
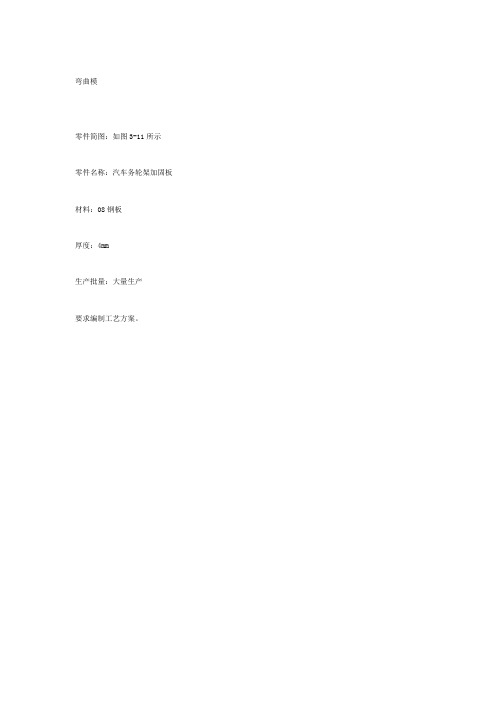
弯曲模零件简图:如图3-11所示零件名称:汽车务轮架加固板材料:08钢板厚度:4mm生产批量:大量生产要求编制工艺方案。
图3-11 汽车备轮架加固板零件图一. 冲压件的工艺分析该零件为备轮架加固板,材料较厚,其主要作用是增加汽车备轮架强度。
零件外形对称,无尖角、凹陷或其他形状突变,系典型的板料冲压件。
零件外形尺寸无公差要求,壁部圆角半径,相对圆角半径为,大于表相关资料所示的最小弯曲半径值,因此可以弯曲成形。
的八个小孔和两个腰圆孔分别均布在零件的三个平面上,孔距有们置要求,但孔径无公差配合。
圆孔精度不高,弯曲角为,也无公差要求。
通过上述工艺分析,可以看出该零件为普通的厚板弯曲件,尺寸精度要求不高,主要是轮廓成形问题,又属大量生产,因此可以用冲压方法生产。
二. 确定工艺方案(1)计算毛坯尺寸该零件的毛坯展开尺寸可按式下式计算:上式中圆角半径;板料厚度;为中性层系数,由表查得;,为直边尺寸,由图3-13可知,将这些数值代入,得毛坯宽度方向的计算尺寸考虑到弯曲时板料纤维的伸长,经过试压修正,实际毛坯尺寸取。
同理,可计算出其他部位尺寸,最后得出如图3-14所示的弯曲毛坯的形状和尺寸。
(2)确定排样方式和计算材料利用率图3-14的毛坯形状和尺寸较大,为便于手工送料,选用单排冲压。
有三种排样方式,见图3-15a、b、c。
由表查得沿送料进方向的搭边,侧向搭边,因此,三种单排样方式产材料利用率分别为64%、64%和70%。
第三种排样方式,落料时需二次送进,但材料利用率最高,为此,本实例可选用第三种排样方法。
图3-14 加固板冲压件展开图a)材料利用率64% b)材料利用率64%c)材料利用率70%图3-15 加固板的排样方式(3)冲压工序性质和工序次数的选择冲压该零件,需要的基本工序和次数有:(a)落料;(b)冲孔6个;(c)冲底部孔2个;(d)冲孔;(e)冲2个腰圆孔;(f)首次弯曲成形;(g)二次弯曲成形。
(1)工序组合及其方案比较根据以上这些工序,可以作出下列各种组合方案。
第九讲冲压模具设计实例分析
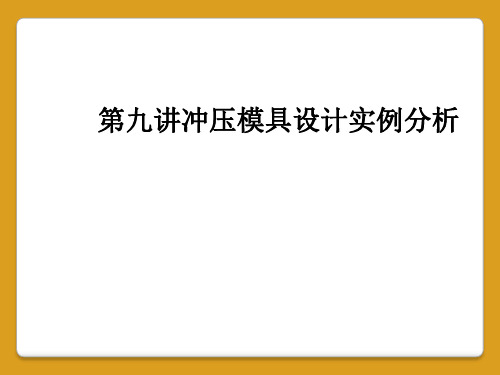
第八章 冲压模具结构及设计
9、模具的装配 根据级进模装配要点,选凹模作为装配基准件,先装下模,再装上模,并调整间隙、试冲、返修。
第八章 冲压模具结构及设计
二、拉深模设计与制造实例
零件名称:端盖 生产批量:大批量 材料:镀锌铁皮 材料厚度:1mm
第八章 冲压模具结构及设计
1、冲压件工艺性分析 冲压工序:落料、拉深; 材料:为镀锌铁皮,具有良好的拉深性能,适合拉深; 结构:简单对称; 精度:全部为自由公差,工件厚度变化也没有作要求,只是该工件作为另一零件的盖,口部尺寸 φ69可稍作小些。而工件总高度尺寸14mm可在拉深后采用修边达要求 。
第八章 冲压模具结构及设计
2、冲压工艺方案的确定 方案一:先落料,后拉深。采用单工序模生产。 方案二:落料-拉深复合冲压。采用复合模生产。 方案三:拉深级进冲压。采用级进模生产。 方案一:模具结构简单,但成本高而生产效率低; 方案二:生产效率较高,尽管模具结构较复杂,但因零件简单对称,模具制造并不困难; 方案三:生产效率高,但模具结构比较复杂,送进操作不方便,加之工件尺寸偏大。 结论:采用方案二为最佳工艺方案。
起粗定距的活动挡料销、弹簧和螺塞选用标准件,规格为8×16。
φ8mm导正销
第八章 冲压模具结构及设计
(3)导料板的设计 (4)卸料部件的设计
① 卸料板的设计 ②卸料螺钉的选用 (5)模架及其它零部件设计
第八章 冲压模具结构及设计
6、模具总装图(右图) 7、冲压设备的选定 8、模具零件加工工艺
模具关键零件因采用线切割,所以这些零件的加工 就变得相对简单。
第八章 冲压模具结构及设计
(4)冲压工序压力计算 拟采用正装复合模,固定卸料与刚性推件。 根据冲压工艺总力计算结果并结合工件高度,初选开式双柱可倾压力机J23-25。
冲压模具设计与制造实例
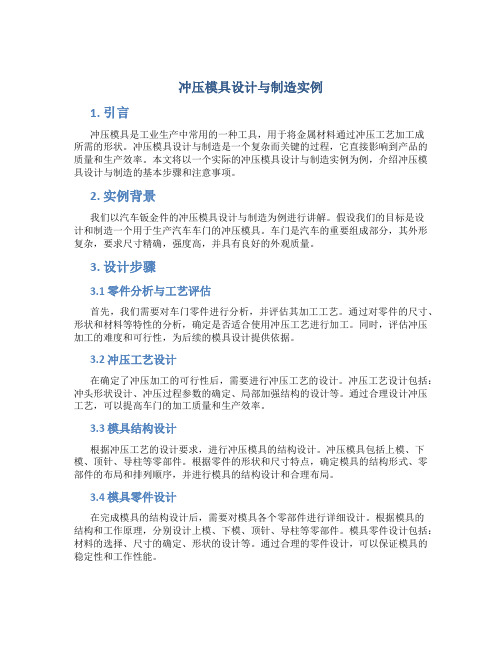
冲压模具设计与制造实例1. 引言冲压模具是工业生产中常用的一种工具,用于将金属材料通过冲压工艺加工成所需的形状。
冲压模具设计与制造是一个复杂而关键的过程,它直接影响到产品的质量和生产效率。
本文将以一个实际的冲压模具设计与制造实例为例,介绍冲压模具设计与制造的基本步骤和注意事项。
2. 实例背景我们以汽车钣金件的冲压模具设计与制造为例进行讲解。
假设我们的目标是设计和制造一个用于生产汽车车门的冲压模具。
车门是汽车的重要组成部分,其外形复杂,要求尺寸精确,强度高,并具有良好的外观质量。
3. 设计步骤3.1 零件分析与工艺评估首先,我们需要对车门零件进行分析,并评估其加工工艺。
通过对零件的尺寸、形状和材料等特性的分析,确定是否适合使用冲压工艺进行加工。
同时,评估冲压加工的难度和可行性,为后续的模具设计提供依据。
3.2 冲压工艺设计在确定了冲压加工的可行性后,需要进行冲压工艺的设计。
冲压工艺设计包括:冲头形状设计、冲压过程参数的确定、局部加强结构的设计等。
通过合理设计冲压工艺,可以提高车门的加工质量和生产效率。
3.3 模具结构设计根据冲压工艺的设计要求,进行冲压模具的结构设计。
冲压模具包括上模、下模、顶针、导柱等零部件。
根据零件的形状和尺寸特点,确定模具的结构形式、零部件的布局和排列顺序,并进行模具的结构设计和合理布局。
3.4 模具零件设计在完成模具的结构设计后,需要对模具各个零部件进行详细设计。
根据模具的结构和工作原理,分别设计上模、下模、顶针、导柱等零部件。
模具零件设计包括:材料的选择、尺寸的确定、形状的设计等。
通过合理的零件设计,可以保证模具的稳定性和工作性能。
4. 制造步骤4.1 模具加工在完成模具设计后,需要进行模具的加工制造。
模具加工包括:材料采购、加工设备的选择、加工工艺的制定等。
根据模具的设计要求,选择适合加工模具的机床设备,进行模具零部件的加工。
加工过程中,需要严格控制尺寸和精度。
4.2 零部件组装模具零部件加工完成后,需要进行零部件的组装。
冲压模具装配设计图解
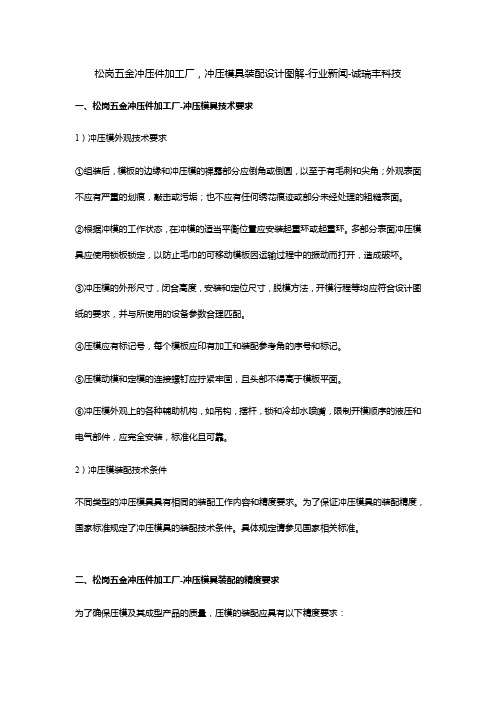
松岗五金冲压件加工厂,冲压模具装配设计图解-行业新闻-诚瑞丰科技一、松岗五金冲压件加工厂-冲压模具技术要求1)冲压模外观技术要求①组装后,模板的边缘和冲压模的裸露部分应倒角或倒圆,以至于有毛刺和尖角;外观表面不应有严重的划痕,敲击或污垢;也不应有任何绣花痕迹或部分未经处理的粗糙表面。
②根据冲模的工作状态,在冲模的适当平衡位置应安装起重环或起重环。
多部分表面冲压模具应使用锁板锁定,以防止毛巾的可移动模板因运输过程中的振动而打开,造成破坏。
③冲压模的外形尺寸,闭合高度,安装和定位尺寸,脱模方法,开模行程等均应符合设计图纸的要求,并与所使用的设备参数合理匹配。
④压模应有标记号,每个模板应印有加工和装配参考角的序号和标记。
⑤压模动模和定模的连接螺钉应拧紧牢固,且头部不得高于模板平面。
⑥冲压模外观上的各种辅助机构,如吊钩,摆杆,锁和冷却水喷嘴,限制开模顺序的液压和电气部件,应完全安装,标准化且可靠。
2)冲压模装配技术条件不同类型的冲压模具具有相同的装配工作内容和精度要求。
为了保证冲压模具的装配精度,国家标准规定了冲压模具的装配技术条件。
具体规定请参见国家相关标准。
二、松岗五金冲压件加工厂-冲压模具装配的精度要求为了确保压模及其成型产品的质量,压模的装配应具有以下精度要求:①冲压模的零件应满足一定的相互定位精度,如同轴度,平行度,垂直度,倾斜度等。
②活动部件应具有相对运动精度的要求,如各种机构的旋转精度,旋转运动精度和线性运动精度。
③指导定位精度例如活动模具和固定模具,或上,下模具的开合运动指导,型腔(凹模)和型芯(冲模)的安装和定位,以及滑动运动的指导和定位。
④匹配精度和接触精度装配精度主要是指相互匹配的零件表面之间应达到的装配间隙或干涉度;例如型腔和型芯,插入件和模板孔,导柱,导套和模板的配合。
接触精度是指两个配合面和连接面之间的指定接触面积和实际接触点的分布程度;例如分型表面上接触点的均匀性,锁紧楔块的倾斜表面的接触产品尺寸等。
冲压模具设计装配图.
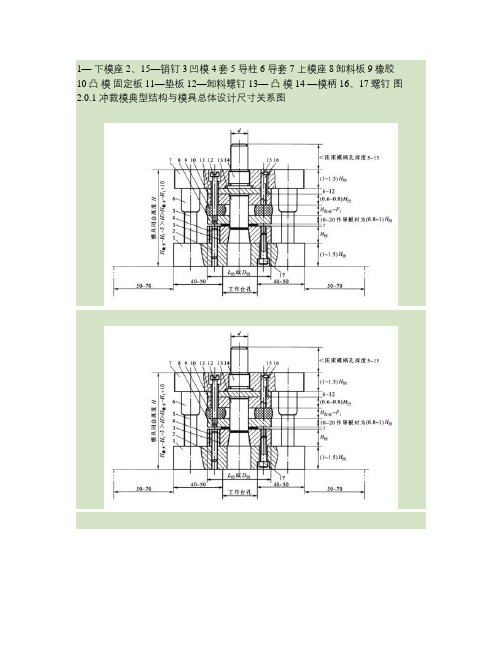
1—下模座2、15—销钉3凹模4套5 导柱 6 导套 7 上模座 8卸料板9橡胶10凸模固定板 11—垫板12—卸料螺钉13—凸模14 —模柄 16、17螺钉图2.0.1 冲裁模典型结构与模具总体设计尺寸关系图复合模的基本结构1—凸模;2—凹模;3—上模固定板;4、16—垫板;5—上模座;6—模柄;7—推杆; 8—推块; 9—推销;10—推件块;11、18—活动档料销;12—固定挡料销;13—卸料板14—凸凹模;15—下模固定板;17—下模座;19—弹簧1-下模座;2、5-销钉;3-凹模;4-凸模 1-凹模;2-凸模;3-定位钉;4-压料板;5-靠板 6-上模座;7-顶杆;8-弹簧;图3.4.2 L形件弯曲模 9、11-螺钉;10-可调定位板1.冲裁间隙过大时,断面将出现二次光亮带。
( ×)2.冲裁件的塑性差,则断面上毛面和塌角的比例大。
( ×)3.形状复杂的冲裁件,适于用凸、凹模分开加工。
( ×)4.对配作加工的凸、凹模,其零件图无需标注尺寸和公差,只说明配作间隙值。
( ×)5.整修时材料的变形过程与冲裁完全相同。
( ×)6.利用结构废料冲制冲件,也是合理排样的一种方法。
(∨)7.采用斜刃冲裁或阶梯冲裁,不仅可以降低冲裁力,而且也能减少冲裁功。
( ×)8.冲裁厚板或表面质量及精度要求不高的零件时,为了降低冲裁力,一般采用加热冲裁的方法进行。
(∨)9.冲裁力是由冲压力、卸料力、推料力及顶料力四部分组成。
( ×)10.模具的压力中心就是冲压件的重心。
( ×)11.冲裁规则形状的冲件时,模具的压力中心就是冲裁件的几何中心。
( ×)12.在压力机的一次行程中完成两道或两道以上冲孔(或落料)的冲模称为复合模。
×13.凡是有凸凹模的模具就是复合模。
( ×)14.在冲模中,直接对毛坯和板料进行冲压加工的零件称为工作零件。
冲压模具设计和制造实例

冲压模具设计和制造实例冲压模具是指在金属板材冲压加工过程中使用的一种专业加工工具。
它是将板材经过模具的加工,使其按照设定的形状和尺寸进行变形或者分割的过程。
下面将为大家介绍一个冲压模具设计和制造的实例。
该实例是针对手机外壳的冲压模具设计和制造。
手机外壳是指手机整机的外部保护壳。
它起到保护手机内部电子元器件的作用,同时也是消费者对手机外观的第一印象。
因此,制造外观精美、质量可靠的手机外壳对手机制造商来说非常重要。
在这个实例中,冲压模具设计和制造的大致步骤如下:1.确定模具结构和尺寸:根据手机外壳的设计图纸,确定模具的结构和尺寸。
模具结构可以分为上模、下模和顶出模组成。
上模和下模通过导柱进行定位,保证模具的稳定性。
通过翻转上模和下模可以实现对外壳内外表面的冲压。
顶出模是用于排出冲压件的模块。
2.模具材料选择:根据冲压工件的材料和厚度,选择适合的模具材料。
常用的模具材料有工具钢和硬质合金。
工具钢具有良好的热处理性能和可磨削性,适合制造形状复杂的模具。
硬质合金具有高硬度和抗磨损性能,适合制造耐磨性能要求高的模具。
3.绘制模具零件图纸:根据模具结构和尺寸,绘制模具零件的图纸。
主要包括上模、下模、顶出模的轮廓形状和孔位等。
根据零件图纸可以制造模具的零件。
C加工模具零件:使用数控加工设备,根据模具的零件图纸进行加工。
零件加工包括铣削、钻孔和螺纹加工等。
通过CNC加工可以保证模具的精度和质量。
5.模具装配和调试:将加工好的模具零件进行装配和调试。
根据模具装配图纸进行模具组装,同时通过调试模具使其达到冲压工艺要求。
6.冲压试产:将手机外壳材料放入模具中,进行试产。
通过试产可以检验模具的设计和制造是否合理,以及工件的质量和尺寸是否符合要求。
如果不符合要求,需要进行修改和调整。
7.产品化生产:在通过冲压试产验证无误后,可以开始进行产品化生产。
根据市场需求和订单量,确定冲压模具的加工数量,进行批量生产。
通过以上的步骤,一个手机外壳的冲压模具设计和制造就完成了。
冲压模具设计与制造实例

冲压模具设计与制造实例冲压模具是工业生产中常用的一种模具类型,它主要用于冲压加工金属材料,实现金属板材的成型、剪切、翻边等工艺。
下面我们将给出一个冲压模具设计与制造的实例,以便更好地理解冲压模具的工作原理和制造流程。
实例:汽车车门冲压模具设计与制造1.设计工作开始前,需要对车门的设计图纸进行详细的分析和理解,确定车门的形状、尺寸、材料等信息。
同时,还需要参考汽车厂商提供的标准和要求,确保设计的模具能够满足实际生产的需要。
2.根据车门的设计和要求,制定出冲压模具的设计方案。
这包括模具结构、构成零部件、动力系统、导向系统等方面的设计。
例如,我们可以采用单步冲压模具结构,由上下模具、导向柱、导向套等部件组成。
3.根据设计方案,进行具体的零部件的设计。
这包括上下模的设计、导向柱、导向套、挡块、压力座以及弹簧等部件的设计。
这些部件的设计需要考虑到材料的选择、尺寸的确定以及工艺要求等。
4.根据零部件的设计,进行各个部件的加工制造。
这包括零部件的加工、热处理、装配等工艺过程。
例如,上下模具可以采用精密数控机床进行加工,导向柱、导向套可以采用热处理进行强化处理。
5.在模具制造完成后,进行模具的调试和试产。
这包括模具的安装、调整、模具的正常运行以及质量检查等工作。
例如,我们可以采用冲压机进行模具的试产,调整模具的参数和位置,确保生产出的车门符合设计要求。
6.在模具试产成功后,批量生产汽车车门。
这包括模具投入生产、调整生产过程、质量检查等工作。
同时,还需要制定模具的保养和维护计划,确保模具能够长期稳定地运行。
冲压模具设计与制造是一个复杂的工作,需要设计师具备较高的专业知识和技能。
同时,还需要进行大量的试验和实践,通过实际的生产验证设计和制造的可行性,确保模具的质量和性能。
只有设计与制造出高质量的冲压模具,才能保证汽车车门的质量和使用寿命。
以上是一个汽车车门冲压模具设计与制造的实例,通过详细的设计和制造过程,我们可以更好地了解冲压模具的工作原理和制造流程,加深对冲压模具的理解和掌握。
冲压模具设计实例讲解
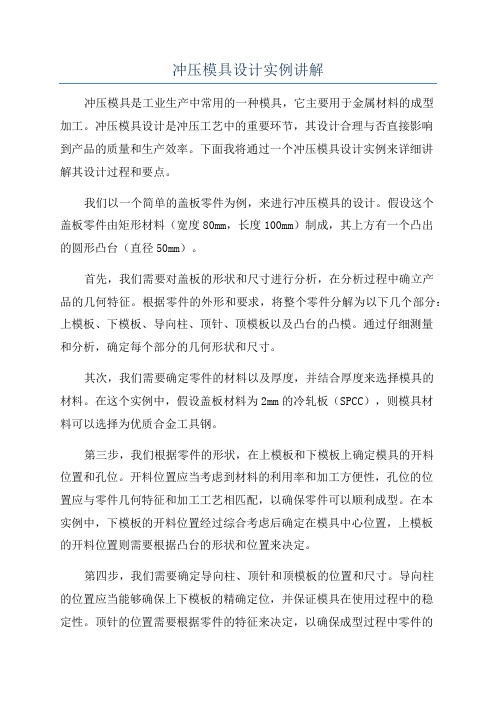
冲压模具设计实例讲解冲压模具是工业生产中常用的一种模具,它主要用于金属材料的成型加工。
冲压模具设计是冲压工艺中的重要环节,其设计合理与否直接影响到产品的质量和生产效率。
下面我将通过一个冲压模具设计实例来详细讲解其设计过程和要点。
我们以一个简单的盖板零件为例,来进行冲压模具的设计。
假设这个盖板零件由矩形材料(宽度80mm,长度100mm)制成,其上方有一个凸出的圆形凸台(直径50mm)。
首先,我们需要对盖板的形状和尺寸进行分析,在分析过程中确立产品的几何特征。
根据零件的外形和要求,将整个零件分解为以下几个部分:上模板、下模板、导向柱、顶针、顶模板以及凸台的凸模。
通过仔细测量和分析,确定每个部分的几何形状和尺寸。
其次,我们需要确定零件的材料以及厚度,并结合厚度来选择模具的材料。
在这个实例中,假设盖板材料为2mm的冷轧板(SPCC),则模具材料可以选择为优质合金工具钢。
第三步,我们根据零件的形状,在上模板和下模板上确定模具的开料位置和孔位。
开料位置应当考虑到材料的利用率和加工方便性,孔位的位置应与零件几何特征和加工工艺相匹配,以确保零件可以顺利成型。
在本实例中,下模板的开料位置经过综合考虑后确定在模具中心位置,上模板的开料位置则需要根据凸台的形状和位置来决定。
第四步,我们需要确定导向柱、顶针和顶模板的位置和尺寸。
导向柱的位置应当能够确保上下模板的精确定位,并保证模具在使用过程中的稳定性。
顶针的位置需要根据零件的特征来决定,以确保成型过程中零件的成型质量。
顶模板则需要根据零件的形状和材料选择合适的凸模形状和尺寸,以确保零件的成型质量。
最后一步,我们需要根据上述设计结果进行模具的绘图制作。
绘图要求精确、准确,需要包含所有的模具建构要素和加工尺寸等信息,以便制造部门进行模具加工和组装。
综上所述,冲压模具设计涉及到多个方面的考虑和决策,需要综合考虑零件的特征、工艺要求、材料特性等多个因素。
通过合理的设计和制作,可以保证模具的质量和使用效果,提高产品的生产效率和质量。
冲压模具设计实例

冲压模具设计实例设计实例:汽车车门内板冲压模具1.需求分析首先进行需求分析,了解客户对产品的要求。
在这个实例中,我们的客户要求生产汽车车门内板,需要模具能够冲压出符合要求的车门内板。
2.零件设计根据客户需求,设计车门内板零件。
考虑到实际生产中的材料和工艺要求,确定车门内板的形状、尺寸和厚度等。
3.工艺设计根据车门内板的形状和材料特性,确定冲压工艺。
包括冲压次数、冲压力度、冲裁布局等。
4.模具设计根据上述工艺要求,开始进行冲压模具的设计。
主要步骤如下:(1)模具结构设计:确定模具的结构形式,包括上模座、下模座、导柱、导套等部件。
(2)模具材料选择:根据模具的使用要求和生产批量确定模具材料。
汽车车门内板的生产通常使用耐磨性、强度高的工具钢。
(3)模具零件设计:根据模具结构设计的要求,设计模具的每个零件,包括上模、下模、剪切刀等。
(4)组件装配设计:将每个零件进行装配设计,确保零件可以精准地定位和配合。
(5)冲裁布局设计:根据冲裁过程的要求,确定上模、下模和冲裁刀的位置和布局,确保冲裁过程稳定和准确。
(6)模具热处理设计:由于模具在冲压过程中受到较大的应力和摩擦力,需要进行热处理,提高其硬度和耐磨性。
(7)模具安装设计:考虑到模具的使用和维护,设计合理的模具安装方式,方便更换模具和进行维护。
5.模具加工制造根据模具设计图纸,进行模具加工制造。
包括数控加工、磨削、电火花等工艺。
确保模具加工精度和质量。
6.模具调试和试产完成模具制造后,进行模具的调试和试产。
包括模具的安装和调整,冲压参数的调整等。
确保模具运行稳定和冲压产品质量合格。
通过以上步骤,完成一套汽车车门内板冲压模具的设计和制造。
在实际生产中,可以根据需求进行相应的改进和优化。
冲压模具设计是一门综合性较强的工程技术,需要综合考虑材料、工艺、机械、加工等方面的知识。
只有通过科学合理的设计,才能制造出高质量的冲压模具。
冲压模具设计实施方案和制造实例[]
![冲压模具设计实施方案和制造实例[]](https://img.taocdn.com/s3/m/d7d3b55e1eb91a37f1115cc6.png)
冲压模具设计与制造实例例:图1所示冲裁件,材料为A3,厚度为2mm,大批量生产.试制定工件冲压工艺规程、设计其模具、编制模具零件地加工工艺规程.零件名称:止动件生产批量:大批材料:A3材料厚度:t=2mm一、冲压工艺与模具设计1.冲压件工艺分析①材料:该冲裁件地材料A3钢是普通碳素钢,具有较好地可冲压性能.②零件结构:该冲裁件结构简单,并在转角有四处R2圆角,比较适合冲裁.③尺寸精度:零件图上所有未注公差地尺寸,属自由尺寸,-0.74 0-0.52-0.52-0.52-0.52可按IT14级确定工件尺寸地公差.孔边距12mm 地公差为-0.11,属11级精度.查公差表可得各尺寸公差为:零件外形:65 mm24 mm30 mm R30 mm R2 mm零件内形:10 mm孔心距:37±0.31mm 结论:适合冲裁.2.工艺方案及模具结构类型该零件包括落料、冲孔两个工序,可以采用以下三种工艺方案:①先落料,再冲孔,采用单工序模生产. ②落料-冲孔复合冲压,采用复合模生产. ③冲孔-落料连续冲压,采用级进模生产.方案①模具结构简单,但需要两道工序、两套模具才能完成零件地加工,生产效率较低,难以满足零件大批量生产地需求.由于零件结构简单,为提高生产效率,主要应采用复合冲裁或级进冲裁方式.由于孔边距尺寸12 mm 有公差要求,为了更好地保证此尺寸精度,最后确定 用复合冲裁方式进行生产.+0.36 0-0.11工件尺寸可知,凸凹模壁厚大于最小壁厚,为便于操作,所以复合模结构采用倒装复合模及弹性卸料和定位钉定位方式.3.排样设计查《冲压模具设计与制造》表2.5.2,确定搭边值:两工件间地搭边:a=2.2mm工件边缘搭边:a1=2.5mm步距为:32.2mm条料宽度B=D+2a1=65+2*2.5=70确定后排样图如2所示一个步距内地材料利用率η为:η=A/BS×100%=1550÷(70×32.2)×100%=68.8%查板材标准,宜选900mm×1000mm地钢板,每张钢板可剪裁为14张条料(70mm×1000mm),每张条料可冲378个工件,则η为:η=nA1/LB×100%=378×1550/900×1000×100%=65.1%即每张板材地材料利用率为65.1%4.冲压力与压力中心计算⑴冲压力落料力F总=1.3Ltτ=1.3×215.96×2×450=252.67(KN)其中τ按非退火A3钢板计算.冲孔力F冲=1.3Ltτ=1.3×2π×10×2×450=74.48(KN)其中:d 为冲孔直径,2πd为两个圆周长之和. 卸料力F卸=K卸F卸=0.05×252.67=12.63(KN)推件力F推=nK推F推=6×0.055×37.24=12.30(KN)其中n=6 是因有两个孔.总冲压力:F总= F落+ F冲+ F卸+ F推=252.67+74.48+12.63+12.30=352.07(KN)⑵压力中心如图3所示:由于工件X方向对称,故压力中心x0=32.5mm=13.0mm其中:L1=24mm y1=12mmL2=60mm y2=0mmL3=24mm y1=12mmL4=60mm y4=24mmL5=60mm y5=27.96mmL6=60mm y6=24mmL7=60mm y7=12mmL8=60mm y8=12mm计算时,忽略边缘4-R2圆角.由以上计算可知冲压件压力中心地坐标为(32.5,13)5.工作零件刃口尺寸计算落料部分以落料凹模为基准计算,落料凸模按间隙值配制;冲孔部分以冲孔凸模为基准计算,冲孔凹模按间隙值配制.即以落料凹模、冲孔凸模为基准,凸凹模按间隙值配制.刃口尺寸计算见表16.工作零件结构尺寸落料凹模板尺寸:凹模厚度:H=kb(≥15mm)H=0.28×65=18.2.mm凹模边壁厚:c≥(1.5~2)H=(1.5~2)×18.2=(27.3~36.4)mm 实取c=30mm凹模板边长:L=b+2c=65+2×30=125mm查标准JB/T -6743.1-94:凹模板宽B=125mm故确定凹模板外形为:125×125×18(mm).将凹模板作成薄型形式并加空心垫板后实取为:125×125×14(mm).凸凹模尺寸:凸凹模长度:L=h1+h2+h=16+10+24=50(mm)其中:h1-凸凹模固定板厚度h2-弹性卸料板厚度h-增加长度(包括凸模进入凹模深度,弹性元件安装高度等)凸凹模内外刃口间壁厚校核:根据冲裁件结构凸凹模内外刃口最小壁厚为7mm,根据强度要求查《冲压模具设计与制造》表2.9.6知,该壁厚为4.9mm即可,故该凸凹模侧壁强度足够.冲孔凸模尺寸:凸模长度:L凸= h1+h2+h3=14+12+1440mm其中:h1-凸模固定板厚h2-空心垫板厚h3-凹模板厚凸模强度校核:该凸模不属于细长杆,强度足够.7.其它模具零件结构尺寸根据倒装复合模形式特点:凹模板尺寸并查标准JB/T-6743.1-94,确定其它模具模板尺寸列于表2:根据模具零件结构尺寸,查标准GB/T2855.5-90选取后侧导柱125×25标准模架一副.8.冲床选用根据总冲压力F总=352KN,模具闭合高度,冲床工作台面尺寸等,并结合现有设备,选用J23-63开式双柱可倾冲床,并在工作台面上备制垫块.其主要工艺参数如下:公称压力:63KN滑块行程:130mm行程次数:50次/分最大闭合高度:360mm连杆调节长度:80mm工作台尺寸(前后×左右):480mm×710mm二、模具制造1、主要模具零件加工工艺过程制件:柴油机飞轮锁片材料:Q235料厚:1.2mm该制件为大批量生产,制品图如下:(一)冲裁件地工艺分析1、冲裁件为Q235号钢,是普通碳素钢,有较好地冲压性能,由设计书查得τ=350Mpa.2、该工作外形简单,规则,适合冲压加工.3、所有未标注公差尺寸,都按IT14级制造.4、结论:工艺性较好,可以冲裁.方案选择:方案一:采用单工序模.方案二:采用级进模.方案三:采用复合模.单工序模地分析单工序模又称简单模,是压力机在一次行程内只完成一个工序地冲裁模.工件属大批量生产,为提高生产效率,不宜采用单工序模,而且单工序模定位精度不是很高,所以采用级进模或复合模.级进模地分析级进模是在压力机一次行程中,在一副模具上依次在几个不同地位置同时完成多道工序地冲模.因为冲裁是依次在几个不同地位置逐步冲出地,因此要控制冲裁件地孔与外形地相对位置精度就必须严格控制送料步距,为此,级进模有两种基本结构类型:用导正销定距地级进模和用侧刃定距地级进模.另外级进模有多个工序所以比复合模效率低.复合模地分析复合模是在压力机一次工作行程中,在模具同一位置同时完成多道工序地冲模.它不存在冲压时地定位误差.特点:结构紧凑,生产率高,精度高,孔与外形地位置精度容易保证,用于生产批量大.复合模还分为倒装和正装两种,各有优缺点.倒装复合模但采用直刃壁凹模洞口凸凹模内有积存废料账力较大,正装复合模地优点是:就软就薄地冲裁件,冲出地工件比较平整,平直度高,凸凹模内不积存废料减小孔内废料地胀力,有利于凸凹模减小最小壁厚.经比较分析,该制件地模具制造选用导料销加固定挡料销定位地弹性卸料及上出件地正装复合模.(二)排样图设计及冲压力和压力中心地计算由3-6,3-8表可查得:a1=0.8,a=1.0,△=0.6查书391.料宽计算:B=(D+2a)=62+2*1.0=64mm2.步距:A=D=a1=62+0.8=62.8mm3.材料利用率计算:η=A/BS×100%=πR2-(πR2+12*4.2)/62.8*64=3.14*312-(3.14*18.52+50.4)/62.8*64×100%=47.08%(其中a是搭边值,a1是工作间隙,D是平行于送料方向冲材件地宽度,S是一个步距内制件地实际面积,A是步距,B 是料宽,R1是大圆半径,R2是小圆半径,12×4.2是方孔地面积,η为一个步距内地材料地利用率)4.冲裁总压力地确定:L=2*3.14*31+2*3.14*18.5+12+2*4.2=331.26(周边总长)计算冲裁力:F=KLtτ查设计指导书得τ=350MpaF=1.3*331.6*1.2*350≈180KN落料力:F落=1.3ltτ=1.3*(2*3.14*31)*1.2*350=106295.28N卸料力:F卸=kF落=0.02*106295.28=2125.9N冲孔力:F冲=1.3*3.14dtτ+1.3*(12+2*4.2)*1.2*350=74572.68N顶件力:F顶=-k2F落=0.06*106295.28=6377.7N冲裁总压力:F∑=F落+F卸+F冲+F顶=106295.28+2125.9+74572.68+6377.7=189.4KNF压=(1.1~1.3)F∑=246KN说明:K为安全系数,一般取1.3;k为卸料力系数,其值为0.02~0.06,在上式中取值为0.02;k2为顶件力系数,其值为0.03~0.07,式中取值为0.065.压力机地初步选用:根据制件地冲裁地公称压力,选用开式双柱可倾式压力机,公称压力为350k N 形号为J23-35 满足:F压≥F∑版权申明本文部分内容,包括文字、图片、以及设计等在网上搜集整理.版权为个人所有This article includes some parts, including text, pictures, and design. Copyright is personal ownership.eUts8。
冲压模具装配工艺样本
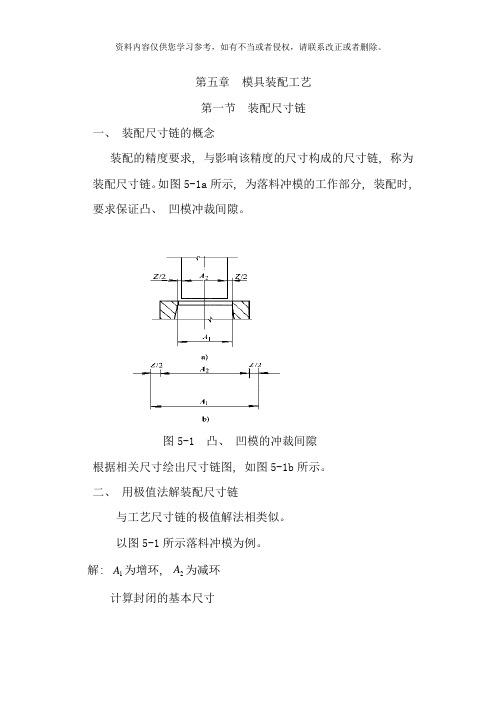
第五章 模具装配工艺第一节 装配尺寸链一、 装配尺寸链的概念装配的精度要求, 与影响该精度的尺寸构成的尺寸链, 称为装配尺寸链。
如图5-1a 所示, 为落料冲模的工作部分,装配时,要求保证凸、 凹模冲裁间隙。
图5-1 凸、 凹模的冲裁间隙根据相关尺寸绘出尺寸链图, 如图5-1b 所示。
二、 用极值法解装配尺寸链与工艺尺寸链的极值解法相类似。
以图5-1所示落料冲模为例。
解: 1A 为增环, 2A 为减环计算封闭的基本尺寸)(10.064.2974.29111mm A A Z A n m i i mi i =-=-==∑∑-+==∑ 计算封闭环的上、 下偏差)(04.0)016.0(024.0111mm A EI A ES ESA n m i i mi i =--+=-=∑∑-+==∑ 0111=-=∑∑-+==∑n m i i mi i A ES A EI EIA 求出冲裁间隙的尺寸及偏差为mm 040.0010.0+, 能满足,mm Z 10.0min =mm Z 14.0max =。
第二节 装配方法及其应用范围一、 互换装配法1.完全互换法( 1) 在装配时各配合零件不经修理、 选择和调整即可达到装配的精度要求。
∑-=-∑=+++≥11121n i i n T T T T T( 2) 特点装配简单, 对工人技术要求不高, 装配质量稳定, 易于流水作业, 生产率高, 产品维修方便; 但其零件加工困难。
试用范围广。
2.不完全互换法按∑-=∑=112n i i TT 确定装配尺寸链中各组成零件的尺寸公差,可使尺寸链政治中个组成环的公差增大, 使产品加工容易和经济, 但将有0.27%的零件不合格。
适用于成批和大量生产二、 分组装配法1.在成批和大量生产中, 将产品各配合副的零件按实测尺寸分组, 装配时按组进行呼唤装配以达到装配精度的方法。
先将零件的制造公差扩大数倍, 按经济精度进行加工, 然后将加工出来的零件按扩大前的公差大小分组进行装配。
冲压模具设计和制造实例

冲压模具设计和制造实例Document serial number【NL89WT-NY98YT-NC8CB-NNUUT-NUT108】冲压模具设计与制造实例例:图1所示冲裁件,材料为A3,厚度为2mm,大批量生产。
试制定工件冲压工艺规程、设计其模具、编制模具零件的加工工艺规程。
零件名称:止动件生产批量:大批材料:A3材料厚度:t=2mm一、冲压工艺与模具设计1.冲压件工艺分析①材料:该冲裁件的材料A3钢是普通碳素钢,具有较好的可冲压性能。
②零件结构:该冲裁件结构简单,并在转角有四处R2圆角,比较适合冲裁。
③尺寸精度:零件图上所有未注公差的尺寸,属自由尺00000寸,可按IT14级确定工件尺寸的公差。
孔边距12mm的公差为,属11级精度。
查公差表可得各尺寸公差为:零件外形:65 mm 24 mm 30 mm R30 mm R2 mm+零件内形:10 mm孔心距:37±0.31mm结论:适合冲裁。
2.工艺方案及模具结构类型该零件包括落料、冲孔两个工序,可以采用以下三种工艺方案:①先落料,再冲孔,采用单工序模生产。
②落料-冲孔复合冲压,采用复合模生产。
③冲孔-落料连续冲压,采用级进模生产。
方案①模具结构简单,但需要两道工序、两套模具才能完成零件的加工,生产效率较低,难以满足零件大批量生产的需求。
由于零件结构简单,为提高生产效率,主要应采用复合冲裁或级进冲裁方式。
由于孔边距尺寸12 mm有公差要求,为了更好地保证此尺寸精度,最后确定用复合冲裁方式进行生产。
工件尺寸可知,凸凹模壁厚大于最小壁厚,为便于操作,所以复合模结构采用倒装复合模及弹性卸料和定位钉定位方式。
3.排样设计查《冲压模具设计与制造》表2.5.2,确定搭边值:两工件间的搭边:a=2.2mm工件边缘搭边:a1=2.5mm步距为:32.2mm条料宽度B=D+2a1=65+2*=70确定后排样图如2所示一个步距内的材料利用率η为:η=A/BS×100%=1550÷(70×)×100%=%查板材标准,宜选900mm×1000mm的钢板,每张钢板可剪裁为14张条料(70mm×1000mm),每张条料可冲378个工件,则η为:η=nA1/LB×100%=378×1550/900×1000×100%=%即每张板材的材料利用率为%4.冲压力与压力中心计算⑴冲压力落料力 F总=τ=××2×450=(KN)其中τ按非退火A3钢板计算。
冲压模具实例

冲压模具实例例8.2.1冲裁模设计与制造实例工件名称:手柄工件简图:如图8.2.1所示。
生产批量:中批量材料:Q235-A钢材料厚度:1.2mm1.冲压件工艺性分析此工件只有落料和冲孔两个工序。
材料为Q235-A钢,具有良好的冲压性能,适合冲裁。
工件结构相对简单,有一个φ8mm的孔和5个φ5mm的孔;孔与孔、孔与边缘之间的距离也满足要求,最小壁厚为3.5mm(大端4个φ5mm的孔与φ8mm孔、φ5mm的孔与R16mm外圆之间的壁厚)。
工件的尺寸全部为自由公差,可看作IT14级,尺寸精度较低,普通冲裁完全能满足要求。
2.冲压工艺方案的确定该工件包括落料、冲孔两个基本工序,可有以下三种工艺方案:方案一:先落料,后冲孔。
采用单工序模生产。
方案二:落料-冲孔复合冲压。
采用复合模生产。
方案三:冲孔-落料级进冲压。
采用级进模生产。
方案一模具结构简单,但需两道工序两副模具,成本高而生产效率低,难以满足中批量生产要求。
方案二只需一副模具,工件的精度及生产效率都较高,但工件最小壁厚3.5mm接近凸凹模许用最小壁厚3.2mm,模具强度较差,制造难度大,并且冲压后成品件留在模具上,在清理模具上的物料时会影响冲压速度,操作不方便。
方案三也只需一副模具,生产效率高,操作方便,工件精度也能满足要求。
通过对上述三种方案的分析比较,该件的冲压生产采用方案三为佳。
3.主要设计计算(1)排样方式的确定及其计算图8.2.1手柄工件简图(2)冲压力的计算该模具采用级进模,拟选择弹性卸料、下出件。
冲压力的相关计算见表图8.2.2手柄排样图8.2.1。
根据计算结果,冲压设备拟选J23-25。
(3)压力中心的确定及相关计算计算压力中心时,先画出凹模型口图,如图8.2.3所示。
在图中将某oy坐标系建立在图示的对称中心线上,将冲裁轮廓线按几何图形分解成L1~L6共6组基本线段,用解析法求得该模具的压力中心C点的坐标(13.57,11.64)。
有关计算如表8.2.2所示。
- 1、下载文档前请自行甄别文档内容的完整性,平台不提供额外的编辑、内容补充、找答案等附加服务。
- 2、"仅部分预览"的文档,不可在线预览部分如存在完整性等问题,可反馈申请退款(可完整预览的文档不适用该条件!)。
- 3、如文档侵犯您的权益,请联系客服反馈,我们会尽快为您处理(人工客服工作时间:9:00-18:30)。
(2)复合冲裁模的装配过程及步骤 复合冲裁模主要工作零件的加工
01 备料(材料CrWMn,棒料,备料时要考虑锻造时的烧损) 备料(材料CrWMn,棒料,备料时要考虑锻造时的烧损) 02 锻造(锻成146 ㎜×l26 ㎜×31 ㎜的坯料) 锻造(锻成146 ㎜×l26 ㎜×31 03 热处理(退火) 04 铣(刨)削 (铣或刨削六面成141㎜×l21 ㎜×26㎜) (铣或刨削六面成141㎜×l21 ㎜×26㎜ 05 磨削(磨削上、下两端面及相邻两侧基面,用90角尺测量相邻两面 磨削(磨削上、下两端面及相邻两侧基面,用90角尺测量相邻两面 的垂直度) 06 钳工加工(用平板和划线盘按图划线,并打洋冲眼,用φ8.5的钻头 钳工加工(用平板和划线盘按图划线,并打洋冲眼,用φ8.5的钻头 钻4-M10的螺纹预孔;用φ9.7mm的钻头钻2-φ100+0.015mm圆柱销孔的 M10的螺纹预孔;用φ9.7mm的钻头钻2 φ100+0.015mm圆柱销孔的 预孔;用φ9mm的钻头钻3 φ9mm×35mm的挡料销让位孔;用φ3mm的 预孔;用φ9mm的钻头钻3-φ9mm×35mm的挡料销让位孔;用φ3mm的 钻头在R9.820 +0.08mm中心处钻穿丝孔φ3mm;正、反面孔口倒角; 钻头在R9.820 +0.08mm中心处钻穿丝孔φ3mm;正、反面孔口倒角; 攻螺纹4 M10;铰孔2 φ100+0.015mm。) 攻螺纹4-M10;铰孔2-φ100+0.015mm。) 07 铣削(平口钳装夹工件;用φ10mm的立铣刀铣削20 mm×70 mm的 铣削(平口钳装夹工件;用φ10mm的立铣刀铣削20 mm× mm的 型孔至尺寸,保证深度为13.2mm.) 型孔至尺寸,保证深度为13.2mm.) 08 热处理 (工件淬硬至HRC60~64HRC) (工件淬硬至HRC60~64HRC) 09 平磨(磨上、下两端面及相邻两侧基面,用90°角尺测量相邻两面 平磨(磨上、下两端面及相邻两侧基面,用90° 的垂直度;退磁) 10 线切割(按图编制线切割程序,切割凹模型孔形状,留单面研磨余 量0.005mm) 0.005mm) 11 钳工加工(研光线切割面) 12 检验
④下模座的补充加工
下模座上有一个处于中心位置的漏料孔 ;紧固螺钉的沉孔过孔 ; 卸料螺钉头的过孔 ;下模座上进行钻孔加工时,必须从下固 定板上引钻
⑤装配下模部分
将凸凹模组件、下垫板和下模座找正位置,在销孔中用铜棒打 入圆柱销,用紧固螺钉把它们紧固起来(卸料板暂时不装)。
⑥组装冲孔凸模组件
先把第一个圆凸模压人上固定板(若有大凸模,则要先装大 凸模;若凸模大小基本一致,则可任选一个凸模),用90° 凸模;若凸模大小基本一致,则可任选一个凸模),用90° 角尺测量相邻两基面的垂直度,使第一个凸模和固定板平面 垂直。再将第二个圆凸模压入固定板,压入第二个圆凸模后, 必须以凸凹模上的冲孔凹模型孔为基准,用透光法检查间隙。 若间隙不均匀,则要调整后面装入的凸模,使其间隙均匀。 装完凸模后,磨平凸模的上下两端面。
⑾组装上模部分 将落料凹模10套在凸凹模28上,垫好等高垫块,使 将落料凹模10套在凸凹模28上,垫好等高垫块,使 落料凹模进人凸凹模5mm左右。将推块挂板和推块 落料凹模进人凸凹模5mm左右。将推块挂板和推块 的组件装入落料凹模的型孔之中。 以导柱、导套导向,将上固定板、上垫板与上模座 组件放在落料凹模上。卸下平行夹板,使上固定板 与凹模面贴合,用紧固螺钉14把上模部分连接起来, 与凹模面贴合,用紧固螺钉14把上模部分连接起来, 螺钉不要旋紧。 用铜棒轻击落料凹模,用垫片法调整好落料凹模与 凸凹模之间的间隙,旋紧紧固螺钉14。撬动上模切 凸凹模之间的间隙,旋紧紧固螺钉14。撬动上模切 纸检查。 用撬杠撬开上模,用φ10mm的钻头通过落料凹模销 用撬杠撬开上模,用φ10mm的钻头通过落料凹模销 孔(φ100+0.015)在上模座上钻出锥窝,再用 孔(φ100+0.015)在上模座上钻出锥窝,再用 φ9.8mm的钻头在上模座上钻出预孔,然后用 φ9.8mm的钻头在上模座上钻出预孔,然后用 φ10mm的铰刀铰孔。选配圆柱销20装入。 φ10mm的铰刀铰孔。选配圆柱销20装入。
⑦上固定板的补充加工
上固定板11上有四个螺钉过孔、四个圆柱销孔以及四个推销 上固定板11上有四个螺钉过孔、四个圆柱销孔以及四个推销 过孔需配做。 装配时,以上固定板的两个凸模安装孔为基准,按上垫板中 的推板过孔形状在上固定板上划出推板的轮廓线。将上固定 板和上垫板按线找正,用平行夹板将两板夹紧。
⑧上模座的补充加工 上模座上有四个紧固螺钉过孔必须与凹模的相应孔配做。 将落料凹模套在凸凹模上,并垫好等高垫块,使凹模进人凸 凹模5mm左右。 凹模5mm左右。 将推块挂板和推块用螺钉组装后装入落料凹模型孔中。 将冲孔凸模组件装入,使冲孔凸模穿过推块进人凸凹模,以 导柱、导套导向,合上上模座(此时不装入上垫板) 导柱、导套导向,合上上模座(此时不装入上垫板)。用平行 夹板夹紧上模部分。 用φ8.5㎜的钻头通过落料凹模的四个M10的螺孔在上模座上 φ8.5㎜的钻头通过落料凹模的四个M10的螺孔在上模座上 钻出锥窝。注意做好记号后再拆开。 用φ11 mm的钻头在上模座上钻出四个M10的螺钉过孔。用 mm的钻头在上模座上钻出四个M10的螺钉过孔。用 φ16mm的钻头在上模座的顶面将φ11 mm的孔扩到 φ16mm的钻头在上模座的顶面将φ11 mm的孔扩到 φ16mm×15mm。用φ16 mm的锪孔钻钻孔深至18 mm。 φ16mm×15mm。用φ16 mm的锪孔钻钻孔深至18 mm。 将上模座正、反面孔端面倒角后备用
调整方法 整修或更换凸模 调整间隙 减小侧刃长度,加宽挡块 加长侧刃长度,减窄挡块 扩大型孔加镶件,重新加工 更换导正销 修正挡料销 整修或重装导料板 减小间隙 减小侧压 调整浮顶器 重装导料板 修整侧刃、挡块 整修卸料板 更换弹性元件 修整漏料孔 修整凹模 修整有关零件,重装 重装凸模、导柱或模柄 更换导向装置
冲压模具装配实例
1.单工序冲裁模的装配实例 1.单工序冲裁模的装配实例
(1)装配前准备工作 1)把凸模压入到固定板中,并铆接; 1)把凸模压入到固定板中,并铆接; 2)铆接之后把凸模末端的大平面磨平,保证按触面的 2)铆接之后把凸模末端的大平面磨平,保证按触面的 平面度、表面粗糙度的要求。 (2)装配凸模、固定板为一个组件 1)确定好凹模对下模座的位置; 2) 凹模与下模座配钻、铰定位销孔,完工之后打入 定位销; 3) 在凹模与下模板配钻出螺钉孔,凹模扩成螺钉过 孔,下模板攻丝,完工之后旋入螺钉并紧固; 4) 以下模座的底平面定位,平磨凹模刃口,保证刃 口面的装配要求。
(3)装配凹模与下模座
1)确定好凹模对下模座的位置; 2) 凹模与下模座配钻、铰定位销孔,完工之后打入定位销; 3) 在凹模与下模板配钻出螺钉孔,凹模扩成螺钉过孔,下模 板攻丝,完工之后旋入螺钉并紧固; 4) 以下模座的底平面定位,平磨凹模刃口,保证刃口面的装配 要求。
(4)装配上模座 1) 在凹模刃口周边放上适当厚度的金属片,控制单边的间 隙; 2) 把凸模组件的凸模刃口平放入凹模型腔中(3~4)㎜, 把凸模组件的凸模刃口平放入凹模型腔中(3~4)㎜, 用等高铁垫平面; 3) 检查凸、凹模之间的间隙情况,保证均匀即可; 4) 把上模座的导套对正下模座的导柱轻轻合上,平放在垫 板上; 5) 观察没有问题后,将整个模座压紧在工作台面上; 6) 配钻、铰上模座板与固定板的定位圆销孔,完工之后打 入定位销; 7) 配钻攻固定板上的螺孔及上模板上的沉头过孔,完工之 后旋入螺钉并紧固; 8) 以上模座板的上平面定位,平磨凸模的刃口,达到装配 要求;
⑨组装模柄组件 将上模座的顶面向下放在等高垫块上,将模柄压入上模座,压入时必须 不断检查其垂直度。装好后磨平模柄的下端面。 用φ5.9mm的钻头钻防转圆柱销预孔,用φ6mm的铰刀铰防转圆柱销孔, φ5.9mm的钻头钻防转圆柱销预孔,用φ6mm的铰刀铰防转圆柱销孔, 然后装入防转圆柱销18。 然后装入防转圆柱销18。 ⑩合装上固定板、上垫板与上模座(凹模暂不装) 上固定板11、上垫板12与上模座13之间的定位圆柱销的直径为φ10mm, 上固定板11、上垫板12与上模座13之间的定位圆柱销的直径为φ10mm, 需要配做。用垫片法调整冲孔凸模24和凸凹模28之间的间隙。 需要配做。用垫片法调整冲孔凸模24和凸凹模28之间的间隙。 将上垫板12按记号方向放置在上固定板11之上,找正各孔位置后,将推 将上垫板12按记号方向放置在上固定板11之上,找正各孔位置后,将推 板放入上垫板的型孔中。将推杆17插入模柄16的孔内后,合上上模座, 板放入上垫板的型孔中。将推杆17插入模柄16的孔内后,合上上模座, 并用平行夹板将三块板(上固定板11、上垫板12与上模座13)夹紧。撬 并用平行夹板将三块板(上固定板11、上垫板12与上模座13)夹紧。撬 动上模切纸检查。 用撬杠撬开上模。用φ9.8mm的钻头通过上固定板11上的φ10㎜ 用撬杠撬开上模。用φ9.8mm的钻头通过上固定板11上的φ10㎜的圆柱 销预孔在上模座上钻圆柱销预孔,再用φ10mm的铰刀铰孔。 销预孔在上模座上钻圆柱销预孔,再用φ10mm的铰刀铰孔。 选配并装入上固定板11和上模座13之间的圆柱销l5。 选配并装入上固定板11和上模座13之间的圆柱销l5。 试模 参看书P229 参看书P229
(5)装配卸料装置
1) 把卸料板套入凸模上并压紧,配钻,攻卸料板上的螺孔 和扩上模板上的沉头过孔; 2) 以卸料板为样板做出橡胶块上的型腔和圆孔; 3) 通过螺栓把橡胶块,卸料板联接到上模座上;
(6)装配其他零件
1) 将导料板与凹模配合加工销孔和螺纹过孔; 2) 把挡料销轻压入凹模孔中。
(7)检验,试冲
①复检模具零件 ②组装凸凹模组件 用压入法将凸凹模28压入下固定板4 用压入法将凸凹模28压入下固定板4中,在压入过 程中应随时利用90° 程中应随时利用90°角尺检查垂直度。压入后磨凸 凹模下面与下固定板齐平,再磨平凸凹模上面 ③弹压卸料板补充加工 将弹压卸料板6 将弹压卸料板6套在凸凹模组件上,垫入等高垫块, 并用平行夹板把凸凹模和弹压卸料板夹紧。用 φ9mm的钻头通过下固定板的螺钉过孔(φ9mm) φ9mm的钻头通过下固定板的螺钉过孔(φ9mm) 在弹压卸料板上钻出锥窝,做记号后分开。再用 φ5.1mm的钻头按锥窝钻出弹压卸料板M6的螺纹底 φ5.1mm的钻头按锥窝钻出弹压卸料板M6的螺纹底 孔。然后,将弹压卸料板的正反面孔口倒角后,用 M6的丝锥攻螺纹后备用。 M6的丝锥攻螺纹后备用。