瓦楞纸板问题汇总1
瓦楞纸板常见纸病的解决方案

瓦楞纸板常见纸病的解决方案一、开胶、假粘1、里纸开胶原因分析:1.1胶质量不符生产要求或腐败变质;1.2上胶量太小;1.3车速过快,瓦楞辊、压力辊热量不足;1.4压力辊压力不足;1.5瓦楞辊、压力辊的中高严重磨损。
解决方法:1.1更换合格胶液;1.2适量调大涂胶量;1.3提高瓦楞辊、压力辊温度,保证180℃以上开机,同时根据温度情况调整车速;1.4适当调整压力辊压力,以里、瓦纸粘合良好,里纸不露楞、瓦纸不碎为宜;1.5打磨或更换新压力辊、瓦楞辊。
1、面纸开胶、夹芯开胶原因分析:2.1胶量过小、烘干机速度过慢;2.2胶液稀薄,涂胶辊挂胶不足;2.3烘干机热板温度不足,胶液未充分糊化;2.4烘干机车速过快,纸板烘干不足;2.5烘干机传输带上面的压载辊没完全落下。
解决方法:2.1适当加大涂胶量,并酌情提高车速;2.2更换胶液或在原胶液中加入适量乳化剂;2.3升高烘干机热板温度至180℃以上开机;2.4减慢车速;2. 5落下压载浮辊。
原因分析:3.1瓦楞辊温度不足;3.2胶量过小,温度过高;3.3车速缓慢造成萃胶;3.4胶液黏度不够。
解决方法:3.1提高单面机工作温度;3.2调整涂胶量,关闭热源,待温度下降至180℃以下,160℃以上开机;3.3提高单面机速度;3.4适当增加胶液黏度。
2、面纸假粘原因分析:4.1烘干机热板温度不足;4.2胶液沉淀变质;4.3纸板在烘干机内停留时间过长。
解决方法:4.1待温度达到胶液能糊化时开机;4.2更换新胶;4.3尽量减少停机时间,换单换纸和断纸再续时动作要果断迅速。
二、倒楞1、单面纸板倒楞原因分析:1.1瓦楞辊磨损;1.2上下瓦楞辊间隙过大;1.3瓦楞纸定量太高且厚度太厚;1.4瓦楞纸水分过大;1.5瓦楞纸未经预热器,可塑性差。
解决方法:1.1磨削或更换瓦楞辊;1.2调整瓦楞辊间隙至0.5mm;1.3更换瓦楞纸;1.4调大预热包角,增大预热面积;1.5将瓦楞纸穿过预热器。
瓦楞纸板脱胶原因及改善措施(一)
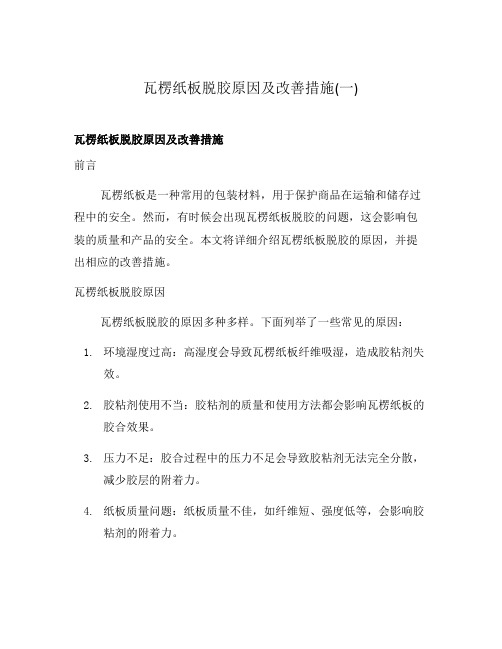
瓦楞纸板脱胶原因及改善措施(一)瓦楞纸板脱胶原因及改善措施前言瓦楞纸板是一种常用的包装材料,用于保护商品在运输和储存过程中的安全。
然而,有时候会出现瓦楞纸板脱胶的问题,这会影响包装的质量和产品的安全。
本文将详细介绍瓦楞纸板脱胶的原因,并提出相应的改善措施。
瓦楞纸板脱胶原因瓦楞纸板脱胶的原因多种多样。
下面列举了一些常见的原因:1.环境湿度过高:高湿度会导致瓦楞纸板纤维吸湿,造成胶粘剂失效。
2.胶粘剂使用不当:胶粘剂的质量和使用方法都会影响瓦楞纸板的胶合效果。
3.压力不足:胶合过程中的压力不足会导致胶粘剂无法完全分散,减少胶层的附着力。
4.纸板质量问题:纸板质量不佳,如纤维短、强度低等,会影响胶粘剂的附着力。
5.操作不当:胶粘剂施加不均匀、操作过程中的温度控制不当等,都会影响瓦楞纸板的胶合效果。
改善措施针对瓦楞纸板脱胶的原因,我们可以采取以下改善措施:1. 控制环境湿度•在生产车间中使用空调设备,保持温度和湿度在适宜范围内。
•安装湿度调节装置,及时调整湿度,确保在正常工作范围内。
2. 优化胶粘剂选择和使用方法•选用质量可靠的胶粘剂,并按照厂家建议的使用方法使用。
•加强对胶粘剂施加过程的监控和管理,确保胶粘剂的合理用量和均匀分布。
3. 提高胶合压力•针对胶粘剂的特性和纸板的厚度,调整瓦楞纸板生产设备中的压力参数,确保胶粘剂能够完全分散。
4. 选用优质纸板•选择纤维长、强度高的纸板材料,提高瓦楞纸板的质量。
•定期检查纸板供应商的资质和质量控制体系,确保所采购的纸板符合要求。
5. 加强操作培训与控制•对操作人员进行胶粘剂使用和设备操作的培训,提高其技能水平。
•建立操作规范和质量控制程序,确保每个环节都符合要求。
•定期检查和维护瓦楞纸板生产设备,确保其正常运行。
总结瓦楞纸板脱胶是一个影响包装质量的重要问题,但通过控制环境湿度,优化胶粘剂的选择和使用方法,提高胶合压力,选用优质纸板,并加强操作培训与控制,我们可以有效地解决这个问题。
瓦楞纸板不良原因分析

瓦楞纸板不良原因分析瓦楞纸板是由瓦楞纸板芯和面纸组成的一种多层结构材料。
它主要用于包装和运输行业,承载能力强,便于加工和加工。
然而,在实际生产和使用过程中,我们经常会遇到各种瓦楞纸板的不良问题,这直接影响了其使用效果和质量。
以下是对瓦楞纸板不良原因进行分析的一些常见问题。
1.压痕和划痕:瓦楞纸板在生产过程中可能会出现压痕和划痕的问题。
这可能是由于设备不当调整或操作不规范导致的。
例如,如果压痕辊的间距不正确,或者生产速度过快,纸板受到了太大的力,就会出现压痕。
而划痕则可能是由于切割工具不锋利或切割速度过快而导致的。
2.破裂和撕裂:瓦楞纸板在运输和使用过程中容易出现破裂和撕裂的问题。
这可能是由于纸板的强度不足造成的,可能是由于纸板芯的纸张质量不好,或者纸张的厚度不足。
此外,如果瓦楞纸板在存储或运输过程中受到了湿气或温度变化的影响,也会导致纸板的强度减小,容易发生破裂和撕裂。
3.潞水和水印:潞水是指瓦楞纸板表面出现水印痕迹,给纸板的外观质量带来影响。
潞水可能是由于纸张表面平整度不好,或者纸张吸水性能不佳导致的。
此外,如果生产过程中的湿度控制不当,或者纸板表面存在杂质或污染物,也会导致潞水问题的出现。
4.尺寸不一致:瓦楞纸板的尺寸一致性是其质量的重要指标之一、如果纸板的尺寸不一致,可能会导致包装箱的组合困难,影响使用效果。
尺寸不一致的原因可能是由于生产过程中的设备调整不准确或操作不规范,或者纸板芯的厚度不一致,造成纸板的尺寸差异。
5.外观缺陷:瓦楞纸板的外观缺陷可能是指纸板芯表面的起泡、蜂窝状,或者面纸的褶皱、异常颜色等问题。
这些缺陷可能是由于纸张质量不佳、生产过程中的设备故障或不良操作导致的。
例如,如果纸张含水量不均匀,或者设备温度过高,就会导致瓦楞纸板表面起泡或蜂窝状。
综上所述,瓦楞纸板的不良问题可能是由于生产过程中的设备故障、操作不良、纸张质量不佳等因素导致的。
为了解决这些问题,生产厂家应该加强对设备的维护和调整,确保操作人员的培训和规范。
瓦楞纸板不良原因分析

瓦楞纸板不良原因分析瓦楞纸板是一种由多层纸板互相粘合而成的材料,具有良好的抗压性能和缓冲性能,广泛应用于各个行业的包装中。
然而,在生产和使用过程中,瓦楞纸板可能会出现一些不良现象,影响其使用效果和寿命。
下面将分析一些可能导致瓦楞纸板不良的原因。
1.原材料质量不良:瓦楞纸板的质量主要受原材料的影响,如果原材料质量不好,会直接影响到瓦楞纸板的质量。
比如,纸张的纤维长度不足、杂质过多、含湿率过高等都会导致瓦楞纸板的强度下降和易碎性增加。
2.生产过程不规范:瓦楞纸板的生产过程包括纸张的加工、糊合、干燥等环节,如果操作不规范或控制不当,会导致质量不良。
比如,糊合时糊胶的浓度不合适、温度控制不好、糊胶的均匀性不好等都会影响瓦楞纸板的强度和质量稳定性。
3.设备老化或损坏:生产瓦楞纸板需要使用一系列的设备,如纸张预处理机、糊合机、干燥机等。
如果这些设备老化或损坏,就会影响生产过程的正常进行,进而导致瓦楞纸板的质量下降。
4.储存条件不好:瓦楞纸板在生产出来后需要进行储存,如果储存条件不好,比如温度过高或者潮湿,会导致纸张变形、发霉,进而影响瓦楞纸板的强度和质量。
5.运输和包装不当:瓦楞纸板在运输和包装过程中也容易遭受挤压、湿泡等不良影响,特别是在长途运输或者储存时间较长的情况下,容易出现不均匀应力分布,导致瓦楞纸板强度下降或出现划痕、弯曲等问题。
6.设计不合理:瓦楞纸板在使用过程中有时受到外力的作用,特别是在堆叠、挤压等情况下,如果设计不合理,纸板可能容易变形、产生断裂、划痕等不良现象。
综上所述,瓦楞纸板不良的原因多种多样,涉及到原材料、生产过程、设备、储存和运输等多个方面。
为了提高瓦楞纸板的质量,减少不良现象的发生,需要从原材料的选择和质量控制、生产过程的改善和规范、设备的维护和更新、储存和运输条件的优化以及设计的合理性等方面进行改进和管理。
只有全面有效地把控这些方面,才能保证瓦楞纸板的质量和可靠性,满足各个行业对包装的需求。
瓦楞纸板的常见问题
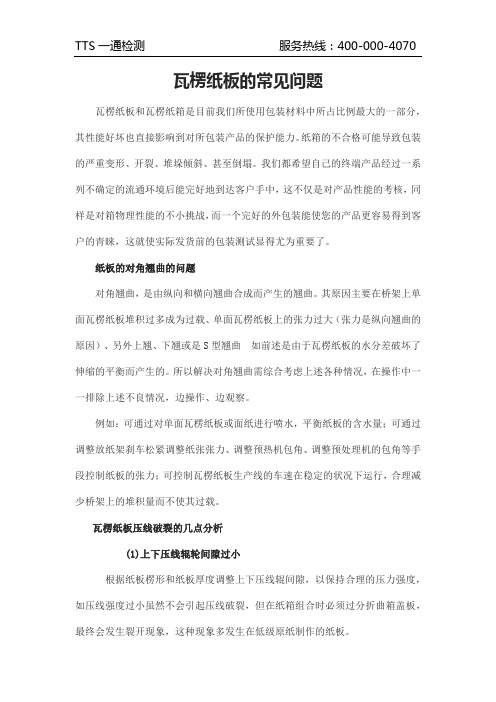
瓦楞纸板的常见问题瓦楞纸板和瓦楞纸箱是目前我们所使用包装材料中所占比例最大的一部分,其性能好坏也直接影响到对所包装产品的保护能力。
纸箱的不合格可能导致包装的严重变形、开裂、堆垛倾斜、甚至倒塌。
我们都希望自己的终端产品经过一系列不确定的流通环境后能完好地到达客户手中,这不仅是对产品性能的考核,同样是对箱物理性能的不小挑战,而一个完好的外包装能使您的产品更容易得到客户的青睐,这就使实际发货前的包装测试显得尤为重要了。
纸板的对角翘曲的问题对角翘曲,是由纵向和横向翘曲合成而产生的翘曲。
其原因主要在桥架上单面瓦楞纸板堆积过多成为过载、单面瓦楞纸板上的张力过大(张力是纵向翘曲的原因)、另外上翘、下翘或是S型翘曲 如前述是由于瓦楞纸板的水分差破坏了伸缩的平衡而产生的。
所以解决对角翘曲需综合考虑上述各种情况,在操作中一一排除上述不良情况,边操作、边观察。
例如:可通过对单面瓦楞纸板或面纸进行喷水,平衡纸板的含水量;可通过调整放纸架刹车松紧调整纸张张力、调整预热机包角、调整预处理机的包角等手段控制纸板的张力;可控制瓦楞纸板生产线的车速在稳定的状况下运行,合理减少桥架上的堆积量而不使其过载。
瓦楞纸板压线破裂的几点分析(1)上下压线辊轮间隙过小根据纸板楞形和纸板厚度调整上下压线辊间隙,以保持合理的压力强度,如压线强度过小虽然不会引起压线破裂,但在纸箱组合时必须过分折曲箱盖板,最终会发生裂开现象,这种现象多发生在低级原纸制作的纸板。
(2)压线轮的组合位置不对中为了准确安装压线轮,通常在加工压线轮时都有1mm的对中开槽缝,配合不好不但会发生压线破裂和箱体组合时棱角不好,还会发生摇盖虚缝或搭叠现象,造成纸板箱的缺陷。
当然,各种机器压线轮本身的加工缺陷也会引起压线破裂。
(3)二次滚压压力问题上下压线轮滚压的横向压痕线棱角总不如碰线压痕机压痕的结果,但二者生产力和经济性是难以相提并论的。
所以要使纸板生产线纵向压痕分纸机器的上下压线轮压痕达到或接近磁线压痕的棱角,需在纸板压痕机前后的两根压线轴上分别安装上下压线轮,纸板经过的第一次滚线为预滚压痕线,改变压痕处瓦楞纸板结构,再经第二次滚压压痕线,第一次预压力略低于第二次滚压压力,这样就能达到良好的棱角。
瓦楞纸板各种常见纸病的解决方案
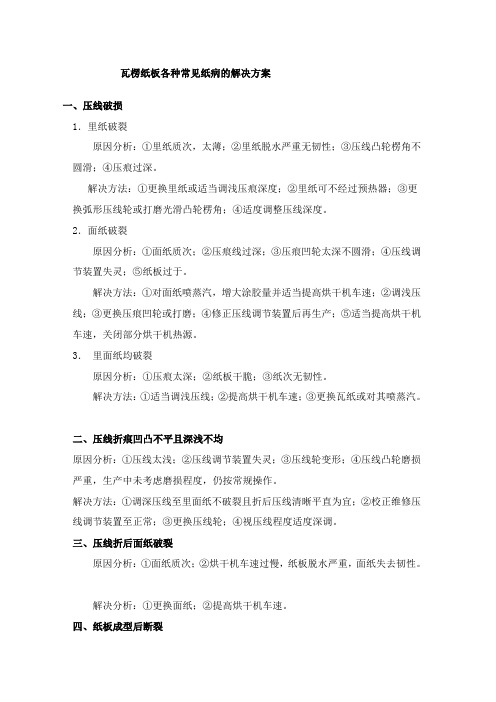
瓦楞纸板各种常见纸病的解决方案一、压线破损1.里纸破裂原因分析:①里纸质次,太薄;②里纸脱水严重无韧性;③压线凸轮楞角不圆滑;④压痕过深。
解决方法:①更换里纸或适当调浅压痕深度;②里纸可不经过预热器;③更换弧形压线轮或打磨光滑凸轮楞角;④适度调整压线深度。
2.面纸破裂原因分析:①面纸质次;②压痕线过深;③压痕凹轮太深不圆滑;④压线调节装置失灵;⑤纸板过于。
解决方法:①对面纸喷蒸汽,增大涂胶量并适当提高烘干机车速;②调浅压线;③更换压痕凹轮或打磨;④修正压线调节装置后再生产;⑤适当提高烘干机车速,关闭部分烘干机热源。
3.里面纸均破裂原因分析:①压痕太深;②纸板干脆;③纸次无韧性。
解决方法:①适当调浅压线;②提高烘干机车速;③更换瓦纸或对其喷蒸汽。
二、压线折痕凹凸不平且深浅不均原因分析:①压线太浅;②压线调节装置失灵;③压线轮变形;④压线凸轮磨损严重,生产中未考虑磨损程度,仍按常规操作。
解决方法:①调深压线至里面纸不破裂且折后压线清晰平直为宜;②校正维修压线调节装置至正常;③更换压线轮;④视压线程度适度深调。
三、压线折后面纸破裂原因分析:①面纸质次;②烘干机车速过慢,纸板脱水严重,面纸失去韧性。
解决分析:①更换面纸;②提高烘干机车速。
四、纸板成型后断裂原因分析:①瓦纸质次;②纸板过分干燥;③成型工序设备调节不当;④压线太浅,瓦楞未压扁或成型后折叠摇盖时高强瓦楞将面纸撑破,瓦楞随之断裂。
解决方法:①更换瓦纸;②保证纸板含水量在10±3左右;③注意成形各工序的设备调节并调至最佳状态;④烘干机加速并加大涂胶量,压线调深。
五、纵切毛边原因分析:①分纸刀已钝或刀刃有缺口;②上下刀咬合过深;③上下刀之间有间隙。
解决方法:①打磨或更换新刀;②调节上下刀重合至最佳状态;③将上下两刀靠紧,用手转动刀轮,灵活不伤刀为宜。
六、横切纸板拖尾原因分析:①横刀已钝;②横切刀上下两片咬合不正,纸板切不断的部位在机械力作用下带起撕裂的面瓦纸;③横切机瞬时加速调节不当,引起阻纸。
瓦楞纸板常见质量问题和产生原因及解决办法

修正瓦楞辊的贴合间隙 清理瓦楞表面异物
瓦楞辊贴合间隙大
• 修正瓦楞辊的贴合间隙
瓦画辊贴合间隙不平衡 •
导纸板位置不正、磨损或带
脏
瓦楞原纸含水水均衡
•
瓦楞原纸的张力太小
•
检查并修正或更换导纸 板
加大予热包角 适当调整张力控制
瓦楞纸板常见质量问题和产生原因及 解决办法
质量问题
平行度
• 瓦楞辊表面带脏
• 清理瓦楞辊,保持干净
• 导纸板位置不正,、带脏或磨损 • 检查、修正、清理或更换导
纸板
• 涂胶辊、浮动辊间隙不当
• 调整二者的贴合间隙
• 粘合剂质量不好
• 检查并重新制作粘合剂
• 瓦楞原纸含水不均衡张力小 • 适当予热并加大张力控制
• 过纸天桥张力不均衡
瓦楞纸板常见质量问题和产生原因及 解决办法
1. 面纸予热包角太大 2. 里纸予热包角太小 3. 过纸天桥堆积过多 4. 单面机涂胶量过大
5.涂胶仙涂胶量偏少
6.车速太低
7.双面机热板温度高
8.重量辊施加压力过大
解决办法
• 减少包角、降低予热 • 增大包角、加强予热 • 减少过纸天桥的堆积 • 适当控制单面机的着胶
量 • 适当增大涂胶机的着胶
7.双面机热板温度高 8.重量辊施加压力过大
解决办法
• 减少包角、降低予热
• 增大包角、加强予热 • 减少过纸天桥的堆积 • 适当控制单面机的着胶
量 • 适当增大涂胶机的着胶
量 • 根据实际运行质量,适
当提高车速
• 提高车速或人为降低热 板
• 适当投放重量辊
PPT文档演模板
瓦楞纸板常见质量问题和产生原因及 解决办法
常见的瓦楞纸板缺陷及其解决方法
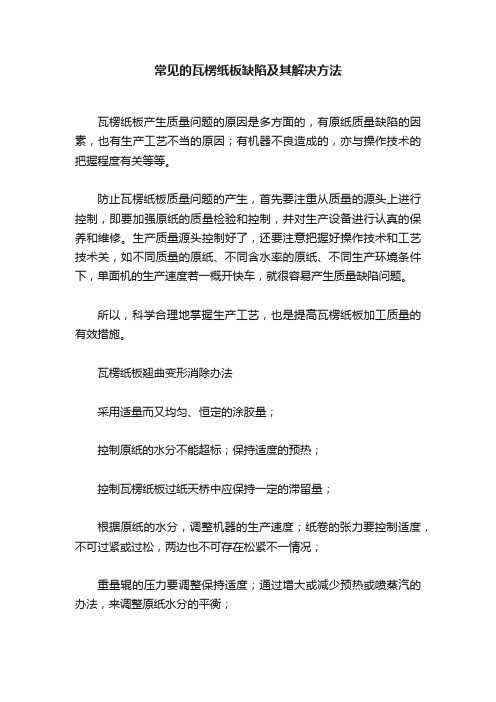
常见的瓦楞纸板缺陷及其解决方法瓦楞纸板产生质量问题的原因是多方面的,有原纸质量缺陷的因素,也有生产工艺不当的原因;有机器不良造成的,亦与操作技术的把握程度有关等等。
防止瓦楞纸板质量问题的产生,首先要注重从质量的源头上进行控制,即要加强原纸的质量检验和控制,并对生产设备进行认真的保养和维修。
生产质量源头控制好了,还要注意把握好操作技术和工艺技术关,如不同质量的原纸、不同含水率的原纸、不同生产环境条件下,单面机的生产速度若一概开快车,就很容易产生质量缺陷问题。
所以,科学合理地掌握生产工艺,也是提高瓦楞纸板加工质量的有效措施。
瓦楞纸板翘曲变形消除办法采用适量而又均匀、恒定的涂胶量;控制原纸的水分不能超标;保持适度的预热;控制瓦楞纸板过纸天桥中应保持一定的滞留量;根据原纸的水分,调整机器的生产速度;纸卷的张力要控制适度,不可过紧或过松,两边也不可存在松紧不一情况;重量辊的压力要调整保持适度;通过增大或减少预热或喷蒸汽的办法,来调整原纸水分的平衡;控制单面机或双面机生产环境保持稳定的温湿度;瓦楞辊、压力辊、活动辊和预热辊要调整保持平衡状态;对使用磨损厉害的瓦楞辊应更换新辊;切忌将含水率高低悬殊过大的瓦楞纸、面纸或里纸(箱板纸)进行配套成型加工。
瓦楞纸板出现搓衣板状变形的原因瓦楞纸板由于受到温度、黏合剂和机器张力和原纸质量等方面的作用,就容易出现搓衣板状变形。
产生原因:1、原纸的纤维组织的伸缩率差异较大;2、面纸或里纸的定量偏低和原纸的纤维组织过于柔软的话,成型后其挺度相应也就差;3、黏合剂涂布量过多或不均匀时,使瓦楞楞顶两侧边缘也有胶液,当其与面纸或里纸黏结干燥后,由于收缩作用导致对面纸或里纸构成一定扭力;4、黏合剂的黏度偏低,与里纸或面纸的纤维组织没有很好地黏结成坚固的整体;5、单面机或双面机的瓦楞辊、压力辊间隙不适、不平衡;6、瓦楞辊楞齿顶磨损严重时,由于楞齿顶面积增大而加大胶的涂布量,使面纸或里纸黏结后容易变形;7、瓦楞辊、压力辊或预热辊的温度过高或过低等情况存在时,都容易使瓦楞纸板成型后出现搓衣板状变形现象。
瓦楞纸板线的质量问题及解决

1.粘合不好
产生原因
1.面纸张力过大 2.面纸、芯纸水份大 3.瓦楞辊与涂胶辊不平行 4.粘合剂附着量小 5.粘合剂质量不好 6.导纸板位置不正或有脏物 7.涂胶辊和浮动辊不平行 8.帆布带升降机构工作不正常 9.热量不够,淀粉未凝合 10.热量过大,淀粉过早凝合 11.双面机重量辊放置不当 12.粘合剂形成团块,上胶不匀
解决办法
调整刹车装置,减小磨擦力 •加大予热力度或换纸 •调整二者之间的合理间隙 •加大粘合剂附着量 •修正粘合剂的质量 •修正导纸板位置,清理脏物 •调整二者之间的合理间隙 •检查油压装置和机械调整系统 •检查并排除热量不足的因素 •适当减少予热 •调整和重置重量辊 •解决粘合剂的质量
2、横向向下翘曲
解决办法
1.涂胶辊和浮动辊不平行
•检查和修正二者的调整装置
2.双面机重量辊位置不当或压力大 •适当控制重量辊的投放并检查平衡度
3.过纸天桥张力太大
•减低控制器的张力
4.瓦楞原纸含水过高
•加大予热器包角和双面机热量
5.瓦楞辊不平行
•调整和修正瓦楞辊的平行度
6.瓦楞辊贴合间隙太小
•修正瓦楞辊的贴合间隙
13、楞不均
•检查并修正帆布带的张力 •适当增大输出张力控制 •喷水并适当予热 •减小对面纸的张力控制
6、S形翘曲
产生原因
解决办法
1原纸水分分布不均衡 2瓦楞辊使用不同幅面的纸, 表面磨损不均匀
3环境湿度太大 4涂胶辊和浮动辊不平行
1喷淋或予控制 2简易修复或更换瓦楞辊 3增大予热器包角、降低车速、 提高粘合剂质量
产生原因
解决办法
1.瓦楞辊表面有脏物 2.瓦楞辊贴合间隙大 3.瓦楞辊贴合间隙不平衡 4.导纸板位置不正、磨损或带脏 5.瓦楞原纸含水水均衡 6.瓦楞原纸的张力太小
瓦楞纸板生产过程中常见问题浅析
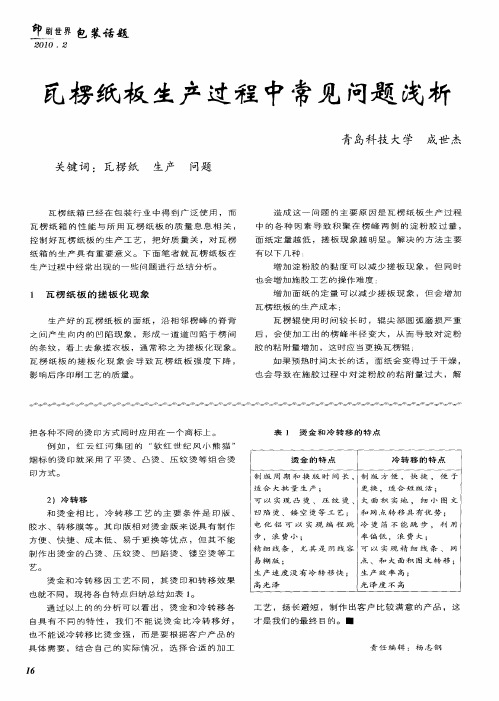
增 加 面 纸 的定 量 可 以 减 少 搓 板 现 象 ,但 会 增 加 瓦楞 纸板 的生产成 本 ; 瓦 楞 辊 使 用 时 间 较 长 时 , 辊 尖 部 圆 弧 磨 损 严 重 后 ,会 使 加 工 出 的 楞 峰 半 径 变 大 , 从 而 导 致 对 淀 粉 胶 的粘 附 量 增 加 , 这 时 应 当 更 换 瓦 楞 辊 ; 如 果 预 热 时 间 太 长 的话 ,面 纸 会 变 得 过 于 干 燥 ,
艺。
凹 陷 烫 、镂 空 烫 等 工 艺 ; 和 网点 转 移 具 有优 势 :
电 化 铝 可 以 实 现 编 程 跳 冷 烫 箔 不 能 跳 步 。 利 用
步 .浪 费 小 ;
易糊 版 :
率 偏 低 ,浪 费 大 ;
点 、和 大 面 积 图 文 转 移 ;
精 细 线 条 . 尤 其 是 阴 线 容 可 以 实 现 精 细 线 条 、 网
楞 深 度 、 芯 纸 厚 度 、 面 纸 厚 度 与 里 纸 厚 度 之 和 。 但
在 瓦 楞 纸 板 的 加 工 过 程 中 ,经 常 出 现 实 际 瓦 楞 纸 板
厚 度 低 于 设 计 厚 度 的 情 况 , 造 成 这 一 问 题 的 低 或 太 高 ,甚 至 出 现 集 聚 凝 结 ,
增 加 淀 粉 胶 的 黏 度 可 以 减 少 搓 板 现 象 ,但 同 时
也 会增加施胶 工 艺的操作难 度 :
1 瓦 楞 纸 板 的 搓 板 化 现 象
瓦楞纸箱常见问题原因及解决方法
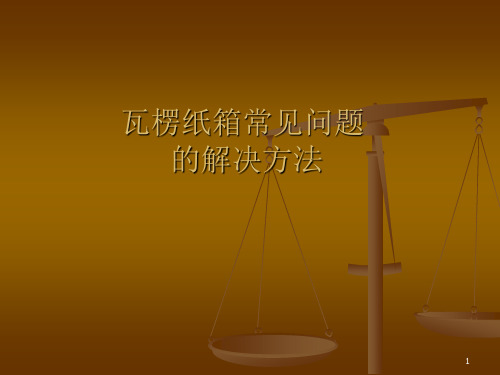
2.
水墨、纸板、印刷机结构方面的改 变 , 印版、使用速度及环境、供应 商、操作员习惯或机器设定的改变
原因 只是整个的图像周围有重影 1. 印版的压力过大 2. 网纹辊与印版压力过大 只最前边缘/ 最后边缘有重影 1. 网纹辊印版压力过大 2. 印版包衬变形 3. 印版或版筒衬垫松弛
解决 只是整个的图像周围有重影 1. 减小印版与纸板压力 2. 调整减少网纹辊压力,检查印版 水平和衬垫 只最前边缘/ 最后边缘有重影 1. 调整减少网纹辊压力,检查印版 水平和衬垫 2. 使用薄的衬版材料 3. 重装印版使其贴紧版筒
解决 4.调整水墨pH值至规定值或用 新鲜的水墨替换 5.改变表面张力、减少水墨膜 层厚度或提高干燥能力 6.联系水墨供应商,听取水墨供 应商建议
4
5.表面张力过高不利于干燥
6.第二色墨与第一色墨不相容
因素 1.由於水墨不干或水墨膜层太厚
解决
2.
底层水墨膜层不均匀 (重影, 颜色 不均匀)
3. 过高的表面张力致水墨不易干燥
解决 1. a)压紧衬垫与印版 b) 增加水墨粘度 c) 增加水墨膜层厚度 d) 使用比较软的衬垫 2.调整印刷压力 3.换上备用品并同供应商联系处理 4.加新鲜的水墨提高水墨粘度 5.加新鲜的水墨或将脱水剂加入水 墨 6.清洁或更换网纹辊l
11
因素 7. 印刷机内的水墨被污染 8.水墨 pH太低
瓦楞纸箱常见问题 的解决方法
1
瓦楞纸箱常见问题的解决
一些实用的建议 全部是常见的问题 不用很快就下结论 每次只改变 1 个条件 当面对一个问题的时候 ,记得有我在帮你 如果我们能帮到你,请打电话给我们 祝您好运 !
瓦楞纸板生产线故障与对策

瓦楞纸板生产线故障与对策在制造瓦楞纸板时会产生很多故障,其中有原材料问题,粘合剂问题,机械本身问题,操作技术问题及熟练程度的问题,在当今市场需求尤其在生产过程控制特别要求尽量尽快减少。
由上述故障引出的质量问题造成的报废数量和频率是重中之重。
经公司研究决定,由技术部编写本对策以解决生产急需达到降低控制成本之目的。
一、瓦楞纸断裂这是鉴别瓦楞纸适应性的重要指标。
其形原因:1、单面机预热张力2、瓦楞纸刹车器3、在进入上下瓦楞辊时受到的弯曲与剪切力产生原因解决办法①瓦楞原纸质量不好①更换瓦楞原纸②瓦楞辊磨损②进行简易修复或更换瓦楞辊③瓦楞辊间隙太小③修正和调整瓦楞辊的贴合间隙④运行中机械性损坏④检查并修复机械性不当造成的损伤⑤刹车过紧⑤降低气刹压力减少刹车紧力⑥预热包角过大⑥减少预热包角二、瓦楞折皱产生原因解决办法①瓦楞原纸在抄造或抄宽方向上有湿斑或料斑①增大预热器包角②瓦楞原纸的制动力不强②加大制动力平衡张力③瓦楞辊的平行度不好③修正或调整瓦楞辊的平行度④瓦楞原纸含水平不均衡④适当预热或喷蒸气使其保持平衡的含水三、瓦楞的变形表现为:没有达到规定的瓦楞高度,瓦楞变形,瓦楞形不整齐的现象。
这样的瓦楞成形的纸板本身比较软,平面强度低,刚性也低,做成的纸箱抗压强度也低,戳穿强度也小。
此种原因在流水线上有发生,在制箱过程中也有发生。
产生原因解决办法①使用了低强度的瓦楞原纸本身抗压强度不够①更换高强度瓦楞纸②瓦楞原纸水分过低或过高易变形②加大预热包角或喷雾均衡水分③上、下瓦辊间压力不足时瓦楞成型不好③调整合适压力④瓦楞辊磨损,降低了瓦楞高度④更换瓦辊和压力辊可解决⑤双面机上涂胶辊和压载辊的间隙调节不当⑤调节合适间隙达到正常合适⑥加热部和冷却部的加重辊压力不适当导致压溃⑥调整加大压辊间隙高度⑦瓦楞纸板水分高或热板温度不够不能使其定型⑦加大蒸气压力使温度升高到合适温度,或检查导致温度不好的原因以解决⑧横切机压辊调节太重,导致压溃瓦楞⑧调节重辊铊的间隙距离可解决四、瓦楞的倾斜表现为:瓦楞向纸板运动方向倾斜,但还没倒塌。
瓦楞纸板常见故障原因分析与排除
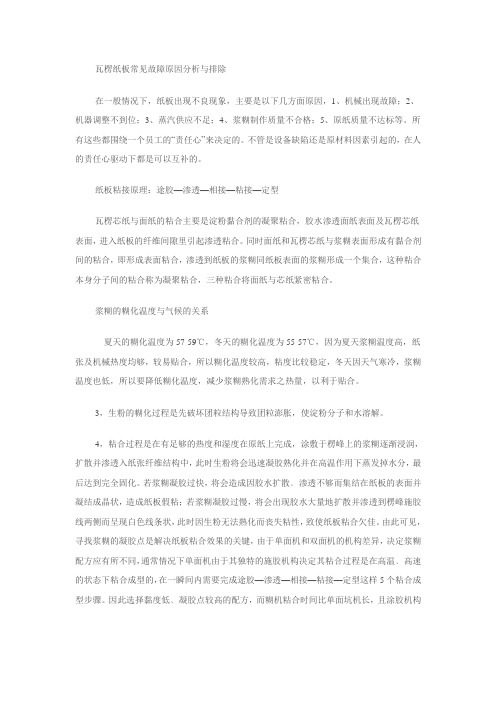
瓦楞纸板常见故障原因分析与排除在一般情况下,纸板出现不良现象,主要是以下几方面原因,1、机械出现故障;2、机器调整不到位;3、蒸汽供应不足;4、浆糊制作质量不合格;5、原纸质量不达标等。
所有这些都围绕一个员工的“责任心”来决定的。
不管是设备缺陷还是原材料因素引起的,在人的责任心驱动下都是可以互补的。
纸板粘接原理:途胶—渗透—相接—粘接—定型瓦楞芯纸与面纸的粘合主要是淀粉黏合剂的凝聚粘合,胶水渗透面纸表面及瓦楞芯纸表面,进入纸板的纤维间隙里引起渗透粘合。
同时面纸和瓦楞芯纸与浆糊表面形成有黏合剂间的粘合,即形成表面粘合,渗透到纸板的浆糊同纸板表面的浆糊形成一个集合,这种粘合本身分子间的粘合称为凝聚粘合,三种粘合将面纸与芯纸紧密粘合。
浆糊的糊化温度与气候的关系夏天的糊化温度为57-59℃,冬天的糊化温度为55-57℃,因为夏天浆糊温度高,纸张及机械热度均够,较易贴合,所以糊化温度较高,粘度比较稳定,冬天因天气寒冷,浆糊温度也低,所以要降低糊化温度,减少浆糊熟化需求之热量,以利于贴合。
3,生粉的糊化过程是先破坏团粒结构导致团粒澎胀,使淀粉分子和水溶解。
4,粘合过程是在有足够的热度和湿度在原纸上完成,涂敷于楞峰上的浆糊逐渐浸润,扩散并渗透入纸张纤维结构中,此时生粉将会迅速凝胶熟化并在高温作用下蒸发掉水分,最后达到完全固化。
若浆糊凝胶过快,将会造成因胶水扩散﹑渗透不够而集结在纸板的表面并凝结成晶状,造成纸板假粘;若浆糊凝胶过慢,将会出现胶水大量地扩散并渗透到楞峰施胶线两侧而呈现白色线条状,此时因生粉无法熟化而丧失粘性,致使纸板粘合欠佳。
由此可见,寻找浆糊的凝胶点是解决纸板粘合效果的关键,由于单面机和双面机的机构差异,决定浆糊配方应有所不同,通常情况下单面机由于其独特的施胶机构决定其粘合过程是在高温﹑高速的状态下粘合成型的,在一瞬间内需要完成途胶—渗透—相接—粘接—定型这样5个粘合成型步骤。
因此选择黏度低﹑凝胶点较高的配方,而糊机粘合时间比单面坑机长,且涂胶机构为冷态施胶,它的粘合过程是在常温下完成粘合成型,这就要求选择黏度高﹑凝胶点较低的配方,以满足纸板粘合成型的需要。
瓦楞纸板产生的故障及解决(一)

瓦楞纸板制造过程可能故障及解决(一)平行切刀,耐折试验机,纸张表面吸收重量测定仪的检测设备大量使用在纸品包装行业,为预防瓦楞纸板制造故障的发生提供了帮助,同时保证了瓦楞纸板的产品品质。
平行切刀是瓦楞纸板边压(竖压/粘合)强度试验必须的专用器具,适用于纸版生产行业,包装行业商检,科研院对纸、纸张进行环压强度的物理性能测试样的必备工具.耐折测试仪适合纸张、金属薄片的耐弯折试验,适合造纸、包装材料及薄金属板等行业使用。
试法系将试片两端固定于本机上、下夹具,上夹具施于所须之荷重,使试片承受一定之张力。
下夹具则在试片垂直状态下,向左右两边往复弯折,直到折断试片,记录弯折次数.纸张吸性测试仪是纸和纸板表面吸水性试验的常规仪器,亦称为纸张表面吸收重量测定仪。
这种仪器采用吸收性试验多种方法中的可勃(Cobb)试验法,因此也称为可勃吸收性测定仪。
该产品主要用于测定施胶纸和纸板包括瓦楞纸板的表面吸水性。
本仪器只是测定纸与纸板表面吸水性,但不适用于准确评价纸或纸板的书写性能。
在制造瓦楞纸板时会产生很多故障,其中有原材料问题,粘合剂问题,机械本身问题,操作技术问题及熟练程度的问题,在当今市场需求尤其在生产过程控制特别要求尽量尽快减少。
由上述故障引出的质量问题造成的报废数量和频率是重中之重。
我们就制造瓦楞纸板产生的故障及解决方法做一些研究探讨。
一、瓦楞纸断裂这是鉴别瓦楞纸适应性的重要指标。
其形原因:1、单面机预热张力2、瓦楞纸刹车器3、在进入上下瓦楞辊时受到的弯曲与剪切力产生原因解决办法①瓦楞原纸质量不好①更换瓦楞原纸②瓦楞辊磨损②进行简易修复或更换瓦楞辊③瓦楞辊间隙太小③修正和调整瓦楞辊的贴合间隙④运行中机械性损坏④检查并修复机械性不当造成的损伤⑤刹车过紧⑤降低气刹压力减少刹车紧力⑥预热包角过大⑥减少预热包角二、瓦楞折皱产生原因解决办法①瓦楞原纸在抄造或抄宽方向上有湿斑或料斑①增大预热器包角②瓦楞原纸的制动力不强②加大制动力平衡张力③瓦楞辊的平行度不好③修正或调整瓦楞辊的平行度④瓦楞原纸含水平不均衡④适当预热或喷蒸气使其保持平衡的含水三、瓦楞的变形表现为:没有达到规定的瓦楞高度,瓦楞变形,瓦楞形不整齐的现象。
瓦楞纸板印刷机械常见故障原因及解决方法

瓦楞纸板印刷机械常见故障原因及解决方法故障现象1:印刷走位
印刷走位故障原因:
1、压印辊未压紧或位置不合适。
2、压印辊与印刷滚筒不平行。
3、印版未挂紧,有松动。
4、印版长时间使用,有磨损。
5、纸板宽度太小。
印刷走位解决方法:
1、调整压印辊压力和位置。
2、调整压印辊与印刷滚筒的平行度。
3、拧紧挂版两端的棘轮,使印版张紧。
4、更换新印版。
5、选用合适的纸板宽度。
故障现象2:流水纹
瓦楞纸板印刷机流水纹故障原因:
1、机器速度太慢。
2、水墨浓度偏低。
解决方法:
1、加快机器速度。
2、加高水墨浓度。
故障现象3:印刷漏白
瓦楞纸板印刷机印刷漏白故障原因:
1、网纹辊与印版接触不良。
2、压印辊与印刷滚筒间隙不合适。
3、印版衬垫损坏。
4、水墨快干。
解决方法:
1、调整网纹辊与印辊间隙。
2、调整底压辊与印辊间隙。
3、更换新衬垫。
4、给水墨加慢干剂,或更换水墨。
故障现象4:印刷起毛边
故障原因:
1、网纹辊与印辊间隙太小。
2、各印刷单元所用的印版材质不同。
3、水墨粘度过高。
4、压印辊与印辊间隙过小。
解决方法:
1、重新调整网纹辊与印辊间隙。
2、选用同一材质的印版。
3、适当降低水墨粘度。
4、重新调整底压辊与印辊间隙。
瓦楞纸板质量不良现象及原因

瓦楞纸板质量不良现象及原因露楞:指在纸面上能明显看到坑纹的楞高。
一般厂家生产的纸板的底纸均有露楞现象,此属正常,但露坑不能超过3mm且面纸不得露楞。
缺材:指纸板的宽度不够。
引起缺材的原因可能是原纸不足度、原纸经加热后缩水、错边(也叫纸边不齐)。
引起这些原因可能是驳纸未对齐、纸架走位、原纸简端面不平整。
此外,还与面纸、底纸、见坑纸在运行中的张紧度有关。
露坑:指纸面上能明显看到坑纹,由面纸或底纸缺材引起。
塌楞:指坑纸的峰楞受到超过其承受本领的压力而被压塌。
引起塌楞的原因可能是坑机运转、调机不正常(原则上每天均应试机),双面机内有杂物也与见坑纸所受的压力大小有关(如浆糊轮压不到位或压辊不平衡)。
脱坑:指纸板的各层纸黏合不良。
检验脱坑的方法有三种:(1)将纸板长度的一边靠近地面约成60°,用手掌在纸面上推动;(2)拿住纸板幅寬的两边,用适当的力向中心挤压;(3)剥离法,如黏合处的纸张纤维未受到破坏,则说明纸黏合不良。
脱坑产生的原因可能是施胶量小、异物堵塞浆糊管道、浆位调试不妥、浆糊黏度较小、受热时间与温度不合要求;纸板胀缩比例悬殊较大(如面、底、见坑);面纸、底纸、见坑纸受压不妥。
起泡:一般显现在面纸或底纸,原因有以下几方面:(1)原纸所含水分大(2)原纸的质量差(厚度不均、杂质较多);(3)施胶量不合要求(头机涂胶太少,吹风后甩坑或头机涂胶太多,抽风散热时间短,水分来不及蒸发);(4)浆糊水分蒸发慢,在纸板内形成空膜;(5)温度掌控不妥,紧要为热板;(6)压力不妥,如浆糊轮压不到位。
油污、斑点:纸板内外不得有油污,面纸不得有斑点(C纸除外)。
破损:纸板中心不能破损,纸板边沿破损以不影响外观为准。
折皱:指纸板面纸或底纸有明显皱纹,引起原因有以下几方面:(1)原纸来料折皱;(2)生产中未将纸面舒张平整;(3)张力掌控器没有掌控好面纸与底纸的张紧度:(4)面纸与底纸的张紧不协调。
弯曲:弯曲度是指纸板弯曲后水平面之间的最高高度与纸板弯曲方向的长度的百分比,分为横向弯曲(坑纹方向)和纵向弯曲(纸板长度方向)两种,一般横向弯曲情况较多。
瓦楞纸板各种常见纸病的解决方案

瓦楞纸板各种常见纸病的解决方案(一)来源: 作者:newmaker 时间:2006-04-24 18:06:16 字体:[大中小] 收藏我要投稿在瓦楞纸板的加工过程中,一些问题经常影响瓦楞纸板的品质和质量,下面对这些常见问题进行了汇总。
一、开胶、假粘1.里纸开胶原因分析:①胶质量不符合生产要求或腐败变质;②胶量太小;③瓦楞辊、压力辊热量不足;④压力辊压力不足;⑤瓦辊、压力辊的中高严重磨损。
解决方法:①更换合格胶液;②适量调大涂胶量;③提高压力辊、瓦楞辊的温度,保证180cC 以上温度开机;④适当调整压力辊压力,以里、瓦纸粘合良好,里纸不露楞为宜;⑤打磨或更损新压力辊、瓦楞辊。
2.面纸开胶原因分析:①胶量过小,烘干机车速过慢;②胶液稀薄,涂胶辊带胶不足;③烘干机热板温度不足,胶液未充分糊化;④烘干机车速过快、烘干不足;⑤烘干机和传输带上面的压载辊没完全落下。
解决方法:①适当加大涂胶量,并酌情提高车速;②更换胶液或在原胶液中加人适量乳化剂;③提高烘干机热板温度至180℃以上开机;④降低车速;⑤落下压载浮辊。
3.里纸假粘原因分析:①瓦楞辊温度不足;②胶量过小,温度过高;③车速缓慢,造成粹胶;④胶液粘度不够。
解决方法:①提高单面机温度;②调整涂胶量,关闭热源待温度降至180℃以下,160℃以上开机;③提高单面机速度;④适当增加胶液粘度。
4.面纸假粘原因分析:①烘干机热板温度不足;②胶液沉淀变质;③纸板在烘干机内停留时间过长。
解决方法:①待温度达到胶液能糊化时开机;②更换新胶;③降低面纸无轴支架的张力闸阀张力后仍出现面纸断裂,可更换拉力好的纸筒。
估计断纸重续时间可能超过两分钟,立即割断单面瓦楞纸板.将烘于机内的纸板开出后再续纸,昼减少纸板在烘干机内的停留时间。
二、倒楞1.单面纸板倒楞原因分析:①瓦楞辊磨损;②上下瓦辊间隙过大;③瓦纸克重太大太厚;④瓦纸水分过大;⑤瓦纸未经预热器可塑性差。
解决方法:①更换瓦辊或磨削;②调整两瓦辊间隙至0.5mm;③更换瓦纸;④调大瓦纸预热包角;⑤将瓦纸穿过预热器。
瓦楞纸板生产线常见问题及维护方法一
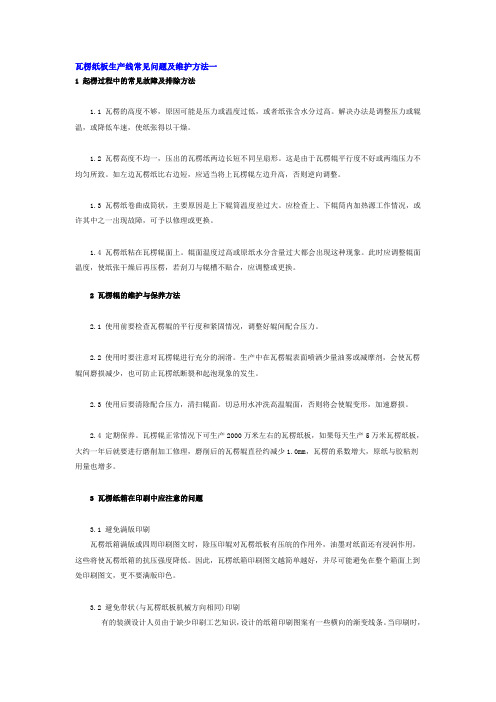
瓦楞纸板生产线常见问题及维护方法一1 起楞过程中的常见故障及排除方法1.1 瓦楞的高度不够,原因可能是压力或温度过低,或者纸张含水分过高。
解决办法是调整压力或辊温,或降低车速,使纸张得以干燥。
1.2 瓦楞高度不均一,压出的瓦楞纸两边长短不同呈扇形。
这是由于瓦楞辊平行度不好或两端压力不均匀所致。
如左边瓦楞纸比右边短,应适当将上瓦楞辊左边升高,否则逆向调整。
1.3 瓦楞纸卷曲成筒状,主要原因是上下辊筒温度差过大。
应检查上、下辊筒内加热源工作情况,或许其中之一出现故障,可予以修理或更换。
1.4 瓦楞纸粘在瓦楞辊面上。
辊面温度过高或原纸水分含量过大都会出现这种现象。
此时应调整辊面温度,使纸张干燥后再压楞,若刮刀与辊槽不贴合,应调整或更换。
2 瓦楞辊的维护与保养方法2.1 使用前要检查瓦楞辊的平行度和紧固情况,调整好辊间配合压力。
2.2 使用时要注意对瓦楞辊进行充分的润滑。
生产中在瓦楞辊表面喷洒少量油雾或减摩剂,会使瓦楞辊间磨损减少,也可防止瓦楞纸断裂和起泡现象的发生。
2.3 使用后要清除配合压力,清扫辊面。
切忌用水冲洗高温辊面,否则将会使辊变形,加速磨损。
2.4 定期保养。
瓦楞辊正常情况下可生产2000万米左右的瓦楞纸板,如果每天生产5万米瓦楞纸板,大约一年后就要进行磨削加工修理,磨削后的瓦楞辊直径约减少1.0mm,瓦楞的系数增大,原纸与胶粘剂用量也增多。
3 瓦楞纸箱在印刷中应注意的问题3.1 避免满版印刷瓦楞纸箱满版或四周印刷图文时,除压印辊对瓦楞纸板有压皖的作用外,油墨对纸面还有浸润作用,这些将使瓦楞纸箱的抗压强度降低。
因此,瓦楞纸箱印刷图文越简单越好,并尽可能避免在整个箱面上到处印刷图文,更不要满版印色。
3.2 避免带状(与瓦楞纸板机械方向相同)印刷有的装潢设计人员由于缺少印刷工艺知识,设计的纸箱印刷图案有一些横向的渐变线条。
当印刷时,印刷压力将瓦楞压溃。
纸箱的这一区域将发生应力集中,因而最易折断。
- 1、下载文档前请自行甄别文档内容的完整性,平台不提供额外的编辑、内容补充、找答案等附加服务。
- 2、"仅部分预览"的文档,不可在线预览部分如存在完整性等问题,可反馈申请退款(可完整预览的文档不适用该条件!)。
- 3、如文档侵犯您的权益,请联系客服反馈,我们会尽快为您处理(人工客服工作时间:9:00-18:30)。
瓦楞纸板生产线问题综述国产瓦楞纸板生产线常规的双面机烘干部加热、加压机构均由固定式的加热板和重力辊压力装置组成。
这两个装置在机器速度运行变化时,热传递是一固定值,在生产纸板的过程中,根据纸质等级、定量、厚度,通过蒸汽压力来调整热板热量来满足不同纸板的供热要求。
但当生产过程中特别是生产中、低档瓦楞纸板,由于纸板拉力不够,原级接头、缺口及断头情况常常会使纸板生产线运行速度发生变化(无全自动接纸装置)。
任何显着的速度变化都将打破热传递的平衡,而常规的双面烘干机热板是固定的不能调整。
此时纸板'十时间" 处于加热加压状态,过多的热量造成纸板受热过度,致使瓦楞纸板出现过量横向收缩.(翘曲)、发一脆和搓板状,甚至在压线处破裂等,最终导致成型后的瓦楞纸板压缩强度降低、印刷套印不准确、纸箱破损等缺陷。
根据热传递平衡,在热板中供给瓦楞纸板的热量必须适应瓦楞纸板生产线运行速度。
原纸的种类,这是制作质地均匀、不弯曲、不脆曲纸板的关键。
可将瓦楞板生产线常现双面机固定式的加热板设计为一套液压提升可变热量的加热系统。
因为在实际生产中要改变热板的温度是不可能的,只能通过调整热板的倾斜程度,使热板与一瓦楞纸板形成一个楔形,产生一定的空隙使部分热量从空隙散出,从而减少热板对瓦楞纸板供给的热量,达到热传递平衡的目的,确保瓦楞纸板通过双面烘干机时能有效地按不同瓦楞纸板烘干要求调节供给热量,保证瓦楞纸板的各种技术指标。
现有固定式热板装置的瓦楞纸板生产线无法改造成为可变热量加热系统(若要改,除非花大量资金投入进行改造),可设计一套空气注入系统,也就是隔层加热板烘干法。
它是在热板间的空隙处设计安装上窄小的喷管,用一组空气调气阀门,根据纸板运行速度的大小而调节阀门开闭角度,以控制喷管注入的空气量的大小,空气在热板与瓦楞纸板之间形成薄薄的空气层,以减少热板对瓦楞纸板热的传递,其原理就是当瓦楞纸板生产线运行速度降低时开启调节阀门,使吹火热板与纸板间的空气扩散,形成一个刚好能把瓦楞纸板与帆布带从热板上托起的薄片状空气股,从而减少热板对纸板过多热量的传递。
各种翘曲的主要原因和对策向上翘曲单面瓦楞纸板在单面瓦楞机及裱糊机处均要上胶,横向伸长大,而挂面纸(面纸张)由于直接与预热器和双面机的平板烘缸接触形成过干燥状态,进入双面机的冷却部后成为瓦楞纸板送出。
瓦楞纸板暴露到空气中,为达到水分平衡,水分大的单面瓦楞侧放出水分,同时发生收缩;而干燥的挂面纸吸收水分而伸长,因此产生上翘曲现象。
若当上述情况相反时(实际上是与平板烘缸的干燥能力相比粘合速度过快)则产生下翘。
使用单面瓦楞纸板的挂面纸比瓦楞纸板的面纸水分多3%的纸卷时,92%成为上翘曲。
使用瓦楞纸板的面纸水分比单瓦楞纸板的挂面纸水分多3%的纸卷时,75%成为下翘曲。
故在选择原纸时,挂面纸(单面机的挂面纸与瓦楞纸板的面纸)的水分波动必须保持3%以内。
作为解决上翘曲,除了原纸水分之外在瓦楞纸板机上还要注意:增加单面瓦楞机处的预热机与预处理机的包角。
尽量减少单面瓦楞机的上胶量。
减少过桥上单面瓦楞纸板的堆积量,尽可能保持单面瓦楞机与双面机的速度一致。
尽量减少瓦楞纸板在裱糊机处的上胶量。
以上4 条都是为了解决纸板上翘,尽可能减少单面瓦楞纸板进入双面机时水分过多设置的。
S 型翘曲上翘曲和下翘曲都是单纯的翘曲,s 型翘曲和以后叙述的对角翘曲,是很麻烦的翘曲。
发生这种翘曲时在生产线收纸处要以10-20 张纸板为一组进行翻转180 度方可堆积起来。
同时,这种翘曲严重时,除用上述方法堆积外,上面还要加上重物来压平翘曲,否则会造成后道制箱工序上的障碍。
发生S 型翘曲的原因是:挂机纸卷的横向的湿条斑。
挂面纸卷筒边的水分大。
双面机加热温度不均匀。
从上述3 条中得出克服S 型翘曲的主要关键是原纸的含水量要均匀,其次为双面机控制温度要均匀。
长度方向的翘曲瓦楞纸板的长度方向翘曲与原纸无关,这是因为在瓦楞纸板生产过程中张力调整方面而引起的。
即是由于瓦楞纸板面纸在放纸架、三层预热机上的拉力过紧,与单面瓦楞纸板的张力差过大而引起。
同时瓦楞纸板的面纸拉力过紧,也是在切纸机上产生长度误差的原因之一。
解决方法就是在操作上减少作用在单面瓦楞纸板与瓦楞纸板面纸上张力的差值。
对角翘曲对角翘曲,是由纵向和横向翘曲合成而产生的翘曲。
其原因主要在桥架上单面瓦楞纸板堆积过多成为过载、单面瓦楞纸板上的张力过大(张力是纵向翘曲的原因)、另外上翘、下翘或是S 型翘曲如前述是由于瓦楞纸板的水分差破坏了伸缩的平衡而产生的。
所以解决对角翘曲需综合考虑上述各种情况,在操作中一一排除上述不良情况,边操作、边观察。
例如:可通过对单面瓦楞纸板或面纸进行喷水,平衡纸板的含水量;可通过调整放纸架刹车松紧调整纸张张力、调整预热机包角、调整预处理机的包角等手段控制纸板的张力;可控制瓦楞纸板生产线的车速在稳定的状况下运行,合理减少桥架上的堆积量而不使其过载。
生产的纸板偏软纸板偏软是纸棉线线普遍存在的问题,主要有材料、淀粉糊度、温度、环境湿度等因素。
材料的优劣是主要原因。
随着市场竞争日趋激烈,各厂家压低价格抢占市场。
某些厂采用劣质原料,降低生产成本,这些低克数的原纸表现为厚薄不均、施胶极少、含沙量偏高、韧性纤维极少等。
这种材料非但不能做出优质的纸板,而且会加速瓦楞辊的磨损。
许多人认为淀粉糊太稠就是粘性极好,这是错误的。
相反浆太稠或单、双面机浆量过大是造成纸板偏软的原因。
纸板生产温度包括蒸汽温度和环境温度。
纸板线蒸汤温度通常在165℃~185℃之间,应在车速高时提高温度,车速低时降低温度,避免高温低速生产。
纸板与环境的温差太大就会造成纸板极易吸潮变软,特别是使用了无施胶的原纸。
压力的调节不当亦会引起纸板偏软。
要注意双面机上胶辊与压力辊的间隙调节以及热床压力辊的高低控制。
压力辊调得太低时,会导致楞峰顶变形造成纸板抗压力不够引起偏软。
瓦楞纸板生产线的操作及调整--瓦楞纸板的不良种类及判断调整不良纸板的分类在生产当中,会出现各种各样的不良现象,有时产生意料不到的不良品,而最常见的不良现象主要可分为三大类。
一、贴合不良面纸贴合不良;面纸纸边贴合不良;面纸起泡;A、B 楞之间贴合不良;底纸、中纸出现贴合不良起泡;A 芯、B 芯出现倒楞或高低楞。
二、纸板弯曲左右上弯曲;左右下弯曲;前后上弯曲;前后下弯曲;侧(扭)弯曲;S 型弯曲。
三、面纸排骨状刮痕状排骨;楞间凹陷排骨状;后痕、黑线排骨状。
不良纸板的原因分析在一般情况下,纸板出现不良现象,主要是以下几方面原因,1、机械出现故障;2、机器调整不到位;3、蒸汽供应不足;4、浆糊制作不合格;5、原纸质量不达标等。
如要解决问题,必须仔细分析产生不良纸板的真正原因,再想办法针对问题予以解决,切不可盲目操作调整。
下面就针对三大类不良品出现现象进行分析:一、贴合不良1、面纸贴合不良原因:浆糊供应不足(失糊);热板与帆布间隙提的太高;车速太快造成浆糊糊化时间不足;刮糊辘间隙太小,上糊量不足;浆糊粘度不达标(太高或太低);楞尖浆糊成白色粉状,这是糊化温度太高,浆糊没有熟化;楞尖浆糊成黑线且是亮晶晶的,这是糊化温度太低,在纸板未进入热板以前就已糊化;A、B 楞刹车辘刹车压力太低或面纸太松;三重预热缸温度不足或积水;热板温度不足或积水。
2、面纸纸边帖合不良原因:浆糊糊化温度太高;浆糊糊化温度太低;原纸施胶不够或施胶太大;帆布边上磨损太多;面纸纸边水份太高;底纸压力太重;天桥积纸太多或A、B 楞吸风力不够。
3、面纸起泡原因:原纸张力太小;热板与帆布间隙太高;原纸挂浆不匀或太过干燥;A、B 楞出现高低楞或倒楞。
4、A 楞与B 楞贴不良原因:车速太快,浆糊来不及熟化;糊化温度太高或太低;浆糊粘度不达标;上糊量太小(刮糊辘间隙太小;三重预热缸温度不足或积水;热板温度不足或积水;A、B 楞吸风力太低;A、B 楞在三重工业预热缸上的预热面积太小,导致预热不足;帆布与热板间隙提的太高;A 楞、B 楞生于潮湿,水份太高。
5、底纸起泡原因:原纸两边平行度未调整好;自动接纸板张力不足,原纸架刹车力量太小;糊辘间隙调整不到位;原纸截面水份不均匀;压力棍间隙没有调好;底纸刹车张力太高;糊辘磨损极其严重;车速突然加快或降低;原纸挂浆不匀或太过干燥。
6、底纸贴合不良原因:(1)压力辊间隙没有调整到位;(2)楞棍的偏芯未调整到位;(3)原纸水份太高;(4)原纸架刹车张力太小;(5)底纸、芯纸预热面积太少;(6)预热缸、压力辊、瓦楞辊积水、温度不足;(7)蒸汽供应不足;(8)楞辊间隙调整不到位;(9)刮糊辊间隙太小,糊量上的太少;(10)浆糊的粘度不达标;(11)糊化温度太高或太低;(12)车速太快。
7、单面机芯纸出现倒楞或高低楞原因(1)瓦楞辊偏芯没有调整好;(2)瓦楞棍磨损严重;(3)瓦楞辊上粘有浆糊,灰尘等杂物;(4)芯纸出现太多,太大的缺口;(5)鲁纸吸风车吸风太强或太弱;(6)上下瓦楞辊两边压力不均匀。
二、纸板弯曲:纸板弯曲要受到原纸含水率的多少,纸的性质及种类,主要经过预热缸的预热程序、上糊量、张力进行调整。
1、左右上弯曲原因:里纸水份太高里纸水份预热不足;里纸上糊量太大;过胶机里纸刹车张力太小,三重预热缸温度不足;面纸刹车张力太大,三重预热缸面纸预热太大;面纸上糊量太小;热板温度太高;帆布压的太低;车速太慢。
2、左右下弯曲原因:与左右上弯曲相反3、前后上弯曲原因:过胶机A 楞与B 楞刹车压力太高;面纸刹车辘线太低。
4、前后下弯曲原因:与前后上弯曲原因相反。
5、侧(扭)弯曲原因:过胶机A 楞、B 楞等纸辘不平行,造成生纸张力不均;面纸水份不均;面纸刹车张力太高。
6、"S"型弯曲原因里纸上糊不均;里纸水份不均;里纸平行度调整未到位;面纸上糊不均;面纸水份不均;面纸平行度调整未到位。
三、面纸排骨状1、刮痕排骨状原因:主要是由于热板未能调整平行及两块热板之间前一块高度低于后一块高度造成。
2、楞间凹陷状原因:原纸物性不达标;糊量太大;热板磨损(高低不平);芯纸有高低楞现象;面纸张力太大、受热太高。
3、压痕、黑纸状原因:过胶机压棍压的太低;糊量上的太大;帆布压的太低;片碱量太大造成渗透力太强。
减少及预防不良品产生在前面列出了一些不良品的产生原因,主要有机械、原物料、技术的等各种各样因素存在,那么,在这一节中就一些常见的不良品如何以技术方面进行预防及解决。
解决贴合不良从以下几方面着手:浆糊制作;蒸汽供应;机械控制。
只要熟练地掌握了这三方面的操作方法,贴合不良就基本可以解决。
1、浆糊问题:浆糊制作的好坏,对纸板的质量起到了绝对的重要作用,因此相关人员必须完全掌握浆糊的制作方法及原物料配比,及时地调整纸板粘合所需要的糊化温度及其粘度。