不锈钢的切削
分析不锈钢的机械加工方法

分析不锈钢的机械加工方法不锈钢是一种耐腐蚀的金属材料,广泛应用于制造行业中。
机械加工是对不锈钢进行形状加工和表面处理的重要方法之一,本文将分析常用的不锈钢机械加工方法。
1.铣削加工:铣削是将刀具在工件上旋转切削的一种加工方法。
不锈钢的硬度相对较高,因此在铣削过程中需要选用高硬度的刀具,并采用适当的切削速度和进给速度。
对于精密加工,还可采用数控铣床进行精确控制。
2.车削加工:车削是通过旋转车刀将工件宽度修整到设计尺寸的加工方法。
不锈钢的硬度高,具有很高的切削难度。
为了保证加工质量,需要选用刀具的刀片材料具有良好的切削性能,经常更换刀片,并且适当选择进给速度和切削速度。
3.钻削加工:钻削是通过旋转刀具在工件上切削孔洞的加工方法。
在不锈钢的钻削中,由于工件硬度高,钻头容易损坏。
因此,应选择硬质合金钻头,采用较低的切削转速,并进行冷却润滑剂的切削润滑。
4.磨削加工:磨削是通过磨料颗粒对工件进行磨削的一种加工方法。
不锈钢硬度高,适合采用砂轮进行磨削。
在磨削过程中,应选用适当的磨具和磨削磨粒,并保证切削液的良好冷却和润滑。
5.锻造加工:锻造是通过对不锈钢材料施加压力,使其发生塑性变形并改变形状的一种加工方法。
不锈钢具有较好的锻造性能,适合进行锻造加工。
通过锻造可以获得高强度和良好的耐腐蚀性能的零件。
6.激光切割:激光切割是通过高能激光束对不锈钢表面进行烧蚀,达到切割的目的。
激光切割具有高精度、高速度的特点,可用于制造复杂形状的零件。
7.电火花加工:电火花加工是通过电脉冲在工件表面产生高能量火花,使工件表面产生微小的氧化腐蚀,从而实现对不锈钢进行精细加工和切割的一种方法。
以上是常见的不锈钢机械加工方法,每种方法都具有适用的情况和要求。
在实际应用中,需要根据具体的加工需求和工件材料特性进行选择,以获得最佳的加工效果。
不锈钢车削参数
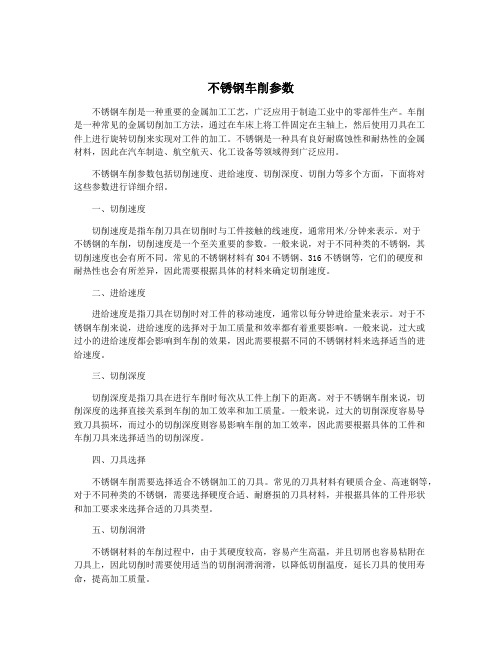
不锈钢车削参数不锈钢车削是一种重要的金属加工工艺,广泛应用于制造工业中的零部件生产。
车削是一种常见的金属切削加工方法,通过在车床上将工件固定在主轴上,然后使用刀具在工件上进行旋转切削来实现对工件的加工。
不锈钢是一种具有良好耐腐蚀性和耐热性的金属材料,因此在汽车制造、航空航天、化工设备等领域得到广泛应用。
不锈钢车削参数包括切削速度、进给速度、切削深度、切削力等多个方面,下面将对这些参数进行详细介绍。
一、切削速度切削速度是指车削刀具在切削时与工件接触的线速度,通常用米/分钟来表示。
对于不锈钢的车削,切削速度是一个至关重要的参数。
一般来说,对于不同种类的不锈钢,其切削速度也会有所不同。
常见的不锈钢材料有304不锈钢、316不锈钢等,它们的硬度和耐热性也会有所差异,因此需要根据具体的材料来确定切削速度。
二、进给速度进给速度是指刀具在切削时对工件的移动速度,通常以每分钟进给量来表示。
对于不锈钢车削来说,进给速度的选择对于加工质量和效率都有着重要影响。
一般来说,过大或过小的进给速度都会影响到车削的效果,因此需要根据不同的不锈钢材料来选择适当的进给速度。
三、切削深度切削深度是指刀具在进行车削时每次从工件上削下的距离。
对于不锈钢车削来说,切削深度的选择直接关系到车削的加工效率和加工质量。
一般来说,过大的切削深度容易导致刀具损坏,而过小的切削深度则容易影响车削的加工效率,因此需要根据具体的工件和车削刀具来选择适当的切削深度。
四、刀具选择不锈钢车削需要选择适合不锈钢加工的刀具。
常见的刀具材料有硬质合金、高速钢等,对于不同种类的不锈钢,需要选择硬度合适、耐磨损的刀具材料,并根据具体的工件形状和加工要求来选择合适的刀具类型。
五、切削润滑不锈钢材料的车削过程中,由于其硬度较高,容易产生高温,并且切屑也容易粘附在刀具上,因此切削时需要使用适当的切削润滑润滑,以降低切削温度,延长刀具的使用寿命,提高加工质量。
通过对不锈钢车削参数的合理选择,在保证车削加工效率的还能够得到尺寸精确、表面光滑的加工零件。
不锈钢的车削技巧

不锈钢的车削技巧主要包括以下几个方面:1.刀具选择:选择适合不锈钢车削的刀具非常重要。
通常,选择具有较高耐热性、耐磨性和与不锈钢亲和作用小的刀具材料,如高碳、高钒或钼系的高速钢。
此外,刀具的几何形状和角度也需要根据具体加工要求进行选择。
2.切削用量选择:切削用量包括切削速度、进给量和切削深度。
对于不锈钢的车削,切削速度通常较低,一般为普通碳钢切削速度的40%~60%。
进给量和切削深度也需要根据具体情况进行选择,以避免刀具过度磨损和工件表面质量下降。
3.冷却液选择:使用合适的冷却液可以有效降低切削温度,减少刀具磨损和提高工件表面质量。
对于不锈钢的车削,通常选择具有较好冷却和润滑性能的冷却液。
4.操作技巧:在车削不锈钢时,需要注意以下几点操作技巧:首先,保持刀具的锋利,及时更换磨损的刀具;其次,避免使用过大的切削用量,以减少刀具的受力;最后,注意工件的装夹方式和切削力的方向,以避免工件变形或振动。
此外,还需要注意以下几点:1.由于不锈钢的塑性大、韧性高,车削时容易产生积屑瘤和鳞刺,这不仅影响工件的表面粗糙度,还会使刀具的磨损加快。
因此,需要选择合适的刀具材料和几何角度,以及合理的切削用量来避免这些问题的产生。
2.不锈钢的导热性差,导致切削热无法及时散出,使刀具的刃口温度升高,加剧刀具磨损。
为了降低切削温度,可以采用浇注冷却液的方法。
3.在车削过程中,应随时注意观察切削情况,如发现异常现象(如振动、噪声、温度升高等),应及时采取措施进行调整。
4.对于不同种类和规格的不锈钢材料,其车削性能也会有所不同。
因此,在实际加工前,最好先进行一些试验性切削,以确定最佳的切削参数和工艺方案。
总之,掌握不锈钢的车削技巧需要综合考虑多个因素,包括刀具选择、切削用量、冷却液和操作技巧等。
通过合理的选择和调整这些参数,可以提高加工效率、降低生产成本并获得高质量的工件。
不锈钢车削参数

不锈钢车削参数不锈钢车削参数是指在车削加工过程中,针对不锈钢材料的特性和要求所设定的一系列切削参数。
这些参数对于保证加工质量和提高生产效率具有重要意义。
以下是一些建议的不锈钢车削参数:1. 切削速度(Vc):切削速度是刀具在旋转时与工件接触点的速度。
对于不锈钢材料,切削速度应适当降低,以防止刀具过热和磨损。
一般推荐切削速度为20-60m/min。
2. 进给量(f):进给量是指刀具在每次切削行程中沿工件轴向移动的距离。
对于不锈钢材料,进给量应适当降低,以减小刀具磨损和切削力。
一般推荐进给量为0.1-0.3mm/r。
3. 切削深度(ap):切削深度是指刀具在每次切削行程中切入工件的深度。
对于不锈钢材料,切削深度应适当降低,以减小刀具磨损和切削力。
一般推荐切削深度为0.1-0.5mm。
4. 刀具前角(γo):刀具前角是指刀具主切削刃与工件表面的夹角。
对于不锈钢材料,刀具前角应适当增大,以提高切削性能和减少刀具磨损。
一般推荐前角为10-20°。
5. 刀具后角(αo):刀具后角是指刀具主切削刃与工件表面的夹角。
对于不锈钢材料,刀具后角应适当增大,以提高切削性能和减少刀具磨损。
一般推荐后角为8-12°。
6. 切削液:不锈钢车削过程中,应使用适当的切削液来冷却和润滑刀具和工件,以降低切削温度和减少刀具磨损。
常用的切削液有水溶性切削液、油溶性切削液和乳化液等。
7. 刀具材质:不锈钢车削过程中,应选择具有良好耐磨性和抗腐蚀性的刀具材质,如硬质合金、陶瓷和高速钢等。
8. 机床刚性:不锈钢车削过程中,应选择具有较高刚性的机床,以保证加工精度和表面质量。
9. 工艺路线:不锈钢车削过程中,应根据工件的形状和尺寸选择合适的工艺路线,以减少切削力和热量对加工质量的影响。
总之,不锈钢车削参数的选择应根据具体的工件材料、形状和尺寸以及加工要求进行综合考虑,以达到最佳的加工效果。
不锈钢切削工作总结

不锈钢切削工作总结
不锈钢由于其自身特性,在切削加工过程中难度较大,容易产生磨损。
经过这次切削工作,我总结几点经验:
1. 使用正确的工具材料。
不锈钢最好使用陶瓷或超级陶瓷的刀具,降低磨损。
使用碳钢或高速钢的刀具在切削不锈钢时寿命较短。
2. 选择合适的切削参数。
切削速度和进给率不能太大,否则容易造成刀具断裂。
速度一般控制在100-150/之间,进给率控制在0.1-0.2/转之间。
3. 减小切屑厚度。
一次切除厚度控制在0.2以下,多次切削完成整个形状,减轻单次切削的负担。
4. 切削材料预热。
将不锈钢材料预热到150-200°,可以减少切削时的力量和延展冷缩应力,有利于延长刀具使用寿命。
5. 增大切削液流量。
合理使用切削液冷却和清洗作用,有效减少风化和磨损。
通过这次总结,下次切削不锈钢时能选择更合适的工具和参数,操作过程更顺利,也为日后不锈钢加工积累经验。
不锈钢加工参数表

不锈钢加工参数表1. 切削速度:切削速度是指在切削过程中,刀具与工件接触点处的线速度。
不锈钢的切削速度通常在20-60m/min之间,具体数值取决于刀具材料、刀具几何形状、工件材料和加工要求等因素。
切削速度过高可能导致刀具磨损加快,切削力增大,加工精度降低;切削速度过低则可能导致刀具寿命降低,加工效率降低。
2. 进给速度:进给速度是指刀具在切削过程中沿工件进给方向的移动速度。
不锈钢的进给速度通常在0.1-0.5mm/r之间,具体数值取决于刀具材料、刀具几何形状、工件材料和加工要求等因素。
进给速度过高可能导致刀具磨损加快,切削力增大,加工精度降低;进给速度过低则可能导致刀具寿命降低,加工效率降低。
3. 切削深度:切削深度是指刀具在一次切削过程中切入工件的深度。
不锈钢的切削深度通常在0.1-0.5mm之间,具体数值取决于刀具材料、刀具几何形状、工件材料和加工要求等因素。
切削深度过大可能导致刀具磨损加快,切削力增大,加工精度降低;切削深度过小则可能导致刀具寿命降低,加工效率降低。
4. 切削宽度:切削宽度是指刀具在一次切削过程中切入工件的宽度。
不锈钢的切削宽度通常在2-10mm之间,具体数值取决于刀具材料、刀具几何形状、工件材料和加工要求等因素。
切削宽度过大可能导致刀具磨损加快,切削力增大,加工精度降低;切削宽度过小则可能导致刀具寿命降低,加工效率降低。
5. 切削油或冷却液:不锈钢加工过程中,为了降低切削温度,减少刀具磨损,提高加工精度和表面质量,通常需要使用切削油或冷却液。
切削油或冷却液的选择应根据不锈钢材料、刀具材料、加工条件等因素进行。
常用的切削油或冷却液有矿物油、乳化液、水溶性切削液等。
6. 刀具材料:不锈钢加工过程中,常用的刀具材料有高速钢、硬质合金、陶瓷、金刚石等。
不同材料的刀具对不锈钢的加工性能和加工效果有很大影响。
选择合适的刀具材料可以提高加工效率,延长刀具寿命,提高加工精度和表面质量。
不锈钢加工参数表

不锈钢加工参数表1. 引言不锈钢是一种具有耐腐蚀性能的合金材料,广泛应用于制造业中。
在不锈钢加工过程中,为了保证产品质量和生产效率,需要确定适当的加工参数。
本文将详细介绍不锈钢加工参数表的编写方法和相关注意事项。
2. 不锈钢材料特性不锈钢具有以下特性:•高强度:不锈钢具有较高的强度,能够承受较大的载荷。
•耐腐蚀性:不锈钢能够抵抗大多数化学物质的侵蚀。
•良好的机械性能:不锈钢具有良好的塑性和可焊接性。
•耐高温性:不锈钢在高温下仍然保持较好的力学性能。
3. 不锈钢加工参数3.1 切削速度(Cutting Speed)切削速度是指切削刀具在单位时间内通过工件表面的线速度。
在不同材料和切削过程中,切削速度会有所变化。
下表列出了常见类型的不锈钢材料的推荐切削速度范围(单位:m/min):不锈钢材料范围304不锈钢50-100316不锈钢40-80430不锈钢60-1203.2 进给量(Feed Rate)进给量是指切削工具在单位时间内与工件接触的长度。
进给量的选择需要考虑切削力和表面粗糙度等因素。
下表列出了常见类型的不锈钢材料的推荐进给量范围(单位:mm/rev):不锈钢材料范围304不锈钢0.1-0.2316不锈钢0.08-0.15430不锈钢0.15-0.253.3 刀具半径(Tool Radius)刀具半径是指切削工具刀尖到刀具轴线的距离。
合适的刀具半径能够减小加工过程中产生的振动和应力集中。
下表列出了常见类型的不锈钢材料的推荐刀具半径范围(单位:mm):不锈钢材料范围304不锈钢0.5-1.0316不锈钢0.4-0.8430不锈钢0.6-1.23.4 冷却液(Coolant)冷却液在不锈钢加工过程中起到冷却切削区域、润滑切削面和清洁切屑的作用。
选择适当的冷却液可以提高加工效率和延长刀具寿命。
常用的冷却液有水溶性切削油和合成切削油。
3.5 加工方式(Machining Method)根据不同的加工要求,可以选择旋转铣削、车削、线切割等加工方式。
不锈钢车削参数
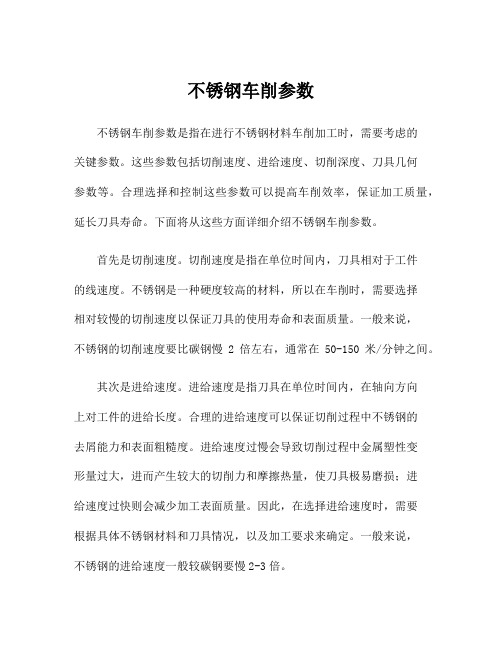
不锈钢车削参数不锈钢车削参数是指在进行不锈钢材料车削加工时,需要考虑的关键参数。
这些参数包括切削速度、进给速度、切削深度、刀具几何参数等。
合理选择和控制这些参数可以提高车削效率,保证加工质量,延长刀具寿命。
下面将从这些方面详细介绍不锈钢车削参数。
首先是切削速度。
切削速度是指在单位时间内,刀具相对于工件的线速度。
不锈钢是一种硬度较高的材料,所以在车削时,需要选择相对较慢的切削速度以保证刀具的使用寿命和表面质量。
一般来说,不锈钢的切削速度要比碳钢慢2倍左右,通常在50-150米/分钟之间。
其次是进给速度。
进给速度是指刀具在单位时间内,在轴向方向上对工件的进给长度。
合理的进给速度可以保证切削过程中不锈钢的去屑能力和表面粗糙度。
进给速度过慢会导致切削过程中金属塑性变形量过大,进而产生较大的切削力和摩擦热量,使刀具极易磨损;进给速度过快则会减少加工表面质量。
因此,在选择进给速度时,需要根据具体不锈钢材料和刀具情况,以及加工要求来确定。
一般来说,不锈钢的进给速度一般较碳钢要慢2-3倍。
第三是切削深度。
切削深度是指刀具在一次车削过程中与工件接触的长度。
合理的切削深度可以控制不锈钢的切削力和切削温度,避免损耗过大和材料表面的过热变焦。
切削深度要根据不锈钢的强度、硬度和材料加工性能来确定。
通常情况下,不锈钢的切削深度要较小,以保证刀具的使用寿命和加工表面质量。
最后是刀具几何参数。
刀具几何参数主要包括刀具刃磨角度、前角、主偏角和刀具尺寸等。
合理选择刀具几何参数可以减小切削力和摩擦热量,从而延长刀具寿命,并提高加工质量。
对于不锈钢材料,刀具刃磨角度一般要小于碳钢,以减小热应力和摩擦热量;前角适当增大可以增强刀具的切削能力和排屑能力;主偏角的选择要结合不锈钢材料的切削性能和加工要求来确定。
此外,刀具的尺寸也要根据工件的尺寸和切削要求进行选择,通常要保证切削力和切削厚度的均衡。
综上所述,不锈钢车削参数是进行不锈钢加工时需要考虑的关键参数,包括切削速度、进给速度、切削深度和刀具几何参数等。
- 1、下载文档前请自行甄别文档内容的完整性,平台不提供额外的编辑、内容补充、找答案等附加服务。
- 2、"仅部分预览"的文档,不可在线预览部分如存在完整性等问题,可反馈申请退款(可完整预览的文档不适用该条件!)。
- 3、如文档侵犯您的权益,请联系客服反馈,我们会尽快为您处理(人工客服工作时间:9:00-18:30)。
( 削 液 为乳 化 剂 ) 切 ,车 床 转 速 6 rm n 0/ i ,进 给 量
0 2 m, 虽 然 仍 出 现 主 切 削 刀 磨 损 且 产 生 切 削 瘤 现 .m
象 ,但 比前 一 次 能 够 加 工 的 时 间 有 所 加 长 ,达 到
3 mm 左 右 。 0
1 .加 工 特 性
2 j - 参 数 选 择 .) r  ̄
由于工件 长度和 直 径之 比近 1 5倍 , 属 于 细 长 轴
磨损 更严 重 。过 低转 速 反 而使 刀 具 更 容 易 磨 损 ,这
种情 况我 们 当初 没料 到 。后 把 转 速 再 次 调 高 ,但 工
加工 。工件 本 身 刚 性 弱 ,容 易 弯 曲和 振 动 ,不 容 易
表性 的一种 ,具 有 良好 的抗 蚀 性 和耐 酸 性 ,韧性 高 、
高温机 械强 度 高 ,易 冲 压 和 焊 接 。此 次 加 工 的不 锈
钢管是热 轧 板 卷 焊 管 ,表 面黑 皮 在 焊 接 部 位 与 没 有
焊接部 位 的硬 度 不 一 样 。 其韧 性 大 ,切 削 困 难 ,高 温强度 高 、硬度 高 ,切 削 时粘 刀 性 很 强 ,切 削 过 程
我们 先调直 毛坯 件 的弯 曲 度 ,加 工 时将 掉 头 的 次数
有错 ,原 因可 能 是 工 件 本 身 的黑 皮 硬 和 焊 口回火 处
硬一点 。切 削 时摩 擦 产 生 的 热 和加 工 时 遇 到 冷却 水 突然温 度 急剧 下 降 ,使 表 皮 的 硬 度 增加 ,刀 具 承 受
工 时 出现 的 热 膨 胀 轴 向 延 长 ,处 理 不 及 时 而 导 致 工
切削普通 碳 素钢 的刀 具 9 。 刀 和 4 。 刀 ,刀 片材 0牟 5车 质为 Y 1 T 5硬 质合 金 。但 发现 其 主切 削刃 在工 作 时磨 损非 常快并 有 切 削 瘤 产 生 ,再 切 削 下 去便 会 产生 扎 刀现 象 ,切 削非 常不顺 利 ,只车 1 m 0 m之 多 年刀就 磨
1 r8 iT 在奥 氏体 类 不 锈 钢 应 中是 最 有 代 C l N9 i
分析 出现 以上 的原 因 ,Y 1 、Y 1 T 5 T 4两种 硬 质合 金 ,抗 冲击 和抗 振 性 能 好 ,但 耐磨 性 能 较 差 。之 后
又选 用通 用 性 能 较 好 的 Y w1硬 质 合 金 ,9 。 夹 偏 0机 刀 刀片进 行 试验 切 削 ,考 虑 到 工 件 表 面加 工 条件 不
是很 好 ,Y 耐 冲击 和抗 振性 能低 ,我 们 把 车 床转 W1
速定 为 3 . rmi ,背 吃 刀 量 0 2 3 5/ n . mm,加 上 切 削 液 ,
中易产生 切 削瘤 ;切 削 时 导热 率 很 低 ,产 生 的 热 量
不能及 时散 发 掉 ;加 工 时 硬化 现象 很 强 ,车 削 刀 具 易磨 损 ;切 屑 容 易折 断 ,易 塞刀 ,易 使 刀具 损 坏 ; £削 过 程 中 的 振 动 不 仅 会 使 工 件 加 ] 表 面 恶 化 , U _ 也会 加 强 不锈 钢 的 加 工 硬 化 ,给 切 削 加 工 增 加 困
这批 零 件 材 料 为 1 r8 iT C l N9 i不 锈 钢 ,毛 坯 直 径
2 6 m,长 3 0 mm,粗 车 至 + 1 mm,长 314 lr a 19 22 0 nl,两端 需车 加工长 1 0 m、直 径 12 1 1 m 两个 l1 1 0r 了。
增加 一次 ,且车 床 尾座 顶 尖 顶 的不 宜 过 紧 ,可在 切
削 过 程 中 随 时 观 察 由 切 削 热 引 起 的 热 膨 胀 ,调 整 尾 座顶尖 的支顶 松 紧程度 。 本 次 加 工 的 材 料 是 热 轧 板 卷 焊 卷 材 ,开 始 时 用
在切 削液 使 用 问 题 上 , 由于 没 能认 识 到 它 的 重 要性 ,开 始 使用 的泵 流 量 小 ,冷却 效果 差 ,工件 加
C 。
不锈钢 的切 削
秦 皇 岛秦 冶 重 工 有 限公 司 ( 北 河 061 ) 6 3 8 唐丽君 王 凯乐
在 加 工 玻 璃 设 备 零 件 时 ,有 一 批 不 锈 钢 工 件 。
损坏 了 ,几乎 不能 车 削。之 后改 用主 偏角 为 7 。 车 5的 刀 ,材 质为 Y 1 T 4硬 质 合 金 的 刀 片 ,加 切 削液 切 削
难。
但 结 果和 前两次 区别不 大 。 考虑 到不锈 钢管 太长 ( 长 3O 0 全 0 mm) ,料本 身 平衡 不好 ,车床 转 速用 6 rri。如果 进 给量 小 ,加 0/ n a
工时 间延 长 ,效 率 低 ;而 进 给 量 大 ,车 刀 磨 损 又 严 重 ,我们 选 择 背 吃 刀 量 0 2 m,但 加 工 效 果 不 好 。 .r a 后又 把车 床转速 降到 3 rm n左右 还是不 行 ,且车 刀 0/ i
获得 满意 的 儿何 精 度 ,加 工 中的 切 削 热 容易 使丁 件
件 在 切 削 时 义 产 生 振 动 。 最 后 ,把 转 速 定 在 6 0
rmi ,背 吃 刀 量 为 0 3 / n . mm。 对 于 出 现 的 问 题 ,笔 者 认 为 刀 具 材 质 的 选 用 没
发生 线性 膨胀 ,产生 弯 曲变 形 ,使 工件 车 成 多棱 形 。
件热 变形 弯 曲 ,后 来 换 一 个 大 流量 泵 冷 却 效 果 非 常 明显 ,而且 随 时注 意 尾 座 顶 尖 工作 状 况 并 随 时 调 整
参磊
冷 加
^ m e【 、 al 帕
Ⅲ
n叠●  ̄U CO y o m -
要
5 1
工件 ,热 变形 减 小 了很 多 。使 , 的 乳化 液 浓 度 应 浓 [ } J