油气集输处理工艺发展现状及发展前景
油气集输处理工艺发展现状及发展前景
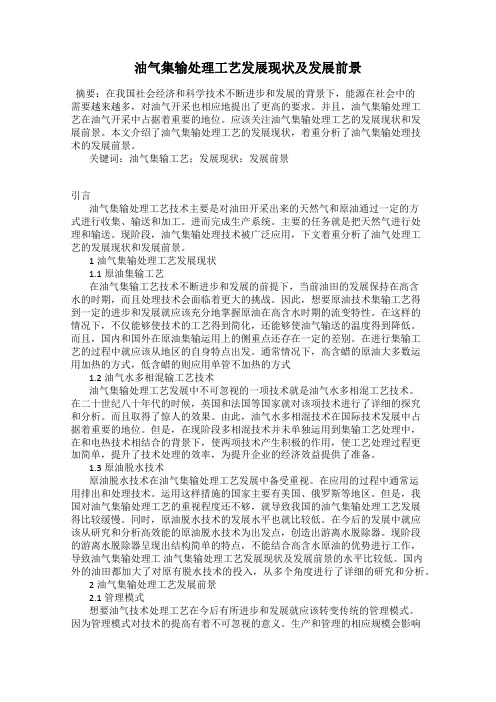
油气集输处理工艺发展现状及发展前景摘要:在我国社会经济和科学技术不断进步和发展的背景下,能源在社会中的需要越来越多,对油气开采也相应地提出了更高的要求。
并且,油气集输处理工艺在油气开采中占据着重要的地位。
应该关注油气集输处理工艺的发展现状和发展前景。
本文介绍了油气集输处理工艺的发展现状,着重分析了油气集输处理技术的发展前景。
关键词:油气集输工艺;发展现状;发展前景引言油气集输处理工艺技术主要是对油田开采出来的天然气和原油通过一定的方式进行收集、输送和加工。
进而完成生产系统。
主要的任务就是把天然气进行处理和输送。
现阶段,油气集输处理技术被广泛应用,下文着重分析了油气处理工艺的发展现状和发展前景。
1油气集输处理工艺发展现状1.1原油集输工艺在油气集输工艺技术不断进步和发展的前提下,当前油田的发展保持在高含水的时期,而且处理技术会面临着更大的挑战。
因此,想要原油技术集输工艺得到一定的进步和发展就应该充分地掌握原油在高含水时期的流变特性。
在这样的情况下,不仅能够使技术的工艺得到简化,还能够使油气输送的温度得到降低。
而且,国内和国外在原油集输运用上的侧重点还存在一定的差别。
在进行集输工艺的过程中就应该从地区的自身特点出发。
通常情况下,高含蜡的原油大多数运用加热的方式,低含蜡的则应用单管不加热的方式1.2油气水多相混输工艺技术油气集输处理工艺发展中不可忽视的一项技术就是油气水多相混工艺技术。
在二十世纪八十年代的时候,英国和法国等国家就对该项技术进行了详细的探究和分析。
而且取得了惊人的效果。
由此,油气水多相混技术在国际技术发展中占据着重要的地位。
但是,在现阶段多相混技术并未单独运用到集输工艺处理中,在和电热技术相结合的背景下,使两项技术产生积极的作用,使工艺处理过程更加简单,提升了技术处理的效率,为提升企业的经济效益提供了准备。
1.3原油脱水技术原油脱水技术在油气集输处理工艺发展中备受重视。
在应用的过程中通常运用排出和处理技术。
当前油气集输处理工艺发展现状及发展前景

当前油气集输处理工艺发展现状及发展前景【摘要】随着我国社会经济发展的突飞猛进,人类对天然气和原油的需求也在不断的加大,油田开发的重要性也随之显现。
近年来,国家加大了对油田开采项目的投资,以确保满足人民群众生产生活中的需求。
随着油田开发项目不断地扩大,油气集输生产受到了社会各界的关注,并且对油气集输生产过程中的油气集输处理工艺的要求越来越严格,由于油气集输本身具连续性生产以及涉及的范围面广,因此,存在一定的复杂性和危险性,但它却是油田开采过程中一项关键的生产环节。
为了满足社会各界对油气集输处理工艺的要求,就必须加强对油气集输处理工艺的研究,从而让油气集输处理工艺水平得到有效地提高。
【关键词】油气集输处理工艺现状发展前景在油田开采的过程中,油气集输主要的工作是简单加工、采集、运输以及储存刚开采出来的原油和天然气。
通过对天然气和原油的分开处理之后,将检验合格的原油运送至油田原油库进行储存,天然气则需被输送至天然气处理厂进行二次加工,油田原油库和天然气处理厂将使用不同工艺深加工的原油和天然气,通过油气集输工艺传输给广大的用户。
由于油气集输工艺本身存在一定的危险性和复杂性,因此,油气集输处理工艺的生产安全成为了社会各界的重点关注,在油田开采的过程中,油气集输处理工艺具有重要的作用,它不仅决定了油田开采的总体水平,也可以有效地提高油气企业的社会经济效益。
1 油气集输处理工艺的发展现状1.1 原油集输工艺由于油田开采项目不断地增长,目前的油田都处于高含水期,这种情况给油气集输处理工艺带来了更为严格的要求,如何针对原油高含水期的特点进行原油集输工艺的改良,是目前有待解决的问题。
由于高含水期的原油存在一定的流变特征,因此,可以根据这一特点,对油气集输工艺进行适当的调整,可以对流变性原油运送的过程中降低原油的温度。
由于各个地区油田的特点不同,油田集输处理工艺必须根据不同特点进行不同的处理。
油田集输处理工作在进行的过程中,对含蜡高的原油必须采用单管集输的输送方法,并且进行加热以及加入适量的化学药剂,而对于含蜡低的原油则采取单管集输,但是输送过程中无需加热和添加化学药剂。
分析油气集输工艺技术在生产中的应用

分析油气集输工艺技术在生产中的应用随着全球能源需求的增长和技术的不断进步,油气集输工艺技术在油气生产中的应用越来越广泛,对于提高油气生产效率、降低成本、保障安全生产起到了至关重要的作用。
本文将从油气集输工艺技术的概念、发展现状和在生产中的应用方面进行分析。
一、油气集输工艺技术的概念及发展现状油气集输工艺技术是指将采油、采气、作业和输送等一系列生产过程综合起来,采用先进的工艺和设备,对原油和天然气进行处理、储存、运输的一种技术。
随着油气勘探开发的深入和对资源利用的要求越来越高,油气集输技术也在不断发展壮大。
目前,国际上较为先进的油气集输工艺技术主要包括:智能化管道系统、大型气液输送系统、多相流动技术等。
1. 智能化管道系统:利用先进的传感器技术、数据处理技术和物联网技术,实现对管道系统各项参数的实时监测和控制,提高管道的安全性和运行效率。
还能够对管道进行远程监控和智能化运维管理,大大降低了人工成本和维护成本。
2. 大型气液输送系统:采用高压气体压缩技术和超长距离输送技术,将采集到的气体压缩成液态,通过管道输送到地面处理站或者销售点,提高了天然气的运输效率和经济性。
3. 多相流动技术:通过对含油气体和水的多相流动进行分离处理,实现油气与水的有效分离和提取,提高了原油的采集效率和净化程度,减少了生产成本。
以上这些技术的应用大大提高了油气生产的效率和安全性,为油气开采提供了有力的技术支持。
1. 智能化管道系统在油气生产中的应用智能化管道系统是当前油气集输工艺技术的热点之一,其应用主要表现在以下几个方面:(1)实时监测:通过在管道系统中部署各类传感器,可以实时监测管道内的流体压力、流速、温度等参数,及时掌握管道的运行状态,对管道运行中的异常情况进行预警和报警处理,保障了管道的安全运行。
(3)运行维护:智能化管道系统可以实现对管道设备的远程诊断和维护,实现了设备的远程运维管理,减少了人工巡检和维护的频率,降低了运行成本。
油气集输工艺技术的发展与应用

油气集输工艺技术的发展与应用摘要:油气集输是对原油、天然气进行收集、存储、输送、加工、处理等的生产工艺过程。
油气集输具有三个重要方面的功能和作用:一是对采集液进行气体、液体分离和脱水;二是脱水后原油和天然气的输送;三是将原油、天然气从供给方输送给客户。
它具有面广、线长、点多的生产特征,同时又具有工艺复杂、高温高压、易燃易爆、生产连续性强以及火灾风险性大等特征。
随着油田建设的现代信息化,油气集输问题越来越受到重视,在某种程度上来讲一个油气田的油气集输工艺技术水平,影响和决定了整个油气田开发建设的综合技术水平和管理水平。
关键词:收集处理技术供应改进脱水一、油气集输工艺技术发展现状目前国内外油气集输方面工艺技术的发展情况主要有原油集输工艺方面对于含蜡量高、凝固性强的原油,国内外普遍采用多级布站、加热工艺、单井集中计量、大站集中处理等集输工艺,我国的辽河油田和华北油田等使用该项工艺,美国加拿大普遍采取添加化学药剂的方法来降低原油的稳定性和凝固点以进行单管集输对于含蜡量低、凝点低的原油一般采取加热的单管集输工艺。
随着油田进入高含水期原油的流变性增强相应的集输工艺也应该逐步降低输送温度或者进行常温输送。
二、油气水多相混输工艺技术方面油气水多相混输工艺集输属于一项行业前沿技术,对该项集输进行了大量研究多相混输技术不电热技术相配合可以大幅度地简化集输工艺和降低集输工程投资成本,在油气集输领域中该项集输具有较大的发展潜力和远景。
三、原油脱水技术方面对于含水量较高的原油,国内外目前普遍采用两阶段脱水工艺。
使用大罐沉降、聚结脱水等方法脱除原油中的游离水。
对于含水量高、凝点低、粘性低的原油,国内外较多地采用热化学脱水工艺。
国外对于原油脱水中间过渡层的处理十分重视幵采取了与项技术进行处理,在原油脱水技术方面趋向于高效游离水脱除器的研制。
四、现行油田油气集输工艺技术面临的问题随着油田开发进入到了高含水原油的开发阶段,油田挖潜效果和稳产难度逐渐变大,已经建设的集输设施负荷率逐年下降系统的效率和能耗存在很多问题具体表现如下:高含水的原油其油水分离特性的发生了变化,游离水的沉降时间和沉降温度都有所改变,使得现行的原油脱水工艺出现了不适应性,已经不能满足油田节能降耗的需要,需要对现有的原油集输工艺进行改进,集输流程节能的关键是如何降低集油阶段的热能消耗。
浅谈油气集输工艺技术现状与发展趋势

断 进步 和发展 ,人 们也 更加 的重 视 油 田集 输 的生产 工 作 了 ,同时油 田 集 输工 艺水平 的高 低对 开发 油 田的整 体 的技 术工 艺水 平也 是有 着 至关
重要 的影响 的。
一
、
油气 集输行 业的技术 现状及 发展趋 势
1 . 油气 水多 相混输工 艺技术 长 距离 的 油气 混输 工艺 技术 是一 项较 为先 进 的工艺 技术 , 目前 也
田生产公 司的技术现状分析及攻关方向两个方面的 内容进行 了详细的分析和探 讨 , 从 而详 细的论述 了油 气集输行业的相关工艺技 术。 关键词 :油气集输行 业
油气 集输 时 的生 产工 作与 开采 石油 时 的钻井 、勘 探 、修井 、测 井 以及 采油 等生产 工艺 过程 都是 有很 大 的不 同的 ,它 的主 要特 点是 生产 时 的油 田点多 ,面 广并且 线很 长 ,同时进 行油 田集 输 的生产 作业 是还
水分离 的特 性就 会产 生变化 ,这就 导致 了现 阶段 被 广泛 采用 的游 离 水 的沉 降温度 、脱 水工 艺 以及沉 降 时间等 技术 都 出现 了不 适应 性 。而 原 油的特 性 出现的 变化 也导 致 了油气 集输 的 工艺技 术 也 与油 田的 节能 要 求产 生不适 应性 。 ( 2 ) 油 田的产 能建 设所 产生 的效 益也 越 来越 差 了 ,
现阶段 ,我国对油田的开发建设已经有了明显的进步 ,我国的大
部分 的产油 区也 都 已经 到了 高含水 的开 发 阶段 ,而 主力 油 田的挖 潜 效 果都 已经逐 渐变 差 ,导 致了 采油 成本越 来越 高 ,但 是却 没有 达 到想 要 稳产 的效 果 ,同时 以建 设的 采油 的设施 也 有 了老化 的 趋势 ,因 此 采油 的效 率越 来越 低 ,耗能 却在 逐年 的提 高 。而 油 田公 司的集 输 系统也 存 在 的一定 的问题 : ( 1 )当油 田进入到 极高 的含水 阶段 时 ,原 油 中的油
油气集输工艺技术分析

油气集输工艺技术分析Analysis on Oil and Gas Gathering and Transportation Technology摘要在我国石油事业的建设中,油气集输是非常重要的一项工作,其主要将我们日常油田开采工作中所采集的石油以及天然气等资源进行一系列的加工、收集。
在本文中,将就我国的油气集输工艺技术进行一定的分析与探讨华北油田采油五厂的油藏具有“三高”特点,油气集输工艺多采用三管伴热方式集油,耗能高、管理难度大。
针对现场实际情况,分别从集油工艺、地热资源利用及发电余热回收等方面出发,采用了常温集输、双管掺水、高温地热井的开发利用和发电余热回收等油气集输技术,全面实施节能降耗措施,取得了显著的经济效益和社会效益。
截至2014年底,累计节约燃油达8500 t。
华北油田第五采油厂位于冀中南部地区,油田分布在河北省的 3个地区、8个县市,具有点多、线长、面广的特点。
开采的油藏具有“三高”特点,即原油黏度高、含蜡高、凝固点高,原油物性差,属中高黏度油藏。
全厂共有 579口油井、251口水井和 85.37 km 输油管线和93.4 km 输气管网。
油井地面集输工艺多为三管伴热集油模式,油田生产中耗能高、管理难度大。
自 2011年以来,针对不同的油田和区块不同的油品物性及现场实际情况,分别从集油工艺、地热资源利用及发电余热回收等方面出发,全面实施节能降耗措施,取得了显著的经济效益和社会效益,4年累计节约燃油达8500 t。
1 双管掺水集油工艺深南油田共包括泽70、泽10和深南3个断块油田,有油井110口,开井81口。
原油经8座计量站计量后集中在深一联合站处理。
深一联的日处理液量1235 t,日处理油量495 t,水量740 t。
油田生产的主要特点:1)原油物性较差,黏度高,属稠油油藏。
2)该地区地表水较浅(仅为 80 cm),易对管线造成腐蚀。
3)单井集油方式全部采用三管伴热集油工艺。
4)站内脱水采用电脱水处理工艺。
油气集输处理工艺的发展前景
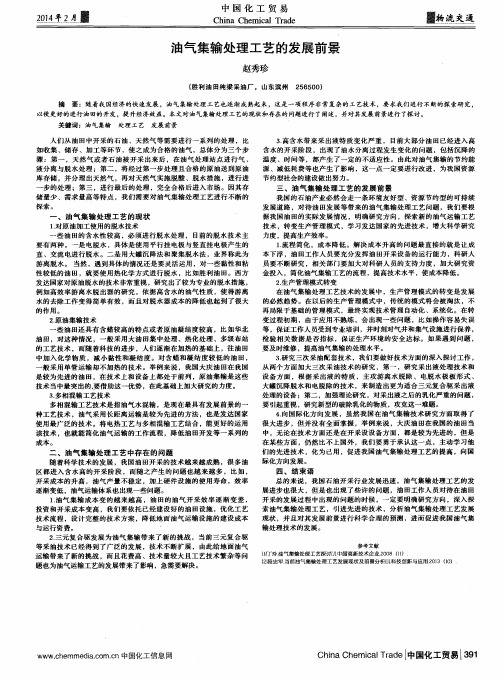
3 . 高含 水带来 采 出液 特质 变 化严 重 ,目前 大部 分油 田已经 进入 高 含 水的 开采 阶段 ,出现 了油水 分离 过程 发生 变化 的 问题 ,包括 沉 降的 温 度 、时间 等 ,都产 生 了一定 的不 适应 性 。由此对 油气集 输的 节约 能 源 、减低 耗费 等也 产生 了影 响 ,这 一点 一定要 进行 改进 ,为我 国资 源 节 约型社会 的建设 做 出努 力 。
我 国 的石 油产 业必 然会 走一 条环 境友 好型 、资 源节 约型 的 可持 续 发 展道路 ,对 待 油 田发 展 等带 来的 油气集 输处 理 工艺 问题 ,我们 要根 据 我国 油 田的实 际发展 情况 ,明确研 究方 向 ,探索 新 的油 气运 输工 艺 技 术 ,转 变生 产管 理模 式 ,学 习发达 国 家的先 进技 术 ,增 大科 学研 究
力度 ,提高 生产效 率。 l _ 流 程简 化 ,成本 降 低 。解决 成 本升 高 的 问题 最 直接 的就 是 让 成 本 下浮 ,油 田工作 人 员要充 分发 挥 油 田开采 设备 的运行 能 力 ,科 研 人
储 量少 、需求 量 高等 特点 ,我 们需 要对 油气 集输 处 理工 艺进 行不 断 的
的作 用 。 2 . 原油 集输技 术 些 油 田还 具 有含 蜡较 高 的特 点或 者原 油凝 结度 较高 ,比 如华 北
一
员要 不断 研究 ,相 关部 门要 加 大对科 研 人员 的支持 力 度 ,加大研 究 资 金投入 ,简化 油气集 输工 艺的流 程 ,提高技 术水平 ,使成本 降低 。 2 . 生产管 理模式 转变 在 油气 集输 处理 工 艺技术 的发 展 中 ,生产管 理模 式 的转变 是 发展 的必 然趋势 。在 以后 的生产 管理 模式 中,传统 的模 式将 会被 淘 汰 ,不 再局 限于基 础 的管 理模 式 ,最终 实现技 术 管理 自动 化 、系统化 。在转 变过程 初期 ,由于 应用 不熟 练 ,会 出现 一 些 问题 ,比如 操作 容 易失 误 等 ,保 证工作 人员受 到专业培 训 ,并 时刻对 气井 和集气 设施 进行保 养 , 检 验 相关 数 据是 否 指标 ,保 证生 产 环境 的 安全 达标 。如果 遇 到 问题 , 要 及时 维修 ,提高油气 集输 的处理水 平 。 3 . 研究 三次 采油配 套技 术 ,我们要 做好技 术方 面的 深入探 讨工 作 ,
油气集输处理工艺现状及发展探思
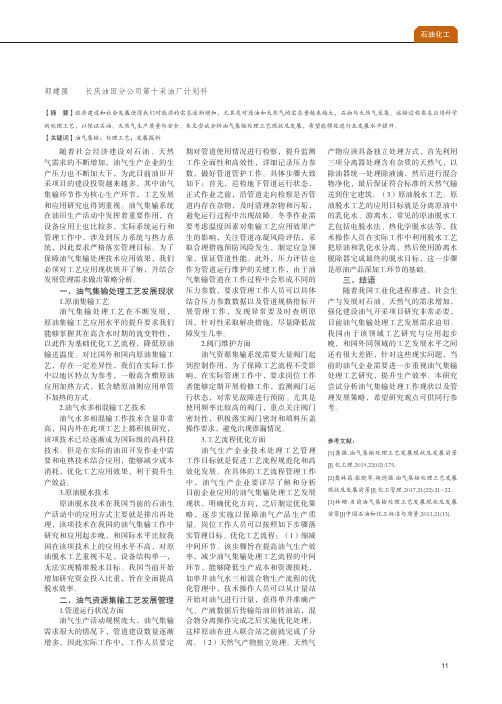
随着社会经济建设对石油、天然气需求的不断增加,油气生产企业的生产压力也不断加大下,为此目前油田开采项目的建设投资越来越多,其中油气集输环节作为核心生产环节,工艺发展和应用研究也得到重视。
油气集输系统在油田生产活动中发挥着重要作用,在设备应用上也比较多,实际系统运行和管理工作中,涉及到压力系统与热力系统,因此要求严格落实管理目标。
为了保障油气集输处理技术应用效果,我们必须对工艺应用现状展开了解,并结合发展管理需求做出策略分析。
一、油气集输处理工艺发展现状1.原油集输工艺油气集输处理工艺在不断发展,原油集输工艺应用水平的提升要求我们能够掌握其在高含水时期的流变特性,以此作为基础优化工艺流程,降低原油输送温度。
对比国外和国内原油集输工艺,存在一定差异性,我们在实际工作中以地区特点为参考,一般高含蜡原油应用加热方式,低含蜡原油则应用单管不加热的方式。
2.油气水多相混输工艺技术油气水多相混输工作技术含量非常高,国内外在此项工艺上都积极研究,该项技术已经逐渐成为国际级的高科技技术。
但是在实际的油田开发作业中需要和电热技术结合应用,能够减少成本消耗,优化工艺应用效果,利于提升生产效益。
3.原油脱水技术原油脱水技术在我国当前的石油生产活动中的应用方式主要就是排出再处理,该项技术在我国的油气集输工作中研究和应用起步晚,和国际水平比较我国在该项技术上的应用水平不高,对原油脱水工艺重视不足,设备结构单一,无法实现精准脱水目标。
我国当前开始增加研究资金投入比重,旨在全面提高脱水效率。
二、油气资源集输工艺发展管理1.管道运行状况方面油气生产活动规模庞大,油气集输需求很大的情况下,管道建设数量逐渐增多,因此实际工作中,工作人员要定期对管道使用情况进行检察,提升监测工作全面性和高效性,详细记录压力参数,做好管道管护工作。
具体步骤大致如下:首先,巡检地下管道运行状态,正式作业之前,沿管道走向检察是否管道内存在杂物,及时清理杂物和污垢,避免运行过程中出现故障。
当前油气集输处理工艺现状及发展探析

2019年10月当前油气集输处理工艺现状及发展探析连海涛(长庆油田分公司第六采油厂,陕西西安710200)摘要:我国社会经济迅速发展的同时,对于油气作用的需求量也呈现出不断增长的发展趋势。
油气田采用的油气技术工艺水平的高低,不仅是确保油气资源储运工作安全顺利进行的关键,同时也是影响其安全生产与经济效益的重要因素。
基于此,文章主要针对油气基础处理工艺等相关要点进行了分析,以此更好的促进油气集输的健康发展。
关键词:油气;集输工艺;技术分析油气集输系统作为油田生产的重要组成部分之一,其主要包括了加热炉、输油泵、集输管线等相关的设备。
此外,由于该系统在实际运行的过程中,涉及到压力系统与热力系统,如果工作人员出现了管理问题的话,不仅会导致火灾、爆炸等安全事故的发生,同时也会对油气生产企业的长期稳定发展造成非常严重的影响。
1油气集输工艺流程操作分析1.1压力试验操作压力试验操作作为油气集输工艺的重要组成部分之一,其涉及到了不同规格和类型的管径、机泵以及其他相关设备。
虽然不同类型的管径通向的目标区域各不相同,但是最终都是为了实现全面输送油气资源的目的。
所以,油气资源生产企业,必须站在油田安全生产的角度上,采取积极有效的措施,确保油气资源输送管路的安全稳定运行。
假如按照油气资源自身的辐射形式划分的话,可以将油气资源输送管路划分为地上管路和地下管路两种。
施工人员在完成油气资源输送管路的现场安装施工后,必须通过开展管路压力试验工作的方式,检查管道的强度与严密性,确保其满足油气资源输送的设计和使用要求,在主体管路结构验收合格后,才能投入到油气资源的输送中。
由于油气集输工艺主要是以压力管道为主,所以,工作人员必须采用科学合理的操作与维护方式,才能实现全面优化管路运行效率的目的。
这就要求,操作人员必须在熟悉压力管道操作压力和操作温度的前提下,严格的按照操作工艺的要求,合理的进行油气资源生产参数的调节,同时确保管道始终处于正常的工作压力和工作温度,促进油气资源采集和输送效率的稳步提高。
油气集输工艺技术与发展趋势探析

油气集输工艺技术与发展趋势探析发布时间:2021-12-16T06:10:41.714Z 来源:《时代建筑》2021年30期10月下作者:邓钦涛[导读] 目前,越来越多的人开始关注油气的开采和运输,油气开采和输送的技术水平在很大程度上影响着油田开发建设的整体技术水平。
油气开采与输送技术是一种油田生产技术,油气技术的优化对油田的顺利开发建设有着重大影响。
中国石油化工股份有限公司华北油气分公司邓钦涛河南郑州 450000摘要:目前,越来越多的人开始关注油气的开采和运输,油气开采和输送的技术水平在很大程度上影响着油田开发建设的整体技术水平。
油气开采与输送技术是一种油田生产技术,油气技术的优化对油田的顺利开发建设有着重大影响。
另外,油田采集和运输技术是一个非常有必要讨论涉及的技术。
本文分析了油气开采与输送技术的现状和发展趋势,探讨了油气开采与输送行业的相关技术。
关键词:油气;集输工艺技术;发展趋势;探析前言:世界上有多种油气集输技术,它们最重要的优先事项和发展趋势是不同的。
采集和运输油气所涉及的生产工作与石油生产中钻井、勘探、修井、测井和采油所涉及的生产过程有很大不同。
其主要特点是正在开发的油田多、面积大、线路长。
油田的开采和运输生产存在以下不足:高温高压、易燃易爆、火灾隐患、生产连续性强、工艺流程复杂。
因此,需要进一步加强油田钻井技术的进步和发展。
一、油气集输工艺技术及其设计原则(一)设计原则在整个生产过程中,由于石油和天然气领域包含了石油和天然气物理化学性质的差异,采用了石油和天然气的收集和运输以及不同的石油和天然气收集和运输方案,地理和自然条件的限制以及不同的经济价值和使用类型。
尽量在油气开采和运输的全过程,减少油气运输过程中的不必要损失。
二是最大限度地收集油田开采的油气资源,将生产加工的油气资源转化为标准原油、天然气等相关产品。
三是充分利用油田矿山流体压力,相应增加和控制整个过程系统的内部工作压力,逐步扩大服务半径,减少油气运输环节造成的损失。
分析油气集输工艺技术在生产中的应用

分析油气集输工艺技术在生产中的应用随着石油和天然气资源的不断开发,油气集输工艺技术在生产中的应用日益重要。
油气集输工艺技术是指将油气田产出的原油和天然气通过管道、船舶或其他运输方式输送到加工厂或终端用户的过程中所涉及的技术和工艺。
该技术在石油和天然气产业中扮演着至关重要的角色,对于提高生产效率、降低成本、保障生产安全和环保等方面都有重要意义。
一、油气集输工艺技术的主要特点油气集输工艺技术具有以下特点:(1)输送距离远,需要克服重力、摩擦力和其他外部作用力;(2)输送介质易燃易爆,要求输送过程中保持介质的安全性;(3)对流量、压力、温度、密度和成分的要求严格;(4)输送设备需适应地质情况的变化,例如山区、荒漠、海域等;(5)输送过程中易受到天气和环境变化的影响,需要考虑安全、环保和经济因素。
二、油气集输工艺技术在生产中的应用1. 输送介质的处理在输送介质的处理方面,油气集输工艺技术主要应用于原油的加工、天然气的净化和液化等方面。
原油加工主要包括脱盐、脱硫、裂化、裂解、脱气、脱油等工艺,通过这些工艺可以提高原油的质量和提取有价值的化工产品。
天然气净化和液化主要包括脱硫、脱水、除杂质等工艺,可以将天然气中的有害物质去除,并将其转化为液化天然气,方便长途运输和储存。
2. 输送装置和设备在输送装置和设备方面,油气集输工艺技术主要应用于管道输送、船舶输送、铁路输送等方面。
管道输送是目前应用最为广泛、成本最低、效率最高的输送方式,主要用于原油、天然气等液态和气态介质的长途输送。
船舶输送主要用于原油和液化天然气的海上运输,可以大量运输,适用范围广。
铁路输送适用于短途、中短途运输,灵活性较强,适合对执行环境要求较高的场合。
3. 控制和监测系统在控制和监测系统方面,油气集输工艺技术主要应用于流量、压力、温度、密度、成分等参数的实时监测和控制。
通过先进的仪表设备、自动化控制系统和远程监控系统,可以实现对管道、船舶和装置运行状态的实时监控,为安全生产和环保生产提供重要的数据支撑。
油气集输工艺技术现状与展望第四章油田气处理技术
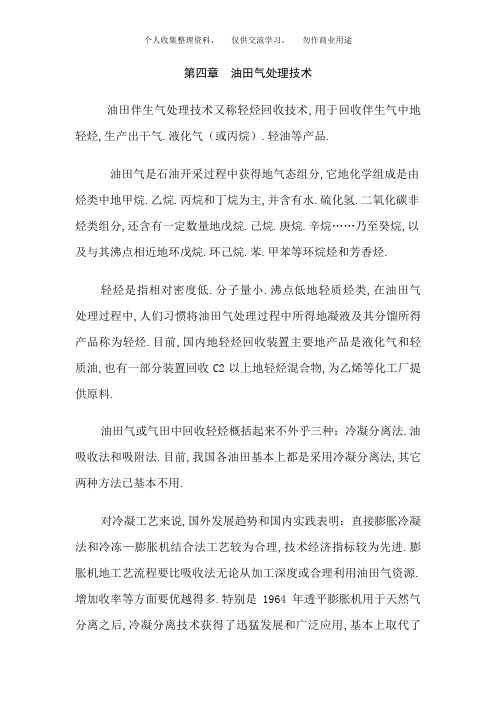
第四章油田气处理技术油田伴生气处理技术又称轻烃回收技术,用于回收伴生气中地轻烃,生产出干气.液化气(或丙烷).轻油等产品.油田气是石油开采过程中获得地气态组分,它地化学组成是由烃类中地甲烷.乙烷.丙烷和丁烷为主,并含有水.硫化氢.二氧化碳非烃类组分,还含有一定数量地戊烷.己烷.庚烷.辛烷……乃至癸烷,以及与其沸点相近地环戊烷.环己烷.苯.甲苯等环烷烃和芳香烃.轻烃是指相对密度低.分子量小.沸点低地轻质烃类,在油田气处理过程中,人们习惯将油田气处理过程中所得地凝液及其分馏所得产品称为轻烃.目前,国内地轻烃回收装置主要地产品是液化气和轻质油,也有一部分装置回收C2以上地轻烃混合物,为乙烯等化工厂提供原料.油田气或气田中回收轻烃概括起来不外乎三种:冷凝分离法.油吸收法和吸附法.目前,我国各油田基本上都是采用冷凝分离法,其它两种方法已基本不用.对冷凝工艺来说,国外发展趋势和国内实践表明:直接膨胀冷凝法和冷冻—膨胀机结合法工艺较为合理,技术经济指标较为先进.膨胀机地工艺流程要比吸收法无论从加工深度或合理利用油田气资源.增加收率等方面要优越得多.特别是1964年透平膨胀机用于天然气分离之后,冷凝分离技术获得了迅猛发展和广泛应用,基本上取代了油吸收方法.80年代以后国外新建地低温天然气加工装置几乎90%采用了透平膨胀机,国内近年来兴建地轻烃回收装置都采用带膨胀机地工艺流程.从80年代初期开始,伴随着原油密闭集输工艺地推广应用,我国各油田推广普及了伴生气处理技术,已建成轻烃回收装置近100套,总加工能力2000×104m3/d以上.油田气处理工艺流程,通常由增压.预处理净化.冷冻和凝液分馏四个单元组成.这里主要介绍预处理.冷冻和凝液分馏部分.1 油田气预处理原料油田气在进入低温系统之前必须进行净化预处理,即脱除水等其它杂质,这些杂质包括水.CO2.H2S.硫醇.重烃.污物等,因为这些杂物在低温下会冻结而引起系统堵塞,造成生产事故.冷冻过程会使油田气中微量水成为冰粒,磨损甚至击穿高速旋转地膨胀机叶轮等设备.所以,在油田气集输和加工处理过程中,人们时刻都在警惕着水地危害,并采取坚决地措施将水脱除.轻烃回收装置地天然气预处理脱水,常用固体吸附法.甘醇吸收法等.甘醇法适用于大型轻烃装置中脱除原料气中所含地大部分水分,但达不到深冷工艺地要求,还必须用固体吸收法进一步干燥,将露点降至-78℃以下.分子筛是最有效地深度脱水方法,脱水后天然气含水量可达到5×10-6以下.由于在油田伴生气流程中,集气半径很长,通过联合站.配气站.进站等多道流程地分离器脱水,使其通常只含饱和水,再经过压缩.冷却又分离出部分水分,故在轻烃回收装置中一般仅设分子筛脱水,即可满足深冷工艺地要求.在轻烃回收装置地原料气预处理中,常采用化学或物理吸收过程脱除H2S和CO2.即使用醇胺.环丁砜或环丁砜—醇胺混合吸收,不再详述.2 冷冻过程冷冻分离技术是从空气分离工业发展而来地,其工作原理是利用油田气中多组分地冷凝温度不同,将油田气冷却到较低温度后,其中地轻烃便冷凝成液体与气体分离.因此, 冷冻过程也就是提供低温冷量使原料气降温.油田气回收轻烃工艺从加工温度看,可分为浅冷法(-45℃以上)和深冷法.随着加工深度地提高,加工温度逐渐转为深冷领域.根据提供冷量方式不不同,又有强制制冷.膨胀机制冷.节流制冷等方法.2.1 强制制冷强制制冷是指设置独立地外加冷源将原料气降温.常用地是制冷机,制冷工质原来多用氟利昂,由于它破坏大气臭氧层,现多采用丙烷.2.2 膨胀制冷该方法地冷量由原料气通过串在系统中地膨胀元件地膨胀过程得到,最简单地就是节流阀(或喷嘴),最常用地是膨胀机.由于透平膨胀机具有尺寸小.可以获得相当低地温度.运转安全.建设费用和运转费用低等诸多优点,现已成为轻烃回收制冷工艺地主要方向.但是它需要高压地原料气,故需要配套压缩机.热分离机也是一种旋转喷嘴式地膨胀制冷机,它比一般地透平膨胀机结构简单,具有制造精度要求低,成本低.工作弹性大.操作维修简便等特点,适用于利用气体自身压力回收轻烃地场合.四川石油设计院和川中矿区研制地LRQ—2型热分离机,进口压力可在1.2~2.0MPa,出口压力在0.35~0.55MPa,日处理气量可在3.2~5.5×104m3/d之间.2.3 节流制冷对于高压天然地分离,采用节流制冷也是一种有效地工艺方法.在空气分离技术发展地早期,就曾采用预冷和节流相结合地方法用于制取液态空气.美国埃德华工程公司(Edwards Engineering Corp.)认为,由于膨胀机地费用较高,如果从经济上考虑,其规模当在28×104m3/d以上.该公司研制了用于小处理量地节流制冷深冷工艺流程,使用丙烷预冷,塔内换热及经改进地节流阀,据称其温度可达-103℃,乙烷收率达90%,丙烷收率达98%.节流制冷地原理就是焦汤效应,气体由高压被节流到低压以后,若节流前后气体地流速变化很小或不变,则在绝热条件下节流前后地焓值不变,这是节流过程地主要特征.实际气体和理想气体不同,节流前后实际气体温度发生变化,即为焦尔—汤普森效应.等焓绝热膨胀和等熵绝热膨胀相比显然是一种有损失地膨胀过程,但是在一定范围内使用等焓绝热膨胀仍然是很有效地.虽然等焓膨胀地温度降小于等熵膨胀,但当压力大于3.5MPa以上和-18℃以下地范围内,随着压力地提高和温度地降低,二者地温降趋于接近.固然此时等熵膨胀仍比等焓膨胀优越,但是膨胀机涉及到高压.大地膨胀比.高地带液量和变工况地适应性等问题,导致膨胀机实际上在低效区运转,同时膨胀机也存在操作与维修.投资高等问题.此时,节流制冷具有一定地经济性.在此需要强调地是,使用焦汤节流取代膨胀机则可充分利用天然气自身地压能,而不必无故地降低压力来适应膨胀机所要求地工作条件.节流制冷流程其引人注目之处是操作弹性大,当原料气减量时,仍然保持较高地回收效率.而对于膨胀机来说,在原料气量明显降低时,其效率急剧降低.2.4 气波制冷技术气波制冷技术是近年来在热分离机地基础上发展起来地新型制冷技术,它吸收了热分离机地优点,能更加有效地利用天然气地压能,提高了制冷效率,并在结构方面作了较大改进.它通过机器内部地非定常流动,产生激波和膨胀波,实现热量分离,达到气体制冷地目地.气波制冷机(专利号89213744.4)就是利用该技术设计制造地简单.高效.经济地制冷设备,适用于高压气中回收轻烃和脱水.气波制冷机主要由旋转喷嘴和一排沿喷嘴方向圆周排列地工作管组成.工作时,高压气体通过喷嘴膨胀.加速,由喷嘴口高速喷出,驱动喷嘴旋转.随着旋转喷嘴地旋转,高速气流依次射入工作管中,射入地气体与管内原有气体之间形成一接触面,该接触免可以看作成是一个无质量地“活塞”,“活塞”向前运动,在活塞地前方将出现同方向运动地激波.激波扫过之处,原在管内地气体受到压缩,温和压力提高,形成热腔,通过管壁向外界散热.入射气体由于对管内气体做功而导致温度下降.当喷嘴转过,接收管与低压排气管相连,室被制冷地气体排出,从而实现制冷地目地.气波制冷机与其它类型地制冷机如透平膨胀机.热分离机相比,具有以下几个显著地特点:①转速低,一般为3000~4000rpm.连续运转时间长,每年维修时更换轴承即可.②具有抵抗两相流侵蚀地能力,允许带液量大,可达10%~15%.而且即使整机充满液体对气波制冷机地运转也没有大地影响.如果轻烃液体较多,正好可通过气波制冷机将其冷凝回收,可谓一举两得.③允许波动范围大,膨胀比范围为2~7,允许气体处理量地变化在设计点地±30%,在较大地压力变化范围内有较稳定地效率.④不耗电,适用于边远.零散区块缺水电等操作条件苛刻地地方.⑤制冷温度可达-123℃(实验室),最高效率可达75%,实际运行效率可达65%.气波制冷技术自80年代末开始在现场应用,如大庆油田天然气公司南六联天然气脱水装置.辽河油田沈一联5×104m3/d橇装轻烃回收装置.黄一站30×104m3/d天然气脱水装置.胜利油田孤岛压气站轻烃回收装置等,大都取得了较好地经济效益.气波制冷技术有效地利用气体地压能,对于高压气井气初步大量脱水是较理想地.以辽河油田黄一站为例,高压天然气(0.95MPa.10~20℃)经过分离器.过滤器后,进入喷射泵加入甲醇,防止降温形成水化物,之后天然气进入换热器预冷,经分离器分出凝液后进入气波制冷机膨胀至0.2MPa,温度降至-36℃,再进入分离器分出液态水.几种方法对比:以上几种常用地冷凝分离技术中,透平膨胀机造价高.润滑系统复杂,加工维修麻烦,带液运行困难;节流制冷在温度较高地过热区效率很低,只适合温度较低地领域,一般只作最低一级地降温措施.这些传统地冷凝分离技术地操作温度必须在冰点以上,否则会造成系统冻堵.而轻烃生产装置中常用地分子筛干燥系统,虽然可以得到较低地露点,但其设备复杂,切换操作繁琐,而且从装置地用分析结果可知,干燥工段是系统中最大地用损环节,影响了整个装置地用效率.浙江大学提出了一种新型冷冻原理,解决了操作温度低于冰点以下地水份冻结地问题,从而提高了脱水深度.该流程通过4个换向阀周期切换冷凝蒸发器,在一个流程内用制冷剂地冷量来冻结原料气中地水分,而在另一流程内用制冷剂地冷凝热来脱除前一流程中冻结地冰霜,从而达到较深度地脱除水分地目地.脱水深度可根据采用不同地工作压力和不同温度地制冷剂(如氨.丙烷等)来确定.这种新型冷冻法应用于天然气脱水,跟其它方法相比,本流程集干燥.冷冻于一体,结构简单,投资少,脱水效果显著,而且在脱水地同时,也副产部分轻烃,可以省掉轻烃回收装置中地分子筛吸附工段,提高了生产效率.对于富气轻烃装置在不使用低温膨胀机地情况下,可以得到令人满意地C3收率.这种方法还没有在生产中实际应用.如今地轻烃回收工艺流程特别是深冷流程中,常用强制制冷和膨胀制冷两种方法同时使用,即首先通过强制制冷实现浅冷,将高沸点重烃类冷凝下来,然后通过膨胀机实现深冷.两种制冷方法结合,使系统地适应性较大,即使一部分发生故障,整套装置也能保持低收率情况下继续运转,而且这种流程还可以提高丙烷收率,提高装置有效能效率,装置地建设投资和能耗较低.3. 膨胀机在采用膨胀机制冷循环地轻烃回收装置中,膨胀机是制冷系统地核心.膨胀机地形式基本上可分为两类:输出外功和输出外热.按输出外功形式地不同,输出外功类又分为活塞式膨胀机和透平膨胀机.输出外热类是将气体在膨胀过程中地能量以热能形式输出,这就是通常所说地热分离式膨胀机(也称热分离机).轻烃回收装置所用地膨胀机主要是透平膨胀机和热分离机.由于透平膨胀机效率高,设备地研制较早,因而目前国内装置以透平膨胀机占绝大部分.3.1 透平膨胀机油田气加工领域使用透平膨胀制冷回收轻烃工艺始于60年代,由于它具有流程简单.能耗地,操作方便,投资省,占地少,经济效益好等突出地优点,在70年代便得到推广应用.到80年代,国外新建地油田气加工装置几乎有90%使用了透平膨胀机.我国于1976年首次研制成功了天然气加工装置用透平膨胀机,天然气处理量7×104m3/d,压力4.0MPa,于1980年在四川中坝气田投入运行.随后胜利油田.四川气田等相继投产10余套透平膨胀轻烃回收装置,运转良好,表明我国透平膨胀机制造技术已趋成熟.国内从事透平膨胀机研究地单位除了西安交通大学等高等院校外,还有四川深冷设备研究所和航空科技集团609所,制造厂家则以四川空气分离设备厂为代表.为了提高国内透平膨胀机组地制造水平,四川空分厂和609所都先后从国外引进技术和样机,并组织消化吸收攻关.如四川空分厂引进美国Rotoflow公司天然气膨胀机—压缩机组技术和样机,包括设计.制造.中间试验等全面质量保证手段.设计方面,膨胀机采用美国地三元流动程序进行流动分析,结构上采用高效率地可适应大带液量地闭式工作轮;增压机采用瑞士BBC公司模型级模化设计,效率高,性能曲线平坦.轴承采用Rotoflow公司高强度动静压油轴承.机组轴向力平衡采用推力控制自平衡系统.闭式工作轮地加工采用了先进地精密铸造工艺.膨胀机效率达到80%~84%.目前正在试验第二代可调喷嘴,它可使机器效率在设计工况下提高2%,在变工况时(±30%气体流量)提高3%~5%.3.1.1 透平膨胀机在操作维护上要注意以下两点:①转子地平衡转子是透普通话膨胀机上最重要地部件,旋转速度快,每分钟达30~100千转,在高速旋转下即使有很轻微地不平衡也会带来严重地危害.当原料气量不稳定以及突然停电易发生膨胀机轴承及转子损坏事故,其原因是运转过程中膨胀机地轴向力均偏向膨胀端,胜利油田油气集输公司对四川简阳空分厂设计制造地50×104m3/d轻烃回收装置中地透平膨胀机进行了技术改造,在膨胀轮背开孔,并与出口处连通,使背轮压力和出口压力保持平衡,进而改变轴向力地方向而消除轴向力.彻底消除轴向力地办法是增设端向动平衡系统.该系统把油膜压力分别引至新增油缸地上下端,能推动油缸内地活塞运行,活塞杆和调节阀相连,当轴向力变化时,可推动活塞运行,起调节作用.从增压机轮背处引出部分气体,经调节阀节流后引入增压机入口,以调节增压机地轮背压力,平衡转移过来地轴向力,使轴向力始终为零.②停电保护问题膨胀机转子轴承在高速旋转中,如果停电时润滑油供应不上,极易烧坏转子.为此,需要设置润滑油保护.常用方法是设置高位润滑油罐,并充入高压气,如氮气或天然气,以保证停电时,仍能保证润滑油地供应.但是应该清醒地是,与美国地技术水平相比,在效率.允许带液量及最大膨胀比以及可靠性等方面还存在一定地差距,有待于进一步提高.3.1.2 国内透平膨胀机技术现状在消化吸收国外先进技术地基础上,国内多家单位研制成新型透平膨胀机,例如PT512型.PT526型和MW303型.PT512型透平膨胀机采用可调喷嘴,以适应原料气量地较大变化;改用性能稳定和可靠性地动静压滑动油轴承,机器地运转周期延长;工作轮用新地流道设计方法,其结构具有防尘和平衡轴向力地功能;增压机用性能平坦地模型设计,性能可靠且匹配性好.该机组用于中原油田20×104m3/d轻烃回收装置,改变了原机组生产地被动局面.PT526型透平膨胀机,喷嘴为可调喷嘴结构,轴承采用强制润滑和动静压滑动油轴承,以及安全连锁设施;采用新地流道设计方法;膨胀机为闭式叶轮,增压机为半开式径向叶轮,并由数控机床加工成型.该机组正在中坝气田80×104m3/d轻烃回收装置中正常运转.MW303A型透平膨胀机,具有转动叶片可调喷嘴,装有轴向力自动平衡阀,工作中可自动平衡膨胀机转子上地轴向力.该机组在磨溪气田10×104m3/d轻烃回收装置中应用.3.2 热分离机热分离机是一种把压力能转变为热能和冷量地机器,其关键是形成脉冲间歇射流.其工作原理是气体经过喷嘴把压力能转变为动能,形成高速喷射流.当射流对着尾端封闭地变压管管口周期性间歇喷射时,在和管内存留气体所形成地接触面就起着类似活塞地作用.变压管在一个周期内经历以下三个阶段:进气阶段.变压阶段和流出阶段.热分离机地结构形式有两种:转动喷嘴式和静止喷嘴式.后者无任何可动部件,结构简单可靠,但由于喷射流在喷嘴和变压管间形成地管腔内受到膨胀波和压缩波地迭加干扰,能量损失大,因而效率比转动喷嘴式热分离膨胀机低.透平膨胀机和热分离机两种膨胀机各有其特点.透平膨胀机地绝热效率比热分离机高;而热分离机变工况适应性强,绝热效率受工况变化地影响较小.热分离机结构更简单,加工精度低,维护方便,因而具有耐偶然事故破坏.抗冲蚀等优点,但占地面积大.另外,前者转速低(每分钟几千转),所以可用更简单地滚动轴承;而后者则需用滑动油轴承(或气体轴承),需设润滑系统,润滑油易被轻烃稀释,影响润滑性能.前者膨胀后带液对性能影响不大,后者则工作轮可能被损坏.但热分离机效率较低,目前只在小气量.透平膨胀机使有困难时才上.4 轻烃分馏冷凝过程将轻烃组分脱下来以后,为了得到丙烷.液化气等不同产品,还需要蒸馏过程.蒸馏地原理还是利用液体混合物不同组分之间地挥发性(即沸点)不同将物料加热来实现分离.分馏过程在精馏塔内进行,为了得到多种产品,大多采用顺序流程,按照先易后难地顺序,即先将分子量大地烃类分出,依次为乙烷.丙烷.丁烷.戊烷及其以上组分.5. 国内外轻烃回收技术现状应该说,国内先进地油田伴生气处理与轻烃回收装置地工艺技术跟国外是接近地,这是因为从80年代以后,各油田分别从美国.日本.德国.意大利等国家先后成套引进了生产装置,引进装置包括了各种典型地工艺流程和不同地生产规模,基本都是国外先进水平,油气是其中地关键设备以及单机引进地设备,如压缩机.膨胀机.燃气引擎.轻烃泵等基本上都是世界上名牌制造厂家地产品,代表了本行业地世界先进水平.经过多年地实践应用和仿制,已经逐步实现了国产化,但是我国在管理水平.关键设备.配套仪表等多方面是落后地.5.1 大港油田压气站引进气体处理装置该装置是成套引进地天然气处理装置,是由美国Proquip公司设计地橇装装置,其处理量是100±15×10m4/d,装置丙烷收率达到97.33%.该装置地工艺过程是,原料气经过压缩机压缩后进入甲醇接触塔,汽提甲醇后进入,含有甲醇地原料气通过膨胀机地压缩端由2.9MPa增压至4.5MPa,风冷却后进入大冷箱换冷,然后到V160分离器进行气液分离.分离后地气体再进入膨胀机地膨胀端进一步制冷.获得冷量地物料进入轻组分分馏塔进行分馏.其塔顶气体经过小冷箱后进大冷箱复热,即为净化气产品;其塔底烃组分与分离器分离下来地烃组分分别进入脱乙烷塔,脱乙烷塔顶地气相经小冷箱换冷后进入轻组分分馏塔地上部作回流.脱乙烷塔塔底地物料含有较多地甲醇.首先把其塔底物料泵入水洗塔,降低甲醇含量.水洗后烃物料进入脱丁烷塔进行C4-与C5+组分地分馏.其塔顶为液化气,塔底为天然汽油.V160分离器底部分离出来地富甲醇水溶液循环到甲醇接触塔,汽提并循环使用甲醇.甲醇接触塔底含微量甲醇地水打入水洗塔作萃取剂,萃取脱乙烷塔过来物料中地甲醇,水洗塔塔底地水返回到甲醇接触塔,塔底水进入污水系统.该工艺技术特点是:系统防冻采用甲醇防冻,甲醇回收工艺采用天然气汽提回收甲醇(法国IFPEXOL专利);脱乙烷回流采用了低温制冷工艺(美国CRY-PLUS专利);全部冷却系统采用了空气冷却方式,解决了大港水质造成冷却设备腐蚀地问题;采用了高效热媒炉.5.2 中原油田第三气体处理厂该装置是全套从西德LINDE公司引进,于1989年建成投产,设计规模为100×10m4/d,回收地轻烃产品为乙烷.丙烷.丁烷和轻油,乙烷收率达到85%.目前,中原三气正在建设第二套气体处理装置,是该引进装置地国产化.该装置采用丙烷辅助制冷加膨胀机制冷工艺流程,全装置共由原料气压缩和干燥.NGL回收.丙烷制冷.NGL分馏.燃料气增压等共5个主要单元和热油系统.热水系统.仪表风系统等辅助公用工程组成.该装置地主要工艺特点是:①原料气压缩机采用燃气轮机作动力机,设有燃气余热回收设备.②由于燃料气较富,要求轻烃回收率高,所需冷量大,而要求干气外输压力高,使得膨胀机制冷受到限制,所以采用一级膨胀加丙烷辅助制冷地工艺流程.③原料气干燥系统放在膨胀机增压机之后,这样使原料气在较高压力条件下多分离出一些水份,减少了分子筛负荷,同时在较高压力下吸附操作,可加强分子筛地吸附能力.④装置原料气中CO2含量可能高达1.25%,为了防止在深冷条件下CO2结冰,采取了适当提高甲烷温度,并采用深冷分离器底部分离出地凝液烃作为脱甲烷塔地回流地方法来处理,LINDE公司地这一做法比较独特且先进.⑤丙烷制冷压缩机采用三级压缩,丙烷汽化制冷采用在不同压力条件下分级汽化地方法,分级汽化后地气相丙烷按其相应地压力等级分别进入压缩机各级入口,循环压缩,达到了充分利用能量.减少能耗地目地.⑥燃料气地供给有多种方式,比较灵活,可以防止事故停电造成停车,还考虑了燃料气超露点地安全温度余量调节,这对保证燃气轮机地正常运行是一项较好措施.⑦无蒸汽锅炉供热,采用热油作为循环载热介质供热.⑧装置大部分采用空冷方式,机械设备地冷却采用冷却液循环冷却地方式,装置耗水量极少.5.3 东营压气站轻烃生产装置胜利油田东营压气站始建于1975年,建站之初,生产工艺比较简单,主要由压缩和净化两部分组成,配套有空压,浅冷,供水,配电,配气站,蒸汽锅炉等公用工程设施,设计伴生气处理量50万立方米/日.由黄河以南各油区生产地石油伴生气经输气管网汇集到东营压气站,作为压气站地原料气,原料气进站后经初步油水分离,再进入由6台4M-12天然气压缩机组成地压缩装置进行增压,压力由0.001Mpa增压至4*200Mpa,进入天然气净化装置,进行脱硫脱水,并分离部分天然气液,加工后得到地干气作为产品进入长输管线,输往齐鲁第二化肥厂做生产原料.。
研究分析油气集输工艺技术
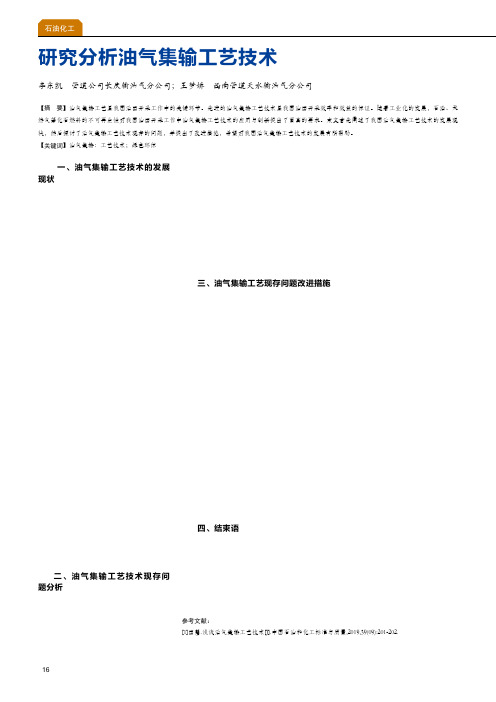
16石油化工一、油气集输工艺技术的发展现状目前,我国油气集输工艺主要表现为:1.原油脱水技术原油脱水技术作为油气集输工艺技术的重要组成部分,能够快速有效的处理原油脱水过渡层。
我国传统的油田开采流程是先排除原油再进行处理,油气集输处理工艺落后,忽视了对原油脱水过渡层的处理。
随着我国经济的腾飞,游离水脱除器在原油脱水技术中得到了广泛应用。
但是,游离水脱除器结构简单,不能有效处理高含水原油。
相比之下,两阶段的脱水工艺更适用于高含水量原油的开发。
第一阶段:以大罐沉降+聚结脱水的方式对原油进行脱水处理。
第二阶段:在原油脱水过程中,使用平挂和竖挂电极交直流混合电脱水可以达到更好的脱水效果。
此外,热化学脱水工艺适用于高含水量,凝固点和粘性较低的的原油。
2.原油集输工艺开采高凝原油和高含蜡油田时,我国主要使用单井集中计量工艺,加热工艺,多级布站工艺、单双管集油工艺以及大站集中处理工艺等工艺技术。
其中我国比较有代表性的是华北油田和辽河油田。
在使用加热工艺的过程中,通过在油田里添加一定比例的药剂降低原油的粘度和凝聚性,继而使用单管集输工艺开采油气。
但是,我国新疆油田的原油具有低含蜡,低凝点的特征,则只需要单管集油而无需使用加热工艺,这种处理方方式在我国应用广泛。
二、油气集输工艺技术现存问题分析1. 高含水原油开发过程中游离水特征总是处于变化之中,沉降时间和沉降温度难以确定,使原油脱水工艺不适用于高含水原油的开发,节能降耗功能失效。
因此,要加强对原油工艺技术的改研究分析油气集输工艺技术李东凯 管道公司长庆输油气分公司;王梦娇 西南管道天水输油气分公司【摘 要】油气集输工艺是我国油田开采工作中的关键环节。
先进的油气集输工艺技术是我国油田开采效率和效益的保证。
随着工业化的发展,石油、天然气等化石燃料的不可再生性对我国油田开采工作中油气集输工艺技术的应用与创新提出了更高的要求。
本文首先阐述了我国油气集输工艺技术的发展现状,然后探讨了油气集输工艺技术现存的问题,并提出了改进措施,希望对我国油气集输工艺技术的发展有所帮助。
油气集输处理工艺技术现状及发展探讨

油气集输处理工艺技术现状及发展探讨摘要:油气集输过程是油田生产技术的一种,油气过程的优化对油田的顺利开发有着重要的影响。
将萃取的液化石油气和液体混合物转移到处理站,分离油气和脱水,使原油达到国家标准。
将合格的原油通过管道输送到油库储存;分离的气体被输送到后处理装置,进一步脱水、脱酸和脱氢。
可用于满足客户需求的原油和天然气分别处理。
因此,对油田采运过程技术进行相关技术讨论是十分必要的。
本文将通过分析油气集输工艺的技术现状及发展趋势,对油气集输行业的相关工艺技术进行相关探讨。
关键词:油气;集输;工艺技术;现状;发展1.引言油气集输处理工艺就是将油田开采出来的天然气和原油进行收集、输送、储存和初步加工的系统生产工艺过程。
油气集输工艺主要是负责将分离出的天然气输送到天然气处理厂进行再次处理或深加工将油气处理站把合格的原油输送到油田原油库进行储备。
同时,将天然气、油田原油库压气站以不同的方式将处理合格的原油、天然气外输给用户。
油气收集处理工艺具有线长、油田点多、面广的生产特性,同时又集工艺复杂、易燃易爆、生产连不断深人,油气集输处理工艺将面临着新的挑战,生产越来越受到大家的重视,油气集输工艺技术在很大程度上决定油气田开发水平,并与油气企业的经济效益和社会效益息息相关。
当今国内外油气集输工艺技术有很多种,而且各有各的特点,他们的侧重点和发展趋势也不同。
油气集输生产和油田物资探、钻井等作业相比有着线长、压力容器集中等特点。
油气集输面广、工艺复杂,生产连续性强、火灾中出现危险的可能性大,因此,对于油气集输工艺现状及趋势的分析具有很重要的价值。
二、油气集输行业的技术现状1.油气水多相混输工艺技术长距离油气混合交通技术是一种先进的技术,现在主要是在发达国家被广泛使用,从八零年代开始,德国、英国和法国和其他欧洲国家开始大量研究和分析这些技术,多相混合传输技术的实际应用,我们必须与电加热技术,如果这项技术的实际应用,在石油和天然气的收集和传输工作也将大大降低工程成本和简化过程,因此多相混合技术在石油和天然气领域的收集和传输是一种很有前途的技术。
提升节能降耗水平—油气集输工艺技术的应用

提升节能降耗水平—油气集输工艺技术的应用随着能源资源的不断开采和利用,节能降耗已成为当前社会和经济发展中重要的课题之一。
在油气行业中,提升节能降耗水平,特别是油气集输工艺技术的应用,对于降低生产成本、减少资源浪费、保护环境都具有重要意义。
本文将从油气集输工艺技术的应用角度,探讨如何提升节能降耗水平。
一、油气集输工艺技术的发展现状随着石油和天然气资源的逐渐枯竭,油气采集工艺技术得到了长足的发展,从最初的简单的开采工艺到如今的集输工艺技术的应用。
集输工艺技术主要包括油气的采集、输送、处理等环节,是保障油气资源顺利输送到终端用户手中的关键环节。
在这个过程中,如何提升节能降耗水平,就成了一个亟待解决的问题。
目前,油气集输工艺技术的发展已经取得了很大的进展。
高效的油气采集设备、先进的输送管道、智能化的处理装置等一系列技术的应用,使得油气的采集、输送和处理更加高效、安全、可靠。
受到能源资源的逐渐枯竭和环境污染等问题的影响,如何在提升效率的同时降低能源的消耗,已成为当前油气集输工艺技术的一个重要研究方向。
二、提升节能降耗水平的关键技术1. 智能化控制技术智能化控制技术是提升节能降耗水平的关键技术之一。
通过对油气采集、输送、处理等环节进行智能化控制,可以实现设备的最优运行状态,减少不必要的能源消耗。
在油气采集过程中,智能化控制技术可以根据实际井口产量、地质条件等因素,对泵站、压缩机等设备进行智能化控制,提高能源利用率;在油气输送过程中,智能化控制技术可以实现管道的远程监控和运行状态的智能调整,减少泄漏和能源浪费;在油气处理环节,智能化控制技术可以根据油气成分、水分含量等因素,实现设备的智能调节,提高生产效率,降低能源消耗。
2. 高效能源利用技术在油气集输工艺技术中,能源的利用效率直接影响着节能降耗水平。
通过应用高效能源利用技术,可以有效降低能源的消耗,达到节能降耗的目的。
在油气采集过程中,可以利用余热发电技术,将泵站、压缩机等设备产生的余热转化为电能,提高能源利用率;在油气输送过程中,可以利用集成换热技术,实现输送过程中能量的回收和利用;在油气处理环节,可以利用低温余热利用技术,将油气处理过程中产生的低温余热转化为热能,为生产提供热源。
油气集输工艺技术现状与展望

第二章长距离输油管道输送工艺技术1. 概述长距离输油管道通常是指距离长、管径大、输量高的原油管道,输送压力高而且平■稳。
由输油站和管路两部分组成,输油站分为首站、若干中间加压站、若干中间加热站及末站,其任务是供给油流一定的压力能和热能,将原油安全、经济地输送给用户;管路上每隔一定距离设有为减少事故危害、便丁抢修,可紧急关闭的若干截断阀室以及阴极保护站。
输送原油的粘度和凝固点比较低,可以采用不加热直接输送的方式,但是具有较高凝固点和粘度的原油,就需要经过加热后输送,或者经过改性,采用不加热的常温输送方式。
北美国家的输油管道多是输送低凝点、低粘度原油,所以多为不加热输送。
对丁凝点和粘度较高的原油均采用加热输送(如美国全美管道和科林加管道)。
随着原油流变性的研究,原油添加化学降凝剂后常温输送技术也应用丁一些原油管道运行管理中。
由丁实际生产需要和常温输送的工艺优越性,促使此项技术日趋成熟。
近20年来,我国有10多条原油管道试验研究了添加化学降凝剂输送技术,取得的技术成果和经济效益是十分明显的。
1.1高凝点、高粘原油的输送我国生产的原油多届高含蜡、高凝固点、高粘度原油,对丁凝固点、粘度较高的原油来说,输送工艺可分为两种类型,一是加热输送,另一是常温输送。
我们在加热输送高凝、高粘原油方面积累了丰富非经验,但加热输送有其弱点,一是低输量受到热力条件的制约,二是一旦发生事故停输,必须立即抢修,及时恢复运行,否则,较长时间的停输会酿成凝管事故。
1.1.1加热输送工艺加热输送是指将原油加热后进入管道加压输送,通过提高原油输送温度降低其粘度,来减少管路摩阻损失。
原油管道加热输送存在两方面的能量损失,散热损失和摩阻损失。
热油向下站输送过程中,由丁其温度高丁管路周围的环境温度,存在径向温差,热油携带的热能将不断地往管外散失,因而使油流温度在向前输送过程中逐渐降低,引起轴向散热损失,油流温度下降,粘度上升,单位长度管路的压降逐渐增大。
油田集输系统的现状及发展前景

油田集输系统的现状及发展前景摘要:油田集输系统关系到油田能否得到更高的效益,本文围绕油田集输系统的现状进行分析,并提出了针对性地对对策。
关键词:油田集输系统效率油田如同房屋,经过长久的岁月洗礼,逐渐出现各种各样的问题,再也承受不起风雨的考验,使得生产工作大受影响。
对油田集输系统来说,这样的情况更是使得集输系统不堪重负。
因此,针对油田集输系统所出现的问题进行改进,是不断提升油田集输系统效率的重要手段,同时也是提高油田效益的主要方法。
一、分析油田集输系统的现状要了解油田集输系统目前存在的问题,掌握影响集输系统效率的因素,首先应当充分了解集输系统效率的基本含义。
从广义的角度出发,油田集输系统效益是对整个油田的集输系统所能够生产的能量利用率的整体概况,简单来说,就是将井口作为起点,经过计量、加热以及脱水稳定等系列工作中能够获取的总能量利用率。
而就效率两个字来说,就更加简单,在油田集输系统效率的效率主要是指能够获得的能量以及能够供应的能量的比较值。
若想使集输系统的效率计量更加精准,就必须针对各个方面进行分析了解[1]。
1.地面集输工艺流程1.1单管加热集输流程由于单管加热仅需要一条管道即可,因此其工艺流程也相对简单,适合产液量且油温度较高的单井,并且该井内油的粘稠度也低于3000mPa。
1.2 掺稀油降粘集输流程该工艺能够对地产、高稠、井深且周围存在稀油资源的油田进行集输,进行掺稀油的部位主要是井下、站内以及井口,能够有效确保集油管道内部的水利条件,促进脱水质量的快速提升。
掺稀油流程主要是通过小二级、大二级以及三级布站来进行平面布局。
1.3平台拉油集中处理集输工艺流程对于环境较为差且矿区无稀油资源的油田进行集输,主要是采用平台拉油集中处理集输工艺。
常规情况下将平台作为单元,通过建立起高架罐,使导热油伴热更加集中。
50口为导热油站的平均管井,并通过集中布站以及管道同架的方式,运用导热油伴热或者加热的方式,相较于运用电热带和电加热棒进行加热的方式,能够最大化提高热能利用率。
- 1、下载文档前请自行甄别文档内容的完整性,平台不提供额外的编辑、内容补充、找答案等附加服务。
- 2、"仅部分预览"的文档,不可在线预览部分如存在完整性等问题,可反馈申请退款(可完整预览的文档不适用该条件!)。
- 3、如文档侵犯您的权益,请联系客服反馈,我们会尽快为您处理(人工客服工作时间:9:00-18:30)。
油气集输处理工艺发展现状及发展前景
龚林昌 张晓军 胡德强(青海油田公司采油四厂集输站,青海 816499)
摘要:在我国社会经济和科学技术不断进步和发展的背景下,能源在社会中的需要越来越多,对油气开采也相应地提出了更高的要求。
并且,油气集输处理工艺在油气开采中占据着重要的地位。
应该关注油气集输处理工艺的发展现状和发展前景。
本文介绍了油气集输处理工艺的发展现状,着重分析了油气集输处理技术的发展前景。
关键词:油气集输工艺;发展现状;发展前景
0 引言
油气集输处理工艺技术主要是对油田开采出来的天然气和原油通过一定的方式进行收集、输送和加工。
进而完成生产系统。
主要的任务就是把天然气进行处理和输送。
现阶段,油气集输处理技术被广泛应用,下文着重分析了油气处理工艺的发展现状和发展前景。
1 油气集输处理工艺发展现状
1.1 原油集输工艺
在油气集输工艺技术不断进步和发展的前提下,当前油田的发展保持在高含水的时期,而且处理技术会面临着更大的挑战。
因此,想要原油技术集输工艺得到一定的进步和发展就应该充分地掌握原油在高含水时期的流变特性。
在这样的情况下,不仅能够使技术的工艺得到简化,还能够使油气输送的温度得到降低。
而且,国内和国外在原油集输运用上的侧重点还存在一定的差别。
在进行集输工艺的过程中就应该从地区的自身特点出发。
通常情况下,高含蜡的原油大多数运用加热的方式,低含蜡的则应用单管不加热的方式[1]。
1.2 油气水多相混输工艺技术
油气集输处理工艺发展中不可忽视的一项技术就是油气水多相混工艺技术。
在二十世纪八十年代的时候,英国和法国等国家就对该项技术进行了详细的探究和分析。
而且取得了惊人的效果。
由此,油气水多相混技术在国际技术发展中占据着重要的地位。
但是,在现阶段多相混技术并未单独运用到集输工艺处理中,在和电热技术相结合的背景下,使两项技术产生积极的作用,使工艺处理过程更加简单,提升了技术处理的效率,为提升企业的经济效益提供了准备。
1.3 原油脱水技术
原油脱水技术在油气集输处理工艺发展中备受重视。
在应用的过程中通常运用排出和处理技术。
运用这样措施的国家主要有美国、俄罗斯等地区。
但是,我国对油气集输处理工艺的重视程度还不够,就导致我国的油气集输处理工艺发展得比较缓慢。
同时,原油脱水技术的发展水平也就比较低。
在今后的发展中就应该从研究和分析高效能的原油脱水技术为出发点,创造出游离水脱除器。
现阶段的游离水脱除器呈现出结构简单的特点,不能结合高含水原油的优势进行工作,导致油气集输处理工艺的水平比较低。
国内外的油田都加大了对原有脱水技术的投入,从多个角度进行了详细的研究和分析[2]。
2 油气集输处理工艺发展前景
2.1 管理模式
想要油气技术处理工艺在今后有所进步和发展就应该转变传统的管理模式。
因为管理模式对技术的提高有着不可忽视的意义。
生产和管理的相应规模会影响着油气集输处理工艺技术的水平和效果。
由此可见,在进行油田开采的过程中,就应该更加重视对管理模式的创新和转变。
在转变的初期会出现一些问题,但是,想要完善管理模式就应该在制定策略的时候防止出现操作的问题,对操作实行严格监管和控制。
并建立和完善人事管理制度,在对于工作人员进行有效管理的基础上进行仪器设备的生产。
2.2 原油稳定技术
原油稳定技术是油气集输处理工艺发展的一个前景。
在进行集输工艺处理的过程中应用原油稳定技术,可以把原油和天然气分离。
最终的目的就是把天然气从原油中脱离出来。
主要原理就是降低原油的蒸汽压。
在最近几年,在油气集输工艺处理技术不断进步和发展的背景下,原油稳定技术也被带动起来。
并且呈现出不断提升的趋势。
由此,原油稳定技术成为油气集输处理工艺发展中不可忽视的一部分。
并且存在一定的优势,比如可以降低油气的损害,提高了油气处理技术的效率和水平。
2.3 节能简化
节能简化也成为油气集输处理工艺发展的一个趋势。
因为节能简化技术能够降低生产的成本,并提升企业的经济效益和水平。
在社会不断发展和进步的状况下,人们的节能意识逐渐提升。
并且在社会中也得到了更加广泛的应用。
传统的工艺处理技术效率低下,不能满足企业发展需求。
因此,在进行集输技术处理的过程中,应该不断研究新型技术,使系统更加优化,进而提升油气技术处理技术工艺的水平,提升生产的效率[3]。
3 结语
综上所述,随着人们生活水平的提升,油气资源的需求也逐渐增加。
而且油气集输处理工艺在油田开采中有着不可替代的作用。
企业就应该合理研究油气集输处理工艺技术,为企业的发展和进步提供坚实的保障。
可以从转变管理模式,采用原油稳定技术和进行节能简化三方面进行技术的优化,使油气集输处理工艺朝着更好的方向发展。
参考文献:
[1]刘佳.
当前油气集输处理工艺现状及发展探析[J].中国石油和化工标准与质量,2014,(05):63.
[2]林珊.当前油气集输处理工艺发展现状及发展前景[J].中国石油和化工标准与质量,2013,(13):256.
[3]段忠军.当前油气集输处理工艺发展现状及前景分析[J].科技创新与应用,2013,(04):108.。