渗碳层深度
热处理渗碳层深度
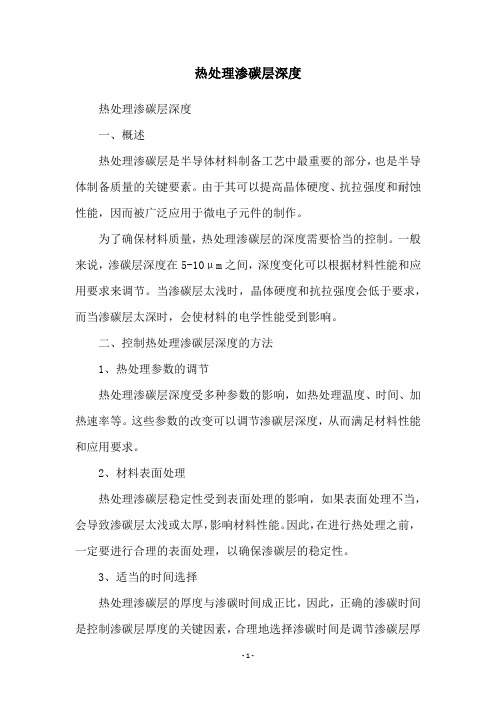
热处理渗碳层深度
热处理渗碳层深度
一、概述
热处理渗碳层是半导体材料制备工艺中最重要的部分,也是半导体制备质量的关键要素。
由于其可以提高晶体硬度、抗拉强度和耐蚀性能,因而被广泛应用于微电子元件的制作。
为了确保材料质量,热处理渗碳层的深度需要恰当的控制。
一般来说,渗碳层深度在5-10μm之间,深度变化可以根据材料性能和应用要求来调节。
当渗碳层太浅时,晶体硬度和抗拉强度会低于要求,而当渗碳层太深时,会使材料的电学性能受到影响。
二、控制热处理渗碳层深度的方法
1、热处理参数的调节
热处理渗碳层深度受多种参数的影响,如热处理温度、时间、加热速率等。
这些参数的改变可以调节渗碳层深度,从而满足材料性能和应用要求。
2、材料表面处理
热处理渗碳层稳定性受到表面处理的影响,如果表面处理不当,会导致渗碳层太浅或太厚,影响材料性能。
因此,在进行热处理之前,一定要进行合理的表面处理,以确保渗碳层的稳定性。
3、适当的时间选择
热处理渗碳层的厚度与渗碳时间成正比,因此,正确的渗碳时间是控制渗碳层厚度的关键因素,合理地选择渗碳时间是调节渗碳层厚
度的重要手段。
三、总结
热处理渗碳层深度是半导体晶片制备的关键要素,深度的变化会影响晶片的性能和使用效果。
为了确保材料质量,需要恰当地控制渗碳层深度。
可以通过改变热处理参数、进行合理的表面处理以及选择合理的渗碳时间来调节渗碳层厚度。
渗碳层深度
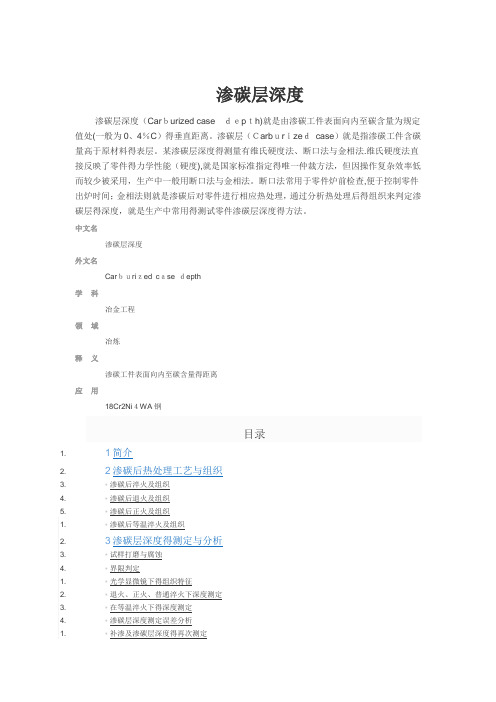
渗碳层深度渗碳层深度(Carburized casedepth)就是由渗碳工件表面向内至碳含量为规定值处(一般为0、4%C)得垂直距离。
渗碳层(Carburizedcase)就是指渗碳工件含碳量高于原材料得表层。
某渗碳层深度得测量有维氏硬度法、断口法与金相法.维氏硬度法直接反映了零件得力学性能(硬度),就是国家标准指定得唯一仲裁方法,但因操作复杂效率低而较少被采用,生产中一般用断口法与金相法。
断口法常用于零件炉前检查,便于控制零件出炉时间;金相法则就是渗碳后对零件进行相应热处理,通过分析热处理后得组织来判定渗碳层得深度,就是生产中常用得测试零件渗碳层深度得方法。
中文名渗碳层深度外文名Carburized case depth学科冶金工程领域冶炼释义渗碳工件表面向内至碳含量得距离应用18Cr2Ni4WA钢目录2. ▪维氏硬度测定法简介3. 4总结简介编辑低碳钢与合金钢渗碳时得主要区别在于低碳钢比合金钢渗层中得碳浓度要低,其组织与硬度略有不同,但对渗碳层深度测量无影响。
由于渗碳层具有变化得碳浓度,其由表及里逐渐减小,退火状态得渗碳层由表及里由以下三个区域组成:①过共析层组织为珠光体+二次渗碳体;②共析层组织为珠光体;③亚共析渗碳层过渡层,组织为珠光体+铁素体。
珠光体逐渐减少,铁素体逐渐增加,直到心部原始组织(珠光体+铁素体),渗碳缓冷试样渗碳层界限为出现铁素体组织,较容易区分.飞机防扭臂销棒材料为18Cr2Ni4WA钢,要求在外径φ38、5mm得两端各40mm内渗碳,渗碳层深度为1、0~1、4mm。
采用气体渗碳法对该零件进行渗碳,对渗碳后过程试样水淬打断,测定渗碳深度为1、2mm,深度符合要求,零件及随炉试样出炉。
随炉试样经正火后测定渗碳层深度为0、9mm,渗碳层深度不符合要求,零件判定为不合格。
为此,针对炉前测定合格、随炉试样正火后检测为不合格,且两者测定深度相差0、3mm得情况,开展了渗碳后热处理工艺、组织与深度测试得分析与探讨[1]。
550渗碳层深度计算公式

550渗碳层深度计算公式550渗碳层深度的计算是钢铁工业中的一项重要技术,它对于钢铁材料的强度和硬度提升起着关键作用。
在本文中,我们将介绍550渗碳层深度计算的公式及其应用,并给出一些实际操作的指导意义。
首先,让我们来了解什么是渗碳层深度。
渗碳是指将钢铁材料浸渍在含有碳的介质中,使得碳从介质中扩散到钢铁的表面和内部,从而增加其碳含量,并形成一层硬度较高的渗碳层。
渗碳层的厚度决定了钢铁材料的强度和硬度,因此渗碳层深度的计算非常重要。
计算550渗碳层深度的公式为:渗碳层深度(mm)= 0.4 × (温度/10) × 雇佣数在该公式中,温度是指渗碳时的处理温度,而雇佣数是与钢铁材料的特性有关的一个参数。
它取决于钢铁的化学成分、照射时间等因素,通常需要根据具体情况进行实验测定。
实际操作中,计算550渗碳层深度的公式需要采集一定数量的数据进行统计分析。
首先,我们需要准确测量温度,确保其精度和稳定性。
然后,根据实验结果确定钢铁材料的雇佣数,可以借助专业设备进行测定,如光谱仪、显微镜等。
最后,将这些参数代入公式中计算出渗碳层的深度。
在实际应用中,550渗碳层深度的计算对于钢铁材料的制造和应用具有重要意义。
首先,通过控制温度和雇佣数,可以精确计算出钢铁材料的渗碳层深度,从而满足特定工程需求。
此外,渗碳层深度还与钢铁材料的机械性能密切相关,合理的渗碳层深度可以提高钢铁材料的强度、硬度和耐磨性。
总之,550渗碳层深度的计算公式及其应用对于钢铁工业具有重要的指导意义。
它通过科学的计算方法,帮助我们掌握钢铁材料的渗碳层厚度,进而提高钢铁产品的质量和性能。
然而,渗碳层深度的计算是一个复杂的过程,需要综合考虑多个因素,并结合实验结果进行调整。
因此,在实际应用中,我们需要不断积累经验,提高对材料特性的认识,以确保渗碳层深度的计算准确可靠。
渗碳层深度
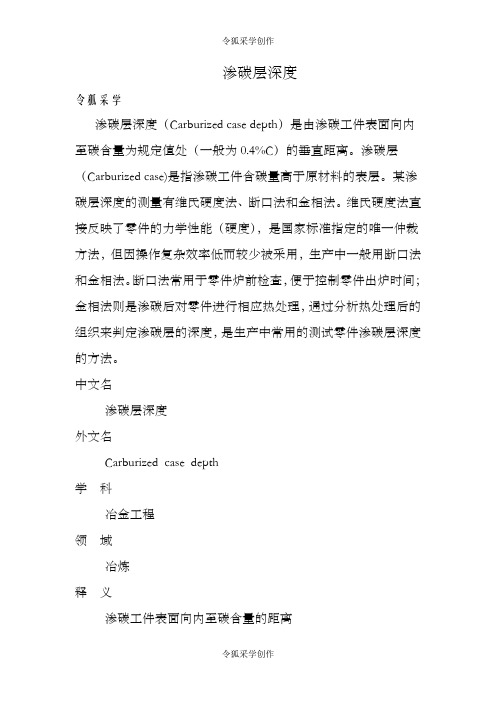
渗碳层深度令狐采学渗碳层深度(Carburized case depth)是由渗碳工件表面向内至碳含量为规定值处(一般为0.4%C)的垂直距离。
渗碳层(Carburized case)是指渗碳工件含碳量高于原材料的表层。
某渗碳层深度的测量有维氏硬度法、断口法和金相法。
维氏硬度法直接反映了零件的力学性能(硬度),是国家标准指定的唯一仲裁方法,但因操作复杂效率低而较少被采用,生产中一般用断口法和金相法。
断口法常用于零件炉前检查,便于控制零件出炉时间;金相法则是渗碳后对零件进行相应热处理,通过分析热处理后的组织来判定渗碳层的深度,是生产中常用的测试零件渗碳层深度的方法。
中文名渗碳层深度外文名Carburized case depth学科冶金工程领域冶炼释义渗碳工件表面向内至碳含量的距离应用18Cr2Ni4WA钢目录1. 1 简介2. 2 渗碳后热处理工艺与组织3. ▪渗碳后淬火及组织4. ▪渗碳后退火及组织5. ▪渗碳后正火及组织简介编辑低碳钢与合金钢渗碳时的主要区别在于低碳钢比合金钢渗层中的碳浓度要低,其组织和硬度略有不同,但对渗碳层深度测量无影响。
由于渗碳层具有变化的碳浓度,其由表及里逐渐减小,退火状态的渗碳层由表及里由以下三个区域组成:①过共析层组织为珠光体+二次渗碳体;②共析层组织为珠光体;③亚共析渗碳层过渡层,组织为珠光体+铁素体。
珠光体逐渐减少,铁素体逐渐增加,直到心部原始组织(珠光体+铁素体),渗碳缓冷试样渗碳层界限为出现铁素体组织,较容易区分。
飞机防扭臂销棒材料为18Cr2Ni4WA钢,要求在外径φ38.5mm 的两端各40mm内渗碳,渗碳层深度为1.0~1.4mm。
采用气体渗碳法对该零件进行渗碳,对渗碳后过程试样水淬打断,测定渗碳深度为1.2mm,深度符合要求,零件及随炉试样出炉。
随炉试样经正火后测定渗碳层深度为0.9mm,渗碳层深度不符合要求,零件判定为不合格。
为此,针对炉前测定合格、随炉试样正火后检测为不合格,且两者测定深度相差0.3mm的情况,开展了渗碳后热处理工艺、组织与深度测试的分析与探讨[1] 。
渗碳检验及组织缺陷
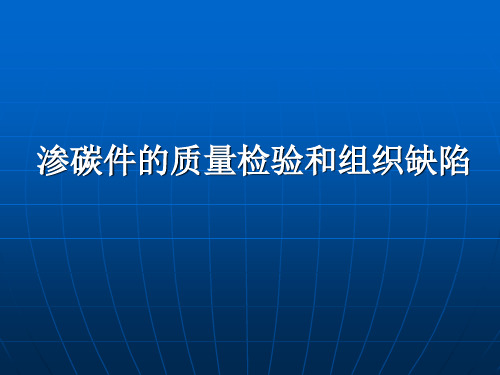
一、渗碳工件的检验项目
渗碳层深度的检验,一般在渗碳后进行。
渗碳层和心部硬度的检验,一般在热处理后进行。 渗碳层含碳量及浓度梯度的检验,要定期做剥离检验。 渗碳层和心部组织的检验。 渗碳件力学性能的检验。此种检验的目的是为了寻求合 理的渗碳工艺参数,主要是测量渗碳试样的硬度、耐磨 性、抗拉强度、接触疲劳强度、冲击韧性等。
法已得到应用,其温度可达980~1080℃。由于真空炉的推广,
也大大促进了真空渗碳工艺的发展。离子氮化成功地用于生 产也带动了离子渗碳的研究。为了节约能源和石油消耗,直
接在工作炉内滴注有机液体以获得渗碳气氛,或以氮基气为
载体气的气体渗碳法目前也有了长足的进展。采用微机对渗 碳过程进行全自动控制是一个重要的发展方向。
一般应用较广而且比较容易测量的是以组织中有50%珠光体处
为标准分界,即渗碳层深度等于过共析层十共析层+1/2亚共析
层的总和。有时对于某些合金钢的渗碳层是测量到出现原始组 织为止。
2. 渗碳层金相组织检验
金相组织检验主要是指检验渗碳层碳化物
级别、马氏体级别、残留奥氏体的数量和 组织缺陷。
3. 渗碳层浓度梯度的检验
4.渗碳件的组织缺陷
(1)渗碳层出现粗大的网状碳化物
这是由于渗碳不当造成的,在齿轮的齿顶处特别容易产生 这种粗大网状碳化物组织。这种组织的出现,不仅严重影
响工件的使用寿命,而且容易在淬火或者磨削加工时产生
开裂。为消除网状碳化物应严格控制渗碳时炉气的碳势和 工艺参数,使渗层浓度不致于过高,一旦出现网状碳化物,
是,在通常的情况下,增加渗层厚度将会增加表面碳浓度并
使组织恶化。所以,增加渗层深度并不一定使疲劳强度增加。
渗碳层深度国标
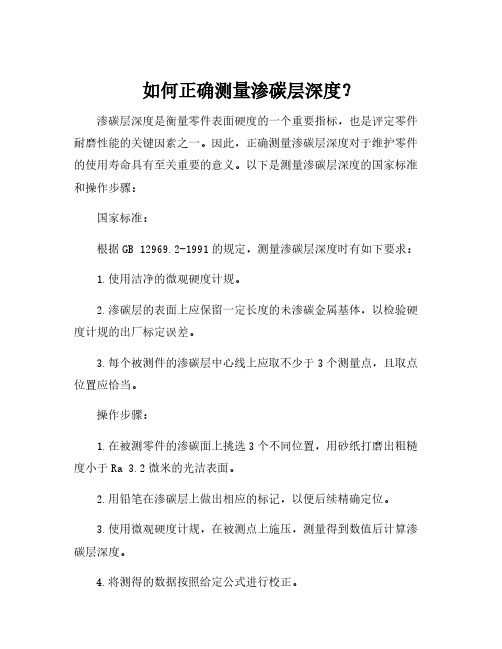
如何正确测量渗碳层深度?
渗碳层深度是衡量零件表面硬度的一个重要指标,也是评定零件耐磨性能的关键因素之一。
因此,正确测量渗碳层深度对于维护零件的使用寿命具有至关重要的意义。
以下是测量渗碳层深度的国家标准和操作步骤:
国家标准:
根据GB 12969.2-1991的规定,测量渗碳层深度时有如下要求:
1.使用洁净的微观硬度计规。
2.渗碳层的表面上应保留一定长度的未渗碳金属基体,以检验硬度计规的出厂标定误差。
3.每个被测件的渗碳层中心线上应取不少于3个测量点,且取点位置应恰当。
操作步骤:
1.在被测零件的渗碳面上挑选3个不同位置,用砂纸打磨出粗糙度小于Ra 3.2微米的光洁表面。
2.用铅笔在渗碳层上做出相应的标记,以便后续精确定位。
3.使用微观硬度计规,在被测点上施压,测量得到数值后计算渗碳层深度。
4.将测得的数据按照给定公式进行校正。
5.将测得的渗碳层深度和误差数据记录下来。
总结:
正确测量渗碳层深度不仅是国家标准的要求,更是保证零件使用寿命和机械性能的重要环节。
对于经常进行渗碳加工的产业,严谨遵守测量规程并对仪器设备进行定期检验、校准等保养,是维持制造质量标准的关键。
渗碳件质量检查
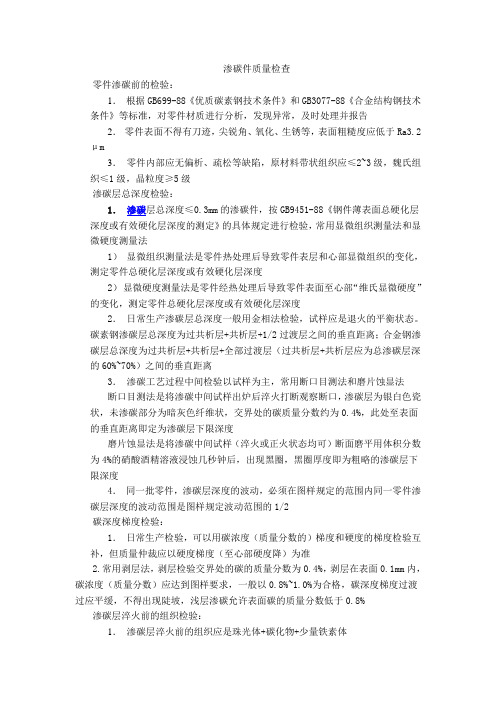
渗碳件质量检查零件渗碳前的检验:1.根据GB699-88《优质碳素钢技术条件》和GB3077-88《合金结构钢技术条件》等标准,对零件材质进行分析,发现异常,及时处理并报告2.零件表面不得有刀迹,尖锐角、氧化、生锈等,表面粗糙度应低于Ra3.2μm3.零件内部应无偏析、疏松等缺陷,原材料带状组织应≤2~3级,魏氏组织≤1级,晶粒度≥5级渗碳层总深度检验:1.渗碳层总深度≤0.3mm的渗碳件,按GB9451-88《钢件薄表面总硬化层深度或有效硬化层深度的测定》的具体规定进行检验,常用显微组织测量法和显微硬度测量法1)显微组织测量法是零件热处理后导致零件表层和心部显微组织的变化,测定零件总硬化层深度或有效硬化层深度2)显微硬度测量法是零件经热处理后导致零件表面至心部“维氏显微硬度”的变化,测定零件总硬化层深度或有效硬化层深度2.日常生产渗碳层总深度一般用金相法检验,试样应是退火的平衡状态。
碳素钢渗碳层总深度为过共析层+共析层+1/2过渡层之间的垂直距离;合金钢渗碳层总深度为过共析层+共析层+全部过渡层(过共析层+共析层应为总渗碳层深的60%~70%)之间的垂直距离3.渗碳工艺过程中间检验以试样为主,常用断口目测法和磨片蚀显法断口目测法是将渗碳中间试样出炉后淬火打断观察断口,渗碳层为银白色瓷状,未渗碳部分为暗灰色纤维状,交界处的碳质量分数约为0.4%,此处至表面的垂直距离即定为渗碳层下限深度磨片蚀显法是将渗碳中间试样(淬火或正火状态均可)断面磨平用体积分数为4%的硝酸酒精溶液浸蚀几秒钟后,出现黑圈,黑圈厚度即为粗略的渗碳层下限深度4.同一批零件,渗碳层深度的波动,必须在图样规定的范围内同一零件渗碳层深度的波动范围是图样规定波动范围的1/2碳深度梯度检验:1.日常生产检验,可以用碳浓度(质量分数的)梯度和硬度的梯度检验互补,但质量仲裁应以硬度梯度(至心部硬度降)为准2.常用剥层法,剥层检验交界处的碳的质量分数为0.4%,剥层在表面0.1mm内,碳浓度(质量分数)应达到图样要求,一般以0.8%~1.0%为合格,碳深度梯度过渡过应平缓,不得出现陡坡,浅层渗碳允许表面碳的质量分数低于0.8% 渗碳层淬火前的组织检验:1.渗碳层淬火前的组织应是珠光体+碳化物+少量铁素体2.渗碳层中有大块或网状碳化物,应建议两次淬火或一次正火,一次淬火,一般碳化物级别小于6级3.渗碳后,心部出现3级以上带状组织或晶粒度小于5级时,应正火后,重新检验合格方可淬火4.渗碳层中出现网状碳化物与游离铁素体不合格时应正火消除渗碳件淬、回火后的硬度检验:1.渗碳件表面硬度检验时,应去除氧化皮,脱碳层、增碳层,应以洛氏和维氏硬度计检验为准2.硬度应符合图样或技术文件规定,一般碳钢(10、20钢)硬度在50~55HRC 或58~63HRC,合金钢硬度在58~63HRC3.硬度终检以实物为准,但允许用随炉不同位置两个以上的试样代替实物检验。
渗碳层深度的测定
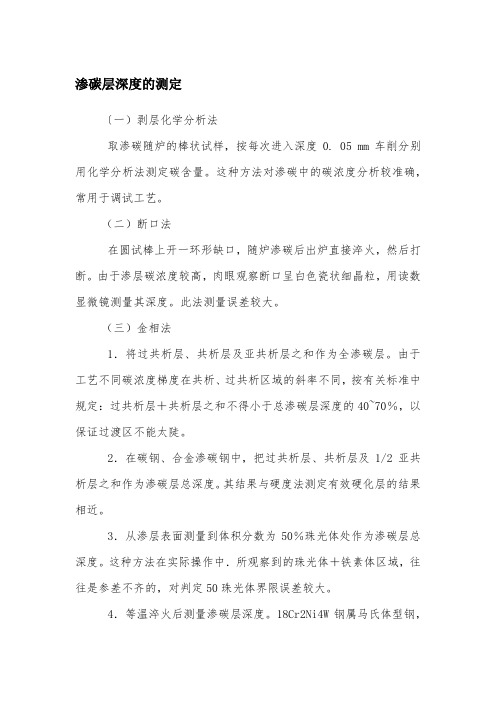
渗碳层深度的测定〔一)剥层化学分析法取渗碳随炉的棒状试样,按每次进入深度0. 05 mm车削分别用化学分析法测定碳含量。
这种方法对渗碳中的碳浓度分析较准确,常用于调试工艺。
(二)断口法在圆试棒上开一环形缺口,随炉渗碳后出炉直接淬火,然后打断。
由于渗层碳浓度较高,肉眼观察断口呈白色瓷状细晶粒,用读数显微镜测量其深度。
此法测量误差较大。
(三)金相法1.将过共析层、共析层及亚共析层之和作为全渗碳层。
由于工艺不同碳浓度梯度在共析、过共析区域的斜率不同,按有关标准中规定:过共析层+共析层之和不得小于总渗碳层深度的40~70%,以保证过渡区不能太陡。
2.在碳钢、合金渗碳钢中,把过共析层、共析层及1/2亚共析层之和作为渗碳层总深度。
其结果与硬度法测定有效硬化层的结果相近。
3.从渗层表面测量到体积分数为50%珠光体处作为渗碳层总深度。
这种方法在实际操作中.所观察到的珠光体+铁素体区域,往往是参差不齐的,对判定50珠光体界限误差较大。
4.等温淬火后测量渗碳层深度。
18Cr2Ni4W钢属马氏体型钢,它没有平衡组织,只能在等温淬火后测其深度。
这种钢渗碳后随炉冷却,从表面至心部均为马氏体,在基体与高碳区交界处有贝氏体析出,但在金相显微镜下观察其界限不甚清晰。
一般是将试样再加热到860℃后,放人280℃等温槽,数分钟后水淬,这时对含碳量的质量分数大于0.3%的区域形成淬火马氏体,而在含碳量近0.3%区域由于Ms点较高则形成回火马氏体,金相试样侵蚀后则有明显的白色(马氏体)区和黑色(回火马氏体)区的界线。
其相关标准可见JB/T 7710-1995《薄层碳氮共渗或薄层渗碳钢件显微组织检测》等行业标准。
(四)显微硬度法(有效硬化层深度测定法)显微硬度法是从试样边缘起测量显微硬度值的分布梯度,根据GB/T 9450-1988《钢件渗碳淬火有效硬化层深度的测定和校核》的标准规定判断渗层深度。
对GB/T 9450-1988标准的应用应注意:1.有效硬化层深度是指:从零件表面到维氏硬度值为550 HV 处的垂直距离。
渗碳层深度检验方法(金相法)
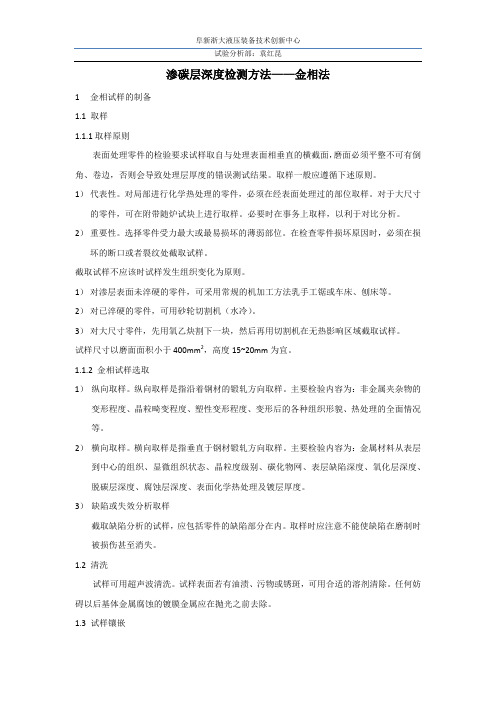
渗碳层深度检测方法——金相法1金相试样的制备1.1 取样1.1.1取样原则表面处理零件的检验要求试样取自与处理表面相垂直的横截面,磨面必须平整不可有倒角、卷边,否则会导致处理层厚度的错误测试结果。
取样一般应遵循下述原则。
1)代表性。
对局部进行化学热处理的零件,必须在经表面处理过的部位取样。
对于大尺寸的零件,可在附带随炉试块上进行取样。
必要时在事务上取样,以利于对比分析。
2)重要性。
选择零件受力最大或最易损坏的薄弱部位。
在检查零件损坏原因时,必须在损坏的断口或者裂纹处截取试样。
截取试样不应该时试样发生组织变化为原则。
1)对渗层表面未淬硬的零件,可采用常规的机加工方法乳手工锯或车床、刨床等。
2)对已淬硬的零件,可用砂轮切割机(水冷)。
3)对大尺寸零件,先用氧乙炔割下一块,然后再用切割机在无热影响区域截取试样。
试样尺寸以磨面面积小于400mm2,高度15~20mm为宜。
1.1.2 金相试样选取1)纵向取样。
纵向取样是指沿着钢材的锻轧方向取样。
主要检验内容为:非金属夹杂物的变形程度、晶粒畸变程度、塑性变形程度、变形后的各种组织形貌、热处理的全面情况等。
2)横向取样。
横向取样是指垂直于钢材锻轧方向取样。
主要检验内容为:金属材料从表层到中心的组织、显微组织状态、晶粒度级别、碳化物网、表层缺陷深度、氧化层深度、脱碳层深度、腐蚀层深度、表面化学热处理及镀层厚度。
3)缺陷或失效分析取样截取缺陷分析的试样,应包括零件的缺陷部分在内。
取样时应注意不能使缺陷在磨制时被损伤甚至消失。
1.2清洗试样可用超声波清洗。
试样表面若有油渍、污物或锈斑,可用合适的溶剂清除。
任何妨碍以后基体金属腐蚀的镀膜金属应在抛光之前去除。
1.3试样镶嵌若试样过于细薄或过软、易碎、或需检验边缘组织、或者为便于在自动磨抛机上研磨试样实验室通常采用可采用热压镶嵌法和浇注镶嵌法较为方便。
所选用先前方法均不得改变试样原始组织。
1.3.1热压镶嵌法将样品磨面朝下放入模中,树脂倒入模中超过样品高度,封紧模子并加热、加压。
渗碳时间与渗碳层深度计算公式
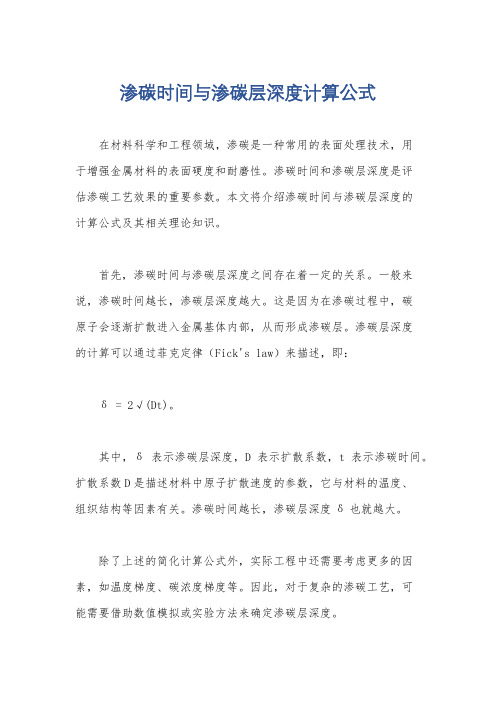
渗碳时间与渗碳层深度计算公式
在材料科学和工程领域,渗碳是一种常用的表面处理技术,用
于增强金属材料的表面硬度和耐磨性。
渗碳时间和渗碳层深度是评
估渗碳工艺效果的重要参数。
本文将介绍渗碳时间与渗碳层深度的
计算公式及其相关理论知识。
首先,渗碳时间与渗碳层深度之间存在着一定的关系。
一般来说,渗碳时间越长,渗碳层深度越大。
这是因为在渗碳过程中,碳
原子会逐渐扩散进入金属基体内部,从而形成渗碳层。
渗碳层深度
的计算可以通过菲克定律(Fick's law)来描述,即:
δ = 2√(Dt)。
其中,δ表示渗碳层深度,D表示扩散系数,t表示渗碳时间。
扩散系数D是描述材料中原子扩散速度的参数,它与材料的温度、
组织结构等因素有关。
渗碳时间越长,渗碳层深度δ也就越大。
除了上述的简化计算公式外,实际工程中还需要考虑更多的因素,如温度梯度、碳浓度梯度等。
因此,对于复杂的渗碳工艺,可
能需要借助数值模拟或实验方法来确定渗碳层深度。
总之,渗碳时间与渗碳层深度是渗碳工艺中重要的参数,其计算公式可以通过扩散理论来描述。
通过合理地控制渗碳时间,可以获得理想的渗碳层深度,从而改善金属材料的表面性能,延长其使用寿命。
希望本文对您理解渗碳工艺有所帮助。
渗碳层深度
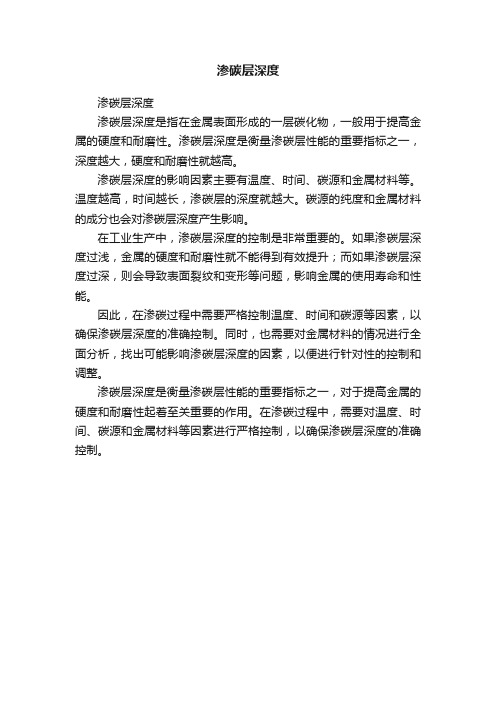
渗碳层深度
渗碳层深度
渗碳层深度是指在金属表面形成的一层碳化物,一般用于提高金属的硬度和耐磨性。
渗碳层深度是衡量渗碳层性能的重要指标之一,深度越大,硬度和耐磨性就越高。
渗碳层深度的影响因素主要有温度、时间、碳源和金属材料等。
温度越高,时间越长,渗碳层的深度就越大。
碳源的纯度和金属材料的成分也会对渗碳层深度产生影响。
在工业生产中,渗碳层深度的控制是非常重要的。
如果渗碳层深度过浅,金属的硬度和耐磨性就不能得到有效提升;而如果渗碳层深度过深,则会导致表面裂纹和变形等问题,影响金属的使用寿命和性能。
因此,在渗碳过程中需要严格控制温度、时间和碳源等因素,以确保渗碳层深度的准确控制。
同时,也需要对金属材料的情况进行全面分析,找出可能影响渗碳层深度的因素,以便进行针对性的控制和调整。
渗碳层深度是衡量渗碳层性能的重要指标之一,对于提高金属的硬度和耐磨性起着至关重要的作用。
在渗碳过程中,需要对温度、时间、碳源和金属材料等因素进行严格控制,以确保渗碳层深度的准确控制。
渗碳层深度
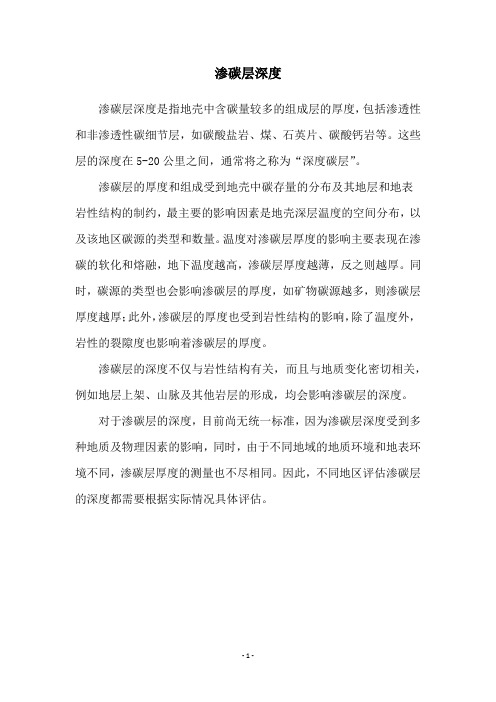
渗碳层深度
渗碳层深度是指地壳中含碳量较多的组成层的厚度,包括渗透性和非渗透性碳细节层,如碳酸盐岩、煤、石英片、碳酸钙岩等。
这些层的深度在5-20公里之间,通常将之称为“深度碳层”。
渗碳层的厚度和组成受到地壳中碳存量的分布及其地层和地表
岩性结构的制约,最主要的影响因素是地壳深层温度的空间分布,以及该地区碳源的类型和数量。
温度对渗碳层厚度的影响主要表现在渗碳的软化和熔融,地下温度越高,渗碳层厚度越薄,反之则越厚。
同时,碳源的类型也会影响渗碳层的厚度,如矿物碳源越多,则渗碳层厚度越厚;此外,渗碳层的厚度也受到岩性结构的影响,除了温度外,岩性的裂隙度也影响着渗碳层的厚度。
渗碳层的深度不仅与岩性结构有关,而且与地质变化密切相关,例如地层上架、山脉及其他岩层的形成,均会影响渗碳层的深度。
对于渗碳层的深度,目前尚无统一标准,因为渗碳层深度受到多种地质及物理因素的影响,同时,由于不同地域的地质环境和地表环境不同,渗碳层厚度的测量也不尽相同。
因此,不同地区评估渗碳层的深度都需要根据实际情况具体评估。
- 1 -。
渗碳层深度检测标准

渗碳层深度检测标准渗碳层深度是指在金属材料表面形成的一层碳化物,通常用于增强金属材料的硬度和耐磨性。
渗碳层深度的准确检测对于材料的质量控制和工程应用具有重要意义。
因此,制定一套科学严谨的渗碳层深度检测标准显得尤为重要。
一、检测方法。
1. 金相显微镜法。
金相显微镜是一种通过金相显微镜观察金属材料显微组织结构来检测渗碳层深度的方法。
通过金相显微镜的放大倍数和图像分析软件的辅助,可以准确测量渗碳层的深度。
2. 硬度计法。
硬度计是一种通过在金属材料表面进行硬度测试来间接检测渗碳层深度的方法。
由于渗碳层通常比基体金属硬度高,因此可以通过硬度值的变化来推断渗碳层的深度。
3. 电子探针法。
电子探针是一种通过电子束轰击样品表面并测量反射电子能谱来确定元素组成和深度分布的方法。
通过电子探针的分析,可以准确测量出渗碳层的深度和碳浓度。
二、检测标准。
1. 检测设备要求。
金相显微镜、硬度计和电子探针等检测设备应符合国家标准,且经过定期校准和维护,确保检测结果的准确性和可靠性。
2. 检测操作规程。
检测人员应经过专业培训,并熟练掌握各种检测方法的操作技巧和注意事项。
在进行渗碳层深度检测时,应按照标准的操作规程进行,确保检测结果的准确性。
3. 检测结果评定。
根据检测方法的测量结果,对渗碳层深度进行评定。
对于不同的工程应用和材料要求,可以制定相应的渗碳层深度标准,以确保材料的质量和性能满足要求。
三、质量控制。
1. 质量管理体系。
建立健全的质量管理体系,对渗碳层深度检测工作进行全面管理和控制。
包括检测设备的管理维护、检测人员的培训考核、检测操作规程的制定和执行等方面。
2. 数据分析与应用。
对渗碳层深度检测结果进行数据分析和应用,及时发现和解决存在的质量问题。
并根据检测结果,对生产工艺进行调整和改进,以提高渗碳层深度的稳定性和一致性。
3. 质量监督抽查。
定期进行质量监督抽查,对渗碳层深度检测工作进行全面检查和评估。
发现问题及时整改,确保检测结果的准确性和可靠性。
为保证应有的渗碳或渗氮层深度的尺寸换算

主题:为保证应有的渗碳或渗氮层深度的尺寸换算随着科学技术的迅速发展,金属材料的加工工艺也日益完善。
在金属材料的表面处理过程中,渗碳或渗氮是常用的一种方法,通过在金属表面渗入碳或氮元素,可以提高金属材料的硬度和耐磨性。
在渗碳或渗氮过程中,如何准确计算并控制渗层的深度,是一个非常重要的问题。
本文将介绍如何进行渗层深度的尺寸换算,以保证金属材料的质量和性能。
一、渗碳或渗氮层的深度计算原理在金属材料的表面处理过程中,常常使用渗碳或渗氮的方法来增强材料的硬度和耐磨性。
渗碳或渗氮层的深度计算原理是根据材料的温度、处理时间和渗碳或渗氮的浓度来进行计算的。
一般来说,渗碳或渗氮层深度与温度、处理时间、浓度的关系可以用以下公式表示:渗层深度 = 渗碳速度或渗氮速度× 处理时间其中,渗碳速度或渗氮速度是指单位时间内材料表面渗入碳或氮元素的厚度,通常以μm/h为单位。
处理时间则是指金属材料在渗碳或渗氮过程中所经历的时间,通常以小时为单位。
二、渗层深度的尺寸换算方法为了保证金属材料的质量和性能,需要对渗碳或渗氮层的深度进行准确的计算和换算。
在实际操作中,可以采用以下方法进行尺寸换算:1. 温度、处理时间和浓度的确定首先需要确定金属材料的温度、处理时间和渗碳或渗氮的浓度。
通常情况下,温度和处理时间是由加工设备和工艺参数确定的,而渗碳或渗氮的浓度可以通过检测设备和实验来确定。
2. 计算渗碳或渗氮速度根据温度、处理时间和浓度来计算渗碳或渗氮的速度,通常情况下可以通过实验或理论计算来得到。
3. 进行深度换算通过上述公式,利用渗碳或渗氮速度和处理时间来计算出渗层的深度。
在实际操作中,可以使用计算机软件来进行精确计算,也可以通过实验来验证结论。
三、渗碳或渗氮层深度的影响因素渗碳或渗氮层的深度受到多种因素的影响,如温度、处理时间、材料的性质和表面粗糙度等。
在进行渗层深度的尺寸换算时,需要充分考虑这些影响因素,以保证计算结果的准确性和可靠性。
渗碳层深度不合格的原因与防止方法

渗碳层深度不合格的原因与防止方法1、渗层太浅(1)原因●炉温偏低,渗碳时间短。
●装炉量过多或新工装没有补渗,没有增加煤油滴量。
●排气不充分就进入强渗期。
●炉子密封不严,炉气压力过低。
●工件表面被炭黑或覆盖影响活性碳原子被钢件吸收。
●操作者判断渗层试样失误。
(2)被救方法:重新入炉进行被渗处理,将原试样同炉被渗。
2、渗层过深(1)原因●渗碳温度偏高,渗入时间过长。
●碳势太高,加快了渗碳速度。
●仪表失灵跑温。
●操作者判断出炉试样失误。
(2)处理意见:一般应报废或打不合格品让步接收报告。
3、渗层不均原因●装炉量过多,工件之间未留间隔,互相接触。
●工件表面有油污和锈斑。
●炉内气氛不均匀,局部有死角。
●炉罐长期不清理。
●炉内没安装导风板或已损坏。
4、过共析+共析层过深(1)原因●强渗期炉内碳势太高。
●强渗时间太长,扩散时间太短。
(2)补救方法:如渗层总深度偏下限,可在渗碳炉内进行扩散处理,加以补救。
5、过共析+共析层过深(1)原因●强渗期炉内碳势太低。
●强渗时间短,扩散时间长。
(2)补救方法:如在总渗层深度范围内,可在高碳势气氛中补渗。
6、防止方法(1)渗碳温度渗碳温度对渗碳速度影响很大。
一旦工艺温度确定以后,必须保持渗碳温度的稳定性,不能过高或过低,过高容易使渗层太深,过低容易使渗层太浅。
(2)渗碳时间碳在钢中的扩散及扩散层深度是温度和时间的函数,因此在渗碳温度稳定的情况下,要正确地掌握渗碳时间,不能过长和过短,过长容易使渗层太深,过短容易使渗层太浅。
(3)炉气压力炉气压力的大小明显地影响炉内各种化学反应速度,当炉压过小时,不利于排除废气并使氧化性气体进入炉内,过高的压力不利于有机渗剂的进一步分解,因而影响碳势的提高。
在强渗期炉气压力控制在198~392Pa,扩散期炉压控制在49~198Pa。
所以,一般使炉气压力维持正压,有利于渗碳过程的顺序进行。
(4)渗剂滴量●排气阶段———由于工件刚装炉带入大量空气和微量水份,使炉内出现氧化气氛,应迅速将氧化气氛排出,甲醇裂化分解温度比煤油低,又不产生炭黑,且产气量比煤油大一倍,所以排气前期用甲醇比用煤油效果好。
热处理渗碳层深度
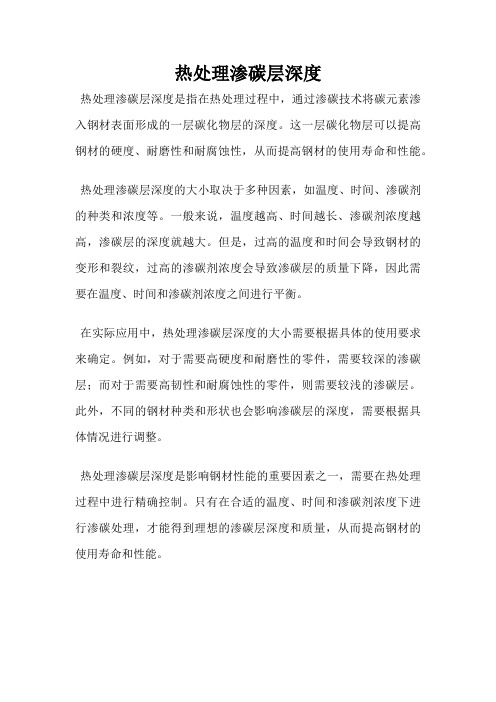
热处理渗碳层深度
热处理渗碳层深度是指在热处理过程中,通过渗碳技术将碳元素渗入钢材表面形成的一层碳化物层的深度。
这一层碳化物层可以提高钢材的硬度、耐磨性和耐腐蚀性,从而提高钢材的使用寿命和性能。
热处理渗碳层深度的大小取决于多种因素,如温度、时间、渗碳剂的种类和浓度等。
一般来说,温度越高、时间越长、渗碳剂浓度越高,渗碳层的深度就越大。
但是,过高的温度和时间会导致钢材的变形和裂纹,过高的渗碳剂浓度会导致渗碳层的质量下降,因此需要在温度、时间和渗碳剂浓度之间进行平衡。
在实际应用中,热处理渗碳层深度的大小需要根据具体的使用要求来确定。
例如,对于需要高硬度和耐磨性的零件,需要较深的渗碳层;而对于需要高韧性和耐腐蚀性的零件,则需要较浅的渗碳层。
此外,不同的钢材种类和形状也会影响渗碳层的深度,需要根据具体情况进行调整。
热处理渗碳层深度是影响钢材性能的重要因素之一,需要在热处理过程中进行精确控制。
只有在合适的温度、时间和渗碳剂浓度下进行渗碳处理,才能得到理想的渗碳层深度和质量,从而提高钢材的使用寿命和性能。
- 1、下载文档前请自行甄别文档内容的完整性,平台不提供额外的编辑、内容补充、找答案等附加服务。
- 2、"仅部分预览"的文档,不可在线预览部分如存在完整性等问题,可反馈申请退款(可完整预览的文档不适用该条件!)。
- 3、如文档侵犯您的权益,请联系客服反馈,我们会尽快为您处理(人工客服工作时间:9:00-18:30)。
规范要求 Specification Requirement
渗碳层深度 case depth
备注/解释 Remark/Inter pretion
结论 Conclusion 检验员Tested by: 日期Date
合格Conform 校对Reviewed by: 日期Date
不合格Non-conform 批准Approved by 日期Date
Material Specification(Rev.)
设备型号 Equipment Model 检测方法 Analysis Method 客户 Customer
渗碳层深度检测结果The Results of case depth Inspection
样品编号 Sample Number
金相照片metallograph
声明Statement:1.此分析结果仅对来样而言。Analysis results are only for requested sample.2.未经材料 验室书面批准,不得部分复制检验报告。The report shall not be reproduced except in full without the written approval of the MTL.
日期Date
ted sample.2.未经材料实 in full withouAPHIC INSPECTION REPORT
QC144
报告编号 Report NO. 零件件号 Part No. 批次号 Part Rev. 样品状态 Sample Station 材料牌号 Material 检验规范(版本) Analysis Specification(Rev.) 校准日期 Calibration Date 热处理批次号 Heattreatment lot NO. 请检单号 Requisition Sheet NO. 零件名称 Lot No. 零件版本号 Part Name 样品数量 Sample Quantity 材料规范(版本)