产品量产初期验证计划
产验证工作制度

产验证工作制度是指在生产过程中,对产品进行的一系列验证活动,以确保产品符合设计要求、满足客户需求,并符合相关法规标准。
产验证工作制度是企业质量管理体系的重要组成部分,对于提高产品质量、降低不良率、提升客户满意度具有重要意义。
以下是产验证工作制度的内容及实施要点。
一、产验证工作制度的内容1. 验证计划的制定根据产品设计文件、客户需求、相关法规标准等因素,制定验证计划,明确验证的对象、内容、方法、周期等。
2. 验证团队的组建组建专门的验证团队,负责实施验证计划。
验证团队应具备相应的专业知识和技能,确保验证活动的有效进行。
3. 验证文件的编写编写验证文件,包括验证大纲、验证表格、试验方法、判定标准等,以确保验证活动的规范进行。
4. 验证活动的实施按照验证计划和验证文件,开展验证活动。
验证活动包括实验室验证、现场验证、过程验证等,涵盖产品的整个生命周期。
5. 验证结果的记录与分析记录验证活动的结果,进行数据分析,评估产品的质量状况,为改进措施提供依据。
6. 验证报告的编制编制验证报告,包括验证总结、问题清单、改进措施等,提交给相关部门或领导,以便采取相应措施。
7. 验证改进措施的跟踪与验证对采取的改进措施进行跟踪,验证改进效果,确保产品质量的持续提升。
二、产验证工作制度的实施要点1. 加强人员培训加强对验证团队人员的培训,提高其专业知识和技能,确保验证活动的有效进行。
2. 完善验证设施和设备配置完善的验证设施和设备,确保验证活动的顺利进行。
3. 建立健全沟通机制建立有效的沟通机制,确保验证活动中出现的问题能够及时反馈、解决。
4. 强化过程控制在生产过程中,强化过程控制,及时发现和纠正问题,确保产品质量。
5. 落实责任制明确验证活动中各环节的责任人,落实责任制,确保验证活动的规范进行。
6. 持续改进根据验证结果,持续改进产品设计和生产过程,提高产品质量。
7. 建立完善的记录和追溯体系建立完善的记录和追溯体系,确保验证活动的可追溯性,便于问题的追踪和处理。
产品质量先期策划
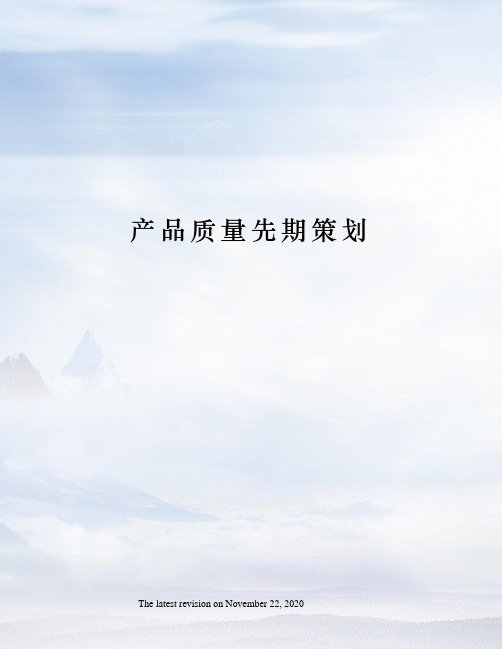
产品质量先期策划 The latest revision on November 22, 2020上海司南卫星导航技术股份有限公司产品质量先期策划控制程序文件编号:版次:A/0受控状态:分发序号:年月日发布年月日实施修改记录1目的本程序明确了产品开发过程的阶段和各阶段的输入、任务、输出及对应的责任人,规定了工作流程及内容要求,加强产品开发的过程控制,确保产品满足顾客和相关法规的要求。
2适用范围适用于汽车供应链卫星导航产品平台开发和应用开发过程的产品质量先期策划。
3定义3.1特殊特性显着影响安全与法律法规和显着使顾客不满意的产品特性和过程特性。
3.2产品特性在图纸或其他工程技术资料中所描述的零部件、产品的特点和性能。
3.3过程特性与产品特性具有因果关系的过程变量。
过程特性仅能在发生时才能测量出。
对于一个产品特性,可能有多个过程特性。
在某个过程中,一个过程特性可能影响到整个产品特性。
4职责产品质量先期策划过程中,各职能部门的具体职责如下图1-1所示。
其中:4.1APQP小组(产品质量先期策划小组)APQP小组通常为跨部门功能小组,负责制定产品质量先期策划的APQP计划总表。
4.2研发中心负责产品开发的归口管理,组织开发项目的技术评审,负责项目管理工作。
4.3营销中心负责市场调研和顾客需求收集,提出产品应用开发建议,提供产品开发需要的相关参数;负责顾客的落实及配合研发部门试配产品;负责用户验收的跟踪服务。
4.4生产技术部负责工艺性分析、工艺审查、试制工艺设计和工艺验证。
4.5采购部负责供应商选择、采购件的采购、验证工作。
4.6生产车间负责生产准备、生产和验证工作。
4.7质量部负责采购零件和产品试验的质量监控,及供应商管理工作。
图1-1APQP小组职责分配5工作流程图6工作程序6.1计划和确定项目市场调研组织过程资产营销中心通过对市场调查、顾客信息反馈和质量信息报告、顾客的要求和顾客期望等多种信息进行分析,提交总工程师。
产品质量先期策划(项目管理)管理程序

1.0 目的:本程序规定了xxxxxx产品和过程开发的流程,通过产品质量先期策划的结构性方法,确定和制定产品和过程开发所需的步骤,引导资源以确保所要求的步骤按时完成,促进对所需更改的早期识别,避免晚期更改,以最低的成本及时提供优质的产品,使顾客满意。
2.0 适用范围:本程序适用于xxxxxx所有新产品开发项目和产品改进项目,本程序所规定的产品和过程开发流程与AITS 的全球产品开发流程(AIPDS)一致。
3.0 职责:3.1 项目管理部项目经理负责产品质量先期策划(APQP)全过程管理,对项目的开发进度、质量、财务收益、开发成本控制负责;3.2 由各职能部门派出的专业人员组成多功能团队的项目组,依据本流程内容中所描述的责任,完成产品质量先期策划(APQP)的各项工作;3.2.1 市场营销部负责新产品客户报价,以及各阶段试制产品客户订单的接收和交付工作;3.2.2 技术中心负责产品的设计开发工作;3.2.3 工艺部负责过程的设计和开发工作;3.2.4 生产部负责产品工装样件、试生产产品的试制制造;3.2.5 质量保证部QE负责在产品及过程开发阶段质量控制工作。
同时,与项目经理一起负责开发过程符合本程序的规定;3.2.6 质量保证部SQE 负责供应商APQP 过程管理和供应商各阶段零件检查、确认和认可;3.2.7 采购部负责供应商选点、零部件价格控制和第6阶段前各阶段试制产品需求零部件的采购;3.2.8 计划物流部负责产品包装方案、物流方案的确定,第6阶段后需求零部件的采购,以及各阶段试制产品的发运;3.2.9 财务信息部负责新产品报价财务模块的测算及各阶段财务成本的更新和控制;3.2.10 人力资源部负责组织对参与APQP的成员进行策划活动所涉及的分析技术如FMEA,PPAP,SPC,MSA和开发技能的培训4.0 工作内容:4.1 xxx全球产品开发系统(AIPDS)即xxx(上海)xxx的产品和过程开发流程将整个产品和过程开发阶段分为六个阶段进行管理,包含:Phase 1-Quote Business商务报价阶段;Phase 2- Plan and Define项目计划和定义阶段;Phase 3- Design and Development设计和开发阶段;Phase 4- Product and Process validation产品和过程验证阶段 ;Phase 5- Production Preparation生产准备阶段;Phase 6- Stable Production稳定生产阶段;4.2 产品和过程开发流程各阶段主要内容:4.2.1 第1阶段商务报价阶段本阶段总体责任由市场营销部主导并负责。
浅谈APQP(量产之前的质量计划)

浅谈APQP(量产之前的质量计划)2008年12月18日AM 09:11APQP (Advanced Product Quality Planning):量产之前的质量计划~~定义:产品从研发到生产应该有一套完整的质量规划及管制计划,制定各阶段的作业方式与质量活动,以确保产品在研发、初期样品、小批量试作、量产,等阶段之管理活动有效运作。
APQP参考手册经QS9000条文的引用,字句中有Shall、Will、Must是具有强制性,的其他并不强制,窗体中示范仅供参考用不强制性。
APQP规划时程:5个阶段1.企划及开发阶段。
2.产品开发设计验证。
3.制程设计开发阶段。
4.产品及制程确认。
5.回馈稽查及矫正措施。
APQP的PDSA:P-plan,D-do,S-study,A-act∙企划及开发阶段(第一阶段):Plan and Define Program 从概念提出到开发计划核准。
1.确保客户需求与期望被充分了解。
2.投入因素:1.来自客户反应的讯息:a.市场研究 b.客诉记录与质量履历数据 c.小组经验。
2.经营计划/营销3.产品或制程的标竿。
4.产品或制程描诉。
5.产品可靠度研究。
6.客户需求与期望(满意度指标)。
3. 产出项目:1.设计目标(概念之具体化与量化)。
2.可靠度与质量目标。
3.初期材料清单(含分包商名单)。
4.初期制程流程图。
5.初期制造与产品之管制特性列表。
:决定特殊特性因素有:a.客户或图面指定 b.A级或AR及 c.跨功能小组决定 d.过去质量履历 e.严重度较高者或成本较高者。
6.产品保证计划。
7.管理阶层之支持。
∙产品开发设计验证(第二阶段):Production Define &Development verification 从计划到原型产品建立。
1.以原型产品(Prototype)确认产品或服务是否符合客户要求或期望。
2.有效考虑产能、开发时机时程要求、工程要求、质量要求、投资成本、与单位成本。
产品质量先期策划(APQP)
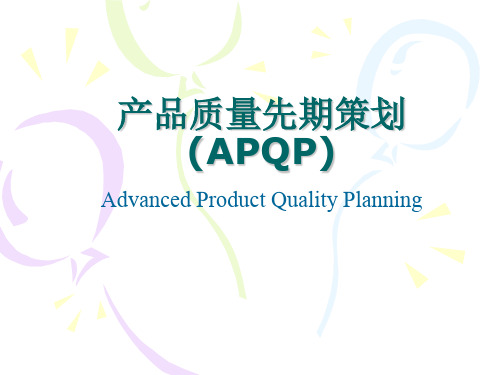
产品设计和开发
• 新的设备、工装和设施 在设计评审期间,横向职能小组可能会确定需 要新的设备、工装和设施。这些细节必须提出 并包括在总的进度计划内。必须把重点放在确 保按时完成新的设备、工装和设施。
产品设计和开发
• 特殊特性的最后确定 在这一阶段,大部分的技术信息都已明确,因此,横向职 能小组应就特殊特性取得一致意见并将其最终确定下来。 控制计划应指出已最终确定的特殊特性。
产品质量先期策划 (APQP)
Advanced Product Quality Planning
• 什么是产品质量先期策划? 一种确定和建立保证产品满足顾
客要求的步骤的结构化方法。
• 产品质量先期策划的目标 促进涉及到产品的每个人的联系,
确保要求的步骤能够按时完成。
• 产品质量先期策划的益处
1)向着使顾客满意的方向引导资源; 2)促进及早识别需要进行的更改; 3)避免事后更改; 4)以最低的成本及时提供高质量的产品
产品设计和开发
• 设计评审(有文件纪录的正式评审) 进行设计评审是为了监控项目相对于顾客要求的进展。这 些评审由横向职能小组进行,而且每次评审的结果都必须 以文件存档。 一般来说,设计评审可包括设计失效模式及后果分析 、 设计验证进展、可靠性试验和研究、计算机模拟结果、基 准数据和相对于时间限制的总体进度。
APQP PDCA-循环
行动
反馈评定和 纠正措施
计划 计划和确定
产品和过程确认 产品设计和开发
过程设计和开发
检查
实施
PDCA:计划-实施-检查-行动
产品 APQP 进度图表
概念 项目批准 提出/批准
试
限产
做
策划
产品设计和开发. 过程设计和开发 产品和过程确认
(完整word版)产品量产的初期管理
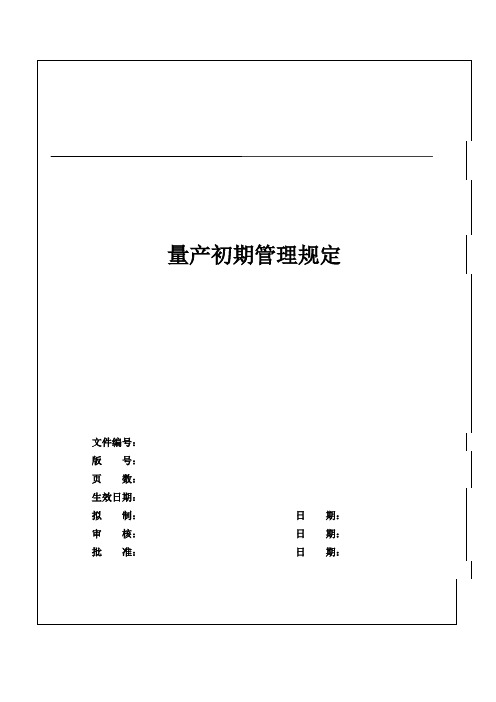
一、目的监控新产品量产转交后生产初期(人、机、料、法、环、测)等影响质量因素的管理,确保早期产品质量稳定。
二、适用范围适用于所有新产品及其改进型新型号产品开发完成后转交量产的产品生产。
三、定义.3.1初期管理:为确保初期产品的质量和工序的早期稳定化,进行量产以后在一定期间(以下,初期管理期间)和数量(批次、吨数等)的质量保证活动。
3.2.初期管理时间:根据产品生产控制难易程度在进行初期管理活期间决定初期数量或时间,要通过以下原则:(客户另行规定除外)3.3初期产品:初期管理期间生产的全部产品(合格品、各种废料含落地料、高铁料、筛上料、清洗料等)。
3.4初期产品评价:在初期管理期间,以判断产品质量的正确、设计质量、工序配备、设备稳定上的问题点的措施、改善为目的的初期产品的质量的确认活动。
3.4初期产品管理:对处理产品从生产过程、入库、销售过程,按规定措施采取管理活动。
四、职责与权限4.1研发中心:负责完成新产品的项目开发、客户对新品的确认、技术文件及文档归档管理,将整套生产的应用文件、标准、规范、样品等转、教生产系统进行量产,并指导量产与解决量产中出现的技术问题。
4.2工艺工程部:负责量产初期生产过程的技术、工艺工作,包括生产工艺稳定、生产培训与指导、设备稳定评估以及生产过程出现的技术、工艺等问题的组织解决。
4.3质量部:负责产初期生产过程的质量监控与评估以及决定初期管理的限定条件解除。
4.4生产工厂:按公司经营计划与客户订单状况组织生产量产,包括定额合格生产人员、合格稳定生产设备、满足量产的生产环境与场所等。
4.5采购部:负责提供满足量产的合格物料。
4.6其他部门:按各自职能对生产量产进行支持与配合,完成部门承担的职责。
五、内容5.1量产初期准备5.1.1研发中心整理整套的量产需要的技术文件、标准、规范等,包括《生产技术条件》(含环境保护保证)、《工艺流程图》、《原材料标准》、《产品标准》、《扩试检查表》、《中试记录》、《设计开发中试总结报告》、《扩试记录》、《设计开发扩试总结报告》、《产品规格书》、《客户反馈报告》、《D-FMEA检查表》、《新产品性能检查表》、《生产节(产能)拍分析表》、《新产品人员培训教材》、《新产品量产培训计划》、《新产品产品性能检验》、《定型试验报告》、《生产场地平面布置图》、《产品特殊特性清单》、《生产设备清单》、《检测设备清单》、《新品供应商明细表》、样品、《客户承认书》等转、教生产系统相应部门。
产品工程验证方案模板
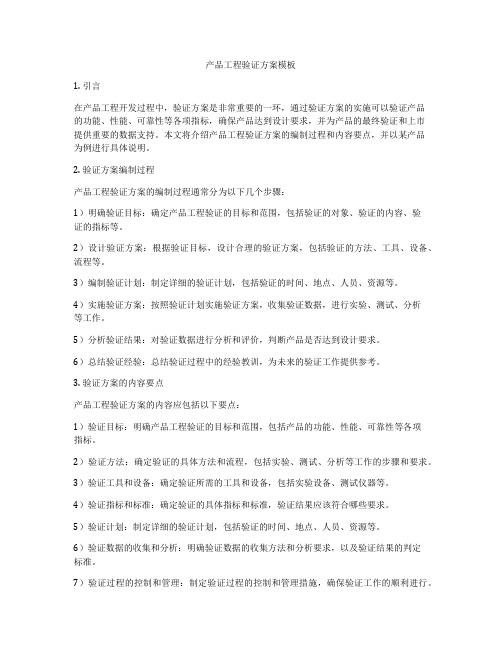
产品工程验证方案模板1. 引言在产品工程开发过程中,验证方案是非常重要的一环,通过验证方案的实施可以验证产品的功能、性能、可靠性等各项指标,确保产品达到设计要求,并为产品的最终验证和上市提供重要的数据支持。
本文将介绍产品工程验证方案的编制过程和内容要点,并以某产品为例进行具体说明。
2. 验证方案编制过程产品工程验证方案的编制过程通常分为以下几个步骤:1)明确验证目标:确定产品工程验证的目标和范围,包括验证的对象、验证的内容、验证的指标等。
2)设计验证方案:根据验证目标,设计合理的验证方案,包括验证的方法、工具、设备、流程等。
3)编制验证计划:制定详细的验证计划,包括验证的时间、地点、人员、资源等。
4)实施验证方案:按照验证计划实施验证方案,收集验证数据,进行实验、测试、分析等工作。
5)分析验证结果:对验证数据进行分析和评价,判断产品是否达到设计要求。
6)总结验证经验:总结验证过程中的经验教训,为未来的验证工作提供参考。
3. 验证方案的内容要点产品工程验证方案的内容应包括以下要点:1)验证目标:明确产品工程验证的目标和范围,包括产品的功能、性能、可靠性等各项指标。
2)验证方法:确定验证的具体方法和流程,包括实验、测试、分析等工作的步骤和要求。
3)验证工具和设备:确定验证所需的工具和设备,包括实验设备、测试仪器等。
4)验证指标和标准:确定验证的具体指标和标准,验证结果应该符合哪些要求。
5)验证计划:制定详细的验证计划,包括验证的时间、地点、人员、资源等。
6)验证数据的收集和分析:明确验证数据的收集方法和分析要求,以及验证结果的判定标准。
7)验证过程的控制和管理:制定验证过程的控制和管理措施,确保验证工作的顺利进行。
4. 产品工程验证方案实施案例以某产品为例,介绍产品工程验证方案的具体内容和实施步骤。
4.1 验证目标本产品经过设计和加工后,需要验证其功能、性能和可靠性等指标,确保产品达到设计要求,为产品的最终验证和上市提供重要的数据支持。
产品前期质量策划和控制计划概述

Advanced Product Quality Planning and Control Plan
1
课程目的
1)了解APQP的5个阶段 2)了解每个阶段的具体操作 3)了解YFJC APQP的特殊过程 4)了解Control Plan的概念
2
APQP在整改生产制造过程中处于那个阶段?
1)组织小组 2)确定范围 3)小组间的联系 4)培训 5)客户与供方的参与 6)同步工程 7)控制计划 8)问题解决 9)产品质量的进度计划 10)与进度表有关的辅助计划
项目小组第一次会议的 内容包括那些?
小组间的联系模式有 那些?
培训包括内部的、供 应商的
模具计划、检具计划、设 备采购计划、等
7
12
产品设计和开发
设计分析 产品图面与规范
具有设计责任的产品
设计验证与评审 设备、工装、量具 需求及开发计划表 特殊产品和过程特性
外包规划
转换的图纸 样件控制计划 试验标准及结果 材料标准及结果 图纸ECO更改记录 分供方清单 材料等效替代申请 表
OTS样件制作和提交
第二阶段评审、反馈评审结果、制定纠正措施
PPAP样件+尺寸报告 YFJC对供应商
PSO
实施生产过程审
核
PPAP PACKAGE
材料替代报告
32
APQP 流程介绍
供应商启动会议
1 召开供应商启动会议的前提: YFJC 采购部完成产品定点; YFJC 发放SSOW,图纸、规范、技术要求等; 供应商已消化产品技术要求,产品开发进度等要求; 供应商已确定SDT名单等内部准备工作 2 会议参加人员:(至少包括以下范围) YFJC:技术中心、采购部、质量部、工厂 供应商:项目、技术、质量、销售 3 会议主要内容: 供应商反馈项目开发要求以及产品技术要求等消化结果; 双方对项目开发要求及产品技术要求等进行沟通并确定; 确定建立AQP跟踪及更新频次
产品质量先期策划程序(2)
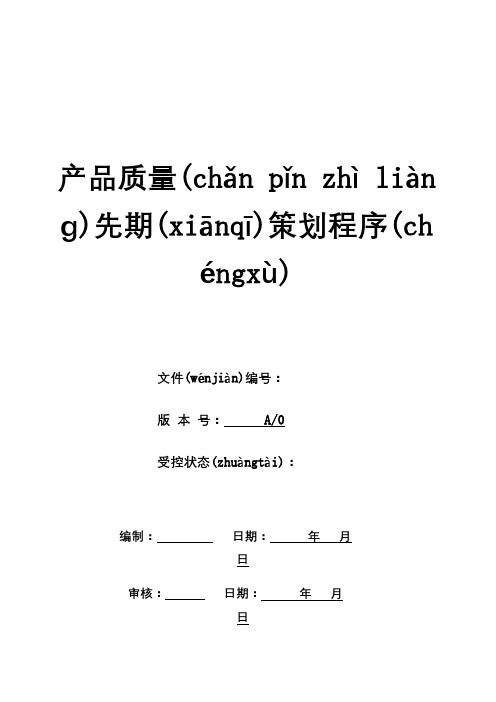
产品质量(chǎn pǐn zhì liàn ɡ)先期(xiānqī)策划程序(chéngxù)文件(wénjiàn)编号:版本号: A/0受控状态(zhuàngtài):编制:日期:年月日审核:日期:年月日批准:日期:年月日2014年11月1日发布(fābù) 2014年11月1日实施(shíshī)1.目的(mùdì):作为(zuòwéi)产品质量先期策划管理工作的规范,使之能快速有序的进行,从进度、质量、成本方面进行控制,确保新产品策划开发按期保质满足客户的需求并为之后的生产交付提供(tígōng)足够的前期规划。
2.适用范围:公司开发的所有(suǒyǒu)新产品。
3.定义(dìngyì):3.1项目小组 project team包括公司内部技术、生产、采购物流、质保、市场、人事行政等部门成员及供应商、客户方面代表。
3.2过程流程图 process flow chart对产品过程流程的系统描述,它用来分析制造、检验、流转、储存全部生产过程。
3.3场地平面布置图 site layout plan反映了制造过程中各个环节在生产场地中位置及流转状况,基本包括各道工位点、检验点、控制图位置、不同状态产品的摆放区域、存储等。
其材料流程要与过程流程图相协调一致。
3.4 潜在失效模式与效果分析 FMEA对新的/修改产品的潜在问题进行预防、解决或监控。
它包括设计FMEA、过程FMEA及系统FMEA,FMEA是一种动态文件,当发现新的失效模式时,项目小组需要对它进行评审和更新。
3.5 控制计划 control plan控制计划,在制造过程中对产品进行的尺寸测量和材料、功能试验的描述。
根据开发的不同阶段,它包括样件控制计划、试生产控制计划及生产控制计划。
首件检验控制程序

首件检验控制程序一、目的为了保证产品生产质量,在产品量产前对影响产品质量的因素和首件产品实物质量进行验证和确认,尽早发现生产过程中影响产品质量的因素,避免出现批量性质量问题。
二、范围适用所有新项目,新产品开发设计,供方提供产品等的首件新产品验证,设计、工艺变更后的首件检验以及每日批量生产前首件验证。
2.1在新开发产品首次上线生产时的首件检验。
2.1.1新产品的内部首检。
2.1.2新产品交付顾客前的外部首件检验(顾客有要求现场验证的情况)。
2.1.3供应商(外包、外购)提供的新产品首件检验。
2.2因后续设计、工艺更改等变化导致先前首检失效的首件检验。
2.3在批量生产过程中(每个生产班次开始加工的第一个工件,或加工过程中因换人、换料及换工装、调整机床等改变工序条件后加工的第一个工件)的首件检验。
三、定义3.1 P-FAI(Process XXX)即工序首检,是对工序的制程因素及其结果的验证。
3.2 FAI (XXX)即首件检验。
是指按照手艺文件的要求,对批量生产前的首个零(部或组)件进行周全的工序和成品搜检、考核,以确定零部件是否满足手艺要求,是否具备批量的、不乱的生产合格产品的本领。
3.3产品制造过程外包:公司提供技术要求(技术协议、图纸等)、必要时提供零部件(或原材料、半成品),要求供应商按技术要求进行相应工序加工的过程。
3.4外购:产品不是由组织(公司)设计的,通过选型向外界直接购买。
(四)职责4.1营销部门(或新产品项目组)4.1.1负责对客户提供技术资料、图纸等外来文件的审核、传递、归档。
4.1.2负责对客户所提供的图纸、验收准则等存在分歧的沟通协调处理。
4.1.3卖力提供产品的一切图纸、原材料清单、手艺标准、关键零部件清单等检验准则,编制内部首件检验计划。
4.1.4负责组织相关人员对供方提供的零部件新产品的首件验证及对产品制造过程外包的首件验证,对其它新产品的首样验证要求供方提供相关资料。
产品试产量产总结报告

产品试产量产总结报告一、引言产品试产量产是指在产品研发和设计完成后,进行小批量生产和试制的阶段。
通过试产量产,可以验证产品的可行性、性能和质量,并为后续的大规模生产做准备。
本报告旨在对产品试产量产阶段的工作进行总结,分析存在的问题并提出改进措施,以期提高产品的生产效率和质量。
二、试产量产过程总结1. 生产计划安排在试产量产阶段,需要根据产品的特性和市场需求,合理安排生产计划。
这包括确定生产任务、制定生产流程、安排生产人员和设备等。
在实际操作中,我们按照计划进行生产,并及时调整和优化生产过程,以保证产品的准时交付。
2. 工艺流程优化在试产量产过程中,我们不断优化产品的工艺流程,以提高生产效率和产品质量。
通过对工艺流程的分析和改进,我们发现了一些可以简化或优化的环节,如减少不必要的加工步骤、优化工艺参数等。
通过这些优化措施,我们有效提高了产品的生产效率和质量稳定性。
3. 质量控制在试产量产过程中,质量控制是至关重要的环节。
我们建立了一套完善的质量控制体系,包括原材料的选择和检验、生产过程中的质量监控、成品的检验和测试等。
通过严格执行质量控制标准,我们确保了产品的质量稳定性和一致性。
4. 问题分析与改进在试产量产过程中,我们积极分析和解决存在的问题,以提高产品的生产效率和质量。
通过对问题的深入分析,我们找出了问题的根源,并采取相应的改进措施。
例如,在生产过程中出现的质量问题,我们及时调整工艺参数,优化生产流程,以确保产品的质量符合标准。
三、存在的问题及改进措施1. 生产效率低下在试产量产过程中,我们发现生产效率不高的问题。
主要原因是生产流程中存在一些瓶颈环节,导致生产进度滞后。
为了提高生产效率,我们需要进一步优化生产流程,缩短生产周期。
同时,加强对生产设备的维护和保养,以确保设备的正常运行。
2. 质量波动较大尽管我们在质量控制方面做了很多工作,但仍然存在质量波动较大的问题。
这主要与产品设计和生产工艺的不稳定性有关。
新品量产前工作流程

新品量产前工作流程一、项目启动阶段1、需求沟通与明确:接收产品设计方案后,与产品设计师进行需求分析与沟通,明确产品的设计、功能和性能要求。
2、市场调研:进行市场调研,了解目标用户群体的需求和偏好,了解竞品产品的优劣势,为产品的量产提供参考。
3、初步评估:根据产品设计方案和市场调研的结果,进行初步评估,确定产品的量产可行性,制定初步的量产计划和预算。
4、团队组建:根据产品设计方案的要求,组建相应的生产研发团队,确定各个团队的负责人和成员。
5、立项决策:进行项目立项决策,确定产品量产的目标和时间节点,制定项目执行计划和目标。
二、工艺准备阶段1、工艺设计:根据产品的设计要求,制定工艺流程和生产工艺指导书,确定产品的生产工艺路线。
2、设备采购:根据工艺设计,确定生产所需的设备、工具和生产线,进行设备的采购和调试。
3、原料采购:根据产品生产的要求,确定原料的选型和采购渠道,进行原料的采购和检验。
4、生产线布局:根据设备和工艺要求,进行生产线的布局规划,确定生产车间的区域划分和工位设置。
5、人员培训:根据工艺要求,进行生产人员的培训和技能提升,确保员工熟悉生产流程和操作规程。
三、生产试制阶段1、样品制作:根据工艺设计和原料采购,进行样品制作,进行生产工艺的验证与调整。
2、设备调试:进行设备的调试和参数设置,确保设备的正常运行和生产效率。
3、生产试运行:根据样品制作和设备调试的结果,进行生产试运行,验证生产工艺和生产线的稳定性和可靠性。
4、质量控制:对生产过程进行质量控制和监督,确保产品的质量达到设计要求。
5、生产数据分析:对生产数据进行分析,找出生产过程中存在的问题和改进的方向,确保生产过程的优化和改进。
四、量产准备阶段1、生产计划制定:根据产品的量产需求和生产技术要求,制定生产计划和生产排程。
2、生产指导书制订:根据生产工艺和工艺要求,制定产品的生产指导书和作业指导书,确保生产过程的标准化和规范化。
3、质量管理体系建立:建立质量管理体系和质量控制流程,确保产品的质量可控和可持续。
量产前试产可行性评估报告
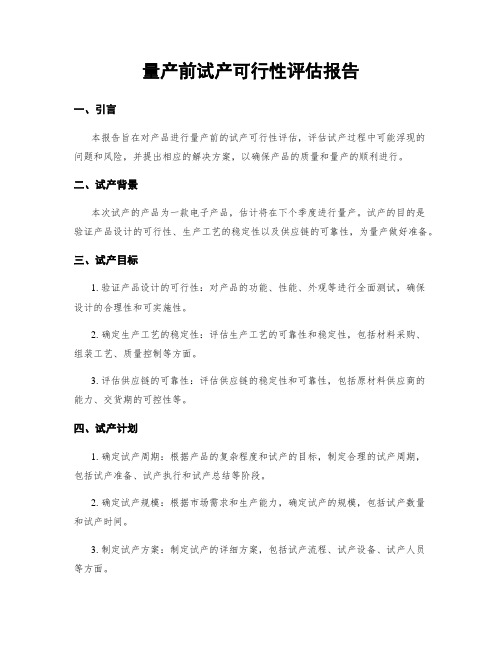
量产前试产可行性评估报告一、引言本报告旨在对产品进行量产前的试产可行性评估,评估试产过程中可能浮现的问题和风险,并提出相应的解决方案,以确保产品的质量和量产的顺利进行。
二、试产背景本次试产的产品为一款电子产品,估计将在下个季度进行量产。
试产的目的是验证产品设计的可行性、生产工艺的稳定性以及供应链的可靠性,为量产做好准备。
三、试产目标1. 验证产品设计的可行性:对产品的功能、性能、外观等进行全面测试,确保设计的合理性和可实施性。
2. 确定生产工艺的稳定性:评估生产工艺的可靠性和稳定性,包括材料采购、组装工艺、质量控制等方面。
3. 评估供应链的可靠性:评估供应链的稳定性和可靠性,包括原材料供应商的能力、交货期的可控性等。
四、试产计划1. 确定试产周期:根据产品的复杂程度和试产的目标,制定合理的试产周期,包括试产准备、试产执行和试产总结等阶段。
2. 确定试产规模:根据市场需求和生产能力,确定试产的规模,包括试产数量和试产时间。
3. 制定试产方案:制定试产的详细方案,包括试产流程、试产设备、试产人员等方面。
五、试产过程及问题分析1. 试产准备阶段:对试产所需的材料和设备进行采购,建立试产流程和质量控制标准。
2. 试产执行阶段:按照试产方案进行试产,对产品进行全面测试和评估。
问题1:在试产过程中,发现部份原材料的交货期延迟,导致试产进度受到影响。
解决方案:与供应商密切合作,要求加快交货进度,或者寻觅备用供应商。
问题2:在试产过程中,浮现了一些产品质量问题,如组装不良、功能异常等。
解决方案:加强质量控制,优化生产工艺,对不良品进行返工或者淘汰。
3. 试产总结阶段:对试产过程进行总结,分析问题原因,提出改进措施。
问题3:试产周期较长,导致产品交付时间延迟。
解决方案:优化试产流程,提高生产效率,缩短试产周期。
六、风险评估1. 供应链风险:原材料供应商无法按时交货,导致试产进度延迟。
2. 技术风险:产品设计存在缺陷,无法满足市场需求。
食品行业新产品研发、试产、量产流程

新产品研发试产流程对于食品生产企业,每个产品都有生命周期,再成熟的产品也要根据市场的发展而改良,产品的改良和新产品的研发不仅能延续产品周期,还能拓宽公司品牌的市场领域,创造更大价值。
但一个成功的新产品面世往往需要反复的论证、实验,在一次次失败中不断的积累经验和提升。
今天在这里结合自身经验,和大家一起梳理下,新产品研发试产的流程,望各位在相关的工作中少走些弯路。
项目策划:召开新产品策划会议,讨论新产品研发计划内容,明确分工、要求和进度。
研发过程:1.研发准备:确定研发进度,收集与产品质量、安全相关的法律、法规、标准,准备新产品研发所需要的原辅料。
2.样品制作:研发人员在实验室进行配方设计和样品制作,根据产品的难易和复杂程度规定好样品研发周期。
3.样品评估:完成的样品获得产品策划人员的确认和反馈,并进行稳定性评估实验和保质期验证,并把相关信息反馈到各部门。
4.结果输出:对新产品的试产工艺流程、配料表、基本信息、原辅料验收标准、添加剂资料等进行输出,核算成本,制定新产品质量安全管理体系文件,进行新产品第三方送检包括营养成分检测,对新产品标签及外箱设计信息进行输出。
生产线评估:各部门联合对生产线进行评估,若需要增加投资,改造生产线时,共同制定技改方案,并进行评审和实施。
新产品试产:1.小试准备:制定小试计划,包括产量、包装要求、时间等,准备原辅料,对小试相关人员进行工艺流程、感官确认等方面的培训。
2.小试过程:对新产品工艺符合性、设备参数、设备运行情况进行跟踪、记录,对样品进行确认,并对小试产品进行检验,必要时进行工艺参数调整。
3.小试评估:小试产品获得产品策划人员的确认和反馈,小试过程中出现的问题进行汇总必要时工艺进行改进,对小试样品的货架期稳定性及口味进行测试,样品作为新产品SC扩项或增项的申报样品。
4.中试准备:小试结果符合要求,可安排中试,拟定中试产量,准备原辅材料及最新的中试工艺文件。
5.中试过程:对中试过程中的各项工艺参数、设备参数、清洗情况进行跟踪、记录,并对中试产品进行检验。
产品量产的初期管理

产品量产的初期管理编号:修改履历版次/修改码A/0 页码1/7修修改页码更改前更改修改人/日批准人A/0 全部- 新版生成程冰蕾/20141022一、目的监控新产品量产转交后生产初期(人、机、料、法、环、测)等影响质量因素的管理,确保早期产品质量稳定。
二、适用范围适用于所有新产品及其改进型新型号产品开发完成后转交量产的产品生产。
三、定义.3.1初期管理:为确保初期产品的质量和工序的早期稳定化,进行量产以后在一定期间(以下,初期管理期间)和数量(批次、吨数等)的质量保证活动。
3.2.初期管理时间:根据产品生产控制难易程度在进行初期管理活期间决定初期数量或时间,要通过以下原则:(客户另行规定除外)分类期间生产数量重要客户的产品量产后6个月20吨非重要客户量产后1个月5批次3.3初期产品:初期管理期间生产的全部产品(合格品、各种废料含落地料、高铁料、筛上料、清洗料等)。
3.4初期产品评价:在初期管理期间,以判断产品质量的正确、设计质量、工序配备、设备稳定上的问题点的措施、改善为目的的初期产品的质量的确认活动。
3.4初期产品管理:对处理产品从生产过程、入库、销售过程,按规定措施采取管理活动。
四、职责与权限4.1研发中心:负责完成新产品的项目开发、客户对新品的确认、技术文件及文档归档管理,将整套生产的应用文件、标准、规范、样品等转、教生产系统进行量产,并指导量产与解决量产中出现的技术问题。
4.2工艺工程部:负责量产初期生产过程的技术、工艺工作,包括生产工艺稳定、生产培训与指导、设备稳定评估以及生产过程出现的技术、工艺等问题的组织解决。
4.3质量部:负责产初期生产过程的质量监控与评估以及决定初期管理的限定条件解除。
4.4生产工厂:按公司经营计划与客户订单状况组织生产量产,包括定额合格生产人员、合格稳定生产设备、满足量产的生产环境与场所等。
4.5采购部:负责提供满足量产的合格物料。
4.6其他部门:按各自职能对生产量产进行支持与配合,完成部门承担的职责。
初期产品品质规划(APQP).

先期产品质量规划(Advanced Product Quality Planning)11. 产品开发各阶段规划作业任务◆:主要负责◇:协助办理22. 先期产品质量规划各阶段作业要点33. 设计管制作业程序1. 目的:将本公司所委托制造(OEM)及委托设计与制造(ODM)生产零件,建立并维持书面程序,藉以管制与查证产品之设计及生产规划,以确保规定要求得以达成。
2. 范围:适用于本公司各项新产品的设计开发作业,及技术移转的OEM&ODM产品生产规划作业执行。
3. 权责:3.1 业务部:负责新产品市场需求调整及客户联络,提出样品需求单; 3.2 研发部:负责产品开发/设计执行,试产时生产技术支持; 3.3 生管部:负责量试阶段材料购入及生产日期安排; 3.4 制造部:负责试产阶段的制造;3.5 品保部:负责量试阶段验证之质量作业执行;3.6 质量规划小组:负责产品设计阶段审查之工作,其组织权责如附件一。
4. 作业要点:4.1 产品类别及设计适用阶段如下表:◆:代表每阶段必须实施。
◇:代表视需要选择实施或不实施。
4.2 产品设计管制各阶段流程(附件二)。
4.3 规划评估阶段:4.3.1 业务部或研发部于产品设计研发规划时,得考虑下列情况信息输入。
a. 搜集公司年(月)产能预估;b. 客户满意度调查结果;c. 产品质量履历;d. 竞争厂商之质量;e. 交货状况;f. 客户需求之产品图面、规格及参考样品等。
44.3.2 业务部或产品设计提案部门依4.3.1项信息需求,提出「样品需求单」依「客户索样设计评估作业程序」规定,实施审查核准。
4.3.3 样品需求提案受理研发部设计担当人员受理「样品需求单」赋与项目设计编号后,依需求单内容及其它相关数据进行如4.3.1所述设计评估,必要时召集相关部门检讨并完成下列任务。
a. 「制造能力评估表」作成(参照客户索样及设计评估作业程序);b. 初步流程图作成(附表一);c. 材料、规格清单;d. 开发进度管制表(附表二)。
从样品走向量产--产品试制验证管理

从样品走向量产--产品试制验证管理课程背景我们在为企业提供研发管理咨询服务的过程中发现,很多企业的新产品开发从样机到量产的过程中(产品化过程)存在着共同的问题:1. 新品没有经过中试或中试的时间很短,制造部门戏称研发的新品是“三无”产品,没有生产文件、没有工装、生产现场出了问题没人管;2. 转产没有标准,研发想快点转产,生产对有问题的产品又不愿接收,希望研发把问题都解决了才转过来,而市场又催得急,经常被迫接收,长此以往,导致研发与生产的矛盾激化;3. 有些企业开始成立中试部门,希望在中试阶段把产品质量问题解决掉,但中试的定位与运作也很困惑,发生质量与进度的冲突时,如何取舍与平衡,以前研发与制造的矛盾转化为研发与中试、中试与生产的矛盾,中试成了矛盾集散中心;4. 市场的压力并不因中试的产生而减少,中试需要从哪些方面努力才能满足产品的质量、进度的要求?中试的业务是面向研发还是面向制造,还是兼而有之?5. 量产后才发现产品可制造性差、成品率低、经常返工,影响发货;6. 产品到了生产后还发生大量的设计变更;7. 产品到了客户手中还冒出各种各样的问题以致要研发人员到处去“救火”……本课程将基于多年的实践、长期的研发咨询积累,总结出一套理论与实践相结合的可操作的方法,配以大量实际案例,以指导研发/试产/制造部门主管如何高效的实现产品从样品走向量产。
培训收益1、业界公司在不同发展阶段的产品中试管理模式与实践2、面向制造系统的产品设计(DFM)的方法与实施过程3、面向生产测试的产品设计(DFT)的方法与实施过程4、面向制造系统的新产品验证的过程与方法5、在满足质量标准的前提下缩短产品试制周期的方法和技巧6、如何建立从样品到量产的管理机制课程内容一、案例研讨二、从样品到量产概述1. 企业在追求什么:技术?样品?产品?商品?2. 研发与制造的矛盾:1)制造系统如何面对研发的三无产品?2)研发如何面对制造系统越来越高的门槛?3. 研发与制造矛盾的激化:中试的产生成为必然4. 中试的定位与发展:1)研发(RD)、中试(D&P)、生产(P)的关系2)中试的使命是什么?3)中试如何定位?4)中试的发展问题:* 大而全?* 专业化分工?* 产品线划分与共享平台* 中试人员的发展定位:广度与深度问题5. 中试的业务范围1)中试业务:新产品导入(NPI)2)承上:如何面向产品的研发?3)启下:如何面向产品的制造?4)桥梁:中试作为连接研发与制造的桥梁,独木桥还是阳关道?6. 演练与问题讨论根据企业的实际情况,是否需要建立并发展中试的职能?三、新产品导入团队1. 新产品导入团队的构成1)工艺工程2)设备工程3)测试工程4)工业工程5)产品验证6)试生产(计划、生产、质量)2. 新产品导入团队的职责3. 新产品导入团队与产品开发团队的关系1)开发模式的演变:串行变并行2)并行工程在产品开发中如何体现?3)新产品导入团队如何提前介入研发?* 为什么要提前介入?* 提前到什么时候介入?* 提前介入做什么?4)新产品导入团队的管理* 新产品导入团队与产品开发团队、职能部门的沟通* 新产品导入团队成员的汇报、考核和管理机制4. 演练与问题讨论根据企业的实际情况,研讨建立新产品导入团队的时机四、面向制造系统的产品设计(DFM)1. 如何在产品设计与开发过程中进行可制造性设计1)从制造的角度来看产品设计2)工艺人员介入产品开发过程的切入点:从立项就开始3)工艺管理的三个阶段:工艺设计、工艺调制与验证、工艺管制4)工艺设计:* 如何提出可制造性需求?* 需要哪些典型的工艺规范?* 可制造性需求如何落实到产品设计方案中?* 工艺设计与产品设计如何并行?* 产品工艺流程设计* 电装、整装、包装与物流的可制造性设计分析* 如何确保可制造性需求在产品开发中已被实现?* 工艺评审如何操作?* 什么时候考虑工装?* 如何在开发过程中同步输出工艺文件与生产操作指导文件5)工艺调制与验证* 工艺验证的时机* 工艺验证方案包括哪些内容?* 如何实施工艺验证?* 工艺验证报告的内容* 如何推动工艺验证的问题解决?* 研发人员如何配合新产品的工艺验证?* 制造外包模式下的工艺如何验证?6)工艺管制* 工艺管制的困惑:救火何时是尽头?* 工艺转产评审(标准、流程、责任)* 量产过程中的例行监控与异常管理2. 演练与问题讨论分析学员企业的工艺管理工作做到什么程度?存在哪些差距?3. 工艺管理平台建设1)谁负责工艺平台的建设?2)工艺委员会的产生:责任与运作模式3)如何进行工艺规划?4)基础工艺研究与应用5)支撑工艺管理平台的四大规范:* 品质规范* 设备规范* 工艺规范* 设计规划6)工艺管理部门如何推动DFM业务的开展?7)工艺体系的组织构成、发展与演变8)工艺人员的培养与技能提升4. 演练与问题讨论分析学员企业的工艺平台建设工作做到什么程度?存在哪些差距?如何改进?五、面向生产测试的产品设计(DFT)1. 基于产品生命周期全流程的测试策略1)研发测试(Alpha)、试验局测试(Beta)、生产测试2. 研发测试(Alpha)与BETA测试1)测试人员介入产品开发过程的时机(提可测试性需求的时机)2)可测试性需求需要考虑的内容(示例)3)单元测试、模块测试、系统集成测试、专业化测试、BETA测试的重点分析4)产品开发过程中测试业务流程分析5)企业在不同的发展阶段如何开展测试的相关工作(短平快的项目测试工作如何开展)3. 面向生产测试业务的产品设计与开发1)生产测试业务流程分析2)典型的部品测试、整机测试方法介绍3)开发专门的生产测试工装的条件分析4)生产测试工装的开发管理5)在产品开发过程中如何实施面向生产测试的产品设计?* 如何提出可测试性需求?* 可测试性需求如何落实到产品设计方案中?* 研发面对众多的需求如何取舍?可测试性需求的优先级分析* 如何在产品开发过程中同步开发生产测试工装?* 如何在产品开发过程中同步输出生产测试所需的操作指导文件?* 如何进行测试工装的验证?* 如何推动测试验证问题的解决?6)如何推动可测试性设计(DFT)业务的开展7)如何进行测试平台的建设?4. 演练与问题讨论分析学员企业的DFT工作做到什么程度?存在哪些差距?如何改进?六、产品试制验证管理1. 影响产品试制周期的因素分析2. 研发人员对试制准备提供的支持3. 试制团队的构成、职责与定位(设置试制部门的时机与优缺点分析)4. 试制人员介入产品开发过程的时机1)如何进行试制准备(准备要素示例)5. 面向制造系统的验证1)研发人员如何在试制过程中进行产品设计的优化2)制造系统的验证策略与计划3)制造系统的验证方案4)如何实施制造系统的验证:* 工艺验证(工艺流程、工艺路线、单板工艺、整机工艺、包装工艺、物流工艺)* 工装验证(装配工装、测试工装、生产设备)* 结构验证* 产品数据验证(BOM验证、制造文档验证)* 产品试制验证(质量、效率、成本)5)批次验证报告,验证多少批才合适?6)如何推动验证问题的解决?6. 转产评审1)研发人员如何支持新产品的转产工作2)转产评审的评审组织如何构成?* 评审标准是什么?* 如何判定是否转产?* 评审流程与运作机制7. 产品转产后的管理1)新产品的试制效果评价2)新产品的质量目标达成情况3)工程变更管理4)缺陷与问题管理5)质量审计8. 演练与问题讨论分析学员企业的产品试制验证过程,分析差距,提出改进建议讲师资质 Charles 资深顾问专业背景十几年高科技行业从业背景,丰富的研发管理咨询经验,在国内某大型知名企业工作近10年,主持和参与过多个大型产品的研发工作,先后担任过开发工程师、项目经理、产品经理、新产品导入部总监、研发项目管理部总监等职位。
- 1、下载文档前请自行甄别文档内容的完整性,平台不提供额外的编辑、内容补充、找答案等附加服务。
- 2、"仅部分预览"的文档,不可在线预览部分如存在完整性等问题,可反馈申请退款(可完整预览的文档不适用该条件!)。
- 3、如文档侵犯您的权益,请联系客服反馈,我们会尽快为您处理(人工客服工作时间:9:00-18:30)。
供应商代码零部件号
日期
海马汽车AQE 签名
日期
序号
技术要求
检查/试验方法
备注
1
密度要求:24~27g/L/黑色
1量杯重量电子称重/黑色
2186g~195g
电子称重3不可有破损、缺料、萎缩、进料不饱、起
鼓、变形不良。
目视4毛边2mm以下、破损不可有,料枪/顶杆凹凸要求在±1mm,进料不饱要求连续3料以
下可放行。
目视5尺寸见图纸,附件1
游标卡尺/卷尺6156g~186g
电子称重7产品外观无破损、脏污、混料。
标签信息
与实物信息相符。
目视零部件名称前缓冲块
SA14-50-330
产品量产初期验证计划
供应商名称郑州双燕塑料泡沫有限公司
101-ZD078每批来货检查
100%全检
成品外观检查100%全检
成型湿重检查2h/1次
成型外观检查原材料密度/外观检验
每批抽测5pcs检查并记录
包装检查100%全检
供应商签名检查项目
检查/试验频次
成品尺寸检查每批抽测5pcs检查并记录
成品重量检查。