基于ASME B31G准则的油气管道腐蚀安全性评估
基于爆破试验数据对腐蚀管道剩余强度评定方法的验证

(3)
式中 UTS ———极限拉伸强度 ,MPa
d ———缺陷深度 ,mm
Q ———长度校正系数
113 PCORRC 方法
PCORRC 方法的公式如下 :
pb
=σu
2t D
{
1
-
d t
[1
-
exp (
-
01157
×L
) ]}
(4)
R ( t - d)
式中 σu ———管道实际失效压力时的真实拉伸强
·5 ·
© 1994-2009 China Academic Journal Electronic Publishing House. All rights reserved.
CPVT 基于爆破试验数据对腐蚀管道剩余强度评定方法的验证 Vol231No10 2006
轴向和弯曲载荷 。此标准分别针对单一缺陷 、交互
作用缺陷 、复杂缺陷开发了不同的方法 。本文主要
研究内压作用下的单一缺陷 , 故下面给出单一轴向 腐蚀缺陷在只有内压作用下 , 许用应力法的失效压 力计算公式 :
pf
=
2 tUTS D- t1
1 -
- d/ t d/ ( tQ)
(2)
Q = 1 + 0131 ( L / Dt ) 2
《确定腐蚀管线剩余强度的手册 ———补充部分》[2] 。 1999 年 ,由英国燃气公司 BG 和挪威船级社 DNV 合 作开发了 DNV - RP - F101 标准[3] ,该标准提供了两 种腐蚀缺陷评价方法 :分项安全系数和许用应力法 。 最近 ,一些研究者提出了 PCORRC ( Pipeline CORRo2 sion Criterion) [4] 方法 , 用于评价含钝口腐蚀缺陷的 中高强度等级管道由塑性失稳导致失效的剩余强 度 。虽然 , PCORRC 方法开发的时间较短 , 但其在改 善评价方法的保守性方面表现出了优越性 。
输油臂腐蚀评估模型的建立与应用

㊀2019年㊀第2期Pipeline㊀Technique㊀and㊀Equipment2019㊀No 2㊀收稿日期:2018-09-05输油臂腐蚀评估模型的建立与应用练㊀斌1,李松林2,王海锋1,赵元元1(1.中海油(天津)管道工程技术有限公司,天津㊀300452;2.中海油能源发展股份有限公司工程技术分公司,天津㊀300452)㊀㊀摘要:码头输油臂常年处于海洋大气环境,且输送介质本身也具有腐蚀性,对输油臂进行腐蚀检测评估可以判断输油臂的腐蚀严重程度,为输油臂的安全运行㊁维护保养和检测提供参考㊂文中依据ASMEB31G 2009和TSGD7003 2010规范,介绍3种适用性分级评价,以某码头输油臂腐蚀检测数据为例,对该输油臂进行了腐蚀评价,确定了该输油臂的最大允许工作压力㊁剩余服役寿命和下一次检测时间㊂关键词:输油臂;适用性分级;剩余寿命评价;检测周期中图分类号:TE985㊀㊀㊀文献标识码:A㊀㊀㊀文章编号:1004-9614(2019)02-0053-04EstablishmentandApplicationofCorrosionAssessmentModelforOilDeliveryArmLIANBin1,LISong⁃lin2,WANGHai⁃feng1,ZHAOYuan⁃yuan1(1.CNOOC(Tianjin)PipelineEngineeringTechnologyCo.,Ltd.,Tianjin300452,China;2.CNOOCEnerTech⁃Drilling&ProductionCo.,Tianjin300452,China)Abstract:Wharfoildeliveryarmisalwaysinthemarineatmosphericenvironment,andthetransportmediumitselfiscorro⁃sive,corrosiondetectionandevaluationofoildeliveryarmcandeterminetheseverityofoildeliveryarmcorrosion,forthesafeoperation,maintenanceandtestingofoildeliveryarmprovidesreference.BasedontheASMEB31G 2009andTSGD7003 2010specifications,thispaperintroducedthreeapplicabilitygradingevaluations.Takingthecorrosiondetectiondataofawharfoildeliveryarmasanexample,thecorrosionevaluationoftheoildeliveryarmwerecarriedout,andthemaximumallowableworkpressureoftheoildeliveryarm,remainingservicelifeandnextinspectiontimeweredetermined.Keywords:oildeliveryarm;applicabilityrating;residuallifeevaluation;detectioncycle0㊀引言输油臂实际应用越来越多㊂受海边潮湿㊁盐雾环境影响,输油臂腐蚀严重㊂为了确保设备的运行稳定,输油臂的评估很重要㊂1㊀输油臂的结构输油臂,是安装在码头,用于完成液态石油化工产品的装㊁卸船作业任务的设备,具备适应不同潮汐㊁干舷及船体运动的能力,是一种高效㊁安全的油品码头装卸设备㊂输油臂由立柱㊁支承㊁内臂㊁外臂㊁旋转接头㊁平衡系统等部分组成㊂2㊀基于ASMEB31G—2009的适用性评价适用性评价根据收集的数据数量和质量,采用分级评价的理念,分为3个等级,ASMEB31G 2009[1]是专用于管道腐蚀缺陷目标适应性评估方面的标准㊂依据ASMEB31G 2009在对缺陷进行适用性评价[2]时,先进行Level0评价,若评价结果为缺陷不允许,则依次进行Level1㊁Level2评价[2-6]㊂2.1㊀适用性分级2.1.1㊀Level0依据缺陷的长度㊁深度等参数进行评价,不需要进行详细计算㊂依据相关记录或现场检测结果确定管道壁厚和外径;确定材料特性MAOP㊁SMYS㊁SMTS等;确定清洗缺陷表面后的轴向长度L和最大深度d;依据ASMEB31G 2009中对应管道外径D和名义壁厚t,确定最大允许缺陷长度Lᶄ;如果LᶄȡL,则缺陷可以接受,如果Lᶄ<L,则缺陷不可接受㊂注意:评价时应注意下列条件:如果壁厚减薄小于10%,则评价进不需要考虑缺陷长度;如果壁厚减薄大于80%,则缺陷不予评价,应开展进一步评估㊂2.1.2㊀Level1根据测量金属损失的轴向拉伸和最大深度,进行㊀㊀㊀㊀㊀54㊀PipelineTechniqueandEquipmentMar 2019㊀简单计算㊂依据相关记录或现场检测结果确定管道壁厚和外径;确定材料特性MAOP㊁SMYS㊁SMTS等;确定清洗缺陷表面后的轴向长度L和最大深度d;确定安全系数SF,计算缺陷参数z,流变应力Sflow,鼓胀系数M,评估的管道失效压力pF,评估的管道安全操作压力pS,评估的失效应力SF㊂pF㊁SF的单位均为MPa㊂z=L2/(Dt)(1)Sflow=1.1ˑSMYS(2)M=(1+0.8z)1/2(3)SF=Sflow1-23(d/t)1-23(d/t)/Méëêêêêêùûúúúúú㊀㊀(zɤ20)(4)SF=Sflow(1-d/t)㊀㊀(z>20)(5)pF=SFD(2tnom)(6)pS=pF/SF(7)式中:tnom为管道的名义壁厚;z为中间参量;Sflow为流变应力,对于普通碳钢且服役温度小于120ħ的管道,Sflow=1.1SMYS且SflowɤSMTS;SF为安全系数,对于塑性材料,1.5ɤSFɤ2.0,保守评价取SF=2.0㊂p为设计压力,若pFȡSFˑp,则缺陷可以接受,设备可以继续使用;否则,缺陷不能接受,应采取降压㊁修复或更换措施[3]㊂2.1.3㊀Level2二级评价比一级更详细,目的是更精确地评价失效压力,更精确地测量腐蚀表面的轮廓,考虑金属损失的实际分布㊂L2级评价的流程和方法与L1级评价相同,只是SF的计算公式有所变化:SF=Sflow1-(A/A0)1-(A/A0)/Méëêêùûúú(8)式中:A为轴向平面上的缺陷投影面积,通过划分网格测量缺陷处的金属损失并制作轴向金属损失剖面图,据此进行迭代或积分求解;A0为缺陷区域的原始金属面积,A0=Lt㊂2.2㊀实例计算以渤海某作业码头输油臂为例,此输油臂直管段外径均为323.900mm㊁名义壁厚为9.530mm(基础数据见表1),因此应查表Table3-3M(图1)确定缺陷的最大允许轴向长度㊂对此次导波检测到的缺陷进行评价,结果见表2㊂由于缺陷的最大深度为0.486mm(图1中最接近的一行是d=0.5mm),管道名义壁厚为9.530mm(图1中最接近的一列是t=9.3mm),据此查表确定的缺陷最大允许轴向长度为 Nolimit(无限制) ,因此此次导波检测到的所有缺陷都是允许的㊂图1㊀ASMEB31G—2009Level0评价时管道(管径273 406mm)允许的最大轴向缺陷长度表表1㊀渤海某码头输油臂基础参数数据名称数据值备注设计压力p1MPa取自设计资料设计系数F0.4按保守原则取0.4输油臂直管段外径D323.90mm取自设计资料名义壁厚tnom9.530mm取自设计资料屈服强度SMYS289MPa取自设计资料要求的最小屈服强度抗拉强度SMTS415MPa取自设计资料要求的最小抗拉强度输油臂服役时间T16a输油臂设备自2002年投入使用,至2018年已经服役16a表2㊀检测数据的缺陷评价结果缺陷位置缺陷深度相对深度/%绝对深度/mm允许的缺陷最大轴向长度缺陷是否可以接受1.75m处5.10.486无限制接受输油臂A外臂管道-检测点32.86m处2.40.229无限制接受3.31m处2.10.200无限制接受输油臂B立柱管道-检测点12.42m处5.10.486无限制接受4.41m处2.60.248无限制接受输油臂B内臂管道-检测点24.16m处3.20.305无限制接受5.00m处3.60.343无限制接受此外,根据ASMEB31G 2009的Level1评价方㊀㊀㊀㊀㊀第2期练斌等:输油臂腐蚀评估模型的建立与应用55㊀㊀法,依据式(1) 式(7),对检测得到的缺陷深度最大的缺陷(即输油臂B立柱管道检测点1的2.42m处和输油臂A外臂管道检测点3的1.75m处缺陷进行了适用性评价㊂根据表1的设备基础数据,D=323.900mm,tnom=9.530mm,SMYS=289MPa,d取导波检测中的最大缺陷深度(d=0.486mm),p=1.0335MPa㊂表3给出了从缺陷轴向长度L=0直到L=248.466mm范围内的SF㊁pF㊁pS以及缺陷是否接受的评价结果㊂从表3可以看出,在检测缺陷存在条件下,管道的最小pS为9.11MPa,也大于SFˑp=2.067MPa,因此缺陷可以接受,输油臂可以继续使用㊂表3㊀ASMEB31G 2009Level1评价方法对输油臂缺陷的评价结果缺陷轴向长度L/mm中间参量z鼓胀系数M失效应力SF/MPa评估的失效压力pF/MPa评估的安全操作压力pS/MPa缺陷是否可以接受001.000317.918.719.36接受40.0000.5181.189316.118.609.30接受80.0002.0731.631313.618.469.23接受120.0004.6652.175312.018.369.18接受160.0008.2932.763310.918.309.15接受200.00012.963.371310.218.269.13接受240.00018.6603.991309.718.239.12接受248.46620.0004.123309.618.229.11接受>248.466>20.000>4.123301.717.758.88接受3㊀依据TSGD7003 2010标准计算剩余寿命和检验周期3.1㊀剩余寿命计算根据TSGD7003 2010提供的管道腐蚀剩余寿命计算公式(式(9))计算输油臂的剩余寿命[7-8]㊂RL=CˑSMtGR(9)SM=计算失效压力屈服压力-MAOP屈服压力(10)式中:RL为管道腐蚀寿命;C=0.85;SM为安全裕量;MAOP为管段许用压力;GR为腐蚀速率;t为名义壁厚㊂按照式(9)和式(10),计算失效压力取pF=17.75MPa,管段许用压力MAOP为设计压力p,名义壁厚t为tnom=9.53mm,腐蚀速率GR=d/T=0.486/16=0.03mm/a,则:RL=CˑSMˑt/GR=15.65a即在检测的缺陷存在下,输油臂至少可以继续服役15.65a㊂3.2㊀检验周期计算TSGD7003 2010给出的检验周期表[8-9]如图2所示㊂此次检测采用的是直接检验方法,所以应根据操作条件下的应力水平与SMYS的数量关系确定㊂图2㊀TSGD7003 2010给出的全面检验周期表在缺陷评价中,设定设计系数F=0.4,即设定输油臂在运行过程中的最大应力不能超过0.4SMYS㊂评价结果表明输油臂的最大允许工作压力MAWP=2.42MPa,大于设计压力p=1.0335MPa,表明评价过程中考虑的应力水平实际上是大于输油臂实际操作条件下的应力水平的,因此根据图2操作条件下的应力水平应选择30% 50%SMYS一列[8]㊂由于此次只选择了一些关键位置进行检测,与TSGD7003 2010标准中对直接检测中的抽样检测危险迹象的规定一致,并且检测过程中也发现输油臂的壁厚有减薄现象,特别是弯头部位减薄比较严重,因此检验周期定为5a㊂在导波检测的缺陷评价中,评价得到的安全操作压力为pS=8.88MPa,根据PD=2tσ公式,可以估算出输油臂的最大应力为σ=pSD/(2tnom)=150.90MPa(可根据SF/SF来估算安全操作条件下的最大应力,取评估的失效应力为SF=301.7MPa,则安全操作条件下的最大应力为SF/SF=301.7/2.0=150.85MPa),约为SMYS的52%㊂因此根据图2操作条件下的应力水平应选择ȡ50%SMYS一列㊂由于检测技术只能检测到体积型缺陷的深度和位置,而不能对缺陷的轴向长度进行量化检测,与TSGD7003 2010标准中对直接检测中的抽样检测危险迹象的规定一致,所以检验周期㊀㊀㊀㊀㊀56㊀PipelineTechniqueandEquipmentMar 2019㊀定为5a㊂综合上述分析,检验周期定为5a,即在5a后应再对输油臂进行全面检测,检查输油臂的壁厚减薄和缺陷发展状况,掌握输油臂的安全状况,并对影响输油臂安全运行的隐患和缺陷及早采取维修护措施,确保输油臂运行的安全高效㊂4 结束语按照ASMEB31G 2009对检测缺陷的适用性评价结果,输油臂A和B的剩余服役寿命为15.65a,同时确保后续输油臂运行安全,需要收集更多的数据以进一步分析输油臂的腐蚀情况和安全状态,建议5a后对输油臂进行全面检测,重点检测弯头部位的壁厚减薄状况,并检查是否有局部腐蚀或点蚀发生,同时,在今后的检测和维护保养工作中应对立柱弯头(特别是外侧)和三向回转接头弯头(特别是内侧)予以重点关注㊂参考文献:[1]㊀AmericanSocietyofMechanicalEngineers.ManualforDeter⁃miningtheRemainingStrengthofCorrodedPipelines:ASMEB31G 2009[S].NewYork:ASMEB31Committee,2009:1-47.[2]㊀马彬,帅键,李晓魁,等.新版ASMEB31G 2009管道剩余强度评价标准先进性分析[J].天然气工业,2011(8):112-115;140-141.[3]㊀张振永,张金源,李朝,等.油气管道腐蚀缺陷评估方法研究综述[J].腐蚀与防护,2015,36(S1):43-46.[4]㊀程海霞,司珊珊,王炳英,等.三版ASMEB31G标准的评价方法比较研究[J].内蒙古石油化工,2014,40(4):34-36.[5]㊀黄志强,谭智勇,谢豆,等.腐蚀管道评价标准ASMEB31G 2009和SY/T6151 2009对比研究[J].中国安全生产科学技术,2015,11(4):116-122.[6]㊀初飞雪,仇斌,刘秀敏,等.应用修正的B31G公式预测腐蚀管道失效应力[J].油气储运,2005(8):19-21;60-63.[7]㊀姜如桦,张鹏,陈莉琼,等.腐蚀管道剩余寿命的性能衰减模型研究[J].油气储运,2001(11):13-17;58-4.[8]㊀国家质量监督检验检疫总局.压力管道定期检验规则长输(油气)管道:TSGD7003 2010[S].北京:新华出版社,2010:5-6.[9]㊀林现喜,杨勇,裴存锋,等.油气长输管道内检测周期预测方法[J].油气田地面工程,2018,37(5):65-69.作者简介:练斌(1986 ),工程师,硕士研究生,主要从事海底管道内腐蚀检测与风险评估方面的工作㊂(上接第48页)区㊂说明沟槽腐蚀的发生是从焊缝开始,这些性能的差异是形成沟槽腐蚀的根本原因㊂(2)80ksi钢级HFW高频焊管沟槽腐蚀区域的电流密度分布沿焊缝方向是不均匀的,表明腐蚀过程中沿焊缝纵向也不是均匀的,在焊缝区出现电流密度锯齿形波动,这也说明了沟槽腐蚀形成不是一个点,而是有大量的深浅不一的腐蚀坑共同组成,这是沟槽出现忽深忽浅的原因㊂参考文献:[1]㊀孙宝福.ERW高频直缝焊管成型机理及工艺性研究[D].青岛:中国石油大学(华东),2010.[2]㊀刘志俭.ERW直缝焊管成型装置的发展[J].钢管,2007,36(1):1-8.[3]㊀高惠临,董玉华,周好斌.管线钢的发展趋势与展望[J].焊管,1999(3):4-8.[4]㊀林里.热处理工艺对HFW焊缝显微组织和力学性能的影响[J].焊管,2012(6):63-68.[5]㊀毕宗岳,赵晶.HFW焊管热张力减径后的组织与性能[J].焊管,2013(10):5-10.[6]㊀王涛,任永峰,何石磊,等.不同热处理工艺对HFW焊管沟槽腐蚀的影响[J].焊管,2016(6):18-21.[7]㊀王炜,齐慧滨,肖光成,等.ERW焊管沟槽腐蚀行为研究与评价[J].世界钢铁,2007,42(6):20-24.[8]㊀黄淑菊,金时麟.国产电阻焊钢管的沟槽腐蚀倾向[J].焊管,1993,16(5):18-21.[9]㊀KATOC,OTOGUROY,KADOS,etal.Groovingcorrosioninelectricresistanceweldsteelpipeinseawater[J].CorrosinScience,1978,18(1):61-74.[10]㊀KURISUT,KYUNOT,HARADAS,etal.Effectofwariousfactors,mechanismsandpreventivemethodsofgroovingcorrsionofERWandCBWcarbonsteelpipes[J].KawasakiSteelTechnicalReport,1979,11(3):321-336.[11]㊀毕宗岳,任永峰,井晓天.微电极扫描法对HFW焊缝沟槽腐蚀敏感性研究[J].焊管,2011,34(10):5-8.[12]㊀王荣.J55钢直缝焊油井套管沟槽腐蚀性能研究[J].中国腐蚀与防护学报,2004,24(6):360-363.[13]㊀温宏伟,周勇.HFW焊管无缝化及实现[J].焊管,2011(3):51-53.[14]㊀何石磊,白鹤,张峰,等.HFW焊缝性能优化工艺研究[J].焊管,2013(12):39-44.作者简介:任永峰(1971 ),工程师,主要从事油气管材耐腐蚀性研究工作㊂E⁃mail:bsgryf8420@cnpc.com.cn。
基于管道爆破试验对ASME B31G标准中相关参数的修正

结 果见表 3 表 中 1 , ~4管 道 分 别对 应 原 料 气 主 线、 原料气 复线 、 品气 主线 、 品气 复线 。 表 3 产 产
中对 于缺陷长度 的选 取依 照英 国天然气 协会 的研 究 结果 : 当缺 陷长度 超过 管道 直 径 的 7 % 时对 剩 5
余 强度不 再影 响 l 。因此 , 管径 的 7 % 作为 缺 3 J 取 5
更接近 试验 结果 。 降低 了原标 准的保 守性 , 同时 又能保证 一 定的安全裕 度 。 关键词 :石 油天 然气 管道 ;A ME B 1 S 3 G;剩余 强度 ;流 变应 力 ;等 效应 力
中图分 类号 :T 4 5 文 献标 志码 :A 文章 编号 :10 — 9 8 2 0 ) 1 0 8 - 4 G0 0 1 3 3 ( 0 8 0 — 0 4 0
( ) oa 2 F l s系数 的修 正 i 当 L/ t O时 , D ≤5
M =
早在 2 O世纪 6 年代末 7 O O年代初 , 国德克 美
萨斯州 东方 运输公 司和美 国天然气 协会 管 道管 理
委 员会 就 进 行 了一 项 研 究 , 出 了 N 提 G一1 面 8表
√十6 。3 ; 7 . 一o5 。2 . 。 5 o7 7 3
当L/t 2 时,= Z <0 A ÷以 , D
当 L/ r 2 D  ̄ 0时 , > A=d L。
2 3 AS 3 G:9 1标 准 . ME B 1 1 9
由于 A MEB 1 18 S 3 G:9 4标准 的计 算结 果过 分
保守 , 9 年 A M 1 1 9 S E重新颁布了 B 1 3 G标准 , 从三
0 前
言
1 在 役 管道 的腐 蚀 与 水 压 爆 破试 验
基于内检测数据的腐蚀管道完整性评价

止谕牽鏑均仪器PETROLEUM TUBULAR GOODS&INSTRUMENTS2021年4月・68・・失效分析与预防・基于内检测数据的腐蚀管道完整性评价贾向明1,刘诗茵2,白天阳2,蔡亮彳,祁庆芳°,梁昌晶彳(1•国家管网集团西南管道有限责任公司天水输油气分公司甘肃天水741002;2.中油国际管道有限公司北京100029;3.中航油京津冀物流有限公司天津300300;4.中国石油青海油田分公司管道处青海格尔木816000)摘要:完整性评价是完整性管理中的重要环节。
GB32167—2015《油气管道完整性管理规定》中建议优先采用内检测数据对管道的完整性进行评价。
基于工程实例,对某管线内检测检出缺陷进行分级、分类评价,并根据评价结果制定相应的维修响应策略。
结果表明,该管道的内腐蚀较为严重,且集中在5~7点钟方向,可采用预估维修比(ERF)作为缺陷是否需要进行维修响应的判定条件。
通过综合分析,所有缺陷ERF均小于1,剩余强度满足要求;应立即响应的缺陷共有6处,可在1a内计划响应的缺陷共有85处;应在2024年7月13日前再次开展內检测作业。
关键词:内检测;ERF;腐蚀深度;响应策略中图法分类号:TE988.2文献标识码:A文章编号:2096-0077(2021)02-0068-05DOI:10.19459/ki.61-1500/te.2021.02.015Integrity Evaluation of Corroded Pipeline Based onInternal Inspection DataJIA Xiangming1,LIU Shiyin2,BAI Tianyang2,CAI Liang3,QI Qingfang4,LIANG Changjing2(1.Tianshui Sub Company qf South West Pipeline Co.,Ltd,PipeChina Corporation,Tianshui,Gansu741002,Ch加a;2.Sino-Pipeline International Company Ltd.,Beijing100029,China;AF Beijing-Tiaiyin-Hebei Logistics TrarsportionCo.,Ltd,Tianjin300300,China;4.Pipeline at the China Petroleum Qinghai Oilfield Company,Geermu,Qinghai816000,China)Abstract:Integrity assessment is an important part of integrity management.It is recommended in GB32167-2015Oil and Gas Pipeline Integrity Management Specification that the internal inspection data is preferred to evaluate the integrity of the pipeline.Based on the project example,the detected defects in a pipeline are graded and classified,and the corresponding maintenance response strategy is formulated according to the evaluation results.It is shown that the pipeline internal corrosion is serious and concentrated in the5to7o'clock direction. The estimated service ratio(ERF)can be used as the criterion for determining whether a defect requires a service response.Through comprehensive analysis,it is found that the ERF of all defects in the pipeline are less than1,and the residual strength meets the requirements. 6defects should be responded for maintenance immediately,and85defects can be responded within1year.The time for retesting is recommended till July13,2024.Key words:internal detection;ERF;corrosion depth;response strategy0引言随着油气管道服役时间的延长,因土壤、大气、应力和输送介质等原因造成的管道腐蚀问题越来越严重,并引发爆炸和火灾等恶性事故,造成人员伤亡和财产损失,是影响管道运行可靠性和服役寿命的关键因素⑴,也成为在役管道完整性研究的重要课题。
三种腐蚀管道剩余强度评定准则解析

三种腐蚀管道剩余强度评定准则解析刘甲斌;冯格;李秉昌【摘要】To analysis and compare three kinds of corroded pipelines remaining strength standards, the ASME B31G-1984 standard, ASMEB31G-2009 standard and RSTRENG standard were introduced. These three standards were used to calculate the remaining strength of a corroded pipeline. Comparing the results, the conclusion showed that the ASMEB31G-2009 level one evaluation standard was most conservative, the ASME B31G-1984 standard was less conservative than ASME B31G-2009 level one evaluation standard, and the RSTRENG standard was the least conservation standard of all.%为了分析对比三种腐蚀管道剩余强度计算准则,通过对 ASME B31G-1984准则、 ASME B31G-2009准则以及RSTRENG准则进行介绍,对比其计算管道剩余强度的异同点,并对一组腐蚀管道数据进行计算,对比计算结果。
得出 ASME B31G-2009准则一级评价最为保守, ASME B31G-1984准则保守性次之, RSTRENG准则保守性最低。
【期刊名称】《广州化工》【年(卷),期】2015(000)004【总页数】3页(P168-170)【关键词】腐蚀管道;强度评定;剩余强度【作者】刘甲斌;冯格;李秉昌【作者单位】陕西能源职业技术学院,陕西咸阳 712000;咸阳市马泉中学,陕西咸阳 712000;陕西能源职业技术学院,陕西咸阳 712000【正文语种】中文【中图分类】TQ055.8;TE973管道作为一种常见的工业产品大量应用于民用和工业生产中,截至2008 年年底,我国已建油气管道的总长度约为6.4 万千米[1]。
三版ASME B31G标准的评价方法比较研究

三版ASME B31G标准的评价方法比较研究
程海霞;司姗姗;王炳英;侯振波
【期刊名称】《内蒙古石油化工》
【年(卷),期】2014(000)004
【摘要】基于断裂力学的NG-18公式,美国机械工程师协会(ASME)颁布了ASME B31G-1984标准,该评价方法便于计算,可以很快求得腐蚀缺陷管道的极限承载能力和最大允许安全运行压力.针对B31G-1984标准的保守性,对其修改后推出ASME B31G-1991规范.2009年,对该标准又进行了一次修改,得到ASME B31G-2009,该版B31G标准延续并完善了原始的B31G评价方法.主要介绍了三版B31G 标准评价腐蚀缺陷剩余强度的方法及流程,并对三版标准进行比较,方便评估工作者进行选择.
【总页数】3页(P34-36)
【作者】程海霞;司姗姗;王炳英;侯振波
【作者单位】中国石化集团胜利油田东辛采油厂,山东东营257000;中国石化集团胜利油田东辛采油厂,山东东营257000;中国石化集团胜利油田东辛采油厂,山东东营257000;中国石化集团胜利油田东辛采油厂,山东东营257000
【正文语种】中文
【中图分类】TE357
【相关文献】
1.学术期刊评价中标准分与原始分的比较研究——科技评价方法必须进行革命性改良 [J], 俞立平;武夷山
2.生态住宅小区声环境评价方法与评估标准比较研究 [J], 姚珊珊;余术刚
3.基于管道爆破试验对ASME B31G标准中相关参数的修正 [J], 宋旭;张振文;闫琳;张建勋
4.ASME B31G 系列评价方法的演进及影响因素研究 [J], 朱涛
5.ASME B31G剩余强度评价方法分析 [J], 蒲文莲
因版权原因,仅展示原文概要,查看原文内容请购买。
3. 含腐蚀缺陷管道剩余强度评价

含腐蚀缺陷管道剩余强度评价方法SY/T 6151(ASME B31G )要点符号说明:D是管道的名义外径 mm t是管道名义壁厚 mmL腐蚀金属损失缺陷的轴向长度mm d实测的腐蚀区域最大深度 mm m L腐蚀允许轴向长度 mm‘P腐蚀区域最大安全运行压力 MPaMAOP 是指在根据适用的设计规范和规定确定的界限下,管道或管段可能操作的最大压力 MPa0P 为MAOP 与设计压力D2StFTP 之间的较大值 MPa S 管材屈服强度 MPa F 管道设计强度系数 T 管道设计温度系数1、缺陷剩余强度评价方法介绍本缺陷评价方法基于ASME B31G 。
该评估方法只使用两个缺陷参数(深度和长度)来评估在什么样的运行压力下有缺陷的管道不会发生断裂,主要用于对孤立缺陷进行评估。
在ASME B31G 中,缺陷环向宽度对破坏压力的影响可以忽略,因此在评价中不考虑宽度因素。
在ASME B31G 方法中,腐蚀缺陷的形态近似成抛物线形或半椭圆形。
图1 ASME B31G 缺陷强度评价方法参数2、缺陷评价流程1)测量腐蚀区域的最大深度d 并与管道壁厚t 相比如果缺陷的腐蚀深度小于10%名义壁厚(%10td<),该含缺陷管道可以继续留用。
不需要对缺陷进行修复。
但需要对缺陷进行防腐,防止缺陷的进一步扩大。
如果缺陷的腐蚀深度大于80%名义壁厚(%80td>),该含缺陷管道必须停输并换管。
2)对于缺陷的腐蚀深度介于10%~80%的情况,需要计算腐蚀允许轴向长度L m 并将L m 与实际腐蚀长度L 相比。
Dt B 12.1L m =B 是管道的腐蚀系数,按下列规定取值:当%5.17%10<<td时,B=4.0当%5.17>td时,115.01.12-⎪⎪⎭⎫ ⎝⎛-=t d t d B 3)如果L m >L ,则含缺陷管道可以留用。
但要做好防腐,防止缺陷的进一步扩大。
4)如果L m <L ,则需要计算腐蚀区域最大安全运行压力‘P ,并将‘P 与管道最大允许操作压力MAOP 比较。
基于管道爆破试验对ASME+B31G标准中相关参数的修正

·84·
●标准化
焊管·第31卷第1期-2008年1月
基于管道爆破试验
对ASME B3 1 G标准中相关参数的修正+
宋 旭1,张振文2,闫 琳1,张建勋1
(1.西安交通大学材料科学与工程学院,西安710049; 2.中国石油长庆油田分公司第一采气厂,陕西靖边719000)
摘要:ASME B31G标准是针对含体积缺陷压力管道进行剩余强度评价的标准。运用此标 准对陕西靖边地区天然气集输站在役管道进行了剩余强度的计算,针对B31G标准计算的剩 余强度相对水压爆破试验结果过于保守的问题,考虑到B3lG标准的适用范围,从Mises等效 应力和流变应力两个方面对B31G标准计算方法进行了修正。结果表明,修正后的评价结果 更接近试验结果,降低了原标准的保守性,同时又能保证一定的安全裕度。 关键词:石油天然气管道;ASME B31G;剩余强度;流变应力;等效应力 中图分类号:TG405文献标志码:A文章编号:1001—3938(2008)01—0084—04
·85·
表3在役管道的腐蚀缺陷
式中:S=1.1R。L,R。L为管材的最小屈服强度;
%=/—1+0—.8L__堕2;
(4)
2 ASME B31G标准概述
2.1 NG一18表面缺陷公式
早在20世纪60年代末70年代初,美国德克
萨斯州东方运输公司和美国天然气协会管道管理
油气管道管壁腐蚀程度预测方法研究
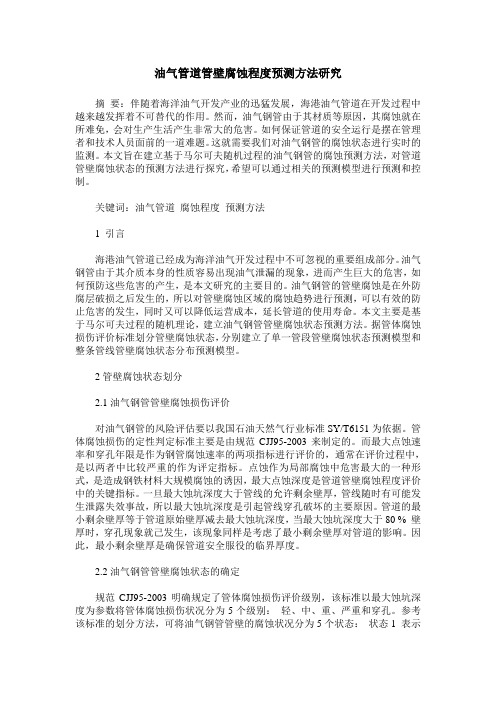
油气管道管壁腐蚀程度预测方法研究摘要:伴随着海洋油气开发产业的迅猛发展,海港油气管道在开发过程中越来越发挥着不可替代的作用。
然而,油气钢管由于其材质等原因,其腐蚀就在所难免,会对生产生活产生非常大的危害。
如何保证管道的安全运行是摆在管理者和技术人员面前的一道难题。
这就需要我们对油气钢管的腐蚀状态进行实时的监测。
本文旨在建立基于马尔可夫随机过程的油气钢管的腐蚀预测方法,对管道管壁腐蚀状态的预测方法进行探究,希望可以通过相关的预测模型进行预测和控制。
关键词:油气管道腐蚀程度预测方法1 引言海港油气管道已经成为海洋油气开发过程中不可忽视的重要组成部分。
油气钢管由于其介质本身的性质容易出现油气泄漏的现象,进而产生巨大的危害,如何预防这些危害的产生,是本文研究的主要目的。
油气钢管的管壁腐蚀是在外防腐层破损之后发生的,所以对管壁腐蚀区域的腐蚀趋势进行预测,可以有效的防止危害的发生,同时又可以降低运营成本,延长管道的使用寿命。
本文主要是基于马尔可夫过程的随机理论,建立油气钢管管壁腐蚀状态预测方法。
据管体腐蚀损伤评价标准划分管壁腐蚀状态,分别建立了单一管段管壁腐蚀状态预测模型和整条管线管壁腐蚀状态分布预测模型。
2管壁腐蚀状态划分2.1油气钢管管壁腐蚀损伤评价对油气钢管的风险评估要以我国石油天然气行业标准SY/T6151为依据。
管体腐蚀损伤的定性判定标准主要是由规范CJJ95-2003来制定的。
而最大点蚀速率和穿孔年限是作为钢管腐蚀速率的两项指标进行评价的,通常在评价过程中,是以两者中比较严重的作为评定指标。
点蚀作为局部腐蚀中危害最大的一种形式,是造成钢铁材料大规模腐蚀的诱因,最大点蚀深度是管道管壁腐蚀程度评价中的关键指标。
一旦最大蚀坑深度大于管线的允许剩余壁厚,管线随时有可能发生泄露失效事故,所以最大蚀坑深度是引起管线穿孔破坏的主要原因。
管道的最小剩余壁厚等于管道原始壁厚减去最大蚀坑深度,当最大蚀坑深度大于80 % 壁厚时,穿孔现象就己发生,该现象同样是考虑了最小剩余壁厚对管道的影响。
ASMEB31G-2009在管道剩余强度计算中的应用

ASME B31G-2009在管道剩余强度计算中的应用1 引言近年来我国油气管道腐蚀现象日趋严重,由腐蚀造成的管道泄漏事故危害重大,因此,对腐蚀管道进行剩余强度评价极为重要。
对于含缺陷管道的剩余强度评价通常分为三种:采用断裂力学方法进行评价;采用以弹塑性力学为基础的数值分析方法进行评价;采用断裂力学和工程实践经验相结合的半经验公式进行评价。
20世纪60年代末,国内外一直在进行管道剩余强度评价方面的研究,多个国家颁布了相关的评价标准及规范。
1984年美国机械工程师协会颁布的ASMEB31G—1984标准是研究腐蚀管道剩余强度评价方面使用最广泛、最基本的评价标准之一,之后又推出了ASME B31G—1991修改版及改进的RSTRENG方法。
在应用的过程中,针对ASME B31G-1984评价准则的保守性,有关学者在1989年对ASME B31G-1984准则进行了修正,得到了ASME B31G-1991评价准则,该准则消除了原准则的一些不足。
2 ASME B31G-2009评价准则美国机械工程师协会于2009年更新了ASME B31G评价准则,即ASME B31G-2009,该评价准则延续并完善了之前的评价准则,但是提出了分级评价的概念,认为在应用该方法时,应根据实际情况选择不同等级的评价方法,使评价过程更为细化[1]。
2.1 零级评价为一系列查询表格,根据测量的腐蚀缺陷深度、管径、壁厚等参数,查询表格可以得到此缺陷最大允许长度,若实际腐蚀长度小于该极限长度,则缺陷处于安全状态,反之则表示没有通过评价,应采取维修措施或选择更高级别的评价方法。
该表格基本是根据原版的ASME B31G 评价方程计算得到的,只是增加了公制单位。
零级评价具有方便现场人员查阅、操作简单的特点,但其评价结果保守性较大。
2.2 一级评价ASME B31G-2009 推荐借助改进的B31G 评价方程来计算缺陷的剩余强度,该级评价应由相应的工程师、腐蚀技术人员或涂层检验人员来完成。
三版ASME B31G标准的评价方法比较研究

《腐蚀管道剩余强度的简明评价方法》规范,该评价 方法便于计算,可以很快求得腐蚀缺陷管道的极限 承载能力和最大允许安全运行压力,适合评价含有 单一轴向缺陷腐蚀管道的剩余强度n] 。
1971年Ei ber 、Maxey、Dul l y给出一个计算Mt
的表达式,即B31G一19 84中给出的表达式:
34
内蒙古石油化工
2014年 第4期
三 版 ASME B31G标 准 的 评 价 方 法 比 较 研 究
程海霞,司姗姗,王炳英,候振波
( 中国石化集团胜利油田东辛采油厂,山东东营257000)
摘要:基于断裂力学的NG一18公式,美国机械工程师协会( ASME) 颁布了ASME B31G一1984
标准, 该评价方法便 于计算,可以 很快求得腐 蚀缺陷管道的 极限承载能 力和最大允许 安全运行压力 。针 对B31G一1984标准的保守性,对其修改后推出ASME B31G一1991规范。2009年,对该标准又进行了 一次修改,得到ASME B31G- - 2009,该版B31G标准延续并完善了原始的B31G评价方法。主要介绍了 三版B31G标准评价腐蚀缺陷剩余强度的方法及流程,并对三版标准进行比较,方便评估工作者进行选 择。
M。=( 1+0.4845kz) //2≈√1+0.8L2/( Di t ) ( 1)
为建立几何参数的评价准则,ASME B31G一 1984作了如下假设[ 3】:①材料的流变应力Sf l ow是 材料的最小屈服强度SMYS的1.1倍,最PSf l ow=1. I SMYS;( 至) Fol i a s 系数用式( 1) 表示;⑧利用投影 面积来表达腐蚀区金属损失的面积。当L2/Dt ≤20 时,缺陷视为短缺陷,此时投影面积近似为抛物线形 面积,即:
油气管道腐蚀缺陷剩余强度评估的研究
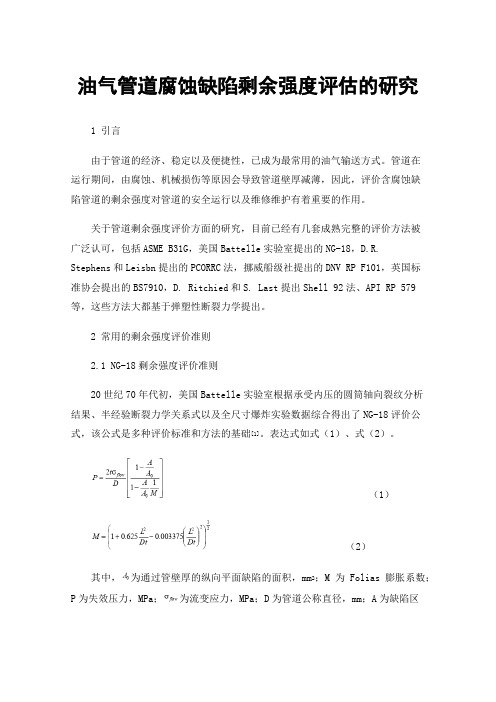
油气管道腐蚀缺陷剩余强度评估的研究1 引言由于管道的经济、稳定以及便捷性,已成为最常用的油气输送方式。
管道在运行期间,由腐蚀、机械损伤等原因会导致管道壁厚减薄,因此,评价含腐蚀缺陷管道的剩余强度对管道的安全运行以及维修维护有着重要的作用。
关于管道剩余强度评价方面的研究,目前已经有几套成熟完整的评价方法被广泛认可,包括ASME B31G,美国Battelle实验室提出的NG-18,D.R.Stephens和Leisbn提出的PCORRC法,挪威船级社提出的DNV RP F101,英国标准协会提出的BS7910,D. Ritchied和S. Last提出Shell 92法、API RP 579等,这些方法大都基于弹塑性断裂力学提出。
2 常用的剩余强度评价准则2.1 NG-18剩余强度评价准则20世纪70年代初,美国Battelle实验室根据承受内压的圆筒轴向裂纹分析结果、半经验断裂力学关系式以及全尺寸爆炸实验数据综合得出了NG-18评价公式,该公式是多种评价标准和方法的基础[1]。
表达式如式(1)、式(2)。
(1)(2)其中,为通过管壁厚的纵向平面缺陷的面积,mm2;M为Folias膨胀系数;P为失效压力,MPa;为流变应力,MPa;D为管道公称直径,mm;A为缺陷区域金属损失面积,mm2;t为管道公称厚度,mm;d为最大腐蚀深度,mm;L为腐蚀长度,mm。
2.2 ASME B31G剩余强度评价准则20世纪80年代初,美国机械工程师协会颁布了腐蚀管道剩余强度测定手册ASME B31G,该测定方法是由半经验公式NG-18演变而成,模型对流变应力、Folias因子以及腐蚀缺陷参数进行了多次修正,对腐蚀缺陷进行分级评价,降低了模型评价的保守性。
该模型适用于评估带有轴向缺陷的中低强度钢腐蚀管道,模型假设只存在内压载荷,不考虑缺陷的轴向轮廓、形状及缺陷间的相互作用[2]。
ASME B31G-1984是该准则最早的版本,该版本认为材料最小屈服强度的1.1倍为材料的流变应力,管道腐蚀缺陷区域的金属损失通过投影面积来表示,当腐蚀缺陷为长缺陷时,投影面积近似描述为矩形面积,当腐蚀缺陷为短缺陷时,投影面积近似描述为抛物线围成的面积,表达式如下:当时,(3)当时,(4)在应用过程中,ASME B31G-1984较为保守,P.H. Vieth和J.F. Kiefner在对不同形状缺陷的管道失效压力分析的基础上,对1984版进行了改进,提出了ASME B31G-1991评价准则,该准则认为材料的流变应力应为屈服强度加69MPa],失效压力表达式如下:(5)当时,(6)当时,(7)ASME B31G-2009版和ASME B31G-2012版将剩余强度评价级别分为四个等级:零级评价、一级评价、二级评价以及三级评价。
基于智能内检测的腐蚀海底管道剩余寿命评估

基于智能内检测的腐蚀海底管道剩余寿命评估张东卫,孙国民,翁强,吕建伟(海洋石油工程股份有限公司, 天津 300452)[摘 要] 腐蚀是海底管道最常见的失效形式。
本文以渤海某海底管道为例,介绍了基于多次智能内检测的腐蚀海底管道剩余强度和剩余寿命评估,对管道腐蚀原因进行了分析,对生产运行和检测提出了切实可行的建议,可有效指导油田生产。
[关键词] 海底管道;腐蚀;智能内检测;剩余强度;剩余寿命作者简介:张东卫(1985—),男,河北保定人,硕士,工程师。
研究方向为海洋工程结构设计与评估。
在现代海洋开发事业中,海洋石油开发最引人注目。
我国拥有广阔的大陆架,含有较丰富的油气资源,现已开发的海上油气田包括渤海、黄海、东海和南海的所有中国海域。
伴随着我国海上油气田的开发,海底输送管道的建设取得了长足进步。
海底管道放置在海底或埋藏在海底土壤中,会受到来自内部和外部的许多因素的破坏。
海底管道本身的擦痕、划痕、金属材料自身缺陷以及焊接缺陷是影响海底管道安全的先天缺陷。
土壤、海水、细菌和杂散电流等因素是海底管道腐蚀的外在因素。
随着海底管道使用年限的增加,管道发生腐蚀的可能性增加。
一旦发生穿孔、泄漏,将会给油田作业者带来重大经济损失和社会影响[1]。
目前,国内外已经出台了相关的腐蚀管道剩余强度评价标准和评价体系,如ASME B31G 准则、修正的B31G 准则、RSTRENG 方法、DNV-RP-F101准则以及中国石油天然气行业标准SY/T 10048《腐蚀管道评估推荐做法》等[2]。
另外,随着智能内检测技术的发展,国内海底管道的完整性管理逐渐成熟,海底管道的检测逐渐规范化。
基于内检测结果的腐蚀海底管道剩余强度和剩余寿命评估的需求日益增多。
本文以ASME B31G 规范[3][4]为基础,对渤海某海管进行了基于多次智能内检测结果的腐蚀海底管道的剩余强度和剩余寿命评估。
1 评估标准1.1 ASME B31G 准则1984年美国机械工程师协会出台了最早的腐蚀管道剩余强度评估标准ASME B31G-1984,它是评价标准的基础[2]。
含腐蚀缺陷管道安全评价准则选择探讨

pf
=
2tσ
f
1−
d t
D
−
t
1
−
d Qt
(7)
式中流变应力σ f = σ b ,Q缺陷长度校正系数。 2.5 PCORRC评价准则
图1 管道缺陷评价准则比较
技
P C O R R C 评 价 准 则 ( P i p e l i n e C o r r o s i o n 3 结语
术
Criterion)针对X65~X80中高强度等级管道因塑性
经验交流 Experience Exchange
含腐蚀缺陷管道
安全评价准则选择探讨
王风雷
(中国石油管道局工程有限公司第四分公司,河北 廊坊 065000)
摘 要:外腐蚀是威胁管道安全的重要因素,极易导致管道泄漏或失效断裂事故。我国长
输管道全面实施完整性管理,应根据管道历史失效事件,开展管道剩余强度评价与剩余寿命预
evaluation criteria. Key words: long distance pipeline; corrosion defect; failure; evaluation; criterion; accuracy
作者简介:王风雷 (1975-) ,河北廊坊人,工程师,主要从事管道工程项目管理工作。
式中流变应力σ f = σb ;R管道外径和内径的
平均值,mm。
(3)BS 7910准则、DNV RP-F101准则和 PCORRC准则适用于中高钢级含缺陷管道安全性评
2.6 管道缺陷安全评价准则比选
价,其中DNV RP-F101准则和 PCORRC准则最优;
收集50例不同钢级(X42~X100)含腐蚀缺陷
(1)根据管道运行状况和缺陷特征,考虑上述
腐蚀油气管线的可靠性分析

腐蚀油气管线的可靠性分析
徐伟;刘茂
【期刊名称】《中国工程科学》
【年(卷),期】2010(012)009
【摘要】ASME B31G是国际通用的评价腐蚀管线失效应力的标准,考虑到这种方法的保守性,以修正后的B31G模型作为研究腐蚀管线失效应力的基础,考虑管壁厚度、腐蚀速率、工作压力、缺陷深度等随机变量,构建腐蚀油气管线可靠性极限状态函数.然后,采用一次二阶矩法对腐蚀管线进行可靠性分析,得出管线的失效概率、可靠性指标以及剩余使用寿命.此外,为了更加规范的管理腐蚀管线,参照美国石油组织的相关规定,对不同失效概率的管线进行了等级划分.在最后的案例分析中,还讨论失效概率对不同变异系数对的敏感性,计算结果表明失效概率对管壁厚度的变异系数最为敏感.
【总页数】5页(P69-72,77)
【作者】徐伟;刘茂
【作者单位】南开大学城市公共安全研究中心,天津,300071;南开大学城市公共安全研究中心,天津,300071
【正文语种】中文
【中图分类】X913.1
【相关文献】
1.基于失效评定图的油气管线可靠性分析 [J], 帅健;辛艳霞
2.油气管线腐蚀监测与防护研究 [J], 陈亚颐;赵黎;李兵元;木塔里甫·木拉提;罗李黎
3.炼化俄罗斯原油对常减压塔顶油气管线腐蚀防护分析 [J], 南海;姜健;黄晓妮;韩圣霖
4.基于遗传-神经网络算法的含均匀腐蚀缺陷油气管线爆破压力预测研究 [J], 贾思奇;郄彦辉;李煜彤;李宁宁
5.油气管线钢土壤环境硫酸盐还原菌腐蚀研究进展 [J], 韦博鑫;许进;高立群;覃清钰;付琦;于长坤;孙成;王振尧
因版权原因,仅展示原文概要,查看原文内容请购买。
管道剩余强度评价标准ASME B31G-2009的应用及优化改进

管道剩余强度评价标准ASME B31G-2009的应用及优化改
进
高富超
【期刊名称】《内蒙古石油化工》
【年(卷),期】2014(000)012
【摘要】管道是我国天然气、原油、成品油等能源输送的重要方式,随着国家多条战略能源管道服役年限的增长,腐蚀成为威胁管道安全运行的较大因素.目前我国在役输油气管道体积型腐蚀缺陷评价多采用ASME B31G标准.ASME B31G标准几经修改形成目前的ASME B31G-2009版本,本文通过比较ASME B31G-1984、ASME B31G-2009评定方法的不同,分析得出ASME B31G-2009的优化方法及结论.
【总页数】3页(P25-27)
【作者】高富超
【作者单位】中石油管道联合有限公司西部分公司,新疆乌鲁木齐830000
【正文语种】中文
【中图分类】TE988.202
【相关文献】
1.基于腐蚀缺陷管道的剩余强度评价标准应用 [J], 杨理践;刘凤艳;高松巍
2.含体积型缺陷油气管道剩余强度评价标准对比分析研究 [J], 张奕;高富超;杨锋平;王琴;张良;王珂
3.含裂纹型缺陷油气管道剩余强度评价标准对比分析研究 [J], 杨锋平;高富超;邹斌;罗金恒;贾海东
4.ASME B31G-2012标准在含体积型缺陷管道剩余强度评价中的应用研究 [J], 青松铸;范小霞;阳梓杰;米小双;孙明楠;高健;周秀兰
5.含体积型缺陷油气管道剩余强度评价标准对比分析研究 [J], 张奕;高富超;杨锋平;王琴;张良;王珂;
因版权原因,仅展示原文概要,查看原文内容请购买。
长输管道的腐蚀风险评价
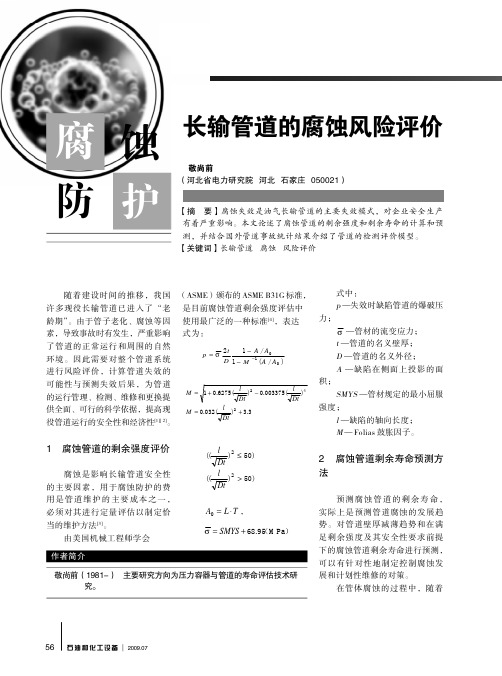
事故抢险时间,取其平均值,也可 以根据评估要求取其最大值。
4 结束语
腐蚀管道的安全至关重要, 我国目前还缺乏完整和有效的保 证体系。管道的风险评价可以供 制定和发展我国管道安全评价体 系参考借鉴;是保证现役管道安全 可靠运行必不可少和亟待深入开 展的一项工作;对于当前热门的管 道完整性研究领域,发展有效的 完整性检测和评价技术极其重要。 因此,应加强风险评价的技术跟 踪,尽快开发适用于现役管道风 险评估的软件系统,提高我国石 化管道运行的可靠性和经济性。
在管体腐蚀的过程中,随着
56 石 油 和 化 工 设 备 2009.07
腐蚀防护
FU SHI FANG HU
时间的增加,对整条管道而言,腐 蚀缺陷点数、腐蚀区域、腐蚀程度 和失效概率呈增加趋势,如不经 维修,出现泄漏或破裂的次数会 逐年增加。但由于不同区段管体 腐蚀条件存在差异,腐蚀的发展 趋势也不尽相同。
hazard pipelines 2000
9.钱成文.牛国赞 基于风险分析的管道检测(RBI)与评价[期刊论文]-油气储运 2000(08)
相似文献(10条)
1.期刊论文 赵新潮.罗艳红.盘丁铨 基于Smart-CET技术石油长输管道内腐蚀实时在线监测系统构建 -科学时代(上半月)2010,""(4)
Smart-CET技术是美国霍尼韦尔公司旗下的InterCorr国际腐蚀公司开发的自动电化学监测专利技术,本文论述了该技术在石油长输管道的现场适用性.其可以对长输管道内腐蚀状态进 行实时检测、动态跟踪、分析和评估,反映内腐蚀变化过程,从而减小腐蚀危害.
2009.07 石 油 和 化 工 设 备 57
工 艺 创新
表 2 不同等级外腐蚀泄漏事故的发生频率[3]
- 1、下载文档前请自行甄别文档内容的完整性,平台不提供额外的编辑、内容补充、找答案等附加服务。
- 2、"仅部分预览"的文档,不可在线预览部分如存在完整性等问题,可反馈申请退款(可完整预览的文档不适用该条件!)。
- 3、如文档侵犯您的权益,请联系客服反馈,我们会尽快为您处理(人工客服工作时间:9:00-18:30)。
2013年第39卷第1期工业安全与环保Ja nuar y 2013I ndust r i al Saf e t y a nd Envi r onm e nt alPr o £ect i on 57基于A SM EB 31G 准则的油气管道腐蚀安全性评估王翔1(1.中国石油大学机电工程学院山东青岛266555;赵东风22.中国石油大学化学化工学院山东青岛266555)摘要腐蚀是在役管道失效的最主要原因之一。
腐蚀后的管道会造成局部减薄,使其局部承载力下降,一旦发生泄漏,极易发生火灾爆炸事故。
采用通用的A SM E B 31G 准则对管道进行腐蚀安全性评估,研究了不同级别管道的最大允许缺陷长度和最大安全运行压力,计算了不同腐蚀长度对管道安全性的影响,可以为管道维护策略和应急管理提供科学依据。
关键词A SM E B 31G 准则管道腐蚀安全性Saf e t y Ass esaneat of O i l G as Pi pel i ne s C or r os i on B as ed onA SM E 1131G St andar dW A N G Ⅺ肌FZ H A OD onsf 耐(1.C ol l ege of M echani caland E l ect r oni c E ngi ne er i ng C hi na U ni ver si t yofP a w l at mQ i ngd 肋,Shandong 266555)A 】b 劬嘀dC or r osi on ison e0f t he m ai nr e ason sf or f ai lur e of i n ser v i ce pi pe l i nes .T he w al l t hi cknes s 0f ot )r i 'od ed pi pel i nesw il l drop ,w hi ch l ea ds t he de c rea s e d t he l ocal c apa c i t y ,he nce fi r e a nd exp l osi on ac ci dent s oo c u rff t he pi p el i n es l e ak .I nt h i s paper ,t he ge ner a l A S M E B 31G st andar d is appl i e d t o pe rf or m saf et y asse 删dt hepive №,them a xi m um al l ow edl eng t h of def e ct a nd m 豳唧safetypr es sur eof di f f er ent gr adepjpeli 麟isdi scusse d a nd t he i nf l ue nce s of di f f er ent def ect1ens t ho nt he saf et y of pi p el i n es ar eobt ai ned ,w hi chc anof fer s cient i fi c bas i s t o t he m ai nt enance pl a n a nd em er gen cy man-a gem e ntof pi p el i nes .K eyW or dsA SM EB 31G st andar dpi pe l i necor r osi onsaf et y0引言我国的油气管道预计在2015年达到总长14万陆,其中许多建于上世纪的管道“带病”运行,安全可靠性难以满足安全生产的需要。
有资料表明,腐蚀失效是油气管道失效的主要原因之一u-2J 。
特别是老龄化管道,发生腐蚀后会造成管道局部减薄,使管道的局部承载力下降,一旦发生泄漏,极易发生火灾爆炸事故,造成重大人员和财产损失【3J 。
因此,深入研究油气管道的腐蚀安全性,可以科学地指导管道的维修计划和应急管理,对确保长输管道的安全运行有着重要意义。
1腐蚀管道评估方法管道腐蚀会造成管壁减薄,使管道的局部承载力下降,工程上常采用剩余强度来表示管道强度的减弱以评估管道的最大安全运行压力。
腐蚀管道的剩余强度评价是管道完整性管理的重要内容,通过对剩余强度评估,可以为管道的实时监控和维修计划提供科学依据,具有十分重要的实际意义。
1.1管道剩余强度的计算模型管道腐蚀缺陷会造成局部的应力集中,因此会导致环向力沿着缺陷深度和长度重新分布H J 。
图1是一个钢质管道壁上表面径向腐蚀缺陷示意图。
其中,t 是管道壁厚,d 是缺陷深度,L 是腐蚀区域在管道纵轴向的投影长度。
这种腐蚀缺陷会继续扩展,当发展到一定程度时,失效发生,导致泄漏或者断裂,失效的形式取决于缺陷的尺寸大小,这里只考虑管道失效而不考虑失效的形式。
图1管道腐蚀缺陷示意管道的腐蚀缺陷受多种不确定性因素的影响,包括缺陷尺寸、压力、腐蚀增长率、屈服应力和几何尺寸等。
因此,腐蚀管段的剩余强度(Q )是一个随时间变化的多个随机变量的函数,主要取决于管道腐蚀后金属损失量与原完好管道的比值,K i 幽一5J等人提出一个用于计算管道腐蚀缺陷失效压力的模型:Q=警【揣】㈩式中,A 为腐蚀部分在管道纵轴向的投影面积,A o58是腐蚀区域的初始面积,M是考虑管道失效前发生鼓包的F ol i as系数,D是管径。
1.2A S M E B31G准则目前国内外管道剩余强度评价的方法有很多,包括A SM E B31G准则、A PI579准则、有限元法和失效评估图法等,其中A SM E B31G准则是美国最早建立的《腐蚀管道剩余强度的简明评价方法》,该准则基于材料弹塑性断裂力学理论,将理论分析和实验相结合,用方程来表示材料不连续时管道的应力,由该准则得出的结果是建立在实验数据基础上的半理论半经验公式。
该方法应用方便,可以很快求出单一轴向缺陷腐蚀管道的极限承载力和安全运行压J3C6-7],因此,在管道可靠性评价中得到广泛应用。
1.2.1A S M E B31G准则的理论基础A S M E B31G准则的理论基础主要是K i ef ner提出的一个用于计算管道腐蚀缺陷失效压力的模型,A S M E B31G准则评价腐蚀管道可靠性的主要步骤如下i s一9]:(1)确定管道的缺陷深度与壁厚的比值d/t。
(2)计算允许存在腐蚀缺陷的最大轴向长度己:L=1.12B湎(2)式中,B是一个与管道最大缺陷深度壁厚比d/t有关的参数,8与d/t的关系如式(3):I B=4o1<d/‘<o175,.1B=【(揣)2一lr o.175<d/t<0.8(3)当d/t≥O.8时,这样的腐蚀缺陷不可接受,因为这时的缺陷深度将导致管道破裂。
(3)傅里叶系数舾的确定:膨:扛孚式中,k是腐蚀缺陷的轴向长度。
(4)计算管道的允许最大安全压力P,:Pf=1.1盯。
碧×南黜(5)式中,盯。
为管道材料的最小屈服强度,这里需要说明的是,B31G准则在K i ef ner腐蚀管道模型的基础上进行了几点假设【10】:①假设管道材料的屈服应力d,是管材最小屈服应力d。
的1.1倍,即盯,=1.10r。
;②Fol i as系数材与腐蚀缺陷长度Lm、管径D及壁厚‘有关;③与式(1)相比,将腐蚀区域轴向投影面积A和腐蚀区域的初始面积A o近似地表示为:A=昔L。
d和A o=L。
I,其中d和L。
分别是缺陷的平均深度和轴向长度。
应用B31G准则进行计算时,若计算结果小于管道的运行压力,则管道不能继续使用,处于失效状态,必须更换或者维修。
1.2.2A SM E B31G准则的修正由于B31G准则在Fol i as系数的计算和腐蚀缺陷宽度上的考虑不够精确,使计算结果比较保守,A G A在1989年对B31G准则进行了修正,主要是以下3点:(1)管材的最小屈服应力盯,=盯。
+68.95M Pa;(2)对F ol i as系数计算式进行修正:,厂—————7厂—————可1"2}肚√1+0.6275茜_o-0)3375而/-am蓄@㈨1,2,2旧,【M=0.032岽+3.3瓦/'11“>50(3)修正的B31G准则在计算时还对缺陷的环向长度进行了考虑[11],当缺陷的深度壁厚比d/t< 0.5时,忽略缺陷的环向长度对计算结果的影响;当0.5<d/t<0.6时,要求缺陷的环向长度必须小于周长的1/6;当0.6<d/t<0.8时,缺陷的环向长度必须小于周长的1/12;当d/t>0.8时,管道处于失效状态,必须进行维修或者更换。
修正后的B31G 准则计算管道剩余强度:Pf=(¨68.95)砻×南黜(7)2基于B31G准则的腐蚀管道安全评价2.1B31G准则与修正B31G准则的比较为了对B31G准则与修正后B31G准则计算结果进行比较,取西气东输二线某区段大孔径钢制管道为例,管道材料为A PI5L X80钢,直径D为l219 nl nl,壁厚#为22m i l l。
缺陷最大的轴向投影长度£。
为100艘n,材料的最小屈服应力为555M Pa,取缺陷的最大深度为2—16r eal,分别进行最大允许长度和剩余强度的计算,结果见表1和图2。
表l管道最大安全运行压力评价结果缺陷深度最大允许长度B31G计算结修正B31G计d/na n L/ran果/M Pa算结果/M Pt l由表1和图2可以看出,当缺陷深度从2m i l l到16nl nl变化时,B31G准则和修正后的准则计算的最大允许缺陷长度三相同,当缺陷深度为16l l l l n 时,59蛊22.5穗戮K20.0嚼19.5缺陷深度/m m图21131(;准则和修正后的B31f;准则计算结果比较最大允许缺陷长度为92.03rf l n'l,而假定的缺陷长度为100hi m,显然,这样的缺陷长度是不允许的,管道必须进行维修和更换。
同时可以看出,在相同的缺陷深度前提下,修正后准则计算出的管道剩余强度要高于未修正的准则0.5M Pa左右,说明修正后的B31G准则一定程度上提高了腐蚀管道的最大安全运行压力,克服了B31G准则的保守性。
2.2高级别钢制管道的剩余强度评价2.2.1不同钢级管道的剩余强度评估为评估不同钢级管道的腐蚀可靠性,现取X52、X70、X803种管线钢,3种管材的腐蚀长度£。
均取100m i l l,管材的参数如表2所示,应用修正后的B31G 准则计算3种腐蚀管道的最大运行压力和最大允许腐蚀长度,计算结果见表3和图3。
表2管材参数表3不同钢级管道最大允许腐蚀长度计算结果m i l l对鲁21.0壹20.5代出20.0端19.5删:V-4190悄18.5签18.0略8缺陷深度/m m图3不同钢级管道最大安全运行压力与缺陷深度关系由图3和表3可以看出,相同的腐蚀深度,钢级越高,管道的最大允许腐蚀长度越大,并且管道腐蚀后的最大安全运行压力越大,管道腐蚀后的安全性越高;当腐蚀深度大于3n"f l'n时,X52管道腐蚀长度大于最大允许长度,管道必须进行更换或维修,而对于X70和X80管道,这一临界值分别为10r t l m和12 nl l n,计算管道处于缺陷长度不可接受临界点时的d/t值,分别为0.3、0.526、0.545,如果缺陷深度与壁厚的比值大于此值,管道失效。