最新橡胶工艺原理14
橡胶成型原理

橡胶成型原理
橡胶成型原理指的是将橡胶材料通过特定的加工工艺,加热软化后注入模具中,经过冷却固化形成所需形状的工艺过程。
橡胶成型原理主要涉及到以下几个方面:
1. 橡胶材料选择:根据不同的需求,选择适当的橡胶材料进行成型。
常用的橡胶材料有天然橡胶、丁苯橡胶、氯丁橡胶等。
2. 模具设计:根据产品的形状和尺寸要求,设计相应的模具。
模具通常由上模和下模组成,可以根据需要加入一些辅助结构,如冷却水道和排气孔等。
3. 橡胶材料处理:将橡胶材料加热至一定温度,使其软化,便于注入模具中。
这一步骤通常称为预热或热塑化处理。
4. 模具注塑:将软化的橡胶材料注入模具中。
通常使用注射机将橡胶材料注入模具的腔室中,然后通过模具的开合运动,使橡胶材料填充整个模腔。
5. 冷却固化:注塑完成后,模具会快速冷却,使橡胶材料迅速固化。
这是为了保证成型件的尺寸稳定性和物理性能。
6. 拆模与处理:冷却固化后,将模具打开,取出成型件。
成型件通常需要进行去除毛刺、修整或进行表面处理等工艺。
综上所述,橡胶成型原理是通过将橡胶材料加热软化后注入模具中,经冷却固化形成所需形状的工艺过程。
这一过程包括橡
胶材料选择、模具设计、橡胶材料处理、模具注塑、冷却固化以及成品处理等多个环节。
橡胶加工原理
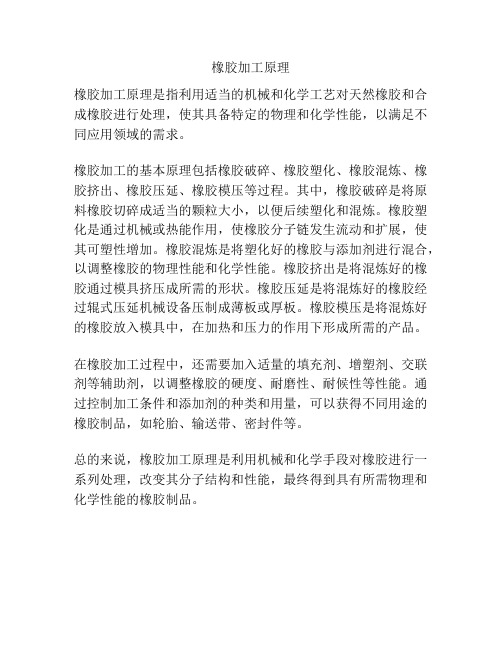
橡胶加工原理
橡胶加工原理是指利用适当的机械和化学工艺对天然橡胶和合成橡胶进行处理,使其具备特定的物理和化学性能,以满足不同应用领域的需求。
橡胶加工的基本原理包括橡胶破碎、橡胶塑化、橡胶混炼、橡胶挤出、橡胶压延、橡胶模压等过程。
其中,橡胶破碎是将原料橡胶切碎成适当的颗粒大小,以便后续塑化和混炼。
橡胶塑化是通过机械或热能作用,使橡胶分子链发生流动和扩展,使其可塑性增加。
橡胶混炼是将塑化好的橡胶与添加剂进行混合,以调整橡胶的物理性能和化学性能。
橡胶挤出是将混炼好的橡胶通过模具挤压成所需的形状。
橡胶压延是将混炼好的橡胶经过辊式压延机械设备压制成薄板或厚板。
橡胶模压是将混炼好的橡胶放入模具中,在加热和压力的作用下形成所需的产品。
在橡胶加工过程中,还需要加入适量的填充剂、增塑剂、交联剂等辅助剂,以调整橡胶的硬度、耐磨性、耐候性等性能。
通过控制加工条件和添加剂的种类和用量,可以获得不同用途的橡胶制品,如轮胎、输送带、密封件等。
总的来说,橡胶加工原理是利用机械和化学手段对橡胶进行一系列处理,改变其分子结构和性能,最终得到具有所需物理和化学性能的橡胶制品。
橡胶 工艺 原理

橡胶工艺原理
橡胶是一种由橡胶树的乳液经过加工制成的具有弹性的材料。
橡胶的工艺原理主要包括以下几个方面。
1. 采集橡胶乳液:橡胶树的树干被割开后,乳液会自然流出。
采集工人使用刮刀将乳液慢慢刮下,收集到容器中。
2. 乳液稳定化:采集到的橡胶乳液中含有大量的水分和其他杂质,需要经过稳定化处理。
常用的稳定化剂包括氨水和醋酸,它们可以使乳液保持稳定状态,并防止乳液中的橡胶团聚。
3. 合成橡胶:乳液经过稳定化处理后,需要加入硫化剂、填充剂和加工助剂等多种化学物质进行合成橡胶的加工。
其中,硫化剂可以使橡胶分子之间的交联结构更加牢固,增加橡胶材料的强度和耐磨性;填充剂可以提高橡胶材料的硬度和耐磨性;加工助剂则可以调整橡胶材料的流动性和加工性能。
4. 橡胶成型:合成橡胶经过调配后,可以通过各种成型方法将其制成不同形状的橡胶制品。
常见的成型方法包括压延、压缩模压、浇注和挤出等。
5. 硫化和固化:成型后的橡胶制品需要进行硫化或固化处理,使其获得所需的弹性和耐磨性。
硫化是将成型的橡胶制品置于加热的硫化炉中,在一定温度下与硫化剂反应,形成较为稳定的交联结构;固化则是使用特定的固化剂或光线照射,使成型的橡胶制品的分子链交联,增加其硬度和强度。
通过以上的工艺原理,橡胶可以被制备成各种应用于工业、交通、建筑和日常生活中的橡胶制品,如轮胎、密封件、橡胶管、橡胶鞋等。
橡胶加工原理

橡胶加工原理
橡胶是一种重要的材料,广泛应用于汽车轮胎、橡胶制品、橡胶管等领域。
橡胶的加工原理是指将橡胶原料通过一系列的加工工艺,使其具有特定的物理和化学性能,以满足不同领域的需求。
橡胶加工原理主要包括橡胶混炼、压延、硫化等过程。
首先,橡胶混炼是橡胶加工的第一步。
橡胶混炼的目的是将橡胶原料与各种添加剂充分混合,以提高橡胶的可加工性和性能。
混炼过程中,橡胶原料经过粗炼、精炼、压片等工艺,最终形成均匀的橡胶混炼胶。
橡胶混炼的质量直接影响着后续加工工艺和成品的质量。
其次,橡胶压延是橡胶加工的重要环节。
橡胶压延是指将橡胶混炼胶通过压延机进行塑炼,使其成为具有一定形状和尺寸的橡胶片或橡胶带。
在压延过程中,橡胶混炼胶经过预热、压延、冷却等工艺,最终形成具有一定厚度和宽度的橡胶半成品。
橡胶压延的质量直接影响着成品的外观和性能。
最后,橡胶硫化是橡胶加工的关键环节。
橡胶硫化是指将橡胶半成品通过硫化机进行硫化处理,使其具有良好的耐热、耐老化和
弹性等性能。
在硫化过程中,橡胶半成品经过加热、硫化、冷却等工艺,最终形成具有一定硬度和弹性的橡胶成品。
橡胶硫化的质量直接影响着成品的使用寿命和性能稳定性。
总之,橡胶加工原理是橡胶加工过程中的核心内容,它直接影响着成品的质量和性能。
只有深入理解橡胶加工原理,并严格控制每个环节的质量,才能生产出高质量的橡胶制品,满足不同领域的需求。
希望本文对橡胶加工原理有所帮助,谢谢阅读!。
橡胶工艺原理教学课件全套
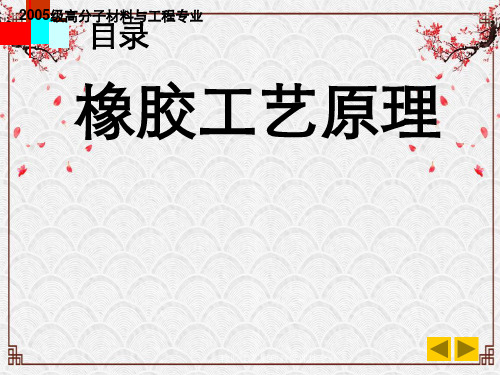
橡胶工艺原理教学课件全套
七、橡胶制品的分类
各类轮胎
胶管 胶带类
分类
工业制品 (杂制品)
鞋类
橡胶工艺原理教学课件全套
鞋类
橡胶工艺原理教学课件全套
工业杂制品
橡胶工艺原理教学课件全套
五、生胶和配合剂
配合剂——在生胶中所加入的各种化学药品。
橡胶工艺原理教学课件全套
绪 论[学习要求]
学习目的: 通过学习,初步了解本门课程的主要内容,
能正确使用相关术语,并对本门课程产生兴趣。 学习重点:
橡胶行业中常见的几个概念:橡胶(包括生 胶和硫化胶)以及橡胶类似物。 学习难点:
生胶和硫化胶概念的区别。
橡胶工艺原理教学课件全套
一、橡胶的发展历史
1.天然橡胶的发现和利用
命名 分类
趋于按原料单体组成来命名 如由丁二烯聚合的叫丁二
烯橡胶;由丁二烯和苯乙烯 ①通分用类合趋成于橡按胶其:性性能共能和聚与用的N途则R可叫相分丁近为苯,:橡物胶机。
性能和加工性能较好。
②特种合成橡胶:具有特殊性能
橡胶工艺原理教学课件全套
二、通用合成橡胶
(一)聚丁二烯橡胶(顺丁胶,BR,无色或 浅色,透明)
(1)考古发现人类在11世纪就开始使用橡胶。 (2)1493~1496年哥伦布发现美洲大陆时看到当地民玩 耍橡胶球并将其带回欧洲,欧洲人开始认识天然橡胶。 (3) 1735年,法国科学家 Condamine等将当地居民所 制橡胶制品带回欧洲,引起进一步研究和利用橡胶的兴 趣。 (4)1823年在英国建立第一个橡胶工厂,将橡胶溶于苯
类型 生胶及橡胶类似物 硫化体系(硫化剂促进剂
天然橡胶的制造原理及过程
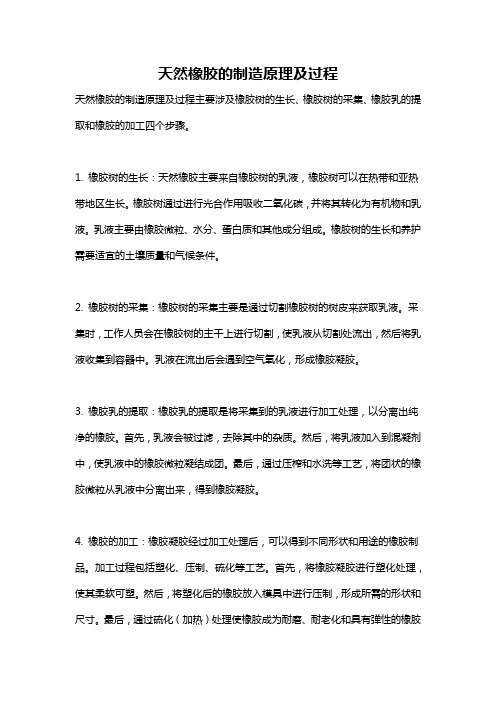
天然橡胶的制造原理及过程
天然橡胶的制造原理及过程主要涉及橡胶树的生长、橡胶树的采集、橡胶乳的提取和橡胶的加工四个步骤。
1. 橡胶树的生长:天然橡胶主要来自橡胶树的乳液,橡胶树可以在热带和亚热带地区生长。
橡胶树通过进行光合作用吸收二氧化碳,并将其转化为有机物和乳液。
乳液主要由橡胶微粒、水分、蛋白质和其他成分组成。
橡胶树的生长和养护需要适宜的土壤质量和气候条件。
2. 橡胶树的采集:橡胶树的采集主要是通过切割橡胶树的树皮来获取乳液。
采集时,工作人员会在橡胶树的主干上进行切割,使乳液从切割处流出,然后将乳液收集到容器中。
乳液在流出后会遇到空气氧化,形成橡胶凝胶。
3. 橡胶乳的提取:橡胶乳的提取是将采集到的乳液进行加工处理,以分离出纯净的橡胶。
首先,乳液会被过滤,去除其中的杂质。
然后,将乳液加入到混凝剂中,使乳液中的橡胶微粒凝结成团。
最后,通过压榨和水洗等工艺,将团状的橡胶微粒从乳液中分离出来,得到橡胶凝胶。
4. 橡胶的加工:橡胶凝胶经过加工处理后,可以得到不同形状和用途的橡胶制品。
加工过程包括塑化、压制、硫化等工艺。
首先,将橡胶凝胶进行塑化处理,使其柔软可塑。
然后,将塑化后的橡胶放入模具中进行压制,形成所需的形状和尺寸。
最后,通过硫化(加热)处理使橡胶成为耐磨、耐老化和具有弹性的橡胶
制品。
以上就是天然橡胶的制造原理及过程。
天然橡胶制造过程的细节和具体工艺可能因不同的工厂或生产线而有所不同。
橡胶工艺原理
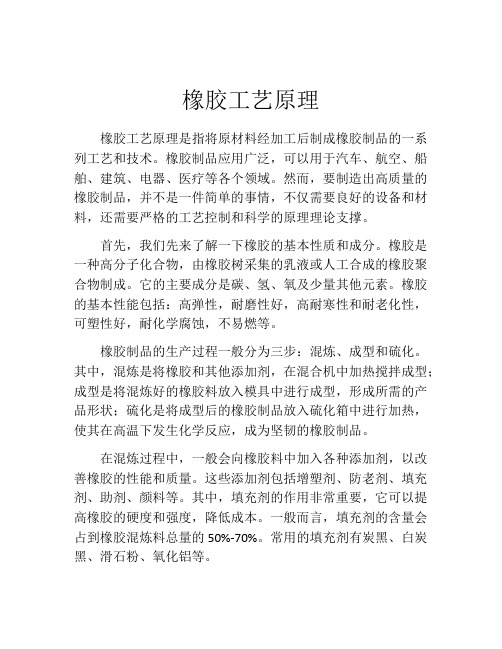
橡胶工艺原理橡胶工艺原理是指将原材料经加工后制成橡胶制品的一系列工艺和技术。
橡胶制品应用广泛,可以用于汽车、航空、船舶、建筑、电器、医疗等各个领域。
然而,要制造出高质量的橡胶制品,并不是一件简单的事情,不仅需要良好的设备和材料,还需要严格的工艺控制和科学的原理理论支撑。
首先,我们先来了解一下橡胶的基本性质和成分。
橡胶是一种高分子化合物,由橡胶树采集的乳液或人工合成的橡胶聚合物制成。
它的主要成分是碳、氢、氧及少量其他元素。
橡胶的基本性能包括:高弹性,耐磨性好,高耐寒性和耐老化性,可塑性好,耐化学腐蚀,不易燃等。
橡胶制品的生产过程一般分为三步:混炼、成型和硫化。
其中,混炼是将橡胶和其他添加剂,在混合机中加热搅拌成型;成型是将混炼好的橡胶料放入模具中进行成型,形成所需的产品形状;硫化是将成型后的橡胶制品放入硫化箱中进行加热,使其在高温下发生化学反应,成为坚韧的橡胶制品。
在混炼过程中,一般会向橡胶料中加入各种添加剂,以改善橡胶的性能和质量。
这些添加剂包括增塑剂、防老剂、填充剂、助剂、颜料等。
其中,填充剂的作用非常重要,它可以提高橡胶的硬度和强度,降低成本。
一般而言,填充剂的含量会占到橡胶混炼料总量的50%-70%。
常用的填充剂有炭黑、白炭黑、滑石粉、氧化铝等。
成型过程则包括挤出、压缩成型、注塑、挤压等多种方式。
其中,挤出是指将热压橡胶料挤出成型,常用于制造板材、管材和带材等;压缩成型是将混炼好的橡胶料放到压力机模具中压缩成型,常用于制造密封件、垫片和橡胶板等;注塑是将热熔态的橡胶料注入模具中成型,常用于制造零件、机械件等;挤压是将橡胶料通过挤压机制成所需的形状,常用于制造密封圈、管子等产品。
硫化则是通过加热使橡胶聚合物中的硫和碳原子相互交联,从而增加橡胶制品的硬度和强度,提高耐磨性和耐寒性。
硫化温度和时间是影响橡胶制品性能的关键因素,硫化温度过高或时间过长会导致橡胶制品变质、失去弹性等问题。
总的来说,橡胶工艺原理的核心问题在于如何在制造过程中控制好各种参数,确保所制造的橡胶制品具有优异的性能和质量。
实验14 -橡胶的成型加工

实验14橡胶制品的成型加工一、实验目的1.掌握橡胶制品配方设计基本知识。
熟悉橡胶加工全过程和橡胶制品模型硫化工艺;2.了解橡胶加工的主要机械设备如开炼机、平板硫化机等基本结构,掌握这些设备的操作方法;3.掌握橡胶物理机械性能测试试样制备工艺及性能测试方法。
二、实验原理橡胶制品的基本工艺过程包括配合,生胶塑炼,胶料混炼,成型,硫化五个基本过程,如图14-1所示。
图14-1橡胶制品生产工艺过程1.生胶的塑炼生胶是线型的高分子化合物,在常温下大多数处于高弹态。
然而生胶的高弹性却给成型加工带来极大的困难,一方面各种配合剂无法在生胶中分散均匀,另一方面,由于可塑性小,不能获得所需的各种形状。
为满足各种加工工艺的要求,使生胶由强韧的弹性状态变成柔软而具有可塑性的状态的工艺过程称作塑炼。
生胶经塑炼以增加其可塑性,其实质是橡胶分子链断裂,相对分子质量降低,从而橡胶的弹性下降。
在橡胶塑炼时,主要受到机械力、氧、热、电和某些化学增塑剂等因素的作用。
工艺上用以降低橡胶相对分子质量获得可塑性的塑炼方法可分为机械塑炼法和化学塑炼法两大类,其中机械塑炼法应用最为广泛。
橡胶机械塑炼的实质是力化学反应过程,即以机械力作用及在氧或其它自由基受体存在下进行的。
在机械塑炼过程中,机械力作用使大分子链断裂,氧对橡胶分子起化学降解作用,这两个作用同时存在。
本实验选用开炼机对天然橡胶进行机械法塑炼。
天然生胶置于开炼机的两个相向转动的辊筒间隙中,在常温(小于50℃)下反复受机械力作用,使分子链断裂,与此同时断裂后的大分子自由基在空气中的氧化作用下,发生了一系列力学与化学反应,最终达到降解,生胶从原先强韧高弹性变为柔软可塑性,满足混炼的要求。
塑炼的程度和塑炼的效率主要与辊筒的间隙和温度有关,若间隙愈小、温度愈低,力化学作用愈大,塑炼效率愈高。
此外,塑炼的时间,塑炼工艺操作方法及是否加入塑解剂也影响塑炼的效果。
2.橡胶的配合橡胶必须经过交联(硫化)才能改善其物理机械性能和化学性能,使橡胶制品具有实用价值。
橡胶硫化原理

橡胶硫化原理橡胶硫化是指橡胶在加入硫化剂的条件下,经过一定时间和温度的处理,使其分子内部发生交联反应,从而改善橡胶的物理性能和化学性能的过程。
橡胶硫化是橡胶加工的重要工艺之一,也是橡胶制品得以广泛应用的基础。
下面将从硫化的原理、影响硫化的因素以及硫化后橡胶的性能等方面对橡胶硫化进行详细介绍。
橡胶硫化的原理是指在硫化剂的作用下,橡胶分子链中的双键发生断裂,形成自由基,然后自由基与硫原子结合,形成硫键,最终实现橡胶分子的交联。
这种交联作用可以使橡胶分子链之间产生空间网状结构,从而使橡胶变得更加坚固和耐磨。
同时,硫化还可以改善橡胶的耐老化性能,提高橡胶的强度、硬度和弹性,增加橡胶的耐磨性和耐油性,改善橡胶的加工性能和热稳定性。
影响橡胶硫化的因素有很多,主要包括硫化剂的种类和用量、硫化温度和硫化时间等。
硫化剂的种类和用量直接影响着橡胶硫化的速度和程度,不同种类的硫化剂对橡胶的硫化速度和效果都有所差异。
硫化温度和硫化时间则是影响硫化反应进行的重要因素,温度过高会导致硫化剂过早挥发,温度过低则会延缓硫化反应的进行,硫化时间过长则会造成硫化过度,影响橡胶的性能。
硫化后的橡胶具有很多优良的性能,如耐热性、耐寒性、耐老化性、耐磨性、耐油性等。
这些性能使硫化后的橡胶被广泛应用于轮胎、橡胶管、橡胶板、橡胶密封件、橡胶软管等领域。
同时,硫化后的橡胶还可以通过改变硫化条件和硫化体系,实现不同硬度、不同强度和不同弹性的橡胶制品。
总之,橡胶硫化是一种重要的加工工艺,通过硫化过程可以改善橡胶的物理性能和化学性能,使其得以广泛应用于各个领域。
因此,对橡胶硫化原理的深入了解和掌握,对于提高橡胶制品的质量和性能具有重要意义。
橡胶制品的工作原理
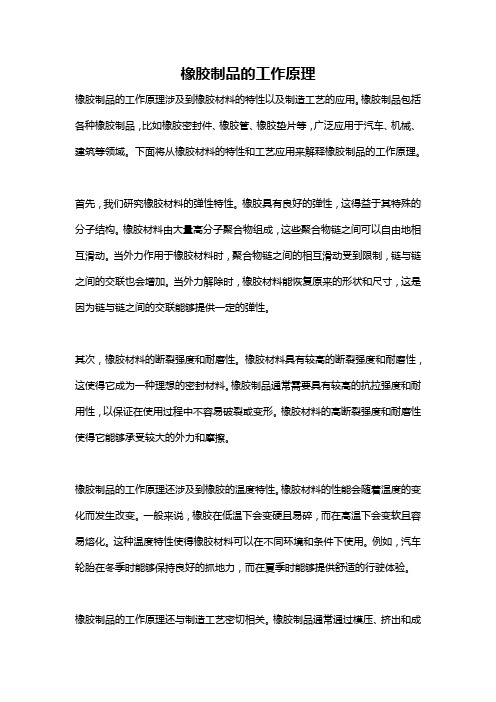
橡胶制品的工作原理橡胶制品的工作原理涉及到橡胶材料的特性以及制造工艺的应用。
橡胶制品包括各种橡胶制品,比如橡胶密封件、橡胶管、橡胶垫片等,广泛应用于汽车、机械、建筑等领域。
下面将从橡胶材料的特性和工艺应用来解释橡胶制品的工作原理。
首先,我们研究橡胶材料的弹性特性。
橡胶具有良好的弹性,这得益于其特殊的分子结构。
橡胶材料由大量高分子聚合物组成,这些聚合物链之间可以自由地相互滑动。
当外力作用于橡胶材料时,聚合物链之间的相互滑动受到限制,链与链之间的交联也会增加。
当外力解除时,橡胶材料能恢复原来的形状和尺寸,这是因为链与链之间的交联能够提供一定的弹性。
其次,橡胶材料的断裂强度和耐磨性。
橡胶材料具有较高的断裂强度和耐磨性,这使得它成为一种理想的密封材料。
橡胶制品通常需要具有较高的抗拉强度和耐用性,以保证在使用过程中不容易破裂或变形。
橡胶材料的高断裂强度和耐磨性使得它能够承受较大的外力和摩擦。
橡胶制品的工作原理还涉及到橡胶的温度特性。
橡胶材料的性能会随着温度的变化而发生改变。
一般来说,橡胶在低温下会变硬且易碎,而在高温下会变软且容易熔化。
这种温度特性使得橡胶材料可以在不同环境和条件下使用。
例如,汽车轮胎在冬季时能够保持良好的抓地力,而在夏季时能够提供舒适的行驶体验。
橡胶制品的工作原理还与制造工艺密切相关。
橡胶制品通常通过模压、挤出和成型等工艺进行生产。
在模压过程中,橡胶材料被加热并注入到模具中,然后经过冷却和固化,最终得到所需的形状和尺寸。
在挤出过程中,橡胶材料被挤压通过模头形成所需的截面形状。
在成型过程中,橡胶材料通过注塑、压缩或胶接等工艺与其他材料结合。
这些制造工艺的运用可以使橡胶制品具有理想的性能和形状,以满足各种应用需求。
综上所述,橡胶制品的工作原理涉及到橡胶材料的弹性特性、断裂强度和耐磨性、温度特性以及制造工艺的应用。
橡胶制品通过其特殊的物理和化学性质,能够在各种环境和条件下发挥优异的性能。
橡胶制品的工作原理的理解对于合理选用橡胶材料,并进行正确的制造和使用,具有重要的意义。
橡胶工艺原理
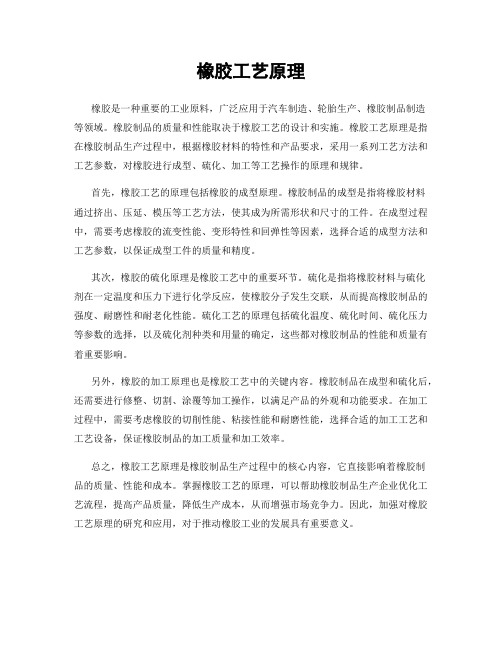
橡胶工艺原理
橡胶是一种重要的工业原料,广泛应用于汽车制造、轮胎生产、橡胶制品制造
等领域。
橡胶制品的质量和性能取决于橡胶工艺的设计和实施。
橡胶工艺原理是指在橡胶制品生产过程中,根据橡胶材料的特性和产品要求,采用一系列工艺方法和工艺参数,对橡胶进行成型、硫化、加工等工艺操作的原理和规律。
首先,橡胶工艺的原理包括橡胶的成型原理。
橡胶制品的成型是指将橡胶材料
通过挤出、压延、模压等工艺方法,使其成为所需形状和尺寸的工件。
在成型过程中,需要考虑橡胶的流变性能、变形特性和回弹性等因素,选择合适的成型方法和工艺参数,以保证成型工件的质量和精度。
其次,橡胶的硫化原理是橡胶工艺中的重要环节。
硫化是指将橡胶材料与硫化
剂在一定温度和压力下进行化学反应,使橡胶分子发生交联,从而提高橡胶制品的强度、耐磨性和耐老化性能。
硫化工艺的原理包括硫化温度、硫化时间、硫化压力等参数的选择,以及硫化剂种类和用量的确定,这些都对橡胶制品的性能和质量有着重要影响。
另外,橡胶的加工原理也是橡胶工艺中的关键内容。
橡胶制品在成型和硫化后,还需要进行修整、切割、涂覆等加工操作,以满足产品的外观和功能要求。
在加工过程中,需要考虑橡胶的切削性能、粘接性能和耐磨性能,选择合适的加工工艺和工艺设备,保证橡胶制品的加工质量和加工效率。
总之,橡胶工艺原理是橡胶制品生产过程中的核心内容,它直接影响着橡胶制
品的质量、性能和成本。
掌握橡胶工艺的原理,可以帮助橡胶制品生产企业优化工艺流程,提高产品质量,降低生产成本,从而增强市场竞争力。
因此,加强对橡胶工艺原理的研究和应用,对于推动橡胶工业的发展具有重要意义。
橡胶硫化工艺

橡胶硫化工艺橡胶硫化工艺是将天然橡胶或合成橡胶通过硫化反应,使其具备强度、耐磨性、耐老化性等特性的一种工艺。
本文将从橡胶硫化的原理、硫化剂的选择、硫化工艺流程以及硫化后橡胶的性能等方面展开阐述。
一、橡胶硫化的原理橡胶硫化是指通过将橡胶与硫化剂在一定温度下反应,使橡胶中的双键与硫原子发生加成反应,形成交联结构的过程。
在硫化过程中,硫化剂中的硫原子会与橡胶中的双键发生反应,形成硫化橡胶。
硫化反应可以使橡胶具备耐高温、耐溶剂、耐老化等优异性能。
二、硫化剂的选择硫化剂是橡胶硫化过程中的重要组成部分,常用的硫化剂有硫、过氧化氮、过氧化物等。
硫是一种常用的硫化剂,其硫化反应速度较慢,但可以获得较好的硫化效果。
过氧化氮是一种加速剂,可以提高硫化反应速度和效果。
过氧化物则是一种高温硫化剂,适用于高温硫化橡胶。
三、硫化工艺流程橡胶硫化一般包括预硫化和硫化两个阶段。
预硫化是指在较低温度下对橡胶进行预处理,使其具备一定的硫化程度,提高硫化效果。
硫化是指在较高温度下对橡胶进行硫化反应,形成交联结构。
硫化温度一般在120℃-180℃之间,硫化时间根据橡胶种类和硫化剂的不同而定。
四、硫化后橡胶的性能橡胶经过硫化后,其性能得到显著改善。
硫化可以提高橡胶的强度、硬度、耐磨性、耐油性、耐老化性等。
硫化后的橡胶具有较好的弹性和可塑性,广泛应用于橡胶制品、轮胎、密封材料等领域。
总结:橡胶硫化工艺是将橡胶经过硫化反应,使其具备优异性能的一种工艺。
硫化剂的选择和硫化工艺流程对于硫化效果具有重要影响。
硫化后的橡胶具有较好的强度、耐磨性、耐老化性等性能,广泛应用于各个领域。
橡胶硫化工艺的研究和应用对于提高橡胶制品的品质和性能具有重要意义。
橡胶的成型加工原理

通常在三辊压延机中采用中、下辊等速,中、 上辊采用低速比的方法
3、压延效应
定义:压延后的胶片,纵向扯断强度比横向大,伸长率 比横向小,收缩率则比横向大,此纵横向性能差异的现 象,叫做“压延效应” 产生原因:胶料中橡胶和配合剂分子经压延产生定向排列 应用:对球胆制品不利
对需要高纵向扯断强度的制品有利
4.常用橡胶的压延特性
(1)天然橡胶
热塑性大,收缩率小,易压延
(2)丁苯橡胶
收缩率大,需充分塑炼 收缩快而裹入的气泡多,难排除
(3)氯丁橡胶
对温度敏感,需控制辊温 在70~94℃时因胶粘辊不易压延
(4)丁腈橡胶
热塑性小,收缩性大,需加入填充剂或软 化剂,减少收缩率
粘性小,易粘冷辊
配合剂种类 /大小
混炼
塑炼
常用胶混炼特性
辊挤压成型
压片/纹/贴胶
热炼/可塑度 /辊温/辊速
橡胶加工
压延
挤出
常用胶压延特性
力化学降解
开/密炼
分子量/温度/氧 /化学塑解剂 常用胶塑炼特性
造型/联动 螺杆挤出
胶性质/挤出 机/温度/速度 常用胶挤出特性
完成下表
HOMEWORK
塑炼 混炼 压延 挤出
原理 加工条件 影响因素 加工方法
(B)压型
使胶料压制成具有一定断面形状或表面有某种花纹
(1)压型的原理
据胶料流动性的变化,急速冷却,使花纹定型
(2)压型的要求
压型要求规格准确、花纹清晰、胶料致密性好
(C)织物挂胶
在骨架织物上覆上一层薄胶(贴胶、擦胶)
(1)挂胶目的
使织物的线与线、层与层之间互相紧密的贴合成整体, 共同承受外力的作用; 提高织物弹性、防水性,保证制品有良好的使用性能
最新橡胶工艺原理_十_王作龄
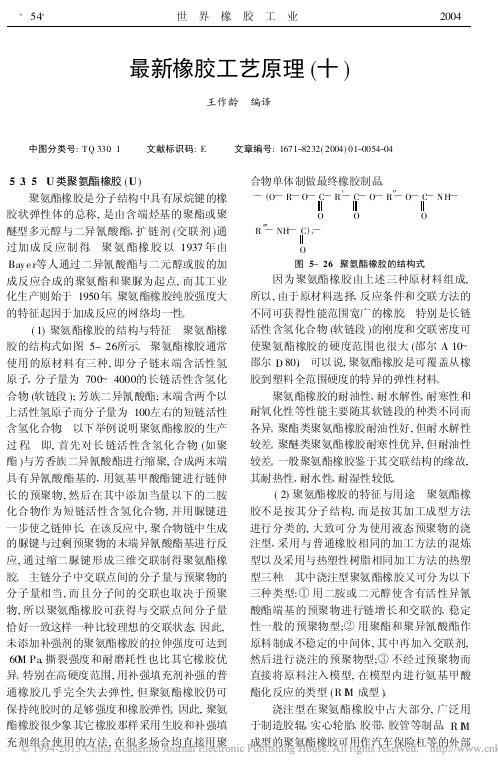
的硫黄硫化型。 氟化膦腈橡胶因其骨架完全由 无机聚合物构成, 而且其侧链的氟烷氧基保护 着主链, 所以它具有优异的耐寒性、耐热性, 可 使用的温度范围较宽 ( - 60~ 200°C ), 同时其耐 油性、耐化学品性、生物适应性也较优异。 磷腈 橡胶一般以混炼胶形式供给, 因其价格较高, 现 在仅 部分 用于 军工、 宇宙 、飞机 制造 业和 医疗 等
nN aS x
— ( CH 2— CH2— O— CH 2— O— CH 2—
CH 2— S x )n— + 2nN aC l
由上述缩聚反应制得的高分子量聚硫橡胶, 通
过 氢硫 化钠 ( N aSH )和 亚硫 酸钠 ( N a2SO 2 )还
原, 使其分子断裂而变成低分子量液体聚合物。
聚硫橡胶的最终结构如图 5- 27所示, 其分子
量约在 1000~ 8000的范围内。
HS— ( C2H 4— O— CH 2— O— CH2— S— S )n— C2H 4— O— CH 2— O— C2H 4— SH
图 5- 27 聚硫橡胶的结构式
( 2) 聚硫橡胶的结构与特征 液体聚硫橡
胶的分子末端含有活性的巯基, 在常温下比较
稳定。固化反应系利用巯基中的活性氢, 固化剂
应, 通过缩二脲键形成三维交联制得聚氨酯橡 胶。 主链分子中交联点间的分子量与预聚物的 分子量相当, 而且分子间的交联也取决于预聚 物, 所以聚氨酯橡胶可获得与交联点间分子量 恰好一致这样一种比较理想的交联状态。因此, 未添加补强剂的聚氨酯橡胶的拉伸强度可达到
橡胶浇注工艺
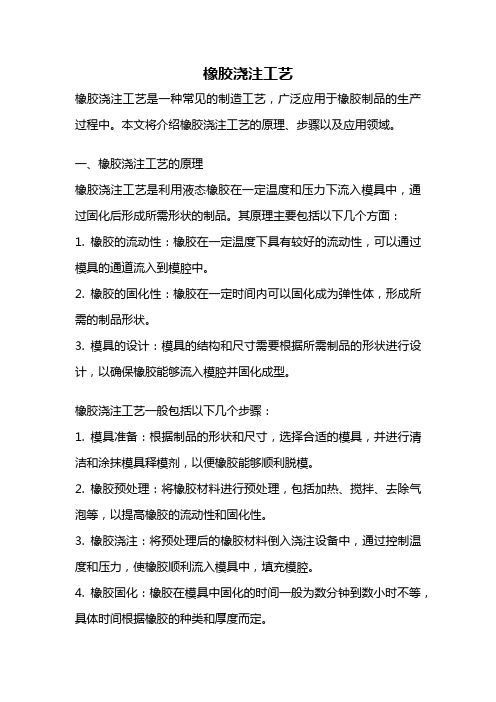
橡胶浇注工艺橡胶浇注工艺是一种常见的制造工艺,广泛应用于橡胶制品的生产过程中。
本文将介绍橡胶浇注工艺的原理、步骤以及应用领域。
一、橡胶浇注工艺的原理橡胶浇注工艺是利用液态橡胶在一定温度和压力下流入模具中,通过固化后形成所需形状的制品。
其原理主要包括以下几个方面:1. 橡胶的流动性:橡胶在一定温度下具有较好的流动性,可以通过模具的通道流入到模腔中。
2. 橡胶的固化性:橡胶在一定时间内可以固化成为弹性体,形成所需的制品形状。
3. 模具的设计:模具的结构和尺寸需要根据所需制品的形状进行设计,以确保橡胶能够流入模腔并固化成型。
橡胶浇注工艺一般包括以下几个步骤:1. 模具准备:根据制品的形状和尺寸,选择合适的模具,并进行清洁和涂抹模具释模剂,以便橡胶能够顺利脱模。
2. 橡胶预处理:将橡胶材料进行预处理,包括加热、搅拌、去除气泡等,以提高橡胶的流动性和固化性。
3. 橡胶浇注:将预处理后的橡胶材料倒入浇注设备中,通过控制温度和压力,使橡胶顺利流入模具中,填充模腔。
4. 橡胶固化:橡胶在模具中固化的时间一般为数分钟到数小时不等,具体时间根据橡胶的种类和厚度而定。
5. 脱模和后处理:橡胶固化后,将制品从模具中取出,进行脱模。
然后根据需要进行修整、清洁、检验等后处理工序。
三、橡胶浇注工艺的应用领域橡胶浇注工艺广泛应用于橡胶制品的生产中,主要包括以下几个领域:1. 汽车工业:橡胶浇注工艺可以用于汽车零部件的制造,如橡胶密封件、橡胶管件等。
2. 电子工业:橡胶浇注工艺可以用于电子产品的制造中,如橡胶按键、橡胶密封圈等。
3. 医疗器械:橡胶浇注工艺可以用于医疗器械的制造,如橡胶导管、橡胶垫片等。
4. 工程机械:橡胶浇注工艺可以用于工程机械的制造,如橡胶履带、橡胶振动器等。
5. 日用品:橡胶浇注工艺可以用于日用品的制造,如橡胶手柄、橡胶垫等。
橡胶浇注工艺是一种常见且重要的制造工艺,通过控制橡胶的流动性和固化性,以及合理设计模具,可以制造出各种形状的橡胶制品。
2020年(塑料橡胶材料)橡胶工艺原理讲稿橡胶工艺原理讲稿

(塑料橡胶材料)橡胶工艺原理讲稿橡胶工艺原理讲稿《橡胶工艺原理》讲稿绪论一.橡胶材料的特点1.高弹性:弹性模量低,伸长变形大,有可恢复的变形,并能在很宽的温度(-50~150℃)范围内保持弹性。
2.粘弹性:橡胶材料在产生形变和恢复形变时受温度和时间的影响,表现有明显的应力松弛和蠕变现象,在震动或交变应力作用下,产生滞后损失。
3.电绝缘性:橡胶和塑料一样是电绝缘材料。
4.有老化现象:如金属腐蚀、木材腐朽、岩石风化一样,橡胶也会因为环境条件的变化而产生老化现象,使性能变坏,寿命下降。
5.必须进行硫化才能使用,热塑性弹性体除外。
6.必须加入配合剂。
其它如比重小、硬度低、柔软性好、气密性好等特点,都属于橡胶的宝贵性能。
表征橡胶物理机械性能的指标:1.拉伸强度:又称扯断强度、抗张强度,指试片拉伸至断裂时单位断面上所承受的负荷,单位为兆帕(MPa),以往为公斤力/平方厘米(kgf/cm2)。
2.定伸应力:旧称定伸强度,指试样被拉伸到一定长度时单位面积所承受的负荷。
计量单位同拉伸强度。
常用的有100%、300%和500%定伸应力。
它反映的是橡胶抵抗外力变形能力的高低。
3.撕裂强度:将特殊试片(带有割口或直角形)撕裂时单位厚度所承受的负荷,表示材料的抗撕裂性,单位为kN/m。
4.伸长率:试片拉断时,伸长部分与原长度之比叫作伸长率;用百分比表示。
5.永久变形:试样拉伸至断裂后,标距伸长变形不可恢复部分占原始长度的百分比。
在解除了外力作用并放置一定时间(一般为3分钟),以%表示。
6.回弹性:又称冲击弹性,指橡胶受冲击之后恢复原状的能力,以%表示。
7.硬度:表示橡胶抵抗外力压入的能力,常用邵尔硬度计测定。
橡胶的硬度范围一般在20~100之间,单位为邵氏A。
二.关于橡胶的几个概念1.橡胶:世界上通用的橡胶的定义引自美国的国家标准ASTM-D1566(America Society of Test and Material)。
《橡胶工艺原理》讲稿doc-《橡胶工艺原理》讲稿
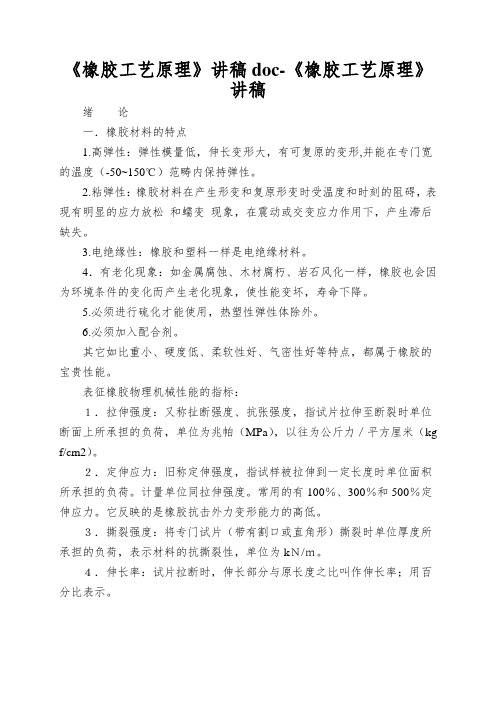
《橡胶工艺原理》讲稿doc-《橡胶工艺原理》讲稿绪论一.橡胶材料的特点1.高弹性:弹性模量低,伸长变形大,有可复原的变形,并能在专门宽的温度(-50~150℃)范畴内保持弹性。
2.粘弹性:橡胶材料在产生形变和复原形变时受温度和时刻的阻碍,表现有明显的应力放松和蠕变现象,在震动或交变应力作用下,产生滞后缺失。
3.电绝缘性:橡胶和塑料一样是电绝缘材料。
4.有老化现象:如金属腐蚀、木材腐朽、岩石风化一样,橡胶也会因为环境条件的变化而产生老化现象,使性能变坏,寿命下降。
5.必须进行硫化才能使用,热塑性弹性体除外。
6.必须加入配合剂。
其它如比重小、硬度低、柔软性好、气密性好等特点,都属于橡胶的宝贵性能。
表征橡胶物理机械性能的指标:1.拉伸强度:又称扯断强度、抗张强度,指试片拉伸至断裂时单位断面上所承担的负荷,单位为兆帕(MPa),以往为公斤力/平方厘米(kg f/cm2)。
2.定伸应力:旧称定伸强度,指试样被拉伸到一定长度时单位面积所承担的负荷。
计量单位同拉伸强度。
常用的有100%、300%和500%定伸应力。
它反映的是橡胶抗击外力变形能力的高低。
3.撕裂强度:将专门试片(带有割口或直角形)撕裂时单位厚度所承担的负荷,表示材料的抗撕裂性,单位为kN/m。
4.伸长率:试片拉断时,伸长部分与原长度之比叫作伸长率;用百分比表示。
5.永久变形:试样拉伸至断裂后,标距伸长变形不可复原部分占原始长度的百分比。
在解除了外力作用并放置一定时刻(一样为3分钟),以%表示。
6.回弹性:又称冲击弹性,指橡胶受冲击之后复原原状的能力,以%表示。
7.硬度:表示橡胶抗击外力压入的能力,常用邵尔硬度计测定。
橡胶的硬度范畴一样在20~100之间,单位为邵氏A。
二.关于橡胶的几个概念1.橡胶:世界上通用的橡胶的定义引自美国的国家标准ASTM-D156 6(America Society of Test and Material)。
定义如下:橡胶是一种材料,它在大的变形下能迅速而有力地复原其变形,能够被改性(硫化)。
橡胶包胶工艺
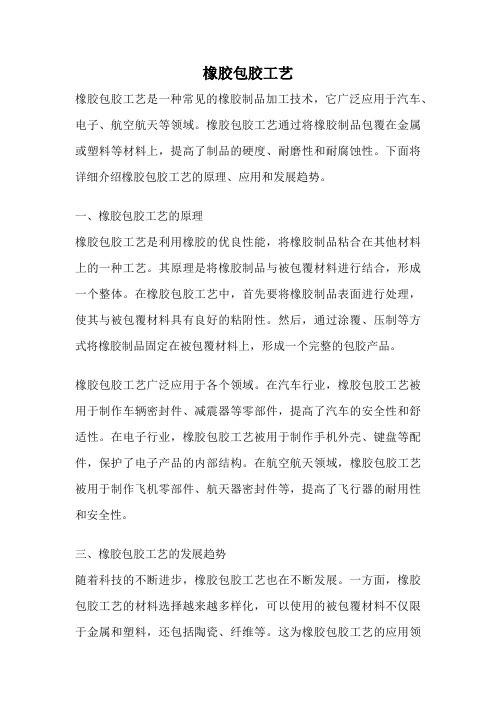
橡胶包胶工艺橡胶包胶工艺是一种常见的橡胶制品加工技术,它广泛应用于汽车、电子、航空航天等领域。
橡胶包胶工艺通过将橡胶制品包覆在金属或塑料等材料上,提高了制品的硬度、耐磨性和耐腐蚀性。
下面将详细介绍橡胶包胶工艺的原理、应用和发展趋势。
一、橡胶包胶工艺的原理橡胶包胶工艺是利用橡胶的优良性能,将橡胶制品粘合在其他材料上的一种工艺。
其原理是将橡胶制品与被包覆材料进行结合,形成一个整体。
在橡胶包胶工艺中,首先要将橡胶制品表面进行处理,使其与被包覆材料具有良好的粘附性。
然后,通过涂覆、压制等方式将橡胶制品固定在被包覆材料上,形成一个完整的包胶产品。
橡胶包胶工艺广泛应用于各个领域。
在汽车行业,橡胶包胶工艺被用于制作车辆密封件、减震器等零部件,提高了汽车的安全性和舒适性。
在电子行业,橡胶包胶工艺被用于制作手机外壳、键盘等配件,保护了电子产品的内部结构。
在航空航天领域,橡胶包胶工艺被用于制作飞机零部件、航天器密封件等,提高了飞行器的耐用性和安全性。
三、橡胶包胶工艺的发展趋势随着科技的不断进步,橡胶包胶工艺也在不断发展。
一方面,橡胶包胶工艺的材料选择越来越多样化,可以使用的被包覆材料不仅限于金属和塑料,还包括陶瓷、纤维等。
这为橡胶包胶工艺的应用领域提供了更多可能性。
另一方面,橡胶包胶工艺的加工方法也在不断改进。
传统的涂覆、压制等方法已经可以实现高效、精准的包胶效果,同时也出现了一些新的加工方法,如激光包胶、热熔包胶等。
这些新的加工方法可以更好地满足特定领域的需求,提高了橡胶包胶工艺的适用性和灵活性。
橡胶包胶工艺是一种重要的橡胶制品加工技术,具有广泛的应用前景。
随着材料科学和加工技术的不断发展,橡胶包胶工艺将进一步提高制品的性能和质量,满足人们对于高性能、高可靠性橡胶制品的需求。
相信在未来的发展中,橡胶包胶工艺将发挥更大的作用,为各个行业的发展做出更大的贡献。
- 1、下载文档前请自行甄别文档内容的完整性,平台不提供额外的编辑、内容补充、找答案等附加服务。
- 2、"仅部分预览"的文档,不可在线预览部分如存在完整性等问题,可反馈申请退款(可完整预览的文档不适用该条件!)。
- 3、如文档侵犯您的权益,请联系客服反馈,我们会尽快为您处理(人工客服工作时间:9:00-18:30)。
最新橡胶工艺原理(十四)王作龄 编译 中图分类号:TQ330.1 文献标识码:E 文章编号:167128232(2004)0520047208第7章 填充剂7.1 引言填充剂是混入橡胶中以赋与橡胶补强、增容和特殊功能为目的使用的配合剂。
作为填充剂代表的炭黑不仅可以提高橡胶的定伸应力和拉伸强度等力学性能,而且还可赋与橡胶导电等性能,是橡胶材料不可缺少的配合剂。
一般,填充剂按不同材质、有无补强性和功能性进行分类。
按材质分类,有白炭黑、陶土、碳酸钙等无机填充剂和树脂、木粉、软木粉等有机填充剂。
按有无补强性分类有炭黑、白炭黑等补强性填充剂和陶土、滑石粉、碳酸钙等非补强性填充剂。
通常将用于提高橡胶物理机械强度的配合剂称为补强剂。
补强剂除了上述的补强填充剂外,还有高苯乙烯树脂等补强性树脂和补强性短纤维。
本章节以补强性高的炭黑、白炭黑和短纤维的基本性能、基本性能与橡胶复合体物理性能之间的关系及这些补强剂的补强机理为主进行叙述。
7.2 补强性填充剂补强性填充剂和非补强性填充剂的区别可用填充剂粒子的大小(粒子表面积)加以说明。
此外,粒子的形态和表面特性对橡胶的补强效果也有很大影响。
SBR中配入不同填充剂时的各比表面积与拉伸强的关系如图7-1所示。
若仅在白色填充剂范围内考虑,那么拉伸强度与比表面之间有相关性。
相同比表面积的炭黑的拉伸强度比白色填充剂的大,这是因为炭黑和橡胶分子的相互作用强。
为提高白炭黑等填充剂的补强性,大多还同时使用偶联剂。
图7-1 不同填充剂的比表面积与拉伸强度的关系(SBR1500)1—碳酸钙(55vo l%);2—硅酸盐(25vo l%);3—湿法白炭黑(25vo l%);4—炭黑(27vo l%);5—陶土(30vo l%)7.2.1 炭黑炭黑是由约95%以上无定形的炭组成的毫微米级的微粒,是在燃烧木材和煤时产生的所谓“煤烟子”(含有以多量灰分和焦油为主要成分的溶剂抽出分,炭含量在50%以下)的不同物质。
自1910年发现炭黑对橡胶具有显著的补强效果以来,炭黑成为支持橡胶工业发展的重要材料。
炭黑的用途除了用作以汽车轮胎为主的橡胶制品的补强剂外,还可用作印刷油墨、涂料、塑料等的黑色颜料,以及赋与电池活性物质以导电性的填充剂等。
但是,从数量上看,炭黑在像胶工业中的需求量占绝对多数,1996年日本橡胶工业的炭黑需求量占日本总需求量约95%,其中约75%用于汽车轮胎。
a.炭黑的种类炭黑按制造方法的分类如表7-1所示。
表7-2为A STM D1765-98的炭黑分类表。
现在,橡胶和染料工业使用的炭黑几乎都是用油炉法生产的。
表7-1 炭黑按制造方法的分类制造方法主要原料热裂解法热裂法天然气乙炔法乙炔不完全燃烧法接触法(槽法、天然气槽法、圆盘法)天然气、芳香族油灯烟法矿物油、植物油天然气炉法天然气油炉法芳香族烃油 b.炭黑的基本特性炭黑的最小单位被称为一次聚集体,微球形基本粒子之间相互溶融,被支化成链状或不规则链锁状的复杂的聚集状态(图7-2)。
作为对橡胶产生补强性的重要因素的是炭黑的基本性质——基本粒子的大小(比表面积)、一次聚集体的聚集结构和粒子表面性状。
(1)基本粒子的大小与比表面积:把构成炭黑一次聚集体的微球形部分看作单一粒子(基本粒子),其粒径及其粒径分布是炭黑最基本的特性。
炭黑的透射电子显微镜(T E M)的照片为测定了2000~10000个炭黑粒子的直径后求出的平均粒径及其分布。
具有代表性的橡胶用炭黑的T E M粒径分布如图7-3所示。
表7-2 AST M的炭黑分类(AST MD1765-98,摘要)A STM 代号旧分类(参考)吸碘值m g gDBP吸油值m l 100g压缩试样DBP吸油值m l 100g氮吸附法比表面积m2 gST SAm2 g比着色力松密度kg m3300%定伸应力M Pa3N110SA F14511398130117124335-3.2 N11516011396143121123345-3.4 N12012211498126131131335-1.2 N121121132109124117121320+0.2 N12511710489122122123370-2.6 N134142127102145134132320-0.6 N135151135117141-119320-0.4 S212-8582120105115400-6.4 N220ISA F2HM121114100115105115345-2.2 N231ISA F2LM1219286111107117390-4.6 N234120125103120113124320-0.8 N29314510092130109120375-4.8 N29910812410510399113335+0.2 S315-79759186-450-6.4 N326HA F2L S8272697878112465-4.0 N330HA F82102887976103375-1.4 N33592110948585110345+0.2 N339901201019288110345+0.3 N343921301049691114336+2.1 347HA F2H S9012410085831053350.0 N35168120977169100345+0.6 N356921541129187115280+1.4 N35884150112827899290+2.3 N37590114979391115345-0.2 N53943111844039-385-1.8 N550FEF43121884139-360-1.4 N58210018011480-67190-1.8续表7-2A STM 代号旧分类(参考)吸碘值mgg DBP 吸油值m l 100g 压缩试样DBP 吸油值m l 100g 氮吸附法比表面积m 2 g ST SA m 2 g 比着色力松密度kg m 3300%定伸应力M Pa 3N 6303678623432-465-4.4N 64236646239--513-5.4N 65036122873734370-1.0N 660GPF 3690753534-425-2.4N 683A PF35133-3735-335-0.8N 7542458572524-495-6.6N 762SR F 2LM 2765602829-505-4.8N 76531115823634375-2.0N 7723065583131505-4.8N 774SR F 2HM 2972622929-495-4.6N 7873080743032-450-4.2N 907-34-109---9.4N 908-34-109---10.2N 990M T -434098---8.6N 991M T-353898---10.2 3硫化胶(145°C ×30分)300%定伸应力是表示评价用N R 配合硫化胶与I RB #7(工业参考炭黑7#)的差。
图7-2 炭黑一次聚集体的透射电子显微镜照片图7-3 由透射电子显微镜求出的橡胶用炭黑的粒经分布 但是,用T E M 测定粒径所需的时间较长,所以不宜在现场的质量检验中采用。
因此,通常采用单位质量的比表面积替代基本粒子的大小的测定。
若基本粒子的粒度变小则单位质量的比表面积增大。
测定比表面积的做法一般是将已知道粒度的分子通过单分子吸附在炭黑表面上,再根据其吸附量求取比表面积。
作为被吸附的分子有氮、碘、溴化十六烷基三甲基铵(CTAB ),每个分子的吸附截面积是,氮为16.2∼2,碘为21.52∼2,CTAB 为61.6∼2。
通常称氮吸附法比表面积为N 2SA (m 2 g ),CTAB 法比表面积为CTAB (m 2 g ),碘吸附法比表面积为I A (m g g )。
关于炭黑的比表面积,它与橡胶的接触面积也是很重要的。
(2)一次聚集体的聚集结构:由于图象解析装置的发展,根据T E M 照片,对一次聚集体的大小和状态(结构复杂性和各向异性)直接进行测定和定量的方法也取得了很大的进步。
一次聚集体状态的解析结果如表7-3所示。
但是,该测定方法既费时间又费劳力,所以其富有研究性的味道。
实际上,作为评价一次聚集体被支化成不规则链锁状的程度,即评价结构发达程度的方表7-3 一次聚集体的状态解析结果种类测定个数基本粒径nm 最大长度nm 周边长度nm 面积nm 2体积10-3nm 3N 22015022.51254496612230N 23415125.21464288438300N 32615130.31163956763274N 33015028.616155*********N 33945424.61545479162357N 34714327.717162011931509N 55015142.2270895255421806法,可对一次聚集体聚集时形成的空隙进行测定。
结构发达的炭黑,其一次聚集体间的空隙增大。
一次聚集体间的空隙一般用邻苯二甲酸二丁酯(DB P )充填,用其DB P 的体积表示。
DB P (m l 100g )值大表示结构发达。
但是,尚若在橡胶混炼中施加较大的力,便可知,一次聚集体较弱部分将被破坏,所以也可采用测定前施以剪切压缩力,将一次聚集体破坏后再测定DB P 吸油值这样的方法。
炭黑的压缩次数与DB P 吸油值变化的关系如图7-4所示。
由该图可知,高结构炭黑的DB P 吸油值降低显著。
关于DB P 吸油值的测定,可通过求取全空隙体积的方法实现,但该法不能求出空隙大小的分布。
作为求取空隙大小分布的方法有水银压入法和热微孔尺寸测定仪法(在此省略)。
图7-4 炭黑压缩处理次数与D BP 吸油值变化的关系(压缩力为2400磅 英寸2) 测定一次聚集体大小的方法除了透射电子显微镜法以外,还研究了离心沉降法、光透法、光散射法、小角度X 射线散射法等多种方法,其中最常用的是离心沉降法。
用离心沉降法求出的一次聚集体的大小因为是根据斯托克斯(Stokes )沉降速度公式求出的,所以称其为斯托克斯粒径。
橡胶用代表性炭黑的斯托克斯粒径分布如图7-5所示。
斯托克斯粒径的大小与基本粒径和结构双方存在相关性,不能将其分离开,其用途在于可以得到用比表面积法和DB P 吸油值法测定所无法得到的有关粒径分布的信息。
图7-5 橡胶用炭黑的斯托克斯粒径(D st )分布 (3)表面性状:炭黑粒子的表面性状包括物理性能和化学性能两个方面。
物理性能是用扫描隧道式电子显微镜(STM )和原子显微镜(A FM )观察粒子表面的微结构后获得的。
Don 2net 等人用STM 观察了炭黑粒子表面结构,提出了如图7-6所示的炭黑粒子新的表面模型。