APQP流程文件
APQP过程流程

APQP过程流程一、计划和确定项目1.1成立多功能小组(项目负责人)1.2评审客户文件资料,确定可靠性目标(CFT小组)1。
3编制产品质量保证计划(CFT小组)1.4初始材料清单 (研发部)1。
5关键重要特性初始明细表(研发部)1.6接受客户对文件资料的审查(CFT小组)1。
7 项目风险评估(CFT小组)*1.8项目进度表(满足要求是进入下一阶段的标志)(研发部)二、手工样件阶段2.1 手工样件文件及资料的评审(CFT小组)2。
2 手工装样件的生产策划(研发部)2。
3 手工样件的生产设计(研发部)2.4 工程图纸、规范(研发部)2.5 特殊特性清单(研发部)2。
6 设计失效模式分析DFMEA(研发部)2.7 样件控制计划(研发部)2。
8 设计验证计划(品保部)2。
9 量具、试验设备清单(品保部)2.10 新设备、工装和设施清单(研发部生产部)2.11 手工样件生产(研发部)2.12 手工样件的检验、试验(品保部)2。
13 接受客户对文件资料的审查(CFT小组)*2.14 提交手工样件和检验报告(合格是进入下一阶段的标志)(品保部)三、工装样件阶段3.1工装样件生产的工艺设计(车间平面布置图、工艺流程图)(生产部研发部) 3。
2 试生产控制计划(研发部)3。
3 过程失效模式分析PFMEA(品保部)3。
4 工装样件的生产准备(生产部)3。
5 测量系统分析计划(品保部)3.6 初始制程能力分析计划(品保部)3.7 过程作业指导书 (研发部)3.8 包装标准与规范 (研发部)3.9 工装样件的生产计划确定(生产部)3。
10 首批工装样件的生产(生产部)3。
11 组织满负荷生产的内部工艺验收(CFT小组)3。
12 首批工装样件的检验、试验(品保部)3.13 客户开发阶段的过程审核(视需要)(CFT小组)*3.14 提交首批工装样件和检验报告(复验合格是进入下一阶段的标志)(品保部)四、小批量生产件阶段4.1 小批量样件的生产准备(生产部)4。
APQP过程流程

APQP过程流程APQP(Advanced Product Quality Planning,先进产品质量规划)是一种用于规范新产品开发和质量管理的过程,在汽车行业尤其常见。
APQP旨在确保在新产品或过程的设计和开发过程中,质量规划活动与设计、工程、制造和服务过程相互关联和统一阶段一:计划和定义在此阶段,确定产品开发的范围、目标、质量特性和性能要求。
主要任务包括:制定项目计划,明确项目目标和里程碑;识别产品的特殊要求、技术挑战和风险因素;建立项目团队和各个相关部门的沟通机制;确定供应商和客户的需求,并评估是否能够满足。
阶段二:产品设计与开发在此阶段,进行产品的概念设计、详细设计和开发工作。
主要任务包括:进行市场调研,了解客户需求;制定产品设计和制造的目标,明确产品的特征和性能要求;评估产品的可制造性和可靠性,确保产品的设计与制造的可行性;制定测试和验证计划,以确保产品符合质量标准。
阶段三:制造能力和过程确认在此阶段,确保产品的生产工序和制造过程可行,并满足质量要求。
主要任务包括:开展制造工序的能力分析,确保供应商和生产线的技术和设备能够满足产品要求;开展过程分析和FMEA(故障模式与效应分析),识别潜在的问题和风险;开展制造过程的装配和模拟测试,确保产品装配过程的准确性和质量可控。
阶段四:产品验证在此阶段,对产品进行全面的测试和验证,以确保产品满足设计要求和客户需求。
主要任务包括:制定产品验证计划,并进行样品的生产测试;进行产品的可靠性测试、环境测试和性能测试,以验证产品在各种条件下的工作情况;与客户的技术团队进行沟通和协商,确保产品符合客户的需求。
阶段五:项目启动和持续改进在此阶段,启动产品的量产过程,并进行持续的质量改进。
主要任务包括:制定产品的量产计划,确保产品能够按时交付;建立和监控产品的质量指标,制定纠正措施和预防措施;持续监控产品的性能和质量,及时进行反馈和改进。
总结APQP过程是一个系统性和规范化的质量管理方法,它在产品开发和生产过程中,将质量规划活动与设计、工程、制造和服务等过程相结合,以确保产品的质量和客户满意度。
APQP五大阶段文件目录

TS16949五大工具一.五大工具简介 1.1 五大工具:1.1.1 APQP 先期产品质量策划与控制计划:用来确定和制定确保某产品使顾客满意所需步骤的一种结构化方法。
1.1.2 FMEA 失效模式与后果分析 DFMEA: 设计失效模式及后果分析 PFMEA: 过程失效模式及后果分析 1.1.3 SPC 统计过程控制供正在进行过程控制的操作者使用;有助于过程在质量上和成本上能持续地,可预测地保持下去; 使过程达到:更高的质量;更低的成本;更高的能力。
1.1.4 MSA 测量系统分析:用来获得表示产品或过程特性的数值的系统。
测量系统是与测量结果有关的仪器、设备、软件、程序、操作人员、环境的集合。
量具: 任何用来获得测量结果的装置,包 括用来测量合格/不合格的装置 。
1.1.5 PPAP 生产件批准程序1.2 五大工具的相互关系策过程设计和开发产品与过程确认生 产反馈、评定和纠正措施策划产品设计和开发 计划 确定项目产品设计和开发验证过程设计和开发验证产品和过程确认反馈、评定和纠正措施生产试生产样件提出/批准 项目批准PPAP是APQP第四阶段(试生产)的输出,即PPAP是试生产阶段所产生的资料PPAP资料有19个提交项,其中包括SPC、MSA、FMEAMSA是为保证SPC的可靠性,故先MSA(如用到Xbar-R图)后SPC,两者相辅相成SPC是FMEA中的一种工具及方法五大工具中,PPAP、MSA、SPC、FEMA均围绕着APQP系统在运转1.3 PPAP的作用1).需方了解供方对产品的理解能力2).需方了解供方的制造能力PPAP相当于《样品承认》的一个高级版本,一般体现形式即为一份表格资料二、APQP开展步骤(技术部分)2.1 市场调研、顾客要求→顾客要求评审(贯穿于整个APQP过程)→新产品可行性分析→立项申请→成本核算→成立APQP小组,召开会议→APQP总进度策划,确定时间节点和设计任务→编制设计质量可靠性目标、初始流程图、初始特性、初始材料清单等→编制产品保证书→阶段评审→管理者支持2.2 市场调研、顾客要求→顾客要求评审(贯穿于整个APQP过程)→新产品可行性分析→立项申请→成本核算→成立APQP小组,召开会议→APQP总进度策划,确定时间节点和设计任务→编制设计质量可靠性目标、初始流程图、初始特性、初始材料清单等→编制产品保证书→阶段评审→管理者支持2.3制造过程设计输入评审→根据第二阶段输出文件更新过程流程图→场地平面布置图→特性矩阵图→过程FMEA→试生产控制计划→文件评审→设备工装、量检具配备→过程指导书→检验指导书→包装规范→MSA分析计划→过程能力研究计划→培训计划→试生产计划→试生产准备→员工培训→过程审核→阶段总结评审,管理者支持2.4 试生产→设备工装验证→工艺验证→生产能力分析→MSA分析报告→过程能力研究报告→样品验证(材料、全尺寸、性能、包装等)→产品审核→试生产总结评审→生产控制计划→PPAP整理提交→更新作业指导书、过程流程图、PFMEA等工艺文件→过程审核、管理者评审→质量策划认定及管理者支持2.5总结:根据设计目标、初始材料清单编制初始过程流程图(第一阶段)---初始流程图、初始特殊特性清单编制DFMEA(第二阶段)---样件控制计划---样件生产中问题解决---更新DFMEA---更新过程流程图---编制PFMEA---更新控制计划(试生产控制计划)---作业指导书---试生产问题解决---生产控制计划---更新PFMEA---更新工艺文件---量产设计和开发流程:第一阶段+第二阶段设计和开发策划(第一阶段)→设计和开发输入(第一阶段输出)→设计和开发输出→设计和开发评审→设计和开发验证→设计和开发确认→设计和开发更改的控制无设计责任1)市场调研→立项可行性分析→立项申请→成本核算→成立APQP 小组,召开会议,确定时间节点→编制APQP 计划→编制设计任务书→编制产品保证书→阶段评审 2)无第二阶段3)根据第一阶段输出编制特殊特性明细→更新过程流程图→平面布置图→特性矩阵图→过程FMEA →样件控制计划→文件评审→提出设备设施要求→编制过程指导书→检验指导书→包装规范→样件制作→样件评审、变差分析→样件验证→样件评审→MSA 分析计划→过程能力计划→培训计划→员工培训→阶段评审,小组可行性承诺→更新设备设施要求→试生产控制计划→工艺文件更新4、小批量试产→工艺验证→工装设备验证→生产能力分析→样件验证→样件确认→生产总结样件评审→PPAP 提交→生产控制计划→更新工艺文件→管理者评审→质量策划认定总结三、APQP 的实施1、计划和确定项目阶段(13项) 1.1 本阶段工作目的及任务1)进行总体策划,包括人员,资源及时间安排 2)确定顾客的需要和期望,提供比竞争者更好的产品 3)确定设计目标和设计要求 1.2 本阶段的输入及输出的文件市场调研、顾客要求→顾客要求评审(贯穿于整个APQP 过程)→新产品可行性分析→立项申请→成本核算→成立APQP 小组,召开会议→APQP 总进度策划,确定时间节点和设计任务→编制设计质量可靠性目标、初始流程图、初始特性、初始材料清单等→编制产品保证书→阶段评审→管理者支持序号 输入输出 备注 1 顾客的呼声:市场调研、产品保修记录和质量信息、小组经验市场调研报告 或顾客要求清单2 业务计划/营销战略 顾客要求评审 新产品可行性分析报告3 产品/过程标杆数据4 产品/过程设想5 产品可靠性研究6 顾客输入7 立项申请 新产品开发建议书8 成品核算 成本核算报告/报价表 9成立APQP 开发小组《APQP 小组名单》10 小组会议,进行总体策划《新产品开发进度计划》11设计任务设计目标12 可靠性与质量目标13 初始材料清单14 初始过程流程图15 初始特性明细16 试验项目(要考虑顾客要求及产品标准)及接收准则17 明确设计项目的各类保证措施产品保证计划18 总结评审评审记录,管理者支持1.2.1市场调研或整理确认顾客要求,输出《顾客要求清单》;1.2.2 组织对顾客要求进行评审,输出《顾客要求评审记录》1.2.3进行新产品可行性分析,内容包括:①市场调研结果:②保证记录和质量信息:③小组经验:④业务计划/营销策略:⑤产品/过程指标:⑥产品/过程设想:⑦产品可靠性研究:⑧顾客输入。
APQP程序文件

1.目的:2.适用范围:适用于所有新产品、改型的产品和新过程。
3.定义:3.1 特殊特性:根据供方或顾客对产品及过程的经验,此种特性可能影响到产品安全性、法规的符合性或对装配、功能、性能或后续的产品加工产生影响。
4.作业流程:见页次 3-10。
5.补充说明:无。
生效日期2005.09.01资源,预防缺陷,降低成本,持续不断地改进,以最低的成本及时提供优质产品,使客户满意。
确定和制定确保产品使客户满意所需的步骤,促进与所涉及的每个人的联系,以确保所要求的步骤能按时完成,并引导产品质量先期策划管制程序页次2/10版本(次)A产品初始材料清单产品初始材料清单多方论证小组成立通知单APQP 开发计划APQP 开发计划多方论证小组人员及职责表业务部工程部研发部顾客Gerber 资料、制作要求及检验规范等A PQP小组成员包括研发部、工程部、制造部、品保部、业务部、采购部、若需要时,也可以要求供方人员或要求客户代表参加,多方论证小组小组要推选小组负责人,并明确小组及各方代表的职责,且要总经理批准工程部收到业务签发的《客户提供资料与制作明细表》后,对客户的Gerber 资料,工程图纸、制作要求及检验规范等进行初步确认,然后通知业务此产品是否可以继续开发,若确认可继续开发,则由研发部负责召集成立多方论证小组研发部工程部品保部制造部业务部采购部多方论证小组成立通知单顾客的Gerber 资料、图纸、制作要求及检验规范等多方论证小组多方论证小组掌握顾客的需求和期望,拟定整个产品的策划计划,编制APQP开发计划顾客的Gerber 资料、图纸、制作要求及检验规范等多方论证小组对顾客提供的新产品的质量及材料要求,进行研究及确认,并根据用量开出产品初始材料清单页次3/10输入表单记录输出责任单位作业说明参考文件4.作业流程产品质量先期策划管制程序2005.09.01版本(次)A 生效日期业务部接收顾客提供的各项资料,如Gerber 资料、客户图纸、客户检验规范等填写《客户提供资料与制作明细表》提交工程部《客户提供资料与制作明细表》顾客要求开始接收顾客要求确认可行性成立小组制定开发计划初始材料清单《样品制作流程》Gerber资料、图纸、制作要求、检验规范及《产品过程流程图》等《样品制作流程》《原始资料CHECKLIST 》工程部顾客的Gerber 资料、图纸、制作要求及检验规范等4/10A 2005.09.01输出《产品和过程特殊特性初始清单》工程部根据顾客提供的Gerber 资料、图纸、制作要求、检验规范等制作《产品过程流程图》《产品过程流程图》工程部根据顾客Gerber 资料、图纸、客户要求、检验规范、相关法律法规及行业要求等,识别出特殊特性,填写《产品和过程特殊特性初始清单》,并提交各APQP 小组的所有成员讨论认可顾客多方认证小组工程部《产品过程流程图》工程部参考文件表单记录《产品和过程特殊特性初始清单》页次产品质量先期策划管制程序版本(次)生效日期工程部法律法规要求、行业要求,顾客需求工程部根据顾客Gerber 资料、图纸、检验规范等,依据《MI 资料作业规范》及《CAD-CAM 作业规范》等,对各种资料进行评审若要变更图纸、Gerber 资料、制作要求时,需填写《工程变更申请单》4.作业流程输入责任单位作业说明Gerber资料、图纸、制作要求及检验规范等《产品过程流程图》工程部根据顾客提供的Gerber 资料、图纸、制作要求、检验规范及《产品过程流程图》等,编制《样品制作流程》,制作中要体现出新技术,复杂性、包括制造要求、工程标准、可靠性、耐久性等产品保证的内容工程资料评审特殊特性确认制定流程图样品制作流程顾客图纸产品的设计、包装及运输要求工程部当顾客有包装标准时由工程部负责识别评审并转换为包装说明,加注在《样品制作流程》中工程部、品保部、多方论证小组根据对顾客资料的评审结果及《样品制作流程》,对客户在产品数量、规格、可靠性要求等方面做出承诺,填写《小组可行性承诺》并获得管理者支持产品、过程体系评审的要求品保部多方论证小组品保部根据产品的检验要点及相应的各项要求,确立过程质量控制体系,并通过《产品过程质量检查表》加以确认产品、过程控制体系工程部品保部维护部采购部多方论证小组《样品制作流程》《小组可行性承诺》管理者支持工程部品保部多方论证小组(副)总经理《样品制作流程》《工程资料checklist 》工程部、品保部、维护部、采购部及多方论证小组等,根据产品的要求及《样品制作流程》,准备相应的设备,并填写《新设备、工装、量具和试验设备开发计划进度表》《新设备、工装和试验设备检查表》《量具、试验设备检查表》输出《新设备、工装、量具和试验设备开发计划进度表》《新设备、工装和试验设备检查表》《量具、试验设备检查表》《制造过程管制程序》《进料检验与测试管制程序》《制程检验与测试管制程序》《最终检验与测试管制程序》《新设备、工装、量具和试验设备开发计划进度表》《新设备、工装和试验设备检查表》《量具、试验设备检查表》2005.09.01参考文件表单记录《产品/过程质量检查表》页次5/10产品质量先期策划管制程序版本(次)A 生效日期4.作业流程输入责任单位作业说明包装说明设备评审承诺、支持包装标准质量体系评审工程部根据顾客提供的Gerber 资料、图纸、制作要求、检验规范等所做的《样品制作流程》可作为试生产控制计划《样品制作流程》《样品制作流程》 PFMEA 《产品过程流程图》 特殊特性一览表工程部品保部根据《样品制作流程》、FMEA 、产品过程流程图等编写各种标准作业指导书作业指导书制造部材料流程对新的/修改过的过程进行分析、评审、预防、解决,制作潜在失效模式及后果分析表,并由多方论证小组负责对FMEA 进行查检潜在失效模式及后果分析多方论证小组产品潜在过程问题,BOM ,过程流程图车间平面布置图关键特性、材料、功能试验、检查要求、生产过程确定的过程特殊特性,产品和过程特殊特性清单多方论证小组多方论证小组应对特殊特性清单进行提炼,评审并达成一致,并将其转换成特性矩阵图,来显示过程参数和制造工位之间的关系.特殊特性矩阵图工程部输出参考文件表单记录制造部制定《车间平面部制图》,以决定制造场地内检验点、半成品、成品储存区等是否合理,是否能最大限度的利用场地和空间,使物流,产品能有序流动且最经济,并且要用《车间平面布置图检查表》对布置图进行评审《车间平面布置图检查表》4.作业流程输入责任单位作业说明页次6/10产品质量先期策划管制程序版本(次)生效日期A 2005.09.01车间平面布置图特殊特性矩阵图PFMEA试生产计划作业指导书品保部人员依据测量系统分析计划进行测量系统分析测量系统分析结果《测量系统分析作业规范》工程部项目开发计划测量系统分析计划品保部工程部根据项目开发计划,在时机成熟时,导入试生产计划,并根据《样品制作通知单》所要求的数量及交期,进行试生产《样品制作通知单》开发阶段的各项信息多方论证小组多方论证小组总结开发阶段的各项信息,对项目进行开发性评审,并获得管理者支持阶段总结报告PFMEA顾客包装标准,产品的运输要求《样品制作流程》工程部如顾客有包装特殊要求,按顾客要求制作包装标准书,若顾客没有特殊要求,工程部负责产品的包装设计,以满足运输的要求包装标准书制定测量系统分析计划,确保过程式开发阶段具有适当的测量系统和过程评估技术以及对特殊特性制作SPC分析计划测量系统分析计划SPC分析计划2005.09.01输出参考文件表单记录4.作业流程输入责任单位作业说明《样品制作流程》量具检测设备/产品检验规范《产品过程流程图》品保部页次7/10产品质量先期策划管制程序版本(次)A生效日期制定分析计划制定包装规范总结报告试生产的导入实施MSA《产品质量策划总结和认定报告》控制计划过程作业标准书 MSA 分析结果多方论证小组多方论证小组负责对控制计划,作业指导书和测量设备进行评价并记录于《产品质量策划总结和认定报告》《产品质量策划总结与认定报告》PFMEA《样品制作流程》试生产时的各种信息工程部品保部工程部根据PFMEA 及可执行的控制手段,结合生产实际, 制定生产控制计划生产控制计划包装规范工程部在实际生产过程中对包装规范进行评估评估结果PPAP 的各项文件及样品多方论证小组根据顾客的要求,提交相应的PPAP 文件及标准样品提交的PPAPSPC 分析结果SPC 分析计划品保部品保部负责进行SPC 分析来察看制程是否稳定受控工程规范的要求工程部品保部工程部负责建立产品的测试标准,品保部负责对产品进行测试,并记录于测试报告中测试报告4.作业流程输入责任单位作业说明产品质量先期策划管制程序版本(次)表单记录A 页次8/10输出参考文件生效日期2005.09.01SPC 分析确认试生产结果PPAP 的提交包装评价制定控制计划产品质量策划总结《顾客满意度调查管制程序》标准样品得到顾客确认或接到生管的生产通知后,工程部制作《D/S 料号制作流程》《MLB 料号制作流程》发放给相关部门,制造部根据生管的安排进行批量生产量产的产品顾客满意度调查结果Xbar -R 图SPC手册工程部生管部制造部顾客满意度的调查要求业务部业务部依据《顾客满意度调查管制程序》进行顾客满意度调查控制要求和方法品保部品保部根据顾客对产品的特性要求和工程的过程特性要求用Xbar -R 图对过程的稳定性进行监控标准样品,生产计划,作业指导书订单,试生产报告,产能,负荷,库存生管部生管部根据顾客的订单及内部生产能力,制定量产计划《在制品分布表》(WIP)表单记录包装规范/试产报告/PPAP 报告工程部(副)总经理工程部总结试产阶段的信息,提交报告经总经理批准后,项目正式转交生产会议记录4.作业流程输入责任单位作业说明输出参考文件页次9/10产品质量先期策划管制程序版本(次)A 生效日期2005.09.01总结报告制定量产计划批量生产监控生产稳定性顾客满意度调查《记录管制程序》产品质量先期策划过程产生的记录品保部产品质量先期策划过程产生的记录由品保部文管中心按《记录管制程序》进行管理存储有序的记录《顾客抱怨管制程序》顾客反馈业务部品保部制造部根据收集取得之信息,于量产中作持续改善,特别是要针对顾客的特殊特性和达到稳定过程能力的改进,同时也要对APQP 的相关内容进行更新持续改善措施《纠正及预防措施管制程序》、《持续改善管制程序》交付服务业务部品保部持续监控交付和服务,并取得顾客要求信息顾客反馈2005.09.014.作业流程输入责任单位作业说明输出参考文件表单记录页次10/10产品质量先期策划管制程序版本(次)A 生效日期交付和服务持续改进资料归档结束。
APQP程序

5.2.5PFMEA;
5.2.6《控制计划》。
编号: QT/BHHS-02-09
版本: A/0
APQP程序(APQP CONTROL PROCEDURE)
报价流程
责任单位/人
相关文件
业务部
业务部
业务部
业务部
技术部
业务部
业务部
业务部
新品报价条件
新品报价条件
顾客要求识别与评审表
新品报价评审讨论
1. 目的: 规定产品过程设计及开发的策划过程, 确保满足客户规定的质量要求。
2. 范围: 凡公司新产品过程设计与开发和生产的质量控制, 皆适用。
3. 职责:
3.1多功能小组是APQP的主要权责机构, 对整个产品质量策划阶段的有效策划、按计划实施及顺利完成负责。
3.2公司各相关职能部门负责指派合适人员参加多功能小组, 并对策划内容的顺利实现负相关责任。
计划
品保
技术要求
业务/铸造
依“SPC作业指导书”
过程能力研究计划
管理者支持
总经理
项目进展相关信息
多功能小组
成员
听取业务客户负责人关于项目进
展的汇报, 提供必要的支持
展的汇报,提供必要的支持
协调会议记录
尺寸测量与理化
试验
技术/品保
样品
铸造/品保
技术和品保分别负责尺寸检验及
理化试验, 并提供报告。
理化试验,并提供报告。
和人员
在识别顾客要求(包括特殊要求
)的基础上, 组织对相关内容的
培训。
与顾客有关的培训
要求及人员培训计
划
小组可行性承诺
业务
APQP五大阶段文件目录详解
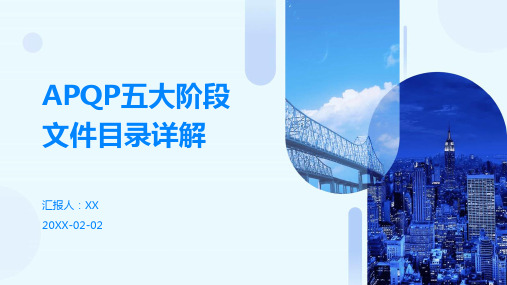
部署过程能力提升计划,明确责 任人、时间节点和预期效果。
04
持续改进计划制定
强调持续改进的重要性和 意义。
制定持续改进计划,包括 改进目标、措施和时间表 等。
ABCD
分析生产过程中存在的问 题和改进机会。
建立持续改进的跟踪和评 估机制,确保改进计划的 有效实施。
04
CATALOGUE
产品和过程确认阶段
纠正预防措施跟踪验证情况报告
纠正预防措施实施计划
01
列出所有已制定的纠正预防措施。
跟踪验证记录
02
记录每项措施的实施情况和验证结果。
有效性评估
03
对纠正预防措施的有效性进行评估,确定是否需要进一步调整
。
总结经验教训,持续改进
经验教训总结报告
总结项目过程中的经验教训,提出改进建议。
持续改进计划
根据总结报告,制定具体的持续改进计划和目标。
05
CATALOGUE
反馈、评定和纠正措施阶段
顾客满意度调查结果展示
顾客满意度调查表
包括产品质量、交付、服务等方面的评价。
顾客满意度分析报告
对调查结果进行统计分析,识别主要问题和改进方向。
产品质量问题分析及整改方案
产品质量问题清单
列出所有已知的产品质量问题。
问题根本原因分析
针对每个问题,进行深入分析,找出根本原因。
设备选型、采购及安装调试计划
根据产品特性和生产需求,确 定所需设备的类型、规格和数
量。
制定设备采购计划,明确采购 时间、价格和付款方式等。
进行设备市场调研,选择性价 比高的设备供应商。
制定设备安装调试计划,确保 设备按时到位并顺利投入生产 。
apqp开发流程文件及职责

apqp开发流程文件及职责APQP (Advanced Product Quality Planning,高级产品质量规划) 是一种按照特定流程进行产品开发的方法。
它的目标是确保在产品开发过程中的所有阶段都能够有效地执行,并最终实现高质量的产品。
在APQP开发流程中,有许多文件和职责需要被明确定义和执行。
本文将详细介绍APQP开发流程文件及职责。
一、APQP开发流程文件1. 项目计划文件:该文件包含项目的整体计划,包括项目的目标、时间表、资源分配等。
该文件由项目经理负责编制,并在整个开发过程中进行更新和调整。
2. 产品设计文件:该文件包含产品的设计要求、功能规范、技术规范等。
产品设计文件由设计工程师负责编制,并与客户进行确认和审查。
3. 过程流程图:该文件描述了产品的制造和装配过程,包括各个工序的顺序、流程和关键控制点。
过程流程图由工艺工程师负责编制,并与制造团队进行讨论和确认。
4. 控制计划:该文件描述了产品开发过程中的质量控制要求和控制措施,包括检验标准、检验方法、检验频率等。
控制计划由质量工程师负责编制,并与制造团队进行讨论和确认。
5. 测试计划:该文件描述了产品的测试要求和测试方法,包括功能测试、可靠性测试、安全性测试等。
测试计划由测试工程师负责编制,并与研发团队进行讨论和确认。
6. 供应商评估报告:该文件描述了供应商的能力和质量管理体系,包括供应商的设备、技术、人员等方面的评估结果。
供应商评估报告由采购工程师负责编制,并与供应商进行确认和审查。
二、APQP开发流程职责1. 项目经理:负责整个项目的计划、组织和控制,确保项目按时、按质、按量完成。
项目经理需要与各个部门进行协调和沟通,解决项目中的问题和风险。
2. 设计工程师:负责产品的设计和技术规范的编制。
设计工程师需要与客户进行沟通和确认,确保产品的设计符合客户的要求和期望。
3. 工艺工程师:负责制定产品的制造和装配过程,编制过程流程图。
APQP程序文件

APQP程序文件引言概述APQP(AdvancedProductQualityPlanning,先进产品质量计划)是一种用于规划和管理新产品或变更产品的质量计划和过程的方法。
APQP程序文件是指在APQP过程中所需要准备和使用的各类文件,包括文件的名称、内容和使用方式等。
正文内容1.APQP程序文件的概述1.1APQP过程和需求意识文件定义和规划项目的目标和需求确定产品特征和功能1.2设计与开发文件设计FMEA(FlureModeandEffectsAnalysis,失效模式和影响分析)制定设计验证计划和报告1.3生产过程文件制定控制计划和作业指导书定义关键工序和特殊特性1.4测量、检验与试验文件确定测量和检验方法制定试验计划和报告1.5过程评估文件进行过程审核和产品审核制定纠正措施和预防措施2.APQP过程和需求意识文件2.1项目目标和需求文件确定项目的关键目标和指标收集和分析市场需求2.2产品特征和功能文件定义产品的功能和特征制定产品设计规范和标准3.设计与开发文件3.1设计FMEA文件识别潜在的设计失效模式和其影响制定应对措施和改进计划3.2设计验证计划和报告文件制定设计验证的方法和计划进行设计验证并记录结果4.生产过程文件4.1控制计划和作业指导书文件制定生产过程的控制点和关键参数编制作业指导书和操作规程4.2关键工序和特殊特性文件确定生产过程中的关键工序和特殊特性制定检验和控制措施5.测量、检验与试验文件5.1测量和检验方法文件确定产品测量和检验的方法和要求编制测量和检验的标准和程序5.2试验计划和报告文件制定产品试验的方法和计划进行试验并记录结果总结APQP程序文件是在APQP过程中使用的各类文件集合,用于规划和管理新产品或变更产品的质量计划和过程。
这些文件包括项目目标和需求文件、产品特征和功能文件、设计与开发文件、生产过程文件、测量、检验与试验文件以及过程评估文件。
每份文件都在不同阶段起到重要作用,帮助企业确保产品质量并满足顾客需求。
APQP流程图

制定样件控制计划
P
N O
Q
批准
编制样件试作计划
P
YES
第
整理图纸
样件制造 N
二 阶
N
O
是否需
顾客确
YES N
产品设计 验证/评审
O D
段
认
YES
O
产品设
计
YES 产品设计验证资料整理
: 产 品 设
图纸送顾客确认
更改评 审
产品设计更改
N
YESNຫໍສະໝຸດ O是否需YES
顾客确
公
N认 O
样件送顾客确认
计 和
与顾客沟 O 通或放弃
确定新产品设计/开发来源
A
A
N
新产品制造可行性
O
编制新产品项目设计/开发进度计划
P
评估和风险分析
Q
YES
N
O 核准
P
新产品制造可行性报告资料整理
YES
第
新产品项目设计/开发计划发行 N
一 阶
成本核算
O
N O
报价
与顾客沟通或放弃
产品设计输入评审
段
YES
YES
:
通知和召集相关部门进行合同评审
计
N O
划
合同评审
和设施要求
G
G
确定产品和过程 特殊特性
确定量具/试验 设备要求
产品设 计
输出评 审YES
N O
H
小组可行性承诺
管理者支持
I
I
J 制造过程设计输入
A
P
过程设
N O 重新进行
Q
计
过程设计
APQP流程文件清单

7
√
市场部 XX-QR/4-PD-006(A/0)
8 报价表-XX.xls
√
XX-QR/4-PD-007(A/0)
模具报价单-XX.xls
√
市场部/财务部 XX-QR/4-PD-008(A/0)
9
×
项目部/市场部
10
×
市场部
11
√
项目部 XX-QR/4-PD-009(A/0)
×
项目部 XX-QR/4-PD-069(A/0)
×
项目部 XX-QR/4-PD-070(A/0)
×
设备部
×
项目部 XX-QR/4-PD-071(A/0)
×
项目部
项目部
×
项目部 XX-QR/4-PD-033(A/0)
×
项目部 XX-QR/4-PD-034(A/0)
×
项目部 XX-QR/4-PD-072(A/0)
3.05 文件制作与更新
NO
项目
文件或记录
控制计划检查清单
生产作业指导书
质量检验作业指导书
包装评审单 3.06
包装规范(初始)
3.07 制定初始过程能力 初始能力研究计划
、MSA分析计
MSA计划
主导部门
有
项目部/项目
项目部/项目
√
项目部/项目
√
项目部/项目
项目部/项目
√
质量部
质量部
3.08
分零件OTS样件的 认可
工艺流程图
项目部/项目
√
新产品评审表
项目部/项目
产品检验标准
项目部/项目
APQP项目全过程文件范例

APQP项目全过程文件范例APQP(Advanced Product Quality Planning)中文意思是:产品质量先期策划,是QS9000/IATF16949质量管理体系的一部分。
产品质量策划是一种结构化的方法,用来确定和制定确保某产品使顾客满意所需的步骤。
产品质量先期策划主要包括五个阶段:计划和项目确定,产品设计和开发,过程设计和开发,产品和过程确认,反馈、评定和纠正措施。
现将各阶段部分文件摘录如下。
第一阶段计划和项目确定一、可行性分析01 项目可行性研究报告(一)项目概况1. 产品概况及市场前景2. 产品的主要性能指标3. 产品的技术质量指标总体水平达到或超过国家行业标准要求。
4. 企业实施该项目的优势5. 可行性研究报告项目负责人(二)产品生产安排及依据1. 产品的市场分析2. 生产大纲(1)生产规模:(2)产品系列:(3)设备(4)原材料供应(5)能源供应(6)厂房(三)生产工艺技术、设备和人员配置1. 工艺流程2. 产品规格3. 生产设备(1)主要生产设备(2)设备能力测算表(3)人员配置(四)项目进度安排(五)结论二、小组成员01 项目负责人任命书02 APQP小组成员及职责表三、开发计划01 设计开发方案02 设计开发任务书03设计开发计划书四、设计输入01 产品内控标准02 项目建议书03设计开发输入清单04 设计开发信息联络单五、供方材料清单六、初始过程流程图七、APQP项目计划八、第一阶段评审报告第二阶段产品设计和开发一、控制计划(样件)01 控制计划特殊特性(选用)02 产品过程特性矩阵图03 生产工艺流程图04 控制计划-原材料04 控制计划-工序04 控制计划-成品检验05 控制计划检查表二、工程规范01 客户产品要求(略)02 产品规格书(略)三、材料规范四、产品图纸(略)五、特殊特性清单六、DFMEA及检查表01 DFMEA(样品、小批量、批量)02 DFMEA检查表(样品、小批量、批量)七、设备设施01 生产设备设施清单(略)02 检测设备清单(略)八、样件生产01 材料检验记录(略)02 生产记录(样品生产计划/投料单/工序管理表/产品测试记录/成品检验记录,略)九、设计评审报告01 设计开发一阶段评审报告02 设计小样评审报告十、设计开发验证01 样品负荷测试数据(略)02 样品负荷测试报告(略)03 客户检测报告(略)04 设计开发验证报告十一、小组可行性承诺十二、第二阶段评审报告01 设计开发输出清单02 第二阶段评审报告第三阶段过程设计和开发一、质量保证体系评审01 产品/过程质量检查表二、过程流程图及检查表01 过程流程图02 过程流程图检查表修订日期:制定人:三、制造过程特性矩阵图四、车间平面图及检查表01 车间平面布置图(略)02 车间平面图检查表顾客或内部零件号修订水平_________________日期:制定人:五、PFMEA及检查表01 PFMEA(样品、小批量、批量)02 PFMEA检查表(样品、小批量、批量)顾客或内部零件号修订水平修订日期:制定人:六、包装方案七、控制计划及检查表01 生产工艺流程图02 控制计划-原材料02 控制计划-工序02 控制计划-成品检验03 控制计划检查表顾客或内部零件号修订水平__________制定人:日期:八、作业指导书01 产品技术标准(略)02 SOP作业指导书(分工序)03 SIP检验指导书(工序/成品/出库,略)九、测量系统分析计划十、初始过程能力研究计划十一、第三阶段评审报告第四阶段产品和过程确认一、试生产制造计划编制:批准:二、MSA报告三、初期过程能力分析四、试生产报告01 试产报告02 试产总结报告03 新产品鉴定评审报告五、PPAP生产件批准程序01 PPAP提交清单02 零件提交保证书03 材料试验报告(略)04 尺寸测量报告(略)05 性能试验报告(内部/顾客/第三方,略)06 CPK报告(关键工序)07 供方清单(略)六、生产确认试验01 质量一致性检验报告(略)02 第三方机构检测报告(略)七、包装评价01 包装箱坠落实验报告02 包装评价表八、生产控制计划01 控制计划-原材料02 控制计划-工序03 控制计划-成品检验九、产品质量策划总结和认定报告十、第四阶段评审报告十二、量产通知单编制:批准:日期:日期:第五阶段反馈、评定和纠正措施一、减少变差(CPK报告)二、顾客满意01 质量承诺书(略)02 顾客满意度调查报告(略)。
APQP程序文件
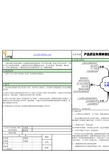
文件编号文件版次文件页次适用于本公司所开发的新产品或产品变更的先期策划。
3.4其他各部门负责完成产品质量先期策划的相应职能的工作任务。
过程负责人:技术部主管4.1风险分析4.1.1计算机及CAD等软件、生产设备、检验试验设备损坏时,如何处理?4.1.2资源不足时,如何处理?主条款:针对所确少的资源,及时提交总经理,由总经理提供必要的资源。
辅条款:4.1.3执行者能力不足时,如何处理?技术部采购部品质部市场部生产部 4.1.4衡量指标没有完成如何处理?本程序确定和制定确保产品使顾客满意所需的新产品开发的步骤,促进与所涉及的每一个项目开发小组成员的联系,以确保所要求的步骤能按时完成,并引导资源,预防缺陷,降低成本,持续不断地改进,以最低的成本及时提供优质产品,使顾客满意。
3.1总经理负责组建产品开发项目小组,任命项目小组组长,对先期产品质量策划工作全过程提供支持。
3.2项目小组组长对接受的项目负有从产品设计开发到产品投产的全部责任,定期召开项目策划小组会议,落实进度,并随时向总经理汇报工作进程。
3.3项目小组为新产品或产品变更进行生产准备。
小组活动应包括:特殊特性的建立和确定;失效模式及后果分析的建立和评审;制定措施,以减少具有较高风险顺序数的潜在失效模式;控制计划的建立和评审。
首先定期的对相关的文件进行备份,定期的对设备进行维护保养,对重点设备准备充分的易损件配件,出现问题时立即使用合格的设备,并在四个工作日内对损坏的设备进行修复。
技术部人员应具备的技能:能够熟练的使用计算机及Office、CAD、CAE等办公软件;能够熟悉公司的产品质量先期策划控制程序;能够熟练的进行DFMEA/PFMEA的分析。
各相关部门应具备的技能:具备配合多功能小组进行产品质量先期策划的能力;具备各部门工作应有的能力。
对技术人员、各部门及多功能小组的现有能力进行确认,当不存在上述能力时,立即组织培训并评价其有效性,以便满足相关人员应具备的技能。
APQP过程文件清单
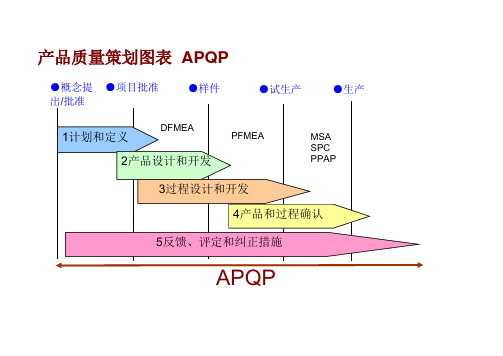
产品质量策划图表APQP●概念提●项目批准●样件●试生产●生产一、策划输入文件名输出文件名顾客的声音设计目标业务计划/营销策略可靠性和质量目标产品/过程标杆数据初始材料清单产品/过程假设初始过程流程图产品可靠性研究产品和过程特殊特性的初始清单顾客输入产品保证计划管理者支持包括项目进度和对支持所需产能的资源和人员的策划二、产品设计和开发输入文件名输出文件名设计目标设计失效模式及后果分析可靠性和质量目标可制造性和装配设计初始材料清单设计验证初始过程流程图设计评审产品和过程特殊性的初始清单样件制造—控制计划产品保证计划工程图样(包括数学数据)管理者支持工程规范材料规范图样和规范更改产品质量策划小组输出(作为第三章的输入)新设备、工装和设施要求产品和过程特殊性量具/实验设备要求小组可行性承诺和管理者支持三、过程设计和开发输入文件名输出文件名设计失效模式及后果分析包装标准和规范可制造性和装配设计产品/过程质量体系评审设计验证过程流程图设计评审工厂平面布置图样件制造—控制计划特性矩阵图工程图样(包括数学数据)过程失效模式及后果分析工程规范试生产控制计划(包括防错装置)材料规范过程指导书图样和规范的更改测量系统分析计划新设备、工装和设施要求初始过程能力研究计划产品和过程特殊特性管理者支持(包括操作员和培训计划)量具/实验设备要求小组可行性承诺和管理者支持四、产品与过程确认输入文件名输出文件名包装标准和规范一定数量的生产运行产品/过程质量体系评审测量系统评价过程流程图初始过程能力研究工厂平面布置图生产零件批准特性矩阵图生产确认试验过程失效模式及后果分析包装评价试生产控制计划生产控制计划过程说明书质量策划认定和管理者支持测量系统分析计划初始过程能力研究计划管理者支持五、反馈,评定和纠正措施输入文件名输出文件名减少变差增进顾客满意增进交付和服务习得经验/最佳实践的有效利用。
APQP程序文件
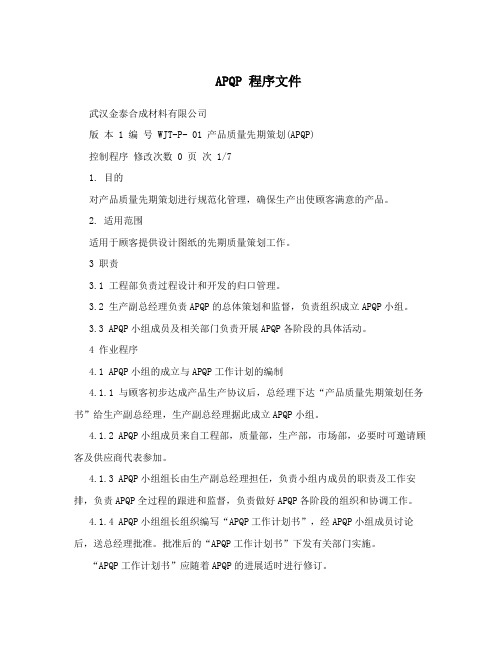
APQP 程序文件武汉金泰合成材料有限公司版本 1 编号 WJT-P- 01 产品质量先期策划(APQP)控制程序修改次数 0 页次 1/71. 目的对产品质量先期策划进行规范化管理,确保生产出使顾客满意的产品。
2. 适用范围适用于顾客提供设计图纸的先期质量策划工作。
3 职责3.1 工程部负责过程设计和开发的归口管理。
3.2 生产副总经理负责APQP的总体策划和监督,负责组织成立APQP小组。
3.3 APQP小组成员及相关部门负责开展APQP各阶段的具体活动。
4 作业程序4.1 APQP小组的成立与APQP工作计划的编制4.1.1 与顾客初步达成产品生产协议后,总经理下达“产品质量先期策划任务书”给生产副总经理,生产副总经理据此成立APQP小组。
4.1.2 APQP小组成员来自工程部,质量部,生产部,市场部,必要时可邀请顾客及供应商代表参加。
4.1.3 APQP小组组长由生产副总经理担任,负责小组内成员的职责及工作安排,负责APQP全过程的跟进和监督,负责做好APQP各阶段的组织和协调工作。
4.1.4 APQP小组组长组织编写“APQP工作计划书”,经APQP小组成员讨论后,送总经理批准。
批准后的“APQP工作计划书”下发有关部门实施。
“APQP工作计划书”应随着APQP的进展适时进行修订。
4.2 计划和项目的确定4.2.1 顾客产品设计的评审(1)公司不进行产品设计,但要对顾客提供的图纸、技术资料进行评审;(2) APQP小组用“设计信息检查清单”对设计的可行性、有效性作出评价。
对评审中发现的问题,要及时与顾客联络解决;(3)评审中要确定需进行先行试验及可靠性研究的项目(如有的话)。
4.2.2 顾客信息的收集与分析质量部对顾客以往的投诉、建议进行收集、分析,整理出“顾客投诉、建议分析报告”送交APQP小组及有关部门,作为此次APQP的参考资料。
4.2.3 顾客的业务计划与营销战略的研究必要时,APQP小组应对顾客的业务计划与营销战略进行研究,以识别顾客现在和未来最关注的事项。
APQP工作流程及说明

APQP工作流程及说明APQP(Advanced Product Quality Planning,高级产品质量规划)是一种流程化的方法,用于规划并确保产品在设计、工程、制造和服务过程中达到高质量水平。
它在汽车行业得到广泛应用,也适用于其他制造业。
1.规划和定义阶段:在该阶段,制定产品的质量目标和开发计划。
团队成员评估相关需求、法规要求以及潜在风险,并根据这些因素制定APQP计划。
此外,还制定产品设计和制程开发的时间表,并确定APQP团队成员。
2.产品设计和开发阶段:该阶段的关键目标是开发出满足客户需求和规定要求的产品设计。
团队成员使用设计评审、特性矩阵、质量功能展开(QFD)和设计失效模式与影响分析(DFMEA)等工具来完成该目标。
同时,对供应商进行评估和选择,并与供应商建立质量计划。
3.制程设计和开发阶段:在这个阶段,团队成员开发和优化制造工艺,确保产品的质量并满足设计要求。
流程评估、流程失效模式与影响分析(PFMEA)和可行性研究等工具被广泛应用于该阶段。
此外,还进行生产控制计划的制定,并对测量和试验设备进行校准和验证。
4.产品和过程验证阶段:在这个阶段,团队成员验证产品和制程是否达到设计要求和客户期望。
通过样品测试、过程验证和生产试运行,确保产品和制程的稳定性和一致性。
在此阶段还进行了供应商相关的评估,并控制实验和生产的相关文档。
5.生产评估阶段:在生产开始之前的最后一个阶段,团队成员将进行产品质量的最终评估。
通过审查生产和测量数据、统计过程控制技术和上线前检查等,确保产品质量的稳定性和一致性。
任何未解决的问题都将回到之前的阶段进行修正。
值得注意的是,APQP不是一次性的过程,而是一个循环的过程。
如果在各个阶段发现了任何问题或改进的机会,团队将重新回到相应的阶段进行修正。
此外,团队成员应紧密合作,及时沟通并共享信息,以确保项目按时、高质量地完成。
APQP的目标是通过规划和预防活动来确保产品的质量,并在产品开发早期发现和解决潜在问题,以减少后期的成本和风险。
APQP流程

n一、计划和确定项目n1、顾客的呼声
n2、业务计划/营销战略
n3、产品/过程基准数据
n4、产品/过程设想
n5、产品可靠性研究
n6、顾客输入
n1、设计目标
n2、可靠性和质量目标
n3、初始材料清单
n4、初始过程流程图
n5、产品和过程特殊特性的初始清单
n6、产品保证计划
n7、管理者支持
n二、产品设计和开发n1、 DFMEA-设计失效模式和后 果分析
n2、可制造性和装配设计
n3、设计验证
n4、设计评审
n5、样件制造--控制计划
n6、工程图样(包括数学数据)
n7、工程规范
n8、材料规范
n9、图样和规范的更改
n10、新设备、工装和设施要求
n11、产品和过程特殊特性
n12、量具/试验设备要求
n13、小组可行性承诺和管理者的支持
n三、过程设计和开发n1、包装标准
n2、产品/过程质量体系评审
n3、过程流程图
n4、车间平面布置图
n5、特性矩阵图
n6、过程失效模式及后果分-PFMEA
n7、试生产控制计划
n8、过程指导书
n9、测量系统分析计划
n10、初始过程能力研究计划
n11、包装规范
n12、管理者支持
n四、产品和过程确认
n1、试生产
n2、测量系统评价
n3、初始过程能力研究
n4、生产件批准
n5、生产确认试验
n6、包装评价
n7、生产控制计划
8、质量策划认定和管理者 支持
n五、反馈、评定和纠正措施n1、减少变差
n2、顾客满意
n3、交付和服务。
APQP过程流程

APQP过程流程Advanced Product Quality Planning (APQP) is a framework that is used in the automotive industry to ensure that the entire product development process is carefully planned, monitored and controlled. APQP helps in identifying potential risks and defects early on, and also ensures that customer needs and expectations are met. In this article, let us discuss the APQP process flow in detail.1. Plan and Define the Program:2. Product Design and Development:Once the project is planned and defined, the product design and development phase begins. In this phase, the team works on designing the product to meet the customer requirements. The team considers various factors such as functionality, performance, safety, reliability, and manufacturability while designing the product. They also develop prototypes and conduct testing to ensure that the product meets the desired specifications.3. Process Design and Development:In parallel with product design and development, the process design and development phase takes place. Here, the team focuses on developing the manufacturing processes required to produce the product. The team identifies the critical manufacturingprocesses, develops process flow charts, and determines the control plan for each process. They also conduct process capability studies to ensure that the processes are capable of meeting the desired product specifications.4. Product and Process Validation:5. Feedback, Assessment, and Corrective Actions:Throughout the APQP process, the team gathers feedback from various stakeholders, including customers, suppliers, and internal teams. This feedback is used to assess the performance of the product and processes. The team analyzes the feedback and identifies any non-conformances or defects. Corrective actions are then implemented to address these issues and prevent recurrence.6. Launch, Feedback, and Continuous Improvement:Once the product and processes are validated and approved, the product is launched into production. In this phase, the team closely monitors the production process, gathers feedback from customers, and tracks the performance of the product. They also focus on continuous improvement to enhance product quality, reduce defects, and optimize manufacturing processes.7. Post-Launch Assessment:After the product has been launched, a post-launch assessment is conducted. The team evaluates the overallperformance of the product and processes. They identify areas for improvement and take corrective actions if necessary. The team also documents the lessons learned throughout the APQP process and updates the APQP documentation for future reference.。
- 1、下载文档前请自行甄别文档内容的完整性,平台不提供额外的编辑、内容补充、找答案等附加服务。
- 2、"仅部分预览"的文档,不可在线预览部分如存在完整性等问题,可反馈申请退款(可完整预览的文档不适用该条件!)。
- 3、如文档侵犯您的权益,请联系客服反馈,我们会尽快为您处理(人工客服工作时间:9:00-18:30)。
28-Feb-2013
23-Jun-2011
APQP Elements
Subactivities
M i l e s t o n e s
VPD
AA
PPC
PC
PV
IR
CR
PE Action Plan Description Owner / Responsible Target Close Date Remarks / Comments
05-Apr-2012
2011-11-10
Project / Product Name:
##
Oxygen 2 I P D
Supplier name:
ZUHAI ACTION PLAN / COUNTER MEASURE
APQP Review Date:
10-Nov-2011
19-May-2011
03-May-2012
23-Sep-2010
29-Sep-2011
0) General
Does the supplier have a valid SEAT / UAT 534 certification, GPA and evidence of compliance to Philips Sustainability requirements? List team members from Philips and the supplier with their contact details and indicate their attendance and agree on the APQP review frequency and roles & responsibilities per APQP Element Jointly review VoC analysis and NPS data. Ensure VoC is translated to CTQ requirements. Discuss and agree the design / functional performance / system requirements. If applicable, discuss and agree the aestethic/craftmanship targets Discuss and agree the KPIs including quality targets (ppm or Cpk) including internal/external FOR and the reliability targets (e.g. MTBF, FiT or FCR/PFQ) Review and agree program timing dates (including gateways and milestones) Review and agree ramp-up plan and ensure the volume & mix forecasts are achievable. Review and agree safety and approbation requirements (eg IEC60065) Verify Philips RoHS, REACH & Regulated Substances requirements (Declaration, test reports, inspection plan) are fulfilled. Ensure previous lessons learned are included/considered. Jointly review every function of the product and ensure every function is included / considered. Define & list the failure modes in technical and measurable terms and first assess the severity(S) of all failure modes, then the occurence(O) and finally the current controls(D).
2011-11-10
Project / Product Name:
##
Oxygen 2 I P D
Supplier name:
ZUHAI ACTION PLAN / COUNTER MEASURE
APQP Review Date:
10-Nov-2011
19-May-2011
03-May-2012
17-May-2012
Printed @ 2014-7-28 16:20 CLSB - 1413 KONINKLIJKE PHILIPS ELECTRONICS N.V. 2010 All rights are reserved. Reproduction in whole or in part is prohibited without the written consent of the copyright owner
1) Customer Input Requirements
Jointly assess the impacts of failure effects by considering the outcome on the product, next higher assembly, system, customer wants and government regulations. Verify the potential causes and/or mechanisms of failure are 2) DFMEA identified for all failure modes. Ensure corrective actions, responsibilities and completion dates are assigned to high Severity, high Criticality (S x O) and high RPN (S x O x D) failure modes. Verify the corrective actions being implemented before RPNs are revised Use DFMEA to identify and review potential CTQ characteristics Translate and transfer the high Severity, high Criticality (S x O) and high RPN failure modes which cannot be reduced by design to the PFMEA. (The outcome of DFMEA is fed into PFMEA.) Ensure DFMEA will be updated when there is design and/or process change. Organise regular technical design reviews (at design owner) at appropriate intervals with appropriate team members Ensure the most promising concept selected and prove the technical feasibility 3) Design Review(s) Ensure the material selection is done according to agreed reliability targets (where applicable) Assess & agree capability of agreed critical requirements for components or sub modules to relevant CTQ's against targets with prototypes and/or FOS Ensure there is clear identification and agreement on; * all applicable tests (including design verification, product verification, SET, reliability, HALT, MEOST, lifetime quality tests tests) * methods, * equipment, * acceptance criteria, * sample sizes and sample allocation plan, * design level, 4) Design * timing and Verification / * the ownership (supplier or Philips) Product Ensure the tests that address the effects of the internal /external Validation Plan & environment including customer usage are considered. Review Ensure variable data is used where possible. Ensure the design verification tests are performed on representative prototype (made by prototype technologies and/or FOS) to verify potential CTQ-Sep-2010
29-Sep-2011
Ensure the product validation tests are performed on the products produced during the product trial run (running at R @R) to verify CTQ's. Ensure the DV / PV tests are successfully completed inline with the project timing. Agree on the frequency of reporting and confirm the contact details of related personnel for lifetime tests. Issue Bill-of-Materials (includes components/modules related to safety and CTQs) with sub-suppliers identified Identify potential critical sub suppliers, assess the risks and verify there is an action plan to minimise the risk (where required) on the 5) Sub supplier project Verify potential key/critical subsuppliers with direct contract to Philips Risk are ISO 9000 certified, compliant to Philips Sustainability Declaration Management and Restricted Substances Declaration requirements and have a robust plan to achieve ISO14001 in one year from the date of sourcing (or ISO14401 compliant) Verify sub-suppliers are capable of supporting the program requirements including quality targets, timing and volume Verify the timing of appropriate resources to ensure they are available and in place ontime to design, develop and implement the project and meet the targets. Provide the project team with the sufficient information to estimate/calculate investments for facilities, tools and gauges