薄膜技术英文课件:1introduction
膜技术介绍-中英对照版

Wuhan Kaidi Water Technology Co., Ltd.
一.超滤膜过滤原理 I. Working Principle of Ultrafiltration Membrane
超滤膜技术是一种压力驱动下的膜孔分离技术; 超滤膜技术是一种压力驱动下的膜孔分离技术; Ultrafiltration is a membrane pore separation technology driven by pressure; 根据膜孔径大小不同,可有效截留水中的悬浮物颗粒、胶体、 根据膜孔径大小不同,可有效截留水中的悬浮物颗粒、胶体、有机大 分子、细菌、微生物等; 分子、细菌、微生物等; Based on different membrane pore diameters, it can effectively intercept suspended particles, colloids, organic macro molecules, bacteria and microbes, etc. 对胶体的去除率≥90%; 对胶体的去除率 ; The removal rate of colloids ≥90%; 结合微絮凝技术,对有机物的去除效果也较为明显。 结合微絮凝技术,对有机物的去除效果也较为明显。 Combined with micro flocculation technology, it effectively removes organic substances.
Wuhan Kaidi Water Technology Co., Ltd.
过滤 / 分离范围 Range of Filtration / Separation
Colloids 胶体 Bacteria 细菌 Pollens 花粉 200 100 10 Yeasts 酵母 1 0.1 Viruses 病毒
6. Metal Etch Introduction

(Al2O3) 加入BCl3 的主要目的有二: 1. BCl3與O2 及水分的反應性很好,所以加入BCl3將可減少Cl2電漿內的 O2與H2O的含量; 2. BCl3在電漿內可形成BClX原子團及BCl3+正離子,其中BCl3+是產生離 子轟擊的重要離子來源之一.
P.7 P.7
Metal etch concept(4) 金屬的蝕刻金屬的蝕刻- - Difference mask material
P.6 P.6
Metal etch concept(3) 金屬的蝕刻(氣體 氣體) 金屬的蝕刻- - Gas (氣體) - - Cl2/BCl3
Cl2 - Plasma - - >Cl +Cl ---Al (s) +3Cl (g) AlCl3 (g)
- - - - -反應式 - - - - -反應式
(a) CVD 鎢的沉積 (b) 鎢的乾式回蝕 (c) 鎢的回蝕過度 (d) TiN 層的過度回蝕
P.11 P.11
WF6 的沸點為17.1 oC, 因此可使用氟化物氣體來進行鎢回蝕步驟
SF6 → F ⋅ + SFx ( g )
W( s ) + 6 F ⋅ → WF6 ( g )
Vapor Pressure of Metal Fluorides and Chlorides
Al°BCl3 or Cl2 Al° 2(AlCl3• 6H2O)
AlCl3 ( Lewis acid) ---- etching mechanism Al(OH)3 + 3 HCl ------------(1) ------------(1) Al2O3 + 9 H2O + 6HCl ------------(2) 6HCl ------------(2) AlCl3 + H2 --------------------------(3) --------------------------(3)
薄膜技术英文PPT课件-07 Thin film stress and adhesion

– O into Ti film Tensile stress obtained by molecular leave the
film – NH3 out of the Si3N4 film
Factor of growth stress--microstructure
Thermal stress
f
TE f 1 f
EAl
ETiN
Classification of film stress Tensile stress(+) Compressed stress(-)
Thermal stress Growth stress
Growth stress(intrinsic stress): stress distributions present in films following growth on substrates or on adjacent layers.
Thin film stress:the force per unit area on the cross-section of thin film usually the stress is the average value on the cross-section.
Stress Measurement of thin film
Total stress = growth stress + thermal stress
Factor of growth stress
➢ Chemical element ➢ microstructure ➢ Energetic bombardment
薄膜技术英文课件:04Thin-Film sputtering processes

– The electric field accelerates electrons and negatively charged ions toward the anode substrate where they impinge on the growing film.
Technology of Thin Film
Thin-Film Sputtering Processes
Outline
1. Introduction 2. Plasmas, Discharges, and Arcs 3. Physics of sputtering
2
Introduction
• Evaporation and sputtering are quite different
✓Thermal plasma:highly ionized plasma, with high temperature of ion and high temperature of electron. (eg: Sun)
Production of Plasma
• Gas discharge:gas ionize in electric field by collision between energic electron and gas molecular.
Schematics of simplified sputtering systems: (a) DC, (b) RF.
薄膜技术英文PPT课件-05Thin-Film CVD

G
RT
ln
rCc rAa rBb
ri
ai ai
ΔG>0,react in reverse-direction
ΔG<0;react in forward-direction Judge feasibility or direction of reaction
e.g.
Obtain the O2 partial pressure
e.g. GaAsepitaxical film by MOCVD:
e.g.硬质涂层的化学气相沉积
Disproportionation
• Disproportionation reactions are possible when a nonvolatile metal can form volatile compounds having different degrees of stability depending on the temperature.
5. Heterogeneous reactions catalyzed by the surface leading to film formation
6. Desorption of the volatile by-products of surface reactions
7. Convective and diffusive transport of the reaction by-products away from the reaction zone
Technology of Thin Film
Chemical Vapor Deposition
Xuhai Zhang
School of Material Science and Engineering Southeast University
薄膜技术02Vacuum Science and Technology

Gas impingement Flux Application: Contamination of substrate
Time for complete monolayercoverage of a surface
N N 2MRT
NAp
• In air at atmospheric pressure and ambient
Where can we find the vacuum?
1.2 Unit of vacuum
• International System of Units :Pascals 1 atm=101.325 kPa • traditional unit of pressure: Torr 1Torr=133.3224Pa
<1×10−10
1×10−4 to < 3×10-15
Atmosphere 1 1 to 0.03
1.3 Vacuum >102Pa
Medium vacuum 102 ~10-1Pa
High vacuum 10-1~10-5Pa
Vacuum evapration
2. Kinetic Theory of Gases
Maxwell-Boltzmann distribution
f (v)
4
(M
)
3 2
v
2
e
Mv2 2 RT
2RT
M--molecular weight T--absolute temperature R--gas constant
Velocity distributions for Al vapor and H2 gas.
second • So gases mix together rather slowly even
薄膜技术英文PPT课件-04Thin-Film sputtering processes

Production and maintenance of Plasma
靶
基片
Glow discharge plasma
a plasma formed by the passage of electric current through a low-pressure gas. It is created by applying a voltage between two metal electrodes in a glass tube containing gas. 。
Technology of Thin Film
Thin-Film Sputtering Processes
Xuhai Zhang
School of Material Science and Engineering Southeast University
Outline
1. Introduction 2. Plasmas, Discharges, and Arcs 3. Physics of sputtering
Arcs have been defined as gas or vapor discharges where the cathode voltage drop is of the order of the minimum ionizing or excitation potential.
Furthermore, the arc is a self-sustained discharge that supports high currents by providing its own mechanism for electron emission from negative or positive electrodes.
Film Information

断裂伸长率(MD/TD)
%
GB/T 1040.3
all
√
Elongation at Break
弹性模量(MD/TD)
Mpa
GB/T 1040.3
all
√
Modulus of Elasticity
热收缩率 hot-shrinkage rat
%
GB/T 10003
all
√
表面张力
Dyne/cm GB/T 14216
all
√
%
GB/T 2410
clear
√
透明度Transparence
GB/T 2410
clear
光泽度 Gloss(60°)
%
all
√
白度 Whiteness
white
√
C.O.F
GB/T 10006
(Static/Dynamic)
拉伸强度(MD/TD)
Mpa
GB/T 1040.3
all
√
Tensile Strength
熔融指数
➢ 熔融指数对应分子量(成反 比),体现熔体流动性
➢ 均聚2~4g/10min ➢ 共聚4~7g/10min(乙烯含量
3~5%) ➢ 分子量大,拉伸强度大,机械
性能好,结晶度降低; ➢ 分子量分布窄,拉伸强度大,
加工困难 ➢ PP数均分子量8500
6
Define
• 薄膜是聚合物的一种二维形 式,其特征是表面积与体积比 很大。
Cast(CPP, CPE) Blowing(IPP, IPE)
Biaxially Oriented (BOPP, BOPET, BOPA)
10
薄膜技术绪论PPT课件

薄膜科学的应用
2.金刚石薄膜
金刚石具有一系列优异的物理性质,包括已知物 质中最高的硬度、耐磨性和弹性模量,极高的电阻率、 击穿场强和很低的介电常数,宽的光谱透过范围,极 高的热导率,极低的线膨胀系数,很宽的禁带宽度, 极高的载流子迁移率和极高的化学稳定性。
金刚石薄膜的应用
(1)力学性质的应用 利用其高硬度、高耐磨性。焊接在工具尖端或直接沉积在
第2页/共38页
薄膜科学的发展历史
对液体薄膜首先作了正式描写的是美国著名的科学家、作家兼政治家的富 兰克林(Benjamin Franklin),他在1774年的文件中留下了这样的描述:
“不超过一茶匙的油,迅即地展开为数平方码,然后很惊人地慢慢扩展,直 到抵达在下风处的水池边缘,布满了水池的那个区域,可能有半英亩(1英亩约 为4000平方公尺)之广,而表面平滑的像面镜子。”
第7页/共38页
薄膜科学的发展历史
❖ 从人类开始制作陶瓷器皿的彩釉算起, 薄膜的制备 与应用已经有一千多年的发展历史。
❖ 从制备技术、分析方法、形成机理等方面系统地 研究薄膜材料则起始于上世纪五十年代。
❖ 直到上世纪80年代, 薄膜科学才发展成为一门相对 独立的学科。
❖ 促使薄膜科学迅速发展的重要原因是薄膜材料的 强大的应用背景、低维凝聚态理论的不断发展和 现代分析技术的出现及分析能力的不断提高。
第13页/共38页
薄膜科学的应用
(2)热学性质的应用
利用其极高的热导率。室温下,金刚石的热导率是铜 的5倍。本身又是极好的绝缘材料。因此,金刚石薄膜可 用于高功率光电子元件、激光器、集成电路芯片的散热器 材料。
(3)电学性质的应用
利用其高载流子迁移率、宽禁带宽度、高击穿场强、 高热导率和高饱和运动速度等优点。使之成为制造高温、 高压、高功率和高频强辐射条件下工作的电子器件的绝好 材料。
《薄膜材料与技术》课件
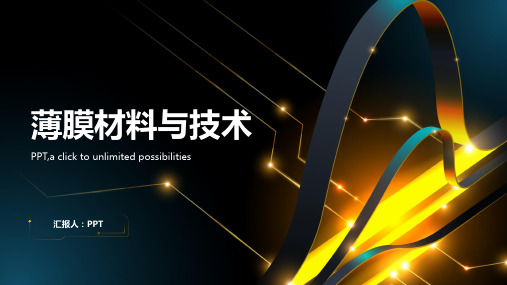
Part One
单击添加章节标题
Part Two
薄膜材料的种类
金属薄膜
铝薄膜:广泛 应用于包装、
电子等领域
铜薄膜:常用 于电子电路、 太阳能电池等
领域
镍薄膜:常用 于电子电路、
电池等领域
钛薄膜:常用 于航空航天、 生物医学等领
域
塑料薄膜
聚乙烯薄膜:广泛应用于食品包装、药品包装等领域 聚丙烯薄膜:具有较好的耐热性和耐化学性,常用于包装和印刷 聚氯乙烯薄膜:具有良好的耐候性和耐化学性,常用于建筑和工业领域 聚酯薄膜:具有良好的耐热性和耐化学性,常用于包装和印刷
面的研究
研究目标:开发具有优异性 能的新型薄膜材料
研究意义:推动薄膜技术的 发展,提高薄膜材料的性能
和应用范围
薄膜材料在新能源领域的应用研究
储能电池:薄膜材料作为储 能电池的电极,提高能量存 储密度
燃料电池:薄膜材料作为燃 料电池的电极,提高电化学 反应效率
太阳能电池:薄膜材料作为 太阳能电池的基底,提高光 电转换效率
超级电容器:薄膜材料作为 超级电容器的电极,提高能
量存储和释放速度
热电材料:薄膜材料作为热 电材料的基底,提高热电转
换效率
光热材料:薄膜材料作为光 热材料的基底,提高光热转
换效率
薄膜材料在其他领域的应用研究
电子领域:薄膜材料在电子设备中的广泛应用,如薄膜太阳能电池、薄膜显示器等
光学领域:薄膜材料在光学器件中的应用,如薄膜光学镜片、薄膜光学传感器等 生物医学领域:薄膜材料在生物医学领域的应用,如薄膜生物传感器、薄膜药物载体等 环境领域:薄膜材料在环境领域的应用,如薄膜空气净化器、薄膜水处理设备等
力学特性
弹性模量:薄膜 材料的弹性模量 通常较小,易于 弯曲和变形
英文版BOPP薄膜简介

英⽂版BOPP薄膜简介Biaxially Oriented Polypropylene Film (BOPP)Many of the unique characteristics of polypropylene enhance its utilization in the application of film. The main application for polypropylene film are the packaging of food, textiles and tobacco products. Biaxially Oriented Film (BOPP)Biaxial orientation is a process in which a continuous cast film is heated to bring it to a stretchable temperature and thereafter it is stretched in machine and then in transverse direction.Biaxial orientation of polypropylene (BOPP) film is done by two methodsTenter frame processDouble bubble processTenter Frame ProcessTenter frame process is a very expensive way of processing BOPP film. However it has become popular due to higher production rate with very thin and wide width film (Fig. 1)ExtrudersExtruders with 150 to 200 mm dia screws having L/D of 26:1 to 30:1 are more popular.Dies600 to 1500 mm wide coat hanger type of dies are usedThe Tenter Frame ProcessCasting & QuenchingThe molten polymer extruded from the die is placed against a chill roll or multiple chill rolls. The most popular being casting onto a chill roll partially submerged in a water bath. The chill roll and water bath temperatures are generally 20 to 25°C. Usually, these chill rolls are 1000 to 2000 mm in diameter and approximately 1000 to 1500 mm wide. The surface of the chill roll must be very smooth; pitting or irregularities on the surface of the roller will influence the film quality. An air knife is used to force proper contact of molten polymer against the casting roll. The cooled web proceeds towards the machine direction orientation section.Machine Direction Orientation (MDO)The base sheet is alternatively heated by passing it over the heated rollers (145 - 150°C) to achieve uniform heating of web throughout its thickness. These rollers are usually smaller in diameter (450 to 600mm) compared to the casting drums (chilled rolls).When the film reaches the necessary stretching temperature, it is passed over a series of stretching rolls which are usually arranged in pairs. Each pair has a rubber nip roll to prevent slipping of the web while stretching. These first set of nip rollers are run at a speed similar to preheat rollers. The next set of rollers are operated at higher speeds than the first set of nip rollers. Usually the stretch ratio is kept between 4:1 to 6:1.From the stretching rollers, the film is passed on to a series of annealing rollers, which are heated to a temperature, adequate to prevent shrinkage in the machine direction (MD) of the web. Transverse Direction Orientation (TDO)From the machine direction orienter, the film is guided on to the chain (Fig. 3), containing clips (Fig. 4) which close on to the film. A rail guides the chain with clips to preheating section, where the film is heated with hot air at 160°C, slightly below the melting point of polypropylene.As the film leaves the preheat section of the oven, the chain diverges quite rapidly to a ratio of 8:1 to 10:1. The film is then passed on to annealing oven where it is maintained at 155°C, to reduce the shrinkage of the film. Usually the tenter frame run at line speeds of 200 to 300 meters/min.WindingEdges of the film remain thick, as they are in the clips while the film is being stetched. These edges are then trimmed off as the film leaves the tenter frame. The wide film is slit into the required width by rotating knives and wound on to separate winders.Double Bubble ProcessThe equipment for this process is small compared to that of tenter frame process (Fig. 5). It is difficult to produce thin film in double bubble process. The output in term of quantity and width of the film is also very low compared to that in tenter frame.ExtrudersGenerally 50 mm to 75 mm extruders are usedDiesCircular dies of 150 to 200 mm diameters are more popularQuenchingThe extruded tube from the die is directly taken into the quenching bath (20-25°C) collapsed between the nip rollers located at the bottom of the quench bath. The film is then taken up to second set of nip rollers via a drying unit. The water is stripped in the drying unit.PreheatingThe tube in its flattened state is heated (at 150 to 160°C) either by IR heaters or hot air. The heated tube is inflated to its new dimensions, which is usually 5 to 6 times its original diameter. With the third set of nip rollers, the film is stretched in the machine direction at the ratio of 5:1 to 6:1A set of cooling rings are used to cool the inflated bubble prior to being collapsed. Collapsed tube is slit on both the edges and the web is then separated before winding.Effect of Processing Variables on Film PropertiesFilm properties depend on different processing variables, as described below1.Requirement: A :High modulus and tensile strengthB :Low shrinkageA Tensile strength and Modulus can be improved by :-Lowering the temperatures of chill roll and quench water-Increasing the stretch roll temperature-Increasing the line speed-Increasing the stretch ratiosB Lower shrinkage can be achieved by :-Using higher stretching temperature-Using higher annealing temperatureII Requirements : A :Low HazeB :High GlossA Haze can be reduced by-Lowering temperature of chill roll and quench water-Increasing the temperatures of stretching and annealingB Gloss can be improved by-Using higher melt temperature-Using chill roll, MD rolls and die having clean and smooth surfacesRepol Polypropylene Grades for BOPP FilmRepol Grade MFICharacteristics(g/10min)HOMOPOLYMERH029SG 2.9Good processability andlow gelsRANDOM COPOLYMERR070EY7.0Contains antiblock andslip. Low heat sealtemperaturesApplications of BOPP FilmsFollowing are the important features of BOPP film which make it a material of choice for flexible packaging :Low specific gravity which results in higher yield (m2/kg)Higher mechanical properties, which allow for thinner films to be madeBOPP films have by far the highest moisture barrier of all plastic films. WVRT values at 38°C and 98% RH of different film substrates are as follows :20 microns OPP- 4.85 gms/sq.m/24 hrs20 microns HDPE- 6.25 gms/sq.m/24 hrs25 micron Cast PP-10.00 gms/sq.m/24 hrs25 micron LDPE-15.00 - 20.00 gms/sq.m/24 hrs10 micron PET-45.00 gms/sq.m/24 hrsBOPP films have good barrier to flavours and aromas, particularly at the levels of concentration normally encountered in packaged products.Co-extruded BOPP film with good barrier and high transparency is heat sealable as produced i.e. without having to be coated, avoiding additional operation. The other major advantage is, being heat sealable on both surfaces, it is possible to seal particularly on VFFS operations with better seal integrity and a much neater pack.?BOPP films have outstanding optical properties and thegloss/transparency/sparkle obtained are among the best available on any material.BOPP films have extremely high strength - particularly tensile strength, puncture resistance, bursting strength, stiffness, tear strength and abrasion resistance.BOPP film packages also have a very crisp feel which make them definitely superior to those made from flexible materials.BOPP films have very high stability / performance over a very wide range of temperatures and environmental conditions. They are not susceptible to high relative humidity like cellophane and hence retain their properties and dimensional stability over the entire range of conditions normally encountered by packages.BOPP films have very high chemical resistance to fats/oils - particularly of vegetable origin, most chemicals and many solvents. The basic material (polypropylene) is essentially a highly compatible with most packaged products. It is particularly suitable for direct food contact.BOPP films have extremely high flex crack resistance. Polypropylene is the only basic resin that has an "integral hinge" property, in that it can be flexed any number of times without fracture. This property is extremely important in flexible pouches during their transit and handling.BOPP films are eminently suitable for down stream operations. They are highly amenable to all operations like printing, coating, lamination, metallisation and pouching.BOPP film can be subjected to sterilization without impairing mechanical properties and hence has wider packaging applications.BOPP film is heat sealable at high speeds using co-ex OPP or off-line coated film Due to the higher stiffness of BOPP film, higher packaging speeds (50-60 m/min) are possibleBOPP films can be vacuum metallised with high purity aluminium, to significantly enhance barrier propertiesSome of the typical applications of BOPP film are as follows :(A)Plain filmIndustrial tape (25-40 mic)Pressure sensitive tapesLamination (10-20 mic)Book covers, brochures, catalogues, shopping bags, carton boxes, cosmetic boxes, restaurant menus, film to film laminates (PET/BOPP/POLY)Food packing (20-40 mic)Laminates, metallizingOthers (12-40 mic)Tea chest lining, flower over-wrapping, textiles, cable over-wrappings, photo albums, release film, biscuit inner-wraps, envelope windows, tear tapes,metallizing, stationery(B)Co-Extruded filmOver wrapping (18-23 mic)Cigarette, audio/video cassette boxes, cartons, blades, toffees and candiesGeneral purpose (20-40 mic)Lamination, snack food, bakeries, cosmetic, noodles, textiles, bread, audio/video cassette, metallizing, twistwrapFood packing (20-50 mic)Lamination, food, chipsSuper Seal (25-35 mic)Powdery material, food grain, sugarBOPP FilmTrouble Shooting GuideTenter frameDefect Source SolutionThickness variation-Adjust the die gap-Adjust die heat temperatures-Check screen pack or filter, change ifnecessary-Check air knife position-Look for air bubbles under the sheetMDO-Increase temperature of preheat rolls-Decrease gap between stretching rolls-Decrease speed of MDO rollsTDO-Adjust stretching section temperatures-Examine oven for foreign objects blockinghot air nozzlesExtruder Surging -Check melt temperature fluctuation and pressure fluctuations-Increase back pressure by lowering metering section temperatures-Increase first transition zone temperatureSplits Foreignparticles in theresin -Examine for gels or dirt-Discontinue putting reclaim or repelletized pellets in main feed-Change filter packOvens-Raise temperature of the preheat section ofovenWater in theresin-Change resin feedGauge Band-Find source of gauge variation and fix Jerky chain-Lubricate rail and chainOil drops on film in oven -Decrease oil flow to chain and rail and wipe off excess oilDirty clips-Wind base sheet on MDO winder andcheck chain-Clean clips or remove faulty clip andreplaceHaze bandsfrom MDO-Increase stretching heat of MDONon uniformmelt-Adjust extruder heat profilePoor optics High Haze Low GlossMDO Heats-Increase temperature of preheat rolls andstretching rolls if haze bands are present Low extrusionheats-Raise melt temperatureSlow cooling incasting section-Decrease casting drum temperature-Decrease bath temperatureWater marks Water carry-over to MDOsection-Remove water from web before MDOBubbles or Voids Resin airentrapment -Change resin-Increase the transition zone temperature -Increase the back pressure BOPP FilmTrouble Shooting GuideDouble Bubble frameDefect Source Solution Thickness variation Die : poor flow-Adjust the die gap -Adjust the die temperaturesPolymer filter unplugged -Check screen pack or filter, change if necessary Unlevel water-Adjust level of water ring or bathAir draft onbubble-Seal air leaks in enclosure around bubble Blow-outs or BubblebreaksOven-Oven heats too low, raise temperatureGels in film-Change filter-Change resinPlate-Out marks from mandrel -Wipe off mandrel-Lower melt temperature -Raise mandrel temperature -Change resins。
薄膜物理与技术课件1-8
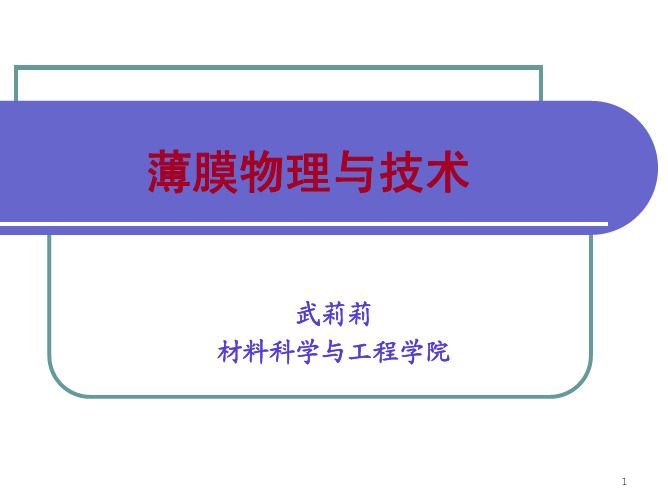
③ 指定空间内,低于一个大气压的气体状态(科学概念) 用气压表示空气的稀密程度。
什么是气压?
容器里飞来飞去的气体分子一直在频繁地撞击容器壁, 其趋势是向外推挤容器壁。单个分子碰在器壁上产生的力自 然是微不足道的,然而同时碰在器壁上的分子数目非常巨 大,合起来就是很大的力,这种推力就是气压。 气压的性质是,当温度和体积不变时,容器中的空气越 稀薄,也就是说容器中气体分子的数越少,气压越低。在自 然环境中,海拔越高的地方,气压越低。也就是说,越往高 空(外太空)去,便越接近“完全空”的真空。
22
1.1.2
真空术语(six vacuum terms)
ቤተ መጻሕፍቲ ባይዱ
① 速度分布(velocity distribution) 教材图1-1的麦克斯韦速率分布曲线。 最可几速度 平均速度
v m = 1 . 41 RT ( cm / s )( 1 − 3 ) 讨论速度分布 M
v a = 1 . 59
v r = 1 . 73
11
微机械与薄膜技术
薄膜技术能实现材料的微米、纳米超微细加工。由此实现的微机 械具有无限的应用前景。
图0-7
微型马达实例图
12
图0-7
微机械挽救重症患者生命(左),可进入血管的微型机器人(右)
13
加速度传感器
用于汽车防撞系统的气囊,及时充气膨胀就是靠检测汽车的加速度,并由 此触发信号。 机器人行走,也要靠行走中因倾斜产生的力(加速度)来控制步行姿势。 为了测量加速度,离不开由薄膜技术及超微细加工技术制作的传感器。
26
真空术语(续) ⑤ 饱和蒸汽压(重点与难点)
把各种固液体放入密闭的容器中,在任何温度下都会蒸发,蒸发出 来的气压称为蒸汽压。在一定温度下,单位时间内蒸发出来的分子数与
薄膜技术03Thin-Film Evaporation

2
Introduction
• Thermal energy is imparted to atoms in a liquid or solid source such that their temperature is raised to the point where they either efficiently evaporate or sublime.
dN max Aedt
N APe
2MRT
molecules/cm2-s.
The key variable influencing evaporation rates is temperature since it has a profound effect on equilibrium vapor pressures
• First industrial production: optical components such as mirrors and beam splitters, and later of antireflection coatings.
• Higher deposition rates, better vacuum and cleaner environments for film formation and growth, and general applicability to all classes of materials were among the reasons for the ascendancy of evaporation methods.
薄膜技术英文课件:02Vacuum Science and Technology

What is the “Vacum
In vacuum scientific field, vacuum is a region with a gaseous pressure much less than atmospheric pressure.
Features of vacuum
Technology of Thin Film
Vacuum Science & Technology
Outline
1. Concept of vacuum 2. Kinetic Theory of Gases 3. Gas Transport and Pumping 4. Vacuum Pumps 5. Vacuum Systems 6. Conclusion
Where can we find the vacuum?
1.2 Unit of vacuum
• International System of Units :Pascals 1 atm=101.325 kPa • traditional unit of pressure: Torr 1Torr=133.3224Pa
The pressure in vacuum is lower than 1 atm, so the evacuated chambers are under pressure from atmosphere.
Features of vacuum
There are less gas in the state of vacuum, the frequency of collision between gas moleculars would be decrease.
Outer space
薄膜技术及应用PPT课件

⑵光学薄膜 减反射膜、反射膜、分光镜、滤光片; 照明光源所用的反热镜与冷光镜薄膜; 建筑物、汽车等交通工具所用的镀膜玻璃; 激光唱片与光盘中的光存储薄膜; 集成光学元件所用的介质薄膜与半导体薄膜。
ANTI-REFLECTION CHART
three layers
20
⑶硬质膜、耐蚀膜、润滑膜 ⑷有机分子薄膜 ⑸装饰膜 ⑹包装膜
薄膜材料是采用特殊的方法,在体材料的表面沉 积或制备的一层性质与体材料性质完全不同的物质 层。
薄膜材料往往具有特殊的材料性能或性能组合。
4
薄膜材料科学成为材料科学中发展最迅速分支 的原因:
(1)现代科学技术的发展,特别是微电子技 术的发展,过去需要众多材料组合才能实现的 功能,现在仅仅需要少数几个器件或一块集成 电路板就可以完成。薄膜技术正是实现器件和 系统微型化的最有效的技术手段。
刀具表面氮化物、氧化物、碳化物镀膜
21
22
薄膜材料学涉及的内容: (1)薄膜材料的制备手段; (2)薄膜材料的形核与生长理论; (3)薄膜材料的表征技术; (4)薄膜材料的体系、性能及应用。
23
24
25
26
27
28
• High performance Nano-FETs • Nano-Optoelectronic Devices • Photodetectors • Nano LEDs • Sensors • Solar cell
SiGe:H、a-SiC:H、a-SiN:H、a-Si/a-SiC等一 系列晶态与非晶态超晶格薄膜。
C-V Characteristics of GaAs/AlGaAs ure showing capacitance Oscillations Associated
薄膜技术英文课件:1introduction

Thin film
ρb≤ρtf(有问题)
Mb≤Mtf
small(um )
Large(mm)
17
2. Thin film vs. block material-1
Density Melting point Crystalline size
Bolck
Thin film
ρb≤ρtf(有问题)
Mb≤Mtf
39
Chemical vapor deposition(CVD)
• Thermal decomposition • Reaction on surface of substrate
The process of chemically reacting a volatile compound of a material to be deposited, with other gases, to produce a nonvolatile solid that deposits atomistically on a suitably placed substrate.
• GaN 、GaAs/GaAlAs、a-Si/a-SiC
– Thin film resistor(电阻), thin film capacitor(电容)
electroluminescence
• Ni-Cr low resistance thin film resistor
– Thin-film solar cell
– Piezoelectric(1.压电的) thin film for wave filtering
• ZnO 、AlN
– Sensitive thin fi2
• Optical thin film薄膜
薄膜技术英文PPT课件-02Vacuum Science and Technology (2)

2. Kinetic Theory of Gases
Maxwell-Boltzmann distribution
f (v)
4
(M
)
3 2
v
2e
Mv2 2 RT
2RT
M--molecular weight T--absolute temperature R--gas constant
Velocity distributions for Al vapor and H2 gas.
17
Outline
1. Concept of vacuum 2. Kinetic Theory of Gases 3. Gas Transport and Pumping 4. Vacuum Pumps 5. Vacuum Systems 6. Monitoring the Vacuum Environment 7. Conclusion
• At low pressure, the mean distance between molecular collisions is large compared to the dimensions of the system, there are only molecule-chamber wall collisions.
p nMva2 nRT
8N A
NA
n-- the number per unit volume
NA-- Avogadro's number n/NA—the number of moles per unit volume
The gas pressure is related to to their kinetic energy or temperature.
- 1、下载文档前请自行甄别文档内容的完整性,平台不提供额外的编辑、内容补充、找答案等附加服务。
- 2、"仅部分预览"的文档,不可在线预览部分如存在完整性等问题,可反馈申请退款(可完整预览的文档不适用该条件!)。
- 3、如文档侵犯您的权益,请联系客服反馈,我们会尽快为您处理(人工客服工作时间:9:00-18:30)。
Density Melting point Crystalline size
Bolck ≤ ≤
small(um )
Thin film Large(mm)
14
2. Thin film vs. block material-1
Density Melting point Crystalline size
➢ Stoichiometric ratio
– Non-stoichiometry is common in thin film
• SiO2
SiOx
• Transparent conductive film
– Tin indium oxide (InSnyOx) condConductivecond
Thin film: thickness less than 1 micrometer
Coating: thickness lagrer than1 micrometer
12
Difference between thin film and block material
13
Thin film vs. block material
thin film for semiconductive dives and integrated circuit(集成电路)
• Al、 polysilicon、SiO2
small(um )
Large(mm)
20
2. Thin film vs. block material-1
Density Melting point Crystalline size
Bolck
Thin film
ρb≤ρtf(有问题)
Mb≤Mtf
small(um )
Large(mm)
21
2. Thin film vs. block material -2
24
25
Gold-decorated Technology 鎏 金
• The process of “liujing”
– Making AuHg alloy (煞金) – Brushing Au compound (抹金) – Evaprating Hg (开金) – Making Au denser(密集的) (压光)
2
What is the “thin film”
3
4
5
6
7
8
9
10
11
What is the thin film?
a very thin layer of a substance on a supporting material; especially : a coating (as of a semiconductor) that is deposited in a layer one atom or one molecule thick
Technology of Thin Film:
Introduction
Outline
1. Concept of thin film 2. Difference between thin film and block material 3. History of thin film and coatingd 4. Modern technology for thin film deposition 5. The content of this course
small(um )
Large(mm)
18
Melting point (℃)
Thickness (Ᾱ)
19
2. Thin film vs. block material
Density Melting point Crystalline size
Bolck
Thin film
ρb≤ρtf(有问题)
Mb≤Mtf
29
Application in Modern Time
Electronic thin film Optical thin film Magnetic thin film Mechanical functional thin film
30
• Electronic thin film
– Conductive thin film and dielectric(介电)
26
Bronze(青铜) Mirror Polishing
27
Bronze Mirror Polishing
• There is Sn rich transparent layer with several hundred nanometer thickness on the surface of mirror.
• Dense SnO2 films with
microcrystallines
are
ห้องสมุดไป่ตู้
detected on the top of the Sn
Bronze mirror from easten han dynasty rich layer.
28
Glazing 上 釉
Glazing for ceramic • beautiful • clean
Bolck ≤ ≤
small(um )
Thin film Large(mm)
15
Density g/cm3
Temprature of substrate
16
Thin film vs. block material
Density Melting point Crystalline size
Bolck
Thin film
ρb≤ρtf(有问题)
Mb≤Mtf
small(um )
Large(mm)
17
2. Thin film vs. block material-1
Density Melting point Crystalline size
Bolck
Thin film
ρb≤ρtf(有问题)
Mb≤Mtf
Conductivity
22
Comparing to bulk materials, thin film materials have some unique properties
23
3. The History of Thin Film or Coating
Application in ancient time Application in morden time