船舶建造工艺课件09_边缘加工
船舶建造工艺课件

船体装配
总结词
船体装配是将加工好的船体零件和分段按照设计要求进行组装的过程。
详细描述
船体装配是船舶建造的关键环节,需要保证装配的精度和质量,以确保船体的整 体性能和使用寿命。同时,装配过程还需要考虑生产效率和成本等因素。
船舶下水与试航
总结词
船舶下水与试航是在船体装配完成后进行的,是对船舶性能的全面检验。
验、完工检验等方面的质量控制方法。
输标02入题
材料检验是质量控制的基础,涉及到原材料、外购件 、焊接材料等方面的检验和控制,以确保材料的质量 符合设计要求和规范标准。
01
03
完工检验是质量控制的最后环节,涉及到船舶整体性 能的测试和验证,以确保船舶的整体性能符合设计要
求和规范标准。
04
工序检验是质量控制的关键环节,涉及到船体结构焊 接、设备安装、涂装等方面的检验和控制,以确保各 道工序的质量符合要求。
船体设计
高速客轮的船体设计需要采用轻质材料和高强度材料,以减小船体重量和阻力。同时,需 要考虑船体的线型和船体结构,以提高航速和稳定性。
推进系统
高速客轮需要配备大功率的发动机和推进器,以确保在短途航行中能够快速到达目的地。 同时,为了减小噪音和振动,需要选择低噪音、低振动的发动机和推进器。
案例三:高速客轮的建造工艺
内部装修
豪华游艇的内部装修需要考虑材料的选择、工艺的处理和细节的处理。采用高品质的材料和精细的工 艺,打造豪华、舒适的内部空间。同时,还需考虑船员的居住和工作空间,以确保航行的顺利进行。
案例三:高速客轮的建造工艺
总结词
高速客轮主要用于城市间或岛屿间的短途运输,其建造工艺注重船体的轻巧和高速性能。 同时,为了提供良好的乘客体验,对船体的隔音和减震性能要求也很高。
船舶建造工艺边缘加工
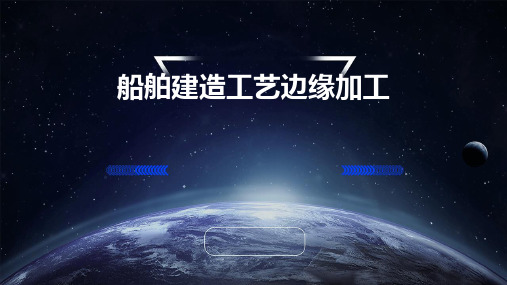
边缘加工的工艺流程
要点一
总结词
边缘加工的工艺流程主要包括准备、切割、打磨和检验四 个阶段。
要点二
详细描述
准备阶段主要是对钢板进行预处理,包括清洁、矫平和定 位等。切割阶段则是根据设计要求,利用切割设备将钢板 切开。打磨阶段则是利用砂轮、砂带等工具对钢板边缘进 行磨削,使其平滑。检验阶段则是检查钢板边缘的质量, 包括外观、尺寸和粗糙度等。如果质量不符合要求,需要 进行返工或重加工。
切割是边缘加工中最基本的一种,包括火焰切割、等 离子切割和水切割等。火焰切割利用高温火焰将钢板 切开,等离子切割则是利用等离子弧将钢板切开,水 切割则是利用高压水射流将钢板切开。打磨主要是利 用砂轮、砂带等工具对钢板边缘进行磨削,使其平滑 。压延则是利用压延机将钢板边缘压制成一定形状, 常用于折弯和卷筒等工艺。
详细描述
边缘加工是指在船舶建造过程中,对钢板边缘进行加工处理的一种工艺。通过边缘加工,可以去除钢板边缘的毛 刺、锐边和不平整的部分,提高结构强度、美观性和防水性能。边缘加工还可以使钢板更好地与其他结构件连接 ,提高整体结构的稳定性。
边缘加工的种类
总结词
边缘加工主要分为三种类型:切割、打磨和压延。
详细描述
智能化
智能化技术如人工智能、机器学习等在船舶建造工艺边缘加工中的应用,能够 实现自适应加工和智能优化,进一步提高加工质量和效率。
高精度与高效率
高精度
随着船舶行业的不断发展,对船舶建造工艺的要求也越来越 高。边缘加工的高精度能够提高船舶的整体质量和性能,满 足更加严格的设计要求。
高效率
高效率的边缘加工能够缩短船舶建造周期,提高生产效率, 降低生产成本。通过优化加工流程和选用高效能的加工设备 ,可以实现高效率的边缘加工。
船舶建造工艺学讲义

船舶制造技术讲义前言蓝天白云,碧海无垠,翩翩风帆,百舸争流。
这是大江、大海带给我们的遐想。
一艘艘优美而各具个性的水之精灵——船舶,总是给我们以劈波斩浪、一往无前的豪气!当我第一次踏上RORO船时,不由自主地为他庞大的体积所震惊。
在他的怀抱里,人、车犹如蚁群迁徙,实在是太壮观了!如果这艘船是你的杰作,你该有何等的骄傲!当然,我们也有冰海沉船、江艇倾覆的痛苦与思索。
但无论是雄壮还是凄婉,我们都难免要探究,那行进在水面上的美丽“天鹅”是如何从灰扑扑、脏兮兮的“丑小鸭”——钢板、型材而变成的呢?如何避免象“TITANIC”那样的悲剧?今天的船怎样才能更快、更舒适、更安全、更经济呢?你们接触船船舶知识已有若干时间,是否认识清楚了造船到底是一个什么样的过程呢?从今天开始,我们一起来解读这个过程。
这个过程也就是我们这门课程的主干。
当然,今天我的开场白或许有着点点丝丝的矫情,在以后的学习中,你们会发现完全不是那回事!好乏味呀。
是的,过程总是比结果令人乏味,但既然是过程就总是要过,而且要好好地过,乐在其中地过。
是吧?!我们开始吧。
先认识几个同学。
本课程学习要求:1.本课程特点:教学难点:理论推导少、面宽、应用型、约定俗成广泛性灵活性实践性——存在学习难度学习难点:不符合过去的学习习惯、实际经验少2.重点讲述章节: 1、2、4、5、7、8章3.课堂要求:遵守学校规定 . “互动”4.习题要求:认真思考、积极讨论、主动提问、独立完成、按时上交5.外文参考书:《GROUP TECHNOLOGY:A FOUMDATION BETTER TOTAL COMPANY OPERSTION》 G.M.RANSON6.100个英语单词:随课给出。
第一章造船(SHIPBUILDING)工程概论讲述内容:制造工艺学的涵义及任务、造船工艺流程(FLOW)、造船模式(MODE)、造船生产机械化和自动化、造船生产准备。
讲述重点:造船工艺流程......§1-1制造工艺学概述.......1.制造工艺学的重要地位20世纪80年代初在世界范围兴起的新技术革命正方兴未艾,必将由它引发第四次工业革命。
船舶建造工艺边缘加工
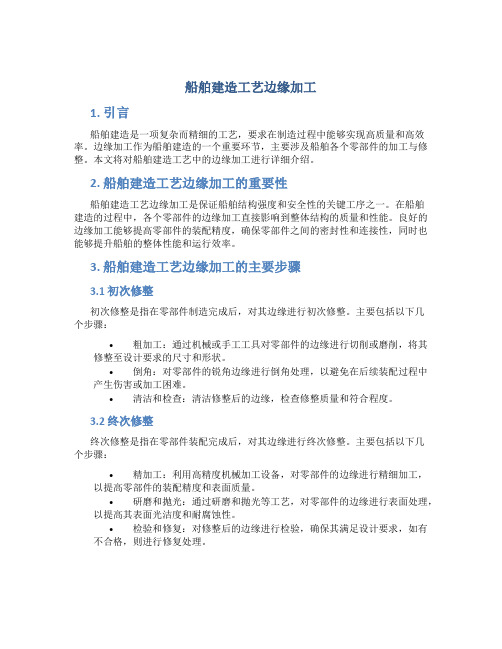
船舶建造工艺边缘加工1. 引言船舶建造是一项复杂而精细的工艺,要求在制造过程中能够实现高质量和高效率。
边缘加工作为船舶建造的一个重要环节,主要涉及船舶各个零部件的加工与修整。
本文将对船舶建造工艺中的边缘加工进行详细介绍。
2. 船舶建造工艺边缘加工的重要性船舶建造工艺边缘加工是保证船舶结构强度和安全性的关键工序之一。
在船舶建造的过程中,各个零部件的边缘加工直接影响到整体结构的质量和性能。
良好的边缘加工能够提高零部件的装配精度,确保零部件之间的密封性和连接性,同时也能够提升船舶的整体性能和运行效率。
3. 船舶建造工艺边缘加工的主要步骤3.1 初次修整初次修整是指在零部件制造完成后,对其边缘进行初次修整。
主要包括以下几个步骤:•粗加工:通过机械或手工工具对零部件的边缘进行切削或磨削,将其修整至设计要求的尺寸和形状。
•倒角:对零部件的锐角边缘进行倒角处理,以避免在后续装配过程中产生伤害或加工困难。
•清洁和检查:清洁修整后的边缘,检查修整质量和符合程度。
3.2 终次修整终次修整是指在零部件装配完成后,对其边缘进行终次修整。
主要包括以下几个步骤:•精加工:利用高精度机械加工设备,对零部件的边缘进行精细加工,以提高零部件的装配精度和表面质量。
•研磨和抛光:通过研磨和抛光等工艺,对零部件的边缘进行表面处理,以提高其表面光洁度和耐腐蚀性。
•检验和修复:对修整后的边缘进行检验,确保其满足设计要求,如有不合格,则进行修复处理。
3.3 检验和验收在边缘加工完成后,对零部件进行检验和验收。
主要包括以下几个方面:•尺寸和形状:利用测量工具检查零部件边缘的尺寸和形状是否符合设计要求。
•表面质量:通过目视或触摸等方式检查零部件边缘的表面质量,如有明显缺陷则需进行修复。
•密封性和连接性:对零部件的边缘进行密封性和连接性测试,确保其满足船舶的结构要求和功能要求。
4. 船舶建造工艺边缘加工的关键问题和技术要点4.1 加工工艺选择根据不同的零部件和材料特性,选择适合的加工工艺和工具。
船舶建造工艺课件-09边缘加工
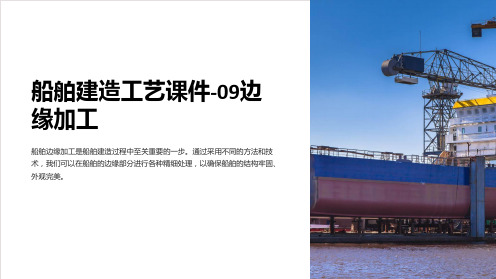
结论和要点
1 边缘加工是船舶建造 2 常见的边缘加工方法 3 边缘加工的关键步骤
过程中不可或缺的一
包括剪切、折弯、焊
包括预处理、加工和
环。
接和铣削等。
收尾。
4 质量控制包括尺寸精度、强度检测
和外观质量。
5 边缘加工广泛应用于船舶制造业和
金属加工行业。
2 强度检测
对焊接点和加工过的边缘 进行强度测试,确保船舶无缺陷程度,确保外 观质量优良。
边缘加工的应用领域
船舶制造业
边缘加工在船舶制造过程中起着重要作用,涉及船 体结构、船舶设备等各个方面。
金属加工行业
边缘加工技术广泛应用于金属制造、焊接和加工行 业,用于加工各种金属制品。
边缘加工的常见方法
剪切
采用切割工具对材料进行剪切,以确定船舶边 缘的形状和尺寸。
焊接
使用焊接技术将船舶的边缘部分连接起来,提 高结构的牢固性。
折弯
通过对材料施加外力使其发生弯曲,实现船舶 边缘的成型。
铣削
通过铣床等机械设备对船舶边缘进行修整和加 工,以确保板材的平整度和尺寸精度。
边缘加工的关键步骤
船舶建造工艺课件-09边 缘加工
船舶边缘加工是船舶建造过程中至关重要的一步。通过采用不同的方法和技 术,我们可以在船舶的边缘部分进行各种精细处理,以确保船舶的结构牢固、 外观完美。
边缘加工的定义和意义
边缘加工是指对船舶结构边缘部分进行各种加工和处理的过程。它的目的是增强船舶的结构强度,提高外观质 量,并确保船舶能够适应各种海上环境和工作条件。
1
预处理
在进行边缘加工之前,需要对船舶结构进行清理和表面处理,以确保加工质量。
2
加工
根据设计要求和边缘加工方法,对船舶边缘进行剪切、折弯、焊接、铣削等操作。
船舶建造工艺课件(PPT 28页)
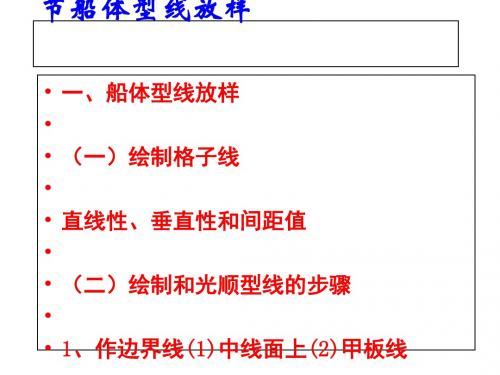
型线修正的原则(1)
• 归纳起来有这样几点
• 型线修改时,要保证原型线所围的体 积不变,以免影响舱室和排水体积。 特别是▽对各项性能有一定的影响
• 型值的修正量水上与水下应区别对待
• 修改点和改动量应尽量少
型线修正的原则(2)
对下列部位的型值原则上不能改动
• 表示主尺度的型值(有关几何体积和技 术性能)
肋骨型线图
O
R'8
R8
R9 R10 R11
R’9 R’10
(轴壳部位)
A-A’斜剖面
A
R’11
O 轴中心线 O8 R8
B
O9 R9
O10 R10
O11 R11
O12 O'
肋距 L
A
#7
#8
#9
#10
#11
#12
修改前后的尾轴出口处肋骨型线比对图
#7 #8 #9
#10
#11
O
#12
肋骨型线图 (轴壳部位)
作外板接缝线
• 外板接缝的排列布置是在已放出结构 线的肋骨型线图上进行的
• 龙骨板、舷顶列板和舭列板在强度中 的作用 ,其宽度在设计中已规定, 可先确定这些板的位置
外板接缝线的布置原则
• 充分利用原材料 纵缝线尽可能与肋骨线正交,使 展开后的外板形状近似为矩形
• 便于外板的加工 考虑加工的可行性,一块外板上 的曲度变化不要过大;对弯曲严重或双向曲度的 外板,可将钢板的长度或宽度减少。
• 双向曲度板在几何上属不可展曲面,只能采用 近似的方法进行展开
• 近似展开的原理可以借助于微分学的概念来理 解
展开的基本原理
• 当n→∞时,正n边形趋近于圆 • 将一个曲面分为若干小曲面,当小曲
船舶建造工艺课件(PPT 28页)

一 船体结构线放样概述
船体结构线放样定义
依据肋骨型线图、外板展开图和结构图提供的信息,绘 出全部船体结构的理论线
船体结构
船体外板
横缝(一般//肋骨剖面) 纵缝
甲板(同外板) 内部构件
横向—横梁、横舱壁、肋骨、肋板等 纵向—纵桁(骨)、纵舱壁等
横201向9/构8/1件1 在肋骨型线图上形状和位置船已舶建定造工艺
• 三者是矛盾的也是统一的
• 型线修正的目的就是要解决型线光顺 和型值吻合这一矛盾,使光顺性、协 调型和一致投影性的到统一,使型线 图能正确表达船体表面的真实形状
型线修正的原则(1)
• 归纳起来有这样几点
• 型线修改时,要保证原型线所围的体 积不变,以免影响舱室和排水体积。 特别是▽对各项性能有一定的影响
二、 绘制肋骨型线图
• 理论型线图放样只解决了船体外表面 光顺的问题,与指导施工有很大差距
• 每档肋位上构件依据肋骨剖面的形状 进行加工,因此须作出肋骨型线图, 也称为施工型线图
• 决定船体肋骨剖面形状、构件的布置 • 外板接缝线排列和展开的重要依据 • 样板,样箱的制作依据
1、肋骨线放样
• 肋骨型线的性质与理论站线一样
始凸(起2)处尾的轴原中肋心骨线线布置位置和布置形式 ((33) )在 开横 始剖 凸线 起图 的上 肋, 骨斜 号剖线应贯穿整个轴壳
板 (4)出口处船尾舶建轴造半工艺径
圆弧型双尾鳍肋骨型线放样
• 保证轴壳纵向和横向与船体曲面光顺过渡 • 轴壳在相应肋骨处的圆弧半径、用轴心作圆 • 用反圆弧将其与肋骨线光顺连接
• 双尾鳍—圆弧形状,非圆弧形状(较多)
2.肋骨型线放样
2019/8/11
船舶建造工艺
船舶工艺.ppt
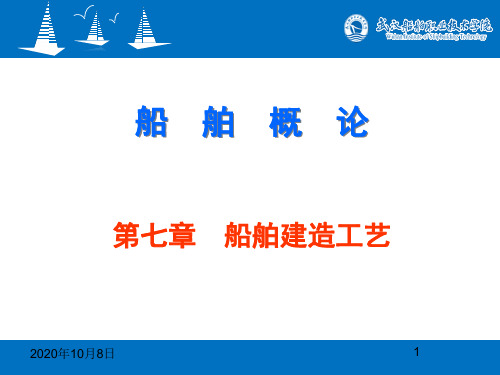
(1)船体结构预装焊:预制部件、分(总)段的工艺过程。
① 部件装焊:将单个零件经过一次或多次装焊组合成各种部 件或组合件的工艺过程,也称为小合拢。
张 远
② 分段装焊:将零、部件装焊成分段或将分段装焊成大型分 段或总段的工艺过程,也称为中合拢。
双
(2)船台(或坞)装焊:在船台(或船坞)将少量散装零、部件
双
上绘制外板的边、端接缝线。
14
船
4)构件展开
舶
那些在投影图上不能表示出真实形状的空间曲面构件的实形求出,
概 并摊开在平面上的过程。
论
7
6
上纵缝线
5
1
2
O7
4
O6 O5
3
2 O1
O2
张 7'
远
6' 5'
双
4' 3'
2'
1'
O4
O3 O2 O1
1 测地线 (准线)
1'
2'
3
O3
3'
4 O4
4'
上纵缝线
船舶涂装除了船体防腐外,还有外表装饰和防污等作用。
四)船舶下水
将船舶从船台上(或船坞里)移到水中去的工艺过程。船舶下
张
水有三类方法:
远 双
1、重力式下水
2、机械化下水
3、漂浮下水
7
五)船舶试验
船
1、系泊试验
舶
在船舶基本竣工时,将船系在码头上对主机、辅机及各种设
概
备和系统进行试验,以检查船舶的完整性和可靠性。
(1)实尺放样:按1:1的比例进行的放样。
张
(2)比例放样:按1:5或1:10等缩小比例,在特制的台面(放
讲课七-构件的边缘加工
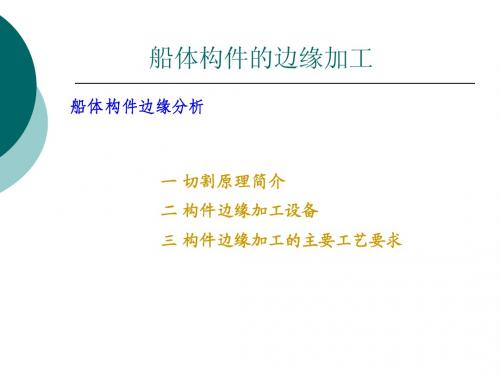
门式自动气割机(multiple-torch automatic gas cutting
machine) (photo-electric tracing gas cutting machine) 数控切割机(N.C. flame-cutting machine)
光电跟踪切割机
3.刨边设 刨边设 备
刨边机(edge planer) 铣边机(edge miller)
一 切割原理简介
1.机械剪切过程 机械剪切过程 2.气割过程(gas cutting) 气割过程( 气割过程 ) 3.等离子切割 等离子切割
采用具有较强导电能力、 采用具有较强导电能力、能受电场和磁场作用的处于完全 电离状态的气体(等离子体——由带电的离子所组成, ——由带电的离子所组成 电离状态的气体(等离子体——由带电的离子所组成,整体却 保持电中性),通过设定装置,获得流速达300~1500m/s、 ),通过设定装置 保持电中性),通过设定装置,获得流速达 、 温度达15000~33000摄氏度的高速高温等离子弧及其焰流, 摄氏度的高速高温等离子弧及其焰流, 温度达 摄氏度的高速高温等离子弧及其焰流 将割缝处的金属熔化、蒸发并吹离基体, 将割缝处的金属熔化、蒸发并吹离基体,随着割嘴的移动而形 成割缝。 成割缝。
flamecuttingmachine刨边机edgeplaner铣边机edgemiller剪切工艺要求1剪切前应根据构件尺度和边缘特征选择合适的剪切机床核对机床的工作能力是否满足所剪材料的要求2根据构件厚度调整上下刀片的间隙使其在整个刀片长度内保持一致3一张钢板上排列多个构件时根据排列情况预先确定剪切顺序以便顺利地进行操作4剪切时应使构件的剪切线与上下刀口边缘严格对准保证剪切边缘不发生偏差5加工后构件的剪断位置与划线位置的偏移应不超过10mm断面不垂直度应不超过5气割工艺要求1根据构件的厚度选择合适的割嘴2切割薄板时割嘴宜后倾3045切割厚板时割嘴宜前倾10203为减少构件切割热变形操作中应按下述切割顺序操作
船舶建造工艺课件09边缘加工
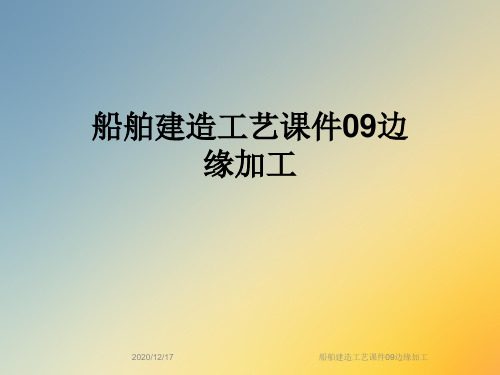
n 乙炔的特点是火焰集中、温度高、预热时间短, 起割快,具有一定的切割速度
n 乙炔爆炸极限较宽
液化石油气做为燃气
n 在常温下的液化压力较低,便于贮存、运输 和管理
n 在气割过程中没有污水和废渣产生,回火和 爆炸的可能性很小,使用安全
n 切割出的割缝切口光洁、棱角整齐,而且很 少粘渣,在中、厚板中更为突出
n 气割过程中上层金属燃烧放热对下层预热 的作用十分重要
n 金属燃烧放出的热量是预热被割金属的主 要热源
金属燃烧应是放热反应
n 金属的燃烧是吸热反应,可能造成割 缝中未燃烧金属预热不足
n 预热达不到金属的燃点,气割过程就 会中断
n 此时要使气割过程连续进行,需要消 耗更多的热能预热金属,用以维持金 属的燃点温度
n 使氧化物熔点升高;妨碍金属燃烧;使割缝 处金属性能变坏、引起裂纹等等
n 含C>0.7%的钢,必须预热到400℃~ 700℃ 时才能进行气割,否则会在割缝表面产生淬 化组织,甚至出现裂纹
n 钢中含硫量超过1%~1.2%时,就不能进行气 割
(二) 气割工艺过程
1. 气割过程常用的燃气
n 气割中常用的燃气主要是乙炔(C2H2)和液化石油气 (以丙烷C3H8为主,含有一定的丁烷C4H10和烯烃等 成分)
压力剪切机上下刀刃的夹角取为9°~ 12° 上下剪刀平面之间的间隙S在所剪板材厚度的2
%~7%的范围内调整
压力剪床的种类
根据剪刀装置的方向,压力剪切机分纵向 和横向两种
横向式压力剪切机如图所示
• 喉深为600~1000mm
• 板材剪切的宽度受到 喉深的限制
• 纵向式压力剪切机无 喉深的限制
船舶建造工艺课件(PPT28张)

展开的基本原理
• 当n→∞时,正n边形趋近于圆 • 将一个曲面分为若干小曲面,当小曲 面足够小时,小曲面可用小平面代替 • 所有小平面在同一平面内拼接,即可 得到近似的曲面展开图 • 双曲度外板的近似展开,将一张外板 划分为许多小块曲面,将这些小块曲 面当作平面或单向曲度面进行展开 • 展开方法有很多,但基本思想一样
#8 #9 #10
A' R’9 R’10 R'8 O R8 R9 R10 R11 肋骨型线图 (轴壳部位) R'8
#11
#12
R’11
R’9
R’10
A-A’斜剖面
A
R’11
O
轴中心线
O8 R8
O9 R9
O10
O11
O12 R11
O'
B
R10
肋距 L
A
#7 #8 #9 #10 #11 #12
修改前后的尾轴出口处肋骨型线比对图
• 船体型线放样与构件放样结束后,应 编制完工型值表,包括 理论型线型值表 肋骨型线型值表 结构线和板缝线型值
第三节 船体构件的展开
• 肋骨型线图,又称施工型线图 • 船体构件在肋骨型线图的表达形式分 为两类 构件的投影反映其真实形状 构件的投影不反映其真实形状
船体型线图的投影关系
构不 件投 在影 肋反 骨映 型其 线真 图实 上形 的状
• 绘制时根据设计绘出的实际肋骨间距 和横向构件沿船长分布的位置 • 在型线图做出一组理论横剖面平行的 剖切面,并将其与船体表面的交线投 到横剖线图上,即得肋骨型线图
肋骨线放样
• 肋骨型线放样涉及到尾轴出口处肋骨 型线修正问题,此处外板光顺性被破 坏,对强度、水动力性能及工艺性都 有影响
船体建造工艺讲座PPT课件

所需的实际形状。 1)板材加工
-冷加工 用于加工单向曲度的板 水(油)压机、三星辊等
-热加工 用于加工曲度很大的双曲度板 需要制作压模,周期长、成本高
-水火弯板 用于加工曲度较小的双曲度板 利用热胀冷缩产生的内应力是钢板产生变形, 成本低,对施工人员要求较高
第24页/共34页
船体建造工艺
第25页/共34页
第19页/共34页
船体建造工艺
第20页/共34页
第21页/共34页
船体建造工艺
激光切割 优点:-能量密度高、热量输入低、热 影响区小、易于控制 是未来造船钢板切割的发展方向
水射流切割 分为--纯水射流切割 --添加磨料的水射流切割
第22页/共34页
船体建造工艺
*机械剪切和冲裁 由于剪切和冲裁边缘受到外力作用产生塑
造船工艺
一、以前-1、船体建造工艺 2、舾装工艺
第1页/共34页
造船工艺
二、现在-1、船体建造工艺 2、舾装工艺 3、涂装工艺
理由:1、自进入20世纪70年代以来,由于船 舶大型化导致涂装工程大量增加 2、质量要求不断提高 3、涂装技术得到迅速发展 涂装作业从舾装作业中分离开来
- 1、下载文档前请自行甄别文档内容的完整性,平台不提供额外的编辑、内容补充、找答案等附加服务。
- 2、"仅部分预览"的文档,不可在线预览部分如存在完整性等问题,可反馈申请退款(可完整预览的文档不适用该条件!)。
- 3、如文档侵犯您的权益,请联系客服反馈,我们会尽快为您处理(人工客服工作时间:9:00-18:30)。
(4) 金属的导热率不应过高
气割过程中这一点必须满足 金属导热率过高,金属切割处的热量 将因金属本身的传导而迅速散失 切割处温度很快低于燃点,使切割过 程不能开始或者中断 即使切割过程能够进行,也会导致割 缝过大
剪刀刀口间隙调整曲线
斜刃龙门剪床剪板刀片
斜刃龙门剪床的剪板刀片较长,为1.5~8.3m 剪刀的后角γ 为2°~ 3° 剪床的下剪刀固定,上剪刀经由离合器与剪床的 运动部分相连
斜刃龙门剪床工作过程(1)
剪切操作时合上离合器,上剪刀做一次下 剪动作 完成一次剪切后,上剪刀回到原来位置, 离合器自行脱开,工作部分停止运动 保证安全操作 有充分的时间进行下一次剪切的准备工作, 有利于提高剪切质量 剪刀每分钟行程次数为5~45次 剪切板厚可达20~50mm
气割形成的氧化物熔点低、流动性好,便容 易被高速氧气流吹除 若氧化物熔点高于金属的熔点,则氧化物 不可能以液体状态从切割处排除 氧化物薄膜附着在割缝金属表面产生粘渣 现象,从而妨碍切割过程的进行 铜、铝等金属不符合这个条件,一般不能 用气割的方法进行切割
(3)金属在氧气中燃烧是放热反应 且能放出较多的热量
含碳量对黑色金属燃点和熔点的影响
由铁碳合金相图可知,黑色金属的含碳量 对其燃点和熔点的影响很大
铁碳合金随含碳量的增加,熔点降低、燃 点升高 含碳量达到0.7%时,铁碳合金的熔点与燃 点相同 一般含碳量小于0.7%的黑色金属都能满足 气割过程是燃烧过程的要求
(2)氧化物熔点应低于金属的熔点 并且具有良好的流动性
压力剪床的种类
根据剪刀装置的方向,压力剪切机分纵向 和横向两种 横向式压力剪切机如图所示
• 喉深为600~1000mm • 板材剪切的宽度受到 喉深的限制 • 纵向式压力剪切机无 喉深的限制 • 可冲剪金属板材和剪 切角钢等型材
纵向式压力剪切机示意图
3. 圆盘剪切机
厚度较小,具有任意曲线边缘的船体构件, 可用圆盘剪切机进行剪切 圆盘剪切机的工作部分如图所示
3Fe+2O2→ Fe3O4+ 1.117×106 J/mol 从气割过程的特点可知,只有满足一定条 件的金属才能被气割
(1)被割金属的燃点必须低于其熔点
气割能正常进行的基本条件,因为气割 的实质是金属在氧气中的燃烧 如果被割金属的燃点高于其熔点,那么 金属尚未达到燃点就已熔化,切割过程 不是燃烧过程而只是熔化过程 气割方法所提供的热能大大低于物理切 割法,因此难以得到光滑平整的割缝 低碳钢和低合金钢都属于燃点低于熔点 的金属,都具有良好的气割性能
射割炬
预热氧气经喷射管由细小喷射孔射出 在射孔周围造成一个负压区,将聚积在该区的低压 乙炔吸出 氧和乙炔在混合室以一定比例混合,从割嘴喷出以 维持预热火焰的燃烧 切割氧气用来加速金属的燃烧
(2) 半自动气割机
由三部分组成 切割部分(包括割 嘴、气体管路及 调节装置等) 动力部分(行走电 动机和减速装置 等)
液化石油气做为燃气
在常温下的液化压力较低,便于贮存、运输 和管理 在气割过程中没有污水和废渣产生,回火和 爆炸的可能性很小,使用安全 切割出的割缝切口光洁、棱角整齐,而且很 少粘渣,在中、厚板中更为突出 液化石油气的比重大于空气,在低洼处容易 堆积发生危险 丙烷气的火焰大、分布宽,对钢板的预热时 间长,耗氧量大
ห้องสมุดไป่ตู้
在气割过程中,预热焰的热量约占总热量 30%,金属燃烧产生的热量约占70% 排除氧化物带走一部分热量,大部分热量 用来预热金属并保持切口的温度 气割过程中上层金属燃烧放热对下层预热 的作用十分重要 金属燃烧放出的热量是预热被割金属的主 要热源
金属燃烧应是放热反应
金属的燃烧是吸热反应,可能造成割 缝中未燃烧金属预热不足
• 辅助设备(直线轨道和割圆圆规等) • 气割机由电动机驱动,沿直线轨道做匀速 运动而实现构件直线边缘的切割
半自动气割机性能
割嘴可以倾斜一定角度切割V型或X型焊接 坡口 小车行走速度就是切割速度,可以在50~ 750mm/min的范围进行无极调速 切割钢板的厚度为5~60mm 切割圆弧的直径为200~2000mm 割缝光洁,切割精度高 与自动切割机比,具有设备简单、移动方 便、操作容易以及适应性强、投资少、易 于扩大施工面等优点
气割的过程
借助高速氧气流的动 能将燃烧生成的熔渣 (即金属氧化物)迅速 吹除掉 连续不断地进行上述 过程,从而在被割金 属上形成一条割缝将 金属分开,达到切割 的目的
铁在纯氧中燃烧的化学反应式
2Fe+ O2→2FeO + 5.380×105 J/mol
4Fe+3O2→2Fe2O3+ 1.660×106 J/mol
4. 剪切加工的主要工艺要求
根据构件尺度和边缘特征选择合适的剪切机床, 核对机床的工作能力是否满足所剪材料的要求 根据构件厚度调整上下刀片的间隙,使其在整 个刀片长度内保持一致
一张钢板上排列多个构件时,根据排列情况预 先确定剪切顺序,以便顺利地进行操作
剪切时,应使构件的剪切线与上下刀口边缘严 格对准,保证剪切边缘不发生偏差 加工后,构件的剪断位置与划线位置的偏移应 不超过1.0mm,断面不垂直度应不超过5°
剪切后的断面
剪切边缘有两个明显区域 窄面亮的条带区(相当于塑性变形阶段) 较宽面无光的断裂条带区 在条带区附近纤维受挤部分是机座剪切所 造成的硬化区
(二)机械剪切加工工艺
船体构件的边缘有直线和曲线之分,加工 所用的机械设备和方法也有不同 直边构件:加工车床主要有斜刃龙门剪床 和压力剪切机(或联合冲剪机)两种 斜刃龙门剪床是剪切长直边工件的专用 设备,对中、薄板较为适宜 压力剪切机用于短直线的剪切,加工长 直线或缓曲线时,质量较差且操作复杂 曲线边缘:加工车床主要是圆盘剪切机, 应用较少
机械剪切的实质 在超过材料极限强度的剪切力作用下,被 加工金属受挤压而发生剪切变形和断裂的 过程 这一过程大致分为三个连续发生的阶段 弹性变形阶段 塑性变形阶段 断裂阶段
剪切过程的三个阶段
弹性变形阶段 剪切开始时上剪刃下压至被加工构件 构件在剪切力的作用下发生弹性变形 内应力低于材料的屈服极限 塑性变形阶段 上剪刃继续下压,使被加工构件的内应力 超过屈服点并继续上升 直到相当于材料抗剪强度的最大值 构件在剪力作用下发生塑性的剪切变形
2. 压力剪切机
常用的压力剪切机为剪切和冲孔两用的联合机 床,可剪切板材和型材也可进行冲孔作业 剪切机的刀片较短,在300~600mm的范围内 刀片实际有效的工作长度为250~300mm,适宜 于剪切短直线 剪切较长直线及曲度较小的外弯曲线,剪切的 质量不理想 压力剪切机上下刀刃的夹角取为9°~ 12° 上下剪刀平面之间的间隙S在所剪板材厚度的2 %~7%的范围内调整
1. 斜刃龙门剪床
图示为斜刃龙门剪床工作部分 剪切板材时,上剪刀不断做上下往复运动, 剪切范围为图中平行四边形ABCD
上下剪刀之间的夹角
剪床的功率与四边形面积ABCD成正比
增大剪床上下剪刀间的夹角可使四边形 面积减小,从而降低剪切所需的功率
• 过大时,斜剪刃所产生的水平分力
第二节 船体构件的边缘加工
船体构件的边缘加工主要是指零件的边缘 切割和焊接坡口加工
船体构件有直线边缘和曲线边缘之分,加 工所用的机械设备和方法也有不同 边缘加工的方法有
机械切割法(剪切、冲孔、刨边和铣边)
化学切割法(氧乙炔气割和氧丙烷气割)
物理切割法(等离子切割和激光切割)
一、机械剪切法
(一)机械剪切原理
• 剪刀由两个锥 形圆盘组成 • 轴线平行安装 (图a)) • 轴线倾斜安装 (图b))
圆盘剪切机的应用
上刀盘为主动盘,下刀盘为从动盘 剪刀刃口的重叠值h为板厚的1/5~1/3 两个剪刃重叠的弧线很短,所以可用转 动被加工构件的方式剪裁曲线轮廓 这在斜装的剪床上尤为方便 这种剪床操作复杂、劳动强度大,在船 体构件的边缘加工中应用较少 主要用于薄板和有色金属构件的曲线边 缘切割
会使板材移动,给剪切操作带来不便
• 上下剪刃夹角在1.5°~ 5°范围取值
斜口刀刃的剪角
值根据所剪材料
的硬度确定 在保证刀刃强度的情 况下 剪切硬或中等硬度材 料时,为75°~85° 软质金属其值约为 65°~ 70° • 为便于刀刃的调用,也有将其做成90°
剪刀平面之间的间隙S
为减少刀刃与剪截 板边的摩擦,有利 于板材分离,上下 刃口间应留有一定 间隙 S值根据所剪板材 的材料和厚度决定 最大不超过板材厚 度的7%
塑性变形阶段 最大剪切变形从剪刀的刃边部分开始,变 形沿滑移面发生 由于上下剪刃间具有一定的间隙,剪切变 形的同时还存在着弯曲和拉伸变形 剪刀挤入被剪金属的深度视材料的硬度和 塑性而定 一般为被剪金属厚度的20%~50% 断裂阶段 随塑性变形增加,沿着滑移面的方向逐渐 形成裂缝并迅速扩大,直到完全脱离→剪 断
(5)金属中不应含有使气割过程 恶化的杂质
气割方法属于化学方法,金属中的有害杂质 会给气割带来不利影响 使氧化物熔点升高;妨碍金属燃烧;使割缝 处金属性能变坏、引起裂纹等等 含C>0.7%的钢,必须预热到400℃~ 700℃ 时才能进行气割,否则会在割缝表面产生淬 化组织,甚至出现裂纹 钢中含硫量超过1%~1.2%时,就不能进行气 割