金工实习典型零件加工工艺过程ppt课件
合集下载
典型零件机械加工工艺过程(共29张PPT)精选

第十八页,共29页。
第十九页,共29页。
接盘(jiē pán)加工工艺规 程卡片
工序号 工种 工 序 内 容
加工简图
设备
1
锻
锻造毛坯
三爪自定心卡盘夹
小端,粗车大端面
2
车 见平,粗车大外圆
至Ø96。
车床
第二十页,共29页。
工序号 工种 工 序 内 容
加工简图
调头夹大端,粗车
小端面保证总长52,
3
第三页,共29页。
传动轴工艺规程
(guīchéng)卡片
工 序
工 种
工序内容
加工简 图
设 备
1
下 料
圆钢ø60×265
锯 床
车一端面见平;调 2 车 头,车另一端面保
证总长259。
车 床
3
车
钻一端中心孔;钻 另一端中心孔。
车 床
第四页,共29页。
工工 序种
工序内容
加工简 图
设 备
用尾架顶尖顶住,粗
10
铣
深度比图样规定尺 寸多铣0. 25mm,作
为磨削的余量。
加工简图
设 备
铣 床
11 钳 修研两端中心孔
车 床
第九页,共29页。
工工 序种
工序内容
加工简图
设 备
磨外圆Q,M,并用砂
轮端面靠磨台肩H,1,
12 磨 调头,磨外圆N,尸, 靠磨台肩G。
外 圆 磨 床
13 检
检验
第十页,共29页。
2.中间轴机械加工工艺规程 中间轴的材料(cáiliào)为45号钢,生 产批量为600件,中间轴如下图:
第十三页,共29页。
工序号 工序名称
第十九页,共29页。
接盘(jiē pán)加工工艺规 程卡片
工序号 工种 工 序 内 容
加工简图
设备
1
锻
锻造毛坯
三爪自定心卡盘夹
小端,粗车大端面
2
车 见平,粗车大外圆
至Ø96。
车床
第二十页,共29页。
工序号 工种 工 序 内 容
加工简图
调头夹大端,粗车
小端面保证总长52,
3
第三页,共29页。
传动轴工艺规程
(guīchéng)卡片
工 序
工 种
工序内容
加工简 图
设 备
1
下 料
圆钢ø60×265
锯 床
车一端面见平;调 2 车 头,车另一端面保
证总长259。
车 床
3
车
钻一端中心孔;钻 另一端中心孔。
车 床
第四页,共29页。
工工 序种
工序内容
加工简 图
设 备
用尾架顶尖顶住,粗
10
铣
深度比图样规定尺 寸多铣0. 25mm,作
为磨削的余量。
加工简图
设 备
铣 床
11 钳 修研两端中心孔
车 床
第九页,共29页。
工工 序种
工序内容
加工简图
设 备
磨外圆Q,M,并用砂
轮端面靠磨台肩H,1,
12 磨 调头,磨外圆N,尸, 靠磨台肩G。
外 圆 磨 床
13 检
检验
第十页,共29页。
2.中间轴机械加工工艺规程 中间轴的材料(cáiliào)为45号钢,生 产批量为600件,中间轴如下图:
第十三页,共29页。
工序号 工序名称
《金工实习》课件 《金工实习》第十章PPT

1)顶尖安装 磨削轴类零件的外圆时常用前、后顶尖装夹。其安装方法与车削中顶尖
的安装方法基本相同。
2)卡盘安装 工件较长且只有一端有中心孔时应采用卡盘安装。安装方法与车床的安装方法基本 相同,如下左图所示
3)心轴安装 盘套类空心工件常用心轴安装。心轴的安装与车床的安装方法相同,不同的是磨削 用的心轴精度要求更高些,且多用锥度(锥度为1/5 000~1/7 000)心轴,如下右 图所示。
磨削硬材料时选用软砂轮。
10.3.2 砂轮的种类
为了适应各种加工条件和不同类型的磨削结构,砂轮分为平形砂轮、单面凹形 砂轮、薄片形砂轮、筒形砂轮和双斜边形砂轮等,如图所示。
(a)平形
(b)单面凹形
(c)薄片形
(d)筒形
平形砂轮:主要用于磨外圆、内圆和平面等。 单面凹形砂轮:主要用于磨削内圆和平面等。
纵向进给运动是指工作台带动工件所做的直线往复运动。纵向进给量 是指工件相对 于砂轮沿纵向运动方向上的移动量,单位为mm/r。
4.横向进给运动及横向进给量
横向进给运动是指砂轮沿工件径向上的移动,横向进给量 是指工作台每往复行 程(或单行程)一次,砂轮相对于工件径向移动的距离,单位为mm/r。
10.1.2 磨工的加工范围
1—工件转动变速旋钮;2—工件转动点动按钮; 3—工作头架;4—工作台;5—工作台手动手轮; 6—床身;7—工作台左、右端停留时间调整旋钮;
8—工作台自动及无级调速旋钮; 9—砂轮横向手动手轮;10—砂轮启动按钮; 11—砂轮引进、工件转动、切削液泵启动旋钮; 12—液压油泵启动按钮;13—电器操纵板;14—
1—砂轮横向手动手轮;2—磨头;3—工作台;4— 工作台手动手轮;5—床身;6—工作台自动及无级 调速手柄;7—砂轮自动进给(断续或连续)旋钮; 8—砂轮升降手动手轮;9—砂轮垂向进给微动手柄; 10—总停按钮;11—液压油泵启动按钮;12—砂轮 上升点动按钮;13—砂轮下降点动按钮;14—电磁 吸盘开关;15—电器操纵板;16—切削液泵开关; 17—砂轮高速启动按钮;18—砂轮停止按钮;19— 砂轮低速启动按钮;20—电源指示灯;21—砂轮修 整器;22—砂轮横向自动进给换向推拉手柄;23—
的安装方法基本相同。
2)卡盘安装 工件较长且只有一端有中心孔时应采用卡盘安装。安装方法与车床的安装方法基本 相同,如下左图所示
3)心轴安装 盘套类空心工件常用心轴安装。心轴的安装与车床的安装方法相同,不同的是磨削 用的心轴精度要求更高些,且多用锥度(锥度为1/5 000~1/7 000)心轴,如下右 图所示。
磨削硬材料时选用软砂轮。
10.3.2 砂轮的种类
为了适应各种加工条件和不同类型的磨削结构,砂轮分为平形砂轮、单面凹形 砂轮、薄片形砂轮、筒形砂轮和双斜边形砂轮等,如图所示。
(a)平形
(b)单面凹形
(c)薄片形
(d)筒形
平形砂轮:主要用于磨外圆、内圆和平面等。 单面凹形砂轮:主要用于磨削内圆和平面等。
纵向进给运动是指工作台带动工件所做的直线往复运动。纵向进给量 是指工件相对 于砂轮沿纵向运动方向上的移动量,单位为mm/r。
4.横向进给运动及横向进给量
横向进给运动是指砂轮沿工件径向上的移动,横向进给量 是指工作台每往复行 程(或单行程)一次,砂轮相对于工件径向移动的距离,单位为mm/r。
10.1.2 磨工的加工范围
1—工件转动变速旋钮;2—工件转动点动按钮; 3—工作头架;4—工作台;5—工作台手动手轮; 6—床身;7—工作台左、右端停留时间调整旋钮;
8—工作台自动及无级调速旋钮; 9—砂轮横向手动手轮;10—砂轮启动按钮; 11—砂轮引进、工件转动、切削液泵启动旋钮; 12—液压油泵启动按钮;13—电器操纵板;14—
1—砂轮横向手动手轮;2—磨头;3—工作台;4— 工作台手动手轮;5—床身;6—工作台自动及无级 调速手柄;7—砂轮自动进给(断续或连续)旋钮; 8—砂轮升降手动手轮;9—砂轮垂向进给微动手柄; 10—总停按钮;11—液压油泵启动按钮;12—砂轮 上升点动按钮;13—砂轮下降点动按钮;14—电磁 吸盘开关;15—电器操纵板;16—切削液泵开关; 17—砂轮高速启动按钮;18—砂轮停止按钮;19— 砂轮低速启动按钮;20—电源指示灯;21—砂轮修 整器;22—砂轮横向自动进给换向推拉手柄;23—
金工实习课件

①金属液温度足够高。 ②金属液的化学成分应符合要求。 ③熔化效率高,燃料消耗少。
冲天炉的构造
后炉 前炉 加料系统 送风系统 检测系统
二、炉料及其作用
冲天炉熔化用的炉料包括金属炉料、燃 料和熔剂三部分
金属炉料 燃料 熔剂
三、冲天炉的熔化过程
熔化原理 基本操作过程
(1)平稳地将金属液充满型腔,以得到完整铸件。 (2)除渣,阻止金属液中的杂质和熔渣进入型腔。 (3)控制金属液流入型腔的速度和方向。 (4)调节铸件各部分温度,以补充液态金属在冷 却时的体积收缩。
3、浇注系统
1) 浇注系统的构造
(1)外浇口 (2)直浇口 (3)横浇口 (4)内浇口 ⑴一般不在铸件的重要加工面、定位基准面或特殊 重要部位开浇口。 ⑵使液体金属顺着型壁流动,避免直接冲击砂芯或 砂型的突出部分 ⑶内浇口的形状应考虑清理方便。 ⑷应考虑对铸件凝固顺序的要求。
§5.1.5 刨削加工
1. 刨水平面。 2. 刨垂直面。 3. 刨斜面。
§5.2 拉削与镗削
1. 拉削是在拉床上用拉刀加工工件内、 外表面的方法。 2. 镗削是在镗床、车床或铣床上,用镗 刀或工件旋转作主运动,镗刀或工件作 进给运动,对工件的孔进行的切削加工 方法。
§5.2.1 拉削
1.砂轮的旋转运动、 工件的旋转运动、 工件的轴向往复运动、砂轮的横向进给 运动。 2.磨削安全主要内容 。
§6.1.2 砂轮
1.砂轮的种类。 2.砂轮的安装与维修。
§6.1.3 常用磨削类砂轮
1.万能外圆磨床及其工作。 2.平面磨床及其工作。
《金工实习》课件 《金工实习》第八章PPT 第八章 铣工

2.回转工作台 回转工作台又称转盘、圆形工作台和平分盘等
3.分度头 分度是指在铣削六方、齿轮和花键等工件时,工件每铣过一个面或一个槽之后,转过一个角
度,再铣下一个面或者槽的工作。分度所用的附件为分度头 。
回转工作台
在回转工作台上铣圆弧槽
分度头
8.3.2 工件的安装
铣床上常用的工件安装方法有平口钳安装、压板螺栓安装、V形铁安装和分度头 安装,如图所示。当零件的生产批量大时,可采用专用夹具或组合夹具安装工件。
铣封闭式键槽一般是在立式铣床上用键槽铣刀和立铣刀铣削。
8.5 铣工综合实例
熟悉了铣工的各种工艺方法之后,请同学们尝试加工图 8-14 所示的零件,其材料 为 45 钢。毛坯尺寸为110 mm 80 mm 70 mm 。
该零件的参考加工过程如表
8.6 数控铣床及其加工
8.6.1 数控铣床
1.数控铣床的概述 数控铣床和普通铣床的铣削加工原理是一样的,不同之处就是数控铣床的进
3)圆盘工作台 圆盘工作台主要用于装夹形状比较规则的具有内外圆弧面的零件。
机用虎钳装夹工件
圆盘工作台
3.数控铣床的主要附件 1)数控回转工作台 数控回转工作台与普通铣床的回转工作台相似,所不同的是数控回转工作台是 由伺服系统来驱动的。不仅可以加工简单的直线、斜线和圆弧,还可以加工复杂的 曲面和球类零件。 2)对刀仪 数控铣床上使用的对刀仪与数控车床上使用的基本相同,但是由于铣刀属于 多刃刀具,因此对刀仪除了用来测量刀具基本几何尺寸外,还起着调刀的作用。
8.2.3 铣刀及其安装
铣刀实质上是由几把单刃刀具组成的多刃刀具,它的刀齿分布在圆柱铣刀的外回 转表面或端铣刀的端面上。 1.带孔铣刀
带孔铣刀多用于卧式铣床。常用的带孔铣刀有 :
金工实训金工实训课件.ppt

(2)测量时,最好双手掌握千分尺,左手握住弓架, 用右手旋转活动套筒(图1-11),当螺杆即将接触工 件时,改为旋转棘轮盘,直到棘轮发出“卡”、“卡” 声为止。
(3)读数时,最好不取下进行读数,如需要取下读数 时,应先锁紧螺杆,然后轻轻取下千分尺,防止尺寸
变动。
读数方法如下:
被测工件的尺寸=副尺所指的主 尺上的整数(应为0.5毫米的整 倍数)+主尺中线所指副尺的格 数×0.01
3.3.3常用车刀的刃磨方法
一、砂轮的选择
二、刃磨方法
3.3.4车刀的安装
刀头前刀面朝上;保证刀头部分刃磨的几何角度 安装时的正确(即工作角度与标注角度一致); 刀尖必须装得与车床主轴中心等高车刀伸出刀架 部分的长度一般应小于刀杆厚度的二倍;夹持车 刀的紧固螺栓至少要拧紧两个 。
§3.4工件的安装
2、錾削的起削:
窄槽起錾时将錾子刃口抵紧开槽 部位的边缘
较宽平面起錾时将錾子刃口抵紧 工件的边缘尖角处
3、切削的收尾:
每次錾削至终端10mm左右时为 防止边缘崩裂,应调头錾去残余的 金属。
§2.3 锯削
锯削是指用手锯把材料工件进行分割或切槽等的加工方法。 锯削的操作要点 1、锯条安装齿尖向前,松紧适中。 2、工件装夹牢固,伸出台虎钳口不宜过长,锯缝应尽量靠近装
第一章 金工实习基础知识
§1.1安全生产 安全要求: 1、应虚心听从指导人员的指导,注意听课和
示范; 2、按指定地点工作,不得随便离岗走动,打
闹嬉戏; 3、实习时要穿工作服,女同学要戴工作帽,
长头发要压入帽内,严禁戴手套操作机床,不 准穿拖鞋、凉鞋、高跟鞋进厂;
4、机器设备,未经许可,严禁擅自动手操作。 设备使用前要检查,发现损坏或其它故障应停 止操作并及时报告;
(3)读数时,最好不取下进行读数,如需要取下读数 时,应先锁紧螺杆,然后轻轻取下千分尺,防止尺寸
变动。
读数方法如下:
被测工件的尺寸=副尺所指的主 尺上的整数(应为0.5毫米的整 倍数)+主尺中线所指副尺的格 数×0.01
3.3.3常用车刀的刃磨方法
一、砂轮的选择
二、刃磨方法
3.3.4车刀的安装
刀头前刀面朝上;保证刀头部分刃磨的几何角度 安装时的正确(即工作角度与标注角度一致); 刀尖必须装得与车床主轴中心等高车刀伸出刀架 部分的长度一般应小于刀杆厚度的二倍;夹持车 刀的紧固螺栓至少要拧紧两个 。
§3.4工件的安装
2、錾削的起削:
窄槽起錾时将錾子刃口抵紧开槽 部位的边缘
较宽平面起錾时将錾子刃口抵紧 工件的边缘尖角处
3、切削的收尾:
每次錾削至终端10mm左右时为 防止边缘崩裂,应调头錾去残余的 金属。
§2.3 锯削
锯削是指用手锯把材料工件进行分割或切槽等的加工方法。 锯削的操作要点 1、锯条安装齿尖向前,松紧适中。 2、工件装夹牢固,伸出台虎钳口不宜过长,锯缝应尽量靠近装
第一章 金工实习基础知识
§1.1安全生产 安全要求: 1、应虚心听从指导人员的指导,注意听课和
示范; 2、按指定地点工作,不得随便离岗走动,打
闹嬉戏; 3、实习时要穿工作服,女同学要戴工作帽,
长头发要压入帽内,严禁戴手套操作机床,不 准穿拖鞋、凉鞋、高跟鞋进厂;
4、机器设备,未经许可,严禁擅自动手操作。 设备使用前要检查,发现损坏或其它故障应停 止操作并及时报告;
《金工实习》教学ppt课件—08磨削

式中: d—- 砂轮直径(mm); n—- 砂轮每分钟的转速(r/min)
外圆和平面磨削的磨削速度一般为35m/s左右,内圆磨削速度一般为18~30m/s。
8.2知识准备
8.2.1 概述
8.2.1.2 磨削运动及磨削用量
( 2 ) 圆 周 进 给 运 动 及 进 给 速 度 vw 工件的旋转运动是圆周进给运动。工件外圆相对于砂轮的瞬时速度称为圆周进给速度 vw, 可用下式计算: S
8.2.3.1 砂轮的特性
表示砂轮的特性主要包括磨料、粒度、硬度、 结合剂、组织、形状和尺寸等。
图8-11 砂轮的组成
1—磨粒;2一结合剂;3—过渡表面; 4—空隙;5—待加工表面;6—砂轮;
7— 已加工表面;8—工件
8.2知识准备
8.2.3 砂轮8.2.3 Nhomakorabea1 砂轮的特性
(1)磨料
磨料是砂轮的主要成分,直接担负着切削工作。磨料在磨削过程中承受着强烈的挤 压力扩高温的作用,所以必须硬度高、耐热性好,还必须有锋利的棱边和一定的强 度。用于制造砂轮的磨料有刚玉类、碳化硅类和超硬磨料。常用磨料代号、特点及 适用范围如表8-2所示。
棕黑色,硬度仅次于人造金刚石,韧 度较人造金刚石好
磨削硬质合金、光学玻璃、宝石 磨削高性能高速钢,耐热钢、不锈钢
8.2知识准备
8.2.3 砂轮
8.2.3.1 砂轮的特性
(2)粒度
粒度是指磨料颗粒的大小,分为磨粒与微粉两种。磨粒用筛选法分类,它的粒度号指每 平方英寸筛网范围内的筛孔数。
粒度号越大,磨粒越细;当磨粒的直径小于40um 时,称为微粉,微粉号以磨料的实际尺 寸来表示。
w60、w50、w40、w28、w20、w14、w10、w7、w5、 w3.5、w2.5、w1.5、w1、w0.5
外圆和平面磨削的磨削速度一般为35m/s左右,内圆磨削速度一般为18~30m/s。
8.2知识准备
8.2.1 概述
8.2.1.2 磨削运动及磨削用量
( 2 ) 圆 周 进 给 运 动 及 进 给 速 度 vw 工件的旋转运动是圆周进给运动。工件外圆相对于砂轮的瞬时速度称为圆周进给速度 vw, 可用下式计算: S
8.2.3.1 砂轮的特性
表示砂轮的特性主要包括磨料、粒度、硬度、 结合剂、组织、形状和尺寸等。
图8-11 砂轮的组成
1—磨粒;2一结合剂;3—过渡表面; 4—空隙;5—待加工表面;6—砂轮;
7— 已加工表面;8—工件
8.2知识准备
8.2.3 砂轮8.2.3 Nhomakorabea1 砂轮的特性
(1)磨料
磨料是砂轮的主要成分,直接担负着切削工作。磨料在磨削过程中承受着强烈的挤 压力扩高温的作用,所以必须硬度高、耐热性好,还必须有锋利的棱边和一定的强 度。用于制造砂轮的磨料有刚玉类、碳化硅类和超硬磨料。常用磨料代号、特点及 适用范围如表8-2所示。
棕黑色,硬度仅次于人造金刚石,韧 度较人造金刚石好
磨削硬质合金、光学玻璃、宝石 磨削高性能高速钢,耐热钢、不锈钢
8.2知识准备
8.2.3 砂轮
8.2.3.1 砂轮的特性
(2)粒度
粒度是指磨料颗粒的大小,分为磨粒与微粉两种。磨粒用筛选法分类,它的粒度号指每 平方英寸筛网范围内的筛孔数。
粒度号越大,磨粒越细;当磨粒的直径小于40um 时,称为微粉,微粉号以磨料的实际尺 寸来表示。
w60、w50、w40、w28、w20、w14、w10、w7、w5、 w3.5、w2.5、w1.5、w1、w0.5
金工实习--切削加工 ppt课件
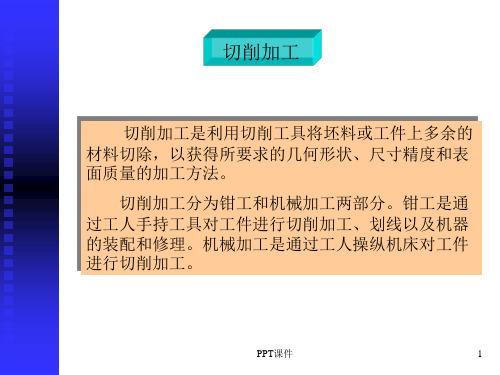
一转,则蜗轮被转二个齿。所以蜗轮蜗杆的传动比
是 i K Z 。因为Z比K大得多,这时传动副的传动可以 得到较大的降速比。蜗轮蜗杆传动的优点是结构紧凑, 传动平稳,噪声小,缺点是效率低。
PPT课件
22
2、机床的传动分析
由机床传动系统图,可以写出主运动链和进给 运动链,然后进行传动分析。 (1)主运动链
动平稳,结构平稳,结构简单,制造方便,适用于二 轴间距较长时用。当加工时,切削用量过大超负荷时, 皮带打滑,不至于造成机器损坏,能起到保护作用, 缺点是由于皮带滑动不能保证正确的传动比。
PPT课件
21
( 3 )蜗轮蜗杆传动:假设蜗杆为主动件,蜗轮为被 动件,蜗杆上螺旋线的头数(K)相当于齿轮的齿数, 蜗轮的齿数为Z,二者传动时,单头蜗杆(K=1)每 转一转,则蜗轮被转一个齿;蜗杆为双头时,蜗杆转
PPT课件
9
(四)机床分类和编号
金属切削机床是机械加工中的主要设备。机床种 类繁多,为了便于设计、制造、使用和管理,必须 进行分类,并赋予各自的型号。
机床分类:
(一)按加工性质和所用刀具分为12 大门类。 我国通用机床分为十二大类,每一类以一个拼音字母来表示,即 B——刨床,C——车床,D——电加工机床,G——切断机床, L——拉床,M——磨床,S——螺纹加工机床,T——镗床,X— —铣床,Y——齿轮加工机床,Z——钻床,Q——其他机床。 (二)按机床工作精度分类:普通机床、精密机床、高精度机床。 (三)按机床加工件大小和机床自身重量分类:仪表机床、中小型 机床、大型机床 10t 、重型机床 30t 、特重型机床 100t 。 (四)按机床通用性分类:通用机床、专门化机床、专用机床、组 合机床。
PPT课件
18
金工实习PPT课件

实习目的
1、初步了解数控机床各部分的结构 2、了解各种数控机床坐标系的判断方法 3、 初步了解数控机床操作过程 4、初步掌握数控机床程序的编写及其
注Hale Waihona Puke 事项01.12.2020金工实习
数控机床概述
——数控机床的介绍
背景 :
随着社会的生产和科学技术的飞速发展,机床制造技 术发生了深刻的变化,机械产品日趋精密复杂,且改型频 繁,尤其是宇航、军事、造船等领域所需的零件,精度要 求高,形状复杂,批量又小。传统的普通机械加工设备已 难以适应市场对产品多样化的需求。为了满足上诉要求, 以数字控制技术为核心的新型数字程序控制机床应运而生。
控机床自动完成。若配合自动装卸手段,则是无
人控制工厂的基本组成环节。数控加工减轻了操
作者的劳动强度,改善了劳动条件;省去了划线、
多次装夹定位、检测等工序及其辅助操作,有效
地提高了生产效率。
01.12.2020
金工实习
(2) 对加工对象的适应性强。改变加工对
象时,除了更换刀具和解决毛坯装夹方式外,只
01.12.2020
金工实习
ZZ XX
XX ZZ
ZZ XX
YY
(a)
(a) 卧式车床;
01.12.2020
(b)
(b) 立式铣床
金工实习
(2)X轴
对于工件旋转的机床,X轴的方向是在工 件的径向上,且平行于横滑座,刀具离开 工件旋转中心的方向为X轴正方向;对于 刀具旋转的立式机床、规定水平方向为X 轴方向,且当从刀具(主轴)向立柱看时, X轴正方向在右边;对于刀具旋转的卧式 机床,规定水平方向仍为X轴方向,且从 刀具(主轴)尾端向工件看时,右手所在 方向为X轴正方向。
1、初步了解数控机床各部分的结构 2、了解各种数控机床坐标系的判断方法 3、 初步了解数控机床操作过程 4、初步掌握数控机床程序的编写及其
注Hale Waihona Puke 事项01.12.2020金工实习
数控机床概述
——数控机床的介绍
背景 :
随着社会的生产和科学技术的飞速发展,机床制造技 术发生了深刻的变化,机械产品日趋精密复杂,且改型频 繁,尤其是宇航、军事、造船等领域所需的零件,精度要 求高,形状复杂,批量又小。传统的普通机械加工设备已 难以适应市场对产品多样化的需求。为了满足上诉要求, 以数字控制技术为核心的新型数字程序控制机床应运而生。
控机床自动完成。若配合自动装卸手段,则是无
人控制工厂的基本组成环节。数控加工减轻了操
作者的劳动强度,改善了劳动条件;省去了划线、
多次装夹定位、检测等工序及其辅助操作,有效
地提高了生产效率。
01.12.2020
金工实习
(2) 对加工对象的适应性强。改变加工对
象时,除了更换刀具和解决毛坯装夹方式外,只
01.12.2020
金工实习
ZZ XX
XX ZZ
ZZ XX
YY
(a)
(a) 卧式车床;
01.12.2020
(b)
(b) 立式铣床
金工实习
(2)X轴
对于工件旋转的机床,X轴的方向是在工 件的径向上,且平行于横滑座,刀具离开 工件旋转中心的方向为X轴正方向;对于 刀具旋转的立式机床、规定水平方向为X 轴方向,且当从刀具(主轴)向立柱看时, X轴正方向在右边;对于刀具旋转的卧式 机床,规定水平方向仍为X轴方向,且从 刀具(主轴)尾端向工件看时,右手所在 方向为X轴正方向。
金工实训最全课件整套ppt完整版教学教程全套电子讲义讲义(最新)

车工实训
❖ 车削台阶
车台阶是车工最基本的操作技能。台阶是由外圆与端面的基本 要素组成,外圆与端面也是各类零件车削基础。首先要掌握外圆 与端面加工的知识及车削,再渐渐掌握车削台阶操作方法。
1.工件的装夹
常用装夹方法 : (1)卡盘装夹。包括 ① 三爪自定心卡盘 ② 四爪单动卡盘 (2)顶尖装夹 。顶尖装夹包括两种方式, 即两顶尖装夹和一夹一顶工件装夹。 (3)其他方式。
vc
nd 1000
d —工件或刀具的最大直径mm; n —主轴转速,r/mm; Vc —切削速度m/min。
图 2-11 切削用量三要素
车工实训
❖ 车刀的基本知识
1.车刀材料应具备的性能
(1)高硬度和良好的耐磨性 (2)足够的强度与冲击韧性
(3)高的耐热性 (4)良好的工艺性和经济性。
2.车刀材料
(a) 车外圆锥
(b)车内圆锥
图2-41 车削内外圆锥示意图
图2-43 用靠模车圆 锥的方法
车工实训
3.圆锥的测量
锥度或斜度的测量方法有多种,选用哪一种测量方法比较适合, 应该根据被检测的对象和要求来确定。
1)用万能角度尺检测 用万能角度尺检测时的测量精度不高,只适用于单件小批量生产。 2)用样板检测 样板是专门制造的测量工具,观察样板和工件侧面中间的透光程度 可判断加工精度。适用批量生产(图2-45 )。 3)用标准锥度量规检测 检测当工件是标准圆锥时,用标准锥度量规来测量。锥度量规由塞 规和套规组成,塞规用来测量锥孔,套规用来测量锥体。(图2-46)
3.清扫 (1)下班前打扫、收拾。 (2)清理擦拭车床、工具箱、门、窗。 (3)扫除垃圾、纸屑、塑料袋等。 (4)将废料、余料等归类清理。
车工实训
金工实习铸锻ppt课件

第一部分 砂型铸造 ❖ 第二部分 锻压
2
第一部分 砂型铸造
❖ 实习目的:
❖
1、了解铸造生产的工艺过程及其特点。
❖
2、了解型砂、型芯砂等造型材料的性能及其制备。
❖
3、了解铸铁的熔炼设备及其熔化过程。
❖
4、了解各种造型方法。并能独立操作中等复杂件。
❖
5、了解模型设计原则。
❖
6、概略了解型砂处理,及造型清理过程、设备
35
第六节 铸造缺陷及其产生原因
▉渣眼:产生的主要原因 (1)浇注时挡渣不良 (2)浇口尺寸不对,挡渣效果差。 (3)浇注时金属液体温度低,渣不易浮起。 渣眼特征:孔内形状不规则,孔内塞满渣。
36
第七节 特种铸造的特点及应用
▉砂型铸造-----§应用广泛; -----§单件,小批量生产,具有设备简单,成
44
锻造
第一节 概述 第二节 金属的加热 第三节 金属加热时易产生的缺陷 第四节 锻件的冷却 第五节 锻造用工具与设备 第六节 自由锻造的基本工序 第七节 《安全操作规程》
小结 复习思考题
45
第一节 概述
什么是锻造:锻造是属于压力加工的一种,它是利用外力 使金属材料产生永久变形,从而获得具有一定形状和尺寸 的毛坯或零件的一种加工方法。
须离开一定距离。两人抬铁水包时要稳,步伐要一致; 七、浇铸前必须烘干铁水包,挡渣棒要预热,贴水面上只能覆
盖干草灰不能用草包等易燃物; 八、浇注速度及流量要掌握适当,浇注时人不能站在铁水正面,
并严禁从冒气口正面观察铁水; 九、发生任何事故时,要保持镇静,服从统一指挥。
38
小结 《安全操作规程》及复习思考题
工艺特点:
▉分模两箱造型---有些铸件最大断面不在端部,若采 取用整模的造型方法就无法将模型起出,在这种情 况下模型沿最大断面分开,使造型方便,整个分型 面形成了平整分型面,但上下型都有型腔,分模造 型操作简便,应用广泛。
2
第一部分 砂型铸造
❖ 实习目的:
❖
1、了解铸造生产的工艺过程及其特点。
❖
2、了解型砂、型芯砂等造型材料的性能及其制备。
❖
3、了解铸铁的熔炼设备及其熔化过程。
❖
4、了解各种造型方法。并能独立操作中等复杂件。
❖
5、了解模型设计原则。
❖
6、概略了解型砂处理,及造型清理过程、设备
35
第六节 铸造缺陷及其产生原因
▉渣眼:产生的主要原因 (1)浇注时挡渣不良 (2)浇口尺寸不对,挡渣效果差。 (3)浇注时金属液体温度低,渣不易浮起。 渣眼特征:孔内形状不规则,孔内塞满渣。
36
第七节 特种铸造的特点及应用
▉砂型铸造-----§应用广泛; -----§单件,小批量生产,具有设备简单,成
44
锻造
第一节 概述 第二节 金属的加热 第三节 金属加热时易产生的缺陷 第四节 锻件的冷却 第五节 锻造用工具与设备 第六节 自由锻造的基本工序 第七节 《安全操作规程》
小结 复习思考题
45
第一节 概述
什么是锻造:锻造是属于压力加工的一种,它是利用外力 使金属材料产生永久变形,从而获得具有一定形状和尺寸 的毛坯或零件的一种加工方法。
须离开一定距离。两人抬铁水包时要稳,步伐要一致; 七、浇铸前必须烘干铁水包,挡渣棒要预热,贴水面上只能覆
盖干草灰不能用草包等易燃物; 八、浇注速度及流量要掌握适当,浇注时人不能站在铁水正面,
并严禁从冒气口正面观察铁水; 九、发生任何事故时,要保持镇静,服从统一指挥。
38
小结 《安全操作规程》及复习思考题
工艺特点:
▉分模两箱造型---有些铸件最大断面不在端部,若采 取用整模的造型方法就无法将模型起出,在这种情 况下模型沿最大断面分开,使造型方便,整个分型 面形成了平整分型面,但上下型都有型腔,分模造 型操作简便,应用广泛。
- 1、下载文档前请自行甄别文档内容的完整性,平台不提供额外的编辑、内容补充、找答案等附加服务。
- 2、"仅部分预览"的文档,不可在线预览部分如存在完整性等问题,可反馈申请退款(可完整预览的文档不适用该条件!)。
- 3、如文档侵犯您的权益,请联系客服反馈,我们会尽快为您处理(人工客服工作时间:9:00-18:30)。
孔,再以轴两端的中心孔为定位精基准 尽可能基准重合、基准统一、互为基准 采用外圆表面定位装夹 采用三爪自定心卡盘、四爪单动卡盘 采用各种堵头或拉杆心轴定位装夹 加工空心轴用带中心孔的堵头或拉杆心轴
11
堵头 拉杆心轴
12
4.轴类零件工艺过程示例
13
CA6140车床主轴的结构特点 既是阶梯轴,又是空心轴;是长径比小
16
CA6140主轴结构的设计要求: 合理的结构设计 足够的刚度 有具有一定的尺寸、形状、位置精度和
表面质量 足够的耐磨性、抗振性及尺寸稳定性 足够的抗疲劳强度
17
CA6140车床主轴技术条件的分析
主轴支承轴颈的技术要求
支承轴颈是主轴的装配基准,其精度直 接影响主轴的回转精度;主轴上各重要 表面又以支承轴颈为设计基准,有严格 的位置要求
毛坯热处理:去锻造应力,细化晶粒 切削前正火(预备热处理):改善切削加
工性能和机械-物理性能;去锻造应力
半精加工前调质:去应力,改善切削加工性
能,提高综合机械性能
精加工前局部高频淬火:提高运动表面耐
磨性
精加工后定性处理:低温时效和冰冷处理 38
加工阶段的划分 如前所述,分为三个阶段。
善其装配工艺性和装配精度 表面粗糙度Ra=0.8~0.2μm
24
CA6140车床主轴图
25
主轴的机械加工工艺过程
主轴加工工艺过程制订的依据 主轴的结构;技术要求;生产批量;
设备条件 主轴加工工艺过程 批量:大批;材料:45钢;毛坯:模
锻件
26
工艺过程: 分为三个阶段(参见表5-5):
主轴的技术要求高,毛坯为模锻件,加 工余量大,精度高,故应分阶段加工
9
轴类零件的热处理 正火或退火处理
锻造毛坯加工前——细化晶粒,消除锻 造应力,降低硬度,改善切削性能 调质 粗车后半精车前——改善物理力学性能 表面淬火 精加工前——提高硬度 低温时效 局部淬火或粗磨后——稳定性能
10
3.轴类零件的安装方式
采用两中心孔定位装夹 以重要外圆表面为粗基准定位加工出中心
表面粗糙度:支承轴颈为Ra0.2~1.6μ m, 配合轴颈为Ra0.4~3.2μ m
其他:热处理、倒角、倒棱、外观修饰 8
2.轴类零件的材料、毛坯及热处理 轴类零件材料 45钢、40Cr、GCr15、65Mn、球墨铸
铁、20CrMnTi、20Mn2B、20Cr 轴类毛坯 圆棒料、锻件、铸件
20
主轴轴端外锥(短锥)的技术要求 用来安装卡盘或花盘的;也是定心表面 对锥面的尺寸精度、形状精度、粗糙度、
接触精度都要求高 轴心线应与支承轴颈同轴 对支承轴颈的径向圆跳动为0.008;端
面圆跳动为0.008 粗糙度 Ra≤1.25μm ,硬度为HRC45~50
21
空套齿轮轴颈的技术要求 影响传动的平稳性;可能导致噪声 有同轴度要求,对支承轴颈的径向圆
支承轴颈为三支承结构,并且跨度大
支承轴颈采用锥面 (1:12) 结构,接触 率≥70%,可用来调整轴承间隙
18
中间支承为IT5~IT6,粗糙度为: Ra≤0.63μm
支承轴颈圆度误差为0.005mm,径向跳 动为0.005mm
其他外圆的圆度要求,误差小于50%尺 寸公差,高精度者为5~10%
跳动为0.01~0.015 尺寸精度要求为IT5~IT6
22
螺纹的技术要求 用来固定零件或调整轴承间隙 螺母的端面圆跳动(应≤0.05)会影响
轴承的内环轴线倾斜 螺母与轴颈的同轴度误差≤0.025 螺纹精度为6h
23
主轴各表面的表面层要求 要有较高的耐磨性 要有适当的硬度(HRC45以上),以改
典型零件加工工艺过程
1
• 轴类 • 箱体类 • 齿轮类
2
一、轴(杆)类零件的加工
3
一、轴(杆)类零件的加工
1.轴类零件的分类、技术要求 轴类零件的作用 支撑传动零件; 承受载荷; 传递扭矩。
4
轴类零件的特点 长度大于直径; 加工表面为内外圆柱面、圆锥面、
螺纹、花键、沟槽等; 有一定的回转精度。
粗加工:工序 1~6 半精加工:工序 7~13(7为预备) 精加工:工序 14~26(14为预备)
27
28
29
30
31
32
33
34
35
36
主轴加工工艺过程分析 主轴毛坯的制造方法 自由锻件:小批量或单件生产 模锻件:大批量生产
37
主轴的材料和热处理 热处理工序的安排
于12的刚性轴 不但传递旋转运动和扭矩,而且是工件
或刀具回转精度的基础
主要加工表面有内外圆柱面、圆锥面, 次要表面有螺纹、花键、沟槽、端面结 合孔等
机械加工工艺主要是车削、磨削,其次 是铣削和钻削
14
特别值得注意的工艺问题有: 1) 定位基准的选择 2) 加工顺序的安排 3) 深孔加工 4) 热处理变形
5
轴类零件的分类 光滑轴 阶梯轴 空心轴 异形轴(曲轴、齿轮轴、偏心轴、
十字轴、凸轮轴、花键轴)
6
常见轴类的类型
7
轴类零件的技术要求
尺寸精度:支承轴颈为IT5~IT7,配合轴 颈为IT6~IT9
几何形状精度:轴颈表面、外圆锥面、 锥孔等的圆度、圆柱度
相互位置精度:同轴度、径向跳动、重 要端面对轴心线垂直度、端面间平行度
轴颈与有关表面的同轴度误差应很小
19
主轴工作表面(锥孔)的技术要求 用来安装顶尖或刀具锥柄:定心表面
对锥面的尺寸精度、形状精ቤተ መጻሕፍቲ ባይዱ、粗糙 度、接触精度都要求高
轴心线应与支承轴颈同轴
锥孔对轴颈的径向圆跳动近轴端为 0.005,离轴端300处为0.01,锥面接 触率≥70%,粗糙度Ra≤0.63μm,硬 度为HRC48~50。
CA6140车床主轴的功用 承受扭转力矩 承受弯曲力矩 保证回转运动精度
15
CA6140车床主轴的设计要求
扭转和弯曲刚度高
回转精度高(径向圆跳动、端面圆跳 动、回转轴线稳定)
制造精度高 1) 结构尺寸及动态特性要好 2) 主轴本身及其轴承精度高 3) 轴承的结构和润滑 4) 齿轮的布置 5) 固定件的平衡等
11
堵头 拉杆心轴
12
4.轴类零件工艺过程示例
13
CA6140车床主轴的结构特点 既是阶梯轴,又是空心轴;是长径比小
16
CA6140主轴结构的设计要求: 合理的结构设计 足够的刚度 有具有一定的尺寸、形状、位置精度和
表面质量 足够的耐磨性、抗振性及尺寸稳定性 足够的抗疲劳强度
17
CA6140车床主轴技术条件的分析
主轴支承轴颈的技术要求
支承轴颈是主轴的装配基准,其精度直 接影响主轴的回转精度;主轴上各重要 表面又以支承轴颈为设计基准,有严格 的位置要求
毛坯热处理:去锻造应力,细化晶粒 切削前正火(预备热处理):改善切削加
工性能和机械-物理性能;去锻造应力
半精加工前调质:去应力,改善切削加工性
能,提高综合机械性能
精加工前局部高频淬火:提高运动表面耐
磨性
精加工后定性处理:低温时效和冰冷处理 38
加工阶段的划分 如前所述,分为三个阶段。
善其装配工艺性和装配精度 表面粗糙度Ra=0.8~0.2μm
24
CA6140车床主轴图
25
主轴的机械加工工艺过程
主轴加工工艺过程制订的依据 主轴的结构;技术要求;生产批量;
设备条件 主轴加工工艺过程 批量:大批;材料:45钢;毛坯:模
锻件
26
工艺过程: 分为三个阶段(参见表5-5):
主轴的技术要求高,毛坯为模锻件,加 工余量大,精度高,故应分阶段加工
9
轴类零件的热处理 正火或退火处理
锻造毛坯加工前——细化晶粒,消除锻 造应力,降低硬度,改善切削性能 调质 粗车后半精车前——改善物理力学性能 表面淬火 精加工前——提高硬度 低温时效 局部淬火或粗磨后——稳定性能
10
3.轴类零件的安装方式
采用两中心孔定位装夹 以重要外圆表面为粗基准定位加工出中心
表面粗糙度:支承轴颈为Ra0.2~1.6μ m, 配合轴颈为Ra0.4~3.2μ m
其他:热处理、倒角、倒棱、外观修饰 8
2.轴类零件的材料、毛坯及热处理 轴类零件材料 45钢、40Cr、GCr15、65Mn、球墨铸
铁、20CrMnTi、20Mn2B、20Cr 轴类毛坯 圆棒料、锻件、铸件
20
主轴轴端外锥(短锥)的技术要求 用来安装卡盘或花盘的;也是定心表面 对锥面的尺寸精度、形状精度、粗糙度、
接触精度都要求高 轴心线应与支承轴颈同轴 对支承轴颈的径向圆跳动为0.008;端
面圆跳动为0.008 粗糙度 Ra≤1.25μm ,硬度为HRC45~50
21
空套齿轮轴颈的技术要求 影响传动的平稳性;可能导致噪声 有同轴度要求,对支承轴颈的径向圆
支承轴颈为三支承结构,并且跨度大
支承轴颈采用锥面 (1:12) 结构,接触 率≥70%,可用来调整轴承间隙
18
中间支承为IT5~IT6,粗糙度为: Ra≤0.63μm
支承轴颈圆度误差为0.005mm,径向跳 动为0.005mm
其他外圆的圆度要求,误差小于50%尺 寸公差,高精度者为5~10%
跳动为0.01~0.015 尺寸精度要求为IT5~IT6
22
螺纹的技术要求 用来固定零件或调整轴承间隙 螺母的端面圆跳动(应≤0.05)会影响
轴承的内环轴线倾斜 螺母与轴颈的同轴度误差≤0.025 螺纹精度为6h
23
主轴各表面的表面层要求 要有较高的耐磨性 要有适当的硬度(HRC45以上),以改
典型零件加工工艺过程
1
• 轴类 • 箱体类 • 齿轮类
2
一、轴(杆)类零件的加工
3
一、轴(杆)类零件的加工
1.轴类零件的分类、技术要求 轴类零件的作用 支撑传动零件; 承受载荷; 传递扭矩。
4
轴类零件的特点 长度大于直径; 加工表面为内外圆柱面、圆锥面、
螺纹、花键、沟槽等; 有一定的回转精度。
粗加工:工序 1~6 半精加工:工序 7~13(7为预备) 精加工:工序 14~26(14为预备)
27
28
29
30
31
32
33
34
35
36
主轴加工工艺过程分析 主轴毛坯的制造方法 自由锻件:小批量或单件生产 模锻件:大批量生产
37
主轴的材料和热处理 热处理工序的安排
于12的刚性轴 不但传递旋转运动和扭矩,而且是工件
或刀具回转精度的基础
主要加工表面有内外圆柱面、圆锥面, 次要表面有螺纹、花键、沟槽、端面结 合孔等
机械加工工艺主要是车削、磨削,其次 是铣削和钻削
14
特别值得注意的工艺问题有: 1) 定位基准的选择 2) 加工顺序的安排 3) 深孔加工 4) 热处理变形
5
轴类零件的分类 光滑轴 阶梯轴 空心轴 异形轴(曲轴、齿轮轴、偏心轴、
十字轴、凸轮轴、花键轴)
6
常见轴类的类型
7
轴类零件的技术要求
尺寸精度:支承轴颈为IT5~IT7,配合轴 颈为IT6~IT9
几何形状精度:轴颈表面、外圆锥面、 锥孔等的圆度、圆柱度
相互位置精度:同轴度、径向跳动、重 要端面对轴心线垂直度、端面间平行度
轴颈与有关表面的同轴度误差应很小
19
主轴工作表面(锥孔)的技术要求 用来安装顶尖或刀具锥柄:定心表面
对锥面的尺寸精度、形状精ቤተ መጻሕፍቲ ባይዱ、粗糙 度、接触精度都要求高
轴心线应与支承轴颈同轴
锥孔对轴颈的径向圆跳动近轴端为 0.005,离轴端300处为0.01,锥面接 触率≥70%,粗糙度Ra≤0.63μm,硬 度为HRC48~50。
CA6140车床主轴的功用 承受扭转力矩 承受弯曲力矩 保证回转运动精度
15
CA6140车床主轴的设计要求
扭转和弯曲刚度高
回转精度高(径向圆跳动、端面圆跳 动、回转轴线稳定)
制造精度高 1) 结构尺寸及动态特性要好 2) 主轴本身及其轴承精度高 3) 轴承的结构和润滑 4) 齿轮的布置 5) 固定件的平衡等