物料需求计划表
物料需求计划(MRP)

即使在产品需求量是均衡的情况下,考虑到 零部件的生产批量以及一种零部件可能用于生 产不同的最终成品,也会使得对零部件的需求 是波动的。波动需求现象意味着订购点法不宜 用于制造业中零部件的库存控制。
计算机提供的数据处理能力,可以迅速地完 成对零部件需求的计算。
MRP的主要思想:
把所有物料分成独立需求和相关需求两种 类型
需求无关的某一物料的需求。 这种独立需求大多是最终产品或维修件 这类需求受市场因素的影响,需求多为随机波动。 独立需求一般根据订单与市场预测来确定---订货点法+预测;
相关需求( Dependent Demand )是指与另一物料或产品需求直
接相关的某一物料的需求。
(2) 如果用订货点法控制零部件和原料库存,会形成“块 状”需求
假设产成品的需求率是均匀的,如果采用订货点方法,使 零件和原材料的需求呈“块状”。 “块状”需求与均匀需求相比,平均库存水平几乎提高一 倍,占用更多的资金。
块状需求示意图
产品 零部件 原材料
解决“块装”问题的办法
相关需求可以从最终 产品的需求量中推算 出来的。 相关需求不是随机的, 其数量和时间是由上 一级物料需求确定的--MRP;
低层代码概念:当一个零件或部件出现在多种产品结构的不同层 次,或者出现在一个产品结构的不同层次上时,该零(部)件就具有 不同的层次码。以它的数字最大的代码为其低层代码。
(3) 库存状态文件
库存状态文件保存了每一种物料的有关数据,产品结 构文件是相对稳定的,而库存状态文件却处于不断变 动之中。
零部件 抽屉
制造业生产中的零部件、原材料的库存管理,与 产品或用于维修服务的零部件库存不同,不能当作
独立项目看待。它们的需求是根据由它们装配而成 的最终成品的需求所决定的,属称相关需求。
物料需求计划

3、现有库存量(POH)
其概念与MPS中的概念相同,指每周需求被满足之后手头仍有的库存量。该记录随着每周 进货或出货的情况而更新,未来各周的POH则可计算的出
4、计划订货入库量 (PR)
含义是,计划订货或生产、但订单尚未发出的订货量。这个量的意义是要保持POH的量不 低于安全库存(在MPS中未考虑安全库存,保持POH非负即可)。对于某些不需要安全库
某办公家具公司,其两种主要产品(即企业要出厂的最终产品)是办公用椅A和B,其需 求大致稳定:产品A每周需30个,产品B每周需20个。这两种产品都需要用到一种支架部
件C。因此,对C的平均需求量是每周50个。A和B的装配期是1周
如右图示,在这种格式中,左上方通常要标出产品名称及其性质(如右图中,表明C是支 架部件),右上方表示计划因子,通常包括三项:生产批量、生产周期和安全库存量。 在本例中,C的批量是230个,生产周期为2周,安全库存量为50个。这些计划因子的量都 需要预先选定。当这些值发生变化以后,管理人员必须及时更新库存记录。下面首先来
存的中间物料,则如同MPS,其意义是要保持POH非负
在库存记录中所表示的PR量应包括这两种情况: 1)在POH出现短缺(或为负值或小于安全库存量)的当周制订一个PR量,其值的大小应是POH大于等于安全库存 2)继续计算其后各周的POH,当又出现短缺时,制订下一个PR量
5、计划发出订货量 (plannedorderreleas
基本计算模式
物料需求计划(MRP)的制定需要三个关键信息:MPS、BOM、库存记录
MPS
主生产计划
BOM
物料清单
库存记录
在MRP的制定过程中,库存记录的计算方法构成了MRP的基本计算模型
计划bom表

计划bom表在制造业中,BOM表(Bill of Materials)是非常重要的一项文档,它记录了产品所需的各种原材料、零部件和组件的清单。
BOM表不仅是生产计划和生产过程中的重要参考依据,也是产品设计、采购和库存管理的基础。
因此,编制一份准确、完整的BOM表对于企业的生产运营至关重要。
首先,BOM表的编制需要明确产品的设计要求和规格参数。
在设计阶段,工程师需要详细了解产品的功能特性,确定各个零部件之间的关联关系,以及各个零部件的规格、尺寸、材料等信息。
这些信息将直接影响到BOM表的编制,因此设计人员需要与BOM表编制人员密切合作,确保BOM表的准确性和完整性。
其次,BOM表的编制还需要考虑到产品的生命周期管理。
随着产品的不断更新换代和改进,BOM表也需要不断进行修订和更新。
因此,在编制BOM表时,需要考虑到产品的版本管理和变更控制,确保BOM表与实际生产的一致性。
同时,还需要与产品设计、工艺工程、采购和供应链等部门进行有效的沟通和协调,及时获取最新的产品信息,以便及时更新BOM表。
另外,BOM表的编制还需要考虑到供应链管理和采购计划。
在编制BOM表时,需要充分考虑到各种原材料、零部件和组件的采购渠道、供应商信息、价格和交货周期等因素,以便为采购部门提供参考依据,帮助其制定合理的采购计划和库存管理策略。
同时,还需要与供应商保持密切的合作关系,及时了解市场变化和供应商的动态,以便调整BOM表和采购计划。
最后,BOM表的编制还需要考虑到生产计划和物料需求计划。
在编制BOM表时,需要充分考虑到生产工艺流程、生产能力和物料需求计划等因素,以便为生产计划部门提供参考依据,帮助其合理安排生产计划和物料供应。
同时,还需要与生产计划部门保持密切的沟通和协调,及时了解生产进度和物料需求情况,以便调整BOM表和生产计划。
综上所述,BOM表的编制是一个复杂而又重要的工作,它需要各个部门之间的密切合作和协调。
只有通过有效的沟通和协作,才能编制出准确、完整的BOM 表,为企业的生产运营提供有力的支持。
第九讲物料需求计划
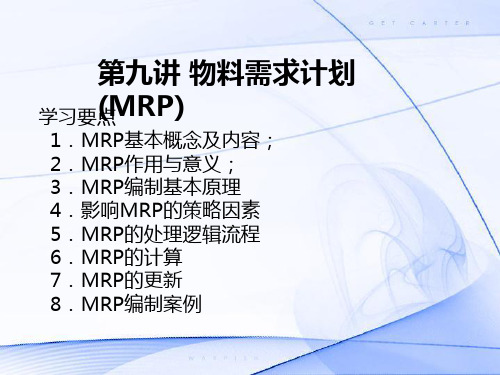
MRP项目
计划周期
1 2 3 4 5 6 25 7 8 30 40 25 40 15 15 30 15 15 30 9 10 11 15 15 30 12 13
X(LT=4) Y(LT=6) 相关需求X-A 相关需求Y-A 独立需求A
A的毛需求
15
40
40
30
15
45
【例题9.3:应用低位码 计算物料的净需求】 已知:MPS为在第8个 计划周期时产出200件A 产品;各物料的计划接 收量和已分配量为0; 物料ABCD期初库存分别 为0、120、60、70件, 安全库存量为0;物料 ABCD批量规则为直接批 量法。求物料ABCD的净 需求。
毛需求计算考虑因素
• • • • •
是否存在独立需求 是否共用物料 是否低位码 是否是计划BOM 是否存在替代
如果存在替代,要不要替代则考虑: • 是否可以降低工作量 • 是否可以降低成本 • 客户是否满意 • 近期是否短缺
(3)计算净需求量。 考虑安全库存推算特定时段的净需求量。 当PAB初值≥安全库存时,净需求=0 当PAB初值<安全库存时,净需求=安全库存- PAB初值
生产什么? MPS
主生产计划
2
(物料清单) 用到什么?
产品信息
4 物料需求计划 MRP
已有什么? (物料可用量)
3 库存信息
买什么?
采购计划
做什么?
生产计划
MRP 回答了
问
4 个制造业的主要问题
答
(生产什么 1 生产什么?
2 用到什么? 3 已有什么?
+
用到什么) - 已有什么 1 主生产计划( MPS) = 还缺什么
(二)MRP中的输出数据项 1.采购订单 采购什么? 采购多少? 何时开始采购? 何时完成采购? 2.制造订单 制造什么? 制造多少? 何时开始制造? 何时完成制造?
第十一章ERP之物料需求计划
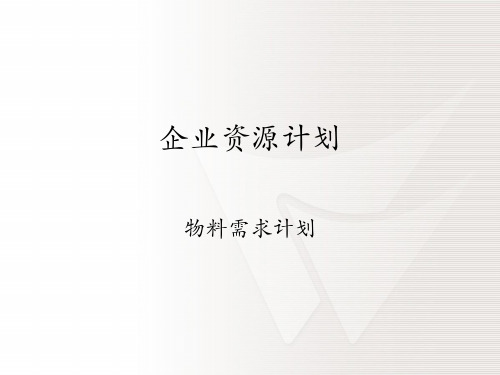
X(LT=4)
Y(LT=6)
A(1)
B(1)
A(1)
产品X、Y的BOM图(物料X的需求关系〕
C(1)
物料A的毛需求计算表
周
1 2 3 4 5 6 7 8 9 10 11 12 13
2.独立需求
当一个项目的需求不能直接从另一个项目的需求计划得到时 ,这种需求称为独立需求;否则,为相关需求。 ➢ 独立需求与相关需求的概念是相对的。例如,若生产园
珠笔,则笔的需求是独立需求,其需求数量是由预测 得 到的,而对构成笔的笔芯和弹簧之类的项目而言便是相 关需求。其需求数量是通过计划 得到的。但是,若想单 独销售笔芯,则笔芯又是独立需求。 ➢ 在编制物料需求计划时,必须认真地分析与收集独立需 求与相关需求。
5.其它因素
(1)低阶码(low level code,LLC)
➢ 低阶码,又称层次码或低层码,是系统分配给物料清单 上的每个物品一个从0至N的数字码。在产品BOM结构 中,最上层的层级码为0,下一层部件的层级码则为l, 依此类推。
➢ 一个物品只能有一个MRP低阶码,当一个物品在多个产 品中所处的产品结构层次不同或即使处于同一产品结构 中但却处于不同产品结构层次时,则取处在最低层的层 级码作为该物品的低阶码,也即取层次最低的、数字最 大的层级码。
• MRP的概念 • MRP的工作原理 • MRP处理过程 • MRP的编制案例 • MRP的更新方法 • 能力需求计划 • MRP和LRP
MRP的编制案例
例1 求毛需求及发出订货计划
• 例1 求毛需求及发出订货计划:已知MPS为在第8个计划周 期时产出100件A产品,其中A产品的BOM图见下图。
即一个项目是采购件还是制造件的标识码。采购或制造标识 码通常用一个字母(P或M)表示。当MRP运行时,该码决定 做采购订单或制造订单计划。
BOM表制作

一、BOM表的定义 二、BOM表的作用 三、BOM表的相关流程图 1、BOM发布流程 2、BOM禁用流程 四、BOM表包含哪些物料 五、BOM表出错导致哪些后果
一、BOM表的定义
BOM是Bill of Materials(物料清单)的缩写,是指产 品所需零部件明细表及其结构,在MRP2中,物料一词有着广 泛的含义,它是所有产品、半成品、在制品、原材料、配套 件、协作件、易耗品等等与生产有关的物料的统称。 ,如 工时、材料、设备、工装、车间等。用以描述产品零件、半 成品和成品之间的关系。在某些工业领域,可能称为“配 方”、“要素表”或其他名称。从概念上来理解BOM有以下 的含义: 1.狭义的BOM一般说来,我们对BOM最初的理解就 是顾名思义,材料清单,也就是通常所说的产品结构,这是 BOM狭义理解。业界先驱,著名ERP专家陈启申先生,在它的 著作《MRPII制造资源计划基础》中,有详细的介绍和论述。 2.广义的BOM对于某一物料的产品结构,每个人都有不同的 理解,那么就会有不同的产品结构树定义;同时,同一个物 料,可以有多种产品结构,这样,在BOM定义过程中,容易 出现偏差。
打开产品文件夹 找到要放的位置
找到放置的位置后新建产品BOM,如下:
点击单一BOM
出现以下画面
输入编码和名称,如下:
点击组成如下:
点击引用物料出现在以下页面:
输入需要的 物料编码
点击查询出现所需物料点击确定出现以下页面:
输入需要的数量和装配位置,其它所需要物料都以此方 法输入
BOM建好后,启动流程,点中一般BOM归档/升级 流程
常用封装
目前我们公司 有几款封装为: 0805封装、0603 封装、1206封装、 2010封装、1210 封装、1812封装、 2512封装,最为 常用的有0805、 1206、0603三类。
物料需求

例: X对A的需求
周
1 2 3 45
毛需求 10 量
20 15
Y对A的需求
6 71 2 3 4
25
30 40
独立A需求
5612 20 10 15 15
30 40
10
20 15
25
15
20 10
2020/8/11
2. 物料统管: 库存控制、物料搬运、厂内外运输、外协外包
、利废利材、采购供应、厂内仓库等由一个物料经理统一领 导。
3. 物料编码:唯一性:同一零件不同加工阶段、不同颜色就
是不同零件。编码最大可达15位。6位编码可编号为: 000,000——999,999 , 100万种。
4. 项目主文件: 2020/8/11
1U的数目=1 200 +2V的数目=2 300
=800
2U的数目=2 200=400
2V的数目=2 300=600
一个简单的MRP例子
现在考虑获得上述物料项的时间
假设:T需要1周;U需要2周;V需要2周;W需要3周; X需要1周;Y需要1周。
所有物料何时订货?何时到货?才能满足生 产产品T的需要。
1 主生产计划(MPS):
各种型号产品时段计划 展开的零件时段计划
主生产计划
2. 物料清单(BOM): 根据产品结构而定
BOM
物物料料需需求求计计划划
库存信息
的零件 3。库存信息
结果如何?
N CP
看能力平衡(CP)
Y
2020/8/11
生产计划
采购计划
§10-2 MRP的运算依据(续)
MRP运行所需的信息
2020/8/11
一个简单的MRP例子
七、物料需求计划

第七讲物料需求计划1、物料需求计划的基本原理用料预算方法□用料预算第一条常备材料:由生产管理单位依生产及保养计划定期编制"材料预算及存量基准明细表"拟订用料预算。
第二条预备材料:由生产管理单位依生产及保养计划的材料耗用基准,按科别(产品表)定期编制"材料预算及存量基准明细表"拟订用料预算,其杂务用品直接依过去实际领用数量,并考虑库存情况,拟订次月用料预算。
第三条非常备材料:订货生产的用料,由生产管理单位依生产用料基准,逐批拟订产品用料预算,其他材料直接由使用单位定期拟订用料预算。
□存量管理第四条常备材料:物料管理单位依材料预算用量,交货所需时间、需用资金、仓储容量、变质速率及危险性等因素,选用适当管理方法以"材料预算及存量基准明细表"列示各项材料的管理点,连同设定资料呈主管核准后,作为存量管理的基准,并拟"常备材料控制表"进行存量管理作业,但材料存量基准设定因素变动足以影响管理点时,物料管理单位应即修正存量管理基准。
第五条预备材料:物料管理单位应考虑材料预算用量,在精简采购、仓储成本的原则下,酌情以"材料预算及存量基准明细表"设定存量管理基准加以管理,但材料存量基准设定因素变动时,物料管理单位必须修正其存量管理基准。
第六条非常备材料:由物料管理单位依据预算用量及库存情况实施管理(管理方法由各公司自订)。
□用料差异分析第七条材料预算用量与实际用量差异超过管理基准时,依下列规定办理:(一)常备材料:物料管理单位应于每月10日前就上月实际用量与预算用量比较(内购材料用)或前三个月累计实际用量与累计预算用量比较(外购材料用)其差异率在管理基准(各公司自订)以上者,需填制"材料使用量差异分析月报表"送生产管理单位分析原因,并提出改善对策。
(二)预备材料:物料管理单位以每月或每三个月一期,于次月10日前就最近一个月或三个月累计实际用量与累计预算用量比较,其差异率在管理基准(各公司自订)以上者按科别填制"材料使用量差异分析月报表",送生产管理单位分析原因,并提出改善对策。
物料需求计划例题
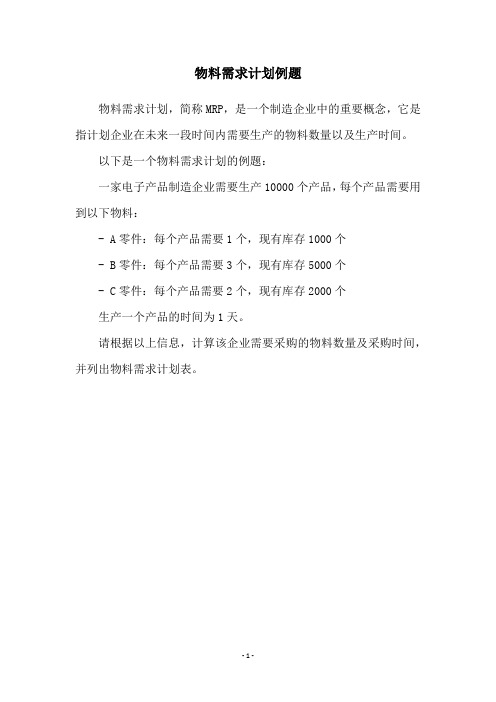
物料需求计划例题
物料需求计划,简称MRP,是一个制造企业中的重要概念,它是指计划企业在未来一段时间内需要生产的物料数量以及生产时间。
以下是一个物料需求计划的例题:
一家电子产品制造企业需要生产10000个产品,每个产品需要用到以下物料:
- A零件:每个产品需要1个,现有库存1000个
- B零件:每个产品需要3个,现有库存5000个
- C零件:每个产品需要2个,现有库存2000个
生产一个产品的时间为1天。
请根据以上信息,计算该企业需要采购的物料数量及采购时间,并列出物料需求计划表。
- 1 -。
物料需求计划表

201202032董其昌手册画册201202037品藏东方201202037品藏东方201202037品藏东方201202037品藏东方201202037品藏东方201202037品藏东方201202037品藏东方201202037品藏东方201202037品藏东方201202037品藏东方201202037品藏东方201202037品藏东方201202037品藏东方201202038上海滩礼券书签201202038上海滩礼券书签201202038上海滩礼券书签201202038上海滩礼券书签201202038上海滩礼券书签201202038上海滩礼券书签201202038上海滩礼券书签201202038上海滩礼券书签201202028荣威750车模盒子201202028荣威750车模盒子201202028荣威750车模盒子201202028荣威750车模盒子201202028荣威750车模盒子201202028荣威750车模盒子201202032董其昌手册画册201202032董其昌手册画册201202032董其昌手册画册201202032董其昌手册画册201202032董其昌手册画册201202032董其昌手册画册201202030周海歌画册201202030周海歌画册201202030周海歌画册201201019-4怪斋书匣新装订要求201201019-4怪斋书匣新装订要求201202034新富春山居图画加印201202034新富春山居图画加印201202034新富春山居图画加印201202034新富春山居图画加印201202034新富春山居图画加印201202034新富春山居图画加印201202034新富春山居图画加印201202034新富春山居图画加印201202034新富春山居图画加印201202034新富春山居图画加印201202034新富春山居图画加印201202036石城萃影201202036石城萃影。
物料需求计划
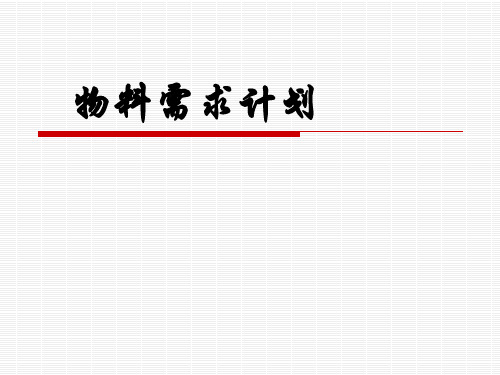
物料需求计划系统的输入输出
BOM MPS
库存文件
MRP
加工定单
采购定单
修改定单
MRP 的 逻 辑 流 程 图
市场要什么? 预测
1
潜在 客户 合同
卖什么? MPS
3 库存信息
(物料可用量)
主生产计划
2
产品信息
(物料清单) (工艺路线)
4 物料需求计划 MRP
买什么?
采购计划
做什么?
生产计划
MRP的相关概念
5
6 6
5
5
13
5
5
5
5
2
5
13
5
5
5
8 7 10
8
13 2 10
6
10 5 10
5
12 13 20
7
12 3 10
7
10 6 2
10 1
10 4
20 2
10 8
主生产计划的生产总量必须等于综合计划确 定的生产量 所确定的是最终物料项 主生产计划必须考虑企业能力、资源的约束 条件 主生产计划最终形成的计划在系统中运行前 要进行核实
O
时 段
毛 需 求 计划接收量 预计库存量 净 需 求 计划产出量 计划投入量
批量=40 现有量=10
1
2 20
9 10 11 12 10 0 10 40 0 30 10 40 40
CHEN.039 001
50 30 30 10 10 30 30 10 10
40
(2)MRP运算后生成的中间信息 毛需求:要生产什么?预测和订单组合(不是简单相加) 计划接收量:前期在制,也可理解为正在途中即将到达的物 料。 预计可用库存:已有了什么?即每个时区的期末库存余量 预计可用库存=前一时区末的可用库存 +本时区计划接收量-本 时区毛需求 +本时区计划产出量 净需求:还缺什么? 净需求=本时区毛需求-(前时区期末的可用库存+本时区计划 接收量) 计划产出量:为了满足净需求应生产量(考虑批量) 计划投入量:什么时间下达订单即投入生产或订货(考虑提 前期、废品率 )
物料需求计划【共49张PPT】
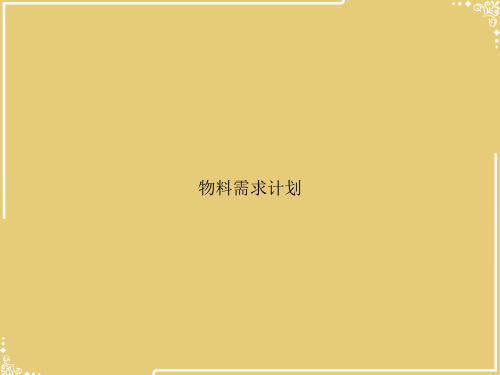
采购供应计划
每一项加工件的建议计划 • 需求数量 • 开始日期和完工日期
每一项采购件的建议计划 • 需求数量 • 订货日期和到货日期
MRP 的基本逻辑
四、MRPII的输入信息
MRP的输入有3个部分: • 主生产计划(产品出产计划MPS)
• 物料清单(产品结构文件,BOM) • 库存状态文件
物料清单(产品结构文件,BOM)
净需求=总需求—(预计到货量+现有量)+安全库存 于是,人们便思考:怎样才能在需要的时间,按需要的数量得到真正需用的物料?从而消除盲目性,实现低库存与高服务水平并存。 ERP是在MRP基础上发展起来的,以供应链思想为基础,融现代管理思想为一身,以现代化的计算机及网络通信技术为运行平台,集企业的各项管理功能为一身,并能对供应链上所有资源进行有效控 制的计算机管理系统。
件;要加工各种零件,就必须提前一定时间准备所需
数量的各种毛坯,直至提前一定时间准备各种原材料 。
其主要功能及运算依据为:
处 理 的 问 题 1. 生 产 什 么 ?生 产 多 少 ? 2. 要 用 到 什 么 ? 3. 已 具 备 什 么 ? 4. 还 缺 什 么 ? 何 时 需 要 ?
所 需 信 息 1. 切 实 可 行 的 主 生 产 计 划 ( M PS) 2. 准 确 的 物 料 清 单 ( BOM表 ) 3. 准 确 的 物 料 库 存 数 据 4. M RP的 计 算 结 果 ( 生 产 计 划 和 采 购 计 划 )
物料需求计划
本章学习目标
• 物料需求计划(MRP):
– Material Requirements Planning
• 制造资源计划(MRPⅡ ):
– Manufacturing Resource Planning
物料需求计划(MRP)

运行步骤
(1)根据市场预测和客户订单,正确编制可靠的生产计划和生产作业计划,在计划中 规定生产的品种、规格、数量和交货日期,同时,生产计划必须是同现有生产能力相适应的 计划。
(2)正确编制产品结构图和各种物料、零件的用料明细表。 (3)正确掌握各种物料和零件的实际库存量。 (4)正确规定各种物料和零件的采购交货日期,以及订货周期和订购批量。 (5)通过 MRP 逻辑运算确定各种物料和零件的总需要量以及实际需要量。 (6)向采购部门发出采购通知单或向本企业生产车间发出生产指令。
基本数据
制订物料需求计划前就必须具备以下的基本数据:
第一项数据是主生产计划,它指明在某一计划时间段内应生产出的各种产品和备件,它 是物料需求计划制订的一个最重要的数据来源。
第二项数据是物料清单(BOM),它指明了物料之间的结构关系,以及每种物料需求的数 量,它是物料需求计划系统中最为基础的数据。
第三项数据是库存记录,它把每个物料品目的现有库存量和计划接受量的实际状态反映 出来。
分类
(1)再生式 MRP,它表示每次计算时,都会覆盖原来的 MRP 数据,生成全新的 MRP。 再生式 MRP 是周期性运算 MRP,通常的运算周期是一周。
(2)净变式 MRP,它表示只会根据指定条件而变化,例如 MPS 变化、BOM 变化等, 经过局部运算更新原来 MRP 的部分数据。净变式 MRP 是一种连续性的操作,当指定数据 改变时就需要立即运行。
目录
.
1 含义内容
.
2 特点
.
3 基本数据
.
4 计算步骤
.
5 实现目标
其主要内容包括客户需求管理、产品生产计划、原材料计划以及库存记录。其中客户需 求管理包括客户订单管理及销售预测,将实际的客户订单数与科学的客户需求预测相结合即 能得出客户需要什么以及需求多少。
物料需求计划
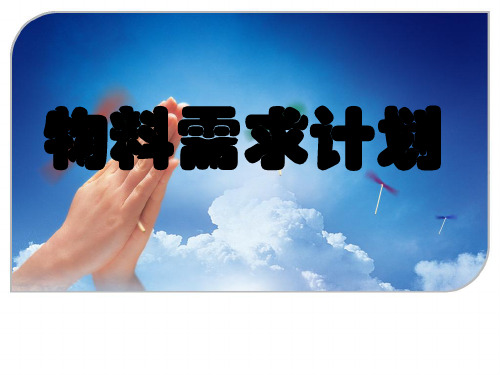
ERP原理与应用
C
D C
2
2 3
2 3
1
1 2
表2 MPS中X和Y的计划投入量
时段 1 2 3 4 5 6 7 8
X
Y
5
12
7
15
13
22
5
16
6
9
5
15
4
10
3
12
表3-MRP件的计划到货
1 A B C D 2 3 5 2 7 3 13 20 4 5 6 7
15 30
Байду номын сангаас
0 0
-15 15
15 30
0 0
-15 15
15 30
0 0
30
第四节 MRP计算过程
例题2:低层码 1.确定BOM
ERP原理与应用
第四节 MRP计算过程
2.确定主生产计划MPS
ERP原理与应用
MPS的计算方法参见第四章
第四节 MRP计算过程
3.确定MRP的毛需求(1层)
ERP原理与应用
计划期
小时/天/周
优先级
时间
目的是在准确的时间、准确的地点、得到准确的物料,即在“需要的时 候得到需要数量的物料”。
第一节 MRP的定义与作用
ERP原理与应用
MRP和定货点法的区别
消耗 定货 点法 MRP 均衡 不均衡 依据 历史 资料 产品结 构展开 相关需求 不考虑 考虑 库存 有余 减少 供给 定时 需要时 优先级 不考虑 考虑
物料需求计划
主 要 内 容
1 2 3 4
MRP的定义与作用
ERP原理与应用
物料清单
MRP工作原理
生产中使用的各种表格

生产中使用的各种表格
生产中使用的表格种类很多,以下是一些常见的生产表格:
1.生产计划表:用于安排生产计划,包括产品名称、数量、生产日
期等信息。
2.物料需求计划表:根据生产计划表,计算出所需物料种类、数量、
采购时间等信息。
3.生产进度表:记录生产进度,包括各工序的完成情况、生产数量、
生产日期等信息。
4.质量控制表:用于记录产品质量检测数据,包括检测项目、标准
值、实际值、判定结果等信息。
5.设备维护表:记录设备的维护情况,包括设备名称、维护时间、
维护内容等信息。
6.人员考勤表:记录生产人员的考勤情况,包括姓名、出勤时间、
工作内容等信息。
7.生产日报表:汇总当日的生产情况,包括生产计划完成情况、设
备运行情况、质量问题等信息。
8.不良品处理表:记录不良品的处理情况,包括不良品数量、原因、
处理措施等信息。
9.工艺流程表:详细描述产品的生产工艺流程,包括各工序的操作
方法、设备要求、检测标准等信息。
10.产品BOM表:列出产品所需的物料清单,包括物料名称、规格型
号、数量等信息。
以上表格可以根据实际需要进行调整和修改,以满足生产管理的需要。
物料需求计划(MRP)计算
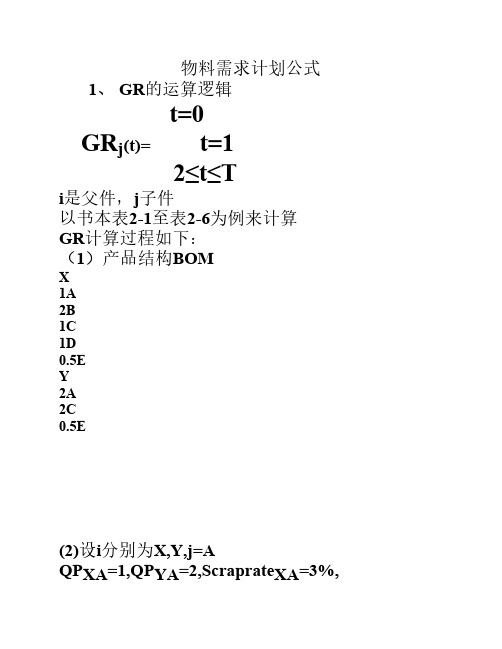
物料需求计划公式1、 GR的运算逻辑t=0GR j(t)= t=12≤t≤Ti是父件,j子件以书本表2-1至表2-6为例来计算GR计算过程如下:(1)产品结构BOMX1A2B1C1D0.5EY2A2C0.5E(2)设i分别为X,Y,j=AQP XA=1,QP YA=2,Scraprate XA=3%,Scraprate YA=5%t=0时,父件X,Y的POR都等于0POR x(0)=0,PORy(0) =0,indmd x(0)=0, indmd y(0)=0GR A(0)= 0t=1时,父件X,Y的POR分别为POR x(1)=200,POR y(1) =200,indmd x(1)=0, indmd y(1)=0GRA(1)= (200×1)/(1-3%)+(200×2)/(1-5%)+0+0=627.2t=2时, 父件X,Y的POR分别为POR x(2)= 0,POR y(1) =150,indmd x(1)=0, indmd y(1)=0GR A(2)= ( 0×1)/(1-3%)+(150×2)/(1-5%)+0=315.8 2.SR的来源T=0的逾期量SR j(0)是应到未到量,T≥1的SR j(t)为排定在未来t时段将会取得的“已订未交量”3、 POH的运算逻辑OH j+SR j(1)+SR j(0)-AL j-GR j(1) t=1POH j(t)=PAB j(t-1)+SR j(t)-GR j(t) 2≤t≤TOH A=300,SR A(1)=500,SR A(0)=0,AL A=200,GR A(1)=627(1) 还是以上面的例子来计算t=1时,j=APOH A(1)= OH A+ SR A(1)+ SR A(0)- AL A-GR A(1)=-27t=2时,j=APOH A(2)=PAB A(1)+SR A(2)-GR A(2)=473+0-315.8=157.24、 NR的运算逻辑NR j(t)=IF{POH j(t)≥SS j,0,} 1≤t≤T以上面的例子,j=APOH A(1)=-27, SS A=10,Yield A=100%NR A(1)= IF{POH A(1)≥SS A,0,}=IF{-27≥10,0,37}=37NR A(2)=05、 PORC的运算逻辑PORC j(t)=F(NR j(t),LSR) 1≤t≤T(1) 最小订购量法,即一旦有净需求,订购量最少应为某基准量LSPORC j(t)=IF(NR j(t)>0,max{NR j(t),LS j},0) 1≤t≤T(2) 定量批量法,即一旦有净需求,订购量始终为某基准量LS整数倍PORC j(t)=IF(NR j(t)>0,CEILING{NR j(t),LS j},0)1≤t≤T以上面例子为例j=A时NR A(1)=37, LS A=500,A的批量法则LSR为最小订购量法,所以用公式(1)PORC A(1)=IF(NR A(1)>0,max{ NR A(1),LS A},0)=500PORC A(2)=06、 PAB的运算逻辑PAB j(t)=POH j(t)+PORC j(t) 1≤t≤T以上面例子为例当t=1,j=A时POH A(1)= -27,PORC A(1)=500PAB A(1)=-27+500=4737、 POR的运算逻辑t=0POR j(t)= PORC j(t+LT j) 1≤t≤T-LT j0 T- LT j<t≤T以上面例子为例当t=0时,j=A,因此LT j=2POR A(t)=PORC A(1)+PORC A(2)=500+0=500当t=1时, j=A,因此LT j=2计算PORC A(3)案例MRP计算步骤如下:(1)首先计算第1阶MRP物料A和B全部期别的毛需求(2)随机选取A或B,此处假设选A,按{POH(t)→NR(t)→PORC(t)→PAB(t)}的顺序依次计算第1至第9期数据。