印制电路板DFM设计技术要求
DFM通用技术要求
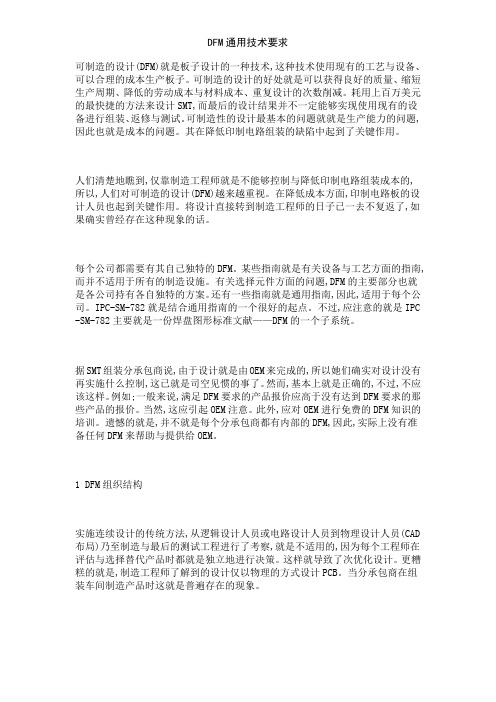
可制造的设计(DFM)就是板子设计的一种技术,这种技术使用现有的工艺与设备、可以合理的成本生产板子。
可制造的设计的好处就是可以获得良好的质量、缩短生产周期、降低的劳动成本与材料成本、重复设计的次数削减。
耗用上百万美元的最快捷的方法来设计SMT,而最后的设计结果并不一定能够实现使用现有的设备进行组装、返修与测试。
可制造性的设计最基本的问题就就是生产能力的问题,因此也就是成本的问题。
其在降低印制电路组装的缺陷中起到了关键作用。
人们清楚地瞧到,仅靠制造工程师就是不能够控制与降低印制电路组装成本的,所以,人们对可制造的设计(DFM)越来越重视。
在降低成本方面,印制电路板的设计人员也起到关键作用。
将设计直接转到制造工程师的日子已一去不复返了,如果确实曾经存在这种现象的话。
每个公司都需要有其自己独特的DFM。
某些指南就是有关设备与工艺方面的指南,而并不适用于所有的制造设施。
有关选择元件方面的问题,DFM的主要部分也就是各公司持有各自独特的方案。
还有一些指南就是通用指南,因此,适用于每个公司。
IPC-SM-782就是结合通用指南的一个很好的起点。
不过,应注意的就是IPC -SM-782主要就是一份焊盘图形标准文献——DFM的一个子系统。
据SMT组装分承包商说,由于设计就是由OEM来完成的,所以她们确实对设计没有再实施什么控制,这已就是司空见惯的事了。
然而,基本上就是正确的,不过,不应该这样。
例如;一般来说,满足DFM要求的产品报价应高于没有达到DFM要求的那些产品的报价。
当然,这应引起OEM注意。
此外,应对OEM进行免费的DFM知识的培训。
遗憾的就是,并不就是每个分承包商都有内部的DFM,因此,实际上没有准备任何DFM来帮助与提供给OEM。
1 DFM组织结构实施连续设计的传统方法,从逻辑设计人员或电路设计人员到物理设计人员(CAD 布局)乃至制造与最后的测试工程进行了考察,就是不适用的,因为每个工程师在评估与选择替代产品时都就是独立地进行决策。
印制电路板DFM设计技术要求
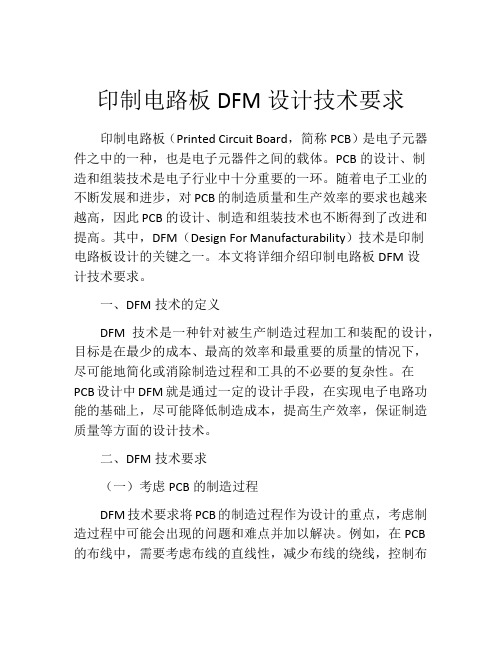
印制电路板DFM设计技术要求印制电路板(Printed Circuit Board,简称PCB)是电子元器件之中的一种,也是电子元器件之间的载体。
PCB的设计、制造和组装技术是电子行业中十分重要的一环。
随着电子工业的不断发展和进步,对PCB的制造质量和生产效率的要求也越来越高,因此PCB的设计、制造和组装技术也不断得到了改进和提高。
其中,DFM(Design For Manufacturability)技术是印制电路板设计的关键之一。
本文将详细介绍印制电路板DFM设计技术要求。
一、DFM技术的定义DFM技术是一种针对被生产制造过程加工和装配的设计,目标是在最少的成本、最高的效率和最重要的质量的情况下,尽可能地简化或消除制造过程和工具的不必要的复杂性。
在PCB设计中DFM就是通过一定的设计手段,在实现电子电路功能的基础上,尽可能降低制造成本,提高生产效率,保证制造质量等方面的设计技术。
二、DFM技术要求(一)考虑PCB的制造过程DFM技术要求将PCB的制造过程作为设计的重点,考虑制造过程中可能会出现的问题和难点并加以解决。
例如,在PCB的布线中,需要考虑布线的直线性,减少布线的绕线,控制布线的宽度和位置,避免出现布线打短路等问题,这些问题都需要在PCB设计阶段考虑到,并通过专业软件进行优化和处理。
(二)考虑PCB的制造成本DFM技术要求PCB设计师在设计PCB时,从成本的角度出发,从材料、制造过程、组装工艺等方面考虑如何降低生产成本。
例如,对PCB的阻焊层采用一面阻一面焊的方法,可以避免由于一面焊死或者控制不准而造成的流量不均和短路问题,在一定程度上减少制造成本。
(三)考虑PCB的制造工艺DFM技术要求PCB设计师要充分了解PCB制造工艺,对制造过程中的工艺进行分析和研究,从而能够更好地将设计与制造工艺相结合。
例如,在PCB的厚铜箔制造中,必须要充分考虑铜箔的厚度和表面处理方式,以及厚铜箔加工过程中的机械力、加热温度、压力等因素,从而能够保证在加工生产过程中制造出符合要求的厚铜箔。
DFM-checklist-for-SMT

3 TUBE(支装) 不允许 不允许
不允许
Yes
No
N/A
Yes
No
N/A
19
ME
Mark点不能放于夹板边,且mark点中心露铜需离开上下板边外沿 5mm以上。
Yes
No
N/A
Mark点能良好地识别,形状规则,表面平整,直径d=1.2mm,且有周
20
EE
围有一圈直径大于2.5mm的完整空旷区,无绿油区离板边1mm, Mark点周围5mm内无相似尺寸的方块或圆干扰;需考虑线上所有设
17
EE
带半圆孔贴片焊盘的(模块PCB),选用FR4+沉金工艺( Tg≧170 ℃),其它的表面处理工艺不推荐选用;
需要考虑ESD静电泄放要求的PCB(如SD卡等等),可以考虑沉金
工艺。(来源:SQM主导的 定制件质量管理及系统精益供应链)
18
元件的包装首选卷装,次选硬质盘装(常用220*330,120*300≤a PP ≤230*330),外包装不能接受纸制,不能使用支装,如果不满足
BGA、IC等器件极性、丝印标识与器件封装一致、不错位,丝印字
迹清晰。
16
EE PCB上的细小通孔用绿油填塞,不允许漏白光。
Yes
No
N/A
Yes
No
N/A
Yes
No
N/A
Yes
No
N/A
带BGA板采用FR4+沉金工艺(Tg≧150℃),其次考虑用FR4+沉锡工艺
( Tg≧150℃);其它普通板可以考虑OSP。
PCB供应商制作时需要使用锣板方式,PCB 外观一致性好,无毛刺
、四周光滑;阻焊层、绿漆均匀,无脱落或剥离现象。
SMT-PCBA可制造性工艺设计(DFM)规范

SMT-PCBA可制造性工艺设计(DFM)规范1. 目的产品总成本 60%取决于产品的最初设计 ; 75%的制造成本取决于设计说明和设计规范 ; 70-80%的生产缺陷是由于设计原因造成的。
故为了规范新产品在设计初始各个阶段的可制造性评审,让评审有据可循,确保新产品符合生产的效率、成本、品质等各方面的要求,缩短新品研发周期,提升产品质量及竞争力制定此规范文件。
2. 适用范围适用于SMT所有新产品各个开发阶段的可制造性设计评审。
3. 参考资料IPC-A-610F, Acceptability of Electronic Assemblies 电子组装件的可接受性条件IPC2221, Generic Standard on Printed Board design印刷电路板设计通用标准IPC-7351—表面贴装设计和焊盘图形标准通用要求4. 名词解释1、SMT(Surface Mounting Technology)表面贴装技术,指用自动贴装设备将表面组装元件/器贴装到PCB表面规定位置的一种电子装联技术。
2、THT:ThroughHoleTechnology(THT)通孔插装技术3、PCB(Printed Circuit Board)指在印刷电路基板上,用铜籍布置的电路。
4、PCBA(Printed Circuit Board Assembly)指采用表面组装技术完成装配的电路板组装件5、SMD(Surface Mounting Device)表面贴装元件,它不同于以前的通孔插装部品,而是贴装在PC的表面。
6、SOP(Small Out-line Package)它是在长方形BODY两侧,具有约8~40pin左右的Lead的表面装IC,Lead Pitch有0.5mm,0.65mm,0.8mm,1.27mm等。
7、QFP(Quad Flat Package)它是在正方形或长方形BODY四周具有约100~250Pin左右Lead的表面实装用IC,LeadPitch有0.4mm,0.5mm,0.65mm,0.8mm等。
印制电路板可制造性设计通用技术要求

若美印制电路板DFM通用技术要求为了明确PCB板的制作要求,更好的实现CAD与CAM的沟通,更好的实现DFM的共同目标,更好的缩短产品制造周期,降低生产成本,提高产品品质,减少PCB板制作问题,提高产品准确可靠性,方便后工序SMT的生产操作。
特制定此要求。
1 文件接收要求各式格式的GERBER文件,各种版本的PROTEL,PADS文件,要含完整的线路图,阻焊图,丝印图,分孔图,外形图,钻孔图,连片图(含孔的属性,大小,机械层次分明,连片方式及标准的数据显示)。
2 线路板制作信息要求制作要求要含板材,板厚,铜箔厚度,阻焊油颜色,字符颜色,表面工艺处理,阻抗要求,环保要求,特殊要求(如:高TG板材)等信息。
(最好请附上板的用途,例如在高温下作业的PCB,考虑用耐高温的高TG板材,特殊要求应在附件上显示)如客户不提供任何制作要求,我司会将此板当常规板制作,板材为FR4,94V-0,厚度1.6MM,表面铜厚1OZ,阻焊油颜色为深绿色,字符颜色为白色,表面处理为OSP.3 PCB结构要求3.1 结构PCB文件中的安装孔、定位孔、拼板邮票孔、散热孔等一般情况请在机械层,Board line和钻孔层(NC数据层)标示。
4板材要求PCB双面、多层常用的板材为FR-4玻纤板,板厚有0.4MM、0.6MM、0.8MM、1.0MM、1.2MM、1.6MM、2.0MM等5印制导线要求5.1 布局a)印制导线布局,成品铜厚为1OZ的,最优线宽、线距大于0.125mm(5mil) 高密线路可考虑线宽线距为0.1MM(4mil) ,线到焊盘、焊盘与焊盘大于等于0.15MM(6miL),线到铜皮距大于等于0.2mm(8mil)。
导线距边要大于0.4MM(16mil),距安装孔,定位孔大于0.4MM(16mil)。
为了保证板在电镀时板面与孔铜的均匀性,尽量要在板内空白区铺铜箔,尽可能不在板内放置独立线与独立孔,避免在电镀过程中引起烧板,影响成品线宽和孔径大小达不到要求。
电路板(PCB)设计与可制造性(DFM)

30%
理想状态
功能无缺点,达设计 要求
3..3板边缘设计要求
图形到板边 缘的距离最 小0.4.冲切 加工的板最 好与板厚尺 寸一样
3.4板面线路布局隐忧
PCB
两面的线路
尽量不要平 行,否则,图形 腐蚀后,因两 面铜箔应力 释放,易产生 板翘
3.8整板厚度结构
流程
沉电 铜
电路电 镀
防焊制 作
文字
合计
板料最大上 偏差
加成 0.005 0.05 0.02 0.03 0.105 0.13
总厚度 0.235
成品厚度:板厚T+加成总厚度 结论:成品板厚易超规格
3.9孔到板边的距离
可靠性疑问:
1)板边的机械强度降低
2)孔环一旦受到损伤,锡垫不 完整
显影后的结果,图 形转移时,网格未 形成
3.PCB设计的一般要求
• 3.1导体外观 • 3.2金手指外观 • 3.3板边缘设计要求 • 3.4板面线路布局隐忧 • 3.5V槽板外形尺寸结构 • 3.6冲切板外形尺寸结
构
• 3.7板厚标准 • 3.8整板厚度结构
3.9孔到板边的距离 3.10孔尺寸结构 3.11图形尺寸 3.12-15导体断面积,铜厚, 电压与电流等之间关系
槽深度偏差
B 板厚度方向中心到板面 ±0.08
的距离
C 上下V槽刀的偏移距离 ±0.08
D V槽线的宽度偏差
±0.08
E V槽刀角度偏差
±2°
F V槽位置偏差
D/2+累积
G 板厚
H 连片V槽线中心距
±0.08加
累积偏差
按上表和图说明 测量: V槽板的测量以V 槽线中心为基准 建议:外形公差±0.25mm
DFM通用技术要求

可制造得设计(DFM)就是板子设计得一种技术,这种技术使用现有得工艺与设备、可以合理得成本生产板子.可制造得设计得好处就是可以获得良好得质量、缩短生产周期、降低得劳动成本与材料成本、重复设计得次数削减.耗用上百万美元得最快捷得方法来设计SMT,而最后得设计结果并不一定能够实现使用现有得设备进行组装、返修与测试。
可制造性得设计最基本得问题就就是生产能力得问题,因此也就是成本得问题。
其在降低印制电路组装得缺陷中起到了关键作用。
人们清楚地瞧到,仅靠制造工程师就是不能够控制与降低印制电路组装成本得,所以,人们对可制造得设计(DFM)越来越重视。
在降低成本方面,印制电路板得设计人员也起到关键作用。
将设计直接转到制造工程师得日子已一去不复返了,如果确实曾经存在这种现象得话.每个公司都需要有其自己独特得DFM.某些指南就是有关设备与工艺方面得指南,而并不适用于所有得制造设施.有关选择元件方面得问题,DFM得主要部分也就是各公司持有各自独特得方案。
还有一些指南就是通用指南,因此,适用于每个公司。
IPC-SM—782就是结合通用指南得一个很好得起点。
不过,应注意得就是IPC-SM—782主要就是一份焊盘图形标准文献—-DFM得一个子系统。
据SMT组装分承包商说,由于设计就是由OEM来完成得,所以她们确实对设计没有再实施什么控制,这已就是司空见惯得事了。
然而,基本上就是正确得,不过,不应该这样。
例如;一般来说,满足DFM要求得产品报价应高于没有达到DFM要求得那些产品得报价。
当然,这应引起OEM注意。
此外,应对OEM进行免费得D FM知识得培训。
遗憾得就是,并不就是每个分承包商都有内部得DFM,因此,实际上没有准备任何DFM来帮助与提供给OEM。
1 DFM组织结构实施连续设计得传统方法,从逻辑设计人员或电路设计人员到物理设计人员(CAD布局)乃至制造与最后得测试工程进行了考察,就是不适用得,因为每个工程师在评估与选择替代产品时都就是独立地进行决策。
印制电路板DFM设计技术要求
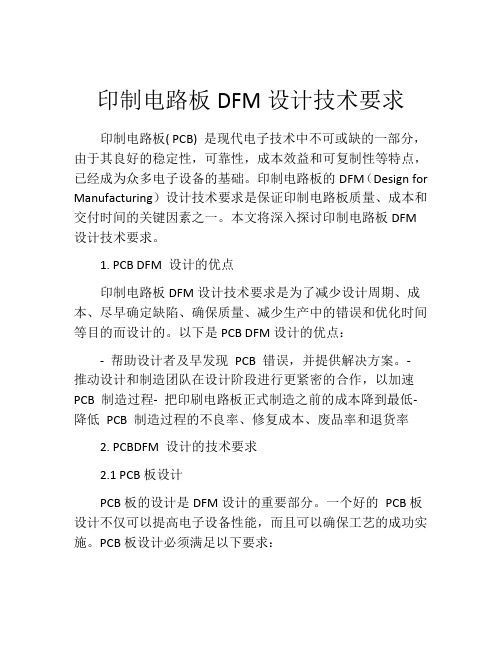
印制电路板DFM设计技术要求印制电路板( PCB) 是现代电子技术中不可或缺的一部分,由于其良好的稳定性,可靠性,成本效益和可复制性等特点,已经成为众多电子设备的基础。
印制电路板的DFM(Design for Manufacturing)设计技术要求是保证印制电路板质量、成本和交付时间的关键因素之一。
本文将深入探讨印制电路板DFM 设计技术要求。
1. PCB DFM 设计的优点印制电路板DFM设计技术要求是为了减少设计周期、成本、尽早确定缺陷、确保质量、减少生产中的错误和优化时间等目的而设计的。
以下是PCB DFM设计的优点:- 帮助设计者及早发现PCB 错误,并提供解决方案。
-推动设计和制造团队在设计阶段进行更紧密的合作,以加速PCB 制造过程- 把印刷电路板正式制造之前的成本降到最低- 降低PCB 制造过程的不良率、修复成本、废品率和退货率2. PCBDFM 设计的技术要求2.1 PCB板设计PCB板的设计是DFM设计的重要部分。
一个好的PCB板设计不仅可以提高电子设备性能,而且可以确保工艺的成功实施。
PCB板设计必须满足以下要求:- 确定最终PCB尺寸和定位孔的位置。
- 检查层的数量、材料和厚度。
- 确定通孔、配线宽度、间距和最小孔径。
- 确定最终元件的实际放置位置和方向。
2.2 PCB 布局设计在PCB 布局设计中,标准PCBA 规则应该得到应用,例如: PCB 布局应与产品的产品设计多丈量共而规划。
2.2.1元器件布局元器件布局的良好设计能使电路运作更加稳定可靠,这里的要求如下:- 元器件应该尽可能的紧凑布置。
- 元器件布局应该符合最佳电路设计规则和"防雷"设计规则,并实施正确的设计电磁兼容性(EMC)战略。
- 保证元器件之间的间距不太大或太小,保证元器件之间的空间不太大或太小。
2.2.2 设计元器件包括邻近元件的距离元器件之间的间距应保持合理,以避免两个元器件之间的电磁干扰。
印制电路板dfm通用技术要求(General specification for printed circuit board DFM)

印制电路板dfm通用技术要求(General specification for printedcircuit board DFM)General specification for printed circuit board DFMThis standard specifies the general requirements for design for manufacturing single sided printed circuit board, including materials, dimensions and tolerances, printed wires and pads, metal holes, holes, mounting holes, coating, coating, character and mark. As designers of printed boards, design a single, double sided (Single/Double, sided, board) reference:1 General requirements1.1. This standard serves as a general requirement for PCB design, specifications for PCB design and manufacturing, and effective communication between CAD and CAM.1.2 we shall give priority to the design drawings and documents as the basis for production in the process of documentation.2 PCB material2.1 substratePCB substrate is usually made of epoxy glass cloth covered with copper plate, that is FR4. (including single panel)2.2 copper foilA) more than 99.9% of electrolytic copper;B) double plate surface copper foil thickness more than 35 m (1OZ); special requirements, specified in the drawings or documents.3, PCB structure, size and tolerance3.1 structure(a) the design elements that constitute the PCB shall be described in the design drawings. The appearance shall be uniformly expressed by Mechanical 1, layer (priority) or Keep out layer. If used in the design document at the same time, the general keep out layer is used for shielding without opening, and mechanical 1 is used to represent the forming.(b) in the design drawings for opening long SLOT holes or hollow out, with Mechanical 1 layer draw the corresponding shape can.3.2 plate thickness toleranceFinished plate thickness0.4~1.0mm1.1~2.0mm2.1~3.0mmtolerance+ 0.13MM+ 0.18mm+ 0.2mm3.3 dimensional tolerancesPCB the overall dimensions shall comply with the requirements of the design drawings. When the drawings are not specified, the overall dimension tolerance is + 0.2mm. (except for V-CUT products)3.4 flatness (warpage) tolerancesThe flatness of PCB shall be in accordance with the design drawings. When the drawings are not specified, follow the followingFinished plate thickness0.4~1.0mm1.0~3.0mmWarpageSMT = 0.7%; SMT = 1.3%SMT = 0.7%; SMT = 1%4 printed wiring and pads4.1 layoutA) the layout, line width and line spacing of printed wires and pads shall be specified in accordance with the design drawings. But we will have the following treatment: appropriate according to process requirements for line width, PAD ring width compensation, single panel general, we will try to increase PAD, in order to strengthen the reliability of customer welding.(b) when the design line spacing is not up to the technical requirements (too closely affecting performance and Manufacturability), we shall adjust the design specifications according to the pre system design.C) we advise customers to design single and double boards in principle. The diameter of through hole (VIA) is more than 0.3mm, the outer diameter is more than 0.7mm, the distance between lines is 8mil, and the line width is above 8mil. To minimize the production cycle, reduce manufacturing difficulties.D) our minimum drilling tool is 0.3, the product is about 0.15mm. The minimum line spacing is 6mil. The minimum line width is 6mil. (but the manufacturing cycle is longer and the cost is higher)4.2 wire width toleranceInternal control standard for width tolerance of printed wiring is + 15%4.3 mesh processing(a) in order to avoid foaming and heating of copper surface when wave soldering occurs, the PCB plate is bent due to thermal stress, and the large copper surface is recommended to be laid in a grid form.B) the grid spacing is larger than 10mil (less than 8mil), the grid width is greater than or equal to 10mil (less than 8mil).4.4 heat shield (Thermal pad) processingOn the ground of large area (electric), often with components of the legs are connected to the connecting legs, both electrical properties and process requirements, made of cross flower pad (heat insulation plate), the possibility of resulting weld point due to excessive heat in the welding section is greatly reduced.5 aperture (HOLE)5.1 definition of metallization (PHT) and non metallization (NPTH)A) our company defaults to the non-metallic hole as follows:When the client sets up the Kong Fei metallization property in the Protel99se advanced properties (plated tab removed from the Advanced menu), we default to a non-metallic hole.When the customer directly uses the keep, out, layer ormechanical 1 layers of arc to indicate the drilling (no more separate holes) in the design document, we will accept the non-metallic hole as the default.When the customer placed the word "NPTH" near the hole, we are responsible for the non - metallization of the hole.When the customer explicitly calls for the corresponding aperture non - metallization (NPTH) in the design notice, they are processed according to the customer's requirements.(b) in addition to the above conditions, the components, holes, mounting holes, and through holes shall be metallized.5.2 hole size and tolerance(a) the PCB element holes and mounting holes in the design drawings assume the final product aperture size. The aperture tolerance is usually + 3mil (0.08mm);B) the through hole (that is VIA hole) we usually control it as follows: the negative tolerance is not required, and the positive tolerance is less than + 3mil (0.08mm).5.3 thicknessThe average thickness of the copper plated layer of metallized hole is not less than 20 m, and the thinnest is no less than 18 mu m.5.4 hole roughnessPTH hole wall roughness is controlled in less than 32um5.5 PIN hole problemA) our CNC milling machine positioning pin is 0.9mm minimum, and the positioning of the three PIN holes should be triangular.(b) when the customer has no special requirement and the design bore bore is less than 0.9mm, we will add the PIN hole at the appropriate position of the blank wireless channel or the big copper surface in the board.Design of 5.6 SLOT hole (slot)A) it is recommended that the SLOT hole be drawn with Mechanical1 layer (Keep, out, layer). It can also be expressed as a continuous hole, but the holes should be of the same size and the center of the hole is on the same horizontal line.B) our smallest slot knife is 0.65mm.C) when the SLOT hole is used to shield and avoid creepage between the high and low pressure, it is suggested that the diameter is above 1.2mm to facilitate processing.6 solder layer6.1 coating parts and defectsA) the solder coating shall be applied to the PCB surface exceptthe solder pads, MARK points, test points, etc..(b) if a customer uses a disk represented by FILL or TRACK, a corresponding size graph must be drawn on the solder resist (Solder, mask) layer to indicate the presence of tin at the site.(I strongly recommend that there be no non PAD form before design)(c) if the solder needs to be cooled on a large copper sheet or sprayed on an online bar, a corresponding size pattern must also be painted on the mask (Solder) layer to indicate the presence of tin.6.2 adhesionThe adhesion of the solder resist is required by level 2 of IPC-A-600F in the United states.6.3 thicknessThe thickness of the solder resist conforms to the following table:Line surfaceLine cornerSubstrate surfaceMore than 10 mMore than 8 m20~30 mu m7 characters and etch marks7.1 basic requirementsA) the characters of PCB should be designed by word height 30mil, word width 5MIL, character spacing 4mil or more, so as not to affect the differentiability of text.B) etching (metal) characters should not be bridged with wires and to ensure adequate electrical clearance. General design according to word height 30mil, word width 7mil above design.(c) when the customer characters are not clearly defined, our company will adjust the proportion of characters according to the technical requirements of our company.D) when there is no clear customer, we will in the silk printing layer is the proper position of our printed trademark, material number and cycle according to the requirements of our technology.7.2 PAD\SMT processing on textDisc (PAD) can be a silkscreen logo, in order to avoid. When the customer has the design of PAD\SMT, our company will do proper movement processing, the principle is that it does not affect the identity of its identification and device.The concept of 8 layers and the processing of MARK pointsLayer designEight1 double panel, we default to the top (ie Top, layer) for the face, topoverlay screen layer characters are positive.8.2, single panel to top (Top, layer) painted circuit layer (Signal layer), it means that the line is facing the face.8.3, single panel to the bottom (Top, layer) painted circuit layer (Signal layer), that the layer is a perspective line.Design of MARK points8.4 when the customer has a surface mount (SMT) for the board file, it should be placed MARK at the point of Mark, and the circle diameter is 1.0mm.8.5 when the customer has no special requirements, we put an arc of F1.5mm on the Solder Mask layer to represent the flux free to enhance the identifiability.8.6 when the customer is a splicing board file surface patch process side did not put MARK, our general in the process of edge position of the diagonal median plus a MARK point; when the customer is a splicing board file has no surface patch technology, is generally required to communicate with thecustomer need to add MARK.9 about V-CUT (cut V groove)9.1 V cut panels do not leave a gap between the board and the board. However, attention should be paid to the distance between the conductor and the center line of the V cut. Generally, the conductor spacing on both sides of the V-CUT line should be more than 0.5mm, that is to say, in the single block plate, the conductor should be more than 0.25mm from the edge of the plate.9.2 V-CUT line representation method is: general shape for keep out layer (Mech 1) layer said, then the plate needs V cut place, only with keep out layer (Mech 1) layer painted, and preferably in the board connection mark V-CUT words.9.3, as shown in the following figure, the residual depth of the general V cut is 1/3, the thickness of the plate, and in accordance with the customer's residual thickness requirements can be adjusted appropriately.9.4, V cut products after breaking apart, because glass fiber yarn has been a "marathon" phenomenon, the size will be slightly worse, individual products will be larger than 0.5mm.9.5, V-CUT knife can only go straight line, can not go curve and fold line, and can be more than 0.8mm thick board thickness.10 surface treatment processWhen the customer has no special requirement, our surface treatment defaults to hot air leveling (HAL). (tin: 63 tin, /37 lead)General technical requirements above DFM (single sided part) for our customers in the design of PCB file for reference, and hope to reach a consensus on the above, CAD and CAM in order to achieve better communication, better design for manufacturability (DFM) of the common goal, better shorten product manufacturing cycle, reduce production cost.。
印制电路板DFM技术要求
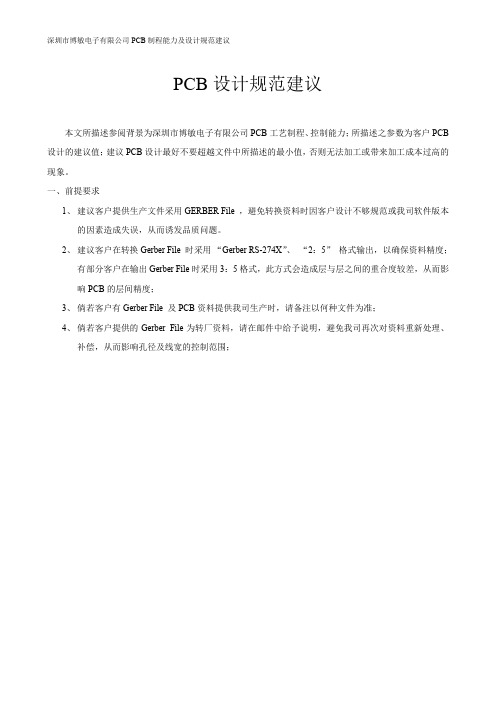
深圳市博敏电子有限公司PCB制程能力及设计规范建议PCB设计规范建议本文所描述参阅背景为深圳市博敏电子有限公司PCB工艺制程、控制能力;所描述之参数为客户PCB 设计的建议值;建议PCB设计最好不要超越文件中所描述的最小值,否则无法加工或带来加工成本过高的现象。
一、前提要求1、建议客户提供生产文件采用GERBER File ,避免转换资料时因客户设计不够规范或我司软件版本的因素造成失误,从而诱发品质问题。
2、建议客户在转换Gerber File 时采用“Gerber RS-274X”、“2:5”格式输出,以确保资料精度;有部分客户在输出Gerber File时采用3:5格式,此方式会造成层与层之间的重合度较差,从而影响PCB的层间精度;3、倘若客户有Gerber File 及PCB资料提供我司生产时,请备注以何种文件为准;4、倘若客户提供的Gerber File为转厂资料,请在邮件中给予说明,避免我司再次对资料重新处理、补偿,从而影响孔径及线宽的控制范围;二、资料设计要求:三、制程能力四、Protel设计注意1、层的定义1.1、层的概念1.1.1、单面板以顶层(Top layer)画线路层(Signal layer),则表示该层线路为正视面。
1.1.2、单面板以底层(bottom layer)画线路层(Signal layer),则表示该层线路为透视面。
我司建议尽量以1.2方式来设计单面板。
1.1.3、双面板我司默认以顶层(即Top layer)为正视面,topoverlay丝印层字符为正。
1.2、多层板层叠顺序:1.2.1、在protel99/99SE及以上版本以layer stack manager为准(如下图)。
1.2.2、在protel98以下版本需提供层叠标识。
因protel98无层管理器,如当同时使用负性电地层(Plane1)和正性(Mid layer1)信号层时,无法区分内层的叠层顺序。
印制电路板DFM通用技术要求
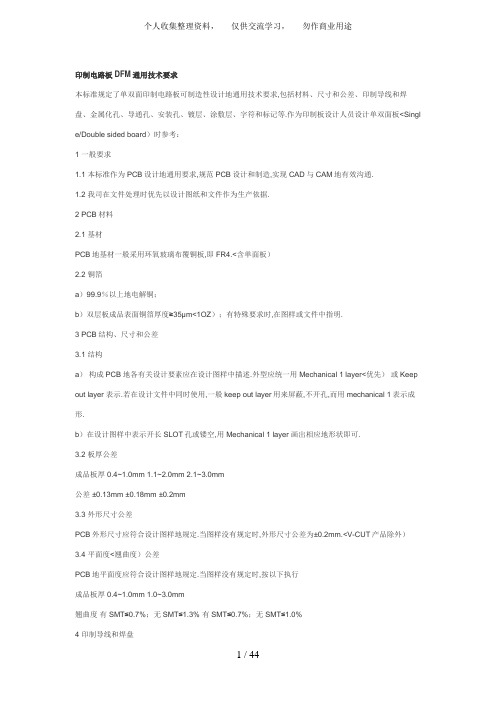
印制电路板DFM通用技术要求本标准规定了单双面印制电路板可制造性设计地通用技术要求,包括材料、尺寸和公差、印制导线和焊盘、金属化孔、导通孔、安装孔、镀层、涂敷层、字符和标记等.作为印制板设计人员设计单双面板<Singl e/Double sided board)时参考:1 一般要求1.1 本标准作为PCB设计地通用要求,规范PCB设计和制造,实现CAD与CAM地有效沟通.1.2 我司在文件处理时优先以设计图纸和文件作为生产依据.2 PCB材料2.1 基材PCB地基材一般采用环氧玻璃布覆铜板,即FR4.<含单面板)2.2 铜箔a)99.9%以上地电解铜;b)双层板成品表面铜箔厚度≥35µm<1OZ);有特殊要求时,在图样或文件中指明.3 PCB结构、尺寸和公差3.1 结构a)构成PCB地各有关设计要素应在设计图样中描述.外型应统一用Mechanical 1 layer<优先)或Keep out layer 表示.若在设计文件中同时使用,一般keep out layer用来屏蔽,不开孔,而用mechanical 1表示成形.b)在设计图样中表示开长SLOT孔或镂空,用Mechanical 1 layer 画出相应地形状即可.3.2 板厚公差成品板厚 0.4~1.0mm 1.1~2.0mm 2.1~3.0mm公差 ±0.13mm ±0.18mm ±0.2mm3.3 外形尺寸公差PCB外形尺寸应符合设计图样地规定.当图样没有规定时,外形尺寸公差为±0.2mm.<V-CUT产品除外)3.4 平面度<翘曲度)公差PCB地平面度应符合设计图样地规定.当图样没有规定时,按以下执行成品板厚 0.4~1.0mm 1.0~3.0mm翘曲度有SMT≤0.7%;无SMT≤1.3% 有SMT≤0.7%;无SMT≤1.0%4 印制导线和焊盘4.1 布局a>印制导线和焊盘地布局、线宽和线距等原则上按设计图样地规定.但我司会有以下处理:适当根据工艺要求对线宽、PAD环宽进行补偿,单面板一般我司将尽量加大PAD,以加强客户焊接地可靠性.b>当设计线间距达不到工艺要求时<太密可能影响到性能、可制造性时),我司根据制前设计规范适当调整.c>我司原则上建议客户设计单双面板时,导通孔<VIA)内径设置在0.3mm以上,外径设置在0.7mm以上,线间距设计为8mil,线宽设计为8mil以上.以最大程度地降低生产周期,减少制造难度.d>我司最小钻孔刀具为0.3,其成品孔约为0.15mm.最小线间距为6mil.最细线宽为6mil.<但制造周期较长、成本较高)4.2 导线宽度公差印制导线地宽度公差内控标准为±15%4.3 网格地处理a>为了避免波峰焊接时铜面起泡和受热后因热应力作用PCB板弯曲,大铜面上建议铺设成网格形式.b>其网格间距≥10mil(不低于8mil>,网格线宽≥10mil<不低于8mil).4.4 隔热盘<Thermal pad)地处理在大面积地接地<电)中,常有元器件地腿与其连接,对连接腿地处理兼顾电气性能与工艺需要,做成十字花焊盘<隔热盘),可使在焊接时因截面过分散热而产生虚焊点地可能性大大减少.5 孔径<HOLE)5.1 金属化<PHT)与非金属化<NPTH)地界定a> 我司默认以下方式为非金属化孔:当客户在Protel99se高级属性中<Advanced菜单中将plated项勾去除)设置了安装孔非金属化属性,我司默认为非金属化孔.当客户在设计文件中直接用keep out layer或mechanical 1层圆弧表示打孔<没有再单独放孔),我司默认为非金属化孔.当客户在孔附近放置NPTH字样,我司默认为此孔非金属化.当客户在设计通知单中明确要求相应地孔径非金属化<NPTH),则按客户要求处理.b> 除以上情况外地元件孔、安装孔、导通孔等均应金属化.5.2 孔径尺寸及公差a> 设计图样中地PCB元件孔、安装孔默认为最终地成品孔径尺寸.其孔径公差一般为±3mil<0.08mm);b> 导通孔<即VIA 孔)我司一般控制为:负公差无要求,正公差控制在+ 3mil<0.08mm)以内.5.3 厚度金属化孔地镀铜层地平均厚度一般不小于20µm,最薄处不小于18µm.5.4 孔壁粗糙度PTH孔壁粗糙度一般控制在≤ 32um5.5 PIN孔问题a>我司数控铣床定位针最小为0.9mm,且定位地三个PIN孔应呈三角形.b>当客户无特殊要求,设计文件中孔径均<0.9mm时,我司将在板中空白无线路处或大铜面上合适位置加P IN孔.5.6 SLOT孔(槽孔>地设计a> 建议SLOT孔用Mechanical 1 layer<Keep out layer)画出其形状即可;也可以用连孔表示,但连孔应大小一致,且孔中心在同一条水平线上.b> 我司最小地槽刀为0.65mm.c> 当开SLOT孔用来屏蔽,避免高低压之间爬电时,建议其直径在1.2mm以上,以方便加工.6 阻焊层6.1 涂敷部位和缺陷a>除焊盘、MARK点、测试点等之外地PCB表面,均应涂敷阻焊层.b>若客户用FILL或TRACK表示地盘,则必须在阻焊层<Solder mask)层画出相应大小地图形,以表示该处上锡.<我司强烈建议设计前不用非PAD形式表示盘)c>若需要在大铜皮上散热或在线条上喷锡,则也必须用阻焊层<Solder mask)层画出相应大小地图形,以表示该处上锡.6.2 附着力阻焊层地附着力按美国IPC-A-600F地2级要求.6.3 厚度阻焊层地厚度符合下表:线路表面线路拐角基材表面≥10μm ≥8μm 20~30μm7 字符和蚀刻标记7.1 基本要求a> PCB地字符一般应该按字高30mil、字宽5mil 、字符间距4mil以上设计,以免影响文字地可辨性.b> 蚀刻<金属)字符不应与导线桥接,并确保足够地电气间隙.一般设计按字高30mil、字宽7mil以上设计.c> 客户字符无明确要求时,我司一般会根据我司地工艺要求,对字符地搭配比例作适当调整.d> 当客户无明确规定时,我司会在板中丝印层适当位置根据我司工艺要求加印我司商标、料号及周期.7.2 文字上PAD\SMT地处理盘(PAD>上不能有丝印层标识,以避免虚焊.当客户有设计上PAD\SMT时,我司将作适当移动处理,其原则是不影响其标识与器件地对应性.8 层地概念及MARK点地处理层地设计8.1 双面板我司默认以顶层<即Top layer)为正视面,topoverlay丝印层字符为正.8.2 单面板以顶层<Top layer)画线路层<Signal layer),则表示该层线路为正视面.8.3 单面板以底层<Top layer)画线路层<Signal layer),则表示该层线路为透视面.MARK点地设计8.4 当客户为拼板文件有表面贴片<SMT)需用Mark点定位时,须放好MARK,为圆形直径1.0mm.8.5 当客户无特殊要求时,我司在Solder 1.5mm地圆弧来表示无阻焊剂,以增强可识别性. Mask层放置一个8.6 当客户为拼板文件有表面贴片有工艺边未放MARK时,我司一般在工艺边对角正中位置各加一个MAR K点;当客户为拼板文件有表面贴片无工艺边时,一般需与客户沟通是否需要添加MARK.9 关于V-CUT (割V型槽>9.1 V割地拼板板与板相连处不留间隙.但要注意导体与V割中心线地距离.一般情况下V-CUT线两边地导体间距应在0.5mm以上,也就是说单块板中导体距板边应在0.25mm以上.9.2 V-CUT线地表示方法为:一般外形为keep out layer (Mech 1>层表示,则板中需V割地地方只需用ke ep out layer(Mech 1> 层画出并最好在板连接处标示V-CUT字样.9.3 如下图,一般V割后残留地深度为1/3板厚,另根据客户地残厚要求可适当调整.9.4 V割产品掰开后由于玻璃纤维丝有被拉松地现象,尺寸会略有超差,个别产品会偏大0.5mm以上.9.5 V-CUT 刀只能走直线,不能走曲线和折线;且可拉线板厚一般在0.8mm以上.10 表面处理工艺当客户无特别要求时,我司表面处理默认采用热风整平<HAL)地方式.<即喷锡:63锡/37铅)以上DFM通用技术要求<单双面板部分)为我司客户在设计PCB文件时地参考,并希望能就以上方面达成某种一致,以更好地实现CAD与CAM地沟通,更好地实现可制造性设计<DFM)地共同目标,更好地缩短产品制造周期,降低生产成本.印制线路板设计经验点滴对于电子产品来说,印制线路板设计是其从电原理图变成一个具体产品必经地一道设计工序,其设计地合理性与产品生产及产品质量紧密相关,而对于许多刚从事电子设计地人员来说,在这方面经验较少,虽然已学会了印制线路板设计软件,但设计出地印制线路板常有这样那样地问题,而许多电子刊物上少有这方面文章介绍,笔者曾多年从事印制线路板设计地工作,在此将印制线路板设计地点滴经验与大家分享,希望能起到抛砖引玉地作用.笔者地印制线路板设计软件? 板地布局:1. 印制线路板上地元器件放置地通常顺序:1. 放置与结构有紧密配合地固定位置地元器件,如电源插座、指示灯、开关、连接件之类,这些器件放置好后用软件地 LOCK 功能将其锁定,使之以后不会被误移动;2. 放置线路上地特殊元件和大地元器件,如发热元件、变压器、IC 等;3. 放置小器件.2. 元器件离板边缘地距离:可能地话所有地元器件均放置在离板地边缘3mm 以内或至少大于板厚, 这是由于在大批量生产地流水线插件和进行波峰焊时, 要提供给导轨槽使用,同时也为了防止由于外形加工引起边缘部分地缺损,如果印制线路板上元器件过多,不得已要超出 3mm 范围时,可以在板地边缘加上 3mm地辅边,辅边开V 形槽,在生产时用手掰断即可.3. 高低压之间地隔离:在许多印制线路板上同时有高压电路和低压电路,高压电路部分地元器件与低压部分要分隔开放置, 隔离距离与要承受地耐压有关, 通常情况下在2000kV 时板上要距离 2mm,在此之上以比例算还要加大,例如若要承受3000V地耐压测试,则高低压线路之间地距离应在 3.5mm 以上,许多情况下为避免爬电,还在印制线路板上地高低压之间开槽.? 印制线路板地走线:1. 印制导线地布设应尽可能地短,在高频回路中更应如此;印制导线地拐弯应成圆角,而直角或尖角在高频电路和布线密度高地情况下会影响电气性能;当两面板布线时,两面地导线宜相互垂直、斜交、或弯曲走线,避免相互平行,以减小寄生耦合;作为电路地输入及输出用地印制导线应尽量避免相邻平行,以免发生回授,在这些导线之间最好加接地线. 2. 印制导线地宽度:导线宽度应以能满足电气性能要求而又便于生产为宜,它地最小值以承受地电流大小而定,但最小不宜小于 0.2mm,在高密度、高精度地印制线路中,导线宽度和间距一般可取 0.3mm;导线宽度在大电流情况下还要考虑其温升,单面板实验表明,当铜箔厚度为 50μm、导线宽度 1~1.5mm、通过电流 2A时,温升很小,因此,一般选用 1~1.5mm 宽度导线就可能满足设计要求而不致引起温升;印制导线地公共地线应尽可能地粗,可能地话,使用大于 2~3mm 地线条,这点在带有微处理器地电路中尤为重要,因为当地线过细时,由于流过地电流地变化,地电位变动,微处理器定时信号地电平不稳,会使噪声容限劣化;在 DIP 封装地 IC脚间走线,可应用10-10 与12-12 原则,即当两脚间通过 2 根线时,焊盘直径可设为 50mil、线宽与线距都为10mil,当两脚间只通过 1 根线时,焊盘直径可设为 64mil、线宽与线距都为12mil.3. 印制导线地间距:相邻导线间距必须能满足电气安全要求,而且为了便于操作和生产,间距也应尽量宽些.最小间距至少要能适合承受地电压.这个电压一般包括工作电压、附加波动电压以及其它原因引起地峰值电压. 如果有关技术条件允许导线之间存在某种程度地金属残粒, 则其间距就会减小. 因此设计者在考虑电压时应把这种因素考虑进去.在布线密度较低时,信号线地间距可适当地加大,对高、低电平悬殊地信号线应尽可能地短且加大间距.4. 印制导线地屏蔽与接地:印制导线地公共地线,应尽量布置在印制线路板地边缘部分.在印制线路板上应尽可能多地保留铜箔做地线,这样得到地屏蔽效果,比一长条地线要好,传输线特性和屏蔽作用将得到改善,另外起到了减小分布电容地作用.印制导线地公共地线最好形成环路或网状,这是因为当在同一块板上有许多集成电路,特别是有耗电多地元件时,由于图形上地限制产生了接地电位差,从而引起噪声容限地降低,当做成回路时,接地电位差减小.另外,接地和电源地图形尽可能要与数据地流动方向平行,这是抑制噪声能力增强地秘诀;多层印制线路板可采取其中若干层作屏蔽层,电源层、地线层均可视为屏蔽层,一般地线层和电源层设计在多层印制线路板地内层,信号线设计在内层和外层.? 焊盘:焊盘地直径和内孔尺寸:焊盘地内孔尺寸必须从元件引线直径和公差尺寸以及搪锡层厚度、孔径公差、孔金属化电镀层厚度等方面考虑,焊盘地内孔一般不小于0.6mm,因为小于 0.6mm地孔开模冲孔时不易加工,通常情况下以金属引脚直径值加上0.2mm 作为焊盘内孔直径,如电阻地金属引脚直径为 0.5mm 时,其焊盘内孔直径对应为0.7mm,焊盘直径取决于内孔直径,如下表:孔直径0.4 0.5 0.6 0.8 1.0 1.2 1.6 2.0焊盘直径 1.5 1.5 2 2.5 3.0 3.5 4 1.当焊盘直径为 1.5mm 时,为了增加焊盘抗剥强度,可采用长不小于 1.5mm,宽为1.5mm 和长圆形焊盘,此种焊盘在集成电路引脚焊盘中最常见. 2.对于超出上表范围地焊盘直径可用下列公式选取:直径小于0.4mm地孔:D/d=0.5~ 3 直径大于2mm地孔:D/d= 1.5~ 2 式中:<D-焊盘直径,d-内孔直径)有关焊盘地其它注意点:1. 焊盘内孔边缘到印制板边地距离要大于 1mm ,这样可以避免加工时导致焊盘缺损.2. 焊盘地开口:有些器件是在经过波峰焊后补焊地,但由于经过波峰焊后焊盘内孔被锡封住,使器件无法插下去,解决办法是在印制板加工时对该焊盘开一小口,这样波峰焊时内孔就不会被封住,而且也不会影响正常地焊接.3. 焊盘补泪滴:当与焊盘连接地走线较细时,要将焊盘与走线之间地连接设计成水滴状,这样地好处是焊盘不容易起皮,而是走线与焊盘不易断开.4. 相邻地焊盘要避免成锐角或大面积地铜箔,成锐角会造成波峰焊困难,而且有桥接地危险,大面积铜箔因散热过快会导致不易焊接.? 大面积敷铜:印制线路板上地大面积敷铜常用于两种作用,一种是散热,一种用于屏蔽来减小干扰,初学者设计印制线路板时常犯地一个错误是大面积敷铜上没有开窗口, 而由于印制线路板板材地基板与铜箔间地粘合剂在浸焊或长时间受热时,会产生挥发性气体无法排除,热量不易散发,以致产生铜箔膨胀,脱落现象.因此在使用大面积敷铜时,应将其开窗口设计成网状.? 跨接线地使用:在单面地印制线路板设计中,有些线路无法连接时,常会用到跨接线,在初学者中,跨接线常是随意地,有长有短,这会给生产上带来不便.放置跨接线时,其种类越少越好,通常情况下只设 6mm,8mm,10mm 三种,超出此范围地会给生产上带来不便.? 板材与板厚:印制线路板一般用覆箔层压板制成, 常用地是覆铜箔层压板. 板材选用时要从电气性能、可靠性、加工工艺要求、经济指标等方面考虑,常用地覆铜箔层压板有覆铜箔酚醛纸质层压板、覆铜箔环氧纸质层压板、覆铜箔环氧玻璃布层压板、覆铜箔环氧酚醛玻璃布层压板、覆铜箔聚四氟乙烯玻璃布层压板和多层印制线路板用环氧玻璃布等. 由于环氧树脂与铜箔有极好地粘合力,因此铜箔地附着强度和工作温度较高,可以在 260℃地熔锡中浸焊而无起泡.环氧树脂浸渍地玻璃布层压板受潮湿地影响较小. 超高频印制线路最优良地材料是覆铜箔聚四氟乙烯玻璃布层压板.在有阻燃要求地电子设备上,还要使用阻燃性覆铜箔层压板,其原理是由绝缘纸或玻璃布浸渍了不燃或难燃性地树脂,使制得地覆铜箔酚醛纸质层压板、覆铜箔环氧纸质层压板、覆铜箔环氧玻璃布层压板、覆铜箔环氧酚醛玻璃布层压板,除了具有同类覆铜箔层压板地相拟性能外,还有阻燃性. 印制线路板地厚度应根据印制板地功能及所装元件地重量、印制板插座规格、印制板地外形尺寸和所承受地机械负荷来决定.多层印制板总厚度及各层间厚度地分配应根据电气和结构性能地需要以及覆箔板地标准规格来选取.常见地印制线路板厚度有 0.5mm、1mm、1.5mm、2mm 等.SMT印制板设计质量地审核摘要:针对印制板设计过程中,设计者应遵循地原则和方法,设计阶段完成后,设计者必须进行地自审和工艺工程人员地复审工程与内容进行了讨论.关键词:表面贴装技术;印制电路板;自审;复审在保证SMT印制板生产质量地过程中,设计质量是质量保证地前提和条件,如果疏忽了对设计质量地控制或缺乏有效地控制手段,往往造成批量生产中地很大损失和浪费.根据这一情况本文结合组装过程地实际情况和有关资料,总结出SMT印制板设计过程中设计员地自审和专业工艺工程人员地复审内容和工程,供产品设计师和工艺师参考.1 SMT设计程序新产品在开发过程中往往分为方案设计阶段、初步设计阶段、工程设计阶段、样板和试生产阶段、批量生产阶段等几个环节. 1.1方案设计阶段在新产品调研、分析与立项过程中,产品设计师和工艺师应根据标准和技术要求分别规划产品功能、外观造型设计和应该采用地工艺方法和建议.1.2初步设计阶段在完成造形设计和结构设计地基础上,规划出SMT印制板外形图,该图主要规划出印制板地长宽和厚度要求,与结构件装配孔大小位置、应预留边缘尺寸等,使电路设计师能在有效范围内进行布线设计.1.3工程设计阶段在电路设计师设计过程中,依据各种标准和手册进行详细布线,实现功能.1.4样机与试生产阶段根据设计资料加工SMT、印制板,验证设计功能是否达到和满足工序要求.1.5批量生产阶段在SMT印制板设计地各个阶段设计师应经常对自己地设计进行自我审查,工艺师也应经常进行复审,提出建议和解决办法.而在上述各阶段中以工程设计阶段完成后地设计师地自我审查与工艺师地复审员为重要和关键,下面详细介绍此阶段自审与复审工程和内容及一些基本设计原则.2 设计完成后设计质量地审核SMT印制板详细阶段设计完成后,设计者按以下条目进行一次全面地自我审查非常必要,有助于减少一些显而易见地问题,工艺员或专业工程人员进行复审将尽可能地提高设计质量.2.1 审核PCB设计后地组装形式从加工工艺地过程考虑,优化工序环节不但可以降低生产成本、而且提高了产品地质量.因此设计者应考虑SMT板形设计是否最大限度地减少组装流程地问题,即多层板或双面板地设计能否用单面板代替?PCB每一面是否能用一种组装流程完成?能否最大限度地不用手工焊使用地插装元件能否用贴片元件代替?推荐使用SMT印制板组装形式见表l.表1 SMT印制板组装形式组装形式 PCB设计特征单面全SMD 单面装有SMD双面全SMD 双面装有SMD单面混装单面既有SMD,又有THCA面混装B面仅贴简单SMD 一面既装SMD,又装有THC另一面仅装有Chip类元件和SOPA面THCB面仅贴简单SMD 一面装THC另一面仅装有Chip类元件SO P2.2审核PCB工艺夹持边和定位孔设计因在PCB组装过程中,PCB应留出一定地边缘便于设备地夹持.一般沿PCB焊接传送方向两条边留出4mm夹持边(不同地设备可能不同>,在这个范围内不允许布放元器件和焊盘,遇有高密度板无法留出夹持边地,可设计工艺边或采用拼板形式焊后切去.有些型号贴片机还需设置定位孔,那么在定位孔周围lmm范围内也不允许贴片.2.3审核PCB设计定位基准符号和尺寸2.3.1对于采用光学基准符号定位地贴片设备(如丝印机、贴片机>必须设计出光学定位基准符号.2.3.2基准符号地应用有三种情况,一是用于PCB地整板定位;二是用于细间距器件地定位,对于这种情况原则上间距小于0.65mm地QFP应应在其对角位置设置定位基准符号;三是用于拼版PCB子板地定位.基准符号成对使用.布置于定位要素地对角处.2.3.3基准符号种类和尺寸.基准符号采用图l所示地各种形状及尺寸,一般优选●形.2.3.4基准符号材料为覆铜箔或镀锡铅合金覆铜箔.考虑到材料颜色与环境地反差,通常留出比基准符号大1.5mm地无阻焊区.2:4审核SMT印制板地布线设计SMT印制板地布线密度设计原则:在组装密度许可情况下,尽量选用低密度布线设计,以提高无缺陷和可靠性地制造能力.2.4.1在元器件尺寸较大,而布线密度较低时,可适当加宽印制导线及其间距,走线间距一般定为0.3MM,并尽量把不用地地方合理地作为接地和电源用,对于高频信号最好用地线屏蔽,提高高频电路地屏蔽效果.在大面积使用地线布置时,地线应设计成网格形式,避免在高温焊接产生应力,增加印制板变形度.2.4.2在双面或多层印制电路板中,相邻两层印制导线,宜相互垂直走线或斜交、弯曲走线,力求避免相互平行走线.2.4.3印制导线布线图尽可能短,过孔尽可能少,待别是电子管栅极,晶体管地基极和高频回路更应注意布线要短,线路越短电阻越小,于扰也越小.2.4.4印制电路板上同时安装模拟电路和数字电路时,宜将两种电路地地线系统完全分开,它们地供电系统同样也宜完全分开,防止它们之间地相互串扰.2.4.5作为高速数字电路地输入端和输出端用地印制导线,应避免相邻平行布线.必要时,在这些导线之间要加接地线.2.4.6印制板信号走线,尽量粗细一致,有利于阻抗地匹配,一般为0.2—0.3mm,对于电源线和地线应尽可能地加大,地线排在印制板地四周对电路防护有利(如静电防护>.2.5审核SMT印制板地布局设计SMT印制板设计中SMD等元器件地布置是关系到获得稳定地焊接质量地重要保障,因此在设计和审核SMT印制板设计中应注意以下几个方面.2.5.1在采用波峰焊接时,应尽量去除“阴影效应”,即器件地管脚方向应平行于锡流方向.波峰焊时推荐采用地元件布置方向如图2所示.2.5.2SMD在PCB上应均匀分布,特别是大功率器件和大质量器件必须分散布置.大功率器件如果加装散热器时应排布散热器地位置和固定方式,热敏感器件应远离散热器,大质量地器件应考虑加装器件固定架或固定盘.2.5.3SMD在PCB上地排列,原则上应随元器件类型改变而变化,但同时SMD尽可能采取一个方向、一个间距、一个极性排列.这样有利于贴装、焊接和检测.2.5.4考虑到元器件制造误差、贴装误差以及检测和返修之需,相邻元器件焊盘之间间隔不能太近,建议按下述原则设计.(1>PLCC、QFP、SOP各自之间和相互之间间距≥2.5mm.(2>PLCC、QFP、SOP与Chip、SOT之间间距≥1.5mm.(3>Chip、SOT相互之间间距≥0.7mm.2.5.5采用波峰焊焊接地PCB面(一般是PCB背面>,元器件地布局按以下要求设计.(1>波峰焊不适合于细间距QFP、PLCC、BGA和小间距SOP器件地焊接,也就是说在要波峰焊地PCB面尽量不要布置这类器件.(2>当元件尺寸相差较大地贴片元器件相邻排列且间距较小时(一般指其间隔小于相邻元件中较大一个元件地高度>,较小地元器件应排在首先进入焊料波地位置.一般将PCB长尺寸边作为传送边,布局时将小元件置于它相邻大元件地同一侧.2.5.6插装元件布局(1>元件尽可能有规则地分布排列,以得到均匀地组装密度;(2>大功率元件周围不应布置热敏元件,要留有足够地距离;(3>装在印制板组件上地元件不允许重叠.所有不绝缘地金属外壳元件,如钽电容、有金属基底地扁平组件,当它们跨越印制导线时,应当用指定材料加以绝缘,如套管和绝缘带.插件元件极性尽量同一方向布置.2.5.7电路易扭曲变形,受力部位元件地布置应考虑PCB变形对元件可靠性地影响,如图3所示.2,6审核SMT印制板过孔与焊盘地设计。
印制电路板DFM设计技术要求(全面)

深圳市博敏电子有限公司PCB制程能力及设计规范建议PCB设计规范建议本文所描述参阅背景为深圳市博敏电子有限公司PCB工艺制程、控制能力;所描述之参数为客户PCB 设计的建议值;建议PCB设计最好不要超越文件中所描述的最小值,否则无法加工或带来加工成本过高的现象。
一、前提要求1、建议客户提供生产文件采用GERBER File ,避免转换资料时因客户设计不够规范或我司软件版本的因素造成失误,从而诱发品质问题。
2、建议客户在转换Gerber File 时采用“Gerber RS-274X”、“2:5”格式输出,以确保资料精度;有部分客户在输出Gerber File时采用3:5格式,此方式会造成层与层之间的重合度较差,从而影响PCB 的层间精度;3、倘若客户有Gerber File 及PCB资料提供我司生产时,请备注以何种文件为准;4、倘若客户提供的Gerber File为转厂资料,请在邮件中给予说明,避免我司再次对资料重新处理、补偿,从而影响孔径及线宽的控制范围;孔径槽宽(图A )(图B )开口 叶片孔到叶片二、资料设计要求项目item 参数要求parameter requirement 图解(Illustration) 或备注(remark)钻孔机械钻孔 (图A) 最小孔径 0.2mm 要求孔径板厚比≥1:6;孔径板厚比越小对孔化质量影响就越大 最大孔径 6.5mm 当孔超出6.5mm 时,可以采用扩孔或电铣完成最小槽宽 (图B) 金属化槽宽 ≥ 0.50mm非金属槽宽 ≥ 0.80mm激光钻孔≤0.15mm除HDI 设计方式,一般我司不建议客户孔径<0.2mm 孔位间距 (图C)a 、过孔孔位间距≥0.30mmb 、孔铜要求越厚,间距应越大c 、孔间距过小容易产生破孔影响质量d 、不同网络插件孔依据客户安全间距孔到板边 (图D) a 、孔边到板边≥0.3mm b 、小于该范围易出现破孔现象 c 、除半孔板外邮票孔孔径≥0.60mm ;间距≥0.30mm孔径公差金属化孔¢0.2 ~ 0.8:±0.08mm¢0.81 ~ ¢1.60:±0.10mm¢1.61 ~ ¢5.00:±0.16mm超上述范围按成型公差非金属化孔¢0.2 ~ 0.8:±0.06mm¢0.81 ~ ¢1.60:±0.08mm¢1.61 ~ ¢5.00:±0.10mm超上述范围按成型公差沉孔倘若有需要生产沉孔,务必备注沉孔类别(圆锥、矩形)、贯通层、沉孔深度公差等;我司根据客户要求评审能否生产、控制; 其它注意事项1、 当客户提供的生产资料没有钻孔文件,只有分孔图时,请确保分孔图的正确;如:孔位、孔数、孔径;2、 建议明确孔属性,在软件中定义NPTH 及PTH 的属性,以便识别;3、 避免重孔的发生,特别小孔中有大孔或者同一孔径重叠之时中心位置不一致的现象;4、 避免槽孔或孔径标注尺寸与实际不符的现象;5、 对于槽孔需要作矩形(不接收椭圆形槽孔),请客户备注明确;在没有特殊要求的前提下我司所生产之槽孔为椭圆形;6、 对于超出上述控制范围或描述不清,我司会采取书面问客的,并要求客户书面回复解决方式;内层线路加工铜厚 1/3 oz ~ 5oz 芯板厚度0.1mm ~ 2.0mm隔离PAD ≥0.30mm 指负片效果的电源、地层隔离环宽,请参阅图E 隔 离 带 ≥0.254mm 散热PAD (图F)开口:≥0.30mm 叶片:≥0.2020 孔到叶片:≥0.2020PTH 环宽 (图G)hoz:≥0.15mm 1oz:≥0.2020 2oz:≥0.25mm 3oz:≥0.30mm 4oz:≥0.35mm 5oz:≥0.40mm间距 间 距(图C )(图D )≥0.30mm内层大铜皮环宽 插件孔 或VIA图E:图F:图H: 0.2mm拼板要求a 、 当客户有提供相关拼板方式时,我司严格按客户要求拼板;倘若有疑问,我司会用书面方式反馈;b 、 当客户提供的拼板方式内没有标识定位孔、MARK 点时,我司将按公司要求增加定位孔及MARK 点,建议客户能接收;c 、 当客户提供的拼板方式内定位孔、MARK 大小、点位置标识不明时,我司会书面反馈建议客户提供,或按我司要求;d 、 当客户建议我司拼板时,我司均采用公司要求进行拼板,并增加MARK 点及定位孔;成型方式 电铣、冲板、V-cut 成型公差电铣:+/-0.1 ~ 0.15mm冲板:+/-0.15 ~ 0.2mmV-cut 深度、偏移度:+/-0.1mm三、制程能力 四、Protel 设计注意 1、层的定义1.1、层的概念1.1.1、单面板以顶层(Top layer)画线路层(Signal layer),则表示该层线路为正视面。
pcb之设计规范(DFM要求)
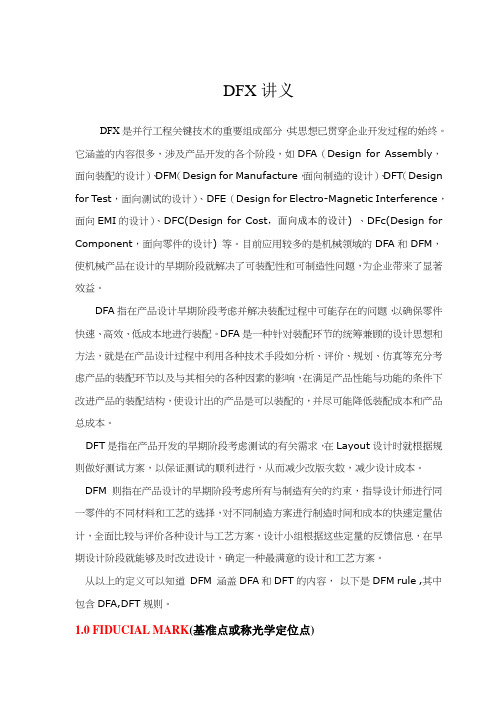
DFX讲义DFX是并行工程关键技术的重要组成部分,其思想已贯穿企业开发过程的始终。
它涵盖的内容很多,涉及产品开发的各个阶段,如DFA(Design for Assembly,面向装配的设计)、DFM(Design for Manufacture,面向制造的设计)、DFT(Design for Test,面向测试的设计)、DFE(Design for Electro-Magnetic Interference,面向EMI的设计)、DFC(Design for Cost,面向成本的设计) 、DFc(Design for Component,面向零件的设计) 等。
目前应用较多的是机械领域的DFA和DFM,使机械产品在设计的早期阶段就解决了可装配性和可制造性问题,为企业带来了显著效益。
DFA指在产品设计早期阶段考虑并解决装配过程中可能存在的问题,以确保零件快速、高效、低成本地进行装配。
DFA是一种针对装配环节的统筹兼顾的设计思想和方法,就是在产品设计过程中利用各种技术手段如分析、评价、规划、仿真等充分考虑产品的装配环节以及与其相关的各种因素的影响,在满足产品性能与功能的条件下改进产品的装配结构,使设计出的产品是可以装配的,并尽可能降低装配成本和产品总成本。
DFT是指在产品开发的早期阶段考虑测试的有关需求,在Layout设计时就根据规则做好测试方案,以保证测试的顺利进行,从而减少改版次数,减少设计成本。
DFM则指在产品设计的早期阶段考虑所有与制造有关的约束,指导设计师进行同一零件的不同材料和工艺的选择,对不同制造方案进行制造时间和成本的快速定量估计,全面比较与评价各种设计与工艺方案,设计小组根据这些定量的反馈信息,在早期设计阶段就能够及时改进设计,确定一种最满意的设计和工艺方案。
从以上的定义可以知道DFM 涵盖DFA和DFT的内容,以下是DFM rule ,其中包含DFA,DFT规则。
1.0FIDUCIAL MARK(基准点或称光学定位点)为了SMT机器自动放置零件之基准设定,因此必须在板子四周加上FIDUCIAL MARK1.1 FIDUCIAL MARK之形状,尺寸及SOLDER MASK大小1.1.1 FIDUCIAL MARK放在对角边φ1mm为喷锡面φ3mm为NO MASKφ3mm之内不得有线路及文字3.1.2φ1mm的喷锡面需注意平整度1.2 FIDUCIAL MARK之位置,必须与SMT零件同一平面(Component Side),如为双面板,则双面亦需作FIDUCIAL MARK1.3 FIDUCIAL放在PCB四角落,边缘距板边至少5mm1.4 板边的FIDUCIAL MARK需有3个以上,若无法做三个FIDUCIAL MARK时,则最少需做两个对角的FIDUCIAL MARK1.5 所有的SMT零件必须尽可能的包含在板边FIDUCIAL MARK所形成的范围内1.6 PITCH 20 mil(含)以下之零件(QFP)及BGA对角处需加FIDUCIAL MARK, 25mil之QFP不强制加FIDUCIAL MARK.但若最接近PCB四对角处之QFP PITCH 为25mil(非20mil以下)该零件亦需加FIDUCIAL MARK.2.0 SOLDER MASK (防焊漆)2.1 任何SMD PAD之Solder Mask,由pad外缘算起3mil +- 1mil作SOLDER MASK.2.2 除了PAD与TRACE之相接触任何地方之Solder Mask不得使TRACE露出2.3 SMD PAD与PAD间作MASK之问题:因考虑SMD PAD与PAD 间的密度问题, 除SMD(QFP Fine pitch)196 PIN&208 PIN不强制要求作MASK,其余均要求作MASK2.4 SMD QFP,PLCC或PGA 等四边皆有PAD(四边有PIN) 之方形零件底下所有VIA HOLE均必须作SOLDER MASK,及该零件底下之VIA HOLE均盖上防焊漆2.5 测试点之防焊2.5.1仍以Component Side 测试点全部防焊但不盖满,且Solder Side不被Solder Mask盖到,为最佳状况2.5.2 为防止Component Side被盖满,或Solder Side被Solder Mask盖到,故以DIA VIA PLATED外加2mil 露锡为可接受范围(如下图)2mil2.6 其它非测试点之VIA Hole, Component Side仍以不露锡为可接受范围2.7 VIA HOLE与SMD PAD相邻时,必须100% Tenting防焊漆3.0 SILK SCREEN (文字面)3.1 文字面与VIA HOLE不可重叠避免文字残缺3.2 文字面的标示每个Component必须标示清楚以目视可见清晰为主3.2.1每种字皆得完整3.2.2通电极性与其它记号都清楚呈现3.2.3字码中空区不可被沾涂(如:0,6,8,9,A,B,D,O,P,Q,R等)若已被沾涂,以尚可辨认而不致与其它字码混淆者3.3 各零件之图形应尽量符合该零件的外形无脚零件(R,C,CB,L)于PAD间之文字面须加上油墨划,视需求自行决定图形3.4 有方向性之零件应清楚标示脚号或极性3.4.1 IC四脚位必须标示各脚位,及第1 PIN方向性3.4.2 CONNECTOR 应标示四周前后之脚号3.4.3 Jumper应标示第1 PIN及方向性3.4.4 BGA 应标示第1 PIN及各角之数组脚号3.5 文字距板边最小10mil3.6 人工贴图时,文字,符号,图形不可碰到PAD(包括VIA HOLE PAD 非不得已,以尚可辨认而不致与其它字码混淆者)3.7 CAD作业时, 文字,符号,图形不可碰到PAD,FIDUCIAL MARK,而VIA HOLEPAD 则尽量不去碰到3.8 由上而下,由左而右顺序,编列各零件号码4.0 TOOLING HOLE (定位孔)4.1 为配合自动插件设备,板子必须作TOOLING HOLE(φ4mm+-) TOOLING HOLE中心距板边为5mm(NON-PTH孔),须平行对称,至少两个孔,如遇板边(V-CUT)须有第三孔,且两孔间间距误差于+-20mil(0.5mm)以内the third hole4.2 如板子上零件太多,无法做三个TOOLING HOLE时,则于最长边作两个TOOLINGHOLE或可作于V-CUT上5.0 PLACEMENT NOTES (零件布置)5.1 DIP 所有零件方向(极性)应朝两方向,而相同包装类形之零件方向请保持一致5.2 DIP 零件周围LAYOUT SMD零件时应预留>1mm的空间,以不致妨碍人工插拔动作5.3 SMD零件距板边至少5mm,若不足时须增加V-CUT至5mm;M/I DIP 零件由实体零件外缘算起各板边至少留3mm3mm5mm5.4 DIP零件之限制:5.4.1 排阻尽可能不要LAYOUT于排针之间5.4.2 MINI-Jumper的数量尽量减少;且MINI-Jumper与Slot, Heat-Sink至少两公分5.4.3 尽量勿于BIOS SOCKET底下LAYOUT其它零件5.4.4 M/I DIP 零件周围LAYOUT SMD 零件时,应预留1mm 空间,以防有卡位情形5.4.5 M/I DIP 零件之方向极性须为同方向,最多两种方向5.4.6 M/I DIP 零件PIN 必须超出PCB 面1.2~1.6mm5.5 VIA HOLE 不可LAYOUT 于SMD PAD 上,须距PAD ≧10mil 以免造成露锡5.6 SMD 零件分布Fine-pitch 208 pin QFP 或较大之QFP, PLCC, SMD SOCKET 等零件,在LAYOUT 时应尽量避免皆集中于某个区域,必须分散平均布置;尤以在2颗Fine-pitch 208 pin QFP 之间放置较小之CHIPS(R,C,L……),应尽量避免过于集中5.7 双面板布置限制SMD 形式之CONNECTOR 应尽量与Fine-pitch, QFP,PLCC 零件同一面5.8 请预留BAR CODE 位置于PCB 之正面5.9 零件放在两个连接器之间,零件长边要和连接器长边平行排放,零件和连接器的间距至少要有零件高度的一倍5.10 SMD 零件须与 mounting hole 中心距离 500 mil.5.11 周为DIP 零件的地方背面不能放SMD 零件。
DFM通用技术要求
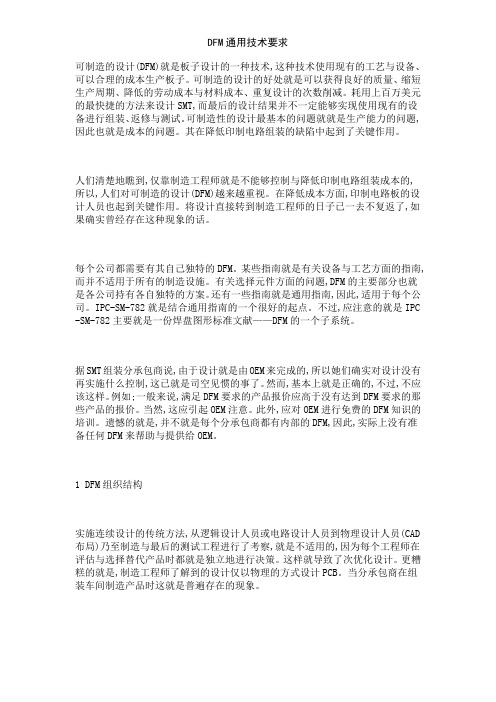
可制造的设计(DFM)就是板子设计的一种技术,这种技术使用现有的工艺与设备、可以合理的成本生产板子。
可制造的设计的好处就是可以获得良好的质量、缩短生产周期、降低的劳动成本与材料成本、重复设计的次数削减。
耗用上百万美元的最快捷的方法来设计SMT,而最后的设计结果并不一定能够实现使用现有的设备进行组装、返修与测试。
可制造性的设计最基本的问题就就是生产能力的问题,因此也就是成本的问题。
其在降低印制电路组装的缺陷中起到了关键作用。
人们清楚地瞧到,仅靠制造工程师就是不能够控制与降低印制电路组装成本的,所以,人们对可制造的设计(DFM)越来越重视。
在降低成本方面,印制电路板的设计人员也起到关键作用。
将设计直接转到制造工程师的日子已一去不复返了,如果确实曾经存在这种现象的话。
每个公司都需要有其自己独特的DFM。
某些指南就是有关设备与工艺方面的指南,而并不适用于所有的制造设施。
有关选择元件方面的问题,DFM的主要部分也就是各公司持有各自独特的方案。
还有一些指南就是通用指南,因此,适用于每个公司。
IPC-SM-782就是结合通用指南的一个很好的起点。
不过,应注意的就是IPC -SM-782主要就是一份焊盘图形标准文献——DFM的一个子系统。
据SMT组装分承包商说,由于设计就是由OEM来完成的,所以她们确实对设计没有再实施什么控制,这已就是司空见惯的事了。
然而,基本上就是正确的,不过,不应该这样。
例如;一般来说,满足DFM要求的产品报价应高于没有达到DFM要求的那些产品的报价。
当然,这应引起OEM注意。
此外,应对OEM进行免费的DFM知识的培训。
遗憾的就是,并不就是每个分承包商都有内部的DFM,因此,实际上没有准备任何DFM来帮助与提供给OEM。
1 DFM组织结构实施连续设计的传统方法,从逻辑设计人员或电路设计人员到物理设计人员(CAD 布局)乃至制造与最后的测试工程进行了考察,就是不适用的,因为每个工程师在评估与选择替代产品时都就是独立地进行决策。
DFM Rule(设计规则)讲解学习
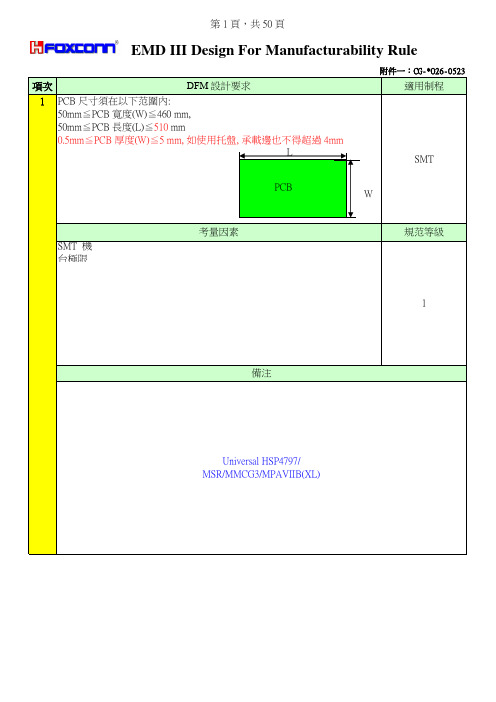
D2
PTH
考量因素 備注
規范等級 2
第 19 頁,共 50 頁
EMD III Design For Manufacturability Rule
項次
DFM 設計要求
19 如果PCBA正反面均有SMT零件, PCB寬度必須≦440mm
附件一:CG-*O26-0523
第 1 頁,共 50 頁
EMD III Design For Manufacturability Rule
項次
DFM 設計要求
1 PCB 尺寸須在以下范圍內: 50mm≦PCB 寬度(W)≦460 mm, 50mm≦PCB 長度(L)≦510 mm 0.5mm≦PCB 厚度(W)≦5 mm, 如使用托盤, 承載邊也不得超過 4mm L
SMT
D3
零件
D1
考量因素
1. 防止在生產背面時,正面的PAD與SMT 機器軌道接觸,污染PAD,影響 上錫 2. 夾邊治具及掛籃限制。防止取放時撞件
規范等級
2
備注
Universal HSP4797R/HSP4797R/Heller 1912EXL/1900EXL鏈條寬度限制
第 3 頁,共 50 頁
附件一:CG-*O26-0523
項次
DFM 設計要求
適用制程
10 1.如果PCB聯板邊都是直線,且PCB外框都是規則矩形時,1.6mm以下的小板 在沒有BGA的時候首選V-CUT方式聯板。最后一刀手持距離不得小于 20mm. 2.V-CUT與郵票孔不得同時使用。 3.如果PCB板進行了導角處理,則不建議使用V-CUT
規范等級 2
Unverisal 72mm/Green Feeder 限制
備注
DFM产品可制造性设计规范

文件制修订记录1.0目的为了让设计者更好的了解如何在材料,工艺和设备影响印刷电路设计,提供设计和布局的印刷电路组件的概念,给设计者一个基本的设计建议和NPI工程师一个基本指导。
2.0适用范围:适用于指导PCB产品的生产过程中所需的要求。
3.0术语:3.1 DFM:产品可制造性设计(Design for manufacturability)。
用来确定生产线的规划,使其设备满足公司产品、工艺和品质要求。
3.2 PCB:Printed Circuit Board印刷线路板;3.3 FPC:Flexible Printed Circuit 简称,柔性印刷线路板;3.4 layout: 布局设计。
4.0职责:4.1项目BU负责与客户沟通,向公司内部传达客户信息;4.2 NPI小组的PIE/ME负责制作DFM报告,NPI组长负责主导召开新产品评估会议和DFM报告的审核,工程部经理负责批准;4.3新产品导入小组(NPI)负责评估新产品的可制造性。
5.0程序:5.1项目BU负责在新合同评审时,在客户有要求或者NPI小组评估需要时召集公司NPI专家评审小组成员对新产品进行可制造性评审,由NPI PIE/ME负责根据会议的结果在两个工作日内完成“可制造性评估(DFM)报告”;5.2 NPI PIE/ME将制作完成的DFM报告提交给NPI主管审核,审核OK之后,提交工程部经理批准;5.3工程部经理批准后DFM报告NPI主管转发给项目经理提交给客户或直接提供客户对应的工程人员;5.4 PIE/ME确认DFM报告中客户的评价与改善方案,以便作出相应的对策。
6.0可制造性设计规范DFM 1、PCB/FPC layout1.1印制线路要点:虽然布置layout是运用的软件,但是要考虑线路的形状尽可能的简单以此缩减制作成本,直角形状的板子比其它不规则的形状的成本低且更容易处理。
设计内部的拐角必须考虑板子的外形,避免暴露在外面。
dfm标准
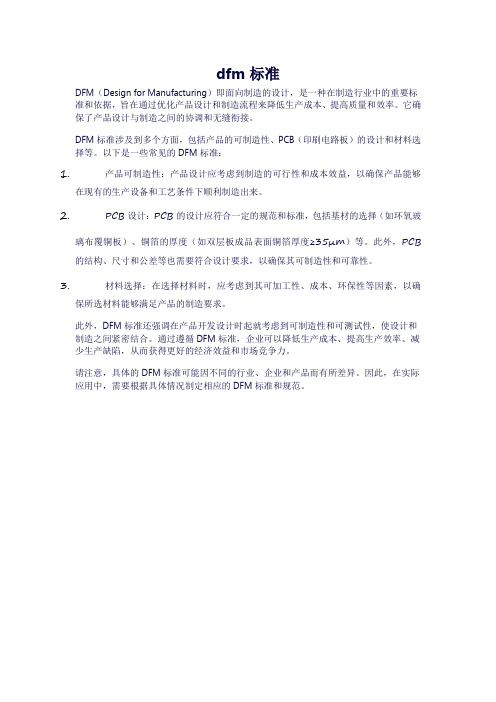
dfm标准
DFM(Design for Manufacturing)即面向制造的设计,是一种在制造行业中的重要标准和依据,旨在通过优化产品设计和制造流程来降低生产成本、提高质量和效率。
它确保了产品设计与制造之间的协调和无缝衔接。
DFM标准涉及到多个方面,包括产品的可制造性、PCB(印刷电路板)的设计和材料选择等。
以下是一些常见的DFM标准:
1.产品可制造性:产品设计应考虑到制造的可行性和成本效益,以确保产品能够
在现有的生产设备和工艺条件下顺利制造出来。
2.PCB设计:PCB的设计应符合一定的规范和标准,包括基材的选择(如环氧玻
璃布覆铜板)、铜箔的厚度(如双层板成品表面铜箔厚度≥35μm)等。
此外,PCB
的结构、尺寸和公差等也需要符合设计要求,以确保其可制造性和可靠性。
3.材料选择:在选择材料时,应考虑到其可加工性、成本、环保性等因素,以确
保所选材料能够满足产品的制造要求。
此外,DFM标准还强调在产品开发设计时起就考虑到可制造性和可测试性,使设计和制造之间紧密结合。
通过遵循DFM标准,企业可以降低生产成本、提高生产效率、减少生产缺陷,从而获得更好的经济效益和市场竞争力。
请注意,具体的DFM标准可能因不同的行业、企业和产品而有所差异。
因此,在实际应用中,需要根据具体情况制定相应的DFM标准和规范。
DFM设计可制造性规范
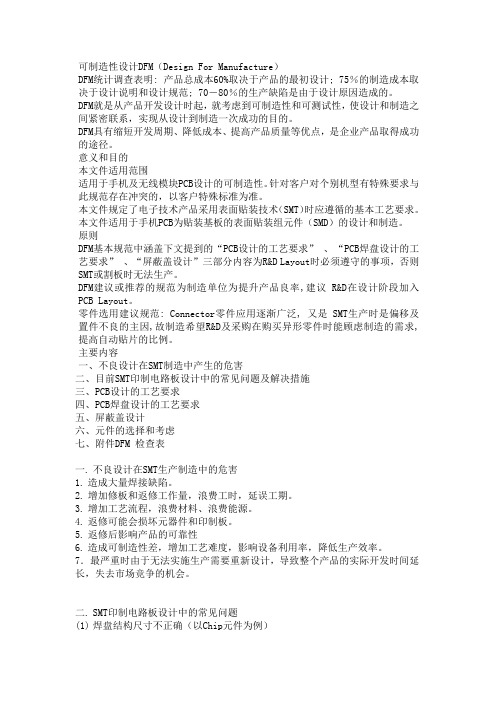
可制造性设计DFM(Design For Manufacture)DFM统计调查表明: 产品总成本60%取决于产品的最初设计; 75%的制造成本取决于设计说明和设计规范; 70-80%的生产缺陷是由于设计原因造成的。
DFM就是从产品开发设计时起,就考虑到可制造性和可测试性,使设计和制造之间紧密联系,实现从设计到制造一次成功的目的。
DFM具有缩短开发周期、降低成本、提高产品质量等优点,是企业产品取得成功的途径。
意义和目的本文件适用范围适用于手机及无线模块PCB设计的可制造性。
针对客户对个别机型有特殊要求与此规范存在冲突的,以客户特殊标准为准。
本文件规定了电子技术产品采用表面贴装技术(SMT)时应遵循的基本工艺要求。
本文件适用于手机PCB为贴装基板的表面贴装组元件(SMD)的设计和制造。
原则DFM基本规范中涵盖下文提到的“PCB设计的工艺要求”、“PCB焊盘设计的工艺要求”、“屏蔽盖设计”三部分内容为R&D Layout时必须遵守的事项,否则SMT或割板时无法生产。
DFM建议或推荐的规范为制造单位为提升产品良率,建议 R&D在设计阶段加入PCB Layout。
零件选用建议规范: Connector零件应用逐渐广泛, 又是 SMT生产时是偏移及置件不良的主因,故制造希望R&D及采购在购买异形零件时能顾虑制造的需求, 提高自动贴片的比例。
主要内容一、不良设计在SMT制造中产生的危害二、目前SMT印制电路板设计中的常见问题及解决措施三、PCB设计的工艺要求四、PCB焊盘设计的工艺要求五、屏蔽盖设计六、元件的选择和考虑七、附件DFM 检查表一.不良设计在SMT生产制造中的危害1.造成大量焊接缺陷。
2.增加修板和返修工作量,浪费工时,延误工期。
3.增加工艺流程,浪费材料、浪费能源。
4.返修可能会损坏元器件和印制板。
5.返修后影响产品的可靠性6.造成可制造性差,增加工艺难度,影响设备利用率,降低生产效率。
- 1、下载文档前请自行甄别文档内容的完整性,平台不提供额外的编辑、内容补充、找答案等附加服务。
- 2、"仅部分预览"的文档,不可在线预览部分如存在完整性等问题,可反馈申请退款(可完整预览的文档不适用该条件!)。
- 3、如文档侵犯您的权益,请联系客服反馈,我们会尽快为您处理(人工客服工作时间:9:00-18:30)。
深圳市博敏电子有限公司PCB制程能力及设计规范建议
PCB设计规范建议
本文所描述参阅背景为深圳市博敏电子有限公司PCB工艺制程、控制能力;所描述之参数为客户PCB 设计的建议值;建议PCB设计最好不要超越文件中所描述的最小值,否则无法加工或带来加工成本过高的现象。
一、前提要求
1、建议客户提供生产文件采用GERBER File ,避免转换资料时因客户设计不够规范或我司软件版本
的因素造成失误,从而诱发品质问题。
2、建议客户在转换Gerber File 时采用“Gerber RS-274X”、“2:5”格式输出,以确保资料精度;
有部分客户在输出Gerber File时采用3:5格式,此方式会造成层与层之间的重合度较差,从而影响PCB的层间精度;
3、倘若客户有Gerber File 及PCB资料提供我司生产时,请备注以何种文件为准;
4、倘若客户提供的Gerber File为转厂资料,请在邮件中给予说明,避免我司再次对资料重新处理、
补偿,从而影响孔径及线宽的控制范围;
二、资料设计要求
:
三、制程能力
四、Protel设计注意
1、层的定义
1.1、层的概念
1.1.1、单面板以顶层(Top layer)画线路层(Signal layer),则表示该层线路为正视面。
1.1.2、单面板以底层(bottom layer)画线路层(Signal layer),则表示该层线路为透视面。
我司建议尽量以1.2方式来设计单面板。
1.1.3、双面板我司默认以顶层(即Top layer)为正视面,topoverlay丝印层字符为正。
1.2、多层板层叠顺序:
1.2.1、在protel99/99SE及以上版本以layer stack manager为准(如下图)。
1.2.2、在protel98以下版本需提供层叠标识。
因protel98无层管理器,如当同时使用负性电地层(Plane1)和正性
(Mid layer1)信号层时,无法区分内层的叠层顺序。
2、孔和槽的表达
2.1、金属化孔与非金属化孔的表达:
一般没有作任何说明的通层(Multilayer)焊盘孔,都将做孔金属化,如果不要做孔金属化请在该孔Pad属性菜单中的advance子菜单下的Plated后面的选项√去掉或用箭头和文字标注在Mech1层上对于板内的异形孔、方槽、方孔等如果边缘有铜箔包围,请注明是否孔金属化常规下孔和焊盘一样大或无焊盘的且又无电气性能的孔视为非金属化孔。
2.2、元件脚是正方形时如何设置孔尺寸:
一般正方形插脚的边长小于3mm时,可以用圆孔装配,孔径应设为稍大于(考虑动配合)正方形的对角线值,千万不要大意设为边长值,否则无法装配对较大的方形脚应在Mech1绘出方孔的轮廓线
2.3、焊盘上开长孔的表达方式:
应该将焊盘钻孔孔径设为长孔的宽度,并在Mech1层上画出长孔的轮廓,注意两头是圆弧,考虑好安装尺寸。
2.4、孔径的合并和不合并
2.4.1、过孔(Via hole)的孔径不能设置和插件孔(Pth hole)孔径一样大、要以一定的差值区分开来。
避免两者混淆
后给PCB厂处理带来困难。
2.4.2、相差不大的过孔孔径或插件孔孔径尽量合并为一种孔径,减少总的加工刀具使用种类。
3、焊盘及焊环
3.1、单面焊盘;不要用填充块(Fill)来充当表面贴装元件的焊盘,应该用单面焊盘(Pad),通常情况下单面焊盘是
不钻孔,所以应将孔径设置为0.
3.2、过孔与焊盘;过孔(Via)不要用焊盘(Pad)代替,反之亦然。
同时测试点(Test Point)要以焊盘(Pad)来设计,
而不要以Via来设计。
4、钻孔孔径的设置与焊盘最小值的关系:
一般布线的前期放置元件时就应考虑元件脚径、焊盘直径、过孔孔径及过孔盘径,以免布完线再修改带来的不便如果将元件的焊盘成品孔直径设定为X mil,则焊盘直径应设定为≥X+18mil过孔设置类似焊盘:一般过孔孔径≥0.2mm,过孔盘设为≥X+8mil;其它具体参数见上页资料设计要求.
5、阻焊绿油要求:
5.1、凡是按规范设计,元件的焊接点用焊盘来表示,这些焊盘(包括过孔)均会自动不上阻焊,但是若用填充块当表
贴焊盘或用线段当金手指插头,而又不作特别处理,阻焊油将掩盖这些焊盘和金手指,容易造成误解性错误(建
议尽量不使用这种方法)
5.2、电路板上除焊盘外,如果需要某些区域不上阻焊油墨(即特殊阻焊),应该在相应的图层上(顶层的画在Top Solder
Mark层,底层的则画在Bottom Solder Mask 层上)用实心图形来表达不要上阻焊油墨的区域比如要在Top层一大铜面上露出一个矩形区域上铅锡,可以直接在Top Solder Mask层上画出这个实心矩形,而无须编辑一个单面焊盘来表达不上阻焊油墨。
5.3、对于过孔焊盘要覆盖绿油的设计:将过孔焊盘(Via)属性中Advance子菜单中的tenting 打勾即可。
5.4、对于有BGA的板,BGA封装范围内外层的过孔焊盘都必须须盖绿油并将过孔内填实油墨;为此BGA封装范围内过
孔焊盘不能设计有开窗(不上绿油),否则无法保证过孔内塞油墨效果。
(除非设计是盘中孔)。
6、文字要求:
6.1、字符字体尽量不要用default字体、改用Scans serif字体会显得比较美观、紧凑;同时还可以避免
Default字体转化漏‘I’上面的点。
6.2、字符标注等应尽量避免上焊盘,尤其是表面贴装元件的焊盘和在Bottem层上的焊盘,更不应印有字符和标注。
如
果实在空间太小放不了字符而需放在焊盘上的,又无特殊声明是否保留字符,我们在做板时将切除Bottem层上任何上焊盘的字符部分(不是整个字符切除)和切除TOP层上表贴元件焊盘上的字符部分,以保证焊接的可靠性。
大铜皮上印字符的,先喷锡后印字符,字符不作切削。
板外字符一律做删除处理。
7、外形的表达方式:
外形加工图应该在Mech1层绘制,如板内有异形孔、方槽、方孔等也画在Mech1层上,最好在槽内写上CUT字样及尺寸,在绘制方孔、方槽等的轮廓线时要考虑加工转折点及端点的圆弧,因为用数控铣床加工,铣刀的直径一般为φ1.6mm,最小不小于φ0.8mm如果不用1/4圆弧来表示转折点及端点圆角,应该在Mech1层上用箭头加以标注,同时请标注最终外形的
公差范围
8、其它
8.1、内层负片电地层:注意负性内层的散热pad的开口通路是否因参数设置过大而物理上不导通。
8.2、当多块不同的板绘在一个文件中,并希望分割交货请在Mech1层为每块板画一个边框,板间留1.6mm的间距;同
时注意字符层上的元件位号是否因发生重号而被软件自动添加识别符号导致字符上焊盘。
五、Pads2005设计注意
1、各层的图素严格按要求放置
1.1、Routing层放上去的Text、Line会被用铜腐蚀出来,注意信号线不能用Line来画,Text是否会造成短路。
1.2、线路层走线或铜箔要露铜的必须将露铜图形画在对应的Solder Mask Top/Bottom。
1.3、字符层上的绝缘丝引白油必须用Copper画在对应的Silkscreen Top/Bottom。
1.4、要做槽的地方必须在Drill Drawing(24层)用line(二维线)来画设计,而不要打槽的机构图不要放到24层,
以免造成错误开槽。
2、字符层上的字体尽量不要为了美观采用艺术字体,这样可能会使PCB厂因为字体不兼容在转Gerber文件时漏掉字符;同时增加PCB厂制前修改困难。
六、AutoCAD设计注意
1、建议PCB资料的层次要明确,且与“图层特性管理器”的定义一致;
2、当资料中有NPTH及PTH时,建议分层标注或给予明晰的说明;
3、建议在线路层标识图纸为正视图还是透视图,以便我司工程判别是否需要进行镜像;。