连续变断面挤压制品组织的变化规律
连续挤压原理
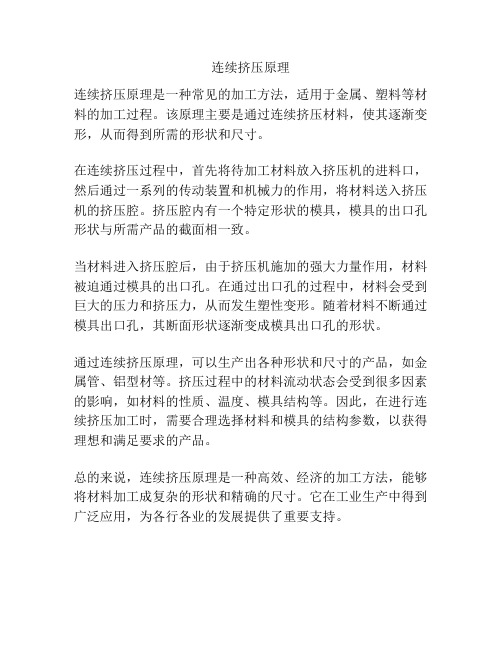
连续挤压原理
连续挤压原理是一种常见的加工方法,适用于金属、塑料等材料的加工过程。
该原理主要是通过连续挤压材料,使其逐渐变形,从而得到所需的形状和尺寸。
在连续挤压过程中,首先将待加工材料放入挤压机的进料口,然后通过一系列的传动装置和机械力的作用,将材料送入挤压机的挤压腔。
挤压腔内有一个特定形状的模具,模具的出口孔形状与所需产品的截面相一致。
当材料进入挤压腔后,由于挤压机施加的强大力量作用,材料被迫通过模具的出口孔。
在通过出口孔的过程中,材料会受到巨大的压力和挤压力,从而发生塑性变形。
随着材料不断通过模具出口孔,其断面形状逐渐变成模具出口孔的形状。
通过连续挤压原理,可以生产出各种形状和尺寸的产品,如金属管、铝型材等。
挤压过程中的材料流动状态会受到很多因素的影响,如材料的性质、温度、模具结构等。
因此,在进行连续挤压加工时,需要合理选择材料和模具的结构参数,以获得理想和满足要求的产品。
总的来说,连续挤压原理是一种高效、经济的加工方法,能够将材料加工成复杂的形状和精确的尺寸。
它在工业生产中得到广泛应用,为各行各业的发展提供了重要支持。
(完整版)连续挤压与连续铸挤
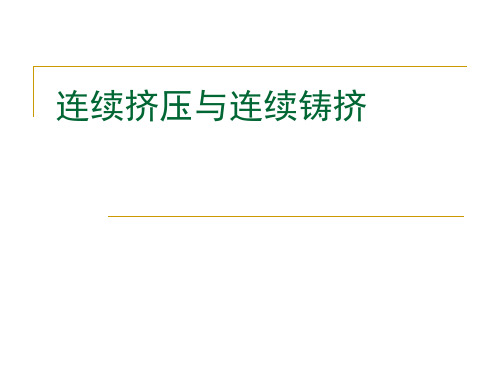
(4)具有较为广泛的适用范围。从材料种类来看,Coform 连续挤压法已成功地应用于铝及软铝合金、铜及部分铜 合金的挤压生产;坯料的形状可以是杆状、颗粒状,也 可以是熔融状态;制品种类包括管材、线材、型材,以 及以铝包钢线为典型代表的包覆材料。
(5)设备紧凑,占地面积小,设备造价及基建费用较低。 由上所述可知,Conform连续挤压法具有许多常规
挤压制品
压轮
槽封块 挤压靴
这一方法称为Conform连续挤压法,是由 英国原子能局(UKAEA)斯普林菲尔德研究所 的格林(D.Green)于1971年提出来的。
2.2 Conform连续挤压特点
(1)由于挤压型腔与坯料之间的摩擦大部分得到有效利用,挤压变 形的能耗大大降低。常规正挤压法中,用于克服挤压筒壁上的摩 擦所消耗的能量可达整个挤压变形能耗的30%以上,有的甚至可 达50%。据计算,在其它条件基本相同的条件下,Conform连续 挤压可比常规正挤压的能耗降低30%以上。
(4)挤压轮凹槽表面、槽封块、堵头等始终处于高 温高摩擦状态,因而对工模具材料的耐磨耐热性 能要求高。
(5)由于设备结构与挤压工作原理上的特点,工模 具更换比常规挤压困难。
(6)对设备液挤压的应用
Conform连续挤压技术在铝及铝合金、铜及铜合金等有色金属加 工上具有较为广泛的应用,主要体现在以下几个方面。
(2)挤压筒应具有无限连续工作长度……
采用槽轮(挤压轮)来代替槽块。随 着挤压轮的不断旋转,即可获得 “无限”工作长度的挤压筒。
挤压时,借助于挤压轮凹槽表面 的主动摩擦力作用,坯料(一般为 连续线杆)连续不断地被送入,通 过安装在挤压靴(模座)上的模子挤 出制品。
连续挤压技术

连续挤压技术文稿归稿存档编号:[KKUY-KKIO69-OTM243-OLUI129-G00I-FDQS58-连续挤压技术一、连续挤压技术的原理及应用挤压是有色金属、钢铁材料生产与零件生产、零件成型加工的主要生产方法之一,也是各种复合材料、粉末材料等先进材料制备与加工的重要方法。
有色金属挤压制品在国民经济的各个领域获得了广泛的应用。
连续挤压技术是挤压成型技术的一项较新的技术,以连续挤压技术为基础发展起来的连续挤压复合、连续铸挤技术为有色金属管、棒、型、线及其复合材料的生产提供了新的技术手段和发展空间。
1.连续挤压技术的原理传统的挤压方法主要有正向挤压、反向挤压、静液挤压等。
以正挤压为例,如图1所示:图1. 正向挤压正向挤压时,挤压杆运动方向与挤压产品的出料方向一致,坯料与挤压筒之间产生相对滑动,存在很大的摩擦,这种摩擦阻力使金属流动不均匀,从而给挤压制品的质量带来了不利影响,导致挤压制品组织性能不均匀,挤压能耗增加,由于强烈的摩擦发热作用,限制了挤压速度且加快了模具的磨损。
反向挤压和静液挤压等方法虽然从不同的角度对正向挤压进行了改进,但是这些传统的挤压方法都存在一个共同的缺点,即生产的不连续性,制品长度受到限制,前后坯料的挤压之间需要进行分离压余、填充坯料等一系列辅助操作,影响了挤压生产的效率。
为了解决传统挤压中的问题,20世纪70年代人们开始致力于挤压生产的连续性研究。
1971年,英国原子能局的D.Green发明了CONFORM连续挤压方法。
此方法以颗粒料或杆料为坯料,巧妙地利用了变形金属与工具之间的摩擦力。
如图2所示,由旋转的挤压轮上的矩形断面槽和固定模座所组成的环形通道起到普通挤压法中挤压筒的作用,当挤压轮旋转时,借助于槽壁上的摩擦力不断地将杆状坯料送入而实现连续挤压。
连续挤压时坯料与工具表面的摩擦发热较为显着,因此,对于低熔点金属,如铝及铝合金,不需进行外部加热即可使变形区的温度上升400~500℃而实现热挤压。
连续挤压技术
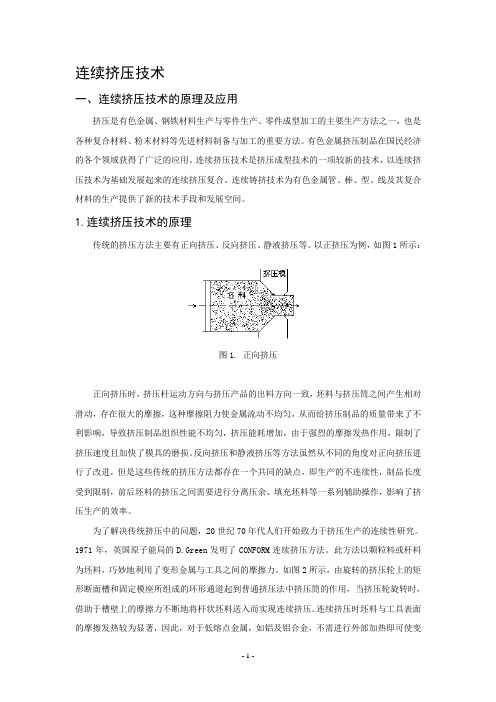
连续挤压技术一、连续挤压技术的原理及应用挤压是有色金属、钢铁材料生产与零件生产、零件成型加工的主要生产方法之一,也是各种复合材料、粉末材料等先进材料制备与加工的重要方法。
有色金属挤压制品在国民经济的各个领域获得了广泛的应用。
连续挤压技术是挤压成型技术的一项较新的技术,以连续挤压技术为基础发展起来的连续挤压复合、连续铸挤技术为有色金属管、棒、型、线及其复合材料的生产提供了新的技术手段和发展空间。
1.连续挤压技术的原理传统的挤压方法主要有正向挤压、反向挤压、静液挤压等。
以正挤压为例,如图1所示:图1. 正向挤压正向挤压时,挤压杆运动方向与挤压产品的出料方向一致,坯料与挤压筒之间产生相对滑动,存在很大的摩擦,这种摩擦阻力使金属流动不均匀,从而给挤压制品的质量带来了不利影响,导致挤压制品组织性能不均匀,挤压能耗增加,由于强烈的摩擦发热作用,限制了挤压速度且加快了模具的磨损。
反向挤压和静液挤压等方法虽然从不同的角度对正向挤压进行了改进,但是这些传统的挤压方法都存在一个共同的缺点,即生产的不连续性,制品长度受到限制,前后坯料的挤压之间需要进行分离压余、填充坯料等一系列辅助操作,影响了挤压生产的效率。
为了解决传统挤压中的问题,20世纪70年代人们开始致力于挤压生产的连续性研究。
1971年,英国原子能局的D.Green发明了CONFORM连续挤压方法。
此方法以颗粒料或杆料为坯料,巧妙地利用了变形金属与工具之间的摩擦力。
如图2所示,由旋转的挤压轮上的矩形断面槽和固定模座所组成的环形通道起到普通挤压法中挤压筒的作用,当挤压轮旋转时,借助于槽壁上的摩擦力不断地将杆状坯料送入而实现连续挤压。
连续挤压时坯料与工具表面的摩擦发热较为显著,因此,对于低熔点金属,如铝及铝合金,不需进行外部加热即可使变形区的温度上升400~500℃而实现热挤压。
图2. 连续挤压原理在常规的正挤压中,变形是通过挤压轴将所需的挤压力直接施加于坯料上来实现的,由于挤压筒的长度有限,要实现无间断的连续挤压是不可能的。
纯铜连续挤压全过程的组织演变
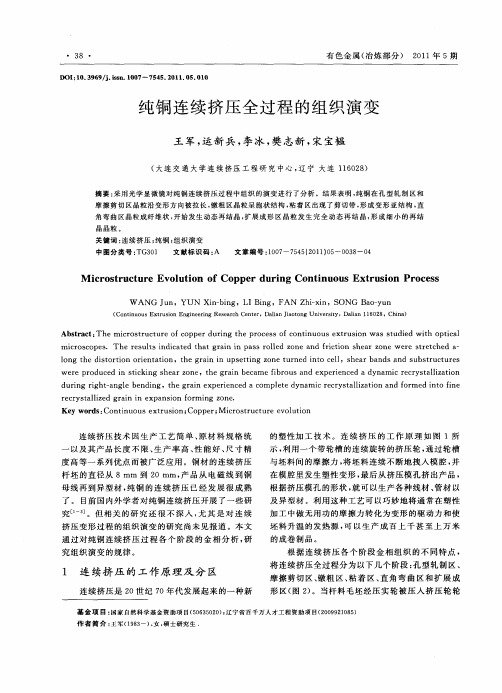
以及 其 产 品长 度 不 限 、 产 率 高 、 能 好 、 寸精 生 性 尺
度 高 等一 系列 优点 而被 广 泛应 用 。铜材 的连续 挤压 杆 坯 的 直径从 8mm 到 2 0mm, 品 从 电 磁 线 到 铜 产 母 线再 到异 型材 , 铜 的连 续 挤 压 已经 发展 很 成熟 纯 了 。 目前 国内外 学者 对纯 铜 连续 挤压 开展 了一 些 研 究 [ 。但 相关 的研 究 还 很 不 深 入 , 其 是 对 连 续 1 ] 尤
角 弯 曲 区 晶 粒 成 纤 维 状 , 始 发 生 动 态 再 结 晶 , 展 成 形 区 晶 粒 发 生 完 全 动 态 再 结 晶 , 成 细 小 的 再 结 开 扩 形
晶晶粒 。
关 键 词 : 续 挤 压 ; 铜 ; 织 演 变 连 纯 组
中 图 分 类 号 : G3 1 T 0 文 献 标 识码 : A 文 章 编 号 :0 7 5 5 2 1 ) 5 0 8 4 1 0 —7 4 (0 1 0 —0 3 —0
( n iu u tu in En n e ig Re e rh Ce e ,DainJa o g U nv r i Co tn o sEx r so gie rn s a c ntr l iotn iest a y,Dain 1 6 2 l 1 0 8,Chn ) a ia
・3 8・
DOI 1 . 9 9 j i n 1 0 - 7 4 . 0 1 0 . 1 :0 3 6 /.s . 0 7- 5 5 2 1 . 5 0 0 s
有 色金 属 ( 冶炼 部分 ) 2 1 0 1年 5期
纯 铜 连 续 挤 压 全 过 程 的组 织演 变
王 军 , 新 兵 , 冰 , 志 新 , 宝韫 运 李 樊 宋
金属材料加工考试重点

4)适当的温度
轧机:依靠两根或多根旋转圆柱体将物体拽入使 它发生塑性变形的机械装置称为轧机。
轧制过程 轧辊与轧件相互作用,轧件被摩擦力拽入旋转的轧辊间,受到压 缩而发生塑性变形的过程称为轧制过程。 几何变形区的金属流动
(1) l/h增大,变形深入,沿高度方向上应力和变形趋于均匀,变形 前的垂直横截面,变形后还是垂直横截面,宽度可以忽略不记, 这又称作“平断面假设”;
(2) 质点轧制线方向上的运动速度(考察5个关键的横截面); (3) 附加应力分析(在轧制线方向,由于金属流动不均匀而产生 的)。方法:考查变形区与外端相互作用而引起的附加应力。
超塑性成形工艺的应用
(3)挤压和模锻。高温合金及钛合金在常态下塑性很差,变形抗力大,不均 匀变形引起各向异性的敏感性强,通常的成形方法较难成形,材料损耗极 大,致使产品成本很高。如果在超塑性状态下进行模锻,就完全克服了上 述缺点,节约材料,降低成本。
超塑性模锻工艺特点:
(1)扩大了可锻金属材料种类。如过去只能采用锻造成形的镍基合金,也可 以进行超塑性模锻成形。 (2)金属填充模膛的性能好,可锻出尺寸精度高、机械加工余量小甚至不用 加工的零件。 (3)能获得均匀细小的晶粒组织,零件力学性能均匀一致。 (4)金属的变形抗力小,可充分发挥中、小设备的作用。
原因:在变形区,高向上流动不均匀,而在外端,高向上速度却要
变成一样,因此外端对变形区出来的部分必然引起附加应力
2.3 厚轧件的变形特点
(1) l/h减小,变形不深入,只发生表面变形,呈
双鼓形; (2) 质点轧制线方向上的运动速度(考察5个关 键的横截面); (3) 附加应力分布(在轧制线方向,由于金属流 动不均匀而产生的)产生的后果
连续挤压技术理论发展概述

连续挤压技术理论发展概述本学期通过对连续挤压的初步学习,对该项技术页有了初步的认知。
下面对其发展及一些理论技术简单做以概述。
连续挤压技术是塑性加工新方法,被誉为有色金属加工技术的一次革命。
该技术从提出到工业化应用经历了不断完善,提高和应用领域扩展过程。
我国自1984年开始引进国外设备,当时主要用于电冰箱铝管的生产,为了加快消化吸收过程,1986年将软铝连续挤压技术的研究列为国家“七五”重点科技攻关项目。
通过近20余年的不懈努力,在设备类型方面,从250单槽挤压发展到350双槽挤压和包覆;在产品的品种方面,从单一材料发展到多种材料的复合,实现了直接包覆和间接包覆;在成形的金属材料方面,从铝、铜扩展到铝合金及铜合金,先后研制成功了KLJ250、TL250、TLJ300、LLJ300、TLJ350、SLJB350、,TLJ400生产线,分别用于加工铝及合金的管材与型材、铝包钢丝、光纤护套、有线电视同轴电缆(CATV)、铁路通信信号电缆、电力机车铜合金接触导线、光纤复合架空地线(OPGW)、优质铜扁线、铜母线、铜型材等产品,形成了完全国产化的连续挤压和连续包覆系列成套设备和具有自主产权的关键技术,使我国在该方面的研究达到了目前的国际先进水平,在某些方面已处于世界领先地位。
在该研究方向的一系列研究成果曾两次荣获国家科技进步奖,六次荣获省部级科技进步奖。
截至目前为止,为国内外装备了250余条生产线,产品遍及国内25个省、直辖市以及亚洲、欧洲、澳洲等十几个国家和地区。
我国连续挤压技术历经20余年的发展,已经从开始时的仿制、改进,到拥有自主产权的再创新,产品升级,成功打人该技术的原发地欧洲市场,其中凝结了学术界的一批有识之士的智慧和汗水,得益于一批独具慧眼和胆识的企业家的信赖和支持,使我国的连续挤压技术和装备得以快速发展,进口设备逐渐退出我国市场。
据统计和测算,采用国产连续挤压技术和装备,已经为我国的企业创造近百亿元的产值,节省外汇上亿美元。
金属在挤压过程中的流动特点PPT课件

挤压变形区的金属流动
变形区金属受到强烈的三向压 应力作用,有利于塑性变形。
金属流动方向与挤压力方向一 致,流动速度逐渐加快。
变形区金属的温度和变形程度 对流动行为有显著影响。
挤压变形区外的金属流动
变形区外金属受到较小的压应力作用, 塑性变形程度较低。
变形区外金属的温度和变形程度对流 动行为的影响较小。
https://
2023 WORK SUMMARY
金属在挤压过程中的 流动特点ppt课件
REPORTING
https://
目录
• 引言 • 金属流动特点概述 • 挤压过程中金属的流动规律 • 金属流动对挤压制品质量的影响 • 控制金属流动的工艺措施 • 总结与展望
挤压力的大小和分布直接影响金属的流动 方向和变形程度。
模具的形状和尺寸
挤压温度和速度
模具的形状和尺寸对金属的流动具有导向 作用,不同的模具设计会导致不同的金属 流动行为。
挤压温度和速度对金属的塑性和流动性具 有重要影响,过高的温度或速度可能导致 金属流动不稳定或产生缺陷。
PART 03
挤压过程中金属的流动规 律
模具内应力对力学性能的影响
模具内的应力分布直接影响制品的力学性能,如残余应力、内应力等会导致制品在使用过 程中出现变形、开裂等问题。
金属组织变化对力学性能的影响
挤压过程中金属的组织结构会发生变化,如晶粒细化、相变等会对制品的力学性能产生影 响,合理的组织结构能够提高制品的力学性能。
PART 05
控制金属流动的工艺措施
点。
挤压工艺广Байду номын сангаас应用于铝、铜、钢 等金属的加工领域,如建筑、交
通、电子等行业。
PART 02
C194合金连续挤压全过程的组织与性能演变
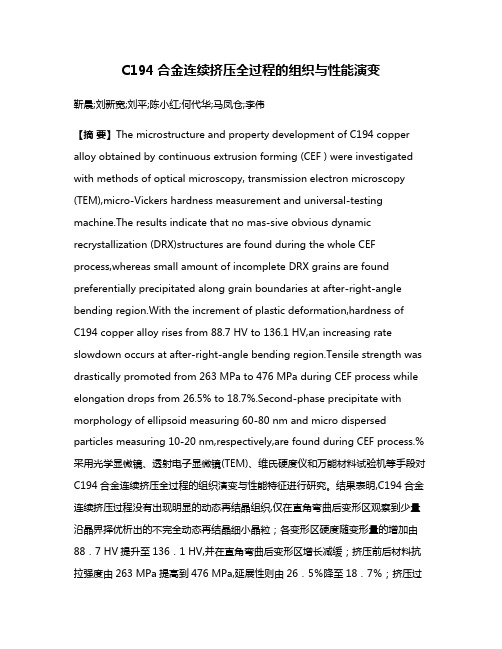
C194合金连续挤压全过程的组织与性能演变靳晨;刘新宽;刘平;陈小红;何代华;马凤仓;李伟【摘要】The microstructure and property development of C194 copper alloy obtained by continuous extrusion forming (CEF ) were investigated with methods of optical microscopy, transmission electron microscopy (TEM),micro-Vickers hardness measurement and universal-testing machine.The results indicate that no mas-sive obvious dynamic recrystallization (DRX)structures are found during the whole CEF process,whereas small amount of incomplete DRX grains are found preferentially precipitated along grain boundaries at after-right-angle bending region.With the increment of plastic deformation,hardness ofC194 copper alloy rises from 88.7 HV to 136.1 HV,an increasing rate slowdown occurs at after-right-angle bending region.Tensile strength was drastically promoted from 263 MPa to 476 MPa during CEF process while elongation drops from 26.5% to 18.7%.Second-phase precipitate with morphology of ellipsoid measuring 60-80 nm and micro dispersed particles measuring 10-20 nm,respectively,are found during CEF process.%采用光学显微镜、透射电子显微镜(TEM)、维氏硬度仪和万能材料试验机等手段对C194合金连续挤压全过程的组织演变与性能特征进行研究。
H62黄铜合金连续挤压的变形行为和组织演变特征_隋贤
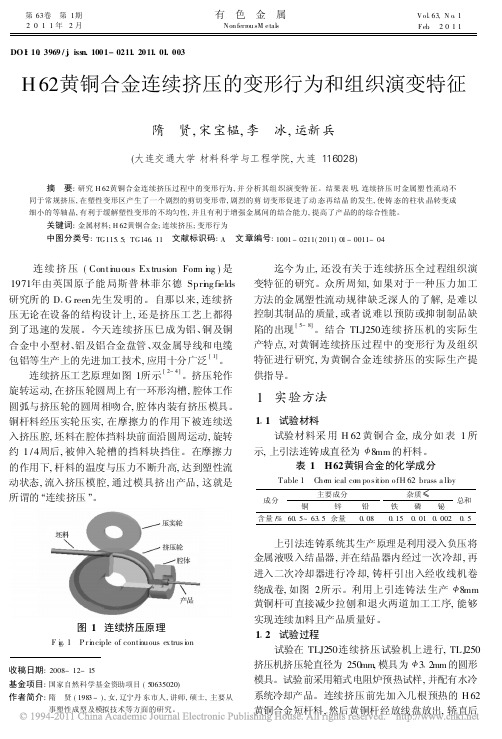
+ 两
相组织, 见图 3( a)。从金相组织中可以明显看出 及 相, 而铸造晶粒及晶界只能在偏光照相时才能 分辨。
为了研究全过程的组织特征, 在坯料上加润滑
( a) - 原材料中心的组织 ; ( b ) - 原材料边缘的组织 ; ( c) - 树枝晶组织 ; ( d) - 剪切变形带组织 ; ( e) - 动态再结晶组织 ; ( f) - 产品的组织
[ 1] 运新兵 , 宋宝韫 , 陈 莉 . 连续等径角挤压制备超细晶铜 [ J] . 中国有色金属学报 , 2006, 16( 9): 1563- 1569. [ 2] M ann inen T, K ata jar inn T e , R am say P . A na lysis o f flash fo r m ation in continuous ro tary ex trusion of copper [ J]. M a teria ls P ro cessing T echno logy , 2006, 177( 1- 3): 600- 603. [ 3] K a tajar inne T, M ann inen T, R am say P . N um er ica l si m ulation o f flash for m ation in continuous ro tary ex trusion o f copper [ J]. Jou rnal ofM a teria ls P ro cessing T echno logy , 2006, 177( 1- 3): 604- 607. [ 4] Cho J R, Jeong H S. Para m e tric investig ation on the curling phenom enon in CON FORM pro cess by three d i m ensiona l fin ite ele m ent ana lys is [ J]. Journa l ofM a teria ls P ro cessing T echno logy , 2001, 110( 1) : 53- 60. [ 5] 汪建敏 , 许晓静 , 石凤健 , 等 . 等 径角挤压获得超细晶铜的研究 [ J]. 热加工工艺 , 2004, 29( 7): 6- 7. [ 6] G eo rgy J R, R uslan Z V, T erry C L, et a . l Continuous processing of ultra fine gra ined A l by ECA P Confor m [ J]. M ate rials Sc ience and Eng ineering , 2004, 382( 2) : 30- 34 . [ 7] 李 冰 , 杨 志 , 刘化民 , 等 . 三辊行 星轧制运动和管坯变形规律的仿真模拟 [ J]. 塑性工程学报 , 2005, 12( 5): 70- 73. [ 8] 刘东华 , 苏玉长 , 邓楚平 , 等 . 三 辊行星轧制过程中 ACR 紫铜管的 组织和 性能演 变 [ J] . 中 国有色 金属学 报 , 2006, 16 ( 5): 881- 886. [ 9] 毛卫民 , 赵新兵 . 金属的 再结晶与晶粒长大 [M ]. 北京 : 冶金 工业出版社 , 1994: 14- 28. Journal of
挤压第二章 挤压基本原理
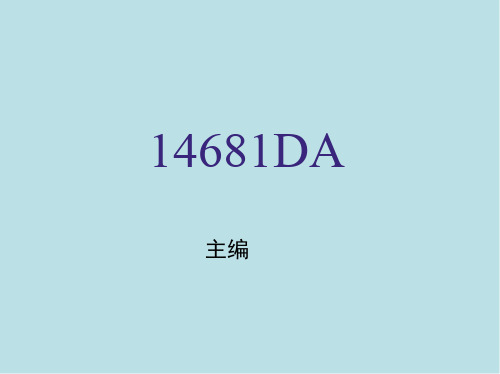
1.对塑性的影响
1)三向压应力状态能遏止晶间相对移动,阻止晶间变形,从而提高了塑性;而拉应力 会促进晶间变形,加速晶界的破坏。 2)三向压应力状态有利于消除由于塑性变形所引起的各种破坏,能促使被破坏了的晶 内和晶间的联系得到恢复。 3)三向压应力状态能使金属内某些夹杂物的危害程度大为降低。 4)三向压应力状态可以抵消或减小由于不均匀变形而引起的附加拉应力,从而减轻了 附加拉应力所造成的破坏作用。
二、挤压变形程度
1.断面减缩率εA 2.挤压比G 3.对数变形程度ϵ
1.断面减缩率εA
(2-1) (2-2) (2-3)
2.挤压比G
(2-4)
3.对数变形程度ϵ
(2-5)
(2-6)
三、应力状态对挤压变形的影响
1.对塑性的影响 挤压变形区中的基本应力状态是三向压应力。 2.对变形抗力的影响 应力状态对变形抗力的影响是很大的,例如,用冷挤压和冷 拉拔方法加工同种材料(退火纯铜)、同样尺寸的零件,见图2-8。
四、裂纹
图2-14 挤压裂纹 a)正挤压表面裂纹 b)反挤压表面裂纹 c)减径挤压内部裂纹
d)复合挤压内部裂纹
第五节 挤压对金属组织和力学性能的影响
一、对金属组织的影响 二、对力学性能的影响
一、对金属组织的影响
挤压时,在强烈的三向压应力作用下金属晶粒 被破碎,原来较大的晶粒挤压后变成为等轴细 晶粒组织,因而提高了强度。
第四节 挤压件的常见缺陷
一、表面折叠 二、表面折缝 三、缩孔 四、裂纹
一、表面折叠
图2-11 挤压折叠 a)正挤压折叠 b)、c)反挤压折叠形成
二、表面折缝
图2-12 挤压表面折缝 a)正挤压时的表面折缝 b)反挤压时的死角区
剥落 c)复合挤压时的横向折缝
连续挤压与连续铸挤
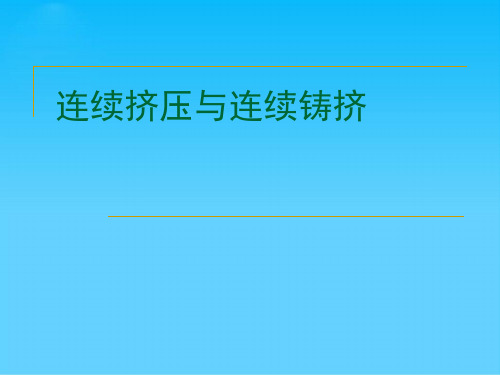
(2)挤压筒应具有无限连续工作长度……
压筒,以代替常规的的圆 由于铜及铜合金的热挤压温度较高(600-800℃),而一般的工模具材料均不允许在550℃以上的高温下长时间连续工作,因而必须将铜
及铜合金的连续挤压温度控制在500-550℃以下,但这又导致金属的变形抗力大大高于挤压铝及铝合金时的情形,影响工模具(尤其是
单轮双槽连续挤压示意图
单轮双槽连续挤压 机是巴 布科克公司的 独创性技术。两个凹 槽内的坯料通过槽封 块的两个进料孔,汇 集到挤压模前的空间 内,焊合成一体后再 通过挤压模成形为所 需的制品。
双轮单槽连续挤压机
在单轮单槽或单轮双槽连续挤压机 采用分流模挤压管材或空心型材, 存在两个缺点:一是由于空间的限 制,分流模的尺寸较小,而挤压压 力较高,分流桥与模芯的强度难以 得到充分保证;由于剧烈的摩擦和 长时间处于高温作用之下,挤压轮 的磨损快、寿命短。为了克服上述 问题,霍尔顿公司开发了双轮单槽 连续挤压机,不仅可以生产管材或 空心型材,同样可以生产线材、棒 材以及包覆材料。
在其上的固定矩形块,简 5-25mm的盘杆,最大坯料横截面积可达1200mm2,铜及铜合金坯料直径一般为φ8-15mm。
由于铜及铜合金的热挤压温度较高(600-800℃),而一般的工模具材料均不允许在550℃以上的高温下长时间连续工作,因而必须将铜 及铜合金的连续挤压温度控制在500-550℃以下,但这又导致金属的变形抗力大大高于挤压铝及铝合金时的情形,影响工模具(尤其是
与通常的Conform连续挤压法相比,连续铸挤法具有如下优点:
方法之一是采用如图所示 由于喂料与杆坯预处理等方面的原因,双轮挤压机多采用立式结构。
由于喂料与杆坯预处理等方面的原因,双轮挤压机多采用立式结构。
挤压时的变形规律

措施:(1)控制长径比 3~4;
(2)梯温挤压(前pp高t课件后完整低)
13
二、基本挤压阶段
1、挤压比 λ= F0/∑F1 制品的断面积为F1
2、变形区内的应力与变形状态
σr≈σθ
|σr |>|σθ|(由中心到边部)
3、主应力分布的不均匀性
轴向 : |变形区入口|>|变形区出口|
|变形区边部|>|变形区中心|
2、缺点
(1) 废料损失大 10-15%;
(2) 加工速度低;(摩擦大,温度升高,易产生废品)
(3) 长度与断面上组织和性能不均匀;
(4) 工具消耗大。
ppt课件完整
5
挤压的品种
棒
(六角棒)
(圆棒)
ppt课件完整
(方棒)
6
管
(铝管)
(防锈铝管)
(散热器管)
(方管)
(方管)
(方管)
ppt课件完整
7
金属流速>边部)。
a. 边部非矩形,中部近矩形
b. 边部剪切变形>中心剪切变形
c. 边部总延伸>中部总延伸(或外层金属的主延伸变形>内层)
d. 纵向上总延伸:前端<后端
e. 纵向上边部延伸:前端>后ppt课端件完整
11
3、存在两个难变形区,前死区,后死区。一般指前死区,用高
度来衡量(hs)。
死区的作用:对提高制品表面质量有利。
摩擦,使挤压力上升。
ppt课件完整
9
◆用网格法研究的结果
挤压流线
ppt课件完整
10
1 、变形区(压缩锥):纵向线在进出压缩锥时,发生方向相
反的两次弯曲,其弯曲的角度由外层向内逐渐减小,挤压中心线 上的纵向线不发生弯曲。
连续挤压技术

连续挤压技术一、连续挤压技术的原理及应用挤压是有色金属、钢铁材料生产与零件生产、零件成型加工的主要生产方法之一,也是各种复合材料、粉末材料等先进材料制备与加工的重要方法。
有色金属挤压制品在国民经济的各个领域获得了广泛的应用。
连续挤压技术是挤压成型技术的一项较新的技术,以连续挤压技术为基础发展起来的连续挤压复合、连续铸挤技术为有色金属管、棒、型、线及其复合材料的生产提供了新的技术手段和发展空间。
1.连续挤压技术的原理传统的挤压方法主要有正向挤压、反向挤压、静液挤压等。
以正挤压为例,如图1所示:图1.正向挤压正向挤压时,挤压杆运动方向与挤压产品的出料方向一致,坯料与挤压筒之间产生相对滑动,存在很大的摩擦,这种摩擦阻力使金属流动不均匀,从而给挤压制品的质量带来了不利影响,导致挤压制品组织性能不均匀,挤压能耗增加,由于强烈的摩擦发热作用,限制了挤压速度且加快了模具的磨损。
反向挤压和静液挤压等方法虽然从不同的角度对正向挤压进行了改进,但是这些传统的挤压方法都存在一个共同的缺点,即生产的不连续性,制品长度受到限制,前后坯料的挤压之间需要进行分离压余、填充坯料等一系列辅助操作,影响了挤压生产的效率。
为了解决传统挤压中的问题,20世纪70年代人们开始致力于挤压生产的连续性研究。
1971年,英国原子能局的D.Gree n发明了CONF OR连续挤压方法。
此方法以颗粒料或杆料为坯料,巧妙地利用了变形金属与工具之间的摩擦力。
如图2所示,由旋转的挤压轮上的矩形断面槽和固定模座所组成的环形通道起到普通挤压法中挤压筒的作用,当挤压轮旋转时,借助于槽壁上的摩擦力不断地将杆状坯料送入而实现连续挤压。
连续挤压时坯料与工具表面的摩擦发热较为显著,因此,对于低熔点金属,如铝及铝合金,不需进行外部加热即可使变形区的温度上升400〜500 C而实现热挤压。
图2.连续挤压原理在常规的正挤压中,变形是通过挤压轴将所需的挤压力直接施加于坯料上来实现的,由于挤压筒的长度有限,要实现无间断的连续挤压是不可能的。
挤压的组织性能特征及形成原因

一.挤压制品的组织特点及产生原因:1.挤压制品组织不均匀性.就实际生产中广泛采用的普通热挤压而言,挤压制品的组织与其他加工方法相比,其特点是在制品的断面与长度方向上都不均匀,一般是头部晶粒很大,尾部晶粒细小;中心晶粒粗大,外层晶粒细小.产生原因:a.摩擦的影响,在制品横断面上,由于摩擦阻力致剪切变形,使外层金属的晶粒遭到较大破碎,且制品由外层至中心变形程度减小而呈现不均匀;在制品长度方向上,由于外摩擦作用,外层金属受到连续不断的剪切变形,晶粒由制品前端至后端受到破坏程度逐渐增大,而呈现不均匀性b、挤压温度和挤压速度的影响挤压速度不同联系温度不一样,制品再结晶温度高晶粒粗大,低则晶粒细小,而呈现不均匀性。
c、合金相的影响在挤压两相或多相合金时,由于温度的变化,使合金在相变的温度下进行塑形变形,也会造成组织不均匀。
2.粗晶环组织.某些铝合金在挤压或随后的热处理过程中,在其外层出现粗大晶粒组织,通常称之为粗晶环.据粗晶环出现的时间可分为两类,一类是在挤压过程中已经形成的粗晶环,另一类是在挤压制品的热处理过程中形成的粗晶环.产生原因:根本原因是在挤压时或在挤压后的淬火时发生了集聚再结晶。
因此,凡是能降低再结晶温度促进再结晶过程的因素均易导致粗晶环。
百度原因:是合金元素含量、均匀化温度、挤压温度、挤压筒加热温度、淬火加热温度及应力状态。
通常均匀化温度越高,时间越长,粗晶环会越大。
随着挤压温度的增高,粗晶环的深度增加。
挤压筒的温度高于锭坯温度时,可减少粗晶环。
淬火温度越高将使粗晶环增加。
消除粗晶环的最根本的办法是减少挤压时的不均匀变形和控制再结晶的进行,对不同的合金则应采取不同的措施。
对锻铝可采取提高挤压温度以及适当降低淬火加热温度的方法;对硬铝可采取增加Mn和Mg含量的方法;但对锻铝LDlo合金采取提高挤压筒温度、降低锭坯加热温度易产生闷车,目前还是采用增加Mn和Si含量的方法控制粗晶环。
A 、合金元素的影响B 、锭坯均匀化的影响C 、挤压温度的影响D、合金中的应力状态的影响E 、挤压方式的影响F变形程度的影响3.层状组织:端口呈现出与本质折断后相似的形貌,分层的断口凹凸不平并带有裂纹;分层面近似平行于轴线;一般出现在前端。
2_挤压的基本原理

第二章 挤压的基本原理
二、实心件正挤压的变形过程
毛坯自由放入凹模型腔内, 整个挤压变形 过程如图1-1所示:
第二章 挤压的基本原理
初始状态,毛坯 与模壁间隙 0.05 -0.10mm 施加压力后, 金属径向流动 而充满型腔 凹模入口处的金属 开始进入模孔,变 形区域逐渐扩大, 开始挤压 毛坯高度S降低, 变形区高度稳定 不变,进入稳定 阶段 毛坯高度S不小 于变形区高度, 挤压完毕
第二章 挤压的基本原理
(4) 挤压后采用有效的热处理方法以 消除残余应力 第一种残余应力用低温回火方法就可大为减 小; 第二种残余应力采用将挤压件加热到稍低于 再结晶温度下可以完全消除;第三种残余应力, 只有经过再结晶才能消除。
第二章 挤压的基本原理
七、挤压对金属组织和性能的影响
组织变化:
变形前
第二章 挤压的基本原理
第二章 挤压的基本原理
本章内容:
• • • • 挤压基本原理 挤压变形的应力应变 挤压变形的附加应力与残余应力 挤压对金属组织和性能的影响
第二章 挤压的基本原理
一、挤压变形四阶段
• 无论零件形状如何,挤压时金属流动可分 以下四阶段: • 充满型腔阶段 施加压力后,金属径向流 动而充满模具型腔 • 开始挤压阶段 凹模入口处的金属开始进 入模孔,变形区域 迅速扩大 。 • 稳定挤压阶段 毛坯高度降低,变形区高 度稳定不变 • 挤压完毕阶段 顶出制件
第二章 挤压的基本原理
(3) 降低金属的耐蚀性 当挤压件表层具有残余应力时, 会降低其耐 蚀性。此外, 残余应力还会使金属的塑性、冲击 韧性及疲劳强度等降低。
第二章 挤压的基本原理
防止和消除附加应力和残余应力的方法:
(1) 减少摩擦阻力的影响 (2) 合理设计模具工作部分的结构和尺寸 以保证挤压件的变形与应力分布较为均 (3) 尽可能采用组织均匀的金属变形 挤压前对坯料进行均匀化处理, 使其尽可能在 晶粒大小均匀的状态下变形, 以减小附加应力。
- 1、下载文档前请自行甄别文档内容的完整性,平台不提供额外的编辑、内容补充、找答案等附加服务。
- 2、"仅部分预览"的文档,不可在线预览部分如存在完整性等问题,可反馈申请退款(可完整预览的文档不适用该条件!)。
- 3、如文档侵犯您的权益,请联系客服反馈,我们会尽快为您处理(人工客服工作时间:9:00-18:30)。
的变形量愈大,生核愈容易,相应的再结晶温度降 低,晶粒尺寸也较小.
Fig.6
图6试样截取部位示意图 Schematic diagram of cutting regions for micro-analysis
(a)A处的晶粒(肛l,“--8.561 1)
(b)B处的品粒(肛2.6,a=8.402 2) 图7挤压比变化(小一大)的晶粒尺寸变化图
变断面挤压件在工业中具有较高的技术经济效 益,不仅能够显著减少半成品的后续机械加工量,获 得全纤维高性能的挤压件,从而提高结构强度性能 和可靠性,而且可以缩短装配的工艺周期,提高材料 利用率,降低成本u J.近年来,随着航空、航天、建筑 以及交通运输业的发展,变断面挤压件的应用领域 不断扩大[2-4】.目前,各种变断面挤压方法都是通 过在模具的结构设计或在机构上做某些改动来实现 的.大部分挤压方法均需在挤压过程中停机,以便 更换模具和调整机构,这势必会影响挤压型材的尺 寸精度E5].在国家自然科学基金的资助下本课组开
囝8中心部的再结晶组织 Fig.8 Recrystallized structure at the center
第30卷
以工业纯铝为研究对象,分析挤压件的组织和性能 沿长度方向上的分布规律. 1挤压工艺及研究方案 1.1挤压工艺
将模孔设计成可移动的活动模块,由侧向液压 伺服缸控制,凸模由液压机主缸控制,凸模和活动模 块的位移由位移传感器测量并反馈输入到计算机 中,计算机通过液压伺服阀控制液压缸的运动方向 和速度,从而使凸模和活动模块按照设定的轨迹协 调动作,实现连续变断面挤压.其设备结构如图1 所示.这种连续变断面挤压方法将用来成形断面连 续反复变化的变断面型材或异形零件,在挤压过程 中无需停机换模,可获得全纤维高性能的挤压 件‘7|.
图1变断面连续挤压设备结构示意图(单位:ram) Flg.1 Schematic diagram of the machine for variable cross—section extrusion(unit:mm)
利用自行设计制造的实验装置及控制软件,进 行了连续变断面挤压实验.实验对象为工业纯铝, 坯料尺寸为25mm×25mm×60mm,最大挤压比为 5,最小挤压比为1.3.主液压缸挤压速度
发了一种新型的变断面挤压新方法,将挤压工艺与 电、液、计算机技术融为一体[6].该工艺具有在挤压 过程中无需停机换模,可制备出全纤维高性能的挤 压件,同时模具结构也大为简化.变断面挤压产品 由于在挤压过程中各点的挤压比都不同,在纵向断 面上存在着严重的不均匀变形,表现在组织上与其 他常规挤压方法相比,在制品的断面与长度方向上 更加不均匀,但在连续变断面挤压时,挤压件沿长度 方向各个截面上的变形程度是按一定规律变化的, 因此挤压件的组织和性能沿长度方向也应该有一定 的变化规律.为了研究连续变断面挤压件的组织,
电解抛光工艺参数:(a)稳压源25V;(b)电解时 间18~20 s;(C)电解温度低于40℃.
实验采用的浸蚀剂为:氢氟酸10mL,水50mL. 浸蚀时间为5~25 S.在显微镜下观察,直到观察到 清晰的晶界为止.
2实验结果及分析
2.1 同一截面不同位置晶粒组织的变化 图2中a断面处不同位置的金相组织如图3所
(a)外层部分组织(a--8 158 3)
(b)l,4处组织似=8 403 3)
(c)中『H1部分组织@=8.425 2)
图3 同一截面不同位置的金相显微组织
Fig.3 Metallographic
of different regions on the same.section
万方数据样截取部位示意图 Fig.4 Schematic diagram of cutting regions for micro-analysis
(a)A部位试样品粒(肛l,a=8.564 2)
(b)B部位试样的品粒(肛1.3,a=8.4252)
(c)C部位试样品粒(扣2 3,a28 303 1)
图5挤压比变化(大一小)时的晶粒尺寸 Fig.5 Grain size at different extrusion ratios
(2)挤压比(小一大)即截面变化(大一小)的 晶粒组织变化.同理,在图6试样上,分别截取C、B 和A部位进行显微组织观察.A点为压余,挤压比 A=1、没有变形.制品挤压变形从C开始到A,C点 挤压比A=1.5,B点挤压比A=2.6.其内部晶粒组 织的变化如图7所示.可以看出,随着挤压比的增 大,晶粒尺寸减小.出现这种现象的原因是再结晶 晶核是在金属中畸变最严重处优先生核,金属经受
摘要利用自行开发的连续变断面挤压新工艺设备,以工业纯铝为研究对象,进行了连续变断面挤压实验,研究了挤压制 品的组织.结果表明:由于连续变断面挤压制品长度方向上各点的挤压比不同,各点的显微晶粒度也不同,晶粒随挤压比的增 大而减小,在截面单一变化的试样中这种现象尤为明显;在同一截面上挤压制品的组织也不均匀,晶粒的尺寸由试样外层到 中部逐渐变大,外层组织多为细小晶粒,中部组织多为粗大晶粒;由于热处理工艺的原因,部分组织还会发生二次再结晶,出 现晶粒的异常长大现象.实验揭示了变断面挤压制品晶粒尺寸的变化规律. 关键词铝;挤压;连续变断面;晶粒;显微组织 分类号TG376
Microstructural evolvement rule of extrusions in continuous variable cross-section
extrusion
HU Shuiping,GAO Xiaodan,REN Xueping,TANG Di School of Materials Science and Engineering,University of Science and Technology Beijing。Beijing 100083,China
ABSTRACT Fine aluminium was extmded by using self·developed continuous variable cross-section extruding equipment,and the microstructure of samples W88 studied.The results showed that the grain size is different in every section along the extruding direction owing to the different extrusion rate.The grain size is fined with increasing extrusion rate.The phenomenon is more obvious in a sin— gle cross-section extruded sample.The grains on the same section are not nonuniform.In the same section,the grain size is increased from outer part to center of the sample.The grains are mostly smaller in the outer part but bigger at the center.Some grains are very big,and the reason is that some grains recrystallize during heat treatment.The research gives the microstructural evolvement rule of extrusions in continuous variable cross-section extrusion. KEY WORDS aluminium;extrusion forming;continuous variable cross-section;grain;microstructure
收稿日期:2007-{}6-26修回日期:2007—10—08 基金项目:国家自然科学基金资助项目(No,50275(}11) 作者简介:胡水平(1967一).男.博士研究生;唐荻(1955一),男:教授.博士生导师,E.mail:tangdi@nercar.usth.edu.cn
万方数据
北京科技大学学报
囝2试佯从连续变断面挤压件上切割位置示惹图
Schematic Fig.2
diagram of cutting regions for micro-analyzing a
variable cross·section extrusion piece
在实验中为了比较不同挤压变形区的组织,每 个试样在典型变形处(如截面变化转角处)各取三个 位置横向切割.同时为了调整实验工艺,将原来截 面大小不一的试样进行线切割,使得试样表面为同 一尺寸8mmx 10mm,以保证在电解抛光中简化实 验条件调试过程,使其适用于所有试样,并在比较晶 粒大小时实现统一.试样机械抛光后进行电解抛 光[8|,电解液为70%(体积分数)的高氯酸10mL,无 水乙醇90mL.
(1)挤压比(大一小)即截面变化(小一大)的晶
粒组织变化.在图4试样上,制品挤压变形是从C 开始到A,分别截取C、B、A部位的试样进行显微组 织观察,试样的截面是由小变大,而挤压比是由大变 小的:C点挤压比A=2.3;B点挤压比A=1.3;A点 为压余,挤压比A=1即没有变形.各点金相显微图 如图5所示.可以看出,晶粒尺寸沿制品长度方向 上是不均匀的,各点晶粒度大小随着挤压比的减小, 晶粒尺寸逐渐变大.
第30卷第7期 2008年7月
北 京科技大学学报 Journal of University of Science and Technology Beijing
VOI.30 NO.7 Jul.2008
连续变断面挤压制品组织的变化规律
胡水平 高晓丹 任学平 唐 获