钢件进给量
刀具切削进给参数表
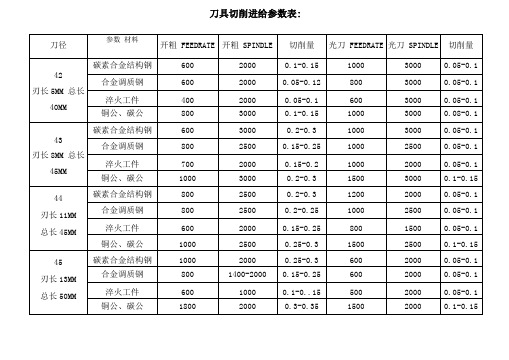
1500
2000
0.6-0.8
2000
2800
0.12-0.15
432R0.8
总长:300、
250、200、150
碳素合金结构钢
2000
1600
0.5-0.8
2000
2400
0.12-0.15
合金调质钢
1800
合金调质钢
2800
1500
0.6-0.8
2500
2000-2400
0.15-0.2
淬火工件
2000
1000
0.4-0.6
2000
1800-2200
0.15-0.2
铜公、碳公
2500
2000
0.6-1.
2500
3000
0.15-0.2
“25R5
总长:83、
132、 207
碳素合金结构钢
2000
1500
0.6-1.
2200
2800
0.15-0.2
合金调质钢
2000
1500
0.6-0.8
1800
2400
0.15-0.2
淬火工件
1500
1000
0.4-0.6
1500
1800
0.15-0.2
铜公、碳公
2800
1500
0.6-1.
2000
2500
0.15-0.2
刀径
参数 材料
开粗FEEDRATE
开粗SPINDLE
800
3600
0.2
1000
3800
0.1
合金调质钢
600
3400
0.2
切削用量表格

高锰钢wmn13%
10-20
铜及铜合金
200-250
120-180
90-120
铝及铝合金
300-600
200-400
150-200
铸铝合金wsi13%
100-180
80-150
60-100
注:切削钢及铸铁时刀具耐用度约为60min。
表二:按表面粗糙度选择进给量的参考值
工件材料
表面粗糙度
Ra/μm
表三:硬质合金车刀粗车外圆及端面的进给量
工件材料
车刀刀杆
尺寸
B×H/mm
工件直径
dw/mm
背吃刀量ap/mm
≤3
>3~5
>5~8
>8~12
>12
进给量f(mm/r)
碳素结构钢、
合金结构钢
及耐热钢
16×25
20
40
60
100
400
0.3~0.4
0.4~0.5
0.5~0.7
0.6~0.9
0.8~1.2
—
碳钢
及
合金钢
>5~10
<50
>50
0.30~0.50
0.40~0.55
0.45~0.60
0.55~0.65
0.55~0.70
0.65~0.70
>2.5~5
<50
>50
0.18~0.25
0.25~0.30
0.25~0.30
0.30~0.35
0.30~0.40
0.30~0.50
>1.25~2.5
<50
50~100
钢料进给参数表+刀长减速表

10:00
S13000 F2000 0.1-0.15 0.2
10:00
S15000 F1200 0.05-0.1 0.2
10:00
S17000 F900
0.05
0.2 10:00
S18000 F800
0.03
0.2 10:00
淬火后中光/预硬料中光
参考转速 参考进给 参考切深 单边余量 参考时间
S6000
数铣钨钢刀加工参数表
刀具名称 圆鼻刀
φ12R0.5 φ10R0.5 φ8R0.5 φ6R0.5 φ4R0.5 φ3R0.2 φ2R0.2 φ1.5R0.2 φ1R0.2
淬火前开粗参数/预硬料开粗
参考转速 参考进给 参考切深 单边余量 参考时间
不介意用新刀开粗
不介意用新刀开粗
S8000
F3500 0.3-0.35 0.5/0.3 15:00
S18000
F800
0.03 0.5/0.2 10:00
淬火后开粗( HRC48-52°)
参考转速 参考进给 参考切深 单边余量 参考时间
不介意用新刀开粗
不介意用新刀开粗
S8000
F3500 0.25-0.3 0.2
10:00
S9000
F3000 0.2-0.25 0.2
10:00
S11000 F2500 0.15-0.2 0.2
参考转速 S4500 S6000 S7000 S8000 S9000 S11000 S13000 S15000 S17000 S18000
参考进给 参考切深 参考时间
F3800
0.2
6:00
F3500
0.18
6:00
F3500
CBN刀具车削加工淬火钢件的切削参数范围

CBN刀具车削加工淬火钢件的切削参数范围CBN刀具车削加工淬火钢件,已经是非常普遍的一种现象,采用CBN刀具以车代磨加工淬火钢件效率成倍提高,而且干式切削,车削加工过程中不添加切削,绿色环保,更适合制造业的绿色制造。
CBN刀具虽然广泛应用于淬火钢件的车削加工,但很多工人还不太了解CBN刀具的切削参数,经常刚上去就出现崩刀、打刀现象。
主要就是不了解CBN刀具的切削参数,用硬质合金刀具的参数测试,效果不好。
小编在机械加工行业摸爬滚打了十几年,还算是有一点小心得,今天分享给大家。
在先介绍CBN刀具车削加工淬火钢件的切削参数范围之前,先来了解一下淬火钢都有哪些难加工问题。
1、淬火钢件的粗加工:车削加工淬火过的齿轮,齿圈的生产过程中,一些齿轮、齿圈淬火或渗碳淬火后,硬度一般在HRC55以上,而且变形严重,如高铁齿轮,工程机械大齿圈,重工行业用大齿圈等,这些大型齿轮齿圈淬火后变形量非常大,这就涉及到淬火钢粗加工。
同样,在模具钢生产过程中,淬火钢的粗加工也经常看到,但很多厂家采取的措施也五花八门,有的先把大余量线切割掉,有的用硬质合金刀具慢慢啃,有的用立方氮化硼(PCBN)刀具多次走刀才能完成加工,工人感慨粗加工淬火钢是有劲使不出,干着急,没办法。
2、淬火钢件的断续加工:间断切削加工一直是个难题,何况是动辄HRC60左右的淬火钢。
特别是在高速车削淬火钢时,刀具在间断车削淬火钢时会以每分钟100次以上的冲击来完成加工,对刀具的抗冲击性能是个很大的挑战。
以汽车齿轮加工为例,淬硬齿轮以车代磨已经成为一种趋势,据了解,作为齿轮产业的三大市场之一,车辆齿轮占据了齿轮市场总额的62%,其中汽车齿轮又占据了车辆齿轮市场份额的62%。
也就是说,汽车所用齿轮占有了整个齿轮市场近40%的比重,可见齿轮对于汽车产业的重要性。
虽然淬火钢的以车代磨和硬车削已经很普及,其实汽车淬硬齿轮加工过程中仍然遇到很多问题,如一些汽车齿轮内孔有油孔,这就出现间断切削加工难题,很多CBN刀具在高速运转时期遇到油孔容易崩刀,齿轮的位置公差难以保证,等等3、淬火钢件的切槽加工:举一个简单的例子,同步器滑套啮合槽淬火后的硬车削加工,虽然立方氮化硼刀具厂家开发出了同步器滑套专用立方氮化硼切槽刀具,但PCBN刀具的寿命仍然不尽如人意。
不锈钢车削参数
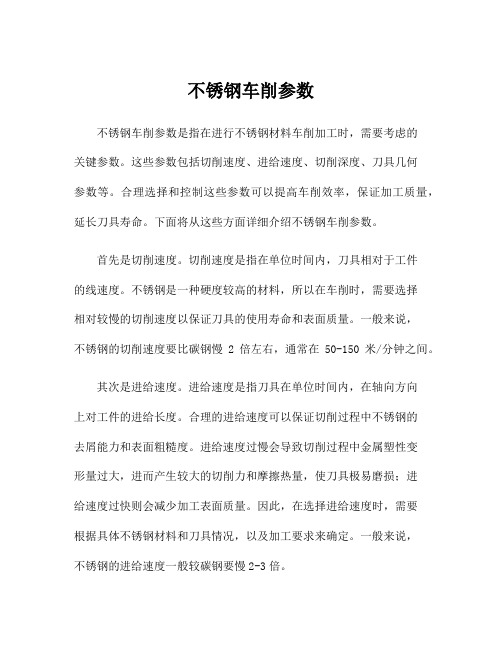
不锈钢车削参数不锈钢车削参数是指在进行不锈钢材料车削加工时,需要考虑的关键参数。
这些参数包括切削速度、进给速度、切削深度、刀具几何参数等。
合理选择和控制这些参数可以提高车削效率,保证加工质量,延长刀具寿命。
下面将从这些方面详细介绍不锈钢车削参数。
首先是切削速度。
切削速度是指在单位时间内,刀具相对于工件的线速度。
不锈钢是一种硬度较高的材料,所以在车削时,需要选择相对较慢的切削速度以保证刀具的使用寿命和表面质量。
一般来说,不锈钢的切削速度要比碳钢慢2倍左右,通常在50-150米/分钟之间。
其次是进给速度。
进给速度是指刀具在单位时间内,在轴向方向上对工件的进给长度。
合理的进给速度可以保证切削过程中不锈钢的去屑能力和表面粗糙度。
进给速度过慢会导致切削过程中金属塑性变形量过大,进而产生较大的切削力和摩擦热量,使刀具极易磨损;进给速度过快则会减少加工表面质量。
因此,在选择进给速度时,需要根据具体不锈钢材料和刀具情况,以及加工要求来确定。
一般来说,不锈钢的进给速度一般较碳钢要慢2-3倍。
第三是切削深度。
切削深度是指刀具在一次车削过程中与工件接触的长度。
合理的切削深度可以控制不锈钢的切削力和切削温度,避免损耗过大和材料表面的过热变焦。
切削深度要根据不锈钢的强度、硬度和材料加工性能来确定。
通常情况下,不锈钢的切削深度要较小,以保证刀具的使用寿命和加工表面质量。
最后是刀具几何参数。
刀具几何参数主要包括刀具刃磨角度、前角、主偏角和刀具尺寸等。
合理选择刀具几何参数可以减小切削力和摩擦热量,从而延长刀具寿命,并提高加工质量。
对于不锈钢材料,刀具刃磨角度一般要小于碳钢,以减小热应力和摩擦热量;前角适当增大可以增强刀具的切削能力和排屑能力;主偏角的选择要结合不锈钢材料的切削性能和加工要求来确定。
此外,刀具的尺寸也要根据工件的尺寸和切削要求进行选择,通常要保证切削力和切削厚度的均衡。
综上所述,不锈钢车削参数是进行不锈钢加工时需要考虑的关键参数,包括切削速度、进给速度、切削深度和刀具几何参数等。
各材料常用刀具转速进给参数对照表
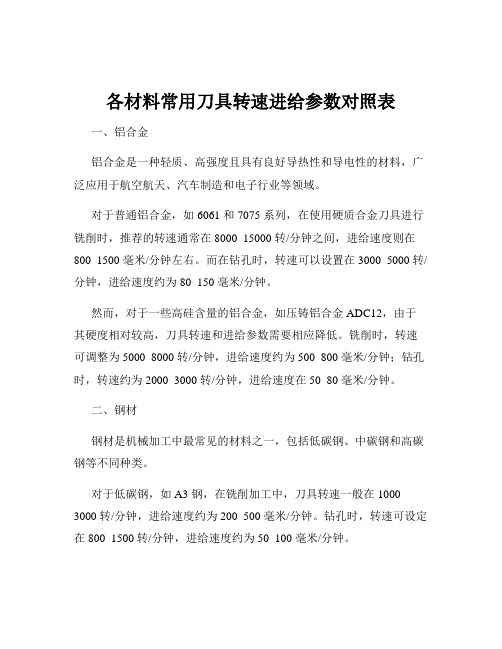
各材料常用刀具转速进给参数对照表一、铝合金铝合金是一种轻质、高强度且具有良好导热性和导电性的材料,广泛应用于航空航天、汽车制造和电子行业等领域。
对于普通铝合金,如 6061 和 7075 系列,在使用硬质合金刀具进行铣削时,推荐的转速通常在 8000 15000 转/分钟之间,进给速度则在800 1500 毫米/分钟左右。
而在钻孔时,转速可以设置在 3000 5000 转/分钟,进给速度约为 80 150 毫米/分钟。
然而,对于一些高硅含量的铝合金,如压铸铝合金 ADC12,由于其硬度相对较高,刀具转速和进给参数需要相应降低。
铣削时,转速可调整为 5000 8000 转/分钟,进给速度约为 500 800 毫米/分钟;钻孔时,转速约为 2000 3000 转/分钟,进给速度在 50 80 毫米/分钟。
二、钢材钢材是机械加工中最常见的材料之一,包括低碳钢、中碳钢和高碳钢等不同种类。
对于低碳钢,如 A3 钢,在铣削加工中,刀具转速一般在 1000 3000 转/分钟,进给速度约为 200 500 毫米/分钟。
钻孔时,转速可设定在 800 1500 转/分钟,进给速度约为 50 100 毫米/分钟。
中碳钢,如 45 号钢,由于其硬度稍高,铣削时转速可在 800 2000 转/分钟,进给速度约为 150 300 毫米/分钟;钻孔时,转速约为 500 1000 转/分钟,进给速度在 30 60 毫米/分钟。
高碳钢则需要更低的转速和进给速度。
在铣削时,转速约为 500 1000 转/分钟,进给速度约为 100 200 毫米/分钟;钻孔时,转速一般在300 600 转/分钟,进给速度约为 15 30 毫米/分钟。
三、不锈钢不锈钢具有良好的耐腐蚀性和耐磨性,但加工难度相对较大。
常见的不锈钢如 304 和 316 系列,在铣削时,刀具转速通常在 600 1200 转/分钟,进给速度约为 80 150 毫米/分钟。
车床的切削用量及单位
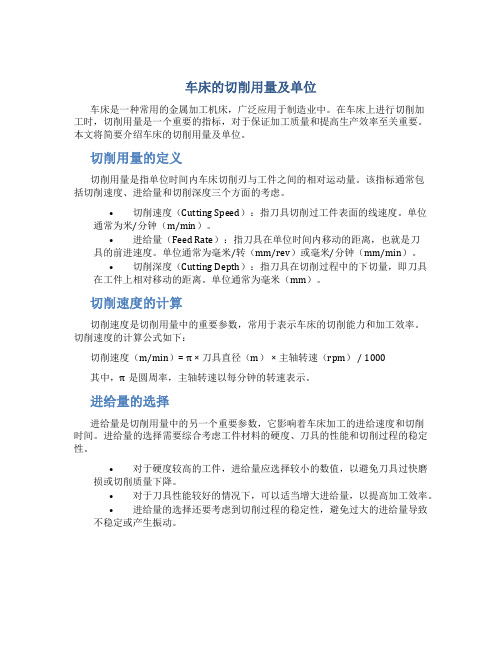
车床的切削用量及单位车床是一种常用的金属加工机床,广泛应用于制造业中。
在车床上进行切削加工时,切削用量是一个重要的指标,对于保证加工质量和提高生产效率至关重要。
本文将简要介绍车床的切削用量及单位。
切削用量的定义切削用量是指单位时间内车床切削刃与工件之间的相对运动量。
该指标通常包括切削速度、进给量和切削深度三个方面的考虑。
•切削速度(Cutting Speed):指刀具切削过工件表面的线速度。
单位通常为米/分钟(m/min)。
•进给量(Feed Rate):指刀具在单位时间内移动的距离,也就是刀具的前进速度。
单位通常为毫米/转(mm/rev)或毫米/分钟(mm/min)。
•切削深度(Cutting Depth):指刀具在切削过程中的下切量,即刀具在工件上相对移动的距离。
单位通常为毫米(mm)。
切削速度的计算切削速度是切削用量中的重要参数,常用于表示车床的切削能力和加工效率。
切削速度的计算公式如下:切削速度(m/min)= π × 刀具直径(m) × 主轴转速(rpm) / 1000其中,π是圆周率,主轴转速以每分钟的转速表示。
进给量的选择进给量是切削用量中的另一个重要参数,它影响着车床加工的进给速度和切削时间。
进给量的选择需要综合考虑工件材料的硬度、刀具的性能和切削过程的稳定性。
•对于硬度较高的工件,进给量应选择较小的数值,以避免刀具过快磨损或切削质量下降。
•对于刀具性能较好的情况下,可以适当增大进给量,以提高加工效率。
•进给量的选择还要考虑到切削过程的稳定性,避免过大的进给量导致不稳定或产生振动。
切削深度的控制切削深度是切削用量中的另一个重要参数,它直接影响到车床的切削性能和加工结果。
切削深度的选择需要根据工件的要求、刀具的刚度和车床的稳定性进行综合考虑。
•对于高精度要求的工件加工,通常选择较小的切削深度,以保证加工精度和表面质量。
•切削深度还应考虑到刀具的刚度,避免过大的切削深度导致刀具振动或断裂。
常用工件材料进给、转速参数表

常用材料进给、转速参数表
1:合理的选择刀具
1平面铣削时应选用不重磨硬质合金端铣刀或立铣刀。
一般铣削时,尽量采用二次走刀加工第一次用端铣刀粗铣,沿工件表面连续走刀,每刀步距为刀具直径的(60%-70%)。
2立铣刀和镶硬质合刀片的端铣刀主要用于加工凸台、凹槽和箱口面。
3球刀、圆鼻刀常用于加工曲面和变斜角轮廓外形。
球刀多用于半精加工和精加工。
镶硬质合金刀具(圆鼻刀)多用于开粗。
2:切削用量三大要素
为切削深度、主轴转速和进给速度。
(总体选择原则:少切削,快进给)
3:刀具按材料分类
普通硬质白钢刀(材料为高速钢),涂层刀具(如镀钛等),合金刀具(如钨钢、氮化硼钢刀具)。
加工45#钢、普通球刀(精加工)
加工45#钢、常用开粗硬质合金刀(镶刀片类)
<
加工紫铜硬质合金刀具单位MM MM(r/min)(mm/min)MM
加工紫铜高速钢刀具单位MM MM(r/min)(mm/min)MM
开粗即粗加工,中光即半精加工,光刀即精加工。
各材料常用刀具转速进给参数对照表

各材料常用刀具转速进给参数对照表一、铝合金铝合金是一种轻质、高强度且具有良好导热性的材料,常用于航空航天、汽车制造和电子设备等领域。
对于普通铝合金(如 6061、6063),在使用硬质合金刀具进行粗加工时,转速一般可设置在 1500 2500 转/分钟,进给速度约为 015 03 毫米/转。
而在进行精加工时,转速可提高到 3000 5000 转/分钟,进给速度降低至 005 015 毫米/转。
当使用涂层刀具时,由于其耐磨性更好,转速和进给速度可以适当提高。
粗加工时,转速可达 2000 3000 转/分钟,进给速度 02 04 毫米/转;精加工时,转速 4000 6000 转/分钟,进给速度 008 012 毫米/转。
二、铜合金铜合金具有良好的导电性、导热性和延展性,常见于电气、电子和模具制造等行业。
对于黄铜(如 H62),粗加工时,使用硬质合金刀具,转速约为800 1500 转/分钟,进给速度 01 02 毫米/转。
精加工时,转速提升到1500 2500 转/分钟,进给速度降至 005 01 毫米/转。
对于青铜(如 QSn65-01),由于其硬度相对较高,粗加工时,转速在 600 1200 转/分钟,进给速度 008 015 毫米/转;精加工时,转速1000 2000 转/分钟,进给速度 003 008 毫米/转。
三、碳钢碳钢是机械制造中应用最广泛的材料之一,其强度和硬度因含碳量的不同而有所差异。
对于低碳钢(如 A3 钢),使用硬质合金刀具进行粗加工,转速可设定在 800 1500 转/分钟,进给速度 015 03 毫米/转。
精加工时,转速提高到 1500 2500 转/分钟,进给速度减小为 008 015 毫米/转。
中碳钢(如 45 钢)在粗加工时,转速一般为 600 1200 转/分钟,进给速度 01 02 毫米/转;精加工时,转速 1000 1800 转/分钟,进给速度005 01 毫米/转。
铰孔切削用量选择参考表

1.5~3.2
钢σb>900MPa
0.15~0.35
0.35~0.7
0.55~1.2
0.65-1.5
0.8-1.8
1.0-2.3
1.2-3.2
铸铁铜及铝合金HB≤170
0.6~1.2
1.0~2.0
1.5~3.0
2.0-4.0
2.5-5.0
3.2-6.4
3.75-7.5
铸铁HB>170
0.4~0.8
7.1
6.8
6.1
5.5
4.8
4.3
d0=80αp=0.25
10
8.9
8.1
7.5
7.1
6.7
6.3
5.6
5.2
4.5
4
高速钢铰刀铰削的切削速度m/min(精铰)
结构碳钢、铬钢、镍铬钢
灰铸铁、可锻铸铁、铜合金
精度等级
加工表面粗糙度Ra(μm)
切削速度υ(m/min)
灰铸铁
可锻铸铁
铜合金
H7~H8
3.2~1.6
0.65~1.3
1.0~2.0
1.3-2.6
1.6-3.2
2.1-4.2
2.6-5.5
0.4~0.6
0.5-0.7
0.6-0.8
0.7-0.9
0.9-1.2
淬硬钢
0.25~0.35
0.3~0.4
0.35-0.45
0.4-0.5
铸铁HB≤170
0.9~1.4
1.0~1.5
灰铸铁190HBf(mm/r)
≤0.5
0.6
0.7
0.8
1
1.2
1.4
车床金属切削速度及进给亮量与工件直径有关

式中,εr为车刀两刃夹角;rp为径向前角;α为牙型角。
1.3高速钢切削时牙型角过大
在高速切削螺纹时,由于车刀对工件的挤压力产生挤压变形,会使加工出的牙型扩大,同时使工件胀大,所以在刃磨车刀时,两刃夹角应适当减小30′。另外,车削外螺纹前工件大径一般比公称尺寸小(约0.13P)。
粗车的目的是尽快地从毛坯上切去大部分的加工余量,使工件接近要求的形状和尺寸。粗车以提高生产率为主,在生产中加大切削深度,对提高生产率最有利,其次适当加大进给量,而采用中等或中等偏低的切削速度。使用高速钢车刀进行粗车的切削用量推荐如下:切削深度ap=0.8~1.5mm,进给量f=0.2~0.3mm/r,切削速度v取30~50m/min(切钢)。
总之,车削螺纹时产生的故障形式是多种多样的,既有设备原因,也有刀具、测量、操作等原因,排除故障时要具体情况具体分析,通过各种检测方法和诊断手段,找出具体的影响因素,采取有效、合理的解决方法。
精车的另一个突出的问题是保证加工表面的粗糙度的要求。减上表面粗糙度Ra值的主要措施有如下几点。
(1)合理选用切削用量。选用较小的切削深度ap和进给量f,可减小残留面积,使Ra值减小。
(2)适当减小副偏角Kr′,或刀尖磨有小圆弧,以减小残留面积,使Ra值减小。
(3)适当加大前角γ0,将刀刃磨得更为锋利。
4乱牙
乱牙的原因是当丝杠转一转时,工件未转过丝杠转数整数倍而造成的,即工件转数不是丝杠转数的整数倍。
常用预防乱牙的方法首先是开倒顺车,即在一次行程结束时,不提起开合螺母,把刀沿径向退出后,将主轴反转,使车刀沿纵向退回,再进行第二次行程,这样往复过程中,因主轴、丝杠和刀架之间的传动没有分离过,车刀始终在原来的螺旋槽中,就不会产生乱牙。其次,当进刀纵向行程完成后,提起开合螺母脱离传动链退回,刀尖位置产生位移,应重新对刀。
被吃刀量、进给量和切削速度的选定

粗加工时,一次走刀尽可能切除全部余量。
半精加工时,被吃刀量取为0.5~2mm。
精加工时,被吃刀量取为0.1~0.4mm
1、被吃刀量的选定
被吃刀量、进给量和切削速度的选定
2、进给量的选定
生产实际中多采用查表法确定进给量。
粗加工时,进给量由机床进给机构强度、刀具强度与刚性、工件的装夹刚度决定。
精加工时,进给量由加工精度和表面粗糙度决定。
图3-45 砂轮磨削区温度和磨粒磨削点温度
六、砂轮的磨损与耐用度
自锐性
由于磨粒的微刃逐步钝化,磨削力逐步增加,致使磨粒破碎或脱落,重新露出锋利的微刃。这种特性称为自锐性。
磨钝标准
粗磨时发生振动、噪音,说明砂轮已经磨钝(由于切屑、碎磨粒把砂轮堵塞,磨粒本身已磨损变钝),应立即打磨砂轮。 精磨时,工件表面出现波浪痕迹或表面粗糙度增大,说明砂轮已经磨钝。
磨削的径向力大; 砂轮有自锐作用; 磨削加工的工艺范围广; 磨削在切削加工中的比重日益增大。
本章结束
汇报人姓名
汇报日期
01
积屑瘤产生的条件及对金属切削过程的影响?如何抑制积屑瘤的产生?
02
用硬质合金车刀(γO=15°、κγ=45°、λS=5°)车削外圆,工件材料为40Cr钢,选用的υc=100m/min,f=0.2mm/r,ap=3mm。试计算(1)主切削力;(2)校验机床功率(机床额定功率为7.5KW,机床传动效率为0.8)。
(1)粗车时, ap、f 较大,故选择较低的v;精车
刀具材料的切削性能愈好,切削速度也选得愈高。
精加工时,应尽量避开积屑瘤和鳞刺产生的区域。
断续切削及加工大件、细长件和薄壁工件时,应 适当降低切削速度。
在易发生振动的情况下,切削速度应避开自激振 动的临界速度。
车削每转进给量参考值

例如
条件判别语句IF,ELSE,ENDIF
格式(i):IF条件表达式
…
ELSE
…
ENDIF
格式(ii):IF条件表达式
…
ENDIF
循环语句WHILE,ENDW
格式:WHILE条件表达式
…
ENDW
#1=B(抛物线Z32 X8)
车削每转进给量参考值
工件材料
Fn (mm/rpm)G95
粗加工
精加工
高速钢车刀
硬质合金车刀
高速钢车刀
硬质合金车刀
钢
01.0~0.15
0.10~0.25
0.02~0.05
0.10~0.15
铸铁
0.12~0.20
0.15~0.30
铝合金
0.15~0.25
0.20~0.40
0.05~0.08
0.10~0.20
320
0.15
2
N2
精车外圆
T0202
93°外圆车刀
1200
0.08
0.25
N3
精车退刀槽
T0303
5mm外圆切槽刀
250
0.05
0.2
N4
精车外螺纹
T0404
60°外螺纹刀
250
2
0.2
O0002
N1
粗车内孔
T0101
90°内孔车刀
320
0.15
2
N2
精车内孔
T0202
93°内孔车刀
1200
0.05
1
#36
6
#2
普通车削的常用的切削速度和进给量

250-200-170
230-190-150
380-265-195
260-180-130
240-165-120
210-145-105
380-265-180
240-170-120
220-150-100
200-130-100
200-140-100
140-100-70
125-100-60
普通车削的常用的切削速度和进给量耐磨性基本牌号韧性材料单位切削力nmm2hb硬度耐磨性基本牌号韧性yng051yng151ybc151ybc251ybc351ybd151ybg201yc10yc40进给量进给量005010200501020104080104080205100104010305030612iso切削速度mmin切削速度mmin碳素钢c015c035c06190021002250125150200600500400500400300400300200550450350500400300400300200480345250440315230385275200460320220440300210380260180380230165300210150260185130510365470335410295180150140410290230380260210330230185170130851601158013010070合金钢退火淬硬淬硬淬硬21002600270028501802753003504503802803202802002702201902301901504103402403002601802502001702301901503802651952601801302401651202101451053802651802401701202201501002001301002001401001401007012510060110755540028027519525518022015512090807026018014518012010016511590145100801007550705035654530554025高合金钢退火淬硬2600390020032538032024019016013035029020017014011035023017017011029020015013010080175115808555403702601801201008023516511580906560453020p铸钢非合金低合金高合金200025002700180200225260220180260220180200180120260210170260210170260150100265185145255180951901309523017012517012080957055275200270185205140
车床金属切削速度及进给亮量与工件直径有关

式中,εr为车刀两刃夹角;rp为径向前角;α为牙型角。
1.3高速钢切削时牙型角过大
在高速切削螺纹时,由于车刀对工件的挤压力产生挤压变形,会使加工出的牙型扩大,同时使工件胀大,所以在刃磨车刀时,两刃夹角应适当减小30′。另外,车削外螺纹前工件大径一般比公称尺寸小(约0.13P)。
(3)车削过程中开合螺母自动抬起引起螺距不正确。解决方法:调整开合螺母镶条适当减小间隙,控制开合螺母传动时抬起,或用重物挂在开合螺母手柄上防止中途抬起。
3表面粗糙度值大
表面粗糙度值大的原因:
一是刀尖产生积屑瘤;
二是刀柄刚性不够,切削时产生振动;
三是车刀径向前角太大,中滑板丝杠螺母间隙过大产生扎刀;
四是高速钢切削螺纹时,切削厚度太小或切屑向倾斜方向排出,拉毛已加工牙侧的表面;
1.2径向前角未修正
为了使车刀排屑顺利,减小表面粗糙度,减少积屑瘤现象,经常磨有径向前角,这样就引起车刀两侧切削不与工件轴向重合,使得车出工件的螺纹牙型角大于车刀的刀尖角,径向前角越大,牙型角的误差也越大。同时使车削出的螺纹牙型在轴向剖面内不是直线,而是曲线,影响螺纹副的配合质量。解决方法:在刃磨有较大径向前角的螺纹车刀车螺纹时,刀尖角必须通过车刀两刃夹角进行修正,尤其加工精度较高的螺纹,其修正计算方法为:
4乱牙
乱牙的原因是当丝杠转一转时,工件未转过丝杠转数整数倍而造成的,即工件转数不是丝杠转数的整数倍。
常用预防乱牙的方法首先是开倒顺车,即在一次行程结束时,不提起开合螺母,把刀沿径向退出后,将主轴反转,使车刀沿纵向退回,再进行第二次行程,这样往复过程中,因主轴、丝杠和刀架之间的传动没有分离过,车刀始终在原来的螺旋槽中,就不会产生乱牙。其次,当进刀纵向行程完成后,提起开合螺母脱离传动链退回,刀尖位置产生位移,应重新对刀。
切削用量表

附2:切削用量表:
1.铣削速度V :指铣刀旋转时的圆周线速度,单位为m /min 。
计算公式:v=1000
n
d π
式中:d------铣刀直径,mm
n------主轴(铣刀);转速,r /
mm
从上式可得到:主轴(铣刀);转速 n=
d
v
1000 π 铣削速度v 推荐值
2.进给量F: 在铣削过程中,工件相对铣刀的移动速度称为进给量。
有三种表示方法:
1) 每齿进给量a f :mm/z 2) 每转进给量f :mm/r 3)
每分钟进给量v f :mm/min
三种进给量的关系为:v f=f·n=a f·z·n
1)铣削宽度a e:铣刀在一次进给中所切掉工件表层的宽度,单位为mm。
一般取铣刀直径的50%~60%
2) 背吃刀量a p:铣刀在一次进给中切掉工件表层的厚度,单位为mm。
一般粗加工立铣不得超过7mm,端铣2~5mm,精铣约0.1mm~0.5mm。
车床金属切削速度及进给亮量与工件直径有关

中径不正确的原因是车刀切削深度不正确,以顶径为基准控制切削深度,忽略了顶径误差的影响;刻度盘使用不当;车削时未及时测量。解决方法:精车时,检查刻度盘是否松动,并且要正确使用,精车余量应适当,要及时测量中径尺寸,考虑顶径的影响,调整切削深度。
6扎刀或顶弯工件
扎刀或顶弯工件的原因:车刀刀尖低于工件(机床)中心;车刀前角太大,中滑板丝杠间隙较大;工件刚性差,而切削用量选择太大。解决方法:第一,安装车刀时,刀尖要对准工件中心,或略高些。第二,减小车刀前角,减小径向力,调整中滑板丝杠间隙。第三,根据工件刚性来选择合理的切削用量;增加工件的刚性,增加车刀刚性。
v=πdn/1000(m/min)
式中:d--工件待加工表面的直径(mm)
n--车床主轴动的距离,称为进给量,以f(mm/r)表示;车刀每一次切去的金属层的厚度,称为切削深度,以ap(mm)表示。
为了保证加工质量和提高生产率,零件加工应分阶段,中等精度的零件,一般按粗车一精车的方案进行。
车床金属切削速度及进给亮量与工件直径有关,比如粗车时你可以采用低速大进给量,精车时你可以采用高速小进给量,加工毛坯时可以采用低速大进给量。这样可以提高加工效率,减小刀具磨损。
四、切削用量的选择
切削速度、进给量和切削深度三者称为切削用量。它们是影响工件加工质量和生产效率的重要因素。
车削时,工件加工表面最大直径处的线速度称为切削速度,以v(m/min)表示。其计算公式:
4乱牙
乱牙的原因是当丝杠转一转时,工件未转过丝杠转数整数倍而造成的,即工件转数不是丝杠转数的整数倍。
常用预防乱牙的方法首先是开倒顺车,即在一次行程结束时,不提起开合螺母,把刀沿径向退出后,将主轴反转,使车刀沿纵向退回,再进行第二次行程,这样往复过程中,因主轴、丝杠和刀架之间的传动没有分离过,车刀始终在原来的螺旋槽中,就不会产生乱牙。其次,当进刀纵向行程完成后,提起开合螺母脱离传动链退回,刀尖位置产生位移,应重新对刀。
车削切削用量选取参考表

车削切削用量选取参考表
一、外圆车削背吃刀量选择表(端面切深减半)
K5()12.5S
2、粗车背吃刀量的景大值是受车床功率的大小决定的。
中尊功率机床可以达到8〜lOmm。
二、高速钢及硬质合金车刀车削外圆及端面的粗车进给量
1.断续切削、有冲击载荷时,乘以修正系数:k=0_75~0.85。
2、加工耐热钢尺其台金时,进给長应不大于ImmAo
3、无外皮时,表内进给昼应乘以系数:k=l.k
4.加工淬硬钢时,进给fi应减小。
硬度为HRC45-56时、乘以修正系教:0・8,硬度为HRC57・62,乘以修正系^:k=0.5o
三、按表面粗糙度选择进给量的参考值
四、车削切削速度参考数值表
五、外圆车削时切削速度公式中的系数和指数选择表
注:1、内表面加工(饉孔、孔内切槽、内表面成形车削)时,用外圆加工的车削
速度乘以系数0.9 O
2、用高速钢车刀加工结构钢、不锈钢尺铸钢,不用切削液时,车削速度乘以系数0.8。
3、用yr车刀对钢件切断尺切槽使用切削液时,车削速度乘以系数L4。
4、成形车削深轮廓尺复杂轮廓工件时,切削速度乘以系数0.85。
5、用高速钢车刀加工热处理钢件时,车削速度应减少:正火,乘以系数0.95; 退火,乘以系数0.9;调质,乘以系数0.8。
6、加工钢和铸鉄的机械性能改变时,车削速度的修正系kMv可按表《钢和铸铁的强度和硬度改变时车削速度的修正系敌kM»计算。
7、其他加工条件改变时,车削速度的修正系数见表《车削条件改变时的修正系数》。
六、车床切削速度计算表
2.
3、上述计算中:。