铸钢件热处理作业指导书
铸钢件作业指导书
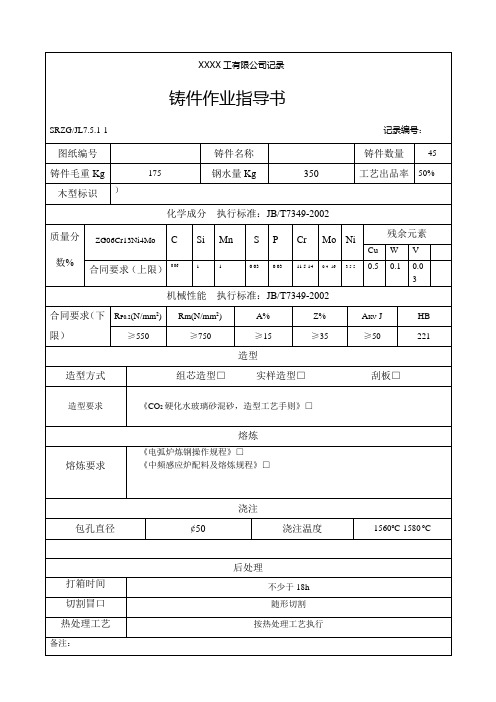
1
1
0.03
0.03
11.5-14
0.4--16.
3.5-5
0.5
0.1
0.03
机械性能执行标准:JB/T7349-2002
合同要求(下限)
RP0.2(N/mm2)
Rm(N/mm2)
A%
Z%
AKVJ
HB
≥550
≥750
≥15
≥35
≥50
221
造型
造型方式
组芯造型□实样造型□刮板□
造型要求
《CO2硬化水玻璃砂混砂,造型工艺手则》□
jbt73492002合同要求下p02nmmhb550750153550221造型造型方式组芯造型实样造型造型要求co硬化水玻璃砂混砂造型工艺手则熔炼熔炼要求电弧炉炼钢操作规程中频感应炉配料及熔炼规程浇注包孔直径50浇注温度1560后处理打箱时间不少于18h切割冒口随形切炼要求
《电弧炉炼钢操作规程》□
《中频感应炉配料及熔炼规程》□
浇注
包孔直径
¢50
浇注温度
1560oC-1580oC
后处理
打箱时间
不少于18h
切割冒口
随形切割
热处理工艺
按热处理工艺执行
备注:
编制
审核
批准
日期
日期
日期
XXXX工有限公司记录
铸件作业指导书
SRZG/JL7.5.1-1记录编号:
图纸编号
铸件名称
铸件数量
45
铸件毛重Kg
175
钢水量Kg
350
工艺出品率
50%
木型标识
)
化学成分执行标准:JB/T7349-2002
铸钢件热处理作业指导书
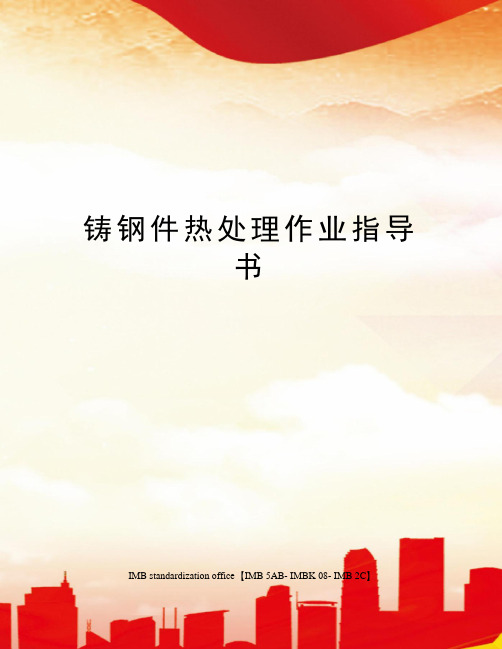
铸钢件热处理作业指导书IMB standardization office【IMB 5AB- IMBK 08- IMB 2C】热处理作业指导书1.目的保证热处理质量。
2.热处理方式按加热和冷却条件不同,铸钢件的主要热处理方式有:退火、正火、均匀化处理、淬火、回火、固溶处理、沉淀硬化、消除应力处理及除氢处理。
3.热处理操作要求.退火退火是将铸钢件加热到Acs 以上20~30℃,保温一定时间,冷却的热处理工艺。
退火的目的是为消除铸造组织中的柱状晶、粗等轴晶、魏氏组织和树枝状偏析,以改善铸钢力学性能。
碳钢退火后的组织:亚共析铸钢为铁素体和珠光体,共析铸钢为珠光体,过共析铸钢为珠光体和碳化物。
适用于所有牌号的铸钢件。
图1—1为几种退火处理工艺的加热规范示意图。
表l—1为铸钢件常用退火工艺类型及其应用。
表1-2铸钢件退火工艺及退火后的硬度。
图1—1为几种退火处理工艺的加热规范示意图表l—1为铸钢件常用退火工艺类型及其应用表1-2铸钢件退火工艺及退火后的硬度.正火正火是将铸钢件目口热到Ac。
温度以上30~50o C 保温,使之完全奥氏体化,然后在静止空气中冷却的热处理工艺。
图1—2为碳钢的正火温度范围示意图。
表1-3铸钢件正火工艺及退火后的硬度,表1-4常用低合金铸件正火或正火+回火工艺及硬度。
正火的目的是细化钢的组织,使其具有所需的力学性能,也司作为以后热处理的预备处理。
正火与退火工艺的区别有两个:其一是正火加热温度要偏高些;其二是正火冷却较快些。
经正火的铸钢强度稍高于退火铸钢,其珠光体组织较细。
一般工程用碳钢及部分厚大、形状复杂的合金钢铸件多采用正火处理。
图1—2为碳钢的正火温度范围示意图正火可消除共析铸钢和过共析铸钢件中的网状碳化物,以利于球化退火;可作为中碳钢以及合金结构钢淬火前的预备处理,以细化晶粒和均匀组织,从而减少铸件在淬火时产生的缺陷。
表1-3铸钢件正火工艺及退火后的硬度表1-4常用低合金铸件正火或正火+回火工艺及硬度.淬火淬火是将零件加热到奥氏体化后(Ac。
铝铸件作业指导书
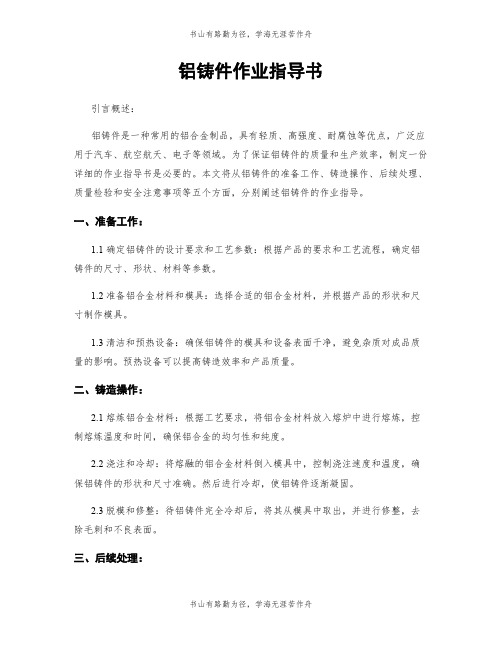
铝铸件作业指导书引言概述:铝铸件是一种常用的铝合金制品,具有轻质、高强度、耐腐蚀等优点,广泛应用于汽车、航空航天、电子等领域。
为了保证铝铸件的质量和生产效率,制定一份详细的作业指导书是必要的。
本文将从铝铸件的准备工作、铸造操作、后续处理、质量检验和安全注意事项等五个方面,分别阐述铝铸件的作业指导。
一、准备工作:1.1 确定铝铸件的设计要求和工艺参数:根据产品的要求和工艺流程,确定铝铸件的尺寸、形状、材料等参数。
1.2 准备铝合金材料和模具:选择合适的铝合金材料,并根据产品的形状和尺寸制作模具。
1.3 清洁和预热设备:确保铝铸件的模具和设备表面干净,避免杂质对成品质量的影响。
预热设备可以提高铸造效率和产品质量。
二、铸造操作:2.1 熔炼铝合金材料:根据工艺要求,将铝合金材料放入熔炉中进行熔炼,控制熔炼温度和时间,确保铝合金的均匀性和纯度。
2.2 浇注和冷却:将熔融的铝合金材料倒入模具中,控制浇注速度和温度,确保铝铸件的形状和尺寸准确。
然后进行冷却,使铝铸件逐渐凝固。
2.3 脱模和修整:待铝铸件完全冷却后,将其从模具中取出,并进行修整,去除毛刺和不良表面。
三、后续处理:3.1 除渣和清洗:将铝铸件浸入除渣剂中,去除表面的氧化物和杂质。
然后进行清洗,保证铝铸件的表面干净。
3.2 热处理:根据铝铸件的要求,进行热处理,改善铝铸件的硬度、强度和耐腐蚀性能。
3.3 表面处理:对铝铸件进行喷涂、抛光、喷砂等表面处理,提高其外观质量和耐腐蚀性。
四、质量检验:4.1 尺寸检测:使用测量工具对铝铸件的尺寸进行检测,确保其符合设计要求。
4.2 成分分析:通过化学分析仪器检测铝铸件的成分,确保其合金成分符合标准。
4.3 缺陷检测:利用X射线检测、超声波检测等方法,对铝铸件进行缺陷检测,确保其无内部缺陷。
五、安全注意事项:5.1 熔炼操作:在熔炼铝合金材料时,需注意熔炉的温度和操作规程,避免发生熔炉爆炸等事故。
5.2 铸造操作:在浇注和冷却过程中,操作人员需佩戴防护设备,避免烫伤和溅射伤害。
铸件热处理工艺指导书.doc
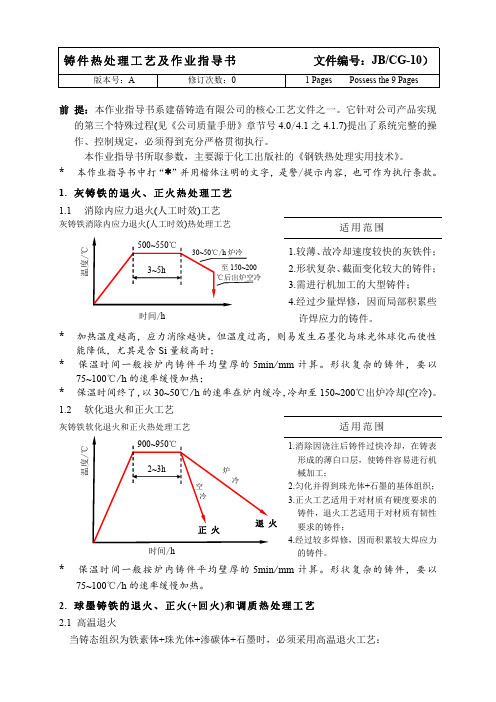
版本号:A修订次数:01Pages Possess the9Pages前提:本作业指导书系建蓓铸造有限公司的核心工艺文件之一。
它针对公司产品实现的第三个特殊过程(见《公司质量手册》章节号4.0/4.1之4.1.7)提出了系统完整的操作、控制规定,必须得到充分严格贯彻执行。
本作业指导书所取参数,主要源于化工出版社的《钢铁热处理实用技术》。
*本作业指导书中打“*”并用楷体注明的文字,是警/提示内容,也可作为执行条款。
1.灰铸铁的退火、正火热处理工艺1.1消除内应力退火(人工时效)工艺灰铸铁消除内应力退火(人工时效)热处理工艺适用范围1.较薄、故冷却速度较快的灰铁件;2.形状复杂、截面变化较大的铸件;3.需进行机加工的大型铸件;4.经过少量焊修,因而局部积累些许焊应力的铸件。
*加热温度越高,应力消除越快。
但温度过高,则易发生石墨化与珠光体球化而使性能降低,尤其是含Si量较高时;*保温时间一般按炉内铸件平均壁厚的5min/mm计算。
形状复杂的铸件,要以75~100℃/h的速率缓慢加热;*保温时间终了,以30~50℃/h的速率在炉内缓冷,冷却至150~200℃出炉冷却(空冷)。
1.2软化退火和正火工艺灰铸铁软化退火和正火热处理工艺适用范围*保温时间一般按炉内铸件平均壁厚的5min/mm计算。
形状复杂的铸件,要以75~100℃/h的速率缓慢加热。
2.球墨铸铁的退火、正火(+回火)和调质热处理工艺2.1高温退火当铸态组织为铁素体+珠光体+渗碳体+石墨时,必须采用高温退火工艺:版本号:A修订次数:02PagesPossess the 9Pages球墨铸铁高温退火热处理工艺适用范围1.获得铁素体球墨铸铁;2.分解渗碳体和珠光体,提高机械性能;3.改善加工性能,使工件容易加工且不易变形。
*退火温度越高,渗碳体组织分解速度越快,白口现象越易消除。
但温度过高将使铸件机械性能反而变坏,发生变形和表面氧化失碳,故须严格控制温度上限。
铝铸件作业指导书
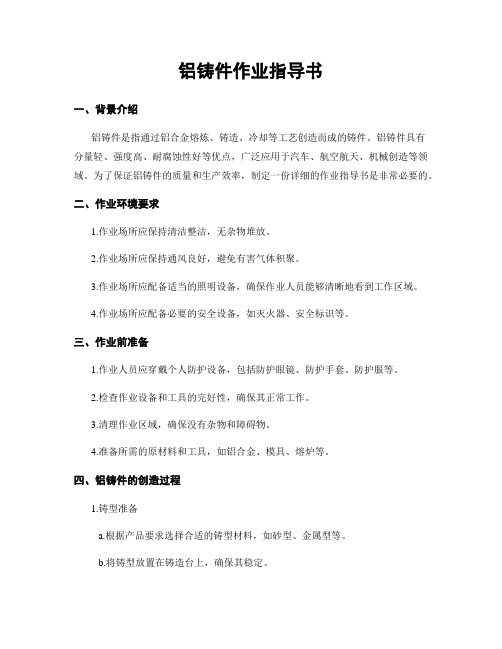
铝铸件作业指导书一、背景介绍铝铸件是指通过铝合金熔炼、铸造、冷却等工艺创造而成的铸件。
铝铸件具有分量轻、强度高、耐腐蚀性好等优点,广泛应用于汽车、航空航天、机械创造等领域。
为了保证铝铸件的质量和生产效率,制定一份详细的作业指导书是非常必要的。
二、作业环境要求1.作业场所应保持清洁整洁,无杂物堆放。
2.作业场所应保持通风良好,避免有害气体积聚。
3.作业场所应配备适当的照明设备,确保作业人员能够清晰地看到工作区域。
4.作业场所应配备必要的安全设备,如灭火器、安全标识等。
三、作业前准备1.作业人员应穿戴个人防护设备,包括防护眼镜、防护手套、防护服等。
2.检查作业设备和工具的完好性,确保其正常工作。
3.清理作业区域,确保没有杂物和障碍物。
4.准备所需的原材料和工具,如铝合金、模具、熔炉等。
四、铝铸件的创造过程1.铸型准备a.根据产品要求选择合适的铸型材料,如砂型、金属型等。
b.将铸型放置在铸造台上,确保其稳定。
c.根据产品要求,在铸型内涂抹防粘剂,以便于后续铸造过程中脱模。
d.根据产品要求,在铸型中放置芯子,以形成内部空腔。
2.熔炼铝合金a.根据产品要求,选择合适的铝合金材料。
b.将铝合金放入熔炉中,加热至熔点以上。
c.在熔炉中加入合适的合金元素,以调整铝合金的成份。
d.搅拌铝合金,使其成份均匀。
3.铸造a.将铝合金倒入铸型中,注意倒注的速度和角度,以避免产生气泡和缺陷。
b.待铝合金冷却至一定温度后,将铸件从铸型中取出。
c.对铸件进行修整,去除多余的毛刺和砂粒。
4.热处理a.根据产品要求,将铸件进行热处理,以提高其力学性能。
b.将铸件放入热处理炉中,按照热处理工艺曲线进行加热和冷却。
5.表面处理a.对铸件进行表面清洁,去除油污和氧化物。
b.根据产品要求,进行喷砂、抛光等表面处理工艺。
6.质量检验a.对铸件进行外观检查,检查是否有裂纹、气孔等缺陷。
b.对铸件进行尺寸测量,检查是否符合产品要求。
c.进行金相组织分析,检查铸件的显微组织结构。
热处理作业指导书

热处理作业指导书引言概述:热处理是一种重要的金属加工工艺,通过控制材料的温度和时间来改变其结构和性能。
为了确保热处理作业的质量和效率,制定一份热处理作业指导书是非常必要的。
本文将详细介绍热处理作业指导书的内容和要点。
一、热处理前的准备工作1.1 清洁工作:在进行热处理之前,要确保工件表面干净无杂质,可以采用化学清洗或者机械清洗等方法。
1.2 检查工件:对工件进行外观检查和尺寸测量,确保工件符合要求。
1.3 准备热处理设备:检查热处理设备的工作状态,保证设备正常运行。
二、热处理工艺参数设定2.1 确定热处理工艺:根据工件材料和要求,选择合适的热处理工艺,包括加热温度、保温时间和冷却方式等。
2.2 设定热处理参数:根据热处理工艺要求,设定炉温、保温时间和冷却速度等参数。
2.3 监控热处理过程:在热处理过程中,要及时监控温度和时间,确保工艺参数的准确性。
三、热处理作业操作流程3.1 上料:将清洁的工件放入热处理炉中,注意罗列方式和间距。
3.2 加热保温:根据设定的工艺参数,进行加热保温处理,保证工件达到所需温度。
3.3 冷却处理:根据工艺要求选择合适的冷却方式,如空冷、水冷或者油冷等,确保工件的结构和性能。
四、热处理后的检验与评定4.1 金相检验:对热处理后的工件进行金相组织观察,评定组织结构是否符合要求。
4.2 硬度测试:进行硬度测试,检测工件的硬度值是否符合标准。
4.3 尺寸测量:对工件的尺寸进行测量,确保尺寸精度符合要求。
五、热处理作业记录与存档5.1 记录数据:对热处理过程中的关键数据进行记录,包括炉温、保温时间、冷却方式等。
5.2 制作报告:根据记录的数据,制作热处理作业报告,包括工艺参数、操作流程和检验结果等。
5.3 存档管理:将热处理作业报告进行存档管理,确保数据的完整性和可追溯性。
结语:热处理作业指导书是热处理作业的重要参考依据,通过严格遵守指导书的要求,可以确保热处理作业的质量和效率。
铸造作业指导书

铸造作业指导书一、背景介绍铸造是一种常见的金属加工方法,通过将熔化的金属注入模具中,使其冷却凝固成为所需的形状。
为了确保铸造作业的质量和效率,制定一份详细的铸造作业指导书是非常必要的。
本文将详细介绍铸造作业的步骤、注意事项和相关数据,以匡助操作人员顺利完成铸造作业。
二、铸造作业步骤1. 准备工作:a. 检查模具的完整性和清洁度,确保模具表面光滑。
b. 准备所需的金属材料,保证其质量和纯度。
c. 准备熔炉和相关设备,确保其正常运行。
d. 确定铸造作业的工艺参数,包括熔化温度、浇注温度和冷却时间等。
2. 熔炼金属:a. 将金属材料放入熔炉中,加热至熔化温度。
b. 在熔炉中加入合适的熔剂,以提高金属的流动性和浇注性能。
c. 搅拌金属熔液,确保其温度均匀和成份均一。
3. 浇注金属:a. 将熔化的金属熔液倒入预先准备好的模具中。
b. 控制浇注速度和角度,以避免气泡和金属流动不均匀。
c. 注意保持模具的稳定,防止金属溅出和模具变形。
4. 冷却和固化:a. 等待金属冷却和固化,根据工艺参数确定冷却时间。
b. 可以采用冷却剂或者冷却设备加速冷却过程。
c. 确保金属彻底固化后,才干进行后续的处理和加工。
5. 后续处理:a. 将固化的金属件从模具中取出,注意避免损坏金属表面。
b. 进行必要的修整、清理和抛光等加工工序,以提高金属件的质量和外观。
c. 进行金属件的热处理、表面处理或者其他特殊处理,以满足客户的要求。
三、注意事项1. 安全第一:a. 操作人员必须戴好防护用具,包括手套、眼镜和耳塞等。
b. 遵守相关的安全操作规程,确保操作过程中的人身安全。
2. 温度控制:a. 严格控制金属熔化和浇注的温度,以避免金属质量不合格。
b. 注意金属熔液的温度变化,及时调整熔炉的加热功率。
3. 模具管理:a. 定期检查和维护模具,确保其完整性和清洁度。
b. 根据模具的使用情况,及时更换损坏的模具。
4. 浇注技巧:a. 控制浇注速度和角度,以保证金属流动的均匀性和浇注质量。
热处理作业指导书

热处理作业指导书一、引言热处理是一种重要的金属加工工艺,通过控制材料的加热和冷却过程,改变其组织结构和性能。
本作业指导书旨在为热处理作业提供详细的操作指导,确保作业过程准确、安全、高效。
二、作业准备1. 确定热处理工艺:根据材料类型、要求性能和工艺规范,选择合适的热处理工艺。
包括加热温度、保温时间和冷却方式等。
2. 准备设备和工具:确保热处理设备完好,如炉子、炉具、控温仪等。
同时,准备好所需的工具,如夹具、测量工具等。
3. 材料准备:检查材料的质量和表面情况,确保无油污、氧化层和其他污染物。
必要时进行清洗和抛光处理。
三、作业步骤1. 加热准备a. 将待处理材料放置在炉子内,注意合理布局,避免过于密集或者接触不良。
b. 设置炉温和保温时间,确保达到所需加热温度并保持一定时间。
c. 启动炉子,开始加热过程。
2. 保温处理a. 在达到所需加热温度后,关闭加热源,进入保温阶段。
b. 根据工艺要求,保持材料在所需温度下保温一定时间。
c. 使用控温仪监测和调整保温温度,确保温度稳定。
3. 冷却处理a. 根据工艺要求,选择合适的冷却方式。
常用的冷却方式包括水淬、油淬和空冷等。
b. 将材料从炉子中取出,迅速进行冷却处理。
根据工艺要求,可采用浸水、喷水、浸油等方式进行冷却。
c. 在冷却过程中,注意材料的位置和姿态,确保冷却效果均匀。
四、安全注意事项1. 作业人员必须戴好防护用品,包括耐高温手套、护目镜和防护服等。
2. 加热和冷却过程中,要保持炉子周围的通风良好,避免产生有害气体和烟雾。
3. 严禁在炉子附近堆放易燃、易爆物品,确保作业环境安全。
4. 在热处理过程中,严禁将手伸入炉子内或者触摸炉具,以免烫伤。
5. 作业结束后,确保炉子和设备的电源已关闭,防止意外发生。
五、质量控制1. 确保热处理工艺符合要求,包括加热温度、保温时间和冷却方式等。
2. 根据工艺要求,对处理后的材料进行性能测试,如硬度测试、金相分析等。
3. 对测试结果进行记录和分析,确保热处理效果达到预期要求。
铸造作业指导书
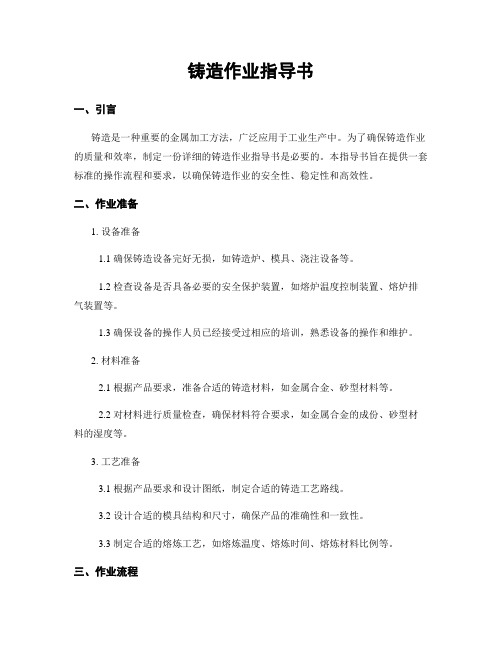
铸造作业指导书一、引言铸造是一种重要的金属加工方法,广泛应用于工业生产中。
为了确保铸造作业的质量和效率,制定一份详细的铸造作业指导书是必要的。
本指导书旨在提供一套标准的操作流程和要求,以确保铸造作业的安全性、稳定性和高效性。
二、作业准备1. 设备准备1.1 确保铸造设备完好无损,如铸造炉、模具、浇注设备等。
1.2 检查设备是否具备必要的安全保护装置,如熔炉温度控制装置、熔炉排气装置等。
1.3 确保设备的操作人员已经接受过相应的培训,熟悉设备的操作和维护。
2. 材料准备2.1 根据产品要求,准备合适的铸造材料,如金属合金、砂型材料等。
2.2 对材料进行质量检查,确保材料符合要求,如金属合金的成份、砂型材料的湿度等。
3. 工艺准备3.1 根据产品要求和设计图纸,制定合适的铸造工艺路线。
3.2 设计合适的模具结构和尺寸,确保产品的准确性和一致性。
3.3 制定合适的熔炼工艺,如熔炼温度、熔炼时间、熔炼材料比例等。
三、作业流程1. 模具准备1.1 清洁模具,确保模具表面光滑无杂质。
1.2 涂抹模具脱模剂,以便于产品脱模。
2. 熔炼材料准备2.1 准备合适的熔炼炉,根据熔炼工艺要求加入合适的熔炼材料。
2.2 控制熔炼温度和时间,确保熔炼材料充分熔化。
3. 浇注3.1 将熔融金属倒入模具中,确保金属充满整个模具腔体。
3.2 控制浇注速度和角度,以避免产生气泡和缺陷。
4. 冷却4.1 等待铸件冷却至合适的温度,以便于脱模和后续处理。
4.2 控制冷却时间,确保铸件的结构和性能稳定。
5. 脱模5.1 将冷却后的铸件从模具中取出。
5.2 检查铸件的表面和尺寸,确保符合产品要求。
6. 后续处理6.1 进行必要的修磨和打磨,以提高产品的表面光洁度和精度。
6.2 进行热处理或者其他特殊处理,以改善产品的性能。
四、作业安全1. 操作人员必须穿戴合适的个人防护装备,如防热手套、防护眼镜等。
2. 确保作业场所通风良好,以排除有害气体和烟尘。
铸钢件热处理作业指导书
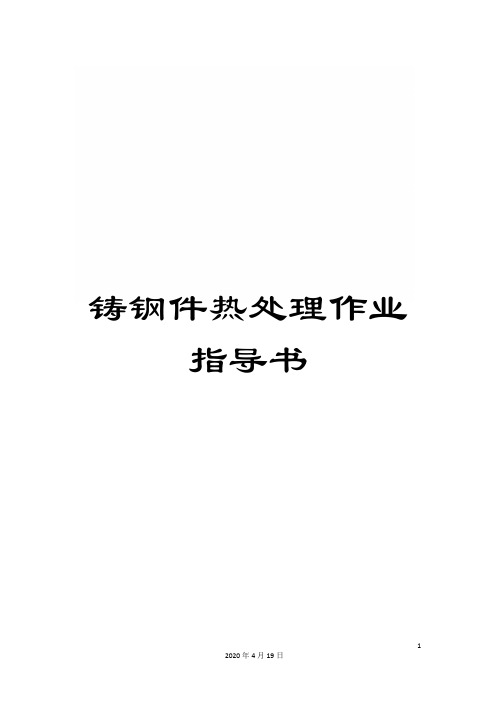
铸钢件热处理作业指导书热处理作业指导书1.目的保证热处理质量。
2.热处理方式按加热和冷却条件不同,铸钢件的主要热处理方式有:退火、正火、均匀化处理、淬火、回火、固溶处理、沉淀硬化、消除应力处理及除氢处理。
3.热处理操作要求3.1.退火退火是将铸钢件加热到Acs 以上20~30℃,保温一定时间,冷却的热处理工艺。
退火的目的是为消除铸造组织中的柱状晶、粗等轴晶、魏氏组织和树枝状偏析,以改进铸钢力学性能。
碳钢退火后的组织:亚共析铸钢为铁素体和珠光体,共析铸钢为珠光体,过共析铸钢为珠光体和碳化物。
适用于所有牌号的铸钢件。
图1—1为几种退火处理工艺的加热规范示意图。
表l—1为铸钢件常见退火工艺类型及其应用。
表1-2铸钢件退火工艺及退火后的硬度。
图1—1为几种退火处理工艺的加热规范示意图表l—1为铸钢件常见退火工艺类型及其应用表1-2铸钢件退火工艺及退火后的硬度3.2.正火正火是将铸钢件目口热到Ac。
温度以上30~50o C 保温,使之完全奥氏体化,然后在静止空气中冷却的热处理工艺。
图1—2为碳钢的正火温度范围示意图。
表1-3铸钢件正火工艺及退火后的硬度,表1-4常见低合金铸件正火或正火+回火工艺及硬度。
正火的目的是细化钢的组织,使其具有所需的力学性能,也司作为以后热处理的预备处理。
正火与退火工艺的区别有两个:其一是正火加热温度要偏高些;其二是正火冷却较快些。
经正火的铸钢强度稍高于退火铸钢,其珠光体组织较细。
一般工程用碳钢及部分厚大、形状复杂的合金钢铸件多采用正火处理。
图1—2为碳钢的正火温度范围示意图正火可消除共析铸钢和过共析铸钢件中的网状碳化物,以利于球化退火;可作为中碳钢以及合金结构钢淬火前的预备处理,以细化晶粒和均匀组织,从而减少铸件在淬火时产生的缺陷。
材质牌号含碳量(质量分数,%)正火温度/℃回火①硬度HBS温度/℃冷却方式ZG230—450ZG270—500 0.20~0.300.35~0.38880~850850~820—550~650133~156143~187件形状复杂者可在正火后回火,一般不必回火。
铸件热处理工艺及作业指导书主
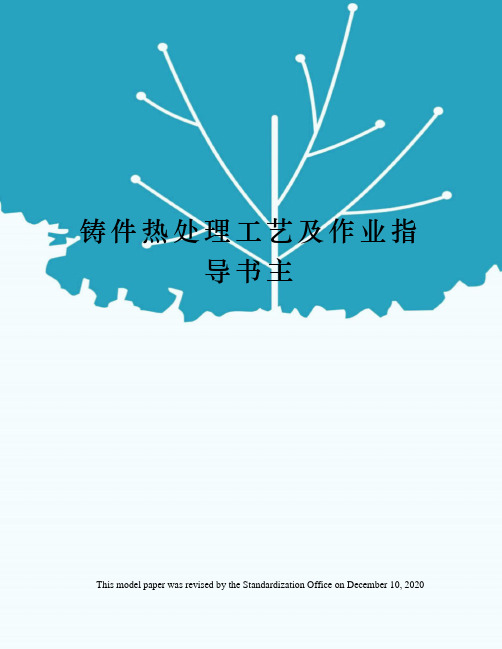
铸件热处理工艺及作业指导书主This model paper was revised by the Standardization Office on December 10, 2020前提:本作业指导书系建蓓铸造有限公司的核心工艺文件之一。
它针对公司产品实现的第三个特殊过程(见《公司质量手册》章节号之4.1.7)提出了系统完整的操作、控制规定,必须得到充分严格贯彻执行。
本作业指导书所取参数,主要源于化工出版社的《钢铁热处理实用技术》。
* 本作业指导书中打“*”并用楷体注明的文字,是警/提示内容,也可作为执行条款。
1.灰铸铁的退火、正火热处理工艺1.1消除内应力退火(人工时效)工艺灰铸铁消除内应力退火(人工时效)热处理工艺适用范围1.较薄、故冷却速度较快的灰铁件;2.形状复杂、截面变化较大的铸件;3.需进行机加工的大型铸件;4.经过少量焊修,因而局部积累些许焊应力的铸件。
* 加热温度越高,应力消除越快。
但温度过高,则易发生石墨化与珠光体球化而使性能降低,尤其是含Si量较高时;* 保温时间一般按炉内铸件平均壁厚的5min/mm计算。
形状复杂的铸件,要以75~100℃/h的速率缓慢加热;* 保温时间终了,以30~50℃/h的速率在炉内缓冷,冷却至150~200℃出炉冷却(空冷)。
1.2软化退火和正火工艺灰铸铁软化退火和正火热处理工艺适用范围3.正火工艺适用于对材质有硬度要求的铸件,退火工艺适用于对材质有韧性要求的铸件;4.经过较多焊修,因而积累较大焊应力的铸件。
* 保温时间一般按炉内铸件平均壁厚的5min/mm计算。
形状复杂的铸件,要以75~100℃/h的速率缓慢加热。
2.球墨铸铁的退火、正火(+回火)和调质热处理工艺高温退火当铸态组织为铁素体+珠光体+渗碳体+石墨时,必须采用高温退火工艺:适用范围1.获得铁素体球墨铸铁;2.分解渗碳体和珠光体,提高机械性能;3.改善加工性能,使工件容易加工且不易变形。
作业指导书(热处理)

作业指导书(热处理)第一篇:作业指导书(热处理)热处理是金属加工中常见的一种工艺,通过加热和冷却金属材料,可以改变其组织结构和性能。
热处理可以分为多种类型,包括退火、淬火、回火等。
本篇文章将重点介绍热处理的基本原理和常见方法。
热处理的基本原理是通过控制金属材料的加热和冷却过程,使其产生期望的组织结构和性能变化。
热处理的过程可以分为三个阶段:加热、保温和冷却。
加热过程将金属材料加热到一定温度,使组织发生相变。
保温过程使金属材料的组织结构得到稳定,并使其达到均匀性。
冷却过程是将金属材料迅速冷却,使其组织结构固定下来。
热处理的常见方法之一是退火。
退火是通过将金属材料加热至适当温度,然后缓慢冷却的过程。
退火可以改善金属材料的塑性和韧性,并降低其硬度。
退火适用于处理冷加工后的金属材料,可以消除内部应力、改善金属的可加工性。
淬火是热处理的另一种常见方法。
淬火是通过将金属材料加热至适当温度,然后迅速冷却的过程。
淬火可以使金属材料产生马氏体组织,提高其硬度和强度。
淬火后的金属材料通常呈脆性,需要进一步进行回火来提高其韧性。
回火是淬火的后续处理步骤,通过将淬火后的金属材料加热至一定温度,然后缓慢冷却。
回火可以降低金属材料的硬度,提高其韧性和抗冲击性。
回火的温度和时间选择取决于金属的种类和期望的性能。
除了退火、淬火和回火,热处理还包括正火、间歇淬火、表面淬火等多种方法。
正火是将金属材料加热至适当温度,然后以较慢的速度冷却的过程。
正火可使金属材料的组织结构细化,提高其强度和韧性。
间歇淬火是将金属材料加热至适当温度,然后在空气中冷却。
表面淬火是将金属材料表面加热至适当温度,然后迅速冷却。
热处理在金属加工中起到了重要的作用。
通过热处理,可以改变金属材料的性能,使其更适合特定的应用。
然而,不同的金属材料对热处理的响应有所差异,因此在进行热处理之前,需要对材料进行详细的分析和实验,以确定最合适的处理方法。
总结起来,热处理是金属加工中常见的一种工艺,通过加热和冷却金属材料,可以改变其组织结构和性能。
(JS01-001)零(铸)件热处理返工作业指导书
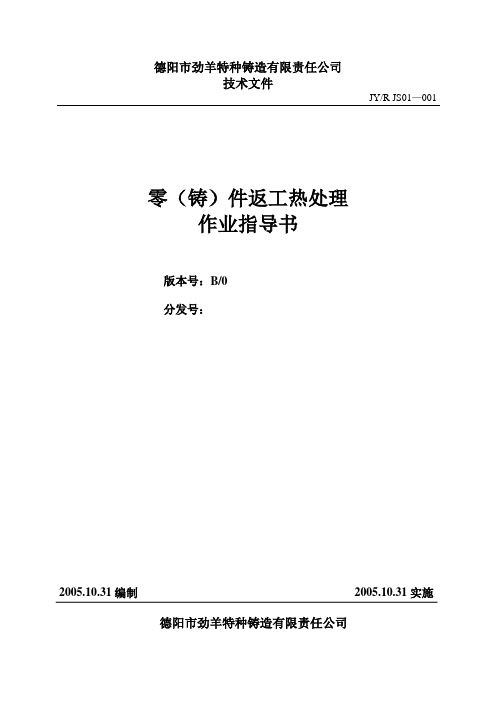
德阳市劲羊特种铸造有限责任公司技术文件JY/R JS01—001零(铸)件返工热处理作业指导书版本号:B/0分发号:2005.10.31编制2005.10.31实施德阳市劲羊特种铸造有限责任公司JY/R JS01—001 1 范围本文件规定了热处理后不合格零(铸)件返工热处理的工艺要求。
本文件适用于公司热处理零(铸)件的返工热处理。
2 返工处理工艺要求2.1 普通铸钢件的返工热处理按正常热处理工艺重新热处理。
当在井式炉中进行返工处理时,应滴入适量煤油保护防止表面脱碳。
2.2 灰铸铁铸件返工热处理2.2.1 铸件出现白口或渗碳体超标,采用石墨化退火,加热温度900—960℃,保温1—4h(取决于壁厚),炉冷至600℃以下出炉空冷。
2.2.2 铸件硬度偏高,采用740—800℃保温2—5.5h,炉冷至600℃以下出炉空冷。
2.2.3 铸件硬度偏低,采用正火处理,采用840—920℃保温2—5.5h, 出炉空冷。
2.3 球墨铸铁铸件返工热处理2.3.1铸件出现白口或渗碳体超标,采用高温石墨化退火,加热温度900—950℃,保温2—5.5h,炉冷至600℃以下出炉空冷。
2.3.2 铸件硬度偏高,采用740—800℃,保温3—6h,炉冷至600℃以下出炉空冷。
2.3.3 铸件硬度偏低,采用正火处理,采用840—920℃保温2—5.5h, 出炉空冷。
2.4 特殊产品返工热处理2.4.1 491G活塞销返工热处理及异常反应计划(1)渗碳层过浅(渗碳层厚度低于0.4mm时),补渗碳工艺为:渗碳温度910±10℃,保温时间3—5h,煤油滴入量为150—180d/分,其它要求按QP·R001执行。
(2)当渗碳温度超过上限但未超过940℃时,而超温时间≤30min时,允许继续渗碳,渗碳结束后检查渗碳层深度,合格时可继续下一工序。
当渗碳温度超过940℃并出现表层严重氧化时应报废处理。
(3)渗碳层>0.8mm或内外层加在一起>1.4mm时,零件作报废处理。
铸件热处理工艺及作业指导书主页

前提:本作业指导书系建蓓铸造有限公司的核心工艺文件之一。
它针对公司产品实现的第三个特殊过程(见《公司质量手册》章节号4.0/4.1之4.1.7)提出了系统完整的操作、控制规定,必须得到充分严格贯彻执行。
本作业指导书所取参数,主要源于化工出版社的《钢铁热处理实用技术》。
* 本作业指导书中打“*”并用楷体注明的文字,是警/提示内容,也可作为执行条款。
1.灰铸铁的退火、正火热处理工艺1.1消除内应力退火(人工时效)工艺灰铸铁消除内应力退火(人工时效)热处理工艺适用范围1.较薄、故冷却速度较快的灰铁件;2.形状复杂、截面变化较大的铸件;3.需进行机加工的大型铸件;4.经过少量焊修,因而局部积累些许焊应力的铸件。
* 加热温度越高,应力消除越快。
但温度过高,则易发生石墨化与珠光体球化而使性能降低,尤其是含Si量较高时;* 保温时间一般按炉内铸件平均壁厚的5min/mm计算。
形状复杂的铸件,要以75~100℃/h 的速率缓慢加热;* 保温时间终了,以30~50℃/h的速率在炉内缓冷,冷却至150~200℃出炉冷却(空冷)。
1.2软化退火和正火工艺灰铸铁软化退火和正火热处理工艺适用范围* 保温时间一般按炉内铸件平均壁厚的5min/mm计算。
形状复杂的铸件,要以75~100℃/h 的速率缓慢加热。
2.球墨铸铁的退火、正火(+回火)和调质热处理工艺2.1 高温退火适用范围1.获得铁素体球墨铸铁;2.分解渗碳体和珠光体,提高机械性能;3.改善加工性能,使工件容易加工且不易变形。
* 退火温度越高,渗碳体组织分解速度越快,白口现象越易消除。
但温度过高将使铸件机械性能反而变坏,发生变形和表面氧化失碳,故须严格控制温度上限。
* 保温时间也可按炉内铸件每15mm的有效厚度、需要保温1~2h计算,铸件白口深度大、渗碳体组织成分多时,应适当增加保温时间。
* 形状复杂的铸件,要以75~100℃/h的速率缓慢加热。
保温终了,以60~80℃/h的速率在炉内缓冷,至600℃后出炉空冷。
310S铸造工艺作业指导书
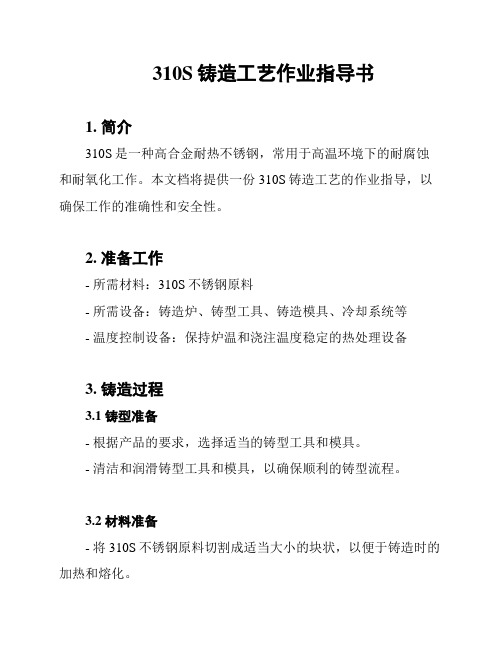
310S铸造工艺作业指导书1. 简介310S是一种高合金耐热不锈钢,常用于高温环境下的耐腐蚀和耐氧化工作。
本文档将提供一份310S铸造工艺的作业指导,以确保工作的准确性和安全性。
2. 准备工作- 所需材料:310S不锈钢原料- 所需设备:铸造炉、铸型工具、铸造模具、冷却系统等- 温度控制设备:保持炉温和浇注温度稳定的热处理设备3. 铸造过程3.1 铸型准备- 根据产品的要求,选择适当的铸型工具和模具。
- 清洁和润滑铸型工具和模具,以确保顺利的铸型流程。
3.2 材料准备- 将310S不锈钢原料切割成适当大小的块状,以便于铸造时的加热和熔化。
- 清洁原料,去除表面杂质和氧化物。
3.3 熔炼和浇注- 将准备好的原料放入铸造炉中,根据炉子的特性和要求设置适当的温度和时间。
- 熔炼过程中,要定期检查原料的状态和温度,确保不出现过热或过冷的情况。
- 当原料完全熔化并达到合适的浇注温度后,开始铸造。
3.4 冷却和固化- 在铸造完成后,将浇注的熔化金属进行冷却处理,以固化成型。
- 使用冷却系统控制冷却速度,避免内部应力和缺陷的产生。
4. 质量控制- 检查铸件表面的质量和完整性,确保没有裂纹、夹杂物和其他缺陷。
- 进行金相显微镜分析,检测晶粒细度和相变情况,以评估铸造工艺的效果。
5. 安全事项- 在熔炼和浇注过程中,必须戴防护眼镜、手套和其他个人防护装备,以防止火花和热炉对人体造成伤害。
- 注意铸炉和冷却系统的温度,防止烫伤和烧伤事故的发生。
以上是310S铸造工艺作业指导书的内容,希望对您的工作有所帮助。
如果有任何疑问,请随时与我们联系。
希望以上310S铸造工艺作业指导书的内容能对您的工作有所帮助。
请随时与我们联系,如果有任何疑问。
热处理作业指导书

热处理作业指导书引言概述:热处理是一种常见的金属材料加工方法,通过控制材料的加热和冷却过程,改变其组织结构和性能,以提高材料的力学性能、耐磨性和耐腐蚀性等。
本文将为您介绍热处理作业的指导书,包括热处理的基本原理、作业流程、注意事项和常见问题解答,以匡助您更好地进行热处理作业。
一、热处理的基本原理1.1 加热过程热处理的第一步是将材料加热到一定温度。
加热温度取决于材料的种类和要达到的性能要求。
常见的加热方法包括火焰加热、电阻加热和感应加热。
在加热过程中,需要注意以下几点:(1)控制加热速率:过快的加热速率可能导致材料内部应力过大,引起变形或者开裂。
因此,应根据材料的热导率和热膨胀系数,合理控制加热速率。
(2)保持均匀加热:确保材料在加热过程中均匀受热,避免浮现温度梯度过大的情况,以免引起组织不均匀或者应力集中。
1.2 保温过程在达到所需加热温度后,需要将材料保持在一定温度下,以使其组织发生相应的变化。
保温时间取决于材料的类型和要达到的性能要求。
在保温过程中,需要注意以下几点:(1)控制保温时间:过短的保温时间可能导致组织转变不彻底,影响材料的性能。
而过长的保温时间则可能导致材料的晶粒长大过大,影响材料的综合性能。
(2)保持稳定温度:保温过程中需要控制温度的稳定性,避免温度波动引起组织不均匀或者性能下降。
1.3 冷却过程在保温结束后,需要将材料迅速冷却,以固定其组织结构和性能。
冷却方法通常包括水淬、油淬和空冷等。
在冷却过程中,需要注意以下几点:(1)选择适当的冷却介质:根据材料的种类和要求的性能,选择合适的冷却介质。
不同的冷却介质会对材料的组织结构和性能产生不同的影响。
(2)控制冷却速率:过快或者过慢的冷却速率都可能导致材料的性能下降。
因此,需要根据材料的热导率和冷却介质的特性,合理控制冷却速率。
二、热处理作业流程2.1 准备工作(1)选择合适的材料:根据需要改善的性能要求,选择合适的材料进行热处理。
铸造作业指导书

1 蜡型1.压蜡温度48-53℃, 压蜡压力0.25-0.4MPa,保压时间10S, 起模时间5min。
2.合模前必须将上下模清理洁净后合模。
3.蜡模表面不得有缺陷。
3、蜡模表面不得有缺陷。
1.非加工面必须光滑、平整、无缺陷。
2、蜡模完全冷却后按左图示意摆放。
3、模样修整后, 不得有飞边、缺角、气孔、皱纹。
4、蜡屑清理洁净。
2.蜡模完全冷却后按左图示意摆放。
3、模样修整后,不得有飞边、缺角、气孔、皱纹。
4、蜡屑清理洁净。
2、蜡模完全冷却后按左图示意摆放。
3.模样修整后,不得有飞边、缺角、气孔、皱纹。
4、蜡屑清理洁净。
2、蜡模完全冷却后按左图示意摆放。
3、模样修整后,不得有飞边、缺角、气孔、皱纹。
4.蜡屑清理洁净。
2、蜡模完全冷却后按左图示意摆放。
3、模样修整后,不得有飞边、缺角、气孔、皱纹。
4、蜡屑清理洁净。
填写登记表(蜡模制造, 编号JZQ/ZZ-QR-02-01)2 浇口道蜡模1.使用05号浇口棒。
2.清理模具, 涂分型剂, 合模后注入蜡液。
3、将木棒插入半凝固蜡液中, 插入深度距离底部5-20mm。
4、冷却取出, 轻擦和模。
5、修刮飞边毛刺, 修补少许缺陷旳蜡模。
5.修刮飞边毛刺,修补少许缺陷旳蜡模。
5、修刮飞边毛刺,修补少许缺陷旳蜡模。
1.浇棒使用与否对旳。
2.检查木棒与否放正。
3.检查木棒插入深度与否符合规定。
3、检查木棒插入深度与否符合规定。
3 蜡模组焊1.焊接蜡件必须放正, 焊接牢固。
2.焊接后必须清理蜡屑。
3.模组焊接摆放整洁。
4.蜡型与浇口间距应不小于80mm。
4、蜡型与浇口间距应不小于80mm。
1.焊接前检查模样与否合格、浇口棒与否合格。
2.焊接后检查与否有缝隙和流蜡。
3.浇口冒口与否焊正。
4、焊接后与否将蜡屑吹洁净。
填写登记表(蜡模组焊, 编号:JZQ/ZZ-QR-02-02)4▲关键工序制壳1.表面层砂粒40-70目, 涂料粘度24-35S(夏季走下限、冬季走上限),用氯化铵硬化液比重1.05-1.12, 硬化时间10-15min, 空干15-20 min。
铸造作业指导书
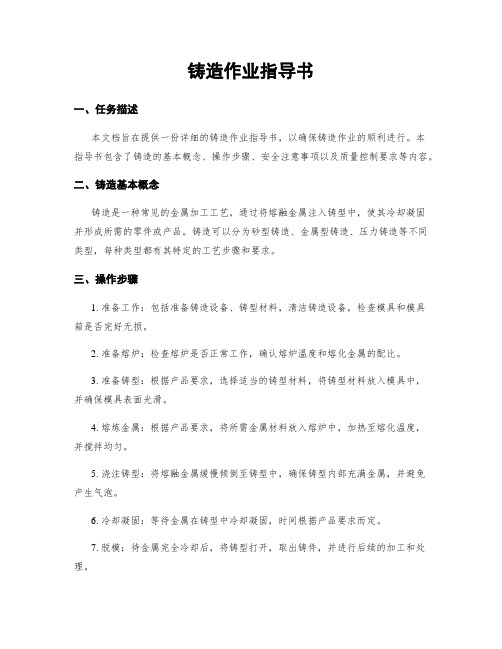
铸造作业指导书一、任务描述本文档旨在提供一份详细的铸造作业指导书,以确保铸造作业的顺利进行。
本指导书包含了铸造的基本概念、操作步骤、安全注意事项以及质量控制要求等内容。
二、铸造基本概念铸造是一种常见的金属加工工艺,通过将熔融金属注入铸型中,使其冷却凝固并形成所需的零件或产品。
铸造可以分为砂型铸造、金属型铸造、压力铸造等不同类型,每种类型都有其特定的工艺步骤和要求。
三、操作步骤1. 准备工作:包括准备铸造设备、铸型材料,清洁铸造设备,检查模具和模具箱是否完好无损。
2. 准备熔炉:检查熔炉是否正常工作,确认熔炉温度和熔化金属的配比。
3. 准备铸型:根据产品要求,选择适当的铸型材料,将铸型材料放入模具中,并确保模具表面光滑。
4. 熔炼金属:根据产品要求,将所需金属材料放入熔炉中,加热至熔化温度,并搅拌均匀。
5. 浇注铸型:将熔融金属缓慢倾倒至铸型中,确保铸型内部充满金属,并避免产生气泡。
6. 冷却凝固:等待金属在铸型中冷却凝固,时间根据产品要求而定。
7. 脱模:待金属完全冷却后,将铸型打开,取出铸件,并进行后续的加工和处理。
四、安全注意事项1. 穿戴个人防护装备:在进行铸造作业时,必须穿戴适当的个人防护装备,包括防护眼镜、耳塞、手套和耐高温服装等。
2. 避免熔融金属的溅落:在倾倒熔融金属时,要保持距离,避免熔融金属溅落到皮肤或衣物上,以免造成烫伤。
3. 注意熔炉安全:在操作熔炉时,要确保周围环境安全,避免发生火灾和爆炸等意外事故。
4. 遵守操作规程:严格按照操作规程进行作业,不得随意更改或省略步骤,以确保作业安全和产品质量。
五、质量控制要求1. 检查铸型:在使用铸型之前,必须对其进行仔细检查,确保没有损坏或缺陷。
2. 控制熔炼温度:根据产品要求,严格控制熔炼金属的温度,避免过高或过低,以免影响产品质量。
3. 检测铸件:对铸件进行必要的检测,包括外观检查、尺寸测量和材料成分分析等,确保产品符合要求。
4. 进行后续处理:根据产品要求,对铸件进行后续的热处理、表面处理等加工工艺,以提高产品的性能和质量。
热处理作业指导书

热处理作业指导书一、引言热处理是一种常见的金属加工工艺,通过控制材料的温度和时间来改变材料的物理和化学性质,以达到增强材料硬度、强度和耐磨性的目的。
本指导书旨在提供热处理作业的详细步骤和注意事项,以确保热处理过程的质量和安全。
二、作业准备1. 确定热处理工艺:根据材料的类型、要求的性能和使用条件,选择适当的热处理工艺,如退火、淬火、回火等。
2. 准备设备和工具:确保热处理设备和工具的正常运行,包括炉子、温度计、夹具、保护气体等。
3. 准备材料:检查材料的质量和规格,确保材料无损伤和污染,并进行必要的清洁处理。
三、作业步骤1. 温度控制:a. 预热炉子:将炉子预热至所需的温度。
b. 加热材料:将材料放入预热好的炉子中,确保材料均匀受热。
c. 控制温度:根据工艺要求,控制炉子温度,并持续保持一定的时间。
d. 冷却:根据需要,采取适当的冷却方式,如水淬、空气冷却等。
2. 时间控制:a. 确定保温时间:根据材料的类型和要求的性能,确定保温时间。
b. 控制保温时间:在保温过程中,严格控制保温时间,避免过短或过长的保温时间对材料性能造成影响。
3. 操作注意事项:a. 安全措施:佩戴适当的防护设备,如耐高温手套、护目镜等,确保操作人员的安全。
b. 操作规范:按照标准操作规程进行热处理作业,避免操作失误和事故发生。
c. 材料标记:对每个材料进行标记,包括材料类型、批次号等,以便追溯和管理。
d. 设备维护:定期检查和维护热处理设备,确保设备的正常运行和准确性。
四、质量控制1. 检测方法:根据要求,选择适当的检测方法,如金相分析、硬度测试、拉伸试验等,对热处理后的材料进行质量检测。
2. 检测标准:根据相关标准和规范,对热处理后的材料进行检测,并与要求的性能指标进行比对。
3. 记录和报告:对热处理过程中的关键参数和检测结果进行记录和报告,以备后续参考和追溯。
五、作业总结1. 分析总结:对热处理过程中出现的问题和不足进行分析总结,找出改进和提升的方向。
- 1、下载文档前请自行甄别文档内容的完整性,平台不提供额外的编辑、内容补充、找答案等附加服务。
- 2、"仅部分预览"的文档,不可在线预览部分如存在完整性等问题,可反馈申请退款(可完整预览的文档不适用该条件!)。
- 3、如文档侵犯您的权益,请联系客服反馈,我们会尽快为您处理(人工客服工作时间:9:00-18:30)。
热处理作业指导书
1. 目的
保证热处理质量。
2. 热处理方式
按加热和冷却条件不同,铸钢件的主要热处理方式有:退火、正火、均匀化处理、淬火、回火、固溶处理、沉淀硬化、消除应力处理及除氢处理。
3. 热处理操作要求
3.1 .退火
退火是将铸钢件加热到Acs以上20〜30C,保温一定时间,冷却的热处理工艺。
退火的目的是为消除铸造组织中的柱状晶、粗等轴晶、魏氏组织和树枝状偏析,以改善铸钢力学性能。
碳钢退火后的组织:亚共析铸钢为铁素体和珠光体,共析铸钢为珠光体,过共析铸钢为珠光体和碳化物。
适用于所有牌号的铸钢件。
图1 —1为几种退火处理工艺的加热规范示意图。
表I —1为铸钢件常用退火工艺类型及其应用。
表1-2铸钢件退火工艺及退火后的硬度。
图1—1为几种退火处理工艺的加热规范示意图
表I—1为铸钢件常用退火工艺类型及其应用
表1-2铸钢件退火工艺及退火后的硬度
3.2 .正火
正火是将铸钢件目口热到Ac。
温度以上30〜50°C保温,使之完全奥氏体化,然后在静止空气中冷却的热处理工艺。
图1—2为碳钢的正火温度范围示意图。
表1-3铸钢件正火工艺及退火后的硬度,表1-4常用低合金铸件正火或正火+回火工艺及硬度。
正火的目的是细化钢的组织,使其具有所需的力学性能,也司作为以后热处理的预备处理。
正火与退火工艺的区别有两个:其一是正火加热温度要偏高些;其二是正火冷却较快些。
经正火的铸钢强度稍高于退火铸钢,其珠光体组织较细。
一般工程用碳钢及部分厚大、形状复杂的合金钢铸件多采用正火处理。
图1—2为碳钢的正火温度范围示意图
正火可消除共析铸钢和过共析铸钢件中的网状碳化物,以利于球化退火; 可作为中碳钢以及合金结构钢淬火前的预备处理,以细化晶粒和均匀组
织,从而减少铸件在淬火时产生的缺陷。
表1-3铸钢件正火工艺及退火后的硬度
表1-4常用低合金铸件正火或正火+回火工艺及硬度
3.3 .淬火
淬火是将零件加热到奥氏体化后(Ac 。
或Ac •以上),保持一定时 间后以适当方式冷却,获得马氏体或贝氏体组织的热处理工艺。
常见的 有水冷淬火、油冷淬火和空冷淬火等。
零件淬火后应及时进行回火处理, 以消除淬火应力及获得所需综合力学性能。
图1 — 3为淬火回火工艺示意
1-5 零件淬火、回火工艺及硬度
图1 — 3为淬火回火工艺示意图
淬火工艺的主要参数:
(1)淬火温度:淬火温度取决于钢的化学成分和相应的临界温度点。
图
1
—3为铸钢件淬火工艺温度范围示意图。
原则上,亚共析钢淬火温度为
Ac 。
以上20〜30oC,常称之为完全淬火。
共析及过共析铸钢在 Ac 。
以上 30〜50oC 淬火,即所谓亚临界淬火或两相区淬火。
这种淬火也可用于亚 共析钢,所获
得的组织较一般淬火的细,适用于低合金铸钢件韧化处理。
⑵淬火介质:淬火的目的是得到完全的马氏体组织。
为此,零件淬火时 的冷却速率必须大于铸钢的临界冷却速率。
否则不能获得马氏体组织及 其相应的性能。
但冷却速率过高易于导致铸件变形或开裂。
为了同时满
胛
足上述要求,应根据零件的材质选用适当的淬火介质,或采用其他冷却
方法(如分级冷却等)。
在650〜400oC区间钢的过冷奥氏体等温转变速
率最快,因此零件淬火时应保证在此温度内快冷。
在Ms点以下希望冷
却缓慢一些,以防止淬火变形或开裂。
淬火介质通常采用火、水溶液、油和空气。
在分级淬火或等温淬火时,采用热油、熔融金属、熔盐或熔碱等。
表1-5铸钢件淬火、回火工艺及硬度
3.4 .回火
回火是将淬火或正火后的铸钢件加热到Ac,以下的某一选定温度,保温一定时间后,以适宜的速率冷却,使淬火或正火后得到的不稳定组织转变为稳定组织,消除淬火(或正火)应力以及提高铸钢的塑性和韧性的一种热处理工艺。
通常淬火加高温回火处理的工艺称之为调质处理。
淬火后的铸钢件必须及时进行回火,而正火后的铸钢件必要时才予以回火处理。
回火后铸钢件的性能取决于回火温度、时间及次数。
随着回火温度的提高和时间的延长,除使铸钢件的淬火应力消除外,还使不稳定的淬火马氏体转变成回火马氏体、托氏体或索氏体,使铸钢的强度和硬度降低,而塑性显著地提高。
对一些含有强烈形成碳化物的合金元素(如铬、钼、钒和钨等)的中合金铸钢,在400〜500oC回火时出现硬度升高、韧性下降的现象,称为二次硬化,即回火状态铸钢的硬度达到最大值。
一
般有二次硬化特性的中合金铸钢需要进行多次(1〜3次)回火处理。
铸钢件的回火按温度不同可分为低温回火和高温回火。
(1)低温回火:一般在150〜250OC温度范围内进行。
回火后可空冷、油冷或水冷。
其目的是在保留铸件高强度和硬度的条件下,消除淬火应力。
主要用于渗
碳、表面淬火及要求高硬度的耐磨铸钢件。
⑵高温回火:高温回火温度为500〜650oC,保温适当时间后冷却。
主要用于在淬
火或正火后调铸钢的组织,使之兼有高强度和良好韧性的碳钢和低、中合金钢铸件。
回火脆性是制定合金钢铸件回火工艺时必须注意的问题。
在下列两个温度范围内均可发生。
在250〜400oC 发生的脆性:经淬火成为马氏体组织的铸钢,在此温度范围内都会产生回火脆性。
如稍高于此脆性温度区回火,则可消除此回火脆性。
而且以后再在上述温度范围内回火时,也不会再出现回火脆性,故常称之为第一类回火脆性。
在400〜500OC(甚至650OC)发生的脆性:这对多数低合金铸钢都会发生,即发生铸钢的高温回火脆性。
如将已在此温度范围内产生脆性的铸钢件再加热到
600OC(或650OC)以上,之后在水或油中快冷,即可消除此种脆性。
然而已消除脆性的铸件,如又加热到产生回火脆性的温度,脆性又会出现。
这常称之为第二类回火脆性。
3.5 .固溶处理固溶处理是将铸件加热至适当温度并保温,使过剩相充分溶解,然后快速冷却以获得过饱和固溶体的热处理工艺。
固溶处理的主要目的是使碳化物或其他析出相溶解于固溶体中,获得过饱和的单相组织。
一般奥氏体不锈耐热钢、奥
氏体锰钢及沉淀硬化不锈耐热钢铸件均需经固溶处理。
固溶温度的选择取决于钢种的化学成分和相图。
奥氏体锰钢铸件一般为
1000〜1100oC奥氏体镍铬不锈钢铸件为1000〜1250OC。
铸钢中含碳量越高,难熔合金元素越多,则其固溶温度应越高。
含铜的沉淀硬化铸钢,由于铸态有硬质富铜相在冷却过程中沉淀,致使铸钢件硬度升高。
为软化组织、改善加工性能,铸钢件需经固溶处理。
其固溶温度为900〜950OC。
经快冷后可得到铜的质量分数为1.0%〜1.5%的过饱和单相组织。
3.6 .沉淀硬化处理 (时效处理 ) 铸件经固溶处理或淬火后,在室温或高于室温
的适当温度保温,在过饱 和固溶体中形成溶质原子偏聚区和 (或)析出弥散分布的强化相而使金属 硬化的处理称为沉淀硬化处理 ( 或时效处理 )。
在高于室温下进行的称为 人工时效。
其实质是:在较高的温度下,自过饱和固溶体中 析出碳化物、氮化物、金属间化合物及其他不稳定的中间相,并弥散分 布于基体中,因而使铸钢的综合力学性能和硬度提高。
时效处理的温度 直接影响铸钢件的最终性能。
时效温度过低,沉淀硬化相析出缓慢;温 度过高,则因析出相的聚集长大引起过时效,而得不到最佳的性能。
所 以应根据铸钢件的牌号及规定的性能要求选用时效温度。
奥氏体耐热铸 钢时效温度一般为550〜850oC,高强度沉淀硬化铸钢为 500oC,时间为
1〜4h 。
含铜的低合金钢和奥氏体耐热钢铸件以及低合金的奥氏体锰钢铸
件多采用时效处理。
图1-4为截面25mm 试样的时效效果。
图1-4
截面2亦n 试棒柱室温和时效处理的效果
I —2(X)T 时效:1] 一室温时效
——斷面收编率;一伸长率
3.7 .消除应力处理
-
富tx 碑铸瓷-H
童•斟U
吉心
盘
其目的是消除铸造应力、淬火应力和机械加工形成的应力,稳定尺寸。
一般加热到Ac,以下100〜200oC保温一定时间,随炉慢冷。
铸件的组
织没有变化。
碳钢、低合金钢或高合金钢铸件均可以进行处理。
3.8 .除氢处理
目的是去除氢气,提高铸钢的塑性。
加热到170〜200oC或280〜320oC, 长时间保温进行处理。
没有组织变化。
主要用于易于产生氢脆倾向的低合金钢铸件。