论低压渗碳技术在DCT项目中的开发及应用
低压真空渗碳的应用与展望

1 优 点 .
( )没有晶间氧化。 1
图1 法NE M低压真空渗碳气淬炉 C
( )由于真空 渗碳设备和工艺 的特 点 ,能够 2
6 27宰 筹。 熟 V 。2 期
晦
ww  ̄ . m e t l or c g g c m o w ll S . o n l O
’ V 热~ 参。 磊 …工 … 加
界先进技术 ,采取高起点、高投入的战略思路 ,在 2 0 年引进低压真空渗碳气淬炉 ,经过多年试验论 02
证 和生 产 应 用 ,取 得 超 出预 期 的实 际 效果 ,生 产效
率和质量大大提高 ,质量稳定可靠 ,为确保产品高
质 量奠 定 了基 础 。
次 性 投 入 费 用 相 对 较 大 ,但 是 产 品 质 量 明 显 提
、
环境影响和经济性分析
传统渗碳过程废气排放和油淬后 的清洗对于环
境 均 有 一 定污 染 。 作业 条 件 差 ,较 大 程 度制 约 着 企
研究更好的渗碳技术 ,以彻底给予改善和提升。
低 压 真 空 渗 碳 工 艺 技 术 可 采 用 更 高 的 工 艺 温 度 ,各 工 艺 参 数 控 制 依 靠 计 算 机 实 施 过 程 监 控 调 节 ,工 艺 技 术成 熟 ,在 解 决 渗碳 问题 、提 高 产 品 质
变形 可 以控 制 到 最小 程 度 。
2 缺点 . ( )与气氛渗碳设备 比较 ,需要更高的初始 1
业的发展或进步。真空低压渗碳工艺技术成功地解
决 了长 期 困 扰 企 业 的技 术 难 题 ,实 现 了 无 污 染 排
放 。采用高压氮气淬火冷却速度可控、无污染 ,热 处理形变更小,并且能够彻底解决内氧化难题 ,渗 碳质量得到大幅度提高 ,零件使用寿命成倍提升。 由于真空低压渗碳淬火高压气淬后 ,仍保持洁净表 面 ,可以省去后清洗工序 ,实现无污染绿色生产。 另外 ,低压真空渗碳温度可采用较传统渗碳更 高的温度 ,提高渗速 ,缩短生产周期 ,可大幅度节
渗碳工艺的中国专利分析

渗碳工艺的中国专利分析渗碳工艺是一种用于改善材料表面硬度和耐磨性的热处理工艺。
在中国,渗碳工艺的研究和发展颇具活力,许多专利对该工艺进行了深入的研究和应用。
本文将结合具体的专利案例,对渗碳工艺的中国专利进行分析,探讨其技术特点、应用范围以及发展趋势。
一、专利案例分析1. 《一种渗碳工艺的改进方法及其应用》该专利提出了一种基于气体渗碳的改进方法,通过控制渗碳温度和时间,使得渗碳层均匀且硬度高,从而提高了材料的耐磨性和使用寿命。
该方法适用于汽车零部件、机械设备等领域,具有很高的实用价值。
2. 《一种工件表面硬质合金渗碳处理工艺》该专利介绍了一种工件表面硬质合金渗碳处理工艺,采用了高频感应加热技术和特殊的渗碳液,可以在较短的时间内实现工件表面的硬质合金渗碳处理,提高了工件的表面硬度和耐磨性,适用于钢铁冶金、机械加工等行业。
该专利提出了一种新型高渗碳化学合金渗碳复合处理工艺,通过将渗碳剂与化学合金进行复合处理,可以形成均匀致密的渗碳层,显著提高了材料的硬度和耐磨性,同时降低了渗碳的成本,具有较高的经济效益。
二、渗碳工艺的技术特点从以上专利案例中可以看出,渗碳工艺在中国的专利研究中呈现出以下几个技术特点:1. 新型工艺改进许多专利案例都提出了一些新型的渗碳工艺改进方法,包括温度控制、时间控制、渗碳剂的改进等,使得渗碳层更加均匀、致密,提高了材料的硬度和耐磨性。
2. 技术与设备结合许多专利案例中都结合了先进的加热技术和特殊的渗碳设备,如高频感应加热技术、渗碳液等,使得渗碳工艺更加高效、环保、节能。
三、渗碳工艺的应用范围渗碳工艺在中国的专利研究中涉及的应用范围非常广泛,主要包括以下几个方面:1. 汽车零部件渗碳工艺可以用于汽车零部件的表面处理,如齿轮、曲轴、凸轮轴等,提高了零部件的表面硬度和耐磨性,延长了零部件的使用寿命。
3. 钢铁冶金渗碳工艺可以用于钢铁冶金行业,提高了钢铁的硬度和耐磨性,延长了材料的使用寿命,降低了生产成本。
低压真空渗碳工艺论文

低压真空渗碳工艺论文摘要:本文通过对可控气氛渗碳工艺和低压真空渗碳工艺各自特点及所采用设备的介绍,说明了低压真空渗碳工艺的优势所在,并指出其在汽车工业等领域的应用前景。
关键词:低压真空渗碳工艺、可控气氛渗碳工艺一、可控气氛渗碳工艺可控气氛渗碳工艺主要包括滴注式气体渗碳工艺、吸热式气体渗碳工艺、氮基气体渗碳工艺、直生式气体渗碳工艺。
滴注式气体渗碳工艺是在密封室内通入有机液体甲醇和丙酮(或乙酸乙酯等),以适当的数量直接滴人炉内而制得所需气氛的。
甲醇热裂分解产物的渗碳能力很低,它主要是起携带气的作用,使炉内有一定的正压;起渗碳作用的气体主要是由丙酮或乙酸乙酯热裂分解形成的。
滴注式气体渗碳工艺对设备要求较低,碳势控制精度较差,只适用于一般零件的处理。
吸热式气体渗碳工艺的渗碳气氛由吸热式气体加富化气组成,吸热式气体主要包括天然气、煤气、丙烷、丁烷等,一般采用甲烷或丙烷作富化气。
需要有吸热式气氛发生装置。
氮基气氛渗碳工艺是指以氮气作为载体添加富化气进行渗碳的工艺,富化气主要有丙烷、丙酮等,同时通入甲醇作为基础气氛。
直生式气氛渗碳工艺是将燃料与氧化剂直接通入炉内形成渗碳气氛的工艺。
采用上述各渗碳工艺时,各种有机液体热裂分解时产生的主要是CO和H。
同时还存在少量的其它产物。
在一定条件下,达到平衡时,炉气的各成分之间具有一定的比例平衡关系。
可控气氛渗碳工艺已应用多年,积累了丰富的经验,可以满足一般零件的性能要求,但也有自身的缺点,例如:无法解决表面内氧化问题,即在渗层表面出现一层很薄的非马氏体组织,影响零件的疲劳性能;无法解决高温渗碳及深层渗碳问题;生产能耗高;生产区域环境较差。
这些设备一般都布置在独立的热处理车间,或者与机加工车间组建联合厂房,但与机加工车间之间需要有隔墙,以减少对加工设备的影响,并要求加强热处理车间的排烟措施,改善生产环境。
二、低压真空渗碳工艺低压真空渗碳工艺的真空压力一般为10—100Pa。
浅谈低压真空渗碳工艺

浅谈低压真空渗碳工艺职教台浅谈低压真空渗碳工艺王东波(攀枝花学院四川攀枝花617000)摘要:介绍了低压真空渗碳的原理,渗碳常用介质,渗碳过程的控制,从被加工件性能,精度,效率,加工成本等多个方面阐述了低压真空渗碳工艺的特点,同时对低压真空渗碳工艺的发展进行了简述.关键词:低压真空渗碳随着工业技术的不断发展,对工件热处理的要求也越来越高.8O年代出现的可控气氛渗碳技术虽已非常完善,但由于其内氧化不可避免,会在渗层表面出现一层很薄的非马氏体组织,对零件的疲劳性能产生不良影响,所以,热处理工作者一直在研究一种更为完善的渗碳工艺.1980年,法国ECM公司在PVF300型真空淬火炉上添加渗碳装置后进行实验获得了满意的成果,并在实验室初步建立了富化率(单位时间内工件表面积上吸收碳原子的质量)理论.1982年,它们第一次展示了低压渗碳过程,并与1988年建造了第一条连续生产线.自此,人们在低压真空渗碳技术上取得了重大突破,一种新的热处理技术在表面处理上得到了逐步的推广和应用.一,低压真空渗碳工艺简介1,低压真空渗碳原理渗碳就是向工件表面渗入碳原子的过程.其目的是提高工件表面碳浓度,使工件心部保持较好塑韧性的同时增强表面硬度和耐磨性.低压真空渗碳实际上就是在低压(压力一般不大于3kPa)真空状态下,通过多个强渗(通人渗碳介质)和扩散(通入保护气体)循环进行,以此提高工件表面碳浓度,从而使其达到热处理要求的工艺过程.2,低压真空渗碳工艺设备简介低压真空渗碳设备是与低压真空渗碳技术同时出现的一种设备,其突出特点是选择的多样性(单室,双室,三室,多室;立式,卧室;周期性,生产线式等),并且具有多种用途(真空渗碳,真空碳氮共渗,真空渗碳+气淬等)和先进的渗碳控制系统(计算机模拟软件等).标准的低压真空渗碳炉由一个或多个加热渗碳室(根据产量选择),一个气淬室,一个装卸料室,一个传送室以及整套的工件传输系统,真空系统,气体循环系统,计算机监控系统等组成.3,低压真空渗碳介质的选择20世纪90年代,低压真空渗碳介质以丙烷为碳源得到了认可,但由于丙烷气在低压真空渗碳中可能有不同的分解反应,当温度高于600℃时,丙烷会在加热室,被加工件附近大量分解,一c+2+2[c】,c=I一2c+【c】,致使加热室内形成碳黑.而又因炉内温度不均匀,在炉子中相对温度较低的部位会形成焦油,对渗碳设备极为有害.所以,乙炔做为渗碳介质也被人们所重视.它以其经济,渗碳压力低,能基本消除碳黑和焦油等优点在在低压真空渗碳中得到一定的推广,特别在小直径,长盲孑L零件的均匀渗碳,高密度和大容量的工件装炉上得到广泛应用.4,低压真空渗碳的控制由于在真空状态下无法通过常规氧势测量的方法来定碳,因此随着富化率概念及相关理论的提出,人们开发出相关的计算机模拟软件来解决这一问题.低压真空渗碳采用渗碳和扩散脉冲方式交替进行,渗碳一般通丙烷,扩散通氮气.在渗碳和扩散过程中,真空系统调节炉压并保持定值,丙烷与氮气流量也保持恒定,并由质量流量计显示通入量.计算机模拟系统根据用户事先输入的渗碳温度,被渗工件原始碳浓度,渗碳后表面饱和碳浓度,扩散后表面碳浓度,最终表面碳浓度,渗碳层深度,介质在工件表面的富化率等工件特性,模拟计算出"渗碳+扩散"的循环次数和每个循环的不同时间参数,并模拟出最终的渗层深度,其精度可达到±5%.二,低压真空渗碳工艺的特点低压真空渗碳技术的应用有助于产品质量和技术能级的提高,与可控气氛渗碳工艺相比较,低压真空渗碳有许多优点:1,提高被加工件的性能由于在真空下进行渗碳处理,没有氧的存在,因此渗层表面没有晶间氧化和表面非马氏体,同时不会产生表面合金元素的贫化及其带来的表面淬透性降低等问题,零件表面硬度,表面残余应力水平将明显提高,可以明显降低零件表面的早期失效,提高零件的使用寿命.如1998年上海股份汽车齿轮总厂为进一步提高齿轴类零件热处理质量,委托法国EMC公司对集中变形要求较高的零件用JCBP一400型低压渗碳炉进行实验,部分结果如下:产品名称:输出轴;材料:20MnCr5;数量:3件;热处理要求:表面硬度680—780HV30,心部硬度350—480HV30;有效硬化层深度(硬度550HV1)O.7—1.0mm.在装满炉量情况下实验,主要工艺参数如下:渗碳温度:950~C;加热和均温时间:50rain;渗碳时间:10.13min;扩散时间:78.87min;淬火介质:高纯氮气;淬火压力:2Mpa;淬火时间:10min;富化率:13.8lmg/h?cm;回火温度:150~(2;回火时间:2.5h.实验后测得的金相结果如下:表面硬度(HV30):725,728,727心部硬度(HV30):434.442齿面有效硬化层深度(硬度550HV1):O.78ram齿面显微组织:碳化物(1级)+残余奥氏体(2级)+马氏体(2级),无明显非马氏体组织,实验后变形较小.从实验结果看,硬度,渗层深度,显微组织均能满足要求,46现代企业教育MODERNENTERPRISEEDUCATION2009年?O8月?下期学术?理论现代衾誊现代高等职业教育的校长素质探讨杨鲁新(青岛恒星职业技术学院动画学院山东青岛266100)摘要:伴随着经济发展我国的职业教育出现了快速发展的局面.主要管理者的管理素质直接影响到高等职业教育的办学水平和质量.本文旨在从管理素质,政治素质,管理才能,学术技术能力,工作责任感这几个维度衡量一个高等职业教育管理者的优秀程度.关键词:高等职业教育校长院长管理素质政治素质管理才能学术技术能力工作责任感白改革开放以来,伴随着经济发展的需要,我国的职业教育出现了快速发展的局面,原来仅在普通高中阶段设立的职业教育已经难以满足社会发展的需求,因此,越来越多的大学增设了大专层次的高等职业教育,另外,更有不少独立的高等职业技术学院纷纷出现,这样的现象已经在改变着原有的高等教育布局.虽然普通大学本科教育仍为高等教育的主体,但不断增加的高等职业教育已经成为高教领域的另一条腿,这样的教育局面无疑会对我国的经济发展起到有益的作用,但也对我国的高等职业教育提出了新的问题,即:靠什么样的人来管理现代高等职业教育工作.由于我国的高等职业教育发展很快,特别是在多元化的办学政策推动下,许多民间资本进入高等教育领域,他们主要集中在高等职业教育范围,这就形成了国有民营齐办,全国处处开花的高等职业教育办学格局,但随之而来的则是高等职业教育管理者的缺位.与发达国家相比,我国的高等职业教育正处在发展的初期,各方面的经验都比较缺乏,但最为缺乏则是经验丰富的合格管理人员,尤其是高等职业院校的校长(以及下级学院的院长).目前,许多职业技术院校对校长(或院长)的任用都具有很大的随意性,这些来自不同岗位和部门的管理者在社会背景,工作经验,管理能力以及学术水平方面存在很大的差异,因而形成了管理者基本水平的良莠不齐,其中还有一定数量的管理者不具备高等职业教育的管理能力.也达不到高等教育对管理者的基本要求,如果不能有效提高改变这样的状况,我们现有的高等职业教育就不可能健康的发展,而教育管理素质较差的管理者从事管理的学校,是很难培养出合格的高等技术人才的.由于管理者的管理素质直接影响到高等职业教育的办学水平和质量,因此,在大力发展高等职业教育的今天,如何认识高等职业管理者的基本素质以及行为特点是个值得研究和探讨的问题.同时工件的变形情况也大为改善,处理结果比较理想.2,精度,效率高低压真空渗碳技术使得传统渗碳工艺中的高温渗碳成了可能,渗速明显提高,工艺周期显着减小,大大的缩短了渗碳时间, 特别对需要取得较深碳层的工件或不锈钢,硅钢等材料非常有利.如低碳钢中,为获得1mm厚的总渗碳深度,在980℃渗碳时所需的总渗碳时间为1.50h,在1038~渗碳是仅需0.80h,相差约2 倍.同时,由于在渗碳过程中,碳势的控制由计算机软件来完成, 所以,所以在实践中可以获得比较准确的控制效果.据有关实验测试.控制精度可达到±0.05ram.3,减少了后续工序.降低了热处理成本低压真空渗碳工艺是在真空状态下对工件进行加热渗碳,所以,避免了大范围的氧化,处理后产品呈银灰色,光亮状,可以不经过清洗,清理喷丸等工序,所以减少了后续的处理工序,有效的降低了成本.4,"绿色"环保相对于常规的可控气氛渗碳(或碳氮共渗)热处理,低压真空渗碳热处理过程中不产生,)1等有害气体,同时大部分采用气体淬火技术且淬火气体可以回收,即使采用油淬技术,也是采用真空淬火油,避免了大量的气体和液体污染,具有"绿色"环保的特点.三,结束语低压真空渗碳技术是将真空渗碳与高压气淬两项技术结合后的产物.它以其特殊的优势和成熟的工艺在渗碳特别是深层渗碳领域得到广泛的应用,根据中国热处理行业协会在欧洲考察的报告,到2010年低压真空渗碳热处理设备将达到50%左右,其工艺应用领域也将得到大范围的扩展,必将成为替代常规渗碳技术的工艺之一.参考文献:【l】孟延军,关昕.金属学及熟处理.北京:冶金工业出版社,2008 (03l【2】严韶云.低压真空渗碳——一种新的化学热处理技术.机械工人(热加工),2001(1):31—33.【3】张连进.一种快速渗层渗碳技术.金属热处理,2003,28(10): 56-58.【4】马森林,高文栋,沈玉明.ECM低压真空渗碳技术应用研究与探讨.汽车工艺与材料,2004(8):27—3O.【5】马森林,沈玉明.ECM低压真空渗碳技术应用研究与探讨. 汽齿科级,2004(1):1—6.【6】6张连进.真空渗碳技术的进展.真空,2003(1):42—45. 【7】高文栋.低压真空渗碳设备的特点及生产应用.机械工人(热加工),2007(10):22—23.【8】朱连光,王砚军,李庆见.脉冲式气体渗碳技术研究和应用.汽车工艺与材料,2005(6):21—23.口现代企业教育MODERNENTERPRlSEEDUCATION47。
低压渗碳真空炉原理
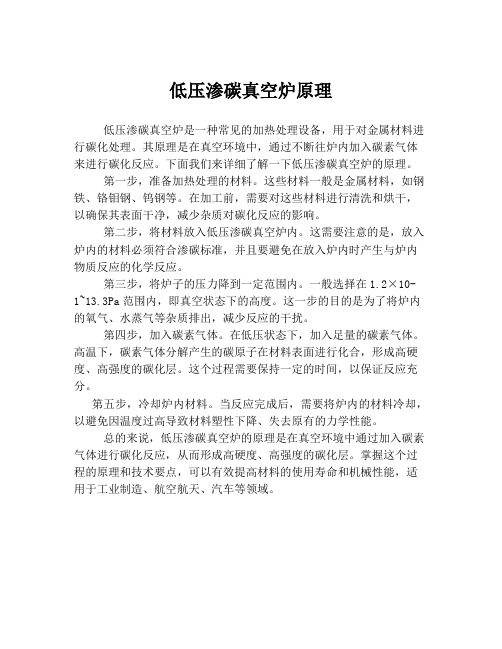
低压渗碳真空炉原理
低压渗碳真空炉是一种常见的加热处理设备,用于对金属材料进行碳化处理。
其原理是在真空环境中,通过不断往炉内加入碳素气体来进行碳化反应。
下面我们来详细了解一下低压渗碳真空炉的原理。
第一步,准备加热处理的材料。
这些材料一般是金属材料,如钢铁、铬钼钢、钨钢等。
在加工前,需要对这些材料进行清洗和烘干,以确保其表面干净,减少杂质对碳化反应的影响。
第二步,将材料放入低压渗碳真空炉内。
这需要注意的是,放入炉内的材料必须符合渗碳标准,并且要避免在放入炉内时产生与炉内物质反应的化学反应。
第三步,将炉子的压力降到一定范围内。
一般选择在1.2×10-
1~13.3Pa范围内,即真空状态下的高度。
这一步的目的是为了将炉内的氧气、水蒸气等杂质排出,减少反应的干扰。
第四步,加入碳素气体。
在低压状态下,加入足量的碳素气体。
高温下,碳素气体分解产生的碳原子在材料表面进行化合,形成高硬度、高强度的碳化层。
这个过程需要保持一定的时间,以保证反应充分。
第五步,冷却炉内材料。
当反应完成后,需要将炉内的材料冷却,以避免因温度过高导致材料塑性下降、失去原有的力学性能。
总的来说,低压渗碳真空炉的原理是在真空环境中通过加入碳素气体进行碳化反应,从而形成高硬度、高强度的碳化层。
掌握这个过程的原理和技术要点,可以有效提高材料的使用寿命和机械性能,适用于工业制造、航空航天、汽车等领域。
低压真空渗碳设备的特点及生产应用
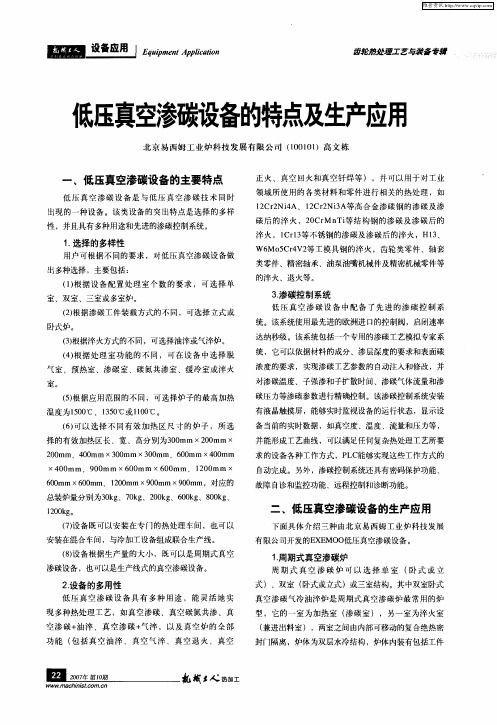
鬣 圈
堡 壁 却i npc 兰 里J eAli p tpa m 空 碳设 特 及 产 用
北京易西姆工业 炉科技 发展有 限公 司 (0 1 1 10 0 )高文栋
一
低压真空渗碳设备的主要特点
周 期 式 真 空 渗 碳 炉 可 以 选 择 单 室 ( 式 或 立 卧 式 )、双室 ( 卧式或立式 )或三室结构 。其 中双室卧式
2设备的多用性 .
低压 真 空 渗 碳 设备 具 有 多 种 用途 ,能 灵 活 地 实 现 多种热处 理工 艺 ,如真 空渗碳 、真 空碳氮 共渗 、真 空 渗碳 + 油淬 、真 空渗 碳 + 气淬 ,以 及真 空 炉 的全 部 功 能 ( 括 真 空 油淬 、真 空 气淬 、真 空退 火 、真 空 包
() 既可以安装 在专 门的热处理车 间 ,也 可以 7设备
安装在混合车 间,与冷加工设备组成联合生产线 。
有限公司开发的E E O X MO 低压真空渗碳 设备 。
( 设备 根据生产 量的大小 ,既可 以是周期式 真空 8 ) 渗碳设备 ,也可以是生产线式的真空渗碳设备 。
1周期式真空渗碳炉 I
正火 、真空 回火 和真 空钎焊 等 ) ,并 可以用 于对 工业 领域所 使用 的各 类材料 和零 件进 行相关 的热 处理 ,如 1C 2 iA、1C 2 3 等 高合 金渗 碳钢的 渗碳 及渗 2 rN 4 2 rNiA 碳后 的淬 火 ,2 C Mn i 结构 钢的 渗碳 及渗 碳后 的 0 r T等
() 应用范 围的不 同 ,可选择 炉子的最 高加热 5根据
温度为10  ̄ 50 C、15  ̄ 10 ℃。 30 C或 10
() 以 选 择不 同有效 加 热 区尺 寸 的炉 子 ,所 选 6可 择 的有效加 热区长 、宽、高分 别为 30 m × 0 mm× 0m 20
低压真空渗碳技术在轴齿热处理中的应用与变形控制

2021年第3期2021No.3汽车工艺与材料Automobile Technology &Material低压真空渗碳技术在轴齿热处理中的应用与变形控制王达鹏1郭成龙2董笑飞3吴宁4姜瑜1高志勇3(1.中国第一汽车集团有限公司工程与生产物流部,长春130011;2.一汽解放汽车有限公司传动事业部,长春130011;3.中国第一汽车集团有限公司研发总院,长春130011;4.一汽解放商用车开发院工艺材料部,长春130011)摘要:介绍了轴齿低压真空渗碳热处理技术的设备系统、工艺原理及实施过程,阐述真空热处理技术应用优势,分析真空热处理技术与传统可控气氛热处理技术的差异;针对变速箱齿轮热处理后变形控制对后续加工和装配工艺有较大影响,分别从材料、气淬压力、预冷温度、装炉方式等多个维度讨论研究某变速箱齿轮渗碳热处理变形的影响因素,分析控制齿轮热后变形的一般办法,保证轴齿产品质量,为变速箱轴齿真空热处理技术的进一步推广应用提供支持。
关键词:真空炉渗碳淬火变形控制影响因素中图分类号:U466文献标识码:BDOI:10.19710/ki.1003-8817.20200141Application and Deformation Control of Low Pressure VacuumCarburizing Technology in Shaft Tooth Heat TreatmentWang Dapeng 1,Guo Chenglong 2,Dong Xiaofei 3,Wu Ning 4,Jiang Yu 1,Gao Zhiyong 3(1.Engineering and Production Logistics Department of China FAW Group Co.,Ltd.,Changchun 130011;2.FAW Jiefang Automobile Co.,Ltd.Transmission Division,Changchun 130011;3.General Research &Institute of China FAW Group Co.,Ltd.,Changchun 130011;4.Process &Materials Department of FAW Jiefang Commercial Vehicle Development Institute,Changchun130011)Abstract :This paper introduces equipment system,process principle and implementation process of low-pressure vacuum carburizing heat treatment technology for shaft teeth,elaborates the advantages of vacuum heat treatment technology application,and analyzes the difference between vacuum heat treatment technology and traditional controllable atmosphere heat treatment technology.Since deformation control post gearbox gear heat treatment has great impact on subsequent processing and assembly processes,the factors affecting the carburizing heat treatment deformation of a gearbox gear are discussed and studied from multiple dimensions such as material,gas quenching pressure,pre-cooling temperature,and furnace loading method,and the general approach to control the deformation of the gear after thermal treatment is analyzed,to ensure the quality of shaft gear products and provide support for the further promotion and application of gearbox shaft gear vacuum heat treatment technology.Key words:Vacuum furnace,Carburizing and quenching,Deformation control,Influencing factors作者简介:王达鹏(1988—),男,工程师,学士学位,研究方向为汽车用金属材料成形技术、金属材料与热处理技术。
单片机原理及应用(特色) 渗碳体

单片机原理及应用(特色)渗碳体单片机原理及应用在现代科技领域中扮演着重要的角色,而渗碳体则是单片机应用中一个备受关注的技术。
渗碳体是指通过对金属表面进行渗碳处理,使其表面形成碳化物层,从而提高金属的硬度、耐磨性和耐腐蚀性能。
在单片机控制下实现渗碳体的制备和应用,不仅可以提高生产效率,还可以保证产品质量,具有广阔的市场前景。
单片机是一种集成了微处理器、存储器和各种输入输出接口的微型计算机系统,具有体积小、功耗低、成本低等特点,广泛应用于自动化控制、通信、家电等领域。
在渗碳体制备中,单片机可以实现精确的温度控制、时间控制和过程监测,提高了渗碳体的生产效率和产品质量。
单片机控制下的渗碳体制备过程主要包括预处理、渗碳处理和后处理三个阶段。
预处理阶段主要是对金属工件表面进行清洁和预热处理,以保证渗碳过程的顺利进行;渗碳处理阶段是将金属工件放入渗碳剂中,在一定温度下进行一定时间的渗碳处理,使金属表面形成均匀的碳化物层;后处理阶段则是对渗碳体进行冷却、清洗和涂层等处理,以提高其表面光洁度和耐腐蚀性能。
单片机在渗碳体制备中的应用主要体现在温度控制和时间控制两个方面。
温度控制是指单片机通过传感器实时监测渗碳炉内的温度,并根据设定值控制加热元件的工作状态,以保证渗碳过程中的温度稳定性;时间控制则是通过单片机内部的定时器控制渗碳处理的时间,确保每个工件都能得到相同的处理时间,保证产品质量的一致性。
除了在渗碳体制备中的应用外,单片机在渗碳体的应用过程中也发挥着重要作用。
例如,在汽车发动机气门的制造中,渗碳体可以提高气门的硬度和耐磨性,延长使用寿命;在机械零件的制造中,渗碳体可以提高零件的耐磨性和抗磨损性能,提高设备的可靠性和稳定性。
总的来说,单片机原理及应用在渗碳体制备中具有巨大的潜力和市场前景。
通过单片机的精确控制,可以实现渗碳体制备过程的自动化和智能化,提高生产效率和产品质量,满足不同行业对金属材料性能的要求,推动工业制造的发展。
低压渗碳技术在汽车变速箱行业中的应用

62018年 第8期 热加工低压渗碳技术在汽车变速箱行业中的应用■ 舒银坤,汪杰摘要:介绍了德国ALD 低压真空渗碳的技术原理、工艺过程。
阐述了低压渗碳与可控气氛渗碳工艺之间的差异。
实际生产应用表明,采用低压渗碳高压气淬技术,生产的零件表面洁净、渗层均匀、淬火变形小。
关键词:低压真空渗碳;汽车变速箱;高压气淬;变形扫码了解更多现代汽车及零部件制造业最具挑战性的任务在于提高能效的同时还要实现“绿色”制造,保护环境,实现可持续发展。
传统的可控气氛渗碳/油淬作为一种有效的表面硬化技术,已经在行业内应用40余年。
传统的渗碳淬火工艺存在渗层均匀性差、容易出现黑色组织、生产能效低、CO 2等有害气体排放多等问题,因此迫切需要推广应用新技术来满足汽车制造业日益增长的市场需求以及实现“绿色”热处理。
自20世纪90年代中期以来,真空低压渗碳/高压气淬技术已逐步开发来满足高质量、高生产率和环境相容的要求。
在欧洲、美国、日本等发达国家真空低压渗碳技术已经得到了广泛应用。
我公司变速箱中的各项制造技术水平一直居于行业前列,2015年斥资约5000万元购置了由德国ALD 公司制造的真空渗碳高压气淬热处理生产线(见图1),对变速箱中的齿轮轴进行热处理。
一、低压真空渗碳及高压气淬工艺1. 低压真空渗碳原理及过程低压渗碳的原理:低压渗碳是一种非平衡的增强扩散型渗碳工艺,工件在低压(8~15mbar ,1bar=105pa )真空状态下,由交替的渗碳和扩散构成的脉冲式渗碳工艺过程。
渗碳时炉内通入渗碳气体介质(高纯乙炔),乙炔在炉内高温低压下充分裂解后渗入工件表面;强渗结束后,通入保护性气体(高纯氮气)进行扩散,此时工件表面的碳向工件内部进行扩散。
一次完整的渗碳和扩散称之为一次脉冲,脉冲循环的次数及每次脉冲所需的气体流量根据工件材料的原始含碳量、装炉数量及渗层要求通过计算机模拟生成。
对于低压真空渗碳过程,最主要的工艺参数是渗碳温度、真空度和脉冲渗碳循环的时间节拍及气体流量。
渗碳工艺的中国专利分析
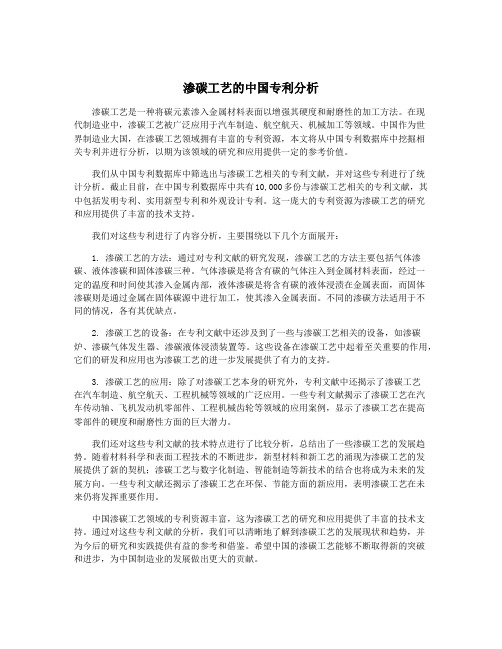
渗碳工艺的中国专利分析渗碳工艺是一种将碳元素渗入金属材料表面以增强其硬度和耐磨性的加工方法。
在现代制造业中,渗碳工艺被广泛应用于汽车制造、航空航天、机械加工等领域。
中国作为世界制造业大国,在渗碳工艺领域拥有丰富的专利资源,本文将从中国专利数据库中挖掘相关专利并进行分析,以期为该领域的研究和应用提供一定的参考价值。
我们从中国专利数据库中筛选出与渗碳工艺相关的专利文献,并对这些专利进行了统计分析。
截止目前,在中国专利数据库中共有10,000多份与渗碳工艺相关的专利文献,其中包括发明专利、实用新型专利和外观设计专利。
这一庞大的专利资源为渗碳工艺的研究和应用提供了丰富的技术支持。
我们对这些专利进行了内容分析,主要围绕以下几个方面展开:1. 渗碳工艺的方法:通过对专利文献的研究发现,渗碳工艺的方法主要包括气体渗碳、液体渗碳和固体渗碳三种。
气体渗碳是将含有碳的气体注入到金属材料表面,经过一定的温度和时间使其渗入金属内部,液体渗碳是将含有碳的液体浸渍在金属表面,而固体渗碳则是通过金属在固体碳源中进行加工,使其渗入金属表面。
不同的渗碳方法适用于不同的情况,各有其优缺点。
2. 渗碳工艺的设备:在专利文献中还涉及到了一些与渗碳工艺相关的设备,如渗碳炉、渗碳气体发生器、渗碳液体浸渍装置等。
这些设备在渗碳工艺中起着至关重要的作用,它们的研发和应用也为渗碳工艺的进一步发展提供了有力的支持。
3. 渗碳工艺的应用:除了对渗碳工艺本身的研究外,专利文献中还揭示了渗碳工艺在汽车制造、航空航天、工程机械等领域的广泛应用。
一些专利文献揭示了渗碳工艺在汽车传动轴、飞机发动机零部件、工程机械齿轮等领域的应用案例,显示了渗碳工艺在提高零部件的硬度和耐磨性方面的巨大潜力。
我们还对这些专利文献的技术特点进行了比较分析,总结出了一些渗碳工艺的发展趋势。
随着材料科学和表面工程技术的不断进步,新型材料和新工艺的涌现为渗碳工艺的发展提供了新的契机;渗碳工艺与数字化制造、智能制造等新技术的结合也将成为未来的发展方向。
渗碳工艺的中国专利分析

渗碳工艺的中国专利分析渗碳工艺是一种通过在金属表面加工装饰膜或改变金属表面化学成分的方法,从而提高金属表面的硬度和耐磨性。
渗碳工艺在金属制造行业中具有广泛的应用,能够提高金属制品的性能和使用寿命。
在中国,渗碳工艺已经发展多年,许多企业和研究机构在这一领域进行了大量的研究和开发工作。
对于渗碳工艺的中国专利分析具有重要的意义,可以帮助我们了解该领域的技术发展情况,为进一步的研究和开发工作提供参考。
一、渗碳工艺的中国专利概况截至目前,关于渗碳工艺的中国专利数量已经相当可观,涵盖了多个方面的技术内容。
这些专利涉及了渗碳工艺的方法、设备、材料、应用等多个方面,为该领域的技术进步提供了重要的支持。
这些专利还反映了渗碳工艺在中国的研究与应用状况,展现了中国在该领域的技术实力和创新能力。
1. 渗碳工艺的方法专利在渗碳工艺的专利中,方法专利占据了相当大的比重。
这些方法专利涉及了渗碳工艺的各个环节,包括工艺流程、工艺参数、渗碳介质、渗碳设备等,涵盖了从表面处理到金属内部渗碳的各个方面。
在这些专利中,有些是对传统渗碳工艺的改进和优化,有些则是针对特定材料和工件的定制化渗碳工艺,这些专利为渗碳工艺的技术提升和应用拓展提供了重要的技术支持。
渗碳工艺的材料专利也是该领域专利中的一个重要内容。
这些材料专利涉及了渗碳介质、渗碳掺杂剂、渗碳保护层等多个方面,这些材料的研发和应用对于渗碳工艺的工艺性能和成本控制具有重要的作用。
这些材料专利为渗碳工艺的材料创新和工业化应用提供了重要的技术支持。
除了上述的基础技术专利外,渗碳工艺在实际应用中还涌现出了一些应用专利。
这些应用专利涉及了渗碳工艺在汽车、航空航天、机械制造等多个行业的具体应用方案,这些专利反映了渗碳工艺在不同行业中的应用需求和技术挑战,为渗碳工艺的工程应用提供了重要的技术支持。
从目前的专利情况来看,渗碳工艺在中国的专利申请数量呈现逐年增长的趋势,显示出渗碳工艺在中国的研究与应用热度不断上升。
渗碳工艺的中国专利分析

渗碳工艺的中国专利分析渗碳工艺是一种常用的表面处理方法,目的是提高钢铁的硬度和耐磨性。
随着工业化的不断发展,渗碳工艺在各个行业中得到了广泛应用。
在中国,相关的渗碳技术也得到了长期的研究和实践。
本文将对中国专利中的渗碳相关技术进行简要分析。
一、渗碳原理渗碳又称渗碳硬化,是一种将碳源掺入合金材料表面,以提高其硬度、磨损和耐腐蚀性的加工工艺。
渗碳工艺主要是利用钢铁在高温条件下吸附碳的特性,通过控制温度、时间和碳源,使钢铁材料表面的碳含量得到相应的提高。
常见的渗碳方式有气体渗碳和固体渗碳两种。
气体渗碳主要是将加热的钢料放在含有高浓度碳的气体中,使其表面吸收碳元素。
固体渗碳则是将钢材浸泡在含有碳化物的固体混合物中,使碳元素向钢铁表面扩散。
1、CN107739084A 渗碳液凝胶及其制备方法及应用该专利涉及一种渗碳液凝胶及其制备方法及应用。
所述液凝胶包括醋酸纤维素、黏土、甲基纤维素、蔗糖乙酸酯、甘油、聚乙二醇等组分。
该渗碳液凝胶在制备时不仅能够保证渗碳效果的同时,还具有降低渗碳过程中残碳率和表面轻微氧化的优点。
该专利适用于钢铁、金属、非金属等材料中的渗碳处理,对于提高被渗碳材料的硬度和耐磨性等性能有显著效果。
该专利公开了一种新型环氧氨基树脂渗碳液及其制备方法。
该液体由烷基酰胺、环氧氨基树脂、淀粉、异氰酸酯、固化剂等组分组成。
所述渗碳液在渗碳过程中可以缩短渗碳时间和温度,同时也能提高被渗碳材料的硬度和耐磨性。
该专利涉及一种渗碳涂层材料及其制备方法,所述涂层材料由钨酸酐、粉末钢、氧化物、微量元素等组分组成。
所述渗碳涂层材料具有渗碳效果显著、渗碳层与底材结合紧密、硬度高等优点,适用于在各种材料表面制备高级别渗碳层的操作。
三、结论通过对中国专利中的渗碳相关技术进行分析,可以看出,中国在渗碳技术领域的研究和发展取得了不俗的成绩。
不仅涉及到渗碳材料的组分和性质的研究,还涵盖了渗碳方法和渗碳涂层等领域的创新和优化。
这些技术的出现和应用不仅为渗碳行业的发展提供了新的思路和途径,而且也对其他相关行业的应用产生了较大的推动作用。
低压真空渗碳工艺的探讨
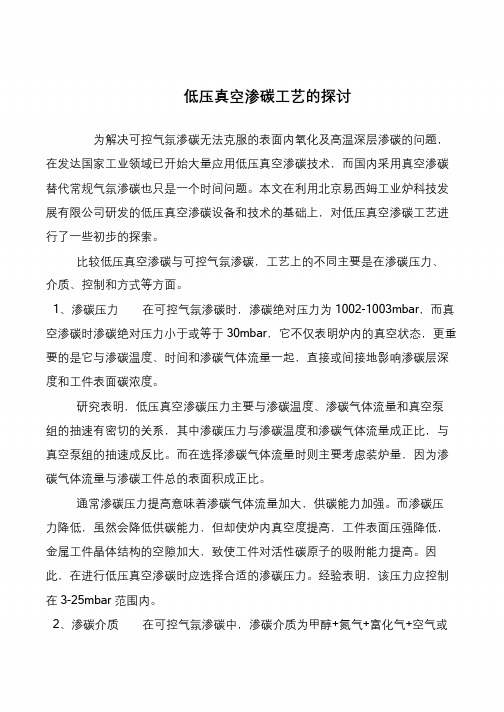
书山有路勤为径,学海无涯苦作舟
低压真空渗碳工艺的探讨
为解决可控气氛渗碳无法克服的表面内氧化及高温深层渗碳的问题,在发达国家工业领域已开始大量应用低压真空渗碳技术,而国内采用真空渗碳替代常规气氛渗碳也只是一个时间问题。
本文在利用北京易西姆工业炉科技发展有限公司研发的低压真空渗碳设备和技术的基础上,对低压真空渗碳工艺进行了一些初步的探索。
比较低压真空渗碳与可控气氛渗碳,工艺上的不同主要是在渗碳压力、介质、控制和方式等方面。
1、渗碳压力在可控气氛渗碳时,渗碳绝对压力为1002-1003mbar,而真空渗碳时渗碳绝对压力小于或等于30mbar,它不仅表明炉内的真空状态,更重要的是它与渗碳温度、时间和渗碳气体流量一起,直接或间接地影响渗碳层深度和工件表面碳浓度。
研究表明,低压真空渗碳压力主要与渗碳温度、渗碳气体流量和真空泵组的抽速有密切的关系,其中渗碳压力与渗碳温度和渗碳气体流量成正比,与真空泵组的抽速成反比。
而在选择渗碳气体流量时则主要考虑装炉量,因为渗碳气体流量与渗碳工件总的表面积成正比。
通常渗碳压力提高意味着渗碳气体流量加大,供碳能力加强。
而渗碳压力降低,虽然会降低供碳能力,但却使炉内真空度提高,工件表面压强降低,金属工件晶体结构的空隙加大,致使工件对活性碳原子的吸附能力提高。
因此,在进行低压真空渗碳时应选择合适的渗碳压力。
经验表明,该压力应控制在3-25mbar 范围内。
2、渗碳介质在可控气氛渗碳中,渗碳介质为甲醇+氮气+富化气+空气或。
低碳低合金渗碳钢的组织、性能与晶体学特征的研究的开题报告

低碳低合金渗碳钢的组织、性能与晶体学特征的研究的开题报告一、研究背景低碳低合金渗碳钢是一种常用的结构钢材料,广泛应用于船舶、机械制造、汽车、航空航天等行业。
其具有优异的强度、韧性和耐磨性等性能,是一种重要的机械零部件材料。
为了进一步提高低碳低合金渗碳钢的性能,必须对其组织、性能和晶体学特征等进行深入研究。
目前,虽然已有许多关于渗碳钢的研究,但仍有许多问题有待解决,如渗碳钢的相变规律、晶体缺陷形成与演变机制等。
二、研究目的和意义本文旨在深入研究低碳低合金渗碳钢的组织、性能和晶体学特征,并探究其优化途径,以提高其性能指标。
具体目的如下:1. 研究低碳低合金渗碳钢的相变规律,探究渗钢中各组织相之间的转变关系和影响因素。
2. 分析低碳低合金渗碳钢的性能特点,包括强度、韧性、抗磨性等,探究其与组织结构之间的关系。
3. 探究低碳低合金渗碳钢的晶体学特征,分析晶体缺陷形成与演变机制,为改善渗钢的性能提供理论基础。
4. 优化低碳低合金渗碳钢的制造工艺和生产工艺,提高其性能指标,为制造高性能机械零部件提供技术支持。
三、研究内容和方法1. 研究低碳低合金渗碳钢的相变规律,采用热处理实验和金相显微镜观察技术。
2. 分析低碳低合金渗碳钢的性能特点,包括强度、韧性、抗磨性等,采用机械性能测试和材料显微分析方法。
3. 探究低碳低合金渗碳钢的晶体学特征,采用X射线衍射、透射电镜和扫描电镜等先进的材料分析仪器。
4. 优化低碳低合金渗碳钢的制造工艺和生产工艺,设计优化的渗碳工艺流程,探究工艺参数的影响。
四、研究进度安排第一年:采集低碳低合金渗碳钢试样,进行热处理实验和金相显微镜观察,分析渗钢组织结构的变化规律。
第二年:进行机械性能测试和材料显微分析,分析低碳低合金渗碳钢的性能特点,包括强度、韧性、抗磨性等。
第三年:采用X射线衍射、透射电镜和扫描电镜等先进的材料分析仪器,探究低碳低合金渗碳钢的晶体学特征,分析晶体缺陷形成与演变机制。
低压真空渗碳—一种新的化学热处理技术
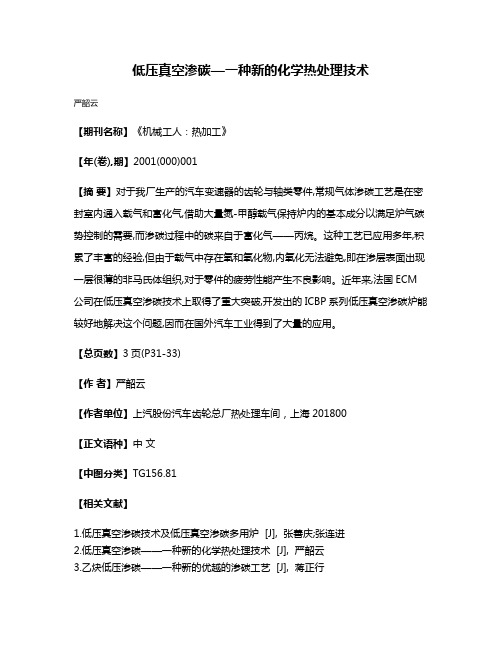
低压真空渗碳—一种新的化学热处理技术
严韶云
【期刊名称】《机械工人:热加工》
【年(卷),期】2001(000)001
【摘要】对于我厂生产的汽车变速器的齿轮与轴类零件,常规气体渗碳工艺是在密封室内通入载气和富化气,借助大量氮-甲醇载气保持炉内的基本成分以满足炉气碳势控制的需要,而渗碳过程中的碳来自于富化气——丙烷。
这种工艺已应用多年,积累了丰富的经验,但由于载气中存在氧和氧化物,内氧化无法避免,即在渗层表面出现一层很薄的非马氏体组织,对于零件的疲劳性能产生不良影响。
近年来,法国ECM 公司在低压真空渗碳技术上取得了重大突破,开发出的ICBP系列低压真空渗碳炉能较好地解决这个问题,因而在国外汽车工业得到了大量的应用。
【总页数】3页(P31-33)
【作者】严韶云
【作者单位】上汽股份汽车齿轮总厂热处理车间,上海201800
【正文语种】中文
【中图分类】TG156.81
【相关文献】
1.低压真空渗碳技术及低压真空渗碳多用炉 [J], 张善庆;张连进
2.低压真空渗碳——一种新的化学热处理技术 [J], 严韶云
3.乙炔低压渗碳——一种新的优越的渗碳工艺 [J], 蒋正行
4.浅谈低压真空渗碳热处理技术 [J], 吴平
5.真空低压渗碳和预氮化技术的应用——西科沃克欧洲公司一种节能减排的渗碳技术 [J], 雍丽;刘香国
因版权原因,仅展示原文概要,查看原文内容请购买。
低温渗碳技术
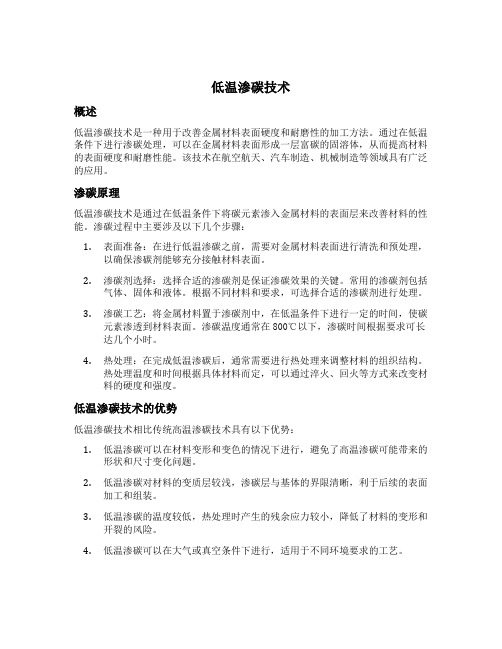
低温渗碳技术概述低温渗碳技术是一种用于改善金属材料表面硬度和耐磨性的加工方法。
通过在低温条件下进行渗碳处理,可以在金属材料表面形成一层富碳的固溶体,从而提高材料的表面硬度和耐磨性能。
该技术在航空航天、汽车制造、机械制造等领域具有广泛的应用。
渗碳原理低温渗碳技术是通过在低温条件下将碳元素渗入金属材料的表面层来改善材料的性能。
渗碳过程中主要涉及以下几个步骤:1.表面准备:在进行低温渗碳之前,需要对金属材料表面进行清洗和预处理,以确保渗碳剂能够充分接触材料表面。
2.渗碳剂选择:选择合适的渗碳剂是保证渗碳效果的关键。
常用的渗碳剂包括气体、固体和液体。
根据不同材料和要求,可选择合适的渗碳剂进行处理。
3.渗碳工艺:将金属材料置于渗碳剂中,在低温条件下进行一定的时间,使碳元素渗透到材料表面。
渗碳温度通常在800℃以下,渗碳时间根据要求可长达几个小时。
4.热处理:在完成低温渗碳后,通常需要进行热处理来调整材料的组织结构。
热处理温度和时间根据具体材料而定,可以通过淬火、回火等方式来改变材料的硬度和强度。
低温渗碳技术的优势低温渗碳技术相比传统高温渗碳技术具有以下优势:1.低温渗碳可以在材料变形和变色的情况下进行,避免了高温渗碳可能带来的形状和尺寸变化问题。
2.低温渗碳对材料的变质层较浅,渗碳层与基体的界限清晰,利于后续的表面加工和组装。
3.低温渗碳的温度较低,热处理时产生的残余应力较小,降低了材料的变形和开裂的风险。
4.低温渗碳可以在大气或真空条件下进行,适用于不同环境要求的工艺。
5.低温渗碳可以在良好的渗碳速率下实现较高的渗层硬度和耐磨性能,改善材料的使用寿命。
应用领域低温渗碳技术在以下领域有广泛的应用:航空航天在航空航天领域,材料的硬度和耐磨性对飞机、卫星等设备的安全和可靠性至关重要。
低温渗碳技术可以提高航空航天材料的表面硬度,增强抗磨损能力,延长零部件的使用寿命。
汽车制造在汽车制造领域,引擎、传动系统和零部件的耐磨性和耐久性是关键的性能指标。
产品渗碳处理方案
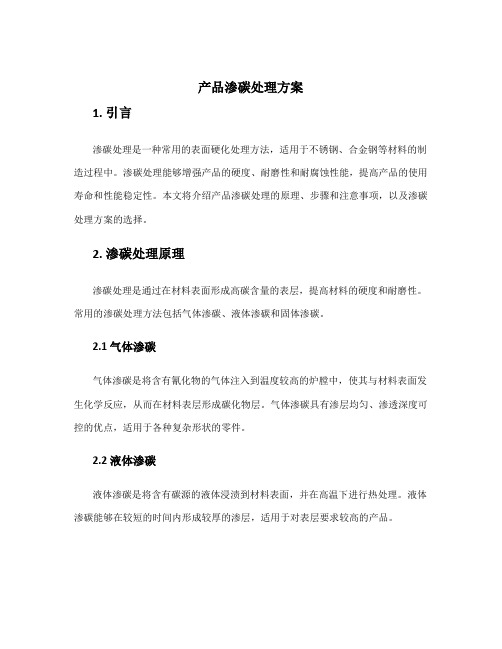
产品渗碳处理方案1. 引言渗碳处理是一种常用的表面硬化处理方法,适用于不锈钢、合金钢等材料的制造过程中。
渗碳处理能够增强产品的硬度、耐磨性和耐腐蚀性能,提高产品的使用寿命和性能稳定性。
本文将介绍产品渗碳处理的原理、步骤和注意事项,以及渗碳处理方案的选择。
2. 渗碳处理原理渗碳处理是通过在材料表面形成高碳含量的表层,提高材料的硬度和耐磨性。
常用的渗碳处理方法包括气体渗碳、液体渗碳和固体渗碳。
2.1 气体渗碳气体渗碳是将含有氰化物的气体注入到温度较高的炉膛中,使其与材料表面发生化学反应,从而在材料表层形成碳化物层。
气体渗碳具有渗层均匀、渗透深度可控的优点,适用于各种复杂形状的零件。
2.2 液体渗碳液体渗碳是将含有碳源的液体浸渍到材料表面,并在高温下进行热处理。
液体渗碳能够在较短的时间内形成较厚的渗层,适用于对表层要求较高的产品。
2.3 固体渗碳固体渗碳是将含有碳源的固体材料与待处理材料一起放入炉膛中进行热处理。
固体渗碳通常需要更长的处理时间,但能够形成均匀的渗层。
它是一种经济且适用于批量处理的方法。
3. 渗碳处理步骤3.1 表面准备在进行渗碳处理之前,需要对待处理的产品进行表面准备。
这包括去除表面油污、氧化皮和锈蚀物,并进行光洁度处理,以提高渗碳效果。
3.2 渗碳介质选择根据产品的要求和具体情况,选择合适的渗碳介质,包括气体、液体或固体介质。
同时需要根据产品的材料和结构特点,确定渗碳的温度和时间。
3.3 渗碳处理将待处理的产品放入渗碳炉中,根据预定的温度和时间进行渗碳处理。
在渗碳过程中,要保持渗碳介质的稳定性,并严格控制温度和时间,以确保渗碳层的均匀和质量。
3.4 冷却处理渗碳处理完成后,将产品从渗碳炉中取出,并进行冷却处理。
冷却处理可以采用自然冷却或快速冷却的方法,以控制渗碳层的组织结构和性能。
4. 渗碳处理注意事项4.1 温度控制温度是影响渗碳效果和渗层质量的重要因素。
要准确控制温度,避免温度过高或过低造成渗碳层的不均匀或质量问题。
液体渗碳技术

液体渗碳技术液体渗碳技术是一种常用的表面强化方法,它通过在金属材料表面形成一层高碳含量的硬化层,从而提高材料的硬度、耐磨性和抗腐蚀性能。
本文将从渗碳原理、工艺流程、设备及应用等方面进行详细介绍。
一、渗碳原理液体渗碳技术主要是利用液态金属中的高浓度活性元素,如碳、氮等,在高温下向金属表面扩散,形成一定厚度的强化层。
其中,液体中的活性元素主要通过化学反应和扩散作用来实现。
在液体渗碳过程中,首先需要将金属件放入预热炉中进行加热处理,使其达到适宜的温度范围。
然后将含有活性元素的溶液(如盐酸、氰酸等)浸泡在金属件周围,并保持一定时间。
在此过程中,活性元素会逐渐扩散到金属表面,并与其发生反应,在表面形成一定厚度的硬化层。
最后将金属件取出冷却,即可完成渗碳处理。
二、工艺流程液体渗碳技术的工艺流程主要包括预处理、渗碳处理和后处理三个环节。
1. 预处理预处理是指在进行液体渗碳前对金属件进行必要的准备工作。
首先需要对金属件进行清洗,去除表面的油污、锈蚀等杂质。
然后将其放入预热炉中进行加热处理,使其达到适宜的温度范围。
2. 渗碳处理渗碳处理是指将含有活性元素的溶液浸泡在金属件周围,并保持一定时间,使活性元素逐渐扩散到金属表面形成硬化层的过程。
具体操作步骤如下:(1)将含有活性元素的溶液倒入渗碳炉中;(2)将预热好的金属件放入渗碳炉中,并确保其表面与溶液充分接触;(3)启动加热系统,使温度逐步升高到设定值,并保持一定时间;(4)关闭加热系统,等待金属件自然冷却至室温。
3. 后处理后处理是指将渗碳处理后的金属件进行必要的加工和表面处理。
主要包括退火、研磨、抛光等环节,以保证其表面质量和性能。
三、设备液体渗碳技术的设备主要包括预热炉、渗碳炉和冷却设备等。
其中,预热炉用于对金属件进行加热处理,使其达到适宜的温度范围;渗碳炉用于浸泡含有活性元素的溶液,并将其扩散到金属表面形成硬化层;冷却设备则用于将金属件冷却至室温。
四、应用液体渗碳技术广泛应用于机械制造、航空航天、汽车制造等领域。
- 1、下载文档前请自行甄别文档内容的完整性,平台不提供额外的编辑、内容补充、找答案等附加服务。
- 2、"仅部分预览"的文档,不可在线预览部分如存在完整性等问题,可反馈申请退款(可完整预览的文档不适用该条件!)。
- 3、如文档侵犯您的权益,请联系客服反馈,我们会尽快为您处理(人工客服工作时间:9:00-18:30)。
在进 行工 艺试 制 时首先 需要 对 9 4 0  ̄ C 渗 碳温 度 下 的富化 率值进 行验 证及 修正 。由于不 同设 备 的真 空度 、 排气 方式 存在 差 异 ,通 过 富化 率 的验 证及 修 正 可使得 工 艺软 件 的模 拟结 果与 实
・ 1 0・
汽齿科技 Nhomakorabea2 0 1 4钜
在 E C M I C B P渗碳 工 艺 中,富 化率 是一 个重 要参 数 ,它 的正确 与否直 接影 响到 工艺模 拟
所 给 出的渗 碳节 拍 。它是 指工 件 在单 位 时 间 、单位 面积 上 吸 附碳 原子 的程 度 ,与 渗碳 气体 和
温 度 有关 。 图 1 为E C M 公 司给 出 的乙炔和 丙烷 的富化率 参考 曲线 。
际加工 的 冶金 结果 更 为一 致 ,并 且 ,炉膛 内不 同位 置 的富化 率值 差 异 能反 映 出炉膛 内的气氛 均 匀性 。
F l u x& C a r b o n S a t u r a t i o n wi t l l Ac e t y l e n e
F i e r : C m e d 鲫 嘲 d i ]
工 艺 ;④低 压 乙炔 渗碳 工艺 的防渗技 术 。
2 深 渗层零件 9 4 0 ℃渗 碳 工 艺 的开 发 应 用
2 . 1 富化率 值 的验证 及修 正 2 . 1 . 1 富 化率值 的定义 及其 重要 性
低 压 渗碳 采 用 的是 碳浓 度 饱 和渗 碳 法 ,通过 在 高温 低压 条件 下脉 冲式 通入 的渗碳 气 体 , 所 裂解 出的活 性碳 原子 被工 件表 面吸 附,并 不 断 向内扩 散来 完成 渗碳 过程 。
I ——F l u x C 3 H 8 F
I I
9 0 0 91 0 92 0 9 30 9 4 0 9 5 0 9 6 0 97 0 9 8 0
Te mpe r a t u r e℃
图1 乙 炔和 丙 烷 的 富 化率 参 考 曲线
2 . 1 . 2 方 法简介
1 引 言
低 压渗 碳( L P C ) 热处 理技 术在 欧 美等 发达 国家 已经 在汽 车 、机械 、航 空航天 等领 域获得 了 广 泛 应用 。它 的技 术特 点是 能解 决可 控 气氛 渗 碳无 法解 决 表面 内氧 化 、深 层渗 碳 及异 形件 盲
孔 渗碳 的 问题 ,并 配 以高 压气 淬 技术 ,能较 好地 控 制热 处 理淬 火 畸变 ,在 齿轮 制 造 中减少 热 后 精加 工 工序 。此 外 ,低压 渗碳 设备 一般 都 是采用 由多个渗 碳加 热室 、l ~ 2个气 体 淬火室 以及
图 2 试 样 分 布位 置 示 意 图
2 . 1 - 3 试 样要 求 富化 率 验证 试 样材 料要 与 模拟 软件 中输入 的 材料 牌 号一 致 ,且表 面 光滑 ,无氧 化 。试样
可 用铅 丝掉 挂 在料 架 上 ,表 面 不 能与 料架 接触 , 以免 影 响渗 碳效 果 ,导 致富 化 率计 算值 的偏 差 。 图 3为我 公 司使用 的试 样尺 寸 。
其 他辅 助 设备( 如清 洗机 、预 热炉 、回火 炉等) 连 接成 自动 生产 线 ,配 以运行 快速 和平 稳 的物 料
自动传 送 系统 ,具 有生 产率 高 、柔性 和 自动化 程 度高等 优 点 。
低 压渗 碳 目前 在行 星传 动式 的 自动变 速箱 零件 ( GF 6产 品) 热 处理 上有较 为 成熟 的应用 。 但 随着产 品 的升 级换 代 ,DC T 等 档位 式传 动 的零件 也开 始 需要进 行低压 渗 碳热处 理 。在这 些档 位 齿 、输 入输 出轴 以及 主减 速齿 低压 热 处理工 艺 的开发 及应 用上 还存 在一 些 函待解 决 的问题 。 诸 如 :① 深 渗层 零 件 高温 渗碳 工 艺 ;② 齿轮 尖 角处 残奥 级 别控 制 ;③ 主减 速 齿高 压气 体直 淬
第 1 期
汽
齿
科
技
论低压渗碳技 术在 D C T项 目中的 开 发 及 应 用
刘 尚 杰
摘要 :本文简要介绍 了 E C M I C B P低压 渗碳 工艺的特性,并通 过在 DC T项 目热处理低压渗碳 工艺 开发 中遇到 的各类 问题 ,提出 了在富化率调整、渗碳节拍手工修正 、气淬参数调整 、工装设计 、防 渗夹具 设计 等方 面的改进 措施 ,并对实际应用结果进行 了简要阐述和分析 。 关键词 :低压渗碳 ;富化 率;工艺模拟;防渗
2 . 1 . 4 工艺参 数设 置
在进 行试 验前 ,需设 定一个 初 始富化 率值 ,可从 图 1 上 获得 ,在 9 4 0  ̄ C、乙炔 渗碳 的条件 下进 行验 证 ,设定 初始 值为 1 2 。需要 注意 的是 ,工 艺模 拟 时强渗后 的最 高含 碳量 值必 须低 于 铁碳 相 图 中奥 氏体 在 9 4 0 ℃ 的饱 和 含碳 量 。因为高 于饱和 值会 导致 试样 吸 附碳 的能力 下 降,甚
嘲 嗽 r a t u
.
/ — ,
一 r
/
J / / / / /
厂
/ 。
/
^ t I 8 霉 筹_ 【
.
m 8 6 4
/
/ / / 。 /
.
/
/
/
/ /
/
l — - — . F l u x c 2 H 2 l
富化 率 的验证 使 用重 量 对 比法 ,先 在工 艺模 拟 软件 上 设定 一个 富 化率 值 ,并得 到 模拟 节 拍。 然后 将预 先称 量好 的试样 按 九点要 求 分布在 料架 各位 置 , 见图 2 , 使用模 拟工 艺进 行渗 碳 , 完成后 再进 行称 量 ,通过 渗碳 前后 称重 的差 值换 算得 到在 该渗碳 温度 下 的实际 富化 率值 。