压力管道环向对接接头相控阵超声检测规范
管道对接焊缝相控阵超声检测
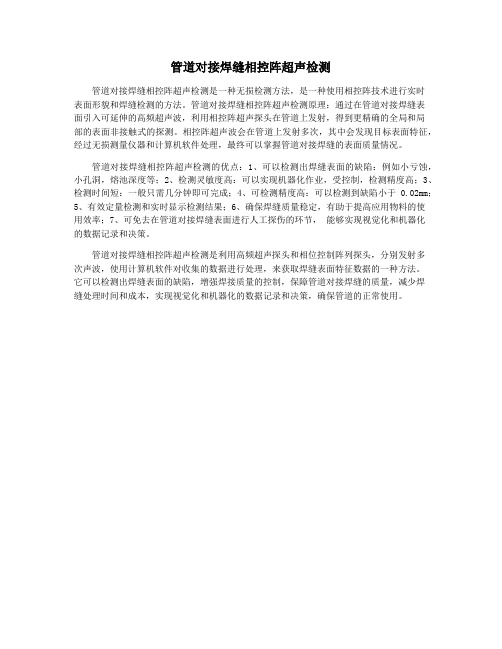
管道对接焊缝相控阵超声检测
管道对接焊缝相控阵超声检测是一种无损检测方法,是一种使用相控阵技术进行实时
表面形貌和焊缝检测的方法。
管道对接焊缝相控阵超声检测原理:通过在管道对接焊缝表
面引入可延伸的高频超声波,利用相控阵超声探头在管道上发射,得到更精确的全局和局
部的表面非接触式的探测。
相控阵超声波会在管道上发射多次,其中会发现目标表面特征,经过无损测量仪器和计算机软件处理,最终可以掌握管道对接焊缝的表面质量情况。
管道对接焊缝相控阵超声检测的优点:1、可以检测出焊缝表面的缺陷:例如小亏蚀,小孔洞,熔池深度等;2、检测灵敏度高:可以实现机器化作业,受控制,检测精度高;3、检测时间短:一般只需几分钟即可完成;4、可检测精度高:可以检测到缺陷小于0.02mm;
5、有效定量检测和实时显示检测结果;
6、确保焊缝质量稳定,有助于提高应用物料的使
用效率;7、可免去在管道对接焊缝表面进行人工探伤的环节,能够实现视觉化和机器化
的数据记录和决策。
管道对接焊缝相控阵超声检测是利用高频超声探头和相位控制阵列探头,分别发射多
次声波,使用计算机软件对收集的数据进行处理,来获取焊缝表面特征数据的一种方法。
它可以检测出焊缝表面的缺陷,增强焊接质量的控制,保障管道对接焊缝的质量,减少焊
缝处理时间和成本,实现视觉化和机器化的数据记录和决策,确保管道的正常使用。
双相不锈钢钢管对接环焊缝的相控阵超声检测
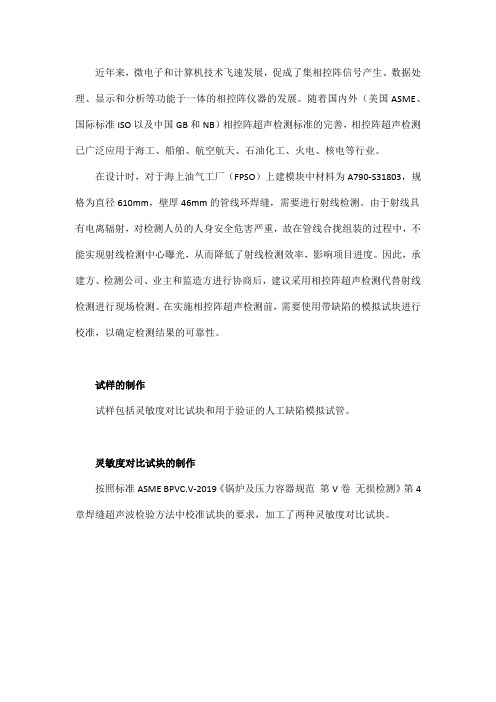
近年来,微电子和计算机技术飞速发展,促成了集相控阵信号产生、数据处理、显示和分析等功能于一体的相控阵仪器的发展。
随着国内外(美国ASME、国际标准ISO以及中国GB和NB)相控阵超声检测标准的完善,相控阵超声检测已广泛应用于海工、船舶、航空航天、石油化工、火电、核电等行业。
在设计时,对于海上油气工厂(FPSO)上建模块中材料为A790-S31803,规格为直径610mm,壁厚46mm的管线环焊缝,需要进行射线检测。
由于射线具有电离辐射,对检测人员的人身安全危害严重,故在管线合拢组装的过程中,不能实现射线检测中心曝光,从而降低了射线检测效率,影响项目进度。
因此,承建方、检测公司、业主和监造方进行协商后,建议采用相控阵超声检测代替射线检测进行现场检测。
在实施相控阵超声检测前,需要使用带缺陷的模拟试块进行校准,以确定检测结果的可靠性。
试样的制作试样包括灵敏度对比试块和用于验证的人工缺陷模拟试管。
灵敏度对比试块的制作按照标准ASME BPVC.V-2019《锅炉及压力容器规范第V卷无损检测》第4章焊缝超声波检验方法中校准试块的要求,加工了两种灵敏度对比试块。
图1 灵敏度对比试块实物如图1(a)所示,在原材料上加工长横孔反射体,制作原材料灵敏度对比试块,用于楔块延迟的校准。
如图1(b)所示,按照焊接工艺焊接后进行切割,制作带有焊缝的长横孔和刻槽的灵敏度对比试块,用于灵敏度校准和TCG (时间校正增益)曲线的制作等。
反射体(长横孔和刻槽)的详细参数如下: 原材料对比试块 试块编号:PAUT-SS-01 人工反射体类型:长横孔长横孔位置:T/4、T/2、3T/4(T为试件厚度)长横孔尺寸:ф3mm×80mm带焊缝对比试块试块编号:T027973人工反射体类型:长横孔长横孔位置:焊缝中心:T/4、T/2、3T/4长横孔尺寸:ф3mm×70mm试块编号:T027972人工反射体类型:长横孔长横孔位置:坡口熔合线:T/4、T/2、3T/4长横孔尺寸:ф3mm×70mm人工反射体类型:刻槽刻槽位置:焊缝上表面刻槽尺寸:70mm×1mm×2mm试块编号:T027974人工反射体类型:刻槽刻槽位置:焊缝下表面刻槽尺寸:70mm×1mm×2mm模拟试管的制作人工缺陷模拟试管采用切除对比试块后的余料制作,依据ASME BPVC.V-2019第4章强制性附录IX中对于缺陷定量和分类的规程评定要求,确定缺陷的数量和位置。
管道焊接接头超声波检验技术规程
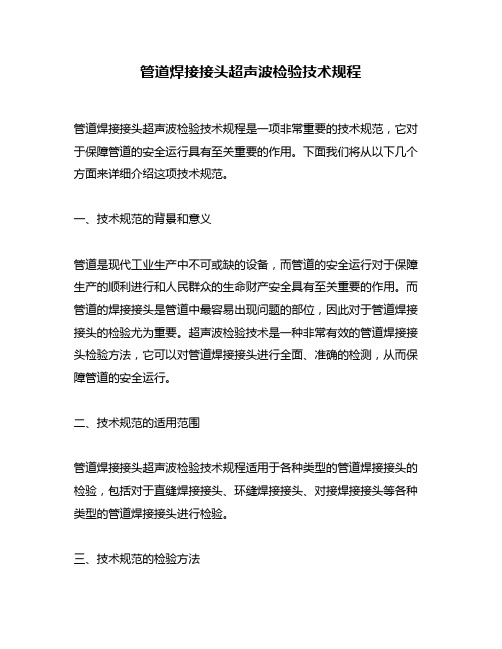
管道焊接接头超声波检验技术规程管道焊接接头超声波检验技术规程是一项非常重要的技术规范,它对于保障管道的安全运行具有至关重要的作用。
下面我们将从以下几个方面来详细介绍这项技术规范。
一、技术规范的背景和意义管道是现代工业生产中不可或缺的设备,而管道的安全运行对于保障生产的顺利进行和人民群众的生命财产安全具有至关重要的作用。
而管道的焊接接头是管道中最容易出现问题的部位,因此对于管道焊接接头的检验尤为重要。
超声波检验技术是一种非常有效的管道焊接接头检验方法,它可以对管道焊接接头进行全面、准确的检测,从而保障管道的安全运行。
二、技术规范的适用范围管道焊接接头超声波检验技术规程适用于各种类型的管道焊接接头的检验,包括对于直缝焊接接头、环缝焊接接头、对接焊接接头等各种类型的管道焊接接头进行检验。
三、技术规范的检验方法管道焊接接头超声波检验技术规程采用超声波检验技术进行检验。
具体的检验方法包括以下几个步骤:1. 准备工作:对于待检验的管道焊接接头进行清洗和除锈,确保检验表面的干净和光滑。
2. 检验设备:使用超声波检验设备对管道焊接接头进行检验,确保设备的正常运行和准确性。
3. 检验过程:将超声波探头放置在管道焊接接头上,通过超声波的反射和传播来检测管道焊接接头的缺陷和问题。
4. 检验结果:根据检验结果来判断管道焊接接头的质量和安全性,对于存在问题的管道焊接接头进行修复或更换。
四、技术规范的注意事项在进行管道焊接接头超声波检验技术规程时,需要注意以下几个事项:1. 检验设备的选择和使用需要符合相关的标准和规范,确保设备的准确性和可靠性。
2. 检验人员需要经过专业的培训和认证,具备相关的技术和知识。
3. 检验过程中需要注意安全,确保检验人员和设备的安全。
4. 对于检验结果需要进行准确的记录和归档,以备后续的参考和使用。
五、技术规范的意义和价值管道焊接接头超声波检验技术规程的实施,可以有效地保障管道的安全运行,减少管道事故的发生,保护人民群众的生命财产安全。
管道对接焊缝相控阵超声检测

管道对接焊缝相控阵超声检测随着工业的发展和科技的进步,相控阵超声检测逐渐被广泛应用于各种金属结构的无损检测中。
相控阵超声技术是一种高精度、高效率和高可靠性的无损检测方法,能有效地检测金属结构中的缺陷和损伤。
在管道对接焊缝的检测中,相控阵超声技术具有非常重要的作用,因为该技术能够在非破坏性的情况下检测到焊缝中的各种缺陷,从而保证管道的安全和可靠性。
管道对接焊缝通常是将两根管道连接起来的重要部分,因此,其质量的好坏直接影响着整个管道系统的安全和可靠性。
然而,在管道对接过程中,焊接工艺的不稳定性和操作不当等因素常常会导致焊缝中产生各种缺陷,如气孔、夹杂、裂纹等。
这些缺陷不仅会降低管道的承压能力和耐腐蚀能力,还可能在使用中引起泄漏和爆炸等严重事故。
因此,对管道对接焊缝进行无损检测,及时发现和修复其中的缺陷,就显得非常必要。
相控阵超声技术是一种声学探伤技术,其原理是利用声波在金属材料中传播的特性来检测其中的缺陷,因此其检测精度和效率都非常高。
相比传统的超声检测技术,相控阵超声技术具有以下优点:1.检测精度高:相控阵超声技术能够实现多角度、多方向的扫描,可以获得更加准确的检测结果。
2.检测速度快:相控阵超声技术可以快速地完成对管道对接焊缝的全面检测,提高了工作效率。
3.自动化程度高:相控阵超声技术采用数字化处理和图像显示技术,可以实现自动检测和数据处理。
在管道对接焊缝的相控阵超声检测中,通常使用的探头一般具有多个发射和接收元件,能够在焊缝表面产生多个声束,以不同的方向和角度对焊缝进行全面扫描。
利用相控阵技术,可以实现对焊缝中各种缺陷的精确定位和识别,确定缺陷的大小、形状和深度等参数,并生成二维和三维图像以便进行后续的分析和处理。
管道对接焊缝相控阵超声检测

管道对接焊缝相控阵超声检测1. 引言1.1 研究背景管道对接焊缝相控阵超声检测是近年来随着工业领域的发展而逐渐兴起的一项重要技术。
管道在工业生产中起着至关重要的作用,而管道对接焊缝则是管道连接中不可或缺的部分。
传统的焊缝检测技术存在着检测精度低、效率低、对焊缝缺陷的检测能力不足等问题,因此急需一种能够高效、准确、全面检测焊缝缺陷的新技术。
目前,随着超声技术的不断发展和改进,管道对接焊缝超声检测成为一种备受瞩目的技术。
相控阵超声检测技术可通过多个超声探头同时发射和接收超声波,实现对焊缝的全面扫描和准确探测,具有高分辨率、高灵敏度、高重复性等优点。
结合管道对接焊缝特点,相控阵超声检测技术被广泛应用于管道对接焊缝的检测领域。
本研究旨在探讨管道对接焊缝相控阵超声检测技术的原理、方法、技术、设备及应用,并研究在实际应用中可能存在的问题,为今后的研究提供借鉴和参考。
通过对该技术进行深入研究和分析,可以为提高管道连接质量、降低安全风险、节约成本、提高生产效率等方面提供有力支撑,具有重要的研究意义和实际应用价值。
1.2 研究目的管道对接焊缝相控阵超声检测是一种非常重要的无损检测技术,可以有效地对管道焊缝进行检测和评估。
本文旨在探讨这一技术在管道工程中的应用和发展。
通过对管道对接焊缝相控阵超声检测的研究,可以深入了解焊缝的结构及缺陷情况,及时发现问题并加以修复,从而保障管道工程的安全运行。
对该检测技术的进一步优化和改进,可以提高检测的准确性和可靠性,为管道工程的施工和维护提供更为可靠的技术支持。
1.3 研究意义管道对接焊缝相控阵超声检测在工业领域扮演着重要的作用,其研究意义主要表现在以下几个方面:管道对接焊缝超声检测技术的发展能够提高工作效率,降低人工成本。
相比于传统的目视检测或X射线检测,超声检测可以实现自动化、高效率的检测,大大减轻了工作人员的劳动强度。
管道对接焊缝超声检测技术的研究还能促进超声检测技术的发展,推动无损检测领域的进步。
管道对接焊缝相控阵超声检测
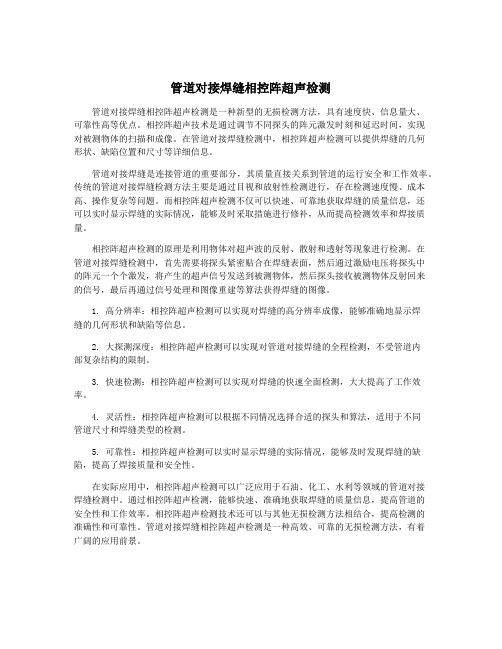
管道对接焊缝相控阵超声检测管道对接焊缝相控阵超声检测是一种新型的无损检测方法,具有速度快、信息量大、可靠性高等优点。
相控阵超声技术是通过调节不同探头的阵元激发时刻和延迟时间,实现对被测物体的扫描和成像。
在管道对接焊缝检测中,相控阵超声检测可以提供焊缝的几何形状、缺陷位置和尺寸等详细信息。
管道对接焊缝是连接管道的重要部分,其质量直接关系到管道的运行安全和工作效率。
传统的管道对接焊缝检测方法主要是通过目视和放射性检测进行,存在检测速度慢、成本高、操作复杂等问题。
而相控阵超声检测不仅可以快速、可靠地获取焊缝的质量信息,还可以实时显示焊缝的实际情况,能够及时采取措施进行修补,从而提高检测效率和焊接质量。
相控阵超声检测的原理是利用物体对超声波的反射、散射和透射等现象进行检测。
在管道对接焊缝检测中,首先需要将探头紧密贴合在焊缝表面,然后通过激励电压将探头中的阵元一个个激发,将产生的超声信号发送到被测物体,然后探头接收被测物体反射回来的信号,最后再通过信号处理和图像重建等算法获得焊缝的图像。
1. 高分辨率:相控阵超声检测可以实现对焊缝的高分辨率成像,能够准确地显示焊缝的几何形状和缺陷等信息。
2. 大探测深度:相控阵超声检测可以实现对管道对接焊缝的全程检测,不受管道内部复杂结构的限制。
3. 快速检测:相控阵超声检测可以实现对焊缝的快速全面检测,大大提高了工作效率。
4. 灵活性:相控阵超声检测可以根据不同情况选择合适的探头和算法,适用于不同管道尺寸和焊缝类型的检测。
5. 可靠性:相控阵超声检测可以实时显示焊缝的实际情况,能够及时发现焊缝的缺陷,提高了焊接质量和安全性。
在实际应用中,相控阵超声检测可以广泛应用于石油、化工、水利等领域的管道对接焊缝检测中。
通过相控阵超声检测,能够快速、准确地获取焊缝的质量信息,提高管道的安全性和工作效率。
相控阵超声检测技术还可以与其他无损检测方法相结合,提高检测的准确性和可靠性。
管道对接焊缝相控阵超声检测是一种高效、可靠的无损检测方法,有着广阔的应用前景。
管道对接焊缝相控阵超声检测
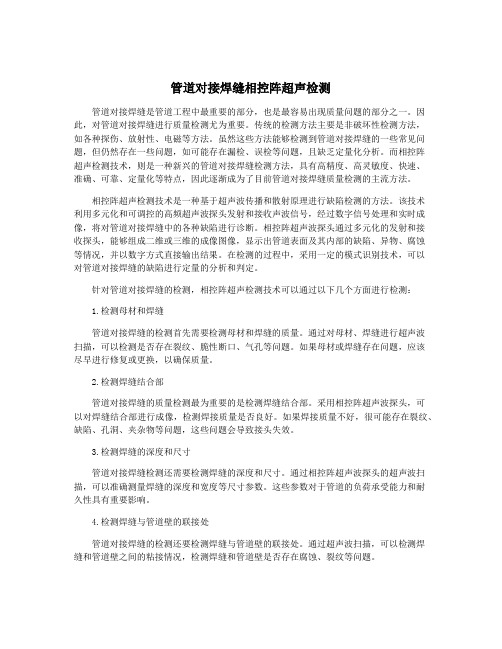
管道对接焊缝相控阵超声检测管道对接焊缝是管道工程中最重要的部分,也是最容易出现质量问题的部分之一。
因此,对管道对接焊缝进行质量检测尤为重要。
传统的检测方法主要是非破坏性检测方法,如各种探伤、放射性、电磁等方法。
虽然这些方法能够检测到管道对接焊缝的一些常见问题,但仍然存在一些问题,如可能存在漏检、误检等问题,且缺乏定量化分析。
而相控阵超声检测技术,则是一种新兴的管道对接焊缝检测方法,具有高精度、高灵敏度、快速、准确、可靠、定量化等特点,因此逐渐成为了目前管道对接焊缝质量检测的主流方法。
相控阵超声检测技术是一种基于超声波传播和散射原理进行缺陷检测的方法。
该技术利用多元化和可调控的高频超声波探头发射和接收声波信号,经过数字信号处理和实时成像,将对管道对接焊缝中的各种缺陷进行诊断。
相控阵超声波探头通过多元化的发射和接收探头,能够组成二维或三维的成像图像,显示出管道表面及其内部的缺陷、异物、腐蚀等情况,并以数字方式直接输出结果。
在检测的过程中,采用一定的模式识别技术,可以对管道对接焊缝的缺陷进行定量的分析和判定。
针对管道对接焊缝的检测,相控阵超声检测技术可以通过以下几个方面进行检测:1.检测母材和焊缝管道对接焊缝的检测首先需要检测母材和焊缝的质量。
通过对母材、焊缝进行超声波扫描,可以检测是否存在裂纹、脆性断口、气孔等问题。
如果母材或焊缝存在问题,应该尽早进行修复或更换,以确保质量。
2.检测焊缝结合部管道对接焊缝的质量检测最为重要的是检测焊缝结合部。
采用相控阵超声波探头,可以对焊缝结合部进行成像,检测焊接质量是否良好。
如果焊接质量不好,很可能存在裂纹、缺陷、孔洞、夹杂物等问题,这些问题会导致接头失效。
3.检测焊缝的深度和尺寸管道对接焊缝检测还需要检测焊缝的深度和尺寸。
通过相控阵超声波探头的超声波扫描,可以准确测量焊缝的深度和宽度等尺寸参数。
这些参数对于管道的负荷承受能力和耐久性具有重要影响。
4.检测焊缝与管道壁的联接处管道对接焊缝的检测还要检测焊缝与管道壁的联接处。
管道对接焊缝相控阵超声检测
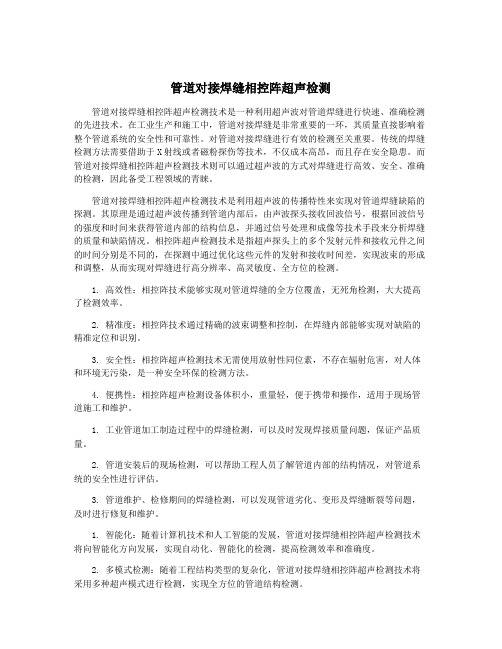
管道对接焊缝相控阵超声检测管道对接焊缝相控阵超声检测技术是一种利用超声波对管道焊缝进行快速、准确检测的先进技术。
在工业生产和施工中,管道对接焊缝是非常重要的一环,其质量直接影响着整个管道系统的安全性和可靠性。
对管道对接焊缝进行有效的检测至关重要。
传统的焊缝检测方法需要借助于X射线或者磁粉探伤等技术,不仅成本高昂,而且存在安全隐患。
而管道对接焊缝相控阵超声检测技术则可以通过超声波的方式对焊缝进行高效、安全、准确的检测,因此备受工程领域的青睐。
管道对接焊缝相控阵超声检测技术是利用超声波的传播特性来实现对管道焊缝缺陷的探测。
其原理是通过超声波传播到管道内部后,由声波探头接收回波信号,根据回波信号的强度和时间来获得管道内部的结构信息,并通过信号处理和成像等技术手段来分析焊缝的质量和缺陷情况。
相控阵超声检测技术是指超声探头上的多个发射元件和接收元件之间的时间分别是不同的,在探测中通过优化这些元件的发射和接收时间差,实现波束的形成和调整,从而实现对焊缝进行高分辨率、高灵敏度、全方位的检测。
1. 高效性:相控阵技术能够实现对管道焊缝的全方位覆盖,无死角检测,大大提高了检测效率。
2. 精准度:相控阵技术通过精确的波束调整和控制,在焊缝内部能够实现对缺陷的精准定位和识别。
3. 安全性:相控阵超声检测技术无需使用放射性同位素,不存在辐射危害,对人体和环境无污染,是一种安全环保的检测方法。
4. 便携性:相控阵超声检测设备体积小,重量轻,便于携带和操作,适用于现场管道施工和维护。
1. 工业管道加工制造过程中的焊缝检测,可以及时发现焊接质量问题,保证产品质量。
2. 管道安装后的现场检测,可以帮助工程人员了解管道内部的结构情况,对管道系统的安全性进行评估。
3. 管道维护、检修期间的焊缝检测,可以发现管道劣化、变形及焊缝断裂等问题,及时进行修复和维护。
1. 智能化:随着计算机技术和人工智能的发展,管道对接焊缝相控阵超声检测技术将向智能化方向发展,实现自动化、智能化的检测,提高检测效率和准确度。
管道对接焊缝相控阵超声检测
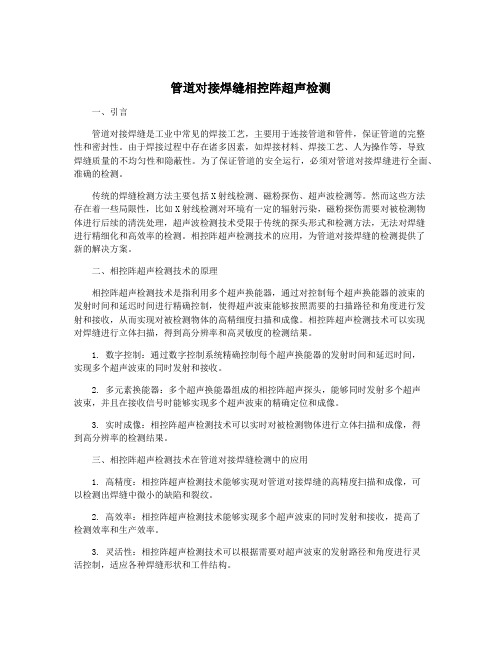
管道对接焊缝相控阵超声检测一、引言管道对接焊缝是工业中常见的焊接工艺,主要用于连接管道和管件,保证管道的完整性和密封性。
由于焊接过程中存在诸多因素,如焊接材料、焊接工艺、人为操作等,导致焊缝质量的不均匀性和隐蔽性。
为了保证管道的安全运行,必须对管道对接焊缝进行全面、准确的检测。
传统的焊缝检测方法主要包括X射线检测、磁粉探伤、超声波检测等。
然而这些方法存在着一些局限性,比如X射线检测对环境有一定的辐射污染,磁粉探伤需要对被检测物体进行后续的清洗处理,超声波检测技术受限于传统的探头形式和检测方法,无法对焊缝进行精细化和高效率的检测。
相控阵超声检测技术的应用,为管道对接焊缝的检测提供了新的解决方案。
二、相控阵超声检测技术的原理相控阵超声检测技术是指利用多个超声换能器,通过对控制每个超声换能器的波束的发射时间和延迟时间进行精确控制,使得超声波束能够按照需要的扫描路径和角度进行发射和接收,从而实现对被检测物体的高精细度扫描和成像。
相控阵超声检测技术可以实现对焊缝进行立体扫描,得到高分辨率和高灵敏度的检测结果。
1. 数字控制:通过数字控制系统精确控制每个超声换能器的发射时间和延迟时间,实现多个超声波束的同时发射和接收。
2. 多元素换能器:多个超声换能器组成的相控阵超声探头,能够同时发射多个超声波束,并且在接收信号时能够实现多个超声波束的精确定位和成像。
3. 实时成像:相控阵超声检测技术可以实时对被检测物体进行立体扫描和成像,得到高分辨率的检测结果。
三、相控阵超声检测技术在管道对接焊缝检测中的应用1. 高精度:相控阵超声检测技术能够实现对管道对接焊缝的高精度扫描和成像,可以检测出焊缝中微小的缺陷和裂纹。
2. 高效率:相控阵超声检测技术能够实现多个超声波束的同时发射和接收,提高了检测效率和生产效率。
3. 灵活性:相控阵超声检测技术可以根据需要对超声波束的发射路径和角度进行灵活控制,适应各种焊缝形状和工件结构。
四、结语随着工业技术的不断发展,相控阵超声检测技术在管道对接焊缝检测中的应用将会越来越广泛。
管道对接焊缝相控阵超声检测

管道对接焊缝相控阵超声检测1. 引言1.1 管道对接焊缝相控阵超声检测的意义管道对接焊缝相控阵超声检测是指利用超声波技术对管道焊缝进行无损检测的一种方法。
其意义在于能够及时准确地发现管道焊缝存在的裂纹、夹杂物、疲劳等缺陷,确保管道的安全运行。
管道在输送液体或气体时承受着巨大的压力和温度变化,焊缝是管道中最容易出现问题的部位之一。
通过对焊缝进行超声检测,可以有效预防管道的泄漏或爆炸事故,保障工业生产和人们的生命财产安全。
管道对接焊缝相控阵超声检测的意义不仅在于检测管道焊缝的质量,也在于提高工作效率、节省成本,并在工程建设领域中发挥着重要作用。
通过对管道对接焊缝相控阵超声检测的研究和应用,可以不断提升检测技术水平,提高管道设备的安全性和可靠性,推动工程技术的发展。
1.2 管道对接焊缝相控阵超声检测的发展历程20世纪80年代,相控阵超声技术开始应用于管道对接焊缝的检测。
通过多元素探头的设计和控制,相控阵超声技术可以实现多角度、多方向的检测,大大提高了检测效率和准确度。
随着数字化技术和计算机技术的发展,相控阵超声检测设备也得到了不断优化和升级,成为现代管道对接焊缝检测的主流技术之一。
经过多年的发展和实践,管道对接焊缝相控阵超声检测技术已经取得了显著的成果。
其检测速度快、精度高、可靠性强的优势,使其在石油、化工、船舶等领域得到了广泛应用。
未来,随着科技的不断进步和创新,相信管道对接焊缝相控阵超声检测技术将会迎来更加辉煌的发展。
1.3 管道对接焊缝相控阵超声检测的现状相控阵超声检测技术的应用范围不断扩大。
不仅可以应用于普通管道的焊缝检测,还可以应用于复杂形状的焊缝检测,如T型、Y型等焊缝。
检测设备不断更新换代,性能不断提升。
随着科技的进步,相控阵超声检测设备的分辨率、灵敏度和稳定性等方面得到了极大的提高,使得焊缝检测更加精准和可靠。
相控阵超声检测方法不断创新。
工程师们在实践中不断摸索和改进检测方法,使得对焊缝的检测更加快捷和全面。
管道对接焊缝相控阵超声检测

管道对接焊缝相控阵超声检测管道对接焊缝是工业生产中常用的一种连接方法,焊缝的质量直接影响着管道的使用安全和性能。
为了确保焊缝的质量,需要使用非破坏检测技术对焊缝进行评估。
相控阵超声检测是一种常用的非破坏检测技术,具有操作灵活、检测效率高、灵敏度高等优点,被广泛应用于管道对接焊缝的检测中。
相控阵超声检测是一种利用超声波对被测对象进行成像检测的方法。
通过控制多个超声换能器按照一定的时序和角度,发射并接收超声波信号,从而获取被测物体的内部结构和缺陷情况。
相控阵超声检测可以实现对焊缝的全面检测,不仅可以检测焊缝的整体结构,还可以检测焊缝中的缺陷和腐蚀等问题。
在管道对接焊缝的相控阵超声检测中,首先需要选择合适的超声波换能器。
一般选择线阵或矩阵式换能器,其具有高发射/接收灵敏度、较宽的视场角和较高的分辨率等特点,可以更精确地获取焊缝的信息。
然后,将换能器安装在管道上,通过控制超声波的发射和接收,实现对焊缝的全方位检测。
相控阵超声检测不仅可以检测焊缝的整体结构,还可以检测焊缝中的缺陷。
通过分析检测信号的反射强度、时间、声速等信息,可以判断焊缝中是否存在裂纹、夹渣等缺陷,并确定其位置、大小和形态等。
还可以对焊缝的腐蚀程度进行评估,为后续的维修和加固提供依据。
相控阵超声检测在管道对接焊缝中的应用具有一定的难度和挑战。
管道的直径和壁厚等参数对检测结果有一定影响,需要根据具体情况进行调整。
焊缝的形态和结构多样,需要选择合适的探头和检测方法来满足实际需求。
相控阵超声检测的数据处理和分析也是一个复杂的过程,需要掌握一定的专业知识和技术手段。
管道对接焊缝的相控阵超声检测是一种常用的非破坏检测方法,可以全方位地评估焊缝的质量和缺陷情况。
但在实际应用中还存在一定的难度和挑战,需要借助专业知识和技术手段来实现准确检测。
相信随着科技的不断进步和发展,相控阵超声检测在管道对接焊缝中的应用会越来越广泛。
管道对接焊缝相控阵超声检测

管道对接焊缝相控阵超声检测1.引言管道工程是石油化工、能源、化工、供热等行业的重要基础设施之一,它与人民的生产生活密切相关。
管道的质量安全问题一直备受关注,而管道对接焊缝是管道工程中最容易出现质量问题的部位之一。
对接焊缝的质量直接影响到管道的安全运行,因此对对接焊缝进行精确、高效的检测显得尤为重要。
传统的检测方法主要包括X射线探伤和射线照相法等,这些方法虽然能够有效地检测焊缝内部的缺陷,但存在着工作环境不适应、检测速度慢、辐射危害大等问题。
相控阵超声检测技术的出现为管道对接焊缝的检测提供了一种高效、精确、非破坏性的解决方案。
2.相控阵超声检测技术原理相控阵超声检测技术是利用声学原理进行检测的一种先进技术。
其原理主要包括声源、声束发射、信号接收和成像四个方面。
(1)声源:声源是相控阵检测的基础,通常采用薄压电换能器作为声源。
压电换能器具有频率响应宽、发射方向可调等优点,可满足相控阵检测的多种需求。
(2)声束发射:在相控阵检测中,需要发射多道声束进行扫描,并且可以对每道声束的发射时间和发射角度进行精确控制。
这样可以实现对被检测目标的全面覆盖和深度探测,使得检测结果更加准确。
(3)信号接收:声波在被检测物体中传播时会产生回波信号,这些信号会被接收到并进行处理,从而获得目标的相关信息。
相控阵技术可以实现对多道声束回波信号的接收和处理,进而得到更加完善的检测结果。
(4)成像:相控阵超声检测技术可以通过对接收信号的处理和分析,形成目标的二维或三维图像,展现目标的内部结构和缺陷情况,提供了便利的检测结果。
3.技术特点相控阵超声检测技术具有以下几个技术特点:(1)高分辨率:相控阵检测技术可以通过对多道声束的发射和接收进行组合,从而获得更高的空间分辨率和深度分辨率,适用于对于微小缺陷的检测。
(2)多通道检测:相控阵技术可以同时对多道声束进行检测,具有高效和快速检测的特点,适用于大面积焊接的管道对接焊缝检测。
(3)灵活可控:相控阵技术可以根据实际需求对声束的发射角度和时间进行精确控制,灵活适应不同尺寸和形状的被检测目标。
管道对接焊缝相控阵超声检测

管道对接焊缝相控阵超声检测【摘要】本文主要介绍了管道对接焊缝相控阵超声检测技术。
首先介绍了该技术的原理,然后详细阐述了相控阵超声检测技术在管道对接焊缝检测中的应用,并介绍了相控阵超声检测设备及方法。
还分析了管道对接焊缝相控阵超声检测的优势,未来发展前景和挑战。
通过对该技术的研究和应用,可以提高焊缝检测的准确性和效率,提升管道工程的安全性和质量。
管道对接焊缝相控阵超声检测技术在工业领域具有重要意义和广阔的应用前景,但同时也面临着一些挑战,需要不断改进和完善。
【关键词】关键词:管道对接焊缝、相控阵超声检测、原理、技术、设备、方法、应用、优势、发展前景、挑战、研究背景、研究目的、研究意义1. 引言1.1 研究背景管道对接焊缝相控阵超声检测是一种非破坏性检测技术,可以有效地检测管道焊缝的缺陷和质量问题。
随着工业化的发展和工程建设的不断推进,对管道焊缝的质量要求也越来越高,因此需要一种高效、准确、可靠的检测方法来保障管道的安全运行。
目前,常规的管道焊缝检测方法存在一些局限性,如检测效率低、操作复杂、对人员技术要求高等问题,而相控阵超声检测技术则能够克服这些问题,具有更高的检测精度和灵活性。
对管道对接焊缝相控阵超声检测技术进行深入研究和应用具有重要意义。
通过对管道对接焊缝相控阵超声检测技术的研究,可以不仅提高管道焊缝的检测效率和准确性,保障管道的安全运行,还可以为管道工程的设计、施工和维护提供重要的参考和支持。
本文旨在对管道对接焊缝相控阵超声检测技术进行深入探讨,为相关领域的研究和应用提供理论支持和实践指导。
1.2 研究目的管道对接焊缝相控阵超声检测是一项重要的非破坏检测技术,在工业领域中具有广泛的应用。
其研究目的包括但不限于以下几个方面:1. 提高检测精度:通过对管道对接焊缝进行超声检测,能够准确、快速地发现焊缝缺陷和裂纹等问题,帮助工程师及时采取修复措施,保障管道安全运行。
2. 降低人工成本:相较于传统的目视检测方法,管道对接焊缝相控阵超声检测能够实现自动化、高效率的检测过程,减少人工操作,并提高工作效率。
管道对接焊缝相控阵超声检测
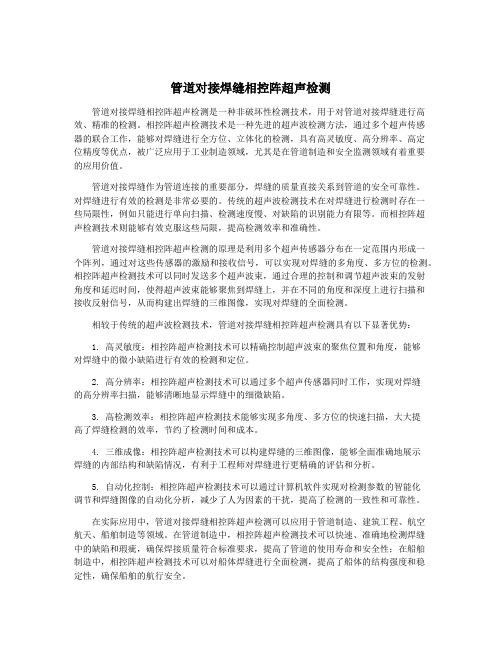
管道对接焊缝相控阵超声检测管道对接焊缝相控阵超声检测是一种非破坏性检测技术,用于对管道对接焊缝进行高效、精准的检测。
相控阵超声检测技术是一种先进的超声波检测方法,通过多个超声传感器的联合工作,能够对焊缝进行全方位、立体化的检测,具有高灵敏度、高分辨率、高定位精度等优点,被广泛应用于工业制造领域,尤其是在管道制造和安全监测领域有着重要的应用价值。
管道对接焊缝作为管道连接的重要部分,焊缝的质量直接关系到管道的安全可靠性。
对焊缝进行有效的检测是非常必要的。
传统的超声波检测技术在对焊缝进行检测时存在一些局限性,例如只能进行单向扫描、检测速度慢、对缺陷的识别能力有限等。
而相控阵超声检测技术则能够有效克服这些局限,提高检测效率和准确性。
管道对接焊缝相控阵超声检测的原理是利用多个超声传感器分布在一定范围内形成一个阵列,通过对这些传感器的激励和接收信号,可以实现对焊缝的多角度、多方位的检测。
相控阵超声检测技术可以同时发送多个超声波束,通过合理的控制和调节超声波束的发射角度和延迟时间,使得超声波束能够聚焦到焊缝上,并在不同的角度和深度上进行扫描和接收反射信号,从而构建出焊缝的三维图像,实现对焊缝的全面检测。
相较于传统的超声波检测技术,管道对接焊缝相控阵超声检测具有以下显著优势:1. 高灵敏度:相控阵超声检测技术可以精确控制超声波束的聚焦位置和角度,能够对焊缝中的微小缺陷进行有效的检测和定位。
2. 高分辨率:相控阵超声检测技术可以通过多个超声传感器同时工作,实现对焊缝的高分辨率扫描,能够清晰地显示焊缝中的细微缺陷。
3. 高检测效率:相控阵超声检测技术能够实现多角度、多方位的快速扫描,大大提高了焊缝检测的效率,节约了检测时间和成本。
4. 三维成像:相控阵超声检测技术可以构建焊缝的三维图像,能够全面准确地展示焊缝的内部结构和缺陷情况,有利于工程师对焊缝进行更精确的评估和分析。
5. 自动化控制:相控阵超声检测技术可以通过计算机软件实现对检测参数的智能化调节和焊缝图像的自动化分析,减少了人为因素的干扰,提高了检测的一致性和可靠性。
无损检测 钢制管道环向焊缝对接接头超声检测方法
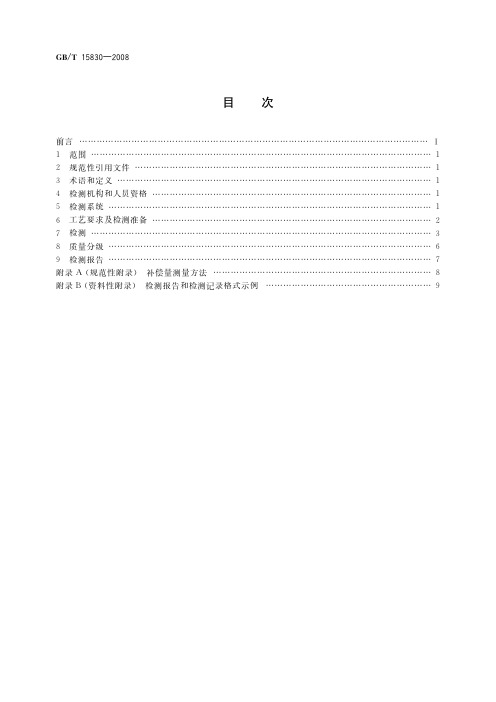
GB/T12604.1和 GB/T20737确立的术语和定义适用于本标准。
4 检 测 机 构 和 人 员 资 格
4.1 机 构 要 求 按本标准实施检测的机构或单位,应符合 GB/T5616或等效标准、法规的相关要求。
4.2 人 员 资 格 按本标准实施检测的人员,应按 GB/T9445或 合 同 各 方 同 意 的 体 系 进 行 资 格 鉴 定 与 认 证,并 由 雇
性 或 其 他 类 型 的 缺 欠 存 在 。 该 项 检 查 仅 作 记 录 ,不 属 于 对 母 材 的 验 收 检 测 。 检 查 的 要 点 如 下 :
a) 检 测 方 法 :接 触 式 脉 冲 反 射 法 ,采 用 频 率 为 (2~5)MHz的 直 探 头 ,晶 片 直 径 (10~25)mm。 b) 检 测 灵 敏 度 :将 无 缺 欠 处 第 二 次 底 波 调 节 到 荧 光 屏 满 刻 度 。
3
犌犅/犜 15830—2008
式中: 犘——— 跨 距 ,单 位 为 毫 米 (mm);
犘 =2犜tanβ
…………………………(2ቤተ መጻሕፍቲ ባይዱ)
犜——— 母 材 厚 度 ,单 位 为 毫 米 (mm);
β——— 探 头 折 射 角 ,单 位 为 度 (°)。 7.2.3 当管壁较厚(壁厚>50mm)时,采用直射法检测,但还需增加一个折射角度大的探头检测,参 见
GB/T5616 无 损 检 测 应 用 导 则 GB/T9445 无 损 检 测 人 员 资 格 鉴 定 与 认 证 (GB/T9445—2008,ISO9712:2005,IDT) GB/T12604.1 无 损 检 测 术 语 超 声 检 测 (GB/T12604.1—2005,ISO5577:2000,IDT) GB/T18852 无损检测 超声检验 测 量 接 触 探 头 声 束 特 性 的 参 考 试 块 和 方 法(GB/T18852— 2002,ISO12715:1999,IDT) GB/T20737 无 损 检 测 通 用 术 语 和 定 义 (GB/T20737—2006,ISO/TS18173:2005,IDT) JB/T8428 无 损 检 测 超 声 检 测 用 试 块 JB/T9214 A 型脉冲反射式超声波探伤系统工作性能 测试方法
管道对接焊缝相控阵超声检测

管道对接焊缝相控阵超声检测【摘要】管道对接焊缝相控阵超声检测在管道焊口检测中起着重要作用。
本文首先介绍了管道对接焊缝相控阵超声检测的重要性,并探讨了前沿技术在该领域的应用。
随后分析了传统管道焊口检测方法存在的问题,详细阐述了管道对接焊缝相控阵超声检测的原理和优势。
对相控阵超声检测设备的发展现状及关键技术进行了讨论。
最后展望了管道对接焊缝相控阵超声检测的未来发展,并总结了其重要性。
管道对接焊缝相控阵超声检测的推广将有效提高管道安全性,减少事故发生的概率,对整个工业领域具有重要意义。
【关键词】管道对接焊缝、相控阵超声检测、传统检测方法、原理、优势、设备发展、关键技术、未来发展、重要性、前沿技术、管道焊口检测、现状1. 引言1.1 管道对接焊缝相控阵超声检测的重要性管道对接焊缝相控阵超声检测在工业领域起着至关重要的作用。
随着现代化工业的快速发展,管道的安全性和可靠性需求也日益提高。
而焊接是管道构造中至关重要的环节,焊缝质量直接关系到管道的使用寿命和安全性。
对管道对接焊缝进行准确、可靠的检测变得非常关键。
传统的管道焊接检测方法存在一些局限性,例如对大面积检测非常困难,同时检测结果的准确性和可靠性也有待提高。
而相控阵超声检测技术的引入,为管道对接焊缝检测带来了新的希望。
相控阵超声检测技术具有高分辨率、高灵敏度和高可靠性的特点,能够更准确地检测管道焊缝内部的缺陷和问题,确保焊接质量符合标准要求。
管道对接焊缝相控阵超声检测在工业生产中具有重要意义,不仅可以提高管道的安全性和可靠性,还可以减少人工检测的时间和成本,提升工作效率和生产质量。
在未来的发展中,相信这项技术将会得到更广泛的应用和进一步的推广。
1.2 前沿技术在管道对接焊缝相控阵超声检测中的应用管道对接焊缝相控阵超声检测是一种高效、精准的检测方法,得到了广泛应用和推广。
在目前的前沿技术中,有一些在管道对接焊缝相控阵超声检测中的应用已经取得了显著的成果。
在超声波传感器方面,采用了先进的相控阵技术,可以实现对焊缝区域的快速、全面扫描,提高了检测的效率和准确性。
对接焊接接头超声波检测工艺规程
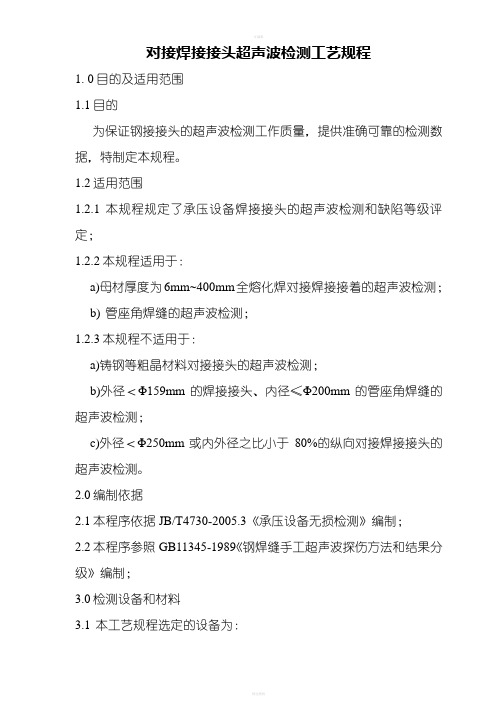
对接焊接接头超声波检测工艺规程1. 0目的及适用范围1.1目的为保证钢接接头的超声波检测工作质量,提供准确可靠的检测数据,特制定本规程。
1.2适用范围1.2.1本规程规定了承压设备焊接接头的超声波检测和缺陷等级评定;1.2.2本规程适用于:a)母材厚度为6mm~400mm全熔化焊对接焊接接着的超声波检测;b) 管座角焊缝的超声波检测;1.2.3本规程不适用于:a)铸钢等粗晶材料对接接头的超声波检测;b)外径<Φ159mm的焊接接头、内径≤Φ200mm的管座角焊缝的超声波检测;c)外径<Φ250mm或内外径之比小于80%的纵向对接焊接接头的超声波检测。
2.0编制依据2.1本程序依据JB/T4730-2005.3《承压设备无损检测》编制;2.2本程序参照GB11345-1989《钢焊缝手工超声波探伤方法和结果分级》编制;3.0检测设备和材料3.1 本工艺规程选定的设备为:数字式A型脉冲接触式超声波检测仪;3.2 为保证超声波检测结果的可靠,超声波检测仪及超声波检测要进行定期校验,必要时可进行随机校验;3.2.1 超声波检测仪和超声波检测用探头的校验方法可依照《数字式超声波检测仪、探头性能测试》程序进行;3.2.2 超声波检测仪和超声波检测用探头的校验的评定标准为:a).水平线性误差值ΔL≯1%;b). 垂直线性误差Δd≯5%;c). 动态范围>26dB。
且保证在达到所检试件最大声程时,其有效灵敏度余量≮10dB;d). 盲区<7mm;e).分辨力F:⑴.直(纵波)探头的分辨力F1≤6mm;⑵.斜(横波)探头的分辨力F2≤6mm。
3.3超声波检测仪和超声波检测用探头的校验周期可依照《数字式超声波检测仪、探头性能测试》程序的要求进行;3.4探头的选用见表1:表1:推荐采用的斜(横波)探头3.5试块试块是超声波检测仪器校准的基准,也是缺陷评定参考基准。
试块的选用必须满足JB/T4730—2005.3标准的要求。
焊接接头超声检测讲稿1-主要规范及标准
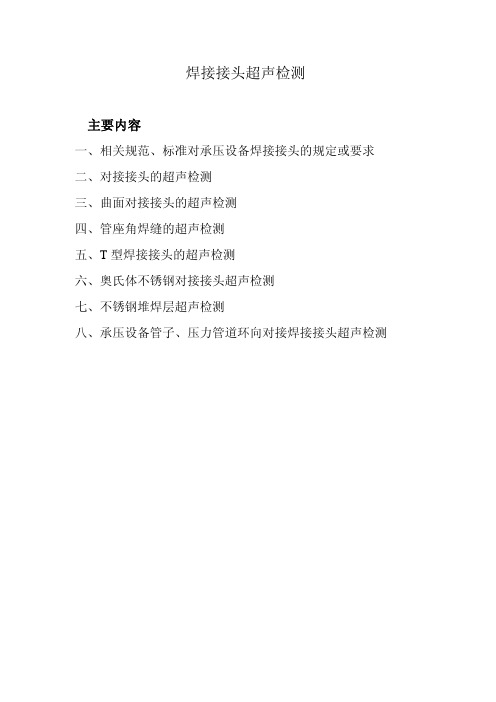
接头;
在检测部位发现超标缺陷时,应当在该 c) 对于满足 GB 150.3 中 6.1.3 不另行补强的接 c) 凡被补强圈、支座、垫板、内件等所覆
缺 陷 两 端 的 延 伸 部 位 各 进 行 不 少 于 管,自开孔中心,沿容器表面的最短长度等于 盖的焊接接头;
开孔直径的范围内的焊接接头;
d) 嵌入式接管与球壳对接连接的焊接接
声检测,超声检测包括衍射时差法超声检 测(TOFD)、可记录的脉冲反射法超声检测 和不可记录的脉冲反射法超声检测。 10.1.2 当采用不可记录的脉冲反射法超声
8.6.1.1 检测方法包括射线检测(X 射线定 向曝光、γ射线周向曝光、γ射线全景曝 光)、超声检测(包括衍射时差法超声检测 (TOFD)、可记录的脉冲反射法超声检测、 不可记录的脉冲反射法超声检测)、磁粉检
除 8.6.3.1 规定以外的对接焊接接头, 应进行局部检测。检测方法按设计文件规
器,其每条 A、B 类对接接头按照以下要 方法按设计文件规定。其中,对低温容器检测长 定,检测长度不得少于各条对接焊接接头
求采用本规程 4.5.3.1 第(1)项的方法进 度不得少于各焊接接头长度的 50%,对非低温容 长度的 20%,且均不得小于 250mm,局部检
(一) TSG R0004-2009 固定式压力容器安全技术监察规程及相关容器标准中 的规定
这里主要介绍 GB150.4-2011 和 GB 12337-2014Biblioteka TSG R0004-2009
4.5 无损检测 4.5.1 无损检测人员
无损检测人员应当按照相关技术规范 进行考核取得相应资格证书后,方能承担 与资格证书的种类和技术等级相对应的无 损检测工作。 4.5.2 无损检测方法 (1)压力容器的无损检测方法包括射线、超 声、磁粉、渗透和涡流检测等; (2)压力容器制造单位或者无损检测机构 应当根据设计图样要求和 JB/T 4730 的规 定制定压力容器的无损检测工艺; (3)采用未列入 JB/T 4730 或者超出其适用 范围的无损检测方法时,按照本规程 1.9 的规定。
- 1、下载文档前请自行甄别文档内容的完整性,平台不提供额外的编辑、内容补充、找答案等附加服务。
- 2、"仅部分预览"的文档,不可在线预览部分如存在完整性等问题,可反馈申请退款(可完整预览的文档不适用该条件!)。
- 3、如文档侵犯您的权益,请联系客服反馈,我们会尽快为您处理(人工客服工作时间:9:00-18:30)。
《压力管道环向对接接头相控阵超声检测规范》河南省地方标准编制说明
一、编制的目的和意义
随着当今社会的飞速发展,压力管道已被广泛应用于石油、化工、冶金、电力、机械等行业以及城市燃气和供热系统,而且占据着越来越重要的地位;由于压力管道所传载的介质多是有毒、易燃、易爆且所处外界环境较为复杂,一旦发生事故将会造成人员伤亡、财产损失、环境污染及恶劣的社会影响。
无损检测技术是压力管道制造和在用检验中的重要检测手段,对保证压力管道管体质量及在用压力管道的安全运行起着至关重要的作用。
近年来,超声相控阵检测技术在压力管道的检验检测中应用越来越广泛,使用超声相控阵检测方法不仅避免了衍射时差法超声检测存在检测盲区技术问题,而且避免了射线检测方法存在安全防护问题。
同时较常规超声检测方法相比能显著提高定位、定量精度,特别是显著提高了对缺陷性质的估判。
与其它压力管道焊接接头内部缺陷检测方法相比,超声相控阵检测技术的优点如下:
1)有利于对压力管道焊接接头中的面积型和体积型缺陷检测,缺陷检出率高;
2) 检测数据呈现三维显示图象,利于缺陷定位、定量和定性分析;
3)检测扫描速度快,一个探头覆盖多个角度,无扫查面盲区;
4)分辨率好,灵敏度高,对缺陷定位和定量准确;
5)检测效率高,采用专用扫查装置,可实现焊缝长度方向的全体积扫查;
6)可达性好,对操作空间狭窄部位焊缝检测,可携带便携式位置编码器扫查或手动锯齿扫查;
7)检测结果直观、重复性好,可实时显示;并可打印、存盘、保存和远程分析;
8)不受作业时间限制,安全环保,劳动强度小,成本低。
为了适应社会经济发展的需要,推动超声相控阵检测技术在压力管道焊接接头检测中的应用,提高对压力管道对接环焊缝超声相控阵检测方法、操作、评定及质量分级的规范性和准确性,弥补现行国家标准GB/T32563-2016中缺陷的评定和质量分级内容的缺失,保证超声相控阵检测技术更好地使用和服务于压力管道对接环焊缝内部缺陷检测工作中,需要制定压力管道环向对接接头相控阵超声检测规范。
二、任务来源及编制原则和依据
1、任务来源
为了使超声相控阵检测技术在压力管道焊接接头检测应用中更加标准化、规范化,亟需制定相应的地方标准或准则来规范
超声相控阵检测技术对压力管道焊接接头的检测、缺陷评定和质量分级,为了保证压力管道在使用过程中的安全,保障人民生命及财产的安全,2018年3月由河南省锅炉压力容器安全检测研究院向河南省质量技术监督局申请了河南省地方标准立项,根据河南省质量技术监督局2018年07月30日下达的豫质监标发【2018】236号《河南省质量技术监督局关于下达2018年第一批河南省地方标准制修订计划的通知》文件(立项编号:20181210154),批准《压力管道环向焊接接头相控阵超声检测规范》地方标准的制定。
之后,河南省锅炉压力容器安全检测研究院和洛阳中油检测工程有限公司的专业技术人员组成了标准起草工作组,收集了有关资料,进行调查研究,根据从2017年3月以来在洛阳中油检测工程有限公司进行的超声相控阵检测技术在压力管道对接焊缝的应用试验研究,以及对现行国家标准、行业标准的对比分析,最终确定了本规范的征求意见稿。
2、编制原则
1)适用性原则:本规范适用于超声相控阵检测技术对压力管道环向对接接头的检测。
2)有效性原则:本规范的执行,在降低成本和劳动强度情况下,可以有效提高压力管道环向焊接接头的质量控制。
3)可操作性原则:规范中的检测程序设置合理,检测人员容易学习掌握,检测项目易于实施。
3、标准制定的依据
本标准的编制依据主要包括有关超声相控阵检测技术以及其他相关超声检测在承压设备焊接接头检测中的应用的国家标准和行业标准及ASME相关标准内容。
主要依据有:
GB/T 12604.1-2005 无损检测术语超声检测
GB/T 23905 无损检测超声检测用试块
GB/T 29302-2012 无损检测仪器超声相控阵检测系统的性能与检验
GB/T 32563-2016无损检测超声检测相控阵超声检测方法NB/T47013.1-2015 承压设备无损检测第1部分:通用要求
NB/T47013.3-2015 承压设备无损检测第3部分:超声检测
NB/T47013.10-2015 承压设备无损检测第10部分:衍射时差法超声检测
ASME BPVC.V-2015 焊缝超声波检验方法
ASTM SE-2700 使用相控阵对焊缝进行接触法超声检测的标准操作方法
TSG Z8001-2013 特种设备无损检测人员考核规则
GB50235-2010工业金属管道工程施工规范
三、编制过程
在申请标准立项之前,由河南省锅炉压力容器安全检测研究院和洛阳中油检测工程有限公司相关人员已经组成课题组从
2017年3月份开始进行超声相控阵检测技术在压力管道对接焊缝检测中的应用研究,经过一年的实验研究,于2018年3月份由河南省锅炉压力容器安全检测研究院向河南省质量技术监督局申请了河南省地方标准立项,立项批准后,由河南省锅炉压力容器安全检测研究院牵头,成立了标准起草小组,研究讨论了标准框架结构、标准涉及内容、确立标准调研内容等,并进行了任务分工,争取及早完成标准的制定工作。
具体工作如下:
2017年3月至2018年3月在洛阳中油检测工程有限公司实验室进行超声相控阵检测技术在压力管道对接焊缝检测中的应用研究,收集积累实验数据;
2018年4月至2018年7月开展调研和资料搜集工作;
2018年8月2日召开标准起草小组成立暨第一次工作会议,参加会议的有标准起草小组和单位主管领导全体人员。
与会代表就标准编制工作大纲、编制分工和进度计划等进行了认真深入的讨论。
2018年中旬形成初稿,并于8月16日召开标准起草小组第二次工作会议,起草单位的有关领导、标准起草小组全体人员参加了会议。
与会人员逐章、逐节、逐条对标准初稿的主要内容、需研究完善的问题进行认真细致的讨论,对下一步的编制工作计划和进度做出具体安排。
2018年9月初,标准起草小组根据第二次编制工作会议提出的意见和建议,对标准初稿进行修改完善,形成征求意见稿。
四、主要内容的确定
1.范围、
2.标准引用文件、
3.术语和定义、
4.基本规定、
5.检测准备、
6.检测系统设置及校准、
7.检测、
8.数据的分析和解释、
9.检测报告及保存、附录、参考文献,共计11方面内容。
其中:
范围:从压力管道材质和规格两方面明确了本规范的适用范围;
标准引用文件:罗列了本规范引用和参考的相关标准及规范;
术语和定义:本规范中出现的术语和定义;
基本规定:包括检测人员、检测设备及器材、试块、耦合剂、检测工艺文件、工艺可靠性验证、检测设备和器材校准、核查、运行核查和检查、安全要求;
检测准备:包括检测区域、扫描类型选择、扫查方式选择、探头选择、楔块选择、扫描覆盖、探头步进偏移确定;
检测系统设置及校准:包括检测系统设置、检测系统校准、灵敏度设置、检测系统复核;
检测:包括扫查面准备、焊缝标识及分段、扫查覆盖、扫查速度、扫查过程观察、检测数据存储、检测温度、母材检测、横向缺陷检测;
数据的分析和解释:包括检测数据的有效性评价、显示分类、缺陷定量、缺陷评定与质量分级;
检测报告及保存:包括检测报告和存档要求;
附录:包括附录A(规范性附录)相控阵超声探头晶片失效率的测试、附录B(规范性附录)相控阵超声探头声束偏转范围的测试、附录 C(资料性附录)检测报告表格、附录 D(资料性附录)条文说明。
五、与国家法律法规和强制性标准的关系
国家没有本规范内容方面的强制性标准,所以本规范是在学习《特种设备安全法》、GB/T 32563-2016无损检测超声检测相控阵超声检测方法、NB/T47013.1-2015 承压设备无损检测第1部分:通用要求、NB/T47013.3-2015 承压设备无损检测第3部分:超声检测、NB/T47013.10-2015 承压设备无损检测第10部分:衍射时差法超声检测等相关国家法律和推荐性标准的基础上进行制定的,是对上述标准采用超声相控阵检测技术对压力管道环向焊接接头检测内容的补充和完善。
六、标准实施的建议
制定本规范的目的,是为了确保超声相控阵检测对压力管道环向焊接接头的内部质量控制,保证压力管道的安全使用,从而保障人民生命及财产的安全,建议本标准作为推荐性地方标准执行,对采用超声相控阵检测技术检测压力管道环向焊接接头能起
到很好的指导和推动作用。
建议由河南省锅炉压力容器安全检测研究院组织相关人员进行标准宣贯。
标准起草小组
2018年9月3日。