Brennan's Guide to Inline Assembly
ISO-34-1-2010

ii
© ISO 2010 – All rights reserved
ISO 34-1:2010(E)
Contents
பைடு நூலகம்
Page
Foreword ............................................................................................................................................................iv
5.2 Nick cutter ..............................................................................................................................................3
Annex B (normative) Calibration schedule ....................................................................................................11
Bibliography ...................................................................................................................................................... 13
© ISO 2010 – All rights reserved
惠普彩色激光打印机 Pro M454 和惠普彩色激光多功能一体机 Pro M479 维修手册说明书
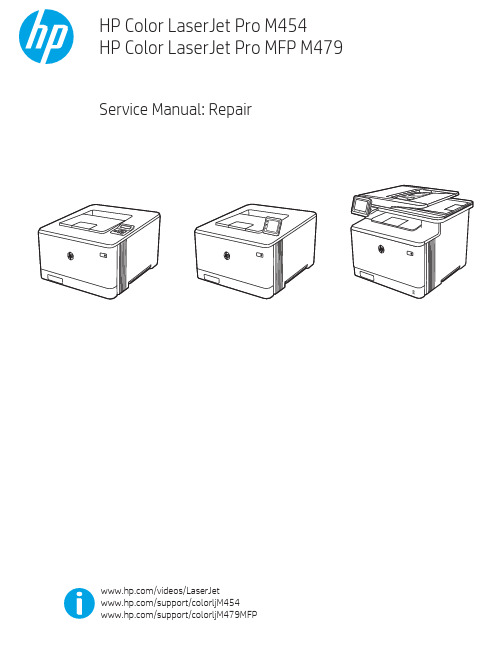
Table -1 Revision history Revision number 1
Revision date 6/2019
Revision notes HP LaserJet Pro M454 HP LaserJet Pro MFP M479 Repair manual initial release
Additional service and support for HP internal personnel HP internal personnel, go to one of the following Web-based Interactive Search Engine (WISE) sites: Americas (AMS) – https:///wise/home/ams-enWISE - English – https:///wise/home/ams-esWISE - Spanish – https:///wise/home/ams-ptWISE - Portuguese – https:///wise/home/ams-frWISE - French Asia Pacific / Japan (APJ) ○ https:///wise/home/apj-enWISE - English ○ https:///wise/home/apj-jaWISE - Japanese ○ https:///wise/home/apj-koWISE - Korean ○ https:///wise/home/apj-zh-HansWISE - Chinese (simplified)
Find information about the following topics ● Service manuals ● Service advisories ● Up-to-date control panel message (CPMD) troubleshooting ● Install and configure ● Printer specifications ● Solutions for printer issues and emerging issues ● Remove and replace part instructions and videos ● Warranty and regulatory information
NMR Users Guide

NMR Users GuideOrganic Chemistry LaboratoryIntroductionThe chemistry department is fortunate to have a high field (400 MHz) Nuclear Magnetic Resonance (NMR) spectrometer. You will be using this instrument for analysis of products throughout the organic laboratory. As such, you will need to be familiar with its use and the use of the Delta software needed to analyze the resulting data.NMR Sample PreparationLiquid samplesAdd the 2-3 drops of the liquid to an NMR tubeAdd enough solvent to fill the NMR tube to 35 mm in height (about three fingers full), roughly 0.75 mL.Gently place a clean cap on the NMR tubeInvert the tube several times to mix the sampleSolid samplesAdd 30 mg (0.030g) of sample to a sample vialAdd about 0.75 mL of solventMix to dissolve the sampleTransfer the solution to an NMR tubeIf necessary add enough solvent to bring the solvent level up to 35 mm in height Gently place a clean cap on the NMR tubeInvert the tube several times to mix the sampleLoading the NMR tubeCarefully insert the NMR tube into the wide end of the Teflon spinnerMake sure the inner piece of the spinner is inserted as far down as possibleUse the clear plastic depth gauge to set the NMR tube to the correct depthPlace the assembly in the auto sample holder in the slot whose number matchesthe one on the spinner assemblyNever reach across the autosampler to load or retrieve a sampleNMR tube cleaningRemove the NMR tube from the sample spinner and return the spinner to the consoleDiscard the NMR solution into an appropriate waste containerPlace the NMR tube cap on the bottom of the NMR tubeInvert the NMR tube into the NMR tube cleaner (SC111)Turn on the water aspiratorRinse the tube with three portions of acetoneRemove the tube and discard the capPlace the NMR tube in the drying oven (SC 112)Running a routine NMR sampleMake sure your sample is loaded in the autosampler and you know the slot number Entering sample informationFilename: your SHU usernameComment: describe the sampleSlot: enter the number your sample is inSolvent: select the solvent you used to prepare the sampleRecheck all of the entered values BEFORE going to the next stepEnter your email address into the Export to dialog boxSelect which type of spectrum to be runProton – runs a simple proton NMR spectrumCarbon – runs a simple carbon-13 NMR spectrumProton and Carbon – runs both spectra, more quickly than selecting bothindividuallyDelta NMR SoftwareInstalling Delta: Copy the appropriate Delta install file (either PC or Mac) from the department NMR website or one of the CDs in the library to your desktop. Double click on the file to begin the installation. Follow the directions during the install. During the install choose minimal for the Installation Set.If you continue to have trouble loading either version visit the Help Desk, they can do it for you.Once the program is installed you will need to give it a license key. To do this, open the program. Choose File:Installation:License Key. In the blank spaces enter: HN-JS-O4-6O-AW. This will activate your version of Delta. If you do not do this your version of Delta will close after 15 minutes.Renaming Delta files: The SHU email system sometimes strips the name off of the Delta file during delivery. The resulting file will be named Delta Data. Unfortunately Delta will not be able to open this file without renaming. All Delta files must end in a dash and a number (e.g. filename-1.jdf). So you will need to rename Delta Data.jdf into this format. I suggest not using the same name repeatedly (e.g. delta data-1.jdf) as you may overwrite any other files you have saves on your computer.Opening an NMR file: Right click on the file and choose ‘open with’. Choose Delta. From now on double clicking any NMR file should open Delta.A detailed manual is available by clicking on the ‘?’ button on the master console. If you run into any problems this is a good place to start.Analyzing a 1H NMR spectrum (see video on department NMR page).When you open your spectrum you should see a correctly phased spectrum. If you see an FID instead, you will need to import the appropriate processing list. Do this by clicking on the processing list button (upper right). In the dialog box that opens up click on‘Global’. Choose proton_autophase.list from the list that appears. The program will automatically run the processing list.Note that holding your cursor over any button will tell you what that button does.Examine the baseline of your spectrum. It should be nice and flat with no peaks extending below the baseline. If not, the spectrum is not correctly phased. You can touch up the phase by clicking on the ‘phasing’ bar on the far right. This will open an inset window in the lower right. By clicking on the P0 and P1 buttons you can adjust the phase. Phasing is particularly important in order to get good integrals.Click on the ‘options’ bar on the right side, this will open another inset window with a number of useful settings.Tools: Across the top of the spectrum are a number of tools useful for analyzing your spectrum.The first is the zoom tool.-Clicking and dragging below the x axis will zoom the x axis only-Clicking and dragging to the left of the y axis will zoom the y axis only-Note the key short cuts above and to the right of the spectrum, these will allow you to quickly move about the spectrum. Reset will remove all zoom to give the full spectrum. Unzoom will undo the last zoom command.Setting the reference-Make sure the X Ref in the options box is 0-Click on the paste reference tool-Click on the TMS peak, this will now be set to zero-If no TMS peak is present, change the X Ref to the solvent and click on the solvent peak (usually chloroform)Integration-Click on the Auto Integrate Button at the very top of the screen-This will integrate all peaks in the spectrum-Split any overlapping peakso Select the integral with the ‘select’ toolo Click on the upper left grab boxo A pair of scissors will appearo Drag these midway between the two peaks and releaseo Repeat as necessary working from left to right-Normalize the integralso Select a known integral (e.g. a methyl group)o Type the integer value into the ‘normal’ box in the option and hit returno Make sure all of the integrals are near integer values, adjust as necessary -Select and delete to remove unwanted integralsPicture in Picture-Allows expansion of multiplets-Select PIP tool-Click and drag in an open area of the spectrum-Use the zoom tool to select the peak(s) of interest-Use the select tool to move the window around and adjust its size-Use the delete key to remove any unwanted PIP windowsFinal Review-Set the x axis to 0-8 ppm (unless you have peaks at >8 ppm)-Make sure all peaks have a normalize integral-Make sure there is an expansion for all defined multipletsAnalyzing a 13C NMR spectrum (see video on department NMR page).Save the file to your computer and double click it to open. It should open as a fully processed spectrum, but if only an FID is present click on the open processing list button and in the global directory select carbon_autophase.list. This should automatically process, if not, click the process button.Open the phasing and options windowsMake sure the phasing is correct, use the manual phasing buttons (P0 and P1) if not.All of the tools work the same way as they do for a proton spectrum. Carbon spectra are not quantitative so they are never integrated. It is also usually not necessary to expand any portions of the carbon spectrum as they tend to be quite simple. It is a good idea to peak pick them however.-Select the automatic peak pick button on the top line-Adjust the threshold button as necessary to include all peaks but not the noise. Set the full spectrum to 0-200 ppm (unless you have a peak above 200)Analyzing an NMR spectrum (see video on department NMR page).1.identify any impurity peaks such as solvent or water (see Table 1). For instance,in the proton spectrum CDCl3 has a residual peak at 7.27 ppm and water shows up at 1.5 ppm (see the table below for other possibilities).2.draw the structure on the spectrum and label each proton or carboning the chemical shift charts in your text assign each of the peaks to a nuclei onthe structure4.all peaks on the spectrum should be assigned to either the compound or animpurityPlotting your spectrum: The most reliable way to print within Delta is to use the built in PDF printer. This has the advantage of giving you an electronic copy of your spectrum as well. Click on the plot button on the top line. Select JEOL PDF. This will open a dialog box prompting you where to save your file. Once you open this PDF file you can print is normally.Table 1. Chemical Shifts for Common NMR Solvents.。
EN 1514-2-2005

BS EN Array1514-2:2005BS EN 1514-2:2005This British Standard was published under the authority of the Standards Policy and Strategy Committee on 28 June 2005© BSI 28June 2005ISBN 0 580 46100 9National forewordThis British Standard is the official English language version ofEN 1514-2:2005. It supersedes BS EN 1514-2:1997 which is withdrawn.The UK participation in its preparation was entrusted to Technical Committee PSE/2, Jointing Materials and Compounds, which has the responsibility to:A list of organizations represented on this committee can be obtained on request to its secretary.Cross-referencesThe British Standards which implement international or Europeanpublications referred to in this document may be found in the BSI Catalogue under the section entitled “International Standards Correspondence Index”, or by using the “Search” facility of the BSI Electronic Catalogue or of British Standards Online.This publication does not purport to include all the necessary provisions of a contract. Users are responsible for its correct application.Compliance with a British Standard does not of itself confer immunity from legal obligations.—aid enquirers to understand the text;——promulgate them in the UK.Summary of pagesThis document comprises a front cover, an inside front cover, the EN title page, pages 2 to 14, an inside back cover and a back cover.The BSI copyright notice displayed in this document indicates when the document was last issued.Amendments issued since publication Amd. No.DateCommentsEUROPEAN STANDARD NORME EUROPÉENNE EUROPÄISCHE NORMEN 1514-2May 2005ICS 23.040.80Supersedes EN 1514-2:1997English versionFlanges and their joints - Gaskets for PN-designated flanges -Part 2: Spiral wound gaskets for use with steel flangesBrides et leurs assemblages - Joints pour les brides désignées PN - Partie 2: Joints spiralés pour utilisationavec des brides en acierFlansche und ihre Verbindungen - Dichtungen für Flanschemit PN-Bezeichnung - Teil 2: Spiraldichtungen fürStahlflanscheThis European Standard was approved by CEN on 24 March 2005.CEN members are bound to comply with the CEN/CENELEC Internal Regulations which stipulate the conditions for giving this European Standard the status of a national standard without any alteration. Up-to-date lists and bibliographical references concerning such national standards may be obtained on application to the Central Secretariat or to any CEN member.This European Standard exists in three official versions (English, French, German). A version in any other language made by translation under the responsibility of a CEN member into its own language and notified to the Central Secretariat has the same status as the official versions.CEN members are the national standards bodies of Austria, Belgium, Cyprus, Czech Republic, Denmark, Estonia, Finland, France,Germany, Greece, Hungary, Iceland, Ireland, Italy, Latvia, Lithuania, Luxembourg, Malta, Netherlands, Norway, Poland, Portugal, Slovakia, Slovenia, Spain, Sweden, Switzerland and United Kingdom.EUROPEAN COMMITTEE FOR STANDARDIZATION C O M I T É E U R O P ÉE N D E N O R M A LI S A T I O N C HES KOM ITEE FÜR NOR M UNG© 2005 CENAll rights of exploitation in any form and by any means reserved worldwide for CEN national Members.Ref. No. EN 1514-2:2005: EEN 1514-2:2005 (E)ContentsPage Foreword (3)Introduction (4)1Scope (5)23Terms and definitions4Designations5Gasket designs (7)6Gasket types (8)7Dimensions (8)8Marking (11)Annex A (informative) Information to be supplied by the purchaser (13)Bibliography (14)EN 1514-2:2005 (E)ForewordThis European Standard (EN 1514-2:2005) has been prepared by Technical Committee CEN/TC 74 “Flanges and their joints”, the secretariat of which is held by DIN.This European Standard shall be given the status of a national standard, either by publication of an identical text or by endorsement, at the latest by November 2005, and conflicting national standards shall be withdrawn at the latest by November 2005.This document supersedes EN 1514-2:1997.EN 1514 consists of the following parts, Flanges and their joints - Dimensions of gaskets for PN-designated flanges:⎯ Part 1: Non-metallic flat gaskets with or without inserts;⎯ Part 2: Spiral wound gaskets for use with steel flanges;⎯ Part 3: Non-metallic PTFE envelope gaskets;⎯ Part 4: Corrugated, flat or grooved metallic and filled metallic gaskets for use with steel flanges;⎯ Part 6: Covered serrated metal gaskets for use with steel flanges;⎯ Part 7: Covered metal jacketed gaskets for use with steel flanges;⎯ Part 8: Polymeric O-Ring gaskets for grooved flanges.According to the CEN/CENELEC Internal Regulations, the national standards organizations of the following countries are bound to implement this European Standard: Austria, Belgium, Cyprus, Czech Republic, Den-mark, Estonia, Finland, France, Germany, Greece, Hungary, Iceland, Ireland, Italy, Latvia, Lithuania, Luxem-bourg, Malta, Netherlands, Norway, Poland, Portugal, Slovakia, Slovenia, Spain, Sweden, Switzerland and United Kingdom.EN 1514-2:2005 (E)IntroductionThis European Standard replaces an earlier one issued in 1997. The reason for the revision is to ensure thatthis European Standard.The dimensions of spiral wound gaskets for tongue and groove flanges and spigot and recess flanges to EN 1092-1 are not included in this European Standard. Such gaskets may be available, however, for these types of flanges and the purchaser is advised to consult the manufacturer as to their availability.EN 1514-2:2005 (E)1 ScopeThis European Standard specifies the dimensions and marking of spiral wound gaskets for use in conjunction with flat face and raised face flanges complying with EN 1092-1 for PN 10, PN 16, PN 25, PN 40, PN 63, PN 100 and PN 160 and up to and including DN 1000.NOTE 1 Dimensions of other types of gaskets for use with flanges to EN 1092-1, EN 1092-2, EN 1092-3 and EN 1092-4 are given in EN 1514-1, EN 1514-3, EN 1514-4, EN 1514-6, EN 1514-7 and EN 1514-8.NOTE 2 Annex A lists information that should be supplied by the purchaser when ordering gaskets in circumstances where the choice of the gasket materials appropriate to the service is left to the supplier.2 Normative referencesThe following referenced documents are indispensable for the application of this document. For dated refer-ences, only the edition cited applies. For undated references, the latest edition of the referenced document (including any amendments) applies.EN 1333, Pipework components — Definition and selection of PN.EN ISO 6708, Pipework components — Definition and selection of DN (nominal size) (ISO 6708:1995).3 Terms and definitionsFor the purposes of this European Standard, the following terms and definitions apply.3.1DNsee EN ISO 67083.2PNsee EN 13334 Designations4.1 Essential Features and Dimensions4.1.1 GeneralA major feature of the design of spiral wound gaskets to the requirements of this European Standard is the mini-misation of the possibility of the inner ring protruding into the bore of the pipe to which the flange is attached. The fit of the inner ring and sealing element relative to the outer ring has been selected to comply with this objective. The essential features of a spiral wound gasket in compliance with this specification are given in Figures 1 and 2 and/or are listed below.Above DN 200 a maximum of 0,4 mmGuide Ring Thickness 3 mm ± 0,25EN 1514-2:2005 (E)Sealing element location groove shall be centrally located in the guide ring Centre ± 0,1 mm Number of empty wraps on external diameter of the sealing 3 to 5 elementNumber of empty wraps on the internal diameter of the sealing 2 to 3 elementMinimum of 4element, i.e. on the empty wraps0,2 mm ± 0,02 mmWidth of the profiled metal of the sealing element4,5 mm 300.+Thickness of the filler material shall be as appropriate for the filler type Protrusion of the filler above the profiled metal of the sealing 0,3 ± 0,1 mmelementCompression of the sealing element shall not result in contact between the flange and the guide ring, see also 4.1.2Graphite ash contentmaximum of 2 %PTFE filler to contain no recycled material and may be either sintered or non-sintered Sharp edges on inner ring and guide ring to be removed Dimensions to be as given in Table 1 4.1.2 Maximum CompressionMetal to metal contact between the guide ring and the flange shall not be achieved with the maximum load that can be generated by the flange bolts. 4.1.3 The Use of an Inner RingAn inner ring shall be used with all gaskets using PTFE as the filler and with all gaskets for pressure groups PN 63, PN 100 and PN 160.In addition to the above, it is strongly recommended that an inner ring should be used with all gaskets, this should therefore be specified on the order for all gaskets for pressure groups PN 10, PN 25 and PN 40.4.2 Range of PN DesignationsGaskets shall be designated as suitable for use with one or more of the following PN designations of flanges: PN 10 PN 63 PN 25 PN 100PN 40PN 160EN 1514-2:2005 (E)4.3 Range of DN (nominal sizes)Gasket nominal sizes shall be designated in accordance with the ranges specified in Table 1.4.4 Gasket typesGasket types, as defined in Clause 6 and as illustrated in Figure 3, shall be designated as:⎯ Type C/I: Sealing element with centring ring and inner ring;⎯ Type C/O: Sealing element with centring ring.4.5 Information to be supplied by the purchaserNOTE Where the purchaser wants the manufacturer to specify the materials of the gasket then the information that should be supplied to the manufacturer with the order is given in Annex A.5 Gasket designsGaskets for which dimensions are specified shall be of one of the designs shown in Figure 1.The clearance between the sealing element and the centring ring shall be as shown in Figure 2.NOTE 1 Figure 1 shows a typical design of a metallic spiral wound gasket and, for use with type A or type B flanges. NOTE 2 Type A and type B flange facings are illustrated in EN 1092-1.NOTE 3 The profile of the metal winding of the sealing element is at the option of the manufacturer.NOTE 4 The materials of the gasket may be either specified by the purchaser or, if required by the purchaser, they may be chosen by the manufacturer to suit the operating conditions. In the latter case, the purchaser should define the operating conditions in the enquiry and/or order (see Annex A).NOTE 5 The attention of the user is drawn to the load necessary to compress spiral wound gaskets and the available load with PN 10 flanges should be verified as adequate prior to using these gaskets.EN 1514-2:2005 (E)a) Type C/Ib) Type C/OFigure 1 — Spiral wound gaskets6 Gasket typesGaskets shall be one of the following types:a) Type C/I Sealing element with centring ring and inner ring;b) Type C/O Sealing element with centring ring.All gaskets shall have a centring ring. All PN 63, PN 100 and PN 160 gaskets shall have an inner ring. All gaskets containing PTFE filler material shall have an inner ring.NOTE 1 The use of an inner ring is recommended for all PN designations and the purchaser should specify on the en-quiry and/or order if an inner ring is required for PN 10, PN 25 and PN 40 gaskets (see Annex A).NOTE 2 The selection of gasket type should take into account the fluids, the operating conditions, the properties of the gasket materials, the type and surface finish of the flange facing and the flange bolt loading. It is recommended that selec-tion of gaskets for any particular application is made in consultation with the gasket supplier (see Annex A).7 DimensionsThe dimensions of spiral wound gaskets for types A and B flange facings shall be as given in Table 1 and overall thickness, including filler, shall be as given in Figure 2.EN 1514-2:2005 (E)Dimensions in millimetresKeya See Table 1 for detailsb Protrusion minimum of 0,2 mmc Gasket shall not compress such that metal to metalcontact between flange and guide rings is achievedd Width (of profiled metal of the sealingelement)e Tolerance:1 2 to 3 empty wraps2 3 to 5 empty wraps3 Central groove ± 0,1 mm4 Sharp edges removed5 Minimum of four welding points for each6 Metal thickness 0,2 mm ± 0,02 mm7 Thickness as appropriate to filler typeGraphite Ash content < 2 %,PTFE filler to contain no re-cycled material and may beeither sintered or non-sintered.Figure 2 — Spiral wound gasket detailsEN 1514-2:2005 (E)10Table 1 — DimensisonsEN 1514-2:2005 (E)8 Marking8.1 GeneralThe guide ring shall be marked with the following information:a) Manufacturer's name or trade mark;b) DN followed by the appropriate number;c) PN designation followed by the appropriate number;d) The manufacturer’s symbols or colour coding as required in 8.2 for the materials of the metal winding, thefiller material and centring ring, unless the latter is carbon steel, and inner ring unless it is 304 stainless steel.EXAMPLE of guide ring marking: AAA/BBB, DN 300, PN 25, XXXGaskets shall be identified either individually or on the packaging containing the gasket(s) with the number of this European Standard, i.e. EN 1514-2.8.2 Colour CodingSpiral wound gaskets shall be marked with colour codes that identify the metal of the winding strip and the filler material.A continuous colour around the centring ring edge shall identify the metal of the winding strip.Intermittent stripes around the edge of the centring ring shall identify the filler material. For gasket sizes below DN 40 there will be a minimum of two stripes spaced approximately 180 degrees apart. For gaskets of DN 40 and above there will be a minimum of four stripes spaced approximately 90 degrees apart.The colour codes shall conform to those listed in Table 2, for materials not given in Table 2, the colour code shall be agreed between the purchaser and the manufacturer.EN 1514-2:2005 (E)Table 2 — Colour coding and abbreviations for spiral-wound gasket materialsEN 1514-2:2005 (E)Annex A(informative)Information to be supplied by the purchaserBefore ordering a gasket it is recommended that the selection of the gasket type should be made in consulta-tion with the gasket supplier. The selection of gasket type should take account of the fluid, the operating con-ditions, the properties of the gasket materials, the type and surface finish of the flange facing and the flange bolt loading.The following information should be supplied by the purchaser when ordering gaskets:a) reference to this European Standard, i.e. EN 1514-2;b) gasket type (see 4.3);c) DN (see Table 1) and any requirement for a specific inner ring inside diameter;d) PN designation (see Table 1);e) whether an inner ring is required (see NOTES 1 and 2 to Clause 6);f) expected operating conditions for which the gasket will be used.EN 1514-2:2005 (E)Bibliography1092-1,Flanges and their joints — Circular flanges for pipes, valves, fittings and accessories, [1] ENPN designated — Part 1: Steel flanges.Flanges and their joints — Circular flanges for pipes, valves, fittings and accessories, [2] EN1092-2,[3] EN1092-3,1092-4,Flanges and their joints — Circular flanges for pipes, valves, fittings and accessories, [4] ENPN designated — Part 4: Aluminium alloy flanges.Flanges and their joints — Gasket parameters and test procedures relevant to the design [5] EN13555,rules for gasketed circular flange connections.BS EN 1514-2:2005BSI389 Chiswick High Road London W4 4ALBSI is the independent national body responsible for preparingBritish Standards. It presents the UK view on standards in Europe and at the international level. It is incorporated by Royal Charter.RevisionsBritish Standards are updated by amendment or revision. Users ofBritish Standards should make sure that they possess the latest amendments or editions.Tel:+44+44(0)2089967400.BSI offers members an individual updating service called PLUS which ensures that subscribers automatically receive the latest editions of standards.Buying standardsOrders for all BSI, international and foreign standards publications should be addressed to Customer Services. Tel:+44(0)2089969001.Fax:+44(0)2089967001. Email:orders@. Standards are also available from the BSI website at .In response to orders for international standards, it is BSI policy to supply the BSI implementation of those that have been published as British Standards,unless otherwise rmation on standardsBSI provides a wide range of information on national, European andinternational standards through its Library and its Technical Help to Exporters Service. Various BSI electronic information services are also available which give details on all its products and services. Contact the Information Centre.Tel:+44(0)2089967111. Fax:+44(0)2089967048. Email:info@.Subscribing members of BSI are kept up to date with standards developments and receive substantial discounts on the purchase price of standards. For details of these and other benefits contact Membership Administration. Tel:+44(0)2089967002. Fax:+44(0)2089967001. Email:membership@.Information regarding online access to British Standards via British Standards Online can be found at /bsonline.Further information about BSI is available on the BSI website at .CopyrightCopyright subsists in all BSI publications. BSI also holds the copyright, in the UK, of the publications of the international standardization bodies. Except as permitted under the Copyright, Designs and Patents Act 1988 no extract may be reproduced, stored in a retrieval system or transmitted in any form or by any means – electronic, photocopying, recording or otherwise – without prior written permission from BSI.This does not preclude the free use, in the course of implementing the standard, of necessary details such as symbols, and size, type or grade designations. If these details are to be used for any other purpose than implementation then the prior written permission of BSI must be obtained.Details and advice can be obtained from the Copyright & Licensing Manager. Tel:+44(0)2089967070. Fax:+44(0)2089967553. Email:copyright@.。
BS EN 15081-2007 工业阀门.部分回转阀门传动装置附件用装配工具箱

BS EN 15081-2007 工业阀门.部分回转阀门传动装置附件用装配工具箱actuator attachmentThe European Standard EN 15081:2007 has the status of a British StandardICS 23.060.99Industrial valves —Mounting kits for part-turn valve BS EN BRITISH STANDARD15081:2007BS EN 15081:2007This British Standard was published under the authority of the Standards Policy and Strategy Committee on 31 October 2007?? BSI 2007ISBN 978 0 580 54764 5Amendments issued since publicationAmd. No. DateCommentsCompliance with a British Standard cannot confer immunity from legal obligations.National forewordThis British Standard is the UK implementation of EN 15081:2007.The UK participation in its preparation was entrusted by Technical Committee PSE/7, Industrial valves, to Subcommittee PSE/7/1, Valves —Basic standards.A list of organizations represented on this committee can be obtained on request to its secretary.This publication does not purport to include all the necessary provisions of a contract. Users are responsible for its correct application.标准分享网 .bzfx免w费.c下o 载mEUROPEAN STANDARDEN 15081NORME EUROP ENNEEUROP??ISCHE NORMOctober 2007ICS 23.060.99 English VersionIndustrial valves - Mounting kits for part-turn valve actuatorattachmentRobinetterie industrielle - Kits de montage pourIndustriearmaturen - Montages tze f r Anschl sse vonraccordement des actionneurs fraction de tourSchwenkantrieben an ArmaturenThis European Standard was approved by CEN on 26 August 2007.CEN members are bound to comply with the CEN/CENELEC Internal Regulations which stipulate the conditions for giving this EuropeanStandard the status of a national standard without any alteration. Up-to-date lists and bibliographical references concerning such nationalstandards may be obtained on application to the CEN Management Centre or to any CEN member.This European Standard exists in three official versions (English, French, German). A version in any other language made by translationunder the responsibility of a CEN member into its own language and notified to the CEN Management Centre has the same status as theofficial versions.CEN members are t睷he national st眮andards bodie抵s of Austria, 晸Belgium, Bulg眮aria, Cyprus,捯 Czech Repub?lic, Denmark, Estonia, Finland,France, Germany, Greece, Hungary, Iceland, Ireland, Italy, Latvia, Lithuania, Luxembourg, Malta, Netherlands, Norway, Poland, Portugal,Romania, Slovakia, Slovenia, Spain, Sweden, Switzerland and United Kingdom.EUROPEAN COMMITTEE FOR STANDARDIZATIONCOMIT EUROP EN DE NORMALISATIONEUROP??ISCHES KOMITEE F R NORMUNGManagement Centre: rue de Stassart, 36 B-1050 Brussels' 2007 CENAll rights of exploitation in any form and by any means reservedRef. No. EN 15081:2007: Eworldwide for CEN national Members.EN 15081:2007 (E) Contents Page Foreword............................................................. ..................................................................... ............................3 1 Scope................................................................ ..................................................................... .................4 2 Normative references........................................................... .................................................................4 3 Terms and definitions.......................................................... .................................................................4 4 Design requirements......................................................... .. (5)4.1 General.............................................................. ..................................................................... .................5 4.2 Materials............................................................ ..................................................................... ................5 4.3 Design temperature.......................................................... .....................................................................6 4.4 Environmental corrosion protection........................................................... .........................................6 4.5 Mounting kit.................................................................. ..................................................................... .....6 4.6 Coupling............................................................. ..................................................................... ...............7 4.7 Designation.......................................................... ..................................................................... .............7 4.8 Position indicator............................................................ ..................................................................... ..8 4.9 Buried service.............................................................. ..................................................................... .....8 4.10 Safety requirement (mechanical/thermal protection).......................................................... ..............8 4.11 Orientation.......................................................... ..................................................................... ...............8 4.12 Additional anti-rotation means................................................................ .............................................8 4.13 Valve/actuator 睷package m眮aintenanc抵 e..............晸.................眮..................捯.................?................................8 5 Dimensions........................................................... ..................................................................... .............9 5.1 Bracket.............................................................. ..................................................................... .................9 5.2 Valve top flange............................................................... .. (1)0 5.3 Coupling............................................................. ..................................................................... .............10 5.4 Spools and adapter flanges.............................................................. ..................................................12 6 Marking.............................................................. ..................................................................... ..............12 6.1 General.............................................................. ..................................................................... ...............12 6.2 Mandatory information.......................................................... ..............................................................12 6.3Optional information.......................................................... .................................................................12 7 Documentation........................................................ ..................................................................... ........12 7.1 Language............................................................. ..................................................................... ............12 7.2 Product documentation........................................................ .. (12)Annex A (normative) Coupling axial clearance............................................................ ..................................13 Annex B (informative) Proposed stem details for ball and butterfly valves................................................15 B.1 General.............................................................. ..................................................................... ...............15 B.2 Proposed stem details for ball valves............................................................... ................................16 B.3 Proposed stem details for butterfly valves............................................................... (16)Bibliography.............................................................................................................................. ........................18 2 标准分享网 .bzfx免w费.c下o载mEN 15081:2007 (E) Foreword This document (EN 15081:2007) has been prepared by Technical Committee CEN/TC 69 “Industrial valves”, the secretariat of which is held by AFNOR. This European Standard shall be given the status of a national standard, either by publication of an identical text or by endorsement, at the latest by April 2008, and conflicting national standards shall be withdrawn at the latest by April 2008. Attention is drawn to the possibility that some of the elements of this document may be the subject of patent rights. CEN [and/or CENELEC] shall not be held responsible for identifying any or all such patent rights. According to the CEN/CENELEC Internal Regulations, the national standards organizations of the following countries are bound to implement this European Standard: Austria, Belgium, Bulgaria, Cyprus, Czech Republic, Denmark, Estonia, Finland, France, Germany, Greece, Hungary, Iceland, Ireland, Italy, Latvia, Lithuania, Luxembourg, Malta, Netherlands, Norway, Poland, Portugal, Romania, Slovakia, Slovenia, Spain, Sweden, Switzerland and the United Kingdom. 睷眮抵晸眮捯?3EN 15081:2007 (E) 1 Scope This European Standard provides requirements for metallic mounting kits for part-turn on-off valves and actuator attachments to enable safe and reliable operation. It includes all components transmitting torques from actuators to valves with a maximum flange torque up to 16 000 Nm (up to F30 flange type). It appliesto part-turn valves and actuators having attachment flanges and drive components as described in EN ISO 5211. It includes recommendations and methods for design and environmental corrosion protection. When reference is made to this European Standard, all the requirements apply, unless otherwise agreed between the purchaser and the manufacturer/supplier, prior to order. For the scope of this European Standard, the term “Valve” covers valve or shaft extension top-flange. 2 Normative references The following referenced documents are indispensable for the application of this document. For dated references, only the edition cited applies. For undated references, the latest edition of the referenced document (including any amendments) applies. EN 736-1:1995, Valves 睷— Termino 眮logy — Pa抵rt 1: Definit晸ion of types眮 of valves EN 736-2:1997, Valves —Terminology —Part 2: Definition of components of 捯valves ?EN 736-3:1999, Valves — Terminology — Part 3: Definition of terms EN ISO 5211:2001, Industrial valves — Part-turn valve actuator attachments (ISO 5211:2001) 3 Terms and definitions For the purposes of this document, the terms and definitions given in EN 736-1:1995, EN 736-2:1997 and EN 736-3:1999 and the following apply. 3.1 mounting kit kit comprising an intermediate support, coupling and bolting 3.2 intermediate support mechanical component (bracket, spool, adapter flange) that allows the attachment between a part-turn valve and actuator 3.3 coupling driven component that allows torque transmission from an actuator driving component to the valve shaft and which includes a position indicator 3.4 axial coupling clearance clearance to ensure that there is axial movement between the actuator and the valve stem to avoidthrust being applied between the driving and driven components 4 标准分享网 .bzfx免w费.c下o载mEN 15081:2007 (E) 3.5 part-turn actuator actuator that transmits torque to the valve for a rotation of one revolution or less and which does not have to be capable of withstanding thrust 3.6 valve top flange part of the valve which allows the attachment of actuating devices and ancillaries via an intermediate support 3.7 valve shaft part of the valve transmitting the drive torque to the obturator 3.8 part-turn actuator attachment attachment interface of the actuator which includes: ?? flange necessary to attach the part-turn actuator to the intermediate support; ?? driving component of the part-turn actuator necessary to attach it to the coupling or to the driven component of the valve, which may be an integral part or a removable component of the actuator 3.9 maximum actuator output torque maximum output torque of the actuator available at the maximum motive energy input 3.10 maximum allowable shaft torque (MAST) maximum torque睷 that can b眮e applied t抵o all the dr晸iven compo眮nents, with捯out damag?e and/or plastic deformation being sustained by any part 4 Design requirements 4.1 General Part-turn actuators shall be in accordance with EN ISO 5211. 4.2 Materials Unless otherwise agreed, mounting kit materials shall be: ?? for intermediate supports, of cast iron (CI), carbon steel (CS) or stainless steel (SS); ?? for coupling, see performance classes (Table 2); ?? for bolting (environmental corrosion categories according to Table 1): ?? categories C2 and C3: stainless steel or a suitably corrosion protected carbon steel; ??categories C4 and C5-I: stainless steel; ?? other categories: material to be specified by the purchaser. Special care shall be taken for material selection, in the event of environmental critical conditions. 5EN 15081:2007 (E) 4.3 Design temperature The mounting kit shall be designed for operation at an ambient temperature range between –20 °C and + 60 °C. 4.4 Environmental corrosion protection Mounting kits shall be protected against corrosion by suitable material selection and/or surface treatment. The manufacturer's technical documentation shall specify the choice of the materials and/or the type of the surface treatment. Surface treatment system for carbon or low-alloy steels (e.g. according to EN 10025) shall be chosen according to the classification categories given in Table 1. Test assessment and test procedures are the responsibility of the manufacturer. NOTE Table 1 may be used to define the corrosion category and help the mounting kit manufacturers to define the surface treatment for corrosion protection. Table 1 —Environmental corrosion categories Typical environments Corrosion category ExteriorInterior C2 (low) Atmospheres with low level of Unheated buildings where 睷眮pollu抵tion. Mostly晸 rural area眮s. co捯ndensation? may occur, e.g. depots, sport halls. C3 (medium) Urban and industrial Production rooms with high atmospheres, moderate sulphur humidity and some air pollution, dioxide pollution. Coastal areas e.g. food-processing plants, with low salinity. laundries, breweries. C4 (high) Industrial areas and coastal Chemical plants, swimming areas with moderate salinity. pools, coastal shipyards. C5-I (very high - industrial)Industrial areas with high Buildings or areas with almost humidity and aggressive permanent condensation and atmosphere. with high pollution. C5-M (very high – marine) Coastal and offshore areas with Buildings or areas with almost high salinity. permanent condensation and with high pollution. Immersed in water or buried in soil: Im 1 (Immersed in fresh water) River installations, hydro-electric power plants. Im 2 (Immersed in sea or brackish Harbour areas and offshore structures. water) Im 3 (buried in soil) Buried pipelines NOTE This table is taken from EN ISO 12944-2:1998. 4.5 Mounting kit 4.5.1 Stiffness The dimensions of the mounting kit given in this European Standard ensure that the maximum flange torque - given in Table 1 of EN ISO 5211 - can be transmitted safely. For non-vertically mounted actuators, the user may need to design an extra support. 6 标准分享网 .bzfx免w费.c下o载mEN 15081:2007 (E) When specified by the purchaser, the mounting kit shall also be designed for external loads (e.g. stepping load, earthquake, wind loading, additional plant induced dynamic loads). In this case, for instance, the thickness as given in Table 3 may be increased. 4.5.2 Intermediate support style The intermediate support provides two equal or different attachment interfaces (actuator and valve), as per EN ISO 5211. The most common type is a ;rectangular” bracket, as defined in 5.1. The ;rectangular; type is predominantly manufactured from a rectangular or square tube in compliance with EN 10219-2 or EN 10210-2. The ;rectangular; type can also be cast, fabricated or machined. Other commonly used types are the following: ?? “adapter flange”: generallymanufactured as one piece from casting, forging, plate or bar. It shall be provided with a suitable venting device; ?? ;spool type;: generally manufactured from two flanges that correspond to the mating faces of valve and actuator, connected together by a piece of tube. The assembly is welded together to form a spool piece. The ;spool; type can also be in one piece: cast, forged or machined. The spool shall be provided with a suitable venting device and/or with a suitable opening to visualise the coupling position. Other types of intermediate support may be used provided they meet the requirements of this European Standard. 4.6 Coupling The design of th睷e coupling 眮shall ensur抵e the maxi晸mum trans眮missible tor 捯que (as sp?ecified in EN ISO 5211), can be delivered to the valve shaft. The coupling performance class shall be specified by the purchaser in accordance with Table 2. The design of both coupling ends (driven/driving) shall avoid any contact between moving and fixed parts. Table 2 —Coupling performance classes Performance Examples of material types Coupling tolerances Minimum yield designation strength type driven end / driving end 2N/mm Class 1 Class 2 Austenitic stainless steels, nickel Group A 200 g9 / H10 g6 / H7 based alloys, carbon steel Duplex steels, martensitic Group B 450 g9 / H10 g6 / H7 stainless steels 4.7 Designation Mounting kits shall be designated as follows: a) mounting kit style: adaptor flange (AF), bracket (BR), spool (SP) or other (OT) followed by the intermediate support material as per 4.2 (CI, CS or SS); b) flange designations according to EN ISO 5211 (actuator flange type/valve flange type); c) coupling drive identification (first for the actuator and second for the valve): 7EN 15081:2007 (E) ?? coupling driven (actuator side) diagonal square “D” designation, as per EN ISO 5211, followed by dimension s as per Table 4; a?? coupling driving (valve side) designation either to Clause 6 of EN ISO 5211:2001 (additional capital letters with actual dimensions d or s) or to specified / agreed dimensions, followed by actual 7dimensions l and l in mm (see Figure A.1); 87d) environmental corrosion category as per Table 1; e) performance group/class as per Table 2. EXAMPLE EN 15081 - BR/CI - F07/F05 - D 14/H 11-11-24 - C3 - B1. NOTE The designation is not a marking requirement. 4.8 Position indicator The coupling design shall have a provision for a clear and permanently marked indicator to show whether the valve is open or closed: special attention, during the assembly, should be taken when installing square drive couplings. 4.9 Buried service When buried service is required, design details and corrosion protection shall be agreed between the purchaser and manufacturer/supplier. 4.10 Safety requirement (mechanical/thermal protection) The adapter flange or t睷he spool s眮hall have a抵 provision 晸 for venting眮 any leaka捯ge that m?ay occur through the stem seal of the valve or from the actuator hydraulic/pneumatic supply. This may be obtained either by including a suitable vent or a pressure relief safety valve. 4.11 Orientation The mounting kit shall be designed to be installed in any mounting position. 4.12 Additional anti-rotation means When needed to resist torsion, vibration and shock loads, suitable means (e.g. dowel pins) may be used. 4.13 Valve/actuator package maintenance The maintenance requirements of any valve/actuator package shall alwaysbe considered when designing and/or ordering the mounting kit. Special consideration shall be given to the following. ?? Access to the fixings that connect the valve and actuator to the mounting kit: the mounting kit should have sufficient clearance to allow the installation and removal of fasteners using standard commercial tooling. ?? Access to external valve gland adjustment mechanisms: some part-turn valves require periodic adjustment to prevent fugitive emissions. ?? Access to valve lubrication facility: some plug valves require periodic lubrication in order to maintain a consistent torque requirement and prevent seizure. ?? Actuator and accessories arrangement in relation to valve/pipeline flanges: the kit should be of sufficient height to allow suitable access for assembly, valve adjustment, and valve/pipeline insulation/lagging. 8 标准分享网 .bzfx免w费.c下o载mEN 15081:2007 (E) 5 Dimensions 5.1 Bracket The bracket consists of two mounting faces which can be either identical or different. In the latter case, the largest flange type dictates the height (H), width (W) and thickness (T), as per Figure 1 and Table 3. When specified, the valve side of the bracket shall be profiled to clear the packing gland. Figure 1 — Bracket dimensions 9EN 15081:2007 (E) Table 3 —Bracket dimensions (in mm) Flange Profile Tolerance type Height WidthLength Thickness?? d ?? d ?? d 234H Tolerance W L ToleranceT x y +0,15F 03 50 50 - 1 80 40 40 + 1 4 25 36 5,5 0,1 0,1 +0,05+0,15F 04 50 50 - 1 80 45 45 + 1 4 30 42 5,5 0,1 0,1 +0,05+0,15F 0560 60 -35 1 100 50 50 + 1 5 50 6,5 0,1 0,1 +0,05+0,15F 07 60 60 - 1 100 70 70 + 2 5 55 70 9 0,1 0,1 +0,05+0,20F 10 80 80 - 1 120 95 95 + 2 5 70 102 11 0,2 0,2 +0,05+0,20F 12 80 80 - 1 160 115 115 + 2 6 85125 13 0,2 0,2 +0,05+0,20F 14 80 80 - 1 160 135 135 + 2 6 100 140 17 0,2 0,2 +0,05+0,20F 16 100 100 - 2 200 160 160 + 2 6 130 165 21 0,4 0,4 +0,05+0,25F 25 200 200 - 2 400 270 270 + 3 10 200 254 17 0,4 0,4 +0,05+0,25F 30 200 200 -230 2 400 320 320 + 5 10 298 21 0,4 0,4 +0,055.2 Valve top flange The valve top flange dimensions shall be in accordance with EN ISO 5211. Additionally - for centering purposes - the valve top flange shall include an integral or additional spigot with a diameter and height corresponding to those dimensions given in EN ISO 5211. The design of the top flange may include either tapped or through holes and proper care shall be paid to ensure adequate engagement. 5.3 Coupling The driven end of the coupling shall be the diagonal square type as per EN ISO 5211 (designation ;D;).10 标准分享网 .bzfx免w费.c下o载mEN 15081:2007 (E) Key 1 Position indicator NOTE The dimensions s, D and l of the flat-head drive coupling shown are given for example only. Other drive types 8may be used. Figure 2 — Coupling dimensions 11EN 15081:2007 (E) Table 4 — Dimensions (in mm) of the driven part of the coupling (actuator side) Flange F03 F04 F05 F07 F10 F12 F14 F16 F25 F30 type s 9 11 14 17 22 27 36 46 55 75 aD 12 14 18 22 28 36 48 60 72 98 l 10 12 16 19 24 29 38 48 57 77 5NOTE The relevant coupling tolerances are as per Table 2. 5.4 Spools and adapter flanges The height of the spoolshall have the same dimension as the rectangular bracket. The height of the adapter flange shall be specified by the valve or actuator manufacturer. 6 Marking 6.1 General Each mounting kit shall bear the permanent indications as stated in 6.2 and 6.3. 6.2 Mandatory information ?? Bracket: flange sizes to EN ISO 5211 (e.g. F05/F05, F07/F05, etc.). ?? Coupling: for the driven end, “D” drive dimension to EN ISO 5211 followed by the driving end dimensions and performance group/class (Table 2) identifications (e.g. D14/H11-B1). 6.3 Optional information ?? Manufacturer/supplier’s identification (name and/or logo and/or trade mark). ?? Reference to this European Standard. 7 Documentation 7.1 Language The language of the relevant documentation shall be agreed between the manufacturer/supplier and the purchaser. 7.2 Product documentation The following documentation shall be provided by the manufacturer/supplier: ?? mounting kit installation, commissioning instructions and weight indication; ?? storage instructions; ?? drawing with itemized components and recommended spare parts list. 12 标准分享网 .bzfx免w费.c下o载mEN 15081:2007 (E) Annex A (normative) Coupling axial clearance Axial clearance, between the coupling and the valve and actuator, is required to permit secure assembly without end loading of the valve stem or actuator drive. The critical axial dimensions of a typical assembly are shown in Figure A.1. The coupling shall provide appropriate drive engagement, for both the driven and driving ends, to ensure that it transmits the rated torque. These considerations are reflected in dimensions l and l. Adequateaxial clearance may be achieved 58by the dimension C in the two positions indicated in Figure A.1. cThe critical axial dimensions of a typical coupling are shown in Figure 2 and may be established, in terms of the dimensions shown in Figure A.1, as follows: L = H + h – l + l – C(A.1) B478c T = L + l(A.2) CB5 The values of the minimum design coupling axial clearance, based on nominal dimensions, are given in Table A.1. Dimension l shall be the maximum value under all foreseeable and/or critical working conditions. Valve 7conditions may change due to valve gland or seat wear and consideration should be given to any resultant changes in coupling axial clearance. It may also be necessary to provide clearance between the coupling and bracket/spool mounting flanges or any protrusions such as bolt heads, centering spigots or valve gland components. Care should be taken to ensure that adequate drive engagements are provided when the coupling travels to either extreme of the axial clearance. Table A.1 — Minimum coupling axial clearance Flange type in accordance with Minimum coupling axial clearance EN ISO 5211 C cmm F 03 to F 07 1 F 10 to F 12 1,5 F 14 to F 16 2 F 25 to F 30 3 13EN 15081:2007 (E) Key 1 Actuator 2 Coupling (adaptor) 3 Bracket 4 Valve 5 Mounting bolt 6 Spigot (integral or additional) H Nominal rectangular bracket or spool height (see Figure 1 and Table 3) h Actuator drive clearance (as per EN ISO 5211) 4l Actuator drive depth 5l Shaft height from valve top flange 7l Coupling driving end engagement length 8C Minimum coupling clearance (see Table A.1) cFigure A.1 — Mounting kitassembly 14 标准分享网 .bzfx免w费.c下o载mEN 15081:2007 (E) Annex B (informative) Proposed stem details for ball and butterfly valves B.1 General This annex has been developed to propose to the European Valve Industry the gradual implementation of new standard dimensions for the driven end of ball and butterfly valve shafts, with the ultimate aim of product optimisation and increased interchangeability levels. The proposed heights l are based on EN ISO 5211, l dimensions and clearances are in line with values 75indicated in Table A.1. Key 1 Valve 2 Spigot (integral or additional) Figure B.1 —Example of flat head shaft 15EN 15081:2007 (E) B.2 Proposed stem details for ball valves Table B.1 —Drive by flat head d s Valve top flange l (min) l827 according to Nominal Tolerance EN ISO 5211 10 7 F03, F04, F05 8 18 0 / to 1,0 12 8 F03, F04, F05 9 22 0 / to 1,0 14 9,5 F04, F05, F07 10,5 27 0 / to 1,0 18 12 F05, F07, F10 13 33 0 / to 1,0 22 15 F07, F10, F12 16 34 0 / to 1,0 28 19 F10, F12, F14 21 45 0 / to 2,0 36 24 F12, F14, F16 26 56 0 / to 2,0 a48 32 F14, F16, F25 34 69 0 / to 2,0 a Larger stems are normally of key drive design and therefore not considered applicable in this proposal. B.3 Proposed stem details for butterfly valves Table B.2 —Drive by flat head d s Valve top flange l(min) l 82 7according to Nominal Tolerance EN ISO 5211 12 9 F03, F04, F05 14 15 0 / to 1,0 14 11 F04, F05, F07 17 18 0 / to 1,0 18 14 F05, F07, F10 21 24 0 / to 1,0 22 17 F07, F10, F12 26 29 0 / to 1,0 25 19 F10, F12 29 32,5 0 / to 1,0 28 22 F10, F12, F14 3337,5 0 / to 2,0 36 27 F12, F14, F16 41 46,5 0 / to 2,0 48 36 F14, F16, F25 54 62 0 / to 2,0 60 46 F16, F25, F30 69 80 0 / to 2,0 72 55 F25, F30 83 96 0 / to 2,0 98 75 F30 113 132 0 / to 2,0 16 标准分享网 .bzfx 免w费.c下o载mEN 15081:2007 (E) Table B.3 —Drive by square head d s Valve top flange l 87according to Nominal Tolerance EN ISO 5211 12 9 F03, F04, F05 9 0 / to 1,0 14 11 F04, F05, F07 11 0 / to 1,0 18 14 F05, F07, F10 15 0 / to 1,0 22 17 F07, F10, F12 18 0 / to 1,0 25 19 F10, F12 20 0 / to 1,0 28 22 F10, F12, F14 22,5 0 / to 2,0 36 27 F12, F14, F16 27,5 0 / to 2,0 48 36 F14, F16, F25 36 0 / to 2,0 60 46 F16, F25, F30 46 0 / to 2,0 72 55 F25, F30 54 0 / to 2,0 98 75 F30 74 0 / to 2,0 Table B.4 —Drive by key (single)d Valve top flange l 77according to Nominal Tolerance EN ISO 5211 12 F0529 0 / to 1,0 14 F05, F07 29 0 / to 1,0 18 F05, F07, F10 29 0 / to 1,0 22 F05, F07, F10, F12 34 0 / to 1,0 28 F07, F10, F12, F14 43,5 0 / to 2,0 36 F10, F12, F14 53,5 0 / to 2,0 48 F12, F14, F16, F25 63 0 / to 2,0 60 F14, F16, F25, F30 78 0 / to 2,0 72 F16, F25, F30 107 0 / to 2,0 98 F25, F30 127 0 / to 2,0 17EN 15081:2007 (E) Bibliography [1] EN ISO 3231, Paints and varnishes — Determination of resistance to humid atmospheres containing sulphur dioxide (ISO 3231:1993) [2] EN ISO 4628-2, Paints and varnishes —Evaluation of degradation of coatings —Designation of quantity and size of defects, and of intensity of uniform changes in appearance — Part 2: Assessment of degree of blistering (ISO 4628-2:2003) [3] EN ISO 4628-3,。
朗基拉风扇产品说明书

Removing Old Cone or VaneSee Figure 2 for identification of all items referenced.For Fan Arrangements 1, 4, 9 and 10:1. Shut off fan and lock out electrical power.2. Remove inlet screens if applicable.3a. For Removing Old Inlet Cone — Loosen fasteners atperiphery of inlet cone and remove old cone.3b. For Pre-1981 Style Inlet Vane Removal — Removehardware from old vane which attaches it to the housing. Remove control link and old inlet vane.3c. For Post-1981 Style Inlet Vane Removal — Removenut (item 14) and pull connecting arm out of the way. Loosen fasteners which hold inlet vane to the fan housing, and remove old inlet vane.For Arrangements 3 and 7:1. Shut off fan and lock out electric power.2. Remove inlet screens if applicable. Release belttension.3. Clean and remove rust from sections of fan shaftwhich extend through fan inlet bearings. File smooth any burrs. Remove bearing bolts and raise shaft enough to take weight off bearing.4. Working through fan outlet or through access door,block under periphery of fan wheel so that fan housing supports the fan wheel.5a. For Fan With Setscrew Locking Collars — Loosensetscrews in fan inlet bearing. Using wedges or pry bars, slide bearing off end of shaft. If it is necessary to force bearing, use a brass rod to drive against inner race of bearing only.5b. For Fans With Split Type Bearing — Remove bearingcap, bearing housing and bearing insert off end of shaft. If the bearing insert must be removed by inexperienced personnel, it is recommended that the bearing manufacturer be contacted to provide instructions for dismounting.6a. For New Installation — Loosen fasteners which holdinlet cone and bearing support frame to the fan housing side. Remove old inlet cone and bearing support frame.6b. For Pre-1981 Style Replacement — Removehardware from old vane which attaches it to the housing side. Remove control arm (or drive link). Loosen fasteners which hold the inlet cone and bearing support frame to the housing side, then remove old inlet vane and bearing support frame.6c. For Post-1981 Style Replacement — Remove nut(item 14) and pull connecting arm out of the way. Loosen fasteners which hold the inlet vane and bearing support frame to the housing side, and remove the inlet vane and bearing support frame.Assembling Nested Inlet VaneFor Fan Arrangements 1, 4, 9 & 10:1. Using Figure 2 as a guide, assemble items 5through 15 to the inlet vane. Threaded linkage rod (item 6) may have to be cut to required length.2. Center inlet vane in location of old vane or cone, and rotate until inlet vane control ring is approximately in the same position as shown in Figure3. If old control linkage is being reused, locate control ring clip so that connecting link can be reattached. Be sure that when vane is partially closed the entering air will be spun in the direction of wheel rotation.3. For installation of new quadrant, using the dimensions in Figure 4, position quadrant (item 2 or 2A) to the housing side. Drill a hole in the fan housing side to match outside diameter of control rod housing (item 4).4. Weld quadrant (item 2 or 2A) to housing frame (or housing side).5. Assemble the remaining parts of control system according to Figure 2. Adjust position of connecting links as required to allow the vane to open and close smoothly.6. Weld threaded linkage housing to hex nuts (item 12). Spot weld the control rod to vane handle and controllinkage bar.©1998 – 2018 Twin City Fan Companies, Ltd.Figure 1. BC, BAF, BCS Fan With Nested Inlet2 Twin City Engineering Supplement ES-394For Arrangements 3 & 7:1. Using Figure 2 as a guide, assemble items 5 through 15 to the inlet vane. Threaded linkage rod (item 6) may have to be cut to required length.2. Center inlet vane in location of old vane or cone, and rotate until inlet vane control ring is approximately in the same position as shown in Figure3. If old control linkage is being reused, locate control ring clip so that connecting link can be reattached.3. For installation of new quadrant, using the dimensions in Figure 4, position quadrant (item 2 or 2A) to the housing side. Drill a hole in the fan housing side to match outside diameter of control rod housing (item 4).4. Weld quadrant (item 2 or 2A) to housing frame (or housing side).5. Reassemble bearing support frame and bolt it to the fan housing as shown in Figure 5.6. Reassemble bearing and tighten bearing fasteners7. Remove blocking under wheel and check to be sure wheel turns freely. Adjust bearing position or inlet vane position as required.8. Assemble the remaining parts of control system according to Figure 2. Adjust position of connecting links as required to allow the vane to open and close smoothly.9. Weld threaded linkage housing to hex nuts (item 12). Spot weld the control rod to vane handle and control linkage bar.Figure 2. Nested Inlet Vane Control System for SWSI BC, BAF, BCS FansNOTES:Twin City Engineering Supplement ES-394 3Figure 3. Control Ring PositionFigure 4. Nested Inlet Vane Handle Location For Non-rotatable FansNOTES:1. For POS. R: CW fan handledown is open. CCW fan handledown is closed. For POS L:CW fan handle down is closed.CCW fan handle down is open.2. Handle location oninlet side of fan.3. Reference ofAS-13460.Figure 5. Nested Inlet Vane Handle Location For Rotatable FansFAN SIZE 165 182 200 222 245 270 300 330 365 A 11.25 12.25 13.50 14.62 15.88 17.50 19.06 20.44 22.88B1.691.691.692.192.192.192.692.692.69TWIN CITY FAN & BLOWER | 5959 Trenton Lane N | Minneapolis, MN 55442 | Phone: 763-551-7600 | Fax: 763-551-7601。
Infinity B G240 - 快速启动指南说明书
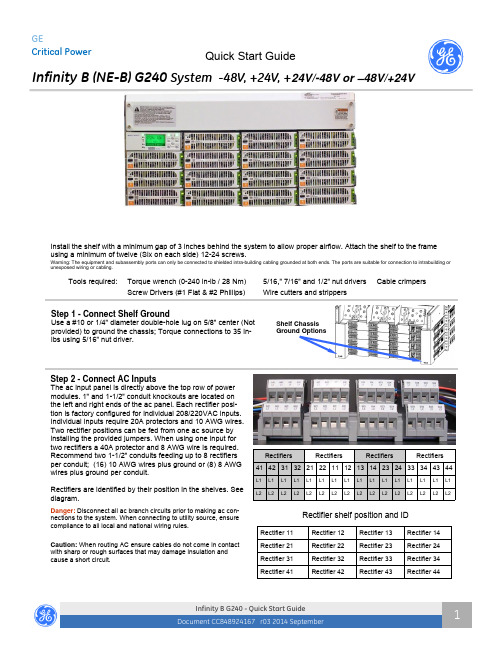
Infinity B G240 - Quick Start GuideDocument CC848924167 r03 2014 September1Infinity B (NE-B) G240 System -48V, +24V, +24V/-48V or –48V/+24VGECritical PowerQuick Start GuideStep 2 - Connect AC InputsThe ac input panel is directly above the top row of power modules. 1” and 1-1/2” conduit knockouts are located on the left and right ends of the ac panel. Each rectifier posi-tion is factory configured for individual 208/220VAC inputs. Individual inputs require 20A protectors and 10 AWG wires. Two rectifier positions can be fed from one ac source by installing the provided jumpers. When using one input for two rectifiers a 40A protector and 8 AWG wire is required. Recommend two 1-1/2” conduits feeding up to 8 rectifiers per conduit; (16) 10 AWG wires plus ground or (8) 8 AWG wires plus ground per conduit.Rectifiers are identified by their position in the shelves. See diagram.Danger: Disconnect all ac branch circuits prior to making ac con-nections to the system. When connecting to utility source, ensure compliance to all local and national wiring rules.Caution: When routing AC ensure cables do not come in contact with sharp or rough surfaces that may damage insulation and cause a short circuit.Tools required: Torque wrench (0-240 in-lb / 28 Nm) 5/16,” 7/16” and 1/2” nut driversScrew Drivers (#1 Flat & #2 Phillips) Wire cutters and strippers Cable crimpersInstall the shelf with a minimum gap of 3 inches behind the system to allow proper airflow. Attach the shelf to the frame using a minimum of twelve (Six on each side) 12-24 screws.Warning: The equipment and subassembly ports can only be connected to shielded intra-building cabling grounded at both ends. The ports are suitable for connection to intrabuilding orunexposed wiring or cabling.Step 1 - Connect Shelf GroundUse a #10 or 1/4” diameter double-hole lug on 5/8” center (Not provided) to ground the chassis; Torque connections to 35 in-lbs using 5/16” nut driver.Shelf Chassis Ground OptionsRectifier 11Rectifier 12 Rectifier 13 Rectifier 14 Rectifier 21 Rectifier 22 Rectifier 23 Rectifier 24 Rectifier 31 Rectifier 32 Rectifier 33 Rectifier 34 Rectifier 41Rectifier 42Rectifier 43Rectifier 44Rectifiers Rectifiers Rectifiers 41 42 31 32 21 22 11 12 13 14 23 24 33 34 43 44L1 L1 L1 L1 L1 L1 L1 L1 L1 L1 L1 L1 L1 L1 L1 L1 L2L2L2L2 L2 L2 L2 L2 L2L2L2L2 L2 L2 L2 L2RectifiersRectifier shelf position and IDStep 4- Controller ConnectionsAttach the 8 AWG AC input wires to the terminal blocks and torque Two controller options are available; CC109128402 NE843A Pulsar slot controller or CC109132024 Millennium II Rack mounted controller. Controller product manuals are available at The Pulsar slot controller mounts in the left most position of the top shelf (as shown in the diagram on page 1). All controller con-nections are accessible with the controller installed. Refer to the table below for detailed alarm connection information. Before in-stalling the controller configure the bus reference voltage and alarm output jumpers;1. Set Jumper 11 to (+) for +24Vdc systems or (-) for -48V/-24V (Factory Default) systems.2. Set jumpers 1 thru 10 for the ten alarm relays as “Close” or “Open” on alarm; Factory default setting is “Close” on alarm. TheAlarm relay jumpers are located under the sliding cover on top of the controller, see figure below.Note: The optional Millennium II rack mount controller can be used instead of the Pulsar when additional controller features are required. See the Millennium II Product Manual at for more information. Bus reference V and Alarm Relay Jumpers under coverClose on Alarm Open on Alarm-48 V/-24V+2411 10 9 8 7 6 5 4 3 2 1 J3 Auxiliary InputsJ4 Alarm OutputsJ1 Optional system Interface. See table below.J2 Thermal probes. See back page.J5 LANSystem reference voltage and alarm output jumpers.Infinity B G240 - Quick Start Guide Document CC848924167 r03 2014 September 1 3Step # 6 - Rectifier, Converter InstallationSlide the rectifier/converter into the slot approximately 3/4 of the way. Open the faceplate by sliding the face-plate latch to the left until the faceplate releases and swings outward.Slide the unit into the slot until it engag-es with the back of the shelf. Swing thefaceplate closed to seat the rectifier/converter. Verify the faceplate is latched.Step # 7 - Initial Start UpVerify all AC, DC, Alarm and system interface connections are complete and secure. If rectifiers have not yet been in-stalled, install rectifiers now as described previously. Once this is complete turn on the AC input breakers. As each rectifier is installed, the controller automatically identifies the new rectifier and begins communication. If there are no alarms, make adjustments to the default settings on the controller as required for this installation. Using the front panel menu to configure settings and functions is intuitive. Refer to the menu map on the next page.The DC can be configured for -48V, +24V, -48V/+24V or +24V/-48V depending on the power modules; -48V rectifiers,+24V Rectifiers or combination of rectifiers and converters. The outputs are located on the rear of the shelf. The shelf is designed to distribute bulk power only; there are no DC output protectors in the shelf. Lug landings accommodate 3/8” di-ameter lugs on 1” centers spaced 1.75“ apart. Three 750 MCM Flex lugs can be connected per bus. Bus extensions are provided to land four additional cables back to back.Step # 5 - Connect DC OutputsThe Millennium II rack mountedcontroller interface serial cable con-nects to any open RJ45. Power andsense leads connect to the 1/4”fastons on bus bars.+24V -48V ReturnsStep # 4- Controller Connections (Continued)Auxiliary InputsJ3 (10 pin connector) provides access to the auxiliary inputs. Default alarm descriptions are shown in the table below and may be changed as needed using web pages or Easyview2.Bus extensions(3 provided)Infinity B G240 - Quick Start GuideDocument CC848924167 r03 2014 September2 GE● 601 Shiloh Rd.● Plano, TX 75074 ● 1- 888 546-3243 4Information: Battery Monitoring (Optional)Battery Monitoring is accomplished with a “Daisy Chained” series of QS873 probes connected to J2. The Probes are used to monitor battery temperature and mid-string voltage (ES771 required to monitor voltage). Bolt the Probe under the “–“ terminal connector hardware; NOT under the connecting lug.58.50 58.50 57.00 57.00 56.00 56.00 52.08 54.40 50.00 51.00 46.00 46.00 44.00 44.00Front Display Menu MapFront DisplayInformation: Controller Basic OperationViewing and changing system parameters from the factory defaults can be accomplished in several ways; A) front display, B) Craft Port on front of controller using a laptop with EasyView2 or HyperTerminal. EasyView2 (GUI) software can be downloaded from , C) J5 LAN port in Static, Client, or Server mode. Static and Client modes are for accessing web pages through a network. Server mode allows local access to the controller web pages directly from a laptop connected to J5 LAN port; Menu>Configure>Communication Ports>Network Settings>DHCP (Server). Server mode default IP address is 192.168.2.1. With the controller set to Server type the default IP address in the web browser address field. Server mode is a temporary setting, once configuration is complete reset the controller to Client or Static before connecting to the network. Static is the factory default setting and the typical setting for most networks. Warning: Do not connect J5 LAN port to a network when set to Server.Controller Alarm Status: The display changes colors; Green = Normal, Amber = Minor Alarm, Red = Critical/Major Alarm Some alarms may occur during initial installation ; example: thermal probe fail or Major/Minor communication fail .To clear these alarms from the Controller Display: follow the menu path; Menu > Control/Operation > Clear Events or Uninstall Equipment .Using web pages or EasyView2; Select the Maintenance ta b > clear latched events and clear missing devices.Verify Basic Installation Settings: To verify Date, Time, Battery Type, number of strings and float voltage for this application using the Controller Display: follow the menu path; Menu > Configuration >System Settings and Menu > Configuration > Batteries . Using web pages or EasyView2; Select the Installation Tab to set the Date, Time. Site ID and Site Description. Select the Settings Tab >Battery Management to verify Battery Type and set number of battery strings installed.NavigationCraft Port Menu LEDsLCD Temperature and voltage monitoringTemperature monitoring。
GUIDE ASSEMBLY

专利名称:GUIDE ASSEMBLY发明人:Knoop, Dietmar申请号:EP15170690.0申请日:20150604公开号:EP3101301A1公开日:20161207专利内容由知识产权出版社提供专利附图:摘要:The present invention relates to a guide assembly for a disc brake. To counter rotational torque, the guide assembly comprises a guide pin comprising a sleeve with a sleeve portion, and a receiving portion of a brake carrier to receive the sleeve portion;wherein the sleeve portion and receiving portion have corresponding non-circular cross-sectional profiles such that, when the sleeve portion is received and aligned in the receiving portion, rotation of the sleeve relative to the brake carrier is thereby at least restricted. By restricting the rotation of the sleeve, the transmission of rotation from the sleeve to a fastener, and consequential loosening of the fastener, is restricted. The present invention further relates to a disc brake comprising a brake carrier, a caliper and at least one guide assembly. If the receiving portion is a recess disposed in the brake carrier, a method of manufacturing the recess in the brake carrier comprises cutting the recess in the brake carrier with a circular inner edge region and a non-circular inner edge region.申请人:Meritor Heavy Vehicle Braking Systems (UK) Limited地址:Grange Road Cwmbran, Gwent NP44 3XU GB国籍:GB代理机构:Hardy, Rosemary更多信息请下载全文后查看。
Linear Guides说明书

· L inear guides utilize steel balls rolling on ground raceways, and theballs are recirculated using plastic return caps.· End seals prevent foreign substances from intruding into the blocks.· M iniature Type has two rows of contacting steel balls in a 4-pointraceway contact design.· M edium/Heavy Load Types have four rows of contacting steel balls ina 2-point raceway contact design.· L oad ratings are the same for all four directions (radial, reverse-radial,and lateral directions). Can be used in any orientation.· M ISUMI-manufactured Blocks and rails guarantee their own radialclearances (preload) and accuracies as sets of blocks and rails. Besure to use the blocks and rails in sets.· C autionsBalls do not fall out of MISUMI linear guides when removed fromrails as the blocks are equipped with ball-retainers. However,the balls may fall out by rapidly removing blocks from the rail orinserting the rail into the block at a angle. Remove and install theblocks with caution.Q Linear Guide - Structure and Features[Pair Variation of Height H]Difference between the min. / max. values of Height (H) Dimension for anumber of blocks combined on one rail.[Pair Variation of Width W2]Difference between the min. / max. values of Width (W) Dimension for anumber of blocks combined on one rail.[Running Parallelism]Measured while the rail is bolted firmly to a standard reference surface base.A relative variation of block's top surface C against the rail's bottom surface A,and a relative variation of block's datum surface C against the rail's datum· C learance and preload of MISUMI Linear Guides are controlled with minute ball size adjustments.· Increased rigidity and reduced elastic deformation will result by preloading (negative clearance).· Generally, selecting some preloads would cause favorable effects on accuracy and life of Linear Guides.· M ISUMI-manufactured Blocks and rails guarantee their own radial clearances (preload) and accuracies assets of blocks and rails. Be sure to use the blocks and rails in sets.Q Allowable Load· B asic Dynamic Load Rating (C)B asic dynamic load rating is defined as: a load applied in a constant direction and ran underequal condition on a group of linear guide specimen where 90% of specimen will reach50x103m without experiencing any damages due to rolling fatigues.· Basic Static Load Rating (Co)B asic static load rating is defined as: a load applied on non-moving linear guides where a sumof rolling element plastic deformation amount and rolling surface plastic deformation amountbecomes equal to 0.0001 times that of the diameter of the rolling element (balls).· Allowable Static Moment (M A, M B, M C)A llowable static moment is a critical static moment load defined by permanent deformationvalue similar to basic static load rating Co.· Static Safety Factor (f S)B asic Static Load Rating Co, in the static state or in low speed, is divided by Static SafetyFactor f S in Table 2 depending on operating conditions.f S: Statistic Safety Factor Co: Basic Static Load Rating (N)M A, M B, M C: Static Allowable Moment (N·m) Q Precision· Ragainst Plane A· Ragainst Plane BQ Friction Force (Required Thrust Force)L inear Guide friction force (required thrust) varies depending onload, speed and lubricant property. Especially when moment load isapplied, Preload Type friction force increases.Although seal resistance varies according to seal lip press-fitallowance and lubrication conditions, it is not proportionate to loadand keeps a constant value.Friction force is obtained by the following formula.F : Friction (N)µ : Dynamic Friction CoefficientW : Applied Loadf : Seal Resistance (2N~5N)Pitch Direction Yaw Direction Roll DirectionTable-2 Static Safety Factor (f S Lower Limit)-4691-4701。
assembly line造句

assembly line造句1、He works on the assembly line at the local car factory他在本地汽车制造厂装配线上工作.2、I improved our assembly line of the TV.我改进了电视的装配线。
3、The assembly line is regarded as a symbol of industry流水线被认为是工业的象征。
4、The production is greatly increased due to a new assembly line installed由于安装了新装配线, 生产量大大提高。
5、My job at the assembly line of the car factory is rather monotonous.我在汽车工厂装配线上的工作颇为单调乏味。
6、The assembly line makes it possible to build more cars at a faster rate.流水线生产使得汽车生产效率大大提高。
7、I work in an assembly line in a car factory.我在一家汽车厂的流水线上工作。
8、With such a system, workers on the assembly line learn nothing and the faults persist.采用这种系统,生产线上的工人什么也学不到,而故障依然存在。
9、An assembly line system is an efficient way to manufacture cars.产品装配线系统是一种有效的生产汽车的方法。
10、The assembly line makes it possible to build more cars at a faster rate流水线生产使得汽车生产效率大大提高。
欧洲电器集成电路安装指南说明书

Assembly Manual / Guide d’assemblage /Manual de ensamblaje /조립설명서 /Montageanleitung2Use the hex keys in the box. / Utilisez les clés hexagonales fournies dans la boite. / Utilice las llaves hexagonales en la caja. /. / Verwenden Sie die Sechskantschlüssel in der Box.Please use a Phillips screwdriver. / Utilisez un tournevis de type Phillips / Por favor, use un destornillador Phillips. / . / Bitte verwenden Sie einen Kreuzschraubenzieher.Y ou may need to use a drill for this step. / Vous pouvez avoir besoin d’utiliser une perceuse pour cette étape. / Puede que tenga que utilizar un taladro para este paso. /. / Für diesen Schritt können Sie einenBohrer verwenden.Wearing protective gloves is recommended. / Le port de gants de protection est recommandé / El uso de guantes de protección se recomienda. / . / Das Tragen von Schutzhandschuhen wird empfohlen.Do not tighten screws all the way for now. / Ne pas visser fermement pour l’instant. /. / Bitte dieSchrauben zum jetzigen Zeitpunkt noch nicht fest anziehen.Sold separately. / Vendus séparément. / vendido en las opciones. // Optional erhältlichOptional step / Étape optionnelle / Paso opcional / / Optionaler SchrittSuggested assembly method / Méthode d’installation suggérée / Método sugerido de montaje / / Vorgeschlagene MontagemethodeTwo or more people are required at this stage. / Deux personnes ou plus sont nécessaires à cette étape./ Dos o más personas se requieren en esta etapa. / . / Für diesen Bauschritt sind 2 oder mehr Personen erforderlich.345X41678910197 c m / 77.6 i n /p oX41X41© Sojag inc.。
谈谈你对装配线的看法英语作文

谈谈你对装配线的看法英语作文Assembly lines have revolutionized the way we produce goods, making mass production not only feasible but efficient. They are the backbone of modern manufacturing, ensuring a steady flow of products that meet consumer demand.The concept of an assembly line is simple yet profound, breaking down complex tasks into smaller, manageable steps. This specialization allows workers to focus on their specific roles, which in turn increases productivity and reduces the likelihood of errors.However, the monotony of repetitive tasks on an assembly line can be a double-edged sword. While it boosts efficiency, it may also lead to worker fatigue and a lack of job satisfaction. It's crucial for industries to find a balance, ensuring that the benefits of an assembly line do not come at the expense of worker well-being.Moreover, the assembly line has paved the way for automation and technological advancements. As machines take over more tasks, we see a shift towards smarter, moreflexible production lines that can adapt to changing market needs.Despite its drawbacks, the assembly line remains an essential component of our industrial society. It's a testament to human ingenuity and our ability to streamlineprocesses for the greater good.In conclusion, the assembly line is a powerful tool in the world of manufacturing. While it requires careful management to maintain a positive work environment, its impact on efficiency and innovation cannot be overstated. As we move forward, the evolution of the assembly line will continue to shape the future of production.。
有关装配线相关的英语作文

有关装配线相关的英语作文1. Assembling lines are like puzzles, with each piece fitting perfectly into place. It's a satisfying feeling to see a product come together right before your eyes.2. The sound of machines whirring and tools clinking fills the air, creating a symphony of productivity in the factory.3. Precision is key in the assembly process, as even the smallest mistake can lead to a faulty product.Attention to detail is crucial.4. Workers on the assembly line move with precision and speed, each knowing their role in the larger process. It's a well-oiled machine, with everyone working together towards a common goal.5. The smell of metal and oil lingers in the air, a reminder of the hard work and dedication that goes intoeach product that rolls off the assembly line.6. Each completed product is a testament to the teamwork and collaboration that takes place on the assembly line. It's a collective effort that results in a finished product that is greater than the sum of its parts.7. As the day comes to an end, the assembly line slows down and eventually comes to a stop. The workers can take pride in a job well done, knowing that they have contributed to the creation of something great.。
EN 1514-2-2005

BS EN Array1514-2:2005BS EN 1514-2:2005This British Standard was published under the authority of the Standards Policy and Strategy Committee on 28 June 2005© BSI 28June 2005ISBN 0 580 46100 9National forewordThis British Standard is the official English language version ofEN 1514-2:2005. It supersedes BS EN 1514-2:1997 which is withdrawn.The UK participation in its preparation was entrusted to Technical Committee PSE/2, Jointing Materials and Compounds, which has the responsibility to:A list of organizations represented on this committee can be obtained on request to its secretary.Cross-referencesThe British Standards which implement international or Europeanpublications referred to in this document may be found in the BSI Catalogue under the section entitled “International Standards Correspondence Index”, or by using the “Search” facility of the BSI Electronic Catalogue or of British Standards Online.This publication does not purport to include all the necessary provisions of a contract. Users are responsible for its correct application.Compliance with a British Standard does not of itself confer immunity from legal obligations.—aid enquirers to understand the text;——promulgate them in the UK.Summary of pagesThis document comprises a front cover, an inside front cover, the EN title page, pages 2 to 14, an inside back cover and a back cover.The BSI copyright notice displayed in this document indicates when the document was last issued.Amendments issued since publication Amd. No.DateCommentsEUROPEAN STANDARD NORME EUROPÉENNE EUROPÄISCHE NORMEN 1514-2May 2005ICS 23.040.80Supersedes EN 1514-2:1997English versionFlanges and their joints - Gaskets for PN-designated flanges -Part 2: Spiral wound gaskets for use with steel flangesBrides et leurs assemblages - Joints pour les brides désignées PN - Partie 2: Joints spiralés pour utilisationavec des brides en acierFlansche und ihre Verbindungen - Dichtungen für Flanschemit PN-Bezeichnung - Teil 2: Spiraldichtungen fürStahlflanscheThis European Standard was approved by CEN on 24 March 2005.CEN members are bound to comply with the CEN/CENELEC Internal Regulations which stipulate the conditions for giving this European Standard the status of a national standard without any alteration. Up-to-date lists and bibliographical references concerning such national standards may be obtained on application to the Central Secretariat or to any CEN member.This European Standard exists in three official versions (English, French, German). A version in any other language made by translation under the responsibility of a CEN member into its own language and notified to the Central Secretariat has the same status as the official versions.CEN members are the national standards bodies of Austria, Belgium, Cyprus, Czech Republic, Denmark, Estonia, Finland, France,Germany, Greece, Hungary, Iceland, Ireland, Italy, Latvia, Lithuania, Luxembourg, Malta, Netherlands, Norway, Poland, Portugal, Slovakia, Slovenia, Spain, Sweden, Switzerland and United Kingdom.EUROPEAN COMMITTEE FOR STANDARDIZATION C O M I T É E U R O P ÉE N D E N O R M A LI S A T I O N C HES KOM ITEE FÜR NOR M UNG© 2005 CENAll rights of exploitation in any form and by any means reserved worldwide for CEN national Members.Ref. No. EN 1514-2:2005: EEN 1514-2:2005 (E)ContentsPage Foreword (3)Introduction (4)1Scope (5)23Terms and definitions4Designations5Gasket designs (7)6Gasket types (8)7Dimensions (8)8Marking (11)Annex A (informative) Information to be supplied by the purchaser (13)Bibliography (14)EN 1514-2:2005 (E)ForewordThis European Standard (EN 1514-2:2005) has been prepared by Technical Committee CEN/TC 74 “Flanges and their joints”, the secretariat of which is held by DIN.This European Standard shall be given the status of a national standard, either by publication of an identical text or by endorsement, at the latest by November 2005, and conflicting national standards shall be withdrawn at the latest by November 2005.This document supersedes EN 1514-2:1997.EN 1514 consists of the following parts, Flanges and their joints - Dimensions of gaskets for PN-designated flanges:⎯ Part 1: Non-metallic flat gaskets with or without inserts;⎯ Part 2: Spiral wound gaskets for use with steel flanges;⎯ Part 3: Non-metallic PTFE envelope gaskets;⎯ Part 4: Corrugated, flat or grooved metallic and filled metallic gaskets for use with steel flanges;⎯ Part 6: Covered serrated metal gaskets for use with steel flanges;⎯ Part 7: Covered metal jacketed gaskets for use with steel flanges;⎯ Part 8: Polymeric O-Ring gaskets for grooved flanges.According to the CEN/CENELEC Internal Regulations, the national standards organizations of the following countries are bound to implement this European Standard: Austria, Belgium, Cyprus, Czech Republic, Den-mark, Estonia, Finland, France, Germany, Greece, Hungary, Iceland, Ireland, Italy, Latvia, Lithuania, Luxem-bourg, Malta, Netherlands, Norway, Poland, Portugal, Slovakia, Slovenia, Spain, Sweden, Switzerland and United Kingdom.EN 1514-2:2005 (E)IntroductionThis European Standard replaces an earlier one issued in 1997. The reason for the revision is to ensure thatthis European Standard.The dimensions of spiral wound gaskets for tongue and groove flanges and spigot and recess flanges to EN 1092-1 are not included in this European Standard. Such gaskets may be available, however, for these types of flanges and the purchaser is advised to consult the manufacturer as to their availability.EN 1514-2:2005 (E)1 ScopeThis European Standard specifies the dimensions and marking of spiral wound gaskets for use in conjunction with flat face and raised face flanges complying with EN 1092-1 for PN 10, PN 16, PN 25, PN 40, PN 63, PN 100 and PN 160 and up to and including DN 1000.NOTE 1 Dimensions of other types of gaskets for use with flanges to EN 1092-1, EN 1092-2, EN 1092-3 and EN 1092-4 are given in EN 1514-1, EN 1514-3, EN 1514-4, EN 1514-6, EN 1514-7 and EN 1514-8.NOTE 2 Annex A lists information that should be supplied by the purchaser when ordering gaskets in circumstances where the choice of the gasket materials appropriate to the service is left to the supplier.2 Normative referencesThe following referenced documents are indispensable for the application of this document. For dated refer-ences, only the edition cited applies. For undated references, the latest edition of the referenced document (including any amendments) applies.EN 1333, Pipework components — Definition and selection of PN.EN ISO 6708, Pipework components — Definition and selection of DN (nominal size) (ISO 6708:1995).3 Terms and definitionsFor the purposes of this European Standard, the following terms and definitions apply.3.1DNsee EN ISO 67083.2PNsee EN 13334 Designations4.1 Essential Features and Dimensions4.1.1 GeneralA major feature of the design of spiral wound gaskets to the requirements of this European Standard is the mini-misation of the possibility of the inner ring protruding into the bore of the pipe to which the flange is attached. The fit of the inner ring and sealing element relative to the outer ring has been selected to comply with this objective. The essential features of a spiral wound gasket in compliance with this specification are given in Figures 1 and 2 and/or are listed below.Above DN 200 a maximum of 0,4 mmGuide Ring Thickness 3 mm ± 0,25EN 1514-2:2005 (E)Sealing element location groove shall be centrally located in the guide ring Centre ± 0,1 mm Number of empty wraps on external diameter of the sealing 3 to 5 elementNumber of empty wraps on the internal diameter of the sealing 2 to 3 elementMinimum of 4element, i.e. on the empty wraps0,2 mm ± 0,02 mmWidth of the profiled metal of the sealing element4,5 mm 300.+Thickness of the filler material shall be as appropriate for the filler type Protrusion of the filler above the profiled metal of the sealing 0,3 ± 0,1 mmelementCompression of the sealing element shall not result in contact between the flange and the guide ring, see also 4.1.2Graphite ash contentmaximum of 2 %PTFE filler to contain no recycled material and may be either sintered or non-sintered Sharp edges on inner ring and guide ring to be removed Dimensions to be as given in Table 1 4.1.2 Maximum CompressionMetal to metal contact between the guide ring and the flange shall not be achieved with the maximum load that can be generated by the flange bolts. 4.1.3 The Use of an Inner RingAn inner ring shall be used with all gaskets using PTFE as the filler and with all gaskets for pressure groups PN 63, PN 100 and PN 160.In addition to the above, it is strongly recommended that an inner ring should be used with all gaskets, this should therefore be specified on the order for all gaskets for pressure groups PN 10, PN 25 and PN 40.4.2 Range of PN DesignationsGaskets shall be designated as suitable for use with one or more of the following PN designations of flanges: PN 10 PN 63 PN 25 PN 100PN 40PN 160EN 1514-2:2005 (E)4.3 Range of DN (nominal sizes)Gasket nominal sizes shall be designated in accordance with the ranges specified in Table 1.4.4 Gasket typesGasket types, as defined in Clause 6 and as illustrated in Figure 3, shall be designated as:⎯ Type C/I: Sealing element with centring ring and inner ring;⎯ Type C/O: Sealing element with centring ring.4.5 Information to be supplied by the purchaserNOTE Where the purchaser wants the manufacturer to specify the materials of the gasket then the information that should be supplied to the manufacturer with the order is given in Annex A.5 Gasket designsGaskets for which dimensions are specified shall be of one of the designs shown in Figure 1.The clearance between the sealing element and the centring ring shall be as shown in Figure 2.NOTE 1 Figure 1 shows a typical design of a metallic spiral wound gasket and, for use with type A or type B flanges. NOTE 2 Type A and type B flange facings are illustrated in EN 1092-1.NOTE 3 The profile of the metal winding of the sealing element is at the option of the manufacturer.NOTE 4 The materials of the gasket may be either specified by the purchaser or, if required by the purchaser, they may be chosen by the manufacturer to suit the operating conditions. In the latter case, the purchaser should define the operating conditions in the enquiry and/or order (see Annex A).NOTE 5 The attention of the user is drawn to the load necessary to compress spiral wound gaskets and the available load with PN 10 flanges should be verified as adequate prior to using these gaskets.EN 1514-2:2005 (E)a) Type C/Ib) Type C/OFigure 1 — Spiral wound gaskets6 Gasket typesGaskets shall be one of the following types:a) Type C/I Sealing element with centring ring and inner ring;b) Type C/O Sealing element with centring ring.All gaskets shall have a centring ring. All PN 63, PN 100 and PN 160 gaskets shall have an inner ring. All gaskets containing PTFE filler material shall have an inner ring.NOTE 1 The use of an inner ring is recommended for all PN designations and the purchaser should specify on the en-quiry and/or order if an inner ring is required for PN 10, PN 25 and PN 40 gaskets (see Annex A).NOTE 2 The selection of gasket type should take into account the fluids, the operating conditions, the properties of the gasket materials, the type and surface finish of the flange facing and the flange bolt loading. It is recommended that selec-tion of gaskets for any particular application is made in consultation with the gasket supplier (see Annex A).7 DimensionsThe dimensions of spiral wound gaskets for types A and B flange facings shall be as given in Table 1 and overall thickness, including filler, shall be as given in Figure 2.EN 1514-2:2005 (E)Dimensions in millimetresKeya See Table 1 for detailsb Protrusion minimum of 0,2 mmc Gasket shall not compress such that metal to metalcontact between flange and guide rings is achievedd Width (of profiled metal of the sealingelement)e Tolerance:1 2 to 3 empty wraps2 3 to 5 empty wraps3 Central groove ± 0,1 mm4 Sharp edges removed5 Minimum of four welding points for each6 Metal thickness 0,2 mm ± 0,02 mm7 Thickness as appropriate to filler typeGraphite Ash content < 2 %,PTFE filler to contain no re-cycled material and may beeither sintered or non-sintered.Figure 2 — Spiral wound gasket detailsEN 1514-2:2005 (E)10Table 1 — DimensisonsEN 1514-2:2005 (E)8 Marking8.1 GeneralThe guide ring shall be marked with the following information:a) Manufacturer's name or trade mark;b) DN followed by the appropriate number;c) PN designation followed by the appropriate number;d) The manufacturer’s symbols or colour coding as required in 8.2 for the materials of the metal winding, thefiller material and centring ring, unless the latter is carbon steel, and inner ring unless it is 304 stainless steel.EXAMPLE of guide ring marking: AAA/BBB, DN 300, PN 25, XXXGaskets shall be identified either individually or on the packaging containing the gasket(s) with the number of this European Standard, i.e. EN 1514-2.8.2 Colour CodingSpiral wound gaskets shall be marked with colour codes that identify the metal of the winding strip and the filler material.A continuous colour around the centring ring edge shall identify the metal of the winding strip.Intermittent stripes around the edge of the centring ring shall identify the filler material. For gasket sizes below DN 40 there will be a minimum of two stripes spaced approximately 180 degrees apart. For gaskets of DN 40 and above there will be a minimum of four stripes spaced approximately 90 degrees apart.The colour codes shall conform to those listed in Table 2, for materials not given in Table 2, the colour code shall be agreed between the purchaser and the manufacturer.EN 1514-2:2005 (E)Table 2 — Colour coding and abbreviations for spiral-wound gasket materialsEN 1514-2:2005 (E)Annex A(informative)Information to be supplied by the purchaserBefore ordering a gasket it is recommended that the selection of the gasket type should be made in consulta-tion with the gasket supplier. The selection of gasket type should take account of the fluid, the operating con-ditions, the properties of the gasket materials, the type and surface finish of the flange facing and the flange bolt loading.The following information should be supplied by the purchaser when ordering gaskets:a) reference to this European Standard, i.e. EN 1514-2;b) gasket type (see 4.3);c) DN (see Table 1) and any requirement for a specific inner ring inside diameter;d) PN designation (see Table 1);e) whether an inner ring is required (see NOTES 1 and 2 to Clause 6);f) expected operating conditions for which the gasket will be used.EN 1514-2:2005 (E)Bibliography1092-1,Flanges and their joints — Circular flanges for pipes, valves, fittings and accessories, [1] ENPN designated — Part 1: Steel flanges.Flanges and their joints — Circular flanges for pipes, valves, fittings and accessories, [2] EN1092-2,[3] EN1092-3,1092-4,Flanges and their joints — Circular flanges for pipes, valves, fittings and accessories, [4] ENPN designated — Part 4: Aluminium alloy flanges.Flanges and their joints — Gasket parameters and test procedures relevant to the design [5] EN13555,rules for gasketed circular flange connections.BS EN 1514-2:2005BSI389 Chiswick High Road London W4 4ALBSI is the independent national body responsible for preparingBritish Standards. It presents the UK view on standards in Europe and at the international level. It is incorporated by Royal Charter.RevisionsBritish Standards are updated by amendment or revision. Users ofBritish Standards should make sure that they possess the latest amendments or editions.Tel:+44+44(0)2089967400.BSI offers members an individual updating service called PLUS which ensures that subscribers automatically receive the latest editions of standards.Buying standardsOrders for all BSI, international and foreign standards publications should be addressed to Customer Services. Tel:+44(0)2089969001.Fax:+44(0)2089967001. Email:orders@. Standards are also available from the BSI website at .In response to orders for international standards, it is BSI policy to supply the BSI implementation of those that have been published as British Standards,unless otherwise rmation on standardsBSI provides a wide range of information on national, European andinternational standards through its Library and its Technical Help to Exporters Service. Various BSI electronic information services are also available which give details on all its products and services. Contact the Information Centre.Tel:+44(0)2089967111. Fax:+44(0)2089967048. Email:info@.Subscribing members of BSI are kept up to date with standards developments and receive substantial discounts on the purchase price of standards. For details of these and other benefits contact Membership Administration. Tel:+44(0)2089967002. Fax:+44(0)2089967001. Email:membership@.Information regarding online access to British Standards via British Standards Online can be found at /bsonline.Further information about BSI is available on the BSI website at .CopyrightCopyright subsists in all BSI publications. BSI also holds the copyright, in the UK, of the publications of the international standardization bodies. Except as permitted under the Copyright, Designs and Patents Act 1988 no extract may be reproduced, stored in a retrieval system or transmitted in any form or by any means – electronic, photocopying, recording or otherwise – without prior written permission from BSI.This does not preclude the free use, in the course of implementing the standard, of necessary details such as symbols, and size, type or grade designations. If these details are to be used for any other purpose than implementation then the prior written permission of BSI must be obtained.Details and advice can be obtained from the Copyright & Licensing Manager. Tel:+44(0)2089967070. Fax:+44(0)2089967553. Email:copyright@.。
布朗灯 lighting 产品安装指南说明书

ROUGH-IN
TL SIDE BLOCKING
1. See continuous run matrix for roughin opening length.
2. Ensure wall is extended 6” above ceiling.
JOINER BRACKET
3. Adjust wall brackets to align with wall studs or blocking support.
© 2016 Birchwood Lighting, Inc. All rights reserved.
6. Bring conduit to fixture thru access panel or end cap and make wire connections inside fixture. Access panel can be temporarily removed to simplify wiring.
INSTRUCTION SHEET
JAKE
PER - Perimeter Flush TL Mud Flange - Side Blocking install
Installation Guide
ALIGNMENT SPLINES WITH 1/16” ALLEN SET SCREWS
WALL BRKT JOINER BRKT
ALIGNMENT SPLINES ALIGNMENT SPLINES
JOINER BRACKET
ROUGH-IN WIDTH
PERMIMETER REGRESS FIXTURES
TR/TL
6”
165
2.563”
225
64位下的相对指令地址-X86指令格式(操作码列和指令列解释)

64位下的相对指令地址-X86指令格式(操作码列和指令列解释)寻找64位系统某符号特征码时发现他的MOV指令⽤的是相对地址,之前32位下从来没听说MOV还能⽤相对地址,故查阅了下Intel指令⼿册。
在MOV指令介绍下找到如下介绍:In 64-bit mode, the instruction’s default operation size is 32 bits. Use of the REX.R prefix permits access to additionalregisters (R8-R15). Use of the REX.W prefix promotes operation to 64 bits. See the summary chart at thebeginning of this section for encoding data and limits.在64位下仍使⽤32位操作数,REX.R扩展寄存器,REX.W扩展指令。
REX前缀结构:关于RIP的介绍:2.2.1.6 RIP-Relative AddressingA new addressing form, RIP-relative (relative instruction-pointer) addressing, is implemented in 64-bit mode. Aneffective address is formed by adding displacement to the 64-bit RIP of the next instruction.In IA-32 architecture and compatibility mode, addressing relative to the instruction pointer is available only withcontrol-transfer instructions. In 64-bit mode, instructions that use ModR/M addressing can use RIP-relativeaddressing. Without RIP-relative addressing, all ModR/M modes address memory relative to zero.RIP-relative addressing allows specific ModR/M modes to address memory relative to the 64-bit RIP using a signed32-bit displacement. This provides an offset range of ±2GB from the RIP. Table 2-7 shows the ModR/M and SIBencodings for RIP-relative addressing. Redundant forms of 32-bit displacement-addressing exist in the currentModR/M and SIB encodings. There is one ModR/M encoding and there are several SIB encodings. RIP-relativeaddressing is encoded using a redundant form.In 64-bit mode, the ModR/M Disp32 (32-bit displacement) encoding is re-defined to be RIP+Disp32 rather thandisplacement-only. See Table 2-7.The ModR/M encoding for RIP-relative addressing does not depend on using a prefix. Specifically, the r/m bit fieldencoding of 101B (used to select RIP-relative addressing) is not affected by the REX prefix. For example, selectingR13 (REX.B = 1, r/m = 101B) with mod = 00B still results in RIP-relative addressing. The 4-bit r/m field of REX.Bcombined with ModR/M is not fully decoded. In order to address R13 with no displacement, software must encodeR13 + 0 using a 1-byte displacement of zero.RIP-relative addressing is enabled by 64-bit mode, not by a 64-bit address-size. The use of the address-size prefixdoes not disable RIP-relative addressing. The effect of the address-size prefix is to truncate and zero-extend thecomputed effective address to 32 bits.RIP是64位的新特性,在64位下,指令使⽤特定的Mod\rm来使⽤RIP,RIP的偏移是32位故寻址范围为上下2GB。
NSK线性导轨安装说明说明书
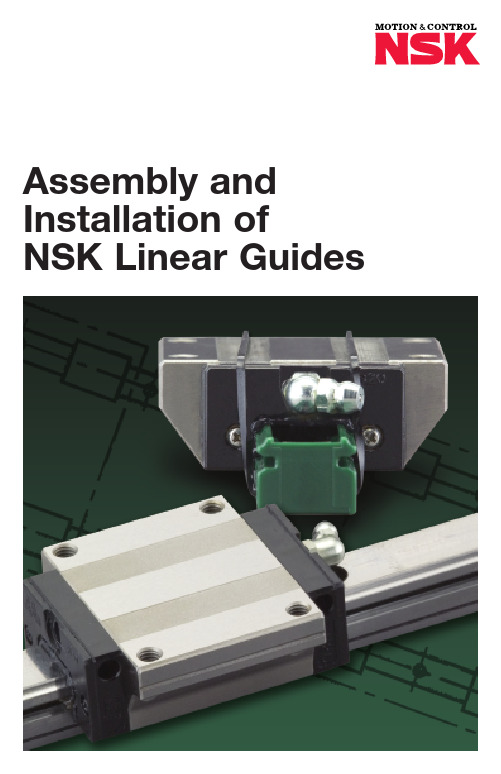
Assembly and Installation of NSK Linear GuidesLinear Guide: Handling PrecautionsNSK linear guides are high quality and are easy to use. NSK places importance onsafety in design. For maximum safety, please follow precautions as outlined below.(1) Lubricationa.Remove the rust preventativerail-coating before installation. If you are using oil as a lubricant, consult NSK for compatibility issues with the pre-packed factory grease.(2) Handlinga.Interchangeable ball slides (randomly matching types between rail and ball slide)are installed to the provisional rail when they leave the factory.Handle the ball slide with care during installation to the rail.b.Do not disassemble the guide unless absolutely necessary.c.Ball slide will move easily. Make sure that the ball slide does not disengage from the rail.d. Standard end cap is made of plasticand may break if a direct force is applied.(3) Precautions in usea.Make every effort not to allow dust and foreign objects to enter.b.The temperature of the place where linear guides are used should not exceed 80˚C (excluding heat-resistant type linear guides.)A highertemperature may damage the plastic end cap.c.If the user cuts the rail, thoroughly remove burrs and sharp edges on the cut surface.d.When hanging upside-down (e.g. the rail is installed upside-down on the ceiling in which the ball slide faces downward),should the end cap be damaged,causing the balls to fall out, the ball slide may be detached from the rail and fall. For such use, take measures including installing a safety device.(4) Storagea.Linear rail may bend if storedinappropriately. Place it on a suitable surface, and store it in a flat position.1Confirm lubrication.Handle with care.Do not drop.Do not disassemble.Do not use direct force.Do not contaminate.Do not hang upside down.Temperature limitation.Store in the correct position.2Thank you for choosing NSK linear guides. This manual briefly describes the recommended handling and installation of NSK linear guides for general industrial use.There are two methods of installing linear guides. The first uses a datum shoulder on the mounting base and provides accurate horizontal alignment in the same way used for machine tools. The other method uses the first rail as a reference for the second rail and is generally used when smooth motion versus high accuracy is required.NSK recommends the interchangeable series LH and LS linear guides for general industrial applications. Their self-aligning feature means a greater tolerance for alignment errors and less time spent on installation. Also, they are interchangeable between rail and slider, easily allowing the addition or replacement of parts.For interchangeable LH and LS Series linear guides, the ball slides and the rails are stocked separately. The ball slides are mounted on plastic provisional rails that allows for easy transfer of the ball slide to and from the steel rail.Provisional rail.Installation ProceduresWhen transferring the ball slide from the provisional rail onto the rail, or vice versa, butt the provisional rail up against the rail and slide the ball slide directly from one onto the other. It is a good idea to secure the ball slide onto theprovisional rail with a rubber band after removal from the rail.The following is a description of how the ball slide should be removed from and replaced on the linear guide rail.The ball slide is held on the provisional rail using a rubber band. The rubber band should catch the bottom channel in the provisional rail and then twist around to secure the ball slide.The ball slides are designed with retaining wires to prevent the balls from falling out when they are removed from the rail. However,NSK recommends that the ball slides should be stored on aprovisional rail prior to installation to prevent contamination from dust and other foreign objects.3Linear guide rail.Provisional rail.If a ball is accidentally droppedcleaned and replaced to theappropriate groove. The correctgroove can be determined by thesize of the clearance between theballs (the groove missing the ballwill have greater clearance thanthe other grooves). It is normalto have a gap of 1.5 balldiameters in each groove.The following section describes how to install the linear guides on the machine.Ball slides and rails are supplied separately. Each is wrapped in vinyl sheet, and packed in a container.an available option for use inhigh contamination areas toprevent debris build-up in thebolt holes which may damagethe slider. Please request theseat time of order.4The rail is always shipped with rust preventive oil, which should be wiped off before use. LH and LS Series ball slides are pre-packed with grease, so no cleaning is required prior to installation.Now the linear guide is ready for installation. Place it carefully on the mounting surface.Then tighten the bolts with a torque wrench to the specified torque starting from one end.In NSK linear guides, the mounting bolt holes are processed after heat treatment using a precision machining center; therefore, the bolt hole pitch accuracy is as good as the positioning accuracy of the machine, which is considered very good.When tightening the bolts, be sure to start at one end and work in order to the other end. If the bolts are tightened at the middle first, it tends to leave the railcurved. If you suspect this has happened, loosen the bolts and start again.5For Smooth Motion of General Machinery Snugly tighten the mounting bolts temporarily so that the rail is firmly against the bed.6The rail that has been tightened can now be used as a reference rail. Using a vernier calipers or other accurate tool, measure the distance between the two rails, and adjust each end until they are the same. Tighten a bolt snugly at each end of the rail.The next step is to install the table, and to use the table to align the rails.Firmly bolt the table to ball slides 1 and 2 on the firmly secured rail as shown in the diagram. Then position ball slide 3 at the left end of the adjusting rail, and bolt the table to this ball slide. Move the ball slide 3 to right and bolt the table to the ball slide 4.Move the table to one end of the rails, and start tightening the adjusting rail bolt sequentially to the specified torque while checking excessive friction of tablemovement. Continue moving the table down the rail tightening each adjacent bolt until they have all been tightened.This method of assembly is for general industrial machinery where smooth linear motion is the overall objective. When precision accuracy is required,read on to the following procedure.For Greater Accuracy ofGeneral MachineryWhen bolting the first rail on themachine base, align it straight usinga straightedge and a dial indicator.Bolt on the rail at the both endslightly, and position a straightedgebeside it. Set the straightedgeparallel to the rail measuringdistance A1 and A2 by a verniercalipers or some other accuratemeasuring tool.Move the dial indicator along the straightedge, and take readings at every bolt hole along the rail. Make fine adjustment of the rail to the straightedge until the desired reading is made, and tighten the bolt to the specified torque.When all of the bolts have been tightened, slide the dial indicator from one end of the rail to the other to ensure that the desired straightness has been achieved.Position the dial indicator on two ballslides on the reference rail as shownin the diagram. Tighten bolts of theadjusting side rail sequentially fromthe one end while noting the readingof the dial indicator.Straightness of NSK linear guidesis controlled so that it can beeasily adjusted manually foreasy installation.During installation, it is recommended that accuracy is checked to ensure smooth operation.78This section describes the allowable tolerances for installation in order to maximize the performance of NSK linear guides.We recommend that the mounting errors e 1or e 2do not exceed the values shown in the table below.If the error readings are equal to or less than the above values, you have correctly assembled the parts. For maximum accuracy, keep the readings below what is shown in the table.If your readings are greater than these values, it is necessary to remove the parts and start over. Please contact your local NSK office with any questions or for assistance. Visit for contact information.Recommended allowable installation error of the LS Series (Maximum) Unit:µmK1™ Handling InstructionsTo maintain the NSK K1™ lubrication unit over a long period of time,please follow these instructions.Ball SlideNSK K1™End (rubber)sealEnd (rubber)sealRail1.Max. operating temperature: 50°C (122°F)Max. peak temperature: 80°C (176°F)If not installed immediately, they should be kept refrigerated.Avoid storage in direct sunlight.2.Never leave the linear guide in close proximity to grease-removing organicsolvents such as hexane, thinners, etc. Never immerse the linear guide in kerosene or rust preventative oils which contain kerosene.NoteOther oils such as: water-based cutting oil, oil-based cutting oil, grease (mineral oil-AS2, ester-PS2) present no problems to the K1™ lubricating units performance.9Assembly Instructions for the K1™Lubricating Unit1.Slide linear bearing on to the linear rail, using the plasticprovisional rail supplied.2.Remove the grease fitting from the end of the bearing.3.Remove the Phillips screws (2 pieces).4.Remove the end lubrication unit from end of bearing.5.For maintenance free operation, install threaded plug; for re-greasingoption, see points 10 & 11 below.6.Install the cover plate from the K1™ lubricating unit kit to the end ofbearing, against the end cap.7.Install K1™ lubricating unit without fixing rings, so it can beexpanded over the rail.8.Put the three (3) fixing rings in position on the K1™ lubricating unit.9.Replace the end seal , in front of the K1™ lubricating unit.10.Install connector screw for grease fitting.11.Replace the grease fitting in connector screw.12.Install the extension Phillips screws (2 pieces, supplied with theK1™ lubricating unit kit).NoteThe K1™ lubricating unit has a shelf life. They should be installed immediately upon receipt. It is important to avoid direct sunlight and extreme heat conditions.40There are two types of lubricating methods –grease and oil –for ball screws and linear guides.Use a lubricant agent and method most suitable to condition requirements and purpose to optimize functions of the ball screws and linear guides.In general, lubricants with low base oil kinematic viscosity are used for high speed operation.Lubrication with high base oil kinematic viscosity is used for oscillating operations, low speed and high temperature.The following are lubrication methods by grease and by oil.Note: Please consult NSK Engineering for grease replenishment interval.Grease LubricationGrease lubrication is widely used because it does not require special oil supply system or piping. Grease lubricants made by NSK are:•Various types of grease in bellowed container which can be instantly attached to the grease pump;• NSK Grease Unit which comprises a hand grease pump and various nozzles. The units are compact and easy to use.NSK grease lubricantsTable 9 shows the marketed general grease widely used for linear guides and ball screws for various applications,conditions and purposes.LubricationTable 9 Grease lubricant for linear guides and ball screwsIntervals of checks and replenishments for grease lubricationFor more info see separate Lubrication InstruktionLG Handbook Printed in Canada © NSK 2005.NSK Ltd. has a basic policy not to export any products or technology designated as controlled items by export-related laws. When exporting the products in thisbr ochur e, the laws of the expor ting countr y must be obser ved. Specifications ar e subject to change without notice and without any obligation on the par t of the manufactur er. Every care has been taken to ensure the accuracy of the data contained in this brochure, but no liability can be accepted for any loss or damage suffered through errors or omissions. We will gratefully acknowledge any additions or corrections.NSK Ltd.-Headquarters, Tokyo, Japan Americas & Europe Department tel: 03-3779-7120Asia Marketing & Sales Department tel: 03-3779-7121AfricaSouth Africa:NSK South Africa (Pty )Ltd.Johannesburgtel: (011)458 3600Asia and OceaniaAustralia:www .au NSK Australia Pty. Ltd.Melbourne tel: (03)9764-8302China:NSK Hong Kong Ltd.Hong Kong tel: 2739-9933Kunshan NSK Co., Ltd.Kunshantel*************Guizhou HS NSK Bearings Co., Ltd.Anshun tel*************NSK (Shanghai )Trading Co., Ltd.Shanghaitel*************NSK representative office Beijing tel: 010-6590-8161NSK representative office Shanghai tel: 21-6209-9051NSK representative office Guangzhou tel: 020-8732-0583NSK representative office Anshun tel*************India:Rane NASTECH Ltd.Chennaitel: 04114-65313, 65314, 65365, 66002NSK representative office Chennai tel: 044-4334732Indonesia:P.T . NSK Bearings Manufacturing Indonesia Jakarta tel: 021-898-0155Korea:NSK Korea Co., Ltd.Seoul tel: 02-3287-0300NSK Korea Co., Ltd., Changwon Plant Changwon tel: 0551-287-6001Malaysia:NSK Bearings (Malaysia )Sdn. Bhd.Kuala Lumpur tel: 03-7958-4396NSK Micro Precision (M )Sdn. Bhd.Kuala Lumpurtel: 03-961-6288New Zealand: NSK New Zealand Ltd.Aucklandtel: (09)276-4992Philippines:NSK representative office Manila tel: 02-759-6246Singapore:NSK International (Singapore )Pte Ltd.Singapore tel: (65)273 0357NSK Singapore (Pte )Ltd.Singapore tel: (65)278 1711Taiwan:T aiwan NSK Precision Co., Ltd.T aipei tel: 02-2591-0656Thailand:NSK Bearings (Thailand )Co., Ltd.Bangkoktel: 02-6412150~58NSK Safety T echnology (Thailand )Co., Ltd.Chonburi tel: (038)214-317-8Siam NASTECH Co., Ltd.Chachoengsaotel: (038)522-343~350EuropeNSK Europe Ltd.(European Headquarters ) Maidenhead, England tel: 0162-850-9800France:NSK France S.A.Paristel: 01 30 57 39 39Germany:NSK Deutschland Gmbh Düsseldorf tel: 02102-481-0NSK Steering Systems Europe Ltd.Stuttgarttel: 0771-79082-277Neuweg Fertigung Gmbh Munderkingen tel: 07393-540Italy:NSK Italia S.P ano tel: 02-995-191Poland:NSK Europe Ltd. Warsaw Liaison Office Warsaw tel: 48-22-645-1525, 1526NSK Iskra S.A.Kielce tel: 48-41-366-6111Spain:NSK Spain S.A.Barcelonatel: 93-575-4041Worldwide Sales OfficesSwitzerland:Waelzlager Industriewerke Bulle AG (W.I.B.)Bulle tel: 026-9191100Turkey:NSK Bearings Middle East Trading Co., Ltd.Istanbultel: 90-216-442-7106United Kingdom:NSK Bearings Europe Ltd.Peterlee, England tel: 0191-586-6111NSK European T echnology Co., Ltd.Ruddington, England tel: 0115-940-5409NSK UK Ltd.Newark, England tel: 0163-660-5123NSK Steering Systems Europe Ltd.Coventry, Englandtel: 024-76-588588North and South AmericaNSK Americas, Inc. (American Headquarters )Ann Arbor, Michigan, U.S.A.tel: 734-913-7500Argentina:NSK Argentina SRLBuenos Airestel: 011-4762-6556Brazil:www.br NSK Brasil Ltda.São Paulotel: 011-3269-4700Canada: NSK Canada Inc.T orontotel: 905-890-0740Mexico:NSK Rodamientos Mexicana, S.A. de C.V .Mexico Citytel: 5-301-2741United States of America: NSK CorporationAnn Arbor, Michigantel: 734-913-7500Sales Offices:Ann Arbor, Michigan tel: 734-913-7500Cerritos, Californiatel: 562-926-2975NSK American T echnical Center Ann Arbor, Michigan tel: 734-913-7500NSK Precision America, Inc.Bloomingdale, Illinoistel: 630-924-8000NASTECHBennington, Vermonttel: 802-442-5448NSK Latin America Miami, Florida tel: (305)477-0605。
Sunnydaze 黑色钢铁炉灶帽与木柴架说明书
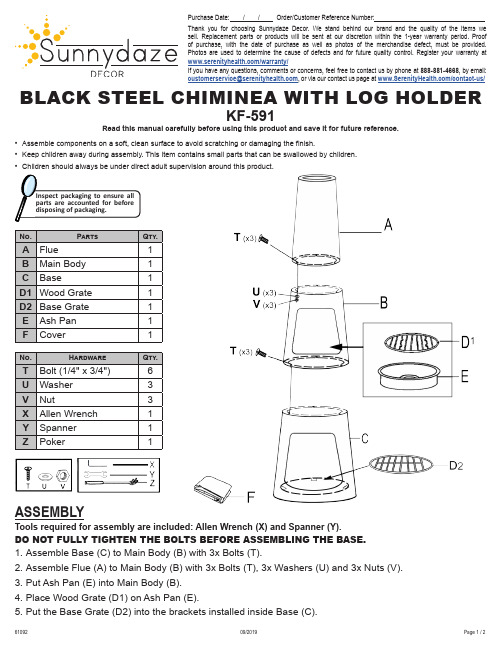
BLACK STEEL CHIMINEA WITH LOG HOLDERKF-591ASSEMBLYTools required for assembly are included: Allen Wrench (X) and Spanner (Y).DO NOT FULLY TIGHTEN THE BOLTS BEFORE ASSEMBLING THE BASE.1. Assemble Base (C) to Main Body (B) with 3x Bolts (T).2. Assemble Flue (A) to Main Body (B) with 3x Bolts (T), 3x Washers (U) and 3x Nuts (V).3. Put Ash Pan (E) into Main Body (B).4. Place Wood Grate (D1) on Ash Pan (E).5. Put the Base Grate (D2) into the brackets installed inside Base (C).Thank you for choosing Sunnydaze Decor. We stand behind our brand and the quality of the items we sell. Replacement parts or products will be sent at our discretion within the 1-year warranty period. Proof of purchase, with the date of purchase as well as photos of the merchandise defect, must be provided. Photos are used to determine the cause of defects and for future quality control. Register your warranty at /warranty/If you have any questions, comments or concerns, feel free to contact us by phone at 888-881-4668, by email: , or via our contact us page at /contact-us/Purchase Date: / / Order/Customer Reference Number:CARING FOR YOUR CHIMINEA:Clean Regularly: All fire pits must be cleaned and inspected periodically. The ash produced in wood-burning chimineas must be cleaned out regularly. Never allow ash to accumulate in the bowl or the flue.Clean Safely: Make sure the fire has completely died down, and the metal is completely cool before you remove the ashes and cleaning the flue.Avoid Accelerants: Never use accelerants to start a fire; this is dangerous and can be damaging to your fire pit as well.Avoid Plastic: Never use any plastic materials in or nearby a fire pit. It is very difficult to remove the residue later, and the burning of this residue can cause the emission of toxic fumes.Use on a Safe Surface: Always use chimineas on a smooth, non-combustible surface; do not use on a wood deck or other combustible surfaces like dry grass, leaves, mulch, etc. Do not use chimineas near combustible structures such as vinyl or wood siding. Take care never to drop your chiminea, as any breakage could cause serious damage and costly repairs.Cover and Store: If you do not plan to use your chiminea for an extended period of time, cover and store it in a dry location; this will protect it from the elements and dust buildup. If you decide only to cover the chiminea, be sure it is not exposed to water. The manufacturer is not liable for rust due to weather conditions. Extinguish: Let fires die down gradually, do not use water to put out a fire as this may cause the metal to crack as a result of the sudden drop in temperature.。
- 1、下载文档前请自行甄别文档内容的完整性,平台不提供额外的编辑、内容补充、找答案等附加服务。
- 2、"仅部分预览"的文档,不可在线预览部分如存在完整性等问题,可反馈申请退款(可完整预览的文档不适用该条件!)。
- 3、如文档侵犯您的权益,请联系客服反馈,我们会尽快为您处理(人工客服工作时间:9:00-18:30)。
Brennan's Guide to Inline Assemblyby Brennan "Bas" UnderwoodDocument version 1.1.2.2Ok. This is meant to be an introduction to inline assembly under DJGPP.DJGPP is based on GCC, so it uses the AT&T/UNIX syntax and has asomewhat unique method of inline assembly. I spent many hours figuringsome of this stuff out and told Info that I hate it, many times.Hopefully if you already know Intel syntax, the examples will be helpful toyou. I've put variable names, register names and other literals in bold type.The SyntaxSo, DJGPP uses the AT&T assembly syntax. What does that mean to you?Register naming:•Register names are prefixed with "%". To reference eax:AT&T: %eax•Intel: eax•Source/Destination Ordering:•In AT&T syntax (which is the UNIX standard, BTW) the source isalways on the left, and the destination is always on the right.So let's load ebx with the value in eax:AT&T: movl %eax, %ebx•Intel: mov ebx, eax•Constant value/immediate value format:•You must prefix all constant/immediate values with "$".Let's load eax with the address of the "C" variable booga, which isstatic.AT&T: movl $_booga, %eax•Intel: mov eax, _booga•Now let's load ebx with 0xd00d:AT&T: movl $0xd00d, %ebxIntel: mov ebx, d00dhOperator size specification:•You must suffix the instruction with one of b, w, or l to specify thewidth of the destination register as a byte, word or longword. If youomit this, GAS (GNU assembler) will attempt to guess. You don'twant GAS to guess, and guess wrong! Don't forget it.AT&T: movw %ax, %bx•Intel: mov bx, ax•The equivalent forms for Intel is byte ptr, word ptr, and dword ptr,but that is for when you are...Referencing memory:•DJGPP uses 386-protected mode, so you can forget all thatreal-mode addressing junk, including the restrictions on whichregister has what default segment, which registers can be base orindex pointers. Now, we just get 6 general purpose registers. (7 ifyou use ebp, but be sure to restore it yourself or compile with-fomit-frame-pointer.)Here is the canonical format for 32-bit addressing:AT&T: immed32(basepointer,indexpointer,indexscale)•Intel: [basepointer + indexpointer*indexscale + immed32]•You could think of the formula to calculate the address as:immed32 + basepointer + indexpointer * indexscaleYou don't have to use all those fields, but you do have to have atleast 1 of immed32, basepointer and you MUST add the size suffix tothe operator!Let's see some simple forms of memory addressing:Addressing a particular C variable:oAT&T: _boogaoo Intel: [_booga]Note: the underscore ("_") is how you get at static (global) Cvariables from assembler. This only works with globalvariables. Otherwise, you can use extended asm to havevariables preloaded into registers for you. I address thatfarther down.Addressing what a register points to:oAT&T: (%eax)oo Intel: [eax]Addressing a variable offset by a value in a register:oAT&T: _variable(%eax)oo Intel: [eax + _variable]Addressing a value in an array of integers (scaling up by 4): oo AT&T: _array(,%eax,4)o Intel: [eax*4 + array]You can also do offsets with the immediate value:oo C code: *(p+1) where p is a char *o AT&T: 1(%eax) where eax has the value of po Intel: [eax + 1]You can do some simple math on the immediate value: oo AT&T: _struct_pointer+8I assume you can do that with Intel format as well.Addressing a particular char in an array of 8-character orecords:eax holds the number of the record desired. ebx has thewanted char's offset within the record.o AT&T: _array(%ebx,%eax,8)o Intel: [ebx + eax*8 + _array]Whew. Hopefully that covers all the addressing you'll need to do. Asa note, you can put esp into the address, but only as the baseregister.Basic inline assemblyThe format for basic inline assembly is very simple, and much likeBorland's method.asm ("statements");Pretty simple, no? Soasm ("nop");will do nothing of course, andasm ("cli");will stop interrupts, withasm ("sti");of course enabling them. You can use __asm__ instead of asm if the keyword asm conflicts with something in your program.When it comes to simple stuff like this, basic inline assembly is fine. You can even push your registers onto the stack, use them, and put them back. asm ("pushl %eax\n\t""movl $0, %eax\n\t""popl %eax");(The \n's and \t's are there so the .s file that GCC generates and hands to GAS comes out right when you've got multiple statements per asm.)It's really meant for issuing instructions for which there is no equivalent in C and don't touch the registers.But if you do touch the registers, and don't fix things at the end of your asm statement, like so:asm ("movl %eax, %ebx");asm ("xorl %ebx, %edx");asm ("movl $0, _booga");then your program will probably blow things to hell. This is because GCC hasn't been told that your asm statement clobbered ebx and edx and booga, which it might have been keeping in a register, and might plan on using later. For that, you need:Extended inline assemblyThe basic format of the inline assembly stays much the same, but now gets Watcom-like extensions to allow input arguments and output arguments. Here is the basic format:asm ( "statements" : output_registers : input_registers :clobbered_registers);Let's just jump straight to a nifty example, which I'll then explain:asm ("cld\n\t""rep\n\t""stosl": /* no output registers */: "c" (count), "a" (fill_value), "D" (dest): "%ecx", "%edi" );The above stores the value in fill_value count times to the pointer dest.Let's look at this bit by bit.asm ("cld\n\t"We are clearing the direction bit of the flags register. You never know what this is going to be left at, and it costs you all of 1 or 2 cycles."rep\n\t""stosl"Notice that GAS requires the rep prefix to occupy a line of it's own. Notice also that stos has the l suffix to make it move longwords.: /* no output registers */Well, there aren't any in this function.: "c" (count), "a" (fill_value), "D" (dest)Here we load ecx with count, eax with fill_value, and edi with dest. Why make GCC do it instead of doing it ourselves? Because GCC, in its register allocating, might be able to arrange for, say, fill_value to already be in eax. If this is in a loop, it might be able to preserve eax thru the loop, and save a movl once per loop.: "%ecx", "%edi" );And here's where we specify to GCC, "you can no longer count on the values you loaded into ecx or edi to be valid." This doesn't mean they will be reloaded for certain. This is the clobberlist.Seem funky? Well, it really helps when optimizing, when GCC can know exactly what you're doing with the registers before and after. It folds your assembly code into the code it's generates (whose rules for generation look remarkably like the above) and then optimizes. It's even smart enough to know that if you tell it to put (x+1) in a register, then if you don't clobber it, and later C code refers to (x+1), and it was able to keep that register free, it will reuse the computation. Whew.Here's the list of register loading codes that you'll be likely to use:a eaxb ebxc ecxd edxS esiD ediI constant value (0 to 31)q,r dynamically allocated register (see below)g eax, ebx, ecx, edx or variable in memoryA eax and edx combined into a 64-bit integer (use long longs)Note that you can't directly refer to the byte registers (ah, al, etc.) or theword registers (ax, bx, etc.) when you're loading this way. Once you've got itin there, though, you can specify ax or whatever all you like.The codes have to be in quotes, and the expressions to load in have to be in parentheses.When you do the clobber list, you specify the registers as above with the %.If you write to a variable, you must include "memory" as one of The Clobbered. This is in case you wrote to a variable that GCC thought it hadin a register. This is the same as clobbering all registers. While I've neverrun into a problem with it, you might also want to add "cc" as a clobber ifyou change the condition codes (the bits in the flags register the jnz, je, etc. operators look at.)Now, that's all fine and good for loading specific registers. But what if you specify, say, ebx, and ecx, and GCC can't arrange for the values to be inthose registers without having to stash the previous values. It's possible tolet GCC pick the register(s). You do this:asm ("leal (%1,%1,4), %0": "=r" (x): "0" (x) );The above example multiplies x by 5 really quickly (1 cycle on the Pentium). Now, we could have specified, say eax. But unless we really need a specific register (like when using rep movsl or rep stosl, which are hardcoded to use ecx, edi, and esi), why not let GCC pick an available one? So when GCC generates the output code for GAS, %0 will be replaced by the register it picked.And where did "q" and "r" come from? Well, "q" causes GCC to allocate from eax, ebx, ecx, and edx. "r" lets GCC also consider esi and edi. So make sure,if you use "r" that it would be possible to use esi or edi in that instruction. If not, use "q".Now, you might wonder, how to determine how the %n tokens get allocatedto the arguments. It's a straightforward first-come-first-served,left-to-right thing, mapping to the "q"'s and "r"'s. But if you want to reuse a register allocated with a "q" or "r", you use "0", "1", "2"... etc.You don't need to put a GCC-allocated register on the clobberlist as GCC knows that you're messing with it.Now for output registers.asm ("leal (%1,%1,4), %0": "=r" (x_times_5): "r" (x) );Note the use of = to specify an output register. You just have to do it thatway. If you want 1 variable to stay in 1 register for both in and out, youhave to respecify the register allocated to it on the way in with the "0" typecodes as mentioned above.asm ("leal (%0,%0,4), %0": "=r" (x): "0" (x) );This also works, by the way:asm ("leal (%%ebx,%%ebx,4), %%ebx": "=b" (x): "b" (x) );2 things here:Note that we don't have to put ebx on the clobberlist, GCC knows it •goes into x. Therefore, since it can know the value of ebx, it isn'tconsidered clobbered.Notice that in extended asm, you must prefix registers with %%•instead of just %. Why, you ask? Because as GCC parses alongfor %0's and %1's and so on, it would interpret %edx as a %eparameter, see that that's non-existent, and ignore it. Then it wouldbitch about finding a symbol named dx, which isn't valid because it'snot prefixed with % and it's not the one you meant anyway.Important note: If your assembly statement must execute where you put it,(i.e. must not be moved out of a loop as an optimization), put the keywordvolatile after asm and before the ()'s. To be ultra-careful, use__asm__ __volatile__ (...whatever...);However, I would like to point out that if your assembly's only purpose is tocalculate the output registers, with no other side effects, you should leaveoff the volatile keyword so your statement will be processed into GCC'scommon subexpression elimination optimization.Some useful examples#define disable() __asm__ __volatile__ ("cli");#define enable() __asm__ __volatile__ ("sti");Of course, libc has these defined too.#define times3(arg1, arg2) \__asm__ ( \"leal (%0,%0,2),%0" \: "=r" (arg2) \: "0" (arg1) );#define times5(arg1, arg2) \__asm__ ( \"leal (%0,%0,4),%0" \: "=r" (arg2) \: "0" (arg1) );#define times9(arg1, arg2) \__asm__ ( \"leal (%0,%0,8),%0" \: "=r" (arg2) \: "0" (arg1) );These multiply arg1 by 3, 5, or 9 and put them in arg2. You should be ok to do:times5(x,x);as well.#define rep_movsl(src, dest, numwords) \__asm__ __volatile__ ( \"cld\n\t" \"rep\n\t" \"movsl" \: : "S" (src), "D" (dest), "c" (numwords) \: "%ecx", "%esi", "%edi" )Helpful Hint: If you say memcpy() with a constant length parameter, GCC will inline it to a rep movsl like above. But if you need a variable length version that inlines and you're always moving dwords, there ya go.#define rep_stosl(value, dest, numwords) \__asm__ __volatile__ ( \"cld\n\t" \"rep\n\t" \"stosl" \: : "a" (value), "D" (dest), "c" (numwords) \: "%ecx", "%edi" )Same as above but for memset(), which doesn't get inlined no matter what (for now.)#define RDTSC(llptr) ({ \__asm__ __volatile__ ( \".byte 0x0f; .byte 0x31" \: "=A" (llptr) \: : "eax", "edx"); })Reads the TimeStampCounter on the Pentium and puts the 64 bit resultinto llptr.The End"The End"?! Yah, I guess so.If you're wondering, I personally am a big fan of AT&T/UNIX syntax now.(It might have helped that I cut my teeth on SPARC assembly. Of course,that machine actually had a decent number of general registers.) It mightseem weird to you at first, but it's really more logical than Intel format, andhas no ambiguities.If I still haven't answered a question of yours, look in the Info pages formore information, particularly on the input/output registers. You can dosome funky stuff like use "A" to allocate two registers at once for 64-bitmath or "m" for static memory locations, and a bunch more that aren'treally used as much as "q" and "r".Alternately, mail me, and I'll see what I can do. (If you find any errors inthe above, please, e-mail me and tell me about it! It's frustrating enough tolearn without buggy docs!) Or heck, mail me to say "boogabooga."It's the least you can do.Related Usenet posts:local labels•fixed point multiplies•Thanks to Eric J. Korpela <korpela@> for somecorrections.Have you seen the DJGPP2+Games Page? Probably.Page written and provided by Brennan Underwood.Copyright © 1996 Brennan Underwood. Share and enjoy!Page created with vi, God's own editor.。