降低细纱断头率的注意点和措施
在细纱机高速生产中 如何加强日常管理工作降低细纱断头
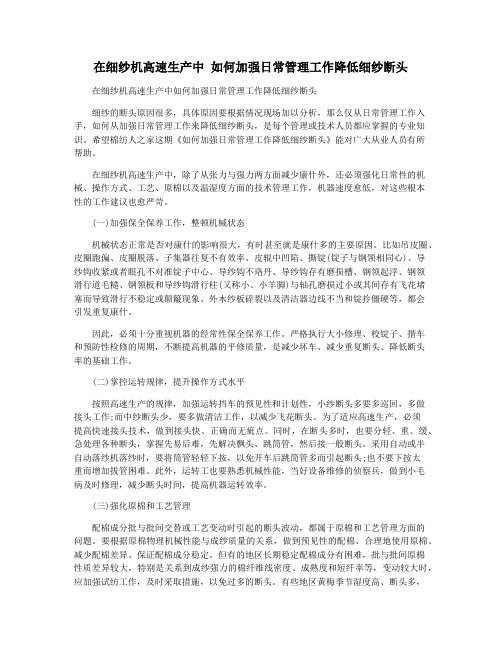
在细纱机高速生产中如何加强日常管理工作降低细纱断头在细纱机高速生产中如何加强日常管理工作降低细纱断头细纱的断头原因很多,具体原因要根据情况现场加以分析,那么仅从日常管理工作入手,如何从加强日常管理工作来降低细纱断头,是每个管理或技术人员都应掌握的专业知识。
希望棉纺人之家这期《如何加强日常管理工作降低细纱断头》能对广大从业人员有所帮助。
在细纱机高速生产中,除了从张力与强力两方面减少康什外,还必须强化日常性的机械、操作方式、工艺、原棉以及温湿度方面的技术管理工作,机器速度愈低,对这些根本性的工作建议也愈严苛。
(一)加强保全保养工作,整顿机械状态机械状态正常是否对康什的影响很大,有时甚至就是康什多的主要原因。
比如吊皮圈、皮圈跑偏、皮圈脱落、子集器往复不有效率、皮辊中凹陷、撕锭(锭子与钢领相同心)、导纱钩收紧或者眼孔不对准锭子中心、导纱钩不珞丹、导纱钩存有磨损槽、钢领起浮、钢领滑行道毛糙、钢领板和导纱钩滑行柱(又称小、小羊脚)与轴孔磨损过小或其间存有飞花堵塞而导致滑行不稳定或颠簸现象、外木纱板碎裂以及清洁器边线不当和锭拎僵硬等,都会引发重复康什。
因此,必须十分重视机器的经常性保全保养工作。
严格执行大小修理、校锭子、揩车和预防性检修的周期,不断提高机器的平修质量,是减少坏车、减少重复断头、降低断头率的基础工作。
(二)掌控运转规律,提升操作方式水平按照高速生产的规律,加强运转挡车的预见性和计划性,小纱断头多要多巡回,多做接头工作;而中纱断头少,要多做清洁工作,以减少飞花断头。
为了适应高速生产,必须提高快速接头技术,做到接头快、正确而无疵点。
同时,在断头多时,也要分轻、重、缓、急处理各种断头,掌握先易后难,先解决飘头、跳筒管,然后接一般断头。
采用自动或半自动落纱机落纱时,要将筒管轻轻下按,以免开车后跳筒管多而引起断头;也不要下按太重而增加拔管困难。
此外,运转工也要熟悉机械性能,当好设备维修的侦察兵,做到小毛病及时修理,减少断头时间,提高机器运转效率。
技术▎紧密纺减少细纱工序断头的措施
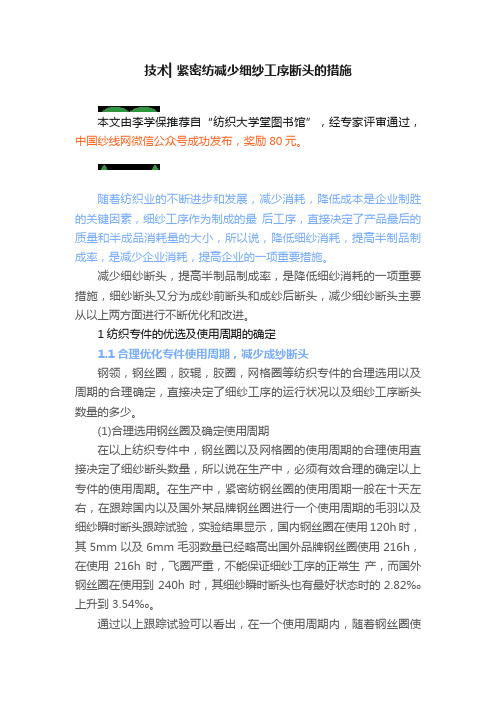
技术▎紧密纺减少细纱工序断头的措施本文由李学保推荐自“纺织大学堂图书馆”,经专家评审通过,中国纱线网微信公众号成功发布,奖励80元。
随着纺织业的不断进步和发展,减少消耗,降低成本是企业制胜的关键因素,细纱工序作为制成的最后工序,直接决定了产品最后的质量和半成品消耗量的大小,所以说,降低细纱消耗,提高半制品制成率,是减少企业消耗,提高企业的一项重要措施。
减少细纱断头,提高半制品制成率,是降低细纱消耗的一项重要措施,细纱断头又分为成纱前断头和成纱后断头,减少细纱断头主要从以上两方面进行不断优化和改进。
1纺织专件的优选及使用周期的确定1.1合理优化专件使用周期,减少成纱断头钢领,钢丝圈,胶辊,胶圈,网格圈等纺织专件的合理选用以及周期的合理确定,直接决定了细纱工序的运行状况以及细纱工序断头数量的多少。
(1)合理选用钢丝圈及确定使用周期在以上纺织专件中,钢丝圈以及网格圈的使用周期的合理使用直接决定了细纱断头数量,所以说在生产中,必须有效合理的确定以上专件的使用周期。
在生产中,紧密纺钢丝圈的使用周期一般在十天左右,在跟踪国内以及国外某品牌钢丝圈进行一个使用周期的毛羽以及细纱瞬时断头跟踪试验,实验结果显示,国内钢丝圈在使用120h时,其5mm以及6mm毛羽数量已经略高出国外品牌钢丝圈使用216h,在使用216h时,飞圈严重,不能保证细纱工序的正常生产,而国外钢丝圈在使用到240h时,其细纱瞬时断头也有最好状态时的2.82‰上升到3.54‰。
通过以上跟踪试验可以看出,在一个使用周期内,随着钢丝圈使用周期的不断增长,纱线毛羽和细纱瞬时断头都有不同程度的变化,所以说,在生产中,钢丝圈的合理选用和使用周期的合理确定是决定细纱断头的一项决定性因素。
钢丝圈型号和号数的选择要根据所纺纱线种类以及根据实际生产(紧密纺,环锭纺)来选择。
首先,紧密纺和环锭纺选择钢丝圈时,具有较大的差异性。
比较而言,紧密纺锭速较高,毛羽较少,钢丝圈缺少润滑,散热较差,需要选择钢丝圈与钢领接触面积较大的圈形,从而散热好,提高钢丝圈运行时间。
降低细纱断头的措施
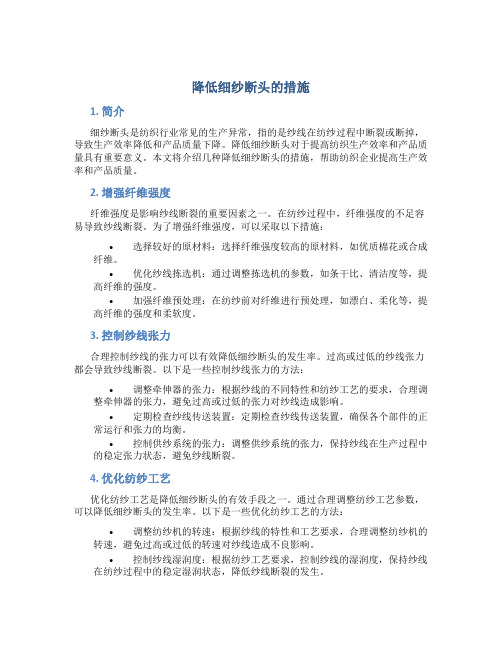
降低细纱断头的措施1. 简介细纱断头是纺织行业常见的生产异常,指的是纱线在纺纱过程中断裂或断掉,导致生产效率降低和产品质量下降。
降低细纱断头对于提高纺织生产效率和产品质量具有重要意义。
本文将介绍几种降低细纱断头的措施,帮助纺织企业提高生产效率和产品质量。
2. 增强纤维强度纤维强度是影响纱线断裂的重要因素之一。
在纺纱过程中,纤维强度的不足容易导致纱线断裂。
为了增强纤维强度,可以采取以下措施:•选择较好的原材料:选择纤维强度较高的原材料,如优质棉花或合成纤维。
•优化纱线拣选机:通过调整拣选机的参数,如条干比、清洁度等,提高纤维的强度。
•加强纤维预处理:在纺纱前对纤维进行预处理,如漂白、柔化等,提高纤维的强度和柔软度。
3. 控制纱线张力合理控制纱线的张力可以有效降低细纱断头的发生率。
过高或过低的纱线张力都会导致纱线断裂。
以下是一些控制纱线张力的方法:•调整牵伸器的张力:根据纱线的不同特性和纺纱工艺的要求,合理调整牵伸器的张力,避免过高或过低的张力对纱线造成影响。
•定期检查纱线传送装置:定期检查纱线传送装置,确保各个部件的正常运行和张力的均衡。
•控制供纱系统的张力:调整供纱系统的张力,保持纱线在生产过程中的稳定张力状态,避免纱线断裂。
4. 优化纺纱工艺优化纺纱工艺是降低细纱断头的有效手段之一。
通过合理调整纺纱工艺参数,可以降低细纱断头的发生率。
以下是一些优化纺纱工艺的方法:•调整纺纱机的转速:根据纱线的特性和工艺要求,合理调整纺纱机的转速,避免过高或过低的转速对纱线造成不良影响。
•控制纱线湿润度:根据纺纱工艺要求,控制纱线的湿润度,保持纱线在纺纱过程中的稳定湿润状态,降低纱线断裂的发生。
•检查纺纱机部件:定期检查纺纱机的各个部件,确保其正常运行和调整,避免因机器故障导致纱线断裂。
5. 增强生产管理良好的生产管理对于降低细纱断头至关重要。
以下措施可以帮助管理者更好地控制纺纱生产,减少细纱断头的发生:•建立生产管理标准:建立一套科学合理的生产管理标准,明确各项工艺参数和质量要求,以便工作人员执行和监督。
紧密纺细纱断头的成因及措施
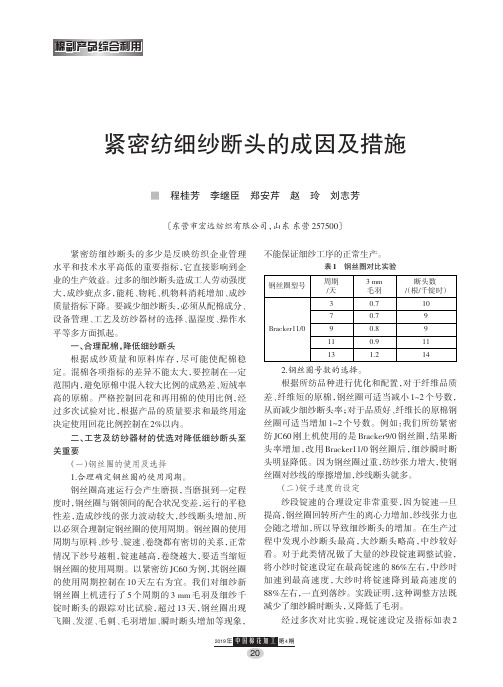
不能保证细纱工序的正常生产。
表 1 钢丝圈对比实验
钢丝圈型号
周期 /天
3 mm 毛羽
断头数 (/ 根/千锭时)
3
0.7
10
7
0.7
9
Bracker11/0
9
0.8
9
11
0.9
11
13
1.2
14
2.钢丝圈号数的选择。 根据所纺品种进行优化和配置,对于纤维品质 差、纤维短的原棉,钢丝圈可适当减小 1~2 个号数, 从而减少细纱断头率;对于品质好、纤维长的原棉钢 丝圈可适当增加 1~2 个号数。例如:我们所纺紧密 纺 JC60 刚上机使用的是 Bracker9/0 钢丝圈,结果断 头率增加,改用 Bracker11/0 钢丝圈后,细纱瞬时断 头明显降低。因为钢丝圈过重,纺纱张力增大,使钢 丝圈对纱线的摩擦增加,纱线断头就多。 (二)锭子速度的设定 纱段锭速的合理设定非常重要,因为锭速一旦 提高,钢丝圈回转所产生的离心力增加,纱线张力也 会随之增加,所以导致细纱断头的增加。在生产过 程中发现小纱断头最高,大纱断头略高,中纱较好 看。对于此类情况做了大量的纱段锭速调整试验, 将小纱时锭速设定在最高锭速的 86%左右,中纱时 加 速 到左右,一直到落纱。实践证明,这种调整方法既 减少了细纱瞬时断头,又降低了毛羽。 经过多次对比实验,现锭速设定及指标如表 2
要合理设计纱尾长度,纱尾长度掌握在 2 圈~3 圈为 宜,纱尾太长既造成浪费又给络筒增加工作量,纱尾 太短增加细纱落纱断头。
三、加强设备的维护保养是减少细纱断头的重 要保证
(一)加强大小平车工作 严格按照保养周期进行逐锭检查、保养,发现不 正常、不符合要求的立即更换;保全要分片承包责任 机台,每周由设备管理部进行抽查、验收,对责任机 台出现的问题,要严格按照责任机台承包管理规定 进行惩罚。 (二)罗拉要求无偏心、弯曲 在平车时严格执行操作规程,用百分表逐节测 定,把罗拉弯曲、偏心控制在 3%之内。 (三)根据实际情况调整前皮辊与前罗拉的前冲 量 因为紧密纺耐磨块的位置对前冲有所限制,上 肖浮游区根据下肖型号来调整,尽量要将浮游区调 小,减少纤维的零散。 (四)紧密纺皮辊要按照周期进行复磨、光照 光照要均匀,以免造成阴阳面;皮辊定期检查, 以免偏心、轴承缺油、轴承损坏等情况的发生,逐只 挑拣并分档、分区、分号使用;皮圈要定期调换和处 理,上下皮圈不能同时使用新的,会造成须条不稳 定,增加断头。 (五)定期测定摇架压力 为了避免出现压力衰退,影响前钳口握持纤维 引导力的波动,造成纤维变速点的不稳定,出现粗细 节、条干不匀,断头增加,应定期测定摇架压力。 (六)平稳运行钢领板、叶子板 钢领板、叶子板高低要一致,运行要平稳、无顿 挫现象;钢领、锭子、叶子板要定期校正,使三者中心 一条线;纺纱时最大气圈高度要控制恰当,不然易引 起气圈不正常,纱线与隔纱板或筒管头摩擦引起断 头。 (七)保证足够的负压 紧密纺装置工作原理显示,有足够的负压才能 使集聚处纱条有规律排列而达到凝聚纤维的效果。 在管理上,根据品种确定负压值,并且定期检查车 头、中间、车尾的负压值,要保持相对的稳定。注意 负压管的堵孔现象,要随时清理,孔内有棉腊的要及 时清洗,避免造成大面积断头。
纱厂细纱千锭时断头表
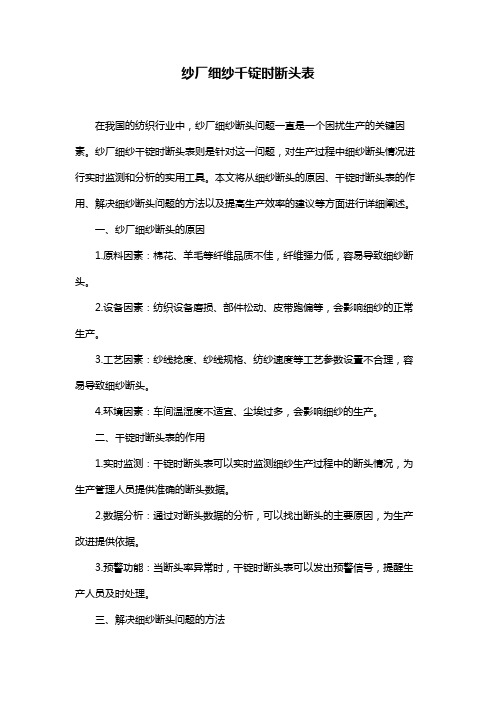
纱厂细纱千锭时断头表在我国的纺织行业中,纱厂细纱断头问题一直是一个困扰生产的关键因素。
纱厂细纱千锭时断头表则是针对这一问题,对生产过程中细纱断头情况进行实时监测和分析的实用工具。
本文将从细纱断头的原因、千锭时断头表的作用、解决细纱断头问题的方法以及提高生产效率的建议等方面进行详细阐述。
一、纱厂细纱断头的原因1.原料因素:棉花、羊毛等纤维品质不佳,纤维强力低,容易导致细纱断头。
2.设备因素:纺织设备磨损、部件松动、皮带跑偏等,会影响细纱的正常生产。
3.工艺因素:纱线捻度、纱线规格、纺纱速度等工艺参数设置不合理,容易导致细纱断头。
4.环境因素:车间温湿度不适宜、尘埃过多,会影响细纱的生产。
二、千锭时断头表的作用1.实时监测:千锭时断头表可以实时监测细纱生产过程中的断头情况,为生产管理人员提供准确的断头数据。
2.数据分析:通过对断头数据的分析,可以找出断头的主要原因,为生产改进提供依据。
3.预警功能:当断头率异常时,千锭时断头表可以发出预警信号,提醒生产人员及时处理。
三、解决细纱断头问题的方法1.优化原料:选用优质原料,提高纤维品质。
2.设备维护:定期对纺织设备进行维护和检修,确保设备正常运行。
3.调整工艺:根据实际情况,合理设置纱线捻度、规格和纺纱速度等工艺参数。
4.改善车间环境:控制车间温湿度,加强尘埃治理。
四、提高生产效率的建议1.加强生产管理:通过数据分析,制定科学的生产计划,提高生产效率。
2.培训操作人员:提高操作人员的技能水平,降低人为因素对生产的影响。
3.创新技术:引进先进的纺纱技术,提高纱线质量。
4.设备更新:逐步淘汰落后设备,更新为高效、智能的纺织设备。
总之,纱厂细纱千锭时断头表在解决细纱断头问题方面具有重要作用。
通过对生产过程中的断头情况进行实时监测和分析,有助于找出问题的根源,从而采取针对性的措施降低断头率,提高生产效率。
细纱断头原因分析及降低细纱断头的措施【最新版】
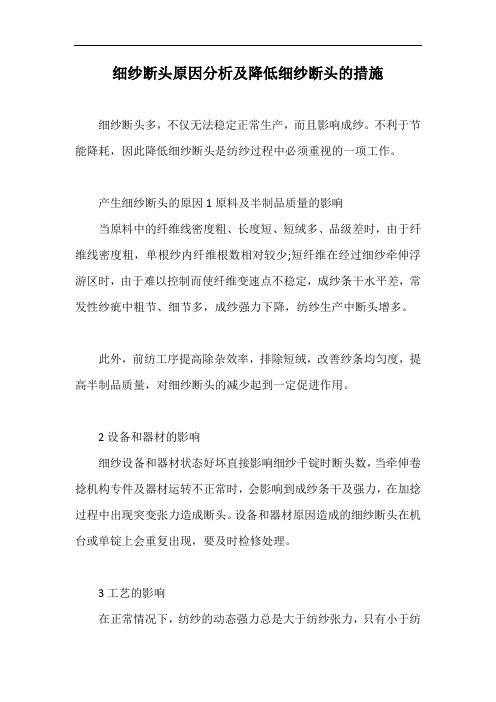
细纱断头原因分析及降低细纱断头的措施细纱断头多,不仅无法稳定正常生产,而且影响成纱。
不利于节能降耗,因此降低细纱断头是纺纱过程中必须重视的一项工作。
产生细纱断头的原因1原料及半制品质量的影响当原料中的纤维线密度粗、长度短、短绒多、品级差时,由于纤维线密度粗,单根纱内纤维根数相对较少;短纤维在经过细纱牵伸浮游区时,由于难以控制而使纤维变速点不稳定,成纱条干水平差,常发性纱疵中粗节、细节多,成纱强力下降,纺纱生产中断头增多。
此外,前纺工序提高除杂效率,排除短绒,改善纱条均匀度,提高半制品质量,对细纱断头的减少起到一定促进作用。
2设备和器材的影响细纱设备和器材状态好坏直接影响细纱千锭时断头数,当牵伸卷捻机构专件及器材运转不正常时,会影响到成纱条干及强力,在加捻过程中出现突变张力造成断头。
设备和器材原因造成的细纱断头在机台或单锭上会重复出现,要及时检修处理。
3工艺的影响在正常情况下,纺纱的动态强力总是大于纺纱张力,只有小于纺纱张力、特别是突变张力时,才会产生断头。
影响纺纱张力的最大因素是锭速,所以锭速应合理。
在锭速合理稳定的前提下,纺纱张力一般用钢丝圈重量来调节,即围绕稳定气圈张力来调节。
另外,由于成纱强力对断头影响较大,因此应围绕改善条干均匀度、提高成纱强力来调整工艺参数、工艺部件,达到降低断头的目的。
4运转操作的影响细纱工序操作因素造成断头的主要原因有:①各牵伸部位及纱线通道飞花附入;②吸棉眼堵塞不及时清理;③粗纱包卷接头不合格;④值车工巡回不及时,产生空粗纱;⑤钢丝圈换错号,特别是两品种交界处机台用错。
操作因素造成的细纱断头一般分散出现在单岗位、单锭上,操作技术差的不熟练者易产生。
5温湿度的影响温湿度与细纱大面积生活和成纱质量关系较大。
在纺纱过程中,纤维处于放湿状态,生活相对好做;而吸湿状态的水分易吸附在纤维表面,产生绕胶辊、缠罗拉等问题。
细纱车间温度一般控制在22 ℃~32 ℃,相对湿度一般控制在55%~62%。
【技术】降低细纱断头,大、中、小纱阶段断头多各应如何处理?
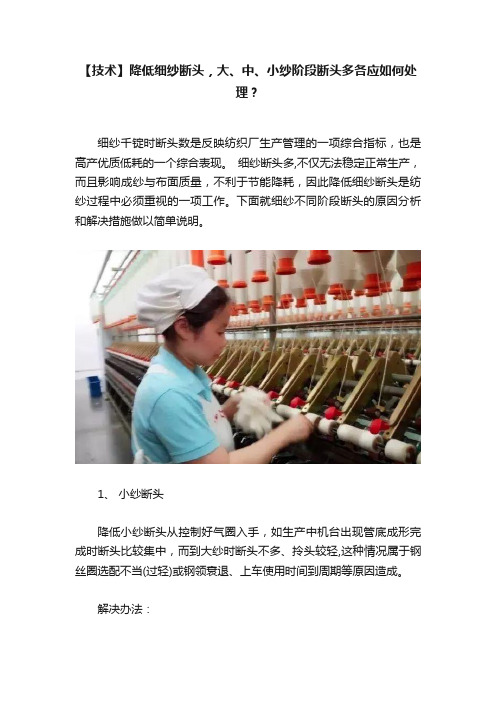
【技术】降低细纱断头,大、中、小纱阶段断头多各应如何处
理?
细纱千锭时断头数是反映纺织厂生产管理的一项综合指标,也是高产优质低耗的一个综合表现。
细纱断头多,不仅无法稳定正常生产,而且影响成纱与布面质量,不利于节能降耗,因此降低细纱断头是纺纱过程中必须重视的一项工作。
下面就细纱不同阶段断头的原因分析和解决措施做以简单说明。
1、小纱断头
降低小纱断头从控制好气圈入手,如生产中机台出现管底成形完成时断头比较集中,而到大纱时断头不多、拎头较轻,这种情况属于钢丝圈选配不当(过轻)或钢领衰退、上车使用时间到周期等原因造成。
解决办法:
(1)结合实际调重钢丝圈;
(2)调换钢领;
(3)适当放低叶子板三角铁以缩小气圈膨胀问题;
(4)检修工及时处理歪锭子、歪隔纱板等。
2 、中大纱断头
如生产机台小纱断头正常,而大纱断头较高,气圈比较平直、弹性小、拎头重,这种现象是属于钢丝圈与钢领之间摩擦力较大,不配套;卷捻部件运转不良或纱条通道起槽、不光洁等造成。
解决办法:
(1)调轻钢丝圈号数;
(2)调换钢丝圈型号,减小纺纱摩擦力;
(3)适当抬高叶子板三角铁,调整大纱时气圈高度,降低断头;
(4)调换起槽卷绕部件,如导纱钩等。
总之,细纱断头与配棉、半制品质量、纺纱器材、工艺、设备、运转操作及温湿度等因素有关。
降低细纱断头的主攻方向是控制气圈、稳定张力、改善纱条均匀度、提高单纱强力、降低强力不匀,尤其是
减少张力突变和强力薄弱环节,才能达到降低断头、提高成纱、布面质量及节能降耗的预期效果。
紧密纺减少细纱工序断头的措施
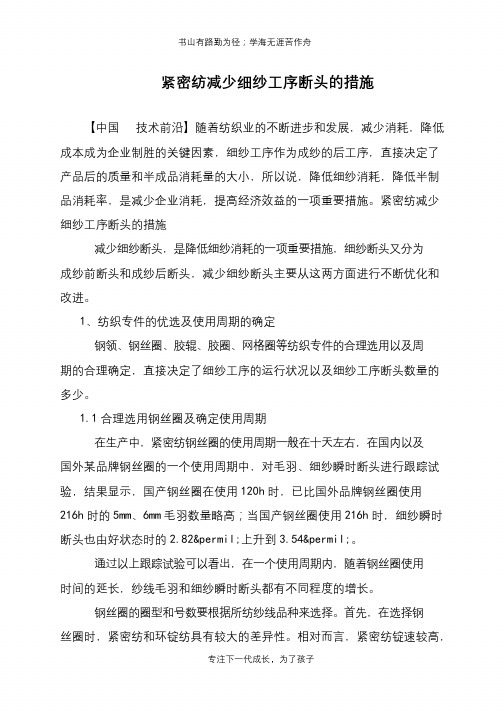
书山有路勤为径;学海无涯苦作舟
紧密纺减少细纱工序断头的措施
【中国技术前沿】随着纺织业的不断进步和发展,减少消耗,降低
成本成为企业制胜的关键因素,细纱工序作为成纱的后工序,直接决定了
产品后的质量和半成品消耗量的大小,所以说,降低细纱消耗,降低半制
品消耗率,是减少企业消耗,提高经济效益的一项重要措施。
紧密纺减少
细纱工序断头的措施
减少细纱断头,是降低细纱消耗的一项重要措施,细纱断头又分为
成纱前断头和成纱后断头,减少细纱断头主要从这两方面进行不断优化和
改进。
1、纺织专件的优选及使用周期的确定
钢领、钢丝圈、胶辊、胶圈、网格圈等纺织专件的合理选用以及周
期的合理确定,直接决定了细纱工序的运行状况以及细纱工序断头数量的
多少。
1.1合理选用钢丝圈及确定使用周期
在生产中,紧密纺钢丝圈的使用周期一般在十天左右,在国内以及
国外某品牌钢丝圈的一个使用周期中,对毛羽、细纱瞬时断头进行跟踪试
验,结果显示,国产钢丝圈在使用120h时,已比国外品牌钢丝圈使用
216h时的5mm、6mm毛羽数量略高;当国产钢丝圈使用216h时,细纱瞬时断头也由好状态时的2.82‰上升到3.54‰。
通过以上跟踪试验可以看出,在一个使用周期内,随着钢丝圈使用
时间的延长,纱线毛羽和细纱瞬时断头都有不同程度的增长。
钢丝圈的圈型和号数要根据所纺纱线品种来选择。
首先,在选择钢
丝圈时,紧密纺和环锭纺具有较大的差异性。
相对而言,紧密纺锭速较高,
专注下一代成长,为了孩子。
细纱机断头原因分析及解决措施1

细纱机断头原因分析及解决措施细纱断头是生产中最主要的疵点,它直接影响高产、优质、低耗,是提高生产效率的障碍。
在日常生产中细纱断头增多,往往是质量波动的信号。
细纱机断头的原因同样也是多方面的,下面我从几个方面作简要分析:1、开车断头。
造成开车断的主要原因有:齿轮咬合过紧、过松,部分齿轮键销不配套,机架变形、主轴振动等,最主要的原因还是停车位置不当,以EJM128K型细纱机为例,最佳位置应是钢领板上升位置以龙筋至钢领板上部为9cm为宜(也可成形桃盘最高点偏转子中心2cm)。
开车时钢领板下降则断头大大减少,是钢领板上升时断头数的1∕3左右,必须调好三自动与刹车位置来确保开车断头降低。
2、整台车全部断头。
车头传动齿轮咬合不良、脱开或损坏,大轴联轴器未紧好,车头内齿形带磨损或断裂,成形部分机件损坏,牵伸部分、级升部分机件损坏使钢领板急速下降,车头主链条断裂等。
3、一面或部分断头。
牵伸变换齿轮轴上缺键,罗拉头断裂,中、后罗拉头齿轮啮合不良或松开,导纱动程过大纱条全部跑出皮辊边缘,顶钢领板,主轴联轴器松脱,牵吊带断裂等。
4、个别锭子断头。
锭子歪、麻手、缺油跳动,钢领、钢丝圈不配套,钢领、钢丝圈超期使用,导纱钩起槽,气圈偏等。
因此,降低细纱断头始终是我们纺纱生产需要解决的首要问题,下面根据自己的工作经验讲一下降低断头的几种方法:一、保证车头蜗轮箱等卷绕机构的良好运转。
记得2005年、2006年期间,八纺细纱蜗轮箱坏的比较多,当时安装才一年多,也不缺油,但打顿的、磨损的就很多了。
后来还是一位叫孙小港的师傅把问题给解决了。
原来,钢领板、叶子板等加捻卷绕部件的重量由蜗轮箱、车头内扭簧链条共同承担。
当时扭簧链条调节的很松,钢领板摇起来很费力,相对而言蜗轮箱承受的力大了,就比较容易坏。
找出原因后,孙师傅和我把扭簧链条调节块调成大约90度,接近于竖直状态。
钢领板摇起来几乎不费力,蜗轮箱承受的力小了,直到现在八纺的蜗轮箱也基本上不坏,断头也少了。
细纱断头的原因及解决方法
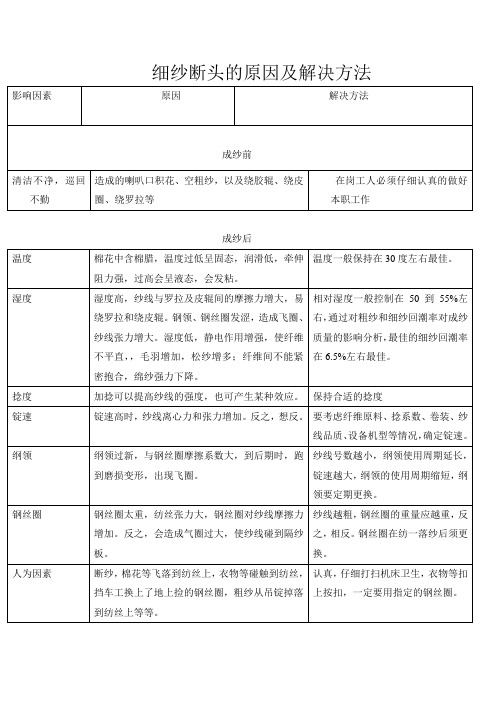
影响因素
原因
解决方法
成纱前
清洁不净,巡回不勤
造成的喇叭口积花、空粗纱,以及绕胶辊、绕皮圈、绕罗拉等
在岗工人必须仔细认真的做好本职工作
成纱后
温度
棉花中含棉腊,温度过低呈固态,润滑低,牵伸阻力强,过高会呈液态,会发粘。温度一般持在30度左右最佳。湿度
湿度高,纱线与罗拉及皮辊间的摩擦力增大,易绕罗拉和绕皮辊。钢领、钢丝圈发涩,造成飞圈、纱线张力增大。湿度低,静电作用增强,使纤维不平直,,毛羽增加,松纱增多;纤维间不能紧密抱合,绵纱强力下降。
认真,仔细打扫机床卫生,衣物等扣上按扣,一定要用指定的钢丝圈。
相对湿度一般控制在50到55%左右,通过对粗纱和细纱回潮率对成纱质量的影响分析,最佳的细纱回潮率在6.5%左右最佳。
捻度
加捻可以提高纱线的强度,也可产生某种效应。
保持合适的捻度
锭速
锭速高时,纱线离心力和张力增加。反之,想反。
要考虑纤维原料、捻系数、卷装、纱线品质、设备机型等情况,确定锭速。
纲领
纲领过新,与钢丝圈摩擦系数大,到后期时,跑到磨损变形,出现飞圈。
纱线号数越小,纲领使用周期延长,锭速越大,纲领的使用周期缩短,纲领要定期更换。
钢丝圈
钢丝圈太重,纺丝张力大,钢丝圈对纱线摩擦力增加。反之,会造成气圈过大,使纱线碰到隔纱板。
纱线越粗,钢丝圈的重量应越重,反之,相反。钢丝圈在纺一落纱后须更换。
人为因素
断纱,棉花等飞落到纺丝上,衣物等碰触到纺丝,挡车工换上了地上捡的钢丝圈,粗纱从吊锭掉落到纺丝上等等。
细纱开车断头原因及解决方法
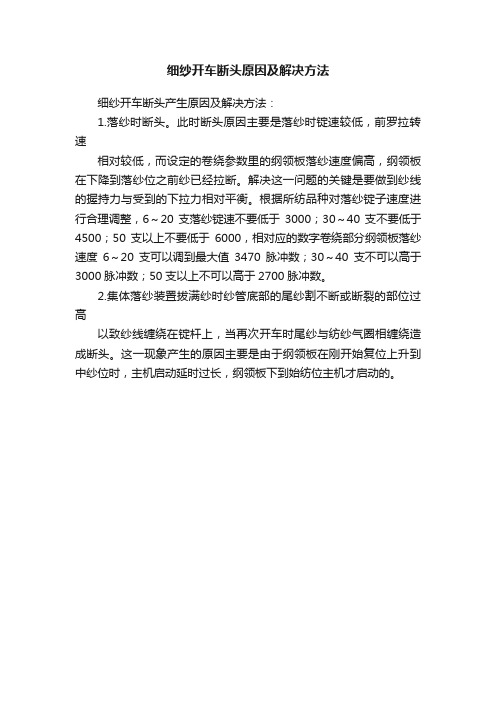
细纱开车断头原因及解决方法
细纱开车断头产生原因及解决方法:
1.落纱时断头。
此时断头原因主要是落纱时锭速较低,前罗拉转速
相对较低,而设定的卷绕参数里的纲领板落纱速度偏高,纲领板在下降到落纱位之前纱已经拉断。
解决这一问题的关键是要做到纱线的握持力与受到的下拉力相对平衡。
根据所纺品种对落纱锭子速度进行合理调整,6~20支落纱锭速不要低于3000;30~40支不要低于4500;50支以上不要低于6000,相对应的数字卷绕部分纲领板落纱速度6~20支可以调到最大值3470脉冲数;30~40支不可以高于3000脉冲数;50支以上不可以高于2700脉冲数。
2.集体落纱装置拔满纱时纱管底部的尾纱割不断或断裂的部位过高
以致纱线缠绕在锭杆上,当再次开车时尾纱与纺纱气圈相缠绕造成断头。
这一现象产生的原因主要是由于纲领板在刚开始复位上升到中纱位时,主机启动延时过长,纲领板下到始纺位主机才启动的。
技术细纱断头的原因和防治(下)
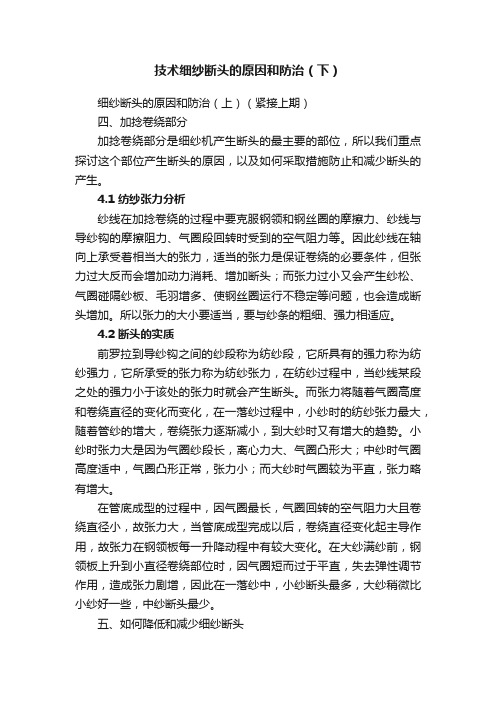
技术细纱断头的原因和防治(下)细纱断头的原因和防治(上)(紧接上期)四、加捻卷绕部分加捻卷绕部分是细纱机产生断头的最主要的部位,所以我们重点探讨这个部位产生断头的原因,以及如何采取措施防止和减少断头的产生。
4.1 纺纱张力分析纱线在加捻卷绕的过程中要克服钢领和钢丝圈的摩擦力、纱线与导纱钩的摩擦阻力、气圈段回转时受到的空气阻力等。
因此纱线在轴向上承受着相当大的张力,适当的张力是保证卷绕的必要条件,但张力过大反而会增加动力消耗、增加断头;而张力过小又会产生纱松、气圈碰隔纱板、毛羽增多、使钢丝圈运行不稳定等问题,也会造成断头增加。
所以张力的大小要适当,要与纱条的粗细、强力相适应。
4.2 断头的实质前罗拉到导纱钩之间的纱段称为纺纱段,它所具有的强力称为纺纱强力,它所承受的张力称为纺纱张力,在纺纱过程中,当纱线某段之处的强力小于该处的张力时就会产生断头。
而张力将随着气圈高度和卷绕直径的变化而变化,在一落纱过程中,小纱时的纺纱张力最大,随着管纱的增大,卷绕张力逐渐减小,到大纱时又有增大的趋势。
小纱时张力大是因为气圈纱段长,离心力大、气圈凸形大;中纱时气圈高度适中,气圈凸形正常,张力小;而大纱时气圈较为平直,张力略有增大。
在管底成型的过程中,因气圈最长,气圈回转的空气阻力大且卷绕直径小,故张力大,当管底成型完成以后,卷绕直径变化起主导作用,故张力在钢领板每一升降动程中有较大变化。
在大纱满纱前,钢领板上升到小直径卷绕部位时,因气圈短而过于平直,失去弹性调节作用,造成张力剧增,因此在一落纱中,小纱断头最多,大纱稍微比小纱好一些,中纱断头最少。
五、如何降低和减少细纱断头主要是降低和减少成纱后断头,即加捻卷绕部分的工作。
既然当纺纱张力大于纺纱强力时就会产生断头,那我们首先就应该提高纱线的强力,但这会受到原料和成本等各方面因素的制约,不过我们可以从提高纱线的平均强力和减少纱线的强力弱环着手,尽可能降低纺纱的平均张力,使纺纱强力与纺纱张力的差值加大,以减少纺纱张力波动的波峰和纱线强力波动的波谷的交叉点数。
下落细纱机开车断头的办法[详解]
![下落细纱机开车断头的办法[详解]](https://img.taocdn.com/s3/m/887da893b8d528ea81c758f5f61fb7360b4c2b1c.png)
降低细纱机开车断头的措施前言细纱机开车断头是一个反映细纱机整体状态的综合体现。
机台运转不良、断头较多、各项工艺调整不当、专件使用管理情况、配棉成分以及操作水平等等,都是影响细纱机开车断头的主要原因,最终导致增加浪费、增加劳动强度、生产效率下降。
为了攻关此项技术难题,从设备的细小环节着手、合理的理论为基础,采取了相应的技术措施,经过反复试验,在降低细纱机开车断头方面取得了一定成效一、开车断头的形成:细纱机落纱后开车始纺时,钢领板处于始纺阶段的位置较低,此时纺纱段气圈长度较长,纱线运动离心力较大,纺纱张力最大,而且开车瞬间钢丝圈从静止状态在无缓冲的基础上,瞬间高速运转,致使纱线张力有无张力突然增至最大,当纱线的张力大与强力时,就造成开车的瞬间产生较多的断头,通常称为开车断。
二、影响细纱机开车断头的因素1、原料的选配:原料的好坏是纱线质量好坏的决定因素,等级、纤维长度、细度、含糖等因素,直接影响所纺纱线的强力和弹性,原棉中的短纤维含量较多时则纺出的纱线强力低、弹性差,并且短纤维容易附着在钢丝圈上,增加了钢丝圈上不必要的重量,使钢丝圈的回转不稳定,严重时锲死,从而大大增加开车断头。
2、温湿度的影响:细纱车间对温湿度的要求比较严格,当相对温湿度低时,纤维抱合力差,短纤维外露,造成纱线强力低,严重时造成断头。
当相对温湿度高时,,致使钢领发涩、钢丝圈挂花回转不稳定,严重时钢丝圈呆滞、锲死,直接造成断头,所以说车间内部要根据各品种的分布区域,合理控制好温湿度,来提高质量、减少断头。
3、器材方面的原因分析3.1 钢领的使用情况非常关键:当钢领上车使用6个月后,该钢领到了衰退期,内跑道毛糙,致使钢丝圈在运行时与钢领的摩擦系数过大,使纱线张力过大,严重影响断头。
3.2 钢丝圈重量与纺纱张力的关系:钢丝圈重量过重,使气圈夹角较小,易碰筒管头,且在纱线的瞬间启动时,产生的阻力大,增加了纱线的卷绕张力,当卷绕张力大于纱线强力的时候就造成断头。
降低细纱断头的技术与管理措施
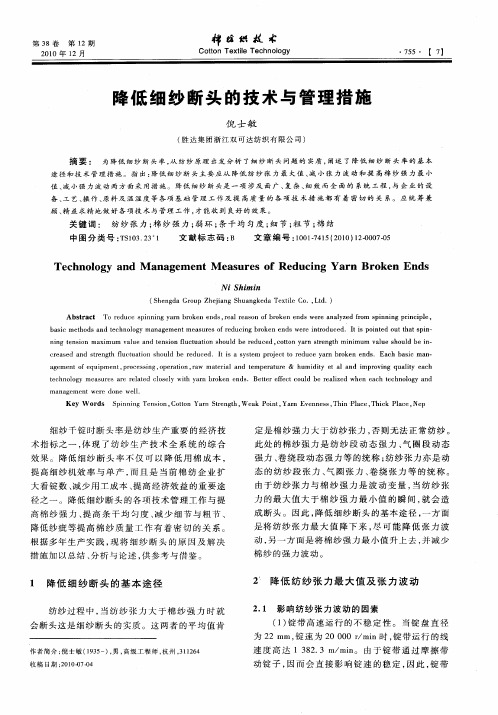
第 3 8卷 第 1 2期 21 0 0年 l 2月
的 品质 、 行状 态对 纺纱 张力 波动有 较大 的影 响 。 运 ( ) 子高 速转 动 的不稳 定 性 0锭 子 高 速 回 2锭
微 振 ; 期 检验 校 准 锭杆 、 盘 的偏断头率, 从纺纱原理 出发分析 了细纱断头问题 的 实质 , 阐述 了降低 细纱断 头率的基本
途 径 和 技 术 管理 措 施 。指 出 : 降低 细 纱 断 头主 要 应 从 降 低 纺 纱 张 力 最 大值 、 小 张 力 波 动 和 提 高棉 纱 强 力 最 小 减
成 断 头 。 因 此 , 低 细 纱 断 头 的 基 本 途 径 , 方 面 降 一
降低纱 疵等 提高 棉 纱 质 量 工作 有 着密 切 的关 系 。
根 据多 年生 产实 践 , 将 细 纱 断 头 的原 因及 解 决 现 措施 加 以总结 、 析与论 述 , 分 供参 考 与借鉴 。
作 者 简介 : 士 敏 ( 9 5 ) 男 , 级 工 程 师 , 州 , 1 2 4 倪 13 一 , 高 杭 3 16 收稿 日期 :0 0 -4 2 1  ̄70
2 降 低 纺 纱 张 力最 大值 及 张 力 波 动 、
2 1 影 响 纺 纱 张 力 波 动 的 因 素 .
( ) 带高 速运 行 的不 稳 定 性 。 当锭 盘 直 径 1锭
长度 、 力正 常 , 可 烂边 、 状 , 可 沾 油污 、 张 不 绞 不 积 纤 维 , 可 与锭 盘 边 、 盘 边 摩 擦 , 头 不 可 厚 、 不 滚 接 硬 , 行 不 可跳 动 ; 带 盘表 面和 轴 承不 可磨 损 , 运 锭 轴承 定 期 清洁 , 可 有硬 化 油 垢 , 不 回转 不 可 跳 动 、
细纱机牵伸区断头原因分析与解决措施

细纱机牵伸区断头原因分析与解决措施⽂/徐学尹中国纱线⽹细纱机断头概括起来主要有三种类型:即喂⼊部分断头、牵伸部分断头、加捻卷绕部分断头。
影响牵伸部分断头的因素主要为:原料与温湿度、⼯艺配置、设备专件状态、清洁操作,⽽细纱牵伸区断头的实质基本是须条在牵伸过程中所受到牵伸⼒⼤于钳⼝握持⼒造成。
下⾯我们具体讨论细纱牵伸区断头的原因:⼀、原料与⼯艺(⼀)原料与温湿度对断头的影响:1、原料⽅⾯:1.1 化纤及混纺纱:由于不同的化学纤维(这⾥以38mm棉型化纤为例),由于摩擦系数和纤维表⾯结构不同、纤维细度不同,在⽣产中主要表现为牵伸不开的断头。
解决措施:适当降低粗纱捻系数、增⼤细纱罗拉隔距、增⼤细纱后区牵伸倍数或使⽤偏⼤⼀些的隔距块。
1.2 纯棉纱:由于棉纤维长度整齐度和马值⼤⼩差异⼤造成的断头,⼀般体现为两⽅⾯:①粗节多或牵伸不开断头,②细节多,纱线弱强多断头。
解决措施:减⼩或增⼤粗纱捻系数、调整细纱罗拉隔距和后区牵伸倍数等。
2、温湿度对断头的影响2.1 ⼀般温度⾼⼀些,湿度偏⼤⼀点,能更好发挥⽪辊⽪圈等专件的控制,利于牵伸顺利进⾏,纤维回潮偏⼤,纱线柔软耐摩擦,断头会有所降低。
2.2 温度⾼、湿度低时,飞花增加,纱线⽑⽻增⼤,纱线变得⼲脆,断头会增加。
2.3 当温湿度变化波动剧烈,区域性差异⼤时,尤其是靠车间的边车机台,长时间停车(温度低、湿度⼤、胶辊胶圈发硬发挺),区域性空⽓流通不顺畅的机台、地⾯上⽔过多的机台更容易出现牵伸不良断头多问题。
(⼆)⼯艺配置对断头的影响⼯艺配置不合理造成的细纱断头与其他原因断头有明显的区别,断头规律主要表现为①断头锭位不固定,⽆规律可循,②⼤⾯积机台⽣活难做,断头多;③断头多为牵伸不良的短粗节或瞬时吐粗纱。
⼯艺配置不良造成的牵伸原因主要有以下⼏种:1、粗纱捻系数过⼤,造成细纱牵伸⼒增加⽽牵伸不开;可以适当降低粗纱捻系数。
2、粗纱定量太重,主牵伸区的上下⽪圈钳⼝和前⽪辊钳⼝难以有效控制;适当降低粗纱定量或者调整细纱牵伸⼯艺参数来适应重定量粗纱的顺利牵伸。
降低集落细纱长车落纱断头的生产实践

降低集落细纱长车落纱断头的生产实践由于集落细纱长车在生产过程中需要将纱线从一个轴上绕到另一个轴上,同时需要经过多次穿越旋转的筒体,因此容易出现落纱断头的情况。
为了解决这一问题,我们进行了以下的生产实践探究。
一、加强设备维护集落细纱长车需要经常保养清洁,特别是轴承部分。
因为如果轴承磨损或者缺乏润滑就容易出现车子抖动或者纱线卡顿的情况,进而造成落纱断头。
因此我们应该在生产前对设备进行彻底的清洁和维护工作。
二、优化车速调整方案纤维筒体的旋转速度也是影响落纱断头的一个关键因素,因此我们需要对车速进行精确的调整。
具体地说,应该根据纱线的细密程度、粘度以及轴距的长度,合理安排车速的大小和加速度,减少车速改变的频率。
同时,应该及时观察车速的变化情况,以便进行调整,确保纱线在生产过程中始终处于稳定的状态。
三、加强操作技能培训落纱断头也有可能是由操作人员的技能不足或者动作不够轻柔引起的。
因此工厂应该定期进行操作技能培训,教授正确的操作方法和技巧,加强操作员的意识和技能水平。
另外,为了确保生产稳定,应该通过实际操作和模拟实验,让操作员更加熟练掌握操作技巧,提高操作效率。
四、增强质量管理意识落纱断头除了对生产效率造成的影响外,还会导致纱线质量下降,进而影响整个产品的质量。
因此我们需要加强质量管理意识,严格把控纱线的质量,加强质检过程,确保产品达到国家标准。
综上所述,降低集落细纱长车落纱断头的问题需要加强设备维护、优化车速调整方案、加强操作技能培训和增强质量管理意识,通过这些措施的实施可以有效降低落纱断头的发生率,提高生产效率和产品质量。
降低细纱断头率的措施
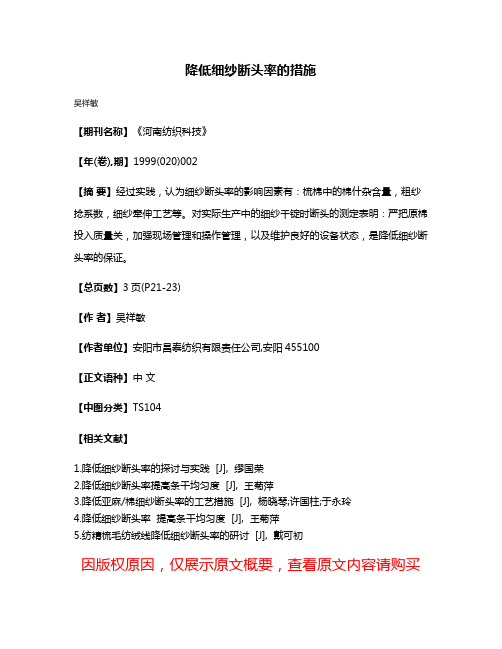
降低细纱断头率的措施
吴祥敏
【期刊名称】《河南纺织科技》
【年(卷),期】1999(020)002
【摘要】经过实践,认为细纱断头率的影响因素有:梳棉中的棉什杂含量,粗纱捻系数,细纱牵伸工艺等。
对实际生产中的细纱千锭时断头的测定表明:严把原棉投入质量关,加强现场管理和操作管理,以及维护良好的设备状态,是降低细纱断头率的保证。
【总页数】3页(P21-23)
【作者】吴祥敏
【作者单位】安阳市昌泰纺织有限责任公司,安阳455100
【正文语种】中文
【中图分类】TS104
【相关文献】
1.降低细纱断头率的探讨与实践 [J], 缪国荣
2.降低细纱断头率提高条干均匀度 [J], 王菊萍
3.降低亚麻/棉细纱断头率的工艺措施 [J], 杨晓琴;许国柱;于永玲
4.降低细纱断头率提高条干均匀度 [J], 王菊萍
5.纺精梳毛纺绒线降低细纱断头率的研讨 [J], 戴可初
因版权原因,仅展示原文概要,查看原文内容请购买。
天门纺机·纺织帮|小粗纱(约3-4层)在细纱退绕断头多的解决办法
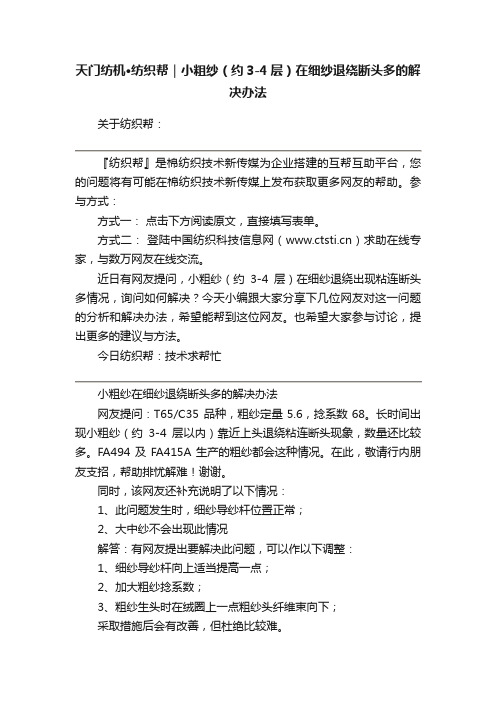
天门纺机·纺织帮|小粗纱(约3-4层)在细纱退绕断头多的解决办法关于纺织帮:『纺织帮』是棉纺织技术新传媒为企业搭建的互帮互助平台,您的问题将有可能在棉纺织技术新传媒上发布获取更多网友的帮助。
参与方式:方式一:点击下方阅读原文,直接填写表单。
方式二:登陆中国纺织科技信息网()求助在线专家,与数万网友在线交流。
近日有网友提问,小粗纱(约3-4层)在细纱退绕出现粘连断头多情况,询问如何解决?今天小编跟大家分享下几位网友对这一问题的分析和解决办法,希望能帮到这位网友。
也希望大家参与讨论,提出更多的建议与方法。
今日纺织帮:技术求帮忙小粗纱在细纱退绕断头多的解决办法网友提问:T65/C35 品种,粗纱定量5.6,捻系数68。
长时间出现小粗纱(约3-4层以内)靠近上头退绕粘连断头现象,数量还比较多。
FA494及FA415A生产的粗纱都会这种情况。
在此,敬请行内朋友支招,帮助排忧解难!谢谢。
同时,该网友还补充说明了以下情况:1、此问题发生时,细纱导纱杆位置正常;2、大中纱不会出现此情况解答:有网友提出要解决此问题,可以作以下调整:1、细纱导纱杆向上适当提高一点;2、加大粗纱捻系数;3、粗纱生头时在绒圈上一点粗纱头纤维束向下;采取措施后会有改善,但杜绝比较难。
另有观点认为:导纱杆可以调到粗纱管的1/3处,加大粗纱捻系数会影响细纱牵伸。
仔细观察粗纱拉断的地方,均在最后三,四层上部换向的地方,里层粗纱跑出来压住外层粗纱而拉断。
问题应该出在粗纱,调整粗纱的卷绕成型。
也有一位成功解决此问题的网友,分享了他们的经验:这个问题我月初刚解决,纺的是C/T80/20品种,了车时到两层左右粗纱上断,中大粗纱时退绕正常。
加大粗纱捻度和加大初始卷绕张力后完全解决。
不知你的配棉情况生产情况经验仅供参考,如果原料一般水平,68的捻系数加到78应该可以的,始纺到十层张力不可太小其后张力不可太大,不然外圈会嵌入里层造成退绕难,另外轴向卷绕密度也要注意是否合适,建议4.3圈每厘米左右。
细纱降低断头的发言稿
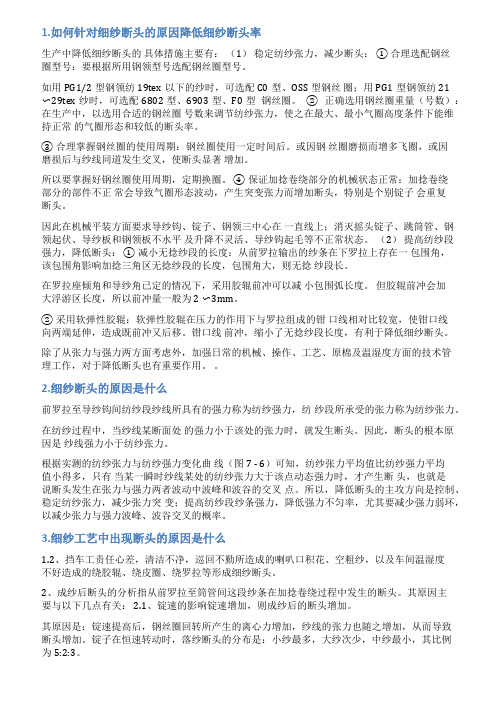
1.如何针对细纱断头的原因降低细纱断头率生产中降低细纱断头的具体措施主要有:(1)稳定纺纱张力,减少断头:①合理选配钢丝圈型号:要根据所用钢领型号选配钢丝圈型号。
如用PG1/2型钢领纺19tex以下的纱时,可选配C0型、OSS型钢丝圈;用PG1型钢领纺21〜29tex纱时,可选配6802型、6903型、F0型钢丝圈。
②正确选用钢丝圈重量(号数):在生产中,以选用合适的钢丝圈号数来调节纺纱张力,使之在最大、最小气圈高度条件下能维持正常的气圈形态和较低的断头率。
③合理掌握钢丝圈的使用周期:钢丝圈使用一定时间后。
或因钢丝圈磨损而增多飞圈,或因磨损后与纱线同道发生交叉,使断头显著增加。
所以要掌握好钢丝圈使用周期,定期换圈。
④保证加捻卷绕部分的机械状态正常:加捻卷绕部分的部件不正常会导致气圈形态波动,产生突变张力而增加断头,特别是个别锭子会重复断头。
因此在机械平装方面要求导纱钩、锭子、钢领三中心在一直线上;消灭摇头锭子、跳筒管、钢领起伏、导纱板和钢领板不水平及升降不灵活、导纱钩起毛等不正常状态。
(2)提高纺纱段强力,降低断头:①减小无捻纱段的长度:从前罗拉输出的纱条在下罗拉上存在一包围角,该包围角影响加捻三角区无捻纱段的长度,包围角大,则无捻纱段长。
在罗拉座倾角和导纱角已定的情况下,采用胶辊前冲可以减小包围弧长度。
但胶辊前冲会加大浮游区长度,所以前冲量一般为 2 〜3mm。
②采用软弹性胶辊:软弹性胶辊在压力的作用下与罗拉组成的钳口线相对比较宽,使钳口线向两端延伸,造成既前冲又后移。
钳口线前冲,缩小了无捻纱段长度,有利于降低细纱断头。
除了从张力与强力两方面考虑外,加强日常的机械、操作、工艺、原棉及温湿度方面的技术管理工作,对于降低断头也有重要作用。
2.细纱断头的原因是什么前罗拉至导纱钩间纺纱段纱线所具有的强力称为纺纱强力,纺纱段所承受的张力称为纺纱张力。
在纺纱过程中,当纱线某断面处的强力小于该处的张力时,就发生断头。
- 1、下载文档前请自行甄别文档内容的完整性,平台不提供额外的编辑、内容补充、找答案等附加服务。
- 2、"仅部分预览"的文档,不可在线预览部分如存在完整性等问题,可反馈申请退款(可完整预览的文档不适用该条件!)。
- 3、如文档侵犯您的权益,请联系客服反馈,我们会尽快为您处理(人工客服工作时间:9:00-18:30)。
降低细纱断头率的注意点和措施降低细纱千锭时断头率的工作是纺纱工程中主要技术任务之一,降低细纱断头的技术途径就是降低纺纱张力波动,增加纺纱强力减少弱节。
降低细纱断头率的注意点和主要措施为:一、细纱机关键零部件的改进和正确的机械保养。
1、用好变频调速器,小纱和大纱时适当降速,因为小纱时气圈高度较大,张力大,断头最集中;中纱时气圈较稳定,断头少;大纱时气圈张力虽较小,但气圈较短,遇张力变化缺乏缓冲,断头比中纱要高些。
2、加捻卷绕机构的保养①在平车交接时严格检査卷绕机构的整体机械性能。
首先是钢领板、气圈环、叶子板三者运行的相对位置要正确,并且要校正气圈,防止气圈歪斜。
②定期专门敲锭子、捉坏气圈,严格用吊锤校正导纱钩、钢领、锭子三者中心一线。
③挡车工和机工密切配合好,对断头多的锭子作记号,做到及时发现及时修理。
④统一断头原因检査方法:—看:看锭子是否摇头,看钢领、锭子和导纱钩三者中心是否一线。
二査:査导纱钩是否起槽,查钢领油线是否短缺、油槽是否缺油。
査油线是否勾钢丝圈。
三摸:摸钢领是否松动,摸钢领是否有波纹磨损、钢领的发毛程度。
⑤锭子:首先严格锭杆锭脚的配套,上板眼的作法是锭杆锭脚“一对”配套,不允许混配。
其次是严格执行专件完好标准:锭脚偏弯小于0.02mm,锭盘偏心在0.03mm 以下,锭尖无明显磨损,锭子摇头振幅小于0.05mm,锭子不下沉,无缺损件、无锈斑、回转灵活。
钢领:选用质量好的钢领。
对新旧钢领都要毎只检查,圆整度小于0.25mm,平整度低于0.15mm,高低度士0.15mm,呈银灰色表面无毛疵、砂痕。
有条件的话也可以考虑进行油煮处理,改善渗油性能。
3、牵伸机构的整修①罗拉牵伸装置中,影响细纱条干最为主要的因素是前罗拉和前皮辊组成的前钳口对纤维束握持的不稳定。
钳口握持力的不稳定在高牵伸倍数下会造成纤维变速点的不稳定。
影响前钳口握持力不稳定的因素中最主要的是罗拉偏心、皮辊偏心和皮辊包覆材料等。
要求前罗拉偏心在0.04mm内,中后罗拉偏心在0.06mm内。
②皮辊的影响往往是皮辊偏心、皮辊包覆村料压缩率差异和皮辊表面性能综合作用的结果。
皮辊一般三个月以后要酸处理一次,但几次下来硬度要偏高到92肖氏度,渐渐在老化。
可在细纱每个品种上机前或利用揩车之际进行皮辊酒精揩试,改善皮辊表面性能、减少酸处理次数。
对皮辊的使用还在于细化管理,不同尺寸不能混用。
③摇架:国产仿SKF摇架在实际使用中有“压力衰退”现象,影响了前钳口握持纤维引导力的波动,易造成纤维变速的不稳定而造成条干不匀和粗细节,使断头率上升。
要定期或不定期测定摇架压力情况、检査“压力衰退”程度,严重者更换新摇架,一般调换零部件进行整修重新安装,轻者在统一压力档次数字的基础上,在运行中通过后座处的调节螺丝调节到一致。
④皮圈上销和弧转托板,组成了前牵伸区的附加摩擦力界。
这一部分最易产生的缺陷是皮圈起拱打顿和上销两边压力不一致现象,为此采取以下措施:⑴不合格皮圈要剔除出来,各批皮圈编批号、不允许混用。
⑵皮圈打顿有一个原因是内圈摩擦力大小的缘故,因此要求高时要对内圈酸处理后磨砺,以增大皮圈和上销,皮圈和下罗拉、弹簧夹的摩擦力。
⑶经常检查弹簧夹弹力、防止弧形托扳在平车时造成表面变形。
⑷严格执行上销完好标准,注意上销、皮辊的安装性能。
二、合理选配原料,通过各种途径改善纺纱性能1、原料的成分和品质原料的成分和品质决定了同支数纱线有不同的强力,直接影响细纱断头。
据理论分析细纱断裂长度最低必须达到5.2千米,全毛品种、毛粘品种的断裂长度在6〜7千米左右,断头率120根/千锭时左右,而毛涤品种的强力要高出一倍,断头要低得多。
2、纺纱性能细纱截面根数不得少于35根这个极限值,“纺纱难”主要指在纺纱过程中绕皮辊绕罗拉而断头,有些品种绕皮辊罗拉断头占全部断头的40%左右。
①含油脂量:羊毛脂粘性较髙,生产时容易把纤维和罗拉皮辊粘绕在一起。
染缸复洗工序尽量洗去羊毛脂。
②毛条染色复洗效果:在大部分品种中,深色品种似乎总要较为难纺些,尤其是毛涤的深色品仲。
原因是染色牢度差、浮色严重,手感粗糙。
为此在毛条染色精复梳后的B306毛条要达到毛条松软滑的要求。
③和毛油和静电;和毛油是前纺工序中改善可纺性的有效办法,和毛油和抗静电剂的选择也较讲究,根据原料成分、回潮率、含量来选择,最终目的是提高纤维之间的抱合力、消除静电现象,使纺纱顺利断头率有所下降。
④回潮率:纱条回潮率过高易引起绕皮辊绕罗拉,回潮率过低又易引起静电飞毛造成飘头断头。
最好的方法就是预调湿。
一般毛纱的调湿平衡时间为12〜15小时,对粗纱来说,为了使粗纱在细纱机上纺纱时处于放湿状态,要给予一定程度的强制给湿,所以粗纱库的相对湿度要高一些,为75%~85%。
⑤贮存时间和疲劳恢复:在生产实践中,给予生毛球、粗纱一定的贮存时间,以利疲劳恢复,是极为有利于纺纱的顺利进行的,事实上当一些品种上机纺纱困难,就贮存几天再上机,纺纱明显改善。
生毛球的储存,全毛品种最好在3天以上,毛涤品种最好在6天以上;粗纱全毛至少要2天以上,毛涤需储存4天以上,急品另行考虑。
⑥车间温湿度调节:温湿度在规定范围内时对纺纱的影响是稳定的。
平时要多注意开冷车前的空调准备,以及通风道口设备的遮挡。
一般要求粗纱库湿度>前纺湿度>细纱湿度。
粗纱库的相对湿度保证不低于80%,最好在85%~90%。
三、改进工艺路线,优化工艺、提高成纱质量1、从工艺操作上提髙粗纱适纺质量根椐实践,粗纱适纺质量是:最佳的内在结构和外观状态及一定的粗纱条干水平。
当粗纱条干达到一定水平后,对细纱条干的影响并不显著。
造成粗纱状态和内在结构不理想的因素有:纤维伸直度低、毛粒、接头后遗症、纱条表面发毛、纱条中纤维的抱紧程度。
为此我们从工艺和操作上分别有侧重地强化:⑴进行针圈牙和两轻质辊重量档次的上机优选,保证条干水平;⑵防止轻质辊的偏心弯曲晃动和前皮辊加压不良,消除粗纱的周期性不匀;⑶严格检查针圈质量,使纤维在钢针良好的梳理下提高纤维伸直度,并减少粗纱内在的短片段不匀;⑷每次上机后对搓捻臂长、搓捻次数、搓皮板张力和隔距进行部分优选调整,以生产出状态良好的“光、圆、紧”粗纱;⑸严格前纺各道清洁工作,针板不允许缺针、断针和弯针,不允许沾油挂毛,针梳机前下罗拉绒板要2小时做一次清洁工作;粗纱机的毛刷和绒板要完好,位置要准确。
减少毛粒至最低程度;⑹B452和FB441的接头要严格控制质量,对接头长度要上机试验后选定,防止条干不匀和大肚纱等。
我们规定粗纱适纺质量(内控指标)为:条干CV%不超过7.2%,毛粒不超过1.5只/克,粗纱状态光圆紧,不允许表面发毛(不允许罗拉皮辊对纱条剥皮开车,皮辊不沾毛),内在结构好。
2、优选细纱工艺提高成纱质量优选的目的在于使粗纱以最佳状态进入皮圈牵伸区并保证以一个最理想的牵伸过程来产出最均匀的纤维束来。
我们认为:牵伸倍数、前罗拉加压、皮辊中凹、罗拉隔距和前隔距、后区牵伸等是影响细纱条干的五个主要因素。
①牵伸倍数:EJ519细纱机最佳牵伸范围是:全毛15倍左右,毛涤18倍左右(根据毛涤含量不同适当调整)。
纺纱设计时粗纱细纱总牵伸倍数可掌握全毛67.5倍,毛涤86.25倍左右,在粗纱3.75〜4.5倍范围内尽量选择较大的粗纱牵伸、较小的细纱牵伸。
②前罗拉加压:前罗拉加压对细纱条干的影响是很敏感的。
根椐试验对比,压力不足会马上影响生产、出现牵不开纺硬头或皱皮纱,压力过大不利于条干。
—般来说,全毛品种压力要比混纺品种小一档。
可以考虑纺全毛时压力放在1〜2档,即23、26.5公斤/双锭;纺毛涤时放在2〜3档,即26.5、30公斤/双锭;倒比例毛涤则放在3档压力上。
③皮辊中凹:皮辊中凹决定了皮圈滑溜槽深度,对皮圈后部摩擦力界强度有影响。
皮辊中凹过大,使纤维失控纺硬头;皮辊中凹过小,又使粗纱进入皮圈牵伸发生障碍而造成涌头或出现皱皮纱。
一般皮辊中凹选择根据原料性能和粗纱克重来选择,另外全毛品种中凹浅一些,混纺品种中凹深一些。
④罗拉隔距和前隔距,目前罗拉隔距一般都是110*90毫米。
罗拉隔距对细纱条干的影响较大,罗拉隔距应与纤维交叉长度相适应。
但由于罗拉隔距变动困难,故在大批量生产时,一般用隔距块来调节,以改善纤维运动规律,加强对短纤维的控制。
⑤后牵伸:EJ519细纱机后区牵伸是张力牵伸。
因为张力牵伸对细纱条干影响很大,且这种张力和粗纱克重、内在结构、外观状态有关,故应每批上机优选。
事实上同一台粗纱机上下来的粗纱在不同细纱机上最佳的后区牵伸值也有不同,这说明后区张力牵伸还跟皮圈有关系(实际上后区张力牵伸是指皮圈和后罗拉之间的牵伸)。
在进行工艺优选时,要考虑各因素的交互作用,尤其是牵伸倍数和前罗拉加压的共同作用对细纱条干的影响。
综上所述,我们在细纱工艺上除了牵伸倍数、罗拉隔距按工艺设计不变外,前罗拉加压、后区牵伸值、隔距块一般都要优选,这样优选实践的结果,细纱质量有了一定改观,细纱断头也降低了。
我们认为降低细纱断头率工作不仅是一项技术工作,而且是一项管理性极强的工作。
经过努力后千锭时断头率平均应稳定在60〜100根/千锭时左右,断头率合格率应达到85%以上。
大多数情况下,细纱断头是由于机械状态不理想和粗纱纺纱性能差的原因造成的。
因此最现实的办法是加强机械保养,改善可纺性。
至于如何进一步提高细纱条干、减少粗细节,从而降低断头,应加强我们的日常质量工作。
2016年10月21日。