挤压生产工艺记录表
挤压车间工艺操作规程

挤压车间⼯艺操作规程挤压车间⼯艺操作规程本规程规定了6063铝合⾦挤压型材⽣产的⼯艺要求。
挤压⼯艺流程:为关键⼯序控制点即为特殊⼯序⼜是关键⼯序控制点⽣产准备遵守挤压车间安全技术规程和设备使⽤维护规程。
1.按照挤压车间安全技术和设备使⽤维护规程,全⾯检查和润滑设备(如:加热炉、挤压机、冷却设备、牵引设备和冷床等),并经空⾏程运转,证明设备正常后,⽅能进⾏⽣产,在连续⽣产过程上,应认真交接班,仔细了解上班的⽣产、设备、⼯具、⼯艺和质量等情况。
2.各种规格型号的⼯模具(包括新产品的⼯模具),在正式投⼊⽣产前必须经过严格试模,经试模合格后⽅可使⽤,在连续⽣产中应根据氮化层的磨损情况及挤压⼯模具管理制度,对模具进⾏氮化处理。
3.检查所⽤挤压⼯具(模具、模垫、模套)的规格,型号尺⼨和表⾯质量是否符合质量和⼯艺要求。
4.铸棒装加热炉时必须依据随⾏卡规定的合⾦牌号、批号、规格、数量等进⾏认真检查,⽆误⽅能装炉,随⾏卡不得擅⾃更改,装炉时,记清熔次号。
5.为了保证产品质量,装炉前应将铸棒表⾯的油污、灰尘、碎屑及其它杂物清理⼲净,确保表⾯清洁。
6.铸锭的化学成份、低倍组织和表⾯质量应符合GB/T3190-96和YS67-93的规定,铸棒规格及使⽤范围应符合表⼀之规定:表⼀7.电⽓和仪表维修⼈员应认真检查铸棒加热炉、挤压筒加热器、模具加热炉和各种电器仪表是否完好。
8.挤压操纵⼿应认真检查与型材接触的⽯墨垫板,⽯墨辊、冷床的导辊、成品锯与型材接触是否完好,不完好的马上更换,以避免划伤制品表⾯。
⼀、装炉加热:1.铸棒装炉时,按照铸棒长度⼤⼩,可以在连续⽣产过程中装运双层或间断双层,但必须保证铸棒在炉内加热时间符合规定的要求,见表⼆。
2.装炉时,铸棒应摆放在转动链条的中部,防⽌转动时偏移或将链条压翻,装炉后要将炉门关好。
3.装炉后进⾏仪表定温,确保铸棒加热温度和加热时间符合表⼆的要求,并做好记录。
4.当铸棒加热温度达到5500C时,应取⾼倍试样检查是否过烧,过烧的铸棒应扒出作废。
铜排连续挤压生产线的工艺流程

铜排连续挤压生产线的工艺流程下载温馨提示:该文档是我店铺精心编制而成,希望大家下载以后,能够帮助大家解决实际的问题。
文档下载后可定制随意修改,请根据实际需要进行相应的调整和使用,谢谢!Download Tip: This document has been carefully written by the editor. I hope that after you download, they can help you solve practical problems. After downloading, the document can be customized and modified. Please adjust and use it according to actual needs. Thank you!铜排连续挤压生产线的工艺流程:①原料准备:选用符合规格要求的铜杆,进行表面清洁处理,去除油污和氧化层,确保材料质量。
②加热:将清理干净的铜杆送入连续加热炉中,采用感应或电阻加热方式均匀加热至适宜的塑性加工温度,一般在600°C~900°C之间。
③铸坯成型:加热后的铜杆通过连续铸造机,高压下高速挤出,形成初步形状的铜坯,此步骤可调整铜坯的截面尺寸和形状。
④挤压成型:铜坯随即进入挤压机,通过精密设计的模具,在强大压力作用下连续挤压变形,形成所需的铜排截面形状,如矩形、槽型等。
⑤冷却与拉伸:挤压出的铜排立即进行水冷或空气冷却,以固定其形状并提高机械性能。
随后,可能根据需要进行拉伸处理,改善内部晶粒结构,提升导电性和机械强度。
⑥矫直与切割:冷却后的铜排通过矫直机消除弯曲,保证直线度,然后根据指定长度由自动切割机切割成段。
⑦质量检验:对切割好的铜排进行尺寸、表面质量及电性能检测,确保产品符合相关标准和客户要求。
⑧包装与入库:合格的铜排经过防氧化处理后,进行打包密封,最后入库或直接发往客户。
挤压车间工艺操作规程模板
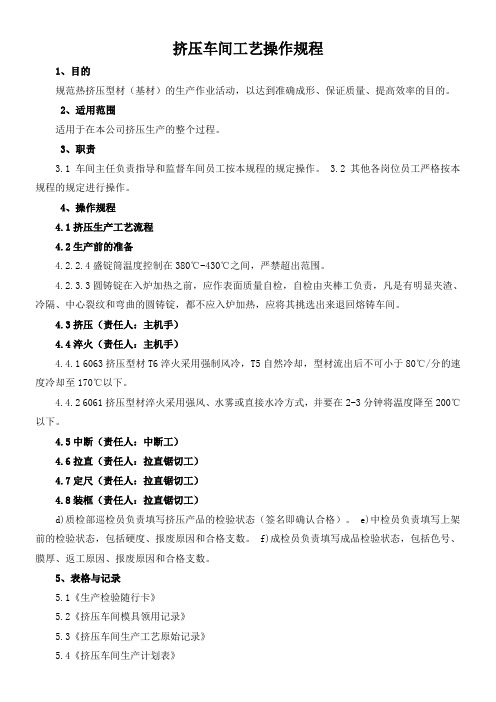
挤压车间工艺操作规程1、目的规范热挤压型材(基材)的生产作业活动,以达到准确成形、保证质量、提高效率的目的。
2、适用范围适用于在本公司挤压生产的整个过程。
3、职责3.1 车间主任负责指导和监督车间员工按本规程的规定操作。
3.2 其他各岗位员工严格按本规程的规定进行操作。
4、操作规程4.1挤压生产工艺流程4.2生产前的准备4.2.2.4盛锭筒温度控制在380℃-430℃之间,严禁超出范围。
4.2.3.3圆铸锭在入炉加热之前,应作表面质量自检,自检由夹棒工负责,凡是有明显夹渣、冷隔、中心裂纹和弯曲的圆铸锭,都不应入炉加热,应将其挑选出来退回熔铸车间。
4.3挤压(责任人:主机手)4.4淬火(责任人:主机手)4.4.1 6063挤压型材T6淬火采用强制风冷,T5自然冷却,型材流出后不可小于80℃/分的速度冷却至170℃以下。
4.4.2 6061挤压型材淬火采用强风、水雾或直接水冷方式,并要在2-3分钟将温度降至200℃以下。
4.5中断(责任人:中断工)4.6拉直(责任人:拉直锯切工)4.7定尺(责任人:拉直锯切工)4.8装框(责任人:拉直锯切工)d)质检部巡检员负责填写挤压产品的检验状态(签名即确认合格)。
e)中检员负责填写上架前的检验状态,包括硬度、报废原因和合格支数。
f)成检员负责填写成品检验状态,包括色号、膜厚、返工原因、报废原因和合格支数。
5、表格与记录5.1《生产检验随行卡》5.2《挤压车间模具领用记录》5.3《挤压车间生产工艺原始记录》5.4《挤压车间生产计划表》5.5《人工时效原始记录》5.6《挤压车间模具加温、铝棒交接班记录》5.7《挤压车间检验原始记录》。
铝型材挤压工艺操作规程

1、目的规范热挤压型材(基材)的生产作业活动,以达到准确成形、保证质量、提高效率的目的。
2、适用范围适用于在本公司挤压生产的整个过程。
3、职责3.1 车间主任负责指导和监督车间员工按本规程的规定操作。
3.2 其他各岗位员工严格按本规程的规定进行操作。
4、操作规程4.1挤压生产工艺流程图:垫应及时清除出车间,防止错用不合格的模具和模垫。
4.2.1.2派模工接到生产计划指令后,组织合格模具,送抛光工处进行抛光,完毕配送机台。
4.2.1.3模具在炉中的停留时间最长不超过8小时。
4.2.1.4模具加热及保温控制如表14.2.2盛锭筒的准备(责任人:挤压班长)4.2.2.1盛锭筒必须保持干净,无严重磨损或大肚,否则,挤压产品将会出现夹渣或气泡。
4.2.2.2盛锭筒与模具配合的端面应平整无损伤和粘铝,否则挤压时会跑料。
4.2.2.3盛锭筒的加热元件必须完好并有足够的加热能力。
否则,盛锭筒将无法达到工艺要求的温度。
4.2.2.4盛锭筒温度控制在380℃-430℃之间,严禁超出范围。
4.2.2.5每班上班前,应对盛锭筒进行一次清缸。
在正常挤压时,每隔20-50支锭应进行一次清缸,以确保盛锭筒内清洁干净。
4.2.2.6盛锭筒应避免急冷急热,在正常情况下,盛锭筒应在工艺要求的温度范围内长期保温,交班时不要断电。
4.2.3铝合金圆铸锭的准备(责任人:主机手)4.2.3.1根据排产单的要求选用相应牌号的合金,其数量由生产任务的多少决定。
4.2.3.2各机台所使用的铝合金圆铸锭必须是有炉次编号的圆铸锭。
4.2.3.3圆铸锭在入炉加热之前,应作表面质量自检,自检由主机手负责,凡是有明显夹渣、冷隔、中心裂纹和弯曲的圆铸锭,都不应入炉加热,应将其挑选出来退回熔铸车间。
4.2.3.4不允许圆铸锭在地面上滚动,凡是表面有泥沙、灰尘时,均应清理干净后再入炉加热。
4.2.3.5出口端的燃烧器主要用作控制铸锭温度,但要靠热工仪表的准确定温来控制燃烧器自动着火和熄火,以确保铸锭温度符合工艺要求。
挤压车间工艺操作规程
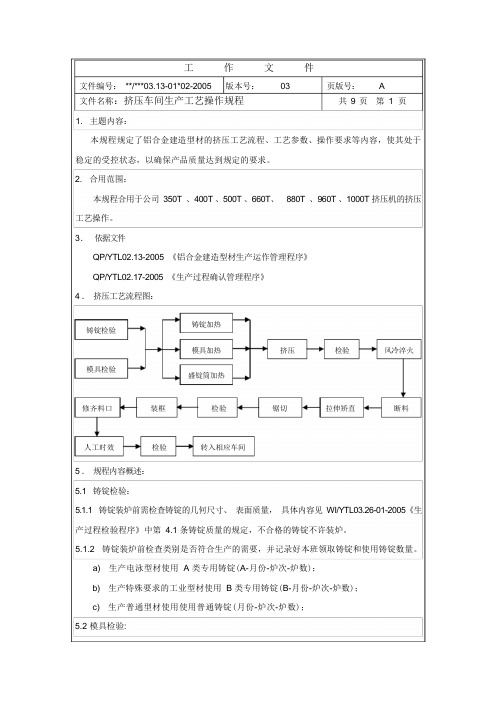
工作文件文件编号:**/***03.13-01*02-2005 版本号:03 文件名称:挤压车间生产工艺操作规程页版号:共9 页A第1 页1. 主题内容:本规程规定了铝合金建造型材的挤压工艺流程、工艺参数、操作要求等内容,使其处于稳定的受控状态,以确保产品质量达到规定的要求。
2. 合用范围:本规程合用于公司350T 、400T 、500T 、660T、880T 、960T 、1000T 挤压机的挤压工艺操作。
3.依据文件QP/YTL02.13-2005 《铝合金建造型材生产运作管理程序》QP/YTL02.17-2005 《生产过程确认管理程序》4 .挤压工艺流程图:铸锭检验模具检验铸锭加热模具加热盛锭筒加热挤压检验风冷淬火修齐料口装框检验锯切拉伸矫直断料人工时效检验转入相应车间5 .规程内容概述:5.1 铸锭检验:5.1.1 铸锭装炉前需检查铸锭的几何尺寸、表面质量,具体内容见WI/YTL03.26-01-2005《生产过程检验程序》中第4.1 条铸锭质量的规定,不合格的铸锭不许装炉。
5.1.2 铸锭装炉前检查类别是否符合生产的需要,并记录好本班领取铸锭和使用铸锭数量。
a) 生产电泳型材使用 A 类专用铸锭(A-月份-炉次-炉数);b) 生产特殊要求的工业型材使用 B 类专用铸锭(B-月份-炉次-炉数);c) 生产普通型材使用使用普通铸锭(月份-炉次-炉数);5.2 模具检验:工作文文件编号**/***03.13-01*02-2005 版本号:03 文件名称:挤压车间生产工艺操作规程件页版号:共9 页A第2 页模具装炉前需检查其模具编号、支重、壁厚是否符合生产计划的要求。
5.3 铸锭加热:5.3.1 铸锭规格使用:a) 盛锭筒φ 125mm 采用φ 120mm 铸锭;b) 盛锭筒φ 105mm 采用φ 100mm 铸锭;c) 盛锭筒φ 75mm 采用φ 73mm 铸锭。
5.3.2 铸锭长度计算方法:a) 铸锭长度计算公式:压余+ 头尾料+ 支重× 支数= 铸锭长度(mm) 铸锭分量(kg/mm)式中:压余长度规定: (压余长度规定见表3 的规定)(表3)铸锭直径(mm) 压余长度(mm) φ 12030φ 10020φ 7315注:生产电泳型材、国标料、工业材及特殊要求的型材压余长度取上限值。
挤压车间操作流程及作业指导书
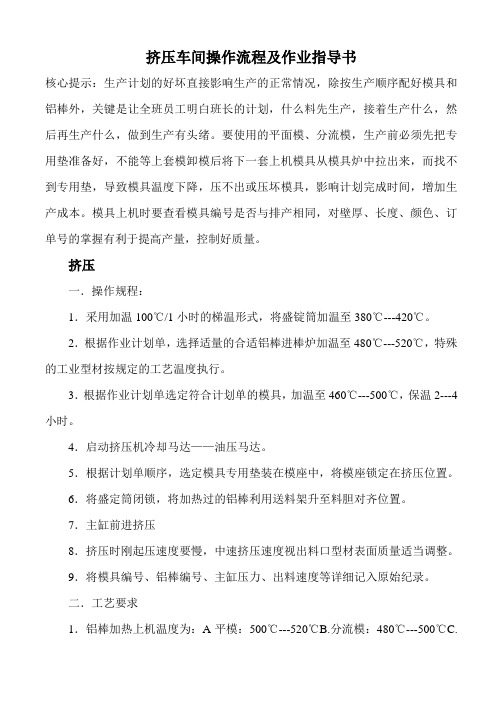
挤压车间操作流程及作业指导书核心提示:生产计划的好坏直接影响生产的正常情况,除按生产顺序配好模具和铝棒外,关键是让全班员工明白班长的计划,什么料先生产,接着生产什么,然后再生产什么,做到生产有头绪。
要使用的平面模、分流模,生产前必须先把专用垫准备好,不能等上套模卸模后将下一套上机模具从模具炉中拉出来,而找不到专用垫,导致模具温度下降,压不出或压坏模具,影响计划完成时间,增加生产成本。
模具上机时要查看模具编号是否与排产相同,对壁厚、长度、颜色、订单号的掌握有利于提高产量,控制好质量。
挤压一.操作规程:1.采用加温100℃/1小时的梯温形式,将盛锭筒加温至380℃---420℃。
2.根据作业计划单,选择适量的合适铝棒进棒炉加温至480℃---520℃,特殊的工业型材按规定的工艺温度执行。
3.根据作业计划单选定符合计划单的模具,加温至460℃---500℃,保温2---4小时。
4.启动挤压机冷却马达——油压马达。
5.根据计划单顺序,选定模具专用垫装在模座中,将模座锁定在挤压位置。
6.将盛定筒闭锁,将加热过的铝棒利用送料架升至料胆对齐位置。
7.主缸前进挤压8.挤压时刚起压速度要慢,中速挤压速度视出料口型材表面质量适当调整。
9.将模具编号、铝棒编号、主缸压力、出料速度等详细记入原始纪录。
二.工艺要求1.铝棒加热上机温度为:A平模:500℃---520℃B.分流模:480℃---500℃C.特殊工业材按特殊的工艺要求执行。
2.模具加温工艺:A.平模:460℃---480℃B.分流模:460℃---500℃3.盛定筒温度:380℃---420℃盛锭筒端面温度为280℃---360℃4.挤压出的料必须表面光滑,纵向压痕无手感,挤压纹细致均匀,无亮带、黑线、阴阳面平面间隙、角度偏差,切斜度按国标高精级。
5.挤压力:≤200㎏/cm26.料胆闭锁压力120㎏/cm2—150㎏/cm2。
7.液压油温度≤45℃8.型材流出速度一般控制在:5米/分钟---30米/分钟9.模具在炉内的时间:≤8小时10.每挤压80支棒-100支棒,必须用专用清缸垫清理一次料胆。
铝型材挤压工艺

挤压一.操作规程:1.采用加温100℃/1小时的梯温形式,将盛锭筒加温至380℃---420℃.2.根据作业计划单,选择适量的合适铝棒进棒炉加温至480℃---520℃,特殊的工业型材按规定的工艺温度执行.3.根据作业计划单选定符合计划单的模具,加温至460℃---500℃,保温2---4小时.4.启动挤压机冷却马达——油压马达.5.根据计划单顺序,选定模具专用垫装在模座中,将模座锁定在挤压位置.6.将盛定筒闭锁,将加热过的铝棒利用送料架升至料胆对齐位置.7.主缸前进挤压8.挤压时刚起压速度要慢,中速挤压速度视出料口型材表面质量适当调整.9.将模具编号、铝棒编号、主缸压力、出料速度等详细记入原始纪录.二.工艺要求1.铝棒加热上机温度为:A平模:500℃---520℃ B.分流模:480℃---500℃C.特殊工业材按特殊的工艺要求执行.2.模具加温工艺:A.平模:460℃---480℃B.分流模:460℃---500℃3.盛定筒温度:380℃---420℃盛锭筒端面温度为280℃---360℃4.挤压出的料必须表面光滑,纵向压痕无手感,挤压纹细致均匀,无亮带、黑线、阴阳面平面间隙、角度偏差,切斜度按国标高精级.5.挤压力:≤200㎏/cm26.料胆闭锁压力120㎏/cm2—150㎏/cm2.7.液压油温度≤45℃8.型材流出速度一般控制在:5米/分钟---30米/分钟9.模具在炉内的时间:≤8小时10.每挤压80支棒-100支棒,必须用专用清缸垫清理一次料胆.三.注意事项1、挤压时,如塞模,闷车时间不得超过5秒.2、装模时,注意安全,防止螺丝滑脱砸伤脚.3、出料时,严禁直线向出料口窥视.4、装模上机前,必须检查中心位,挤压杆是否对中,开机前空载试机运行一次,确认无误正式开机.5、测棒温,模温,盛锭筒温是否达到要求.6、3—5支棒检查一次质量.7、经常检查油温.8、每支铝棒是否有炉号、合金牌号标示.中断一.操作规程1、当主机出料时,用钳子夹住料头,将型材导引至滑出平台并开启冷却风机,对要求水冷的型材打开水冷系统.2、用中断锯锯下约50㎝左右的料头,写明模具编号,集中收放,供修模工参考.3、出料正常,用中断锯锯下约50㎝左右的型材,交给质检员检测质量.4、配合机手根据出料长度,在13米、19米或25米处中断型材,以便矫直.如总长度小于26米.则在料接头上中断.5、型材被中断后,立即用石棉手套轻轻托住推至冷床.6、检查质量.特别是第一、第二支棒,以后每隔3---5支棒就要检查一遍表面质量.二.工艺要求:1、出料口风冷速度不低于110℃/分钟2、锯料时,注意轻压且锯与料同步前进,防止型材压弯.3、推料时,轻拿轻放,避免人为的擦伤和料台擦花.4、锯料时,一定要用手抓住型材,防止型材摆动而擦花.三.注意事项:1、牵引时严禁伸头和操作手正对出料口,以防危险发生.2、开启中断锯时,操作手不能正对中断锯.锯片30㎝范围内,禁止人身靠近,以保安全.3、注意出料道路,防止料床顶住型材.4、注意安全,小心烫伤.5、注意型材出料时扭拧.拉伸一、操作规程:1、检查油压系统是否漏油,空气压力是否正常.2、检查传输带、冷床、储料台是否有破损和擦伤型材之处.3、拉伸前要确认型材的长度,再预定拉伸率,确定拉伸长度,即主夹头移动位置,通常6063T5拉伸率为%--1%,6061 T6拉伸率为%%.4、根据型材的形状确认夹持方法,大断面空心型材,可塞入拉伸垫块,但要尽量确保足够的夹持面积.5、当型材冷却至50℃以下时,开能拉伸型材.6、当型材同时存在弯曲和扭拧时,应先矫正扭拧后拉弯曲.7、第一、二根进行试拉,确认预定拉伸率和夹持方法是否合适.目视弯曲、扭拧、检查型材的平面间隙、扩口、并口,如不合适,要适当调整拉伸率.8、正常拉伸率仍不能消除弯曲、扭拧,或不能使几何尺寸合格时,应通知操作手停止挤压.9、冷却台上的型材不能互相摩擦、碰撞、重叠堆放、防止擦花.二、工艺要求:1、型材冷却温度:≤50℃2、两排料之间要有一定的距离,防止相互擦伤.3、拉伸时,两端的夹持方向要一致.尾夹头夹好后,主夹头才能拉伸.4、主夹头卸压后,钳口打开前、主夹头不要回程.三、注意事项:1、钳口夹持型材时,手不要握在被夹持的部位.2、当油面低于下限,过滤器堵塞或油温过高时,要停止油泵运转.3、出现非正常声音时,要及时判断原因和报告大班长.4、型材表面严禁油污.锯切一、操作规程:1、开启锯床,检查进退是否正常,锯片是否需要维修、更换.2、将矫直过的型材移至塑料滚筒滚床.3、将定尺挡板定于需要处并坚固.4、将型材的头部锯掉约40㎝,然后顶住定尺挡板,用手按住型材,脚踏前进开关,将型材锯断.5、锯片后退、检查每支型材的质量.6、将合格型材装在专用框内.7、料口修整好,填写完跟踪卡,待质检签名后向统计过磅交货.二、工艺要求:1、锯切头料应不小于30㎝,尾料不小于40㎝,以保证质量.2、锯切时大料每次不能超过6支.3、锯口应整齐,无严重的变形和毛刺.4、锯口余量客户没有特殊要求的一般留20㎜,不得副公差.5、移动型材时轻抬轻放,防止擦花,划伤型材.6、装框每层放5根以上垫条,注意不同材的装置,防止变形.7、料口修理均匀、平整.三、注意事项:1、锯片前进时,人不要站在锯片正面严防伤人.2、控制好喷油量,擦干型材上面的油污 .3、锯片伸缩控制在10—15秒之间.4、锯口如卷边或变形应校正清齿或更换.时效一、操作规程:1、开炉前检查一下温度表是否正常,料口、型材质量是否合格,型材品名、数量,框号与跟踪卡是否相符,方可进炉.2、装好炉,打开所有的时效开关如燃气装置、电路等,然后检查每个部位设备是否正常.3、填写好进炉时间、保温时间、出炉时间.4、时效结束,型材出炉,强制冷却.5、跟踪卡按时效情况登记好,检查硬度,合格将卡插进型材框里.二、工艺要求:1、温度:200±5℃2、时间2—小时,炉内温差不能超过10℃.有特殊要求的型材按规定的工艺要求执行.3、料冷却到50℃以下测硬度,韦氏硬度≥8HW.特殊硬度要求的按特殊要求执行.三、注意事项:1、天车下严禁站人2、吊运框架不得碰伤、损坏型材,不得人为践踏型材.3、出炉的型材不应接触腐蚀性气体、尘土等,要求炉前炉后盖好彩条布.4、料框不要高叠架堆放,一般不超过3架.1、机台班长注意事项生产计划的好坏直接影响生产的正常情况,除按生产顺序配好模具和铝棒外,关键是让全班员工明白班长的计划,什么料先生产,接着生产什么,然后再生产什么,做到生产有头绪.要使用的平面模、分流模,生产前必须先把专用垫准备好,不能等上套模卸模后将下一套上机模具从模具炉中拉出来,而找不到专用垫,导致模具温度下降,压不出或压坏模具,影响计划完成时间,增加生产成本.模具上机时要查看模具编号是否与排产相同,对壁厚、长度、颜色、订单号的掌握有利于提高产量,控制好质量.2、主机手注意事项一名合格的主机手必须与班长有默契配合,能与班长沟通,清楚班长的生产计划,班长不在现场时能指挥生产,不会造成停机.机手只有熟悉生产计划,才能懂得开机的技巧,并根据不同的表面处理方式、断面及壁厚控制挤压速度,提高产量,减少废料的生产.严格按照工艺、设备操作规程操作是机手神圣的职责,机械手上、主缸进时要密切注视,手不能离开操作台的暂停控制开关,严防没有上挤压饼或机械手故障引起挤压杆冲断的事故发生.3、中断工的操作规程中断工在交接班时首先要检查锯片的固定、转动装置、安全装置及各按钮是否正常.密切注意出料口型材的行走是否顺畅,当达到型材要求的长度时,开始锯切.按手柄开关或脚垫开关,将锯片压向出料型材,锯切过程中要保持与出料速度相同方向移动中断锯,当型材切断后锯片要迅速移离型材.接着将锯断的型材滑入料架冷却,并且每隔3-5支料时必须锯样板检查表面质量情况,同时适当向锯片涂擦润滑油.4 矫直工操作规程矫直工在交接班时先检查机械紧固件和液压传动系统,操作手柄及按钮是否正常.启动液压泵、电机是否正常.根据型材长度,将后夹头的距离适当调整,并固定好后夹头,空负荷试车试行,操作钳口“开-闭”,大车“拉伸-返回”数次,检查是否正常,确定型材温度低于50℃时方可进行拉直,上料操作钳口松开夹紧,大车返回处于极限位置,后夹头同时夹紧时处于拉直状态.在拉直过程中,用手掰动型材使其平直,或按动夹头旋转使型材平直,按拉伸手柄,拉伸开始,拉伸率应不大于%,并注意型材形状尺寸的变化,避免拉伸过量,拉伸结束后,大车返回,松开前后夹头,将型材送上储料台.型材要及时矫直,防止坯料在冷床上堆积,造成碰伤、划伤、擦花,型材装饰面朝上,避免装饰面擦花,传送调直后坯料的传送带与过桥带保持同步运转.5锯切装框操作规程首先检查锯片固定、传动、安全装置及各按钮是否正常,然后根据挤压排产单上型材长度,颜色,方向装柜,不能混装.送料到锯切台直至碰到挡尺,并将型材摆直.向锯片喷射适量的冷却润滑机油,然后开始锯切.锯切时要控制一次锯切支数,防止擦花,并且对于成品坯料和光面料锯切时,要每支之间用干净布料进行间隔.将锯切好的型材装到指定的料框,有质量问题的料不能进框,在装框过程中厚重型材装在下面,轻薄型材装上面.同时要做到轻拿轻放,防止压伤、压凹、压坏.每层型材间都必须垫隔条,长短不一致的型材原则上不混装,需要混装时,应采取长下短上的装框方式,装好框后用彩条布盖好后需及时转至中转仓进炉时效.。
第10章挤压与拉拔工艺

重金属挤压比λ一般在4~90范围内选取,对组织与性能有一定要求的挤压 制品,挤压比一般不低于4~6。(变形程度=?)
第10章挤压与拉拔工艺
3.锭坯长度的确定 按挤压制品所要求的长度来确定锭坯的长度时,可用下式计算:
(10-1)
式中,L0—锭坯长度; D0—锭坯直径; Dt—挤压筒直径; Kt—填充系数, Lz—制品长度; LQ—切头、切尾长度; hy—压余厚度。
由于磷化膜层本身摩擦系数并不很低,为提高润滑效果,通常磷化后再进行 皂化处理。皂化是利用硬脂酸钠或肥皂作润滑剂,与磷化层中的磷酸锌反应 生成硬脂酸锌,俗称锌肥皂或金属肥皂的过程。典型的磷化-皂化处理工艺包 括除油-酸洗-磷化-中和-皂化-干燥等工序。
第10章挤压与拉拔工艺
10.5 拉拔理论及工艺
10.5.1拉拔的基本理论
1.拉拔工艺概述 1)拉拔的分类 在拉力的作用下,使金属坯料通过模孔,从而获得相应形状和尺寸制品 的塑性加工方法称之为拉拔,如图10.42所示。 拉拔是金属管材、棒材、型材及线材的主要加工方法之一。
第10章挤压与拉拔工艺
•图10.42 拉拔工艺示意
第10章挤压与拉拔工艺
按拉拔时金属的温度分,在再结晶温度以下的拉拔是冷拔,在再结晶温 度以上的拉拔是热拔,在高于室温低于再结晶温度的拉拔是温拔。冷拔 是金属丝、线生产中应用最普遍的拉拔方式。热拔主要用于高熔点金属 如钨、钼等金属丝的拉拔。温拔主要用于难变形的合金如高速钢丝、轴 承钢丝的拉拔。 按拉拔制品的断面形状,可将拉拔分为实心材拉拔和空心材拉拔。实心 材拉拔主要包括棒材、型材及线材的拉拔。空心材拉拔主要用于圆管和 异型管材的拉拔。 按拉拔过程中金属同时通过的模子数分,只通过一个模子的拉拔是单道 次拉拔,依次连续通过若干(2~25)个模子的拉拔是多道次连续拉拔。
铝型材挤压工艺操作规程
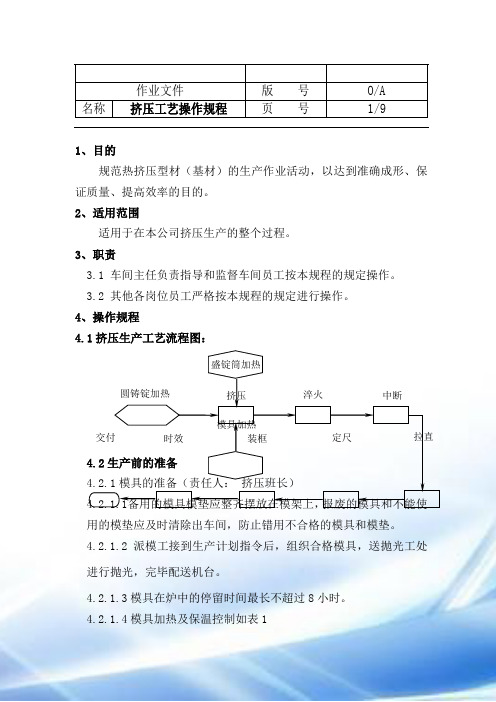
作业文件版号O/A名称挤压工艺操作规程页号1/91、目的规范热挤压型材(基材)的生产作业活动,以达到准确成形、保证质量、提高效率的目的。
2、适用范围适用于在本公司挤压生产的整个过程。
3、职责3.1 车间主任负责指导和监督车间员工按本规程的规定操作。
3.2 其他各岗位员工严格按本规程的规定进行操作。
4、操作规程4.1挤压生产工艺流程图:盛锭筒加热圆铸锭加热挤压淬火中断模具加热交付时效装框定尺拉直4.2生产前的准备4.2.1模具的准备(责任人:挤压班长)4.2.1.1备用的模具模垫应整齐摆放在模架上,报废的模具和不能使用的模垫应及时清除出车间,防止错用不合格的模具和模垫。
4.2.1.2派模工接到生产计划指令后,组织合格模具,送抛光工处进行抛光,完毕配送机台。
4.2.1.3模具在炉中的停留时间最长不超过8小时。
4.2.1.4模具加热及保温控制如表1作业文件版号O/A名称挤压工艺操作规程页号2/9模具外径模具类型加热温度(℃)保温时间(H)平面模440-480 ≥3 Ф278-Ф330分流模440-480 ≥5平面模440-480 ≥2 Ф198-Ф248分流模440-480 ≥2平面模440-480 ≥1 Ф138-Ф148分流模440-468 ≥2平面模440-480 ≥1 Ф138分流模440-480 ≥1.5 4.2.2盛锭筒的准备(责任人:挤压班长)4.2.2.1盛锭筒必须保持干净,无严重磨损或大肚,否则,挤压产品将会出现夹渣或气泡。
4.2.2.2盛锭筒与模具配合的端面应平整无损伤和粘铝,否则挤压时会跑料。
4.2.2.3盛锭筒的加热元件必须完好并有足够的加热能力。
否则,盛锭筒将无法达到工艺要求的温度。
4.2.2.4盛锭筒温度控制在380℃-430℃之间,严禁超出范围。
4.2.2.5每班上班前,应对盛锭筒进行一次清缸。
在正常挤压时,每隔20-50支锭应进行一次清缸,以确保盛锭筒内清洁干净。
4.2.2.6盛锭筒应避免急冷急热,在正常情况下,盛锭筒应在工艺要求的温度范围内长期保温,交班时不要断电。
挤压生产工艺流程
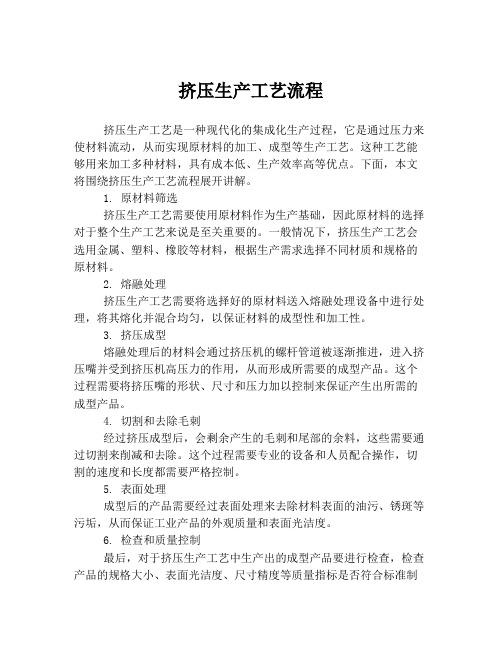
挤压生产工艺流程挤压生产工艺是一种现代化的集成化生产过程,它是通过压力来使材料流动,从而实现原材料的加工、成型等生产工艺。
这种工艺能够用来加工多种材料,具有成本低、生产效率高等优点。
下面,本文将围绕挤压生产工艺流程展开讲解。
1. 原材料筛选挤压生产工艺需要使用原材料作为生产基础,因此原材料的选择对于整个生产工艺来说是至关重要的。
一般情况下,挤压生产工艺会选用金属、塑料、橡胶等材料,根据生产需求选择不同材质和规格的原材料。
2. 熔融处理挤压生产工艺需要将选择好的原材料送入熔融处理设备中进行处理,将其熔化并混合均匀,以保证材料的成型性和加工性。
3. 挤压成型熔融处理后的材料会通过挤压机的螺杆管道被逐渐推进,进入挤压嘴并受到挤压机高压力的作用,从而形成所需要的成型产品。
这个过程需要将挤压嘴的形状、尺寸和压力加以控制来保证产生出所需的成型产品。
4. 切割和去除毛刺经过挤压成型后,会剩余产生的毛刺和尾部的余料,这些需要通过切割来削减和去除。
这个过程需要专业的设备和人员配合操作,切割的速度和长度都需要严格控制。
5. 表面处理成型后的产品需要经过表面处理来去除材料表面的油污、锈斑等污垢,从而保证工业产品的外观质量和表面光洁度。
6. 检查和质量控制最后,对于挤压生产工艺中生产出的成型产品要进行检查,检查产品的规格大小、表面光洁度、尺寸精度等质量指标是否符合标准制定的要求,从而保证整个生产工艺的质量完整性和可靠性。
总之,挤压生产工艺流程是一种非常重要的生产工艺,它适用于多种不同类型的材质,原材料、熔融处理、成型、切割、表面处理、检查和质量控制都是整个过程必不可少的环节。
掌握并精通这一流程是生产中的核心技能,能够为生产企业带来丰厚的经济效益。
复合肥生产挤压工艺流程
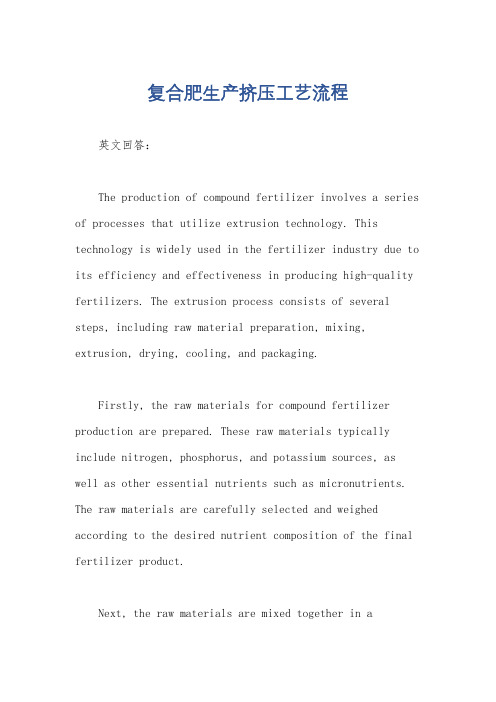
复合肥生产挤压工艺流程英文回答:The production of compound fertilizer involves a series of processes that utilize extrusion technology. This technology is widely used in the fertilizer industry due to its efficiency and effectiveness in producing high-quality fertilizers. The extrusion process consists of several steps, including raw material preparation, mixing, extrusion, drying, cooling, and packaging.Firstly, the raw materials for compound fertilizer production are prepared. These raw materials typically include nitrogen, phosphorus, and potassium sources, as well as other essential nutrients such as micronutrients. The raw materials are carefully selected and weighed according to the desired nutrient composition of the final fertilizer product.Next, the raw materials are mixed together in aspecific ratio to achieve the desired nutrient content. This mixing process ensures that the nutrients are evenly distributed throughout the fertilizer mixture. Various mixing techniques can be used, such as drum mixers or paddle mixers, depending on the specific requirements of the fertilizer formulation.Once the raw materials are thoroughly mixed, they are fed into an extruder. The extruder is a machine that applies pressure and heat to the fertilizer mixture, causing it to form a continuous strip or ribbon. The extrusion process helps to improve the physical properties of the fertilizer, such as its density and particle size.It also helps to activate certain chemical reactions that are beneficial for nutrient release and absorption.After extrusion, the fertilizer strip or ribbon is cut into granules of the desired size. This can be done using a rotary drum granulator or a specialized cutting machine. The granules are then transferred to a drying system, where they are subjected to controlled temperature and airflow to remove excess moisture. Drying is an important step toprevent caking and ensure the stability and shelf life of the final fertilizer product.Once dried, the fertilizer granules are cooled to room temperature to further enhance their stability. Cooling can be achieved using a fluidized bed cooler or a rotary cooler. After cooling, the granules are ready for packaging. They can be packed in bags, sacks, or bulk containers, depending on the market requirements.In conclusion, the production of compound fertilizer using extrusion technology involves several steps,including raw material preparation, mixing, extrusion, drying, cooling, and packaging. This process helps to produce high-quality fertilizers with improved physical properties and nutrient availability. The use of extrusion technology in compound fertilizer production has revolutionized the industry and has become a preferred method for many fertilizer manufacturers.中文回答:复合肥的生产涉及一系列使用挤压技术的工艺过程。
2024 合金反向挤压型材生产工艺
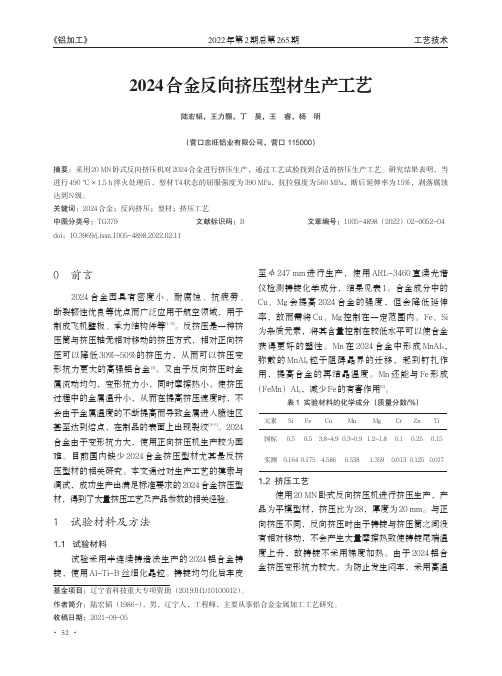
0前言2024合金因具有密度小、耐腐蚀、抗疲劳、断裂韧性优良等优点而广泛应用于航空领域,用于制成飞机壁板、承力结构件等[1-2]。
反挤压是一种挤压筒与挤压轴无相对移动的挤压方式,相对正向挤压可以降低30%~50%的挤压力,从而可以挤压变形抗力更大的高强铝合金[3]。
又由于反向挤压时金属流动均匀,变形抗力小,同时摩擦热小,使挤压过程中的金属温升小,从而在提高挤压速度时,不会由于金属温度的不断提高而导致金属进入脆性区甚至达到熔点,在制品的表面上出现裂纹[4-5]。
2024合金由于变形抗力大,使用正向挤压机生产较为困难。
目前国内缺少2024合金挤压型材尤其是反挤压型材的相关研究。
本文通过对生产工艺的摸索与调试,成功生产出满足标准要求的2024合金挤压型材,得到了大量挤压工艺及产品参数的相关经验。
1试验材料及方法1.1试验材料试验采用半连续铸造法生产的2024铝合金铸锭,使用Al-Ti-B丝细化晶粒。
铸锭均匀化后车皮至ϕ247mm进行生产,使用ARL-3460直读光谱仪检测铸锭化学成分,结果见表1。
合金成分中的Cu、Mg会提高2024合金的强度,但会降低延伸率,故而需将Cu、Mg控制在一定范围内。
Fe、Si 为杂质元素,将其含量控制在较低水平可以使合金获得更好的塑性。
Mn在2024合金中形成MnAl6,弥散的MnAl6粒子阻碍晶界的迁移,起到钉扎作用,提高合金的再结晶温度。
Mn还能与Fe形成(FeMn)Al6,减少Fe的有害作用[6]。
表1实验材料的化学成分(质量分数/%)元素国标实测Si0.50.164Fe0.50.175Cu3.8~4.94.586Mn0.3~0.90.538Mg1.2~1.81.359Cr0.10.013Zn0.250.125Ti0.150.0171.2挤压工艺使用20MN卧式反向挤压机进行挤压生产,产品为平模型材,挤压比为28,厚度为20mm。
与正向挤压不同,反向挤压时由于铸锭与挤压筒之间没有相对移动,不会产生大量摩擦热致使铸锭尾端温度上升,故铸锭不采用梯度加热。
第10章挤压与拉拔工艺
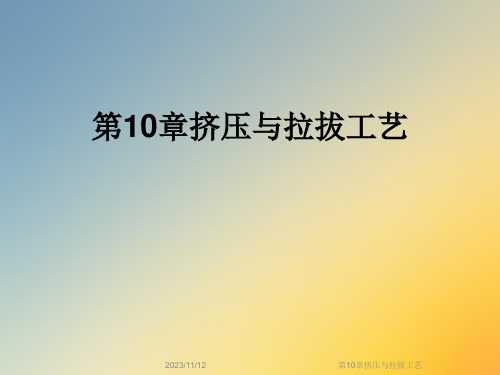
为了获得均匀和较高的力学性能,应尽量选用大的挤压比进行挤压,一 般要求:
一次挤压的棒、型材
λ>10
锻造用毛坯பைடு நூலகம்
λ>5
二次挤压用毛坯
λ可不限
一般轻金属挤压比λ值的范围为8~60,纯金属与软合金允许的值较大,硬 金属较小。挤压型材时λ=10~45,挤压棒材时λ=10~25。为保证焊缝质量, 使用组合模挤压时λ≥25。
第10章挤压与拉拔工艺
3) 铜合金及其他重金属的润滑 重金属大多用45号机油加20%~30%片状石墨作润滑剂; 而青铜、白铜挤压时,用45号机油30%~40%的片状石墨。在冬季为增加 润滑剂的流动性,往往加入5%~9%煤油,在夏季则加适量的松香,可使 石墨质点处于悬浮状态。 铜及铜合金在挤压时都要进行润滑,在模子和穿孔针上薄薄地涂上一层, 挤压筒在挤压后也用蘸有上述润滑剂的布简单擦一下。
(10-2) (2)断面减缩率ψ。 表示拉拔后金属材料横断面积减小量与 初始面积之比,即:
(10-3)
第10章挤压与拉拔工艺
2)实现拉拔过程的基本条件 拉拔过程是借助于在被加工的坯料前端施以拉力实现的,
1
40~250 25~100 3~90 1~3.5 1~2 0.5~5 18~300 12~60
HSn70-1 HA177-2 QSn6.5-0.1 B30 镍及其合金 铅及其合金 锌 锌合金
2.4~6.0 2.4~6.0 1.8~9.0 18~7.2 18~220 6.0~60 2.0~23 2.0~12
第10章挤压与拉拔工艺
2.拉拔的变形指数与拉拔实现条件 1)拉拔时的变形指数 拉拔时坯料发生塑性变形,其形状和尺寸发生改变。以Fq和 Lq表示拉拔前金属坯料的断面积及长度,Fh和Lh表示拉拔后 金属制品的断面积和长度,根据体积不变的条件可得到以下 的变形指数和它们之间的关系式。 (1)延伸系数λ。 表示拉拔后金属材料长度与拉拔前金属材 料长度之比,也等于拉拔前后横断面的面积之比,即:
铝合金挤压生产知识及注意要点
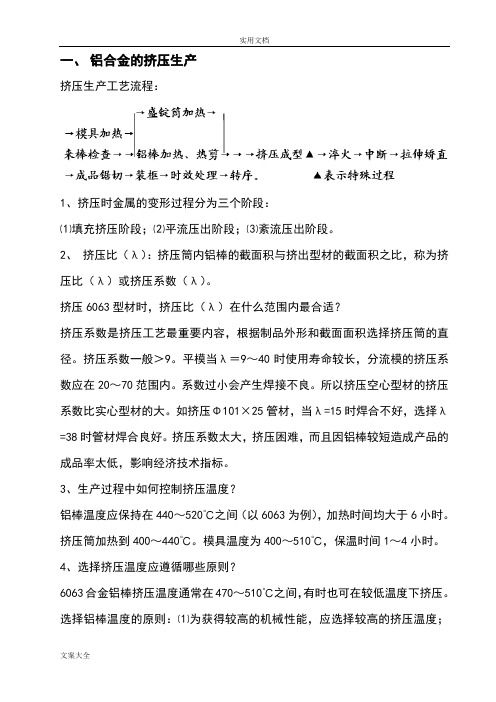
一、铝合金的挤压生产挤压生产工艺流程:1、挤压时金属的变形过程分为三个阶段:⑴填充挤压阶段;⑵平流压出阶段;⑶紊流压出阶段。
2、挤压比(λ):挤压筒内铝棒的截面积与挤出型材的截面积之比,称为挤压比(λ)或挤压系数(λ)。
挤压6063型材时,挤压比(λ)在什么范围内最合适?挤压系数是挤压工艺最重要内容,根据制品外形和截面面积选择挤压筒的直径。
挤压系数一般>9。
平模当λ=9~40时使用寿命较长,分流模的挤压系数应在20~70范围内。
系数过小会产生焊接不良。
所以挤压空心型材的挤压系数比实心型材的大。
如挤压Φ101×25管材,当λ=15时焊合不好,选择λ=38时管材焊合良好。
挤压系数太大,挤压困难,而且因铝棒较短造成产品的成品率太低,影响经济技术指标。
3、生产过程中如何控制挤压温度?铝棒温度应保持在440~520℃之间(以6063为例),加热时间均大于6小时。
挤压筒加热到400~440℃。
模具温度为400~510℃,保温时间1~4小时。
4、选择挤压温度应遵循哪些原则?6063合金铝棒挤压温度通常在470~510℃之间,有时也可在较低温度下挤压。
选择铝棒温度的原则:⑴为获得较高的机械性能,应选择较高的挤压温度;⑵当挤压机能力不足,可通过提高铝棒温度来提高挤压速度;⑶当模具悬臂过大时,可提高铝棒温度,以减小铝棒对模具的压力及摩擦力;⑷挤压温度过高会使产生气泡、撕裂及由于模具工作带粘铝造成表面划痕严重;⑸为了获得高表面质量的产品,宜在较低温度下挤压模具加热及保温控制:5、如何控制挤压速度?挤压速度是影响生产率的一个重要指标。
挤压速度取决于合金种类、几何形状、尺寸和表面状态,同时也与铸锭质量息息相关。
要提高挤压速度,必需合理控制铝棒温度、模具温度、挤压筒温度。
6063铝合金挤压速度范围为:9~80M/min,其中实心型材为:20~80M/min,空心型材的挤压速度一般为实心型材挤压速度的0.5~0.8倍。
挤压机产量及工艺检验记录

编号:JLYL-RF-1A7 用户: 投料批号 规格: 产品批号 原料 牌号
根数
模具 编号
外径mm 最大 最小
日期: 年 壁厚mm 最大 最小
月
日 表面质量 内 外
(早 中 夜)班 晶粒度 判定 不合格原因 签字 结果 备注
(
)班
工艺记录 出炉温度: ℃ 温度梯度: ℃ 挤压筒温度: ℃ 挤压速度: mm/s 主缸压力 MPa
当班运行 状况
设备状况:
挤压筒 剪刀 间隙 挤压垫
清理 未清理 清理 未清理 调整 未调整 擦拭 未擦拭
计量器具 编号 确认结果
交接班会签 当班操作 接班操作 生产统计 合格: Kg; 不合格: Kg; 溢料: Kg, % 交接时间 时 分
铝型材挤压生产加工工艺

铝型材挤压生产加工工艺铝型材挤压生产加工工艺1化学成分的优化控制6063-T5建筑铝型材必须具备一定的力学性能。
在其他条件相同时,其抗拉强度、屈服强度随含量增加而升高。
6063台金的强化相主要是Mg2Si相,到底Mg、Si和Mg2Si的量应取多少为好?Mg2Si相是由2个镁原子同1个硅原子组成,镁的相对原子质量为24.3l,硅的相对原子质量为28.09,因此Mg2Si化合物中,镁硅的质量比为1.73:1。
因此,可根据以上分析结果,如果镁硅含量比值大于1.73,则合金中镁除形成Mg2Si相外,还有过剩镁,反之比值小于1.73,则表明硅除形成Mg2Si相外,还有剩余硅。
镁过剩对合金力学性能是有害的。
镁一般控制在0.5%左右,Mg2Si总量控制在0.79%。
当硅过剩0.01%时合金的力学性能σb约为218Mpa,已大大超过国家标准性能,并过剩硅从0.01%提高到0.13%,σb可提高到250Mpa,即提高14.6%。
要形成一定量的Mg2Si,必须首先考虑到Fe与Mn等杂质含量造成的硅损失,即要保证有一定量的过剩硅。
为了使6063合金中的镁充分与硅匹配,实际配料时,必须有意识地使Mg:Si<1.73。
镁的过剩不仅削弱强化效果,而且又增加了产品成本。
因此,6063合金的成分一般控制为:Mg:0.45%-0.65%;Si:0.35%-0.50%;Mg:Si=1.25-1.30;杂质Fe控制在<0.10%-0.25%;Mn<0.10%。
2优化铸锭均匀化退火工艺在民用挤压型材生产时,6063合金的高温均匀化退火规范为:560±20℃,保温4-6h,冷却方式为出炉强迫风冷或喷水急冷。
合金的均匀化处理能提高挤压速度,同未均匀化处理的铸锭相比,大约可使挤压力降低6%-10%。
均匀化处理后冷却速度对组织的析出行为有重要的影响。
对均热后快冷的铸锭,Mg2Si几乎能全部固溶于基体,过剩的Si也将固溶或以弥散析出的细小质点存在。
铝型材挤压工艺操作规程

1、目的规范热挤压型材(基材)的生产作业活动,以达到准确成形、保证质量、提高效率的目的。
2、适用范围适用于在本公司挤压生产的整个过程。
3、职责3.1 车间主任负责指导和监督车间员工按本规程的规定操作。
3.2 其他各岗位员工严格按本规程的规定进行操作。
4、操作规程4.1挤压生产工艺流程图:4.2生产前的准备4.2.1模具的准备(责任人:挤压班长)4.2.1.1备用的模具模垫应整齐摆放在模架上,报废的模具和不能使用的模垫应及时清除出车间,防止错用不合格的模具和模垫。
4.2.1.2派模工接到生产计划指令后,组织合格模具,送抛光工处进行抛光,完毕配送机台。
4.2.1.3模具在炉中的停留时间最长不超过8小时。
4.2.1.4模具加热及保温控制如表14.2.2盛锭筒的准备(责任人:挤压班长)4.2.2.1盛锭筒必须保持干净,无严重磨损或大肚,否则,挤压产品将会出现夹渣或气泡。
4.2.2.2盛锭筒与模具配合的端面应平整无损伤和粘铝,否则挤压时会跑料。
4.2.2.3盛锭筒的加热元件必须完好并有足够的加热能力。
否则,盛锭筒将无法达到工艺要求的温度。
4.2.2.4盛锭筒温度控制在380℃-430℃之间,严禁超出范围。
4.2.2.5每班上班前,应对盛锭筒进行一次清缸。
在正常挤压时,每隔20-50支锭应进行一次清缸,以确保盛锭筒内清洁干净。
4.2.2.6盛锭筒应避免急冷急热,在正常情况下,盛锭筒应在工艺要求的温度范围内长期保温,交班时不要断电。
4.2.3铝合金圆铸锭的准备(责任人:主机手)4.2.3.1根据排产单的要求选用相应牌号的合金,其数量由生产任务的多少决定。
4.2.3.2各机台所使用的铝合金圆铸锭必须是有炉次编号的圆铸锭。
4.2.3.3圆铸锭在入炉加热之前,应作表面质量自检,自检由主机手负责,凡是有明显夹渣、冷隔、中心裂纹和弯曲的圆铸锭,都不应入炉加热,应将其挑选出来退回熔铸车间。
4.2.3.4不允许圆铸锭在地面上滚动,凡是表面有泥沙、灰尘时,均应清理干净后再入炉加热。
铝、铜材连续挤压工艺
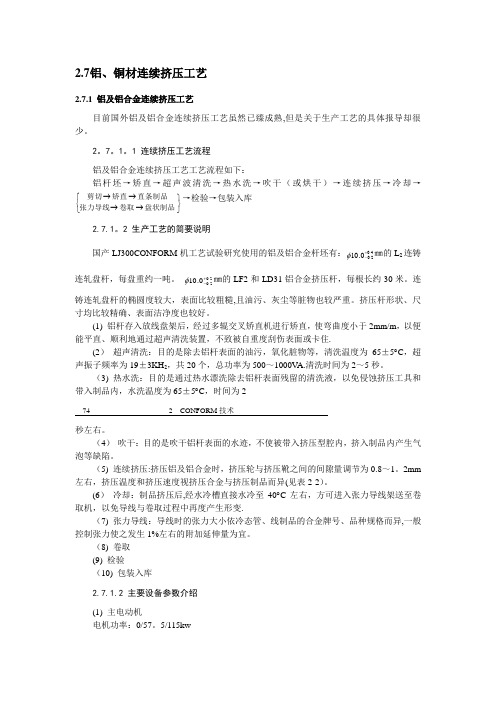
2.7 铝、铜材连续挤压工艺2.7.1 铝及铝合金连续挤压工艺目前国外铝及铝合金连续挤压工艺虽然已臻成熟,但是关于生产工艺的具体报导却很少。
2。
7。
1。
1 连续挤压工艺流程铝及铝合金连续挤压工艺工艺流程如下:铝杆坯→矫直→超声波清洗→热水洗→吹干(或烘干)→连续挤压→冷却→⎭⎬⎫⎩⎨⎧→→→→盘状制品卷取张力导线直条制品矫直剪切→检验→包装入库 2.7.1。
2 生产工艺的简要说明国产LJ300CONFORM 机工艺试验研究使用的铝及铝合金杆坯有:4.02.00.10+-φ㎜的L 2连铸连轧盘杆,每盘重约一吨。
2.02.00.10+-φ㎜的LF2和LD31铝合金挤压杆,每根长约30米。
连铸连轧盘杆的椭圆度较大,表面比较粗糙,且油污、灰尘等脏物也较严重。
挤压杆形状、尺寸均比较精确、表面洁净度也较好。
(1) 铝杆存入放线盘架后,经过多辊交叉矫直机进行矫直,使弯曲度小于2mm/m ,以便能平直、顺利地通过超声清洗装置,不致被自重度刮伤表面或卡住.(2) 超声清洗:目的是除去铝杆表面的油污,氧化脏物等,清洗温度为65±5︒C ,超声振子频率为19±3KH 2,共20个,总功率为500~1000V A.清洗时间为2~5秒。
(3) 热水洗:目的是通过热水漂洗除去铝杆表面残留的清洗液,以免侵蚀挤压工具和带入制品内,水洗温度为65±5︒C ,时间为274 2 CONFORM 技术秒左右。
(4) 吹干:目的是吹干铝杆表面的水迹,不使被带入挤压型腔内,挤入制品内产生气泡等缺陷。
(5) 连续挤压:挤压铝及铝合金时,挤压轮与挤压靴之间的间隙量调节为0.8~1。
2mm 左右,挤压温度和挤压速度视挤压合金与挤压制品而异(见表2-2)。
(6) 冷却:制品挤压后,经水冷槽直接水冷至40︒C 左右,方可进入张力导线架送至卷取机,以免导线与卷取过程中再度产生形变.(7) 张力导线:导线时的张力大小依冷态管、线制品的合金牌号、品种规格而异,一般控制张力使之发生1%左右的附加延伸量为宜。