合成渣精炼法控制钢中夹杂物形态
《炼钢学》考试复习参考资料--最新版
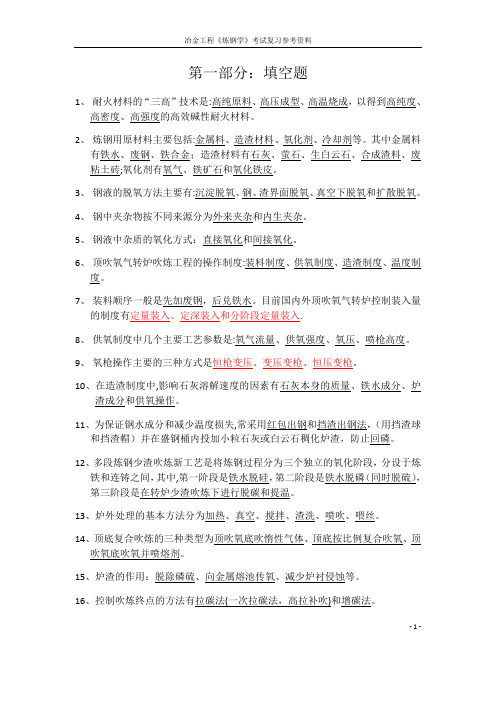
第一部分:填空题1、耐火材料的“三高”技术是:高纯原料、高压成型、高温烧成,以得到高纯度、高密度、高强度的高效碱性耐火材料。
2、炼钢用原材料主要包括:金属料、造渣材料、氧化剂、冷却剂等。
其中金属料有铁水、废钢、铁合金;造渣材料有石灰、萤石、生白云石、合成渣料、废粘土砖;氧化剂有氧气、铁矿石和氧化铁皮。
3、钢液的脱氧方法主要有:沉淀脱氧、钢、渣界面脱氧、真空下脱氧和扩散脱氧。
4、钢中夹杂物按不同来源分为外来夹杂和内生夹杂。
5、钢液中杂质的氧化方式:直接氧化和间接氧化。
6、顶吹氧气转炉吹炼工程的操作制度:装料制度、供氧制度、造渣制度、温度制度。
7、装料顺序一般是先加废钢,后兑铁水。
目前国内外顶吹氧气转炉控制装入量的制度有定量装入、定深装入和分阶段定量装入.8、供氧制度中几个主要工艺参数是:氧气流量、供氧强度、氧压、喷枪高度。
9、氧枪操作主要的三种方式是恒枪变压、变压变枪、恒压变枪。
10、在造渣制度中,影响石灰溶解速度的因素有石灰本身的质量、铁水成分、炉渣成分和供氧操作。
11、为保证钢水成分和减少温度损失,常采用红包出钢和挡渣出钢法,(用挡渣球和挡渣帽)并在盛钢桶内投加小粒石灰或白云石稠化炉渣,防止回磷。
12、多段炼钢少渣吹炼新工艺是将炼钢过程分为三个独立的氧化阶段,分设于炼铁和连铸之间,其中,第一阶段是铁水脱硅,第二阶段是铁水脱磷(同时脱硫),第三阶段是在转炉少渣吹炼下进行脱碳和提温。
13、炉外处理的基本方法分为加热、真空、搅拌、渣洗、喷吹、喂丝。
14、顶底复合吹炼的三种类型为顶吹氧底吹惰性气体、顶底按比例复合吹氧、顶吹氧底吹氧并喷熔剂。
15、炉渣的作用:脱除磷硫、向金属熔池传氧、减少炉衬侵蚀等。
16、控制吹炼终点的方法有拉碳法(一次拉碳法,高拉补吹)和增碳法。
- 1 -17、工业中常用的铁水脱硫剂CaC2,Mg,CaO,Na2O.18、石灰融化因素:石灰质量、炉渣成分、熔池温度、比渣量、熔池搅拌。
炼钢工—论述题 131

1.提高炉龄的措施?答案:(1)采用溅渣护炉技术。
(2)提高炉衬耐火材料质量。
(3)采用综合砌筑技术。
(4)炉渣配适量的氧化镁。
(5)采用计算机动态控制,即采用最佳冶炼控制,提高终点命中率,缩短冶炼周期。
(6)进行有效喷补及合理维护。
(7)改进喷枪结构。
(8)尽可能降低出钢温度。
(9)减少停炉时间。
2.分析冶炼终点硫高的原因及处理措施?答案:一般有以下原因:(1)铁水、废钢硫含量高;(2)造渣剂、冷却剂含硫高;(3)冶炼不正常,化渣不好等。
处理措施:(1)进行铁水预脱硫处理;(2)多倒终渣,再加石灰造高碱度高温炉渣;(3)终点加一定锰铁合金,炉内发生[FeS]+[Mn]=[MnS]+[Fe]反应脱一部分硫;(4)出钢在钢包中加入脱硫剂;(5)采用炉外精炼脱硫等。
3.炉衬损坏原因?答案:由于炉衬工作条件恶劣,损坏原因是多方面的,其主要原因是:(1)废钢、铁水对炉衬冲击及机械磨损;(2)钢液及炉渣的搅动及气体冲刷;(3)炉渣对炉衬的化学侵蚀;(4)炉衬温度激冷激热变化和组织变化的开裂剥落;(5)开炉初期的机械剥落;(6)炉衬内部碳素的氧化。
4.转炉出钢为什么要挡渣?目前挡渣方法有那些?答案:挡渣出钢的主要目的是净化钢水,同时还可以减少合金和脱氧剂的消耗量;减少回磷;减轻耐材侵蚀;有利于钢水二次精炼。
目前国内外普遍采用挡渣挡渣方法有:挡渣球、挡渣棒(塞)、挡渣锥、气动阀(气动挡渣)等。
5.炉渣“返干”及成因?答案:在顶吹转炉吹炼的中期,冶炼温度足够高,碳氧反应激烈,此时枪位比较低,已形成的炉渣的流动性往往会突然减低,甚至会造成结块,即炉渣“返干”出现炉渣“返干”的钢渣组成:钢渣基本代表组成成分SiO2、CaO、FeO三元相图可知,在R=2.33时,当(FeO)比较高时,炉渣是一个均匀的液体;但当(FeO)<16%以后,便有固相的2CaO.SiO2析出;当R=4时,当(FeO)<16%以后,便有固相的3CaO.SiO2及固相的CaO析出。
炉外精炼各种方法
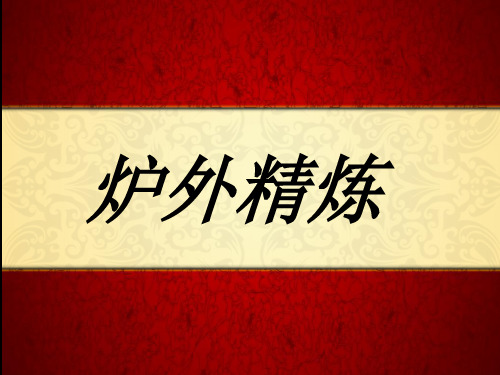
LF
• LF埋弧加热吹氩法是最常用的精炼方法, 能取代电炉还原期,解决了转炉冶炼优钢 问题,具有加热及搅拌功能.
• 电炉EBT出钢,出钢过程加合金,加渣料 (石灰和萤石2%),底吹氩,通电升温,化 渣,10分钟取样分析加渣料1%,测温取样, 加合金看脱氧,准备出钢,一般30-50分钟, 电耗50-80kwh/t,是现代转炉,电炉与连 铸联系的纽带
RH真空工艺过程
• 出钢后,钢包测温取样; • 下降真空室,插入深度为
150-200mm; • 起动真空泵,一根插入管
输入驱动气体; • 当真空室的压力降到26-
10kpa后,循环加剧; • 钢水上升速度为5m/s、
下降速度为1-2m/s; • 气泡在钢液中将气体及夹
杂带出。
VD工艺
• VD(真空馆内钢包脱氧)以轴承钢为例. • 轴承钢最重要的性能指标是疲劳寿命。 • 影响轴承钢寿命的重要指标是钢中氧含量,钢中
RH工艺参数
• 处理容量:大炉子比小炉子好(50t以上); • 处理时间:钢包在真空位的停留时间τ;
τ=Tc/Vt Tc允许温降, Vt平均温降℃/min; • 循环因数:C=ω(t/min).t(min)/Q (ton) ω 循环流量、 t脱气时间、 Q处理容量 • 循环流量ω:主要由上升管与驱动气体流量决定; • 真空度:60-100pa; • 抽气能力。
VD工艺
• 真空保持时间:真空启动后,工作压力达到67 Pa时,保持时间≥15min。
• 真空保持期间调整氩气流量 70NL/min左右,并 通过观察孔观察钢水沸腾情况,及时调整,保持 均匀沸腾。
• 终脱氧后解除真空、开盖、测温,软吹15- 25min,氩气流量 70-100NL/min左右,控制 渣面微动为宜。
关于精炼过程中合成渣行为的探讨
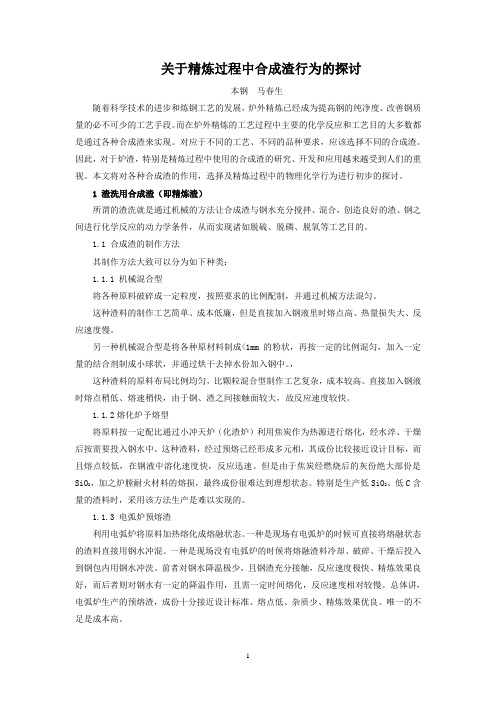
关于精炼过程中合成渣行为的探讨本钢马春生随着科学技术的进步和炼钢工艺的发展,炉外精炼已经成为提高钢的纯净度、改善钢质量的必不可少的工艺手段。
而在炉外精炼的工艺过程中主要的化学反应和工艺目的大多数都是通过各种合成渣来实现。
对应于不同的工艺、不同的品种要求,应该选择不同的合成渣。
因此,对于炉渣,特别是精炼过程中使用的合成渣的研究、开发和应用越来越受到人们的重视。
本文将对各种合成渣的作用,选择及精炼过程中的物理化学行为进行初步的探讨。
1 渣洗用合成渣(即精炼渣)所谓的渣洗就是通过机械的方法让合成渣与钢水充分搅拌、混合,创造良好的渣、钢之间进行化学反应的动力学条件,从而实现诸如脱硫、脱磷、脱氧等工艺目的。
1.1 合成渣的制作方法其制作方法大致可以分为如下种类:1.1.1 机械混合型将各种原料破碎成一定粒度,按照要求的比例配制,并通过机械方法混匀。
这种渣料的制作工艺简单、成本低廉,但是直接加入钢液里时熔点高、热量损失大、反应速度慢。
另一种机械混合型是将各种原材料制成<1mm的粉状,再按一定的比例混匀,加入一定量的结合剂制成小球状,并通过烘干去掉水份加入钢中。
,这种渣料的原料布局比例均匀,比颗粒混合型制作工艺复杂,成本较高。
直接加入钢液时熔点稍低、熔速稍快,由于钢、渣之间接触面较大,故反应速度较快。
1.1.2熔化炉予熔型将原料按一定配比通过小冲天炉(化渣炉)利用焦炭作为热源进行熔化,经水淬、干燥后按需要投入钢水中。
这种渣料,经过预熔已经形成多元相,其成份比较接近设计目标,而且熔点较低,在钢液中溶化速度快,反应迅速。
但是由于焦炭经燃烧后的灰份绝大部份是SiO2,加之炉膛耐火材料的熔损,最终成份很难达到理想状态。
特别是生产低SiO2、低C含量的渣料时,采用该方法生产是难以实现的。
1.1.3 电弧炉预熔渣利用电弧炉将原料加热熔化成熔融状态。
一种是现场有电弧炉的时候可直接将熔融状态的渣料直接用钢水冲混。
一种是现场没有电弧炉的时候将熔融渣料冷却、破碎、干燥后投入到钢包内用钢水冲洗。
炉外精炼各种方法

节流量50-80NL/min,同时测温、取样,加入 硅石2 kg/mm,调整炉渣碱度R=1 .2-1 .5。 • 测温、取样后VD加盖密封,抽真空。 • 真空泵启动期间,调整氩气流量保持30 - 40NL/min。
CAS工艺操作过程
RH钢液循环脱气法
• 主要冶炼高质量产品,如轴承钢、LF钢、硅钢、 不锈钢、齿轮钢等。
• 特点:①反应速度快,表观脱碳速度常数kC可达
到3.5min-1。处理周期短,生产效率高,常与转 炉配套使用。②反应效率高,钢水直接在真空室 内进行反应,可生产H≤0.5×10-6,N≤25×10-6, C≤10×10-6的超纯净钢。③可进行吹氧脱碳和二 次燃烧进行热补偿,减少处理温降;④可进行喷粉 脱硫,生产[S]≤5×10-6的超低硫钢。
VD工艺
• 真空保持时间:真空启动后,工作压力达到67 Pa时,保持时间≥15min。
• 真空保持期间调整氩气流量 70NL/min左右,并 通过观察孔观察钢水沸腾情况,及时调整,保持 均匀沸腾。
• 终脱氧后解除真空、开盖、测温,软吹15- 25min,氩气流量 70-100NL/min左右,控制 渣面微动为宜。
拌,进一步脱碳, 钢液温度达到1670-1750之间. • 6.加合金,微调成分,加铝吹氩搅拌几分 后,破真空浇铸.
AOD炉
AOD炉 主要是冶炼高质量的不锈 钢(C<20ppm,S,P<50ppm)使用更廉 价的原料(采用高碳铬代替低碳铬) 60%-70%的不锈钢产量 炉料:废钢,不锈钢返回料,高碳铬 铁,高碳镍铁 吹炼过程就是温度及氩氧比的控制 T=1680 O2:Ar=4:1(3:1)C下降为0.2% T=1700 O2:Ar=2;1 C下降为0.1% T=1730 O2:Ar=1;2 C下降为0.02% T=1750 O2:Ar=1:3 C下降为0.001%
合成渣精炼法控制帘线钢中的非金属夹杂物
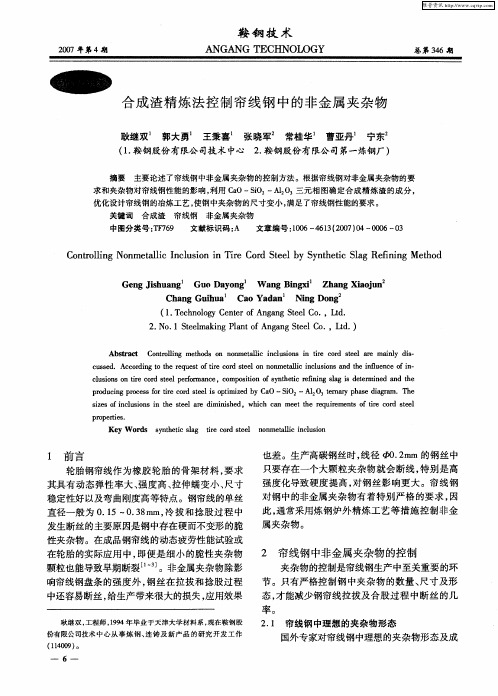
也差 。生 产高 碳钢 丝 时 , 径 鲫 .m 的钢 丝 中 线 2m
只要存在一个大颗粒夹杂物就会断线 , 特别是高 强度化导致硬度 提高 , 对钢丝影响更 大。帘线钢 对钢中的非金属夹杂物有着特别严 格的要求 , 因 此, 通常采用炼钢炉外精炼工艺等措施控制非金 属 夹杂 物 。
稳定性好以及弯 曲刚度高等特点 。钢帘线的单丝 直 径一 般 为 0 1 . 5—03 m 冷 拔 和捻 股 过 程 中 .8 m,
p o ris r pe t . e
Ke o d s n h t lg t e c r te n n tl c i cu in yW r s y te i s i o d se l o mea l n l so c a r i
1 前言
轮胎钢帘线作为橡胶轮胎的骨架材料 , 求 要 其具有动态 弹性率大、 强度高、 拉伸蠕变小、 尺寸
维普资讯
鞍 钢 技 术
20 0 7年第 4期
ANGANG TECHNOLOGY
总第 36期 4
合 成 渣 精 炼法 控 制 帘线 钢 中的非 金 属夹 杂 物
耿继 双 郭 大 勇 王 秉喜 张晓 军 常桂 华 曹 亚丹 宁 东
(. 1鞍钢股份有 限公 司技术中心 2 鞍钢股份有限公司第一炼钢厂) .
耿 继 双 , 程 师 ,9 4年 毕 业 于 天 津 大 学 材 料 系 , 工 19 现在 鞍 钢股
2 帘线钢 中非金属 夹杂物 的控制
夹杂物的控制是帘线钢生产 中至关重要 的环 节。只有严格控制钢 中夹杂物 的数量 、 尺寸及形 态, 才能减少钢帘线拉拔及合股过程 中断丝金属夹杂物 的控制方法 。根据帘线钢对 非金属夹 杂物 的要
求和夹杂 物对 帘线钢性能的影响 , 用 C O—SO 一A : , 利 a i: 10 三元 相图确定 合成 精炼渣 的成分 , 优化设计 帘线 钢的冶炼 工艺 , 使钢 中夹杂物的尺寸变小 , 满足 了帘线钢性 能的要求 。 关键词 合成 渣 帘线钢 非金属夹杂物
炼钢原理---8-2 合成渣洗

下页
3 合成渣洗的精炼作用
(4)夹杂物的去除
1)一方面钢液内的夹杂物与乳化渣滴碰 撞,被渣滴吸附、同化而随渣滴上浮排 除。 2)另一方面促进了二次脱氧反应产物的 排出,从而使钢中的夹杂减少。
下页
3 合成渣洗的精炼作用
(2)合成渣对钢中脱氧元素脱氧能力的影响
1)硅脱氧 用硅脱氧的反应式为:
[Si]+2[O]=(SiO2)
当温度降低时,硅的脱氧能力明显增强。
2)铝脱氧 用Al脱氧的反应式为 2[Al] 3[O] (Al2O3)
反应的平衡常数
K Al
a2Al a[3O] a Al2O3
返回
3 合成渣洗的精炼作用
合成渣洗工艺: 按要求的成分、温度、 渣量先倒入钢包内,然后吊到电弧炉 或转炉出钢位置,靠出钢钢流的冲击 使合成渣乳化,渣和钢充分接触混合, 然后乳化的渣滴上浮至钢液面,完成 钢液的脱硫,脱氧、去除非金属夹杂 等精炼任务。
下页
3 合成渣洗的精炼作用
(1)合成渣的乳化和上浮 倒入钢包内的合成渣在钢流的冲击下, 被分裂成细小的渣滴并弥散于钢液中, 粒径越小,与钢液接触的表面积越大, 渣洗作用越强。乳化的渣滴随钢流紊乱 搅动的同时不断碰撞合并长大上浮。
下页
2 合成渣的性质 (3)合成渣的流动性
合成渣要求有较好的流动性,流动性是影响渣在钢液中的乳化 程度的重要因素。 组试有成验人为是研:在究5粘8了%度AC等la2于OO3、0、.32CP0aa%F•s2S不和iO变N2、a的2A1情0lF%况6对M下白g进O渣、行粘5的%度,A的1发2影O现3响、渣。7的%白熔C渣a点F的2。 随(CaO)和(CaO+MgO)含量的增加而提高。为了使渣的熔点小于 1C5a0O0时℃,,渣必的须熔使点(C会aO急+剧M降gO低)≤。63因%此。,用对A于12O炉3或外N精a炼2A,lF6推代荐替采 用下述成分的合成渣,50%~55%CaO;6%~10%MgO;15 %Ca~F22三0%组S元iO的2;总8量%控~制15在%3A5~12O403;%5之.0间%。Ca。F2。其中SiO2、Al2O3、
精炼渣对高锰钢中非金属夹杂物的影响
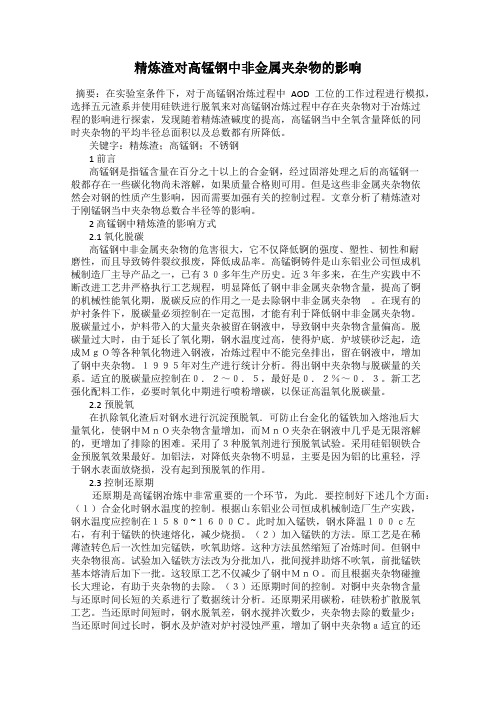
精炼渣对高锰钢中非金属夹杂物的影响摘要:在实验室条件下,对于高锰钢冶炼过程中AOD工位的工作过程进行模拟,选择五元渣系并使用硅铁进行脱氧来对高锰钢冶炼过程中存在夹杂物对于冶炼过程的影响进行探索,发现随着精炼渣碱度的提高,高锰钢当中全氧含量降低的同时夹杂物的平均半径总面积以及总数都有所降低。
关键字:精炼渣;高锰钢;不锈钢1 前言高锰钢是指锰含量在百分之十以上的合金钢,经过固溶处理之后的高锰钢一般都存在一些碳化物尚未溶解,如果质量合格则可用。
但是这些非金属夹杂物依然会对钢的性质产生影响,因而需要加强有关的控制过程。
文章分析了精炼渣对于刚锰钢当中夹杂物总数合半径等的影响。
2 高锰钢中精炼渣的影响方式2.1 氧化脱碳高锰钢中非金属夹杂物的危害很大,它不仅降低锕的强度、塑性、韧性和耐磨性,而且导致铸件裂纹报废,降低成品率。
高锰锕铸件是山东铝业公司恒成机械制造厂主导产品之一,已有30多年生产历史。
近3年多来,在生产实践中不断改进工艺井严格执行工艺规程,明显降低了钢中非金属夹杂物含量,提高了锕的机械性能氧化期,脱碳反应的作用之一是去除钢中非金属夹杂物。
在现有的炉衬条件下,脱碳量必须控制在一定范围,才能有利于降低钢中非金属夹杂物。
脱碳量过小,炉料带入的大量夹杂被留在钢液中,导致钢中夹杂物含量偏高。
脱碳量过大时,由于延长了氧化期,钢水温度过高,使得炉底.炉坡镁砂泛起,造成MgO等各种氧化物进入钢液,冶炼过程中不能完垒排出,留在钢液中,增加了钢中夹杂物。
1995年对生产进行统计分析。
得出钢中夹杂物与脱碳量的关系。
适宜的脱碳量应控制在0.2~0.5,最好是0.2%~0.3。
新工艺强化配料工作,必要时氧化中期进行喷粉增碳,以保证高温氧化脱碳量。
2.2 预脱氧在扒除氧化渣后对钢水进行沉淀预脱氧.可防止台金化的锰铁加入熔池后大量氧化,使钢中MnO夹杂物含量增加,而MnO夹杂在钢液中几乎是无限溶解的,更增加了排除的困难。
采用了3种脱氧剂进行预脱氧试验。
炉外精炼试题答案

答:现状的提高,钢厂普遍采用了炉外精炼工艺流程,它已成为现代炼钢工艺中不可缺少的重要环节。我国早在20世纪50年代末,60年代中期就在炼钢生产中采用高碱度合成渣在出钢过程中脱硫冶炼轴承钢、钢包静态脱气等初步精炼技术,但没有精炼的装备。60年代中期至70年代有些特钢企业(大冶、武钢等)引进一批真空精炼设备。80年代我国自行研制开发的精炼设备逐渐投入使用(如LF炉、喷粉、搅拌设备),黑龙江省冶金研究所等单位联合研制开发了喂线机、包芯线机和合金芯线,完善了炉外精炼技术的辅助技术。目前,我国已经拥有了一套完善的精炼设备,其中包括LF、RH、VOD、VAD、AOD等精炼设备。由于炉外精炼技术的发展,也促进了炼钢生产工艺更加合理完善,原有炼钢炉已成为一种初炼炉,其精炼功能逐步由炉外精炼设施承担,从而减轻了炼钢炉负荷,提高了炼钢炉的生产能力和改善了炼钢炉的作业指标。
4.
答:洁净钢是由Kiessling于1962年首次提出,泛指O,S,P,H,N及Pb,As,Cu,Zn等杂质含量低的钢。一般意义上的洁净钢是指对钢中非金属夹杂物(主要是氧化物、硫化物)进行严格控制的钢种,主要包括:钢中总氧含量低,非金属夹杂物数量少、尺寸小、分布均匀及合适的夹杂物形状。
冶炼流程:
设计思路:(1)先对原料进行高炉熔炼,通过高温氧化还原反应提取铁矿石中的铁,分离出的铁水作为炼钢原料;(2)生铁中一般S含量较高,S在生铁中是有害元素,它促进铁与碳的结合,使铁硬脆,并与铁化合成低熔点的硫化铁,使生铁产生热脆性和减低铁液的流动性。铁水脱硫是一种经济、有效的脱硫方法。同时,铁水预脱硫能减轻转炉负担,提高冶炼效率,使转炉采用低硫铁水冶炼,有利于进一步降低钢水中硫含量,满足用户对超低硫的要求。(3)对铁水进行“三脱”(脱硅、脱磷、脱硫)预处理,可经济有效的去除其中的过高的有害成分磷、硅,并进一步降低硫含量,可有利于实现转炉少渣冶炼。(4)传统冶炼渣量大,炉渣利用率低,难以实现炉渣循环利用。转炉渣量随铁水[Si]波动通常为为100~120kg/t,炼钢产生的大量炉渣往往无法在炼钢生产过程中直接返回利用,造成大量炉渣外排,严重影响环境。而经过铁水进行三脱之后,可以应用转炉少渣冶炼,可大量减少炼钢渣量,并能提高冶炼速度;(5)通过RH真空冶炼,去除钢中H、O、N等有害气体含量,进一步提高钢液质量;(6)对钢液进行浇注,生产出符合要求的洁净钢。
钢中夹杂物的产生与去除途径
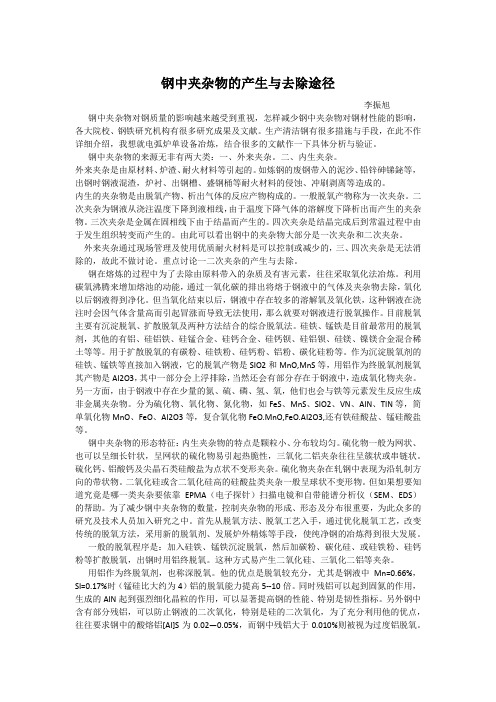
钢中夹杂物的产生与去除途径李振旭钢中夹杂物对钢质量的影响越来越受到重视,怎样减少钢中夹杂物对钢材性能的影响,各大院校、钢铁研究机构有很多研究成果及文献。
生产清洁钢有很多措施与手段,在此不作详细介绍,我想就电弧炉单设备冶炼,结合很多的文献作一下具体分析与验证。
钢中夹杂物的来源无非有两大类:一、外来夹杂。
二、内生夹杂。
外来夹杂是由原材料、炉渣、耐火材料等引起的。
如炼钢的废钢带入的泥沙、铅锌砷锑鉍等,出钢时钢液混渣,炉衬、出钢槽、盛钢桶等耐火材料的侵蚀、冲刷剥离等造成的。
内生的夹杂物是由脱氧产物、析出气体的反应产物构成的。
一般脱氧产物称为一次夹杂。
二次夹杂为钢液从浇注温度下降到液相线,由于温度下降气体的溶解度下降析出而产生的夹杂物。
三次夹杂是金属在固相线下由于结晶而产生的。
四次夹杂是结晶完成后到常温过程中由于发生组织转变而产生的。
由此可以看出钢中的夹杂物大部分是一次夹杂和二次夹杂。
外来夹杂通过现场管理及使用优质耐火材料是可以控制或减少的,三、四次夹杂是无法消除的,故此不做讨论。
重点讨论一二次夹杂的产生与去除。
钢在熔炼的过程中为了去除由原料带入的杂质及有害元素,往往采取氧化法冶炼。
利用碳氧沸腾来增加熔池的动能,通过一氧化碳的排出将熔于钢液中的气体及夹杂物去除,氧化以后钢液得到净化。
但当氧化结束以后,钢液中存在较多的溶解氧及氧化铁,这种钢液在浇注时会因气体含量高而引起冒涨而导致无法使用,那么就要对钢液进行脱氧操作。
目前脱氧主要有沉淀脱氧、扩散脱氧及两种方法结合的综合脱氧法。
硅铁、锰铁是目前最常用的脱氧剂,其他的有铝、硅铝铁、硅锰合金、硅钙合金、硅钙钡、硅铝钡、硅镁、镍镁合金混合稀土等等。
用于扩散脱氧的有碳粉、硅铁粉、硅钙粉、铝粉、碳化硅粉等。
作为沉淀脱氧剂的硅铁、锰铁等直接加入钢液,它的脱氧产物是SIO2和MnO,MnS等,用铝作为终脱氧剂脱氧其产物是AI2O3,其中一部分会上浮排除,当然还会有部分存在于钢液中,造成氧化物夹杂。
转炉出钢过程中脱硫及钢中夹杂物改性_曾加庆
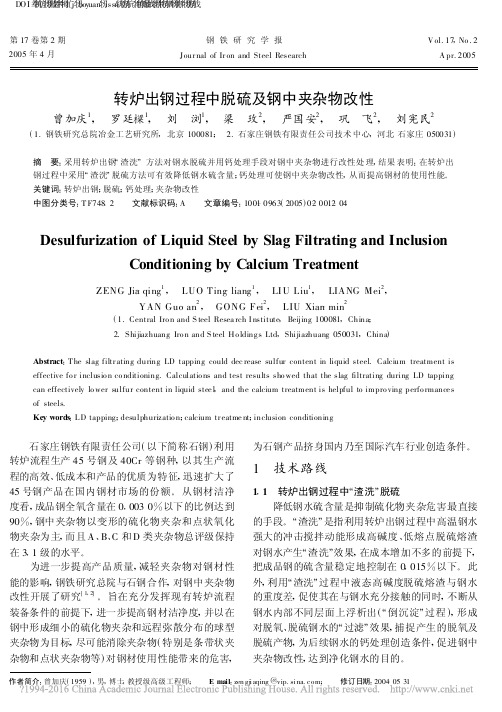
第17卷第2期2005年4月 钢铁研究学报 Jour nal of Ir on and Steel ResearchV ol.17,No.2 A pr.2005作者简介:曾加庆(1959-),男,博士,教授级高级工程师; E -mail :zen gj iaqing @ ; 修订日期:2004-05-31转炉出钢过程中脱硫及钢中夹杂物改性曾加庆1, 罗廷樑1, 刘 浏1, 梁 玫2, 严国安2, 巩 飞2, 刘宪民2(1.钢铁研究总院冶金工艺研究所,北京100081; 2.石家庄钢铁有限责任公司技术中心,河北石家庄050031)摘 要:采用转炉出钢“渣洗”方法对钢水脱硫并用钙处理手段对钢中夹杂物进行改性处理,结果表明:在转炉出钢过程中采用“渣洗”脱硫方法可有效降低钢水硫含量;钙处理可使钢中夹杂物改性,从而提高钢材的使用性能。
关键词:转炉出钢;脱硫;钙处理;夹杂物改性中图分类号:T F748.2 文献标识码:A 文章编号:1001-0963(2005)02-0012-04Desulfurization of Liquid Steel by Slag Filtrating and InclusionConditioning by Calcium TreatmentZENG Jia -qing 1, LUO Ting -liang 1, LI U Liu 1, LIANG Mei 2,YAN Guo -an 2, GONG Fei 2, LIU Xian -min2(1.Central Iro n and S teel Resea rch I nstitute ,Beijing 100081,China ;2.Shijiazhuang Iro n and S teel Ho lding s Ltd ,Shijiazhuang 050031,China )Abstract :T he slag filtr ating during LD tapping could dec rease sulfur content in liquid steel.Calcium treatment is effective fo r inclusio n co nditioning.Calculatio ns and test results sho wed that the slag filtrating during LD tapping can effectively lo wer sulfur content in liquid stee l ,and the calcium treatment is helpful to impro ving perfo rmance s of steels.Key words :L D tapping ;desulphurizatio n ;calcium tr eatme nt ;inclusion conditioning 石家庄钢铁有限责任公司(以下简称石钢)利用转炉流程生产45号钢及40Cr 等钢种,以其生产流程的高效、低成本和产品的优质为特征,迅速扩大了45号钢产品在国内钢材市场的份额。
合成渣精炼法控制钢帘线夹杂物形态
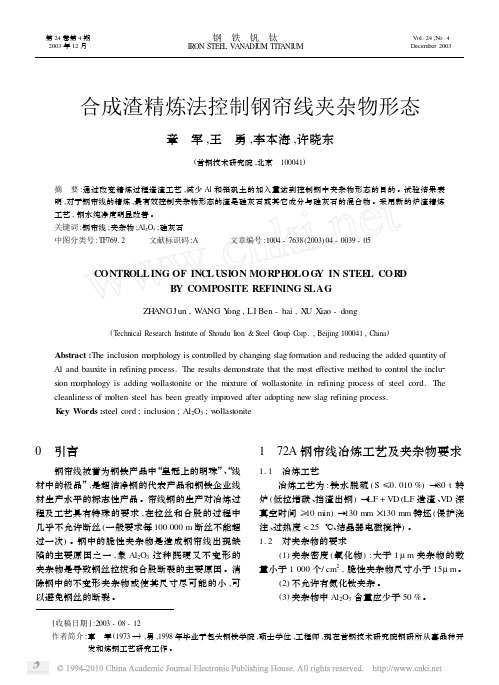
合成渣精炼法控制钢帘线夹杂物形态章 军,王 勇,李本海,许晓东(首钢技术研究院,北京 100041)摘 要:通过改变精炼过程造渣工艺,减少Al 和铝矾土的加入量达到控制钢中夹杂物形态的目的。
试验结果表明,对于钢帘线的精炼,最有效控制夹杂物形态的渣是硅灰石或其它成分与硅灰石的混合物。
采用新的炉渣精炼工艺,钢水纯净度明显改善。
关键词:钢帘线;夹杂物;Al 2O 3;硅灰石中图分类号:TF769.2 文献标识码:A 文章编号:1004-7638(2003)04-0039-05CONTR OLLING OF INCL USION MORPH OLOG Y IN STEE L COR DB Y COMPOSITE REFINING SLAGZH ANGJun ,W ANG Y ong ,LI Ben -hai ,X U X iao -dong(T echnical Research Institute of Shoudu Iron &S teel G roup C orp.,Beijing 100041,China )Abstract :The inclusion m orphology is controlled by changing slag formation and reducing the added quantity of Al and bauxite in refining process.The results dem onstrate that the m ost effective method to control the inclu 2sion m orphology is adding w ollastonite or the mixture of w ollastonite in refining process of steel cord.The cleanliness of m olten steel has been greatly im proved after adopting new slag refining process.K ey Words :steel cord ;inclusion ;Al 2O 3;w ollastonite0 引言 钢帘线被誉为钢铁产品中“皇冠上的明珠”、“线材中的极品”,是超洁净钢的代表产品和钢铁企业线材生产水平的标志性产品。
炉外精炼--合成渣洗

2.2.2.1 合成渣的乳化和上浮
合成渣有液态渣和固态渣,多数为液态渣。
合成渣洗的主要目的是降低钢中的氧,硫 和非金属夹杂物含量,它可以把[O]降至 0.002%、[S]降至0.005%甚至0.003%。
合成渣洗过程:在一个专门容器内(一般 使用电弧炉)熔炼合成渣(液态),炉渣温 度控制在1680~1750ºC,出钢前将熔炼好 的合成渣倒入钢包内并移至炉下,在出钢 过程中钢液流冲击包内的合成渣,充分搅 拌,钢液与合成渣充分接触,使钢液得到 渣洗。为了使钢渣充分搅拌接触,需大出 钢口、深坑出钢,即钢水有一定的冲击力, 钢流有一定的高度和速度,使钢水尽快出 净。混冲高度一般为3~4米,出钢时间要 短,如10t炉子35~55秒,20t炉子45~50 秒,合成渣用量一般为钢水量的5~6%, 进行渣洗的钢液出钢前应扒除炉渣,然后 再出钢。
2.1.1 挡渣技术
做好出钢时的挡渣操作,尽可能地减少 初炼炉的氧化渣进入钢包内是发挥精炼 渣精炼做用的前提。
2.1.1 挡渣技术
为消除或把带入钢包内的渣量降至最低, 目前用于工业生产的挡渣技术有: ( l )挡渣球。( 2 )浮动塞挡渣。( 3 )气动吹气挡渣塞。( 4 )虹吸出钢口 挡渣。( 5 )偏心炉底出钢
2.1.2 顶渣改质
钢包顶渣(覆盖渣)主要由转炉出钢过 程中流入钢包的渣和铁合金脱氧产物所 形成的渣层组成,渣的氧化性高,碱度 低。
钢包顶渣改质是当前普遍应用的一种钢 包顶渣调质工艺。
精炼渣对60Si2Mn弹簧钢中氧含量及夹杂物的影响
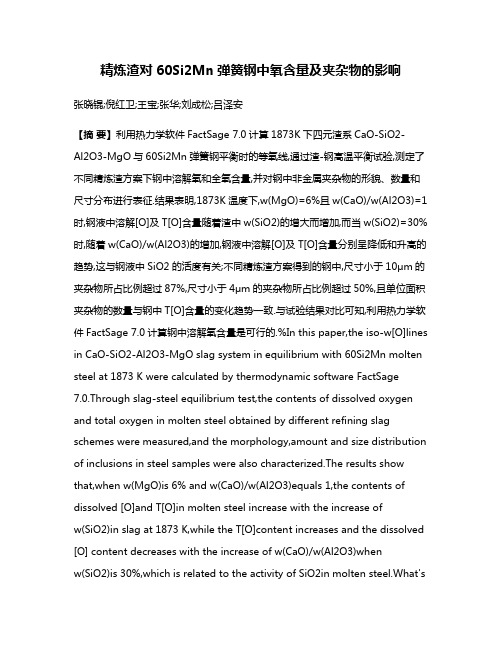
精炼渣对60Si2Mn弹簧钢中氧含量及夹杂物的影响张晓锟;倪红卫;王宝;张华;刘成松;吕泽安【摘要】利用热力学软件FactSage 7.0计算1873K下四元渣系CaO-SiO2-Al2O3-MgO与60Si2Mn弹簧钢平衡时的等氧线,通过渣-钢高温平衡试验,测定了不同精炼渣方案下钢中溶解氧和全氧含量,并对钢中非金属夹杂物的形貌、数量和尺寸分布进行表征.结果表明,1873K温度下,w(MgO)=6%且w(CaO)/w(Al2O3)=1时,钢液中溶解[O]及T[O]含量随着渣中w(SiO2)的增大而增加,而当w(SiO2)=30%时,随着w(CaO)/w(Al2O3)的增加,钢液中溶解[O]及T[O]含量分别呈降低和升高的趋势,这与钢液中SiO2的活度有关;不同精炼渣方案得到的钢中,尺寸小于10μm的夹杂物所占比例超过87%,尺寸小于4μm的夹杂物所占比例超过50%,且单位面积夹杂物的数量与钢中T[O]含量的变化趋势一致.与试验结果对比可知,利用热力学软件FactSage 7.0计算钢中溶解氧含量是可行的.%In this paper,the iso-w[O]lines in CaO-SiO2-Al2O3-MgO slag system in equilibrium with 60Si2Mn molten steel at 1873 K were calculated by thermodynamic software FactSage7.0.Through slag-steel equilibrium test,the contents of dissolved oxygen and total oxygen in molten steel obtained by different refining slag schemes were measured,and the morphology,amount and size distribution of inclusions in steel samples were also characterized.The results show that,when w(MgO)is 6% and w(CaO)/w(Al2O3)equals 1,the contents of dissolved [O]and T[O]in molten steel increase with the increase ofw(SiO2)in slag at 1873 K,while the T[O]content increases and the dissolved [O] content decreases with the increase of w(CaO)/w(Al2O3)whenw(SiO2)is 30%,which is related to the activity of SiO2in molten steel.What'smore,in steel samples obtained by different refining slag schemes,the propotion of inc lusions with size less than 10 μm and 4 μm is more than 87% and 50%, respectively,and the variation of inclusion amounts per unit areais consistent with the change of T[O]content in pared with experimental results,it's feasible to predict the dissolved oxy-gen contentby thermodynamic software FactSage 7.0.【期刊名称】《武汉科技大学学报(自然科学版)》【年(卷),期】2017(040)005【总页数】7页(P326-332)【关键词】60Si2Mn弹簧钢;CaO-SiO2-Al2O3-MgO精炼渣;全氧含量;非金属夹杂物;SiO2活度【作者】张晓锟;倪红卫;王宝;张华;刘成松;吕泽安【作者单位】武汉科技大学省部共建耐火材料与冶金国家重点实验室,湖北武汉,430081;武汉科技大学省部共建耐火材料与冶金国家重点实验室,湖北武汉,430081;武汉科技大学省部共建耐火材料与冶金国家重点实验室,湖北武汉,430081;武汉科技大学省部共建耐火材料与冶金国家重点实验室,湖北武汉,430081;武汉科技大学省部共建耐火材料与冶金国家重点实验室,湖北武汉,430081;武汉科技大学省部共建耐火材料与冶金国家重点实验室,湖北武汉,430081【正文语种】中文【中图分类】TF769弹簧钢广泛应用于飞机、高铁等运输工具及各类工程机械设备中,对其耐疲劳性、抗震性及抗弹减性均有很高要求。