精益生产(1小时了精益生产)
精益生产

零浪费的生产
精益生产(Lean production)是美国麻省理工学 院数位国际汽车计划组织(IMVP)的专家对日本 “丰田JIT(Just In Time)生产方式”的赞誉之称
精,
即少而精,
不投入多余的生产要素,
只
是在适当的时间生产必要数量的市场急需产 品 (或下道工序急需的产品) ; 益 , 即所有
Masaaki lmai:改善协会的创始人和主席
18
意识改善-态度是一切工作的开始
心 变 则 态 度 变 态 度 变 行 为 变 行为变习惯随着变 习 惯 变 人 格 变 人格变人生就会变
19
认识浪费
what is the wastes
什么是浪费:
不增加价值的活动,是浪费;
尽管是增加价值的活动,所用的资源超 过了“绝对最少”的界限,也是浪费。
精益管理 体系的建 立与落实
精益生产 的公司试 点与强化 推进
精益生产 目标的设 定和跟进
精益生产 的指导和 教育、与 素养育成
精益生产 的智慧发 挥和改善 实施
精益生产的终极目标
1. 2. 3. 4. 5. 6. 7. “零”转产工时浪费(Products) “零”库存(Inventory) “零”浪费(Cost) “零”不良(Quality) “零”故障(Maintenance) “零”停滞(Delivery) Focus on “零”灾害(Safety) 零浪费
15
Cell/Line Flexibility柔性生产线
•Takt=40 sec •Cycle=120 sec •Operators=3
•Takt=30 sec •Cycle=120 sec •Operators=4
精益生产管理常用术语
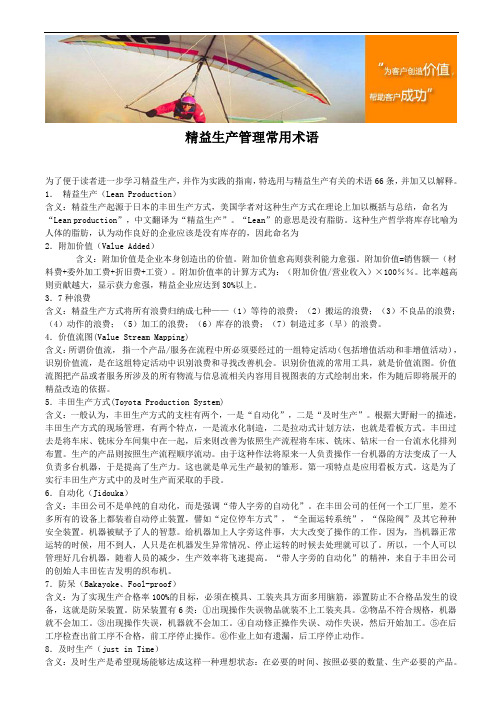
精益生产管理常用术语为了便于读者进一步学习精益生产,并作为实践的指南,特选用与精益生产有关的术语66条,并加又以解释。
1.精益生产(Lean Production)含义:精益生产起源于日本的丰田生产方式,美国学者对这种生产方式在理论上加以概括与总结,命名为“Lean production”,中文翻译为“精益生产”。
“Lean”的意思是没有脂肪。
这种生产哲学将库存比喻为人体的脂肪,认为动作良好的企业应该是没有库存的,因此命名为2.附加价值(Value Added)含义:附加价值是企业本身创造出的价值。
附加价值愈高则获利能力愈强。
附加价值=销售额—(材料费+委外加工费+折旧费+工资)。
附加价值率的计算方式为:(附加价值/营业收入)×100%%。
比率越高则贡献越大,显示获力愈强,精益企业应达到30%以上。
3.7种浪费含义:精益生产方式将所有浪费归纳成七种——(1)等待的浪费;(2)搬运的浪费;(3)不良品的浪费;(4)动作的浪费;(5)加工的浪费;(6)库存的浪费;(7)制造过多(早)的浪费。
4.价值流图(Value Stream Mapping)含义:所谓价值流,指一个产品/服务在流程中所必须要经过的一组特定活动(包括增值活动和非增值活动),识别价值流,是在这组特定活动中识别浪费和寻找改善机会。
识别价值流的常用工具,就是价值流图。
价值流图把产品或者服务所涉及的所有物流与信息流相关内容用目视图表的方式绘制出来,作为随后即将展开的精益改造的依据。
5.丰田生产方式(Toyota Production System)含义:一般认为,丰田生产方式的支柱有两个,一是“自动化”,二是“及时生产”。
根据大野耐一的描述,丰田生产方式的现场管理,有两个特点,一是流水化制造,二是拉动式计划方法,也就是看板方式。
丰田过去是将车床、铣床分车间集中在一起,后来则改善为依照生产流程将车床、铣床、钻床一台一台流水化排列布置。
精益生产概述

精益生产概述一、方法起源精益生产(LP),也称精益制造、精良生产,是美国麻省理工学院数位国际汽车计划组织的专家,在研究日本丰田准时化生产0口)生产方式的过程中提出来的,被认为是目前工业界最佳的生产组织体系和方式之一.(1)精,即少而精,不投入多余的生产要素,只是在适当的时间生产必要数量的市场急需产品(或下道工序急需的产品)。
(2)益,即对所有经营活动要有益有效,具有经济效益。
二、方法核心LP方式jrr是一种以最大限度减少企业生产所占用资源,降低企业管理和运营成本为主要目标的生产方式,是一种理念和文化。
1、LP的本质LP方式jrr的实质是管理过程,在过程管理中实现零浪费,具体如以下几点:人事组织管理优化,精筒中间管理层,实施组织扁平化,减少非直接生产人员。
(2)推行生产均衡化同步化,实现零库存与柔性生产。
(3)推行生产过程的质量保证体系,实现零不良.(4)减少和降低任何环节上的浪费,实现零浪费。
(5)最终实现拉动式准时化生产方式(jrr)2、LP终极目标LP终极目标是“零浪费”,具体七大目标如下:(1)零转产工时浪费:将工序品种切换与装配线转产的时间浪费将为"零”或接近为“零”(2)零库存:将加工与装配相连接流水化,消除中间库存,变市场预估生产为接单同步生产, 将产品库存将为“零、(4)“零”故障:消除机械设备的故障停机,实现“零”故障(5)“零”不良:应该在生产的源头消除不良,追求“零”不良。
(6)“零”停滞:最大限度地压缩前置时间,消除中间停滞,实现“零”停滞。
(7)“零”灾害:人、工厂、产品全面安全预防检查,实行安全巡查制度,实现“零”灾害。
三、方法体系1、识别浪费的方法识别浪费的方法包括质量新老七大手法、增值分析法、价值流分析法、防呆法(FoolProof),还包括挖掘客户需求的QFD工具体系。
2、解决浪费问题所需的工具与方法精益3(LeanSixSigm分缩写为LLS)是精益生产与精益6。
精益生产名词解释

精益生产名词解释一、何为精益生产?精益生产管理,是一种以客户需求为拉动,以消除浪费和不断改善为核心,使企业以最少的投入获取成本和运作效益显著改善的一种全新的生产管理模式。
它的特点是强调客户对时间和价值的要求,以科学合理的制造体系来组织为客户带来增值的生产活动,缩短生产周期,提高质量,从而显著提高企业适应市场万变的能力。
精益生产管理就是控制浪费、降低成本的最有效的一种生产管理方式。
二、什么叫八大浪费八大浪费是定义工厂在JIT生产方式中的,其浪费的含义与社会上通常所说的浪费有所区别。
对于JIT 来讲,凡是超出增加产品价值所必需的绝对最少的物料、设备、人力、场地和时间的部分都是浪费。
因此,JIT生产方式所讲的工厂的浪费归纳为八大种,分别是:不良、修理的浪费,过分加工的浪费,动作的浪费,搬运的浪费,库存的浪费,制造过多过早的浪费,等待的浪费和管理的浪费,简称为八大浪费。
三、何为6S6S 起源于日本,指的是在生产现场中将人员、机器、材料、操作方法等生产要素进行有效管理,它针对企业中每位员工的日常行为方面提出要求,倡导从小事做起,力求使每位员工都养成事事“讲究”的习惯,从而达到提高整体工作质量的目的。
6S就是整理(SEIRI)、整顿(SEITON)、清扫(SEISO)、清洁(SEIKETSU)、素养(SHITSUKE)、安全(SAFETY)六个项目,因均以“S”开头,简称6S。
四、价值流价值流是指从原材料转变为成品的物料、信息流、时间流等,并给它赋予价值的全部活动,包括从供应商处购买的原材料到达企业,企业对其进行加工后转变为成品再交付客户的全过程,企业内以及企业与供应商、客户之间的信息沟通形成的信息流也是价值流的一部分。
一个完整的价值流包括增值和非增值活动,如供应链成员间的沟通,物料的运输,生产计划的制定和安排以及从原材料到产品的物质转换过程等。
五、团队和团队建设团队是指为了实现某一目标而由相互协作的个体所组成的正式群体。
什么是精益生产方式

什么是精益生产方式
精益生产方式是指综合运用多种现代管理方法和手段,以客户需求为依据,充分发挥全体员工的积极性为根本,对企业的各项资源进行有效配置和合理使用,最大限度地为企业谋求经济利益的一种新型生产方式,是全员参与持续改善的一种管理状态。
也是一种适时制造,消除一切浪费和故障,向零缺陷、零库存努力的新型生产管理方式。
精益生产方式的核心实质是要求企业运用精益思维消除一切浪费,以降低生产成本,并以服务对象的需求为依据进行生产,鼓励员工的全面参与,持续改进质量、持续改善工作的一种管理运营方式。
目标是彻底消除无效劳动和浪费,以最小的资源投入为顾客提供及时的产品与服务,为客户创造出尽可能多的价值,最终最大限度地为企业创造经济效益。
精益生产既是一种以最大限度地减少企业生产中所使用的资源和降低企业管理运营成本为主要目标的生产模式,同时它也是一种理念,是支撑个人与企业生命的一种精神力量,是一种员工精益求精无止境追求的企业文化。
精益生产方式是以企业内部、外部客户的需求拉动式生产为特点,有别于以往推动式生产方式,坚持全员参与、持续改善的工作方法,通过准时化生产(JIT),看板管理、作业研究、5S管理、全面质量管理、可视化管理、标准化、现场管理、人本管理、弹性作业、项目团队工作法、并行工程、TPM等有效的方法和手段消除一切浪费,向零缺陷、零库存进军,最终确保Q(质量)C(成本)D(交货期)S(安全)目标的实现与提高。
精益生产管理的十大工具和实施步骤
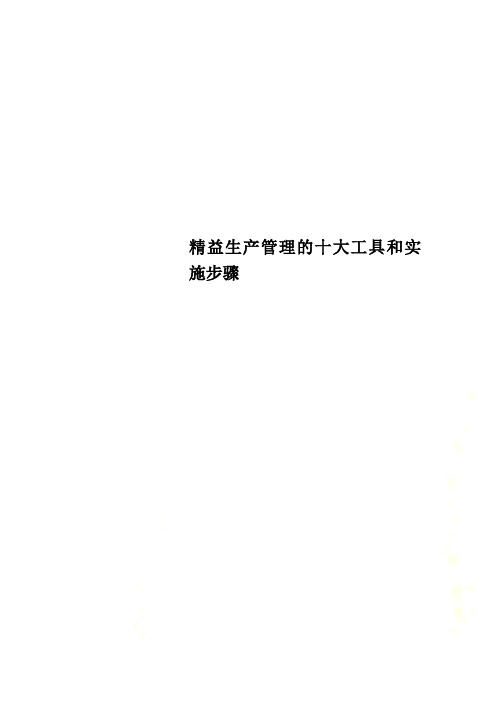
施步骤施步骤一、何为精益生产精益生产(LeanProduction,简称LP)是美国麻省理工学院数位国际汽车计划组织(IMVP)的专家对日本“丰田JIT(JustInTime)生产方式”的赞誉之称,精,即少而精,不投入多余的生产要素,只是在适当的时间生产必要数量的市场急需产品(或下道工序急需的产品);益,即所有经营活动都要有益有效,具有经济性。
精益生产是当前工业界最佳的一种生产组织体系和方式。
精益生产既是一种以最大限度地减少企业生产所占用的资源和降低企业管理和运营成本为主要目标的生产方式,同时它又是一种理念,一种文化。
实施精益生产就是决心追求完美的历程,也是追求卓越的过程,它是支撑个人与企业生命的一种精神力量,也是在永无止境的学习过程中获得自我满足的一种境界。
其目标是精益求精,尽善尽美,永无止境的追求七个零的终极目标。
二、精益生产的四个特点大部分的企业都已经认识到了精益生产对企业的一个重要性,当然精益生产管理企业也是一样的,精益生产在一定的程度上会让企业的生产效率提高,同时还可以在一定的程度上增强企业的自己的竞争能力,但是虽然很多的企业都想实行精益管理,但是却没有真正的明白精益生产的一个特点,那么精益生产管理有什么特点呢?1、消除一切浪费,追求精益求精精益生产的特点是消除一切浪费,追求精益求精和不断改善。
去掉生产环节中一切无用的东西,每个工人及其岗位的安排原则是必须增值,撤除一切不增值的岗位。
精简是它的核心,精简产品开发设计、生产、管理中一切不产生附加值的工作,旨在以最优品质、最低成本和最高效率对市场需求作出最迅速的响应。
2、强调人的作用,发挥人的潜力精益生产方式把工作任务和责任最大限度地转移到直接为产品增值的工人身上。
而且任务分到小组,由小组内的工人协作承担。
为此,要求工人精通多种工作,减少不直接增值的工人,并加大工人对生产的自主权。
当生产线发生故障,工人有权自主决定停机,查找原因,做出决策。
精益生产

准时生产,系统配置,适时供货
(消除多次装配,多次包装,多次运输,多次受损)
信息资源充分共享
(信息传递快速,准确,面广,同步,消除不必要的探索)
精益生产 Lean Manufacture
什么是符合现代 精益生产的制造系统
制造系统的简化和优化 是通过过程中相互依赖 的要素均衡实施来达到
精益生产 Lean Manufacture
多技能作业
一专多能的操作技能 纵向看管作业 跨工艺多样培训
精益生产 Lean Manufacture
合理化作业
U型流水作业 模块菜单式拼装作业 集群控制作业
精益生产 Lean Manufacture
三种流水作业方式
传统流水作业线 U型流水作业线 模块菜单式装配线
三种流水作业方式
精益生产 Lean Manufacture
2.过度超时库存 工序之间零件的停滞 供应商提供的物品过多
如何定义七种主要浪费
精益生产 Lean Manufacture
3.生产废次产品 生产有缺陷的零件与产品
纠正缺陷零件或产品的消耗
如何定义七种主要浪费
精益生产 Lean Manufacture
4.不必要的动作 加工中与过程优化没有关系的动作
加工中不能改善产品质量的动作
导致浪费的原因----不均衡
物料流动的不均衡 作业负荷的不均衡 运行节拍的不均衡 员工能力的不均衡
如何定义七种主要浪费
精益生产 Lean Manufacture
导致浪费的原因----超负荷
设备运行超负荷 员工能力超负荷 员工体能超负荷 安全规范超负荷
精益生产 Lean Manufacture
精益生产的管理技术
零差错作业
精益生产的定义

精益生产的定义什么是精益生产?精益生产是一种管理理念和生产方法,旨在通过最大程度地减少资源浪费,以实现高效生产和提供价值给客户。
精益生产的核心原则是通过不断改善流程,消除浪费,提高生产效率和质量。
这一理念最初起源于丰田汽车公司的生产体系,后来被广泛应用于其他行业和领域。
精益生产的目标精益生产的主要目标是实现以下几点:1.提高生产效率:通过消除浪费,优化流程,提高生产效率和生产率。
2.降低成本:通过减少废品和不必要的生产成本,实现成本的最小化。
3.提高产品质量:通过改进生产过程和流程控制,提高产品质量和稳定性。
4.提高客户满意度:通过及时交付高质量的产品,提高客户满意度和忠诚度。
精益生产的原则精益生产遵循一些核心原则,其中包括:1.价值:专注于为客户创造价值,只集中精力和资源在对客户有意义的活动上。
2.价流:优化价值流动,消除所有形式的浪费,确保产品/服务按需求流动。
3.拉动:基于客户需求拉动生产,避免过度生产和库存积压。
4.流程改进:不断改进生产过程,强调团队合作和持续学习。
5.标准化:建立标准化工作流程和操作规程,确保质量和稳定性。
精益生产的实践精益生产的实践方法包括:1.价值流分析:分析整个价值流,识别不必要的步骤和浪费。
2.5S整理法:通过整理、整顿、清扫、清洁、标准化等步骤,改善工作环境和效率。
3.持续改进:建立改进文化和机制,鼓励员工提出改进建议和参与改进活动。
4.精益供应链管理:与供应商建立紧密合作关系,实现供应链的高效协同和配合。
精益生产的应用范围精益生产不仅适用于制造业,也适用于服务业和其他领域。
在制造业中,精益生产可以帮助企业提高生产效率、降低成本、改善质量;在服务业中,精益生产可以帮助企业提高服务效率、提升客户体验、降低服务成本。
总结精益生产是一种重要的管理理念和生产方法,其核心目标是通过最大程度地减少浪费,实现高效生产和提供价值给客户。
精益生产的原则和实践方法可以帮助企业提高生产效率、降低成本、改善质量,从而获得持续竞争优势。
《精益生产》学习心得范文(三篇)

《精益生产》学习心得范文精益生产是一种高效率的生产管理方法,旨在减少浪费和提高生产流程。
我读完《精益生产》后,对于这一方法有了深刻的认识和理解。
以下是我在学习过程中的心得体会。
首先,精益生产强调的是持续改进。
在传统生产管理中,常常出现因为局限性的思维定式而无法寻求新的解决办法的情况。
而精益生产提倡的是通过不断的改进来实现生产的高效率。
它不仅关注于产量的提高,更注重于提高产品质量以及满足客户需求。
这使我意识到,在现代企业管理中,不断改进是取得持续竞争优势的关键。
其次,精益生产强调的是价值流思维。
价值流指的是完成一个产品所需要的所有流程和活动。
而精益生产的目标是将非价值创造的活动减少至最低。
在学习中,我了解到通过对生产流程的深入分析,可以发现并去除所有无效的环节,从而提高生产效率。
这让我认识到,在管理生产流程时,必须对每个环节进行审视,找到并消除浪费,从而提高整体生产效率。
再次,精益生产注重的是团队合作。
书中提到,要想实现精益生产,必须建立一个具备团队精神的组织文化。
这是因为精益生产需要各个部门之间紧密协作,共同解决问题,而不是各自为战。
在阅读过程中,我了解到只有通过鼓励员工之间的合作和沟通,才能形成高效的团队。
这让我明白,精益生产不仅是一种方法,更是一种组织变革。
只有通过团队合作,才能真正实现生产效率的提高。
最后,精益生产还强调的是标准化管理。
标准化管理是为了提高工作的稳定性和可靠性。
通过标准化,员工可以清楚地知道自己的工作内容以及工作要求。
这让我认识到,在管理生产过程中,必须建立一套稳定的工作流程和标准化的操作方法,以保证生产的稳定和高效。
综上所述,精益生产是一种高效率的生产管理方法,通过持续改进、价值流思维、团队合作和标准化管理来实现生产效率的提高。
通过学习《精益生产》,我对这一方法有了深刻的认识和理解。
在今后的工作中,我将会根据精益生产的原则和思想,不断优化生产流程,提高生产效率,为企业的发展做出贡献。
精益生产(经典课件)
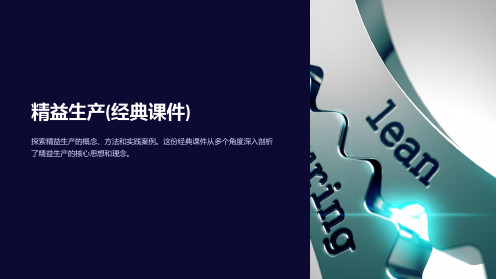
亚马逊零售业应用
精益生产方法的成功运用,将极大地提高亚马 逊的配送速度和交付准确率。
连托克成功案例
将精益生产方法成功应用于不同规模、不同产 品的生产企业。
结论
1 核心思想
2 方法
3 实战案例
价值导向、浪费削减和 流程改善。
精益生产应对了传统制造 的缺陷,使制造企业能够 更加灵活地适应市场需求。
精益生产思维和基本原则
精益生产思维
精益生产思维是一种以价值为导向、强调流程改 善和人员参与的生产方式。
基本原则
未价值增加的活动均属浪费;不合格的产品是浪 费的代表;减少浪费是精益制造的关键。
精益生产的目标和核心方法
1
少即是多
通过减少浪费、缩短生产周期、提高质量和降低成本来实现客户满意度的提升。
2
单一物流
精益生产的主要原则之一,通过减少库存和缩短运输时间来提高运营效率。
3
5S
一种工具和流程,旨在改善工作场所的卫生和安全,提高工作效率和精度。
4
快速换模(S MED)
一种生产工具和技术,能够缩短设备的准备时间,使生产任务更加高效和快速。
质量保证和流程改善
J id o k a
自动停机是精益生产的另一项核心技术,可大大提高生产线的效率和质量。
一致节奏
制定标准作业程序,使生产线上的工作效率更高,同时保证产品的质量。
价值流
通过对核心流程的改善,精益生产可以帮助企业提高产品质量和快速交付时间。
案例分析
丰田生产方式
精益生产最早的应用之一,完美地融合了精益 生产理念和实际实践。
单一物流、5S、快速换 模、Jidoka等一系列方 法和工具的综合运用。
精益生产十大手段

精益生产十大手段
精益生产是一种旨在通过减少浪费和提高效率来优化生产过程的方法。
以下是精益生产的十大手段:
1. 价值流分析:通过对生产过程中的价值流进行分析,识别出浪费和非价值增加的步骤,并提出改进措施。
2. 5S整理法:通过整理、整顿、清扫、清洁和素养的五个步骤,保持工作场所的整洁有序,提高效率和生产质量。
3. 一次性流程设计:通过优化生产过程中的流程,避免重复加工和等待时间,提高生产效率。
4. 作业标准化:通过对工作流程进行标准化,确保每个工人在相同的条件下执行相同的任务,提高生产一致性和质量。
5. 连续流水生产:通过合理安排生产顺序,消除缓冲库存和间隔时间,实现连续流水生产,提高生产效率。
6. 拉动生产方式:根据市场需求进行生产,避免过度生产和库
存积压,减少资源浪费。
7. 建立灵活的人力资源系统:通过培养多技能工人和灵活调度,实现人力资源的最优化利用,并提高响应速度和生产效率。
8. 质量管理:通过建立完善的质量管理体系,提高产品质量和
顾客满意度,减少品质问题和售后成本。
9. 持续改进:鼓励员工积极参与整个生产过程,提出改进意见,并持续跟进改进措施的实施和效果。
10. 建立合作伙伴关系:与供应商、客户和其他相关方建立合
作伙伴关系,共同优化供应链和生产流程,实现更高的效率和利益。
以上是精益生产的十大手段,通过采取这些措施,企业可以优
化生产过程,提高效率,降低成本,并提供更高质量的产品和服务。
精益生产是什么

精益生产是什么精益生产(Lean Manufacturing),又称为精益生产管理或精益制造,是一种强调生产过程中消除浪费、提高效率和质量的管理方式。
它起源于丰田汽车公司,通过优化生产流程和资源利用,帮助企业实现高效、高质量的生产。
本文将介绍精益生产的定义、原则、特点以及实施步骤。
1. 定义精益生产是一种基于消除浪费和提高价值增长的生产方法。
它从资源和生产流程的角度出发,通过减少无效活动和资源浪费,以最少的资源创造出最大的价值。
精益生产强调持续改进和员工参与,旨在提高效率、降低成本、提高质量和满足客户需求。
2. 原则精益生产依据一系列原则进行实施,这些原则有助于指导企业在生产过程中消除浪费和提高效率。
以下是精益生产的主要原则:2.1 价值定义精益生产强调以客户需求为导向,确定什么是对客户有价值的。
通过仔细分析价值流,企业可以识别出哪些步骤和活动是为客户创造价值的,从而优化生产流程。
2.2 流程优化流程优化是精益生产的核心原则之一。
通过分析和优化生产流程,消除不必要的步骤和环节,减少产出的浪费和资源的浪费。
2.3 拉动生产拉动生产是指根据内部和外部需求进行生产,而不是根据预测的需求。
这种方式可以避免过度生产和库存积压,提高生产响应速度。
2.4 持续改进持续改进是精益生产的重要原则之一。
通过不断地改进生产流程和方法,寻求效率和质量的提升,并培养员工参与改进的习惯。
2.5 资源最优化精益生产强调尽可能最大化资源的利用效率。
通过避免不必要的浪费和合理分配资源,提高效率和质量。
3. 特点精益生产具有以下几个特点:3.1 去除浪费精益生产通过消除生产过程中的各种浪费,例如等待时间、运输时间、制造缺陷等,实现资源的最优利用。
3.2 质量优先精益生产强调短期和长期的质量目标。
通过提升质量控制和员工参与,减少缺陷和重新制造,提高质量水平。
3.3 灵活性精益生产追求产品和生产流程的灵活性,以便根据市场需求进行调整和改变。
精益生产主要内容

二、精益生产的主要内容精益生产的内容主要包括减少浪费、准时化生产、“三现"主义和持续改善等四各方面。
1、减少浪费减少浪费就是把生产分为纯作业、浪费作业和附加作业的基础上,把不产生附加值的一切作业包括浪费作业和附加作业都当做浪费。
并指出了七大浪费:生产过程的浪费、制造不良产品的浪费、停工等活的浪费、动作上的浪费、搬运的浪费、加工本身的浪费、库存的浪费等。
在此基础上提出了消除浪费的多种方法.2、准时化生产准时化生产是按照需要的量生产需要的产品以满足各个工序的生产。
准时化生产是以“均衡化生产”为前提条件,由“生产的流程化"、“确定符合需要数量的节拍时间”和“后道工序在必要的时刻到前道工序去领取必要的必要品”三种思想观念组成。
均衡化生产是使产品稳定地平均流动,避免在作业过程中产生不均衡的状态。
生产的流程化就是以流水线来生产产品的生产方式。
生产流程化可以消除各道工序内部、各道工序之间的物资停滞,实现一个生产流。
节拍时间是生产一个产品所花费的时间,是一天的工作时间和一天的需求量的比值,即作业速度。
解决方法:彻底实施标准化作业(节拍时间、作业顺序、标准存货量);建立能够传达生产线异常信息的生产结构。
后道工序领取是指前道工序只生产后道工序所要领取的产品和数量。
按照这种生产方式就不会生产多余的产品,也就不会产生浪费.解决方法:实行看板管理、活用看板的搬运、缩短更换作业程序的时间。
3、“三现”主义“三现”主义是依照“现地(现场)”、“现物(实物)”、“现实(实际情况)”来行动的管理方法。
精益生产中的“现地”、“现物”、“现实”被形象地称为“三现”主义.“三现”主义强调管理人员不能只在办公桌上空发议论,而是要深入到“现场”中去,要用自己的双眼观察“实物",形成正确的“现实”。
丰田的“三现”主义是把它的价值观和打破常规的精神渗透到员工中去的重要手段。
解决对策:倡导“三现”主义的现场管理,必须要摒弃以往的个人特有经验的领先优势;要不断地在现场中反复实践,使管理人员不断地获得第一手的正确信息,形成现场问题正确的解决方案;大力倡导五个“为什么”的方法。
精益生产(1--概述--2)
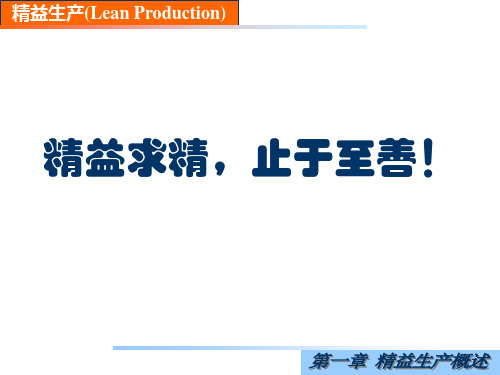
精益生产(Lean Production)
安全不容敷衍 质量不容打折——丰田公司
“踏板门”事件影响
在全世界召回910万辆汽
车(2009年丰田公司全年汽车 产量为680万辆); 用于处理召回问题车的相关
费用约135亿元;
世界汽车品牌排名由2008年
不良造成额外成本
浪费
不良造成的浪费: ☆ 不良品不能修复而产生废品时的材料损失
☆ 设备、人员和工时的损失 ☆ 额外的修复、鉴别、追加检查的损失 ☆ 有时需要降价处理产品,或者由于耽误出货 而导致工厂信誉的下降
不良产生的原因:
☆ 缺少作业标准(SOP) ☆ 员工操作失误 ☆ 原材料不良 ☆ 机器设备性能不佳 ☆ 环境问题等
精益生产(Lean Production)
丰田生产系统(TPS)——丰田屋
精益生产(Lean Production)
精 益 生 产 体 系
精益生产(Lean Production)
精益生产(Lean Production)
最佳品质、最低成本、最佳安全、最高员工士气
准时生产
(JIT)
正确时间 正确数量 正确产品
②不富裕
③文体或措词简练
④在必要性,重要性,质量或成分方面稀缺
同义词:薄,瘦削的,似骨的,消瘦的,细长的,瘦长的
反义词:肥胖的,多肉的,过重的,粗短的,肥大的
精:少而精,不投入多余的生产要素,只是在适当的时 间生产必要数量的急需产品(或下道工序急需的产品)。
益:即所有经营活动都要有益有效,具有经济性。
制造过多/过早的原因:
☆超出下一操作的需求量 ☆提前生产下一操作的需求
精益生产的衡量指标
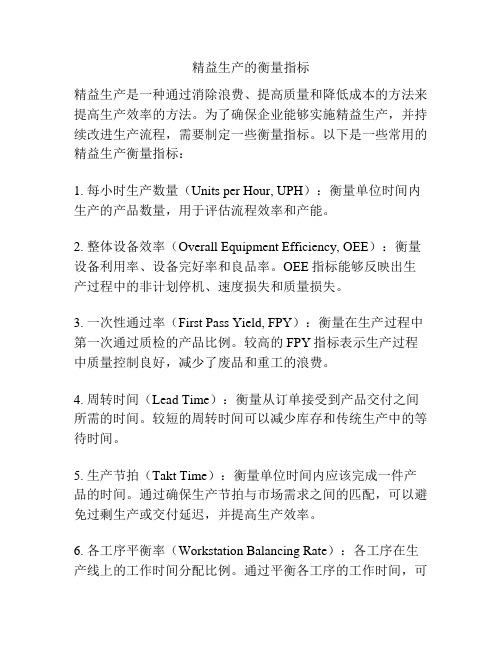
精益生产的衡量指标精益生产是一种通过消除浪费、提高质量和降低成本的方法来提高生产效率的方法。
为了确保企业能够实施精益生产,并持续改进生产流程,需要制定一些衡量指标。
以下是一些常用的精益生产衡量指标:1. 每小时生产数量(Units per Hour, UPH):衡量单位时间内生产的产品数量,用于评估流程效率和产能。
2. 整体设备效率(Overall Equipment Efficiency, OEE):衡量设备利用率、设备完好率和良品率。
OEE指标能够反映出生产过程中的非计划停机、速度损失和质量损失。
3. 一次性通过率(First Pass Yield, FPY):衡量在生产过程中第一次通过质检的产品比例。
较高的FPY指标表示生产过程中质量控制良好,减少了废品和重工的浪费。
4. 周转时间(Lead Time):衡量从订单接受到产品交付之间所需的时间。
较短的周转时间可以减少库存和传统生产中的等待时间。
5. 生产节拍(Takt Time):衡量单位时间内应该完成一件产品的时间。
通过确保生产节拍与市场需求之间的匹配,可以避免过剩生产或交付延迟,并提高生产效率。
6. 各工序平衡率(Workstation Balancing Rate):各工序在生产线上的工作时间分配比例。
通过平衡各工序的工作时间,可以避免生产线上的拥堵和等待时间,提高生产效率。
7. 变动性(Variability):衡量生产过程中的波动性和不确定性。
减少变动性可以降低生产过程中的风险和浪费。
8. 动作决策(Motion Decision):衡量生产过程中不必要的动作、移动和步骤。
通过减少不必要的动作决策,可以提高操作效率。
这些衡量指标可以帮助企业监控生产流程,并发现潜在的问题和改进机会。
根据这些指标,企业可以及时调整生产策略,降低成本,提高质量和交付效率,实现持续改进。
精益生产是一种通过消除浪费、提高质量和降低成本的方法来提高生产效率的方法。
精益生产
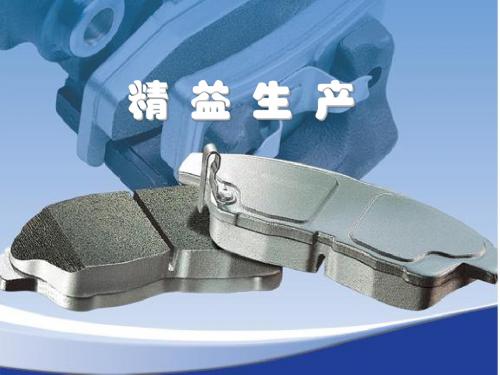
精益生产
五、精益生产方式目标和效益
(1)企业的目标就是在持续不断的提供客户满意产品的同时,追求最大化的利润。在当前很多企 业面临多品种小批量的情况下,如何有效的满足客户同时低成本的生产的困境。
(2)精益生产方式管理,是一种以顾客需求为拉动,以消灭浪费和快速反应为核心,使企业以最 少的投入获取最佳的运作效益和提高对市场的反应速度。其核心就是精简,通过减少和消除产品开 发设计、生产、管理和服务中一切不产生价值的活动(即浪费),缩短对客户的反应周期,快速实 现客户价值增值和企业内部增值,增加企业资金回报率和企业利润率。
精益生产
八、精益生产路线图
定义 价值 识别 价值流
设计 生产系统
实施 生产
执行 拉动系 统
●最佳生产系统 控制机制 ●实施单件流 ●生产线平衡 ●均衡化生产 ●看板拉动系统 ●供应商链管理 ●降低库存 ●处理剩余资产
●定义客户 和市场 ●定义价值
●当前状态价值流 ●绘制产品和信息流 ●绘制流程布局图 ●测评分析现状基础 数据
精益生产
六、 精益生产与工业工程(IE) 精益生产是当前工业界最佳的一种生产组织体系和方式。而IE则是为完成精益生产方 式的工程基础,IE又是精益生产的重要组成部分。 工业工程IE(Industrial Engineering)是对人员、物料、设备、能源和信息所组成的集 成系统进行设计、改善的一门学科。 日本企业在推行精益生产时,运用基础IE中大量的作业研究、动作研究、时间分析 术,使精益生产始终基于科学的基础上,因此生机勃勃、卓有成效。日本企业在运用IE 方面有极大的创造,使得精益生产不仅带来了生产组织方式的质变,而且带来了产品开 发、质量控制、内外协作管理、与用户关系等一连串带根本性的企业组织体制、管理体 制方面的重大变化和企业经营价值观的重大改变,其中最受影响的还包括日本企业的企 业文化。丰田汽车公司生产调查部部长中山清孝认为,丰田生产方式(JIT)就是IE在企 业中的应用。
精益生产是什么?精益生产具有哪些特点

精益生产是什么?精益生产具有哪些特点一、什么是精益生产?精益生产(LeanProduction)又称精良生产,其中“精”表示精良、精确、精美;“益”表示利益、效益等等。
精益生产就是及时制造,消灭故障,消除一切浪费,向零缺陷、零库存进军。
它是美国麻省理工学院在一项名为“国际汽车计划”的研究项目中提出来的。
它们在做了大量的调查和对比后,认为日本丰田汽车公司的生产方式是最适用于现代制造企业的一种生产组织管理方式,称之为精益生产,以针对美国大量生产方式过于臃肿的弊病。
精益生产综合了大量生产与单件生产方式的优点,力求在大量生产中实现多品种和高质量产品的低成本生产。
丰田生产方式又称精细生产方式,或精益生产方式。
二、精益生产的特点2-1、拉动式准时化生产A、以最终用户的需求为生产起点,强调物流平衡,追求零库存,要求上一道工序加工完的零件立即可以进入下一道工序。
B、组织生产线依靠一种称为看板(Kanban)的形式。
2-2、全面质量管理A、强调质量是生产出来而非检验出来的,由生产中的质量管理来保证最终质量。
B、对于出现的质量问题,一般是组织相关的技术与生产人员作为一个小组,一起协作,尽快解决。
2-3、团队工作法团队工作法(Teamwork)。
每位员工在工作中不仅是执行上级的命令。
更重要的是积极地参与,起到决策与辅助决策的作用。
组织团队的原则并不完全按行政组织来划分,而主要根据业务的关系来划分。
团队成员强调一专多能,要求能够比较熟悉团队内其他工作人员的工作,保证工作协调的顺利进行。
团队的组织是变动的,针对不同的事物,建立不同的团队,同一个人可能属于不同的团队。
2-4、并行工程并行工程(ConcurrentEngineering)。
在产品的设计开发期间,将概念设计、结构设计、工艺设计、最终需求等结合起来,保证以最快的速度按要求的质量完成。
精益生产的五大原理包括
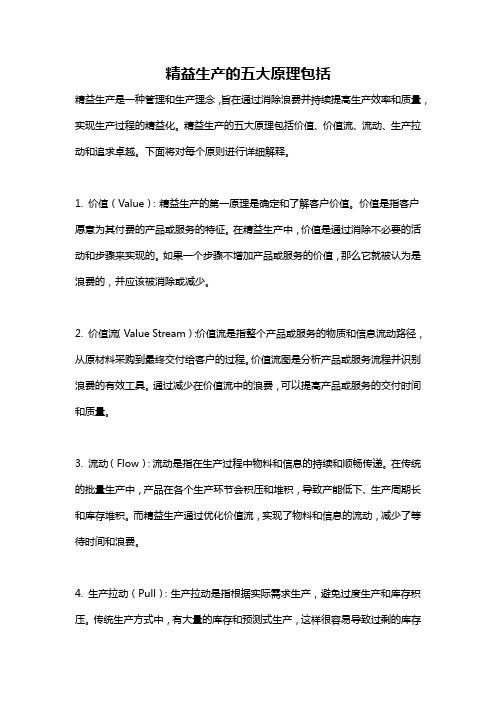
精益生产的五大原理包括精益生产是一种管理和生产理念,旨在通过消除浪费并持续提高生产效率和质量,实现生产过程的精益化。
精益生产的五大原理包括价值、价值流、流动、生产拉动和追求卓越。
下面将对每个原则进行详细解释。
1. 价值(Value):精益生产的第一原理是确定和了解客户价值。
价值是指客户愿意为其付费的产品或服务的特征。
在精益生产中,价值是通过消除不必要的活动和步骤来实现的。
如果一个步骤不增加产品或服务的价值,那么它就被认为是浪费的,并应该被消除或减少。
2. 价值流(Value Stream):价值流是指整个产品或服务的物质和信息流动路径,从原材料采购到最终交付给客户的过程。
价值流图是分析产品或服务流程并识别浪费的有效工具。
通过减少在价值流中的浪费,可以提高产品或服务的交付时间和质量。
3. 流动(Flow):流动是指在生产过程中物料和信息的持续和顺畅传递。
在传统的批量生产中,产品在各个生产环节会积压和堆积,导致产能低下、生产周期长和库存堆积。
而精益生产通过优化价值流,实现了物料和信息的流动,减少了等待时间和浪费。
4. 生产拉动(Pull):生产拉动是指根据实际需求生产,避免过度生产和库存积压。
传统生产方式中,有大量的库存和预测式生产,这样很容易导致过剩的库存和浪费。
而精益生产通过建立由客户需求驱动的生产系统,根据订单及时生产,避免了超额生产和库存积压。
5. 追求卓越(Perfection):追求卓越的原则意味着精益生产是一个持续改进的过程。
在精益生产中,通过精益工具和方法,如持续改进、标准化工作、员工参与等,不断改进和提高生产效率和质量。
以此为基础,为了更好地满足客户需求,实现更高水平的效率和质量。
综上所述,精益生产的五大原则包括价值、价值流、流动、生产拉动和追求卓越。
这些原则帮助企业识别和消除浪费,优化生产过程,提高生产效率和质量。
通过执行这些原则,企业可以实现持续改进和创造更大的价值。
- 1、下载文档前请自行甄别文档内容的完整性,平台不提供额外的编辑、内容补充、找答案等附加服务。
- 2、"仅部分预览"的文档,不可在线预览部分如存在完整性等问题,可反馈申请退款(可完整预览的文档不适用该条件!)。
- 3、如文档侵犯您的权益,请联系客服反馈,我们会尽快为您处理(人工客服工作时间:9:00-18:30)。
page 5
Bono
2 什么是精益生产
Perfect 完美 持续改善
没有任何事物 是完美的 不断改进
Value 价值 (ቤተ መጻሕፍቲ ባይዱ值时间)
站在客户 的立场上
Value Stream 价值流
精益生产系统
从接单到发货 过程的一切活动
Demand Pull
需求拉动 按需求生产
(Kanban/JIT)
象开发的河流 一样通畅流动
•Rework of a Product or Service to Meet Customer Requirements
•为了满足顾客的 要求而对产品或 服务进行较验和 返工
page 14
Bono
3.5 价值-七大浪费过程不当 Processing
•Effort which adds no value to a product or service •对最终产品或服务 •不增加价值的 •过程
40 Bending
5
PLT=
WIP
=
Exit Rate
PLT=
WIP Exit Rate
378 15
=
=
378 15
25H
=
= 3.3Days
25H
6
Station 2
Station 1
5
Satation 4
7
Sation 5
Testing
= 3.3Days
26
6
1
LF
Welding
Grinding
多个工厂/ 供应链
单个工厂
Action
Action
Action
工序
投产 交付 再用
Action
Action
Action
page 18
Bono
4 价值流
增值比率
=
增值时间(Value added time) 制造周期(Manufacturing cycle time)X 100%
增值时间:站在客户立场看制造过程中的增值动作和时间 如:改变形状、改变性能、组装、包装等
Other, more urgent, projects
Hesitation over a decision
100% savings after 1 month
Savings
~60% of gains achieved in a very short time
page 30
Bono
Tim
改善的10项基本原理
交货问题
page 10
Bono
3.2 价值-七大浪费->库存浪费 Inventory
通过降库存暴露问题
库存水平
维修问题
效率问题
质量问题
交货问题
page 11
Bono
3.2 价值-七大浪费->库存浪费 Inventory
通过降库存暴露问题
库存水平
维修问题 效率问题
质量问题
交货问题
page 12
Bono
Customers & Visitors - Plant Show Board • «Customer »Focus Board
管理方式
每周 回顾
每小时 分析
员工
每班 会议
组长 + 员工
区域每天 会议
主管 + 支援部门
每周 跨部门
支援部 门经理
周管 理会议
厂长 + 支援部门
经理
AM PM
N
major causes
SIM Cell
Employees
• Instruction Board • Hourly Tracking Board • SIM Board Cycle 1 • Performance Board
page 32
Bono
3/ Plant
Employees • Performance Board •Project Board • Information Board
Bono
3.7 价值-七大浪费多余动作 Motion
•Any movement which does not contribute value to •the product or service •任何不增加产品或服务价值的人员和设备的动作
Bono
page 17
4 价值流
价值流
概念 订单 在用
page 31
Bono
8 SIM- 即时管理
3 Levels of Communication/三个层级的
沟通
2
AEmupdloiyeeensces/参与人C员ustomers &
SIM
Visitors
Sector
• Performance Board • SIM Board Cycle 2
• Process Show Board • Product Show Board
0 30 De-barrier
30 Mylar Wrapping
Sataion 3
LE /FE
27 Bending
1
1
Station 2
Station 1
1 Satation 4
1
Sation 5
Testing
PLT=
WIP
=
124
=
Exit Rate
15
8H
Bono
page 21
= 0.6Days
精益生产 -快速了解精益生产的精髓
精益生产
• 为什么要做精益生产 • 什么是精益生产 • 价值-七大浪费 • 价值流 • 单件流 • 拉动系统 • 持续改善
• 5S
Bono 2
2
1 为什么要做精益生产
• Shorter lead time and on time delivery 快速并准时交货
1 – Individuals progress
uncoordinatedly
2 – Departments progress in
different directions
3 – Everyone contributes to reaching
objectives within a short period of time
débits horaires BIPOLAIRES : KER = 0,85
nbre personnes postées dans le flux (hors soudeuses)
1
2
3
références
DT OTR
DT
OTR DT OTR
KBC16DCB21
46
39
92
78
138 117
KBC16DCB22
page 24
Bono
6 拉动系统
page 25
Bono
6 拉动系统
不缺料 优化库存及使用面积
Bono 26
6 拉动系统看板数量计算
Quantity (Cmax * n)(2* F)(1 S) ( N -1)
两盒理念 : 每盒的数量高于两次补料周期
消耗量: 补料周期: 数量 / 产品 : 物料盒数量 : 安全系数:
3.3 价值-七大浪费物料搬运 Conveyance
•Any movement of material that does not directly support a lean system •不符合精益生产的 •一切物料搬运活动
维修问题
效率问题
质量问题
交货问题
page 13
Bono
3.4 价值-七大浪费检验/校正/返工 Inspection/Rework
1.丢弃你原来做事的老观念 2.考虑一下新的方法如何做,而不是如何不能做 3.不要相信借口,要全面否定现状 4.不要寻找完美。只要马上做,有一半的进步就可以接受了 5.在发现错误时就立即改正 6. 改善不要花很多的钱 7. 有问题就会给你提供用脑的机会 8. 至少问五次“为什么”,直到你发现问题的根本原因 9. 十个人的主意要好过一个人的,所以要利用一个改善项目 10.改善是永无止境的
• No boundary,business globalize village 无国界,业务“地球村”
page 3
Bono
1 为什么要做精益生产
Life Cycle in year
Life Cycle Change/产品生命周期
30
20
10
0 化装品 玩具
机床
食品
药品
50 年前 现在
Product Styles In Supermarket 超级市场之商品种类
Cmax ( 每小时最多产能 ) F (水蜘蛛巡线周期) n ( 每成品的零件使用数量 ) N ( XX原则,两盒体系) S (系数设定避免缺料)
消耗量: 补料周期: 数量 / 产品 : 物料盒数量 : 安全系数:
Cmax = 10 件/ 小时 F = 2 小时 n =3 N =2 S = 10%
数量 = (10 *3 *(2*(120)/ 60))*(1 + 10%)) / (2-1) 数量 = 132 pcs per box
Flow 流动 (单件流)
降低成本, 改善质量, 缩短生产周期
Bono
page 6
3 价值-七大浪费
七种浪费
1. Overproduction 过量生产 2. Inventory 库存 3. Conveyance 搬运 4. Correction 返工 5. Processing 过程不当 6. Motion 多余动作 7. Waiting 等待