精益生产之_八大浪费.doc
精益生产现场八大浪费
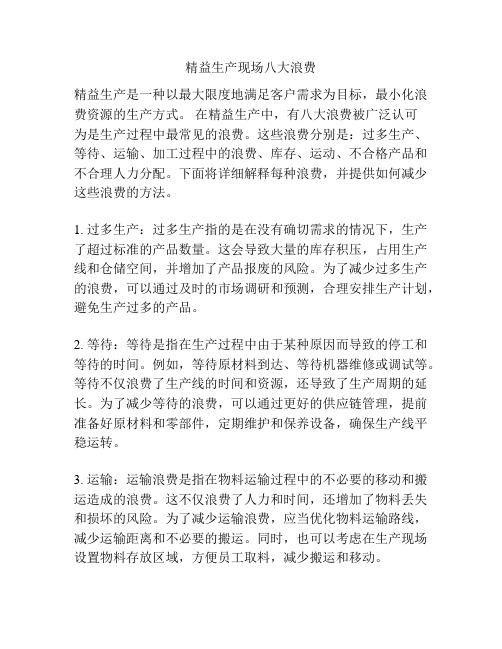
精益生产现场八大浪费精益生产是一种以最大限度地满足客户需求为目标,最小化浪费资源的生产方式。
在精益生产中,有八大浪费被广泛认可为是生产过程中最常见的浪费。
这些浪费分别是:过多生产、等待、运输、加工过程中的浪费、库存、运动、不合格产品和不合理人力分配。
下面将详细解释每种浪费,并提供如何减少这些浪费的方法。
1. 过多生产:过多生产指的是在没有确切需求的情况下,生产了超过标准的产品数量。
这会导致大量的库存积压,占用生产线和仓储空间,并增加了产品报废的风险。
为了减少过多生产的浪费,可以通过及时的市场调研和预测,合理安排生产计划,避免生产过多的产品。
2. 等待:等待是指在生产过程中由于某种原因而导致的停工和等待的时间。
例如,等待原材料到达、等待机器维修或调试等。
等待不仅浪费了生产线的时间和资源,还导致了生产周期的延长。
为了减少等待的浪费,可以通过更好的供应链管理,提前准备好原材料和零部件,定期维护和保养设备,确保生产线平稳运转。
3. 运输:运输浪费是指在物料运输过程中的不必要的移动和搬运造成的浪费。
这不仅浪费了人力和时间,还增加了物料丢失和损坏的风险。
为了减少运输浪费,应当优化物料运输路线,减少运输距离和不必要的搬运。
同时,也可以考虑在生产现场设置物料存放区域,方便员工取料,减少搬运和移动。
4. 加工过程中的浪费:加工过程中的浪费包括很多方面,例如,不必要的额外加工、过度加工、加工错误等。
这些都会增加生产时间和成本,同时也会造成不合格品和废品。
为了减少加工过程中的浪费,可以通过标准化的工艺和操作规程,提高员工的技能和培训水平,减少加工错误和废品产生。
5. 库存:库存浪费是指过多的产品、物料或半成品的库存。
这不仅占用了生产线和仓储空间,还增加了物料报废和货物滞销的风险。
为了减少库存浪费,应当通过精确的需求预测和生产计划,避免生产过多的产品。
另外,也可以采取Just-in-Time (JIT)生产方式,根据客户订单及时生产和交付产品,减少库存积压。
精益生产---八大浪费
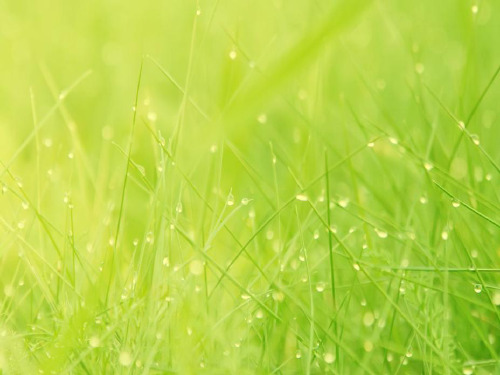
加工过剩浪费---消除方法
对于过剩品质
正确理解客户需求,打破部门间的 隔阂,增强制程能力和稳定性;
对于过剩加工
要求工程师在制作制程工艺标准表的时候合理审 视,避免有超过最低需求的浪费;
过剩检验
不能用过剩检验来弥补制造稳定度弱的缺陷,应 坚决推动精益生产及六西格玛以提高制造能力;
过剩设计 36 带着问题审视我们的加工是否消除了过剩浪费。
请各位将手机调为静音、振动 接电话请到外面走道
谢谢!
精益生产
彭品方 2016.05.06
5
培训内容:
一. 浪费的概念 二. 八大浪费各自的表现、原因
和改善方式 三. 结束语
6
增值的概念
站在客户的立场上,有四种增值的工作 - 使物料变形 - 组装 - 改变性能 - 部分包装
物料从进厂到出厂,只有不到 10% 的时
22
丰田人认为“库存是必要的恶物”
库存的浪费---表现
1、表面损失 a.产生不必要的搬运、堆积、放置、找寻、 防护处理等浪费的动作 b.占用过多仓库场地及场地建设的浪费。 c.保管费用
2、潜在损失
a.占用流动资金,降低资金周转率
b.需要额外承担资金利息
c.市场变动时有销售不出去的风险
23
d.在库物品劣化变质的风险
3>提倡尽量用小的生产批量,而辅
以频繁的搬运;
43
搬运浪费---改善
4>搬运方式及工具 a.机械化原则 b.自动化原则 c.标准化原则 d.均衡原则 e.直线原则 f.安全第一原则
44
动作的浪费 动作的浪费:
不产生附加价值的动作、不合 理的操作、效率不高的姿势和动作 都是浪费。
精益生产之_八大浪费.doc

精益生产之_八大浪费11.不良、修理的浪费所谓不良、修理的浪费,指的是由于工厂内出现不良品,需要进行处置的时间、人力、物力上的浪费,以及由此造成的相关损失。
这类浪费具体包括:材料的损失、不良品变成废品;设备、人员和工时的损失;额外的修复、鉴别、追加检查的损失;有时需要降价处理产品,或者由于耽误出货而导致工厂信誉的下降。
2.加工的浪费加工的浪费也叫过分加工的浪费,主要包含两层含义:第一是多余的加工和过分精确的加工,例如实际加工精度过高造成资源浪费;第二是需要多余的作业时间和辅助设备,还要增加生产用电、气压、油等能源的浪费,另外还增加了管理的工时。
3.动作的浪费动作的浪费现象在很多企业的生产线中都存在,常见的动作浪费主要有以下12种:两手空闲、单手空闲、作业动作突然停止、作业动作过大、左右手交换、步行过多、转身的角度太大,移动中变换“状态”、不明技巧、伸背动作、弯腰动作以及重复动作和不必要的动作等,这些动作的浪费造成了时间和体力上的不必要消耗。
4.搬运的浪费从精益生产的角度看,搬运是一种不产生附加价值的动作,而不产生价值的工作都属于浪费。
搬运的浪费具体表现为放置、堆积、移动、整列等动作浪费,由此带来物品移动所需空间的浪费、时间的浪费和人力工具的占用等不良后果。
国内目前有不少企业管理者认为搬运是必要的,不是浪费。
因此,很多人对搬运浪费视而不见,更谈不上去消灭它。
也有一些企业利用传送带或机器搬运的方式来减少人工搬运,这种做法是花大钱来减少工人体力的消耗,实际上并没有排除搬运本身的浪费。
5.库存的浪费按照过去的管理理念,人们认为库存虽然是不好的东西,但却是必要的。
精益生产认为,库存是没有必要的,甚至认为库存是万恶之源。
由于库存很多,将故障、不良品、缺勤、点点停、计划有误、调整时间过长、品质不一致、能力不平衡等问题全部掩盖住了。
例如,工厂生产线出现故障,造成停机、停线,但由于有库存而不至于断货,这样就将故障造成停机、停线的问题掩盖住了,耽误了故障的排除。
精益生产之如何改善八大浪费

精益生产之如何改善八大浪费精益生产是一种通过精确分析和优化生产过程,减少浪费和提高效率的管理方法。
其中,八大浪费是指在生产过程中浪费了工时、资源和能源的现象。
本文将探讨如何通过精益生产的方法改善八大浪费。
第一,运输浪费。
运输浪费是指在产品生产、运输和分发过程中浪费了时间和资源。
通过优化生产和物流流程,降低运输次数和距离,可以减少运输浪费。
在制定运输计划时,应考虑最短路径、最佳装载和协调配送等因素。
第二,库存浪费。
库存浪费是指库存过多或过少对生产过程造成的损失。
通过精确预测需求,制定合理的库存管理策略,可以减少库存浪费。
同时,优化生产流程,减少等待时间和停顿,也可以减少库存浪费。
第三,移动浪费。
移动浪费是指在生产过程中不必要的移动造成的时间和资源浪费。
通过优化工作站布局,减少工人和物料的移动距离,可以减少移动浪费。
此外,合理安排工作流程,减少重复移动和任务转移,也可以减少移动浪费。
第四,过程浪费。
过程浪费是指生产过程中产生的不合格品和废品,导致资源的浪费。
通过制定和执行严格的质量控制措施,提高生产工艺和标准,可以降低过程浪费。
同时,培训员工加强技能和质量意识,也可以减少过程浪费。
第五,等待浪费。
等待浪费是指在生产过程中因为等待他人、设备或者信息而浪费的时间。
通过合理安排生产计划和任务分配,减少等待时间,可以减少等待浪费。
同时,提供及时和准确的信息,协调各个环节之间的关系,也可以减少等待浪费。
第六,不必要的运动浪费。
不必要的运动浪费是指在生产过程中不必要的动作导致的时间和能源浪费。
通过分析工作流程和使用合适的工具,减少不必要的动作和动作强度,可以降低不必要的运动浪费。
此外,培训员工正确使用工具和设备,也可以减少运动浪费。
第七,不合理的工艺浪费。
不合理的工艺浪费是指采用不合理的工艺和方法造成的资源和能源浪费。
通过对工艺流程的细致分析和改进,优化物料和能源的使用,可以减少不合理的工艺浪费。
同时,培训员工学习和掌握先进的工艺技术,也可以减少工艺浪费。
工厂精益生产之八大浪费
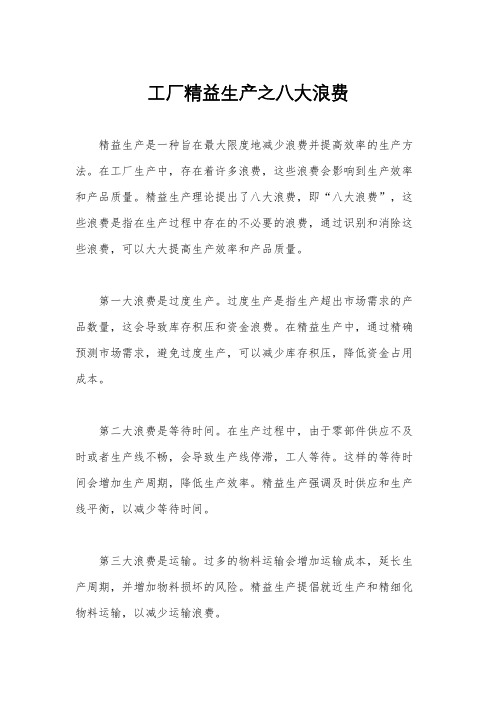
工厂精益生产之八大浪费精益生产是一种旨在最大限度地减少浪费并提高效率的生产方法。
在工厂生产中,存在着许多浪费,这些浪费会影响到生产效率和产品质量。
精益生产理论提出了八大浪费,即“八大浪费”,这些浪费是指在生产过程中存在的不必要的浪费,通过识别和消除这些浪费,可以大大提高生产效率和产品质量。
第一大浪费是过度生产。
过度生产是指生产超出市场需求的产品数量,这会导致库存积压和资金浪费。
在精益生产中,通过精确预测市场需求,避免过度生产,可以减少库存积压,降低资金占用成本。
第二大浪费是等待时间。
在生产过程中,由于零部件供应不及时或者生产线不畅,会导致生产线停滞,工人等待。
这样的等待时间会增加生产周期,降低生产效率。
精益生产强调及时供应和生产线平衡,以减少等待时间。
第三大浪费是运输。
过多的物料运输会增加运输成本,延长生产周期,并增加物料损坏的风险。
精益生产提倡就近生产和精细化物料运输,以减少运输浪费。
第四大浪费是过度加工。
过度加工是指对产品进行超出需求的加工,这会增加生产成本,降低生产效率。
精益生产强调精确理解市场需求,避免过度加工,以提高生产效率。
第五大浪费是库存。
过多的库存会增加资金占用成本,并增加库存积压的风险。
精益生产强调“用时生产”和“精准库存”,以减少库存浪费。
第六大浪费是不合格品。
不合格品会增加返工成本,并影响产品质量和客户满意度。
精益生产强调质量控制和持续改进,以减少不合格品浪费。
第七大浪费是人员运动。
不必要的人员运动会增加生产成本,并降低生产效率。
精益生产强调生产线布局和工作流程优化,以减少人员运动浪费。
第八大浪费是设计不当。
设计不当会导致生产过程中出现问题,增加生产成本和生产周期。
精益生产强调产品设计和生产工艺的协同优化,以减少设计不当浪费。
在实践中,工厂可以通过精益生产的方法,识别并消除这八大浪费,从而提高生产效率,降低生产成本,提高产品质量。
精益生产并不是一蹴而就的过程,需要持续改进和全员参与,但通过不懈努力,工厂一定能够取得显著的成效。
精益生产之八大浪费培训

精益生产之八大浪费培训精益生产是一种通过持续改进和优化生产过程,减少浪费,提高效率的管理方法。
根据精益生产理念,有八大种类的浪费,分别是:过产、等待、运输、过加工、库存、运动、制造缺陷和不必要的动作。
以下是关于这八大浪费的培训内容。
1. 过产:过产是指生产数量超过需求的情况,通常是由于生产计划不准确或生产线设定不合理导致的。
培训中应教授如何制定准确的生产计划,提高生产线的灵活性,并在必要时采取合理的工序调整。
2. 等待:等待是指生产过程中的停工或停滞,可能是由于设备故障、缺少原材料或其他原因引起的。
培训中应重点介绍如何优化设备维护计划,提前准备原材料,并确保及时供应以减少生产线上的等待时间。
3. 运输:运输是指在生产过程中不必要的物料搬运和运输。
培训中应教授如何优化生产布局,减少物料的搬运距离,并合理规划物料存储位置,以降低运输的浪费。
4. 过加工:过加工是指对产品进行超出需求范围的加工。
培训中应着重介绍如何评估产品需求,制定合理的加工标准,并确保每个工序都有明确的目标和要求,避免不必要的过加工。
5. 库存:库存是指生产过程中积压的未完成产品数量,其中包括在制品、原材料和成品。
培训中应教授如何通过优化生产计划、采用just-in-time (JIT) 生产方式以及改进供应链管理来减少库存。
6. 运动:运动是指工人在生产过程中的不必要的移动和动作。
培训中应教授如何优化生产布局,将相关设备和物料放置在便捷的位置,从而减少工人的移动和动作,提高生产效率。
7. 制造缺陷:制造缺陷是指在生产过程中出现的质量问题,需要重新加工或修复。
培训中应着重强调质量控制的重要性,教授如何通过使用质量管理工具和技术,如 Six Sigma 方法,以及提供员工培训和持续监测来减少制造缺陷。
8. 不必要的动作:不必要的动作是指在生产过程中不必要的工作步骤或冗余操作。
培训中应强调流程优化的重要性,通过员工参与和持续改进来识别和消除不必要的动作,从而提高生产效率。
精益生产必备培训之 八大浪费(原创)

精益生产之---八大浪费
目录
1 八大浪费综述
精益生产模型
通过杜绝浪费以缩短生产流程,实现下列目标: 最佳品质、最低成本、最短的前期、最佳安全性、最高员工士气
即时生产
在正确的时间 生产正确数量 的正确零部件
•花时间规划 •持续性流程 •拉式制度 •快速切换 •整合物流作业
人员与团队
挑选
什么是浪费
• 浪费
对产品没有增值的 工作或者资源使 用
浪费
增值
活动
工作的 构成因
素
•增值活动
从客户的角度看是直接产 生价值的活动(比如部 件组装),这也是客户 愿意付钱的部分
附带活动
• 附带活动
对客户没有直接增值,但就目前的运作来 说是必须的(比如,在组装过程中为了 拿去物料而产生的手的运动)
浪费是一种增加成本但不产生价值的工作
加工过 剩浪费
是消除一切无效劳 动和浪费( M u d a )
如何记忆:
搬
不
动 在家
等 过儿
搬不
动在加 等
过
运良
作库工 待
剩
的返
的的本
的
的
浪修
浪浪身 浪
浪
费的
费费的 费
费
浪
浪
费
费
目录
2 库存、等待、搬运浪费
价值流断开的地方很容易出现这三种浪费
采购/制造:过多/过早
等待 搬运 库存 不良
加工作业
现场管理
“丰田模式”概念
浪费的定义
定义:浪费指不增加附加价值,使成本增加的一系 列活动.
对于JIT来讲,凡是超出增加产品价值所绝对必 须的最少量的物料、设备、人力、场地和时间的 部分都是浪费。这里有两层含义﹕
精益生产管理八大浪费与解决方法
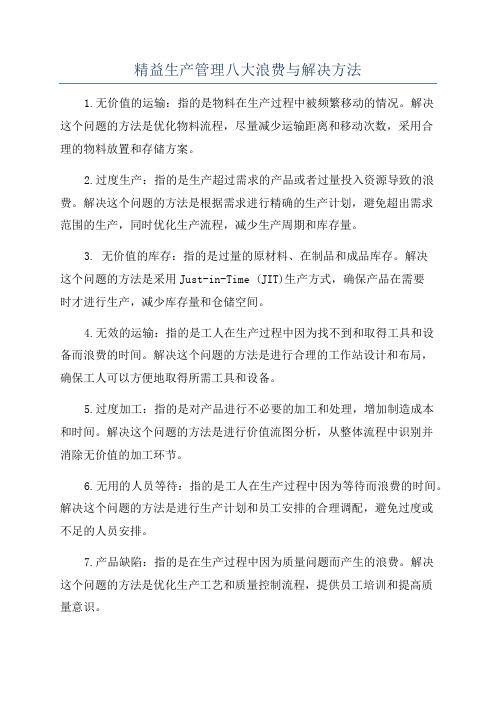
精益生产管理八大浪费与解决方法1.无价值的运输:指的是物料在生产过程中被频繁移动的情况。
解决这个问题的方法是优化物料流程,尽量减少运输距离和移动次数,采用合理的物料放置和存储方案。
2.过度生产:指的是生产超过需求的产品或者过量投入资源导致的浪费。
解决这个问题的方法是根据需求进行精确的生产计划,避免超出需求范围的生产,同时优化生产流程,减少生产周期和库存量。
3. 无价值的库存:指的是过量的原材料、在制品和成品库存。
解决这个问题的方法是采用Just-in-Time (JIT)生产方式,确保产品在需要时才进行生产,减少库存量和仓储空间。
4.无效的运输:指的是工人在生产过程中因为找不到和取得工具和设备而浪费的时间。
解决这个问题的方法是进行合理的工作站设计和布局,确保工人可以方便地取得所需工具和设备。
5.过度加工:指的是对产品进行不必要的加工和处理,增加制造成本和时间。
解决这个问题的方法是进行价值流图分析,从整体流程中识别并消除无价值的加工环节。
6.无用的人员等待:指的是工人在生产过程中因为等待而浪费的时间。
解决这个问题的方法是进行生产计划和员工安排的合理调配,避免过度或不足的人员安排。
7.产品缺陷:指的是在生产过程中因为质量问题而产生的浪费。
解决这个问题的方法是优化生产工艺和质量控制流程,提供员工培训和提高质量意识。
8.无效的运动:指的是工人在生产过程中因为不必要的动作和姿势而浪费的时间和能量。
解决这个问题的方法是进行工作站人机工程学分析,优化工作环境和动作流程,减少工人的疲劳和劳损。
总结起来,精益生产管理八大浪费主要包括无价值的运输、过度生产、无价值的库存、无效的运输、过度加工、无用的人员等待、产品缺陷和无效的运动。
针对这些浪费,可以采取一系列的解决方法,比如优化物料流程、采用Just-in-Time生产方式、进行价值流图分析等,以帮助企业提高生产效率,并减少浪费的发生。
精益生产系列-八大浪费
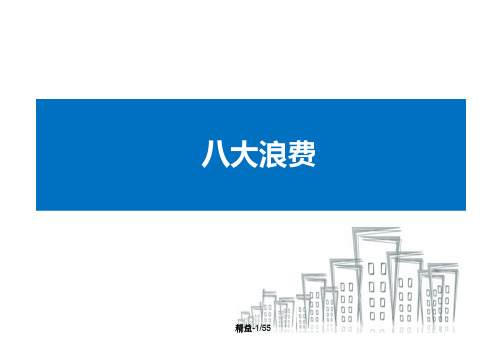
精益-1/55
一.什么是浪费
二.成本和浪费
三.八大浪费
四.如何发现浪费
价值
制造过程中客户愿意付钱的作业内容,改变产品的形状或性质
浪费
制造过程中对客户而言,不产生附加价值,但会增加成本或虽然增加附加价值但消耗超过绝对最少的活动,如搬运、库存、检查
•利用最少的设备、材料、部件、空间、时间等成本要素,是创造附加价值所绝对必要的要素。
但是如果这些不能使产品生成附加价值,则产生浪费;•客户才是价值的决定者
浪费的审视
设备作业的浪费
人员作业的浪费
售价、成本、利润:售价一定,不同的成本造就不一样的利润
成本的秘密:企业的管理、技术水平,造就了企业的实际成本。
实际成本同真正成本的差异,就是浪费,就是改善空间
* 精益的本质和核心,就是消除浪费*
1)不良浪费
1)不良浪费:如何减少不良浪费
* 品质是设计出来的,品质是制造出来的*
2)加工过剩浪费:如何减少加工过剩
3)等待浪费
4)动作浪费:动作浪费的主要形态
5)搬运浪费:产生原因与消除
6)制造过多浪费:原因及对策
7)库存的浪费:改善库存过多的方法
7)库存的浪费:改善库存过多的方法
1)三现原则
2)5why
3)现场观察的方法
The End!
MSA-31/53。
精益生产八大浪费宣传-新

八大浪费之五:返工浪费
返工(不良品浪费) ◆任何的不良品产 生,皆造成材料、 机器、人工等的浪 费。 ◆及早发现不良品, 容易确定不良来源, 进而减少不良品的 产生。 ◆关键是第一次要 把事情做 对,??“零缺陷”
八大浪费之六:动作浪费
动作浪费 12种动作浪费: ◆两手空闲 ◆单手空闲 ◆不连贯停顿 ◆幅度太大 ◆左右手交换 ◆步行多 ◆转身角度大
八大浪费之四:过量生产浪费
过量生产(制造过多或过早 浪费) ◆TPS强调的是“适时生产”。 ◆多做能提高效率,提早做 好能减少产能损失(不做白 不做,机器还不是一样停 着?) 1、提早用掉了材料费、人工 费而已,并不能得到什么好 处。 2、把“等待浪费”隐藏,使 管理人员漠视等待的发生和 存在。 3、积压在制品,使生产周期 L/T变长无形的),而且会使 现场工作空间变大,不知不 觉中吞蚀我们的利润。 4、产生搬运、堆积浪费,先 进先出变得困难。
八大浪费之三:库存浪费
库存浪费 ◆精益生产认为:“库存是万恶之源” ,所 有改善行动皆会直接或间接地和消除库存有关。 ①产生不必要的搬运、堆积、放置、防护处理、 找寻等浪费 ②使先进先出的作业困难 ③损失利息及管理费用 ④物品的价值会减低, 变成呆滞品 ⑤占用厂房空间、造成多余工场、仓库建设 等 ⑥设备能力及人员需求的误判 ◆因库存造成无形损失,绝不亚上述有形损失, 精益生产者认为库存会隐藏问题,而“问题” 在精益生产者被认为是宝藏,问题如果能不断 地被发现解决,则利益便会不断地产生 1、没有管理的紧张感,阻碍改进: 2、库存量一多,因机械故障、不良产品所带 来的不利后果不能马上显现出来,因而也不会 产生对策。 3、由于有了充足的库存,出现问题时可以用 库存先顶上,问题就可以慢慢解决甚至不用解 决,最起码是被掩盖住了,不急迫了,不会被 上级追究了,于是乎本部门的工作成绩就出来 了。
精益生产培训之八大浪费
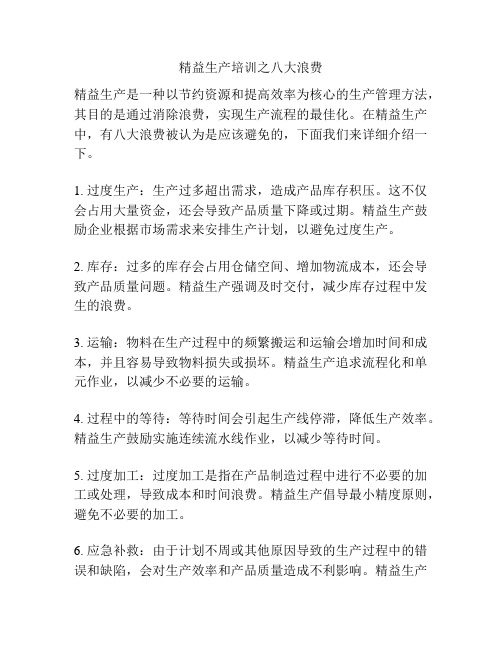
精益生产培训之八大浪费精益生产是一种以节约资源和提高效率为核心的生产管理方法,其目的是通过消除浪费,实现生产流程的最佳化。
在精益生产中,有八大浪费被认为是应该避免的,下面我们来详细介绍一下。
1. 过度生产:生产过多超出需求,造成产品库存积压。
这不仅会占用大量资金,还会导致产品质量下降或过期。
精益生产鼓励企业根据市场需求来安排生产计划,以避免过度生产。
2. 库存:过多的库存会占用仓储空间、增加物流成本,还会导致产品质量问题。
精益生产强调及时交付,减少库存过程中发生的浪费。
3. 运输:物料在生产过程中的频繁搬运和运输会增加时间和成本,并且容易导致物料损失或损坏。
精益生产追求流程化和单元作业,以减少不必要的运输。
4. 过程中的等待:等待时间会引起生产线停滞,降低生产效率。
精益生产鼓励实施连续流水线作业,以减少等待时间。
5. 过度加工:过度加工是指在产品制造过程中进行不必要的加工或处理,导致成本和时间浪费。
精益生产倡导最小精度原则,避免不必要的加工。
6. 应急补救:由于计划不周或其他原因导致的生产过程中的错误和缺陷,会对生产效率和产品质量造成不利影响。
精益生产推崇错误预防和持续改进的方法,避免应急补救。
7. 人员不当利用:未充分发挥员工的能力和技能,或安排不当的工作任务,会导致生产效率下降。
精益生产强调员工参与和培训,提高员工的技能水平和责任感。
8. 无用的动作:一些无效的动作或不必要的步骤会增加生产过程中的时间和劳动力成本。
精益生产倡导精简和标准化的生产流程,以减少无用的动作。
综上所述,精益生产中的八大浪费是企业应该避免的,通过消除这些浪费,企业可以提高生产效率、降低成本,并提供更高质量的产品和服务。
因此,进行精益生产培训是非常重要和必要的。
精益生产是一种以节约资源和提高效率为核心的生产管理方法,旨在通过消除浪费,实现生产流程的优化。
其核心理念是追求价值流的流畅性,即尽可能在最短的时间内,以最低的成本提供最高的质量和价值。
精益生产与八大浪费
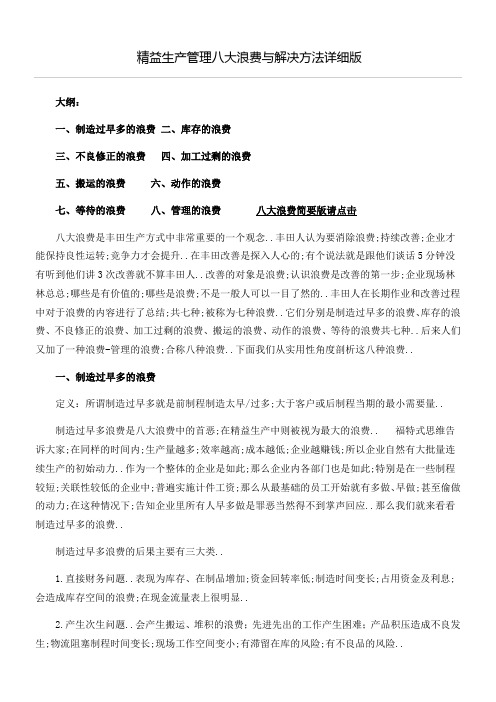
大纲:一、制造过早多的浪费二、库存的浪费三、不良修正的浪费四、加工过剩的浪费五、搬运的浪费六、动作的浪费七、等待的浪费八、管理的浪费八大浪费简要版请点击八大浪费是丰田生产方式中非常重要的一个观念..丰田人认为要消除浪费;持续改善;企业才能保持良性运转;竞争力才会提升..在丰田改善是探入人心的;有个说法就是跟他们谈话5分钟没有听到他们讲3次改善就不算丰田人..改善的对象是浪费;认识浪费是改善的第一步;企业现场林林总总;哪些是有价值的;哪些是浪费;不是一般人可以一目了然的..丰田人在长期作业和改善过程中对于浪费的内容进行了总结;共七种;被称为七种浪费..它们分别是制造过早多的浪费、库存的浪费、不良修正的浪费、加工过剩的浪费、搬运的浪费、动作的浪费、等待的浪费共七种..后来人们又加了一种浪费-管理的浪费;合称八种浪费..下面我们从实用性角度剖析这八种浪费..一、制造过早多的浪费定义:所谓制造过早多就是前制程制造太早/过多;大于客户或后制程当期的最小需要量..制造过早多浪费是八大浪费中的首恶;在精益生产中则被视为最大的浪费.. 福特式思维告诉大家;在同样的时间内;生产量越多;效率越高;成本越低;企业越赚钱;所以企业自然有大批量连续生产的初始动力..作为一个整体的企业是如此;那么企业内各部门也是如此;特别是在一些制程较短;关联性较低的企业中;普遍实施计件工资;那么从最基础的员工开始就有多做、早做;甚至偷做的动力;在这种情况下;告知企业里所有人早多做是罪恶当然得不到掌声回应..那么我们就来看看制造过早多的浪费..制造过早多浪费的后果主要有三大类..1.直接财务问题..表现为库存、在制品增加;资金回转率低;制造时间变长;占用资金及利息;会造成库存空间的浪费;在现金流量表上很明显..2.产生次生问题..会产生搬运、堆积的浪费;先进先出的工作产生困难;产品积压造成不良发生;物流阻塞制程时间变长;现场工作空间变小;有滞留在库的风险;有不良品的风险..3.掩盖问题..为什么“制造过早多浪费是八大浪费中的首恶;在精益生产中则被视为最大的浪费”因为它带给人们一个安心的错觉;掩盖了各种问题;以及隐藏了由于等待所带来的浪费;没有改善的动力;失去了持续改善的时机..1.制造过早多浪费的产生原因..1生产计划方面..1信息准确度问题..信息不准;计划失当;信息传递不准确;导致生产计划作业进行盲目;最终导致制造过早多浪费的产生..2生产计划管控机制方面..让某些制程、生产线、工站甚至作业员有生产伸缩的充分空间和提高产出的利益驱动..比如有的不排班生产计划;也不排日生产计划;而是排周生产计划;一天内的生产排配权利下放到制程、生产线、工站甚至作业员;这时候如果有多余的产能、人力、设备稼动过剩;则很自然地就会提前安排生产;安排满稼动生产;从而造成制造过早多..特别是在某些企业中如玩具;较有可能安排计件生产;多劳多得;那么过量过早生产的积极性就更大了..除非在实施了拉动生产的精益企业里面;一般的企业还是用MRP在做推式生产..这时候生产计划的排配;生产进度的精确控制是企划部门最基础的功能;不能因为制造能力弱;各制程衔接性差就放松对生产计划实施进度的管控..2内部制造能力弱的补偿问题..制造过早多多数时候是出于补偿内部制造能力弱的考虑..制造能力弱;特别是制造中的品质差;换型时间长;在市场信息牛鞭效应的驱动下;为了弥补自身能力不足;而提前过量生产以满足客户需求..如一个企业制造能力弱;多制程时的合计良品率在50%-70%之间分布;那么面对100K的P/O时;它就需要备143-200K的原料;为了安全起见;这时候一般会选择安全系数较高的200K;甚至220K;当这220K投到制程中去的时候;造成生产过多就不可避免了..在这里;制造过多是制造能力弱的补偿;同时制造能力提升也是消除制造过多的必要前提..对于制造过早是补偿制造能力弱的论断;用制造前置时间L/T可以清晰地衡量出来..3产能不平衡及流程不顺方面..1制造过程中由于各功能制造单位、制程产能不平衡;不可避免地造成加工能力低的制程前在制品WIP堆积;同时给后工站的作业带来了极大的不便..图1是T公司制造的一个产能平衡图;T公司制造有冲压、清洗、打磨、焊接、组装共五个制程;有一个产品要顺次经过这五个制程;那么这个产能如何计算呢要看瓶颈制程的加工能力..在冲压-清洗-打磨-挥接-组装这五个制程中;清洗的加工能力高于冲压;所以清洗处不会造成积压;但下面的打磨制程加工能力明显低于前制程清洗;同时打磨制程是五个制程当中加工能力最低的;如果整个制程的生产计划不是以最弱的打磨为基准线;那么堆积就会在打磨之前出现;这就是制造过多;是浪费..在这五个制程中;换型膜具最复杂的当属冲压..如果顾及到冲压稼动率高、制程能力弱不愿换型;而将同一个料号相隔3天的两批次的生产指令合并到一次生产;那么对于后面的制程来说;也仅仅接到了一个批次的生产指令;另一批次的半成品对于它们是无意义的..这就是制造过早;是浪费..在Lean中;平衡产能;使得各制程、工站按照客户需求的节拍T.T而实现一个流线生产是实现及时生产的重要一步..2由于规划不经济不理想;造成制程路程不流线化;无法实现产品流动;而存在迁回、曲折、往复、停滞现象;使得生产不得已提前或有WIP;这也是造成制造过多过早的重要原因..如图2所示;A 公司制程有射出、印刷、组装等;其制程分布如下:本制程为:1楼的射出完成后;由于后面的印刷效率远远大于输出;所以射出后产品只能先入库;经过印刷后;要先在1楼暂存;等当班结束时再入3楼的仓库;后一个制程-组装需要时来3楼的仓库领取..这个流程中有入存2次;WIPI次;势必造成制造过早的浪费..4其他..当设备比较昂贵时;管理及财务人员有倾向提高稼动率;生产过多的产品..下图是P公司的一个案例;其内部各制程分别是SMT-PTH-老化-FT-组装;其产能分布如下:图2五个制程中;产能按照制程顺序逐渐增加;理论上是不会有制作过多的..但SMT;设备远远贵于其他制程设备价值;所以当PTH、组装等制程在每周5天每天18小时的时间稼动率水平上慢悠悠生产的时候;SMT很可能要安排尽量满稼动;很可能是6.5天x24小时;那么这样在PTH之前就不可避免地出现制造过多过早的现象..2.制造过早多浪费的消除方法..1生产计划方面..1主生产计划的准确性..在这方面;应建立以顾客需求为中心的弹性生产系统;保证客户需求信息准确传递..2在没有实施精益生产;还在用MRP推式生产的企业里;企划部门要负贵任地对生产计划的排配、进度控制负责;不能因为制造能力弱就只排大制程的主计划MPS;而对于细部的日计划DPS放任自流;造成基层各车间、生产线的生产计划脱节..2关于补偿内部制造能力弱的问题..内部制造能力弱;品质差;废品率高;制造周期长等问题在生产计划方面的直接体现就是生产计划的不可预知;不知道究竟排多少生产量才可以应付客户交货..实现精益生产的基础是品质稳定化;保证制程内品质稳定;不制造不传递不接收不良品;只有实现了生产稳定高品质;生产的流线化才有可能实现;才有可能生产平准化以至于后补充生产;所以高品质是精益生产实施的基础..3产能不平衡及流程不顺方面..1对于产能不平衡的情况;最终要平衡各制程的产能..仍以T公司为例见图1;应首先列出客户需求基准线;再在此基础上进行产能调配;其中客户需求是每小时加工能力1800;冲压、清洗、组装产能已经超过客户需求;打磨及焊接产能达不到;为此有必要对前者进行降低;后者提升..经过评估后改动如图3所示..组装制程的工站是相对柔性的;产能调配最容易;减少组装人员;对操作进行重组;将组装产能从2000降低到1800;对于打磨及焊接在提高单机效率的基础上增加人力及设备配置并将二者产能分别由800;1500提升到1800;对于第三类就是冲压及清洗;因为这两类设备是模块化的;无法像组装一样按可调比例降低产能就是说;清洗或者1条线产能4500;或者没有生产线;产能为0;所以此二设备人力保持不变;这样经过产能平衡后;图1的产能被改善成了图3的产能..这样基本保证了各制程没有制造过多..对于清洗后产能高过打磨制程的问题;这就要求清洗生产在客户需求基准线基础上不过量生产;进行平准化生产排配或者宁可保持非满稼动..2对于流程不顺的情况;应该在最初的设施规划时;就要将流程流线化作为目标;即便因为制程所限无法完全地实现产品流动;也要尽量减少制程及产品的迂回、曲折、往复和停滞;以尽力减少制程内WIP;从而消除制造过多过早浪费..如上例A公司案例中;可以将制程改善为如下分布见图3..Layout变动;将Layout由设备式布置改为工艺式布置..射出后暂存;当班产品入到3楼的仓库;由于印刷机非常便宜同时生产效率非常高;在这里将印刷与组装连线;组装需要时印刷才生产;不需要时印刷不生产;这样就减少了1次入库;减少了制造过早的浪费..4当设备比较昂贵时;管理及财务人员确实有增加设备稼动的冲动..比如SMT和组装比;因为后者设备价格远远小于前者;所以在对工厂进行绩效考核时;没有人会将组装线的稼动率作为考核指标;而几乎大多数企业都会将SMT线稼动率作为考核指标;稼动低时管理者会坐卧不宁;设法提升..解决这个问题其实只需要明了一点..高稼动是否会带来后面制程的半成品堆积;也就是本制程制造过多过早;如果是就应该坚决地停止机器;进而放弃对高价机器考核稼动率的绩效考核模式..从源头上讲;在产能规划时;在设备采购时;对于高价机器应以“少数量高稼动”的设计方案来采购;这样既能保证低的采购成本又能保证客户需求;只不过可能增量时的增产速度慢点罢了..二、库存的浪费1.定义:库存是生产过程中停滞物料的总称..库存可以按照种类、位置、库存成因、库存用途等分成若干类;但今天我们研究浪费;为简便起见;只把它分为原物料、在制品WIP、成品三大类..库存确实有非常重要的现实意义;库存是:①量产的必然产物..福特式思维认为量产可以降低成本;这在多品种小批量的现在是不适合的;但对于少数还在批量生产的行业来说;批量生产还是降低成本的方法..这些行业一般为市场需要品种少或者是行业价值链上游企业;如食品、纺织等行业在深加工、终端市场上产品的品种非常多;但在上游粗加工时的品种相对少许多..这些为数不多的行业中批量确实会带来低成本;但同时会带来库存..②保证整产零销的局部经济性..当设备快速换线困难如重化工行业时;会存在当面对整产零销局面时换线小批量生产的综合效益不及批量生产的局面;这时企业可能会选择整产零销;会产生一定库存..③市场剧烈增加时的缓冲..市场突然增加时;如果有一定库存;会缓解企业生产能力快速爬坡的压力;这是部分企业考虑安排库存的原因..这类情况在一些特殊行业表现非常突出..如空调只在夏季销售;月饼只在中秋节前一两个月销售;而圣诞树、礼品、部分POP电子产品会在圣诞节前热销;这都是行业特性决定的.. 所以从这个意义上来说;一定的库存是必要的..但库存的存在确实带来非常大的损失;是恶物;丰田人认为“库存是必要的恶物”..2.库存损失分类..在精益生产及丰田生产方式里;库存是浪费;是不该被保有的;而我们认为库存造成的损失;可以分为以下三大类:1表面损失..①产生不必要的搬运、堆积、放置、找寻、防护处理等浪费的动作..②占用过多仓库场地及场地建设的浪费..③保管费用..2潜在损失..①占用流动资金;降低资金周转率..②需要额外承担资金利息..③市场变动时有销售不出去的风险..④在库物品劣化变质的风险..3意识方面的损失..掩盖问题;造成假象..当库存的水位高涨时;管理者就感受不到问题的严重性而失去了改善的机会..正因为这么多损失;所以精益生产才强调降低库存;以零库存为目标..3.改善方法..1转变观念..不要认为库存是想当然;不要认为大量库存才保险..也不要用现在的资产负债表来迷惑自己;要认识到库存是企业的负担和罪恶..2系统改善..库存降低可以促进改善..通常通过降低库存来倒通企业内各环节进行改善;我们研究的各种方法工具都是或直接或间接为降低库存这个指标服务的..比如说用看板管理法可以有效控制或大幅降低制造系统内库存;但之前要有5S、节拍生产、一个流、平准化作保证;而要想节拍生产就要先产线产能平衡改善..要想一个流;就要先Cell;而Cell之前要以多能工、设备小型化、标准化的作业及灵活的组织体系作保障..实际上整个精益生产或者整个丰田生产方式实现的重要途径就是通过降低库存来体现问题而谋得改善以臻于完美..所以降低库存是个系统工程;要从上面说的各个方面对企业进行改善;体质进行增强;当企业体质增强了;库存自然也会降低..下面是最常见的降低库存改善行动实施步骤:①观念宣导;让大家认识到库存是罪恶的..②降低库存目标KPI订定..主要是金额;但对于一些低阶层的执行人员来说;可能库存数量和占地面积比金额更加直观;那么对于他们用数量和仓库面积等都可以..在这时候;启动目视化管理是很重要的;将库存量、金额、库存周转率、利用率等指标的目标与现状情况用目视化方法明示出来;以利于提醒和监督..③导入JIT;用一个流和后拉式生产方式可以有效控制库存..④记得库存管理中的“三不”..1不大批量生产..在排生产工令时;尽量排小批量生产;并且不要给现场太多自由生产的权利;比如周工令..2不大批量搬运..要加快物流速度;及时小批量搬运..3不大批量采购..另外一种思路;面对林林总总的问题不知道如何下手时;谈什么方法、工具都是低效益的;这时降低库存最好的方法就是:先强制降库存;等问题浮现出来后;再将问题一个个消灭;库存自然降低..在上图中;水面代表库存水平;礁石代表问题点;当水面高时礁石在水底;也就是说库存高时;问题都被掩盖..只有当水面低时;礁石才会露出水面;也就是问题点才暴露;这就是库存对于暴露问题的重要意义..三、不良修正的浪费1.定义:生产过程中;因来料或制程不良造成的各种损失;需进行处置的时间、人力和物力的浪费..不良品是工厂中不可容忍的重大浪费现象..我们客户需要的是合乎规范要求的产品;客户不会负担不良品;不仅仅是不良品这部分;随后可能引起的下游延伸制品不良、检查、返工、报废等损失都由企业自己承担..不良品率的高低是企业制程稳定性的最重要的标志;是企业体质好坏的直接体现..2.不良修正的影响..1产品报废..报废的产品不仅仅浪费了材料;它还包含了制程中付出的原材料、人工、制造费用以及管理、财务费用;这些产品价值本来可以计入营业额的;但现在报废了;成本还白白付出了;利润直接下降;对于企业的损失之大是让我们怎么尽力弥补都值得的..2挑选、检查、维修带来的损失..产品不良了;在宣布报废之前;我们可能要处理、挑选、检查、维修;把部分不良品转成良品;这一过程中的全部付出都是浪费;因为客户不会为我们的上述作业负担一分钱;这其中包含我们的时间、人力、设备、场地、辅材等..3信誉的影响..不良品出现会引起交货延迟;有时会产生去客户处换货;或者在客户处随线维修的情况..而如果客户用了我们的问题产品做成下游成品出了状况;那问题就更严重了;所有这些都会引起客户不便进而是抱怨;再进一步就是订单的减少、取消或流失..4延伸的复合损失..出现不良品造成的复合损失是致命的;可能要产品召回;可能要面临赔偿诉讼;可能会引来公众的质疑抱怨;可能会引起主管部门的干预;比如停产、吊销执照、限制出口权等..2007年发生的利达玩具厂老板张数鸿自杀事件;就是由于油漆供应商的20kg色粉含铅超标而最终造成年产值3亿元;在当地玩具界举足轻重的公司的破产..类似的例子太多了;三鹿奶粉事件;频见报道的汽车、笔记本召回事件都让我们深刻体会到了品质问题的残酷和重要性..3.不良修正的产生原因..1设计问题..这里的设计问题是指源头问题;包括产品外观、尺寸、功能、可靠性、可制造性、兼容性等产品设计内容;也包括加工路线、加工方式、检验手段、品质控制点等工艺设计内容;也包括来料选择;供应商控制;包装/存储/运输方式等制造系统方面的设计内容..之所以要把上面的内容合并在一起;原因就是和生产过程中的执行力及稳定性相比较;上面这些源头问题影响着绝大多数企业生产的品质问题..2制造系统体质问题..即制造阶段的管理影响产品质量--无谓的频繁换线带来生产不稳定;人员稳定度低;作业员熟练度不高;标准作业欠缺;人员技能欠缺等..3生产过程执行力及临时性问题..如操作不标准;执行的检验手段有限;货商质量控制不力;来料检验遗漏;对于发生的不良处理不当;原因追查不彻底;选用了非规定的设备及工艺路线等..4.不良修正浪费的改善方法..1设计方面..从源头上做到无缺陷;可制造性强;这是我们的目标..但实际上往往达不到;现在的开发设计是个系统工程;会涉及开发部门、工程部门、供应链、品质为主的几乎所有企业内部门..市场是客户左右的;设计方案是客户或者开发部门决定的;能够达到关键设计要求是需要参与的所有部门的努力;而进度不可能整齐划一;在有瑕疵没有解决的情况下;很可能客户就要求量产了;这时候只能带着缺陷生产;而这会带来无穷后患..这些问题可能包括:①可能一个产品300个尺寸;实际上只有150个不错;而客户认为其中巧15个是关键的;认可了;所以生产了;但某一天另外的120个尺寸中的一个被发现了问题;被重新认定增加为关键尺寸;所以客户退货..②验证中的制程稳定性差;Cpk值只有0.9;没有达到规定的图5的标准;但客户急需产品;所以量产了;但随后的问题也来了..③产品量产了;制程也稳定;但因为只考虑交货能力;所以设计时超过正常水平30%的人力、设备、场地及检验环节;后来降低成本改善时要去掉这30%的人力、设备、场地;需要跟客户沟通;这沟通中需要验证内容太多;几乎等于重新开发一个新产品;得不偿失最后只能浪费着生产..上面三个问题分别是设计时候的规格隐患、制程隐患、制程浪费;都是很典型的设计问题..从这个意义上看;好的设计是消除不良修正浪费的首要保证..2制造系统体质方面..①标准化管理..企业制造系统体质好坏的一个重要标志就是管理的标准化程度..标准化的内容应该包括技术层次的设备、模具、材料、环境、技术参数的标准化;应该包括基础执行层面的5S推动、人员培训、标准化动作、物流规范、模具保养规范等人、机、物料、工艺文件、环境维持、测量系统等方面的标准化;应该包括管制执行层面的计划控制、制造流程、品质管控、产品开发过程的标准化;也应该包括组织系统方面的组织切分、在各制造模块中的部门职责、KPI管理、绩效评定等方面的标准化..在标准化的状态下;企业的生产经营活动是公开的、互通的、执行面可替换的、稳定的..在这里;当一个产品停产一年后再恢复生产时;不必在人、机、料、技术参数、文件、环境等参数方面调试很久才可以正常运转;而是马上就可以正常运转..管理标准化是制造系统体质优良的一个基本要求..②TQM活动及品质系统的良性运行..为了减少不良修正浪费;开展全员性的TQM活动是有必要的..在实施TQM的企业里;每人都参与品质改善;对品质的关注是全过程的;是源头性的;同时对品质的理解是全方面的;不仅仅是品质报废类的狭义理解..在全员全方位全过程关注品质的TQM推动同时;逻辑性强、强制性强的品质系统也是不可或缺的;从客户需求定义、检验标准制定、供应商认证、来料检验、制程品保、品质工程保证、出货检验、问题解决及反馈机制等都应该纳入系统范围强制运行..这样我们就可以有效降低不良的产生;从而减少不良修正浪费的水平..③TPM..为了减少不良浪费;设备的良好保养是必须的;应该保证设备100%的可动率;不会出现设备原因出现的报废..3生产过程执行力及临时性问题..要想保证品质;减少不良修正浪费;在强化企业体质;健全系统;明确责任人的同时;最重要的是执行力度和问题解决速度..没有执行力上面的一切都是空谈..四、加工过剩的浪费1.定义:加工过剩的浪费也叫过分加工的浪费;是指在品质、规格及加工过程上的投入主动超过客户需求从而造成企业资源浪费的情况..加工过剩浪费分四种情况:过分精确品质带来的浪费。
精益生产之八大浪费
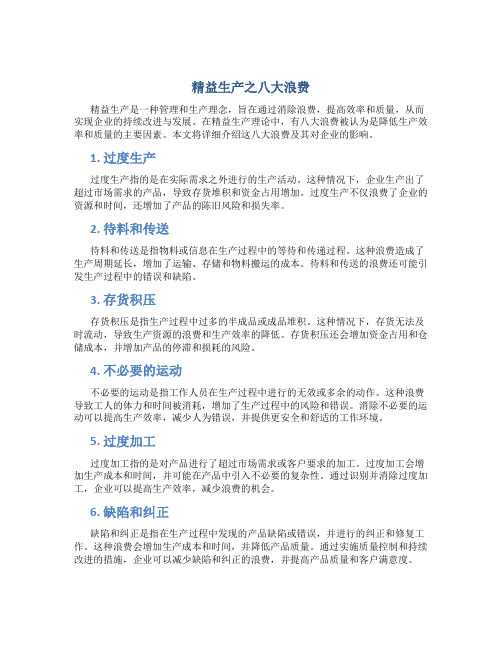
精益生产之八大浪费精益生产是一种管理和生产理念,旨在通过消除浪费,提高效率和质量,从而实现企业的持续改进与发展。
在精益生产理论中,有八大浪费被认为是降低生产效率和质量的主要因素。
本文将详细介绍这八大浪费及其对企业的影响。
1. 过度生产过度生产指的是在实际需求之外进行的生产活动。
这种情况下,企业生产出了超过市场需求的产品,导致存货堆积和资金占用增加。
过度生产不仅浪费了企业的资源和时间,还增加了产品的陈旧风险和损失率。
2. 待料和传送待料和传送是指物料或信息在生产过程中的等待和传递过程。
这种浪费造成了生产周期延长,增加了运输、存储和物料搬运的成本。
待料和传送的浪费还可能引发生产过程中的错误和缺陷。
3. 存货积压存货积压是指生产过程中过多的半成品或成品堆积。
这种情况下,存货无法及时流动,导致生产资源的浪费和生产效率的降低。
存货积压还会增加资金占用和仓储成本,并增加产品的停滞和损耗的风险。
4. 不必要的运动不必要的运动是指工作人员在生产过程中进行的无效或多余的动作。
这种浪费导致工人的体力和时间被消耗,增加了生产过程中的风险和错误。
消除不必要的运动可以提高生产效率,减少人为错误,并提供更安全和舒适的工作环境。
5. 过度加工过度加工指的是对产品进行了超过市场需求或客户要求的加工。
过度加工会增加生产成本和时间,并可能在产品中引入不必要的复杂性。
通过识别并消除过度加工,企业可以提高生产效率,减少浪费的机会。
6. 缺陷和纠正缺陷和纠正是指在生产过程中发现的产品缺陷或错误,并进行的纠正和修复工作。
这种浪费会增加生产成本和时间,并降低产品质量。
通过实施质量控制和持续改进的措施,企业可以减少缺陷和纠正的浪费,并提高产品质量和客户满意度。
7. 不合理的人力资源利用不合理的人力资源利用是指工人在生产过程中没有充分利用其技能和知识,或者存在不平衡的人力资源分配。
这种情况下,员工的潜力未能得到充分发挥,导致生产效率的下降和员工士气的下降。
精益生产之8大浪费

浪费描述为8种类型:
• 过量生产 • 返工 • 搬运 • 过量加工 • 库存 • 等待 • 动作 • 缺乏员工参与
精益工具都是为消除浪费而设计的。
努力并持续的消除浪费,从现在就开始。
思维方式的改变
传统企业
增值
非增值活动95%
传统的生
产改进
增值
非增值活动95%
较小的改进
精益消灭 浪费
增值
非增值 活动
重大的改进
思维方式的变化:从压缩增值活动的时间到压缩非增值活动的时间。
为什么要消除浪费
• 减少浪费让客户、公司和员工都受益
对象
益处
对客户
产品满足所有预期
对公司
减少成本 提高质量 提高操作员柔性 提高声誉
• 尽管是增加价值的活动,但所用的资源超过了 “绝对最少”的界限,也是浪费(资源浪费)
增值与非增值
增值
定义:任何增加产品或服 务价值,或为满足顾客要 求必需进行的活动。
典型例子: • 加工 • 规定的检验
非增值
定义:指任何不会增加额 外价值或无此需要的活动 典型例子: • 搬运 • 检验 • 返工 • 存放 • 等待
原因:
• 生产能力不稳定 • 万一………. • 缺乏沟通(内部、外部) • 本地优势化观点 • 成本计算(贪图便宜) • 缺乏协调一致的计划
返工的浪费
定义 • 对产品或服务进行再处理才能满足客户的要求
返工的浪费
特点:
• 有维修和返工区域 • 增加额外的检查 • 复杂的产品流程 • 有疑问的质量
危害: • 与供应商/客户之间关系不好 • 由于返工,报废,加急运费而
八大浪费
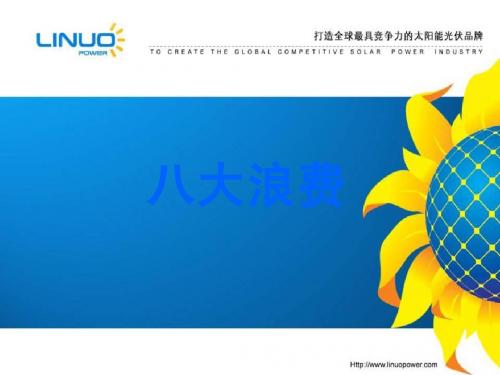
可用工时:22h
可用工时:22h
八大浪费
浪费的定义
何谓浪费:
不产生任何附加价值的动作、方法、行为和计划。
• • • • • • 盲目消耗、挥霍 没有发挥优势 未开发的区域 垃圾 无价值的剩余物 逐渐变弱
用不同的评判标准去判断一 个动作、行为、方法或计划时, 所得到的浪费程度都会不同。
八大浪费
浪费的识别和消除
四.动作浪费
动作浪费
(三) 浪费的产生:
操作不经济﹕动作不精简﹔动作多余 设计不合理﹕可同时完成但未同时﹔
不必要但被增加﹔
可同规格但不同﹔ 未考虑调整/转换/取放 物料需要翻找﹔
四.动作浪费
动作浪费
(四) 浪费的消除:
操作不经济﹕按经济原则设计并标准化﹔制订查 检表发现并消除﹔ 设计不合理﹕合理设计﹔变成设计要素﹔设计验 証与稽核﹔符合人体工效设计﹔
八大浪费
引子
产品包装过程
增值活动
直接为顾客创造价值的活动
设备加工过程
组 织 经 营 活 动
设备维护
必要非增值
多数发生于支援部门
计划变更
来料/制品/成品的检验
物料的浪费
不必要非增值
完全属于浪费
过多的搬运 冗长的会议
八大浪费
引子
不必要但非 增值活动 35%
增值活动 5%
必要但非增 值活动60%
顾客只愿意冲着那5%的增值掏腰包
精益生产的理念最早起源于日本丰田汽车公司的TPS
(Toyota Production System)。TPS的核心是追求消灭一切 “浪费”。 实现精益生产管理,最基本的一条就是消灭浪费。
浪费的识别和消除
八大浪费
- 1、下载文档前请自行甄别文档内容的完整性,平台不提供额外的编辑、内容补充、找答案等附加服务。
- 2、"仅部分预览"的文档,不可在线预览部分如存在完整性等问题,可反馈申请退款(可完整预览的文档不适用该条件!)。
- 3、如文档侵犯您的权益,请联系客服反馈,我们会尽快为您处理(人工客服工作时间:9:00-18:30)。
精益生产之_八大浪费1
1.不良、修理的浪费
所谓不良、修理的浪费,指的是由于工厂内出现不良品,需要进行处置的时间、人力、物力上的浪费,以及由此造成的相关损失。
这类浪费具体包括:材料的损失、不良品变成废品;设备、人员和工时的损失;额外的修复、鉴别、追加检查的损失;有时需要降价处理产品,或者由于耽误出货而导致工厂信誉的下降。
2.加工的浪费
加工的浪费也叫过分加工的浪费,主要包含两层含义:第一是多余的加工和过分精确的加工,例如实际加工精度过高造成资源浪费;第二是需要多余的作业时间和辅助设备,还要增加生产用电、气压、油等能源的浪费,另外还增加了管理的工时。
3.动作的浪费
动作的浪费现象在很多企业的生产线中都存在,常见的动作浪费主要有以下12种:两手空闲、单手空闲、作业动作突然停止、作业动作过大、左右手交换、步行过多、转身的角度太大,移动中变换“状态”、不明技巧、伸背动作、弯腰动作以及重复动作和不必要的动作等,这些动作的浪费造成了时间和体力上的不必要消耗。
4.搬运的浪费
从精益生产的角度看,搬运是一种不产生附加价值的动作,而不产生价值的工作都属于浪费。
搬运的浪费具体表现为放置、
堆积、移动、整列等动作浪费,由此带来物品移动所需空间的浪费、时间的浪费和人力工具的占用等不良后果。
国内目前有不少企业管理者认为搬运是必要的,不是浪费。
因此,很多人对搬运浪费视而不见,更谈不上去消灭它。
也有一些企业利用传送带或机器搬运的方式来减少人工搬运,这种做法是花大钱来减少工人体力的消耗,实际上并没有排除搬运本身的浪费。
5.库存的浪费
按照过去的管理理念,人们认为库存虽然是不好的东西,但却是必要的。
精益生产认为,库存是没有必要的,甚至认为库存是万恶之源。
由于库存很多,将故障、不良品、缺勤、点点停、计划有误、调整时间过长、品质不一致、能力不平衡等问题全部掩盖住了。
例如,工厂生产线出现故障,造成停机、停线,但由于有库存而不至于断货,这样就将故障造成停机、停线的问题掩盖住了,耽误了故障的排除。
如果降低库存,就能将上述问题彻底暴露于水平面,进而能够逐步地解决这些库存浪费。
6.制造过多过早的浪费
制造过多或过早,提前用掉了生产费用,不但没有好处,还隐藏了由于等待所带来的浪费,失去了持续改善的机会。
有些企业由于生产能力比较强大,为了不浪费生产能力而不中断生产,增加了在制品,使得制品周期变短、空间变大,还增加了搬运、堆积的浪费。
此外,制造过多或过早,会带来庞大的库存量,利
息负担增加,不可避免地增加了贬值的风险。
7.等待的浪费
由于生产原料供应中断、作业不平衡和生产计划安排不当等原因造成的无事可做的等待,被称为等待的浪费。
生产线上不同品种之间的切换,如果准备工作不够充分,势必造成等待的浪费;每天的工作量变动幅度过大,有时很忙,有时造成人员、设备闲置不用;上游的工序出现问题,导致下游工序无事可做。
此外,生产线劳逸不均等现象的存在,也是造成等待浪费的重要原因。
8.管理的浪费
管理浪费指的是问题发生以后,管理人员才采取相应的对策来进行补救而产生的额外浪费。
管理浪费是由于事先管理不到位而造成的问题,科学的管理应该是具有相当的预见性,有合理的规划,并在事情的推进过程中加强管理、控制和反馈,这样就可以在很大程度上减少管理浪费现象的发生。
JIT品质管理方法
与传统品质管理不同,精益生产的品质管理强调的是事前预防不良品的发生。
具体是从操作者、机器、工具、材料和生产过程等各方面保证不出现不良品。
它强调从根源上保证品质,品质的控制应该注重于预防,而不是传统方法的事后检验。
传统的品质观念认为不良是不可避免的,所以必须检验。
精益生产的观念与前者的观念恰好相反,精益生产认为:不良是可以避免的,过多的检验工序是多余的。
因此,实行精益化生产的工厂,它的品质管理工人数量都会很少,员工对自己负责,自己
做出的产品自己负责品质管理。
设置过多的品质管理工人反而不能有效的降低不良率。
因为有多道工序的检验,会发生互相推托的情况,前面的工序认为后面还有检验的工序,所以马虎一些没有关系,可是后面的工序往往容易认为前面已经检验过了,也不会太认真。
如果多道工序变成一道,那么责任明确后他反而会非常认真的检验,出货的不良率反而大幅度降低。