盐酸再生脱硅预处理技术和调试要点探讨
探索酸洗废酸的除硅机理与条件
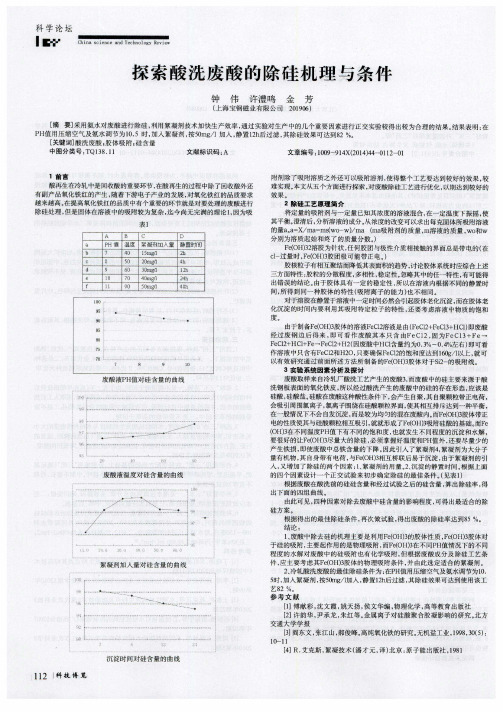
1前 言 酸再生 在冷轧 中是 回收酸 的重要环节 , 在 酸再生 的过程 中除 了回收酸外 还 有 副产 品氧 化铁 红的 产生 , 随着 下游 电子 产业 的发展 , 对 氧 化铁 红的 品质要 求 越 来越高 。 在提 高氧化 铁红 的品质 中有个 重要 的环 节就 是对要处 理的 废酸进 行 除 硅处理 , 但是 固体在 溶 液中 的吸 附较为 复杂 , 迄 今 尚无完 满的理 论 1 , 因为 吸
表1
A B C D
P H值 温廛 鬻黼剂加 A重 静 煎时闺
b 4 0 l 5 m 2 h
附剂 除 了吸附溶 质 之外还 可 以吸附溶 剂 , 使 得整个 工艺 要达 到较好 的效 果 , 较 难实 现。 本 文从五 个方 面进行探 索 , 对 废酸 除硅工 艺进行优 化 , 以期达 到较 好的 效果 。 2除 硅工 艺原 理简 介 将 定量 的吸 附剂与 一定 量 已知 其浓度 的溶 液混 合 , 在 一 定温度 下振 摇 , 使 其平衡 。 澄 清后 , 分析溶 液的成 分。 从 浓度 的改变 可以求 出每克 固体所 吸附溶 液 的量a 。 a = X/ ma =ms ( wo w) / ma ( i i l a 吸 附剂的 质 量 , m溶液 的 质量 , wo 和w 分别 为溶 质起 始和 终 了的质 量分 数 。 ) F e ( O H) 3 2 溶胶为 针状 , 任何 胶 团与极性 介质 相接触 的界 面总是 带 电的 ( 在 c l 一 过量时, F e ( O H) 3 胶 团极可 能带 正 电。 )
1废酸中除去硅的机理主要是利用feoh3的胶体性质feoh3胶体对于硅的吸附主要起作用的是物理吸附而feoh3在不同ph值情况下的不同程度的水解对废酸中的硅吸附也有化学吸附但根据废酸成分及除硅工艺条件应主要考虑其feoh3胶体的物理吸附条件并由此选定适合的絮凝剂
酸再生工艺
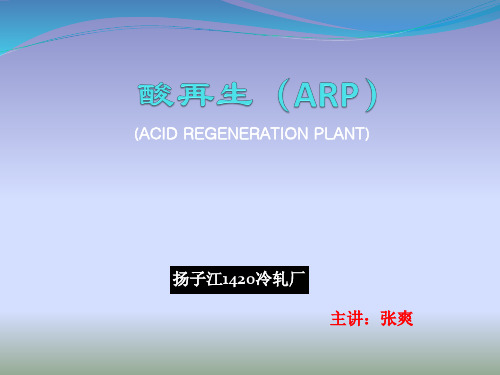
1.2基本原理
1.在废酸中投入废钢,使废酸中的游离HCl和废钢片进行充分的反应,减少废酸
中的游离酸。
Fe+2HCl → FeCl2+H2↑ Fe2O3+6HCl → 2FeCl3+3H2O
2.通过加入氨水,提高废酸的PH值,使一部分Fe2+形成Fe(OH)2,通过曝气
形成Fe(OH)3絮凝体,达到吸附废酸中的硅,通过沉淀池沉淀、压滤机过滤将 废酸中的硅从废酸中去除。 2NH3+2H2O+ FeCl2→ Fe(OH)2+2NH4Cl
浸溶塔 设备数量:1台 设备功能:经石墨加热器加热后的废酸在浸溶塔内与废钢切边料 进行反应,游离盐酸反应生成FeCl2,以尽可能的去除废酸中的 游离酸。 结构形式:立式钢结构圆柱体,敞口容器,底部为锥形。钢衬胶 衬砖材质。被加热的废酸从浸溶塔底部,经过PVDF滤板过滤后 进入容器,并与投加到塔内的废钢片进行反应,在上升过程中, 废酸中的游离盐酸与过量的废钢片充分接触,并完全反应,生成 的氯化亚铁溶液从浸溶塔顶部的出口流出。反应生成的氢气、以 及在此过程中产生的水蒸气、少量的盐酸蒸汽在浸溶塔檐口处被 集中收集,并处理。 介质参数:废酸,HCl-1~60g/l,FeCl2-250~350g/l,FeCl3-1~10g/l, 密度~1.3 kg/dm3
主要参数: 1:1比率泵 流量 ………… 25m3/h 扬程 ……………0.5~0.6MPa 1:2比率泵 流量 ………… 5m3/h 扬程 ……………0.6~1.0MPa 主要材质: 隔膜 ………聚亚安脂polyurethane 阀球 ………聚亚安脂polyurethane 阀座 ………聚亚安脂polyurethane 外壳 ………铸铁
加药系统
絮凝剂投加装置
制备装置 设备数量:1台 设备功能:用于将絮凝剂粉体自动配置成指定浓度的液体药剂,并投加 到机组中。 介质成分:PAM,0.1~0.5%(w/w),脱盐水。 设备形式:全自动干粉投加,包括:除湿料斗、干粉投加机、干粉润湿 器、溶液制备箱、搅拌机、螺杆泵、液位计、流量计、后稀释系统以及 PLC电控系统等。 主要参数: 干粉供料能力 ………………………………500kg/月(max) 溶解投加精度 ………………………………0.5%
废酸再生脱硅预处理浅谈
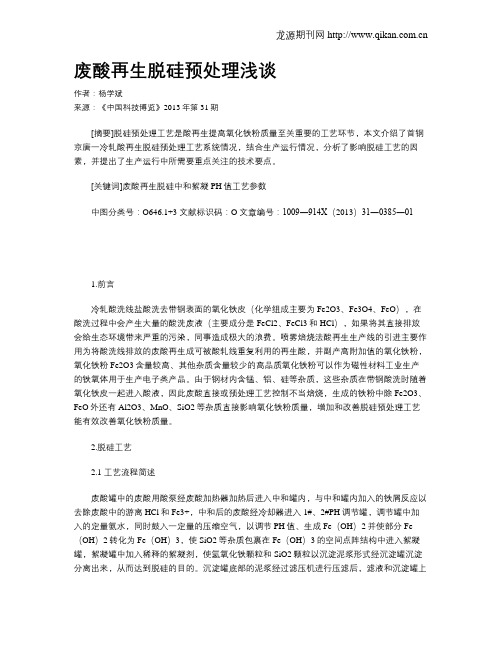
废酸再生脱硅预处理浅谈作者:杨学斌来源:《中国科技博览》2013年第31期[摘要]脱硅预处理工艺是酸再生提高氧化铁粉质量至关重要的工艺环节,本文介绍了首钢京唐一冷轧酸再生脱硅预处理工艺系统情况,结合生产运行情况,分析了影响脱硅工艺的因素,并提出了生产运行中所需要重点关注的技术要点。
[关键词]废酸再生脱硅中和絮凝PH值工艺参数中图分类号:O646.1+3 文献标识码:O 文章编号:1009―914X(2013)31―0385―011.前言冷轧酸洗线盐酸洗去带钢表面的氧化铁皮(化学组成主要为Fe2O3、Fe3O4、FeO),在酸洗过程中会产生大量的酸洗废液(主要成分是FeCl2、FeCl3和HCl),如果将其直接排放会给生态环境带来严重的污染,同事造成极大的浪费。
喷雾焙烧法酸再生生产线的引进主要作用为将酸洗线排放的废酸再生成可被酸轧线重复利用的再生酸,并副产高附加值的氧化铁粉,氧化铁粉Fe2O3含量较高、其他杂质含量较少的高品质氧化铁粉可以作为磁性材料工业生产的铁氧体用于生产电子类产品。
由于钢材内含锰、铝、硅等杂质,这些杂质在带钢酸洗时随着氧化铁皮一起进入酸液,因此废酸直接或预处理工艺控制不当焙烧,生成的铁粉中除Fe2O3、FeO外还有Al2O3、MnO、SiO2等杂质直接影响氧化铁粉质量,增加和改善脱硅预处理工艺能有效改善氧化铁粉质量。
2.脱硅工艺2.1 工艺流程简述废酸罐中的废酸用酸泵经废酸加热器加热后进入中和罐内,与中和罐内加入的铁屑反应以去除废酸中的游离HCl和Fe3+,中和后的废酸经冷却器进入1#、2#PH调节罐,调节罐中加入的定量氨水,同时鼓入一定量的压缩空气,以调节PH值、生成Fe(OH)2并使部分Fe (OH)2转化为Fe(OH)3,使SiO2等杂质包裹在Fe(OH)3的空间点阵结构中进入絮凝罐,絮凝罐中加入稀释的絮凝剂,使氢氧化铁颗粒和SiO2颗粒以沉淀泥浆形式经沉淀罐沉淀分离出来,从而达到脱硅的目的。
酸再生工艺

1.2基本原理
1.在废酸中投入废钢,使废酸中的游离HCl和废钢片进行充分的反应,减少废酸
中的游离酸。 Fe+2HCl → FeCl2+H2↑ Fe2O3+6HCl → 2FeCl3+3H2O
2.通过加入氨水,提高废酸的PH值,使一部分Fe2+形成Fe(OH)2,通过曝气
形成Fe(OH)3絮凝体,达到吸附废酸中的硅,通过沉淀池沉淀、压滤机过滤将 废酸中的硅从废酸中去除。
2NH3+2H2O+ FeCl2→ Fe(OH)2+2NH4Cl 2 Fe(OH)2+1/2O2 +H2O → 2Fe(OH)3 FeCl3+ 3NH3+3H2O → Fe(OH)3+3NH4Cl
1.3盐酸脱硅工艺流程
废钢片
石墨 冷却 器
冷循 却环 水水
浸溶塔
过滤器
蒸汽
石墨
加热
冷凝水
器
废酸
压缩空气
净环水出口温度 ≤45℃
氨水储罐
设备数量:1座
设备功能:用于储存浓度为20~25%的氨水,供脱硅
系统使用。布置在独立的房间内。
结构形式:立式圆柱体(包括顶盖,必要的管嘴、法
兰、人孔等)、普碳钢材质。
主要参数:
容积
…………… 80m3
罐体高度
……………5m
罐体直径
……………5m
中和反应槽
设备数量:1台
过滤面积
……………2m2
过滤精度
……………1000µm
过滤能力
……………18 m3/hr
介质温度
……………85℃
主要材质:
壳体…………………………………………………… PPH
滤筒…………………………………………………… PPH
盐酸深脱技改项目方案收藏版(可编辑)

盐酸深脱技改项目方案收藏版盐酸零解析技术方案一、项目名称:盐酸零解析技术改造项目二、项目建设的必要性: 目前有机硅装置20%稀酸产量约2万吨/年,20万吨甲烷氯化物装置副产22%稀盐酸5万吨,10万吨甲烷氯化物达产后副产22%稀盐酸5万吨/年,目前总计12万吨/年的稀盐酸将影响园区经济运行,利用稀盐酸零解析技术,将22%的稀盐酸进行深度解析处理,得到高纯度的氯化氢气体生产一氯甲烷,解析后回收的废水中含氯化氢低于0.7%,作为吸收剂循环使用或中和后达标排放。
三、技术方案及流程:目前盐酸零解析有二种工艺.1、差压法,2、氯化钙法1、差压法:浓酸罐内约22%左右的酸经过双效换热器加热后入进入高压脱析塔,和脱吸塔底部的被蒸发的氯化氢和水的混合气体充分接触,气液混合物在塔内完成热量与质量交换,浓酸中的氯化氢得到热量被解析出来,经塔顶冷却器和再冷却器冷却后,得到干燥的氯化氢。
脱吸塔底部的稀酸(18%)直接进入真空脱水塔进行脱水,与来自再沸器的混合气体进行传热传质,由于真空状态下酸共沸点较高(22%),水蒸汽通过塔顶冷凝器冷凝成废水后处理排放,塔底的浓酸进入浓酸储罐。
附简图:1.2、氯化钙法氯化钙法的深脱吸流程与现有的盐酸脱吸流程基本相仿,22%的稀盐酸与氯化钙循环泵输送的氯化钙溶液(浓度50%左右)混合后,进入解吸塔,溶液从汽提塔顶部进入,在重力的作用下向下流动过程中通过填料和内件时发生高效传质过程.氯化钙溶液作为共沸打破物,相对于HCl气体的分压来说抑制了水蒸汽的分压。
汽提出的气体首先进入氯化氢一冷器(循环水冷却)冷却到40℃左右,在这里大部分夹带的水被冷凝。
再进入氯化氢二冷器(-15℃冷冻盐水冷却)冷却到≤-5℃左右。
经过二级冷却后的氯化氢气体,经除雾器除沫后输送至用户工序。
在汽提塔底,稀氯化钙溶液(40%左右)被送入氯化钙闪蒸分离罐,过量的水被闪蒸蒸发出去,经蒸发冷凝器将水蒸汽进行充分冷凝后收集到废水槽,然后再用稀酸废水泵送出界区外或去相关工序作为吸收剂吸收HCL制成盐酸循环使用。
常压脱硅操作规程

常压脱硅操作规程常压脱硅是一种常用的化工操作过程,主要用于去除硅元素,使得原料更纯净。
下面是一份常压脱硅操作规程,详细介绍了操作步骤、安全注意事项以及常见故障的处理方法。
一、操作步骤1. 准备工作首先,需要准备好各种设备和试剂。
设备包括脱硅反应器、搅拌机、加热装置、冷却装置和管道连接等。
试剂主要有硅矿石、稀硫酸和稀盐酸等。
2. 开始反应将硅矿石适量投入脱硅反应器中,然后加入足够的稀硫酸和稀盐酸。
启动搅拌机,使反应物充分搅拌。
控制反应温度在80°C 左右。
3. 反应时间根据脱硅反应的具体情况,确定反应时间。
通常情况下,反应时间为4-6小时。
4. 过滤提取反应结束后,将反应物进行过滤提取。
首先,使用滤纸将反应物和溶液分离,得到固体残渣。
然后,将溶液进行提取,得到含硅的溶液。
5. 清洗处理将固体残渣进行清洗处理,去除其中的杂质。
可以使用稀盐酸进行清洗,然后用纯水冲洗干净。
6. 干燥处理将清洗后的固体残渣进行干燥处理,使其完全干燥。
可以使用加热装置进行干燥,控制温度在100°C左右,保持一段时间。
7. 脱硅成品经过干燥处理后,固体残渣即为脱硅成品,可以用于后续工艺。
二、安全注意事项1. 操作人员需戴好安全装备,包括防护眼镜、防护手套、防护口罩等。
2. 操作过程中应注意防止溶液溢出造成伤害。
在加入稀硫酸和稀盐酸时,应缓慢倒入,以避免剧烈反应。
3. 控制反应温度时,应注意不要超过80°C,以防止溶液沸腾溢出。
4. 操作结束后,应立即关闭加热装置、冷却装置和搅拌机,确保设备的安全和实验室的整洁。
5. 反应结束后,应妥善处理废液,避免对环境造成污染。
三、常见故障及处理方法1. 反应温度过高若反应温度超过80°C,有可能导致溶液沸腾溢出,造成安全事故。
此时,需要立即关闭加热装置,并迅速降低温度,可以使用冷却装置。
2. 溶液溢出若溶液溢出,可能是因为反应物加入过多或搅拌机转速过高。
现有的高温脱氯技改配合HCl(Cl2)分离技术处理连续重整再生废气的分析
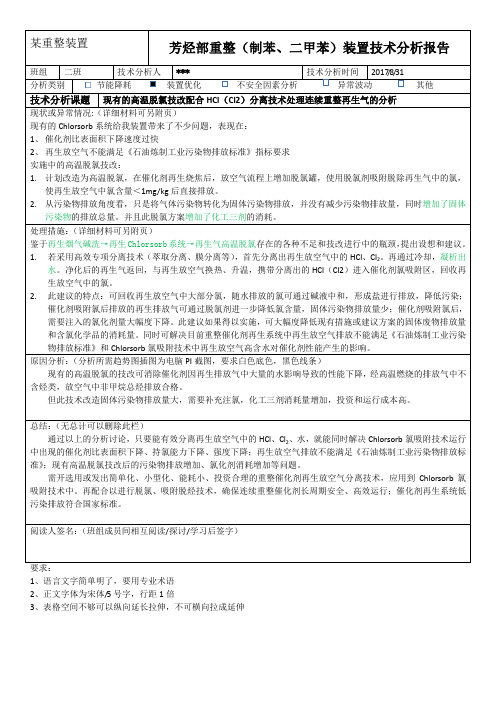
某重整装置芳烃部重整(制苯、二甲苯)装置技术分析报告班组二班技术分析人***技术分析时间2017/8/31分析类别节能降耗装置优化不安全因素分析异常波动其他技术分析课题现有的高温脱氯技改配合HCl(Cl2)分离技术处理连续重整再生气的分析现状或异常情况:(详细材料可另附页)现有的Chlorsorb系统给我装置带来了不少问题,表现在:1、催化剂比表面积下降速度过快2、再生放空气不能满足《石油炼制工业污染物排放标准》指标要求实施中的高温脱氯技改:1.计划改造为高温脱氯,在催化剂再生烧焦后,放空气流程上增加脱氯罐,使用脱氯剂吸附脱除再生气中的氯,使再生放空气中氯含量<1mg/kg后直接排放。
2.从污染物排放角度看,只是将气体污染物转化为固体污染物排放,并没有减少污染物排放量,同时增加了固体污染物的排放总量。
并且此脱氯方案增加了化工三剂的消耗。
处理措施:(详细材料可另附页)鉴于再生烟气碱洗→再生Chlorsorb系统→再生气高温脱氯存在的各种不足和技改进行中的瓶颈,提出设想和建议。
1.若采用高效专项分离技术(萃取分离、膜分离等),首先分离出再生放空气中的HCl、Cl2。
再通过冷却,凝析出水。
净化后的再生气返回,与再生放空气换热、升温,携带分离出的HCl(Cl2)进入催化剂氯吸附区,回收再生放空气中的氯。
2.此建议的特点:可回收再生放空气中大部分氯,随水排放的氯可通过碱液中和,形成盐进行排放,降低污染;催化剂吸附氯后排放的再生排放气可通过脱氯剂进一步降低氯含量,固体污染物排放量少;催化剂吸附氯后,需要注入的氯化剂量大幅度下降。
此建议如果得以实施,可大幅度降低现有措施或建议方案的固体废物排放量和含氯化学品的消耗量。
同时可解决目前重整催化剂再生系统中再生放空气排放不能满足《石油炼制工业污染物排放标准》和Chlorsorb氯吸附技术中再生放空气高含水对催化剂性能产生的影响。
原因分析:(分析所需趋势图插图为电脑PI截图,要求白色底色,黑色线条)现有的高温脱氯的技改可消除催化剂因再生排放气中大量的水影响导致的性能下降,经高温燃烧的排放气中不含烃类,放空气中非甲烷总烃排放合格。
撬装LNG工厂脱酸脱水系统调试及总结

1、净化系统调试天然气净化系统调试准备工作主要包括氮气置换及气密性试验、胺液系统水洗、热碱洗、脱盐水置换、配胺液、胺液冲洗及发泡试验,建立胺液循环。
1.1 净化系统氮气置换机械竣工验收合格后,净化系统即可开始氮气置换和气密性试验。
1.1.1净化系统氮气置换要求净化系统中的氧含量小于0.5%为合格。
1.1.2氮气置换过程采用冲压泄压的方式反复多次,在出口适当位置取样分析氧含量。
氮气置换分高压部分和低压部分(胺液再生系统),利用制氮系统氮气作为置换气源,控制高压部分压力500kPa.G以内,胺液再生系统压力50kPa.G。
净化氮气置换过程主要如下:1)流程确认及阀门状态检查高压部分置换,来自氮气总管的氮气从原料气入口切断阀KV-11101前支路进入天然气主管道,顺着天然气主流程依次经过原料气过滤器F-1101、吸收塔T-1201、吸收塔顶空冷器E-1201、吸收塔顶气液分离器V-1201、吸收塔顶过滤器F-1201、脱硫脱汞塔T-1302、吸附净化塔T-1301ABC、再生气空气冷却器E-1302、再生气冷冻盐水冷却器E-1303、再生气气液分离器V-1301。
冲压至500kPa.G 左右,从不合格气放空管线泄压。
根据现场情况,从AP-13118取样口取样做氧含量分析。
低压部分置换,利用闪蒸罐(氮气压力500kPa.G左右)液位调节阀LV-12506控制再生塔T-1202缓慢升压至50kPa.G,从CO2气液分离器的放空口泄压。
氮气置换前阀门状态检查表见表1-1。
2)净化系统氮气冲压置换中控监视高压部分和低压部分的压力,达到设定压力即关闭氮气补充阀门,依次从各设备放空点、排污点泄压。
降压至10kPa.G左右,反复氮气冲压和泄压。
3)氧含量分析通过现场观察,确定高压部分从AP-13118点取样,低压部分从PG-12604处取样。
利用氧含量分析仪,分析取样点氧含量。
气体氧含量小于0.5%即表示氮气置换合格。
除硅技术优化研究与应用

硬度 现场 48 56 72 原有 48 56 72
总铁 现场 0.09 0.18 0.2 原有 0.09 0.18 0.2
指标(mg/l)
现场 来水 除油罐 混凝池 浮选 除硅 1510 155 22 原有 1510 155 22
1.47 1.47 1
0.65
17 15
4.09
15 20
5
145 94
4
5
胶体硅去除率高
离子硅去除率高
要求进水阳离子含量低、耗能高、投资费用大
要求盐分含量低、无法去除胶体硅
6
成本低、操作方便
抑制效率低下、实用性不强
室内药剂试验
玻璃仪器 试验仪器 实验平台
计量仪器
室内药剂试验
除硅剂 主要成分 主要作用 投加浓度 mg/l
120 100
96 100
除硅剂C
聚合氯化铝
混凝
1730
80 60 40
室内实验水质达标
除硅剂A 氢氧化钠溶液 调节ph值、预除硬 除硅剂B 除硅剂D 硫酸镁晶体 聚丙烯酰胺 生成硅酸镁沉淀 助凝
500 100 130
实验水质 要求指标
30
20
24 2
20 0 SiO2
12 1.04
悬浮物
含油
总硬度
2460 mg/l
室内药剂试验
除硅药剂试验对比
实验水质 要求指标
24 2 1.04 合计 30
40
20
1000 除硅剂D
500 0
合计
除硅剂A
3596
除硅剂B
2460
除硅剂C
20 131 0
除硅剂D
130 12
浅谈氯乙烯生产中盐酸脱析装置常见问题及解决方法

2018年07月浅谈氯乙烯生产中盐酸脱析装置常见问题及解决方法李辉黄晓娟郭丽朱玉祺(甘肃省银光聚银化工有限公司PVC 厂,甘肃白银730900)摘要:结合生产实际情况,分析盐酸脱析装置中塔顶出口温度高、脱析塔压力高等工艺异常现象,提出解决方法。
关键词:氯乙烯;盐酸脱析;工艺异常;解决方法甘肃银光聚银公司PVC 厂采用电石法悬浮聚合工艺生产SG-5型PVC 树脂,生产线自投产以来,运行平稳。
生产聚氯乙烯,需要氯乙烯单体发生聚合反应,而在氯乙烯的生产过程会产生大量的盐酸,产生的盐酸作为副产品销售。
在这个过程中,不仅造成了盐酸的浪费而且产生的酸雾会污染环境。
为了降低生产成本和减少对环境的污染,本厂自2015年成功投用盐酸脱析装置,有效的解决了盐酸回收利用和环境污染问题,装置的投用获得了良好的经济效益和社会效益。
1盐酸脱析原理[1]浓盐酸进入脱析塔后,与塔底再沸器用蒸汽加热的高温氯化氢和水蒸气进行连续接触逆流传质传热。
浓盐酸通过重力的作用沿着填料表面下降,与上升气体接触,使上升气体中的氯化氢含量不断的增加,浓盐酸中的氯化氢气体不断地析出,氯化氢气体和水蒸气从塔顶分别进入一级、二级、三级冷却器,水分经过冷凝后从冷凝器底部流出,高纯度的氯化氢气体,从冷凝器导出至转化工段,用于合成氯乙烯。
2盐酸脱析的工艺流程转化合成单元生产出浓度为26-33%左右的浓盐酸,储存在浓盐酸储槽中。
用浓盐酸泵输送至盐酸脱析装置,浓盐酸经过双效换热器,加热至40-60℃左右从脱析塔顶部进入脱析塔,经过液体分布器,喷淋至填料表面,与来自塔底再沸器约110-130℃的氯化氢和水蒸气混合物在填料表面逆向接触进行传质传热。
提纯后的氯化氢气体和水蒸气温度控制在50-100℃,压力在20-100KPa ,从脱析塔顶部进入以循环水作为冷却介质的一级冷却器进行冷却;未被冷却的混合物进入以5℃水为冷却介质的二级冷却器进行冷却;未被冷却的混合物进入以-35℃冷冻盐水为冷冻介质的三级冷却器进行冷却,得到纯度为99.0%以上的氯化氢气体,经过酸雾捕集器脱出水分后输送至转化合成单元使用。
酸再生脱硅工艺流程

酸再生脱硅工艺流程
朋友!今天跟您唠唠酸再生脱硅这档子事儿。
咱先说说这酸再生脱硅啊,可真是个让人又爱又恨的活儿!我记得我刚入行那会,哇,简直被它搞得晕头转向!
这流程呢,一开始得把那些酸液弄进来。
就这一步,我当初可没少犯错,唉,别提多懊恼了!有次我稀里糊涂的,把顺序都给弄反了,结果被师傅好一顿骂,哈哈!
然后啊,经过一系列的操作,什么加热啦,搅拌啦,这里面的讲究可多了去了。
我跟您说,有一回,我们厂里的小王,就因为加热温度没控制好,那场面,简直是“惨不忍睹”!
说到这搅拌,那声音,“嗡嗡嗡”的,刚开始听着还觉得挺烦,后来习惯了,没这声音还觉得少点啥呢!
这中间还有个关键的步骤,我记得好像是要加入一种特别的试剂,不过也可能记错喽。
要是加错了或者加少了,那可就麻烦大啦!
我这说着说着好像有点乱了。
咱再回来说说前面提到的酸液引进,这里面可还有不少小细节呢。
比如说,酸液的浓度就得把控好,不然整个流程都得玩儿完。
嗯...这后面还有好几步,我先跟您卖个关子,等您自己去琢磨琢磨。
要是您碰到啥难题,别担心,随时来找我!
对了,跟您说个行业里的趣事儿。
有个厂啊,听说他们搞这酸再生脱硅,结果弄出个大乌龙,把整个生产线都给搞停了,那损失,可海了去了!
现在这技术发展得也快,以前那些老办法好多都不管用啦。
就像我,也得不停地学习,不然就得被淘汰喽!。
碱浸取脱硅的方法
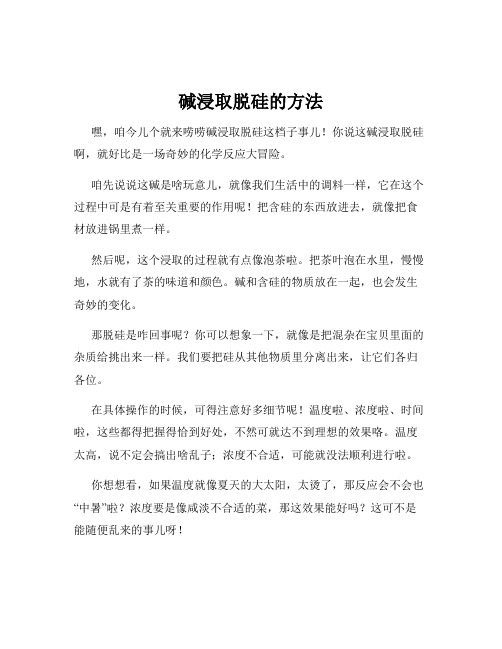
碱浸取脱硅的方法嘿,咱今儿个就来唠唠碱浸取脱硅这档子事儿!你说这碱浸取脱硅啊,就好比是一场奇妙的化学反应大冒险。
咱先说说这碱是啥玩意儿,就像我们生活中的调料一样,它在这个过程中可是有着至关重要的作用呢!把含硅的东西放进去,就像把食材放进锅里煮一样。
然后呢,这个浸取的过程就有点像泡茶啦。
把茶叶泡在水里,慢慢地,水就有了茶的味道和颜色。
碱和含硅的物质放在一起,也会发生奇妙的变化。
那脱硅是咋回事呢?你可以想象一下,就像是把混杂在宝贝里面的杂质给挑出来一样。
我们要把硅从其他物质里分离出来,让它们各归各位。
在具体操作的时候,可得注意好多细节呢!温度啦、浓度啦、时间啦,这些都得把握得恰到好处,不然可就达不到理想的效果咯。
温度太高,说不定会搞出啥乱子;浓度不合适,可能就没法顺利进行啦。
你想想看,如果温度就像夏天的大太阳,太烫了,那反应会不会也“中暑”啦?浓度要是像咸淡不合适的菜,那这效果能好吗?这可不是能随便乱来的事儿呀!而且哦,不同的材料可能需要不同的碱,就跟不同的菜需要不同的调料一样。
选错了碱,那可就像做菜放错了调料,味道就全变啦。
在这个过程中,还得时刻关注着反应的进展,就像看着锅里煮的汤,别煮干了或者煮糊了。
一旦发现有啥不对劲的地方,就得赶紧想办法调整。
碱浸取脱硅的方法虽然听着有点复杂,但只要咱认真对待,就像对待一件心爱的宝贝一样,肯定能把它做好呀!咱可不能小瞧了这小小的化学反应,它能给我们带来大大的惊喜呢!这不就是科学的魅力所在嘛!所以啊,大家可得好好研究研究这碱浸取脱硅的方法,说不定能发现好多有趣的东西呢!让我们一起在这个化学的世界里尽情探索吧!。
预脱硅及高压溶出生产工艺技术
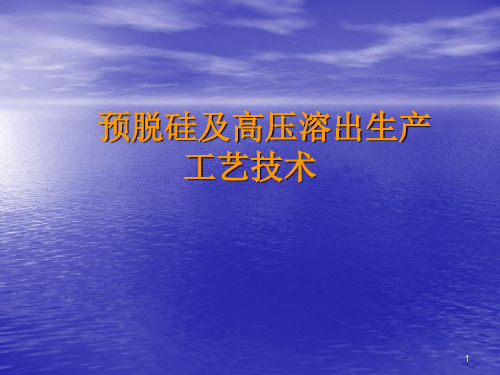
。
7
④脱硅停留时间。时间越长分解速度越快,溶液中最 终的SiO2含量越低。 ⑤铝土矿中存在的高岭石含量和质量。高岭石含量越 高分解速度越快,溶液中最终的SiO2含量越低。 2-2高压溶出 2-2-1相关名词 2-2-1-1铝硅比 铝土矿或赤泥中所含的Al2O3与SiO2的重量之比称为 铝硅比,用A/S表示。 2-2-1-2 αk值 αk值是指铝酸钠溶液中所含的氧化铝(Al2O3)与苛 性氧化钠(Na2OK或减称Nk)的分子比: αk =1.645*NK/A 2-2-1-3 循环效率 1m3循环母液在一次拜耳法循环过程中所能生产出的 氧化铝量称为循环效率,用E表示: 循环效率用αk表示为:
13
三水铝石在接近常压、温度140℃~150℃、循环母液较低的 情况下即可溶出,并能达到工业溶出的速度。而一水软铝石 型铝土矿则较难溶出,溶出温度160℃左右,苛性碱浓度要 求比三水铝石高。一水硬铝石最难溶出,温度要求在200℃ 以上,在高温、高压、高碱浓度时才能较好地溶出。 另外,铝土矿中的杂质含量(如TiO2、Fe2O3、SiO2等)越 多、越分散,氧化铝水合物被其包裹的程度越大,与碱溶液 接触越少,溶出越困难。 2、溶出温度: 温度是影响溶出过程中最重要的影响因素。 提高溶出温度,使溶出速度加快,溶液的粘度下降,有助于 矿石和碱液表面接触,从而提高氧化铝的溶出率。提高溶出 温度由于溶出速度快,可以缩短溶出时间。 随着温度的提高,Al2O3在碱溶液中的溶解度显著增加,溶 出液Rp值升高,有利于分解率的提高,从而可以提高碱液的 循环效率。提高溶出温度后,用浓度较低的循环母液亦可获
16
7、添加石灰: 在溶出一水硬铝石铝土矿时,氧化钛与碱液反应形成钛 酸钠薄膜包裹在矿粒表面,阻碍溶出过程的进行。加入石灰 可以破坏其薄膜,提高氧化铝的溶出率。但是加入石灰量太 多,不但增加赤泥量,而且由于3CaO.Al2O3.6H2O的生成, 造成大量氧化铝损失。 2-2-3各种杂质在溶出过程行为 铝土矿中杂质化学反应的结果,除极少量杂质溶于碱溶液 以外,绝大部分杂质都进入赤泥。铝土矿中的主要杂质: SiO2变成不溶的钠硅渣(Na2O.Al2O3.1.7SiO2. nH2O)和水 化石榴石(CaO.Al2O3.1.1SiO2.nH2O)而进入赤泥;氧化钛 生成不溶于碱溶液的2CaO.TiO2.2H2O而进入赤泥;铁的化 合物最终基本上都以铁的氧化物形态,进入赤泥。
- 1、下载文档前请自行甄别文档内容的完整性,平台不提供额外的编辑、内容补充、找答案等附加服务。
- 2、"仅部分预览"的文档,不可在线预览部分如存在完整性等问题,可反馈申请退款(可完整预览的文档不适用该条件!)。
- 3、如文档侵犯您的权益,请联系客服反馈,我们会尽快为您处理(人工客服工作时间:9:00-18:30)。
盐酸再生脱硅预处理技术探讨陈琦(宝钢工程技术集团有限公司,上海201900)摘要:盐酸再生脱硅预处理工艺与酸碱中和或氧化还原等废水处理工艺有一定类似,但其流程设置、设备配置、药剂选用又有其独特性,属于比较少见的“冷门”水处理工艺,也是仅在钢铁企业水处理系统中才独有的代表性工艺。
本文着重介绍了脱硅工艺的流程、主要设备配置和系统调试、运行中所需要重点关注的技术要点。
Discussion about desiliconization pretreatment treatmentChen Qi(Baosteel Engineering&Technology Group Co.,Ltd., Shanghai 201900)Summary:Desiliconization pretreatment for hydrochloric acid regeneration is similar with the other waste water treatment process such as acid alkali neutralization and oxidation reduction in some aspect. Meanwhile, it is also unique in process setting、equipment configuration and selection of chemical agents compared with other routine waste water treatment system. It is also can be regarded as relatively rare" unpopular" water treatment system and an unique representation water treatment system in the iron steel industry.In this article, it is introduced emphatically the process&main equipment of the desiliconization pretreatment treatment and the key technical points in system commissioning.关键词:盐酸水处理氧化铁粉脱硅浸溶塔氨水絮凝剂pH值板框压滤机一.盐酸再生进行脱硅预处理的目的和意义钢铁企业热轧钢带在进行冷轧加工前,都要进行酸洗工艺,以去除钢带中的氧化铁皮、油污和脏物。
酸洗工艺中,盐酸是非常重要的原料,几乎国内所有的钢铁企业都采用盐酸作为碳钢酸洗介质。
虽然盐酸酸洗可以完全回收,易于再生,但以往国内除了一些大型的钢铁企业建设酸再生站对将经酸洗后带大量金属杂质的废盐酸再生后循环使用外,一般中小型钢厂都将废盐酸与其他含酸废水送至废水处理站进行中和处理后达标排放,不但大大增加新酸消耗,而且高浓度、高金属含量的盐酸采用中和处理,其石灰药剂、污泥处置等费用也是相当可观的。
随着钢铁工业的不断发展和国家对环境保护、循环经济的重视和扶持,现在越来越多的钢铁企业乃至一些中小型的钢铁企业,在兴建酸洗机组的同时均兴建了盐酸再生站,对酸洗后的废盐酸用喷雾焙烧法进行再生,去除金属离子的再生盐酸被送回酸洗机组循环利用。
喷雾焙烧法是目前国内外使用最多的、也是最成熟的盐酸再生方法,废酸中的金属化合物(FeCl2、FeCl3)在高温的焙烧炉内发生分解反应,生成固态的Fe2O3和气态的水蒸气、HCl气体等混合气体,混合气体经旋风分离器分离部分粉尘、预浓缩器浓缩后,在吸收塔内HCl气体被酸洗漂洗水吸收形成可循环再用的再生酸。
与此同时,焙烧反应的固态生成物Fe2O3氧化铁粉作为盐酸再生工艺的副产品可以回收再利用,创造出新的附加值,这也是越来越多的钢铁企业采用废盐酸再生循环使用取代废盐酸直接中和处置的另一个重要原因。
Fe2O3含量较高、其他杂质含量较少的高品质氧化铁粉可以作为磁性材料工业生产的铁氧体用于生产电子类产品,其市场的回报率很高。
根据2008年颁布的国家标准SJ/T10383《软磁铁氧体用氧化铁》(附表1)中规定的氧化铁粉的质量标准,用于磁性材料生产原料至少各主要成分指标达到YHT1级品标准。
附表1:《软磁铁氧体用氧化铁》SJ/T10383部分重要指标化学成分质量百分数(%)YHT0 YHT1 YHT2 YHT3 氧化铁(Fe2O3) 不小于99.40 99.30 99.00 98.80 二氧化硅(SiO2)不大于0.008 0.010 0.015 0.030 三氧化二铝(Al2O3)不大于0.008 0.010 0.020 0.040 氧化锰(MnO)不大于0.30 0.30 0.30 0.30 硫酸盐(以SO42-计)不大于0.05 0.10 0.15 0.15 氯化物(Cl-)不大于0.10 0.15 0.15 0.20 水分(H2O)不大于0.30 0.50 0.50 0.50废盐酸直接焙烧再生后的氧化铁粉副产品Fe2O3含量能基本达到99.3%以上,但其SiO2含量一般在200~500ppm左右,达不到上述可作为磁性材料生产原料的YHT1级品标准,只能作为YHT3级品甚至次品出售,用于颜料和非铁氧体陶瓷生产、粉末冶金工业等相对低端的生产原料甚至只能作为烧结原料在钢铁企业内部自行消化。
是什么原因造成铁粉质量不佳呢?由于钢材内含有锰、铝、硅、铜、锌等杂质,这些杂质随着热轧过程中生成的氧化铁皮在酸洗时脱落一起进入盐酸酸洗液中,因此废盐酸直接进行焙烧反应,生成的固态金属化合物中,除了Fe2O3、FeO等外,还有Al2O3、MnO、SiO2等,直接影响了氧化铁粉的质量。
高品质的氧化铁粉的市场价格在2500~3000元/吨左右,而低质量的氧化铁粉只有700~1000元/吨。
SiO2是影响氧化铁粉质量的重要指标,若能将其含量在100ppm以下则氧化铁粉的价格将翻几倍,所以要获得高质量氧化铁粉必须对SiO2含量进行控制。
在废盐酸进入焙烧酸再生工艺前对其进行脱硅预处理,能有效的改善氧化铁粉的产品质量,大幅度的提高盐酸再生站的经济效益。
前几年在国内,只有宝钢等少数大型企业在兴建盐酸再生站时设置脱硅预处理系统。
这几年随着高品质氧化铁粉的市场需求量日益上升,价格也节节攀高,盐酸再生氧化铁粉副产品的附加值被越来越多的钢铁企业所认识。
一座处理能力在10m3/h的盐酸再生站,设置脱硅预处理系统的总投资在2000~3000万元左右,正常生产每年的氧化铁粉销售额在1500万元左右,扣除运行成本和原料消耗成本,五~六年就能收回建设成本,具有相当的投资价值。
因此,近年来在为新建酸洗机组配套建设盐酸再生站时,带脱硅预处理系统的盐酸再生站被越来越多的钢铁企业所接受,这些有市场远见的钢铁企业不再把盐酸再生站仅仅视为为减少盐酸消耗而建设的环保节能类公辅站房,而是同时作为能产生较高环境效益和经济效益的生产工艺站房。
二.脱硅预处理系统工艺介绍脱硅预处理系统与采用酸碱中和或氧化还原反应的废水处理系统有一定的类似之处,但其流程设置、设备配置、药剂选用又有其独特性,属于比较少见的“冷门”水处理工艺,也是仅在钢铁企业水处理系统中才独有的代表性工艺。
脱硅预处理系统主要由溶解、氧化、反应、沉淀以及污泥处理等工艺过程组成,主要工艺流程如下:废盐酸先进入废酸储罐调节,然后通过提升泵提升至石墨加热器,加热至80℃左右,然后自流从下部进入浸溶塔,在浸溶塔内加入废钢片使废盐酸中的游离酸在高温条件下充分发生以下反应:2HCl + Fe → Fe Cl2 + H26HCl + Fe2O3→ 2 Fe Cl3 + 3H2O从浸溶塔上部溢流出来的饱和废酸液再自流入石墨冷却器,降温至45℃左右后自流至反应罐。
在反应罐内投加氨水将废酸的pH值调整至弱酸性,同时在反应罐底部吹入空气使浸溶反应生成的FeCl2充分氧化成FeCl3并进一步生成Fe(OH)3,反应方程式如下:FeCl2 + 2NH3 + 2H2O = Fe(OH)2 + 2NH4ClFeCl3 + 3NH3 + 3H2O = Fe(OH)3 + 3NH4Cl4Fe(OH)2+O2+2H2O=4Fe(OH)3Fe(OH)3有吸附废酸中的SiO2并生成小颗粒的絮体的功能,反应罐的溢流液进入沉淀罐,通过投加絮凝剂使小絮体变成大絮体,经沉淀罐沉淀分离,达到除硅目的。
沉淀罐底部沉淀的污泥用污泥泵输送送至板框压滤机脱水,沉淀罐上清液和板框压滤机滤液则作为脱硅后的处理酸送入盐酸再生主工艺系统进行焙烧反应。
在脱硅反应的同时,废盐酸中的其他金属离子如锰、铝、铜、锌等在上述反应中也部分生成相应的金属氢氧化物沉淀下来,因此脱硅不仅去除了最影响盐酸再生副产品氧化铁粉质量的SiO2,也部分去除了其他可能影响其品质的其他金属类杂质。
脱硅预处理系统的工艺系统简图见附图1。
附图1:脱硅预处理系统的工艺流程框图在这里重点介绍为何选用氨水作为中和反应的药剂而不是常用的液碱等其他药剂。
脱硅的目的是去除废盐酸中除Fe之外的其他金属杂质,以保证盐酸再生后氧化铁粉的质量,因此选用的中和药剂本身不允许其带有其他金属离子,液碱虽然是最常用的液态中和药剂,但其带有Na离子,脱硅反应后的处理酸焙烧反应后Na2O的含量增大,同样会影响铁粉的品质,其他金属氢氧化物作为药剂也同样存在类似问题。
唯有选用氨水,脱硅反应后的处理酸焙烧反应后仅仅是焙烧烟气中水蒸气和氮氧化物的含量增加,可以通过气体洗涤系统去除,而不会影响固态生成物。
因此,尽管氨水药剂在防爆、贮存等方面对设计和运行管理有更高的要求,氨水也是本系统唯一可选的药剂。
脱硅预处理中的废钢片一般选用的是机组的废切边角料,既因地制宜有效利用了机组生产的废弃物,又省去了另外采购钢片或钢丝的费用。
由于游离盐酸与废钢片的反应在常温下反应速率很慢,无法达到连续进行脱硅处理的目的,在废酸进入浸溶塔与废钢片发生反应前,需要通过石墨加热器将废酸加热至80℃左右,已达到较快的反应速率,热媒一般采用蒸汽。
废酸在高温条件下对设备和管道材质的要求较常温条件下要高得多,因此废酸在出浸溶塔进入中和反应前,通过石墨冷却器将废酸降温至45℃左右,冷媒一般采用循环冷却器。
三.脱硅预处理系统主要设备脱硅预处理的处理介质是腐蚀性液体盐酸,设备材质的合理选择是脱硅系统成败的一个关键因素,加上工艺流程中有高温条件和易燃气体产生(H2),因此系统中有几类非常独特的设备,这里重点介绍以下几组设备:1.浸溶塔浸溶塔是脱硅预处理系统中的核心设备,废酸中的游离酸化合反应生成FeCl2的过程在在此设备中发生。