MT-磁轭法平板焊缝磁化方法示意图
2004年特种设备无损检测MT专业Ⅲ级理论试卷

MT成绩:2004年11月27日北京全国锅炉压力容器无损检测人员资格考核委员会一、是非题(在括号内正确的画“○”,错误的画“×”,每题1分,共15分)1、JB4730《承压设备无损检测》(送审稿)规定:如果被检工件表面残留有涂层,其厚度均匀且不超过0.05mm,不影响检测结果时,可以带涂层进行磁粉检测。
(×)2、JB4730《承压设备无损检测》(送审稿)附录C中介绍的绕电缆法的典型磁化方法是摘自欧洲标准EN1290:1998,其中磁化电流计算公式中的磁化电流以有效值表示。
(○)3、JB4730《承压设备无损检测》(送审稿)附录A中介绍的B型标准试块每次使用前都必须进行退磁。
(×)4、JB4730《承压设备无损检测》(送审稿)规定:对于有延迟裂纹倾向的材料,磁粉检测至少在焊接完成24h后进行。
(○)5、JB4730《承压设备无损检测》(送审稿)规定:油基载液粘度在38℃时不大于3.0mm2/s,使用温度下不大于5.0mm2/s,其目的是为了不妨碍磁粉的流动性。
(○)6、磁场指示器(八角试块)使用时应放置在被检工件表面上,且使有铜皮的一面靠近被检表面。
(×)7、JB4730《承压设备无损检测》(送审稿)规定:当供需双方有争议或认为有其他需要时应对检测结果进行复验。
(×)8、JB4730《承压设备无损检测》(送审稿)规定:不是由漏磁场吸附磁粉形成的磁痕显示叫假显示。
(○)9、JB4730《承压设备无损检测》(送审稿)规定:采用同种检测方法按不同检测工艺进行检测时,如果检测结果不一致,应以危险度大的评定级别为准。
(○)10、JB4730《承压设备无损检测》(送审稿)规定:应根据受检设备的材质、结构、制造方法、工作介质、使用条件和失效模式,预计可能产生的缺陷种类、形状、部位和方向,选择适宜的无损检测方法。
(○)11、JB4730《承压设备无损检测》(送审稿)规定的磁悬液的配制浓度是用梨形沉淀管来测定的。
标准MT-PT

第4部分:磁粉检测1 范围JB/T 4730的本部分规定了承压设备磁粉检测方法及质量分级要求。
本部分适用于铁磁性材料制承压设备的原材料、零部件和焊接接头表面、近表面缺陷的检测,不适用于奥氏体不锈钢和其它非铁磁性材料的检测。
与承压设备有关的支承件和结构件,如有要求也可参照本部分进行磁粉检测。
2 规范性引用文件下列文件中的条款通过JB/T4730的本部分的引用而成为本部分的条款。
凡是注日期的引用文件,其随后所有的修改单(不包括勘误的内容)或修订版均不适用于本部分,然而,鼓励根据本部分达成协议的各方研究是否可使用这些文件的最新版本。
凡是不注日期的引用文件,其最新版本适用于本部分。
GB 11533—1989 标准对数视力表GB/T 16673—1996 无损检测用黑光源(UV-A)辐射的测量JB/T 4730.1 承压设备无损检测第1部分:通用要求JB/T 6063—1992 磁粉探伤用磁粉技术条件JB/T 6065—2004 无损检测磁粉检测用试片JB/T 6066—2004 无损检测磁粉检测用环形试块JB/T 8290—1998 磁粉探伤机3 一般要求磁粉检测的一般要求除应符合JB/T 4730.1的有关规定外,还应符合下列规定。
3.1 磁粉检测人员磁粉检测人员的未经矫正或经矫正的近(距)视力和远(距)视力应不低于5.0(小数记录值为1.0), 测试方法应符合GB 11533的规定。
并1年检查1次,不得有色盲。
3.2 磁粉检测程序磁粉检测程序如下:预处理;磁化;施加磁粉或磁悬液;磁痕的观察与记录;缺陷评级;退磁;后处理。
3.3 磁粉检测设备3.3.1 设备磁粉检测设备应符合JB/T 8290的规定。
3.3.2 提升力当使用磁轭最大间距时,交流电磁轭至少应有45N的提升力;直流电磁轭至少应有177N的提升力;交叉磁轭至少应有118N的提升力(磁极与试件表面间隙为0.5mm)。
3.3.3 断电相位控制器采用剩磁法检测时,交流探伤机应配备断电相位控制器。
作业指引——磁粉检测(MT)

文件名称 磁粉检测(MT)作业指引 发布时间磁粉检测(MT)作业指引编制人: 日期:审核人: 日期:批准人: 日期:修订记录日期修订状态修改内容修改人审核人批准人文件名称 磁粉检测(MT)作业指引 发布时间1.质量控制流程图文件名称 磁粉检测(MT)作业指引 发布时间2.检验人员2.1.检验人员必须持有中国船级社(CCS)颁发的资格证书,并在有效期范围内;应按有关规程的规定经过严格培训和考核,并持有相应考核组织颁发的等级资格证书。
2.2.检验人员的视力应每年检查一次,校正视力不低于1.0,无色盲和色弱。
3.检测方法及要求3.1.检验前,焊缝及其附近的母材表面应进行清理,去除表面的油污、焊接飞溅物、松散的铁锈和氧化皮、厚度较大的各种覆盖层(漆层、保温层等);去除放置在表面的各种器具和物品。
3.2.被捡部位在检验中应至少按下述顺序经历了三个检验步骤:a)用磁粉探伤设备进行过必要的磁化;b)在被磁化的区域内用干法施加过干燥的磁粉,或者用湿法施加过磁悬液(即用磁粉或磁膏同载液配制而成的混合液体);c)对施加过磁粉或磁悬液的部位进行磁痕的观察、分析和评定。
3.3.在一般情况下应尽可能采用连续法进行检验。
3.4.焊缝上的每一个检验部位应至少在相互垂直或近于垂直的两个方向上分别得到磁化(有足够依据说明不会产生横向缺陷的情况除外)。
可采用的磁化方式有以下三种:a)纵向磁化加横向磁化——在垂直于焊缝走向和平行于焊缝走向的两个方向上分别进行磁化,先后次序不论。
b)交叉式磁化——在与焊缝走向大致上成+45°和—45°的方向上分别进行磁化,先后次序不论。
c)旋转磁场或摆动磁场磁化——用能在360°或90°平面范围内自动而又连续改变磁场方向的磁场进行磁化。
3.5.一般应在使用适合局部磁化以磁轭法为主。
3.6.用磁轭法磁化焊缝时,每次被磁化的长度范围,最小50mm,最大200mm。
3.7.用湿法施加磁悬液时,施加到被检表面的磁悬液应尽可能均匀分布,并利用载液的流动特性带动磁粉流动。
磁粉检测-第二章 磁化方法

第二章 磁化方法和磁化规范 2020年11月2日
星期一
5、环形件绕电缆法:
是用软电缆穿绕环形件通电 磁化,形成沿工件圆周方向的周 向磁场,用于发现与磁化电流平 行的径向缺陷,如图2-12所示。 它的优点是非电接触,可避免烧 伤工件。缺点是效率低,不适用 于批量检验。
2-12 环形件绕电缆法
第二章 磁化方法和磁化规范 2020年11月2日
影响材料性能。
第二章 磁化方法和磁化规范 2020年11月2日
星期一
触头法用较小的磁
化电流就可在工件局部
得到必要的磁场强度,
灵敏度高,使用方便。
触头间距应控制在75~
200mm为宜,最短不能 小于75mm,因为在触
图2-10 触头法磁化的有效磁化区(阴影部分)
头附近25mm范围内电流密度过大,产生过度背景,有可能掩
星期一
②应尽量避免工件与电磁轭之间的气隙; ③当极间距大于1m时,工件磁化效果很差; ④形状复杂而且较长的工件,不宜采用整体磁化。 局部磁化要求:便携式电磁轭的磁极间距L一般应控制在75~ 200mm为宜。因为磁极附近25mm范围内,磁通密度过大会 产生过度背景,有可能掩盖相关显示。在磁路上总磁通量一定 的情况下,工件表面的磁场强度随两极间距L的增大而减小, 所以磁极间距也不能太大。 磁轭法优点:①非电接触;②改变磁轭方位,可发现任何方向 的缺陷;③可带到现场,使用灵活方便;④可用于检验带漆层 的工件;⑤检测灵敏度较高。
第二章 磁化方法和磁化规范 2020年11月2日
星期一
磁轭法缺点:①几何形状复杂的工件检验较困难;②一次 磁化只能检验较小的区域,大面积检验时,费时费力。 3、永久磁轭法:可用于对工件局部磁化,适用于无电源和不 允许产生电弧的易燃易爆场所。但在检验大面积工件时,不能 提供足够的磁场强度以得到清晰的磁痕显示,磁场大小也不能 调节。永久磁铁磁场太大时,吸在工件上难以取下,磁极上的 磁粉也不容易被清除掉,还可能把缺陷磁痕弄模糊,所以很少 使用。
焊缝的磁粉检测技术

1.3 磁粉检测的优缺点
1.3.1 磁粉检测的优点 (1) 能直观的显示出缺陷的位置、形状和大小; (2) 可检测出铁磁性材料表面和近表面的缺陷; (3) 检测速度快、工艺简单、成本低、污染少; (4) 灵敏度高,可检测微米级宽的缺陷。 1.3.2 磁粉检测的缺点 (1) 不能检测非铁磁性材料; (2) 不能检测埋藏较深的缺陷; (3) 不容易发现与工件表面夹角极小的缺陷; (4) 直接通电法和触头法因为易产生电弧烧伤工件 而不适用于对表面质量要求较高的工件进行检测; (5) 不能通过对磁痕的分析直接判断缺陷本身的深
141 141
Mining & Processing Equipment
第 35 卷 2007 年第 10 期 缺陷,检测效率很低,因此磁轭法尤其是便携式磁轭 在现场检测时一般只是作为一种辅助磁粉检测方法。
焊缝的磁粉检测技术
2.2 磁化电流的选择
为了在工件上产生磁场而采用的电流称为磁化电 流。磁粉检测采用的磁化电流有交流电、整流电 (单相 半波整流电、单相全波整流电、三相半波整流电和三 相全波整流电)、直流电和冲击电流。其中最常用的磁 化电流有交流电、单相半波整流电和三相全波整流 电,它们在磁粉检测时具有不同特点,应根据不同情 况进行选取。 用交流电磁化时,由于交流电具有趋肤效应,对 于表面微小缺陷检测灵敏度高,但当缺陷在工件表面 2 mm 以下时一般无法检测。由于交流电在生产和生活 中使用最为广泛,在现场易于找到交流电源,因此在 压力容器检验时常用交流电作为磁化电流。另外,用 交流电不但易于退磁,而且两次磁化的工序间可以不 退磁。 整流电能检测近表面较深的缺陷 (最深可达 4 mm),同时因为其含有交流成分,因此对表面缺陷也 有较高的检测灵敏度。在条件具备的情况下应尽量采 用整流电。 直流电可检测到的缺陷深度最大,可检测出 6 mm 深的缺陷,但几乎检测不到表面缺陷,因此有很大的 局限性。
磁粉检测工艺卡的编制
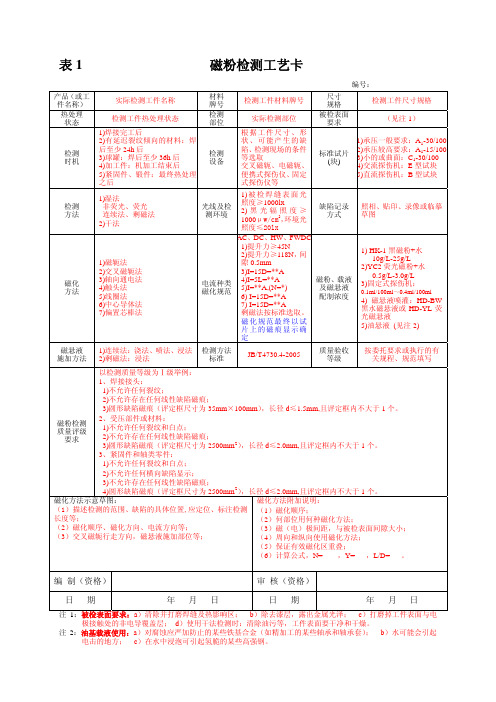
检测 方法
1)湿法 非荧光、荧光
连续法、剩磁法
2)干法
磁化 方法
1)磁轭法 2)交叉磁轭法 3)轴向通电法 4)触头法 5)线圈法 6)中心导体法 7)偏置芯棒法
光线及检 测环境
1) 被 检 焊 缝 表 面 光 照度≥1000lx 2) 黑 光 辐 照 度 ≥ 1000μw/cm2,环境光 照度≤20lx
施加方法 2)剩磁法:浸法
标准
JB/要求或执行的有 关规程、规范填写
以检测质量等级为Ⅰ级举例:
1、焊接接头:
1)不允许任何裂纹;
2)不允许存在任何线性缺陷磁痕;
3)圆形缺陷磁痕(评定框尺寸为 35mm×100mm),长径 d≤1.5mm,且评定框内不大于 1 个。
照相、贴印、录像或临摹 草图
1) HK-1 黑磁粉+水 10g/L-25g/L
2)YC2 荧光磁粉+水 0.5g/L-3.0g/L
3)固定式探伤机:
0.1ml/100ml~0.4ml/100ml
4) 磁悬液喷灌:HD-BW 黑水磁悬液或 HD-YL 荧 光磁悬液 5)油悬液 (见注 2)
磁悬液 1)连续法:浇法、喷法、浸法 检测方法
4)圆形缺陷磁痕(评定框尺寸为 2500mm2),长径 d≤2.0mm,且评定框内不大于 1 个。
磁化方法示意草图:
磁化方法附加说明:
(1)描述检测的范围、缺陷的具体位置,应定位、标注检测 长度等; (2)磁化顺序、磁化方向、电流方向等; (3)交叉磁轭行走方向,磁悬液施加部位等;
(1)磁化顺序; (2)何部位用何种磁化方法; (3)磁(电)极间距,与被检表面间隙大小; (4)周向和纵向使用磁化方法;
5
缺陷评级
磁轭法

8. 磁轭法(1) 磁轭法是用固定式电磁轭两磁极夹住工件进行整体磁化,或用便携式电磁轭两磁极接触工件表面进行局部磁化,用于发现与两磁极连线垂直的缺陷。
在磁轭法中,工件是闭合磁路的一部分,用磁极间对工件感应磁化,所以磁轭法也称为极间法,属于闭路磁化,如图3-28和图3-29所示。
图3-28 电磁轭整体磁化图3-29 电磁轭局部磁化(2) 整体磁化用固定式电磁轭整体磁化的要求是:①只有磁极截面大于工件截面时,才能获得好的探伤效果。
相反,工件中便得不到足够的磁化,在使用直流电磁轭比交流电磁轭时更为严重;②应尽量避免工件与电磁轭之间的空气隙,因空气隙会降低磁化效果;③当极间距大于1m时,工件便不能得到必要的磁化。
④形状复杂而且较长的工件,不宜采用整体磁化。
(3) 局部磁化用便携式电磁轭的两磁极与工件接触,使工件得到局部磁化,两磁极间的磁力线大体上平行两磁极的连线,有利于发现与两磁极连线垂直的缺陷。
图3-30 便携式磁轭磁化的有效磁化区(阴影部分)便携式电磁轭,一般做成带活动关节,磁极间距L一般控制在75mm-200mm为宜,但最短不得小于 75mm。
因为磁极附近25mm范围内,磁通密度过大会产生过度背景,有可能掩盖相关显示。
在磁路上总磁通量一定的情况下,工件表面的磁场强度随着两极间距L的增大而减小,所以磁极间距也不能太大。
JB/T4730.04-2005规定:“磁轭的磁极间距应控制在75mm~200mm之间,检测的有效区域为两极连线两侧各50mm的范围内,磁化区域每次应有不少于15mm的重叠”。
欧洲标准EN1290也规定便携式电磁轭磁化的有效磁化区如图3-30的阴影部分,面积约为(L-50)×(L/2)mm2。
交流电具有趋肤效应,因此对表面缺陷有较高的灵敏度。
又因交流电方向在不断地变化,使交流电磁轭产生的磁场方向也不断地变化,这种方向变化可搅动磁粉,有助于磁粉迁移,从而提高磁粉检测的灵敏度。
而直流电磁轭产生的磁场能深入工件表面较深,有利于发现较深层的缺陷。
磁粉检测(MT-Ⅱ)知识点总结

精心整理磁粉检测(MT-Ⅱ)知识点总结磁粉检测原理铁磁性材料和工件被磁化后,由于不连续性的存在,使工件表面和近表面的磁感应线发生局部畸变而产生漏磁场,吸附施加在工件表面的磁粉,形成在合适光照下目视可见的磁痕,从而显示出不连续性的位置、形状、大小和严重程度。
磁粉检测的基础是不连续性处漏磁场与磁粉的磁性相互作用。
6局限性:1.只能适用于检测铁磁性材料,不适用于检测奥氏体不锈钢及其他非铁磁性材料22.只适合检测工件的表面和近表面缺陷3.检测时的灵敏度与磁化方向有很大关系,若缺陷方向与磁化方向近似平行或缺陷与工件表面夹角小于20°,缺陷就难以发现。
4.受几何形状影响,易产生非相关显示5.若工件表面有覆盖层,将对磁粉检测有不良影响,在通电法和触头发磁化时,易产生打火烧伤6.部分磁化后具有较大剩磁的工件需进行退磁处理磁粉检测的七个程序:(1)预处理;(2)磁化;(3)施加磁粉或磁悬液;(4)磁痕的观察与记录:(5)缺陷评级;(6)退磁;(7)后处理。
磁力线具有以下特性:1)磁感应线是具有方向性的闭合曲线。
在磁体内,磁感应线是由S极到N极;在磁体外,磁感应线是由N极出发,穿过空气进入S极的闭合曲线。
2)磁感应线互不相交。
3)磁感应线可描述磁场的大小和方向。
4)磁感应线沿磁阻最小路径通过磁场强度H=I/(2πr)在SI单位制中,磁场强度的单位是安(培)/米(A/m)奥(斯特)Oe;磁感应强度又称为磁通密度。
在SI单位制中,磁感应强度的单位是特(斯拉)(T)=104高斯(Gs)μμo=α,用Br(1)(2)通电圆柱导体的磁场磁场方向:与电流方向有关,用右手定则确定。
磁场大小:安培环路定律计算通电长导体导体表面的磁场强度为:H=I/2πR导体外r处(r>R)的磁场强度:H=I/2πr导体内部r处(r<R)磁场强度:H=Ir/2πR2用交流电和直流电磁化同一钢棒时,其共同点是:1)在钢棒中心处,磁场强度为零;2)在钢捧表面,磁场强度达到最大;3)离开钢棒表面,磁场强度随r的增大而下降。
磁粉无损检测中12种常见磁化方法的特点

磁粉无损检测中12种常见磁化方法的特点在磁粉探伤中用到的各种磁化方法,如轴向通电法、中心导体法、偏置芯棒法、触头法、感应电流法、环形件绕线电缆法、线圈法、磁轭法、永久磁轭法、交叉磁轭法、直流电磁额与交流通电法复合磁化法、平行电缆磁化法等,其本质都是裂痕、杂质等缺陷处破坏被测部件或区域的正常磁力线的分布,从而出现缺陷处磁粉的堆积现象。
各种磁化方法是依据被检缺陷的所处位置及方向,被检工件或区域的材料性质、厚度、大小、外形、工艺要求,检测方法的操作频率及容易度等细分。
下面就来具体分析各种磁粉探伤中磁化方法的特点。
1.轴向通电法指磁化电极固定轴类部件两端,使磁化电流沿轴类件轴向通过的方法,用于发现与电流平行的纵向缺陷。
其优点是:①操作简单、方便、效率高、灵敏度高;②磁化电流产生周向磁场基本集中在工件的表面及近表面;③磁化电流取值与长度无关;④磁化规范易计算;⑤工件端头无磁极,不产生退磁场;⑥可用大电流在短时间内大面积磁化。
其缺点是:①磁化电流与工件接触不良会产生电击伤;②不能检测半空心工件;③磁化细长工件易变形。
适用于检测机加工件、轴类、管子、铸钢件和锻钢件及特种设备实心和空心工件的焊缝。
示意图:2.中心导体法指磁化导线位于空心轴类部件中轴线的磁化方法,用于发现与电流平行的纵向缺陷及与以磁化导线为圆心的径向缺陷。
其优点是:①工件无电击伤出现;②可检测空心工件各个面;③可一次磁化多个工件;④一次通电,工件全长都能得到周向磁化;⑤操作简单、效率高、灵敏度高。
其缺点是:①检测厚壁工件外表面缺陷的灵敏度偏低;②仅适用于通孔类工件的检验;适用于检测机加工件、管子、铸钢件和锻钢件及特种设备工件等空心工件的焊缝。
示意图:3.偏置芯棒法指磁化导线贯穿空心轴类部件的磁化方法,用于发现与电流平行的纵向缺陷及与以磁化导线为圆心的径向缺陷。
其优点是:①工件无电击伤出现;②可检测空心工件各个面;③可一次磁化多个工件;④一次通电,工件全长都能得到周向磁化;⑤灵敏度高;⑥可用相对较小磁化电流检测较大直径及厚壁类的轴类件。
【基础理论】图解磁化传递技术

【基础理论】图解磁化传递技术磁化转移(magnetization transfer,MT)是近年来推出的MR 成像新技术之一,该技术通过物理方法增加图像对比度或制造一种新的对比。
对于一般组织来说,MR成像的对象实际上是水分子中的质子。
水分子有自由水和结合水之分。
所谓自由水是指不依附于蛋白质分子,且自由运动充分自由的水分子,其T1值和T2值都非常长,难以形成快速有效的弛豫,只有非常窄的频率范围(<0~100Hz)可以激发该池形成共振;结合水是指依附于蛋白质,其自然运动受到限制的水分子,即蛋白质水化层的水分子。
蛋白质分子及结合水中的质子进动频率范围很宽,且T2值很短,所以对MR图像的信号几乎没有直接贡献。
结合水可能与大分子蛋白发生交叉弛豫和化学交换,又可作为自由水与大分子蛋白发生磁化传递的载体,所以通常蛋白质分子与结合水统称为结合池,自由水分子称为自由池。
磁化传递是氢质子在以下三个池之间传递能量的过程:- 自由水- 结合水- 蛋白大分子MR成像时,一般都以自由水中的质子进动频率作为中心频率,如果我们在MR成像序列(可以是GRE序列或SE序列)前,给组织施加一个偏离中心频率约1000~1200Hz的饱和脉冲,那么自由水中的质子不被激发,而蛋白质分子和结合水中的质子将受激发而获得能量。
蛋白质分子和结合水中的质子从射频脉冲得到的能量将传递给其周围的自由水,我们把这种能量传递称为磁化转移。
由于磁化转移,获得能量的自由水将被饱和,当MR成像真正的射频脉冲来临时,这部分水分子将不再能受到能量,未被饱和的自由水才能受到激发。
几乎各种组织都含有一定量的蛋白质和结合水,由于MT预脉冲的施加和MT现象的存在,这些组织中的自由水将不同程度产生饱和效应,因此组织的信号强度将不同程度降低。
各种组织中蛋白质和结合水的含量是不同的,MT效应造成的信号强度衰减程度也将存在差别,这种由于磁化转移现象造成的对比被称为磁化转移对比(magnetization transfer contrast,MTC)。
MT-PT课件

(2) 磁痕分析。在实际的磁粉检测中,磁痕的成因是 多种多样的。观察磁痕时,应特别注意区别假磁痕显示、 无 关显示和相关显示(即缺陷磁痕)。在通常情况下,正确识别 磁痕需要丰富的实践经验,同时还要了解被检工件的制造工 艺。 如不能判断出现的磁痕是否为相关显示时,应进行复验。 磁粉检测中常见的相关磁痕主要有:发纹、非金属夹杂物、 分层、 材料裂纹、 锻造裂纹、 折叠、 焊接裂纹、 气孔、 淬 火裂纹和疲劳裂纹等。
4 系统性能与灵敏度评价
在磁粉检测中,要用标准试板、试环和磁场指示器评价磁 粉检测系统的总性能及检测的灵敏度。其中试板和试环主要用 于评价磁粉检测系统的综合性能,并间接考查检测的操作方法 是否合理。磁场指示器除具有上述用途外,还可以定性地反映 被检测表面的磁场分布特征, 确定磁粉检测的磁化规范。
5 退磁 在大多数情况下,被检工件上带有剩磁是有害的,故须 退磁。 所谓退磁就是将被检工件内的剩磁减小到不妨碍使用 的程度。常用的退磁方法有交流退磁法和直流退磁法。 6 后处理 磁粉检测以后,应清理掉表面上残留的磁粉或磁悬液。 油磁悬液可用汽油等溶剂清理;水磁悬液应先用水进行清洗, 然后干燥。如有必要,可在备检表面上涂敷防护油。干粉可 以直接用压缩空气清除。
图9 毛细现象
毛细现象使液体在管内上升的高度h可用下式计算:
2σ cosθ h= Rρg
力系数;R为细管半径;g为重力加速度。
(6)
式中:θ为液面与管壁接触角;ρ为液体的密度;σ为表面张
磁化过程 二. 磁化过程 1 磁化方法 工件磁化时,当磁场方向与缺陷延伸方向垂直时,缺陷处 的漏磁场最大,检测灵敏度最高。当磁场方向与缺陷延伸方向 夹角为45°时,缺陷可以显示,但灵敏度降低。当磁场方向与 缺陷延伸方向平行时,不产生磁痕显示,发现不了缺陷。 由 于工件中缺陷有各种取向,难以预知,故应根据工件的几何形 状,采用不同的方法直接、间接或通过感应电流对工件进行周 向、纵向或多向磁化,以便在工件上建立不同方向的磁场, 发现所有方向的缺陷,于是出现了各种不同的磁化方法,主要 有通电法、中心导体法、触头法、线圈法、磁轭法、多向磁化 法等。
特种设备无损检测(NDT)磁粉检测(MT)工艺编制及优化

MT工艺编制及优化1 磁粉探伤工艺方法分类及选择1.1 磁粉探伤工艺方法的分类:1.1.1 按施加磁粉的载体分两种:干法(荧光、非荧光)、湿法(荧光、非荧光)。
1.1.2 按施加磁粉的时机分两种:连续法、剩磁法。
1.1.3 按磁化方法分六种:轴向通电法、触头法、线圈法、磁轭法、中心导体法、交叉磁轭法。
1.2 磁粉探伤工艺方法的一般选择原则:1.2.1 连续法和剩磁法都可进行探伤时,优先选择连续法。
1.2.2 对于湿法和干法,优先选择湿法。
1.2.3对于按磁化方法分类的六种探伤方法,优先选用要根据工件的形状、尺寸、探伤操作的困难程度进行。
2 磁粉探伤工艺方法具体介绍2.1 连续法:2.1.1 概念:在磁化的同时,施加磁粉或磁悬液。
2.1.2 适用范围:①形状复杂的工件;②剩磁Br (或矫顽力Hc)较低的工件;③检测灵敏度要求较高的工件;④表面覆盖层无法除掉(涂层厚度均匀不超过0.05mm)的工件。
2.1.3操作要点:①先用磁悬液润湿工件表面;②磁化过程中施加磁悬液,磁化时间1S-3S;③磁化停止前完成施加操作并形成磁痕,时间至少1S;④至少反复磁化两次。
2.1.4优点:1)适用于任何铁磁性材料。
(2)具有最高的检测灵敏度。
(3)可用于多向磁化。
(4)交流磁化不受断电相位的影响。
(5)能发现近表面缺陷。
(6)可用于湿法和干法检验。
2.1.5局限性:(1)效率低。
(2)易产生非相关显示。
(3)目视可达性差。
2.2 剩磁法:2.2.1 概念:停止磁化后,施加磁粉或磁悬液。
2.2.2 适用范围:①矫顽力Hc在1000A/m以上,并保持剩磁Br在0.8T以上的工件,一般如经过热处理的高碳钢和合金结构钢(淬火、回火、渗碳、渗氮、局部正火);低碳钢、处于退火状态或热变形后的钢材都不能采用剩磁法;②成批的中小型零件进行磁粉检测时;③因工件几何形状限制连续法难以检验的部位。
2.2.3操作要点:①磁化结束后施加磁悬液;②磁化后检验完成前,任何磁性物体不得接触被检工件;③磁化时间一般控制在0.25-1S;④浇磁悬液2 –3遍,或浸入磁悬液中10—20S,保证充分润湿;⑤交流磁化时,必须配备断电相位控制器。
MT通用工艺规程2015

1 适用范围1.1 本规程规定了公司承压设备焊缝及其原材料、机加工部件磁粉检测方法和质量分级要求。
1.2 本规程适用于铁磁性材料制板材、复合板材、管材、管件和锻件等表面和近表面缺陷的检测,以及铁磁性材料对接接头、T型焊接接头盒角接接头等表面或近表面缺陷的检测,不适用于非铁磁性材料的检测。
1.3 承压设备有关的支撑件和结构件也可参照本规程进行磁粉检测。
2 依据标准TSG R0004-2009《固定式压力容器安全技术监察规程》GB150-2011《压力容器》NB/T47013-2015《承压设备无损检测》3 术语和定义本规程引用设术语和定义按照NB/T47013.1中第3条款及NB/T47013.4中第3条款的界定。
4 一般要求4.1 检测人员4.1.1 从事磁粉检测的人员应满足NB/T47013.1的有关规定。
4.1.2 磁粉检测人员视力应不低于5.0(小数记录值为 1.0),测试方法应符合GB11533的规定;并每年检查一次,不得有色盲。
4.2磁粉检测程序a)预处理;b)磁化;c)施加磁粉或磁悬液;d)磁痕的观察和记录;e)缺陷的评级;f)退磁;g)后处理。
4.3 检测工艺文件4.3.1 检测工艺文件包括工艺规程和操作指导书。
4.3.2 本规程规定了下列相关因素的具体范围或要求;当相关因素的一项或几项发生变化并超出规定时,应重新编制或修订本规程。
4.3.3 应根据本规程内容和被检工件的检测要求编制操作指导书,其内容除满足NB/T47013.1的要求外,至少还应包括:a)检测区域和表面要求;b)检测环境要求;c)检测技术要求:灵敏度试片显示、磁化方法、磁化规范、磁化时间等;d)磁粉或磁悬液的施加方法;e)磁痕观察条件;f)退磁要求。
4.3.4 操作指导书在首次应用前应采用标准试件进行工艺验证,以确认是否能达到标准规定的要求。
4.4 安全要求4.4.1 电流短路引起的点击或大电流引起的灼伤。
4.4.2 使用或去除多余磁粉,尤其是干磁粉时的悬浮颗粒物等吸入等伤害。
MT操作及判定

1.简述及相关标准磁粉探伤是通过对铁磁材料进行磁化所产生的漏磁场,来发现其表面或近表面缺陷的无损检测方法。
国标:NB/T47013.4-2015;美标:ASTM E1444/E709、ASME V第7章;欧标:EN 99342.磁粉探伤的基本原理磁粉探伤是通过磁粉在缺陷附近漏磁场中的堆积以检测铁磁性材料表面或近表面处缺陷的一种无损检测方法。
磁粉探伤的基本原理:将待测物体置于强磁场中或通以大电流使之磁化,若物体表面或表面附近有缺陷(裂纹、折叠、夹杂物等)存在,由于它们是非铁磁性的,对磁力线通过的阻力很大,磁力线在这些缺陷附近会产生漏磁。
当将导磁性良好的磁粉(通常为磁性氧化铁粉)施加在物体上时,缺陷附近的漏磁场就会吸住磁粉,堆集形成可见的磁粉迹痕,从而把缺陷显示出来,如图1所示。
(a)(b)图1 磁粉探伤原理示意图(a) 表面缺陷(b) 近表面缺陷3、磁化方法与设备3.1 磁轭法在压力容器制造和在用检验中,以焊缝检测为主,一般采用便携式电磁轭,因其结构简单、重量轻、使用方便。
磁轭法适用于大型工件的局部检测,如对接焊缝、角焊缝、筒体钢板母材及坡口等的检测。
其特点是设备简单、操作方便。
NB/T47013 标准规定磁轭法的磁化规范可根据灵敏度试片或提升力来确定。
对于磁轭,当使用电磁轭最大间距时,交流电磁轭至少应有44N 的提升力。
3.2 设备1)马蹄形磁粉探伤仪:无锡市捷成检测设备制造有限公司 XMTY——II 型2)反差增强剂:上海新美达探伤器材有限公司 FA-53)黑油磁悬液:上海新美达探伤器材有限公司 MT-BO4.磁粉探伤的工艺根据被探件的材料、形状、尺寸及需检查缺陷的性质、部位、方向和形状等的不同,所采用的磁粉探伤方法也不尽相同,但其探伤步骤大体如下:1、探伤前的准备校验探伤设备的灵敏度,除去被探伤件表面的油污、铁锈、氧化皮等。
2、磁化(1)确定探伤方法对高碳钢或经热处理(淬火、回火、渗碳、渗氮)的结构钢零件用剩磁法探伤;对低碳钢、软钢用连续法。
关于ISO标准磁轭法检测焊缝的探讨

96材料与工艺 广东造船2023年第5期(总第192期)作者简介:张国林(1989- ),男,工程师。
主要从事船舶及海洋工程无损检测工作。
黄增文(1995- ),男,助理工程师。
主要从事船舶及海洋工程无损检测工作。
收稿日期:2023-06-27关于ISO 标准磁轭法检测焊缝的探讨张国林,黄增文(招商局重工(深圳)有限公司,深圳 518054)摘 要:本文基于ISO 标准磁轭法检测技术在修造船厂的应用,结合笔者的现场经验,分别对磁极间距、有效磁化区域、系统灵敏度验证、有效磁化区域的重叠、固定长度焊缝的最少磁化次数作了详细阐述,列举了现场磁轭检测技术存在的一些不合理做法,并对其进行纠正,对于磁轭法检测焊缝的操作具有现实的指导意义。
关键词:ISO 标准;磁轭;磁粉;检测技术;焊缝中图分类号:U672.9 文献标识码:ADiscussion on ISO Standard Magnetic YokeMethod for Detecting WeldsZHANG Guolin, HUANG Zengwen( China Merchants Heavy Industry (Shenzhen) Co., Ltd., Shenzhen 518054 )Abstract: The article is based on the application of ISO standard magnetic yoke testing technology in shipyard inspection, and combines the author's on-site experience to provide a detailed explanation of magnetic pole spacing, effective magnetization area, system sensitivity verification, overlap of effective magnetization area and minimum magnetization times for fixed length welds. It lists some unreasonable practices in on-site magnetic yoke testing technology and corrects them. It has practical guiding significance for the operation of magnetic yoke method for inspecting welds.Key words: ISO standards; magnetic yokes; magnetic powder; testing techniques; welds1 前言ISO 为国际标准化组织的简称,是目前应用最为广泛的标准体系之一。
特殊铁磁构件的磁轭法检测

磁粉检测作为各标准规范常用检测方法,在核电、锅炉、化工压力容器等设备制造检验过程中有着广泛的应用,标准TSG 11-2020《锅炉安全技术监察规程》、TSG 21-2016《固定式压力容器安全技术监察规程》规定,在可执行磁粉检测的情况下优先推荐使用磁粉检测。
磁粉检测在铁素体材料的检测方面有着无可比拟的优势,标准NB/T 47013.4-2015《承压设备无损检测第4部分:磁粉检测》对磁轭磁粉检测的极间距、磁化方向、磁化次数、磁化时间进行了明确规定,并在附录B(资料性附录) 《各类焊接接头的典型磁化方法》中列举了平板对接接头、板-板T型角接接头、管-板角接接头、管-管角接接头等结构的磁轭磁化方法。
实际工作中遇到的结构类型不止这几类,不同的结构对磁粉检测磁化的要求会有极大的不同。
相关标准未给出一些特殊结构(如焊道层间焊缝、焊缝反面清根区域、焊缝挖补区域、狭窄间隙焊缝的坡口和根部等)的磁化方法,只能参考标准选择合适的检测设备及检测规范,根据试验验证的情况来选择合适的磁化方法。
触头法的应用同样受工件结构的限制,由于其易打火烧伤工件,某些产品会明确禁止使用触头法。
线圈法和绕线法在现场检测应用不方便,相对来说,磁轭法是实际应用中操作灵活、使用方便的一种磁粉检测方法。
1工件结构与磁场分布分析为描述方便,把平板对接接头几何结构表述为一型结构,如图1所示;把角接接头(包括板-板T型角接接头、管-板角接接头、管-管角接接头)结构表述为L型结构,如图2所示;把文中提到的特殊结构(如狭窄间隙焊缝坡口面和根部区域)表述为U型结构,如图3所示。
图1 一型结构示意图2 L型结构示意图3 U型结构示意★一型结构的特点是:① 需磁化区域与两个磁极在同一平面;② 磁场从磁极进入工件后,沿直线传播到下一磁极,磁场路径变化极小,磁场强度随深度的增加逐步减弱;③ 磁极容易与工件表面贴合,磁化操作便捷,工艺简单。
L型结构的特点是:① 磁化区域与两个磁极均不在同一平面,两磁极所在平面呈90°夹角;② 磁场从磁极进入工件后,沿工件表面弯曲传播到另一磁极,最大弯曲角度为90°,磁场强度随深度的增加逐步减弱;③ 磁极不易贴合工件表面,尤其是管管对接接头,一旦贴合不好,检测区域很难达到磁化要求,建议选用斜面接触头磁极。