全承载客车技术的普及与应用
大型客车车身结构及焊装工艺分析

大型客车车身结构及焊装工艺分析 大型客车车身焊装是大型客车生产中的一个重要环节,车身焊装质量是影响大型客车整体质量优劣的重要因素之一。
针对大型客车车身结构特点及其工艺性,在本文中将重点分析焊装工艺、设备、夹具的特点,总结我国大型客车车身焊装生产现状及与国际水平的差距,希望通过我们共同的努力,能不断改进国产大型客车车身焊装生产工艺,提高车身焊装质量。
大型客车车身结构特点 大型客车车身是由底骨架、左/右侧围骨架、前/后围骨架及顶围骨架等6大片骨架经组焊蒙皮而成,是一骨架蒙皮结构。
根据客车车身承受载荷程度的不同,可把客车车身概括地分为半承载、非承载、全承载式三种类型。
1、半承载式车身 半承载式车身结构特征是车身底架与底盘车架合为一体。
通过在底盘车架上焊接牛腿、纵横梁等车身底架构件,将底盘车架与车身底架进行焊接连接,然后与左/右侧骨架、前/后围骨架及顶骨架组焊成车身六面体。
车身底架与底盘车架共同承载,因此称为半承载式车身。
2、非承载式车身 非承载式车身的底架为独立焊制的,是矩形钢管和型钢焊制的平面体结构,比较单薄。
车身底架与左/右侧骨架、前/后围骨架及顶骨架组焊成车身六面体,漆后的车身要装配到三类底盘上,由底盘车架承载,因此称为非承载式车身。
3、全承载式车身 全承载式车身底架为珩架结构,由矩形钢管和型钢焊制而成,底架与左/右侧骨架、前/后围骨架及顶骨架共同组焊成车身六面体。
漆后的车身采用类似轿车的装配工艺,在车身(底架)上装配发动机、前后桥、传动系等底盘部件,因此客车已无底盘车架痕迹,完全由车身承载,因此称为承载式车身。
三种结构车身的焊装工艺性 1、半承载式车身 半承载式车身是在三类底盘上焊制的,生产中底盘自始至终要经过生产的各个环节,因此在焊装生产中也产生一些工艺问题。
如:由于底盘大大增加了车身质量,使车身在焊装线工序运输中不灵便,人工推运困难,往往需要增加机械化输送机构;此外,由于车身六面体合焊时需要在合装设备中定位底盘,为此合装设备需要设计底盘举升机构用于底盘二次定位,因此增加了合装设备造价。
全承载大型客车车身骨架梁单元与壳单元模型有限元计算对比
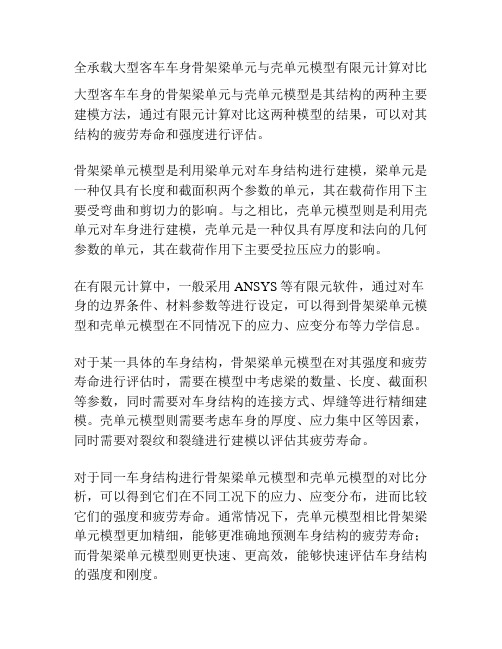
全承载大型客车车身骨架梁单元与壳单元模型有限元计算对比大型客车车身的骨架梁单元与壳单元模型是其结构的两种主要建模方法,通过有限元计算对比这两种模型的结果,可以对其结构的疲劳寿命和强度进行评估。
骨架梁单元模型是利用梁单元对车身结构进行建模,梁单元是一种仅具有长度和截面积两个参数的单元,其在载荷作用下主要受弯曲和剪切力的影响。
与之相比,壳单元模型则是利用壳单元对车身进行建模,壳单元是一种仅具有厚度和法向的几何参数的单元,其在载荷作用下主要受拉压应力的影响。
在有限元计算中,一般采用ANSYS等有限元软件,通过对车身的边界条件、材料参数等进行设定,可以得到骨架梁单元模型和壳单元模型在不同情况下的应力、应变分布等力学信息。
对于某一具体的车身结构,骨架梁单元模型在对其强度和疲劳寿命进行评估时,需要在模型中考虑梁的数量、长度、截面积等参数,同时需要对车身结构的连接方式、焊缝等进行精细建模。
壳单元模型则需要考虑车身的厚度、应力集中区等因素,同时需要对裂纹和裂缝进行建模以评估其疲劳寿命。
对于同一车身结构进行骨架梁单元模型和壳单元模型的对比分析,可以得到它们在不同工况下的应力、应变分布,进而比较它们的强度和疲劳寿命。
通常情况下,壳单元模型相比骨架梁单元模型更加精细,能够更准确地预测车身结构的疲劳寿命;而骨架梁单元模型则更快速、更高效,能够快速评估车身结构的强度和刚度。
总的来说,大型客车车身的骨架梁单元模型和壳单元模型都有其优缺点,选择哪种模型建模应根据具体情况而定。
对比分析两种模型的有限元计算结果可以得到较为全面的评估结果,对于车身结构的优化设计和改进具有一定的指导意义。
基于上述对骨架梁单元模型和壳单元模型的分析,实际上在实际工程应用中,取决于具体的结构设计需求的不同,可以采用单独一种材料或同时设置骨架梁和壳单元来合并应用,来完成对车辆骨架和外壳的建模。
从功能和优化角度来看,应用骨架梁和壳单元并做优化,可以满足更加细致和实用的设计要求,就像现代高层建筑一样,某些部位采用框架结构,而高风险部位则采用坚固的钢结构,该结构不仅强度足够,而且成本不会太高,更加经济实惠。
推进客车技术进步,“全力承载”乘客生命安危——探源安凯客车全承载专利技术对我国客车技术进步的贡献

“ 5 载技 术 的未来和如何促进 中国客车 励 当地客 运企 业采购 全承 载客 车 。 王江 安董事长 说 :通过 1年 的技术 开发 ,安凯上上下下都有种技术情 行 业的 自主研 发。 国内市场上 ,除了安凯一直宣传采 用 了全承载 车身外 ,很多客车企业 结。正 是这种技术情节和对新技术
此前, 由于全承载车身技术的优 越性 , 使得全承载车身技术成为高端 客车的技术标杆之一, 很多客车企业
开始搭这班顺风车。 一度客车市场各 处都充斥着 “ 载”安凯客车本来 全承 ,
安凯全承 载客车车身结构
独有 的全承载车身成为大家都有 的装
普通 客车的结构车身在整 车受
到外力作用 时,特别是 翻滚 时,因
一
时将力通过封闭的连接结构迅速分 解 到整车各 处 ,使车身整体 受力均 匀 ,避 免单 点承受外 力,能在受撞 击时保 证车厢 内的变形最小 ,使乘 客空 间得到有 效 的保 障,确保 车内镉 2 0 -0 i 0 8, '
特 别 关 注
发展 ”—— 安 凯客车全承 载发 明专
全承载车身技 术特有 的车身 结
\ ~
一
利媒体 沟通会 。安凯客车高层首次 构 ,能大大提 高客车 的安全性 、节
自1 9 年安 凯在 国 内率先 开始 3 9
就 获得 全承载发 明专利 一事与媒体 油性和使用寿命 ,很多购车者认识 采 用全承 载技 术 制造 豪华大 客车 , 见面 ,同时与行业协会领 导、行业 到这 点 ,点名购买采用全承载车 身 至今全 承载技术 已经在 中国发展 了
全承载客车制造工艺流程

全承载客车制造工艺流程安徽安凯汽车股份有限公司杨继才[摘要]:简要介绍了全承载客车制造工艺流程及优点关键词:全承载客车,工艺流程。
全承载式车身技术可以形象地被称为鸟笼结构”,以前一直应用于飞机制造业的整体化框架结构技术。
传统的客车在受撞击时底盘会移位,而由于全承载客车的无底盘结构,在制造工艺上与非承载式车身有相似之处,均有冲压、焊装、涂装、总装、检测几个主要工艺,但是在局部内容上仍存在较大区别,下面就全承载客车制造的主要工艺流程做以下说明:一、焊装工艺流程基于全承载的车身结构,安凯客车在小总成焊接、五大片制作、骨架总拼、校正及内外蒙皮的焊装工艺方面有别于国内其他厂家,具有明显的自身特点及其优势。
主要工艺流程:K福酗还阿TTS- --------------------------- * T*林班¥»-童用于挥栈车司且禅屹集及五丈片总遵主产探擅1•小总成焊接:小总成焊接采用16Mn矩形管,是全承载车身的重要特征,其性能较其他钢材有更好的强度2. 底架及五大片焊接:底架及五大片焊接采用可靠工装进行焊接,保证了底盘及车身内外饰安装的精度3. 骨架总拼:骨架采用全承载结构,骨架总成采用液压翻转举升总拼台总拼,使整车骨架的合拢精度更高。
4. 骨架校正:使用火焰对骨架焊接变形部位进行校正,使整车平整度、窗框吻合度等达到更高的精度。
和同行业客车骨架相比有更高的抗冲击性能,安全性能更好。
5. 车身内蒙皮:内蒙皮全部采用双面镀锌板材,使用单面点焊工艺,并且使用安凯特有的火焰校正工艺,对蒙皮进行校正,有效提高蒙皮涨紧度,降低整车噪音。
由于全承载的结构优势,整车密封可以在焊装工序一次性完成,相对于其他结构车型密封难以实现一次或完全密封,有很大的优势。
镀锌板材的防锈蚀性能使用使安凯客车比同行业车辆有更高的使用寿命。
6. 车身外蒙皮:车身蒙皮使用辊压镀锌蒙皮和模压成型件,采用单面点焊焊接工艺,该工艺能有效提高蒙皮的平整度,基本实现大面蒙皮不刮灰。
客车全承载产品知识及产品关键特性

8-9.49 2006 2007 232 340 0 10 0 0 242 2.1% 11381 97.9% 0 14 0 0 354 4.5% 7440 95.5%
小计 956 0 88 0 0 1044 3.3% 30180 96.7%
2005 52 14 1 0 6 73 0.9% 8465
9.5-10.99 2006 2007 84 58 13 8 0 7 112 1.1% 10503 10 17 0 0 85 1.2% 6866
该形式的车身具有 较大的抗弯曲和抗扭转的刚度,质 量小,汽车质心低,高速行驶稳定性较好,但由于道路 负载会通过悬架装置直接传给车身本体,因此噪音和 振动衰减要求更高。
2.2、整体承载式车身(integral construction):此种结构是整个车身都参与承 载,在承受载荷时,“牵一发而动全身”,其本身就可以根据自然法则,自动调 节,以强济弱,使整个车身壳体达到稳定平衡状态。
小计 194 37 26 0 13 270 1.0%
2005 594 139 378 2 97 1210 10.4%
11-13.7 2006 2007 490 422 179 479 1 79 1228 10.3% 10677 89.7% 183 467 36 23 1131 12.6% 7838 87.4%
说明:国内通称的全承载车身即指承载式车身
三种技术路线对比 1、典型特征对比 典型特征 非承载式车身 半承载式车身 承载式车身
独立车架
车身与车架联接方式 承载主体 2、性能对比 性能项目 安全性 燃油经济性
有
挠性联接 车架承载
有,目前有直大梁、三段式结构
刚性联接 车身部分参与承载,车架为主
无
全承载旅游客车结构有限元分析与轻量化改进

本 文采用 有限元 分析方 法对承 载式旅 游客 车车
身 骨架的强度 、 扭 转 刚度 和 车顶 承 载能 力 进行 理 论
中载 荷作用 点 、 支 承点 及 构 件 的拐 点 等作 为 模 型 的
7 / 3 5
22 — 2 5
长 春 工程 学 院学 报 ( 自然 科 学 版 )2 0 1 3年 第 1 4卷 第 3期
J . C h a n g c h u n I n s t . Te c h . ( Na t . S c i . Ed i . ), 2 0 1 3 , Vo 1 . 1 4, No 3
0 引言
承 载式 大客 车 车身 骨架 是 整车 的基 体 , 车 身 骨
架是 由薄 壁 杆件 构 成 的复 杂 的空 间高 次 超 静 定 结 构, 承受 着客车 的所 有 动 、 静态 载 荷 , 受 力情 况 比较 复杂, 结 构分析难 度大 。在设计 初期 , 因缺 乏建立 力 学 特性 ( 强度、 刚 度) 分析 基础 的科学依 据 , 仅 靠经 验 和类 比进 行设计 和选 用 型 材 , 如对 于 某 些应 该 减 少 的构件 、 厚度减 薄 的构 件或 改变结构 形式 的议案 , 因 元 明确 的依据 , 设 计 中也 不敢轻 易决 定 , 使 得设计 偏 向保守 , 承载构 件得不 到充 分利用 , 而导致 客车 自重 过大 , 成 本过高 。而 当在车 身结构 强度 出现 问题 时 , 往往采 用局部加 强 的方 式 , 结 果导 致质量 越来越 大 ,
车 的结构 和承载特 点作 了以下 的简化 :
全承载技术培训材料1

全承载技术和全承载客车全承载的发展历程:早期的汽车都是非承载式的,车辆的载荷都由底盘承受。
低端大客车是有车架的底盘从力学角度分析低端大客车有卡车的柔性车架,从扭转刚性角度看,卡车上层车厢和下层车轴叶片弹簧悬挂都是刚性的,当道路坑洼不平时,中层的柔性车架的作用,除全部承载外还起到关键的缓冲层的作用.所以卡车是三层式结构,即上硬中软下硬.随着汽车技术的发展出现了承载式车身,最早的承载式车身出现在轿车上,承载式车身不仅仅客车的一种车身技术。
客车的承载式车身可以追溯到飞机的承载式车身,汽车上很多的技术都是从飞机技术上演化过来的,如:客车全承载车身技术、ABS技术、航空座椅等技术,包括材料和设计方法的应用都是从飞机上演化而来的。
由于传统的客车在受撞击时底盘会移位,而由于全承载客车的无底盘结构,使其在受力时能将力迅速分解到全身各处,同时全承载客车抗扭曲的钢件设施强度也是其他普通汽车的3-6倍。
因此在40年代末和50年代初,凯斯鲍尔率先将飞机上应用的全承载技术引用到客车上,随后尼奥普兰,雷诺、沃尔沃、MAN等欧洲的大客车企业逐渐都采用了全承载式车身。
高端大客车的首要特征是没有中间的软层-柔性车架,刚性底架与刚性车身构成一个刚性整体,承载车辆的全部负荷.是两层式。
高端大客车的特征之一:具有无车架的全承载车身可以说全承载客车是我国目前最安全的客车之一。
采用全承载结构,使客车的行车更加具有敏捷性、平稳性、舒适性和安全性,再加上其低地板设计、人性化配置、低排放、环保化、乘客空间大等优势,体现出现代社会倡导的“科技领先,以人为本”的理念,也造就了全承载客车独一无二的产品优势。
目前全承载客车技术在高档客车和制造水平和设计水平比较高的企业应用较为普遍。
高端大客车无车架的承载式车身在全承载发展的50年中,随着设计手段、设计水平、材料的应用和工艺水平的提升,全承载技术也在逐渐进步。
目前采用的全承载技术已经经过了几十年的发展,是比较成熟的一种技术。
Setra

Setrasetra凯斯鲍尔200系300系400系公司简介•SETRA和凯斯鲍尔•SETRA在中国的发展•SETRA车型介绍SETRA S200系SETRA S300系SETRA S400系公司简介Setra (赛特拉)戴姆勒-克莱斯勒公司旗下Evobus公司商用车品牌。
Setra标志如果查找任何一本有关Setra历史的资料,都能很容易在醒目的位置找到其创始人凯斯鲍尔的介绍。
从1896年开始,凯斯鲍尔在德国的乌尔姆市创建了以他名字命名的公司,从那时开始,凯斯鲍尔就开始生产专门用于旅客运输的客车了,但是直到1950年,在凯斯鲍尔公司的基础上才正式更名为Setra公司,而此时的Setra则专门致力于制造豪华型客车。
在客车历史上,Setra公司首次完成了全承载式车身的设计,由于全承载式的车身具备三大优势:安全系数大大提高,车身重量得以减少,增加车内乘客空间。
因此,当全承载式车身出现之后,很快便给世界客车工业带来了革命性的变化,现在欧洲客车已经普遍采用了全承载式的车身设计,目前全承载式车身设计在我国也得到了广泛的应用。
另外,在1984年Setra还在全球第一次将ABS列为了客车的标准配置设备。
目前,Setra公司城市客车主要以NF和UL系列为主,长途客车则以HD,HDH和DT系列为主。
1996年S315NF被评为了欧洲年度客车奖,2001年,其Top Class 400再次获得该项殊荣。
在奖台之外,Setra在市场上也获得了不俗的业绩。
2002年12月,S415HDH在上市18个月之后,销量就突破1000辆。
目前作为Evobus的分支,Setra和Mercedes-Benz 在2002年共销售了客车和底盘6720台,实现了8%的增长,而Evobus也因为有了Setra和Mercedes-Benz,其在德国的市场占有率目前已经高达57%。
SETRA和凯斯鲍尔赛特拉(Setra)是艾瓦客车公司旗下两个著名客车品牌之一。
- 1、下载文档前请自行甄别文档内容的完整性,平台不提供额外的编辑、内容补充、找答案等附加服务。
- 2、"仅部分预览"的文档,不可在线预览部分如存在完整性等问题,可反馈申请退款(可完整预览的文档不适用该条件!)。
- 3、如文档侵犯您的权益,请联系客服反馈,我们会尽快为您处理(人工客服工作时间:9:00-18:30)。
一
( ) 能加工设 备 的维护也是 3智 件 不可轻视 的工作 。 : 如 智能合
产过程 中,基 本上用的都是矩形管 前能支持客车三维设计的三维设计 装设 备 、弯管 机 成 形设 备 也 不 能 材料 ,压制件不多了 。这将省下许 系统越来越多 。 排 除故 障 的 可能 性 ,这 些 设 备 是 多费用 。 ( )全承 载客车 技术工序 难点 专业设 备 ,出了故 障, 3 若不 能及 时 ( )客车车身防腐 处理一直 是 是焊 装工序 的点位精度 。 目前 ,这 修复 ,生产 线将 会停止 。 强智能 3 加 行业较为头痛的事。若采取整车处 种合装设备 越来越智能化 、 轻量化 , 加 工设 备 人 才 的培 养 ,是 确保 无
成的客车。长期以来 ,我 国的客车 化是一种总的趋势。客车所 需的功 是菜单式要求 ,而要满足用户要求 生产是处于货车改装状态 。直到 2 能要求客车设计必须对客车进行总 的主动权往往 又在主要总成件的布 0 却不在车身布置层。 实际操 在 世纪 8 年代后期 , 0 仍然许 多客车生 体思考 、进行系统性布置 ,即要基 置层 , 人”的要求来设计客车 ,总的 作 中,这种体 制是无法满足市场多 产厂家还被称作客车改装厂或称作 于 “ 要求是要人性化设计。人性 化必然 样化需 求的。如果没有底盘生产权 客车装配厂 ,其主要原 因是我国 长 要求客车设计和制造模 式要从货车 的厂家采用 了全承载车身技术生产 期没有客车专用底盘 生产 厂家。 这一技术壁垒将不复存在。 目 没有客车专用的底 盘 ,当然是 模式中跳 出来。轿车布置是人性化 客车 , 生产不出真正意义的客车。到了 2 设计的典范 ,客车设 计轿车 化是一 前 已经取得 了客车底盘生产权的客 0 车厂家也意识 了这个 问题 ,于是抢 世纪末 ,我 国开始生产专用客车底 种必然。 盘 ,于是我 国客车生产开始呈规模
()运用全承载技术以后 ,客 2 式的发展 。发展 到 20 年 ,我国 已 06 术 车 制造不再需要大型冲压设备。传 经成 为世界 上第一 客车 生产大 国 。 客车设计轿车化是一种总 的趋 统技术 下需要太多的压制件 ,压 制 但是大多数客车生产仍与货车生 产
0 原理是相 同的,即先有底盘 ,后制 势 ,但是客车乘客 l 人以上 ,有 的 件生产 除了需要一次性投入较大的 达到达 2 0 以上 ,而轿车 只有 4 冲压设备 以外 ,还需要大量的模具 0人 ~ 作客车车 身。
下运用传统客车技术制造出的客车 情 况能 充分地说 明这 一 问题 。 安全性完全是有保 障的 ,无论是 长 ( )事实上 ,客车生产技术 比 3
4全承载客车技术受众厂家钟
情的真正原因
( )有底盘生产权的厂 家处于 1 途 、旅游和公交的乘客都 可以放 心 货车技术要复杂得多 。主要原 因是 优势地位 ,各 客车厂家争取有底盘 地乘坐 , 不存在技术层面 的安全性 。 我国客车生产技术长期落后于货车 生产权的积极 性一直很高 。国家行
车 。可 以说 明全承载客车技术的应
用将得到普及。
2承载货物与承载人的运输工 的设计师 受飞机骨 架设计 的启发 ,
具存在本质上 区别
2 世 目前讨论 “ 应用全承
在 客车设计 中尝试全封闭的车身结
构 。用各种矩形管焊接成一个整体 的车身骨架 ,让车身和底架成为一
1客车生产技术源于货车生产
生产 技术。随着 时代的发展和社会 业管理部 门出于对行 业的保 护 ,对 的进步 ,按 照货车 的生产方式来生 客车底盘生产资质设 立了很 高的门
这样一来 , 底盘 与车身 由不同生 众所周知 ,15 年我国生产 出 产客车 ,已经 阻碍 了客车行业的发 槛 。 97 产厂家分别生产 ,无法适用市场多 我国 自己的第一 台客车。但是事 实 展和进步 。 ( )当前客车设计与布景轿车 样化的需求 。 4 当前 , 客车最终用户都 上这 一台客车是基 于货车底盘改装
3全承载客车技术源于飞机技
先推进 “ 全承载技术”的应用。
3 域弓4 8 辐 2 0 -2 0 7/
维普资讯
技 术 与 研 究
作支撑 ,经常性开模费用也是相当 计方面 ,要求计算软 、硬件技术的 大 的。全承载技术条 件下 ,客车生 支撑。 主要三维设计系统的支持。 当
个不带大梁的整体 , 即为 “ 全承载车 身” 。全承载车身技术的出现 ,标志
( )运用货车 的生产方式生产 真正 区别于货车设计和制造的客车 2 对推动全承载客车技术应用也没有 出来的客车 ,是无法 充分满足人们 技术时代 的到来。
太多 的益处 。这是 因为我国各客车 对客车功能上 的要求 ,当然包括更 生产厂家在国家现行安全技术标准 高的安全性 。我 国客车 的实 际生产
维普资讯
技 术 与 研 究
全承载客车技术的普及与应用
雷 洪 钧
但车 身与底盘 的设 计和 生产与 5 个乘客 , 以说 ,客车设计、制造 所 货车生产一样 仍然是截 然不 同的两 与轿车也有不小差异 。客车与飞机 厦 门金旅等厂家都推 出了全承载技 术的客车 ,从用途上分 ,已经应用 个部分 ,所不同的是 ,一个用于载 同属众人 出行承载工具 ,全 承载客 另一个用于 载人 叫车身 。 车 技术源 于飞机 技术是一 种必然 。 到了公路 、 旅游 、 公交3 大类型的客 货叫货箱 , 目前 , 青年 、宇通 、厦 门金龙 、
载客车技术” 的主要结论是 : 基于更 ( )先生产 出底盘 ,再对其改 1 安全 ,即全承载车身能够在汽车翻 装成各 种用途 的货车 的方式是完全 滚及相撞时, 最大限度减小变形 , 能 符 合货 车的生 产规律 的。而这方式 保证乘客 的安全空间 。笔者认为这 并非完全适宜直接用来生产客车 。 种观点是不全面的 , 也是不公正的 ,